Enerpac EFBE5017 User manual

1
L4309 Rev. B 10/18 EN
1.0 SAFETY
1.1 Introduction
Read all instructions carefully. Follow all recommended
safety precautions to avoid personal injury as well
as damage to the product and/or damage to other
property. Enerpac cannot be responsible for any
damage or injury from unsafe use, lack of maintenance
or incorrect operation. Do not remove warning labels,
tags, or decals. In the event any questions or concerns
arise, contact Enerpac or a local Enerpac distributor for
clarification.
If you have never been trained on high-pressure hydraulic
tool safety, consult your distributor or service center for
information about an Enerpac hydraulic safety course.
This manual follows a system of safety alert symbols,
signal words and safety messages to warn the user of
specific hazards. Failure to comply with these warnings
could result in death or serious personal injury, as well
as damage to the equipment or other property.
The Safety Alert Symbol appears throughout
this manual. It is used to alert you to
potential physical injury hazards. Pay close
attention to Safety Alert Symbols and obey
all safety messages that follow this symbol to avoid the
possibility of death or serious personal injury.
Safety Alert Symbols are used in conjunction with certain
Signal Words that call attention to safety messages or
property damage messages and designate a degree or
level of hazard seriousness. The Signal Words used in
this manual are DANGER, WARNING, CAUTION and
NOTICE.
NOTICE:
DANGER
Indicates a hazardous situation that,
if not avoided, will result in death or
serious personal injury
NOTICE:
WARNING Indicates a hazardous situation that,
if not avoided, could result in death
or serious personal injury.
NOTICE:
CAUTION
Indicates a hazardous situation that,
if not avoided, could result in minor
or moderate personal injury.
NOTICE
Indicates information considered
important, but not hazard related
(e.g. messages relating to property
damage). Please note that the Safety
Alert symbol will not be used with this
signal word.
1.2 Hydraulic Cutter Safety Precautions
NOTICE:
WARNING Failure to observe and comply with the
following precautions and instructions may result in
death or serious personal injury. Property damage
could also occur.
• Read and completely understand the safety
precautions and instructions in this manual. Always
follow all safety precautions and instructions,
including those that are contained within the
procedures of this manual.
• Read this manual before operating the cutter, or
before performing any adjustments, inspections,
maintenance or repairs.
• Follow all instructions and heed all precautions
stated in this manual.
POWERFUL SOLUTIONS. GLOBAL FORCE.
Instruction Sheet
Flat Bar Cutter
Model EFBE5017
INDEX
1.0 SAFETY .............................1
2.0 PRODUCT DATA ......................6
3.0 CONFORMANCE TO NATIONAL AND
INTERNATIONAL STANDARDS ...........7
4.0 DESCRIPTION ........................7
5.0 RECEIVING INSTRUCTIONS .............7
6.0 SET-UP .............................8
7.0 POWER REQUIREMENTS ...............8
8.0 MAJOR FEATURES AND COMPONENTS ..8
9.0 CUTTER OPERATION .................10
10.0 MAINTENANCE .....................12
11.0 CLEANING THE PISTON AREA .........19
12.0 STORAGE .........................20
13.0 TROUBLESHOOTING ................20

2
• Place the tool horizontally on a substantial work
surface. The work surface must have a rated weight
capacity that exceeds the weight of the cutter and of
the material being cut.
• Fragments and splinters may be ejected from the
cutter during normal use. The end of the material
being cut may become a projectile as it separates
during cutting. Stay clear of the cutting head and
surrounding area during operation. Always wear face
and eye protection.
• As needed, remove any foreign objects from
the cutting head that could damage the cutter
and/or injure the operator. Before removing
any foreign objects, always stop the cutter and
disconnect it from AC power supply.
• Avoid touching the cutter’s metal surfaces during
operation and after the cutter has been in use. Be
aware of the risk of burns if the cutter becomes hot.
• Do not use the cutter for activities other than those
it was approved and designed to perform. Refer to
Section 9.1 of this manual for additional information
regarding foreseen use.
• Use the cutter’s built-in handle when lifting or moving
the cutter. Use appropriately rated lifting equipment
if it is necessary to lift the tool by mechanical means.
• Do not exceed equipment ratings. Never attempt to
cut an item which exceeds the maximum allowable
parameters for your cutter model. For additional
information, refer to Section 2.1 of this manual.
Overloading may cause equipment failure and
possible personal injury.
• Do not use the cutter in explosive atmospheres
(for example, in the presence of flammable liquids,
gasses or powders).
• Do not use the cutter on live electric lines, on
pressure vessels or ducts, or on vessels containing
corrosive and/or toxic substances.
• If the cutter malfunctions, stop use immediately.
Check for misaligned or jammed moving parts,
broken components and any other condition that
could make the tool operate incorrectly. Place the
cutter back into operation only after the fault has
been identified and the identified repairs and/or
adjustments have been performed.
• Ensure that any repairs are performed only by
trained, qualified and authorized sta using original
equipment replacement parts. For repair service,
contact the Enerpac authorized service center in
your area.
• Use only original equipment Enerpac parts. Enerpac
parts are designed to fit properly and to withstand
high loads. Non-Enerpac parts may break or cause
the product to malfunction.
• Keep cutting tools clean and replace blades when
they become dull. Suitably maintained cutting tools
with sharp edges are less likely to jam and are easier
to control.
• Keep this manual for future reference in a place that
is accessible to all persons operating or servicing the
cutter.
• Always perform a visual inspection of the cutter
before placing it into operation. If any problems are
found, do not use the tool. Make repairs before using
the cutter.
• Do not use the cutter if it is leaking oil. Do not use the
cutter if damaged, altered or in need of repair.
• Do not remove or disable cutter safety devices.
Before using the cutter, make sure that all the safety
devices (guards, etc.) are in place and in good
condition.
• Do not remove the guards installed on the cutter or
on any accessories. Replace any guards immediately
if they develop faults or become damaged.
• Do not alter the calibration of the safety devices,
such as maximum pressure valves (if equipped).
• Allow only authorized, trained, and experienced
personnel to operate the cutter and supervise its use.
• Ensure that all users are trained and qualified to
operate the cutter. Operators must be aware of
all applicable occupational safety laws and must
operate the cutter in accordance with all such laws.
• Keep the work area clean and well illuminated.
• When operating the cutter, do not wear loose
clothing or jewelry that could get caught up in the
cutter during operation. Tie up long hair.
• Always wear and use appropriate personal protective
equipment (PPE) such as non-skid safety shoes,
hard-hat, hearing protection and face and eye
protection. Use of these and other PPE items (used
as appropriate for conditions) will reduce the chance
of personal injuries. The use of these items may also
be required by local regulations or laws.
• Consult your employer concerning specific safety
requirements and the safety equipment required for
use in your country or region.
• Before reaching inside the cutting area for any
reason, always stop the cutter and disconnect it from
the AC power supply.
• Keep others clear of the work area while the tool is
in use. Be sure that all personnel not operating the
cutter remain at a safe distance when the cutter is
in operation.
• Stop the cutter if people and/or animals enter the
work area.
• Ensure that the operator is alert, observant of the
task being performed and that the work is being
done with care.
• Do not allow use of the cutter by persons that are
tired, or under the influence of drugs, alcohol or
medication.
• Do not allow children to operate the cutter or to assist
with its use. Keep children out of the work area.

3
• Do not expose the tool to heat sources in excess of
158°F [70°C] as this could cause irreversible damage
to cable insulation and other electrical components,
possibly leading to a fire. If tool becomes overheated,
allow tool to cool or remove heat source.
• The tool is designed for noncontinuous use. Allow
suciently long pauses to allow the oil to cool.
Consult Enerpac if prolonged and/or uninterrupted
use is required.
• Do not service or clean the tool, or replace blades
or guards, while the tool is operating and/or if tool is
connected to AC power supply.
• Keep electric tools out of the reach of children. Do
not allow inexperienced users or users who have not
read the instructions to operate them. Electric tools
are dangerous in the hands of non-expert users.
• In accordance with the standards indicated and
followed by the manufacturer, the equipment
components that also perform a safety function
(insulators, guards, etc.) must not be repaired, but
must instead be replaced with original spare parts.
1.4 Additional AC Electric Tool Safety Instructions
NOTICE:
WARNING
Failure to observe and comply with
the following precautions and instructions could
result in death or serious personal injury.
1.4.1 Use and Care
• Store the tool indoors. Keep in a secured area to
prevent use by unauthorized personnel.
• Do not clean the tool with a water spray or the like.
• Do not operate the tool with a damaged cord or
plug, or after the tool malfunctions or is dropped or
damaged in any manner.
• Return the tool to the nearest Enerpac authorized
service center for examination, repair, or electrical or
mechanical adjustment.
1.4.2 Disconnecting Power
• Be sure that tool motor is o before removing plug
from electrical outlet.
• Do not unplug the tool by pulling on the cord. To
unplug, grasp the plug, not the cord.
• Remove plug from electrical outlet when the tool is
not in use and before servicing or cleaning the tool.
DANGER High voltage is present inside the tool
even when tool motor is o. Before servicing the
tool, be sure that the tool power cord is disconnected
from the electrical outlet or other electrical power
source.
CAUTION
Failure to observe and comply with the
following precautions and instructions could result
in minor or moderate personal injury. Property
damage could also occur.
• To help ensure proper operation and best
performance, use only Enerpac HF hydraulic oil. Use
of any other oil may result in unsafe operation and/or
damage to tool. The Enerpac product warranty may
also be invalidated.
• Keep hydraulic equipment away from flames and
heat. Excessive heat will soften packings and seals,
resulting in fluid leaks. Heat also weakens hose
materials and packings.
• Protect all hydraulic equipment from weld spatter.
1.3 Safety Precautions - AC Powered Electric Tools
NOTICE:
WARNING
Failure to observe and comply with the
following precautions and instructions could result
in death or serious personal injury. Property damage
could also occur.
• Always be certain that tool is stopped and
disconnected from AC power supply before
performing any tool cleaning, maintenance or repair
procedures.
• Be certain that the tool is disconnected from the AC
power supply before reaching inside the cutting head
to clear jams, or for any other reason.
• Do not leave the tool unattended in the workplace
when connected to AC power supply. Take all
reasonable precautions to avoid unauthorized use.
• Take precautions so that the tool is not switched on
accidentally. Be certain not to press the trigger when
picking up the tool or when positioning it.
• If it is not possible to unplug the tool power cord from
the AC power outlet, the power must be turned o
and locked out at the AC power supply.
• Always disconnect the tool from AC power before
transporting it. If electric tools are transported while
the operator’s finger is on the trigger and AC power
is connected, accidents can occur.
• Do not use the tool if it cannot be switched on and o
using the trigger. Any tool that cannot be controlled
with the trigger is dangerous and must be repaired.
• Remove all wrenches and adjustment tools (if
present) before switching on the tool. A wrench or
adjustment tool attached to a rotating element of an
electric tool can cause personal injury.
• Make sure the cooling vents are unobstructed and
that the cooling surfaces are clean in order to avoid
dangerous overheating.

4
1.4.3 Grounding Instructions
DANGER Risk of electric shock! Connect the tool
only to a properly grounded outlet.
The tool is double insulated and equipped with a
polarized power plug.
The plug must be plugged into a polarized electrical
outlet that is properly installed and wired in accordance
with all local codes and ordinances.
• If the cord and/or plug are damaged, do not connect
the tool to a live electrical outlet. Repair or replace
the damaged items and be sure the polarized plug
is correctly wired before reconnecting the tool to
the outlet. Consult a qualified electrician if wiring
procedures are not completely understood or if there
is any doubt as to whether the tool is properly wired.
• Do not modify the plug provided with the tool.
If the plug will not fit in the outlet, have a proper
outlet installed by a qualified electrician. A qualified
electrician should be consulted if there is any doubt
as to whether an outlet box is properly wired.
• All 230V tool models: The tool is for use on a single-
phase circuit, which has a nominal rating of more
than 120 volts and is factory equipped with a specific
electric cord and plug.
• If the tool must be used with a dierent type of
electric socket, the plug should be changed by
a qualified electrician. After the plug is changed,
the tool should comply with all local codes and
ordinances.
1.4.4 Use of Extension Cords
It is important to use the proper size extension cord with
the tool power cord when use of an extension cord is
necessary.
A qualified electrician should be consulted to help
specify and select the proper size extension cord.
DANGER Risk of electric shock! Connect the tool
only to a properly wired outlet.
If an extension cord is used:
1) The marked electrical rating of the extension cord
should be at least as great as the electrical rating of the
tool.
2) The extension cord should have a polarized plug
at one end and a polarized receptacle at the other. It
should be wired for single phase power.
3) A long extension cord should be arranged so that it
will not drape over any working area where it can be
tripped over, snagged, or pulled on unintentionally.
If the tool is to be operated outdoors and an extension
cord is needed, use only an outdoor-use extension cord.
An outdoor-use extension cord will be clearly marked
with the sux letter “W” and the statement “Suitable for
Use with Outdoor Appliances.”
1.4.5 Additional Precautions
NOTICE:
WARNING
Do not use electric powered tools in an
explosive atmosphere. Sparks and electrical arcing
could ignite combustible vapors or airborne dust.
NOTICE
To prevent damage to the tool electric motor,
check power specifications on tool data plate. Use of
incorrect outlet will damage the motor.
1.5 Safety Symbols (located on cutter)
WARNING
Failure to observe and comply with the
safety symbols axed to the cutter housing could
result in death or serious personal injury.
WARNING
Make sure the safety symbols (decals,
labels, etc.) are securely axed to the tool and that
they are legible. If not, obtain replacements from
Enerpac. Refer to tool repair parts sheet for locations
and part numbers. Failure to maintain safety symbols
on tool could result in death or serious personal
injury.
The following safety symbols are axed to the cutter
housing:
Crush hazard: Keep hands, fingers and other
body parts away from the cutting head during
operation.
Projectile hazard: Objects may be ejected
from the cutter during operation. Stay clear of
cutting area. Wear eye and face protection.
PPE Alert: Wear personal
protective equipment
(PPE) when using or
servicing equipment.
Instruction Manual Alert: Read the
instruction manual before using or servicing
equipment.

5
1.6 Crush Hazard
DANGER
Cutter will start immediately when
connected to AC power supply and on-o trigger is
depressed.
DO NOT place hands, fingers or other parts of your
body inside the cutting head unless cutter is
disconnected from AC power supply. Death or
serious personal injury will result if cutter is started
while persons are working inside the cutting head.
• Never reach into the cutting head while cutter is in
operation.
• Before reaching inside the cutting head for any
reason, always stop the cutter and disconnect it from
AC power supply.

6
Product specifications are subject to change without notice.
2.0 PRODUCT DATA
2.1 Cutter Maximum Capacities
Material to be Cut Cutter
Model No.
Material Maximum
Height Width Tensile Strength Hardness
in mm in mm psi daN/mm2Rockwell C
Flat metal bars
EFBE5017B 1.96 50 0.67 17 65,267 45 33
EFBE5017E 1.96 50 0.67 17 65,267 45 33
NOTICE
Material to be cut must not exceed any of the stated maximum limits shown in this table.
Cutter may stall during operation if one or more of the maximum limits is exceeded.
2.2 General Specifications
Cutter
Model No.
Max. Cutting
Force Weight
Max. Hydraulic
Operating
Pressure
Ambient
Operating Temp
Hyd.
Pump
Tons kN lb Kg psi bar °F °C Type
EFBE5017B 29.8 265 46 21 8702 600 -40
to
+ 122
-40
to
+ 50
Internal
AC
Electric
EFBE5017E 29.8 265 46 21 8702 600
2.3 Power and Noise Level Specifications
Cutter
Model No. Volts Hz Watts Amps Insulation
Class
Noise Level (typical)
No Load
LWA
†
No Load
Operator
LpAB
EFBE5017B 120 60 1300 11.0 II 101 90
EFBE5017E 230 50 1400 6.8 II 101 90
Notes:
†Per CEI EN 60745-1 and CEI EN 60745-2-8 [dB]. B Per CEI EN 60745-1 and EN ISO 5349.
2.4 External Dimensions
Dimension in mm
A
CB
A 19.0 483
B 6.9 175
C 10.7 272

7
12
123
7
6
9
8
45
11
10
Figure 1, Features and Components
Key:
1. Cutting Head with Fixed Blade
2. Piston and Moving Blade
3. Piston Release Lever
4. Trigger On-O Switch
5. Grip/Handle
6. AC Power Cord
7. Electric Motor
8. Hydraulic Cylinder
9. Support Bolt
10. Fixed Blade
11. Oil Reservoir
12. Storage Case
3.0 CONFORMANCE TO NATIONAL AND
INTERNATIONAL STANDARDS
Enerpac declares that this product has been
tested and conforms to applicable standards
and is compatible with all CE requirements.
A copy of an EU Declaration of Conformity is
enclosed with each shipment of this product.
4.0 DESCRIPTION
The Enerpac model EFBE5017 is a fixed-head hydraulic
cutter designed to cut flat metal bars.
The cutter contains two blades, one fixed and one
moving. The moving blade is actuated by a hydraulic
cylinder.
Hydraulic force is provided by an AC powered electric
motor and an internal hydraulic pump. The pump
provides oil flow to the hydraulic cylinder, which
advances the cylinder piston and moving blade.
A hydraulic reservoir with built-in rubber diaphragm
provides a constant supply of oil to the pump, regardless
of tool orientation or the amount of piston extension.
A trigger style on-o switch, mounted on the cutter grip,
starts and stops the electric motor. The trigger must
remain pressed during the cutting process.
An automatic retract feature returns the piston to the
fully retracted “home” position when the piston reaches
its full stroke and the trigger is released.
See Figure 1 for a description of cutter major features
and components. Refer to Sections 2.1 through
2.4 of this manual for maximum cutting capacities,
specifications and dimensions.
5.0 RECEIVING INSTRUCTIONS
Visually inspect all components for shipping damage.
Shipping damage is not covered by warranty. If shipping
damage is found, notify carrier at once. The carrier is
responsible for all repair and replacement costs resulting
from damage in shipment.

8
8.0 MAJOR FEATURES AND COMPONENTS
8.1 Trigger On-O Switch
NOTICE:
WARNING
To prevent serious personal injury, be
certain that hands, fingers and other body parts are
away from the cutting area before depressing the
cutter trigger.
A trigger mounted in the cutter grip controls cutter
operation. Pressing the trigger automatically starts the
cutter electric motor.
• Press and hold the trigger to advance the piston and
slide the moving blade forward. See Figures 2 and 3.
• Release the trigger at any time to stop the piston and
moving blade. Be advised that there may be a brief
delay until the piston comes to a complete stop.
• After the piston is fully advanced the piston will
automatically reverse direction and move to the fully
retracted “home” position. See Figure 4.
• Automatic return can occur only after the piston has
been fully advanced. If the trigger is released before
the piston is fully advanced, the piston will stop and
remain stopped.
Figure 2, Trigger On-O Switch
Figure 3, Piston and Blade Fully Advanced
6.0 SET-UP
6.1 Delivery and Handling
The cutter and various related items are housed inside a
plastic storage case. The cutter should be stored in this
case when not in use.
Place the cutter on a substantial and stable work
surface. The work surface must be of sucient capacity
to support the weight of the cutter plus the additional
weight of the material to be cut. Refer to Section 2.2 for
cutter weight.
6.2 Before Startup
• Be sure that the shipment includes all components
and that there is no obvious damage.
• Read the following sections of this manual to become
familiar with cutter features and safety devices.
• Verify that the AC power supply is of the correct
specifications and capacity to power the cutter. Refer
to Section 7.0 of this manual for additional information.
NOTICE
Be sure that cutter piston is advanced as far
as possible before removing oil reservoir cap in the
next step. Oil leakage and improper operation may
result if this instruction is not followed.
• Advance the piston as far as possible, disconnect AC
power cord and check the cutter hydraulic oil level.
Add oil if oil level is low. Refer to Section 10.5.2 for
detailed instructions.
• Be sure that the piston release lever is fully tightened.
Refer to Section 8.2.
• Before first use, remove air from the cutter hydraulic
system. Refer to procedure in Section 9.3.
7.0 POWER REQUIREMENTS
The cutter is available in two versions, each with dierent
electrical power requirements:
Model EFBE5017B is designed for 120VAC, single-
phase, 60 Hz power. This version contains a USA style
NEMA 6-15 power plug.
Model EFBE5017E is designed for 230VAC, single-
phase 50 Hz power. This version contains a European
style “Schuko” power plug.
Before connecting electric power to tool, be certain that
the power supply is the proper voltage and Hz for the
cutter version that you are using. Refer to the cutter data
plate.
Also refer to Sections 1.3 and 1.4 of this manual for
important electrical safety information and precautions.
NOTICE:
WARNING
Failure to follow the electrical safety
precautions contained in Sections 1.3 and 1.4 of this
manual could result in electric shock. Death or
serious personal injury could occur.

9
Figure 4, Piston and Blade Fully Retracted
(“Home”) Position
8.2 Piston Release Lever
See Figure 5.
Before using the cutter, check that the piston release
lever is moved fully clockwise to position 1. This will
ensure that the piston automatically retracts and returns
to the home position after it reaches the end of its travel.
In the event that the blade becomes stuck during
cutting, move the piston release lever counterclockwise
to position 2, to manually release and retract the piston.
The piston will return immediately to the home position,
assuming that no dirt or debris is preventing its return.
NOTICE:
CAUTION
To prevent possible oil leakage, do not
loosen the piston release lever more than one full
turn counter-clockwise.
NOTICE
Refer to the procedures in Section 11.0 of this
manual if the blade is not returning due to accumulated
dirt or debris.
Return the piston release lever to position 1 to resume
normal operation. Note that the piston will not advance
when the lever is in position 2.
Be advised that the piston release lever is intended
for occasional use only. If the piston repeatedly fails to
retract automatically after it is fully extended, have the
tool inspected by an Enerpac authorized service center.
2
1
Figure 5, Piston Release Lever
Key:
1. Position 1 (normal operation)
2. Position 2 (piston release)

10
• Injury due to incorrect positioning or inadequate lifting
or moving.
• Injury caused by splinters discharged from the
workpiece.
NOTICE:
WARNING People remaining in the vicinity of the
cutter while it is working are subject to the risk of
flying debris (dangerous objects, etc. ). Serious
personal injury could result.
4. Mechanical vibrations transmitted to the hands and
arms can pose a risk to the health and safety of
workers. The user and/or employer is responsible for
assessing the risk generated by mechanical vibrations
from the cutter, and minimizing the possibility of
injury.
5. Incorrect use:
• The cutter must not be used for purposes other than
indicated in this manual.
• The cutter must not be used in areas subject to the
risk of explosion.
9.0 CUTTER OPERATION
9.1 Foreseen Use and Residual Risks
NOTICE:
WARNING Failure to observe and comply with the
instructions and precautions contained in the
following paragraphs could result in death or serious
personal injury.
1. The cutter must be used only to cut flat metal bars.
Material parameters must not exceed the allowable
values shown in Section 2.1 of this manual.
2. The cutter may be used only if powered by an electrical
system compliant with legislation and current law
(suitably connected to a grounded electrical system
and protected from current surges and short circuits).
3. Operators must observe the instructions in this
manual in order to minimize the risk of accidents. In
particular, operators must pay attention when working
in conditions that could cause:
• Possible burns from overheated metal parts.
90° 90°
A
A
Figure 6, Positioning Material Inside Cutting Head
Support Bolt
Vertically center the material
in the cutting head
Material Position (Optimum)

11
9.2 Operating Precautions
NOTICE:
WARNING Failure to observe the following
precautions and instructions could result in death or
serious personal injury.
• Keep fingers, hands and other body parts clear of
the cutting head. Do not reach into the cutting area
during cutter operation.
• Do not attempt to reposition the item being cut
while the cutter is in operation. If repositioning is
required, stop the cutter and loosen the piston
release lever to retract the piston. Then, tighten the
piston release lever and repeat the cutting process.
• Dangerous projectiles could occur at any time
during cutting. Always wear face and eye protection.
Keep persons away from cutting area.
• Cutter surfaces can become very hot. To prevent
burns, avoid contact with cutter components and
wear appropriate personal protective equipment.
•
Refer to additional safety precautions in Section 1.0
of this manual before using the cutter or performing
any maintenance or repair activities.
9.3 Trapped Air Removal
Before placing a new cutter into operation, cycle the
piston several times without load to remove any trapped
air in the hydraulic circuit.
Air is completely purged when the piston advances and
retracts smoothly in both directions, from fully advanced
to fully retracted.
This procedure should be performed after the oil in the
cutter is changed, and after any maintenance or repair
activity in which the oil is drained and replaced.
9.4 Locating and Positioning the Cutter
• Before inserting material to be cut inside the cutting
head, be certain that the cutter is placed on a solid
and stable work surface of sucient weight rating
capacity. Refer to Section 2.2 for cutter weight.
• Position the cutter as needed using the handle/grip
mounted at the top of the cutter. The handle/grip
can also be used for transporting the cutter short
distances.
NOTICE:
WARNING
Because the cutter components are very
heavy, there is a risk of cuts, crushing or broken bones. To
avoid accidents, use care when working with the cutter.
Serious personal injury may result if the cutter is not
properly supported and handled in an appropriate way.
9.5 Positioning Material Inside the Cutting Head
Be sure that the piston and moving blade are located in
the fully retracted “home” position before placing any
material inside the cutting head. See Figure 4.
Position the material to be cut between the cutter
blades, so that it is perpendicular to the piston axis, as
shown in Figure 6. This will provide the best quality cut
while placing the least amount of load on the cutter. If
possible, center the material vertically to help reduce
side-loading of the piston.
Adjust the support bolt as needed. The head of the
support bolt should just touch the surface of the material
to be cut, when the item is positioned against the fixed
blade of the cutter.
After adjusting the support bolt, be sure that the support
bolt retaining nut is snug tight against the support
bolt mounting ear. This will help prevent support bolt
movement during cutting.
NOTICE
Be certain that the maximum parameters of the
material to be cut are within allowable limits. Refer to
Section 2.1 of this manual for additional information.
Failure to observe this instruction may result in poor
cutting performance and/or damage to the cutter.
9.6 Cutting Procedure (typical)
1. Connect the cutter to the electrical outlet.
2. Be sure that the piston is in the “home” (fully retracted)
position. See Figure 4.
3. Be sure that the piston release lever is turned fully
clockwise to position 1. See Figure 5.
4. Place the material to be cut between the fixed and
moving blades. Refer to instructions in Section 9.5 for
additional information.
NOTICE
Position the item to be cut so that it is as
perpendicular as possible to the blades, as described in
Section 9.5. Positioning the material at an angle will
side-load the piston. Jamming and/or damage to the
cutter may result.
5. Be certain that hands, fingers or other body parts are
not inside the cutting head.
6. Press and hold the trigger to start the motor and begin
cutting.
7. After cutting is completed, wait until the piston
reaches the end of its stroke and then release the
trigger. Verify that the moving blade reverses direction
and moves fully into the “home” (fully retracted)
position.
Figure 7, Material Being Cut (typical - top view)

12
NOTICE:
WARNING
The cutter must sometimes be
operated in order to complete a maintenance or
repair procedure being performed, or to prepare it
for a procedure that is about to be performed.
However, to prevent startup while persons are
working on the cutter, always disconnect the cutter
from the AC power supply before beginning any
procedure steps that require use of tools and/or
physical contact with the cutter. Failure to observe
this precaution may result in death or serious
personal injury.
Table 1 - Periodic Maintenance Chart
Time Interval Maintenance Operation Method To be performed by:
Every 8 hours of
operation:
Check the cutter for loose,
damaged or worn parts.
Check for oil leaks. Tighten,
replace or repair as required.
Visual Operator
Clean the cutter exterior. Refer to instructions in
Section 10.3.
Operator
Clean the cutter piston. Refer to instructions in
Section 11.1 and 11.2.
Operator
Check the tightening torque
of screws and bolts. Replace
any missing screws or bolts.
Use torque wrench. Refer to
repair parts sheet for complete
torque specifications.
Operator
Every 1600 hours
of operation:
Change the hydraulic oil. Refer to instructions in
sections 10.5.1 - 10.5.3.
Service Center
As required: Replace fixed blade. Refer to instructions in
Section 10.6.2.
Operator
Replace moving blade. Refer to instructions in
Section 10.6.3.
Operator
10.0 MAINTENANCE
10.1 Preparation for Maintenance
All cutter maintenance procedures must be performed
under the following conditions:
• Material must be removed from the cutting head.
• The cutter must be disconnected from the AC power
supply.
• The cutter must be given time to cool to prevent burns.
• Procedures must be performed in a suitable work
environment in accordance with all current safety
regulations and/or laws in your country or region.
• The cutter must be cleaned thoroughly before
maintenance procedures are performed.
• Suitable personal protective equipment (PPE) must be
used and/or worn while performing any work.
10.2 Periodic Maintenance Chart
Refer to the Periodic Maintenance Chart (Table 1) for a
list of various routine checks and procedures.
10.3 Cleaning
• Clean the cutter using a dry cloth or compressed air.
For plastic surfaces, use a cloth slightly dampened
with water.
NOTICE:
CAUTION
To prevent possible injury, always wear
safety glasses or face mask when using compressed
air.
• Be sure there are no traces of oil, grease or corrosive
substances on the tool, especially on the grips.
• Use a damp cloth and soapy water to clean plastic
components.
• Do not use gasoline or thinner to clean the tool.
10.4 Fasteners
Periodically check all screws, nuts and other fasteners
for proper tightness. Tighten any loose fasteners.
Replace any worn or damaged fasteners. This should
be performed periodically or every day in the event of
frequent or prolonged cutter operation.
NOTICE
Failure to check and tighten fasteners as
required may result in serious damage to the cutter.
10.5 Cutter Hydraulic System
The cutter contains a small hydraulic pump and an oil
reservoir with a rubber diaphragm. The oil level must be
periodically checked and additional oil must be added if
the oil level is low. In addition, the oil must be completely
changed at the specified interval. Refer to the Periodic
Maintenance Chart (Table 1).

13
4. To prevent contamination, remove any built-up dust
and dirt from the oil reservoir cap and surrounding area.
NOTICE
A small amount of hydraulic oil may leak from
the drain/fill hole when cap is loosened in the next step.
Be prepared to catch this oil in a pan or with a clean rag.
Dispose of spilled oil in accordance with all applicable
laws and regulations.
5. Slowly loosen the oil reservoir cap while watching for
oil flow:
• If oil starts flowing from the oil drain/fill hole as the
cap is loosened, the reservoir is full. Tighten the
cap immediately. To avoid excessive oil spillage,
do not continue loosening the cap if oil flow
occurs. Skip steps 6 through 8 and go on to step 9.
• If no oil flow occurs when the cap is loosened,
fully loosen and remove the cap. Then, check
oil level and add oil (if needed) as described in
steps 6 through 8.
6. Check the oil level in the drain/fill hole. Oil level will be
up to the top of the hole when reservoir is full.
7. If oil level is low, slowly add new Enerpac HF oil
through the oil drain/fill hole, until the oil level is up to
the top of the hole.
8. Remove any residue or metal particles from the oil
reservoir cap (it is magnetic).
9. Install and securely tighten the oil reservoir cap.
10. Using a clean rag, wipe the cutter housing, grip and
motor so that these surfaces are free of oil residue.
11. Connect cutter to AC power supply. Cycle the
piston several times to test for proper operation
before placing the cutter back into service.
10.5.3 Changing the Oil
NOTICE
The oil change procedure is very detailed and
will take a considerable amount of time. It should only
be performed by a trained technician at an Enerpac
authorized service center. Failure to properly perform
the procedure may result in incomplete filling of the
cutter oil reservoir, which could lead to cavitation, air
entrainment, reduced performance, and pump damage.
Change the oil in the cutter reservoir as described in the
following steps. Refer to Figures 8A through 8E:
1. Fill a clean oil dispenser with new Enerpac HF oil. Put
the dispenser aside for later use.
2. Procure a thick, soft metal bar (about 1/4 inch
[6.4 mm] minimum thickness). Put the bar aside for
later use.
NOTICE
The bar selected should be easy to cut, but not
brittle. The bar material must be soft enough so that the
bar will not break into two pieces before it is fully cut.
Later in this procedure, the bar will be partially cut so
that it becomes lodged in between the jaws of the cutter
without being cut through completely, as the piston is
extended to slightly less than maximum travel.
10.5.1 Hydraulic System Maintenance Precautions
NOTICE:
WARNING
Always disconnect cutter from AC power supply
before performing hydraulic system maintenance.
Failure to observe this precaution could result in
accidental startup while maintenance procedures
are being performed. Serious personal injury and
damage to cutter may result.
Wait for cutter to cool before performing hydraulic
system maintenance. Hot oil can cause burns.
Be sure that oil reservoir cap is securely tightened
after checking oil level or changing the oil. Leaking
oil can cause short circuits, fire and explosions.
Additional Precautions:
• Do not check oil level or change the oil in dusty areas.
• Be sure that all tools (wrench, screwdriver, etc.) used
to perform maintenance procedures are clean.
• When adding oil and performing oil changes, take every
precaution to prevent impurities from contaminating
the oil or entering the cutter. Impurities can cause
permanent damage to the hydraulic components.
• The hydraulic reservoir contains a rubber diaphragm
that slightly pressurizes the oil. Some oil spillage may
occur when checking the oil level or when changing
the oil. Wear and/or use appropriate personal
protective equipment (PPE) to prevent exposure to
hydraulic oil.
• Use only new Enerpac HF hydraulic oil poured from a
clean container. Use of other oil brands and/or used
oil may damage the cutter and may void the Enerpac
product warranty.
10.5.2 Checking Oil Level and Adding Oil
NOTICE
The reservoir contains a flexible rubber
diaphragm that slightly pressurizes the oil. To help prevent
excessive oil leakage when the reservoir cap is removed,
be certain that the piston is advanced until there is a gap
of about 1/8 inch [3-4 mm] between the fixed and moving
blades (as described in step 1) before loosening the cap.
The gap between the blades should not be less than
1/8 inch [3-4 mm]. A smaller gap may result in the
piston retracting unexpectedly while the oil level is being
checked.
Refer to Figures 8A through 8E during the following steps:
1. Operate the cutter and advance the piston until
there is a 1/8-inch [3-4 mm] gap between the fixed
and moving blades (until just before the piston
automatically returns).
2. Disconnect the cutter from the AC power supply to
prevent accidental motor startup during the following
steps.
3. Place the cutter in the horizontal position, on a stable
and level work surface, with the oil reservoir cap
facing upwards. Place a pan or suitable container
under the cutter to catch any spilled oil.

14
Figure 8, Hydraulic System Maintenance
Figure 8C, Oil Reservoir Cap - Loosen (1) and
Tighten (2)
21
Figure 8B, Handle Screws (1)
1
1
Figure 8D, Adding Oil to Reservoir Fill Hole (1)
3
2
1
4
5
Figure 8E, Screws (1), Diaphragm Cover (2),
Diaphragm (3), Diaphragm Opening (4) and
Reservoir (5)
Figure 8A, Oil Reservoir Cap (1)
1

15
3. Disconnect the cutter from the AC power supply to
prevent accidental motor start-up during the following
steps.
4. Place the cutter in an upright position, on a stable and
level work surface, with the handle facing upwards.
Place a pan or suitable container under the cutter to
catch any spilled oil.
5. To prevent contamination, remove any built-up dust
and dirt from the oil reservoir cap, diaphragm cover,
and surrounding area.
NOTICE
When the handle is removed the wires from the
trigger on-o switch will still be connected to the electric
motor. Take care not to pull or stretch the wires when
removing the handle or when performing the oil change
procedure.
6. Remove the screws holding the tool handle in place.
Carefully remove the tool handle to gain access to the
diaphragm cover. The tool handle wiring will still be
connected, so use caution to avoid damaging this
wiring.
NOTICE
A small amount of hydraulic oil leakage may
occur when the diaphragm cover is removed in the next
step. Be prepared to catch this oil in a pan or with a
clean rag. Dispose of spilled oil in accordance with all
applicable laws and regulations.
7. Remove the diaphragm cover by removing the six
screws securing it.
8. Remove the diaphragm from the diaphragm opening.
9. Completely drain all old oil from the cutter through the
diaphragm opening, turning it upside down and using
a suitable oil extraction system (used oil extraction
pump) if necessary, so that no oil remains in the cutter
reservoir.
NOTICE
Dispose of all used oil in accordance with all
applicable regulations and laws.
10. After all oil is evacuated, position the cutter with the
diaphragm opening facing up.
NOTICE
Use only new Enerpac HF oil in the following
step. Use of other oils may damage the cutter and may
invalidate the Enerpac product warranty.
11. Using the oil dispenser prepared in step 1, slowly
add new Enerpac HF oil through the diaphragm
opening until the diaphragm opening is nearly full.
NOTICE:
WARNING
To avoid serious personal injury, stay
clear of cutting head and blades during the following
procedures. Wear rubber gloves to prevent contact
with oil. Wear eye and face protection to avoid injury
due to splashing oil.
NOTICE:
WARNING In the following steps, the tool must be
operated with the handle separated from the tool
housing. Use extreme caution to prevent injury as
service procedures are being performed.
12. Connect the cutter to the AC power supply.
13. Cover the diaphragm opening with a rubber-gloved
hand to help prevent oil splashing.
14. Prime the pump by pressing and releasing the
trigger in short bursts. During this process, check
the oil level in the diaphragm opening and add oil
(as needed) to keep the reservoir filled. Failure to
keep reservoir full may result in cavitation and
pump failure. Pump is primed when piston starts
extending.
NOTICE
During priming, the oil may become entrained
with air and may develop a foamy appearance. This is
normal.
15. Continue pressing and releasing the trigger in short
bursts as the piston extends. During this part of the
process, do not add oil, but verify that the pump has
ample oil supply. Continue until piston is extended
to approximately half stroke.
NOTICE
During the following steps, refer to Figure 5 for
piston release lever positions.
16. While covering the diaphragm opening with a
rubber-gloved hand, retract the piston gently by
slowly moving the piston release lever to position 2.
17. Move the piston release lever back to position 1 and
tighten.
18. Place the soft metal bar (refer to step 2) into the
cutting head.
19. Press and release the trigger in short bursts until
the piston is extended as far as possible, but before
it makes a full cut and retracts. The moving blade
will become lodged in the bar, preventing the
piston from retracting. This procedure is necessary
because the cutter mechanism alone may fail to
hold the piston in the partially extended position as
oil is being added in the following steps.
NOTICE
If you cut completely through the bar, try again,
cutting as far as you can without making a full cut.
20. Disconnect the cutter from the AC power supply
to prevent accidental motor start-up during the
following steps.
21. Add oil through the diaphragm opening until the
diaphragm opening is nearly full.
22. Slowly install the diaphragm in the diaphragm
opening. This should result in some oil leakage from
around the diaphragm.
23. Install the diaphragm cover and securely tighten the
six screws securing it.
24. Reinstall the tool handle. Be certain that electrical
wires are not pinched between tool housing and
handle.
25. Move the piston release lever to position 2 to retract
the piston. If piston is stuck, use the bar to manually
push the piston back until it retracts.
26. Remove the soft metal bar from the cutting head.
Do not discard the bar. It will be used again later in
this procedure.

16
10.6 Cutter Blade Replacement
NOTICE:
WARNING
• Always disconnect cutter from AC power supply
before beginning blade replacement procedures.
Failure to observe this precaution could result in
accidental startup during blade replacement. Serious
personal injury could result.
• Use extreme caution when removing and installing
blades. Blades may be sharp even when worn. To
avoid hand injury, wear appropriate personal
protective equipment (PPE) and avoid contact with
blade cutting edges.
10.6.1 Blade Wear
The use of worn blades decreases the eectiveness of
the cutter and can also side load the cylinder, resulting
in possible damage to the tool. Motor overheating can
also occur.
Replace blades immediately if they are worn and/or
damaged or if there has been a noticeable decrease in
cutting performance.
NOTICE
Blades are not sharpenable and must be
replaced when worn. To help ensure optimum cutting
performance, replace both the fixed blade and the
moving blade at the same time.
27. Move the piston release lever to position 1 and
tighten.
28. Connect the cutter to the AC power supply.
NOTICE:
WARNING
To avoid serious personal injury, stay
clear of cutting head and blades during the following
procedures.
29. Start the cutter and cycle the piston through several
advance and return strokes. Ensure that piston is
fully retracted when done.
NOTICE
Orient the oil reservoir cap facing upwards at
this time, and keep it as such until the cap is installed for
the final time. Failure to do so may result in air remaining
in the reservoir. This may require special consideration
when the soft metal bar is used.
30. Do not operate cutter for several hours (preferably
overnight) to allow any remaining air to separate
from the oil.
31. Place the soft metal bar (refer to step 2) into the
cutting head.
32. Press and release the trigger in short bursts until
the piston is extended as far as possible, but before
it makes a full cut and retracts. The moving blade
will become lodged in the bar, preventing the
piston from retracting. This procedure is necessary
because the cutter mechanism alone may fail to
hold the piston in the partially extended position as
oil level is being checked.
NOTICE
If you cut completely through the bar, try again,
cutting as far as you can without making a full cut.
33. Disconnect the cutter from the AC power supply
to prevent accidental motor start-up during the
following steps.
34. Loosen and remove the oil reservoir cap. Check
the oil level in the oil drain/fill hole. If oil level has
dropped, add additional Enerpac HF oil until the oil
level is up to the top of the hole.
35. Install and securely tighten the oil reservoir cap.
36. Move the piston release lever to position 2 to retract
the piston. If piston is stuck, use the bar to manually
push the piston back until it retracts.
37. Using a clean rag, wipe the cutter housing, grip and
motor so that surfaces are free of oil residue.
38. Connect the cutter to the AC power supply. Cycle
the piston several times to test for proper operation
before placing the cutter back into service.

17
Figure 9, Fixed Blade Replacement
1
2
10.6.2 Blade Replacement - Fixed Blade
Replace the fixed blade as described in the following
steps. Refer to Figure 9, items 1 and 2.
1. Be sure that the cutter piston is fully retracted. If not,
start the cutter and cycle the piston until it is fully
retracted.
2. Disconnect cutter from AC power supply to prevent
accidental motor startup during the following steps.
3. Place the cutter horizontally on a stable work surface
with the handle facing upwards.
4. Remove the fixed blade screws.
5. Remove the worn fixed blade and replace it with the
new fixed blade.
6. Secure the new fixed blade using the two new fixed
blade screws included with the new fixed blade. Apply
Loctite 243 thread sealant (or equivalent) to threads.
Torque to 18 ft-lb [25 Nm].
7. Test cutter for proper operation before placing it back
into service.
Key:
1. Fixed Blade Screws
2. Fixed Blade

18
1. Be sure that the cutter piston is fully retracted. If not, start
the cutter and cycle the piston until it is fully retracted.
NOTICE
If the piston will not retract in step 1, move the
piston release lever to position 2 to manually retract the
piston. Refer to instructions in Section 8.2. Also see
Figure 5.
2. Disconnect cutter from AC power supply to prevent
accidental motor startup during the following steps.
3. Place the cutter horizontally on a stable work surface
with the handle facing upwards.
4. Remove the moving blade screws and lock washers.
5. Remove the worn moving blade and replace it with
the new moving blade.
10.6.3 Blade Replacement - Moving Blade
Replace the moving blade as described in the following
steps. Refer to Figure 10, items 1, 2 and 3.
Figure 10, Moving Blade Replacement
1
3
2
NOTICE
If needed, use a screwdriver or small pry bar to
separate the worn moving blade from the mating surface
of the piston.
6. Secure the new moving blade with the new moving
blade screws and lock washers included with the new
moving blade. Apply Loctite 638 thread sealant (or
equivalent) to threads. Torque to 52.9 in-lb [5.98 Nm].
7. If piston release lever is in position 2, move lever
to position 1 to allow normal operation. Refer to
instructions in Section 8.2. Also see Figure 5.
8. Test cutter for proper operation before placing it back
into service.
Key:
1. Moving Blade Screws
2. Lock Washers
3. Moving Blade

19
Figure 11, Piston Manual Retract Procedure
2
1
3
Position 2
Position 1
Piston Release Lever
4. Using a rigid piece of steel bar, manually push the
piston inside the cutter until it is returned to the home
position. See Figure 11, item 3. This should dislodge
any dirt or other material that had prevented the
piston from returning during normal operation.
5. Move the piston release lever fully clockwise to
position 1. See Figure 11.
6. Connect cutter to AC power supply. Quickly depress
and release the trigger repeatedly until the piston is
advanced about 3/4 inch [19 mm].
7. Disconnect cutter from AC power supply to prevent
accidental motor startup during cleaning procedures
in the following step.
8. Clean the exposed portion of the piston. Remove any
debris, chips or dirt from this area. See Figure 11,
item 1.
9. Connect cutter to AC power supply and test cutter
for proper operation. Verify that piston automatically
returns to the “home” position after it is fully advanced
and the trigger is released.
NOTICE
If the piston still does not fully retract after
performing the previously described cleaning procedure,
the cutter should be inspected and serviced by an
Enerpac authorized service center.
11.0 CLEANING THE PISTON AREA
NOTICE:
WARNING Always disconnect cutter from AC
power supply before cleaning the piston head area
or before manually retracting the piston. Failure to
observe this precaution could result in accidental
startup during cleaning procedures. Serious
personal injury could result.
11.1 Cleaning and Inspection
• Keep the piston area clean to ensure that the piston
fully returns after it advances to maximum stroke.
• Remove any built-up dirt or debris from the cutting
head, the piston and moving blade.
11.2 Manually Retracting the Piston
The piston may fail to fully retract if debris is wedged
under or beside the piston and moving blade.
If this condition occurs, it may be necessary to manually
retract the piston into the cylinder to fully return the
piston to the “home” position.
Refer to the following steps. See Figure 11:
1. Disconnect cutter from AC power supply to prevent
accidental motor startup during the following steps.
2. Place the cutter horizontally on a stable work surface.
3. Move the piston release lever counterclockwise to
position 2. See Figure 11.
Position 1
(normal operation)
Position 2
(piston release)
Key:
1. Cutting Head
2. Piston
3. Bar (user-supplied)

20
13.0 TROUBLESHOOTING
Refer to the Cutter Troubleshooting Charts (Tables 2
and 3) for lists of common cutter symptoms, possible
causes and solutions.
For repair service, contact an Enerpac authorized service
center. Inspection and repairs should be performed
only by an Enerpac authorized service center or other
qualified hydraulic tool service facility.
12.0 STORAGE
12.1 Storage Guidelines
If the cutter will be stored for an extended period of time:
• Disconnect cutter from AC power supply.
• Thoroughly clean the cutter. Remove any loose
dust or dirt. Dry the cutter after completing cleaning
procedures.
• Lubricate the cutter metal surfaces using a clean oil-
moistened rag to provide added corrosion protection
during storage.
• Store the cutter in its plastic storage case, in a clean
and dry location, accessible only to authorized
personnel.
12.2 Return to Use (after storage)
Before using the cutter after an extended period of
storage or inactivity, perform the following steps:
• Check the hydraulic oil level and add oil if low. Refer to
instructions in Section 10.5.2.
• Check for oil leaks. Make repairs as required.
• Remove any traces of oil (if present) from the
handle/grip and other parts that can be gripped.
• Remove any oil from cutter metal surfaces.
• Check that the electrical power cord and plug are
undamaged and in good condition.
• Verify that the cutter housing (including the electric
motor) is undamaged.
• Check for any missing, worn or improperly installed
parts.
• Check that all screws, nuts, bolts and other fasteners
are tight. Replace, repair or tighten components as
needed.
• Connect cutter to AC power supply. Cycle the piston
several times to test for proper operation before
placing the cutter back into service.
Table of contents
Other Enerpac Cutter manuals
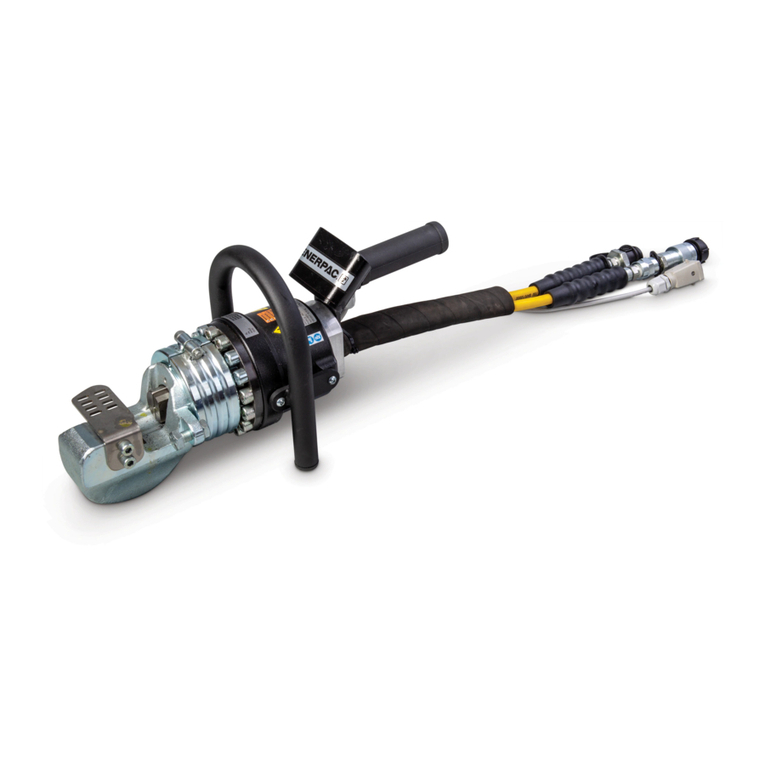
Enerpac
Enerpac EBH35 User manual
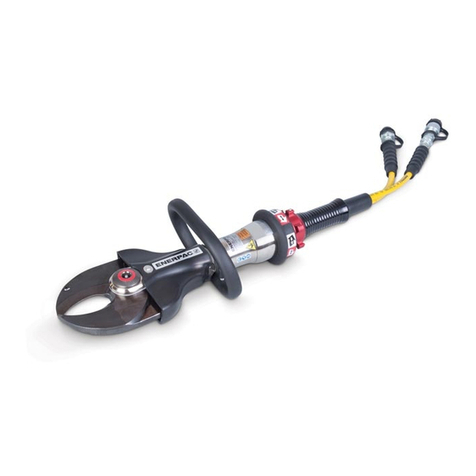
Enerpac
Enerpac EDCH130 User manual

Enerpac
Enerpac EWCH90 User manual
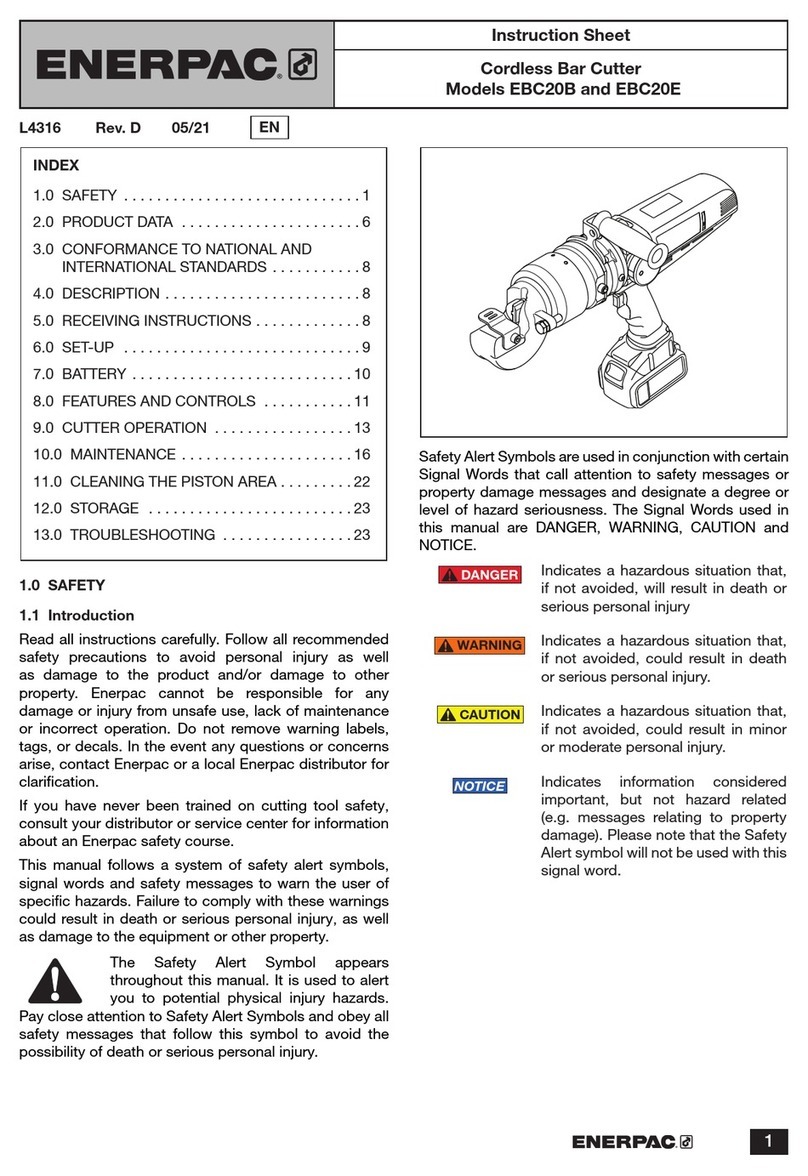
Enerpac
Enerpac EBC20B User manual
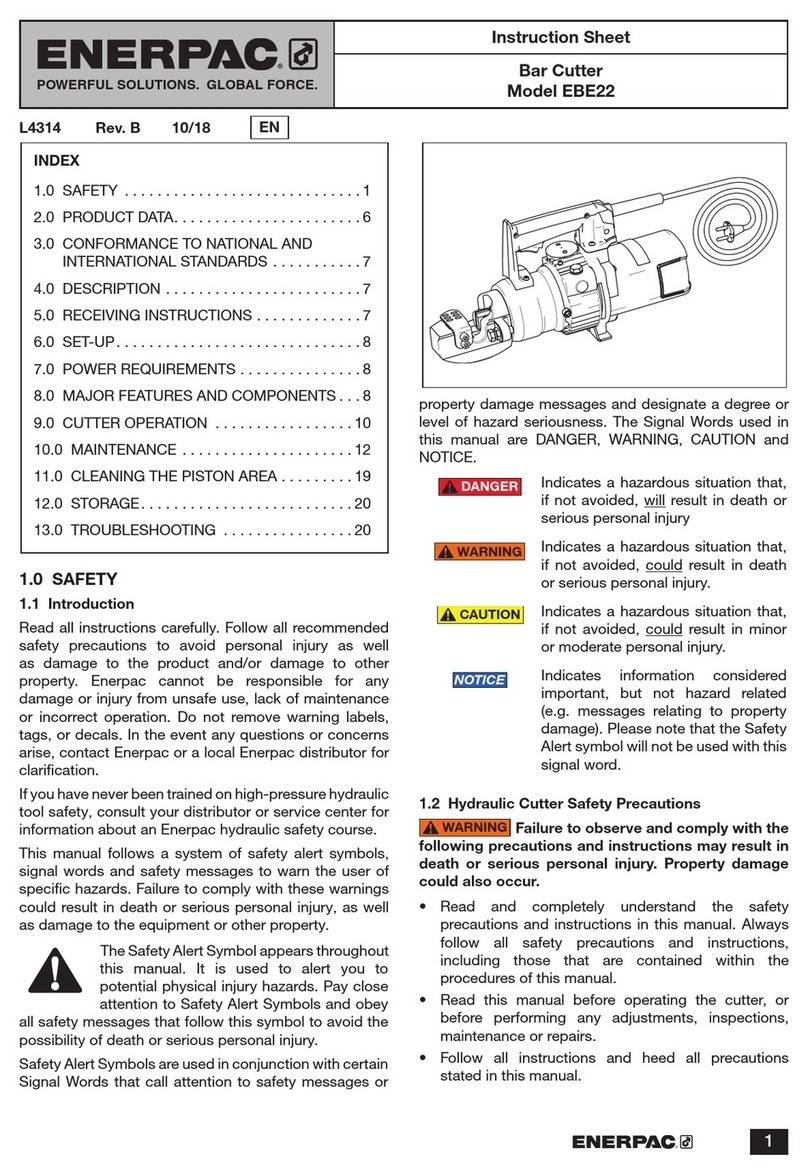
Enerpac
Enerpac EBE22 User manual
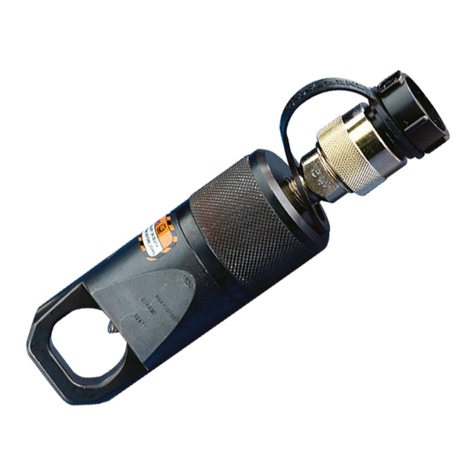
Enerpac
Enerpac NC-1319 User manual
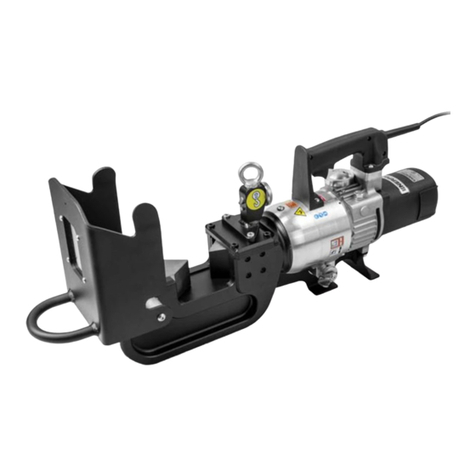
Enerpac
Enerpac ECCE32 User manual
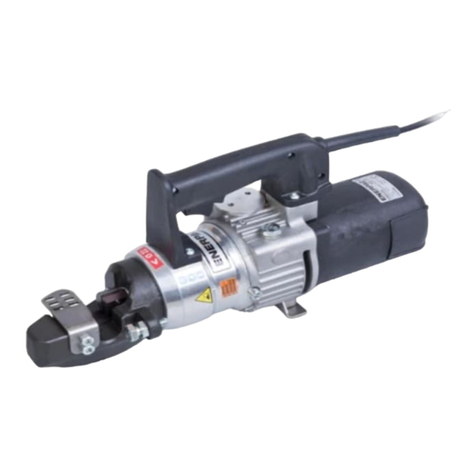
Enerpac
Enerpac EBE26 User manual
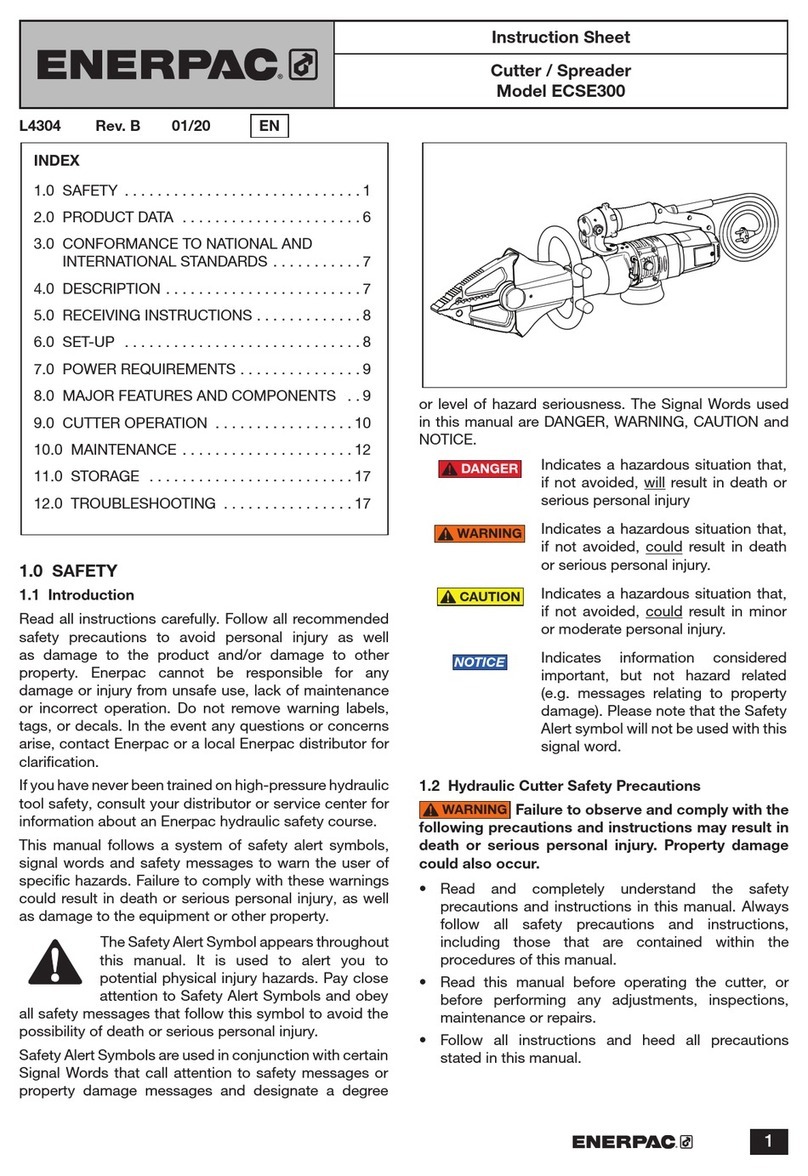
Enerpac
Enerpac ECSE300 User manual
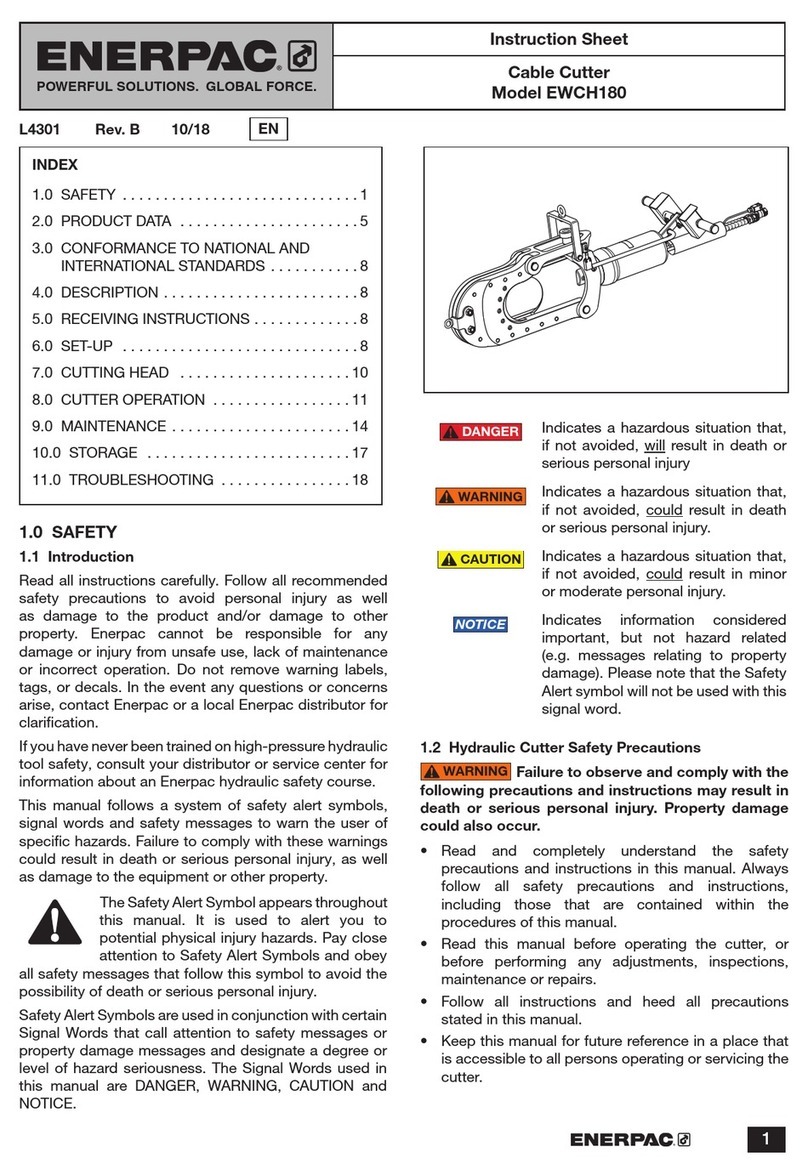
Enerpac
Enerpac EWCH180 User manual