Edwards A50633000 User manual

A50633880
Issue C
Original Instructions
Instruction Manual
GXS Nitrogen Flow Switch Kit
Description Item Number
Nitrogen Flow Switch A50633000
Nitrogen Flow Switch - High Flow A50634000

This page has been intentionally left blank.
D of C to be inserted

© Edwards Limited 2020. All rights reserved. Page i
Edwards and the Edwards logo are trademarks of Edwards Limited.
Contents
A50633880 Issue C
Contents
Section Page
1 Introduction ....................................................................................... 1
1.1 Scope and definitions ................................................................................................... 1
1.2 Product description ...................................................................................................... 2
1.3 Construction .............................................................................................................. 2
2 Technical data .................................................................................... 3
2.1 Technical data ........................................................................................................... 3
3 Installation ......................................................................................... 5
3.1 Safety ...................................................................................................................... 5
3.2 Unpack and inspect ...................................................................................................... 5
3.3 Install the flow switch .................................................................................................. 6
3.4 Adjust the flow switch .................................................................................................. 8
4 Maintenance ....................................................................................... 9
4.1 General .................................................................................................................... 9
4.2 Clean the flow switch ................................................................................................... 9
5 Storage and disposal ........................................................................... 11
5.1 Storage ...................................................................................................................11
5.2 Disposal ...................................................................................................................11
Appendix A1 Tube fittings .............................................................................. 13
A1.1 Correct use of tube fittings ...........................................................................................13
A1.1.1 Connect a tube fitting .................................................................................................13
A1.1.2 Reconnect a tube fitting ...............................................................................................13
For return of equipment, complete the HS Forms at the end of this manual.
Illustrations
Figure Page
1 Flow switch kit general arrangement ................................................................................. 7
2 Flow switch kit electrical connection ................................................................................ 8
A1 Connect a tube fitting .................................................................................................14
A2 Reconnect a tube fitting ...............................................................................................14
Tables
Table Page
1 Flow switch parts list ................................................................................................... 6
dcs/7710/08/15

This page has been intentionally left blank.
A50633880 Issue C
Page ii © Edwards Limited 2020. All rights reserved.
Edwards and the Edwards logo are trademarks of Edwards Limited.

© Edwards Limited 2020. All rights reserved. Page 1
Edwards and the Edwards logo are trademarks of Edwards Limited.
Introduction
A50633880 Issue C
1 Introduction
1.1 Scope and definitions
This manual provides installation, operation and maintenance instructions for the Edwards GXS Dry Pumping System
Nitrogen Flow Switch, abbreviated to Flow Switch in the remainder of this manual. Use the Flow Switch as specified
in this manual. Use this manual in conjunction with the GXS pump manual.
Read this manual before you install and operate the Flow Switch. Important safety information is highlighted as
WARNING and CAUTION instructions; you must obey these instructions. The use of WARNINGS and CAUTIONS is defined
below.
CAUTION
Cautions are given where failure to observe the instruction could result in damage to the equipment, associated
equipment and process.
The abbreviation slm used in this manual refers to a standard litre per minute, i.e. a flow of one litre per minute
under standard conditions of 1 atm pressure at 0°C.
Notes: 1. The content of this manual may change from time to time with out notice. Edwards accepts no liability
for any errors that may appear in this manual nor does it make any expressed or implied warranties
regarding the content. So far as is reasonably practicable Edwards has ensured that its products have
been designed and constructed so as to be safe and with out risks when properly installed and used in
accordance with Edwards operating instructions. Edwards accepts no liability for loss of profit, loss of
market or any other indirect or consequential loss whatsoever.
2. Product warranty and limit of liability are dealt with in Edwards standard terms and conditions of sale
or negotiated contract under which this document is supplied.
WARNING
Warnings are given where failure to observe the instruction could result in injury or death to
people.

A50633880 Issue C
Page 2 © Edwards Limited 2020. All rights reserved.
Edwards and the Edwards logo are trademarks of Edwards Limited.
Introduction
1.2 Product description
The Flow Switch is designed to be externally fitted to an Edwards GXS dry pumping system and connected internally
to the gas module loom.
When installed, the Flow Switch enables the system to monitor the flow of nitrogen purge gas to the dry pumping
system, and to indicate a no-flow condition.
The flow switch is normally open. The presence of a flow of gas, above an adjustable set point, closes the switch.
The actual flow at the switching point depends on the gas supply pressure. For these reasons, the Flow Switch is
suitable for indicating that there is no nitrogen purge flow to the pump system, but it is not suitable for detecting
an abnormally low purge flow.
The flow switch is intended to be used in combination with Edwards suppled flowmeter only. If a flowmeter is not
fitted use either flow monitor 0-60 SLM (A60027043) or flow monitor 0-200 SLM (A60027044) before installing the flow
switch.
1.3 Construction
Refer to Figure 1.
The Flow Switch kit is comprised of:
Flow Switch assembly.
Bracket.
Pipe.
Y cable.
WARNING
This flow switch is designed for use with nitrogen purge gas. However, as an alternative, CDA
(Compressed Dry Air) can be used. It is the user’s responsibility to ensure the selected purge gas
is compatible and safe to use with their process.
WARNING
The Flow Switch is not considered a high integrity safety device by Edwards. For processes where
high dilution flows are required to maintain safety, an appropriate device should be fitted.

© Edwards Limited 2020. All rights reserved. Page 3
Edwards and the Edwards logo are trademarks of Edwards Limited.
Technical data
A50633880 Issue C
2 Technical data
2.1 Technical data
Mass 1.5 kg
Switching voltage 24 V d.c.
Contact rating 50 W(DC)
Maximum switching current 1.0 A(DC)
Accuracy ± 1%
Ambient operating temperature range 5 to 40°C
Maximum ambient operating humidity 90% RH (non condensing)
Maximum working pressure 6.9 bar (100 psig)
Electrical connector type Molex 6W Micro Fit 3.0 Connector

A50633880 Issue C
Page 4 © Edwards Limited 2020. All rights reserved.
Edwards and the Edwards logo are trademarks of Edwards Limited.
This page has been intentionally left blank.

© Edwards Limited 2020. All rights reserved. Page 5
Edwards and the Edwards logo are trademarks of Edwards Limited.
Installation
A50633880 Issue C
3 Installation
3.1 Safety
A suitably trained and supervised technician must install the Flow Switch.
Purge and shut down the dry pumping system and disconnect the nitrogen supply before you start
installation.
Disconnect the dry pumping system and the other components in the process system from the electrical
supply so that they cannot be operated accidentally.
If the dry pump system is operating, shut it down and allow it to cool to a safe temperature before you start
installation.
Do not allow debris to get into the Flow Switch system during installation.
Strong magnetic fields may affect the operation of the Flow Switch. Do not locate equipment which
generates strong magnetic fields close to the Flow Switch and do not route electrical supply cables close to
the Flow Switch.
Leak test the system after installation is complete and seal any leaks found to prevent further leakage.
Leakage rate must be less than 1 x 10-5 mbar ls-1.
Ensure that you connect, disconnect and tighten all tube connection components correctly (Refer to
Figure A1 and A2).
Obey all national and local rules and safety regulations when you install the Flow Switch.
3.2 Unpack and inspect
Remove all packing materials and protective covers and inspect the Flow Switch. If it is damaged, notify your supplier
and the carrier in writing within three days; state the Item Number of the Flow Switch together with your order
number and your supplier’s invoice number. Retain all packing materials for inspection. Do not use the Flow Switch
if it is damaged.
If the Flow Switch is not to be used immediately, refit any protective packaging and store the Flow Switch in suitable
conditions, as described in Section 5.1.
Check that your package contains the items listed in Table 1. If any of these items are missing, notify your supplier
in writing within three days.
WARNING
Obey the safety instructions given below and take note of appropriate precautions. Failure to do
so can cause injury to personnel and/or damage to equipment.
WARNING
This flow switch must not be installed as a safety device. Refer to Section 1.2 for further
information.

A50633880 Issue C
Page 6 © Edwards Limited 2020. All rights reserved.
Edwards and the Edwards logo are trademarks of Edwards Limited.
Installation
3.3 Install the flow switch
Install the Flow Switch as shown in Figure 1.
Take note of the following points before starting installation:
Do not commence installation with the electrical power on.
Refer to instructions in Appendix A1 for assembly of all compression type fittings.
Refer to Figure 1 for the flow switch assembly components.
Check for electrical continuity in the electrical line from the Flow Switch back to the gas module loom.
Leak check the installation. Leakage rate must be less than 1 x 10-5 mbar ls-1
For electrical connection, refer to Figure 2.
Using the PDT, configure the pump set-up to show the switch as fitted.
Setup> scroll to ‘Fit Accessory’> enter password (538)
Scroll to ‘N2 flow sensor’> select FITTED> Enter.
Confirm operation of switch by reducing purge flow to ensure warning (‘Warning 34.01 N2 purge low’) is displayed
on PDT.
Table 1 - Flow switch parts list
Quantity Description Check ()
1 Pipe
2 Male connector
2 6-32 UNC x 3/8 inch screw
2 M4 flat washer
2 M4 single coil washer
1 Flow Switch and bracket
1 Label
1 Isolation plate
1 Y cable

© Edwards Limited 2020. All rights reserved. Page 7
Edwards and the Edwards logo are trademarks of Edwards Limited.
Installation
A50633880 Issue C
Figure 1 - Flow switch kit general arrangement
Item No. Description Qty
1 N2 Flow Switch to Rotameter Pipe 1
2 N2 Flow Switch Assy 1
3 Open Grommet 1
4 M5 Securing Screws 2
A - Molex plug and cable to be fed through the bulkhead at location A and the open grommet secured into
bulkhead. The pressure switch cable may already be in the same hole, if so, the grommet can be removed and
both cables use the same hole. The connector and cable should be fed along the rear of the bulkhead and
connected into the 6 way socket on the supplied Y cable. Use the second 6 way socket to connect the pressure
switch cable and then connect the 6 way plug to the gas module loom. If the pressure switch is not used on the
system connect the flow switch cable directly to the gas module loom.

A50633880 Issue C
Page 8 © Edwards Limited 2020. All rights reserved.
Edwards and the Edwards logo are trademarks of Edwards Limited.
Installation
Figure 2 - Flow switch kit electrical connection
3.4 Adjust the flow switch
The Flow Switch must be adjusted so that it operates at the correct nitrogen flow rate for your process. The flow
switch output will open when the flow rate of nitrogen into the dry pumping system is too low. The Flow Switch
output will reset automatically (that is, close) when the flow rate of purge nitrogen into the dry pumping system is
acceptable.
1. Isolate the inlet of the pumping system from your vacuum system.
2. Ensure that there is a normal flow of purge nitrogen into the pumping system: refer to the pumping system
instruction manual.
3. Reduce the nitrogen flow until the total purge nitrogen flow rate reaches the minimum flow rate for your
process. It is recommended that you reduce the nitrogen supply pressure to below 35 psig to do this.
4. The GXS gas module requires a minimum of 35 psig nitrogen supply pressure for correct flow measurement. If
the nitrogen supply pressure falls below 35 psig the gas module will continue to provide flow measurements until
the supply pressure is insufficient to enable the gas module flow meter to function correctly. If this happens the
flow measurement defaults to zero slm. The actual flow will however continue to fall in proportion to the drop
in supply pressure. For this reason it is recommended that an independent flow measurement device is used to
measure the flow rate if a flow rate below which the module can measure it being set.
5. Refer to Figure 1. With the nitrogen supply pressure reduced to provide your preferred minimum flow rate use a
flat-blade screwdriver to turn the adjuster (14) until the Flow Switch operates.
6. Return the nitrogen supply to normal pressure and flow rate. Check that the Flow Switch has reset correctly.
7. The maximum switching flow of the GXS nitrogen Flow Switch A506-33-000 is 70-80 slm. At flows above this the
switch will be continually closed regardless of switch adjustment, provided the supply pressure is above 35 psig.
8. Nitrogen flow switch A506-34-000 is suitable for use at flows up to 204 slm.

© Edwards Limited 2020. All rights reserved. Page 9
Edwards and the Edwards logo are trademarks of Edwards Limited.
Maintenance
A50633880 Issue C
4 Maintenance
4.1 General
Carry out the following checks when maintaining the dry pumping system:
Check that the switch enclosure is securely fitted to the Flow Switch. If necessary, tighten the screws which
secure the switch enclosure to the Flow Switch.
Check that the bracket is securely fitted to the switch enclosure and is correctly located and attached to the
accessories mount plate. If necessary, tighten the screws which secure the bracket to the switch enclosure
and accessories mount plate.
Check that the nitrogen fittings are secure. Tighten any loose connections.
Check that the nitrogen pipes and fittings are not damaged or corroded. Repair or replace any damaged or
corroded component.
Regularly clean the Flow Switch: refer to Section 4.2.
4.2 Clean the flow switch
A suitably trained technician must clean the Flow Switch.
1. Remove the Flow Switch assembly.
2. Refer to Figure 1. Undo and remove the plug (5).
3. Use a small magnet to remove the piston from the Flow Switch; take note of the orientation of the piston as you
remove it.
4. Turn on the nitrogen supply to flush any dust from the Flow Switch, then turn off the nitrogen supply.
5. Thoroughly clean the piston; if necessary, use a suitable cleaning solution.
6. Refit the piston in the Flow Switch: ensure that the piston is in the same orientation as noted in Step 3.
7. Check and clean the O-ring which seals the plug. Slide the O-ring over the thread on the plug.
8. Refit and tighten the plug (5).
9. Refit the Flow Switch then leak check the Flow Switch on completion of installation. Leakage rate must be less
than 1 x 10-5 mbar ls-1.
WARNING
Prevent and ejected matter from entering the eyes. Use of eye protection (face shield, goggles or
glasses) is recommended.

A50633880 Issue C
Page 10 © Edwards Limited 2020. All rights reserved.
Edwards and the Edwards logo are trademarks of Edwards Limited.
This page has been intentionally left blank.

© Edwards Limited 2020. All rights reserved. Page 11
Edwards and the Edwards logo are trademarks of Edwards Limited.
Storage and disposal
A50633880 Issue C
5 Storage and disposal
5.1 Storage
If the Flow Switch is not used immediately, refit any protective packaging and store in cool, dry conditions until
required. When required for use, install the kit as described in Section 3.3.
5.2 Disposal
Dispose of the Flow Switch and any components in accordance with all local and national safety and environmental
requirements.

A50633880 Issue C
Page 12 © Edwards Limited 2020. All rights reserved.
Edwards and the Edwards logo are trademarks of Edwards Limited.
This page has been intentionally left blank.

© Edwards Limited 2020. All rights reserved. Page 13
Edwards and the Edwards logo are trademarks of Edwards Limited.
Appendix A1
A50633880 Issue C
Appendix A1 Tube fittings
A1.1 Correct use of tube fittings
Note: It is recommended that a second spanner is used to hold the connector in position when connecting or
disconnecting a tube fitting.
You must know how to correctly fit and tighten tube fittings in order to prevent gas leaks; use the procedures in the
following sections.
A1.1.1 Connect a tube fitting
1. Refer to Figure A1 detail A. Undo and remove the nut (4) from the tube fitting (1). Ensure that the front
(tapered) ferrule (2) and the rear ferrule (3) are correctly oriented as shown in detail A, then loosely refit the
nut (4) to the tube fitting (1).
2. Refer to detail B. Insert the tube (5) through the nut (4) and into the tube fitting (1). Ensure that the tube rests
firmly on the shoulder inside the fitting, and that the nut (4) is finger tight.
3. Tighten the nut (4) until you cannot rotate the tube (5). If the tube cannot be turned because of the way it is
installed, tighten the nut by 1/8 th of a turn.
4. Refer to detail C. Mark the nut (4) at the six o’clock position.
5. Refer to detail D. Hold the body of the connector steady, then turn the nut (4) by 1 ¼ turns (to the nine o’clock
position) to fully tighten the connection.
A1.1.2 Reconnect a tube fitting
A tube fitting can be disconnected and reconnected many times whilst still maintaining a correct leak-proof seal.
Refer to Figure A2 detail A which shows a tube fitting after it has been disconnected. Use the following procedure to
reconnect it:
1. Refer to detail B. Insert the tube (5) with the swaged ferrules (2, 3) into the tube fitting (1), until the front
ferrule (2) is fully in the body of the fitting.
2. Refer to detail C. Tighten the nut (4) by hand.
3. Use a wrench or spanner to turn the nut (4) to its original position (an increase in resistance will be felt when
the nut is in its original position), then tighten the nut slightly.

A50633880 Issue C
Page 14 © Edwards Limited 2020. All rights reserved.
Edwards and the Edwards logo are trademarks of Edwards Limited.
Appendix A1
Figure A1 - Connect a tube fitting
Figure A2 - Reconnect a tube fitting
1. Tube fitting
2. Front (tapered) ferrule
3. Rear ferrule
4. Nut
5. Tube
1. Tube fitting
2. Front (tapered) ferrule
3. Rear ferrule
4. Nut
5. Tube
This manual suits for next models
1
Table of contents
Other Edwards Switch manuals
Popular Switch manuals by other brands

Shinybow USA
Shinybow USA SB-5669K instruction manual
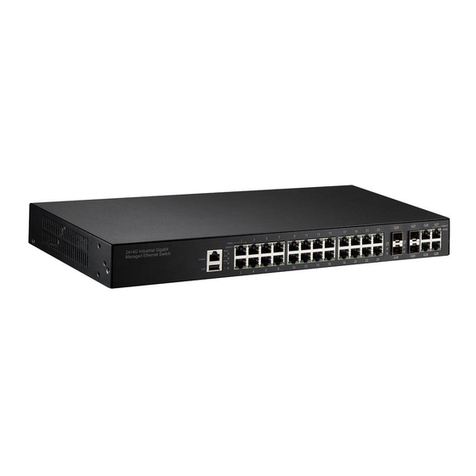
Korenix
Korenix JetNet 5428G Series user manual
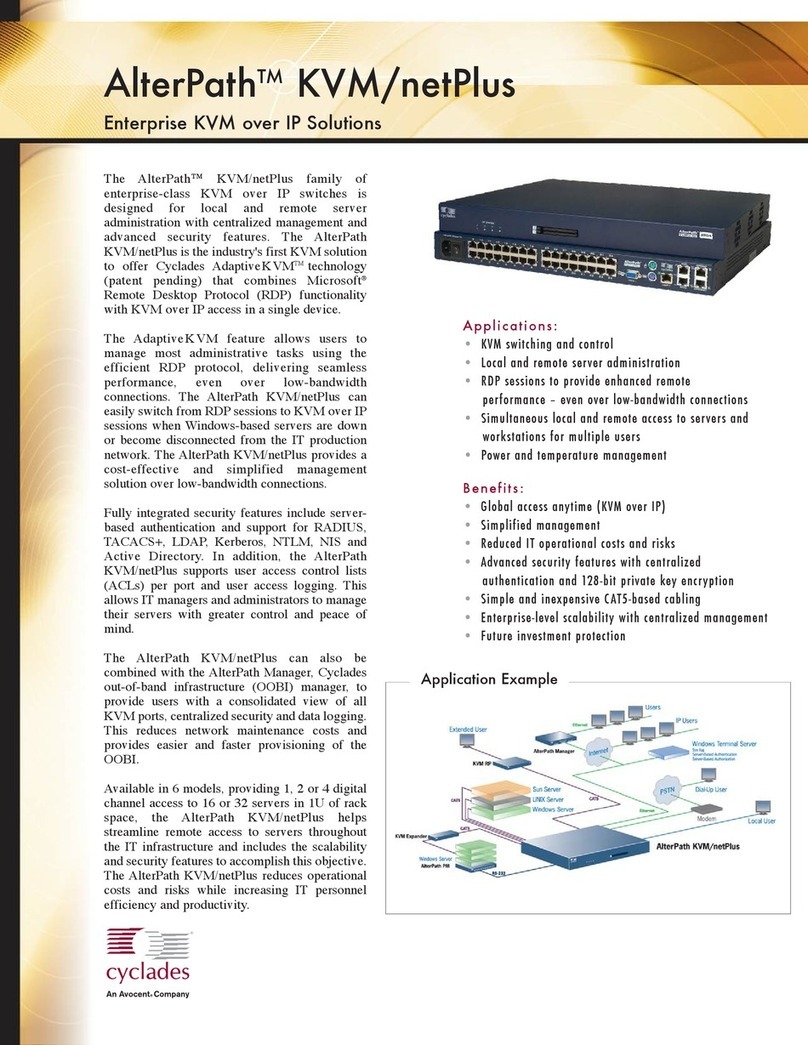
Cyclades
Cyclades AlterPath KVM/netPlus KVM Switch Specifications
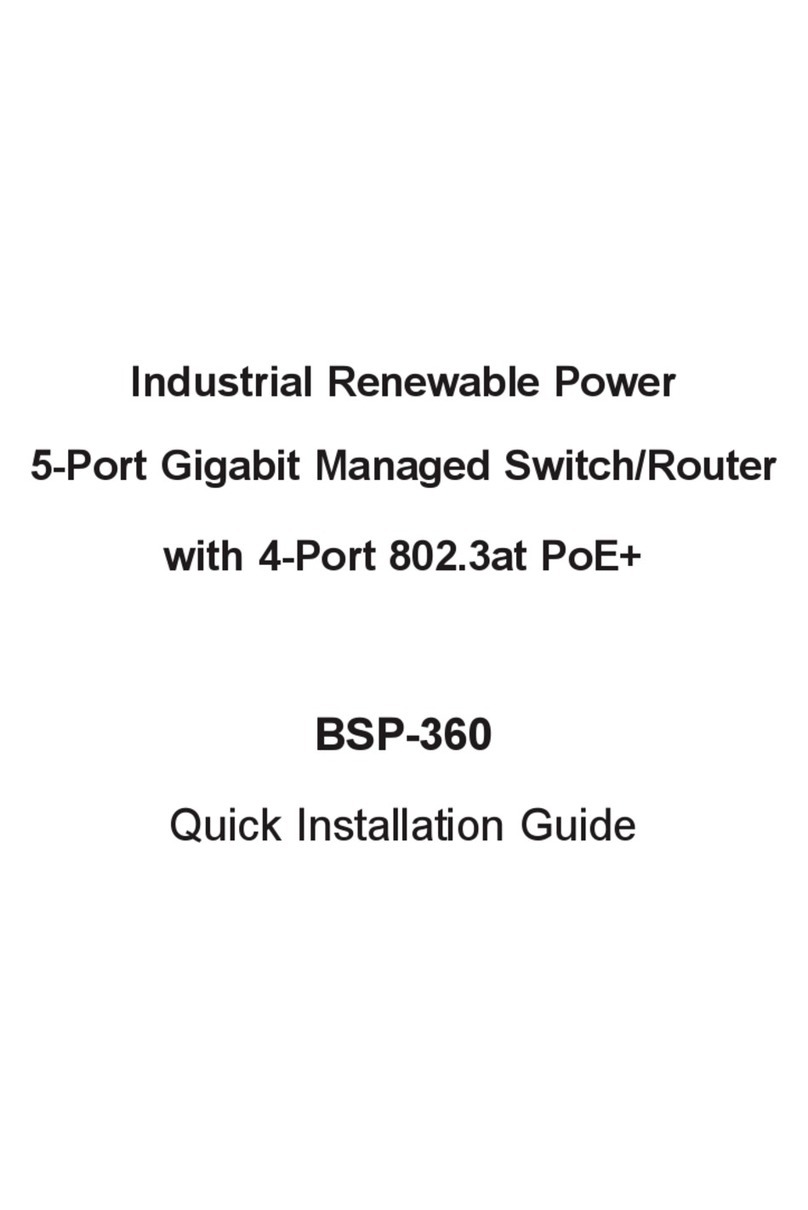
Planet Networking & Communication
Planet Networking & Communication BSP-360 Quick installation guide
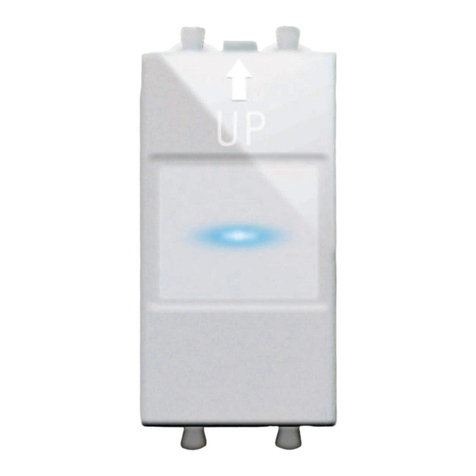
AVE
AVE 442TC01 quick start guide
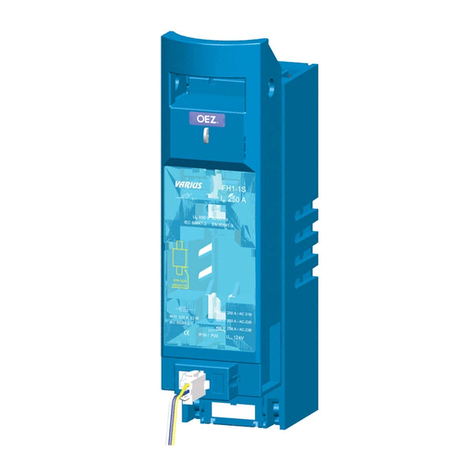
OEZ
OEZ FH1-1 Series Instructions for use
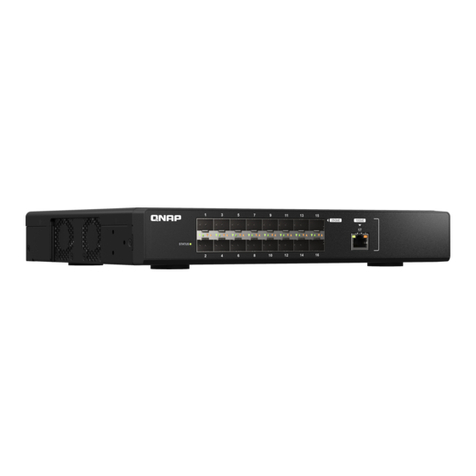
QNAP
QNAP QSW-M5216-1T Quick installation guide
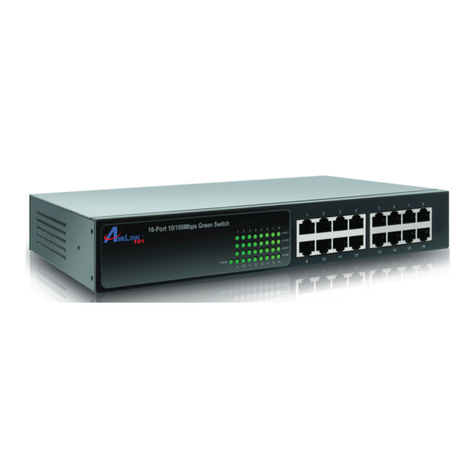
Airlink101
Airlink101 ASW316V2 Quick installation guide

Digitus
Digitus DN-95347-1 Quick installation guide
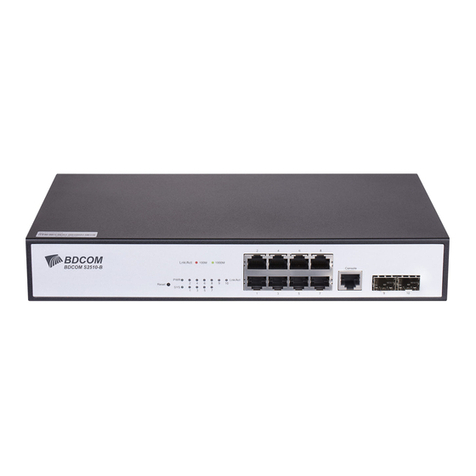
Bdcom
Bdcom S2510-B Hardware installation manual
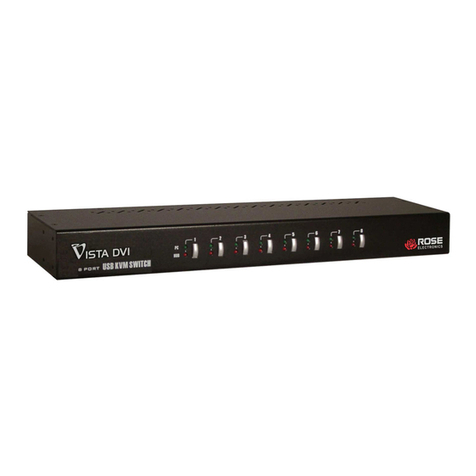
Rose electronics
Rose electronics VISTA DVI quick start guide
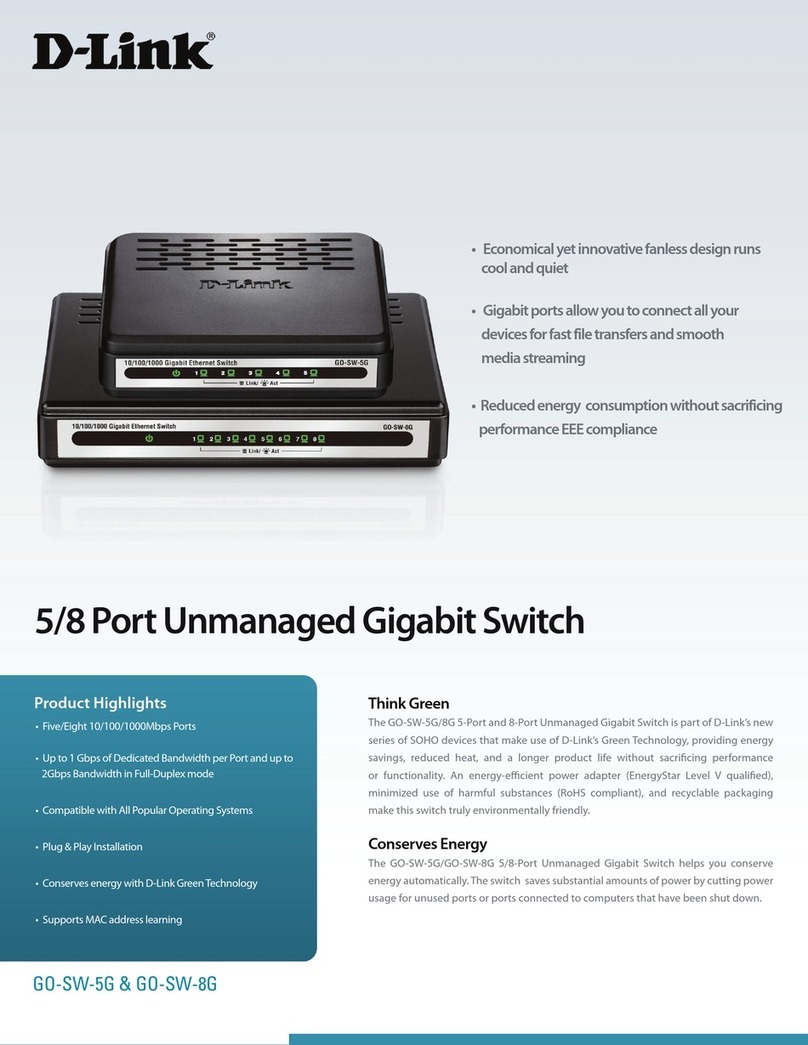
D-Link
D-Link GO-SW-8G Technical specifications