FASTRON. F330 Series Manual

Author – D. Rehe Feb 2020
Fastron - Oztherm Power Controller
F330 Series Calibration Procedure
In this article we discuss the calibration procedure for F330 Series Single Phase
Thyristor (SCR) Controllers.
PCB F311AO(Firing Card)
F311A1 (Option Card)

Author – D. Rehe Feb 2020
Please refer to the F330 installation and commissioning manual for detailed wiring
connection instructions.
Wiring diagrams for various applications;
Standard Thyristor Wiring Diagram
Control Card Wiring Diagram F311A1
New CCE option PCB1019-XX Wiring Diagram
Bridge Output Thyristor Wiring Diagram
Primary Transformer Wiring Diagram
Start Delta Wiring Diagram
Controller Identification
F330 Controllers are fitted with a single PCB marked F321A0 and F311A1. There should
be a silver sticker on the PCB with a serial number in the format of YY-MM-Serial #
Controller Options Identification
There are various options available for this controller which the most common are listed
and indicated by the following nomenclature
(FW) - Four Wire Load (Neutral) Critical for applications with return neutral
currents
(A) - A.C. Voltage Regulation
(C) - Current Limit and Trip
(CC) - Voltage Limit and current Trip. Current Source (A.C. Current Control)
(CCE) - Voltage Limit and current Trip. Current Source (D.C. Current Control)
(CE) - Current Limit and Trip (D.C.)
(F) - High Speed Fuses
(FW) - Four Wire Load
(MI) - Meter Output of Average Current (1mA for moving Coil Ammeter)
(MP) - Meter Output of Average Power (1mA for moving Coil Ammeter)

Author – D. Rehe Feb 2020
(MV) - Meter Output of Average Power (1mA for moving Coil Ammeter)
(PH) - Phase Loss Output
(PLF) - Partial Load Failure
(PW) - Power Limit
(T) - Thermal Overload Protection
For detailed descriptions please refer the F330 installation and commissioning manual.
Various "Specials" (SP) versions exist with customised functions and in many cases very
minor changes to suit specific customer applications. See here for detailed of most SP
versions which have been created to date.
Calibration Procedure
Note: Before beginning please ensure you have at least 200W load connected, can
be incandescent light bulbs, or preferably the heating/welding element you intend to use.
This ensures that you will have enough load to sink the output. Otherwise it will not be
possible to calibrate the controller.
Note: You will need to remove the perspex cover to access the PCB for these
procedures.
Note: Leakage of Thyristor (SCR) Semiconductors
Note there will always be some leakage current from the Thyristor (SCR)
Semiconductors. Generally, in the the low mA range, or for older devices this can
increase as they approach failure, several Amps in the worst cases. What this means
is there will always be a voltage present even when the enable of the controller is not
connected and the controller is effectively turned off. To prevent leakage in off state you
need secondary isolation via contactor or manual isolator to disconnect the circuit fully.
This is particularly important when the user needs to enter or touch the heating chamber
in between usage.
For all F330 controllers except those fitted with
CC,CCE option
1.A Bias(Zero) Adjustment
Set GAIN potentiometer(POT) fully anti-clockwise
Purchase a Current Clamp Meter similar as these Clamp Meters. 300 Amp True RMS
Clamp Meter. Or for additional power quality features you can use this 1000 Amp True
RMS Clamp Power Meter to clamp test the line current for each phase. We recommend
the standard Current Clamp for most applications as it comes with an impedance test
functions which is handy to verify failed SCR's or diodes by measuring Anode to
Cathode and Gate to Cathode for short circuits or low impedance. See our Diode SCR
Testing Blog for the complete test procedure. If you do not have a clamp meter you can
also measure the L1-L2, L2-L3, L3-L1 voltages.
Note: Bias Adjustment can be adjusted from -20% to +20%

Author – D. Rehe Feb 2020
1.B Minimum Control Input
Connect a 4-20mA signal to terminals 0V (0 volt reference) and I (4-20mA signal input).
Input the minimum Control Signal. I.e 0V, 4mA, or 10K POT to 0 position. depending on
the input required. Default is 4mA, for 4-20mA input control.
Clamp the active output wire using the current clamp. Adjust the BIAS POT on the
PCB control card give the minimum output current to the load. You will know when the
controller is at a minimum when the output current will not go down any further.
If you do not have a current clamp available, measure the output voltage to the load and
adjust until you have the minimum voltage across the load.
2.A Gain Adjustment
Connect a 4-20mA signal to terminals 0V (0 volt reference) and I (4-20mA signal input).
Apply the maximum control signal 10V, 5V, 20mA, or 10K POT position.
2.B Maximum Control Input
1. Adjust the GAIN Potentiometer(POT) on the PCB until the maximum current is
output to the load. you will know when you are at maximum when the current will
not increase further. You should now see the expected load current based on the
number of heating/welding elements. If you do not have access to a current
clamp you can monitor the load voltage instead and it will also stop increasing
like the current. In both cases you should wind the GAIN POT back and forth a
little unit you are confident you are right on the maximum output, no more, no
less.
2. Verify the Bias (Zero) again by changing the input signal back to the minimum
value. You will likely find the Bias has moved slightly, re-adjust as necessary as
in step 1.B.
3. Verify the GAIN adjustment by inputting the maximum control input and following
step 2.B again.
Repeat these two steps for a third time to ensure adequate calibration/tuning.
3. Ramp/Soft Start Adjustment
The RAMP potentiometer(POT) sets the step response of the controller for any change
in the control input signal. Setting Range in the standard controller is between 1 and 20
seconds. Special versions are available which allow faster turn on for special
applications such as spot welding. Check here for list of recorded SP versions made
over the last 30+ years. See here for a list of available SP versions.
To check the response time, input a step change to the control input and measure the
time taken to reach the desired output.
4.A Current Limit
Note: The Output of the controller will not be sinusoidal when the output is limited. We
recommend to only use a True RMS Current Clamp for this procedure

Author – D. Rehe Feb 2020
1. Set the LIM potentiometer(POT) fully clockwise along with the Trip POT.
2. Set the FBG POT to approximately half way.
3. Connect a current clamp meter to the load.
4. With the control input set to maximum, gradually turn the LIM Potentiometer
clockwise until the required current limit value is reached. The LIM LED will be lit
while current limit is active.
4.B Unstable Output
If the output is oscillating while current limit is active, you need to turn the FBG POT fully
clockwise, and then gradually turn anticlockwise until the output is stable.
5. Power Limit (PW Option)
1. Set the LIM potentiometer(POT) fully clockwise along with the Trip POT.
2. Set the FBG POT to approximately half way.
3. Connect a current clamp meter to the load. If a voltage connection is available
connect the voltage terminals to the load.
4. With the control input set to maximum, gradually turn the LIM Potentiometer
clockwise until the required power limit value is reached. The LIM LED will be lit
while power limit is active.
Note: The PW option (Power limit) takes the voltage into account when limiting the
output, however with only the C option (Current Limit) it only limits by current. Th reason
is due to some applications with small elements or sensitive applications, where there is
no temperature feedback loop, as in furnaces for example, as the mains voltage
fluctuates, from +10% to -15%, the output power fluctuates. With PW option is measures
the voltage and adjusts the input demand signal as necessary.
5.B Unstable Output
If the output is oscillating while current limit is active, you need to turn the FBG POT fully
clockwise, and then gradually turn anticlockwise until the output is stable.
6. Current Trip
1. Turn the trip POT fully clockwise.
2. With the control input set to maximum, gradually turn the TRIP Potentiometer
anti-clockwise until the required current limit value is reached. The Trip LED is lit,
and the output of the controller turns off, while the enable LED also turns off. You
are now at the maximum output of the controller.
3. Turn the TRIP POT clockwise one or two turns clockwise.
Nuisance Trip
If you are experiencing nuisance trip, turn the TRIP a further half to one turn clockwise.
Trip Relay Output

Author – D. Rehe Feb 2020
On current trip and the controller is disabled and the trip relay energises and latches.
Current Trip can be rest by opening the ENABLE link or by turning off the mains supply
For F330 controllers fitted with CC,CCE option
7.A Bias(Zero) Adjustment
1. Set GAIN & AUX-V potentiometer(POT) fully anti-clockwise
2. Purchase a Current Clamp Meter similar as these Clamp Meters. 300 Amp True
RMS Clamp Meter. Or for additional power quality features you can use this 1000
Amp True RMS Clamp Power Meter. We reccommend the standard Current
Clamp for most applications as it comes with a impedance test functions which is
handy to verify failed SCR's or diodes by measuring Anode to Cathode and Gate
to Cathode for short circuits or low impedance. See our Diode SCR Testing Blog
for the complete test procedure.
Note: Bias Adjustment can be adjusted from -20% to +20%
7.B Minimum Control Input
1. Input the minimum Control Signal. I.e 0V, 4mA, or 10K POT to 0 position.
depending on the input required. Default is 4mA, for 4-20mA input control.
2. Clamp the DC output wire using the current clamp.
3. Set the BIAS POT to the centre position.
4. Input the minimum control input signal.
5. Gradually turn the AUX-V potentiometer clockwise until the output current is
around 5 Amp then adjust the Bias POT until you get zero current through the
load.
8.A Gain Adjustment
Apply the maximum control signal 10V, 5V, 20mA, or 10K POT position.
8.B Maximum Control Input
1. Turn the GAIN Potentiometer(POT) fully clockwise.
2. Gradually turn the AUX-V potentiometer clockwise until about 5 Amp more than
the maximum desired output current is measured. Be careful not to adjust to
higher over the maximum load or you may cause permanent damage to the SCR
due to overheating.
3. Adjust the GAIN POT until the output current is at the maximum desired level.
4. Recheck the output current at maximum and minimum control input and re-adjust
the Bia and Gain as necessary.
5. AUX-V POT controls the output voltage and can be left as a maximum limit or
adjusted as required taking care not to output overvoltage to the load.
9. Ramp/Soft Start Adjustment
The RAMP potentiometer(POT) sets the step response of the controller for any change
in the control input signal. Setting Range in the standard controller is between 1 and 20

Author – D. Rehe Feb 2020
seconds. Special versions are available which allow faster turn on for special
applications such as spot welding. Check here for list of recorded SP versions made
over the last 30+ years. See here for a list of available SP versions.
To check the response time, input a step change to the control input and measure the
time taken to reach the desired output.
10. MI, MV, MP
The standard controller configuration outputs 0-1mA and calibration is performed on the
meter side while the output is at maximum and measured using a current, voltage, or
power meter
This manual suits for next models
1
Table of contents
Other FASTRON. Controllers manuals
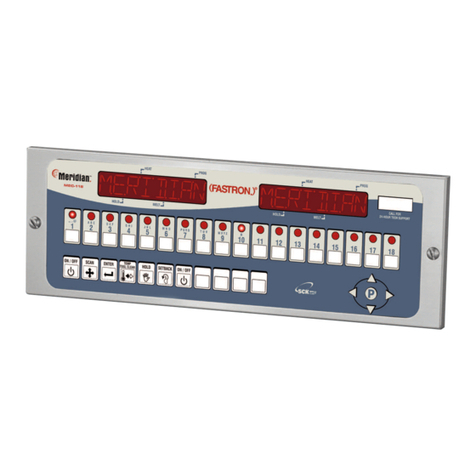
FASTRON.
FASTRON. MERIDIAN Series User manual
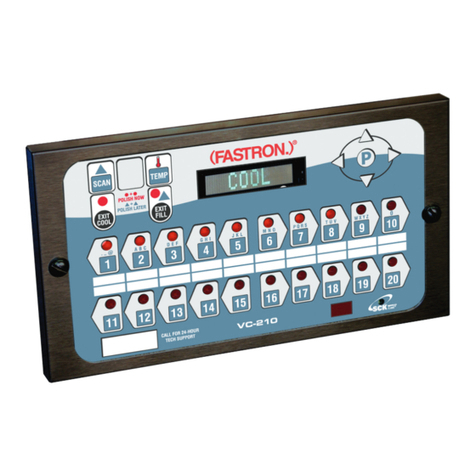
FASTRON.
FASTRON. VC-210 User manual
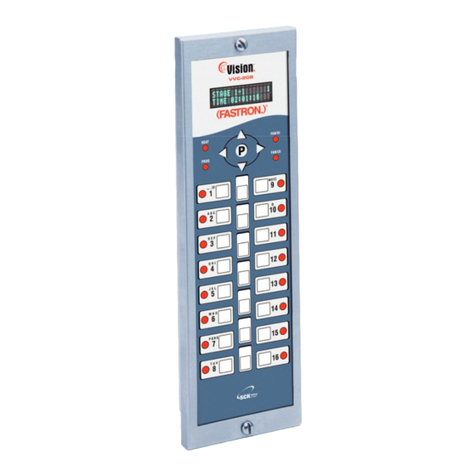
FASTRON.
FASTRON. VISION Series Operating instructions
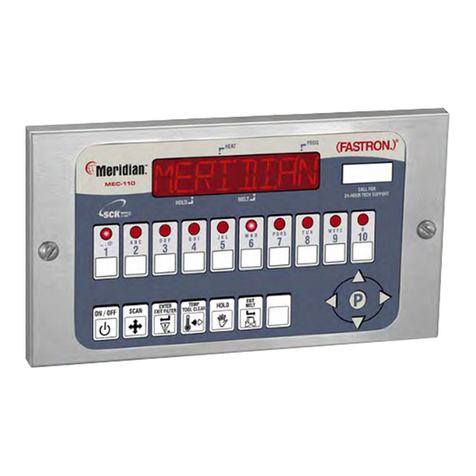
FASTRON.
FASTRON. Meridian MEC-110 User manual
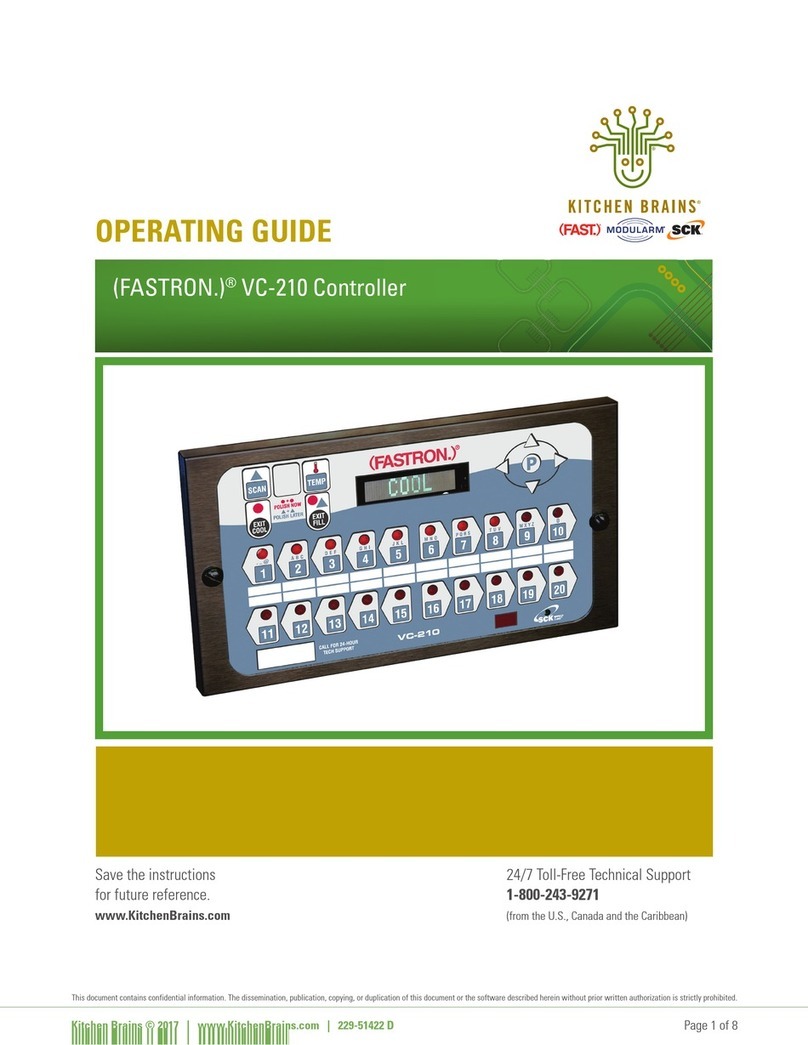
FASTRON.
FASTRON. VC-210 User manual
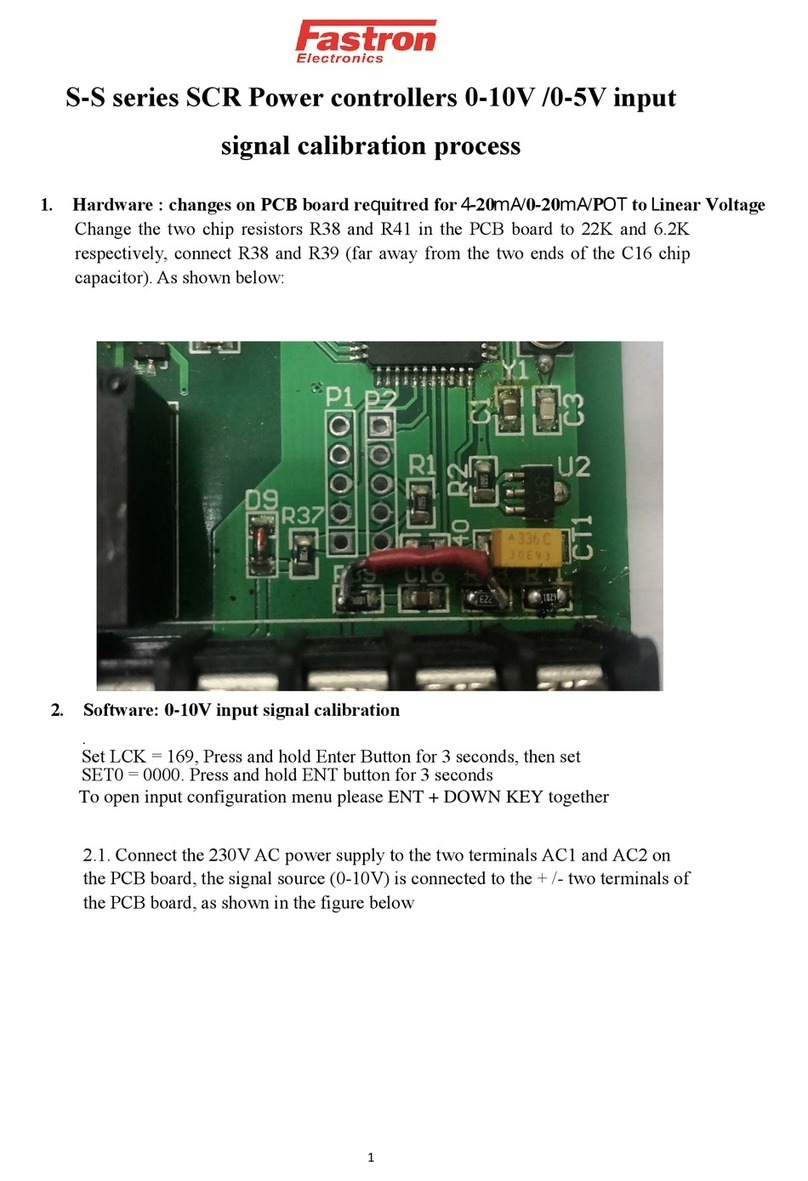
FASTRON.
FASTRON. S-S Series Use and care manual
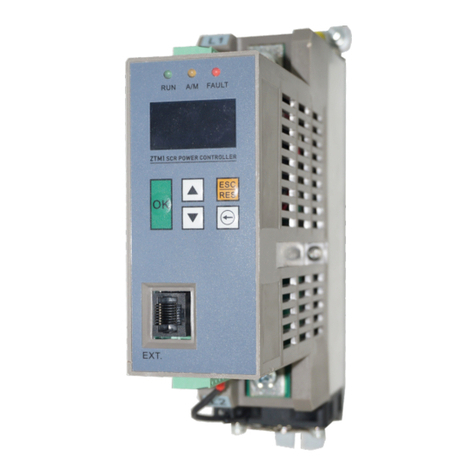
FASTRON.
FASTRON. FTM1 Series User manual
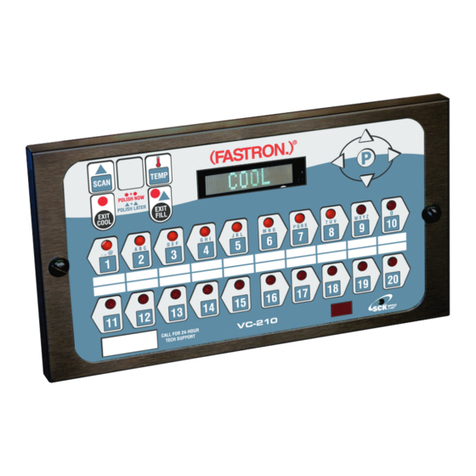
FASTRON.
FASTRON. VC-210 User manual
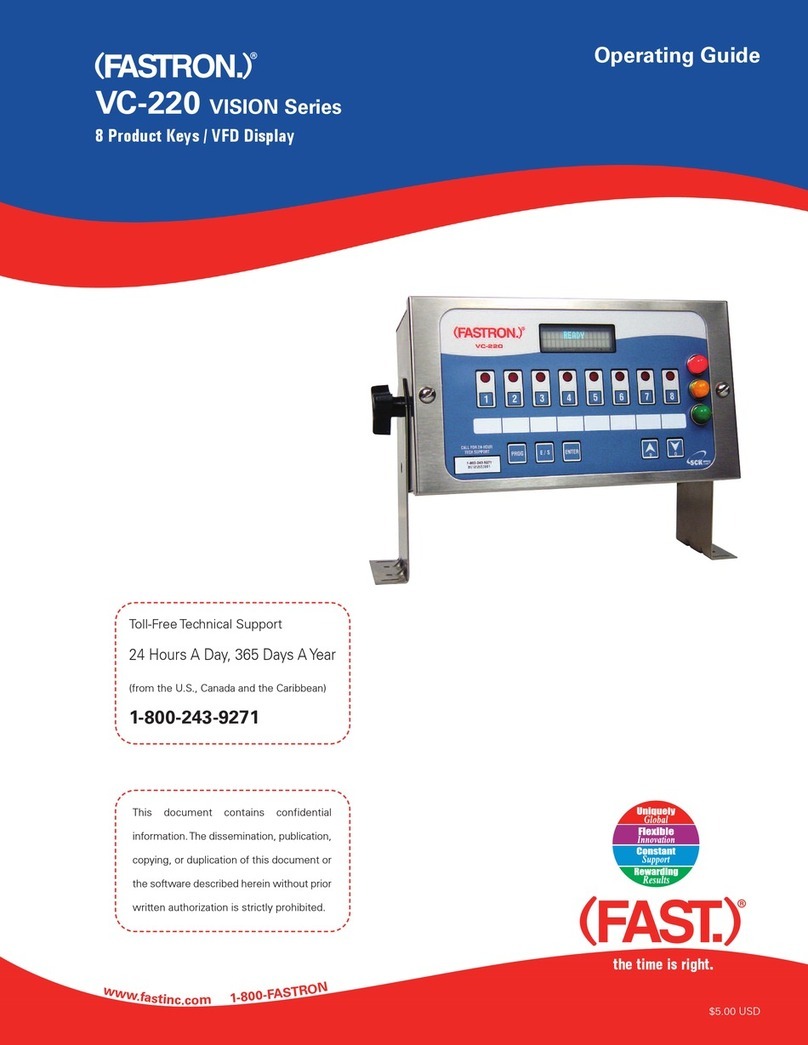
FASTRON.
FASTRON. VISION VC-220 User manual
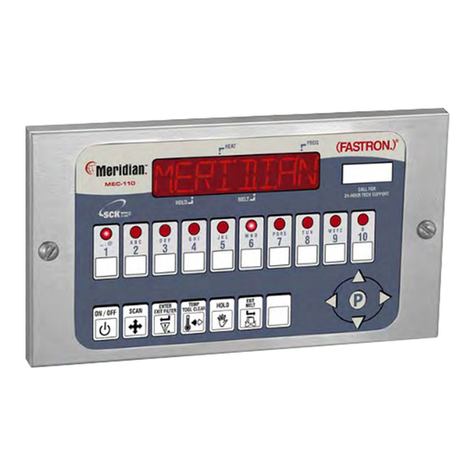
FASTRON.
FASTRON. Meridian MEC-110 User manual