Eddyfi Technologies Floormap X User manual

User’s
Manual
Floormap®X
MFL Array Tank Floor Inspection Solution

!
Contact information:
Eddyfi UK Ltd
Clos Llyn Cwm,
Swansea Enterprise Park,
Swansea,SA6 8QY,
Wales, UK.
+44 (0) 1792 798711
Eddyfi Technologies
3425 Pierre-Ardouin Street,
Québec (QC),
G1P 0B3,
Canada.
+1 418 780 1565
Eddyfi Technologies Europe
1 Terre Neuve Street,
Mini-parc du Verger, H building
91940 Les Ulis,
France .
+33 160 923 965
www.eddyfi.com
FloormapX User Manual Version C-01
Original instructions supplied with the FloormapX system
SIMS GO Software version 1.1R2
SIMS PRO Software version 1.2R3
The text, figures and programs have been worked out with the utmost care. However, we cannot accept either legal responsibility or any liability for any incorrect
statements which may remain, and their consequences. The following documentation is protected by copyright. All rights reserved.
Eddyfi reserves the right to continue developing the system and software without documenting each individual case. Eddyfi holds no responsibility for any damage or
destruction caused when following instructions within this manual.
July 2022

3
Contents
1.
General Precautions and Conventions .............................................................................. 11
1.1 General Precautions ........................................................................................................... 11
1.2 Safety Precautions ............................................................................................................. 11
1.3 Conventions ......................................................................................................................13
1.4 EMC Directive Compliance .................................................................................................15
1.5 EU Declaration of Conformity............................................................................................ 16
1.6 Calibration and Warranty Seals ..........................................................................................17
1.7 Limited Warranty...............................................................................................................17
1.8 Copyrights........................................................................................................................ 18
2.
Introducing FloormapX ..................................................................................................20
2.1 What’s in the Box.............................................................................................................. 20
2.2 FloormapX Overview......................................................................................................... 20
2.3 Assembling the FloormapX.................................................................................................31
2.4 Recommended Scanning Bridge Height ............................................................................. 32
2.5 MFL Technique ................................................................................................................. 33
2.6 Specifications...................................................................................................................34
3.
Inspection Process.........................................................................................................36
3.1 Pre-Inspection preparation ................................................................................................36
3.2 Onsite FloormapX setup preparation .................................................................................36
3.3 FloormapX calibration preparation ....................................................................................36
3.4 In Tank Inspection Setup ................................................................................................... 37
3.5 Scanning checklist............................................................................................................40
3.6 Plate scanning coverage................................................................................................... 41
3.7 Post-inspection checklist................................................................................................... 42
4.
SIMS GO data acquisition Software ................................................................................44
4.1 Introduction .....................................................................................................................44
4.2 Backstage........................................................................................................................44

4
4.3 Frontstage Layout .............................................................................................................51
4.4 Inspection.........................................................................................................................51
4.5 Calibration....................................................................................................................... 53
4.6 Plate Setup Ribbon........................................................................................................... 56
4.7 Plate View Ribbon ............................................................................................................60
4.8 Scan Ribbon.....................................................................................................................65
4.9 Freescan Ribbon............................................................................................................... 67
4.10 Workflows and Operation................................................................................................68
5.
SIMS PRO Reporting Software ........................................................................................70
5.1 Introduction ..................................................................................................................... 70
5.2 Installing SIMS PRO........................................................................................................... 70
5.3 Loading SIMS PRO ............................................................................................................ 70
5.4 SIMS PRO Backstage .........................................................................................................71
5.5 SIMS PRO Frontstage ........................................................................................................ 77
5.6 Home Ribbon...................................................................................................................80
5.7 Design Ribbon .................................................................................................................. 85
5.8 Repair Ribbon ..................................................................................................................88
5.9 Report Ribbon..................................................................................................................90
5.10 Report Tool Ribbon.......................................................................................................... 92
5.11 Data Ribbon.................................................................................................................... 93
5.12 Indication Ribbon ............................................................................................................94
5.13 Modification Ribbon ........................................................................................................96
6.
Maintenance ................................................................................................................99
6.1 FloormapX system precautions ..........................................................................................99
6.2 Transportation and Storage ..............................................................................................99
6.3 Tablet.............................................................................................................................102
6.4 User control ....................................................................................................................102
6.5 Mainframe......................................................................................................................102

5
6.6 Scanning Head ...............................................................................................................103
6.7 Service............................................................................................................................104
7.
Troubleshooting .......................................................................................................... 105
7.1 System won’t power on ....................................................................................................105
7.2 Motorization not functioning............................................................................................105
7.3 Firmware version error message .......................................................................................105

6
Figures
Figure 1: System magnet position indicators ................................................................................ 11
Figure 2: FloormapX front overview ............................................................................................ 20
Figure 3: FloormapX rear overview.............................................................................................. 20
Figure 4: Scanning head overview ...............................................................................................21
Figure 5: Scanning head product and serial number label .............................................................21
Figure 6: Mainframe front overview............................................................................................ 23
Figure 7: Mainframe rear overview ............................................................................................. 23
Figure 8: Mainframe product and serial label .............................................................................. 23
Figure 9: Laser and rear light module ........................................................................................ 24
Figure 10: User control product and serial label ........................................................................... 25
Figure 11: User control button overview....................................................................................... 25
Figure 12: Tablet product and serial label .................................................................................... 26
Figure 13: FloormapX tablet overview ......................................................................................... 26
Figure 14: FloormapX tablet label ............................................................................................... 28
Figure 15: FloormapX battery label ............................................................................................. 28
Figure 16: FloormapX mainframe label ....................................................................................... 28
Figure 17: FloormapX battery ..................................................................................................... 28
Figure 18: FloormapX battery compartment ............................................................................... 28
Figure 19: FloormapX battery charger information ...................................................................... 29
Figure 20: Offering the mainframe to the scanning head .............................................................31
Figure 21: Engaging the mainframe with the scanning head .........................................................31
Figure 22: FloormapX tablet connector....................................................................................... 32
Figure 23: FloormapX battery compartment ............................................................................... 32
Figure 24: Tank floor aligning for horizontal and vertical plane..................................................... 38
Figure 25: Identifying parallel plate rows..................................................................................... 38
Figure 26: Orientating to be perpendicular to plate rows ............................................................. 38
Figure 27: Position of tank datum into the bottom left-hand corner............................................. 39
Figure 28: Plate numbering system with bottom-left tank datum position ................................... 39
Figure 29: Rectangle and sketch plate markings for scan width ...................................................40
Figure 30: FloormapX sensor head mechanical constraints .......................................................... 41
Figure 31: SIMS GO backstage - general......................................................................................44
Figure 32: Create inspection ......................................................................................................45
Figure 33: Tank diameter calculator ........................................................................................... 45
Figure 34: Load inspection .........................................................................................................46
Figure 35: Inspection transfer menu ...........................................................................................46
Figure 36: Load calibration ........................................................................................................ 47

7
Figure 37: Plate list.................................................................................................................... 47
Figure 38: Backstage, documentation ........................................................................................48
Figure 39: Backstage, system ....................................................................................................48
Figure 40: Date and time menu .................................................................................................48
Figure 41: Backstage, display .....................................................................................................49
Figure 42: Backstage, software license .......................................................................................50
Figure 43: Edit contact information............................................................................................50
Figure 44: Backstage, help.........................................................................................................50
Figure 45: Frontstage ribbon.......................................................................................................51
Figure 46: Inspection page..........................................................................................................51
Figure 47: Plate list.................................................................................................................... 52
Figure 48: Full indication list....................................................................................................... 52
Figure 49: Tablet button to change indication status .................................................................. 53
Figure 50: Calibration page ....................................................................................................... 53
Figure 51: Create calibration ......................................................................................................54
Figure 52: Step 1 - top surface scan ............................................................................................54
Figure 53: Step 2 - top surface scan ...........................................................................................54
Figure 54: Step 3 - top surface scan ........................................................................................... 54
Figure 55: Turning the reference plate ........................................................................................ 54
Figure 56: Step 1 - bottom surface scan...................................................................................... 54
Figure 57: Step 2 - bottom surface scan ..................................................................................... 54
Figure 58: Step 3 - bottom surface scan ..................................................................................... 54
Figure 59: Load calibration ........................................................................................................ 55
Figure 60: Importing calibration from another inspection ............................................................ 55
Figure 61: Plate setup page........................................................................................................56
Figure 62: Green tick on calibration ribbon.................................................................................. 56
Figure 63: Purple exclamation mark on calibration ribbon ...........................................................56
Figure 64: Example of horizontal plate ....................................................................................... 57
Figure 65: Example of a vertical plate......................................................................................... 57
Figure 66: Example of parallel scan pattern ................................................................................58
Figure 67: Example of a raster scan pattern................................................................................ 58
Figure 68: Discrepancy between the plate thickness and calibration thickness.............................. 58
Figure 69: Overlap value of 0mm ............................................................................................... 59
Figure 70: Overlap value of 50mm ............................................................................................. 59
Figure 71: Shell offset measurement ........................................................................................... 59
Figure 72: Scanning head side black casing notch .......................................................................59
Figure 73: Created plate status with green circle.........................................................................59
Figure 74: New plate status with orange circle............................................................................ 59

8
Figure 75: Plate view .................................................................................................................60
Figure 76: Plate list....................................................................................................................60
Figure 77: Plate view update for add custom scan....................................................................... 61
Figure 78: Selected scan number................................................................................................ 62
Figure 79: Scan options ............................................................................................................. 62
Figure 80: Start scan position - track origin ................................................................................63
Figure 81: Start scan position - resume .......................................................................................63
Figure 82: Start scan position - plate ref .....................................................................................63
Figure 83: Full indication list....................................................................................................... 65
Figure 84: Tablet button to change indication status ..................................................................65
Figure 85: Scan window during data acquisition.......................................................................... 65
Figure 86: Scanner speed window ..............................................................................................66
Figure 87: Scan markings during acquisition ...............................................................................66
Figure 88: Freescan page........................................................................................................... 67
Figure 89: Screening inspection workflow ...................................................................................68
Figure 90: Mapping inspection workflow.....................................................................................68
Figure 91: SIMS PRO installation wizard....................................................................................... 70
Figure 92: SIMS PRO desktop icon .............................................................................................. 70
Figure 93: SIMS PRO backstage home .........................................................................................71
Figure 94: Import data wizard, asset selection ............................................................................ 72
Figure 95: Import data wizard, import data................................................................................ 72
Figure 96: Load inspection wizard .............................................................................................. 73
Figure 97: Exit inspection options ............................................................................................... 74
Figure 98: Excel manual indication template .............................................................................. 74
Figure 99: Excel patch plate template ........................................................................................ 75
Figure 100: Importing Excel Data Template................................................................................. 75
Figure 101: Template data validation successful .......................................................................... 76
Figure 102: Indication list export configuration ............................................................................ 76
Figure 103: SIMS PRO frontstage ................................................................................................ 77
Figure 104: Home ribbon............................................................................................................80
Figure 105: Plate list tool window ............................................................................................... 81
Figure 106: Indication list tool window ........................................................................................ 81
Figure 107: Additional information for a selected indication ......................................................... 82
Figure 108: Rectangular indication ............................................................................................. 82
Figure 109: Freeform indication ..................................................................................................83
Figure 110: Note marker............................................................................................................. 83
Figure 111: Calibration viewer tool window...................................................................................84
Figure 112: Curve weld indication................................................................................................84

9
Figure 113: Curve weld indication................................................................................................ 85
Figure 114: Design ribbon ...........................................................................................................85
Figure 115: Tank north compass.................................................................................................. 85
Figure 116: Create annular ring wizard ........................................................................................86
Figure 117: Component list tool window ...................................................................................... 87
Figure 118: Repair ribbon............................................................................................................88
Figure 119: Patch plate reference position at center.....................................................................89
Figure 120: Patch plate reference position at top left...................................................................89
Figure 121: Patch plate list tool window.......................................................................................89
Figure 122: Report ribbon ...........................................................................................................90
Figure 123: Report document window.........................................................................................90
Figure 124: Report wizard options............................................................................................... 91
Figure 125: Plate property reportable options .............................................................................. 91
Figure 126: Report tools ribbon................................................................................................... 92
Figure 127: Indication ribbon ......................................................................................................94
Figure 128: Group of selected indications ....................................................................................94
Figure 129: Edit indication by prove-up .......................................................................................95
Figure 130: Edit indications by a percentage variation .................................................................95
Figure 131: Modification ribbon...................................................................................................96
Figure 132: Scanner head transit case packing .......................................................................... 100
Figure 133: Mainframe transit case packing ............................................................................... 101

10
Chapter 1
Precautions and
conventions

General Precautions and Conventions
11
1.
General Precautions and Conventions
1.1 General Precautions
The following safety precautions must always be observed when using the Floormap®X system.
Please ensure that you review them before turning on the system:
• Keep this document in a safe place for future reference.
• Carefully follow the installation and operation procedures detailed herein.
• Observe all warnings, notes and instructions as marked on the packaging, the scanner, and
detailed in the user manual.
• FloormapX system should only be used by trained operators.
• When transporting FloormapX, it is your responsibility to follow all safety precautions as
dictated by the relevant local governing bodies.
• The equipment must not be used for purposes other than those intended. Eddyfi assumes no
responsibility for any damage resulting from such improper usage.
• If you use the system in a manner that deviates from the one specified by Eddyfi, the
protection provided on the equipment may be rendered null and void.
• Do not use substitute parts or perform unauthorized modifications to the system.
• Service instructions, when applicable, are intended for trained service personnel only.
• Ensure by regular checks that the working site, equipment, and environments are kept in a
clean and clearly arranged state.
• Rules and regulations regarding the prevention of accidents that apply to the working site
should be observed.
• If the system does not operate normally, please contact Eddyfi for assistance.
• Do not leave the FloormapX system unattended when not in use.
1.2 Safety Precautions
Observe the following safety precautions rigorously when using FloormapX.
WARNING
Pinch Hazards & Powerful Magnets
The FloormapX system utilizes powerful magnets and as such presents an inherent pinch/crush
hazard. Care must always be taken when handling and using the FloormapX system. It is important
to identify in which state the FloormapX magnets are by referring to the magnet position indicators.
Figure 1: System magnet position indicators
• FloormapX magnets
ON (a non-zero magnet position indicator)
. Here the FloormapX
does
impart magnetism into the inspection surface and so is powerfully attracted to the inspection
surface or any other ferrous surface or object.

General Precautions and Conventions
12
• FloormapX magnets
OFF
(
magnet position indicator at zero
). Here the FloormapX
does not
impart magnetism into the inspection surface and so is
not
attracted to the inspection
surface.
NOTE
There will still be some low-level residual magnetism around the system and there are places
that magnetically attract small ferromagnetic items.
Removal / Deployment
Due to the powerful magnets involved, and regardless of the magnet being in an on or off position,
care must always be taken when handling and using the FloormapX system including when operating
the variable bridge (high / low) mechanism, as the system will exhibit a strong force and present a
finger trap. When investigating the scanning head of the FloormapX system it is
recommended to
set the magnet position to the off position.
Handling / Carrying / Tank entry
When required to carry the FloormapX system, firstly ensure it is safe to do so and it is recommended
to have the magnets situated in scanning head in the ‘off’ position. If moving the FloormapX over a
longer distance it is recommended to use the dedicated transit cases.
During tank entry, it is recommended that the FloormapX is broken down into its component
modules. If possible, tank ingress and egress should be performed with the FloormapX still contained
within the transit cases.
Operators manually handling the system, whether fully assembled or broken into modules, should be
aware of safe manual handling practices. Care should be taken during tank ingress and egress
through the access manway. The system must be lifted by two suitably strong persons.
Magnetic Attraction
Due to the strong magnetism involved, loose ferrous material near the FloormapX system, such as
tools, metal objects or magnets will be attracted to the systems magnetic bridge and may cause
injury as they move towards the poles. Always ensure to work in a clean area, carefully follow handling
instructions and be vigilant.
Pacemakers or other medical devices and mechanical implants
Powerful magnets may interfere with medical electronics such as pacemakers, defibrillators, or other
internal and external medical devices. The interference can be severe and cause malfunctions.
Individuals wearing such devices should not handle strong magnets. If any user has any type of
electronic, mechanical, implanted, or external medical device, they should consult a physician and the
manufacturer of the medical device to determine its susceptibility to static magnetic fields prior to
allowing them to handle the FloormapX. All magnetic products should be kept at a safe distance
from individuals with such devices.
Damage to magnetic media, electronics, and mechanical devices
Any form of credit card, security pass, computer or programmed equipment may be permanently
affected if exposed to the powerful magnetic field of the unit.
Laser
The FloormapX system utilizes a Class 2 (II) laser for indication location. While laser protection
eyewear is not normally necessary, do not deliberately look or stare into the laser beam. Avoid
accidental exposure to eyes. Do not aim at aircraft or vehicles, it is unsafe and illegal.

General Precautions and Conventions
13
1.3 Conventions
Marking and Symbols
The following symbols pertain to safety regulations that should be carefully observed:
This label is used as a general warning sign. Always refer to the user’s manual to obtain the necessary
information for proper protection of the instrument and its users.
This label is used to indicate the presence of strong magnets that generate magnetic fields. Always
refer to the user’s manual to ensure proper protection and safety.
This label is used to indicate the presence of a class 2 (II) laser. Always refer to the user’s manual to
ensure proper protection and safety.
The RoHS compliance logo signifies that this product complies with the Restriction of Hazardous
Substances directive 2011/65/EU and 2015/863/EU. This directive restricts the use of Lead, Mercury,
Cadmium, Hexavalent Chromium, Polybrominated Biphenyl, Bis(2-Ethylhexyl) phthalate, Benzyl
butyl phthalate, Dibutyl phthalate, Diisobutyl phthalate and Polybrominated Diphenyl Ethers in
certain classes of electrical and electronic units as of July 22, 2019.
The FloormapX system is designed to meet the safety requirements in accordance with electrical
safety and electromagnetic compatibility. It has been tested and has left the factory in a condition
in which it is safe to operate. The equipment, when used as intended according to its user manual,
complies with the essential requirements of the following Low Voltage Directive (LVD) 2014/35/EU,
the Radio Equipment Directive (RED) 2014/53/EU, the Electromagnetic Compatibility (EMC) Directive
2014/30/EC, and the Machinery Directive (MD) 2006/42/EC.
This label acts as a reminder that you should dispose of this system in accordance with your local
Waste Electrical and Electronic Equipment (WEEE) regulations. Due to its nature, this product may
contain small quantities of substances known to be hazardous to the environment and to human
health if released in the environment. As such, it falls under WEEE regulations should not be disposed
of in the public waste stream.
Safety Indications in This Document
The safety indications in this document are intended to ensure operator safety and the integrity of
the system.
DANGER!
Danger statements are a description of an imminent hazardous procedure or a practice (or the like)
that, if performed incorrectly, can result in severe injury or death if not avoided and should be limited
to the most extreme situations. Do not ignore danger indications, ensure the condition is understood
before proceeding.
WARNING!
Warning statements are a description of a potentially hazardous procedure or a practice (or the like)
that, if not avoided or if performed incorrectly, could result in injury. Do not ignore warning
indications, ensure the condition is understood before proceeding.

General Precautions and Conventions
14
CAUTION!
Caution statements are a description of a potentially hazardous procedure or a practice (or the like)
that, if not avoided or if performed incorrectly, could result in material damage, loss of data, or both.
Do not ignore warning indications, ensure the condition is understood before proceeding.
READ MANUAL
FloormapX system is designed for a specific use. Using the FloormapX system outside of its intended
use is dangerous. Severe injury or death could result. Read and understand this manual before use.
WARNING MAGNETIC MATERIAL
Due to magnetic material, consult IATA documentation before air shipping and ensure the
appropriate labelling is used to identify the magnetized material contained within the scanner head
transit case.
The FloormapX contains strong magnets that produce an extremely strong magnetic field which may
cause failure or permanent damage to items such as watches, memory devices, CRT monitors, and
medical or other electronics devices.
Strong magnetic fields pose a variety of risks, especially to people who wear implanted cardiac devices
like pacemakers and defibrillators. People with pacemakers or ICD’s must stay at least 2 m (6.5 ft)
away.
WARNING FINGER TRAP
Tools, magnets, and metal objects can cut, pinch, or entrap hands and fingers. HANDLE WITH CARE.
WARNING LASER
The FloormapX system contains a Class 2 (II) laser. While laser protection eyewear is not normally
necessary, do not deliberately look or stare into the laser beam. Avoid accidental exposure to eyes.
Do not aim at aircraft or vehicles, it is unsafe and illegal.
HOT SURFACE
The FloormapX system contains front LED headlights. While hot temperatures are not expected
when lit, care must be taken in this region when touching the system.
REMOVE BATTERY
When the FloormapX system is powered off the battery must be removed from the right-hand active
battery slot and placed into the left-hand storage slot. The battery capacity has a potential of
discharging if left in the active slot when the system is not powered on.
IMPORTANT
Calls the attention to information important to completing tasks.
NOTE
Calls the attention to an operating procedure, a practice, or the like that requires special attention.
Acronyms in this Document
The following acronyms can be found this document.
EPL
Estimated Percentage Loss
MFL
Magnetic Flux Leakage
UT
Ultrasound
Est. Remain
Estimated Remaining Thickness
WT
Wall Thickness

General Precautions and Conventions
15
1.4 EMC Directive Compliance
The FloormapX system has undergone EMC tested and has found to be in compliance with
electromagnetic compatibility directive 2014/30/EU which are covered by the following harmonized
standards EN61326-1 (2013) – Electrical equipment for measurement, control, and laboratory use. The
system configuration of the scanner and tablet can be used in an industrial electromagnetic
environment. The system configuration of the tablet and charger can be used in a basic
electromagnetic environment.
The system has also been found to be in compliance with FFC part 15 subpart B, and ICES-003.
FCC Compliance (USA)
This equipment was tested and found to comply with the limits for a Class A digital device, pursuant
to Part 15 of the FCC Rules. These limits are designed to provide reasonable protection against
harmful interference when the equipment is operated in a commercial environment.
This equipment generates, uses, and can radiate radio frequency energy and, if not installed and used
in accordance with the user’s guide, may cause harmful interference to radio communications.
Operation of this equipment in a residential area is likely to cause harmful interference in which case
you will be required to correct the interference at your own expense.
ICES Compliance (Canada)
This device complies with Canadian ICES-001(A).
Cet appareil est conforme à la norme NMB-001(A) du Canada.

General Precautions and Conventions
16
1.5 EU Declaration of Conformity

General Precautions and Conventions
17
1.6 Calibration and Warranty Seals
The internal electronics module of the FloormapX is equipped with a warranty seal.
IMPORTANT
Broken seals void the calibration certification and product warranty.
1.7 Limited Warranty
LIMITED PRODUCT WARRANTY: Except as otherwise agreed to by EDDYFI in writing, products such as
instruments, mechanical products, spare parts, probes and cables are warranted, to the original
Customer only, for use solely by Customer or direct affiliate, against defects in material and
workmanship for a period of twelve (12) months from the date of delivery. Additional coverage may
be provided under any Hardware Maintenance Plan (HMP) purchased by the Customer. Probes and
cables are considered consumables and require periodic replacement due to wear. EDDYFI does not
warrant the service life of probes, cables and other consumables. EDDYFI does not warrant any
products against damages or defects caused by wear and tear, negligence, misuse, abnormal
operating conditions, alterations or damage caused by events beyond the control of EDDYFI. EDDYFI
shall not be liable for product defects caused by or resulting from any inaccuracies in any drawing,
description or specification supplied by the Customer. Upon Customers written request during the
warranty period, EDDYFI, at its choice, will repair or replace defective products within a reasonable
time. The original term of warranty applies, without extension, for repaired or replacement products.
All defective product shall be sent to EDDYFI freight prepaid by Customer in packaging appropriate
to prevent damage in transit. The Limited Product Warranty does not apply to periodic calibration or
minor maintenance as described in products operating manuals. All Customer paid repairs performed
by EDDYFI are warranted against defects in materials and workmanship for ninety (90) days from
the completion of repair. Upon Customer’s written notice of defect within the ninety (90) day period,
EDDYFI will replace the defective part(s) and/or re-perform the service. This warranty is limited to
failures in areas directly related to the repair performed. EDDYFI does not warrant any non-EDDYFI
products.
SOFTWARE: Any software related to the products is subject to specific Software License Agreement
or Software Subscription Agreement. The software is not sold but granted under a non-exclusive and
restrictive license. The software must be used with the software-enable hardware or software key
supplied by EDDYFI.
TECHNICAL SUPPORT: Eddyfi shall have no obligations to provide technical support and expertise for
i) Hardware Product that are not under a valid calibration certificate or under a valid Hardware
Maintenance Plan (HMP), and ii) Software that has not been updated to the latest version available
under a Software Subscription or a Software Maintenance Plan.
LIMITED SERVICE WARRANTY: EDDYFI agrees to perform service for Customer on the expressed
condition that EDDYFI’s sole obligation will be that the service will be performed in a professional and
competent manner and will be of the kind and quality described in the EDDYFI quotation. EDDYFI
does not warrant the fitness, suitability, or condition of Customer’s equipment upon which EDDYFI
services are performed. If there is a specific problem with the quality of the service performed,
Customer shall inform EDDYFI in writing and, if feasible, the service will be re-performed at no
additional charge. In the event corrective services are performed by EDDYFI, Customer must provide
adequate access to the equipment to allow EDDYFI to perform these services. Any additional costs
incurred to provide access to the equipment will be the responsibility of the Customer. If re-
performance of the service is not feasible, EDDYFI and Customer shall negotiate in good faith to arrive
at an equitable solution.
REGARDLESS OF WHETHER UNDER CONTRACT OR TORT, NEGLIGENCE, OR ANY OTHER LEGAL

General Precautions and Conventions
18
THEORY, THE LIMITED PRODUCT AND SERVICES WARRANTIES SET FORTH HEREIN ARE EXCLUSIVE
AND NO OTHER WARRANTIES, EXPRESSED OR IMPLIED, INCLUDING BUT NOT LIMITED TO THE
IMPLIED WARRANTIES OF MERCHANTIBILITY AND/OR FITNESS FOR A PARTICULAR PURPOSE
SHALL APPLY. THE LIMITED PRODUCT WARRANTY AND THE LIMITED SERVICE WARRANY ARE THE
SOLE LIABILITY OF EDDYFI WITH REGARD TO ITS PRODUCTS AND SERVICES.
LIMITATION OF LIABILITY: EDDYFI’s total liability for any and all losses and damages arising out of any
and all causes whatsoever including, without limitation, defects in the products, services, software,
documentation, or sitework supplied, shall in no event exceed the purchase price of the applicable
item(s). In no case shall EDDYFI be liable for any special, incidental or consequential damages based
upon breach of warranty, breach of contract, negligence, direct liability or any other legal theory.
Excluded damages include, but are not limited to; loss of profit, loss of savings or revenue or other
commercial or economics losses, loss of use of the product or any associated equipment, downtime,
the claims of third parties, including Customer, damage to property or injury to personnel.
Nothing
in these conditions shall however limit or exclude EDDYFI’s liability for any matter in respect of which
it would be unlawful for EDDYFI to exclude or restrict liability.
1.8 Copyrights
This document, the product and programs it describes are protected by copyright laws in the UK, by
laws of other countries, and by international treaties, therefore may not be reproduced, in whole or
in part, whether for sale or not, without prior written consent from Eddyfi UK Ltd. Under copyright
law, copying includes translation in other languages and formats.
© Eddyfi UK Ltd, 2022
This document was prepared with particular attention to usage to ensure the accuracy of the
information it contains. It corresponds to the version of the product manufactured prior to the date
appearing on the inside front cover. There may, however, be some differences between this document
and the product, if the product was modified after publication.
The information contained in this document is subject to change without notice.

19
Chapter 2
FloormapX System
Overview

FloormapX System Overview
20
2.
Introducing FloormapX
The FloormapX is a battery powered, motor driven Magnetic Flux Leakage (MFL) Array tank floor
scanner, tailored towards large scale inspection of flat, ferrous, inspection surfaces to identify areas
of reduced thickness and provide a value of Estimated Plate Loss (EPL) where appropriate. The
dedicated data acquisition software SIMS GO is used to inspect in one of the two scanning modes;
mapping or Freescan, both of which modes can adopt a pause on defect workflow.
2.1 What’s in the Box
The FloormapX is supplied in two rugged transport cases and comes with the following standard
accessories:
Mainframe box
• FloormapX mainframe.
• FloormapX user control.
• 3x NiMH batteries and 2x chargers.
• FloormapX tablet with stylus and SIMS
GO acquisition software.
• FloormapX tablet charger.
• Motorization and sensor probe cables.
• Documentation.
Scanning head box
• FloormapX scanning head. • Documentation.
2.2 FloormapX Overview
The FloormapX system comprises of the following key components:
• Scanning head.
• Mainframe.
• User control.
• Tablet.
• Batteries.
Figure 2: FloormapX front overview
Figure 3: FloormapX rear overview
Other manuals for Floormap X
1
Table of contents
Other Eddyfi Technologies Scanner manuals
Popular Scanner manuals by other brands
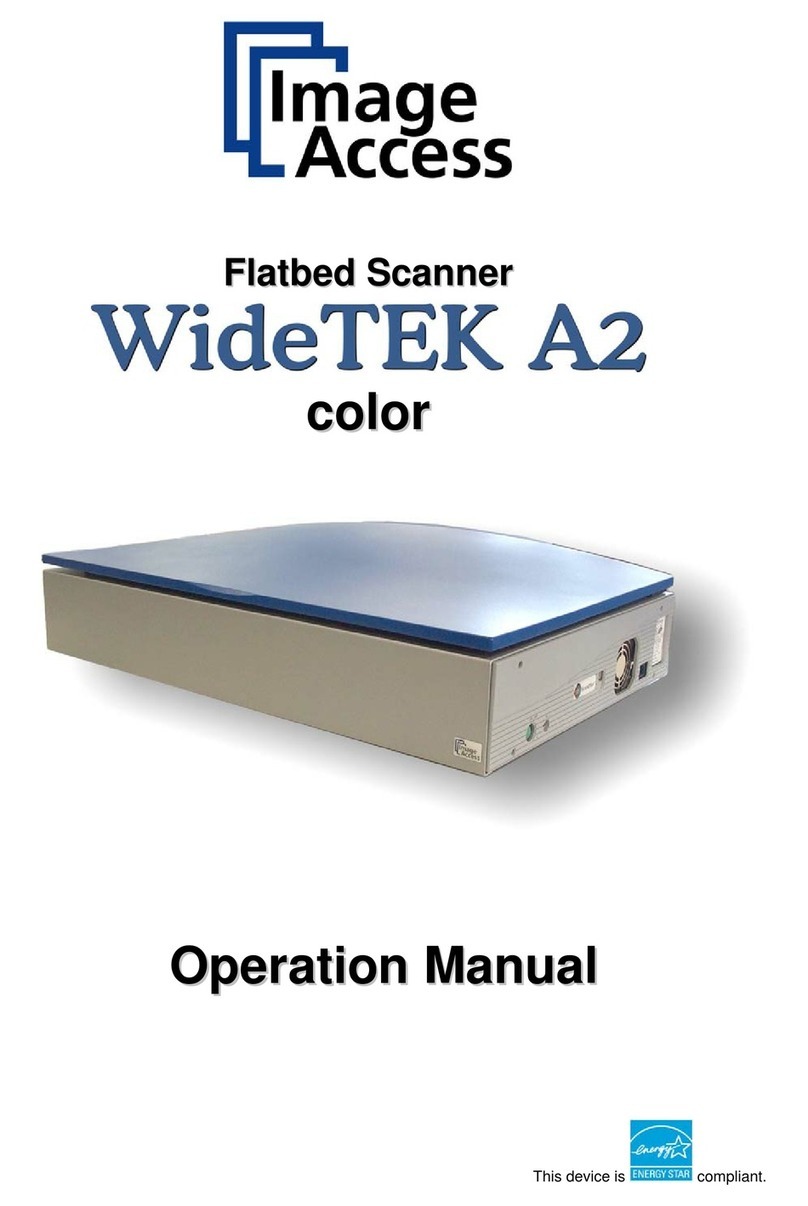
Image Access
Image Access WideTEK A2 Operation manual
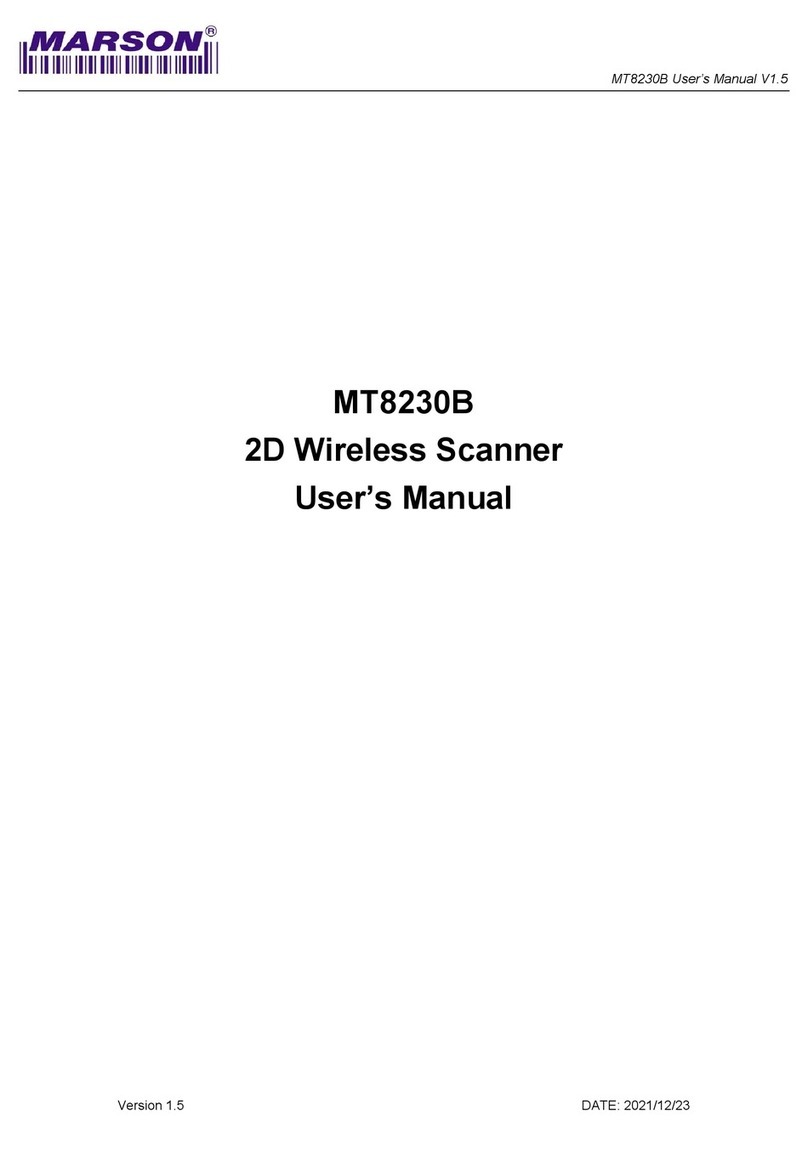
Marson
Marson MT8230B user manual
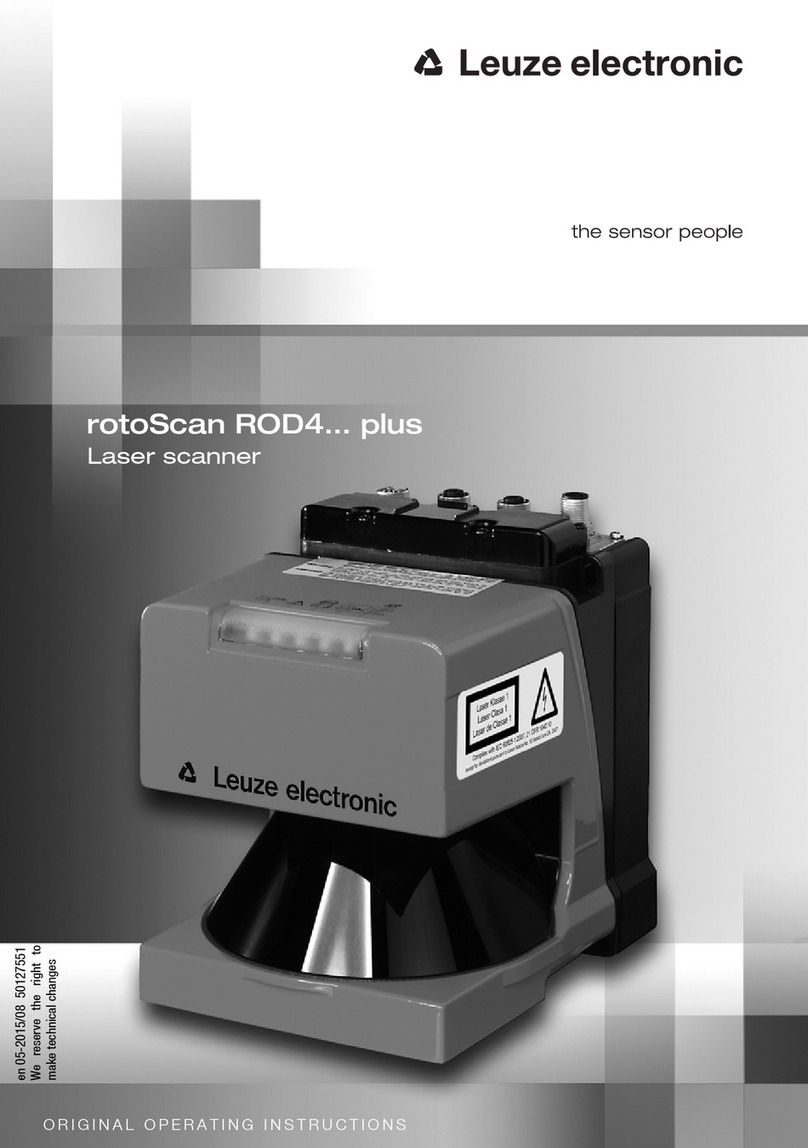
Leuze electronic
Leuze electronic rotoScan ROD4 plus Series Original operating instructions
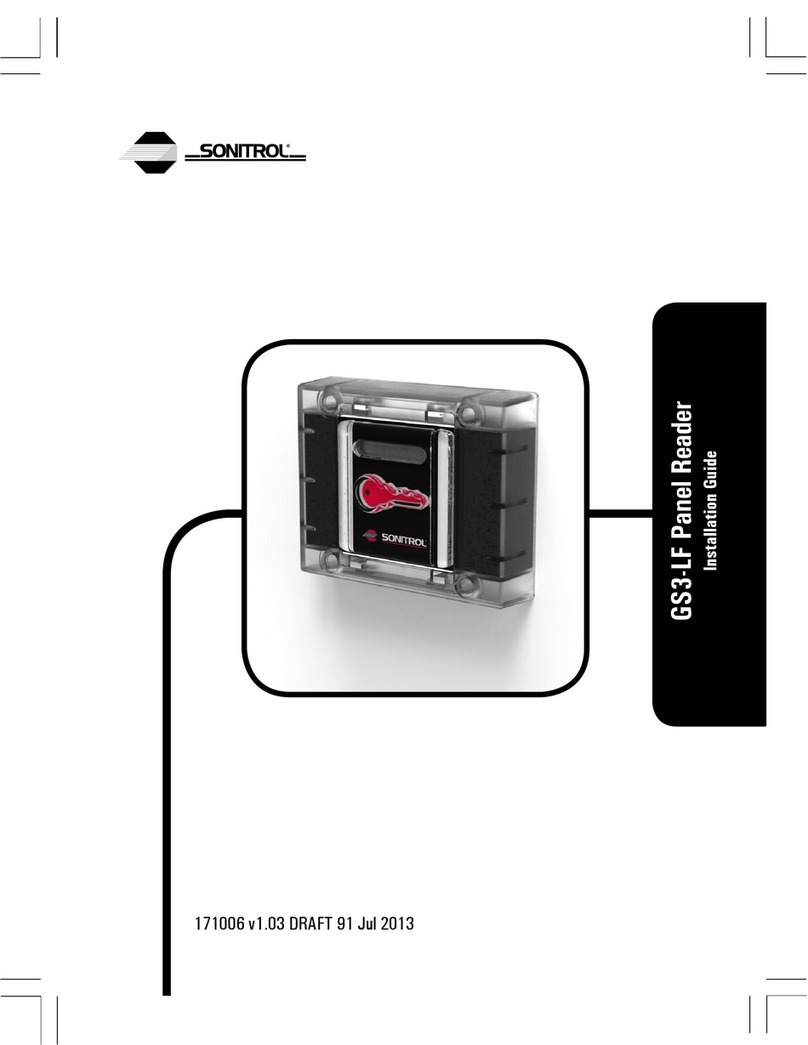
Sonitrol
Sonitrol GS3-LF installation guide
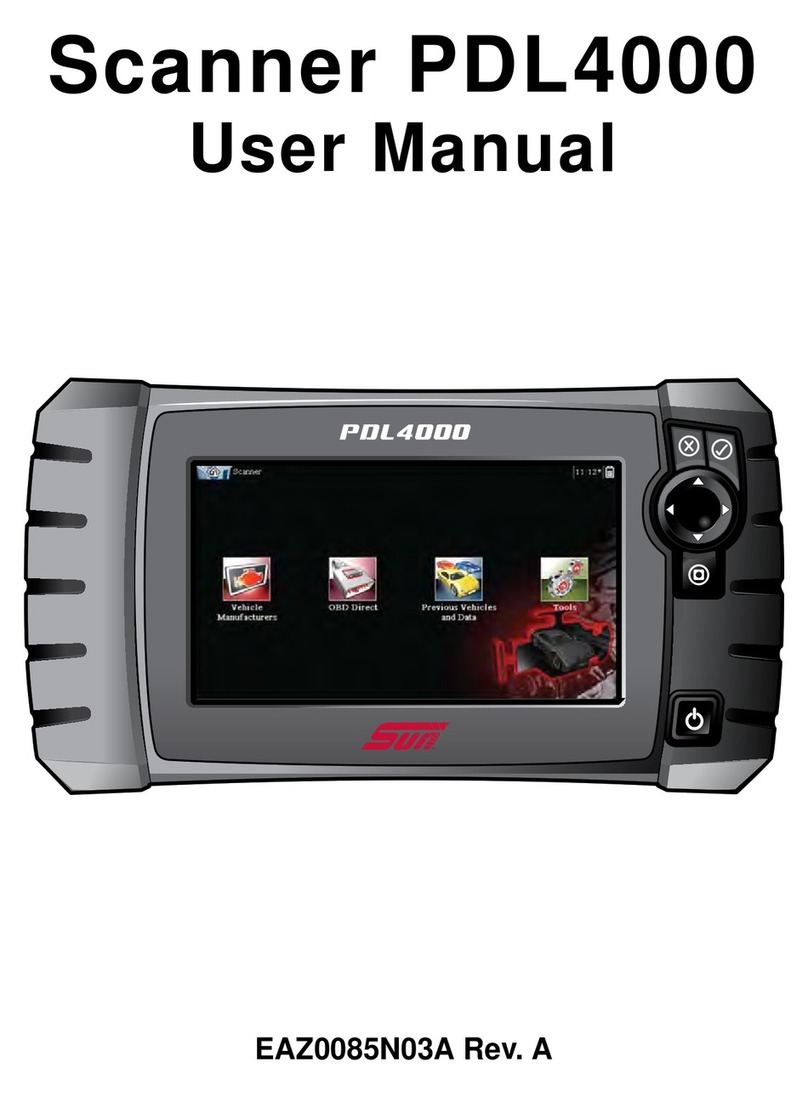
Sun Microsystems
Sun Microsystems PDL4000 user manual
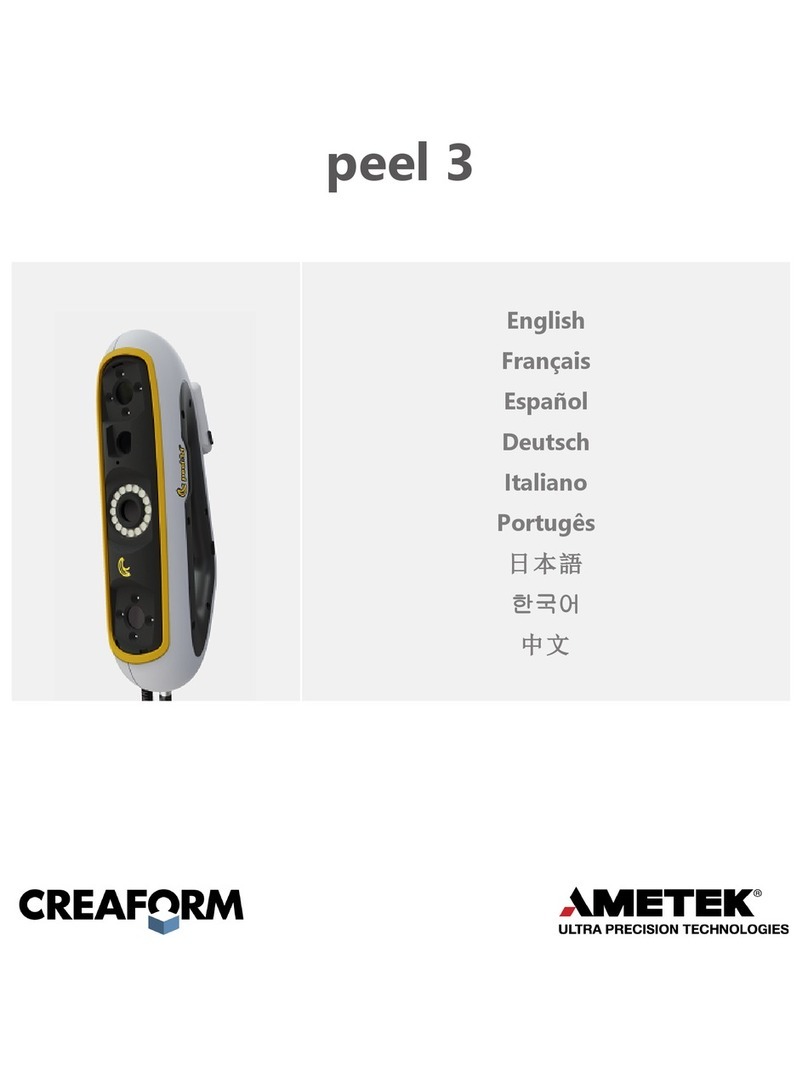
Ametek
Ametek CREAFORM peel 3 user manual