EKE-Electronics CVB1621A User manual

EKE-Trainnet®
CVB1621A and CVB2456A
CAN Vehicle Bus Module
Technical Manual

EKE-Electronics Ltd.
Piispanportti 7, FIN-02240 Espoo, FINLAND
Tel. +358 9 6130 3308
Fax +358 9 6130 3300
e-mail: electronic[email protected]om
Marketing and sales
e-mail: electronic[email protected]om
TMS implementations, passenger train functions and
IEC 61131-3 type application programming
e-mail: electronic[email protected]om
Reports, testing and problem analysis
e-mail: suppor[email protected]m
The most recent information on EKE Electronics’ products and services is available at www.eke.com.
Under copyright law no part of this document may be copied, reproduced or transferred electrically or manually, not even
partly, without prior written permission of EKE-Electronics Ltd. This document is subject to change without notice.
EKE-Trainnet®is a registered trademark of EKE-Electronics Ltd.
Copyright © 2009 EKE-Electronics Ltd. All rights reserved.
EKE-Trainnet® CVB CAN Vehicle Bus Module Technical Manual, version 3.00

Contents
1: General Information ...................................................................................................... 1
1.1 About this chapter ..................................................................................................... 1
1.2 Warning symbols used in this manual ....................................................................... 2
1.3 Safety considerations ................................................................................................ 3
1.4 Correct handling of the module ................................................................................. 3
1.5 Disposal of the CVB module ..................................................................................... 4
2: Overview of the CVB..................................................................................................... 5
2.1 CVB module composition and features ..................................................................... 5
2.2 CVB configuration ..................................................................................................... 7
2.2.1 Functional description ........................................................................................ 7
2.3 Selected specifications ............................................................................................. 8
2.4 Module identification and modification information ................................................... 9
3: Installing the CVB into a rack..................................................................................... 11
3.1 Before you begin ..................................................................................................... 11
3.1.1 Warnings.......................................................................................................... 11
3.1.2 Preparations..................................................................................................... 12
3.2 Installation procedure .............................................................................................. 12
3.2.1 Placing the module in the rack......................................................................... 12
3.2.2 Checking the module ....................................................................................... 13
3.3 Firmware loading ..................................................................................................... 14
3.4 Problems in installation ........................................................................................... 15
4: Troubleshooting.......................................................................................................... 17
4.1 Before you begin ..................................................................................................... 17
4.1.1 Warnings.......................................................................................................... 17
4.1.2 Preparations..................................................................................................... 18
4.2 Getting started with troubleshooting ........................................................................ 18
4.3 LED Diagnostics ...................................................................................................... 19
4.4 Power up self tests .................................................................................................. 20
4.4.1 Automatic self-tests.......................................................................................... 21
4.5 Communication errors ............................................................................................. 22
4.5.1 Missing configuration ....................................................................................... 22
4.5.2 Defective module ............................................................................................. 23
4.5.3 Physical defect in connectors .......................................................................... 23
4.5.4 Wrong connection or a loop connection or missing termination ...................... 23
4.5.5 Missing or defective device.............................................................................. 23
4.5.6 Low signal level or missing signal.................................................................... 23
4.5.7 Missing or inappropriate termination................................................................ 25

5: Command line interface.............................................................................................. 27
5.1 Getting started ......................................................................................................... 27
5.2 Finding the command you need .............................................................................. 27
5.3 HELP command ...................................................................................................... 29
5.4 Debugging commands ............................................................................................ 29
5.4.1 CHECK_LINE (D)- Checking line..................................................................... 29
5.4.2 CANSTAT- CAN Statistics ............................................................................... 30
5.4.3 IN - Input .......................................................................................................... 33
5.4.4 OUT (D)- Output .............................................................................................. 37
5.5 Memory commands ................................................................................................. 38
5.5.1 ADDR - Addressing mode................................................................................ 38
5.5.2 RM - Read Memory.......................................................................................... 40
5.5.3 SM - Set Memory (D) ...................................................................................... 41
5.6 Software development commands .......................................................................... 42
5.6.1 CANINIT (D)..................................................................................................... 42
5.6.2 CANSEND (D) ................................................................................................. 43
5.6.3 RESET (D) ....................................................................................................... 43
5.6.4 VER.................................................................................................................. 44
Appendix A: Technical Specifications .......................................................................... 47
Mechanical specifications ............................................................................................. 47
Pin order and connector specifications ......................................................................... 48
Non-metallic parts ......................................................................................................... 51
Electrical specifications ................................................................................................. 51
Reliability specifications ................................................................................................ 51
Compliance with standards ........................................................................................... 52
Environmental and EMC test specifications .................................................................. 52
Cable recommendations ............................................................................................... 53
Appendix B: Diagrams .................................................................................................... 55
Layout diagrams ............................................................................................................ 55
Schematic diagram ....................................................................................................... 57
Eke-Electronics Ltd. pursues a policy of continual product development. Although
every effort is made to produce up-to-date product documentation this publication
should not be regarded as an infallible guide to current specifications. We reserve the
right to make changes without prior notice.
COPYRIGHT EKE-ELECTRONICS LTD. 2009-12
VERSION NUMBER 3.00

1
CVB1621A and CVB2456A Technical Manual, ver. 3.00
1: General Information
This is the Technical manual for the EKE-Trainnet®CVB1621A and CVB2456A
CAN Vehicle Bus module.
In this manual, the abbreviation CVB is used of the CVB1621A and
CVB2456A CAN Vehicle Bus module.
The abbreviation CAN bus is short for Control Area Network bus.
This manual contains following chapters:
Chapter 1: General Information
Chapter 2: Overview of the CVB module
Chapter 3: Installing the CVB module into a rack
Chapter 4: CVB module operations
Chapter 5: Troubleshooting
Appendix A: Technical Specifications
Appendix B: Diagrams
This manual does not include instructions for the installation or maintenance
of the rack or its components. For these instructions, refer to the
EKE-Trainnet® Rack Technical Manual, or the manual provided by your rack
manufacturer.
Also this manual does not include information on other EKE-Trainnet®
products. If you need to check other modules during troubleshooting, refer to
the manual of the corresponding module.
1.1 About this chapter
This chapter includes general information about the CVB module.
The following topics are covered in this chapter:
Symbols used in this manual
Safety considerations
Correct handling of this module
Disposal of the module

General Information
2CVB1621A and CVB2456A Technical Manual, ver. 3.00
1.2 Warning symbols used in this manual
In this manual, situations that require caution are marked with special warning symbols.
The warning symbols appear in the beginning of the appropriate chapter. The following
symbols are used.
Figure 1.1: Electric shock warning symbol
Figure 1.2: General caution symbol
Figure 1.3: ESD warning symbol
Figure 1.4: Note symbol
Figure 1.5: Separate collection for Waste Electrical and Electronic Equipment according to
Directive 2002/96/EC (WEEE)

General Information
3
CVB1621A and CVB2456A Technical Manual, ver. 3.00
1.3 Safety considerations
The CVB module is a low voltage device. In a normal situation, it presents no safety
risk to the user. However, in case of a severe train malfunction or wiring errors, there
is a risk of an electric shock through the bus cables.
However, in case of a severe train malfunction or wiring errors, there is a
risk of an electric shock through the bus cables.
The CVB module and also the rack can contain sharp edges. Use
protective clothing (gloves etc.).
When you install / remove and handle a module, always hold it by the front
panel or the sides. Do not touch the components.
HOT! In a warm environment, some components may become very hot.
This does not harm the module but it could harm you. Touching these
components may cause burning of skin. Carefully hold the module by the
front panel or sides and DO NOT TOUCH ANY COMPONENTS.
Never disconnect the CVB module from a rack with active power, as this
can damage the CVB module or other modules in the system.
1.4 Correct handling of the module
Electrostatic discharge (ESD) can damage electronic circuits. The EKE-Trainnet®
products are protected against ESD. However, you run the risk of delivering
electrostatic discharges to the module whenever you handle it or any of its
components. To avoid this risk, handle the CPS module only at a static-free
workstation. If this is not possible, you must ground yourself using a wrist strap and a
resistive connection cord.
Remember to handle the module according to these instructions even
when you are removing a defective module and sending it to maintenance.

General Information
4CVB1621A and CVB2456A Technical Manual, ver. 3.00
1.5 Disposal of the CVB module
In order to reduce the environmental load over the product’s entire life cycle,
EKE-Electronics’ products are designed to be as safe as possible to manufacture, use,
and dispose of.
Parts which can be recycled should always be taken to the appropriate processing
centres, after hazardous waste has been removed. All parts and components
containing hazardous materials must be disposed of in accordance with waste
legislation and instructions issued by the environmental authorities. The risks involved
and the necessary precautions must be taken into account when handling waste
products. Therefore, please execute proper processing of disposal in accordance with
local law.
Table 1.1: Disposal of CVB module, X = action, (X) = action in cases where processing is
available
Part Main materials of
disposal
Recyclable
materials
Waste disposal
site
Hazardous
waste (separate
collection)
Frame and
covers
Metal
Aluminium
Stainless steel
X
X
Plastic Polyurethane (PU/PUR)
Other plastics
X
X
Component
boards
(X)
Lead X
Packing Cardboard
Polyethylene (PE)
X
X

5
CVB1621A and CVB2456A Technical Manual, ver. 3.00
2: Overview of the CVB
This chapter lists selected specifications of the EKE-Trainnet®CVB module and
highlights some of its features.
The following topics are covered in this chapter:
CVB module composition and features
Selected specifications
Module identification
Module LEDs
2.1 CVB module composition and features
The CVB module is designed to ensure reliable data transmission on board a train.
The following sections present some CVB features intended for this purpose.The CVB
module is the provider of two interfaces (X1 and X2) to a CAN bus running a CAN
protocol. There is a connector in the front panel for each independent interface. The
implementation is realised with two CAN controller chips and a local microprocessor.
There are two models of the CVB module.The difference between the modules is
whether they have bus termination inside the module or they need external bus
termination.
Table 2.1: CVB module types
The application (ISaGRAF) in the CPU module supervises the gateway between the
CPU and the CVB module. There is a loadable executable running in the CPU module
through which the application is able to access the raw CAN data. The access can be
direct or through a higher level protocol – for instance CANopen. This makes it quick
and easy for the application to run CAN based protocols.
Module type Difference
CVB1621A Internal bus terminators
CVB2456A Needs external bus terminators

Overview of the CVB
6CVB1621A and CVB2456A Technical Manual, ver. 3.00
The Host CPU (enhanced Z180 microprocessor) combines a high-performance CPU
core with a variety of system and resources useful in a broad range of applications. The
CPU core consists of five functional blocks:
Clock generator, which generates the system clock from an external crystal or clock
input bus state controller
Bus State Controller, which performs all the status and bus-control activity
associated with CPU and some on-chip peripherals.
Interrupt controller, which monitors and prioritises the variety of internal and
external interrupts and traps to provide the correct responses from the CPU.
Memory Management Unit (MMU), which allows the user to map the memory used
by the CPU into the 1-MB addressing range supported by the Z180 CPU.
Central processing Unit (CPU) is microcopy to provide a core that is the object-code
compatible with the Z180 CPU
The integrated I/O resources make up the remaining four functional blocks:
Direct Memory Access controller (DMA, 2 channels), which provide
Programmable Reload Times (PRT), which consists of two separate channels,
each containing a 16-bit counter (timer) and count reload registers.
Asynchronous Serial Communication Interface (ASCI) which provide two
full-duplex UARTs. Each channel includes a programmable baud rate generator
and modem control signals.
Clock Serial I/O channel (CSI/O).
The two CAN Controllers (SJA 1000) for both CAN busses (A and B) have:
Reception and transmission of standard and extended frame format messages
Receive First In-First Out (FIFO, 64-byte) queue process technique
Error counter switch read/write access
Programmable error warning limit
Last error code register
Error interrupt for each CAN bus error
Single shot transmission (no re-transmission on error or arbitration lost)
Listen only mode (monitoring the CAN bus, no acknowledge, no error flags)

Overview of the CVB
7
CVB1621A and CVB2456A Technical Manual, ver. 3.00
2.2 CVB configuration
The CVB module configuration is done through the Gateway CPU, and the CVB reads
it through its shared memory at the start-up of the system.The configuration is for the
CVB module read-only, and only managed by the CPU software. If any changes are
made through the debug terminal, the original configuration is retained when the
module is reset.
2.2.1 Functional description
The module there is a Euro 1 size (160x100mm) circuit board which contains (Refer to
2.4 on page 9):
Power supply circuitry
Two (2) CAN bus interfaces
Download and Debug Terminal interface (X4 DLOAD)
Host CPU (Z180) processor
Two (2) CAN Controllers (SJA 1000)
VME Bus interface
The following figure presents a general diagram of the CVB module functionality. For
a more detailed block diagram, see Appendix B.
Figure 2.1: General functionality diagram of then CVB module
HOST CPU
(Z180)
Download/Debug
VME Bus
VME Bus Slave Logic
CAN Controller CAN Controller
(SJA 1000)
(SJA 1000)
CAN A CAN B
CAN BUS B
CAN BUS A
Bus interface (X1) Bus interface (X2)
Terminal interface
(X4 DLOAD)
Shared memory

Overview of the CVB
8CVB1621A and CVB2456A Technical Manual, ver. 3.00
2.3 Selected specifications
The EKE-Trainnet®CVB module is designed for train data transmission. It is an
interface between the VME Bus and devices attached to the CAN Bus.
This section lists some technical specifications of the CVB module. For complete
technical specifications refer to “Appendix A: Technical Specifications”.
Table 2.2: Selected Technical Specifications of the CVB module
Size of the printed circuit board 100 mm * 160 mm (Euro 1)
Width 4 TE
Height 3 U
Required free space in front of the module 75 mm
VME interface A24/D16
Operating temperature –40 — +70 °C
Reliability 500 000 h
calculated from component FIT data at
+40°C ambient temperature

Overview of the CVB
9
CVB1621A and CVB2456A Technical Manual, ver. 3.00
2.4 Module identification and modification
information
Version and modification information appears on the board. The following picture
shows you where to find the modification information.
Figure 2.2: Location of version and modification information on the board
The modification label shows the module modification. It is located above the back
connector of the module. The label includes letters, and the modification is indicated by
crossing out one. If nothing is crossed out, the modification is 00. If the letter A is
crossed out, the modification is 01, and so on. This label gives the modification level of
the entire module, and the board has its own modification field, indicated by numbers.
The module test label indicates that the module has gone through the required testing
cycle. It is located on the back side of the front panel.
Board modification field
Module ID
Board serial number
Board test label
Board ID
Module serial number
Module modification label
X4 DLOAD interface
Channel A
Channel B

Overview of the CVB
10 CVB1621A and CVB2456A Technical Manual, ver. 3.00
The serial number identifies the module. It is found on the back side of the front panel.
The Module ID, located on the front panel handle, indicates an ID for this module. Again
note that the board has its own Board ID.
On the circuit board’s solder side the following labels are located (refer to 2.4
on page 9):
The circuit board may have a different modification level, indicated by numbers,
which are printed on the Board modification field.
The Board ID indicates an ID for the circuit board.
The circuit board has also its own serial number.
The Board test label indicates that the board has gone through the required testing
cycle.
In the error situation the module can be identified according to module ID,
serial number and the information found on the module modification label.

11
CVB1621A and CVB2456A Technical Manual, ver. 3.00
3: Installing the CVB into a
rack
This chapter includes instructions on how to install the EKE-Trainnet®CVB module into
a rack.
The following topics are covered in this chapter:
Before you begin
Installation procedure
Firmware loading
Problems in the installation
3.1 Before you begin
Read the following sections carefully before you start installing the CVB module.
3.1.1 Warnings
This section contains warnings you need to consider before and during the CVB
installation.
Do not turn on the rack power before you have finished the installation.
Never connect the CVB module to, or remove it from, a rack with active
power, as this can damage the CVB module or other modules in the
system. Always turn off the rack power first.
Electrostatic discharge can damage electronic circuits. Always handle the
module at a static free workstation. If this is not possible, ground yourself
using a wrist strap and a resistive connection cord.

Installing the CVB into a rack
12 CVB1621A and CVB2456A Technical Manual, ver. 3.00
When handling the module, only touch the front panel. Do not touch the
board or any of the components on it.
Do not drop the module.
Make sure that the module or any of the components on it do not get wet.
Even when you are removing a defective module and sending it to
maintenance, handle the module according to these instructions.
3.1.2 Preparations
Before you start installing the CVB module into a rack, make the following preparations.
Make sure you have a Pozidrive Pz0 or Pz1 screwdriver to tighten the screws on
the module.
Check the shipping container to see that it is not damaged.
Take the module out of its shipping container carefully. The module is always
shipped in an ESD protective wrapping.
Check the module, especially the connector on the back, for any visible signs of
damage that may have occurred during shipment.
3.2 Installation procedure
The following sections include instructions for installing the CVB module into a rack.
3.2.1 Placing the module in the rack
The first step in the CVB installation is placing it in the rack. Do the following:
1Hold the module by the front plate.
2Place the module on the rails of the rack.
3Slide the module towards the back plane of the rack until it clicks into its place. Do
not use force.
4Tighten the two screws on the front panel.
5If there are other modules in the rack, make sure that the front plate of the CVB
module is at the same level with the other modules.
If the module does not fit into its place in the rack, see section 3.3 on page 14.

Installing the CVB into a rack
13
CVB1621A and CVB2456A Technical Manual, ver. 3.00
The following picture shows a sample rack with modules successfully installed. The
modules in the picture are just an example, and the picture is intended as illustration
only.
Figure 3.1: Modules installed in a rack.
3.2.2 Checking the module
When you have successfully installed the module in the rack, the next step is to check
that the module works. The front panel of the CVB contains four LEDs: two green, one
red and one yellow. You can detect the status of the CVB module by looking at the
LEDs in the front panel.The module status LEDs are located on the right-hand side of
the CVB front panel.
Figure 3.2: Module status LEDs
The following table explains the indication of the LEDs.
Table 3.1: Indication of Module status LEDs System start progress and self-test failure
For detailed description about the LED functions and diagnostics, refer to 4.3: LED
Diagnostics on page 19.
LED Colour In normal
operation
Description
ST Green Lit Hardware status. The FPGA configuration is in normal state.
UB Green Lit or
blinking
Local activity on the CVB module. This means that the
module is transmitting data. The LED will be lit or blink during
a normal operation.
SE Red Unlit System error. Normal operation is prevented. Reset, power
failure or e.g. self-test in progress.
UE Yellow Unlit System start progress and self-test failure indication.
CVB module
UEUB

Installing the CVB into a rack
14 CVB1621A and CVB2456A Technical Manual, ver. 3.00
To check the module, do the following:
1Turn on the rack power.
2Check that the green ST LED is ON. Also, check that the red SE and yellow UE
LEDs are not ON. This means that the module is OK.
3If the red SE and yellow UE LED are constantly ON, the module is not OK. In such
a case, make sure you have placed the CVB module properly in the rack. If these
LEDs still remain on, turn off the rack power, loosen the screws on the module front
panel and pull the module carefully out of the rack.
During module start-up, the red SE LED is ON for a moment and then go
off. This is part of the normal start-up procedure and does not indicate an
error.
If the module is not OK refer to chapter 3.4 on page 15.
3.3 Firmware loading
It is possible to download the latest firmware using the USBFloader (X4 DLOAD).
Never install or remove modules to / from the rack with active power.
Always turn off the rack power first.
1Install the EKE USBFloader software if not already installed.
2Switch the power OFF and remove all other modules from the rack except for the
CVB and the PIU/PSV Power Supply Module.
3Connect a USB cable between your PC’s USB port and the EKE-Trainnet®USB
floader unit (UFI 1528).
4Connect the EKE-Trainnet® FAC 1027 cable between the USB floader unit and the
X4 Load and Debug connector (DLOAD) located on the circuit board of the module.
Refer to Figure 2.2: on page 9.
5Locate the file *.ufo (e.g. CVB_B015_P0000_000.ufo) with the Explorer and
double-click it. The loading will start and the loading progress window appears.
The program informs when the download has been executed successfully.

Installing the CVB into a rack
15
CVB1621A and CVB2456A Technical Manual, ver. 3.00
3.4 Problems in installation
The following table lists some potential problems that may occur during CVB
installation, as well as their causes, and actions you can take to solve the problem.
Table 3.2: Potential problems in the installation procedure
Problem Potential cause Action
The CVB does not fit into the
rack.
The connector pins of the
module are damaged.
Replace the module with a
spare one.
Connector pins are OK, but
the module does not fit into
the rack.
1.The back plane of the rack
or the connectors are faulty
(e.g. damaged) or
2. The rack (with the back
plane) cannot be used with
the CVB.
Examine the rack and the
connectors. If it is faulty or
incorrect then replace the
rack.
The module is installed into
the rack, but it is not working.
1.The input voltage is
incorrect or
2.The module is damaged.
Check the wiring, the cabling
and the train battery.
If the problem still exists
replace the module with a
spare one.

Installing the CVB into a rack
16 CVB1621A and CVB2456A Technical Manual, ver. 3.00
This manual suits for next models
1
Table of contents
Other EKE-Electronics Control Unit manuals
Popular Control Unit manuals by other brands
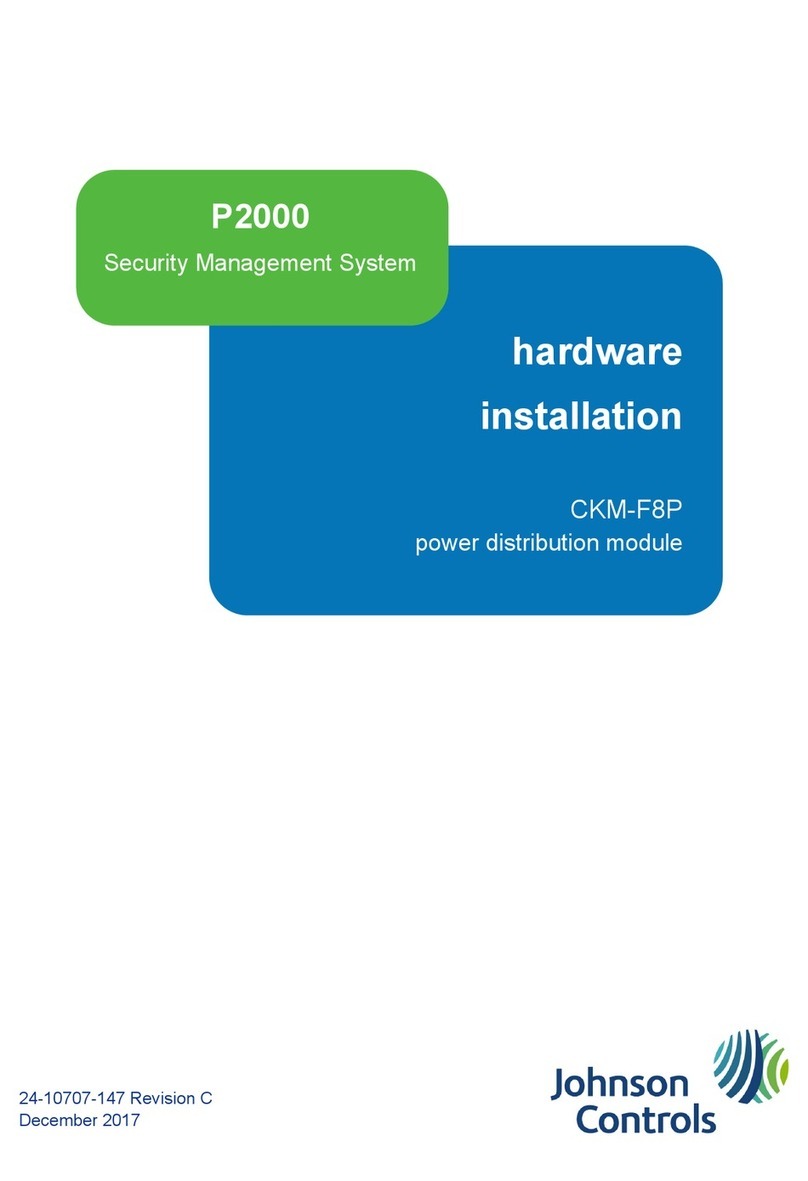
Johnson Controls
Johnson Controls CKM-F8P Hardware installation
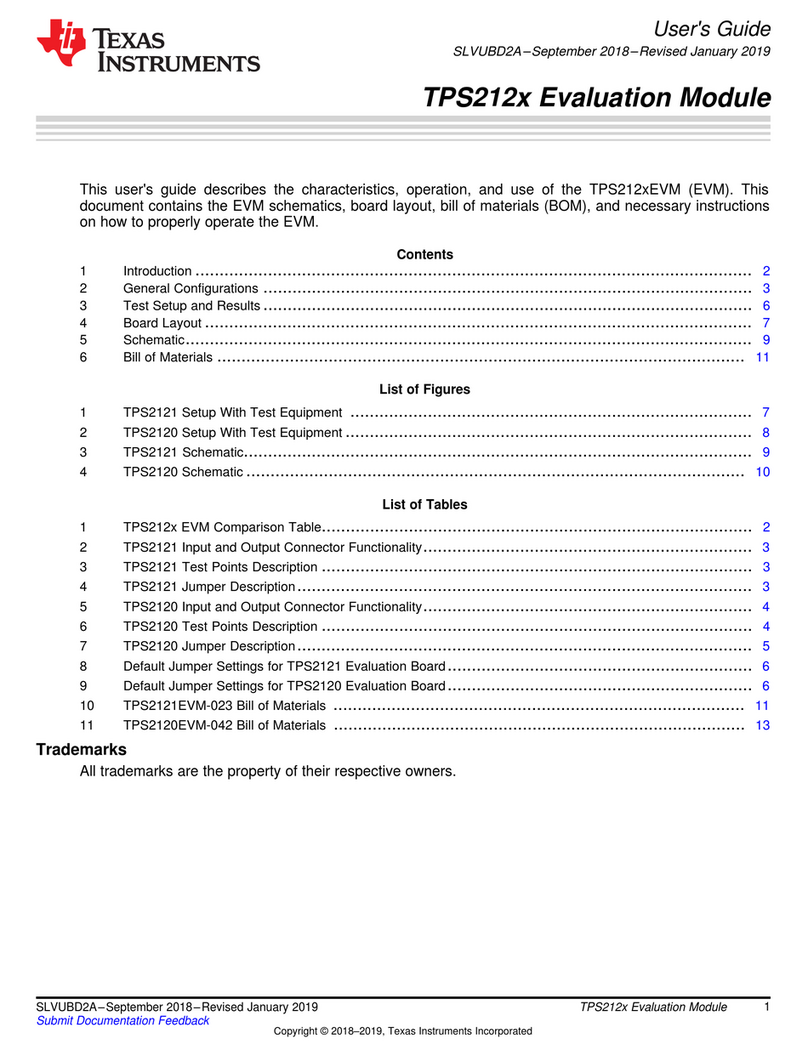
Texas Instruments
Texas Instruments TPS2121EVM user guide

SOMFY
SOMFY EOLIS Inteo Wind Control Installation and operating instructions
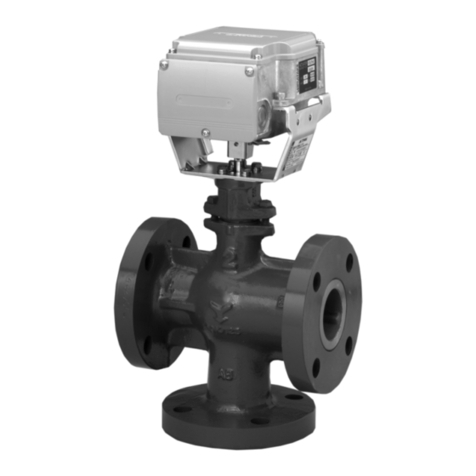
Azbil
Azbil ACTIVAL VY54X0F Series Specifications & instructions
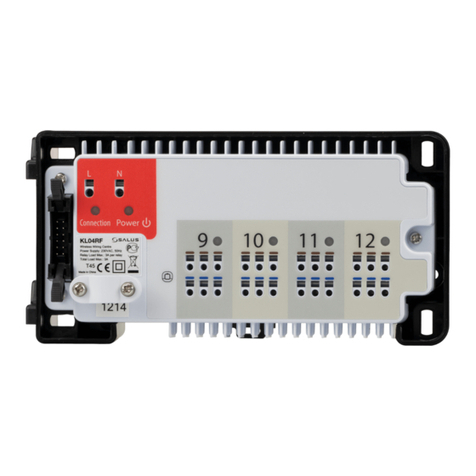
Salus
Salus KL04RF Installation and wiring guide
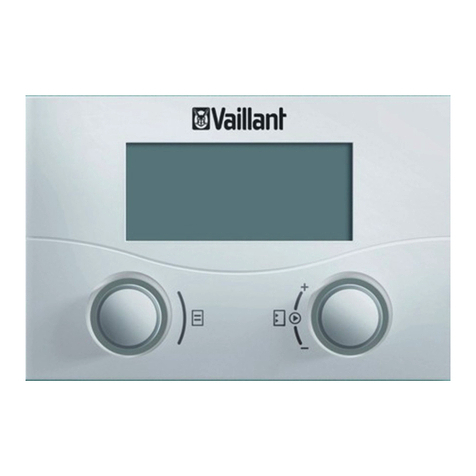
Vaillant
Vaillant VR 90 OPERATING AND INSTALLATION Manual