esera automation Shutter Pro V4 User manual

Art. No. 11231
All rights reserved. Reproduction as well as electronic duplication of this user guide, complete or in part, requires the written consent of
ESERA GmbH. Errors and technical modification subject to change. ESERA GmbH, ESERA-Automation 2020
www.esera.de 11231 V2.0 R1.0 Manual Page 1 of 7
User Guide
Shutter Pro V4
for external roller shutters, awnings,
blinds or venetian blinds
and 1-Wire bus system
Operation purpose / area of operation:
Control of shutters, awnings, blinds or venetian blinds by
control or manual operation
Control of heating mixers
Equipment:
Standard 1-Wire interface and control input
Push-button interface for external DC voltage
Manual control via push-button
Control of powerful tubular motors through
robust module design
Automatic safety switch-off of the motor
LED display for up or down operation
DIN rail housing for control cabinet installation
screw terminal connection
New, with DS2408 interface
1 Introduction
Before you start assembling the Shutter Pro V4 and put the device into operation, please read this assembly and
operating instructions carefully to the end, especially the section referring to the safety notes.
2 Product description
With the Shutter Pro a motor or motor group* for external roller shutters, awnings, blinds or venetian blinds can
easily be controlled. An operation in combination with a heating mixer is also possible.
The Shutter Pro has three interfaces for control. Manual operation via push-button on the module surface, control
inputs for manual operation and the 1-Wire data interface.
The combination of the interfaces makes central and convenient automatic control as well as local decentralised
control possible. All three interfaces can be operated in parallel.
The roller shutter can be operated manually or automatic operation can be stopped at any time by means of
external up/down buttons, which are mounted in the area of the window, for example.
An external DC voltage in the range of 10-30V is used for the operation of the push-buttons.
The Shutter Pro has two modes of operation, which can be divided into the functions of the module push-buttons,
Up/Down and the external interface (push-button interface). The difference is that in this operating mode an
additional push-button function is available for tilting the external blinds (see table Push-button function, no. 6).
An integrated safety function automatically switches off the connected motor after 120 seconds.
If the running direction changes (up/down), a pause is automatically maintained to protect the mechanics of the
tubular motors and roller blinds.
All internal functions are controlled and monitored by a modern microcontroller.
*The use of one isolating relay per tubular motor is necessary to control roller shutter groups.

All rights reserved. Reproduction as well as electronic duplication of this user guide, complete or in part, requires the written consent of
ESERA-Automation or E-Service GmbH. Errors and technical modification subject to change. ESERA-Automation, E-Service GmbH 2020
www.esera.de 11231 V2.0 R1.0 Manual Page 2 of 7
3 Auto-E-Connect® Support
The ESERA Auto-E-Connect® 1-Wire Plug and Play system will be used for the
1-Wire Bus supported. This enables fully automatic configurations of 1-Wire sensors
and actuators on the 1-Wire bus. It is optimized for industrial applications and
enables significant added value beyond the sensor and chip data.
The Auto-E-Connect function automatically recognizes ESERA chips, sensors and actuators, starts suitable
libraries and outputs fully formatted data.
The Auto-E-Connect functionality will be available from mid 2020 via 1-Wire Controllers, 1-Wire Gateways and
1-Wire ECO from ESERA available.
Further information on ESERA Auto-E-Connect can be found on the ESERA website, ESERA Config-Tool 3, or in
the download area for this article in the ESERA Webshop.
4 Technical data
Type: Tubular motor with limit switches and separate connections for up/down
Number of channels: 1, groups can be controlled via isolating relays up to the max. module current.
Switching voltage: 5 to 230V DC or AC voltage
Switching current: max. 5A (internal fuse 5A slow blow)
Switching capacity: max. 1150VA
Safety switch-off: switch-off after 120 seconds
Control input function: 1. roller shutter or awning operation: control inputs for upwards, stop, downwards
2. external blinds or venetian blinds: button, short for tilting movement, button, long for
upwards movement, Stop, Down
During motor operation, the control inputs and module buttons can be used to stop the
movement.
Control inputs: Digital / binary input, 10-30VDC, max. 10mA, pulse duration min. 40ms, e.g. for push
button switch (NO contact)
Inputs isolated from 1-Wire interface and power supply
Isolation: Relay outputs isolated from 1-Wire bus and power supply
Function 1-Wire: Up, stop, downwards, tilting movement through time control up / downwards and stop
Interface: 1-Wire Bus with Ground/GND, Data and +12V, DS2408 Command set
Feedback for output status and digital / binary input (pushbutton interface)
Operating voltage: 12V= (+/-10%),
Current consumption: 12V max. 30 mA (output active)
Display: LED for „up“and „down“, flashes when slats moving up or down
Insulation voltage: min. 500VAC among 1-Wire bus and relay contact (motor voltage)
Connection: Screw terminals (up to 2.5 mm² wire cross section)
Note: To operate the module, a 12 V supply voltage is necessary. For the power supply of the module we
recommend the use of a 1-Wire Hub Art. No. 11322 or 11323
The cables of the control inputs must be electrically insulated from the motor control cable.
5 Ambient conditions
Temperature (operation): 0°C to +50°C
Air humidity: 10 - 92% (non condensing)
Dimensions: 35 x 90 x 70mm (BxHxD)
Protection system: IP20
Protection class: III
6 Conformity
EN 50090-2-2
EN 61000-4-2, ESD
EN 61000-4-3, HF
EN 61000-4-4, Burst
EN 61000-4-5, Surge
EN 61000-6-1, fault-free operation
EN 61000-6-3, stray radiations
RoHS

Art. No. 11231
All rights reserved. Reproduction as well as electronic duplication of this user guide, complete or in part, requires the written consent of
ESERA GmbH. Errors and technical modification subject to change. ESERA GmbH, ESERA-Automation 2020
www.esera.de 11231 V2.0 R1.0 Manual Page 3 of 7
7 LED Display, pushbuttons and inputs
The module has green LED indicators for signalling the running direction. The LED`s flash as soon as the
corresponding running direction has been started.
In addition to the buttons on the top of the module, the module has external control inputs. Via the external control
inputs, the shutter module can be controlled with standard roller shutter switching elements, preferably with button
function, from all switch manufacturers, such as Jung, Berker or Busch Jaeger or two individual buttons.
The operation and running direction of the motor output can be controlled via the external and internal buttons.
The motor output can also be controlled via the 1-wire bus interface.
Motor operation triggered by a button on the top of the module or an external control input cannot be read via the
1-Wire interface.
Button/Input
Designation
Function
Manual
operation „Up“
module
topside
UP
Up and Down pushbuttons have a dual function
- motor control
- Switching the operating mode
1 = blind operation with tilting function
2 = shutter operation
Shutter operation:
- pushbutton => start motor upwards
Blinds operation:
- short pushbutton action =>Tilting movement for blind, motor Up /
Down,
- long pushbutton action => Start motor movement Up / Down
Manual
operation
„Down“
module
topside
DOWN
Up external,
clamp 5
Push-button
input
shutter up
Roller shutter operation:
- pushbutton => start motor upwards
Blinds operation:
- short push-button action =>Tilting movement for blind, motor Up
- long push-button action => Start motor movement Up
Down external,
clamp 6
Push-button
input
shutter down
Roller shutter operation:
- pushbutton => start motor downwards
Blinds operation:
- short pushbutton action => tilting movement for blind, motor
downwards
- long pushbutton action => start motor movement downwards
Note: To control the external button interface, a DC voltage source in the range of 10 - 30 V has to be connected.
The connecting cables between module and push-button must be laid insulated from other cables.
Display
Designation
Function
LED Up
Shutter up
LED flashes, output „upwards“ is active for max. 120 seconds
(switch-off by safety switch-off)
LED Down
Shutter down
LED flashes, output „downwards“ is active for max. 120 seconds
(switch-off by safety switch-off)
LED Up/Down
flash
alternately
LED Up and LED Down flashes 6 times alternately after applying the
operating voltage, then the module is ready for operation.

All rights reserved. Reproduction as well as electronic duplication of this user guide, complete or in part, requires the written consent of
ESERA-Automation or E-Service GmbH. Errors and technical modification subject to change. ESERA-Automation, E-Service GmbH 2020
www.esera.de 11231 V2.0 R1.0 Manual Page 4 of 7
8 Changing the roller shutter / blind operating mode
The Shutter Pro has two operating modes, which differ in the functions of manual operation (push-buttons up
and down on module topside) and the external interface (push-button interface). The difference is that the shutter
operating mode also has a push-button function to tilt the slats (see table LED display, push-button/inputs, no. 6)
This operating mode can only be selected when using the buttons on the top of the module.
How to change the operating mode?
Press the two buttons on the top of the module (UP and DOWN buttons) at the same time for about 2 seconds.
The two LEDs “UP”and “DOWN”will flash twice and will then show the current operating mode for
approx. 3 seconds.
By pressing the buttons UP and DOWN at the same time again, the operating mode will change.
LED “UP” is lit = operating mode with tilting function for blinds and slat curtains
LED “DOWN” is lit = operating mode for roller shutters and awnings, as-delivered condition.
The selected operating mode remains permanently stored in the module, but can be changed as required.
9 Functional description 1-Wire interface, Push Buttons and Control Inputs
All three interfaces, manual operation module top, 1-wire bus interface and external control inputs work in parallel
on the motor output. A motor switched on e.g. by the 1-Wire Bus interface can be stopped by operating the
manual operation or pulse via the external control inputs. The same applies to manual operation or the external
control inputs.
If the motor of a roller shutter is to stop at a certain window position, time control by the control software must be
provided via the bus interface in automatic mode.
The Shutter Pro automatically stops driving in both directions after approx. 120 seconds by switching off the
safety motor.
Within the Shutter Pro module a microcontroller takes over the management of the manual operation, all
interfaces and the control of the relays incl. pause function and safety shutdown. The relays are electronically
connected in such a way that upward and downward operation is never switched simultaneously.
The query of the external interface reacts to status change and pressure duration.
Further details on the ESERA roller shutter system can be found on our website. You will find the information
under the keyword "Roller shutter control".
10 Software / Control 1-Wire interface
The device is controlled by DS2408 1-Wire commands. The status of the output and digital input is reported via
the 1-Wire interface.
The ESERA 1-Wire Controller features special commands for easy control of the Shutter Pro.
Available 1-Wire commands:
Read ROM 33h 64-BIT ROM, RC-FLAG
Match ROM 55h 64-BIT ROM, RC-FLAG
Search ROM F0h 64-BIT ROM, RC-FLAG
Skip ROM CCh RC-FLAG
Read PIO Registers F0h PIO Register
Channel Access Read F5h Input und Output Status
Channel Access Write 5Ah Port Output Latches / Status
11 Control via 1-Wire Controller / 1-Wire Gateway, as of firmware 1.20_26
The 1-Wire interface of the Shutter Pro is controlled by standard commands for the DS2408 device. The relays
switched via manual operation or manual mode can be read back via the 1-Wire interface. The Shutter Pro can
easily be controlled via a 1-Wire Controller / 1-Wire Gateway. The following command is available for this
purpose.
New for this shutter module is a time control, which is executed by the module itself. It is now possible to execute
the run time (Up or Down) by command without preset and with time. Details see below.
Switching a Shutter Pro output without time function
To switch the relay output of the Shutter Pro, use the following command for the 1-Wire Controller or ESERA
Station to set only the selected function 1 = Down, 2 = Up, and 3 = Stop.
Command: SET,OWD,SHT,OWD-Number, Value
Example: set,owd,sht,2,1 => OWD Number 2 will be switched to „DOWN“.
After switching the output, the new state is output as confirmation via the 1-Wire interface. The output value 0
corresponds to the rest position of the Shutter Pro.

Art. No. 11231
All rights reserved. Reproduction as well as electronic duplication of this user guide, complete or in part, requires the written consent of
ESERA GmbH. Errors and technical modification subject to change. ESERA GmbH, ESERA-Automation 2020
www.esera.de 11231 V2.0 R1.0 Manual Page 5 of 7
New, switch one Shutter Pro output with defined runtime
To switch the relay output with a defined runtime of the Shutter Pro use the following command for the 1-Wire
Controller or ESERA Station, which only sets the selected function 1 = Down and 2 = Up with a defined runtime
with a final stop.
Note: The function is supported from controller firmware 1.20_27. If you want to use this function, a
firmware update of the 1-Wire Controller may be necessary.
Command: SET,OWD,SHT,OWD- Number, Value, Time
The following times can be selected:
Runtime for Up and Down function
Input for command
Example
250 milliseconds (ms)
250
set,owd,sht,2,1,250
=> OWD Number 2 is switched to
„DOWN“ for 250ms.
500 milliseconds (ms)
500
set,owd,sht,2,1,500
=> OWD Number 2 is switched to
„DOWN“ for 500ms.
750 Milliseconds (ms)
750
set,owd,sht,2,1,250
=> OWD Number 2 is switched to
„DOWN“ for 750ms.
1 bis 60 seconds
1 -60
set,owd,sht,2,1,34
=> OWD Number 2 is set to
„DOWN“ for 34 seconds.
The Shutter Pro makes a stop after the run time. This switches off the outputs and stops the shutter.
After switching the output, the new state is output as confirmation via the 1-Wire interface. The output value 0
corresponds to the rest position of the Shutter Pro.
There is no feedback at the elapsed time or at the runtime.
Data output 1-Wire controller / ESERA Station 200
For the Shutter Pro switching module the following data are output for the status of the relay output.
Data output:
1_EVT|12:27:40
1_OWD1_1|1 => Controller No._Module No._Data set | decimal value input
1_OWD1_2|00000001 => Controller No._Module No._Data set | binary representation input
1_OWD1_3|7 => Controller No._Module No.-_Data set | decimal value Shutter status
1_OWD1_4|00000111 => Controller No._Module No._Data set | binary representation Shutter status
Further information for options and commands can be found in the latest available documentation for
1–Wire Controller / 1–Wire Gateway.

All rights reserved. Reproduction as well as electronic duplication of this user guide, complete or in part, requires the written consent of
ESERA-Automation or E-Service GmbH. Errors and technical modification subject to change. ESERA-Automation, E-Service GmbH 2020
www.esera.de 11231 V2.0 R1.0 Manual Page 6 of 7
12 Connection plan
The connection diagram is available in the article download area.
Module top side:
Motor:
10 = Input DC or AC voltage
11 = Output up (Up)
12 = Output downwards (Down)
Module bottom side:
1-Wire Bus
1 = GND (ground)
2 = 1-Wire data
3 = +12V voltage
Digital- / binary input 10 –30 VDC
(push-button interface for manual operation)
4 = ground/GND
5 = Push-button control, upwards (Up)
6 = Push-button control, downwards (Down)
13 Operating conditions
The operation of the assembly group can take place only on condition of observing the required voltage and the
ambient conditions. The operating position of the device is irrelevant. The device is meant to be used in dry areas
free of dust.
Should condensed water build up within the sensor, an acclimatization period of at least 2 hours must be met.
The components can be operated only under the supervision of an electrically skilled person. Assembly groups
and components do not belong into the hands of children!
In industrial facilities, the accident prevention regulations of the federation of industrial professional associations
for electrical installations and equipment must be observed. Do not operate the assembly in an environment
where flammable gases, vapours or dust are present or may be present.
14 Assembly
The installation site must be protected from moisture. The device may only be used in dry indoor rooms and in
protected outdoor areas.
The device is intended for installation inside a control cabinet as a stationary device.
15 Disposal Note
Do not dispose of the device in domestic waste! Electronic devices must be disposed of at the
local collection points for electronic waste in accordance with the Directive on Waste Electrical
and Electronic Equipment!
16 Safety instructions
When using products that come into contact with electrical voltage, the valid VDE regulations must be
observed, especially VDE 0100, VDE 0550/0551, VDE 0700, VDE 0711 and VDE 0860
All final or wiring work must be carried out with the power turned off.
Before opening the device, always unplug or make sure that the unit is disconnected from the mains.
Components, modules or devices may only be put into service if they are mounted in a contact proof housing.
During installation they must not have power applied.
Tools may only be used on devices, components or assemblies when it is certain that the devices are disconnected
from the power supply and electrical charges stored in the components inside the device have been discharged.
Live cables or wires to which the device or an assembly is connected, must always be tested for insulation faults or
breaks.
If an error is detected in the supply line, the device must be immediately taken out of operation until the faulty cable
has been replaced.
When using components or modules it is absolutely necessary to comply with the requirements set out in the
accompanying description specifications for electrical quantities.

Art. No. 11231
All rights reserved. Reproduction as well as electronic duplication of this user guide, complete or in part, requires the written consent of
ESERA GmbH. Errors and technical modification subject to change. ESERA GmbH, ESERA-Automation 2020
www.esera.de 11231 V2.0 R1.0 Manual Page 7 of 7
If the available description is not clear to the non-commercial end-user what the applicable electrical characteristics
for a part or assembly are, how to connect an external circuit, which external components or additional devices can
be connected or which values these external components may have, a qualified electrician must be consulted.
It must be examined generally before the commissioning of a device, whether this device or module is basically
suitable for the application in which it is to be used.
In case of doubt, consultation with experts or the manufacturer of the components used is absolutely necessary.
For operational and connection errors outside of our control, we assume no liability of any kind for any resulting
damage.
Kits should be returned without their housing when not functional with an exact error description and the
accompanying instructions. Without an error description it is not possible to repair. For time-consuming assembly or
disassembly of cases charges will be invoiced.
During installation and handling of components which later have mains potential on their parts, the relevant VDE
regulations must be observed.
Devices that are to be operated at a voltage greater than 35 VDC / 12mA, may only be connected by a qualified
electrician and put into operation.
Commissioning may only be realized if the circuit is built into a contact proof housing.
If measurements with an open housing are unavoidable, for safety reasons an isolating transformer must be
installed upstream or a suitable power supply can be used.
After installing the required tests according to DGUV / regulation 3 (German statutory accident insurance,
https://en.wikipedia.org/wiki/German_Statutory_Accident_Insurance) must be carried out.
17 Warranty
ESERA GmbH guarantees that the goods sold at the time of transfer of risk to be free from material and workmanship
defects and have the contractually assured characteristics. The statutory warranty period of two years begins from date of
invoice. The warranty does not extend to the normal operational wear and normal wear and tear. Customer claims for
damages, for example, for non-performance, fault in contracting, breach of secondary contractual obligations,
consequential damages, damages resulting from unauthorized usage and other legal grounds are excluded. Excepting to
this, ESERA GmbH accepts liability for the absence of a guaranteed quality resulting from intent or gross negligence.
Claims made under the Product Liability Act are not affected.
If defects occur for which the ESERA GmbH is responsible, and in the case of replacement goods, the replacement is
faulty, the buyer has the right to have the original purchase price refunded or a reduction of the purchase price.
ESERA GmbH accepts liability neither for the constant and uninterrupted availability of the ESERA GmbH or for technical
or electronic errors in the online offer.
We are constantly developing our products further and reserve the right to make changes and improvements to any of the
products described in this documentation without prior notice. Should you require documents or information on older
18 Trademarks
All mentioned designations, logos, names and trademarks (including those which are not explicitly marked) are
trademarks, registered trademarks or other copyright or trademarks or titles or legally protected designations of their
respective owners and are hereby expressly recognized as such by us. The mention of these designations, logos, names
and trademarks is made for identification purposes only and does not represent a claim of any kind on the part of ESERA
GmbH on these designations, logos, names and trademarks. Moreover, from their appearance on ESERA GmbH
webpages it cannot be concluded that designations, logos, names and trademarks are free of commercial property rights.
ESERA and Auto-E-Connect are registered trademarks of ESERA GmbH.
19 Contact
ESERA GmbH
Adelindastrasse 20
87600 Kaufbeuren
GERMANY
Tel.: +49 8341 999 80-0
Fax: +49 8341 999 80-10
www.esera.de
WEEE-Number: DE30249510
This manual suits for next models
1
Table of contents
Other esera automation Control Unit manuals
Popular Control Unit manuals by other brands
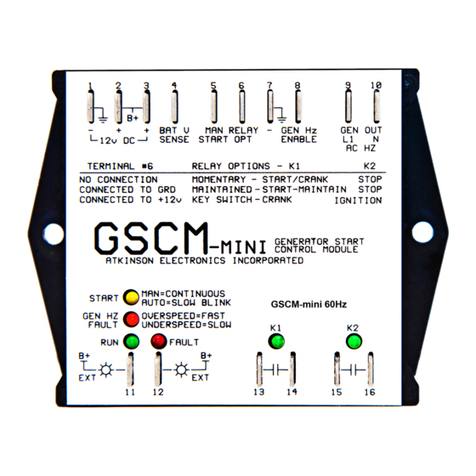
Atkinson Electronics
Atkinson Electronics GSCM-MINI manual

S+S Regeltechnik
S+S Regeltechnik Rymaskon 600 operating instructions
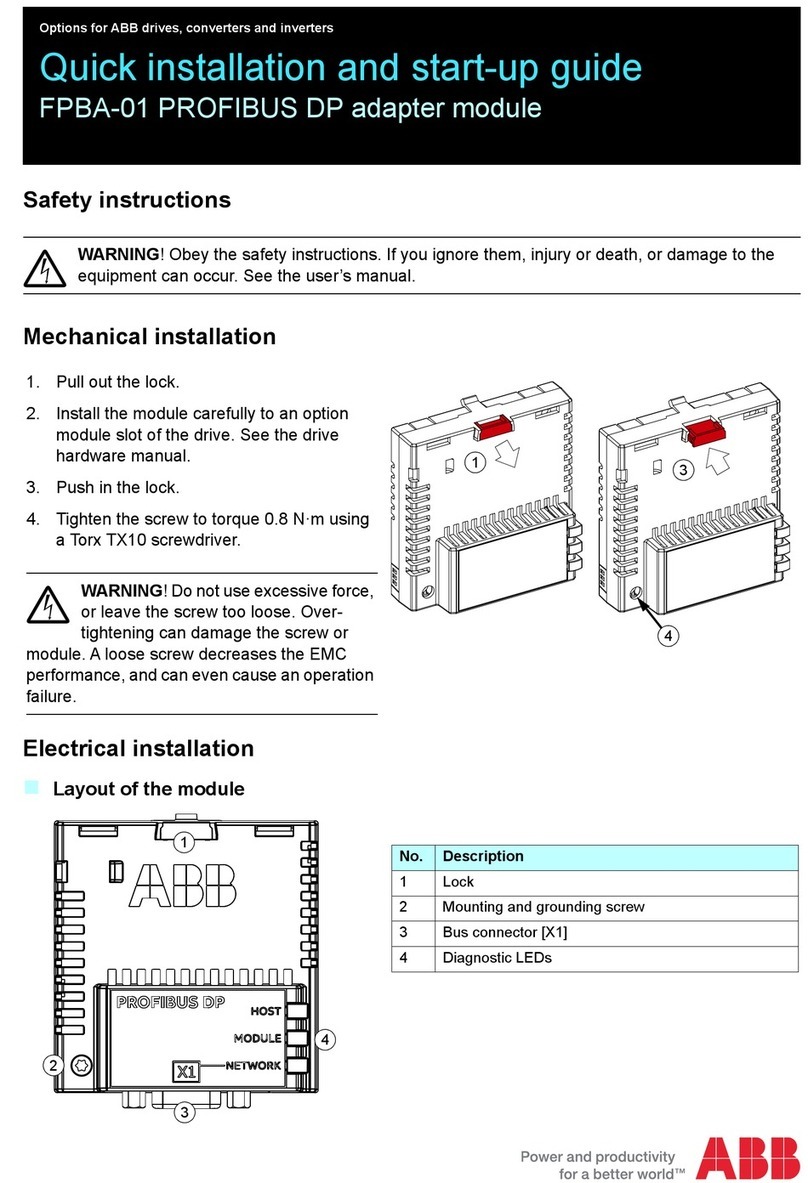
ABB
ABB FPBA-01 PROFIBUS DP Quick installation and start-up guide
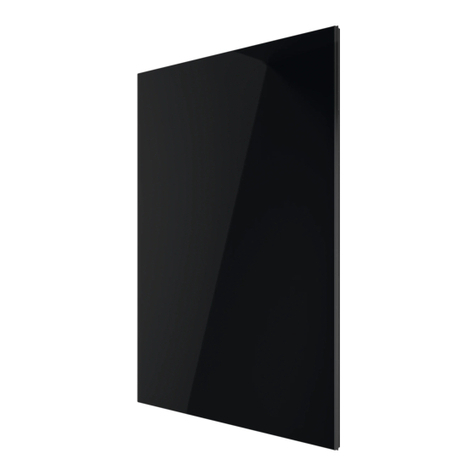
First Solar
First Solar 6 Series user guide
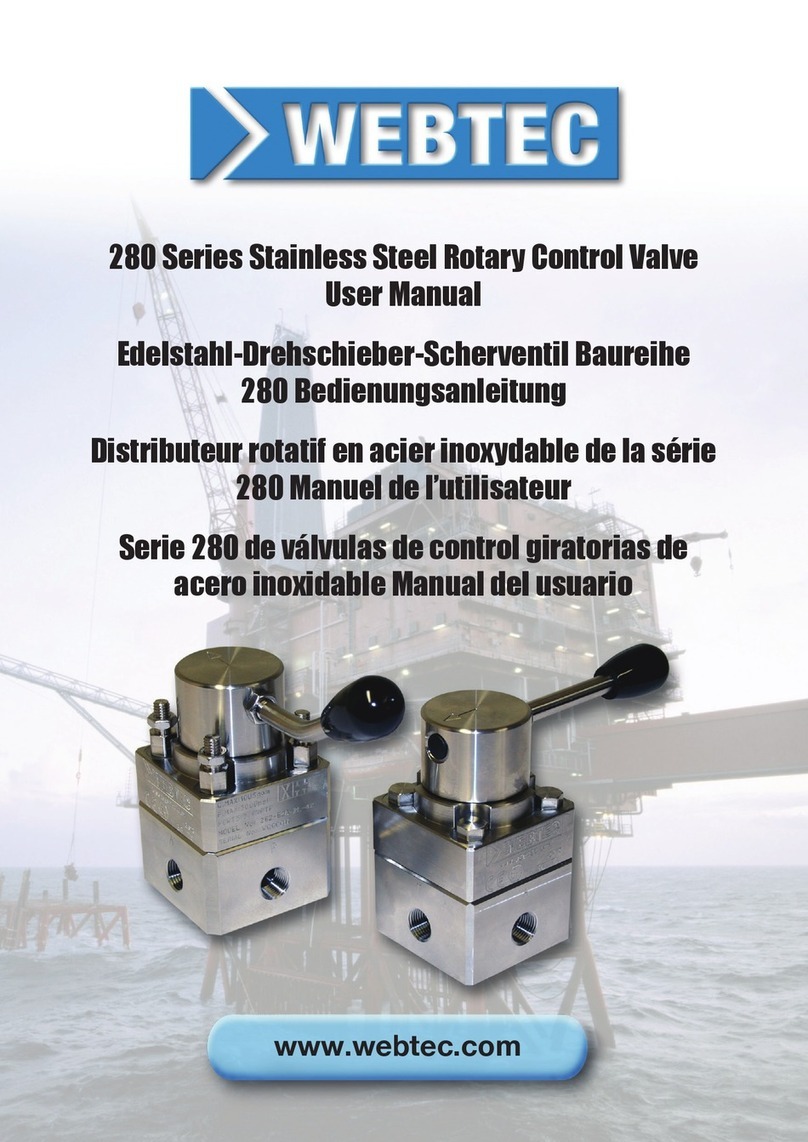
WEBTEC
WEBTEC 280 Series user manual
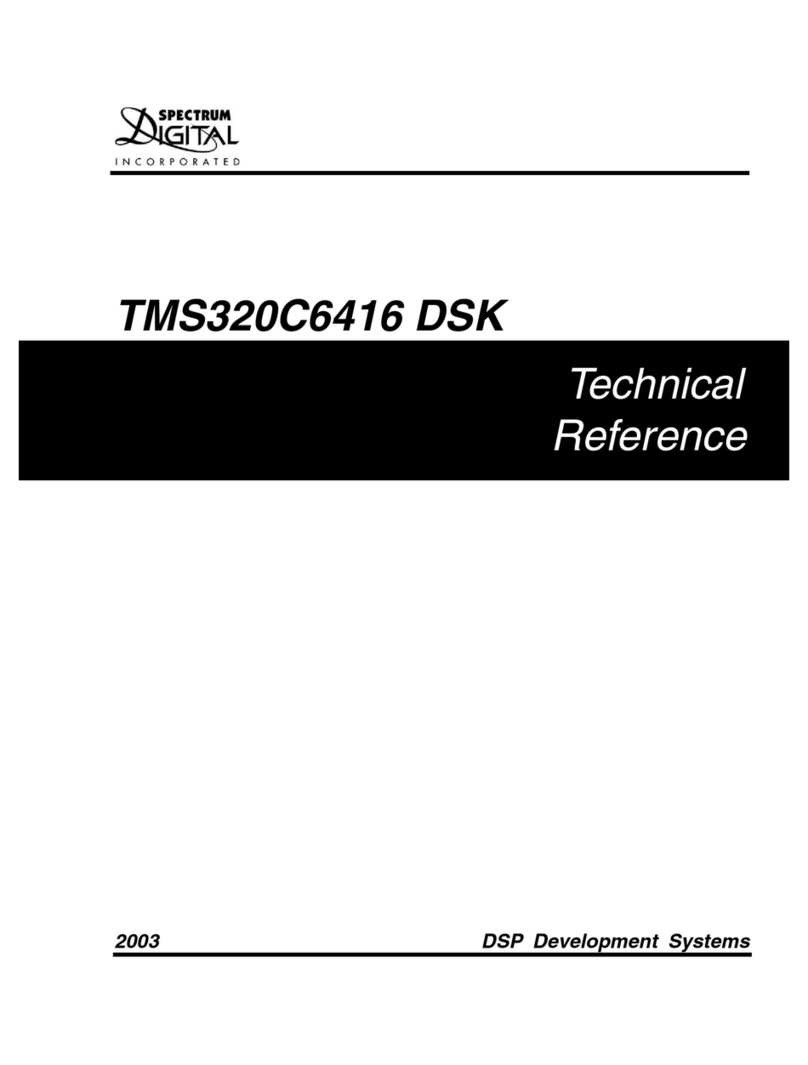
Spectrum Digital
Spectrum Digital TMS320C6416 DSK Technical reference