Elotech R 2000 - 431 User manual

Manual R2000-43-E Release: 1.03 © Elotech GmbH Page 1/24
R 2000 - 431 / 432 / 436 / 433 / 437
4 – Zones
„heat-only“ and „heating-off-cooling“ Temperature Controller
- Heater Current Monitoring (Option)
- CANopen - Interface (Option)
- 2 x Analog input 0-10VDC (Option)
Format: 96 x 96 mm (1/4-DIN)
Installation depth: 122 mm
DESCRIPTION AND OPERATING MANUAL
I.
ELOTECH Industrieelektronik GmbH
Verbindungsstrasse 27
D – 40723 HILDEN
FON +49 2103 / 255 97 0 FAX +49 2103 / 255 97 29

Manual R2000-43-E Release: 1.03 © Elotech GmbH Page 2/24
Contents
I.
Contents............................................................................................................... 1
I.
Contents............................................................................................................... 2
II.
Type code............................................................................................................ 3
III.
Connection Diagram: R2000 - 431 ...................................................................... 4
IV.
Connection Diagram: R2000 - 432 ...................................................................... 5
V.
Connection Diagram: R2000 - 436 ...................................................................... 6
VI.
Connection Diagram: R2000 - 433 ...................................................................... 7
VII.
Connection Diagram: R2000 - 437 ...................................................................... 8
VIII.
Display and Keyboard.......................................................................................... 9
IX.
Tendency Display............................................................................................... 10
X.
Operating Levels................................................................................................ 11
XI.
Configuration Level, general settings................................................................. 12
XII.
Configuration Level, individual selectable for zones 1...4; d1, d2.................... 16
XIII.
Parameter Level, individual selectable for zones 1...4....................................... 19
XIV.
Operating Level, individual selectable for zones 1...4........................................ 22
XV.
Operating Level, Option: only inputs zones d1 and d2 ...................................... 23
XVI.
Technical Data................................................................................................... 23
XVII.
Error displays..................................................................................................... 24
XVIII.
Installation Instructions ...................................................................................... 24
Please read this operating manual before starting up carefully.
Observe the installation and connecting instructions.
Note: Only trained personnel following the regional safety regulations may operate the
hereby discribed instruments. It is essential, that one has well experience in installing electric devices.
The instrument is not suitable for installation in hazardous areas. Do not open the device while the power lines are
connected. Take care to the separat interface- and data transmission descriptions.
Before operation, the unit must be configurated for its intended purpose under an expert guidance.
E.g. controller type, sensor type and range, alarm adjustment etc.. See: Configuration and Parameter levels.
Attention: The „heating“- or „cooling“-outputs can be active while programming or configuring
the controller. This can cause a damage either to the plant itself or its contents.

Manual R2000-43-E Release: 1.03 © Elotech GmbH Page 3/24
II. Type code
R 2000 - aaa - x - y - 000 - d - z
1: power supply: 230 V AC
2: power supply: 115 V AC
3: power supply: 24 V AC
5: power supply: 24 V DC
0: without serial interface
2: ser. interface RS232-C Protocol: ELOTECH - standard
4: ser. interface RS485 Protocol: ELOTECH – standard
InterBus-S via gateway M-IBS -5
5: ser. interface 0/20mA Protocol: ASCII, ELOTECH - standard
7: CAN CANopen Device Profile DS-404
9: Profibus DP EN
0: standard
1: with analog input d1 (0...10 Vdc) (not available with CAN / Profibus-Interface)
2: with analog input d1 and d2 (each 0...10 Vdc) (not available with CAN / Profibus-Interface)
5: with heater current monitoring. Only with bistable voltage outputs. Codes: 432, 436, 437.
0: sensor programmable: RTD (Pt100-DIN), 2- or 3-wire; Type L, Type J; Type K
431 4- zones heat-only or heating-off-cooling controller; control outputs: all, relais (not with heater current monitoring)
432 4- zones heat-only or heating-off-cooling controller; control outputs: heating: bist. voltage signal. Com.: +
cooling: bist. voltage signal. Com.: +
436 4- zones heat-only or heating-off-cooling controller; control outputs: heating: bist. voltage signal. Com.: -
(Preference) cooling: bist. voltage signal. Com.: -
433 4- zones heat-only or heating-off-cooling controller; control outputs: heating: bist. voltage signal. Com.: +
cooling: relais
437 4- zones heat-only or heating-off-cooling controller; control outputs: heating: bist. voltage signal. Com.: -
(Preference) cooling: relais

Manual R2000-43-E Release: 1.03 © Elotech GmbH Page 4/24
III. Connection Diagram: R2000 - 431
k4* k3 k2 k1 70
L / DC- 171
N / DC+ 272
3 73
A1 417 74
A1 518 75
A2 619 Option: d 2: 0...10Vdc+ 76
A2 720 0...10Vdc - 77
Out4 8Out8 21 Option: d 1: 0...10Vdc+ 78
Out4 9Out8 22 0...10Vdc - 79
Out3 10 Out7 23 Zone: Sensor: 80
Out3 11 Out7 24 TC Pt100 81
Out2 12 Out6 25 - 60 82
Out2 13 Out6 26 4 61 83
Out1 14 Out5 27 62
Out1 15 Out5 28 3- 63
GND GND
90
64
RxDout RxD in
91
- 65
TxD in RxDout
92
266
H A
TxDout TxDout
93
67
L B RxD in TxD in
94
1- 68 95
69
CAN
RS485 RS232 0/20mA
96
65: RTD 2. wire RTD 2. wire
66: 3-wire 1. wire 2-wire 1. wire
67: connection 3. wire connection 3. wire = jumper to 2. wire
jumper
jumper
67: RTD 3. wire RTD 3. wire = jumper to 2. wire
68: 3-wire 2. wire 2-wire- 2. wire
69: connection 1. wire connection 1. wire
„heat-only“ or „cool-only“ - controller: „heating-off-cooling“ - controller:
Control output OUT 1: Zone 1; „heating“ or „cooling“ „heating“
to
OUT 4: Zone 4; „heating“ or „cooling“ „heating
Control output OUT 5: Zone 1; „cooling“
to
OUT 8: Zone 4; „cooling“
Alarm Output A1: Alarm 1 ( Temperature monitoring alarm A1 for all zones)
Alarm Output A2: Alarm 2 ( Temperature monitoring alarm A2 for all zones)
Setpoint Controlling: K1: open = Setpoint 1 (SP1) valid
K1: closed = Setpoint 2 (SP2) valid, for all zones
Adjustment lock (LOC): K2: open = Adjustment lock only via „software code“ (see parameter: LOC)
K2: closed = Adjustment locked according to the choosen „software code“.
Setpoint changing: K3: open = individual setpoint adjustment for each zone
K3: closed = if setpoint has been changed in one zone,
this new setpoint is valid (will be overtaken) for all other zones automatically.
CAN-Interface, (Option):K4: open = CAN: „operational“. Operation only with CANopen protocoll.
K4: closed = CAN: „operational“ always active.
K4 must be closed, if the instrument is equipped with a CAN-interface but not used.
Input d1, (Option):0 ... 10 VDC, Display: Zone: d1
Input d2, (Option):0 ... 10 VDC, Display: Zone: d2

Manual R2000-43-E Release: 1.03 © Elotech GmbH Page 5/24
IV. Connection Diagram: R2000 - 432
k4* k3 k2 k1 70
L / DC- 171
N / DC+ 272
3 73
A1 417 Option 74
A1 518 Analog Input 75
A2 619 76:
d 2: 0...10VDC+
76: L1 76
A2 720 77:
0...10VDC -
77: L1 77
8 21 78:
d 1: 0...10VDC+
78: L2 78
9 22 79:
0...10VDC -
79: L2 79
10 23 Zone: Sensor: 80: L3 80
Out 4 -11 Out 8 - 24 TC Pt100 81: L3 81
Out 3 -12 Out 7 - 25 - 60 Option 82
Out 2 -13 Out 6 -26 461 Heater current 83
Out 1 -14 Out 5 - 27 62 transformer
Com.+ 15 Com.+ 28 3- 63
GND GND
90
64
RxDou RxD in
91
- 65
TxD in RxDout
92
266
H A
TxDout TxDout
93
67
L B RxD in TxD in
94
1- 68 95
69
CAN
RS485 RS232 0/20mA
96
It is not permitted to connect the grounds of the sensor-inputs and bist. voltage-outputs with each other.
65: RTD 2. wire RTD 2. wire
66: 3-wire 1. wire 2-wire 1. wire
67: connection 3. wire connection 3. wire = jumper to 2. wire
jumper
jumper
67: RTD 3. wire RTD 3. wire = jumper to 2. wire
68: 3-wire 2. wire 2-wire- 2. wire
69: connection 1. wire connection 1. wire
„heat-only“ or „cool-only“ - controller: „heating-off-cooling“ - controller:
Control output OUT 1: Zone 1; „heating“ or „cooling“ „heating“
to
OUT 4: Zone 4; „heating“ or „cooling“ „heating
Control output OUT 5: Zone 1; „cooling“
to
OUT 8: Zone 4; „cooling“
Alarm Output A1: Alarm 1 ( Temperature- or heater current monitoring alarm A1 for all zones)
Alarm Output A2: Alarm 2 ( Temperature- or heater current monitoring alarm A2 for all zones)
Setpoint Controlling: K1: open = Setpoint 1 (SP1) valid
K1: closed = Setpoint 2 (SP2) valid, for all zones
Adjustment lock (LOC): K2: open = Adjustment lock only via „software code“ (see parameter: LOC)
K2: closed = Adjustment locked according to the choosen „software code“.
Setpoint changing: K3: open = individual setpoint adjustment for each zone
K3: closed = if setpoint has been changed in one zone,
this new setpoint is valid (will be overtaken) for all other zones automatically.
CAN-Interface, (Option):K4: open = CAN: „operational“. Operation only with CANopen protocoll.
K4: closed = CAN: „operational“ always active.
K4 must be closed, if the instrument is equipped with a CAN-interface but not used.
Input d1, (Option):0 ... 10 VDC, Display: Zone: d1
Input d2, (Option):0 ... 10 VDC, Display: Zone: d2
Heater current monitoring: 1 current – transformer / phase
Single phase operation: terminals 76,77: L1
Three-phase operation: terminals 76 – 81: L1, L2, L3

Manual R2000-43-E Release: 1.03 © Elotech GmbH Page 6/24
V. Connection Diagram: R2000 - 436
k4* k3 k2 k1 70
L / DC- 171
N / DC+ 272
3 73
A1 417 Option 74
A1 518 Analog Input 75
A2 619 76:
d 2: 0...10VDC+
76: L1 76
A2 720 77:
0...10VDC -
77: L1 77
8 21 78:
d 1: 0...10VDC+
78: L2 78
9 22 79:
0...10VDC -
79: L2 79
10 23 Zone: Sensor: 80: L3 80
Out 4 +11 Out 8+24 TC Pt100 81: L3 81
Out 3 +12 Out 7+25 - 60 Option 82
Out 2 +13 Out 6+26 461 Heater current 83
Out 1 +14 Out 5+27 62 transformer
Com. - 15 Com.- 28 3- 63
GND GND
90
64
RxDout RxD in
91
- 65
TxD in RxDout
92
266
H A
TxDout TxDout
93
67
L B RxD in TxD in
94
1- 68 95
69
CAN
RS485 RS232 0/20mA
96
It is not permitted to connect the grounds of the sensor-inputs and bist. voltage-outputs with each other.
65: RTD 2. wire RTD 2. wire
66: 3-wire 1. wire 2-wire 1. wire
67: connection 3. wire connection 3. wire = jumper to 2. wire
jumper
jumper
67: RTD 3. wire RTD 3. wire = jumper to 2. wire
68: 3-wire 2. wire 2-wire- 2. wire
69: connection 1. wire connection 1. wire
„heat-only“ or „cool-only“ - controller: „heating-off-cooling“ - controller:
Control output OUT 1: Zone 1; „heating“ or „cooling“ „heating“
to
OUT 4: Zone 4; „heating“ or „cooling“ „heating
Control output OUT 5: Zone 1; „cooling“
to
OUT 8: Zone 4; „cooling“
Alarm Output A1: Alarm 1 ( Temperature- or heater current monitoring alarm A1 for all zones)
Alarm Output A2: Alarm 2 ( Temperature- or heater current monitoring alarm A2 for all zones)
Setpoint Controlling: K1: open = Setpoint 1 (SP1) valid
K1: closed = Setpoint 2 (SP2) valid, for all zones
Adjustment lock (LOC): K2: open = Adjustment lock only via „software code“ (see parameter: LOC)
K2: closed = Adjustment locked according to the choosen „software code“.
Setpoint changing: K3: open = individual setpoint adjustment for each zone
K3: closed = if setpoint has been changed in one zone,
this new setpoint is valid (will be overtaken) for all other zones automatically.
CAN-Interface, (Option):K4: open = CAN: „operational“. Operation only with CANopen protocoll.
K4: closed = CAN: „operational“ always active.
K4 must be closed, if the instrument is equipped with a CAN-interface but not used.
Input d1, (Option):0 ... 10 VDC, Display: Zone: d1
Input d2, (Option):0 ... 10 VDC, Display: Zone: d2
Heater current monitoring: 1 current – transformer / phase
Single phase operation: terminals 76,77: L1
Three-phase operation: terminals 76 – 81: L1, L2, L3

Manual R2000-43-E Release: 1.03 © Elotech GmbH Page 7/24
VI. Connection Diagram: R2000 - 433
k4* k3 k2 k1 70
L / DC- 171
N / DC+ 272
3 73
A1 417 Option 74
A1 518 Analog Input 75
A2 619 76:
d 2: 0...10VDC+
76: L1 76
A2 720 77:
0...10VDC -
77: L1 77
8 Out 8 21 78:
d 1: 0...10VDC+
78: L2 78
9 Out 8 22 79:
0...10VDC -
79: L2 79
10 Out 7 23 Zone: Sensor: 80: L3 80
Out 4 -11 Out 7 24 TC Pt100 81: L3 81
Out 3 -12 Out 6 25 - 60 Option 82
Out 2 -13 Out 6 26 4 61 Heater current 83
Out 1 -14 Out 5 27 62 transformer
Com.+ 15 Out 5 28 3- 63
GND GND
90
64
RxDout RxD in
91
- 65
TxD in RxDout
92
266
H A
TxDout TxDout
93
67
L B RxD in TxD in
94
1- 68 95
69
CAN
RS485 RS232 0/20mA
96
It is not permitted to connect the grounds of the sensor-inputs and bist. voltage-outputs with each other.
65: RTD 2. wire RTD 2. wire
66: 3-wire 1. wire 2-wire 1. wire
67: connection 3. wire connection 3. wire = jumper to 2. wire
jumper
jumper
67: RTD 3. wire RTD 3. wire = jumper to 2. wire
68: 3-wire 2. wire 2-wire- 2. wire
69: connection 1. wire connection 1. wire
„heat-only“ or „cool-only“ - controller: „heating-off-cooling“ - controller:
Control output OUT 1: Zone 1; „heating“ or „cooling“ „heating“
to
OUT 4: Zone 4; „heating“ or „cooling“ „heating
Control output OUT 5: Zone 1; „cooling“
to
OUT 8: Zone 4; „cooling“
Alarm Output A1: Alarm 1 ( Temperature- or heater current monitoring alarm A1 for all zones)
Alarm Output A2: Alarm 2 ( Temperature- or heater current monitoring alarm A2 for all zones)
Setpoint Controlling: K1: open = Setpoint 1 (SP1) valid
K1: closed = Setpoint 2 (SP2) valid, for all zones
Adjustment lock (LOC): K2: open = Adjustment lock only via „software code“ (see parameter: LOC)
K2: closed = Adjustment locked according to the choosen „software code“.
Setpoint changing: K3: open = individual setpoint adjustment for each zone
K3: closed = if setpoint has been changed in one zone,
this new setpoint is valid (will be overtaken) for all other zones automatically.
CAN-Interface, (Option):K4: open = CAN: „operational“. Operation only with CANopen protocoll.
K4: closed = CAN: „operational“ always active.
K4 must be closed, if the instrument is equipped with a CAN-interface but not used.
Input d1, (Option):0 ... 10 VDC, Display: Zone: d1
Input d2, (Option):0 ... 10 VDC, Display: Zone: d2
Heater current monitoring: 1 current – transformer / phase
Single phase operation: terminals 76,77: L1
Three-phase operation: terminals 76 – 81: L1, L2, L3

Manual R2000-43-E Release: 1.03 © Elotech GmbH Page 8/24
VII. Connection Diagram: R2000 - 437
k4* k3 k2 k1 70
L / DC- 171
N / DC+ 272
3 73
A1 417 Option 74
A1 518 Analog Input 75
A2 619 76:
d 2: 0...10VDC+
76: L1 76
A2 720 77:
0...10VDC -
77: L1 77
8 Out 8 21 78:
d 1: 0...10VDC+
78: L2 78
9 Out 8 22 79:
0...10VDC -
79: L2 79
10 Out 7 23 Zone: Sensor: 80: L3 80
Out 4 +11 Out 7 24 TC Pt100 81: L3 81
Out 3 +12 Out 6 25 - 60 Option 82
Out 2 +13 Out 6 26 461 Heater current 83
Out 1 +14 Out 5 27 62 transformer
Com. - 15 Out 5 28 3- 63
GND GND
90
64
RxDout RxD in
91
- 65
TxD in RxDout
92
266
H A
TxDout TxDout
93
67
L B RxD in TxD in
94
1- 68 95
69
CAN
RS485 RS232 0/20mA
96
It is not permitted to connect the grounds of the sensor-inputs and bist. voltage-outputs with each other.
65: RTD 2. wire RTD 2. wire
66: 3-wire 1. wire 2-wire 1. wire
67: connection 3. wire connection 3. wire = jumper to 2. wire
jumper
jumper
67: RTD 3. wire RTD 3. wire = jumper to 2. wire
68: 3-wire 2. wire 2-wire- 2. wire
69: connection 1. wire connection 1. wire
„heat-only“ or „cool-only“ - controller: „heating-off-cooling“ - controller:
Control output OUT 1: Zone 1; „heating“ or „cooling“ „heating“
to
OUT 4: Zone 4; „heating“ or „cooling“ „heating
Control output OUT 5: Zone 1; „cooling“
to
OUT 8: Zone 4; „cooling“
Alarm Output A1: Alarm 1 ( Temperature- or heater current monitoring alarm A1 for all zones)
Alarm Output A2: Alarm 2 ( Temperature- or heater current monitoring alarm A2 for all zones)
Setpoint Controlling: K1: open = Setpoint 1 (SP1) valid
K1: closed = Setpoint 2 (SP2) valid, for all zones
Adjustment lock (LOC): K2: open = Adjustment lock only via „software code“ (see parameter: LOC)
K2: closed = Adjustment locked according to the choosen „software code“.
Setpoint changing: K3: open = individual setpoint adjustment for each zone
K3: closed = if setpoint has been changed in one zone,
this new setpoint is valid (will be overtaken) for all other zones automatically.
CAN-Interface, (Option):K4: open = CAN: „operational“. Operation only with CANopen protocoll.
K4: closed = CAN: „operational“ always active.
K4 must be closed, if the instrument is equipped with a CAN-interface but not used.
Input d1, (Option):0 ... 10 VDC, Display: Zone: d1
Input d2, (Option):0 ... 10 VDC, Display: Zone: d2
Heater current monitoring: 1 current – transformer / phase
Single phase operation: terminals 76,77: L1
Three-phase operation: terminals 76 – 81: L1, L2, L3

Manual R2000-43-E Release: 1.03 © Elotech GmbH Page 9/24
VIII. Display and Keyboard
LED 1: Control output „heating“ of the choosen zone active LED 2: Control output „cooling“ of the choosen zone active
LED A1: Alarm output A1, indication LED _/ : Setpoint ramp of the choosen zone active
LED A2: Alarm output A2, indication LED SP2: Setpoint 2 valid (for all zones)
ZONE
Zone preselection
P
Parameter key (parameter preselection)
Adjustment of chosen parameter (e.g. setpoint) to higher or lower values.
Short operation: single-step adjustment
Longer operation: quick-scanning
When the parameter adjustments have been altered but not entered,
the display will flash bright/dark.
E
Confirmation and storage of the pre-selected values.
The display will show a light chain as a control of this function.
P
Sets the parameter back to the originally stored value.
Any alterations made to the parameters, that are not confirmed (E-key) within
30 seconds, will not be accepted and the parameter will return to its originally
stored value. The actual process value and the setpoint value will be indicated.
F1
Function key, E. g. all zones are displayed cyclic (zone scanning on/off).
Zones, which are not in action (OFF), are not displayed.
The function of this key can be programmed into the configuration level
of zone 0. See parameter „Co.F1“

Manual R2000-43-E Release: 1.03 © Elotech GmbH Page 10/24
IX. Tendency Display
After switching the instrument „on“ a temperature tendency display will be shown, to give an overview about the temperatures
deviations relating to the setpoints in the individual controller zones.
Tendency display. Zone 1 2 3 4
Display „PROCESS“: Temperature deviation zones 1...4:
high temperature, X0,5 % > W
(SP)
temperature o.k.
low temperature, X0,5 % < W
(SP)
Zone Zone Zone Zone
1 2 3 4
The displayed dec.-point shows the
„heating“ or „cooling“: on off off on actual situation of the controllers
output.
Flashing: Alarm indication in the matching zone
high temperature, X0,5 % > W
(SP)
temperature o.k.
low temperature, X0,5 % < W
(SP)
Zone Zone Zone Zone
1 2 3 4
The displayed dec.-point shows the
„heating“ or „cooling“: on off off off actual situation of the controllers
output.
Zone 2: Zone „OFF“, not in use (display: off)
Zone 3: Bottom range end has been reached ( sensor error )
Zone 4: Top range end has been reached ( sensor break, no sensor connected )
Flashing: Alarm indication in the matching zone
O= Selftuning algorithm: active (Opt.) H = Manual mode (Hand)
Dec.-point flashing acc. to the actual output
ratio
Zone scanning:
Now ( according to the configuration of key „F1“ ) the process and setpoint values of the individual zones are shown
in a scanning mode.
If „F1“ is not configurated in this mode (see configuration level) , the individual zones have to be selected manual by
pressing key „ZONE“.

Manual R2000-43-E Release: 1.03 © Elotech GmbH Page 11/24
X. Operating Levels
The operation of the controller is divided into 3 levels.
After switching on the unit, it will be automatically in the operating level.
and and
press press appr. 5 sec.
Parameter- Configuration-
Controller: Operating level level level
“on“
process value Y ( output ratio ) Zone : on / OFF
(process)
setpoint value
(set)
Y ConF
1Y.Hi SEn
Alarm A1
Alarm A2 OFSt COPY
Back into the operation level:
- Press 1 sec. or automatically after appr. 30 sec.
Operating level
(for each zone separatly):
Process- and Setpoint value will be displayed simultaneously. Within the operating level the setpoint can be adjusted
by pressing the " up " / " down " - keys.
Every adjustment has to be quit by pressing the „ E“ - key.
All parameters within the operating level ( including the alarm values ) can , in succession, be displayed by pressing the
„ P “ - key and adjusted by pressing the " up " / " down " - keys. Quit by pressing the „ E“ - key.
Parameter level
(for each zone separatly):
Within the parameter level the values are adjusted to suit each individual process.
This level is reached by simultaneously pressing the "P" - and " E" -keys.
The display of each single parameter within the parameter level and their adjustment, are made in the same way as
within the operating level.
After either pressing the „E“ - key for approx. 1 second, or waiting for a period of approx. 30 seconds,
the unit will automatically return to the operating level (display of process value and setpoint).
Configuration level:
This primary informations have to be entered before taking the instrument into operation.
The configuration level is reached by simultaneously pressing the "P" - and " E" - keys for a period of approx. 5 seconds.
First choose the configuration level in zone 0. Here general settings have to be made.
This has to be programmed at first:
- Only TC- or RTD-connection for all zones? Or: Mixed connection ?
- Alarm configuration (valid for all zones) - Function of key „F1“
- Software key - Serial interface informations
- Heater current monitoring
Than choose the configuration level of each individual controller zone.
This has to be programmed at second:
- Controller type (for each zone)
- Input type (sensor type), sensor range (for each zone)
- Min. and max. setpoint range (for each zone)
The display of each single parameter within the configuration level and their adjustment, made in the same fashion as within
the operating level.
There is also a copy function available. So it is possible, to copy the programmed parameters of one zone to other zones.
After either pressing the „E“ - key for approx. 1 second, or waiting for a period of approx. 30 seconds,
the unit will automatically return to the operating level (display of process value and setpoint).
P
PP
E
E
P P
P
P
P
PP
E
P
P

Manual R2000-43-E Release: 1.03 © Elotech GmbH Page 12/24
XI. Configuration Level, general settings
Select zone 0 and press „P“ - and „E“ - key appr. 5 sec.
Display Parameter Display
"Process" „Set“
P - tc Sensor mix - 4 all 4 zones : Thermocouple - connection
2 2 Zones 1 - 2 : RTD - connection; zones 3-4: Thermocouple- connection
4 - all 4 zones : RTD - connection
Co.A1 Alarm 1-Configuration The selected configuration is effective for all control zones.
(switches relay A1) The individual temperature alarms A1 of all zones are connected
to the main, common contact A1.
If a control zone indicates a fault (sensor short circuit / break ),
the alarm output A1 is generally switched.
OFF alarm OFF, no alarm signalisation (ex works)
1 signal contact, setpoint depentend: off-on
2 limit contact, process value depentend: off-on
3 limit comparator: off-on-off
4 signal contact: on-off
5 limit contact: on-off
6 limit comparator: on-off-on
7 limit comp. with start-up suppression: off-on-off
8 heater current monitoring; limit contact: off-on
9 heater current monitoring; limit contact: on-off
The signal contact is adjusted and displayed The limit contact is adjusted and displayed
relative to the setpoint (deviation alarm). as an absolute value.
LED, Switching behaviour: Configuration: LED, Switching behaviour: Configuration:
off on 1 off on 2, 8
on off 4on off 5, 9
setpoint process process
The limit comparator is adjusted and displayed The alarm relay of the limit comparator with
relative to the setpoint. The selected start-up suppression is activated when the controller
value is effective below and above the setpoint. is first switched on. It is only then deactivated, when the
process value has been within, and left, the o.k. -zone.
LED, Switching behaviour: Configuration: LED, Switching behaviour: Configuration:
on
off on off 3 off on off 7
on off on 6
setpoint process setpoint process
Please note:
In case of sensor error the alarms will react in the same way as range override. The alarm contacts therefore do not offer protection
against all types of plant breakdown. With this in mind, we recommend the use of a second, independent monitor unit.
Care should be used to ensure, that the setpoints of the alarm contacts are programmed within the selected measuring range.
If a setpoint ramp has been programmed, the alarms that are relative to the setpoint (signal contact, limit comparator) follow the
setpoint up the ramp.
signal value
limit range
limit value
limit range

Manual R2000-43-E Release: 1.03 © Elotech GmbH Page 13/24
Display Parameter Display
"Process" „Set“
rE.A1 Relay A1
switching behaviour dir on: LED A1 „on“. Relay A1 "activated"
off: LED A1 „off“. Relay A1 "not active"
inv on: LED A1 „on“. Relay A1 "not active"
off: LED A1 „off“. Relay A1 "activated"
Co.A2 Alarm 2-Configuration The selected configuration is effective for all control zones.
(switches relay A2) The individual temperature alarms A1 of all zones are connected
to the main, common contact A1.
If a control zone indicates a fault (sensor short circuit / break ),
the alarm output A1 is generally switched.
OFF alarm OFF, no alarm signalisation (ex works)
1 signal contact, setpoint depentend: off-on
2 limit contact, process value depentend: off-on
3 limit comparator: off-on-off
4 signal contact: on-off
5 limit contact: on-off
6 limit comparator: on-off-on
7 limit comp. with start-up suppression: off-on-off
8 heater current monitoring; limit contact: off-on
9 heater current monitoring; limit contact: on-off
rE.A2 Relay A2
switching behaviour dir on: LED A2 „on“. Relay A1 "activated"
off: LED A2 „off“. Relay A1 "not active"
inv on: LED A2 „on“. Relay A1 "not active",
off: LED A2 „off“. Relay A1 "activated",
Heater current monitoring
The following parameters will only be displayed if the heater current monitoring system is activated as descriped below:
Heater current monitoring via relay A1: Program parameter Co.A1 to number 8 or 9
Heater current monitoring via relay A2: Program parameter Co.A2 to number 8 or 9
The heater current to be monitored, has to be programed as an absolute value into the operating level for both relays A1 and A2.
See: Operating level, Parameter „A1“ or „A2“.
Please note if the supply voltage is low the heater current is higher than the monitoring value otherwise the alarm signal will be
activated.
If the heater current value falls below the monitoring value, an alarm signal (the relay switches) will be activated.
With the help of the parameter „dL.Ax“ it is possible to program a delay time.
If you do so, it is virtually impossible to get an unauthorized alarm signal.
When switching the power-on, the alarm signalisation will be suppressed until the heating current values for all zones has been
scanned and verified.
The monitoring function and all possible adjustments are valid for all connected heating zones.
Display Parameter- Parameter value
„Process" description Display „Set“
dL.A1 delay time, relay A1 5 steps adjustable (in sec.) Adjustment and display in seconds.
If alarm relay A1 is selected OFF= no delay time The values are dependent on the
for the heater current current detection interval time and the
monitoring. number of active controller zones.
dL.A2 delay time, relay A2 5 steps adjustable (in sec.) Adjustment and display in seconds.
If alarm relay A2 is selected OFF= no delay time The values are dependent on the
for the heater current current detection interval time and the
monitoring. number of active controller zones.

Manual R2000-43-E Release: 1.03 © Elotech GmbH Page 14/24
Display Parameter- Parameter value
„Process" description Display „Set“
Cu.CY Current detection intervall 1 ... 60 sec. Time between the current measuring
of two zones following each other.
C x.x Min. leakage current value OFF; Adjustment of the allowed min.
and leakage current display 0,0...99,9 A leakage current value.
with continous current display. The heater current will be monitored
to detect circuits with an eventual
leakage current (e.g. SSR damage).
SSR`s (especially if they are combined with RC-combinations) normally have small leakage currents.
Heaters also have small leakage currents.
The actual leakage current will be displayed in display „PROCESS“.
Via display „SET“ the min. allowed leakage current value can be adjusted.
Currents below this value will be ignored.
If a permanent current is detected in one zone the alarm relay will be activated and
the display „PROCESS“ will show the error signalisation „Er.Cu“.
The zone with a measured permanent current can be located by pressing the zone
key and watching all temperature indications.
Display indication in this case: „Comparable with„temperature too high.“
But there is no special indication via tendency- or alarm status display.
Display: C 0.2 Er. Cu
PROCESS PROCESS
1.0
SET SET
Leakage current: 0,2A Permanent current detected in one zone.
Min. leakage current Error signalisation: flashing
value: 1,0A
Display Parameter- Parameter value
„Process" description Display „Set“
Co.F1 Select funktion OFF No function
of key „F1“ OPt Selftuning algorithm can be activated by pressing key „F1“
in the matching zone. „F1“ and „E“: stop selftuning.
Y Shows the actual percentage output ratio, while pressing „F1“.
Display „PARAMETER“: Y
LEd.t Lamp (LED) test, while pressing „F1“.
LOC Adjustment lock OFF No adjustment lock (ex works)
P C Parameter and configuration levels locked
n.SP1 All parameters apart from SP1 locked (not SP1)
ALL All parameters locked
All parameters that have been locked with „LOC“ can be
selected and read, but not altered.
This adjustment cannot be changed if the external contact K2 is closed.
Zo.OF Zones offset preselection OFF No offset preselection. Zones indication: 1 - 4
(Continuous numbering of 1 - 91 Zones will be numbered with preselected offset value.
the controller zones) Example: Zo.OF = 1 -> Zone indication: 2 - 5
Zo.OF = 8 -> Zone indication: 9 - 12

Manual R2000-43-E Release: 1.03 © Elotech GmbH Page 15/24
Display Parameter- Parameter value
„Process" description Display „Set“
The following parameters are only valid, if the unit is equipped with a serial interface.
RS232, RS485, 0/20mA.
Prot Protocol preselection ELO ELOTECH- standard protocol
IbS Gateway-protocol valid for Profibus-DP, InterBus-S
Only with RS 485-interface (Code-No.: 4).
Adr Unit adress 1 .... 255 (ex works: 1)
The computer adresses the unit/controller at this adress.
Each unit has ist own adress. With RS-485 it is possible to adress 32 units.
For Data format 7E1 7 data, even, 1 stopbit
7o1 7 data, odd, 1 stopbit
7E2 7 data, even, 2 stopbit
7o2 7 data, odd, 2 stopbit
7n2 7 data, none, 2 stopbit
8E1 8 data, even, 1 stopbit
8o1 8 data, odd, 1 stopbit
8n1 8 data, none, 1 stopbit InterBus-S Gateway
8n2 8 data, none, 2 stopbit
bAud Baud rate OFF; 0,3 ... 9,6 kBaud
The baud rate denotes the transmission rate at which one bit is transmitted.
InterBus-S Gateway = 9,6 kBaud
Details, see: - sep. interface description: ELOTECH – standard-protocol
- sep. interface description: Gateway: M-IBS-5
- Download: www.elotech.de
The following parameters are only valid, if the unit is equipped with a CAN interface.
Adr Unit adress 1 .... 127 (ex works: 1)
bAud Baud rate 10, 20, 50, 100, 125, 250, 500 kBaud, 1MBaud (ex works: 20)
CANopen-specfication: CANopen Master: no
CANopen Slave: yes
Extended Boot-up: no
Minimum Boot-up: yes
COB ID Distribution: yes; default via SDO
Node ID Distribution: no; via device keyboard
No. of POD´s: 0RX, 1TX
PDO Modes: async.
Variable PDO mapping: no
Emergency message: yes
Life guarding: yes
No. of SDO`s: 1RX, 1TX
Device Profile: CiA DS-404
Details, see: - CANopen Device Profile CiA DS-404; ELOTECH Object Dictionary
- Download: www.elotech.de
20xx
EL.xx Control number No function. End of configuration level

Manual R2000-43-E Release: 1.03 © Elotech GmbH Page 16/24
XII. Configuration Level, individual selectable for zones 1...4; d1, d2
Select zone n and press „P“ - and „E“ - key appr. 5 sec.
Display Parameter Display
"Process" „Set“
Zone Zone on / off OFF measuring- or controller zone „off“
on measuring- or controller zone „on“
ConF Controller configuration 2P h 2-point-controller „heating-off“ (ex works)
2P c 2point-controller „cooling-off“
2Pnc 2point-controller „cooling-off“ with non-linear cooling *)
3P 3point-controller „heating-off-cooling“
3Pnc 3point-controller „heating-off-cooling“ with non-linear cooling *)
*) non-linear cooling:
Cooling action can be pre-selected with either linear or
non-linear cooling response curve ( e.g. for vapour cooling).
diSP Zone works as an indicator, no controller action
SEn Sensor selection P1 °C Pt 100, -50,0...100,0 °C
P1 °F Pt 100, -58,0...212,0 °F
P2 °C Pt 100, -90,0...205,0 °C
P2 °F Pt 100, -130... 401 °F
P4 °C Pt 100, 0... 400 °C (ex works)
P4 °F Pt 100, 32... 752 °F
P8°C Pt 100, 0... 800 °C
P8 °F Pt 100, 32...1472 °F
or, if selected as a thermocouple-input zone (depending on parameter „P - tc“ in Zone 0):
L4 °C T/C Fe-CuNi (L), 0... 400 °C
L4 °F T/C Fe-CuNi (L), 32... 752 °F
L8 °C T/C Fe-CuNi (L), 0... 800 °C
L8 °F T/C Fe-CuNi (L), 32... 1472 °F
J8 °C T/C Fe-CuNi (J), 0... 800 °C
J8 °F T/C Fe-CuNi (J), 32... 1472 °F
n1 °C T/C NiCr-Ni (K), 0... 1200 °C
n1 °F T/C NiCr-Ni (K), 32... 2192 °F
S1 °C T/C Pt10Rh-Pt (S), 0... 1600 °C
S1 °F T/C Pt10Rh-Pt (S), 32... 2912 °F
If the Sensor selection is changed, the following parameters will be set as follows and need to be re-adjusted:
Setpoint 1, setpoint 2: SP.Lo Process value offset: OFF
Lower setpoint limitation: Bottom range end; Higher setpoint limitation: Top range end;
Setpoint-ramp values: OFF; Alarm values: OFF;
OPTION: The following parameters are only valid for zones d1 and d2 (Input: 0...10 Vdc).
It is to configurate the display range of the 0...10 Vdc inputs.
The difference between the bottom end of the display range and the top end must amount to a minimum of
100 units and a maximum of 2000 units. By adjustment of one of the above parameters, the other
in this case will automatically follow.
rA.dP decimal points 0; 1; 2 (ex works: 1)
rA.Hi display range top end rA.Lo ... 9999 (ex works: 100,0)
rA.Lo display range bottom end -1999 ... rA.Hi (ex works: 0,0)
unit selectable physical. unit shown in the display „set“ ( e.g. : °C, °F, ba r, volt ... )
SP.Hi higher setpoint limitation programming range: SP.Lo ... top range (ex works: 400)
SP.Lo lower setpoint limitation programming range: bottom range ... SP.Hi (ex works: 0)
COPY Copy function to 1 ... to x Copy all datas of the actual zone to the selected zone x.
Select the target zone (1,2 .... or „to A“ (to all) with the „up/down“ - keys
and press „E“ (enter). After this, the datas would be copied.
Note: It is only possible to copy the configuration, if the sensor
configuration ( Parameter: P - tc ) in the target-zone is the same as in the
actual zone. This means, that it is not possible, to copy configurations of
e.g. RTD-input zones to thermocouple-input zones.

Manual R2000-43-E Release: 1.03 © Elotech GmbH Page 17/24
Display Parameter Display
"Process" „Set“
Softstart-function
TAKE CARE: If you take the softstart-function, make sure that the heating control outputs are
equipped with bistable voltage (logic) outputs.
This function is not allowed for instruments with relay-outputs
(in this case set So.St = OFF).
Otherwise the relais will be destroid becuse they switch too fast.
Softstart (general function):
During the softstart the controllers’ heating output response is limited to a pre-selected ratio, in order
to achieve a slow baking out of high performance heat cartridges.
Simultaneously the output clock frequency is quadrupled. Once the process value reaches
the softstart setpoint, it remains stable at this value for a pre-selcted hold-duration time.
At the end of this period the process value rises to the valid setpoint.
This results in a slower, more regular heating period.
For this purpose the bistable voltage output must be taken, that actuates SSR relays.
If the softstart is active, the controllers’ autotune function can’t operated (Er.OP).
If a setpoint-ramp has been programmed, the softstart has priority, and the ramp will only
become active after the softstart has been completed.
The softstart only works,
- if the parameter „1 P“ (prop. band, xp) is programmed > 0,1%.
- if the actual process value is lower than So.SP – 5% of the selected measuring range.
It is possible, to select this function for each zone individally.
Setpoint SP
So.SP
Softstart setpoint
So. Y
So.ti
t
So.St Softstart-function OFF: Softstart not active (ex works)
Next parameter So.Y, So.SP, So.ti are not shown.
On: Softstart in action.
The softstart function always runs, if the controller is switched on and / or
if the actual temperature is below the softstart setpoint So.SP minus 5%
of the range (e.g. range: 400^C -> 5%= 20°C).
So. Y Softstart output ratio 10 ... 100%
So.SP Softstart setpoint range: SP.Lo .... SP.Hi
So.ti Softstart duration time OFF; 0,1 ... 10,0 min.

Manual R2000-43-E Release: 1.03 © Elotech GmbH Page 18/24
Display Parameter Display
"Process" „Set“
Hand manual output ratio OFF, Auto, Man (ex works: OFF)
Setting: OFF
Function not active
Setting: Auto
In event of sensor break the controller automatically maintains the
last valid output ratio as the actuating signal.
An „H“ is then displayed as the first digit in the setpoint display,
followed by the valid output ratio. This ratio can be manually altered
in steps of 1% (up/down-keys; enter).
Under the following circumstances, the output ratio will be 0%:
- if the output ratio at time of the sensor break was 100%.
- if the controller is working along a setpoint-ramp.
- if the control deviation was more than 0,25% of the total
range at the time of sensor break.
- if th prop. band (P; xp) = 0.
- if the soft start was active at the time of the sensor break.
A few seconds after the sensor break has been rectified, the
controller returns to automatic operation and calculates the required
output ratio.
An additional signal can be issued in the event of sensor break, if
the alarm contacts are programmed accordingly.
Setting: Man
The controller now operates only as an actuator. Within the
operation level, an output ratio can be entered instead of the
setpoint. An „H“ is then displayed as the first digit in the setpoint display,
followed by the output ratio. There is no controlling action.

Manual R2000-43-E Release: 1.03 © Elotech GmbH Page 19/24
XIII. Parameter Level, individual selectable for zones 1...4
Select zone “n” and press „P“ - and „E“ - key appr. 1 sec.
Display Parameter Display
"Process" „Set“
Y valid output ratio -100...0...100 % The output ratio shows the momentary calculated ratio.
It cannot be altered. The display is in percent of the installed
performance capability for heating or cooling.
Output ratio for cooling is shown as a negative value.
1Y.Hi output ratio limit 0...100 % (ex works: 100)
„heating“ Limitation of the output ratio is only necessary when:
the heating or cooling energy supply is grossly over-
dimensioned compared to the power required, or
to turn off a control output (setting = 0%).
under normal circumstances no limitation is needed (setting = 0%).
the limitation becomes effective, when the controllers’ calculated
output ratio is greater than the maximum permissible (limited) ratio.
Warning!
The output ratio limitation does not work during autotune.
2Y.Hi output ratio limit 0...100 % (ex works: 100)
„cooling“
1 P „heating“ OFF; 0,1...100,0 % (ex works: 3,0)
prop. band (P) If „ 1 P “ = OFF (control action: on-off, without feedback)
next parameter: „ 1 Sd “.
1 d „heating“ OFF; 1...200 secs (ex works: 30)
rate (D)
1 J „heating“ OFF; 1...1000 secs (ex works: 150)
reset (I) Normally the controller works using PD/I control action.
This means, controlling without deviation and with practically
no overshoot during start-up.
The control action can be altered in its structure by making the
following adjustments to the parameters:
a. no control action, on-off (setting P = OFF)
b. P-action (setting D and I = 0)
c. PD-action (setting I = 0)
d. PI-action (setting D = 0)
e. PD/I modified PID-action
1 C „heating“ 0,5...240,0 secs (ex works: 10,0)
cycle time The switching frequency of the actuator can be determined
by adjusting the cycle time. This is the total time needed for the
controller to switch on and off once.
a) Relay outputs: cycle time > 10 secs
b) Bistable voltage outputs: cycle time 0,5...10 secs
1 Sd „heating“
Control sensitivity Only if: 1 P = Xp = OFF (On-off action, without feedback)
OFF; 0,1...80,0 °C (ex works: 0,1)
OFF; 0,01 ... 8,00 °C (ranges with dec.point)
Sd = 10,0
on
-5,0 +5,0 off
SETPOINT PROCESS VALUE

Manual R2000-43-E Release: 1.03 © Elotech GmbH Page 20/24
Display Parameter Display
"Process" „Set“
The following parameters are only displayed and valid if configuration is „ 3 P “ or „ 3 Pnc “ .
Only for „heating-off-cooling“ action.
Sh switch-point difference OFF; 0,1... 80,0 °C (ex works: OFF)
OFF; 0,01... 8,00 °C
This parameter raises the setpoint (switch-point) for cooling output
by the displayed value. It can be help to reduce the switching
frequency between the heating and cooling outputs, if this is to high.
Simultaneously activation of heat and cool outputs is not possible.
2 P „cooling“ OFF; 0,1...100,0 % (ex works: 3,0)
prop. band (P) If „ 2 P “ = OFF (control action: on-off, without feedback)
next parameter: „ 2 Sd “.
2 d „cooling“ OFF; 1...200 secs (ex works: 30)
rate (D)
2 J „cooling“ OFF; 1...1000 secs (ex works: 150)
reset (I)
2 C „cooling“ 0,5...240,0 secs (ex works: 10,0)
cycle time The switching frequency of the actuator can be determined
by adjusting the cycle time. This is the total time needed for the
controller to switch on and off once.
a) Relay outputs: cycle time > 10 secs
b) Bistable voltage outputs: cycle time 0,5...10 secs
2 Sd „cooling“
Control sensitivity Only if: 2 P = OFF (On-off action, without feedback)
OFF; 0,01 ... 8,00 °C (ranges with dec.point)
OFF; 0,1...80,0 °C (ex works: 0,1)
Sd = 10,0
on
off -5,0 +5,0
SETPOINT PROCESS VALUE
This manual suits for next models
4
Table of contents
Other Elotech Temperature Controllers manuals
Popular Temperature Controllers manuals by other brands
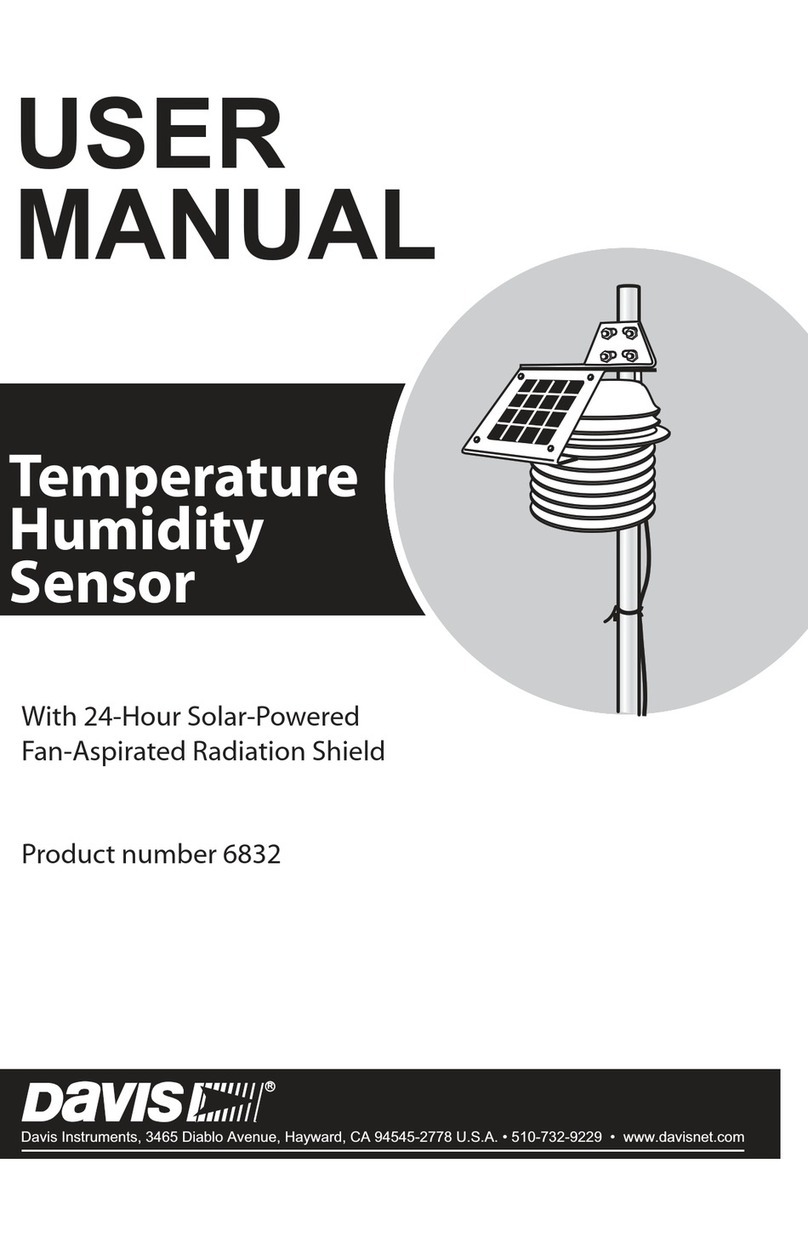
DAVIS
DAVIS 6832 user manual

United Electric Controls
United Electric Controls 800 Installation and maintenance instructions
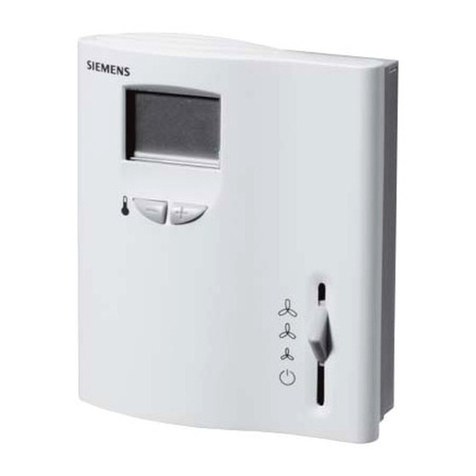
Siemens
Siemens RDF30U Technical instructions
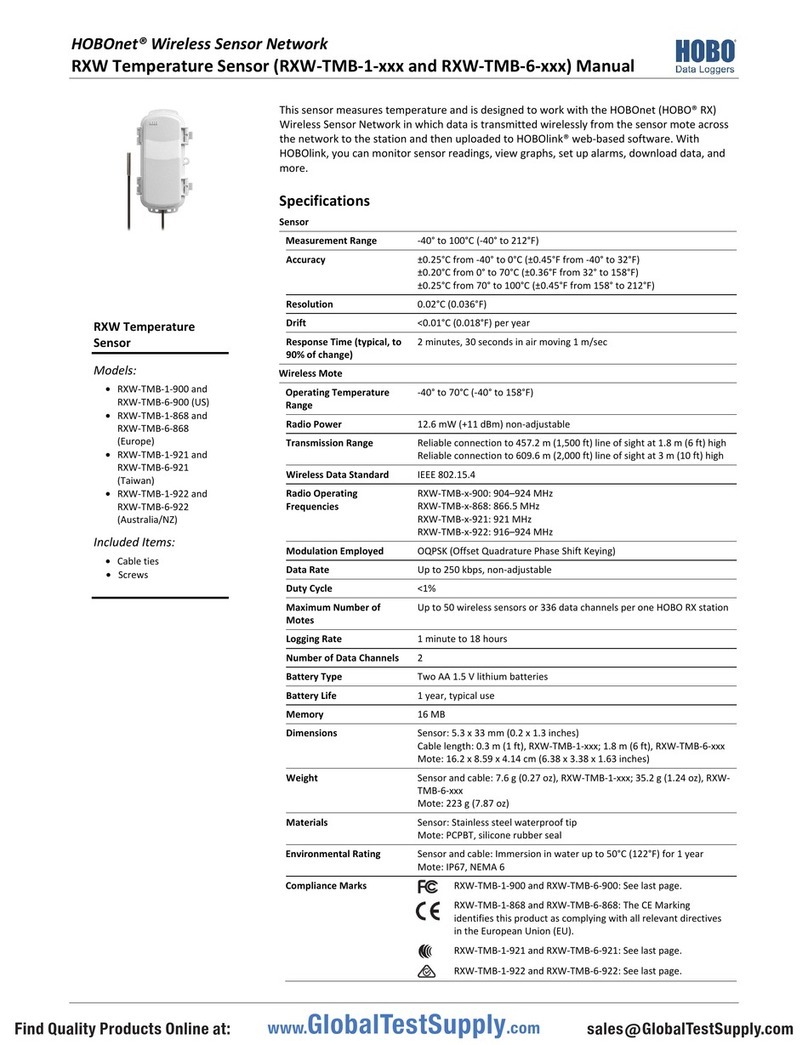
Hobo
Hobo HOBOnet RXW-TMB-1 Series manual
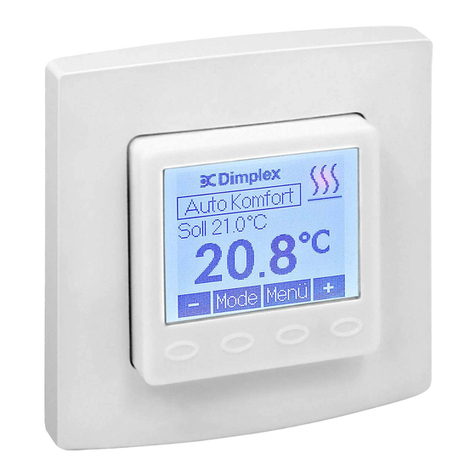
Dimplex
Dimplex BRTU 101 UN Operating instructions and system description

Home
Home H+ Guide & user manual