Echo CS-550 Mounting instructions

INTRODUCTION
We are constantly working on technical im-
provement of our products. For this reason,
technical data, equipment and design are
subject to change without notice. All speci-
fications and directions in this SERVICE
DATA are based on the latest product infor-
mation available at the time of publication.
ECHO SERVICE MANUAL Ord. 401-31
(Model : CS-600) contains additional infor-
mation for servicing this model.
SERVICE DATA
CHAIN SAW
ECHO: CS-550
STAGE MODEL
(Serial number : 37000001 and after)
CONTENTS
page
1 SERVICE INFORMATION.............................. 2
1-1 Specification ............................................... 2
1-2 Technical data............................................. 3
1-3 Torque limits................................................ 4
1-4 Special repairing materials ......................... 5
1-5 Service limits............................................... 6
1-6 Special tools ............................................... 7
2
CARBURETTOR ADJUSTMENT PROCEDURE
.. 8
2-1 General adjusting rules............................... 8
2-2 Presetting Idle adjust screw, L mixture needle
and H mixture needle ....................................... 8
2-3 Adjusting carburettor................................... 9
Reference No. 01-54B-00
ISSUED: 201102
CS-550
01-54B-00 1
0

1 SERVICE INFORMATION
1-1 Specifications
Dimensions Length mm(in) 448 (17.64)
Width mm(in) 253 (9.96)
Height mm(in) 284 (11.18)
Dry weight* kg(lb) 6.0 (13.2)
Engine Type
YAMABIKO, stratified scavenging, air-cooled, two-stroke,
single cylinder Ventilated piston, Semi-automatic decompression
Rotation Clockwise as viewed from the output end
Displacement cm3(in3) 54.1 (3.301)
Bore mm(in) 45.0 (1.772)
Stroke mm(in) 34.0 (1.339)
Compression ratio 7.2
Carburettor Type Diaphragm horizontal-draught
Model Walbro WLA-4 with Large D-shaped mixture needles
Venturi size-Throttle bore mm(in) 13.49 - 15.85 (0.531 - 0.624)
Ignition Type CDI (Capacitor discharge ignition) system
Digital magneto
Spark plug BPMR8Y
Exhaust Muffler type Spark arrester muffler
Starter Type Automatic rewind
Rope diameter x length mm(in) 4.0 x 950 (0.15 x 37.4)
Fuel Type Premixed two-stroke fuel
Mixture ratio 50 : 1 (2 %)
Petrol Minimum 89 octane petrol
Two-stroke air cooled engine oil ISO-L-EGD (ISO/CD13738), JASO FC/FD
Tank capacity L (U.S.fl.oz.) 0.53 (17.9)
Clutch Type
Inboard clutch : Centrifugal, 3-shoe slide with 3-tension spring
Guide bar / Saw chain lubrication type Automatic with volume adjuster
Tank capacity, oil L (U.S.fl.oz.) 0.3 (10.1)
Sprocket Type Floating rim
Number of teeth 7
Pitch in 0.325, 3/8
* Without guide bar and saw chain.
Oregon Saw chain 21BPX
Cutting devices
Guide bar Part No. 38RV58-325E 45RV58-325E 50RV58-325E
Called length cm 38 45 50
Gauge in 0.058
Saw chain Number of drive links 64 72 80
Pitch in 0.325
Gauge in 0.058
SERVICE INFORMATION CS-550
2

1-2 Technical data
Engine
Idling speed r/min 2,800 +/- 200
Wide open throttle speed* r/min 12,500 - 13,500
Clutch engagement speed r/min 4,000
Minimum†r/min 3,300
Compression pressure MPa (kgf/cm2) (psi) 1.04(10.6)(151)
Ignition system
Spark plug gap mm(in) 0.6 - 0.7 (0.024 - 0.028)
Minimum secondary voltage at 1,500 r/min kV 17
Primary coil resistance Ω300 - 340
Secondary coil resistance kΩ2.5 - 2.9
Pole shoe air gaps mm(in) 0.30 - 0.40 (0.012 - 0.016)
Ignition timing at 3,000 r/min °BTDC 5
at 8,000 r/min °BTDC 24
at 12,000 r/min °BTDC 28
PET-9000 Parameter 1 325
Parameter 2 03
Carburettor
Idle adjust screw initial setting turns in** 1 3/8
L mixture needle initial setting turns out*** 1 3/8
H mixture needle initial setting turns out*** 3 3/8
Test Pressure, minimum MPa (kgf/cm2) (psi) 0.05 (0.5) (7.0)
Metering lever height mm(in) 1.50 (0.06) lower than diaphragm seat
Chain oil discharge volume at 7,000 r/min Adjustable 1.5 - 13 (0.05 - 0.39)
mL/min(U.S.fl.oz./min) (Factory set 7.0 mL/min)
BTDC: Before top dead center.
*With 50 cm guide bar and properly adjusted saw chain.
**Set idle adjust screw to the point that its tip just contacts throttle plate before initial setting.
***Turn L/H mixture needles anticlockwise from point that needle is lightly seated.
†If clutch engagement speed is lower than minimum r/min, replace clutch assembly with new one.
Oregon Saw chain 73LGX
Cutting devices
Guide bar Part No. 40RV58-3/8E 45RV58-3/8E 50RV58-3/8E
Called length cm 40 45 50
Gauge in 0.058
Saw chain Number of drive links 60 64 72
Pitch in 3/8
Gauge in 0.058
SERVICE INFORMATIONCS-550 3

1-3 Torque limits
Descriptions Size kgf•cm N•m in•lbf
Starter
system
Starter pawl M5* 60 - 100 6 - 10 50 - 90
Starter case M5 30 - 50 3 - 5 25 - 45
Brake lever side M5* 70 - 90 7 - 9 60 - 80
Ignition
system
Magneto rotor (Flywheel) M8 160 - 200 16 - 20 140 - 175
Ignition coil M5 35 - 50 3.5 - 5 30 - 45
Spark plug M14 130 - 170 13 - 17 113 - 150
Fuel
system
Carburettor M5 30 - 40 3 - 4 25 - 35
Intake bellows M5 75 - 95 7.5 - 9.5 65 - 85
Clutch Clutch hub LM10 300 - 400 30 - 40 265 - 350
Cylinder cover Fan cover side M6 15 - 25 1.5 - 2.5 13 - 22
Recoil side M5 15 - 30 1.5 - 3 13 - 25
Engine Crankcase M5†60-90 6-9 50-80
Cylinder M5†60-100 6-10 50-90
Cylinder cover M5 60 - 90 6 - 9 50 - 80
Muffler M5* 70-110 7-11 60-95
Muffler plate M4 15 - 25 1.5 - 2.5 13 - 22
Exhaust gasket M5 70 - 110 7 - 11 60 - 95
Other Auto-oiler M4 30 - 50 3 - 5 25 - 45
Compression spring
Engine M5 30 - 45 3 - 4.5 25 - 40
Crankcase M5 60 - 80 6 - 8 50 - 70
Front handle M5 60 - 90 6 - 9 50 - 80
Front handle M6 40 - 55 4 - 5.5 35 - 48
M5 40-60 4-6 35-50
Rear handle M5 40 - 60 4 - 6 35 - 50
Brake lever M5 60 - 90 6 - 9 50 - 80
Brake cover M5* 40 - 60 4 - 6 35 - 50
Sprocket guard plate M4* 15 - 25 1.5 - 2.5 13 - 22
Spring holder M5 30 - 45 3 - 4.5 25 - 40
Spike M5 60 - 90 6 - 9 50 - 80
Ignition switch M10 15 - 30 1.5 - 3 13 - 25
Guide bar M5 200 - 230 20 - 23 175 - 200
Regular bolt, nut and screw M3 6 - 10 0.6 - 1 5 - 9
M4 15 - 25 1.5 - 2.5 13 - 22
M5 25 - 45 2.5 - 4.5 22 - 40
M6 45 - 75 4.5 - 7.5 40 - 65
M8 110 - 150 11 - 15 95 - 130
LM: Left-hand thread
*Thread locking sealant (See next page)
†The torque difference between four bolts should not exceed 20 kgf•cm (2N•m, 17in•lbf) per bolt.
SERVICE INFORMATION CS-550
4

1-4 Special repairing materials
Material Location Remarks
Adhesive Guide bar stud Loctite #609, ThreeBond #1373 or equivalent
Starter case Brake lever side
Starter center shaft screw Loctite #222, ThreeBond #1342 or equivalent
Grease Auto-oiler worm
Clutch needle bearing
Rubber cushion, inside
Choke knob
Lithium based grease or ECHO XTended
Rewind spring
Protection
TM
Lubricant
Oil seal inner lips
Starter center shaft
Brake cover
Chain brake (metal contact part) Molybdenum grease (approx. 1 gram)
Thread locking sealant Muffler
Sprocket guard plate Loctite #242, ThreeBond #1324 or equivalent
Starter pawl
SERVICE INFORMATIONCS-550 5

5K083 5K084 5K081
5K082 5K016 5K025
5K174 5K181 5K097
5K173 5K097
5K253
5K254
5K181
ABCD
EFGH
KLMP
N
1-5 Service Limits
Description mm (in)
ACylinder bore When plating is worn and aluminum can be seen
BPiston outer diameter Min. 44. 89 (1.767)
CPiston pin bore Max. 11. 035 (0.4344)
DPiston ring groove Max. 1. 35 (0.053)
EPiston ring side clearance Max. 0. 1 (0.004)
FPiston pin outer diameter Min. 10. 98 (0.4323)
GPiston ring width Min. 1. 15 (0.045)
HPiston ring end gap Max. 0. 5 (0.02)
KCon-rod small end bore Max. 15. 025 (0.5915)
LCrankshaft runout Max. 0. 01 (0.001)
MSprocket bore Max. 13. 90 (0.5472)
NClutch drum bore Max. 71. 5 (2.81)
PSprocket wear limit Max. 0. 5 (0.02)
SERVICE INFORMATION CS-550
6

b
0
0.4
50
0.8
1.2
1.
MPa
0
Ignition Air Gap Gauge
#.014 = .35mm
P/N 91004
b
OPPAMA
PET-9000
INTEGRATED IGNITION ANALYZER
PET-304
b
5.5
1
7
4
3
2
1476
2
8
3
9101112
13
18 19 20 21
14 15
22
16 17
23
5
b = 4 mm
b = 5 mm
b = 6 mm
b = 6 mm
1-6 Special tools
Key Part Number Description Used for:
1 G310-000050 Tachometer PET-304 Measuring engine speed to adjust carburettor
2 X605-000050 Torx L wrench (T27) Removing and installing bolt
3 897537-30130 Piston stopper Locking crankshaft rotation
4 897724-01361 Spring pin tool (4 mm) Removing and installing spring pin (4 mm dia)
5 897724-02831 Spring pin tool (5 mm) Removing and installing spring pin (5 mm dia)
6 897719-02830 Piston holder Making piston steady to remove and install piston / rings
7 897702-30131 Piston pin tool Removing and installing piston pin
8 897501-03938 Puller Removing magneto rotor
9 91004 Module air gap gauge Adjusting pole shoe air gaps
10 897502-19830 Crankcase tool Separating crankcase
11 897701-14732 Bearing tool Removing and installing ball bearings on crankcase
12 91037 Compression gauge Measuring cylinder compression
13 Y089-000090 D-shaped tool Adjusting mixture needle
14 91024 Pressure tester Testing crankcase leakages
15 897726-16431 Oil seal tool Installing starter side oil seal
16 897800-79931 Spark tester PET-4000 Checking ignition system
17 897803-30133 Pressure tester Testing carburettor leakages
18 900300 Ignition Analyzer : PET-9000
Measuring Ignition timing, Primary/Secondary voltage engine speed
19 897714-12330 Oil seal tool
Installing crankcase side oil seal
20 91041 Pressure rubber plug Plugging
exhaust port to test crankcase / cylinder leakages
21 895624-32731 Torx T wrench (T27) Removing and installing bolt
22 897826-16131 Pressure rubber plug Plugging intake port to test crankcase / cylinder leakages
23 897827-16131 Pressure plate Plugging intake port to test crankcase / cylinder leakages
SERVICE INFORMATIONCS-550 7

1
7
4
3
2
(A)
(B)
(C)
(D)
2 CARBURETTOR ADJUSTMENT PROCEDURE
2-1 General adjusting rules
A. Before adjustment, check the following items.
1. The correct spark plug must be clean and properly gapped.
2. The air filter element must be clean and properly installed.
3. The muffler exhaust port must be clear of carbon.
4. The fuel lines, tank vent and fuel filter are in good condition and clear of debris.
5. The fuel is fresh ( > 89 octane : RON ) and properly mixed at 50 : 1 with “ISO L-EGD” or “JASO FC/
FD” 2-stroke oil.
6. The recommended bar and chain must be installed, and properly tensioned.
NOTE : In order to achieve proper carburettor adjustment, a 38, 40, 45 or 50 cm bar and chain should be
installed on the unit. Otherwise serious engine damage will occur due to overspeeding.
B. Preliminary adjustment. Adjustment by Idle adjust screw of carburettor.
Start and run engine for two minutes alternating engine speed between WOT for 10 seconds and idle
for 10 seconds. Adjust idle speed screw to 2,800 +/- 150 r/min. Make sure WOT engine speed in range
12,500 - 13,500 r/min. If engine does not run correctly after this adjustment, proceed to the next step 2-2.
2-2 Presetting Idle adjust screw, L mixture needle and H mixture needle
Tools Required : Small screwdriver with 2.5 mm
blade, P/N G310-000050 electronic tachometer,
P/N Y089-000090 D-shaped tool (A).
1. Turn L and H mixture needle clockwise until
lightly seated, and then turn out both mixture nee-
dles following turns.
L mixture needle (B) : 1 3/8
H mixture needle (C) : 3 3/8
NOTE : If needles are overtighted during seating,
damage to carburettor may occur.
2. Turn Idle adjust screw (D) anticlockwise until
idle adjust screw tip just touches throttle plate.
Then turn it clockwise 1 3/8 turns.
NOTE : The initial carburettor settings for idle
adjust screw, L and H mixture needles are
intended to start and run the engine before making
final carburettor adjustments to meet Emission
Directive. Actual turns required for engine
operation may vary.
SERVICE INFORMATION CS-550
8

(B)
(A)
(C)
1
7
4
3
2
(D)
(C)
(A)
1
7
4
3
2
2-3 Adjusting carburettor
1. Start and warm engine for 1 minute alternating
engine speed between WOT and idle every 5 sec-
onds. Turn H mixture needle (C) anticlockwise until
engine speed drops to approx. 12,000 r/min at WOT.
NOTE : Do not run engine at high speed without
load longer than 10 seconds, or engine damage
may occur.
2. Adjust L mixture needle (B) using D-shaped tool
(A) to reach maximum engine speed just before
lean r/min drop off.
3. Set idle speed to 3,600 r/min by turning Idle
adjust screw (D). Engine speed should be stable
at 3,600 +/- 50 r/min after Idle adjust screw
adjustment.
4. Turn L mixture needle (B) anticlockwise reduc-
ing engine idle speed 800 r/min to set idle speed at
2,800 r/min. The idle speed range is 2,700 - 2,900
r/min.
NOTE : Engine speed must be allowed to stabilize
a minimum of 20 seconds after each adjustment
of L mixture needle to assure accurate tachometer
readings.
5. After adjustment L mixture needle, WOT engine
speed should be 12,000 r/min or less before
adjustment H mixture needle. If engine speed is
higher, turn H mixture needle (C) anticlockwise
until 12,000 r/min is achieved.
Stabilize engine for
45 seconds alternating engine
speed between
WOT for 10 seconds and idle for 5 seconds
.
To make the final WOT engine speed adjustment,
turn the H mixture needle (C) clockwise in 1/8 turn
increments with the engine at idle. After each ad-
justment, accelerate to WOT, and check engine
speed. The final engine speed should fall within
12,800 - 13,000 r/min at WOT.
6. Start engine, and verify engine idle speed ranges from 2,600 to 3,000 r/min, and WOT engine speed
ranges from 12,500 to 13,500 r/min. Make sure the chain does not rotate when engine is idling. When
final adjustment is completed, the engine should idle, accelerate smoothly, and attain WOT per above
specifications.
NOTE : Engine WOT, and idle engine speed in field operation may vary from final adjustment specifica-
tions due to changing ambient conditions, fuel, and engine loads. Safe engine speed variances should be
within the WOT, Idle engine speed ranges listed in Section 1-2, otherwise the carburettor should be read-
justed.
SERVICE INFORMATIONCS-550 9
Table of contents
Other Echo Saw manuals

Echo
Echo QV-670 Instruction Manual
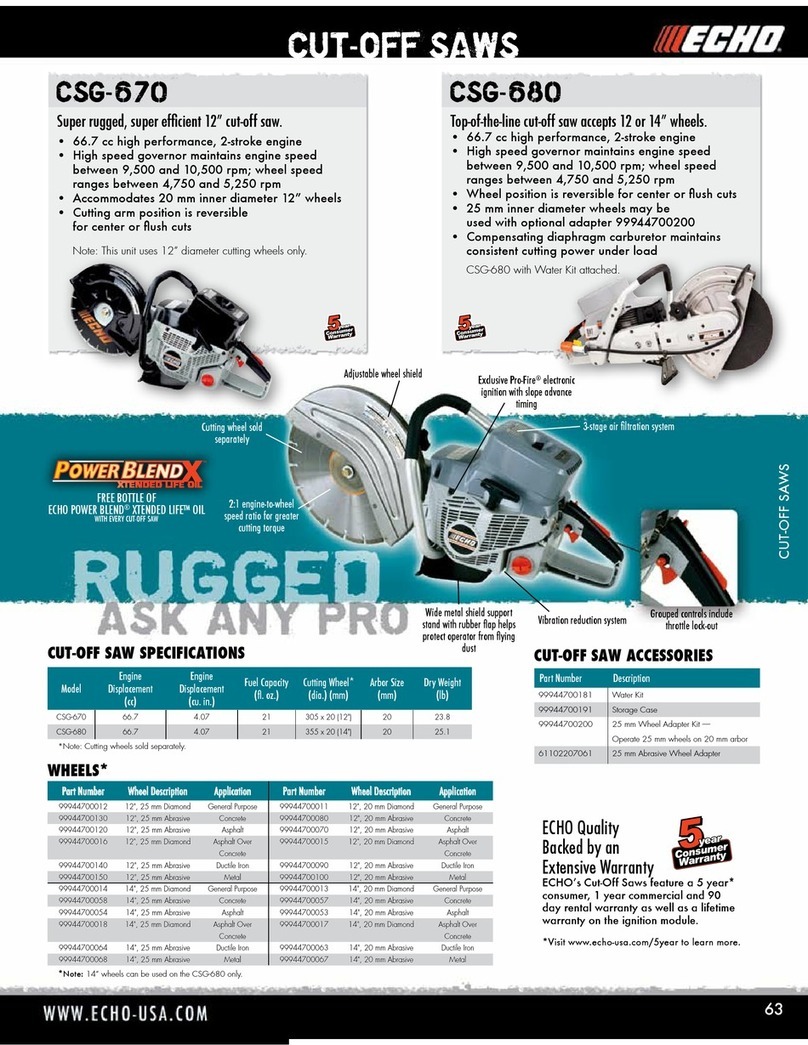
Echo
Echo Power Blend CSG-670 User manual
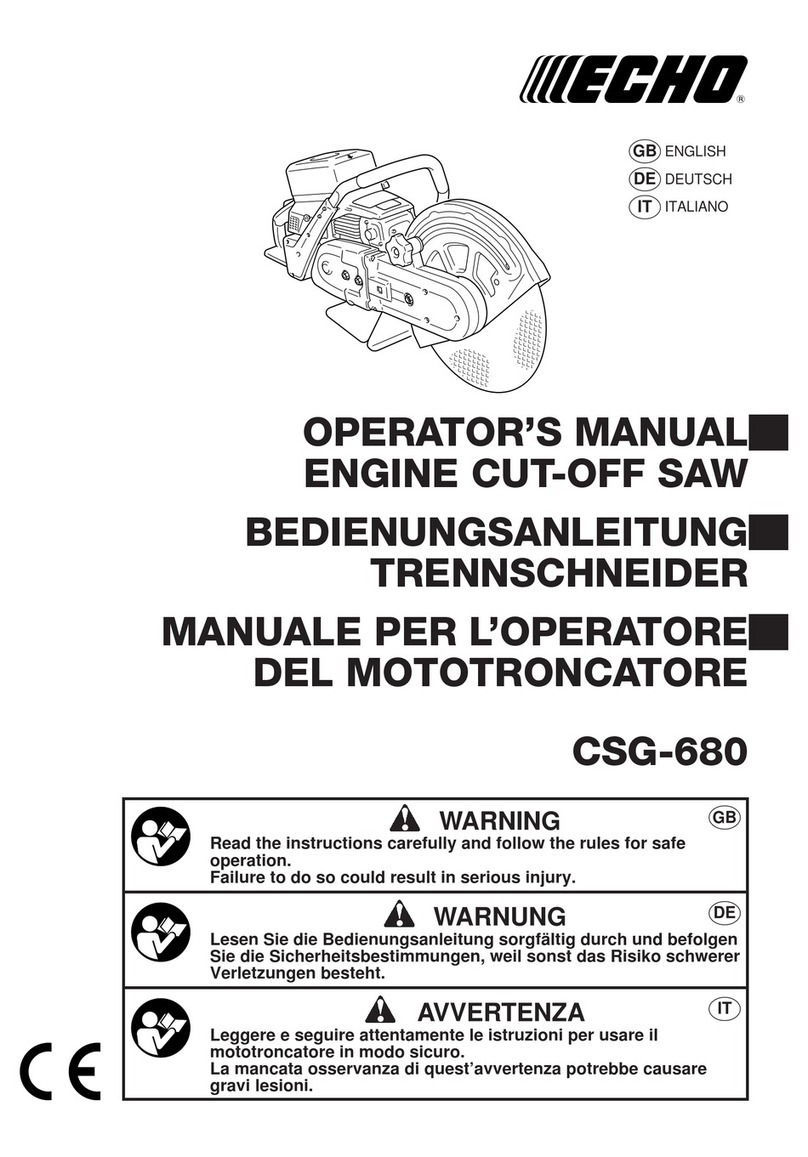
Echo
Echo Power Blend CSG-680 User manual
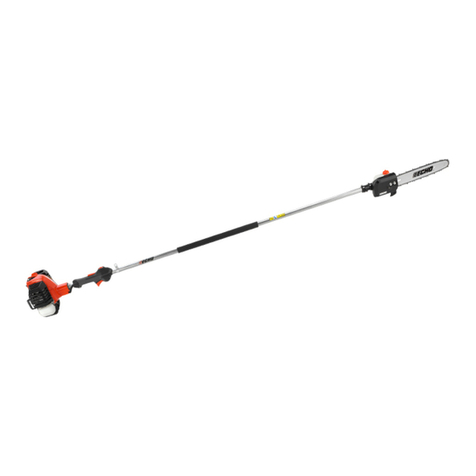
Echo
Echo Power Pruner PPF-2620 User manual
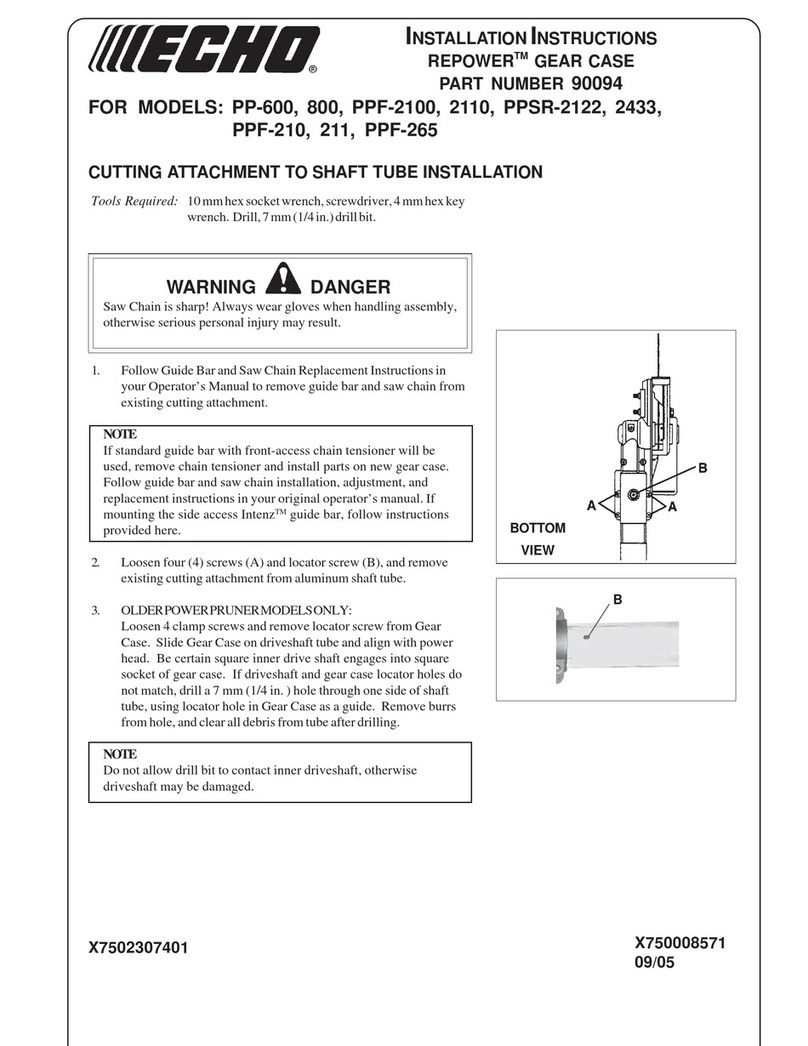
Echo
Echo REPOWER 90094 User manual
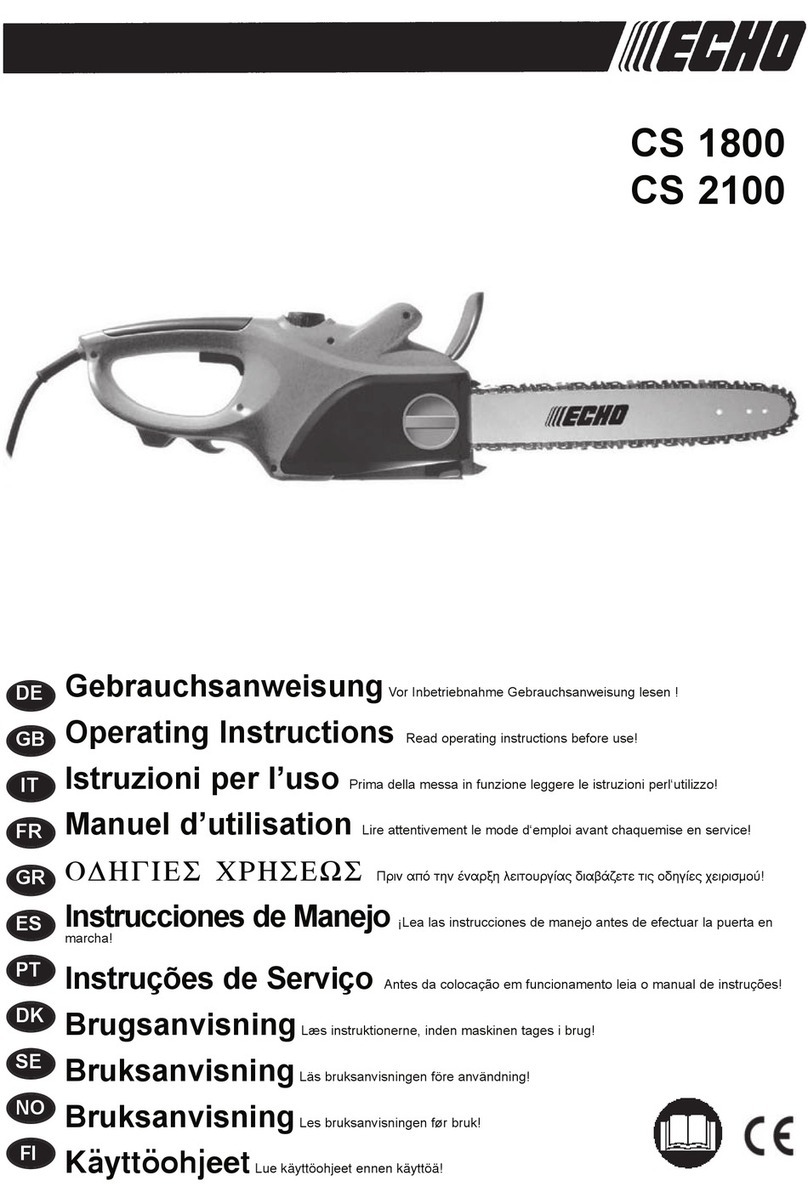
Echo
Echo CS 1800 User manual
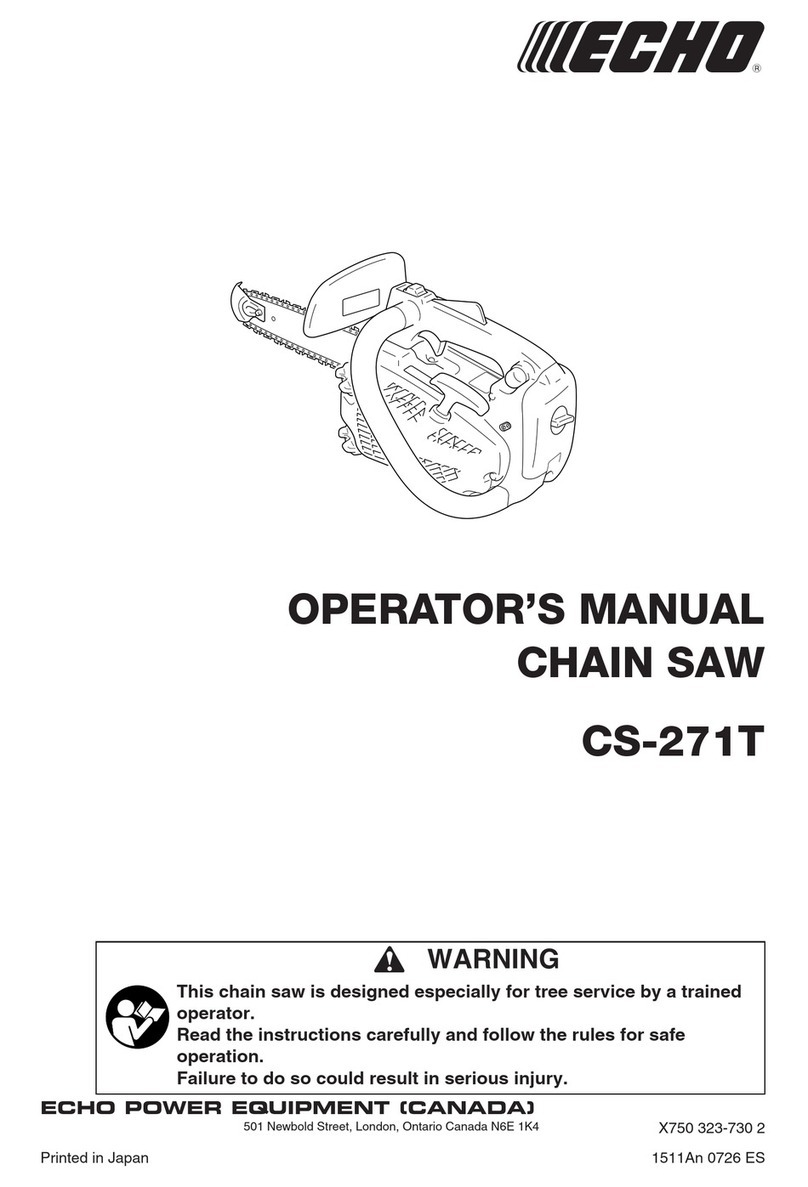
Echo
Echo CS-271T User manual
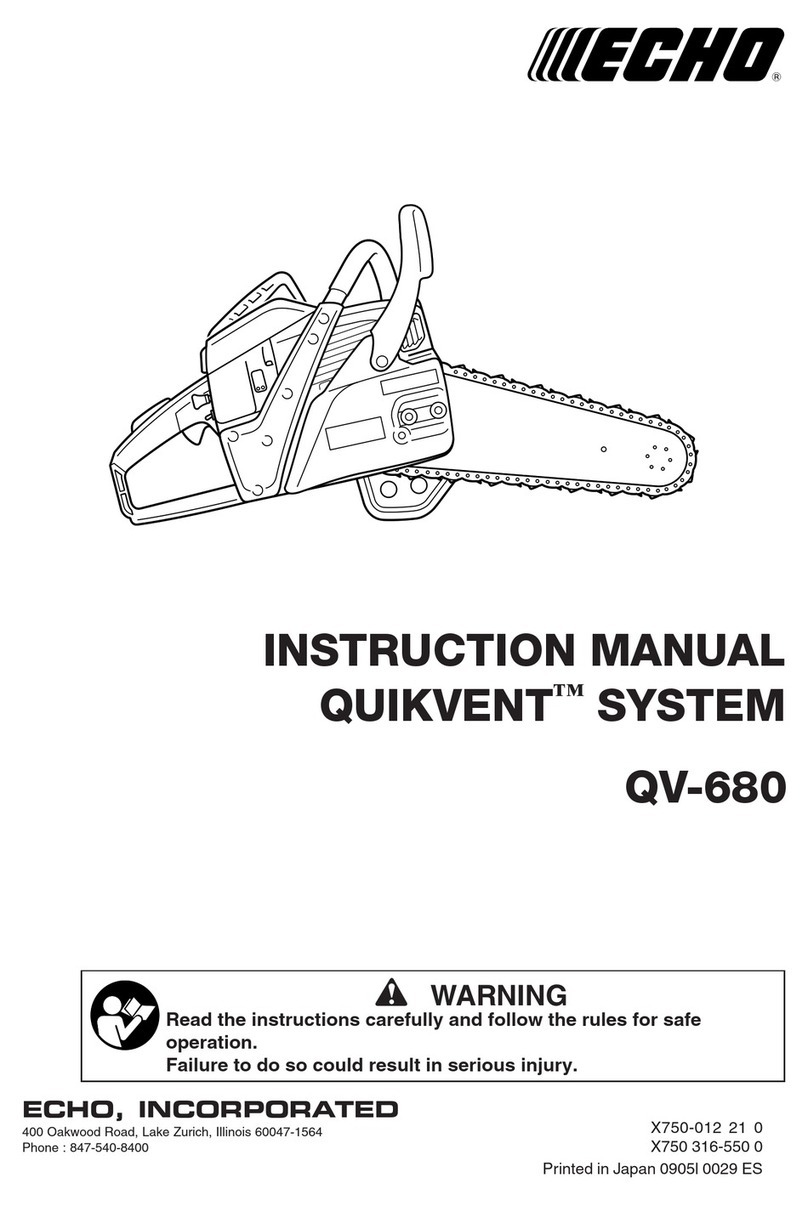
Echo
Echo QV-680 User manual
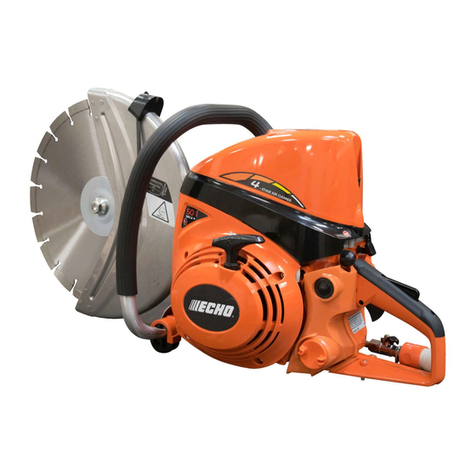
Echo
Echo CSG-7410 User manual
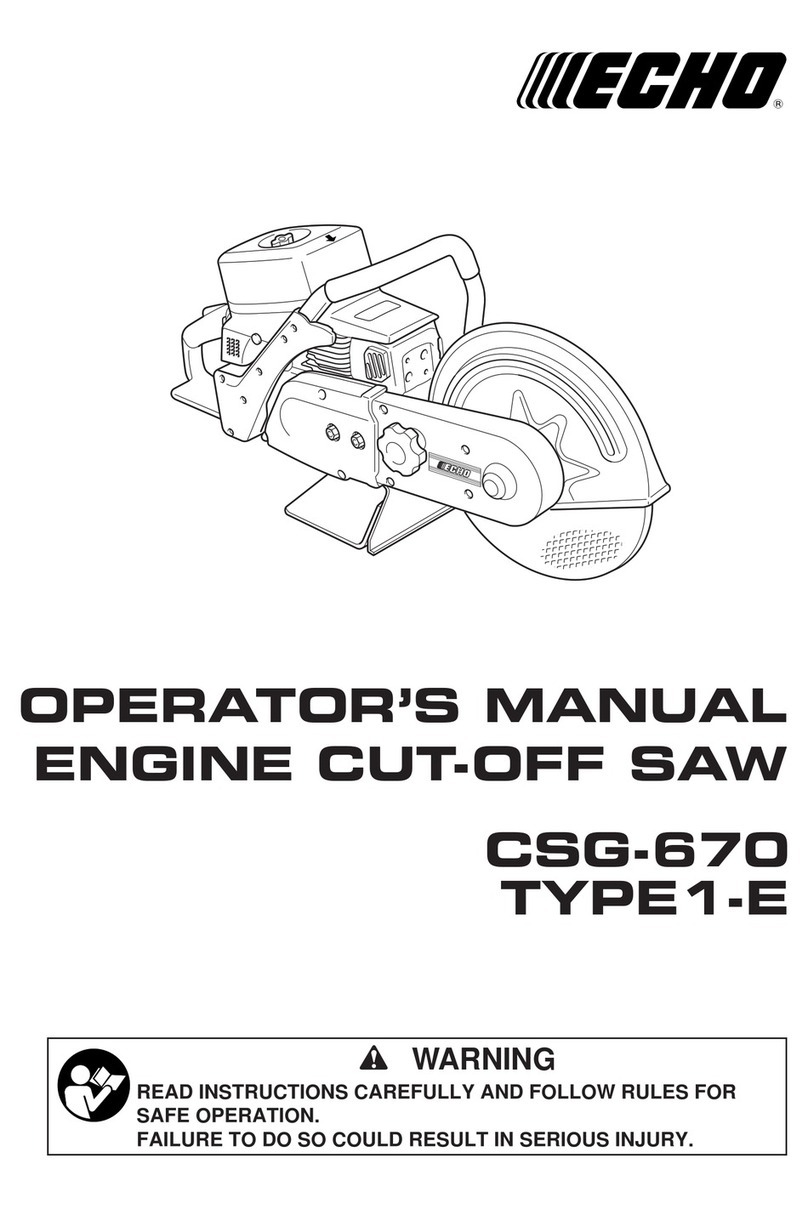
Echo
Echo Power Blend CSG-670 User manual