FG Modellsport 66000 User guide

Mounting instruction for
Competition 4WD Off-Road 1:6 Baja Buggy
Item No 66000, 66001
E.66000-66001-271008
Please thoroughly keep this construction instruction for spare parts’ orders!
FG Modellsport-Vertriebs-GmbH
Spanningerstr. 2
73650 Winterbach-Germany
Phone: +49 7181 9677-0
Fax: +49 7181 9677-20
www.fg-modellsport.de
Weight of the individual bags/boxes:
Item No 66000, 66001
Bag A = 1 part
Bag B = 0.771 kg
Bag C = 0.931 kg
Bag D = 1.085 kg,
Bag E = 0.407 kg
Bag F = 0.900 kg
Bag G = 0.191 kg
Bag H = 0.383 kg
Bag I1 = 0.490 kg, only for 66000
Bag I2 = 0.499 kg, only for 66001
Bag J = 0.117 kg
Bag K = 0.343 kg
Bag L = 0.343 kg
Bag M = 0.285 kg
Bag N1 = 0.027 kg, only for 66000
Bag N2 = 0.038 kg, only for 66001
Bag O = 0.299 kg
Bag P = 0.239 kg
Bag Q = 0.604 kg
Bag R = 0.397 kg
The RCS accumulators and battery charger are not included in the
delivery volume.
We congratulate you on buying this FG Competition model. Please check the contents of
the construction set, respectively of the bags. The individual bags had been thoroughly
packed by us and their weight and content had been checked. When purchasing the indivi-
dual bags, please check their weight and their closure by staples which must not have
been removed or opened and closed several times. It is possible that the weight of an indi-
vidual bag deviates by 5 grams. In case of claims due to missing parts, you always need to
present the label indicating the weight at your specialized dealer. By checking the weight of
the bag, you may exclude that larger parts or several parts are missing.
Are you interested in receiving 4WD news?
For example information about meetings,
races, technical hints. Just send us an email
with your name and email address to
the 4WD news automatically when available.

Comments regarding the construction manual:
Before starting the assembly please see through this construction
manual. This way you will get an overview of the whole execution.
Please check by means of the parts or bag list if the construction kit is
complete and also check the weight of the individual bags for the posi-
tions. Only this way you may be sure that all parts which you need for
the assembly are available. If a part is missing, please immediately con-
tact your specialized dealer.
Contents
Position 1-2: Front and rear differential gear
Position 3-8: Belt drive, belt stretcher, chassis structure
Position 9-15: Rear axle
Position 16-17: Front and rear shock absorber
Position 19-25: Front axle, front bumper
Position 26-32: Engine, clutch, gear , air filter, tank
Position 33-40: RC-plate, receiver box, servo saver
Position 41-45: Roll cage, throttle rods, tuning pipe
Position 46-52: Front and rear tuning disk brake
Position 53-59: Front and rear FG Magura hydr. brake system
Position 60-61: Side guards, front roll cage
The handling with fuels requires circumspective and careful hand-
ling. Imperatively observe the security advices.
-Refuel only if the engine is switched off!
-Take off the body.
-Thoroughly clean the area around the fuels nipple.
-Remove the fuel filler cap and carefully fill in the fuel mixture.
-Smoking or any kind of open fire is not admitted.
-Fuels might contain solvent-like substances. Avoid contact with skin
and eyes. Wear gloves for refueling. Do not inhale fuel vapors.
-Do not spill any fuel. If you have spilled fuel immediately clean the
engine and the model.
-Make sure that no fuel will get into the soils (environmental protection).
Use an appropriate mat.
-Do not refuel in enclosed rooms. Fuel vapors accumulate at the soil
(risk of explosion).
-Transport and store fuels only in admitted and labeled canisters. Keep
fuel out of the range of children.
-The operator is responsible for any damages caused to third persons
in the operating range of the model, respectively of the engine, if they
are injured or in case of property damage.
-The model must only be passed on to persons who are familiar with
this model and its operation, always provide the operating manual.
-Persons with implanted heart pacemakers must not work on running
engines and on live parts of the ignition system when the engine is
being started.
-The engine must neither be started nor operated in enclosed rooms
(without sufficient ventilation).
-When starting the engine, avoid inhaling the exhausts.
-The model must neither be started nor operated without air filter or
without exhaust system.
-Before every start perform a functional check of the safety-relevant
parts.
-The throttle rods must always return automatically to the idle position.
-Any cleaning, maintenance and repair works must only be performed
with the engine being switched off. The engine and silencers are get-
ting very hot. In particular do not touch the silencer.
Our mentioned setting dimensions of steering linkage, wishbone thread
rods aso. are just guiding values which should be modified according
to the track conditions and surfaces.
Chassis adjustments and technical advices
Competition 4WD Off-Road 1:6 Baja Buggy
Our recommended chassis adjustments give you a basic setup. As the
surfaces in the Off-Road sector can be very different certain readjust-
ments may be necessary. This depends on outdoor temperature, on
the roadbed and how strong the track is frequented.
Wheel camber:
Trailing effect:
Toe-in:
Damper springs:
Spring camber:
Damper position:
Damper piston:
Damper oil:
Stabilizer:
Driving height/ Chassis height:
Servo saver:
0° at chassis 90° rebounded
4-6mm clips
slightly open to the front
violet Item N°. 66305
5mm
Wishbone medium boring
5-hole aluminium ø1,9mm Item N°. 06484/05
2000-3000 FG damper oil
Sway bar 4mm
40mm with Baja wheels
Medium hole, outer hole position
0° at chassis 90° rebounded
3°
red Item N°. 66303
10mm
Lower wishbone outer boring
Rear alloy dampler plate outer boring
5-hole aluminium ø1,9mm Item N°. 06484/05
2000-3000 FG damper oil
Sway bar 5mm
45mm Baja wheels
Front axle Rear axle

1. Insert the diff. gearwheels in the diff. housing as described in posi-
tion 1. When using the FG mounting tool item No 08505, the inserting
of the bevel gearwheels will be eased considerably.
2. Lubricate the ball diff. driving axles slightly with grease and push it
in the diff. housing.
3. Mount the diff. bevel gear axle. If the bevel gear axle respectively the
driving axles can only be pushed in severely or if it cannot be pushed
in at any position, you have to dismantle the bevel gearwheels again.
Then insert it again.
4. If the gearwheels have too much clearance, correct it using the
enclosed shim rings. Please make sure that the gearwheel clearance
had not been set too close.
5. Lubricate the gearwheels slightly with multipurpose grease, e.g. item No
06501
6. Put the parts on the alloy diff. housing as described in position 1
and in the given sequence: O-ring large, O-ring small, steel gearwheel
48teeth., rear plastic gear disk 42 teeth, right alloy stop disk. Fasten
the complete unit using the M4x40 countersunk screws
(use the screw retention high-strength).
1. Mount the differential gear for the front axle as described in position
1 under the item 1-5.
2. Then put the parts on the alloy diff. housing as described in position
2 and in the given sequence: O-ring large, O-ring small, front plastic
stop disk left, plastic toothed belt wheel 42 teeth, right plastic stop
disk. Fasten the complete unit using the M4x40 countersunk screws
and the stop nuts M4.
3. Push the bearing shafts 6x50mm centrally in the deflection roller
16mm and in the 12-teeth toothed belt wheel.
Toothed belt
wheel
12 teeth
Bearing
shaft
6x50
Bearing shaft
6x50
Deflection roller
16mm
Front
plastic stop
disk left
Front plastic
toothed belt wheel
42 teeth
Front drive
Right plastic
stop disk
Position 1
Parts are in
bag B
Position 2
Parts are in
bag C
Differential rear
Rear drive
Ball diff.
driving axle
Ball bearing
15x28x7
Screw
M4x40
Needle
bearing f.
Diff
Bronze
bush
Alloy
differential
housing
Diff. bevel
gear axle
O-rings
Shim ring
5x17x0.1
Shim ring
8x20x0.1
Diff. gearwheel B
Diff. gearwheel A
Steel gearwheel
48 teeth
Rear plastic gear disk
42 teeth
Alloy stop disk
right
Chamfer
inbound
Ball diff.
driving axle
Ball bearing
15x28x7
Screw
M4x40
Alloy
differential
housing
Steel gearwheel
48 teeth
Rear plastic
gear disk
42 teeth
Alloy stop disk
right
Stop nut M4
Inserting of the diff.
bevel gearwheels or
of the complete
package is much
easier if you use the
FG mounting tool
8505.
Screw
M4x40
All metric screws need to be secured with thread lock fluid.

Toothed belt wheel
12 teeth
Left
front axle
housing
Left alloy
front axle
housing
Right alloy
front axle
housing
Ball bearing
6x16x6
Toothed belt
Toothed belt
Toothed belt
Alloy chassis
Alloy chassis
Deflection roller
16mm
Rear
differential
gear
Alloy rear axle mount
left
Alloy rear axle
mount left
Upper part
belt channel
Lower part
belt channel
Front differential
mounted
Front
differential gear
Screw
M4x14
Screw
M4x14
Position 3
Parts are in
bag C
Position 4
Parts are in
the bags A,C
Position 5
Parts are in
bag B
1. Push the front differential gear, deflection roller 16mm, toothed belt
wheel 12 teeth in the left alloy front axle housing as described in
position 3.
2. Put the toothed belt on the front differential gear, deflection roller
16mm and the toothed belt wheel with 12 teeth as described in posi-
tion 3.
3. Press the right alloy front axle housing on the front differential gear,
deflection roller 16mm and the toothed belt wheel with 12 teeth
(position 4).
4. Put the complete alloy front axle housing on the alloy chassis and
fasten it using the M4x14 countersunk screws.
1. Put the toothed belt on the rear differential gear as described in
position 5.
2. Press the left and right rear axle mounts on the ball bearings of the
rear differential gear as described in position 5.
3. Put the left and right alloy rear axle mounts on the alloy chassis and
mount it using the M4x14 countersunk screws.
Alloy chassis
Upper part
belt channel
Lower part
belt channel
Screw
M4x14
Screw
4.2x16
Position 6
Parts are in
bag C
Toothed belt
Left alloy
front rear
axle
housing
Right alloy
front rear
axle
housing
1. Put the lower part of the belt channel on the lower part of the too-
thed belt as described in position 6. Then push the upper part of the
belt channel in the lower part of the belt channel. Then insert the com-
plete belt channel in the opening of the alloy front axle housing. Make
sure that the toothed belt is running smoothly.
2. Mount the belt channel to the alloy chassis using the 4.2x16
countersunk screws.

Screw
M4x14
Disk
Ø4.3
Left stretching pulley
housing
Toothed belt
wheel 42 teeth
Toothed belt wheel
40 teeth
Right stretching
pulley housing
Collar
Plastic bearing
seat
Ball bearing
10x19x7
Bearing shaft f.
housing for
stretching pulley
Position 7
Parts are in
bag B
Alloy chassis
Screw
M4x14
Stretching
pulley
housing
Belt channel
mounted
Position 8
Parts are in
bag B
1. Push the bearing shaft for the stretching pulley housing centrically in
the 3 ball bearings 10x19x7.
2. Push the plastic bearing seat with inbound collar in the left and right
stretching pulley housing as described in position 7.
3. Push the bearing shaft which is equipped with ball bearings in the left
and right stretching pulley housings which are equipped with plastic
bearings seats and mount it using M4x14 pan-head screws and disks
Ø4.3.
4. Put the complete stretching pulley housing on the belt and belt
channel as described in position 8 and mount it on the alloy chassis
using the M4x14 countersunk screws. For this purpose, slightly move
the belt.
5. When the assembly is performed, turn the belt in running
direction. The belt has to rotate easily.
Hint: The position of the front bearing seat is made for the front plastic
toothed belt wheel with 42 teeth. The position of the rear bearing seat
is made for the rear plastic toothed belt wheel with 40 teeth.
All metric screws need to be secured with thread lock fluid.

Screw
M5x25
Taper disk
4x Screw Ø5.3 and 1x
screw M5x30
Taper disk
Stop nut M5
Push in guide
bushes
Position 10
Parts are in
bag D 1. Push the rear axle cover between the alloy rear axle mounts and
mount it using an alloy connection brace, a M4x20 pan-head screw
and a disk Ø4.3.
2. Push the guide bushes with collar in the rear lower alloy wishbones
from inside and outside.
3. Mount the M4x25 cylinder screws with stop nuts M4 and disks Ø4.3 in
the rear lower alloy wishbones.
4. Screw the hexagon nuts with M8 left-handed thread on the adjusting
screws 32mm and screw it in the rear lower alloy wishbones, then screw
the hexagon nuts with M8 right-handed thread and alloy ball bearings on
the adjusting screws 32mm.
5. Mount the plastic brace for the stabilizer to the rear lower alloy
wishbone using M3x16 pan-head screws, then push the stabilizer 5mm
in the plastic brace for the stabilizer.
6. Mount the pre-assembled rear lower alloy wishbones to the front
alloy ball-and-socket joints with M5x30 countersunk screws, 4 disks
Ø5.3 and one taper disk each between the alloy ball-and-socket joints
and mount
it to the alloy chassis using M5 stop nuts. Then mount the rear alloy
ball-and-socket joints with M5x25 countersunk screws and one taper disk
each between the alloy ball-and-socket joints and mount it to the alloy
chassis using M5 stop nuts. The mounted wishbones should move easily
up and down.
Hint: Mount taper disks always with the thinner side towards the alloy
ball-and-socket joint.
Alloy chassis
Screw
M4x20
Disk Ø4.3
Screw
M5x25
Screw
M5x30
Screw
M3x16
Screw
M4x25
Stop nut
M4
Disk Ø4.3
Disk Ø5.3
Rear lower alloy
wishbone
Alloy
connection
brace
Stabilizer
5mm
Rear axle
cover
Taper disk
Taper disk
Plastic brace for
stabilizer
Alloy ball-
and- socket
joint
Hexagon nut M8
left-handed thread
Hexagon nut M8
right-handed thread
Adjusting screw
r/l 32mm
Stop nut
M5
Guide bush
with collar
Position 9
Parts are in
bag D
All metric screws need to be secured with thread lock fluid.
ca. 15,5mm
ca. 13-14mm

Square
wheel driver
14mm
Balls for driving shaft
Adjusting clips
Retaining
washer
Wishbone pin
Ball driving
axle
Ball driving
shaft
Protection
bellow
Distance
disk
Hexagon
nut
Headless
pin M6x6
Thread
pin M3x3
Alloy
upright
left
Disk Ø4.3
Screw
M4x8
Screw
M4x8
Use screw retention
high-strength
Screw
M4x20
Screw
M4x20
Guide bush
with collar
Guide bush
with collar
Guide bush
decentered
Guide bush
decentered,
boring
towards bot-
tom
Rear alloy
shock mount
Alloy rear axle
mount right
Rear lower alloy
wishbone
Bearing
8x22x7
1. Mount the rear alloy shock mount to the left and right alloy rear axle
mount using the M4x20 pan-head screws.
2. Push the stabilizer in the rear alloy shock mount and fasten it using
M4x8 pan-head screws and disks Ø4.3.
3. Push the guide bushes with collar from the interior side into the left
and right alloy rear axle mounts. Push the decentered guide bushes with
boring showing to the bottom from the interior side in the rear alloy shock
mount.
4. Mount the ball driving set as described in position 12.
5. Push the ball driving axles in the alloy uprights which are equipped
with ball bearings and mount the square wheel driver 14mm with
recess towards the ball bearing to the surfaces of the ball driving axles
using M6x6 headless pins (use a high-strength screw retention).
6. Push the alloy uprights and headless pins in the rear lower alloy
wishbones as described in position 13. Secure the headless pins using
Ø5 retaining washers.
7. Put two adjusting clips each on the headless pins between the front
alloy uprights and between the rear lower alloy wishbones. Secure the
alloy uprights using M3x3 headless pins. Check if the alloy uprights are
running smoothly.
Position 11
Parts are in
bag D
Position 13
Parts are in
bag D
Apply
lubricating
grease
Slightly lubricate the
ball driving shaft
Protection bellow
Ball diff. axle
Ball driving
axle
Distance disks Balls for
driving shaft
Mounting of the ball driving shafts.
Stick the distance disks in the round relief of the ball drive axle as well
as in the ball diff. axle using some multipurpose grease. Mount the
protection bellows to the ball driving shafts according to the illustra-
tion. When putting on the protection bellow, slightly grease the ball
area. Apply some lubricating grease on the ball holes and push in the
balls. The balls will be held by the lubricating grease and this way the
driving shaft can be mounted more easily. Then push the complete ball
driving shaft in the differential axle and the driving axle. Put the protec-
tion bellows on the ball diff. axles and the driving axles.
Position 12
Parts are in bag B

1. Push the guide bushes with collar in the rear
upper alloy wishbones.
2. Screw the hexagon nuts with M10 left-handed thread
on the rear wishbone thread rods M10/M8 and screw it
in the rear upper alloy wishbones, then screw the hexa-
gon nuts with M8 right-handed thread and alloy
ball-and-socket joints on the rear wishbone thread rods
M10/M8. Use medium screw retention.
3. Push the wishbone pins throughout the alloy rear
axle mounts, rear alloy shock mount and the pre-
assembled rear upper alloy wishbones according to
the illustration. Secure the wishbone pins using Ø5
retaining washers.
4. Push two adjusting clips each in the wishbone
pins at the front between the alloy rear axle mounts
and the rear upper alloy wishbones and push one
adjusting clip each in the wishbone pins at the rear
between the rear alloy shock mount the rear upper
alloy wishbones.
5. Mount the alloy ball-and-socket joints between the
alloy uprights and alloy ball-and-socket joints to the
alloy uprights using M5x30 countersunk screws and
taper disks. Position 15.
6. Screw M5 nuts on M5x25 headless pins and
screw it from the top in the rear upper alloy wishbo-
nes (Rebound stop travel).
Hint: The upper wishbone needs to be shimmed
according to the adjustment of the toe-in using the
adjusting clips. Always mount taper disks with the
thinner side towards the alloy ball-and-socket joint.
Adjusting clips
Adjusting clips
The upper wishbone needs to be shimmed
according to the adjustment of the toe-in
using the adjusting clips.
Retaining
washer Ø5
Wishbone pin
Headless pin
M5x25
Left alloy
uprights
Guide bush
with collar
Rear alloy
shock mount
Hexagon nut M8
right-handed thread
Hexagon nut M10
left-handed thread
Rear wishbone
thread rod
M10/M8
Rear upper
alloy wish-
bone
Alloy ball and sok-
ket joint
Taper disk
Taper disk
Nut
M5
M10
M8
Screw
M5x30
Screw
M5x30
Rebound stop
travel
Position 15
Parts are in
bag D
Position 14
Parts are in
bag D
All metric screws need to be secured with thread lock fluid.
Make sure the driving shaft has not moe than 2-3mm clearance in
horizontal position. Mount enclosed disks Ø8,5/18x1,5 between
rear respectively diff.axle and ball bearing.
ca. 52mm

Screw
M4x20
Screw
M5x25
Nut
M5
Rear shock
absorber
mounted
Stop
nut
M5
Internal
silicone
tube Ø5
Shock absorber locking
Internal silicone
tube Ø4
Disk Ø3.2
Stop
nut M3
O-ring
O-ring
O-ring
Damper spring
red at the rear
violet at the front
Alloy
shock absor-
ber
piston
Spring plate
Shock retaining
short
Threaded
piston rod long
Silicone
O-rings
Alloy
shock absorber
housing
Adjustable
ring
Sheet
gasket
Volume
compensation
Position 17
Parts are in
bag E
Position 18
Parts are in
bag E
Position 16
Parts are in
bag E
1. Insert 2 red silicone O-rings each in the alloy shock absorber hou-
sing as described in position 17.
2. Insert the black O-rings in adjustable rings and screw the adjustable
rings on the alloy shock absorber housing.
3. Mount the O-rings with the smaller groove towards the threaded
piston rod to the alloy shock absorber pistons using a disk Ø3.2 and a
stop nut M3.
4. Carefully insert the threaded piston rods throughout the alloy shock
absorber housings, without damaging the silicone O-rings. Screw the
short shock retaining in the thread of the threaded piston rod until
there is no thread visible anymore.
5. Mount the O-rings to the sheet gaskets and push it in the alloy
shock absorber housing.
6. Fill the alloy shock absorber housing with oil up to about 3mm
below the sheet gasket. Carefully slide the threaded piston rod several
times in and out of the alloy shock absorber housing, so that the air
bubbles in the oil will come up. If no longer air bubbles are coming up,
push the threaded piston rod slowly in the alloy shock absorber hou-
sing until there is only visible about 5mm of the piston rod. Then insert
the volume compensation with cambering towards the oil and screw it
down with the shock absorber locking. If too much oil is filled in it
might leak through the thread.
7. Mount the red damper springs for the rear axle to the shock
absorbers with the larger boring in the shock absorber locking and
secure it using spring plates. Proceed in the same way for the front
shock absorbers with the smaller borings in the shock absorber lok-
king and the violet damper springs.
8.Mount the rear lower mounted shock absorbers to the rear lower
alloy wishbones using M4x20 cylinder screws. Screw M5x25 pan-head
screws in the rear alloy shock mount and counter it using M5 nuts,
then mount the upper shock absorber with internal silicone tube Ø5
and M5 stop nuts.
Hint: Slightly lubricate the silicone O-rings and the threaded piston
rods when mounting. If the FG mounting tool item No 06853 is used,
the mounting of the shock absorbers will be eased considerably.
Rear alloy
damper plate

Screw
M4x12
Screw
M4x12
Screw
4.2x22
Alloy
steering lever
Plastic
steering stop
Front left alloy
upright
Front right alloy
upright
Screw
M4x14
Screw
M4x14
Screw
M3x6
Plastic brace for
stabilizer
Nut
M5
Nut
M5
Headless
pin
M5x20
Headless
pin
M5x20
Headless pin M5x20 to
adjust the rebound stop tra-
vel of the front axle
Alloy front
axle
housing
Front stabilizer
4mm
Front lower
wishbone pin
Rebound
stop travel
Guide for
stabilizer
Guide for
stabilizer
Ball-
type
nipple
Front lower
alloy wishbone
Guide bush
with collar
Ball bearing
15x28x7
Ball bearing
17x26x7
Position 19
Parts are in
bag F
Position 20
Parts are in
bag F
Position 19
Parts are in
bag F
1. Secure the pressed in ball-type nipples in the front lower alloy
wishbones using M3x6 lenticular flange head screws.
2. Push the guide bushes with collar in the front lower alloy wishbones.
3. Mount the plastic brace for the stabilizer to the front lower alloy
wishbones using M4x12 cylinder screws, then push the front stabilizer
4mm in the plastic brace for the stabilizer.
4. Insert the front lower alloy wishbones in the alloy front axle housings
as described in position 19 and push the front lower wishbone pins
with tapped hole towards the front in the alloy front axle housings and
push it in throughout the pre-assembled front lower alloy wishbones.
The alloy wishbones have to move up and down easily.
5. Mount the front stabilizer 4mm to the alloy front axle housings using
the guides for the stabilizer and M4x14 cylinder screws.
6. Screw a M5 nut on a M5x20 headless pin and screw it from the
bottom in the front lower alloy wishbones.
Hint: In order to pull out the front lower wishbone pins, screw a M4
screw from the bottom in the threaded hole.
1. Mount the alloy steering lever to the front left and
right alloy uprights using M4x12 cylinder screws
according to the illustration.
2. Mount the plastic steering stop to the alloy stee-
ring levers using 4.2x22 pan-head screws.
Hint: The front left and right alloy uprights are similar.
They have to be mounted in a different way, due to
the position of the alloy steering levers and the pla-
stic steering stops.

Front lower
alloy wishbone
Retaining
washer Ø5
Distance
disk
Ball
diff.
axle
Adjusting
clips
Adjusting
clips
Guide bush
with collar
Headless
pin
M5x25
Headless
pin
M6x6
Front upper
alloy wishbone
Wishbone
thread rod
front M10/M8
Nut
M5
Front upper
wishbone pin
Protection
bellow
Disk
Ø5.3
Disk
Ø5.3
Disk
Ø8.4
Screw
M5x25
Screw
M5x25
Screw
M5x25
Screw
M5x25
Hexagon nut M8
right-handed thread
Hexagon nut M10
left-handed thread.
Alloy ball-
and-socket
joint
Balls for
the
driving
shaft
Wheel nut
Taper
disk
Taper disk
2x disk Ø5.3
Disk Ø5.3
2x taper disk
Taper
disk
Square wheel
driver
14mm
Universal joint
driving shaft
Front left alloy
upright
mounted
Position 22
Parts are in
bag F
Position 23
Parts are in
bag F
1. Push the guide bushes in the front upper alloy
wishbones.
2. Screw the hexagon nuts M10 with left-handed
thread on the front wishbone thread rods M10/M8
and screw it in the front upper alloy wishbones, then
screw the hexagon nuts M8 with right-handed thre-
ad and alloy ball-and-socket joints on the front wish-
bone thread rods M10/M8. Use medium screw
retention.
3. Push the front upper wishbone pins throughout
the pre-assembled front upper alloy wishbones in
the alloy front axle housing as described in position
22. Mount the front upper wishbone pins using Ø5
retaining washers.
4. Push four adjusting clips each at the front bet-
ween the alloy front axle housing and the front upper
alloy wishbones in the front upper wishbone pins.
6. Screw M5 nuts on M5x25 headless pins and
screw it from the top in the front upper alloy
wishbones.
7. Mount the ball diff. axle, protection bellow, distan-
ce disk and balls for the driving shaft on the univer-
sal joint driving shaft to the rear axle as the same
procedure in the manual of the ball driving shafts
(position 12). Push it in the front differential on the
ball diff. axle using a disk Ø8.4.
8. Push the universal joint driving shafts in the pre-
assembled left and right alloy uprights and mount
the square wheel driver 14mm with recess towards
the bearing to the surfaces of the universal joint dri-
ving shafts using M6x6 headless pins.
(Use a high-strength screw retention)
9. Mount the left and right alloy upright to the lower
alloy wishbones and alloy ball-and-socket joints of
the upper alloy wishbones with 2 disks Ø5.3 bet-
ween taper disk and alloy uprights using M5x25
countersunk screws.
Hint: Mount taper disks always with the thinner side
towards the alloy ball-and-socket joint.
Headless pin M5x25 to adjust
the rebound stop travel of the
front axle
Nut
M5
Headless
pin
M5x25
All metric screws need to be secured with thread lock fluid.
Make sure the universal joint driving shaft
has not more than 2mm clearance in hori-
zontal position. Mount enclosed disk
Ø8,5/18x1,5 between diff.axle and ball
bearing.
ca.24mm

Stop nut
M4
Stop nut
M4
Stop
nut
M4
Front bumper
Reinforcing plate
for front axle
Plastic
fixing plate
Plastic fixing plate
Brake guide rail
Alloy distance
Alloy
distance
Nut
M4
Shock mount
Brake
guide
rail
Disk
Ø4.3
Disk
Ø4.3
Disk
Ø4.3
Disk
Ø4.3
Screw
M4x10
Screw
M4x16
Screw
M4x14
Screw
M4x14
Screw
M5x40
Motor
Alloy
engine mount
small
Stop
nut
M5
Coupling
flange
Screw
M5x16
with disk
Screw
M4x8
Screw
M4x25
Screw
M4x30
Position 24
Parts are in
bag G
Position 25
Parts are in
bag G
Position 26
Parts are in
bag H
1. Mount the shock mount to the reinforcing plate for
the front axle using M4x16 countersunk screws,
disks Ø4.3 and M4 stop nuts.
2. Mount the plastic fixing plate with brake guide rail
and alloy distances between the brake guide rail and
reinforcing plate to the reinforcing plate for the front
axle using M4x30 pan-head screws, disks Ø4.3 and
M4 stop nuts.
3. Then mount the reinforcing plate for the front axle
to the alloy front axle carriers using M4x10 pan-head
screws and disks Ø4.3. (Position 25)
4. Mount the front shock absorbers to the front lower
alloy wishbones using M4x14 cylinder screws. Push
M4x25 countersunk screws in the shock mount (posi-
tion 24) and counter using M4 nuts, then mount the
upper shock absorber with internal silicone tube Ø4
and M4 stop nuts.
Hint: For the mechanic tuning brake, please observe
the fitting of the brake guide rail; also refer to the illu-
stration of position 48.
1. Mount the front bumper to the alloy chassis using M4x8 pan-head
screws and disks Ø4.3 and mount it on the alloy front axle carriers
using M4x14 pan-head screws.
1. Mount the small alloy engine mount to the motor using M5x40 cylin-
der screws and counter with M5 stop nuts. For this purpose, the origi-
nal screws on the motor need to be removed.
2. Mount the coupling flange to the motor using M5x16 cylinder
screws with forced on disk according to the illustration.

Screw
M4x14
Screw
M6x40
Screw
M6x40
Screw
M6x10
Screw
M6x10
Screw
M6x16
Screw
M5x12
Screw
M4x14
Screw
M6x10
Screw for carrier
M6x14 with disk
Motor
Coupling flange
Coupling flange
Clutch block
carrier
Alloy engine
mount
large
Alloy engine
mount large
Steel gearw-
heel 14 teeth
Bowden
cable holder
Bolt for
gear unit
Adjustable screw
Headless
pin
M5x5
Headless
pin
M5x5
Headless
pin
M6x6
Tuning
gear shaft
Longer flat
surfaces
Steel gearwheel
46 teeth
Shim ring
10x16x1
Shim ring
10x16x1
Steel
gearwheel
18 teeth
Alloy
gearwheel
adapter
Alloy
gear
plate
Alloy
gear
plate
Tuning clutch
bell
Bolt for gear
unit
26.5mm
Bolt for gear
unit
24.5mm
Steel fixing
plate
long
Steel fixing
plate
short
Clutch
blocks
Clutch
spring
Dowel screw for
clutch blocks
Wave washer
Running
direction
Disk
6x15x1
Ball bearing
10x19x7
Remove the
screw and cut
of the housing
part.
Ball bearing
10x19x7
Ball bearing
10x22x6
Disk
Ø6.4
Disk
Ø6.4
Position 27
Parts are in
bag H
Position 28
Parts are in
bag I
Position 27a
Parts are in
bag I
1. Remove the recessed head screw from the cover of the engine hou-
sing and cut off the front part of the cover.
2. Mount the long and short steel fixing plate to the large alloy engine
mount using M4x14 pan-head screws, then mount the alloy engine
mount to the coupling flange using a M6x10 pan-head screw.
3. Mount the clutch block carrier to the motor using a M6x14 hexagon
head screw with forced on disk.
4. Secure the clutch spring in the clutch blocks and place one clutch
block on top of the other according to the illustration.
5. Put the wave washers on the dowel screws for the clutch blocks and
push it in the clutch blocks from the side with the arrows (running
direction of the motor). Mount it to the clutch block carrier using disks
6x15x1.
Hint: If the FG piston punching pin item No 08542 is used, the mounting
of the clutch will be considerably simplified.
1. Push the tuning clutch bell in the alloy gear plate as described in
position 28 and put on a shim ring 10x16x1, a steel gearwheel with 18
teeth and two additional shim rings 10x16x1. Mount the steel gearw-
heel on the surfaces of the tuning clutch bell using the M5x5 headless
pins and secure it using a lenticular flange head screw M6x10.
2. Push the tuning gear shaft flush in the alloy gearwheel adapter from
the side with the longer flat surfaces and secure it using M6x6 head-
less pins and a M6x10 lenticular flange head screw.
3. Mount the steel gearwheel with 46 teeth to the alloy gearwheel
adapter using M5x12 pan-head screws.
4. Push the tuning gear shaft in the alloy gear plate.
5. Push 2 bolts for gear unit 26.5mm at the top and one bolt for gear
unit 24.5mm at the bottom from the inside in the alloy gear plate
according to the illustration. For the mechanic tuning brake build in the
bowden cable holder as described in position 27a.
6. Push the tuning gear shaft throughout the ball bearings of the alloy
gear plate and the alloy engine mount and mount the alloy gear plate
to the coupling flange using M6x40 cylinder screws and disks Ø6.4.
7. Push the steel gearwheel with 14 teeth on the tuning gear shaft
according to the illustration and mount it to the surfaces of the tuning
clutch bell using M5x5 headless pins. Secure it using a M6x16 coun-
tersunk screw, use a high-strength screw retention.
Mount the bowden cable holder only for the mechanic tuning
brake, also refer to the illustration of position 51
1. Screw the adjustable screws in the bowden cable holder.
2. Push the bowden cable holder in the bolt for the gear unit and
mount it using 2.9x9.5 pan-head screws.
All metric screws need to be
secured with thread lock fluid.

Screw
M5x16
Screw
M4x30
Screw
M4x14
Screw
4.2x16
Screw
4.2x16
Screw
M4x10
Screw
4,2x13
Screw
4,2x16
Motor
Alloy engine
mount large
Disk
Ø4.3
Disk
Ø4.3
Manifold
Silencer
gasket
Alloy chassis
Tank mount
Tank complete
Tank base
Engine mount
screw
O-ring for
air filter adapter
Air filter
adapter
Filter cover
Foam filter
Basic
body
Gearwheel
cover
gear
Position 29
Parts are in
bag J
Position 30
Parts are in the
bags H, J, K
1. Mount the exhaust manifold to the motor using
M5x16 pan-head screws and a silencer gasket.
2. Mount the gearwheel cover of gear to the large
alloy engine mount using a pan-head screw M4x10
and a disk Ø4.3 as described in position 29.
3. Insert the O-ring for the air filter adapter in the
basic body and mount it to the air filter adapter using
4.2x13 countersunk screws.
4. Press the oiled foam filter on the basic body and
mount it with the filter cover a 4.2x16 countersunk
screw.
5. Insert the pre-assembled motor in the alloy chassis
and mount it throughout the left alloy rear axle mount
using a M4x30 pan-head screw and a disk Ø4.3, but
only put on the M4x30 pan-head screw, do not tigh-
ten it yet. Also refer to position 32.
6. Mount the pre-assembled motor to the alloy chas-
sis using M4x14 countersunk screws and engine
mount screws.
7. Mount the tank with tank cover showing to the
right and tank mount with longer side showing to the
right on the tank base and fasten it using 4.2x16
countersunk screws.
8. Mount the assembled tank on the tank base to the
alloy chassis using 4.2x16 countersunk screws.
Hint: The enclosed foam filter is ready-to-use and
oiled. If at a later point in time a filter is required
which is ready-to-use, please proceed as follows: In
order to oil the foam filter, put the filter together with
FG filter oil for foam filter item No 06441 into a plastic
bag and then press together to rub it in.
Screw
M4x30
Disk
Ø4.3
Alloy rear
axle mount
left
Alloy
connection
brace
Alloy engine
mount large
Fuel hose
black
Fuel hose
yellow Position 32
Parts are in
bag H
Position 31
Parts are in
bag K
1.Tighten the M4x30 pan-head screw after you have
tightened the engine retaining screws.
2. Lay the fuel hoses according to the illustration
and cut them if necessary.
Please make sure that the driving gearwheels, driving shafts, etc. can be easily tur-
ned without any resistance.

Screw
M3x20
Screw
M3x16
Screw
M3x16
Screw
M3x16
Screw
4.2x13
Screw
2.9x9.5
Screw
2.9x9.5
Screw
2.9x9.5
Disk
Ø3.2
Stop nut
M3
Servo
arm
Nut
M3
Stop nut
M3
Distance bolt
48mm
Distance bolts
53mm
Distance
bolts
53mm
Flexible aerial
Aerial mount
Servo mount
plate
Servo mount
plate
Alloy RC
plate
Alloy RC plate
Brake servo
Brake
servo
Steering servo
Steering servo
Steering servo
Steering servo
Throttle/brake
servo
Throttle/brake
servo
Position 33
Parts are in
bag L
Position 34
Parts are in
bag L
1. Mount the distance bolt 53mm at the front and the
distance bolt 48mm at the rear to the alloy RC plate
using 4.2x13 pan-head screws.
2. Mount the servo mount plate from the bottom to
the alloy RC plate using 2.9x9.5 pan-head screws.
Mount the throttle/brake servo and the brake servo to
the servo mount plate using the enclosed fixing rub-
ber bushings and screws as described in position 33.
3. Mount the steering servos to the alloy RC plate
using the enclosed fixing rubber bushings, M3x16
pan-head screws, disks Ø3.2 and M3 stop nuts.
4. Mount the aerial mount to the alloy RC plate using
a M3x16 pan-head screw and a M3 stop nut. Push
the flexible aerial in the aerial mount and fix it using a
2.9x9.5 pan-head screw.
5. Switch on the remote control system and set the
steering servos to the neutral position by using the
remote control.
6. Mount a M3x20 pan-head screw in the servo arm
and secure it using a M3 nut (drill out the servo arm if
necessary). Press the servo arm on the steering ser-
vos according to the illustration and fasten it using
the enclosed screws. If possible, the servo arms
should be at a 90-degree position to the steering
servo and depending on the type, they need to be
cut.
Before you start mounting of the remote control components, ple-
ase also thoroughly read the enclosed RC manual and deal with
the transmitter, receiver and the servos. Charge the receiver and
transmitter batteries to full charging level and check if they are
working properly.
All metric screws need to be secured with thread lock fluid.

Track rod r/l
74mm
Ball-and-socket
joint for M6
Alloy joint ball
Rods M4 Ball-and-
socket joint
7mm
Steel ball
7mm
Screw
M3x20
Screw
M4x20
Nut M3
Stop
nut
M3
Stop
nut M4
Position 38
Parts are in
bag L
For the receiver/servo current supply, we recom-
mend to use the FG Mini-Racing pack item No
06543/01 due to the constricted space conditions.
Additionally, there is also required the FG receiver
cable 06547/02.
1. Mount the pre-assembled alloy RC plate to the alloy
chassis using 4.2x16 countersunk screws as described
in position 35.
2. Screw M4x30 headless pins centrically in the
distance bolts 48mm and mount it to the alloy chas-
sis using the 4.2x16 countersunk screws.
3. Press the lower part of the receiver box on the
M4x30 headless pins. Connect the servo cable,
battery cable, etc. to the receiver and check if it is
working properly.
4. Then stow the cable remnants of the servos in the
receiver box, lead the aerial cable out of the receiver
box and push it in the flexible aerial.
5. In order to lead-in the cables, cut 1-2 holes with a
diameter of approx. 8mm at an appropriate position
of the upper part of the receiver box.
6. For sealing, place an O-ring on the lower part of
the receiver box and then put on the upper part of
the receiver box.
7. Screw the battery stud bolts on the M4x30
headless pins and close the receiver box.
8. Mount the receiver battery to the alloy battery
brace using insulating tape according to the
illustration and put it completely on the battery stud
bolts.
9. Cut the dampening rubber according to the
illustration and put it on the battery stud bolts. Mount
the body clamps in the battery stud bolts in order to
secure it.
Hint: Cover the lower part of the receiver box with
some foam in order to protect the receiver against
vibrations.
Position 36
Parts are in
bag L
Screw
4.2x16
Screw
4.2x16
Distance bolt
48mm
Distance bolt
48mm
Distance bolt
48mm
Headless
pin
M4x30
Receiver
box
O-ring
Battery stud
bolt
Battery stud
bolt
Item No
06543/01
Item No
06547/02
Battery stud
bolt
Body
clamp
Cut off the sur-
face of the
dampening
rubber.
Dampening
rubber
Alloy chassis
Cut off the upper part
of the receiver box
Alloy battery
brace
Alloy battery
brace
Receiver
battery
Position 35
Parts are in
bag L
Flexible
aerial
ca.44mm

Retaining
washer
6mm
Shim ring
7x13x0.3
Alloy servo
saver B
Alloy servo
saver A
Servo
saver
spring
O-rings
Guide bush
7x10x14
Flange sleeve for the
alloy servo saver
Servo saver
axle
Position 37
Parts are in
bag L
1. Mount the servo saver spring to the alloy servo saver A, then push the
flange sleeve for the alloy servo saver in the alloy servo saver A.
2. Push the guide bush 7x10x14 in the alloy servo saver B, until both
are flush with the upper side. Assemble the alloy servo saver B in the
alloy servo saver A.
3. Push the servo saver axle from the upper side throughout the alloy
servo saver A and secure it using a shim ring 7x13x0.3 and a retaining
washer Ø6, then check if it can be moved easily.
4. Press O-rings on the alloy servo saver.
5. Screw ball-and-socket joints for M6 on the track rods r/l 74mm as
described in position 38 and push the alloy joint balls into the ball-and-
socket joints.
6. Screw ball-and-socket joints 7mm on the rods M4 and push steel
balls 7mm into the ball-and-socket joints.
7. Screw M3x20 pan-head screws in the alloy servo saver according to
the illustration and counter using a M3 nut. Mount the assembled
servo rods with collar of the steel ball 7mm towards the alloy servo
saver using a M3 stop nut.
8. Mount the track rods with collar of the alloy joint balls towards the
alloy servo saver to the alloy servo saver according to the illustration
using M4x20 cylinder screws and M4 stop nuts.
Hint: The effect of the alloy servo saver can be adjusted by the num-
ber of the used O-rings. The more O-rings are used, the harder is the
effect of the alloy servo saver.
When using the FG ball mounting device item No 08544, the mounting of
the balls in the ball-and-socket joint will be eased considerably.
Screw
4,2x16
Screw
M4x20
Screw
M5x16
Nut
M4
Roll cage
Alloy chassis
Alloy
steering lever
Disk
Ø5.3
Stop
nut M3
Position 39
Parts are in
the bags L, M
Position 40
Parts are in
bag L
Track rod
mounted
Servo rods
mounted
Screw
M3x20
Nut M3
Nut M3
Stop nut
M3
1. Mount the using a M5x16
pan-head screw and disk Ø5.3
as described in position 39.
2. Mount the track rods to the
alloy steering levers using
M4x20 cylinder screws and M4
nuts as distance.
3. Switch on the remote con-
trol system, set the trimming
of the steering to the central
position. Firstly mount 1 servo
rod to the servo saver, then
mount the other to the servo
saver. Both servo rods need
to be pressed easily and
without resistance on the
M3x20 screw of the servo
saver.
4. Mount the roll cage to the
alloy chassis using 4.2x16
countersunk screws.

Screw
M4x14
Screw
4.2x22
Screw
4.2x22
Screw
4.2x25
Screw
4.2x13
Hose
clamp
Exhaust
hose
Manifold
3-unit tuning
pipe
Plastic com-
ponent for
stiffening
brace
Spark plug
cover
Roll
cage
Plastic brace
long
Plastic brace
short
Spoiler
mount
Rear body
mount Baja
Headless
pin
M4x50
Headless
pin
M5x25
Alloy rear
shock mount
Throttle rods
Collet
Headless
pin M3x3
Carburetor
arm
Servo arm
Stop nut
M3
Stop
nut
M3
Nut
M3
Throttle/brake
servo
Throttle rods
Throttle rods
Collet
Headless pin
M3x3
Screw
M3x25
Pressure
spring
Throttle pivot
post
Steering servo
Position 42
Parts are in
bag N
Position 43
Parts are in
bag N
Position 41
Parts are in
bag M,O
1. Mount the throttle rods to the carburetor arm using collets and M3x3
headless pins. Keep some clearance between the collets and the car-
buretor arm. Please make sure that the carburetor arm can be easily
moved.
2. Push a M3x25 pan-head screw in the servo arm and secure it using
a M3 nut. Screw on two M3 stop nuts as distance and mount the
servo arm using the screw which is enclosed in the throttle/brake
servo.
3. Push the collet, pressure spring, throttl pivot post and collet on the
throttle rods. In doing so, press the throttle pivot post on the M3x25
pan-head screw and secure it using a M3 stop nut. Mount the collets
using M3x3 headless pins.
Switch on the remote control system. Set the servo for throttle and
brake to the central position. Then clamp the collet to the throttle pivot
post using a M3x3 headless pin. Set the transmitter to the full throttle
position. Check, if the carburetor arm is set to the full throttle position.
Hint: Do not tighten the M3 stop nut at the throttle pivot post. The
throttle pivot post and the throttle rods need to run smoothly, move
easily and should neither touch nor clamp in any position.

Screw
4.2x25
Bend the
fixing wire
according to
the illustration
Fixing wire
Headless
pin
M5x5
Headless
pin
M5x5
Hose
clamp
Exhaust
hose
Manifold
3-unit tuning pipe
3-unit tuning
pipe
Plastic com-
ponent for
stiffening
brace
Position 45
Parts are in
the bags M,O
Position 44
Parts are in
the bags M,O
1. Press the exhaust hose with the hose clamps on the 3-unit tuning
pipe, then push it with the free end on the manifold.
2. Screw M5x25 headless pins halfway through in the spoiler mounts
(position 41), then screw on the long plastic braces according to the
illustration.
3. Fasten the mounted spoiler mounts to the rear alloy shock mount
using M4x14 cylinder screws as described in position 41.
4. Mount the short plastic braces to the spoiler mounts and the long
plastic braces using 4.2x22 pan-head screws as described in the posi-
tion 41.
5. Mount the rear body mounts Baja showing outwards to the long pla-
stic braces using 4.2x22 pan-head screws as described in position 41.
6. Mount the spark plug cover to the long plastic braces using 4.2x13
countersunk screws.
7. Screw M4x50 headless pins throughout the roll cage in the long pla-
stic braces, then screw on the plastic components for the stiffening
brace. On the left side you also have to mount the fixing wire for the 3-
unit tuning pipe. Position 41.
8. Bend the fixing wire for the rear 3-unit tuning pipe as described in
position 41 and fasten it on the left side of the spoiler mount. Then
align the shock absorber via the both fixing wires in that way, that it
does not touch at any position. Clamp the fixing wires using the M5x5
headless pins.
9. Then tighten the hose clamps on the exhaust hose.
Hint: When the exhaust hose is heating up the first time, the hose
clamps should be retightened.
All metric screws need to be secured with thread lock fluid.

Balance
collets
Servo
rods Servo
arm
Collet
Headless
pin
M3x3
Brake
guide rail
Position 47
Parts are in
bag R
Position 46
Parts are in
bag R
Position 48
Parts are in
bag R
The position 46-52 shows the Competition 4WD Off-Road 1:6 Baja Buggy item No 66001
with a mechanical brake system.
Front left disk
brake
Front right disk brake
Brake disk
Brake
disk
Alloy bow-
den cable
holder long
Alloy bowden
cable holder
long
Bowden
cable
Bowden
cable holder
Bowden
cable
Guiding
plate
Guiding
plate
Pressure
spring Disk
Brake lever
Alloy brake
caliper
Brake
shafts
Bearing
bush
Stud bolt
Stud
bolt
Ball bearing
flange
Brake shaft
Competition
brake lining
Competition
brake lining
Screw
3x10
Screw
3x20
Screw
3x10
Headless pin
3x10
Stop
nut
M3
Stop
nut
M3
In order to mount the tuning disk brake, please
refer to the descriptions in the enclosed
manual.
Mount the components of the disk brake
according to the construction stages. The
metric screws need to be secured using the
medium screw retention.
The brake shafts are available in two different
types. When mounting, the surface as well as
the boring for the brake lever must show
outwards or respectively to the brake lining.
Adjustment of the brake
If the throttle/brake of the transmitters is set to the
central position, it has to be possible to turn the
brake disks in the left and right direction. In direc-
tion to the brakes (transmitters), both brakes have to
perform an equal braking effect on the disks. If there
is only an one-sided braking effect, tighten the
corresponding bowden cable holder on the balance.
For this purpose you have to loosen the collet. If the
braking effect of both brakes is too much or too
low, loosen the middle collet on the balance and
in accordance with shift the balance to the front or
to the rear.
If there is too much clearance between the brake
linings of the brake disk, you have to tighten the M3
stop nut at the outside brake lining equally.
The brake power of the front brake should be a little
bit higher than the brake power of the rear brake.
Determine the accurate braking distribution when
driving.
The servo rods have to be bent off according
to the guide in the brake guide rail. It must run
smoothly and should not touch at any position.
This manual suits for next models
1
Table of contents
Other FG Modellsport Toy manuals
Popular Toy manuals by other brands

Eduard
Eduard Flakpanzer 38 (Gepard) exterior quick start guide

Nine Eagles
Nine Eagles Sky 500 instruction manual

Phoenix Model
Phoenix Model KATANA-EP instruction manual
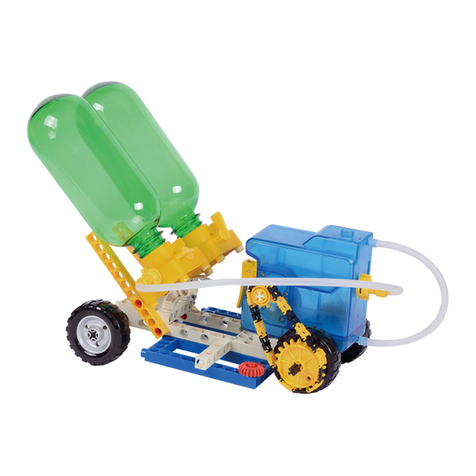
Thames & Kosmos
Thames & Kosmos Air Plus Water Power Plus Experiment manual
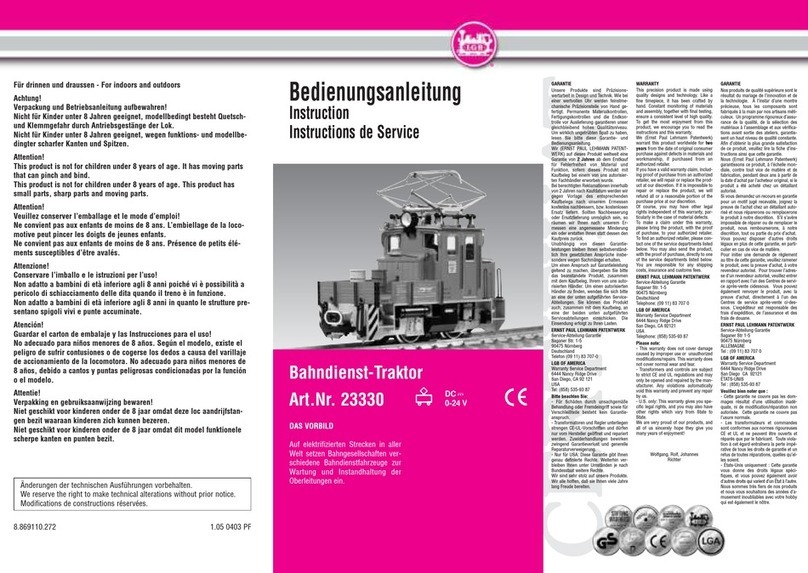
LGB
LGB 23330 instruction manual
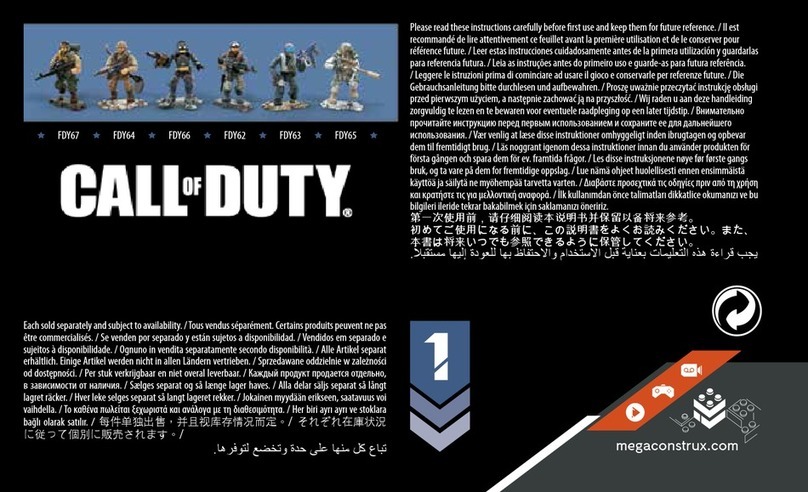
Mega Construx
Mega Construx Call of Duty FDY63 instructions

Mega Bloks
Mega Bloks Barbie Build'n Play Beauty Kiosk manual
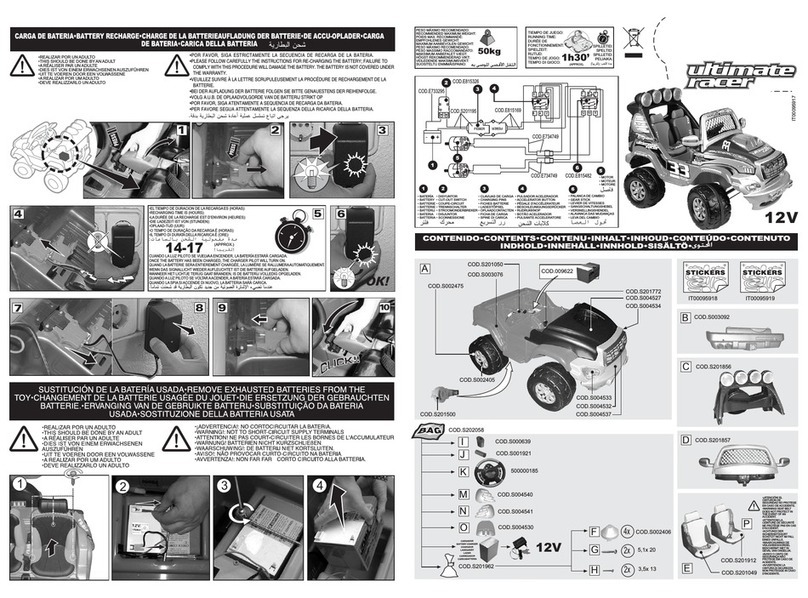
Viking
Viking Ultimate Racer Assembly guide
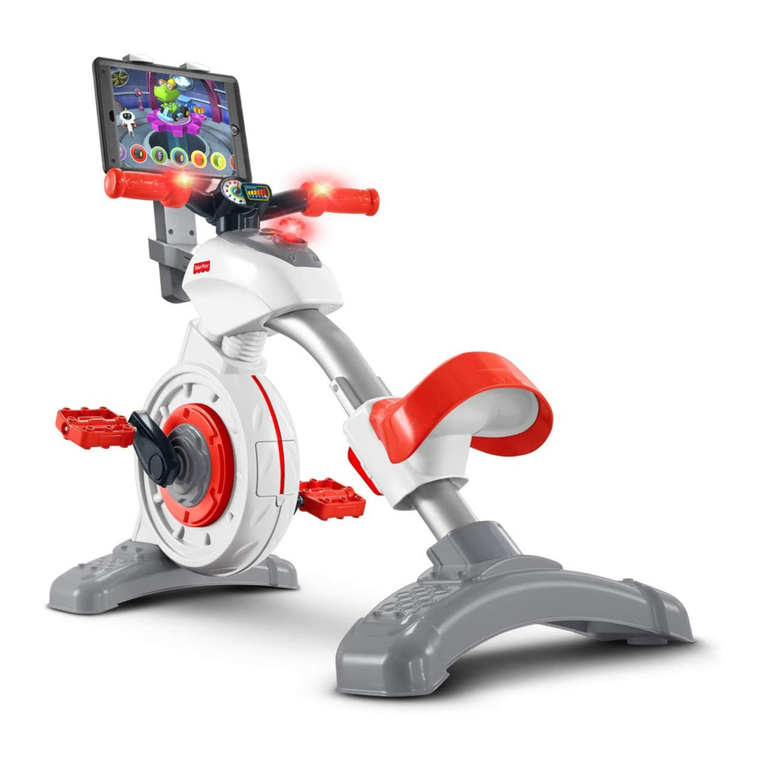
Fisher-Price
Fisher-Price smart cycle Assembly Tip
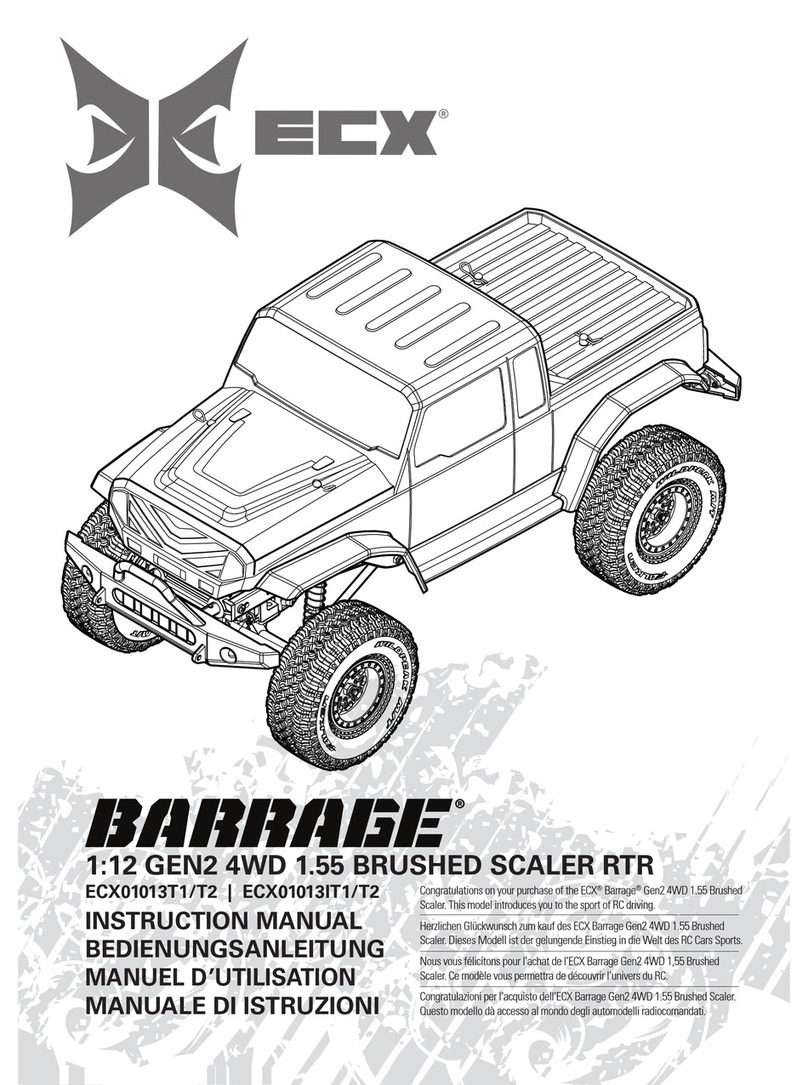
ECX
ECX BARRAGE instruction manual
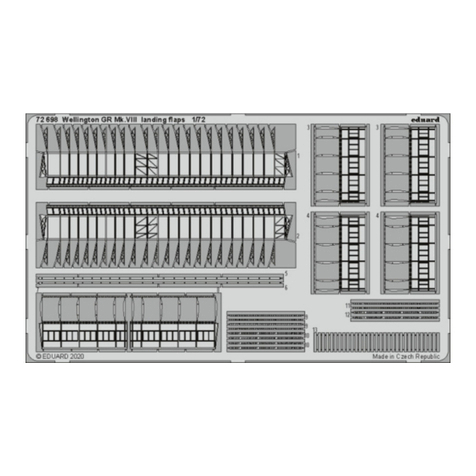
Eduard
Eduard Wellington GR Mk.VIII landing flaps Assembly instructions
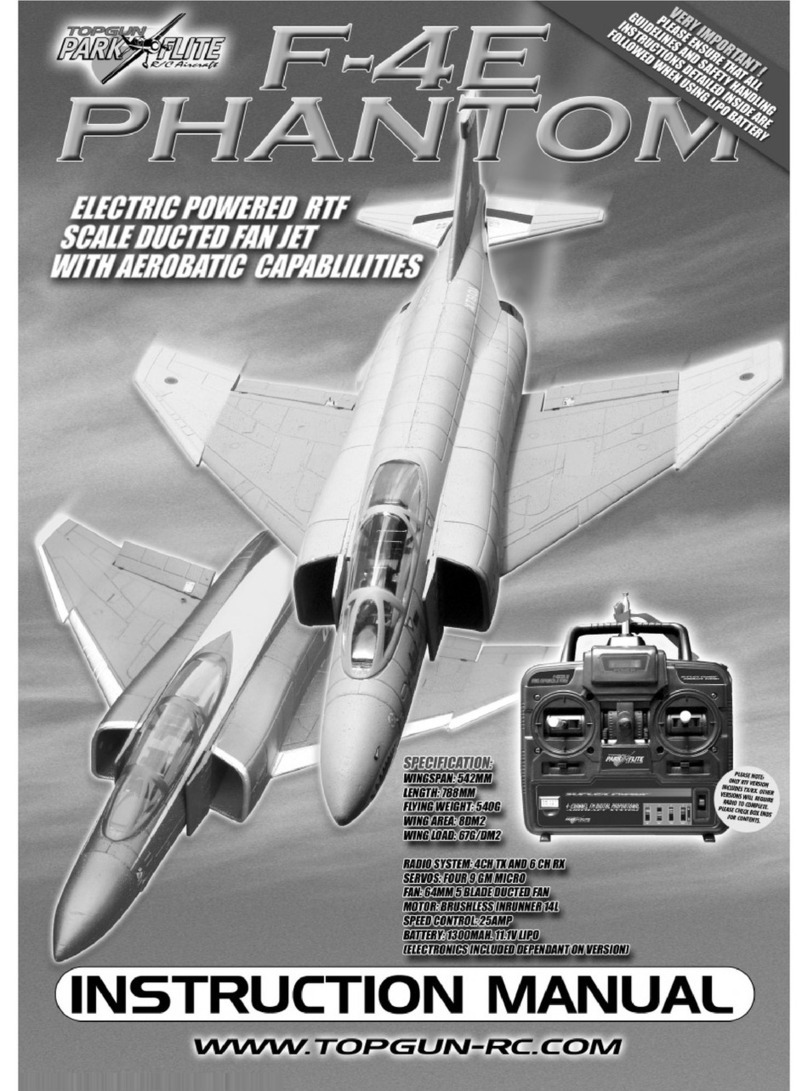
Top Gun Park Flite
Top Gun Park Flite F-4E Phantom instruction manual