Evoqua V10K User manual

Wallace & Tiernan® Instruction
Manual V10k™ Gas Feeder
W3T292561 / WT.025.100.000.GE.IM.0914
Suite 3, 2nd Floor, One 60 London Road, Sevenoaks, TN13 1BT
Tel.: +44 1732 771777 Fax: +44 1732 771800 www.evoqua.com

Important Notice
Evoqua Water Technologies Instruction Manuals are the safety documents for their products. The information provided therein
is in accordance with the best practices known at the time of issue and, if fully implemented, should enable the user to operate
the plant in the safest possible manner. It is therefore most important that instructions be read and understood prior to the
installation, operation or maintenance of the plant.
Notes
Where necessary, special instructions are provided and are
quoted under the following headings:
WARNING: A warning is given in instances where
failure to observe the instruction could result in injury to
personnel.
CAUTION: Cautions are given where failure to
observe the instruction may result in equipment damage,
or pollution to an allied system.
NOTE: Notes are provided to give additional emphasis to
particular points of detail.
The following recommendations are made to ensure safe
and efcient operation:-
1 Only suitably qualied personnel should install, operate
and maintain the equipment.
2 Only Evoqua Water Technologies manufactured or
approved parts should be used.
3 The equipment should not be used for any purpose other
than that for which it was supplied.
4 If equipment being supplied is being put into storage or
not being commissioned immediately, or if the plant is being
de-commissioned, Evoqua Water Technologies urge that
they be contacted for detailed advice.
In an effort to make progressive improvements to products,
changes indesign maybe incorporatedfrom timeto time, which
may not be reected immediately in the instruction manual.
If in doubt, contact Evoqua Water Technologies quoting the
equipment serial number; serial numbers are essential for
effective communication and proper equipment identication.
The equipment described in this manual may be used with
substances that themselves may be hazardous to personnel
safety. It is essential that persons employed in the vacinity of
such substances be aware of the appropriate safety practices
and the location of suitable safety equipment. Provision of
safety cards and codes of practice concerning hazardous
substance should be made by the supplier of the substance.
Warranty
The equipment supplied is guaranteed against mechanical
defect notied to the Seller within a period of 1 year from
the date of delivery. For such guarantee to be valid the
purchaser must notify the seller in writing immediately
such defect becomes apparent. If the Seller so requires,
the Purchaser shall return the defective equipment (at the
Purchaser’s expense) to the Seller. The Seller undertakes
that it will, at its own option and its own expense, and by way
of full discharge of its guarantee obligation hereunder, either
repair, or supply a replacement for the defective equipment,
or refund any purchase monies paid to it in respect of any
such defective equipment, or portion thereof. If title to the
defective equipment is at the time of such replacement or
refund vested in the Purchaser, then title shall thereupon
vest in the Seller. Replacement material situated outside
the U.K. will be supplied F.O.B. U.K. Port. The guarantee
given in this clause shall not be operative and enforceable
if the equipment is not operated strictly in accordance
with the sellers instruction, or in the respect of any defect
arising from accident, deliberate act, misuse, neglect or
from a breach from the terms of the following clause, or
in respect of any defect arising through damage incurred
while being transported after delivery of the equipment, or if
the equipment has been altered or modied in any way by
any person other than the seller, or in respect of any other
cause whatsoever which lies beyond the Sellers control.
The Purchaser must comply with all user instructions
and safety recommendations issued by the Seller, and
must install, commission and maintain the equipment in
accordance with good engineering practice, and under the
supervision of suitably qualied personnel, and the Seller
shall not be liable to the Purchaser for any loss suffered
as a result of the Purchaser’s breach of the terms of this
clause.
Subject to this guarantee all conditions, warranties and
representations, whether expressed or implied (by statute
or otherwise) relating to the equipment, are hereby excluded
in so far as they can be excluded without such exclusion
being void or unenforceable at law.
Wallace & Tiernan, Barrier, Chem-Ad, DEPOLOX, OSEC, and V10k are trademarks of Evoqua, its subsidiaries or affiliates.
The designations used in this publication may be trademarks whose use by third parties for their own purposes could
violate the rights of the owners.All rights, especially those to duplication and distribution as well as translation, are
reserved. No part of this document may be reproduced in any form (printing, photocopying, microlm or any other
method) or saved, processed, duplicated or distributed by the use of electronic systems without the express written
consent of Evoqua Water Technologies.

International Contact Information
Area Phone email


TYPE V10k GAS FEEDER
W3T292561 / WT.025.100.000.GE.IM.0914 1
INTRODUCTION
The Wallace & Tiernan Type V10k Gas Feeder described in this book,
is designed for the precise metering of chlorine, sulphur dioxide, carbon
dioxide or ammonia gas; to mix the gas with water and deliver the
resultant solution to a point-of-application. The V10k is a manually
operated unit with a automatic control option.
This manual has been produced to enable the user to obtain maximum
service from the equipment and comprises installation, operating
instructions, maintenance and spare pats information. Minor changes
may be made to the equipment that are not immediately reected in the
manual - if such a change appears to have been made to your equipment,
contact Evoqua Water Technologies for information.
Our guarantee is conditional upon the equipment being treated in
accordance with the contents of this manual and its supplements. We
invite particular attention to it and urge that its contents be thoroughly
understood and rigidly followed.
Evoqua Water Technologies
CONTENTS
TITLE SECTION
Warnings and notes on protective clothing
Generic installation guidelines
General description 1
Principle of operation 1.1
Gas feeder 1.2
Injectors 1.3
Vacuum demand valve 1.4
Vacuum switches 1.5
Technical data 1.6
Installation 2
Unpacking the equipment 2.1
Location requirements 2.2
Installing the gas feeder 2.3
Installing the injector 2.4
Point of application 2.5
Water supply and
solution delivery pipelines 2.6
Installing the vacuum demand valve 2.7
Electrical connections 2.8

TYPE V10k GAS FEEDER
2W3T292561 / WT.025.100.000.GE.IM.0914
Operation 3
Preparation for initial operation 3.1
Operating procedures 3.2
Changing gas cylinders 3.3
Intermittent start/stop 3.4
Electronic controller 3.5
Maintenance 4
Cleaning the parts 4.1
Preventive maintenance kits 4.2
Maintenance of the Gas Feeder 4.3
Maintenance of the injector 4.4
Maintenance of the vacuum demand valve 4.5
Maintenance of aux. cylinder, drum and
header valves 4.6
Adjusting the electric plug positioner 4.7
Fault nding 4.8
ILLUSTRATIONS
Typical V10k dosing system Fig.1
V10k Gas Feeder Fig.2
V10k owmeters Fig.2A
Vacuum differential valve Fig.3
U.96273 injector Fig.4
U.96274 injector Fig.5
U.96275 injector Fig.6
U.96276 injector Fig.7
Single function vacuum switch Fig.8
Double function vacuum switch Fig.9
Universal yoke assembly Fig.10
Chlorine Institute yoke assembly Fig.11
Auxiliary cylinder valve Fig.12
Auxiliary drum valve Fig.13
Large header valve Fig.14
Vacuum line connections Fig.15
Header manifolds — multi-demand valve Fig.16A
Header manifolds — multi-cylinder Fig.16B
External connection diagram Fig.17
Injector operating requirements
Maintaining the suction demand valve
Activated carbon lter UXA93889

TYPE V10k GAS FEEDER
W3T292561 / WT.025.100.000.GE.IM.0914 3
WARNINGS
1 HAZARDOUS CHEMICALS
All users of this gas feeder should be made aware of the problems
associated with handling chlorine, sulphur dioxide and ammonia in
either liquid or gaseous form and the effects of exposure to their fumes.
Reference should be made to the literature available from the suppliers
of these chemicals, paying particular attention to information and advice
on protective clothing.
2 ELECTRICAL SAFETY
Mains voltage can kill. Before carrying out maintenance or repair, persons
concerned must ensure that the equipment is isolated from the electrical
supply and make tests to verify that isolation is complete.
If the supply cannot be isolated , functional testing, maintenance and
repairs must be undertaken only by persons who are fully aware of the
danger and who have taken adequate precautions.
3 GENERAL
To avoid possible severe personal injury or damage to plant this
equipment should be installed, operated and serviced only by trained,
qualied personnel who are thoroughly familiar with the entire contents
of this instruction book.
The gas feeder and injector are designed to operate under vacuum
only and, must under no circumstances be presented with gas above
atmospheric pressure.

TYPE V10k GAS FEEDER
4W3T292561 / WT.025.100.000.GE.IM.0914
NOTES ON PROTECTIVE EQUIPMENT AND CLOTHING
The following warning is general in nature due to the variety of hazardous
chemicals this equipment is capable of handling.
WARNING: When dealing with hazardous material it is the responsibility
of the equipment user to obtain and follow all safety precautions
recommended by the material manufacturer.
It is good general practice to make use of the following types of protective
clothing when handling any hazardous liquid. IT IS RECOMMENDED
THAT SUCH PROTECTIVE EQUIPMENT BE USED BY ALL
PERSONS SERVICING THIS EQUIPMENT, ASSOCIATED PIPING,
TUBING, VALVES, AND ACCESSORIES, WHEN THE EQUIPMENT
IS HANDLING ANY HAZARDOUS LIQUID OR GAS.
1 Goggles, exible tting, hooded
ventilation (per BS EN 2092)
2 Face shield (BS EN 2092)
3 Chemical apron (BS EN 7184)
4 Chemical gloves (BS EN 7184)
5 Self contained, positive pressure
breathing apparatus (BS 4667)
NOTE : 1 BS EN 7028 “practice for occupational.......eye and
face protection” recommends goggles (see 1 above) as the “preferred
protection” when handling chemicals which present a hazard from splash,
acid burns or fumes; for severe exposure, a face shield (see 2 above) over
the goggles is recommended.
NOTE : 2 An eye ushing fountain and a deluge type shower may
also be recommended.

TYPE V10k GAS FEEDER
W3T292561 / WT.025.100.000.GE.IM.0914 5
GENERIC INSTALLATION GUIDELINES
FOR MAINTAINING EMC INTEGRITY
OF EQUIPMENT SUPPLIED BY EVOQUA WATER TECHNOLOGIES
The Guidelines below are general in nature. They do not guarantee
compliance with legislation. The Installers/Assemblers/End Users
of equipment supplied by Evoqua Water Technologies should satisfy
themselves as to the procedures required to ensure compliance. We
recommend that Installers/Assemblers/End Users are familiar with the
EMCD (Electromagnetic Compatibility Directive 89/336/EEC), the LVD
(Low Voltage Directive 73/23/EEC) and the MSD (Machinery Safety
Directive 86/392/EEC). The Guidelines below should not be taken as
denitive and independent advice should be sought if in doubt.
The EMC Directive is applicable to “systems” it should be noted that
some systems could be congured from apparatus supplied from different
manufacturers. The onus is on the assembler of the system to meet the
requirements of the directives.
The equipment you have been supplied with by Evoqua Water
Technologies has been tested for compliance with the EMC Directive
(Electromagnetic Compatibility Directive 89/336/EEC) and appropriately
marked. It is important that the equipment is installed in a manner that
will maintain the integrity of that EMC requirement, thus ensuring that
complete system being installed/commissioned will comply. For this
Purposes a “system” may be dened as a combination of electrical
apparatus. The term apparatus can be dened as Consisting of a product
with an intrinsic function intended for the end user and is supplied or
intended for supply or taken into service or intended to be taken into
service as a single unit.
Generic Guidelines
Having unpacked the equipment check all parts for obvious damage, If
damage is apparent contact Evoqua Water Technologies immediately. If
the system is not to be installed or commissioned immediately check
the instruction manual for any special storage instructions.
The intended mounting of all equipment should be carefully planned in
advance. The cable lengths should be accurately calculated so as to avoid
unnecessary cable jointing.
Some of the equipment may have been supplied with special signal
cables. Under no circumstances should any of these special cables be
shortened or the connectors modied, changed or removed. If the cables
supplied are too long then reference should be made to the relevant
instruction manual or typical installation drawings (If supplied) to check

TYPE V10k GAS FEEDER
6W3T292561 / WT.025.100.000.GE.IM.0914
any recommendations made as to methods of excess cable storage. If
the cables are too short contact Wallace & Tiernan for supply of correct
cables (This would normally be advised at order time).
Any screened sensor cables should be run separately from all other cables
and the screen should be earthed at the Control/Analyser equipment.
Often this will be shown on the drawings.
All other cables should be run in ridged or exible metal conduit or steel
wire armoured cable securely bonded to earth.
Low Voltage signal cables such as those to relays should be routed
separately to power cables.
All cable entries to metallic coated plastic or metal enclosures should
be via metal glands secured inside the enclosure with unpainted metal
retaining nuts and washers. In the case where plastic glands are supplied
the signal cables should be passed through the gland and the screen should
be connected and securely bonded as indicated on the drawing.
So as not to introduce conducted interference into some analysers and
controllers consideration should be given to the possible ltering of the
relay signal cables. This is very much dependant on usage. The type of
switching that the relay is being asked to perform should be considered.
In general if the relay signal is being fed to, and being processed by,
another piece of Wallace & Tiernan equipment then external ltering
will not be required.
In some instances you may nd it necessary to supply connections into
the Wallace & Tiernan equipment where glands are not provided. If this
is required by your system conguration or the equipment supplied then
care should be taken not to damage any RFI coating/screening applied
to the inside of the enclosure. In order to minimise damage we would
recommend that holes are drilled and not punched. This would also apply
to existing gland “Knockouts”.
You are now advised to read the instruction manuals of the equipment
supplied to nd any additional information that may be relevant to the
installation.

TYPE V10k GAS FEEDER
W3T292561 / WT.025.100.000.GE.IM.0914 7
1 GENERAL DESCRIPTION
The Type V10k Gas Feeder is a V-notch type, vacuum operated, gas
control unit designed to feed chlorine, sulphur dioxide, carbon dioxide
or ammonia gas into a ow of water at dose rates up to 10 kg/hour
(equivalent chlorine).
A V10k Gas Feeder system comprises the following three main items
connected together by the injector suction pipeline:-
1 The gas control unit, which houses the owmeter to give a visual
indication of the gas feed rate; the V-notch plug unit used to control
the gas feed rate and, a differential valve to maintain the vacuum
differential across the V-notch plug.
2 The remote mounted aspirator type injector, which is connected into
a suitable water supply and used to create the systems operating
vacuum.
3 The vacuum demand valve, which ts to the gas cylinder or header
valve and opens on demand (i.e. when a vacuum is applied to it)
to allow gas into the injector suction pipeline.
Operation of the V10k is controlled by starting and stopping the ow
of water through the injector. The gas feeder can be used in conjunction
with either a standard injector or an anti-syphon injector.
Gas feed rate is controlled by varying the position of the V-notch plug.
This is done either manually or automatically. Automatic control operates
in conjunction with either a ow proportional signal, a measured residual
signal or a ow and residual signal.
1.1 Principle of Operation (Fig.1)
When operating water ows through the V10k's injector a vacuum is
created which lls the injector suction pipework. This vacuum pulls
on the diaphragm of the vacuum demand valve causing the valve to
open. Gas enters the suction pipework passing through the owmeter
- where the feed rate is indicated - and the V-notch variable orice -
where the feed rate is controlled - and into the injector. Here the gas
mixes with the injector operating water and the solution passes into
the delivery pipe line.
If the injector operating water is stopped, the vacuum breaks down, the
demand valve closes and the ow of gas is shut-off.
During operation, if a leak develops in the vacuum pipeline between the
injector and the vacuum demand valve, air is drawn into the pipeline
preventing gas from escaping into the atmosphere.

TYPE V10k GAS FEEDER
8W3T292561 / WT.025.100.000.GE.IM.0914
A vacuum demand valve equipped with a pressure relief system is
available. Should the demand valve fail to close when the injector is
shut down, any gas pressure that builds up in the body of the valve will
unseat the relief diaphragm and enter the vent line.
WARNING: The V10k gas feeder is designed to operate under vacuum
only, and must, under no circumstances, be presented with gas above
atmospheric pressure.
1.2 Gas Feeder (Fig.2)
The V10k Gas Feeder comprises a chemical resistant, one piece moulded
headblock tted with a differential regulating valve, a divergent tube
owmeter, a variable orice V-notch plug assembly and a vacuum gauge.
The assembly is tted with a front cover.
Gas dosage is controlled by moving the V-notch plug in/out to varying the
size of the orice in which it ts. The vacuum across the V-notch orice
is kept constant by the differential valve. Movement of the V-notch plug
to change the gas dose rate, is done either manually or automatically.
Manual Dosing Control:
Manual dosing is controlled by winding the control knob, on the underside
of the gas feeder, anticlockwise (outwards) to increase the dosing rate or
clockwise to decrease the dosing rate.
Start/Stop Dosing Control:
Start/Stop dosing is controlled by using either a solenoid operated water
shut-off valve or a water booster pump to supply motive water to the
injector.
Automatic Dosing Control:
Automatic dosing is controlled by varying the position of the V-notch
plug in its orice, using an electric reversing motor. The motor and its
associated printed circuit card are housed in a separate enclosure and
tted, with the gas control unit, onto a wall mounted backplate. The signal
from an electronic controller (supplied separately) is used to switch the
reversing motor on/off in the appropriate direction to achieve the correct
dosing requirement.
Three forms of control system are commonly used:-
FLOW CONTROL - in a ow control system a ow proportional signal
(such as that provided by a W&T Signal Conditioning Unit (SCU)) is
used to drive the plug positioner motor in the appropriate direction.

TYPE V10k GAS FEEDER
W3T292561 / WT.025.100.000.GE.IM.0914 9
RESIDUAL CONTROL - in a residual control system a measured
residual signal (such as that provided by a W&T Process Control Unit
(PCU)) is used to drive the plug positioner motor in the appropriate
direction for correct dosing.
FLOW AND RESIDUAL CONTROL (compound loop) - in a ow
and residual control system a combination of the two signals described
above (such as that provided by a W&T Process Control Unit), is used
to drive the plug positioner motor in the appropriate direction.
The plug positioner drive is disengaged by pulling out the knob on the
front panel of the positioner housing. Once the drive is disengaged the
knob is turned manually for dosing control (e.g. in case of failure of the
automatic control system). To return to automatic control push the knob
back in, turning it slightly to allow it to engage the drive.
1.3 Injectors
Standard Injectors (Figs.4 and 6)
The standard injector used with the V10k Gas Feeder is a xed throat,
aspirator type unit which is available in two ranges; the 25mm Type
U.96273 injector for gas capacities up to 15 kg/hour and the 19mm
Type U.96275 injector for gas capacities up to 5 kg/hour. The injectors
are tted with check valves to prevent a back ow of water into the gas
feeder if the injector is subject to positive back pressure when it is shut
down or if the solution discharge line becomes blocked.
Anti-syphon Injectors (Figs.5 and 7)
The anti-syphon injector versions of both the 19mm and the 25mm
injectors are basically as described above but are tted with a second,
spring loaded, diaphragm assembly to provide a positive shut-off against
negative back pressure at the injector.
Both the standard and anti-syphon injectors are mounted remotely from
the gas control unit.
1.4 Vacuum Demand Valve
The vacuum demand valve is to ensure that gas can only ow, from
the storage cylinder or drum, into the gas supply pipelines when those
pipelines are under the vacuum created at the injector.
Two versions of the vacuum demand valve are available. A non-
switchover version for single cylinder operation and a switchover version
for two cylinder operation.

TYPE V10k GAS FEEDER
10 W3T292561 / WT.025.100.000.GE.IM.0914
The vacuum demand valve designed for automatic switchover is tted
with a mechanical detent. Moving the valve's control knob to the 'stand-
by' position (see Section 1.4.1 below) sets the detent in its latched
position. This version of the valve is used for dosing systems that are
arranged for duty and stand-by operations.
When a duty and stand-by system is running the rst vacuum demand
valve feeds gas until its respective cylinder is depleted (at approximately
1 bar g) causing an increase in the vacuum to a higher than normal level.
This provides sufcient force to unlatch the detent of the second unit.
This valve then opens and takes over the gas supply function. The rst
cylinder can then be replaced and its vacuum demand valve reset for
stand-by mode.
1.4.1 Valve Front Cover
The Front Cover of the demand valve houses the valve control mechanism
and is provided with symbols which indicate the operating condition of
the unit as follows:-
Non - switchover arrangement
OFF ON EXHAUSTED
OFF (valve closed): indicated by an empty cylinder outline with a bar
across its outlet pipeline to show that gas is prevented from owing.
ON (valve open): indicated by a shaded-in cylinder outline with the bar
removed to allow gas to ow through the supply pipeline.
EXHAUSTED (valve open but cylinder empty): indicated by an empty
cylinder outline with bar removed but no ow of gas in the supply
pipeline. In this position a red OUT OF GAS warning indicator, located
immediately above the top of the knob, is also uncovered.

TYPE V10k GAS FEEDER
W3T292561 / WT.025.100.000.GE.IM.0914 11
Switchover arrangement
OFF STAND-BY ON EXHAUSTED
OFF (valve closed): indicated by an empty cylinder outline with a bar
across its outlet pipeline to show that gas is prevented from owing.
STAND-BY (supply available but valve still closed): indicated by a
shaded-in cylinder outline with a bar across its neck and no gas in the
supply pipeline. This shows gas is available but the outlet pipeline is
closed until the gas pressure in the duty cylinder falls to the preset level
causing the changeover mechanism to operate.
ON (valve open): indicated by a shaded-in cylinder outline with the bar
removed to allow gas to ow through the supply pipeline.
EXHAUSTED (valve open but cylinder empty): indicated by an empty
cylinder outline with bar removed but no ow of gas in the supply
pipeline. In this position a red OUT OF GAS warning indicator, located
above the knob, is also uncovered.
1.4.2 Front Housing
The front housing contains the diaphragm assembly and control
mechanism. Fixed in the centre of the diaphragm is the operating shaft
which connects at its top end, via the operating lever, to the control knob.
As the control knob is moved to the required setting so the operating shaft
positions the diaphragm for the corresponding operation. The operating
shaft is also threaded which, when the control knob is manually turned
clockwise or anticlockwise will move the diaphragm into its locked or
unlocked position.
1.4.3 Back Housing
The back housing of the vacuum demand valve is tted with two check
valves, the rst in a nipple which is screwed into the housing of the
second check valve. When the operating vacuum is present the diaphragm
is pulled away from its seat and gas is allowed to enter the vacuum

TYPE V10k GAS FEEDER
12 W3T292561 / WT.025.100.000.GE.IM.0914
pipework. If the operating vacuum is lost for any reason, the diaphragm
will retract under spring pressure and shut-off the gas.
1.4.4 Pressure Relief
The pressure relief valve ts into a recess in the back housing of the demand
valve. The relief valve comprises a diaphragm, plunger and spring.
DIAPHRAGM
PLUNGER
SPRING
The face of the diaphragm is spring loaded against two openings, one
opening connects into the main chamber of the valve and the other
connects to the vent line.
Should the demand valve stems fail to seat when the operating vacuum
is shut off, gas will pass into the main chamber of the valve where its
pressure acts against the underside of relief valve diaphragm at the rst
opening. The relief valve diaphragm is forced against its spring until it
unseats at which point gas is allowed to pass through the second opening
and into the vent line.
1.4.5 Yoke Assembly (Fig.10 and 11)
The vacuum demand valve is supplied with a yoke assembly which
enables the valve to be mounted directly onto a gas cylinder or a wall
mounted header valve.
1.4.6 Heater (optional)
An optional, bolt on heater assembly is available for installations where
reliquefaction of the gas within the valve is a problem due to low external
temperatures. This unit comprises a small 110v or 230v, mains operated
heater capsule which locates in a cavity in the main body of the valve.

TYPE V10k GAS FEEDER
W3T292561 / WT.025.100.000.GE.IM.0914 13
The heater is temperature controlled by a thermostat clamped into a
recess in the side of the valve body.
1.5 Vacuum Switch (optional)
As an optional tting, the vacuum demand valve can be supplied with one
of two types of vacuum alarm switch. A single function vacuum alarm
switch tted inside the valve or a dual function vacuum alarm switch
which is mounted external to the valve.
1.5.1 Single function vacuum alarm switch (Fig.8)
The optional single function vacuum alarm switch, is tted with a single
volt free contact which is used to signal LOSS OF GAS when insufcient
injector suction is detected.
The switch is located adjacent to, and operated by, the valves vacuum
indicator. If the vacuum indicator goes to the red OUT OF GAS position,
its volt free contact will make to initiate an external alarm or to control
the operation of an associated item of equipment.
1.5.2 Dual function vacuum alarm switch (Fig.9)
The optional dual function vacuum alarm switch is mounted on a wall
adjacent to the gas control unit (or a back plate if used with an automatic
gas feeder) and connected to the gas control unit via a ptfe tube. It detects
the level of vacuum being drawn through the V-notch plug and if this level
increases to above – 60 in H2O the volt free 'GAS FAILURE' contact
will operate. If the level of vacuum drawn falls to below – 8 in H2O then
the volt free 'VACUUM FAILURE' contact will operate.
1.6 Technical Data
Accuracy of dosage ± 4% F.S.
Operating temperature 10° C to 50° C
Operating vacuum 40 - 200 mbar (green sector on
manometer)
Operating water pressure at the injector max. 21 bar at 20°C
max. 13 bar at 30°C
max. 10 bar at 40°C
max. 5.9 bar at 50°C
Positioner details:
Mains supply 230V 50 hz, 19 mA
115V 60 Hz, 46 mA
Time 0-100% 80 sec (50 Hz), 66 sec (60 Hz)
Potentiometer 1 kOhm ± 10%
Flowmeter capacities:- 0.06 - 15 kg/h (equivalent chlorine)

TYPE V10k GAS FEEDER
14 W3T292561 / WT.025.100.000.GE.IM.0914
2 INSTALLATION
WARNING: To avoid possible severe personal injury or damage to
plant this equipment should be installed, operated and serviced only by
trained qualied personnel who are thoroughly familiar with the entire
contents of this instruction book.
2.1 Unpacking the Equipment
CAUTION: Some equipment is despatched with temporary plugs tted
to the open ports/connections that come into contact with gas. These
plugs prevent the ingress of moisture and must be left in place until the
equipment is installed. Retain the plugs for use when the item is removed
from service for maintenance purposes.
Unpack the equipment in a clean, dry area, preferably at the installation
site. Open the packing only on the upper side. Take the accessories out
of the cardboard pocket above the chlorinator. Holding the chlorinator
at the mounting plate or at the positioner, NOT at the red valve shaft or
the positioner rack, lift it out of the packing case.
To prevent damage during transport the glass tube owmeter is packed
separately. Handle this glass tube very carefully. Cracks make the glass
tube useless. Check all items against the packing note to ensure that none
is discarded with the packing materials.
2.2 Location Requirements
CAUTION: To avoid personal injury by chlorine gas, install the
equipment so that in case of a fault, chlorine gas may escape within the
storage room only. Those parts of the chlorine system subject to gas
under pressure (such as tanks, reducing valves, relief valve, vent line)
should be installed in the storage room only. Refer to the national or
regional regulations.
When selecting a location for the V10k, attention should be paid to the
following requirements, placing emphasis on personnel safety.
1 An adequate supply of clean water should be available to operate
the injector which should be located as closely as possible to the
gas feeder.
2 To avoid reliquefaction of the gas in the supply line, the ambient
temperature around the gas feeder should be at least as warm as
that around the gas containers. The area should also be clean and
dry and interconnecting pipework should always be routed so that
it is not subject to draughts which would cause lower temperatures
at specic points.

TYPE V10k GAS FEEDER
W3T292561 / WT.025.100.000.GE.IM.0914 15
3 Gas containers are heavy and the location should be chosen to give
the shortest possible gas supply line, consistent with safe handling
of the containers.
4 Ensure the location is such that unauthorised persons can be
excluded from the installation.
5 Adequate access should be available to permit ease of operation
and maintenance of all plant items.
2.3 Installing the Gas Feeder
The Gas Feeder should be installed on a vertical surface, wall, etc. with
the dowels and screws supplied loose. The owmeter should be at a height
suitable for easy reading and for easy removal from the front cover.
The cover is removed by placing the thumb of the right hand on the
manometer and pulling the cover at both sides at the same time. After
mounting, slide the cover over the T - shaped rails of the body, then push
evenly on the right and left hand sides until the cover is ush with the
manometer and locked in position.
The preceding sketch shows the back plate dimensions for the automatic
version of the V10k (other back plates 432mm and 580mm wide
allow, respectively, the tting of an injector and the tting of a Signal
Conditioning Unit to the backplate). Make sure the unit is level and
doesn't distort when tightening the nuts.

TYPE V10k GAS FEEDER
16 W3T292561 / WT.025.100.000.GE.IM.0914
2.3.1 Installingtheowmeter(Fig.2A)
NOTE: The owmeter should only be tted immediately prior to
commissioning to avoid damage to the glass tube.
Apply some silicone grease to the two ‘O’ rings and place them into the
grooves. Place the owmeter tube onto the lower O-ring, the high values
of the scale at the top, press down the lower seat with two ngers, if
necessary press down the lower O-ring with the owmeter tube, position
the tube into the upper seat and slowly release the lower seat. Turn the
tube until the scale is at the front.
Insert the ‘O’ rings here
Press down here with two
fingers at the same time
2.3.2 Adjusting the electric plug positioner
The electric plug positioner is tested and adjusted in the factory before
despatch and should be ready to operate when installation and external
wiring are complete. However, if the plug positioner needs adjusting
turn to Section 4.7 of this manual for details.
2.4 Installing the Injector
CAUTION: DO NOT CUT OFF ANY PORTION OF THE TAILWAY,
If rigid PVC pipe is used, the distance between the centre of the injector
and the rst downstream bend or component should be at least 1.0m
for the injector to operate at maximum efciency. This is known as the
'recovery length'.
When installed with rigid pipework the injector may not need additional
support. However, if the injector is installed with exible pipework the
pipelines will need additional support and should be xed according to
the details shown in Fig 1.
The injector is installed in the operating water pipework in either the
vertical or the horizontal position (if not already tted to a mounting
Other manuals for V10K
2
Table of contents
Other Evoqua Measuring Instrument manuals

Evoqua
Evoqua DEPOLOX User manual

Evoqua
Evoqua WALLACE & TIERNAN SFC BA W3T166501 User manual
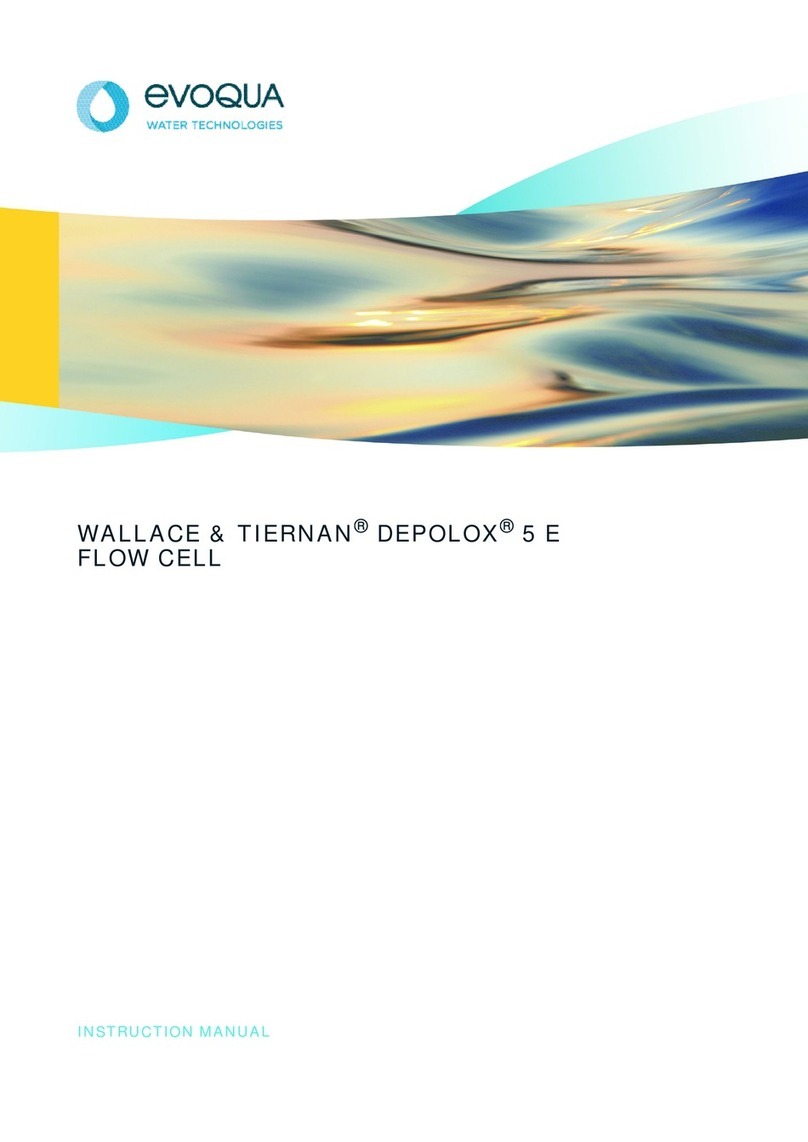
Evoqua
Evoqua WALLACE & TIERNAN DEPOLOX 5 E User manual
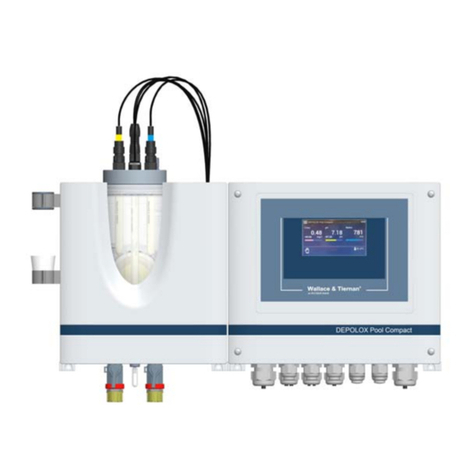
Evoqua
Evoqua DEPOLOX POOL COMPACT WALLACE & TIERNAN User manual

Evoqua
Evoqua Wallace & Tiernan SFC-SC User manual

Evoqua
Evoqua Wallace & Tiernan Depolox 3 plus User manual
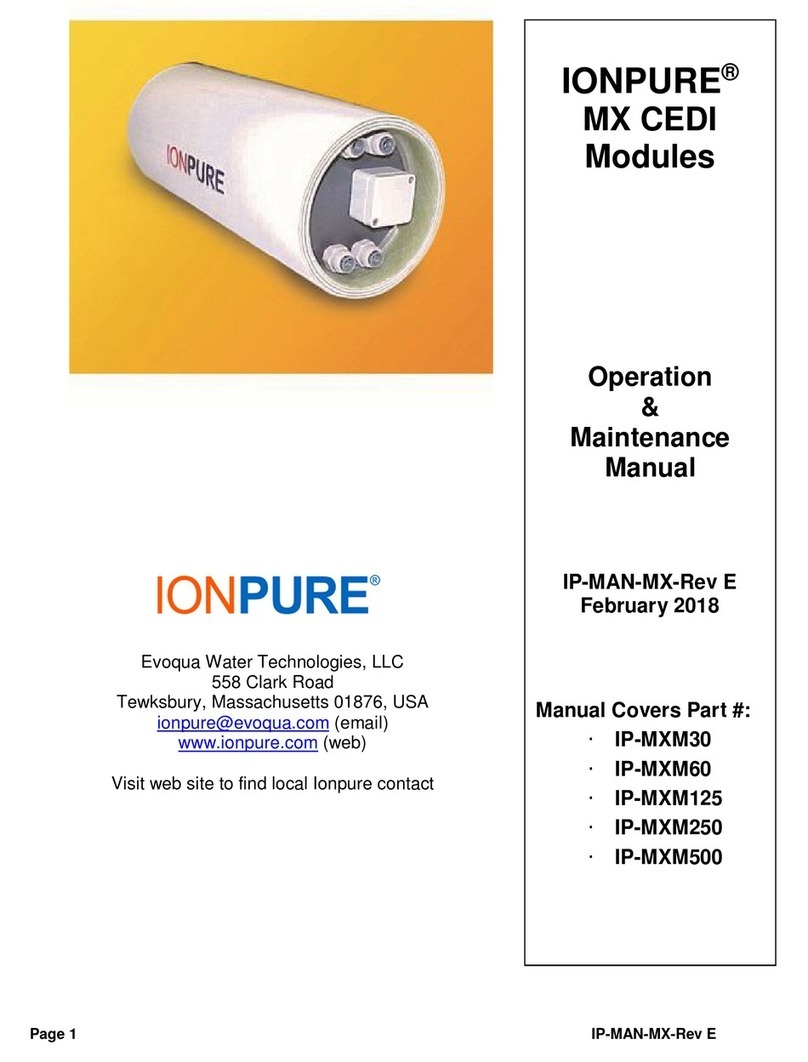
Evoqua
Evoqua IONPURE IP-MXM30 Manual
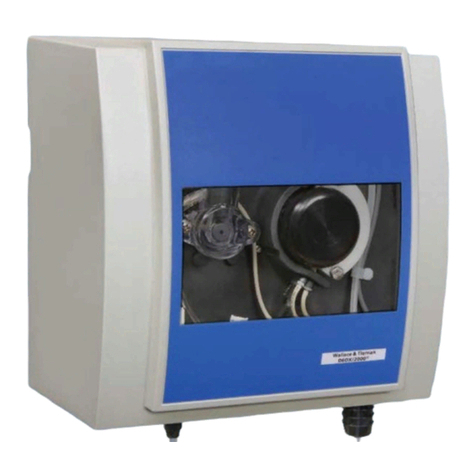
Evoqua
Evoqua WALLACE & TIERNAN MICRO/2000 User manual
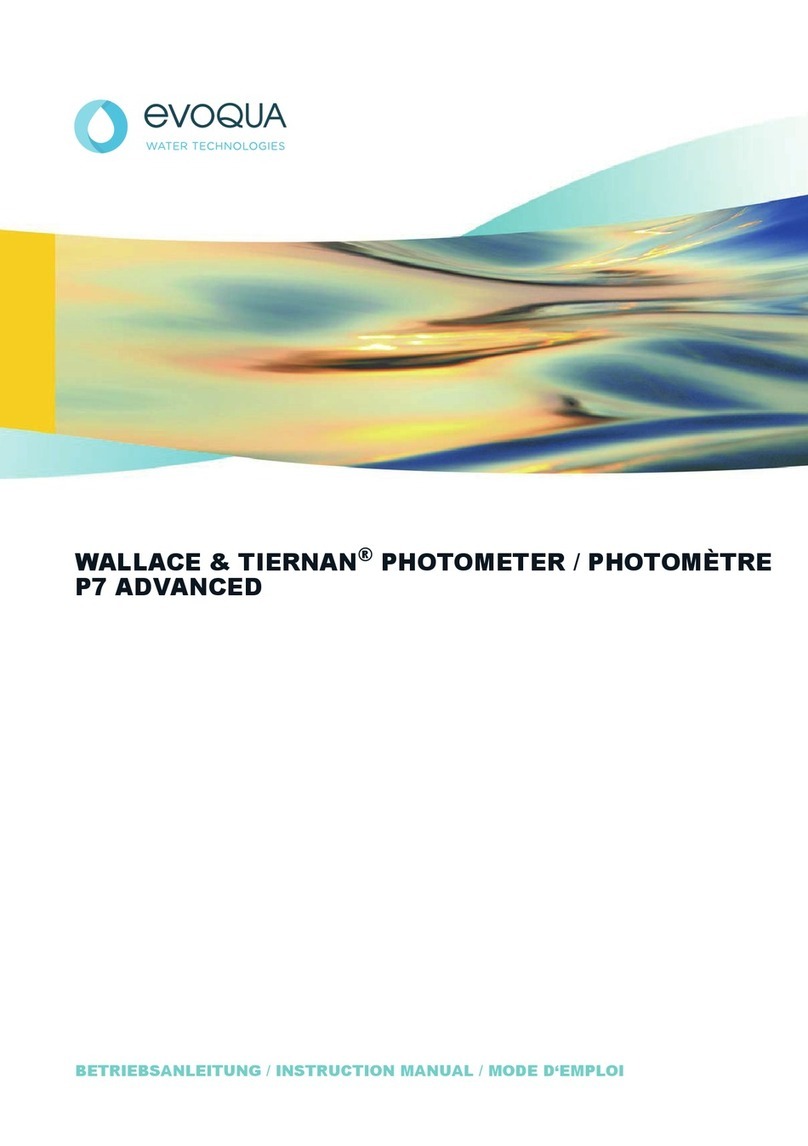
Evoqua
Evoqua WALLACE & TIERNAN P7 ADVANCED User manual

Evoqua
Evoqua WALLACE & TIERNAN DEPOLOX 5 Series User manual