Eurotherm 216 User manual

UU
UU
U
USER MANUALUSER MANUAL
USER MANUALUSER MANUAL
USER MANUAL
02160216
02160216
0216
03160316
03160316
0316
PID CONTROLLERSPID CONTROLLERS
PID CONTROLLERSPID CONTROLLERS
PID CONTROLLERS
02_0316_A_DER.pmd 23/04/2004, 10.481

A. 1
GBGB
GBGB
GB
INDEXINDEX
INDEXINDEX
INDEX
A.A.
A.A.
A.WHAT YOU NEED TO KNOW BEFORE YOUWHAT YOU NEED TO KNOW BEFORE YOU
WHAT YOU NEED TO KNOW BEFORE YOUWHAT YOU NEED TO KNOW BEFORE YOU
WHAT YOU NEED TO KNOW BEFORE YOU
STARTSTART
STARTSTART
START......................................................................................................................................
......................................................................................................................................
................................................................... A.2A.2
A.2A.2
A.2
A.1 OUTLINEANDCUTOUTDIMENSIONS .............A.5
1.1.
1.1.
1.MOUNTINGMOUNTING
MOUNTINGMOUNTING
MOUNTING ............................................................................................................................
............................................................................................................................
.............................................................. 11
11
1
2.2.
2.2.
2.ELECTRICAL CONNECTIONSELECTRICAL CONNECTIONS
ELECTRICAL CONNECTIONSELECTRICAL CONNECTIONS
ELECTRICAL CONNECTIONS..............................................................
..............................................................
............................... 22
22
2
3.3.
3.3.
3.PRELIMINARY HARDWARE SETTINGSPRELIMINARY HARDWARE SETTINGS
PRELIMINARY HARDWARE SETTINGSPRELIMINARY HARDWARE SETTINGS
PRELIMINARY HARDWARE SETTINGS 66
66
6
4.4.
4.4.
4.CONFIGURATIONCONFIGURATION
CONFIGURATIONCONFIGURATION
CONFIGURATION ......................................................................................................
......................................................................................................
................................................... 66
66
6
4.1 Pushbuttonfunction ............................................ 6
4.2 Possible protection of the parameters................ 6
4.3 Access to the configuration procedure ............... 7
4.4 Configurationparameters .................................... 7
5.5.
5.5.
5.OPERATIVE MODEOPERATIVE MODE
OPERATIVE MODEOPERATIVE MODE
OPERATIVE MODE..............................................................................................
..............................................................................................
............................................... 1414
1414
14
5.1 Preliminary comments....................................... 14
5.2 SMARTalgorithm ............................................... 15
5.3 Inhibition of the out signal ................................. 15
5.4 Displaying the set point set
(modelLDE) ........................................................ 16
5.5 SP/SP" selection ............................................... 16
5.6 Direct modification of the set point................... 16
5.7 Timermodedescription ..................................... 16
5.8 Manual reset of the alarm ................................. 20
5.9 Soft Start Ffunction ........................................... 20
5.10 Lamp test........................................................... 20
5.11 Function of the pushbuttons ............................. 20
5.12 Indicators ........................................................... 21
5.13 Operative parameters ........................................ 21
6.6.
6.6.
6.ERROR MESSAGESERROR MESSAGES
ERROR MESSAGESERROR MESSAGES
ERROR MESSAGES ........................................................................................
........................................................................................
............................................ 2424
2424
24
6.1 Measurement anomaly signal .......................... 24
6.2 Error messages ................................................. 25
6.3 List of possible errors ....................................... 25
7.7.
7.7.
7.TECHNICAL CHARACTERISTICSTECHNICAL CHARACTERISTICS
TECHNICAL CHARACTERISTICSTECHNICAL CHARACTERISTICS
TECHNICAL CHARACTERISTICS ............................................
............................................
...................... 2626
2626
26
7.1 Technical specifications .................................... 26
7.2 Inputs ................................................................. 27
7.3 Controlactions................................................... 27
7.4 Outs ................................................................... 28
7.5 CPI - Configuration Port Interface ..................... 28
8.8.
8.8.
8.MAINTENANCEMAINTENANCE
MAINTENANCEMAINTENANCE
MAINTENANCE............................................................................................................
............................................................................................................
...................................................... 2828
2828
28
B.B.
B.B.
B.DEFAULT PARAMETERSDEFAULT PARAMETERS
DEFAULT PARAMETERSDEFAULT PARAMETERS
DEFAULT PARAMETERS ....................................................................
....................................................................
.................................. B.1B.1
B.1B.1
B.1
02_0316_A_DER.pmd 23/04/2004, 10.482

A. 2
A.A.
A.A.
A. EUROTHERM CONTROLLER MODELS 0216 / 0316EUROTHERM CONTROLLER MODELS 0216 / 0316
EUROTHERM CONTROLLER MODELS 0216 / 0316EUROTHERM CONTROLLER MODELS 0216 / 0316
EUROTHERM CONTROLLER MODELS 0216 / 0316
What you need to know before you startWhat you need to know before you start
What you need to know before you startWhat you need to know before you start
What you need to know before you start
Home Screen DefinitionHome Screen Definition
Home Screen DefinitionHome Screen Definition
Home Screen Definition
Model 0216 displays the measured value or the operating
set point. When the timer is running, time remaining is
displayed.
LED “A” flashing indicates the timer is running, LED
“B” flashing indicates SP2 is selected as the
operating set point.
To select between the set point display and the measured
value press pushbutton V.
Model 0316 displays the measured value on the upper
display. The lower display indicates the operating set point
or the time remaining when the timer is running.
LED “A” flashing indicates the timer is running, LED “B”
flashing indicates SP2 is selected as the operating set
point.
02_0316_A_DER.pmd 23/04/2004, 10.493

CONFIGURATION ENTRY & EXITCONFIGURATION ENTRY & EXIT
CONFIGURATION ENTRY & EXITCONFIGURATION ENTRY & EXIT
CONFIGURATION ENTRY & EXIT
EntryEntry
EntryEntry
Entry See operator manual page 7 section 4.3
To gain access to configuration you need to be
in the HOME screen.
While in the HOME screen press the PAGE key
followed by the SCROLL key
Keep both keys pressed for 3 seconds until the
display shows OFFOFF
OFFOFF
OFF and ConFConF
ConFConF
ConF.
Now press either s or t to gain access by
changing OFFOFF
OFFOFF
OFF to ONON
ONON
ON.
ExitExit
ExitExit
Exit See operator manual page 14 after P28
To exit configuration you need to be at the ConfConf
ConfConf
Conf
screen
While in the ConfConf
ConfConf
Conf screen press the PAGE key
followed by the SCROLL key
Keep both keys pressed for 3 seconds until the
display returns to normal numeric display.
POWER OUTPUT On/OffPOWER OUTPUT On/Off
POWER OUTPUT On/OffPOWER OUTPUT On/Off
POWER OUTPUT On/Off
These products allow you manually turn off the
outputpower.
See page 16 section 5.3
OffOff
OffOff
Off To turn the power off press the Vkey
followed by the SCROLL key.
Keep both buttons pressed for 3 seconds until
the display shows OFF.OFF.
OFF.OFF.
OFF.
OnOn
OnOn
On To tune the power on press the Vkey
followed by the SCROLL key.
Keep both buttons pressed for 3 seconds until
the display returns to normal numeric display.
DIRECT SETPOINT ENTRYDIRECT SETPOINT ENTRY
DIRECT SETPOINT ENTRYDIRECT SETPOINT ENTRY
DIRECT SETPOINT ENTRY
See page 16 section 5.6
While viewing the normal display hold either the
Vor Wbutton for more than 2 seconds. The
value will change. After reaching the new set
point do not press any keys for a further 2
seconds and the new value will be entered.
PARAMETER ENTRYPARAMETER ENTRY
PARAMETER ENTRYPARAMETER ENTRY
PARAMETER ENTRY
See page 21 section 5.11
Whenever a parameter is changed using either
the Vor Wbuttons there are 2 options:
Accept new valueAccept new value
Accept new valueAccept new value
Accept new value
Press the SCROLL
key
Cancel the changeCancel the change
Cancel the changeCancel the change
Cancel the change Press the PAGE
key
LAMP TESTLAMP TEST
LAMP TESTLAMP TEST
LAMP TEST
See page 21 section 5.10
The instrument display LED’s can be tested as
follows:
Activate TestActivate Test
Activate TestActivate Test
Activate Test Press Wand together
Cancel TestCancel Test
Cancel TestCancel Test
Cancel Test Press Wand together
A. 3
02_0316_A_DER.pmd 23/04/2004, 10.494

DEFAULT CONFIGURATIONDEFAULT CONFIGURATION
DEFAULT CONFIGURATIONDEFAULT CONFIGURATION
DEFAULT CONFIGURATION
See section B
The instrument can be pre-loaded with factory
default values.
Using the factory default values is ideal for
completely resetting the instrument before
commencing a new configuration.
PARAMETER SECURITYPARAMETER SECURITY
PARAMETER SECURITYPARAMETER SECURITY
PARAMETER SECURITY
See page 6 section 4.2, and page 10 section P11
& P14
The instrument is supplied with access to the
main parameters which are required for the set-up
procedure.
After commissioning it is necessary to select the
correct level of Parameter Security, simplifing the
instrument user interface for normal operation.
The most common security setting would be:
P11 = 1P11 = 1
P11 = 1P11 = 1
P11 = 1
P14 = OffP14 = Off
P14 = OffP14 = Off
P14 = Off
RECOVERY FROM A LOSTRECOVERY FROM A LOST
RECOVERY FROM A LOSTRECOVERY FROM A LOST
RECOVERY FROM A LOST
PASSWORDPASSWORD
PASSWORDPASSWORD
PASSWORD
See page 6 section 4.2, and page 10 section P11
& P14
If you lose your password
Enter Configuration using the Master Code of 408
Go to parameter P11 and enter the Master Code
of 408
You can now reset the password.
A. 4
TIMER CONTROL FROM FRONTTIMER CONTROL FROM FRONT
TIMER CONTROL FROM FRONTTIMER CONTROL FROM FRONT
TIMER CONTROL FROM FRONT
PANEL KEYSPANEL KEYS
PANEL KEYSPANEL KEYS
PANEL KEYS
See page 17 section 5.7
When a timer funtion is configured the
parameter ‘StS’ is enabled.
This parameter functions the same as that
described for a digital input.
‘StS’ = ‘OFF’ means that the time is off
‘StS’ = ‘On’ means that the timer is on.
02_0316_A_DER.pmd 23/04/2004, 10.495

A. 5
A.1A.1
A.1A.1
A.1 OUTLINE AND CUT OUT DIMENSIONSOUTLINE AND CUT OUT DIMENSIONS
OUTLINE AND CUT OUT DIMENSIONSOUTLINE AND CUT OUT DIMENSIONS
OUTLINE AND CUT OUT DIMENSIONS
02160216
02160216
0216
EUROTHERM
EUROTHERM
0 316
0 21 6
03160316
03160316
0316
02_0316_A_DER.pmd 23/04/2004, 10.496

1
GBGB
GBGB
GB
1.1.
1.1.
1. MOUNTINGMOUNTING
MOUNTINGMOUNTING
MOUNTING
Select a mounting location where there is
minimumvibration andthe ambienttemperature
ranges between 0 and 50°C (32 and 122°F).
The instrument can be mounted on a panel up to
15 mm thick with a square cutout of 45 x 45 mm.
Foroutlineand cutout dimensionsreferto
page A.4.
The surface texture of the panel must be better
than 6.3 µm.
The instrument is fitted with a rubber panel gasket.
To assure IP65 and NEMA 4 protection, insert the
panelgasketbetween the instrument andthe
panel as shown in Fig. 1.
While holding the instrument against the panel
proceedasfollows:
1) insert the gasket in the instrument case;
2) insert theinstrumentin thepanelcutout;
3) pushing the instrumentagainstthe panel, insert
themountingbracket;
4) with a screwdriver, turnthescrews with a
torque between 0.3 and 0.4 Nm. Fig. 1 PANEL MOUTING
screws
bracket
gasket
panel
02-0316-1-DER.pmd 22/04/2004, 16.191

2
GBGB
GBGB
GB
MEASURING INPUTSMEASURING INPUTS
MEASURING INPUTSMEASURING INPUTS
MEASURING INPUTS
NOTENOTE
NOTENOTE
NOTE: Any external components (like zener
barriersetc.) connectedbetweensensor andinput
terminals may cause errors in measurement due
toexcessiveand/or not balanced lineresistanceor
possibleleakagecurrents.
TC INPUTTC INPUT
TC INPUTTC INPUT
TC INPUT
Fig. 3 THERMOCOUPLE CONNECTION
NOTESNOTES
NOTESNOTES
NOTES:
1) Do not runinputwires together withpowerline
cables.
2) For TC wiring use proper compensating cable
preferablyshielded.
3) When a shielded cable is used, it should be
connectedatonepointonly.
2.2.
2.2.
2. ELECTRICAL CONNECTIONSELECTRICAL CONNECTIONS
ELECTRICAL CONNECTIONSELECTRICAL CONNECTIONS
ELECTRICAL CONNECTIONS
Connectionsareto be madewiththe instrument
housinginstalled initsproperlocation.
Fig. 2 REAR TERMINAL BLOCK
10
9
+
_
10
9
+
_
Shield
Shield
+
-
02-0316-1-DER.pmd 22/04/2004, 16.192

3
GBGB
GBGB
GB
RTD INPUTRTD INPUT
RTD INPUTRTD INPUT
RTD INPUT
Fig. 4 RESISTANCE TEMPERATURE
DETECTOR CONNECTION
NOTESNOTES
NOTESNOTES
NOTES:
1) Do not runinputwires together withpowerline
cables.
2) Pay attention to the line resistance; a resistance
higher than 20 Ω/wire may cause measurement
errors.
3) When shielded cable is used, it should be
groundedatone sideonlyto avoid groundloop
currents.
4) The impedence of the 3 wires must be the
same.
8
RTD
10
9 8
RTD
10
911
12
Log.input 2
LOGIC INPUTLOGIC INPUT
LOGIC INPUTLOGIC INPUT
LOGIC INPUT
Safetynote:
1) Do notrun logicinput wiringtogether with
powercables.
2) Use an external drycontactcapableof
switching 8 mA, 8 V DC.
3) The instrument needs 300 ms to recognize a
contactstatusvariation.
4) The logic input is NOTNOT
NOTNOT
NOT isolated by the
measuringinput
Fig. 5 - LOGIC INPUT WIRING
The logic input can be programmed as:
A) Set point selector
A.1) In this case it will operate as follows:
logicinput operat.setpoint
open SP
close SP2
B) Start timer
In this case it will operate as described at
paragraph5.7 (Timermodesdescription).
02-0316-1-DER.pmd 22/04/2004, 16.193

4
GBGB
GBGB
GB
3) Usecopper conductors only.
4) Do notrun inputwirestogether withpower
line cables.
The following recommendations avoid serious
problems which may occur it when using relay
output to drive inductive loads.
INDUCTIVE LOADSINDUCTIVE LOADS
INDUCTIVE LOADSINDUCTIVE LOADS
INDUCTIVE LOADS
Highvoltage transientsmayoccur whenswitching
inductiveloads.
Thesetransients mayintroduce disturbances
throughtheinternalcontactswhich canaffectthe
performanceoftheinstrument.
The internal protection (varistors) assures correct
protectionupto0.5Aofinductivecomponentbut
theOUT1 NC contact isnotprotected.
The same problem may occur when a switch is
usedinserieswith the internal contacts.
Fig. 7 EXTERNAL SWITCH IN SERIES WITH
THE INTERNAL CONTACT
In these cases an additional RC network should
beinstalledacross the external contactasshown
in Fig. 7
The value of the capacitor (C) and resistor (R) are
shownin thefollowingtable.
R
C
LOAD
POWER
LINE
RELAY OUTSRELAY OUTS
RELAY OUTSRELAY OUTS
RELAY OUTS
Fig. 6 RELAY OUTS
The OUT 1 NO contact and the OUT 2 and OUT 3
contactsareprotectedbyvaristorsagainstinductive
loadwith inductivecomponent upto 0.5A.
The OUT 1 contact rating is 3A/250V AC on
resistiveload.
The OUT 2 and OUT 3 contact rating is 2A/250V
AC on resistive load.
The number of operations is 1 x 105at specified
rating.
NOTES:NOTES:
NOTES:NOTES:
NOTES:
1) Toavoid electricshock, connectthepower
line at the end of the wiring procedure.
2) For power connections use No 16 AWG or
larger wires rated for at least 75°C.
7
6C
NO
OUT 2
14
15 C
NO
OUT 3
1
3
2C
NC
NO
OUT 1
02-0316-1-DER.pmd 22/04/2004, 16.194

5
GBGB
GBGB
GB
In every case the cable connected to the relay
outs must be routed as far away as possible from
inputorcommunicationcables.
VOLTAGE OUTS FOR SSR DRIVEVOLTAGE OUTS FOR SSR DRIVE
VOLTAGE OUTS FOR SSR DRIVEVOLTAGE OUTS FOR SSR DRIVE
VOLTAGE OUTS FOR SSR DRIVE
Fig. 8 SSR DRIVE OUT WIRING
Itis atimeproportioning out.
Logic level 0Logic level 0
Logic level 0Logic level 0
Logic level 0: Vout < 0.5 V DC.
Logic level 1Logic level 1
Logic level 1Logic level 1
Logic level 1: Maximum current = 20 mA.
- 14 V + 20 % @ 20 mA
- 24 V + 20 % @ 1 mA.
NOTENOTE
NOTENOTE
NOTE: This out is NOT isolated.
AdoubleorreinforcedIsolationbetweeninstrument
output and power supply must be assured by the
external solid state relay.
LOAD
(mA)
<40 mA
<150 mA
<0.5 A
C
(mF)
0.047
0.1
0.33
R
(W)
100
22
47
P.
(W)
1/2
2
2
OPERATING
VOLTAGE
260 V AC
260 V AC
260 V AC
+
__
+
2
1
OUT 1
SOLID STATE
RELAY
POWER LINE WIRINGPOWER LINE WIRING
POWER LINE WIRINGPOWER LINE WIRING
POWER LINE WIRING
Fig. 9 POWER LINE WIRING
NOTESNOTES
NOTESNOTES
NOTES:
1) Before connecting the instrument to the supply,
make sure that the line voltage corresponds to
that indicatedontheratingplate.
2) Toavoid electricshock,connectthepowerlineat
theend ofthewiring procedure.
3) ForsupplyconnectionsuseNo16AWGorlarger
wires rated for at least 75°C.
4) Usecopperconductorsonly.
5) Do not run input wires together with power line
cables.
6) For 24 V AC/DC the polarity does not matter.
7) The powersupplyinput has NOfuseprotection.
Please,provide aTtype1A,250Vfuseexternally.
8) The safety regulations forequipment
permanentlyconnected tothemains require
that there is a switch or circuit breaker in the
buildingelectrical systemandthatthis:
- isnearthedeviceandcaneasilybereachedby
theoperator;
- is marked as the device ON/OFF device.
NOTENOTE
NOTENOTE
NOTE: A single switch or circuit-breaker can drive
morethanone instrument.
4
R (S,T)
R (S,T)
N
5N
Power Line
100 V to 240 V AC (50/60Hz)
or 24 V AC/DC
02-0316-1-DER.pmd 22/04/2004, 16.195

6
GBGB
GBGB
GB
3.3.
3.3.
3. PRELIMINARY HARDWAREPRELIMINARY HARDWARE
PRELIMINARY HARDWAREPRELIMINARY HARDWARE
PRELIMINARY HARDWARE
SETTINGSSETTINGS
SETTINGSSETTINGS
SETTINGS
These instruments can detect the opening of the
input circuit (TC or RTD). This failure is displayed
asanoverrange condition.
For the thermocouples only one can select, by
means of jumpers SH1 and CH1 indicated in Fig.
9,thetype of indicationto be obtainedwhenthe
thermocouple is open (see table at the bottom of
the page).
To gain access to the jumpers the instrument must
be taken out of its case.
SH1 CH1
Fig. 10 SH1 and CH1 JUMPERS
SH1 CH1 Indication
open close overrange (standard)
close open underrange
4.4.
4.4.
4. CONFIGURATIONCONFIGURATION
CONFIGURATIONCONFIGURATION
CONFIGURATION
4.14.1
4.14.1
4.1PUSHBUTTON FUNCTIONPUSHBUTTON FUNCTION
PUSHBUTTON FUNCTIONPUSHBUTTON FUNCTION
PUSHBUTTON FUNCTION
This saves the new value of the
selectedparameterandgoes to the
next parameter (increasing order).
This scrolls back the parameters
without saving the new value.
This increases the value of the selected
parameter.
This decreases the value of the
selectedparameter.
4.24.2
4.24.2
4.2 POSSIBLE PROTECTION OF THEPOSSIBLE PROTECTION OF THE
POSSIBLE PROTECTION OF THEPOSSIBLE PROTECTION OF THE
POSSIBLE PROTECTION OF THE
PARAMETERSPARAMETERS
PARAMETERSPARAMETERS
PARAMETERS
Accesstothe configurationandthe displayand
modificationof theoperativeparameters, canbe
protected by a secret code. The code is entered in
configuration, by means of parameters P11 and
P14.
P11 = 0P11 = 0
P11 = 0P11 = 0
P11 = 0 All the operative parameters can be
displayedand modified.Access tothe
configurationisfree.
P11 = 1 and P14 = OnP11 = 1 and P14 = On
P11 = 1 and P14 = OnP11 = 1 and P14 = On
P11 = 1 and P14 = On All the operative
parameterscanbedisplayedbutnotmodified,
apart from SP (Set Point), SP2 (second set point)
and t (time of the timer function). Access to the
configurationis onlypossibleby enteringthe
masterkeycode when requested.
P11 = 1 and P14 = OFFP11 = 1 and P14 = OFF
P11 = 1 and P14 = OFFP11 = 1 and P14 = OFF
P11 = 1 and P14 = OFF No operative parameter
can be displayed and modified, apart from SP,
SP2 and t. Access to the configuration is only
possiblebyentering master key when requested.
P11 = 2/499P11 = 2/499
P11 = 2/499P11 = 2/499
P11 = 2/499In this case the value programmed in
P11 represents a numerical key which can be
usedto protectaccesstotheconfigurationand,in
operative mode, the modification of the
02-0316-1-DER.pmd 22/04/2004, 16.196

7
GBGB
GBGB
GB
numerical value (or the selection code).
In the
model 0216, the display shows the parameter
code and the numerical value alternatively.
To alter the value set or the option selected press
or and confirm with .
The parameter for loading the default parameters
is shown in section B at the end of the manual.
4.44.4
4.44.4
4.4 CONFIGURATION PARAMETERSCONFIGURATION PARAMETERS
CONFIGURATION PARAMETERSCONFIGURATION PARAMETERS
CONFIGURATION PARAMETERS
P1 - Type of input and standard rangeP1 - Type of input and standard range
P1 - Type of input and standard rangeP1 - Type of input and standard range
P1 - Type of input and standard range
Type of input Range
0 TC type L 0 / +900 °C
1 TC type J 0 / +999 °C (0316)
0 / +1000 °C (0216)
2 TC type K 0 / +999 °C (0316)
0 / +1370 (0216)
3 TC type N 0 / +999 °C (0316)
0 / +1400 °C (0216)
4 RTD type Pt 100 -199 /+800 °C (0316)
-200/+800°C (0216)
5 RTD type Pt 100 -19.9/ +99.9 °C (0316)
-199.9/+400.0 °C (0216)
6 TC type T 0 / +400 °C
8 TC type L 0 / 999 °F (0316)
0 / 1652 °F (0216)
9 TC type J 0 / 999 °F (0316)
0 / 1832 °F (0216)
10 TC type K 0 / 999 °F (0316)
0 / 2498 °F (0216)
11 TC type N 0 / 999 °F (0316)
0 / 2552 °F (0216)
12 RTD type Pt 100 -199 / 999 °F (0316)
-328 / 1472 °F (0216)
13 TC type T 0 / 752 °F
parameters (SP, SP2 and t can always be
modified).
If the modification of the parameters has been
enabled, the passage in configuration is free.
If not it will be allowed by entering, when
requested, the numerical value programmed in
P11, or master key code.
P11 = 500/999P11 = 500/999
P11 = 500/999P11 = 500/999
P11 = 500/999 As forthe previouspoint,withthe
difference that alarm thresholds (AL and AL2) can
be modified as well as SP, SP2 and t.
In the two previous cases, with P14 = On, the
parameters set as not modifiable can however be
displayed. With P14 = OFF they are not.
To set P11 and P14 see section 4.4.
4.34.3
4.34.3
4.3 ACCESS TO THE CONFIGURATIONACCESS TO THE CONFIGURATION
ACCESS TO THE CONFIGURATIONACCESS TO THE CONFIGURATION
ACCESS TO THE CONFIGURATION
PROCEDUREPROCEDURE
PROCEDUREPROCEDURE
PROCEDURE
To access the configuration, press and
simultaneously (press first and immediately
afterwards ) keeping both the pushbuttons
pressed for three seconds.
In the model 0316 the lower display will show Cnf,
theupperOFF.Inmodel0216OFF andCnFwill
appearalternatively.
Pressorwithin 10seconds tosetON, then
confirm with .
If the device is in the protected condition (see
previous section), the lower display (0316) shows
Cnf, the upper a dashed line (instead of OFF). In
model0216 thetwowordingsappearalternately.
By means or enter the value entered in P11,
or master key value. Press to confirm.
The instrument is now in configuration mode, and
thedisplayshowsCnf steadily for bothmodels.
Via we advance to the first parameters.
Inconfiguration, thelowerdisplay showsthe code
of the parameter (P1-P28), the upper the
02-0316-1-DER.pmd 22/04/2004, 16.197

8
GBGB
GBGB
GB
NOTE:NOTE:
NOTE:NOTE:
NOTE: When P1 has been changed, the P2 and
P10 parametrer will be forced to the minimum
value of the selected range while the P3 parameter
will be forced to the maximum value of the
selected range .
P2 = Initial scale valueP2 = Initial scale value
P2 = Initial scale valueP2 = Initial scale value
P2 = Initial scale value
Initial scale value for input from thermocouple/
Resistance Temperature Detector.
NOTESNOTES
NOTESNOTES
NOTES:
1) When P2 has been modified, the rL parameter
will be aligned to it and rH parameter will be
forced to P3 value is rH < rL.
2) When P2 has been modified, if the alarms are
programmed as process alarms (P5=1 and/or
P22=1) and the alarm thresholds are out of
range, AL.1 and/or AL. 2 will be aligned to P2.
P3 = Full scale valueP3 = Full scale value
P3 = Full scale valueP3 = Full scale value
P3 = Full scale value
Full scale value for input from thermocouple/
Resistance Temperature Detector.
NOTESNOTES
NOTESNOTES
NOTES:
1) The minimum input span (P3 - P2) is 300°C or
600°F for TC input and 100°C or 200°F for RTD
input.
3) When P3 has been modified, the rH parameter
will be aligned to it and rl parameter will be
forced to P2 value is rl > rH.
4) When P3 has been modified, if the alarms are
programmed as process alarms (P5=1 and/or
P22=1) and the alarm thresholds are out of
range, AL.1 and/or AL. 2 will be aligned to P3.
P4 = Out 1 actionP4 = Out 1 action
P4 = Out 1 actionP4 = Out 1 action
P4 = Out 1 action
This parameter is not modifiable when P5 = 5
rEU = reverseaction(Heating)
dir = directaction(Cooling)
P5 = Function of Out 2P5 = Function of Out 2
P5 = Function of Out 2P5 = Function of Out 2
P5 = Function of Out 2
0 = Not used or used as event (P27 = 3, 4, 6, 7)
1 = Alarm 1 output - Process alarm
2 = Alarm 1 output - Band alarm
3 = Alarm 1 output - Deviation alarm
4 = Alarm 1 output - Instrument failure alarm
5=Cooling out
NOTES:NOTES:
NOTES:NOTES:
NOTES:
1) Setting P5 = 1, 2, 3:
- if parameter OLH
is less than 0, it is set to
100;
- if parameter IP is less than 0, it is set to 30;
- if parameters AL1 is out of range, it will be
aligned to the lowest value.
2) Setting P5 = 0 or 4:
- if parameter OLH
isless than 0,itisset to 100;
- if parameter IP is less than 0, it is set to 30;
3) Setting P5 = 5:
- parameter P4 automatically assumes the
value“rEU”;
- if parameter P16 is out of range, it will be
aligned to the lowest value;
- if parameter Pb is not 0 and is lower than 1.5,
it is set to 1.5.
4) Setting P5 different 0:
- if P27 parameter is equal to 3, 4, 6 or 7 it will
be forced to 0.
t
Input
t
Input
t
Out
t
Out
ReverseReverse
ReverseReverse
Reverse DirectDirect
DirectDirect
Direct
02-0316-1-DER.pmd 22/04/2004, 16.198

9
GBGB
GBGB
GB
P6 = Out 2 configurationP6 = Out 2 configuration
P6 = Out 2 configurationP6 = Out 2 configuration
P6 = Out 2 configuration
P6 is skipped when P5 = 0.
If P5 = 1, 3 or 4;
H.A. =High alarm with automatic reset
L.A. =Low alarm withautomaticreset
H.L. =High alarm with manual reset
L.L. =Low alarm with manual reset
When P5 = 4, the "high" or "low" selection has no
effect.
If P5 = 2:
H.A. =out of band withautomaticreset
L.A. =in band withautomaticreset
H.L. =out of band with manual reset
L.L. =in band with manual reset
When P5 = 5 this parameter selects the cooling
medium.
AIr = air OIL = oil H2O =water
NOTENOTE
NOTENOTE
NOTE: Modifying parameter P6 automatically
updates the values of the cooling cycle time and
thecooling gain.
P6 C2 RC
Air 10 (s) 1
OIL 4 (s) 0.8
H2O 2 (s) 0.4
P7 = Alarm 1 actionP7 = Alarm 1 action
P7 = Alarm 1 actionP7 = Alarm 1 action
P7 = Alarm 1 action
Only available when P5 is different from 0 or 5.
rEU = reverse (relay de-energized in alarm
condition)
dir = direct (relay energized in alarm condition)
P8 = Stand-by of the alarm 1P8 = Stand-by of the alarm 1
P8 = Stand-by of the alarm 1P8 = Stand-by of the alarm 1
P8 = Stand-by of the alarm 1
Only available when P5 is 1, 2 or 3.
OFF = stand-bydisabled
ON = stand-byenabled
NOTENOTE
NOTENOTE
NOTE: For band or deviation alarm, the alarm
stand-byfunctiondisablesthealarmindicationat
instrumentstartup and after asetpoint
modificationuntilthe processvariablereaches the
alarmthreshold.
Forprocessalarm, thestand-by functionis
activatedat startup only.
P9 = OFFSET applied to the measured valueP9 = OFFSET applied to the measured value
P9 = OFFSET applied to the measured valueP9 = OFFSET applied to the measured value
P9 = OFFSET applied to the measured value
This OFFSET is applied along the whole span.
When P1= 5 P9isprogrammablefrom -19.9
to19.9°C.
When P1 ≠5 P9 is programmablefrom-199
to 199°C or °F.
P10P10
P10P10
P10 ==
==
=Threshold of the “Soft Start” functionThreshold of the “Soft Start” function
Threshold of the “Soft Start” functionThreshold of the “Soft Start” function
Threshold of the “Soft Start” function
The“Softstart”functionlimitsthe maximumout
power(see OLH operativeparameter)fora
programmable time (see tOL operative parameter)
at the instrument start up when the measured
valueislowerthen the programmed threshold.
P10 is the threshold value, in engineering units.
Changing P1 parameter value, P10 parameter will
be forced to the minimum range value of the new
selected range.
Real curve
Readout
Adjusted
curve
Input
P9
02-0316-1-DER.pmd 22/04/2004, 16.199

10
GBGB
GBGB
GB
P11P11
P11P11
P11 ==
==
=Safety lockSafety lock
Safety lockSafety lock
Safety lock
0 = No parameter protection.The device is
always in “unlock” condition and all the
parameters can be always modified.
1 = None parameter, with the exception of
parameters from SP to t, can be modified.
2/499 = This combination numberis a secret
value, to be used in operative mode, to place
the device from the “lock” to the “unlock”
condition (the parameters from SP to tare not
subjected to the lock/unlock rule)
500/999 = This combination number is a secret
value, to be used in operative mode, to place
the device from the “lock” to the “unlock”
condition (the parameters from SP to tand
AL.1 – AL.2 are not subjected to the
lock/unlockrule)
P12P12
P12P12
P12 ==
==
=Out maximum rate of riseOut maximum rate of rise
Out maximum rate of riseOut maximum rate of rise
Out maximum rate of rise
This limit will be used if Pb is different from 0
only.
Programmable from 1 to 25% of the out signal
per second.
Over 25%/s the instrument displays “InF” to
indicate the exclusion of the limitation.
This limit have no effect if the selected contol
algorithmis ON/OFFtype(PB=0)
P13 – FILTER ON INPUT MEASUREP13 – FILTER ON INPUT MEASURE
P13 – FILTER ON INPUT MEASUREP13 – FILTER ON INPUT MEASURE
P13 – FILTER ON INPUT MEASURE
OFF = Filter disabled
On = Filter enabled
P14 =P14 =
P14 =P14 =
P14 = Protected parameters displayProtected parameters display
Protected parameters displayProtected parameters display
Protected parameters display
This parameter is available if P11 is not 0.
This parameter enables/disables the display of
the protected parameter during "operative mode".
OFF = the protected parameters are not
displayed
ON = the protected parameters are displayed
P15P15
P15P15
P15 --
--
-SMART function enabling/SMART function enabling/
SMART function enabling/SMART function enabling/
SMART function enabling/
disablingdisabling
disablingdisabling
disabling
0 = The SMART function is disabled
1 = SMARTfunctionenabling/disablingis
NOTNOT
NOTNOT
NOT protectedby thesafety code.
2 = SMARTfunctionenabling/disablingis
protected by the safety code.
P16P16
P16P16
P16 --
--
-Maximum value of the proportional bandMaximum value of the proportional band
Maximum value of the proportional bandMaximum value of the proportional band
Maximum value of the proportional band
automatically settable by theautomatically settable by the
automatically settable by theautomatically settable by the
automatically settable by the
SMART functionSMART function
SMART functionSMART function
SMART function
This parameter is available if P15 is not 0. It can
assume the following values:
model 0316: between P17 or P18 and 99.9%
model 0216: between P17 or P18 and 100.0%
P17P17
P17P17
P17 --
--
-Proportional minimum band valueProportional minimum band value
Proportional minimum band valueProportional minimum band value
Proportional minimum band value
automatically settable by theautomatically settable by the
automatically settable by theautomatically settable by the
automatically settable by the
SMART function ( one control outSMART function ( one control out
SMART function ( one control outSMART function ( one control out
SMART function ( one control out
only)only)
only)only)
only)
This parameter is only displayed if P5 is not 5 and
P15 is not 0.
It may be programmed from 1.0% to the value of
P16.
P18P18
P18P18
P18 --
--
-Proportional minimum band valueProportional minimum band value
Proportional minimum band valueProportional minimum band value
Proportional minimum band value
automatically settable by theautomatically settable by the
automatically settable by theautomatically settable by the
automatically settable by the
SMART function (two control outs,SMART function (two control outs,
SMART function (two control outs,SMART function (two control outs,
SMART function (two control outs,
heating/cooling)heating/cooling)
heating/cooling)heating/cooling)
heating/cooling)
This parameter is only present if P5 is 5 and P15
is not 0.
This parameter may be programmed from 1.5%
to the value of P16.
02-0316-1-DER.pmd 22/04/2004, 16.1910

11
GBGB
GBGB
GB
P19P19
P19P19
P19 ==
==
=Automatic calculation ofAutomatic calculation of
Automatic calculation ofAutomatic calculation of
Automatic calculation of
"relative cooling gain""relative cooling gain"
"relative cooling gain""relative cooling gain"
"relative cooling gain"
This parameter is only present if P5 is 5 and P15
is not 0.
OFF =the SMART function does NOTNOT
NOTNOT
NOT
calculates the "relative cooling gain".
ON = the SMART function calculates the
"relative cooling gain".
P20P20
P20P20
P20 ==
==
=Minimum integral time valueMinimum integral time value
Minimum integral time valueMinimum integral time value
Minimum integral time value
calculated by the SMART functioncalculated by the SMART function
calculated by the SMART functioncalculated by the SMART function
calculated by the SMART function
This parameter is only present if P15 is not 0.
It can assume the following values:
model 0316: between 0.1 (10 seconds) and 2.0 (2
minutes)
model 0216: between 00.01 (1 second) and 2.00
(2 minutes).
P21P21
P21P21
P21 ==
==
=Extension of the anti-reset-windExtension of the anti-reset-wind
Extension of the anti-reset-windExtension of the anti-reset-wind
Extension of the anti-reset-wind
upup
upup
up
Span: from -30 to +30 % of the proportional
band.
NOTENOTE
NOTENOTE
NOTE: a positive value increases the high limit
of the anti-reset-wind up (over set point) while a
negative value decreases the low limit of the
anti-reset-wind up (under set point).
P22 = OPTION FEATURE(Out3 orP22 = OPTION FEATURE(Out3 or
P22 = OPTION FEATURE(Out3 orP22 = OPTION FEATURE(Out3 or
P22 = OPTION FEATURE(Out3 or
digital input)digital input)
digital input)digital input)
digital input)
0=Outputnotprovided
1=Out3 used as Alarm 2 output – Process alarm
2=Out3 used as Alarm 2 output – Band alarm
3=Out3 used as Alarm 2 output –Deviation alarm
4=Digitalinputenabled
NOTENOTE
NOTENOTE
NOTE: Select option feature in according to
mountedHWcircuitry.
Noneautomaticrecognize isprovided
When P22 = 1, 2, 3 the parameter AL2 will be
checked and set to its low limit if out of range
P23 = Alarm 2 configurationP23 = Alarm 2 configuration
P23 = Alarm 2 configurationP23 = Alarm 2 configuration
P23 = Alarm 2 configuration
P23 is skipped when P22 is equal to 0
If P22 = 1 or 3
H.A. =High alarm with automatic reset
L.A. =Low alarm withautomaticreset
H.L. =High alarm with manual reset
L.L.=Low alarm with manual reset
If P22 = 2:
H.A. =out of band with automatic reset
L.A. =in band with automatic reset
H.L. =out of band with manual reset
L.L.=in band with manual reset
P24 = Alarm 2 actionP24 = Alarm 2 action
P24 = Alarm 2 actionP24 = Alarm 2 action
P24 = Alarm 2 action
P24 is available when P22 is 1, 2 or 3.
rEU = reverse (relay de-energized in alarm
condition)
dir = direct(relayenergizedin alarm condition)
P25 = Stand-by of the alarm 2P25 = Stand-by of the alarm 2
P25 = Stand-by of the alarm 2P25 = Stand-by of the alarm 2
P25 = Stand-by of the alarm 2
P25 is available when P22 is 1, 2 or 3.
OFF = stand-bydisabled
ON = stand-byenabled
NOTENOTE
NOTENOTE
NOTE: The alarm stand-by function disables the
alarm indication at instrument start up and after a
set point modification until the process variable
reaches the alarm threshold.
P26 =P26 =
P26 =P26 =
P26 = Not usedNot used
Not usedNot used
Not used
02-0316-1-DER.pmd 22/04/2004, 16.1911

12
GBGB
GBGB
GB
P27 – FEATURE FUNCTIONP27 – FEATURE FUNCTION
P27 – FEATURE FUNCTIONP27 – FEATURE FUNCTION
P27 – FEATURE FUNCTION
0 = None
1 = SP/SP2 selection
2 up to 5 = Timer function (for SP/SP2
selection)
6 up to 8 = Timer function (for enable/disable
controloutput)
(seeTimerFunctiondescription)
When P27 = 1, 2, 5 the parameter sp2 will be
checked and set to rL if out of range
When P27 = 3, 4 the parameter sp2 will be
checked and set to rL if out of range and
parameter P5 is forced to 0
When P27 = 6,7 the parameter P5 is forced to 0
When P27 is < 6 and it was >= 6, the control
output is forced “enable” at the next start-up.
Timer functionsTimer functions
Timer functionsTimer functions
Timer functions
Notes about all timer modes:
1) Atpoweroffthetimevalueandstatuswillbereset.
2) The time parameter (t) can always be modified
but the new value become operative at the
next start time only.
Timer mode 1 [P27 = 2]Timer mode 1 [P27 = 2]
Timer mode 1 [P27 = 2]Timer mode 1 [P27 = 2]
Timer mode 1 [P27 = 2]
If the logic input remains in open condition for
more than a programmed time the instrument
goesautomaticallyat a stand bytemperature
(SP2).
The time count is reset when the logic input is
closed.
For other details see paragraph "5.7 Timer"5.7 Timer
"5.7 Timer"5.7 Timer
"5.7 Timer
modes description".modes description".
modes description".modes description".
modes description".
Timer mode 2 [P27 = 3]Timer mode 2 [P27 = 3]
Timer mode 2 [P27 = 3]Timer mode 2 [P27 = 3]
Timer mode 2 [P27 = 3]
When the contact is closed, the instrument
controls using SP as operative set point.
When the contact has been opened the
instrument selects SP2 as operative set point
and starts the time count down.
NOTE:NOTE:
NOTE:NOTE:
NOTE: that the guarantee soak function can be
applied to this timer mode (see P28 parameter)
When the time count is equal to 0 the instrument
comes back to the SP set point and the output 2
will be energized.
The Out 2 reset will be made when the logic input
will be closed again.
For other details see paragraph "5.7 Timer"5.7 Timer
"5.7 Timer"5.7 Timer
"5.7 Timer
modes description".modes description".
modes description".modes description".
modes description".
Timer mode 3 [P27 = 4]Timer mode 3 [P27 = 4]
Timer mode 3 [P27 = 4]Timer mode 3 [P27 = 4]
Timer mode 3 [P27 = 4]
When the contact is closed, the instrument
controls using SP as operative set point.
When the contact has been opened the
instrument operate as follows:
- it selects SP2 as operative set point
- it starts the time count down
- it energizes the Output 2
NOTE:NOTE:
NOTE:NOTE:
NOTE: that the guarantee soak function can be
applied to this timer mode (see P28 parameter)
When the time count is equal to 0 the instrument
comes back to the SP set point and the output 2
will be reset.
For other details see paragraph "5.7 Timer"5.7 Timer
"5.7 Timer"5.7 Timer
"5.7 Timer
modes description".modes description".
modes description".modes description".
modes description".
02-0316-1-DER.pmd 22/04/2004, 16.1912

13
GBGB
GBGB
GB
Timer mode 4 [P27 = 5]Timer mode 4 [P27 = 5]
Timer mode 4 [P27 = 5]Timer mode 4 [P27 = 5]
Timer mode 4 [P27 = 5]
The instrument operates using SP set point and
the timer is normally reset.
When the instrument detects the transfer from
contact open to close it selects SP2 as operative
set point and starts the time count down.
NOTE:NOTE:
NOTE:NOTE:
NOTE: that the guarantee soak function can be
applied to this timer mode (see P28 parameter)
When the time count is equal to 0 the instrument
comes back to the SP set point.
For other details see paragraph "5.7 Timer"5.7 Timer
"5.7 Timer"5.7 Timer
"5.7 Timer
modes description".modes description".
modes description".modes description".
modes description".
Timer mode 5 [P27 = 6]Timer mode 5 [P27 = 6]
Timer mode 5 [P27 = 6]Timer mode 5 [P27 = 6]
Timer mode 5 [P27 = 6]
The instrument start in "Power OFF" mode and it
remains in "Power OFF" mode until the contact is
closed.
Whenthecontact has been openedtheinstrument
startsthecontrolusing SP set point andstartsthe
time count down.
NOTES:NOTES:
NOTES:NOTES:
NOTES:
1) The guarantee soak function can be applied to
this timer mode (see P28 parameter)
2) The transfer from "Power OFF" mode to
AUTOMATIC mode starts the "Soft start" and
the "alarm masking" functions (if programmed).
When the time count is equal to 0 the instrument
comes back to the "Power OFF" mode and the
output 2 will be energized.
The Out 2 reset will be made when the logic input
will be closed.
For other details see paragraph "5.7 Timer"5.7 Timer
"5.7 Timer"5.7 Timer
"5.7 Timer
modes description".modes description".
modes description".modes description".
modes description".
Timer mode 6 [P27 = 7]Timer mode 6 [P27 = 7]
Timer mode 6 [P27 = 7]Timer mode 6 [P27 = 7]
Timer mode 6 [P27 = 7]
The instrument starts in "Power OFF" mode and
it remains in "Power OFF" mode until the contact
is closed.
When the contact has been opened the
instrument operate as follows:
- it starts the control using SP set point.
- it starts the time count down
- it energizes the Output 2
NOTES:NOTES:
NOTES:NOTES:
NOTES:
1) The guarantee soak function can be applied to
this timer mode (see P28 parameter)
2) The transfer from "Power OFF" mode to
AUTOMATIC mode starts the "Soft start" and
the "alarm masking" functions (if programmed).
When the time count is equal to 0 the instrument
comes back to the "Power OFF" mode and the
output2will be reset.
For other details see paragraph "5.7 Timer"5.7 Timer
"5.7 Timer"5.7 Timer
"5.7 Timer
modes description".modes description".
modes description".modes description".
modes description".
02-0316-1-DER.pmd 22/04/2004, 16.1913

14
GBGB
GBGB
GB
Timer mode 7 [P27 = 8]Timer mode 7 [P27 = 8]
Timer mode 7 [P27 = 8]Timer mode 7 [P27 = 8]
Timer mode 7 [P27 = 8]
The instrument starts in "Power OFF" mode and
it remains in "Power OFF" mode until a transfer
from open to close of the logic input is detected.
When the instrument detects the transfer from
contactopento closeitstarts thecontrolusing SP
set point and starts the time count down.
NOTES:NOTES:
NOTES:NOTES:
NOTES:
1) The guarantee soak function can be applied to
this timer mode (see P28 parameter)
2) The transfer from "Power OFF" mode to
AUTOMATIC mode starts the "Soft start" and
the "alarm masking" functions (if programmed).
When the time count is equal to 0 the instrument
comes back to the "Power OFF" mode .
For other details see paragraph "5.7 Timer"5.7 Timer
"5.7 Timer"5.7 Timer
"5.7 Timer
modes description".modes description".
modes description".modes description".
modes description".
P28 – BAND FOR TRACKP28 – BAND FOR TRACK
P28 – BAND FOR TRACKP28 – BAND FOR TRACK
P28 – BAND FOR TRACK
(Present if P27 is greater than 2)
0.1 / 50.0 for input range 5
1 / 500 for all other input ranges
Above max value the display shows
“OFF” meaning that the tracking is
disabled
5.5.
5.5.
5. OPERATIVE MODEOPERATIVE MODE
OPERATIVE MODEOPERATIVE MODE
OPERATIVE MODE
The display and modification of the operative
parameters can be protected by a secret code.
For more information see section 4.2.
5.15.1
5.15.1
5.1PRELIMINARY COMMENTSPRELIMINARY COMMENTS
PRELIMINARY COMMENTSPRELIMINARY COMMENTS
PRELIMINARY COMMENTS
It is assumed, at this point, that the instrument
has been correctly configured as indicated in
Section 4.
- Model 0316 displays the measured value on the
upper display: the lower display is normally
used to display the operating set point (below
this condition is defined as “Normal display”) or
the remaining time (when the timer is running).
- Model 0216 displays:
- the measured value (below this condition is
defined as “Normal display”) or
- the operating set point (in this case the SP
led lights up) or
- the remaining time when the timer is running
(in this case the decimal point on the left hand
the LSD will flash).
To change from the display of the set point to
that of the measured value, or vice versa, press
pushbutton .
All the parameters can be displayed sequentially
by pressing the pushbutton.
- Model 0316 displays the abbreviated name of
the selected parameter on the lower display, on
the upper it will display the selected value.
- Model 0216 displays alternately the name of
the parameter and its value: during the
modification it displays only the value.
02-0316-1-DER.pmd 22/04/2004, 16.1914
This manual suits for next models
1
Table of contents
Other Eurotherm Temperature Controllers manuals

Eurotherm
Eurotherm 3116 User manual

Eurotherm
Eurotherm 2216e Owner's manual

Eurotherm
Eurotherm 2108i Wiring diagram

Eurotherm
Eurotherm 2208L User manual
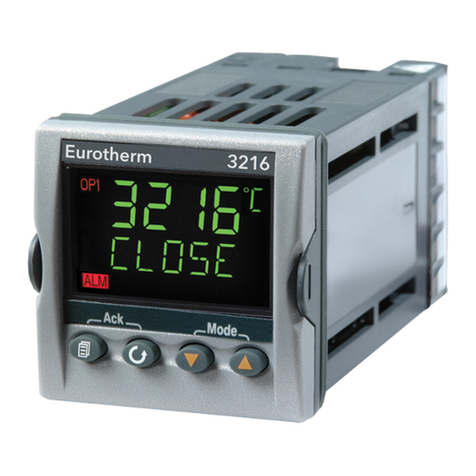
Eurotherm
Eurotherm Invensys 3216 User manual
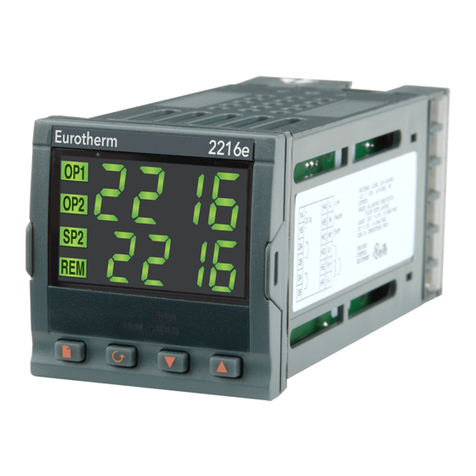
Eurotherm
Eurotherm 2216e Owner's manual
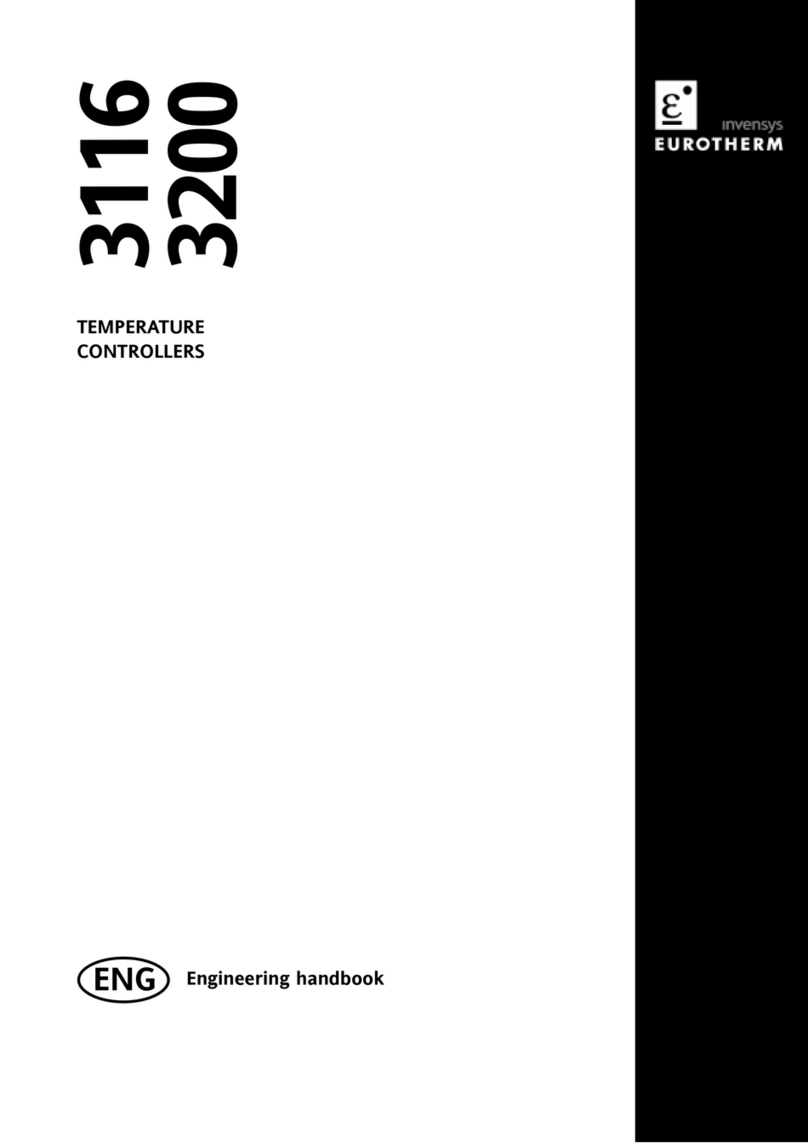
Eurotherm
Eurotherm 3116 User manual

Eurotherm
Eurotherm 2208e Owner's manual

Eurotherm
Eurotherm Invensys 3216 User manual
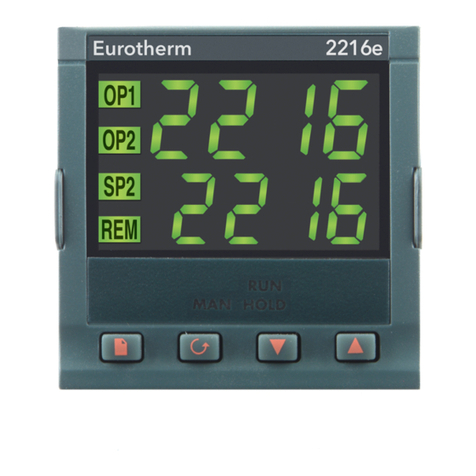
Eurotherm
Eurotherm 2116 User manual