Carbide 3D Shapeoko PRO User manual

Shapeoko PRO
ASSEMBLY GUIDE

Welcome and Congratulations
Stronger. Faster. Beefier. The Shapeoko Pro is an incredibly powerful CNC machine purpose-built for rigidity
and accuracy. An upgraded controller, integrated tool-oset probe, inductive homing switches, and multiple
built-in workholding options will save you time and increase your productivity and workflow eciency.
In this guide we will walk you step-by-step through the assembly of your ShapeokoPro. Precision-machined
parts, pre-assembled components, and self-contained packaging mean assembling your ShapeokoPro is
quick and easy. You’ll be up and machining in no time.
ShapeokoPro Assembly Video
Watch the ShapeokoPro Assembly Overview video at: youtu.be/krwt3C9aSTY.
Power Tools
The use of power tools is not recommended for assembly. Use hand tools only.
Finger-Tight Only
Several steps rely on non-tightened fasteners. Do not tighten fasteners beyond finger-tight until instructed
to do so.
Directional References
In this guide, any reference to direction or placement, such as front, back, left, right, inside, and outside, are
given from the perspective of one standing in front of and facing the machine. This is true, even when the
figure is shown from the rear of the machine.
Notes Used in This Guide
In this guide, you will find information that we’ve called out for you to pay particular attention to. We use
three types of call-outs: Warnings, Notes, and Pro Tips.
Stepper Motors
Your ShapeokoPro gantry is powered by NEMA 23 stepper motors. When the power is o, moving the
motors by hand will cause them to generate electricity.
WARNING: When moving the gantry by hand, go slowly. The power generated by the stepper motors will
feel like bumps. If the lights on the controller are lighting up, it’s very important to slow down because you
are pushing electricity back through the board. Too much back flow could damage the controller.
Firmware
The ShapeokoPro controller ships with GRBL 1.1 firmware, which must be used with Carbide Motion 5. This
document supersedes any information you may find regarding firmware and software on the Carbide 3D
website.
Glossary of Terms
See the Glossary of Terms at the end of this guide for common CNC terms and definitions.
Have Questions? Need Help?
We have a fully-staed support team waiting to help if you run into any trouble while assembling your
WELCOME AND CONGRATULATIONS ................ 1
IMPORTANT SAFETY INSTRUCTIONS ................2
INVENTORY.......................................3
STEP 1 – BASEFRAME ..............................4
1.1 Position Crossmembers & Drag Chain Support Panels........6
1.2 Assemble the Baseframe ................................7
1.3 Install Cable Tie Mounts .................................7
STEP 2 – Y‑RAILS ..................................8
2.1 Install the Y-Left Rail....................................10
2.2 Install Y-Right Rail ..................................... 11
STEP 3 – ENDPLATES .............................12
3.1 Install Front-Right Endplate .............................14
3.2 Install Back-Right Endplate. . . . . . . . . . . . . . . . . . . . . . . . . . . . . . . .16
3.3 Install Left Endplates...................................17
STEP 4 – GANTRY ................................18
4.1 Install X-Axis Gantry .................................. 20
4.2 Install X-Axis Drag Chain Support Panel ..................21
4.3 Attach Belt Clip to Belt ................................ 22
4.4 Install Y-Axis Belts .................................... 22
4.5 Square the Machine .................................. 25
STEP 5 – X/ZASSEMBLY ..........................26
5.1 Install X/ZAssembly .................................. 28
5.2 Install X-Motor and Belt ....................................28
STEP 6 – DRAG CHAIN ............................30
6.1 Install Head Bracket ...................................32
6.2 Install X-Axis Drag Chain ...............................33
6.3 Attach Transition Bracket...............................33
6.4 Install X/Y Transition Bracket & Y-Axis Drag Chain .........34
6.5 Secure Tails of the X- and Y-Axis Drag Chains............ 35
STEP 7 – ROUTER ................................36
7.1 Install Router Mount....................................38
7.2 Install Router..........................................38
7.3 Prepare Drag Chains.................................. 40
7.4 Insert Power Cable ....................................41
7.5 Install Head Bracket .................................. 42
7.6 Attach Transition Bracket ...............................43
7.7 Install X-Axis Drag Chain................................44
7.8 Install Y-Axis Drag Chain. . . . . . . . . . . . . . . . . . . . . . . . . . . . . . . .44
7.9 Secure Tails of the X- and Y-Axis Drag Chains ............ 45
STEP 8 – HYBRID TABLE ..........................46
8.1 Install HDPE Filler Strips (Optional) ......................48
8.2 Install Hybrid Extrusions .............................. 49
8.3 Install MDF Strips .................................... 49
STEP 9 – CONTROLLER ...........................50
9.1 Install Controller ..................................... 52
9.2 Connect Controller Cables ............................ 52
9.3 Connect Cables...................................... 54
9.4 Tidy Cables ......................................... 55
9.5 Connect Power and USB.............................. 56
9.6 Install an End Mill .................................... 56
STEP 10 – SET UP MACHINE‑CONTROL SOFTWARE ..58
10.1 Download CAD/CAM & Machine-Control Software ....... 58
10.2 Connect to Machine ................................. 58
10.3 Update Machine Settings .............................58
10.4 Check Proximity Switches ............................ 59
10.5 Home the Machine .................................. 59
10.6 Set Up the BitSetter ................................. 60
EXTRAS .........................................62
Beginner Tutorials ........................................ 62
Projects and Inspiration on YouTube and CutRocket........... 62
Join Our Community ...................................... 62
Software User Guides and Tutorials ......................... 63
Machining Guides ........................................ 63
Material Guide Videos .................................... 63
Workholding and Dust Collection Videos .................... 63
Glossary of Terms ........................................ 64
Machine-Use Log......................................... 65
Table of Contents

2docs.carbide3d.com [email protected] 3
Important Safety Instructions
The ShapeokoPro is a machine tool and requires the same caution that should be exercised with any
power tool.
Eye Protection
Always wear safety glasses or goggles which are suitably impact-resistant.
Hearing Protection
Always wear earplugs or ear mus. For long jobs, it may be desirable to wear both. Hearing damage is
cumulative and irreversible, so one should always err on the side of caution.
Respiratory Protection
Always wear a filter or respiratory mask suitable for the type of dust generated by the material being cut. If
necessary, arrange for dust collection and proper ventilation.
Clothing, Hair, and Jewelry
Always ensure that clothing, hair, and jewelry cannot become caught in the machine. Always wear
appropriate clothing; long-sleeved shirts, pants, and suitable footwear are recommended. When metal-
working, gloves and an apron are also recommended.
Machine Safety
Never reach into the machine’s working envelope while it is running. Always shut o and unplug the router
to perform tool changes, adjustments, and maintenance. Never leave the machine running unattended.
Always inform someone before operating the machine and check in with them after successfully
completing work. Never allow children to use the ShapeokoPro unsupervised.
Fire Prevention
Consider the possibility of a fire caused by friction from the router and take suitable fire prevention
precautions (e.g. having a fire extinguisher handy and other suitable precautions).
Outlet Requirements
Plug the router into an outlet that has a dedicated on/o switch. Be sure this is accessible while the
machine is running, in case you should need to shut o the ShapeokoPro immediately.
End Mill Safety
Use care when handling end mills—both to avoid being cut and to avoid damaging them. Handling end
mills with suitable gloves, or using a cloth to avoid contaminating them, is recommended. Inspect end mills
carefully before each use, and ensure that they are securely held by the collet.
Debris Disposal
Recycle or safely dispose of milling debris and dust, keeping in mind flammability, (potential) spontaneous
combustion, and chemical considerations. Even natural materials can have disposal implications. For
example, walnut wood dust is allelopathic (it inhibits plant growth), an irritant to the skin and respiratory
tract, and potentially poisonous to some animals. All of these possible disposal implications are in addition
to the spontaneous combustion hazard posed by all types of sawdust.
Shipping Box 1 Contains
Step 1: Baseframe Box
Step 2: Y-Rails Box
Step 3: Endplates Box
Step 4: Gantry Box
Shipping Box 2 Contains
Step 5: X/ZAssembly Box
Step 6: Drag Chain Box
Step 7: Router Box
Step 8: Hybrid Table Box
Step 9: Controller Box
Sweepy 65 V2.0 Box
Inventory
The packaging for your ShapeokoPro was carefully designed to facilitate the easiest assembly possible.
Your Shapeoko Pro arrives in two shipping boxes: box 1 contains everything you will need to complete
steps 1–4, including your assembly tool kit*, and box 2 contains everything you will need for steps 5–9. The
individual boxes in the shipping packages are self-contained steps allowing you to focus on one step at a
time. Therefore, it’s best to resist the urge to open all of the boxes at once.
*A pair of flush-cut pliers or scissors and a tape measure may also be helpful during assembly.
PRO TIP: Your ShapeokoPro kit has been carefully packaged by hand. If you find that something is
Figure I-1
Figure I-2

STEP 1 – Baseframe STEP 1
4docs.carbide3d.com [email protected] 5
Box Components
Step 1 – Baseframe box contents; see Fig.1-1.
Item Description Qty
ACrossmember (with Pre-Installed Standos) 4
BY-Axis LEFT Drag Chain Support Panel 1
CY-Axis RIGHT Drag Chain Support Panel 1
DTool Kit: 1.5, 2, 2.5, 3, 4, 5mm Ball-Nose Hex Keys; 8, 10, 13mm Wrenches 1
EM6×6mm Button Head Cap Screw 8
FCable Tie Mounts 4
GM3×6mm Button Head Cap Screw 4
HPack of 100 Cable Ties 1
Figure 1-1

STEP 1
STEP 1 – Baseframe
6docs.carbide3d.com [email protected] 7
1.1 Position Crossmembers
and Drag Chain Support Panels
1. Position the four crossmembers horizontally
across your table. See Fig. 1-2.
a. Standos up, about 10 inches apart.
2. Check each stando and make sure each is
finger-tight.
Figure 1-2
1.2 Assemble the Baseframe
1. Use a 4mm hex key and eight (8) M6×6mm
BHCS to loosely attach the support panels to
the crossmembers. See Figs. 1-2 and 1-3.
a. Snug the screws, then back out ¼ turn.
b. Don’t worry about squaring the baseframe
yet.
Figure 1-3
1.3 Install Cable Tie Mounts
1. Use a 2mm hex key and four (4) M3×6mm
BHCS to secure two (2) cable tie mounts to
each support panel. See Fig.1-3.
a. Secure mounts to the wide-set M3 holes
toward the back.
NOTE: Set aside the pack of zip ties for cable
cleanup later.
3. Position the two support panels, front to
back, across the outside edges of the four
crossmembers. See Figs. 1-2 and 1-3.
a. M3 threaded holes to the outside.
b. Two close-set M3 holes toward the front.
c. Two wide-set M3 holes toward the back.

STEP 2
STEP 2 – Y‑Rails
8docs.carbide3d.com [email protected] 9
Box Components
Step 2 – Y-Rails box contents; see Fig.2-1.
Item Description Qty
IY-Axis LEFT Extrusion Rail (Y-Left Rail) 1
JY-Axis RIGHT Extrusion Rail with Pre-Installed Wiring (Y-Right Rail) 1
KM6×85mm Shoulder Bolts 8
Figure 2-1
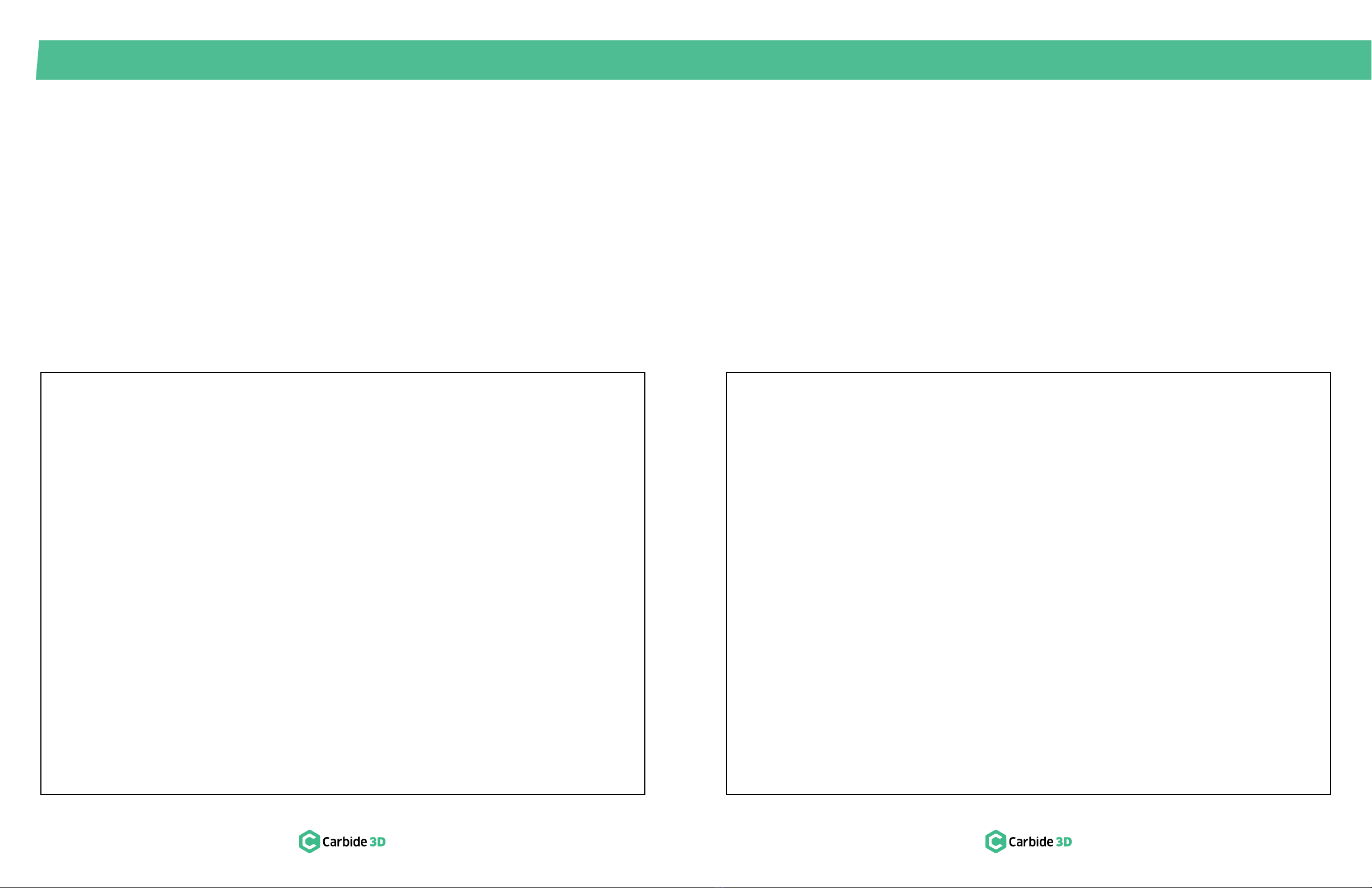
STEP 2
STEP 2 – Y‑Rails
10 docs.carbide3d.com [email protected] 11
2.1 Install the Y‑Left Rail
1. Position the Y-Left extrusion rail on the four
standos on the left side of the baseframe.
See Fig.2-2.
a. Shapeoko Pro decal to inside-front.
b. Linear rail and carrier plate to outside.
NOTE: Don’t remove the SHCS shipping screws
keeping the carrier plates from moving just yet.
Figure 2-2
2.2 Install Y‑Right Rail
1. Position the Y-Right extrusion rail on the four
standos on the right side of the baseframe.
See Fig.2-2.
a. Carbide 3D/flag decal to inside-front.
b. Linear rail and carrier plate to outside.
2. Pull the ends of the two cables out of the front
of the rail.
Figure 2-3
3. Use a 5mm hex key and four (4) M6×85mm
shoulder bolts to loosely attach the Y-Right rail
to the standos.
a. Insert bolts in order: front, back, center.
b. Ensure bolts fit snugly into the lower
through-holes with the shoulder flush
against the rail as shown in Fig.2-3.
c. Snug the bolts, then back out ¼ turn.
2. Use a 5mm hex key and four (4) M6×85mm
shoulder bolts to loosely attach the Y-Left rail
to the standos. See Fig.2-2.
a. Insert bolts in order: front, back, center.
b. Ensure bolts fit snugly into the lower
through-holes with the shoulder flush
against the rail as shown in Fig.2-3.
c. Snug the bolts, then back out ¼ turn.

STEP 3
STEP 3 – Endplates
12 docs.carbide3d.com [email protected] 13
Box Components
Step 3 – Endplates box contents; see Fig.3-1.
Item Description Qty
LBack-Left Endplate 1
MBack-Right Endplate 1
NFront-Left Endplate 1
OFront-Right Endplate (with Integrated Power Button and BitSetter) 1
PM6×12mm Low-Profile Socket Head Cap Screw 16
Figure 3-1

STEP 3
STEP 3 – Endplates
14 docs.carbide3d.com [email protected] 15
3.1 Install Front‑Right
Endplate
1. Position the front-right endplate near the front
end of the Y-Right rail.
a. Power button faces front.
b. BitSetter extends to left.
2. Connect the 4-pin power and the 3-pin
BitSetter leads to the corresponding extension
cables exiting the front of the rail. See Figs.
3-3 and3-4.
Figure 3-2 Figure 3-4
NOTE: Connectors are polarized and will only
connect one way. Do not force a connection. See
Fig.3-3.
3. Tuck the connected cables into the rail cavity,
so the endplate sits flush against the end of
the rail.
4. Use a 4mm hex key and four (4) M6×12mm low
profile SHCS to secure the endplate to the rail.
Fully tighten. Figure3-3
NOTE: Be careful not to pinch the wires between
the rail and endplate.
NOTE: Be careful not to cross-thread the screws.

STEP 3
STEP 3 – Endplates
16 docs.carbide3d.com [email protected] 17
3.2 Install Back‑Right
Endplate
1. Position the back-right endplate at the back
end of the Y-Right rail. See Fig.3-5.
a. Proximity switch to outside/front.
2. Use a 4mm hex key and four (4) M6×12mm low
profile SHCS to secure the endplate to the rail.
Fully tighten.
Figure 3-5
3.3 Install Left Endplates
1. Position the two remaining endplates at either
end of the Y-Left rail. See Fig.3-6.
a. Countersunk holes to the outside; flat side
flush against the rail ends.
b. Tapered corners to the outside/top.
2. Use a 4mm hex key and four (4) M6×12mm low
profile SHCS to secure each endplate to the
rail. Fully tighten.
Figure 3-6

STEP 4
STEP 4 – Gantry
18 docs.carbide3d.com [email protected] 19
Box Components
Step 4 – Gantry box contents; see Fig.4-1.
Item Description Qty
QX-Axis Gantry Assembly (with Pre-Installed Wiring) 1
RX-Axis Drag Chain Support Panel 1
SM6×12mm Button Head Cap Screw 6
T15mm 2GT Belt 1400mm 2
UM5×12mm Socket Head Cap Screw 4
V15mm Belt Clip 4
WM4×8mm Flat Head Screw 5
Figure 4-1

STEP 4
STEP 4 – Gantry
20 docs.carbide3d.com [email protected] 21
4.1 Install X‑Axis Gantry
1. Position the X-Axis gantry across the center
of the baseframe, resting it on the Y-Left and
Y-Right carrier plates/bearing blocks. See
Figs.4-2 and 4-4.
a. Gantry linear rails and carrier plate to front.
b. Left and right gantry endplates rest on top
of the bearing blocks to the inside of the
Y-Axis carrier plates.
Figure 4-2
4.2 Install X‑Axis Drag Chain
Support Panel
1. Position the support panel across the top-back
of the gantry. See Fig.4-3.
a. Countersunk holes up.
b. Tapered corners to back.
c. Two threaded M3 holes to left.
2. Use a 2.5mm hex key and five (5) M4×8mm
FHS to secure the panel to the gantry.
a. Start all screws before fully tightening.
Figure 4-4
NOTE: Tolerances are tight. Be sure the gantry
is centered. If necessary, tilt the still loose Y-rails
outward to fit the gantry between the plates.
2. Align the holes in the two Y-Axis carrier plates
with the left and right gantry endplates.
3. Use a 4mm hex key and six (6) M6×12mm
BHCS to loosely attach the gantry to the
carrier plates. See Fig.4-4.
a. Snug the screws, then back out ¼ turn.
Figure4-3

STEP 4
STEP 4 – Gantry
22 docs.carbide3d.com [email protected] 23
4.3 Attach Belt Clip to Belt
See Fig.4-5.
1. Thread about 5 inches of belt through the
outer slot of the clip, with teeth facing toward
the integrated nut.
2. Loop the belt down through the inner slot and
pull the belt tight against the clip.
3. Bring the two sections of belt together.
Interlock the teeth and extend the belt away
from the integrated nut.
Figure 4-7
4.4 Install Y‑Axis Belts
1. Use a 4mm hex key and one (1) M5×12mm
SHCS to secure the clip to the back-left
endplate. See Fig.4-7.
a. Slotted end of the clip against the rail.
b. Ensure belt teeth interlock where they
meet at the clip.
c. Ensure teeth face down as the belt
extends along the rail.
d. Fully tighten.
2. Thread the belt, teeth down, under the two
idlers onto the left gantry endplate.
3. Use a small hex key to pull a loop of belt up
between the two idlers. See Fig.4-6.
4. Place the loop over the stepper motor pulley.
Figure4-6
1
2
3
Figure4-5

STEP 4
STEP 4 – Gantry
24 docs.carbide3d.com [email protected] 25
5. Thread a second belt clip onto the free end of
the belt.
6. Firmly hold the clip flat against the rail.
7. Adjust the length of the belt so that there is a
2–3mm gap between the clip and the front-left
endplate. See Fig.4-8.
8. Use a 4mm hex key and one (1) M5×12mm
SHCS to secure the clip to the endplate.
a. Maintain downward pressure on the clip.
b. Fully tighten the screw until the belt snaps
back against the rail when gently lifted.
Figure 4-8
4.5 Square the Machine
1. Use a 5mm hex key to remove the M6×35mm
SHCS shipping screws from both Y-Axis carrier
plates, allowing the gantry to slide freely front
and back.
2. Slide the gantry as far forward as it will go.
3. Adjust the squareness of the baseframe
until both ends of the gantry touch the front
endplates. There should be NO GAPS on
either side. See Fig.4-9.
4. Use a 5mm hex key and fully tighten the front-
left and front-right shoulder bolts securing the
Y-rails to the baseframe.
Figure 4-9
a. Fully tighten the remaining shoulder bolts,
moving front to back, sliding the gantry as
you go, and alternating sides.
5. Slide the gantry as far back as it will go.
Ensure there are no gaps between the gantry
and the back endplates.
6. Use a 4mm hex key to fully tighten the six (6)
M6×12mm BHCS securing the gantry to the
left and right Y-Axis carrier plates.
7. Use a 4mm hex key to fully tighten the eight
(8) M6×6mm BHCS securing the left and right
drag chain support panels to the baseframe.
NOTE: Do not overstretch the belt. Stretching
more than 3mm could damage the belt or motors.
9. Repeat Steps 4.3 and 4.4 to install the second
belt to the Y-Right rail.

STEP 5
STEP 5 – X/ZAssembly
26 docs.carbide3d.com [email protected] 27
Box Components
Step 5 – X/ZAssembly box contents; see Fig.5-1.
Item Description Qty
XX/ZAssembly 1
YNema 23 Stepper Motor 1
UM5×12mm Socket Head Cap Screw 4
SM6×12mm Button Head Cap Screw 4
T15mm 2GT Belt 1400mm 1
UM5×12mm Socket Head Cap Screw 2
V15mm Belt Clip 2
Figure 5-1

STEP 5
STEP 5 – X/ZAssembly
28 docs.carbide3d.com [email protected] 29
5.1 Install X/ZAssembly
1. Use a 4mm hex key to remove the M5×25mm
SHCS shipping screw from the front of the
X-Axis carrier plate, allowing it to slide freely
left and right.
2. Position the X/Zassembly over the front of the
X-Axis carrier plate. See Fig.5-2.
a. Z-Axis plate facing front.
b. Z-Axis stepper motor on top.
3. Use a 4mm hex key and four (4) M6×12mm
BHCS to secure the X/Zassembly to the
X-Axis carrier plate. Fully tighten.
Figure 5-2
5.2 Install X‑Motor and Belt
1. Attach one end of the belt to one end of the
X-Axis gantry, threading about 3 inches of belt
through the belt clip. (Refer back to Steps 4.3
and 4.4.) See Fig.5-4.
2. Thread the belt, teeth down under the two
idlers on the back of the X/Zassembly.
3. Use a small hex key to pull a large loop of belt
up between the two idlers and into the motor
housing. See Fig.5-4.
Figure 5-4
4. Position the X-motor over the threaded screw
holes on the motor housing. See Fig.5-3.
a. Motor pulley faces into motor housing,
under the belt loop.
b. Motor lead cables extend up.
5. Use a 4mm hex key and four (4) M5×12mm
SHCS to secure the X-motor to the motor
housing. Fully tighten.
6. Pull the slack out of the belt and secure the
free end to the other end of the X-Axis gantry.
(Refer back to Steps 4.3 and 4.4.) Figure5-3

STEP 6
STEP 6 – Drag Chain
30 docs.carbide3d.com [email protected] 31
Box Components
Step 6 – Drag Chain box contents; see Fig.6-1.
Item Description Qty
ZX-Axis Data Drag Chain: 4-pin male-to-female extension (2), 3-pin male-to-female
extension (1) 1
AA Y-Axis Data Drag Chain: 4-pin male-to-female extension (4), 3-pin female to 8-pin
male proximity switch extension (X and Z) (2) 1
BB Data Drag Chain Head Bracket 1
CC M5×6mm Button Head Cap Screw 2
DD X/Y Right Transition Bracket 1
SM6×12mm Button Head Cap Screw (Extra) 2
GM3×6mm Button Head Cap Screw 8
Figure 6-1

STEP 6
STEP 6 – Drag Chain
32 docs.carbide3d.com [email protected] 33
6.1 Install Head Bracket
1. Position the drag chain head bracket on the
back of X/Zassembly (see Fig.6-2):
a. Upper-left corner (upper-right corner when
viewed from back).
b. Flange down, threaded holes to back.
2. Use a 3mm hex key and two (2) M5×6mm
BHCS to secure the bracket to the
X/Zassembly. Fully tighten.
Figure 6-3
6.2 Install X‑Axis Drag Chain
1. Position X-Axis drag chain along the top of the
X-Axis gantry.
a. Head of the chain to the left; the tail to the
right, ending at the right gantry endplate.
b. Head has all female connectors.
c. Head curls up and attaches to the head
bracket.
2. Use a 2mm hex key and two (2) M3×6mm
BHCS to secure the drag chain to the head
bracket. Fully tighten. See Fig.6-3.
Figure 6-4
6.3 Attach Transition Bracket
1. Position the Z-shaped X/Ytransition bracket
on the head of the Y-Axis drag chain. See
Fig.6-4.
a. Head of chain has all female connectors.
b. Longer arm of the bracket attaches to the
flat side of the head of the drag chain.
2. Use a 2mm hex key and two (2) M3×6mm
BHCS to secure the bracket. Fully tighten.
Figure6-2

STEP 6
STEP 6 – Drag Chain
34 docs.carbide3d.com [email protected] 35
6.4 Install X/Y Transition
Bracket and Y‑Axis Drag Chain
1. Use a 4mm hex key to remove the back two
(2) M6×12mm BHCS from the right gantry
endplate.
2. Position the bracket and Y-Axis drag chain
combo alongside the Y-Right rail. See Fig.6-5.
a. Align the bracket with the two M6 screw
holes.
b. Short arm of the bracket rests on top of
the gantry.
Figure 6-5
6.5 Secure Tails of the X‑ and
Y‑Axis Drag Chains
1. Position the tail of the X-Axis drag chain over
the two M3 screw holes at the top of the
X/Ytransition bracket. See Fig.6-6.
2. Use a 2mm hex key and two (2) M3×6mm
BHCS to secure the tail of the X-Axis drag
chain to the bracket. Fully tighten.
Figure 6-6
3. Position the tail of the Y-Axis drag chain over
the two M3 screw holes on the Y-Right drag
chain support panel. See Fig.6-6.
4. Use a 2mm hex key and two (2) M3×6mm
BHCS to secure the tail of the Y-Axis drag
chain to the support panel. Fully tighten.
c. Body of the drag chain extends forward
from the bracket, then curls down and
back.
3. Use a 4mm hex key and two (2) M6×12mm
BHCS to secure the bracket to the gantry.
Fully tighten.

STEP 7
STEP 7 – Router
36 docs.carbide3d.com [email protected] 37
Box Components
Step 7 – Router box contents; see Fig.7-1.
Item Description Qty
EE Empty X-Axis Drag Chain 1
FF Empty Y-Axis Drag Chain 1
GG Router Drag Chain Head Bracket 1
CC M5×6mm Button Head Cap Screw 2
HH X/Y Left Transition Bracket 1
SM6×12mm Button Head Cap Screw (Extra) 2
GM3×6mm Button Head Cap Screw 8
II 0.25″ and 0.125″ Precision Collets 2
JJ 65mm Router Mount 1
KK M6×40mm Socket Head Cap Screw 2
LL M5×40mm Socket Head Cap Screw 2
MM M6×25mm Socket Head Cap Screw 2
NN M6×10mm Grub Screw 1
Optional ShapeokoPro CNC Router:
Item Description Qty
OO
ShapeokoPro CNC Router Box: Includes ShapeokoPro CNC Router with Collet
and Collet Nut Installed,13mm and 22mm Wrenches, Carbon Brushes (4), User
Manual
1
Figure 7-1
Table of contents
Other Carbide 3D Control System manuals