ECOFOREST ecoSMART Supervisor User guide

06 / 2020
SERVICE CONTACT:
MODEL:
ecoSMART Supervisor
USER, INSTALLER AND TECHNICAL SERVICE MANUAL
EN


ecoSMART Supervisor user, installer and technical service manual
3
EN
Contents
1. General information ................................................................................................................................................................5
1.1. Safety considerations..............................................................................................................................................................5
1.2. Recycling .................................................................................................................................................................................6
1.3. Maintenance ...........................................................................................................................................................................7
2. General description .................................................................................................................................................................7
3. Installation ..............................................................................................................................................................................7
3.1. Transport and handling...........................................................................................................................................................7
3.2. Dimensions .............................................................................................................................................................................7
3.3. Unpacking ...............................................................................................................................................................................8
3.4. Fitting and removing the cover ...............................................................................................................................................8
3.5. Location and assembly............................................................................................................................................................8
3.6. Service areas ...........................................................................................................................................................................9
4. Electrical system ......................................................................................................................................................................9
4.1. General instructions..............................................................................................................................................................10
4.2. Power supply.........................................................................................................................................................................16
4.3. Bus communication ..............................................................................................................................................................17
5. Controller user menu guide ...................................................................................................................................................17
5.1. Control panel ........................................................................................................................................................................18
5.2. Mainscreen ...........................................................................................................................................................................19
5.3. Active components ...............................................................................................................................................................19
5.4. Mode.....................................................................................................................................................................................20
5.5. Operation program ...............................................................................................................................................................21
5.6. Heatpump status...................................................................................................................................................................22
5.7. User menu.............................................................................................................................................................................23
5.8. Installer menu .......................................................................................................................................................................26
6. Configuration and commissioning..........................................................................................................................................29
6.1. Software version and "default values"..................................................................................................................................29
6.2. pLAN address configuration in heat pumps ..........................................................................................................................29
6.3. Control panel Address configuration ....................................................................................................................................30
6.4. pLAN communication cable connection ...............................................................................................................................31
6.5. Selecting the heat pump model ............................................................................................................................................31
6.6. Service configuration ............................................................................................................................................................31
6.7. Configuration of service response priorities .........................................................................................................................31
6.8. Configuration of the remote control.....................................................................................................................................31
6.9. Power limitation and protection configuration ....................................................................................................................32
6.10. Final inspection and commissioning .....................................................................................................................................32
7. Identifying and solving problems ........................................................................................................................................... 33
7.1. Alarm list ...............................................................................................................................................................................33
8. Technical specifications .........................................................................................................................................................33
8.1. Technical data table..............................................................................................................................................................33
8.2. Circuit diagram......................................................................................................................................................................34
8.3. Table of electrical connections .............................................................................................................................................35
9. Symbols .................................................................................................................................................................................37

ecoSMART Supervisor user, installer and technical service manual
4
EN
10. Warranty and technical service.............................................................................................................................................. 38
10.1. Manufacturer's warranty ......................................................................................................................................................38
10.2. Authorised distributors and technical service.......................................................................................................................38

ecoSMART Supervisor user, installer and technical service manual
5
EN
1. General information
Thank you for purchasing an ecoGEO HP heat pump cascade system.
This manual contains information about installing, commissioning and troubleshooting the device. There is also useful information
for the end user, such how to navigate and adjust parameters via the control panel.
To get the greatest benefit from your ecoGEO HP supervisor please read this manual carefully before installation and
commissioning of the equipment. Keep this manual handy for future reference.
This manual contains two different kinds of warnings that should be heeded.
NOTE
Indicates a situation that may cause material damage or equipment malfunction. This may also be
used to indicate practices that are recommended or not recommended for the equipment.
DANGER!
Warning of imminent or potential danger which, if not avoided, may result in injury or even death.
This may also be used to warn of unsafe practices.
This supervisor was designed to control a cascade of several ecoGEO HP heat pumps.
The manufacturer is not responsible for any material damage and/or personal injury resulting from improper use or incorrect
installation of the equipment.
The device must be installed by a licensed installer in accordance with applicable local regulations and in accordance with the
instructions described in the installation manual.
1.1. Safety considerations
The detailed instructions in this section cover important safety aspects and must therefore be strictly complied with.
DANGER!
All the installation and maintenance work described in this manual must be performed by an
authorised engineer.
Improper installation or use of the equipment could cause electrocution, short circuits, leakage of
working fluids, fire or other personal injuries and/or material damage.
If you are unsure of the procedures for installation, maintenance or use of the equipment, contact
your local dealer or technical support for advice.
If you detect a malfunction in the unit, contact your local dealer or technical support to answer any
questions.
This equipment should not be handled by people with physical, sensory or psychological
disabilities, children and people with no suitable experience or knowledge, unless it is under the
supervision or direction of a person responsible for their safety.

ecoSMART Supervisor user, installer and technical service manual
6
EN
When carrying out installation, maintenance or commissioning of the heat pump, always use
appropriate personal protective equipment.
Keep the plastic bags included in the packaging out of the reach of children, as improper use could
result in injury caused by asphyxia.
Hydraulic installation
Installation and subsequent interventions on the hydraulic circuits controlled by the supervisor must be performed only by an
authorised technician in accordance with applicable local regulations and the instructions provided in this manual.
DANGER!
Do not touch the pipes while the unit is in operation or immediately after, as this may result in
burns caused by cold or heat. If these components need to be touched, allow sufficient time for the
temperatures to stabilise and wear protective gloves to avoid injury.
Electrical system
Any intervention on the electrical system must only be performed by an authorised electrician in accordance with applicable local
regulations and the instructions provided in this manual.
DANGER!
The power supply to the unit must have an external switch that can shut off all the circuits.
Ecoforest recommends installing an automatic external switch for each of the electrical power
sources (power supply of the supervisor and power supply of devices controlled by its DO digital
outputs).
Please note that the unit may have more than one electrical power source.
Before performing any operation on the unit, disconnect the power supply.
During installation and maintenance of the unit, never leave the cover open unattended.
Do not touch any electrical component with wet hands, as this could cause an electric shock.
1.2. Recycling
The supervisor cannot be disposed of with household waste when its useful life ends. Carry out the elimination of the appliance in
accordance with the pertinent local regulations, in a correct and respectful way with the environment. Put the product at the end
of its useful life in the hands of the waste manager authorized by the local authorities for transport to an appropriate treatment
plant.

ecoSMART Supervisor user, installer and technical service manual
7
EN
1.3. Maintenance
The supervisor does not require any specific maintenance after commissioning. The internal controller constantly monitors a large
variety of parameters and will alert you if any problem or incident occurs, in which case we recommend that you contact your
dealer.
DANGER!
All maintenance work must be performed by an authorised technician. Improper handling of the
equipment as a whole can result in personal injury and/or damage to materials.
Do not spill water or other liquids directly on the casing or inside it, as this could cause an electric
shock or fire.
2. General description
The ecoSMART Supervisor is an electronic device designed to manage a cascade of ecoGEOHP heat pumps. It can work with a
minimum of 2 heat pumps and a maximum of 6. To do this you must establish pLAN bus communication with all heat pumps.
3. Installation
3.1. Transport and handling
Transport the supervisor so that it is protected from bad weather.
3.2. Dimensions
The general dimensions of the unit are set out below.
Figure 3.1. General dimensions (in mm).
400
600
260
510
130
Ø9
158
400
600
260
510
130
Ø9
158
400
600
260
510
130
Ø9
158

ecoSMART Supervisor user, installer and technical service manual
8
EN
3.3. Unpacking
To unpack the supervisor, carefully remove the box and check that the unit has not been damaged during transportation.
3.4. Fitting and removing the cover
A 4 mm Allen wrench is required to assemble and disassemble the cover. Remove the front cover by loosening the four screws and
pulling it.
Figure 3.2. Removing the front cover of the supervisor.
3.5. Location and assembly
Choose a dry place where there is no risk of frost. The supervisor must be installed on a stable wall that can support the full weight
of the unit. Use a spirit level to ensure that it is completely horizontal.
Figure 3.3. Positioning the supervisor.

ecoSMART Supervisor user, installer and technical service manual
9
EN
NOTE
When removing the cover, take care to remove the control panel cable without damaging it.
3.6. Service areas
The minimum recommended distances around the supervisor to facilitate installation, commissioning and maintenance are set out
below.
Figure 3.4. Recommended minimum service areas around the supervisor (in mm).
4. Electrical system
DANGER!
The power supply to the unit must have an external switch that can shut off all the circuits.
Ecoforest recommends installing an automatic external switch for each of the electrical power
sources (power supply of the supervisor and power supply of devices controlled by its DO digital
outputs).
Please note that the unit may have more than one electrical power source.
Before performing any operation on the unit, disconnect the power supply.
During installation and maintenance of the unit, never leave the cover open unattended.
Do not touch any electrical component with wet hands, as this could cause an electric shock.
100
100
600
100
100

ecoSMART Supervisor user, installer and technical service manual
10
EN
4.1. General instructions
The locations of the main electrical panel components are shown below.
Figure 4.1. Location of internal components.
In addition to the power supply, various temperature probes (analogue inputs AIxx), open/closed contact control signals from
thermostats or other external equipment (digital inputs DIxx), switching on/off of pumps, valves and/or fans (digital outputs DOxx)
or regulation of pumps, valves and/or fans (analogue outputs AOxx) should be connected.
Figures 4.2 and 4.3 show installation examples to indicate the electrical connections of the components.
AOxx
Analogue outputs
Communication ports
FBus, BMS and pLAN
Transformer fuse
230Vac 0.5A
Main switch
24Vac transformer
Digital outputs
DOxx
Control fuse
24Vac 2.5A
DIxx
Digital inputs
Controller pCO OEM+
Main supply 1/N/PE
230Vac
50-60 Hz
DI7 DI8
DI5
DI4
DI3
DI2
DI1
AI12
AI11AI10AI9 DI6AO5AO4AO3AO2AO1AI8
AI7
AI6
AI5
AI4AI2
AI1 AI3
Sgn
Com
Sgn
24Vac
Sgn
24Vac
Sgn
24Vac
Sgn
24Vac
Vout
24Vac
GND
PE
GND
Tx/Rx+
Tx/Rx-
Sgn
Com
Sgn
Com
Sgn
Com
Vout
24Vac
GND
Vout
24Vac
GND
Vout
24Vac
GND
Vout
24Vac
GND
Sgn
Sgn
Sgn
Sgn
Sgn
Sgn
Sgn
GND
GND
GND
GND
GND
GND
GND
Sgn
GND
Sgn
GND
Sgn
GND
Sgn
GND
Sgn
GND
PE
GND
Tx/Rx+
Tx/Rx-
PE
GND
Tx/Rx-
Tx/Rx+
pLAN BMS2 FBus
Fuse 2A
24 Vac
Control Power
Supply 230V DO1 DO2 DO3 DO4 DO5 DO6 DO7 DO8 DO9 DO10 DO11 DO12 DO13
L1 L2/N PE
Fuse 0.5A
NC
COM
NO
NC
COM
NO
NC
COM
NO
NC
COM
NO
NC
COM
NO
NC
COM
NO
NC
COM
NO
NC
COM
NO
NC
COM
NO
NC
COM
NO
NC
COM
NO
NC
COM
NO
NC
COM
NO
AIxx
Analogue inputs
Distributor 24Vac

ecoSMART Supervisor user, installer and technical service manual
11
EN
Figure 4.2. General electrical connection scheme 1. Installation for heating and cooling production with ecoGEO HP3.
T
T
DO17
[1/2/3]
AI11
[1/2/3]AI18
[1/2/3]
DO4
[1/2/3]
DO7[S]
DO7[S]
T
TAI5[S]
DO5[S]
P
DI3
[1/2/3]
TAI12
[1/2/3]
DI1
DI2
EVU
DO2[3]
DO1[3]
DO8[S]
DI1
DI2
EVU
DO2[2]
DO1[2]
DI1
DI2
EVU
DO2[1]
DO1[1]
3
2
1
TT
AI2[S]AI1[S]TT
AI4[S]AI3[S]
AO3[S]
DO6[S]
DO1[S]
AO1[S]
DO2[S]
AO2[S]
DO5[S]
M
T
T
T
T
T
T
T
T
T
DG1SG3SG4SG2
T
TT
M
M
M
T
T
FBus2
SG5
T
M
T
DO5
[1/2/3]
AI17
[1/2/3]DO18
[1/2/3]
DI4
[1/2/3]
AI19
[1/2/3]
DO6
[1/2/3]
DO7
[1/2/3]
DO8
[1/2/3]
DO9
[1/2/3]
DO9
[1/2/3]
AO3
[1/2/3]
AO4
[1/2/3]
AO5
[1/2/3]
AO6
[1/2/3]
AI13
[1/2/3]
AI14
[1/2/3]
AI15
[1/2/3]
AI16
[1/2/3]
DI5
[1/2/3]
DI6
[1/2/3]
DI7
[1/2/3]
DI8
[1/2/3]
DI9
[1/2/3]
DI10
[1/2/3]
DI11
[1/2/3]
DI12
[1/2/3]
DI13
[1/2/3]
DI14
[1/2/3]
DO16
[1/2/3]

ecoSMART Supervisor user, installer and technical service manual
12
EN
Figure 4.3.General electrical connection scheme 2.Installation for simultaneous production of heating and cooling with ecoGEO HP1
DI3
[1/2/3]
DI1
DI2
EVU
T
T
T
T
TAI5[S]
DO3[S]
P
DO1[S]
T
T
T
T
T
T
T
T
DG1 SG3 SG4SG2
TT T
M
M
M
T
T
FBus2
SG5
T
M
DO4[S]
M
M
T
T
DO5[S]
DO2[S]
AO2
[S]
AO1[S] DO8[S]
DI1
DI2
EVU
DI1
DI2
EVU
AI18[1/2/3]
AI11
[1/2/3]
DO17
[1/2/3]
DO4
[1/2/3]
AI12
[1/2/3] DO5
[1/2/3]
AI17
[1/2/3] DO18
[1/2/3]
DI4
[1/2/3]
AI19
[1/2/3]
DO6
[1/2/3]
DO7
[1/2/3]
DO8
[1/2/3]
DO9
[1/2/3]
DO9
[1/2/3]
AO3
[1/2/3]
AO4
[1/2/3]
AO5
[1/2/3]
AO6
[1/2/3]
AI13
[1/2/3]
AI14
[1/2/3]
AI15
[1/2/3]
AI16
[1/2/3]
DI5
[1/2/3]
DI6
[1/2/3]
DI7
[1/2/3]
DI8
[1/2/3]
DI9
[1/2/3]
DI10
[1/2/3]
DI11
[1/2/3]
DI12
[1/2/3]
DI13
[1/2/3]
DI14
[1/2/3]
DO16
[1/2/3]
TT
AI2[S] AI1[S] TT
AI4[S] AI3[S]
DO2[3]
DO1[3]
DO2[2]
DO1[2]
DO2[1]
DO[1]
3
2
1
AO3[S]
DO6[S]
M

ecoSMART Supervisor user, installer and technical service manual
13
EN
NOTE
The schemes in figures 4.2 and 4.3 are provided only to indicate the electrical connections. The
hydraulic design should be carried out by a specialist. Its use in full or in part, as well as any
reproduction or transfer to third parties, is the responsibility of the installation company.
Analogue inputs (AIxx)
These terminals are used to connect external temperature probes. Only passive NTC temperature probes can be connected, so
cable connection polarity is not important.
If necessary, use extension cables with a maximum length of 50 m and a minimum diameter of 0.75 mm2. For greater lengths (up to
120 m) it is recommended to use cable with a section of 1.5 mm2.
NOTE
Use original temperature probes only; other types of components could cause poor heat pump
operation and/or cause heat pump component breakdowns.
Figure 4.4. Example of temperature probe connections.
Description
Signal
Type
Connector
Brine outlet temperature probe
Analogue input
NTC 10K 25 °C Probe
AI1
Brine inlet temperature probe
Analogue input
NTC 10K 25 °C Probe
AI2
Production outlet temperature probe
Analogue input
NTC 10K 25 °C Probe
AI3
Production inlet temperature probe
Analogue input
NTC 10K 25 °C Probe
AI4
Outside temperature probe
Analogue input
NTC 10K 25 °C Probe
AI5
Free
Analogue input
NTC 10K 25 °C Probe
AI6
Free
Analogue input
NTC 10K 25 °C Probe
AI7
Free
Analogue input
NTC 10K 25 °C Probe
AI8
Free
Analogue input
NTC 10K 25 °C Probe
AI9
Free
Analogue input
NTC 10K 25 °C Probe
AI10
Free
Analogue input
NTC 10K 25 °C Probe
AI11
Free
Analogue input
NTC 10K 25 °C Probe
AI12
Table 4.1. List of the connection terminals of the external temperature probes.
Digital control inputs (DIxx)
Digital signals (open/closed contact) from thermostats or other external equipment can be connected to these terminals to control
the sources.
Com
Sgn
AIxx
NTC
DI7 DI8
DI5
DI4
DI3
DI2
DI1
AI12
AI11AI10AI9 DI6AO5AO4AO3AO2AO1AI8
AI7
AI6
AI5
AI4AI2
AI1 AI3
Sgn
Com
Sgn
24Vac
Sgn
24Vac
Sgn
24Vac
Sgn
24Vac
Vout
24Vac
GND
PE
GND
Tx/Rx+
Tx/Rx-
Sgn
Com
Sgn
Com
Sgn
Com
Vout
24Vac
GND
Vout
24Vac
GND
Vout
24Vac
GND
Vout
24Vac
GND
Sgn
Sgn
Sgn
Sgn
Sgn
Sgn
Sgn
GND
GND
GND
GND
GND
GND
GND
Sgn
GND
Sgn
GND
Sgn
GND
Sgn
GND
Sgn
GND
PE
GND
Tx/Rx+
Tx/Rx-
PE
GND
Tx/Rx-
Tx/Rx+
pLAN BMS2 FBus
Fuse2A
24 Vac
ControlPower
Supply230V DO1 DO2 DO3 DO4 DO5 DO6 DO7 DO8 DO9 DO10 DO11 DO12 DO13
L1 L2/N PE
Fuse0.5A
NC
COM
NO
NC
COM
NO
NC
COM
NO
NC
COM
NO
NC
COM
NO
NC
COM
NO
NC
COM
NO
NC
COM
NO
NC
COM
NO
NC
COM
NO
NC
COM
NO
NC
COM
NO
NC
COM
NO

ecoSMART Supervisor user, installer and technical service manual
14
EN
NOTE
Take special care with the working voltage of each digital input; improper handling could cause poor
heat pump operation and/or heat pump component breakdowns. Some digital inputs require
voltage-free signals, while others require 24Vac signals. 24Vac signals are sent from their own
terminal block strip.
Do not mix voltage-free and 24Vac signals.
Figure 4.5. Example of voltage-free digital input connections.
NOTE
24Vac external equipment can be connected directly from the supervisor, and connected equipment
as a whole must not exceed 36VA or 1.5A. Failure to comply with these ranges could cause poor
heat pump operation and/or heat pump component breakdowns.
Figure 4.6. Example of digital input connection with 24Vac voltage.
Description
Signal
Type
Connector
Remote heat pump activation EVU
Digital input
Voltage-free (0V)
DI1
Remote winter/summer program selection
Digital input
Voltage-free (0V)
DI2
Free
Digital input
Voltage-free (0V)
DI3
Free
Digital input
Voltage-free (0V)
DI4
Free
Digital input
24Vdc / 24Vac
DI5
Free
Digital input
24Vdc / 24Vac
DI6
Free
Digital input
24Vdc / 24Vac
DI7
Free
Digital input
24Vdc / 24Vac
DI8
Table 4.2. List of the connection terminals of the external control signals
24Vac
Sgn
DIxx
DI7 DI8
DI5
DI4
DI3
DI2
DI1
AI12
AI11AI10AI9 DI6AO5AO4AO3AO2AO1AI8
AI7
AI6
AI5
AI4AI2
AI1 AI3
Sgn
Com
Sgn
24Vac
Sgn
24Vac
Sgn
24Vac
Sgn
24Vac
Vout
24Vac
GND
PE
GND
Tx/Rx+
Tx/Rx-
Sgn
Com
Sgn
Com
Sgn
Com
Vout
24Vac
GND
Vout
24Vac
GND
Vout
24Vac
GND
Vout
24Vac
GND
Sgn
Sgn
Sgn
Sgn
Sgn
Sgn
Sgn
GND
GND
GND
GND
GND
GND
GND
Sgn
GND
Sgn
GND
Sgn
GND
Sgn
GND
Sgn
GND
PE
GND
Tx/Rx+
Tx/Rx-
PE
GND
Tx/Rx-
Tx/Rx+
pLAN BMS2 FBus
Fuse2A
24 Vac
ControlPower
Supply230V DO1 DO2 DO3 DO4 DO5 DO6 DO7 DO8 DO9 DO10 DO11 DO12 DO13
L1 L2/N PE
Fuse0.5A
NC
COM
NO
NC
COM
NO
NC
COM
NO
NC
COM
NO
NC
COM
NO
NC
COM
NO
NC
COM
NO
NC
COM
NO
NC
COM
NO
NC
COM
NO
NC
COM
NO
NC
COM
NO
NC
COM
NO
Com
Sgn
DIxx
DI7 DI8
DI5
DI4
DI3
DI2
DI1
AI12
AI11AI10AI9 DI6AO5AO4AO3AO2AO1AI8
AI7
AI6
AI5
AI4AI2
AI1 AI3
Sgn
Com
Sgn
24Vac
Sgn
24Vac
Sgn
24Vac
Sgn
24Vac
Vout
24Vac
GND
PE
GND
Tx/Rx+
Tx/Rx-
Sgn
Com
Sgn
Com
Sgn
Com
Vout
24Vac
GND
Vout
24Vac
GND
Vout
24Vac
GND
Vout
24Vac
GND
Sgn
Sgn
Sgn
Sgn
Sgn
Sgn
Sgn
GND
GND
GND
GND
GND
GND
GND
Sgn
GND
Sgn
GND
Sgn
GND
Sgn
GND
Sgn
GND
PE
GND
Tx/Rx+
Tx/Rx-
PE
GND
Tx/Rx-
Tx/Rx+
pLAN BMS2 FBus
Fuse2A
24 Vac
ControlPower
Supply230V DO1 DO2 DO3 DO4 DO5 DO6 DO7 DO8 DO9 DO10 DO11 DO12 DO13
L1 L2/N PE
Fuse0.5A
NC
COM
NO
NC
COM
NO
NC
COM
NO
NC
COM
NO
NC
COM
NO
NC
COM
NO
NC
COM
NO
NC
COM
NO
NC
COM
NO
NC
COM
NO
NC
COM
NO
NC
COM
NO
NC
COM
NO

ecoSMART Supervisor user, installer and technical service manual
15
EN
Analogue outputs (AOxx)
These terminals send analogue 0-10Vdc regulation signals to modulate the control of pumps and/or fans. Moreover, these
connectors have a 24Vac power supply terminal for modulating equipment that requires a 24Vac power supply.
Figure 4.7. Example of 0-10Vdc modulating regulation signal connections.
Description
Signal
Type
Connector
Brine pump adjustment /
Cooling cogeneration valve adjustment
Analogue output
Valve regulation 0 –10Vdc
AO1
Production pump regulation /
Heating cogeneration valve adjustment
Analogue output
Valve regulation 0 –10Vdc
AO2
Auxiliary heating system regulation
Analogue output
Valve regulation 0 –10Vdc
AO3
Free
Analogue output
Valve regulation 0 –10Vdc
AO4
Free
Analogue output
Valve regulation 0 –10Vdc
AO5
Table 4.3. List of the connection terminals of the regulation signals for external equipment.
Digital outputs to relay (DOxx)
The relay terminal block provides digital outputs to control external equipment, such as circulator pumps, fans or open/closed
valves. Each relay should be powered externally with the operating voltage of the component to be controlled. Power is supplied to
each relay separately, so different operating voltages can be used in each. The following figure shows an example of an installation
of a relay power supply.
DI7 DI8
DI5
DI4
DI3
DI2
DI1
AI12
AI11AI10AI9 DI6AO5AO4AO3AO2AO1AI8
AI7
AI6
AI5
AI4AI2
AI1 AI3
Sgn
Com
Sgn
24Vac
Sgn
24Vac
Sgn
24Vac
Sgn
24Vac
Vout
24Vac
GND
PE
GND
Tx/Rx+
Tx/Rx-
Sgn
Com
Sgn
Com
Sgn
Com
Vout
24Vac
GND
Vout
24Vac
GND
Vout
24Vac
GND
Vout
24Vac
GND
Sgn
Sgn
Sgn
Sgn
Sgn
Sgn
Sgn
GND
GND
GND
GND
GND
GND
GND
Sgn
GND
Sgn
GND
Sgn
GND
Sgn
GND
Sgn
GND
PE
GND
Tx/Rx+
Tx/Rx-
PE
GND
Tx/Rx-
Tx/Rx+
pLAN BMS2 FBus
Fuse2A
24 Vac
ControlPower
Supply230V DO1 DO2 DO3 DO4 DO5 DO6 DO7 DO8 DO9 DO10 DO11 DO12 DO13
L1 L2/N PE
Fuse0.5A
NC
COM
NO
NC
COM
NO
NC
COM
NO
NC
COM
NO
NC
COM
NO
NC
COM
NO
NC
COM
NO
NC
COM
NO
NC
COM
NO
NC
COM
NO
NC
COM
NO
NC
COM
NO
NC
COM
NO
L
NC: 22/12
DOxx
COM: 21/11
NO: 24/14
A2/A1
NC
COM
NO
GND
24Vac
Vout
AOxx
M
DI7 DI8
DI5
DI4
DI3
DI2
DI1
AI12
AI11AI10AI9 DI6AO5AO4AO3AO2AO1AI8
AI7
AI6
AI5
AI4AI2
AI1 AI3
Sgn
Com
Sgn
24Vac
Sgn
24Vac
Sgn
24Vac
Sgn
24Vac
Vout
24Vac
GND
PE
GND
Tx/Rx+
Tx/Rx-
Sgn
Com
Sgn
Com
Sgn
Com
Vout
24Vac
GND
Vout
24Vac
GND
Vout
24Vac
GND
Vout
24Vac
GND
Sgn
Sgn
Sgn
Sgn
Sgn
Sgn
Sgn
GND
GND
GND
GND
GND
GND
GND
Sgn
GND
Sgn
GND
Sgn
GND
Sgn
GND
Sgn
GND
PE
GND
Tx/Rx+
Tx/Rx-
PE
GND
Tx/Rx-
Tx/Rx+
pLAN BMS2 FBus
Fuse2A
24 Vac
ControlPower
Supply230V DO1 DO2 DO3 DO4 DO5 DO6 DO7 DO8 DO9 DO10 DO11 DO12 DO13
L1 L2/N PE
Fuse0.5A
NC
COM
NO
NC
COM
NO
NC
COM
NO
NC
COM
NO
NC
COM
NO
NC
COM
NO
NC
COM
NO
NC
COM
NO
NC
COM
NO
NC
COM
NO
NC
COM
NO
NC
COM
NO
NC
COM
NO

ecoSMART Supervisor user, installer and technical service manual
16
EN
Figure 4.8. Example of digital output relay power supply connections.
Each relay allows independent pole switching; it can thus control the switching on/off of the units, including those powered with a
different voltage. The capacity of the relays is 8A/250Vac per pole. If the equipment to be controlled exceeds this capacity, an
external relay or contactor must be installed. Shown below are examples of connections between circulator pumps and 3-way
valves with controls at 2 or 3 points.
NOTE
Pay special attention to the maximum consumption allowed by each relay. Use an intermediate
relay or a contactor for the connection, if necessary.
Figure 4.9. Example of digital output connections.
Description
Signal
Type
Connector
Brine pump activation
Digital output
Activation 230Vac / 8A maximum
DO1
Production pump / buffer pump activation
Digital output
Activation 230Vac / 8A maximum
DO2
Auxiliary brine pump activation
Digital output
Activation 230Vac / 8A maximum
DO3
Auxiliary pump cool tank activation
Digital output
Activation 230Vac / 8A maximum
DO4
Free cooling production activation
Digital output
Activation 230Vac / 8A maximum
DO5
Auxiliary heating system activation
Digital output
Activation 230Vac / 8A maximum
DO6
Active cooling production activation
Digital output
Activation 230Vac / 8A maximum
DO7
DHW production activation
Digital output
Activation 230Vac / 8A maximum
DO8
Free
Digital output
Activation 230Vac / 8A maximum
DO9
Free
Digital output
Activation 230Vac / 8A maximum
DO10
Table 4.4. List of the connections of external equipment to the upper terminal blocks of relays.
4.2. Power supply
The supervisor only requires one electrical connection. The power supply to the 24Vac transformer connects to it to power the
controller and other devices with low power consumption. The following table shows the characteristics of the necessary electrical
connection:
Type of power supply
Type of protection/ Cut-off current
Recommended cable section
1/N/PE 230 V / 50-60 Hz
Magnetic, thermal and differential / 1A
1.5 mm2
DI7 DI8
DI5
DI4
DI3
DI2
DI1
AI12
AI11AI10AI9 DI6AO5AO4AO3AO2AO1AI8
AI7
AI6
AI5
AI4AI2
AI1 AI3
Sgn
Com
Sgn
24Vac
Sgn
24Vac
Sgn
24Vac
Sgn
24Vac
Vout
24Vac
GND
PE
GND
Tx/Rx+
Tx/Rx-
Sgn
Com
Sgn
Com
Sgn
Com
Vout
24Vac
GND
Vout
24Vac
GND
Vout
24Vac
GND
Vout
24Vac
GND
Sgn
Sgn
Sgn
Sgn
Sgn
Sgn
Sgn
GND
GND
GND
GND
GND
GND
GND
Sgn
GND
Sgn
GND
Sgn
GND
Sgn
GND
Sgn
GND
PE
GND
Tx/Rx+
Tx/Rx-
PE
GND
Tx/Rx-
Tx/Rx+
pLAN BMS2 FBus
Fuse2A
24 Vac
ControlPower
Supply230V DO1 DO2 DO3 DO4 DO5 DO6 DO7 DO8 DO9 DO10 DO11 DO12 DO13
L1 L2/N PE
Fuse0.5A
NC
COM
NO
NC
COM
NO
NC
COM
NO
NC
COM
NO
NC
COM
NO
NC
COM
NO
NC
COM
NO
NC
COM
NO
NC
COM
NO
NC
COM
NO
NC
COM
NO
NC
COM
NO
NC
COM
NO
LoffLon
L
NC: 22/12
COM: 21/11
NO: 24/14
A2/A1
DOxx
NC
COM
NO
NC: 22/12
COM: 21/11
NO: 24/14
A2/A1
DOxx
NC
COM
NO
2P 3P

ecoSMART Supervisor user, installer and technical service manual
17
EN
Table 4.5. Characteristics of the supervisor power supply.
Figure 4.10. Connection scheme of the supervisor power supply.
NOTE
The power supply of elements controlled by DO digital outputs must be independent.
4.3. Bus communication
For the supervisor to run properly, it is essential to keep pLAN bus communication with the cascade of heat pumps. Install a
shielded three-pole cable type AWG 20-22 between the pLAN terminals of the supervisor and the heat pumps.
PE
GND
R/T+
R/T-
pLAN
ecoGEO HP
PE
GND
R/T+
R/T-
pLAN
ecoGEO HP
PE
GND
R/T+
R/T-
pLAN
ecoGEO HP
PE
GND
R/T+
R/T-
pLAN
Supervisor
Figure 4.11.Example pLAN bus communication cable connection for installations with cascade of heat pumps.
Some other Ecoforest devices also communicate with each other via their pLAN ports. In any case, all Ecoforest controllers that
connect via pLAN will establish a single pLAN network.
5. Controller user menu guide
NOTE
The information included below corresponds to application versions launched after October 2019.
Other versions, both earlier and later, may differ slightly from the contents found in this section.
Depending on the settings configured by the technical service, there might be screens or screen
contents that are not shown.
If the following screen appears when accessing a menu, this means that the
service requested has not been enabled by the technical service.
DI7 DI8
DI5
DI4
DI3
DI2
DI1
AI12
AI11AI10AI9 DI6AO5AO4AO3AO2AO1AI8
AI7
AI6
AI5
AI4AI2
AI1 AI3
Sgn
Com
Sgn
24Vac
Sgn
24Vac
Sgn
24Vac
Sgn
24Vac
Vout
24Vac
GND
PE
GND
Tx/Rx+
Tx/Rx-
Sgn
Com
Sgn
Com
Sgn
Com
Vout
24Vac
GND
Vout
24Vac
GND
Vout
24Vac
GND
Vout
24Vac
GND
Sgn
Sgn
Sgn
Sgn
Sgn
Sgn
Sgn
GND
GND
GND
GND
GND
GND
GND
Sgn
GND
Sgn
GND
Sgn
GND
Sgn
GND
Sgn
GND
PE
GND
Tx/Rx+
Tx/Rx-
PE
GND
Tx/Rx-
Tx/Rx+
pLAN BMS2 FBus
Fuse2A
24 Vac
ControlPower
Supply230V DO1 DO2 DO3 DO4 DO5 DO6 DO7 DO8 DO9 DO10 DO11 DO12 DO13
L1 L2/N PE
Fuse0.5A
NC
COM
NO
NC
COM
NO
NC
COM
NO
NC
COM
NO
NC
COM
NO
NC
COM
NO
NC
COM
NO
NC
COM
NO
NC
COM
NO
NC
COM
NO
NC
COM
NO
NC
COM
NO
NC
COM
NO
Control Supply
230 Vac
L1
L2/N
Control Supply
230 Vac
L1
L2/N
5h

ecoSMART Supervisor user, installer and technical service manual
18
EN
5.1. Control panel
The supervisor panel has a screen with 6 buttons, like the one shown in the illustration below. The buttons are used to move
through the various user menus and to adjust the parameters.
Figure 5.1. Control panel.
The general functions and operation of each of the buttons are indicated below.
The ALARMS menu can be accessed directly from anywhere in the application.
The list of user menus can be accessed from anywhere in the application.
The user can return to the previous menu from anywhere in the application.
This allows the user to move through the menu lists.
This allows the user to move from one screen to another inside a menu.
This is used to adjust the settings of the parameters contained in a screen.
This allows the user to access the selected menu.
This is used to move from one adjustable parameter to another in the same screen.
This is used to access the INFORMATION menu directly from the main screen.

ecoSMART Supervisor user, installer and technical service manual
19
EN
5.2. Mainscreen
The main screen of the application contains a series of fields with information about heat pump operation.
Figure 5.2. Description of the main screen.
5.3. Active components
This field shows the main components of the heat pump that are activated. A consumption bar is also shown for the compressor
and modulating circulator pumps.
Brinepumpactivated
Compressor in start-up phase
Compressoractivated
Compressor in shut-downphase
Productionpumpactivated
Heatingunitsactivated
Coolingunitsactivated
Auxiliaryheatingunitactivated
Operation mode
Status
Active components
Operation program
Date and time

ecoSMART Supervisor user, installer and technical service manual
20
EN
5.4. Mode
This field shows the icons that indicate the operating modes that are active. Several operating modes can be viewed
simultaneously, depending on the heat pump model and the configuration set up by the technical service.
DIRECT HEATING Mode / DIRECT COOLING Mode
The heat pump sends hot / cold water directly to the heating / cooling system and adjusts the power supply to
the consumption of the home. The outlet temperature and flow are constantly controlled to optimise installation
performance.
These modes are activated when the heat pump receives a heating / cooling request from the interior terminals
installed in the home (thermostats, th-Tune terminals, thT terminals or TH sensors).
BUFFER HEATING Mode / BUFFER COOLING Mode
The heat pump sends hot / cold water to the buffer storage tank of the heating / cooling system. The power
supply, flow and outlet temperature are constantly controlled to maintain storage tank temperature and
optimise installation performance.
These modes are activated when the buffer storage tank temperature is lower / higher than the differential of
start-up temperatures.
DHW mode
The heat pump sends hot water to increase the temperature of the storage tank so it reaches the DHW setpoint
temperature as soon as possible.
This mode is activated when the DHW storage tank temperature is lower than the differential of start-up
temperatures.
POOL mode
The heat pump sends hot water to the pool production exchanger and adjusts the power supply. The outlet
temperature and flow are constantly controlled to optimise installation performance.
This mode is activated when the heat pump receives a demand for pool production.
LEGIONELLA PROTECTION Mode
The heat pump raises the temperature of the storage tank to the final temperature set by the technical service
for the legionella protection program. Heating is produced initially by the compressor, followed by activation of
the auxiliary DHW system, if there is one, until the final temperature is reached.
This mode is activated in compliance with the provisions in the weekly legionella protection program.
NOTE
Activation of the various OPERATING MODES may be affected by the time schedule functions or heat
pump service priorities (DHW, HEATING, COOLING, POOL).
The activation of the HEATING and COOLING operating modes may be affected by service shut-down
temperatures.
Table of contents
Other ECOFOREST Control System manuals
Popular Control System manuals by other brands

ACU-RITE
ACU-RITE MILLPWR G2 user manual
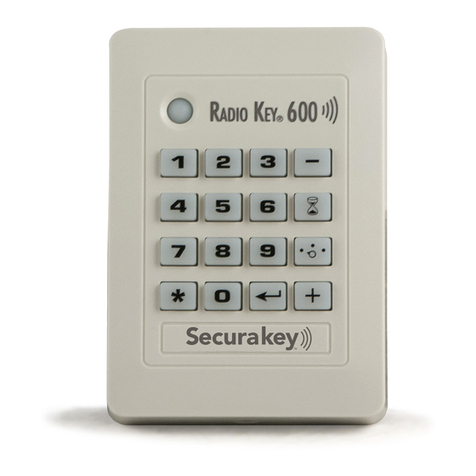
Securakey
Securakey RADIO KEY 600 Operating & installation guide
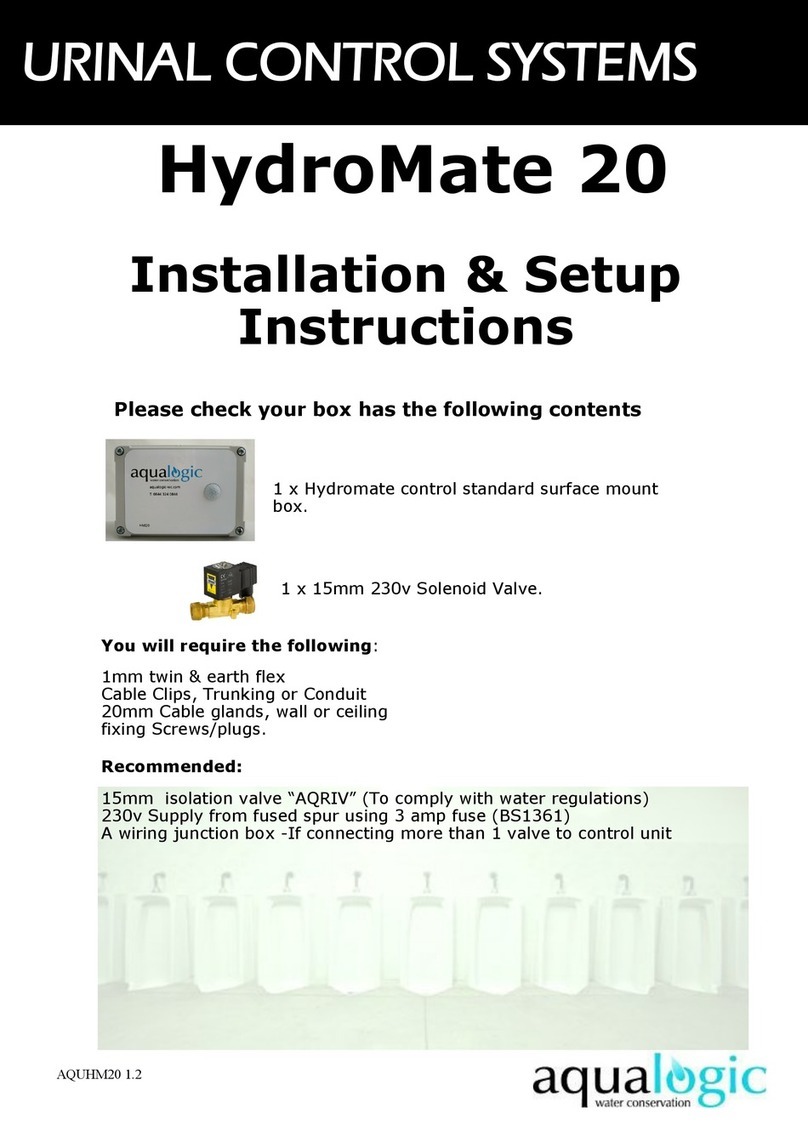
Aqua Logic
Aqua Logic HydroMate 20 Installation & setup instructions
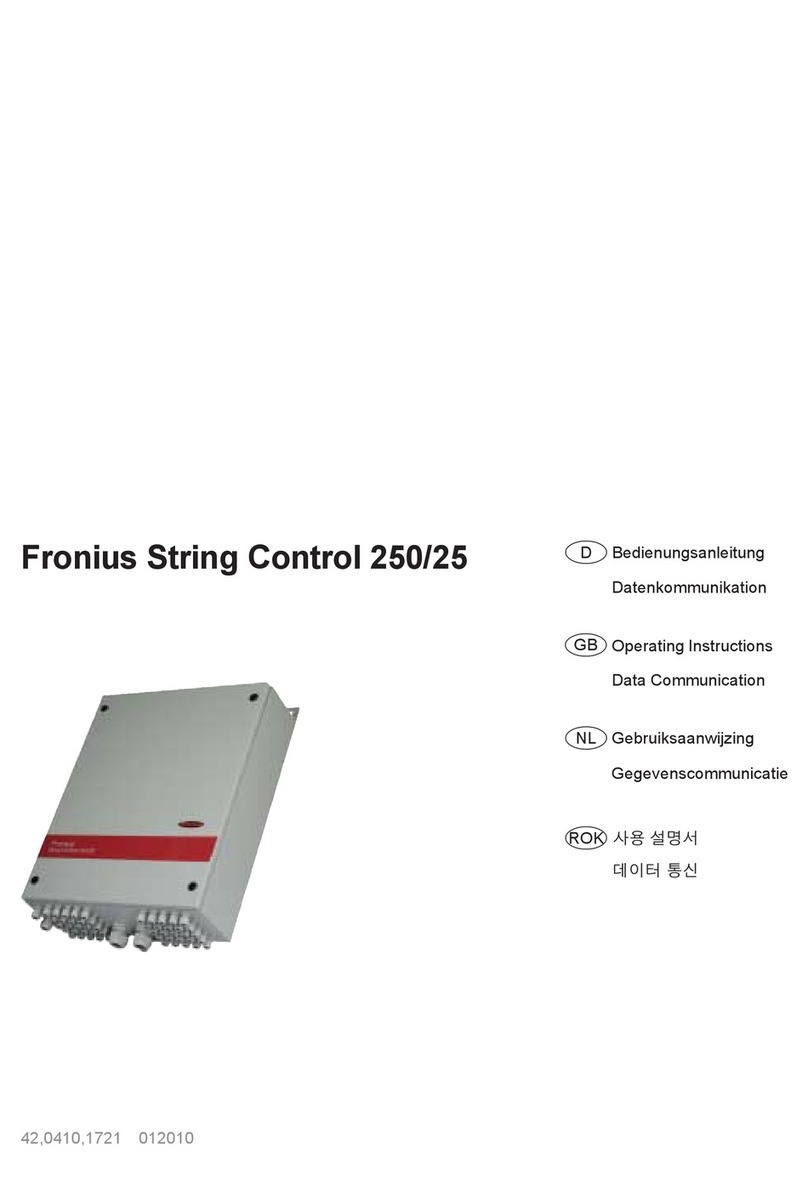
FRONIUS
FRONIUS String Control 250/25 operating instructions

HomeLink
HomeLink UAHL5B manual

HydroQuip
HydroQuip CS7100 installation instructions
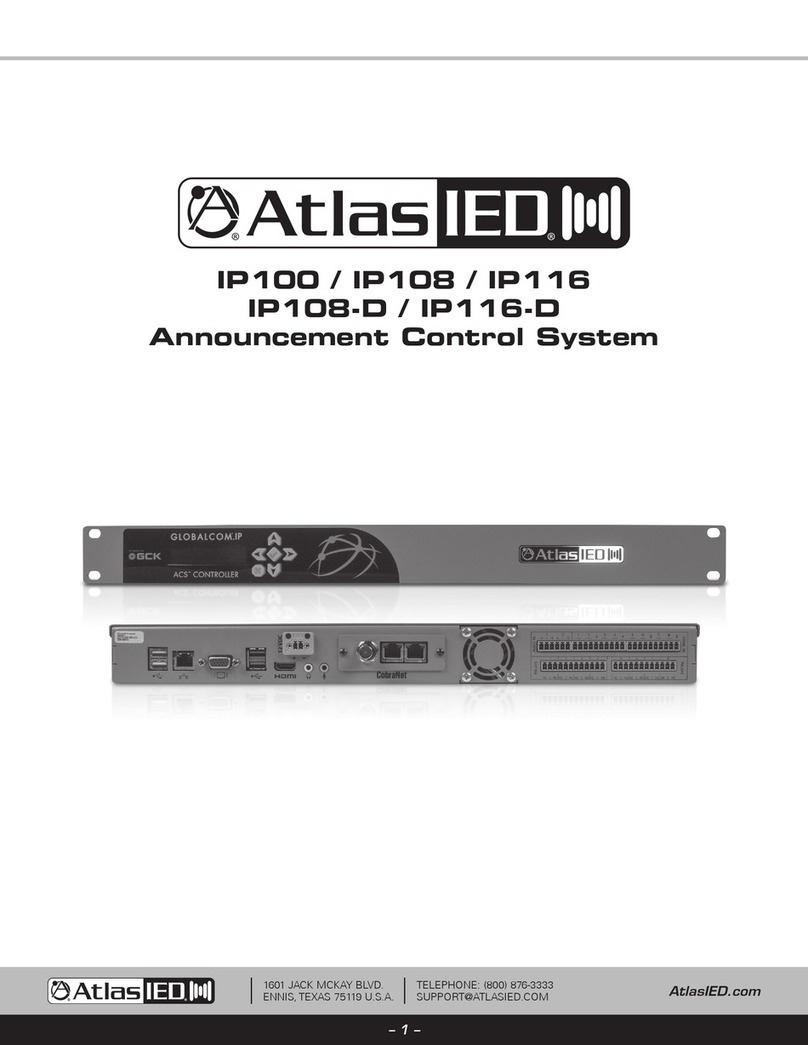
Atlas IED
Atlas IED IP100 quick start guide
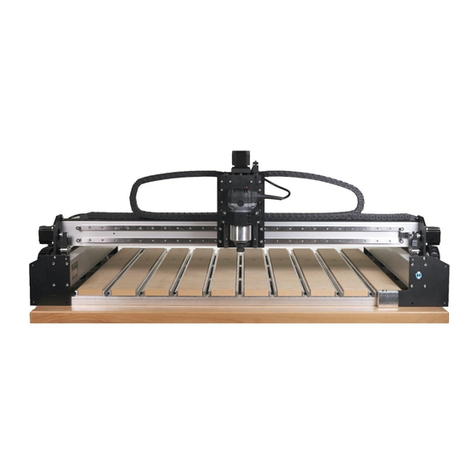
Carbide 3D
Carbide 3D Shapeoko PRO Assembly guide
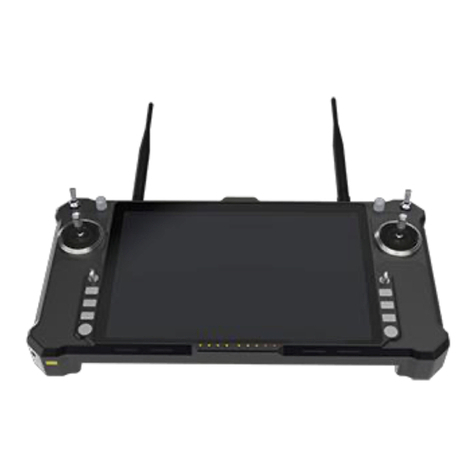
Foxtech
Foxtech T30 user manual

Air Lift
Air Lift Quick SHOT 25572 installation guide
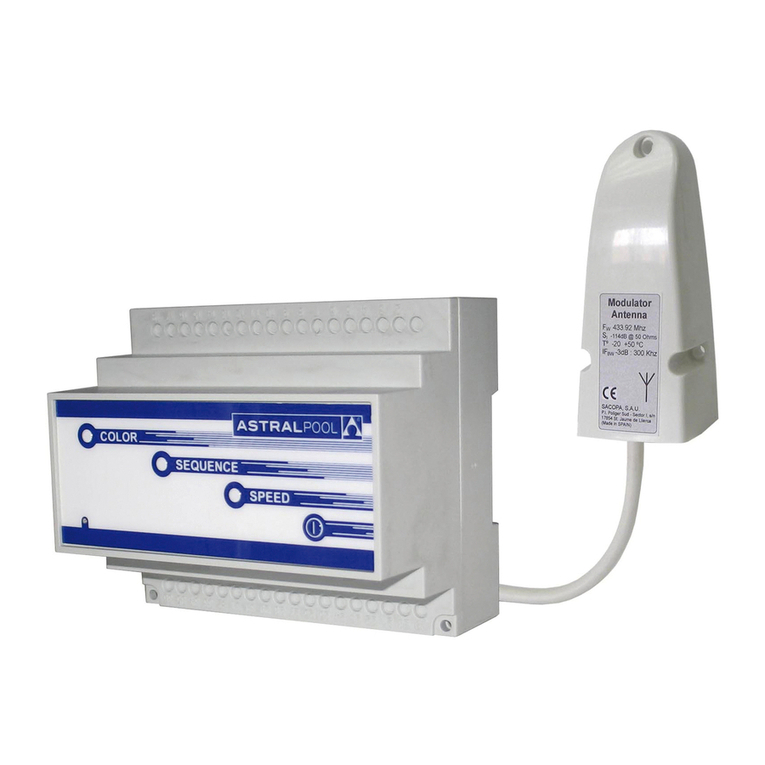
Astral Pool
Astral Pool 27818 Installation and maintenance manual
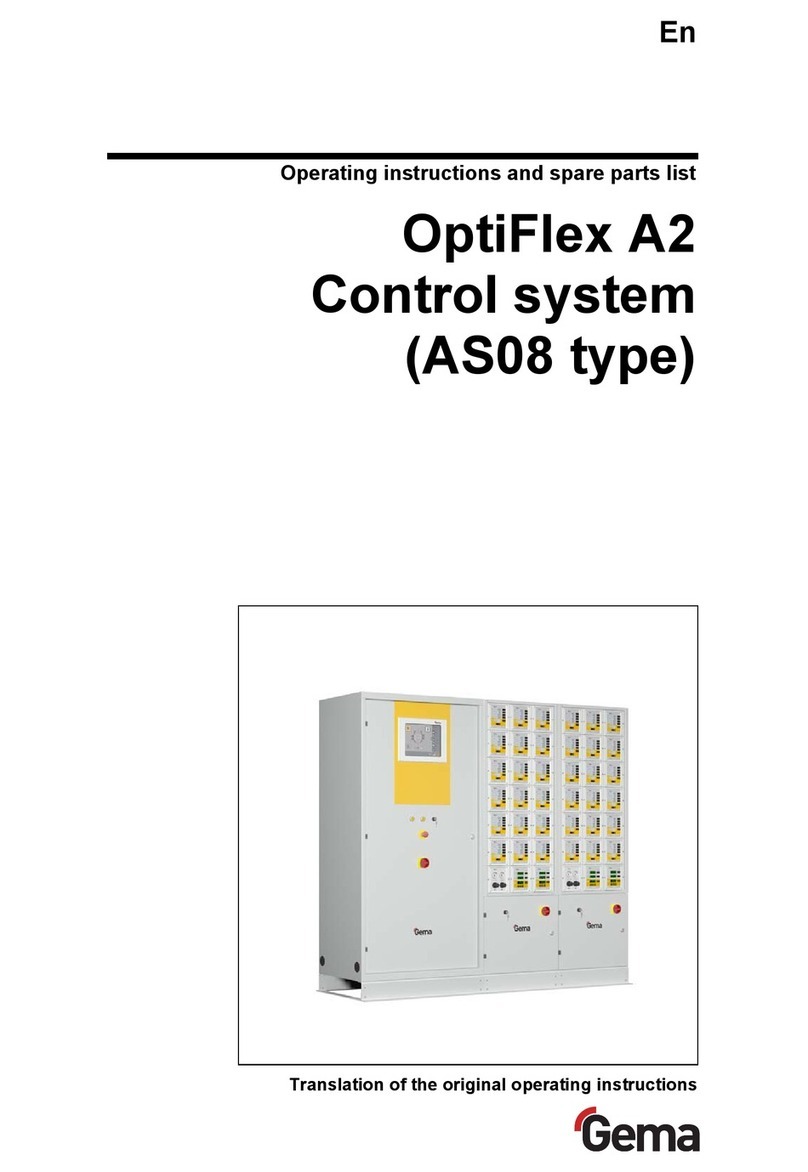
Gema
Gema OptiFlex A2 Operating instructions and spare parts list