FIRETRACE 800095-A User manual

INSTALLATION MANUAL
DUAL PRESSURE SWITCH MODULE
WITH & WITHOUT BYPASS
DIOM P/N: 800095-A
Firetrace USA LLC
Firetrace International LLC
North and South America
8435 N. 90TH St, Suite 2
Scottsdale, AZ 85258 USA
Telephone: 480-607-1218
Fax: 480-315-1316
www.firetrace.com

DIOM 800095-A i 7/22/2022
REV DESCRIPTION OF CHANGE BY APPRVD.
ECO DATE
A INITIAL RELEASE ZS BC DCR22-012 7/22/2022
Dual Pressure Switch Module – Installation Manual
Originally Prepared By: Zach Smith

DIOM 800095-A ii 7/22/2022
Table of Contents
1 FOREWORD ..................................................................................................................................................................... 1
1.1 Warnings ............................................................................................................................................................... 1
1.2 Safety Precautions .................................................................................................................................................. 1
2 GENERAL ........................................................................................................................................................................ 2
2.1 Description ............................................................................................................................................................. 2
2.2 Variants ................................................................................................................................................................. 2
2.3 Product Dimensions ................................................................................................................................................ 2
2.3.1 With Bypass Key Switch .................................................................................................................................... 2
2.3.2 Standard (without Bypass) ................................................................................................................................. 3
2.4 Specifications ......................................................................................................................................................... 3
2.4.1 Electrical ......................................................................................................................................................... 3
2.4.2 Environmental .................................................................................................................................................. 3
3 INSTALLATION ................................................................................................................................................................. 4
3.1 Opening the Module ................................................................................................................................................ 4
3.1.1 With Bypass Key Switch .................................................................................................................................... 4
3.1.2 Standard (without Bypass) ................................................................................................................................. 5
3.2 Configuring the Module ............................................................................................................................................ 5
3.3 Configuration Testing .............................................................................................................................................. 6
3.4 Closing the Module.................................................................................................................................................. 8
3.4.1 With Bypass Switch .......................................................................................................................................... 8
3.4.2 Standard (without Bypass) ................................................................................................................................. 8
3.5 Mounting the Module ............................................................................................................................................... 8
3.5.1 Direct Mounting ................................................................................................................................................ 9
3.5.2 Flange Mounting Kit .......................................................................................................................................... 9
3.5.3 Magnetic Mounting Kit..................................................................................................................................... 10
3.6 Wiring the Module ................................................................................................................................................. 10
3.7 System Activation ................................................................................................................................................. 11
4 SERVICE AND MAINTENANCE .......................................................................................................................................... 12
4.1 General ................................................................................................................................................................ 12
4.2 Post Discharge, System Recharge, and Return to Service .......................................................................................... 12
5 APPENDIX A................................................................................................................................................................... 13
Table of Figures
Figure 1 – Bypass Variant Envelope Dimensions | Top View ............................................................................................................................................. 2
Figure 2 – Bypass Variant Envelope Dimensions | Side View ............................................................................................................................................ 3
Figure 3 – Standard Variant Envelope Dimensions | Top View .......................................................................................................................................... 3
Figure 4 – Standard Variant Envelope Dimensions | Side View ......................................................................................................................................... 3
Figure 5 – Environmental Limitations ................................................................................................................................................................................. 3
Figure 6 – Exploded View | with Bypass ............................................................................................................................................................................. 4
Figure 7 – Exploded View | Standard ................................................................................................................................................................................. 5
Figure 8 – Configuration Board Overview........................................................................................................................................................................... 5
Figure 9 – Switch Position Details ...................................................................................................................................................................................... 6
Figure 10 – Threaded Insert ............................................................................................................................................................................................... 8
Figure 11 – Threaded Insert Dimensions ........................................................................................................................................................................... 9
Figure 12 – Flange Mounting Kit......................................................................................................................................................................................... 9
Figure 13 – Flanges Installed ........................................................................................................................................................................................... 10
Figure 14 – Magnetic Mounting Kit ................................................................................................................................................................................... 10
Figure 15 – Magnets Installed .......................................................................................................................................................................................... 10
Figure 16 – Cable Harness Install | Exploded View .......................................................................................................................................................... 11
Figure 17 – Harness Pinout Diagram ............................................................................................................................................................................... 11

DIOM 800095-A iii 7/22/2022
List of Tables
Table 1 – Variant Specifications ......................................................................................................................................................................................... 2
Table 2 – Configuration Specification | With Bypass .......................................................................................................................................................... 6
Table 3 – Configuration Specification | Standard ............................................................................................................................................................... 6
Table 4 – Testing Reference | With Bypass ....................................................................................................................................................................... 7
Table 5 – Testing Reference | Standard ............................................................................................................................................................................. 8
Table 6 – Pinout Details.................................................................................................................................................................................................... 11

DIOM 800095-A 1 7/22/2022
1 FOREWORD
1.1 Warnings
Safety precautions are essential when any electrical or mechanical equipment is involved. These precautions should be followed when
handling, servicing, and recharging Firetrace Fire Suppression Systems and equipment. If safety precautions are overlooked or ignored,
personal injury or property damage may occur.
The following symbols are used throughout this manual. Always heed these precautions. They are essential to the safe use of the equipment
described in this manual.
DANGER:
This danger symbol identifies immediate hazards and provides specific instructions or procedures, which if not correctly followed WILL
result in severe personal injury or death.
WARNING:
This warning symbol identifies specific instructions or procedures, which if not correctly followed, COULD result in severe personal injury
or death.
CAUTION:
This caution symbol identifies specific instructions or procedures, which if not correctly followed, COULD result in minor personal injury or
equipment or property damage.
1.2 Safety Precautions
The following safety precautions should always be followed:
WARNING
Pressurized
(charged)
cylinders
are
extremely
hazardous
and
if
not
handled
properly
are
capable
of
causing
property
damage, bodily
injury, or death. Always wear safety glasses and make sure the discharge plugs are properly in place before system installation,
servicing,
or
other
general
handling.
Read and understand this manual and the other documents referenced herein.
Wear safety glasses when working with pressurized cylinders and charging equipment.
Make sure that the ball valve (attached to the top of the cylinder valve) is closed (lever is in “OFF” position), the detection tubing has
been removed from the cylinder valve and the safety caps installed before removing the cylinder from the installation and before
performing any charging, leak tests or salvage operations.
Follow all the safety procedures included on the cylinder nameplate and in this manual.
Never assume that a cylinder is empty. Treat all cylinders as if they are fully charged.
Any questions concerning the information contained in this Manual should be addressed to:
Firetrace USA LLC.
Firetrace International LLC
North and South America
8435 N. 90TH St, Suite 2
Scottsdale, AZ 85258 USA
Telephone: 480-607-1218
Fax:480-315-1316
firetrace@firetrace.com
The following web site should be visited for frequent technical announcements
www.firetrace.com

DIOM 800095-A 2 7/22/2022
2 GENERAL
2.1 Description
The Dual Pressure Switch Module gives the ability to monitor the health of the Firetrace fire suppression system and deliver a shutdown / notification
signal in the event of a system discharge due to fire in a single package solution. The pressure switch module also contains an integrated end-of-line
adapter to help simplify the installation process. A signal bypass key switch is also included for ease of servicing.
When purchased, the module comes in a kit that includes:
Dual Pressure Switch Module
Cable Harness
o P/N 203210
Replacement Nameplate
o To align the nameplate with the mounting orientation of the module
2.2 Variants
The Dual Pressure Switch Module is offered in two main variants. Each variant includes two pressure switches utilizing either a supervisory and
activation pressure switch or two activation pressure switches. The “Standard” variant only contains a combination of these two pressure switches and
no signal bypass or end-of-line adapter. The second variant adds the bypass key switch and integrated end-of-line to provide additional functionality
and ease of install. Table 1 below gives an overview of the different variants highlighting part numbers, fire suppression system pressures they are
used with, and the pressure switch types used.
Table 1 – Variant Specifications
Kit P/N Module
P/N
System
Pressure
Pressure
Switch 1
Set
Point
Pressure
Switch 2
Set
Point
With Bypass
603305 601305 195psi Activation 70psi Supervisory 150psi
603315 601315 150psi Activation 70psi Supervisory 99psi
603325 601325 Any Activation 70psi Activation 70psi
Standard
603400 601400 195psi Activation 70psi Supervisory 150psi
603410 601410 150psi Activation 70psi Supervisory 99psi
603420 601420 Any Activation 70psi Activation 70psi
2.3 Product Dimensions
2.3.1 With Bypass Key Switch
Figure 1 – Bypass Variant Envelope Dimensions | Top View

DIOM 800095-A 3 7/22/2022
Figure 2 – Bypass Variant Envelope Dimensions | Side View
2.3.2 Standard (without Bypass)
Figure 3 – Standard Variant Envelope Dimensions | Top View
Figure 4 – Standard Variant Envelope Dimensions | Side View
2.4 Specifications
2.4.1 Electrical
The electrical limitations below are for both variants of the Dual Pressure Switch Module, with and without bypass key switch.
Max Voltage: 24V
Max Current: 2A
2.4.2 Environmental
Variant IP Operating Temp
With Bypass N/A -40°F to 150°F
-40°C to 65.6°C
Standard IP64 -40°F to 150°F
-40°C to 65.6°C
Figure 5 – Environmental Limitations

DIOM 800095-A 4 7/22/2022
3 INSTALLATION
The Dual Pressure Switch Module is an easy addition to any Firetrace fire suppression system installation. There are only a few simple steps to
complete prior to mounting the box in its desired location and connecting it to the detection tubing network.
1. Open the pressure switch module to gain access to the configuration panel
2. Set the toggle switches to the specified position based on the configuration required for the installation
3. Close the pressure switch module
4. Secure the Dual Pressure Switch Module in place
5. Wire the pressure switch module using the supplied cable harness
6. Insert tubing into the slip-on fitting to connect the module to the detection network
7. Pressurize the Firetrace detection tubing.
The rest of the installation of the Firetrace fire suppression systems should follow the instructions called out in the specific DIOM of the system being
installed. Reference the following sections for more detail on each of the steps outlined above.
3.1 Opening the Module
3.1.1 With Bypass Key Switch
Figure 6 – Exploded View | with Bypass
Reference the number callouts in Figure 6 above for the process below
1. Remove pressure gauge (1) from integrated end-of-line adapter (4)
2. Remove retaining nut (2) from integrated end-of-line adapter (4)
3. Remove bonded washer (3) from integrated end-of-line adapter (4)
4. Unscrew the four screws (5) in the corner of the box
5. Remove cover
1
2
3
4
5

DIOM 800095-A 5 7/22/2022
3.1.2 Standard (without Bypass)
Figure 7 – Exploded View | Standard
Reference the number callouts in Figure 7 above for the process below
1. Unscrew the four screws (1) in the corner of the box
2. Remove cover
3.2 Configuring the Module
The Dual Pressure Switch Module utilizes a series of adjustable toggle switches on a circuit board to configure the available pressure switch and
bypass key switch states. In Figure 8, the toggle switches numbered for identification and highlight which pressure switch they are tied to. These
toggle switch numbers will be referenced in Table 2 & Table 3. The identification numbers for the toggle switches are screen-printed onto the PCB
The bypass key switch can be configured to perform distinct functions on each of the pressure switches when the key is moved to the bypass position.
Figure 8 – Configuration Board Overview
1

DIOM 800095-A 6 7/22/2022
Figure 9 – Switch Position Details
Table 2 – Configuration Specification | With Bypass
Install
Requirements PS1* PS2* Module
Config # SW1 SW3 SW5 SW2 SW4 SW6
Bypass Both
Activation &
Service
NC NC 1 1 1 1 1 1 1
NC NO 2 1 1 1 2 2 3
NO NO 3 2 2 3 2 2 3
NO NC 4 2 2 3 1 1 1
Bypass
Activation,
Force Service
**
NC NC 5 1 1 1 1 2 3
NC NO 6 1 1 1 2 1 1
NO NO 7 2 2 3 2 1 1
NO NC 8 2 2 3 1 2 3
Bypass Only
Activation
NC NC 9 1 1 1 1 2 2
NC NO 10 1 1 1 2 2 2
NO NO 11 2 2 3 2 2 2
NO NC 12 2 2 3 1 2 2
No Bypass
NC NC 13 1 2 2 1 2 2
NC NO 14 1 2 2 2 2 2
NO NO 15 2 2 2 2 2 2
NO NC 16 2 2 2 1 2 2
* Pressure switch configured to either normally open (NO) or normally closed (NC). Reference
Table 1 for pressure switch details.
** when in Bypass, service switch changes state
Table 3 – Configuration Specification | Standard
Install
Requirements PS1* PS2* Module
Config # SW1 SW3 SW5 SW2 SW4 SW6
No Bypass
NC NC 1 1 2 2 1 2 2
NC NO 2 1 2 2 2 2 2
NO NO 3 2 2 2 2 2 2
NO NC 4 2 2 2 1 2 2
* Pressure switch configured to either normally open (NO) or normally closed (NC). Reference
Table 1 for pressure switch detail
s
3.3 Configuration Testing

DIOM 800095-A 7 7/22/2022
A continuity test using the continuity test function on a multi-meter can be performed on the Dual Pressure Switch Module to verify the configuration is
what is needed or to verify proper functionality of the pressure switches during servicing. Table 4 & Table 5 below specifies the state of each pressure
switch when the module is in either a pressurized or unpressurized state and when the bypass key switch is in the normal or bypass position for the
module with the bypass functionality.
1. Note the configuration # the module has been set to
2. Set the key switch position to “Normal”
3. Connect the module to the detection circuit.
4. Connect the leads to the first pressure switch being tested to a multi-meter set to the continuity test function.
a. Reference Table 6 in Section 3.6 below for pinout details on the cable harness.
5. Verify the first pressure switch is in the correct state when normal and unpressurized.
6. Connect the multi-meter to the leads for the second pressure switch.
7. Verify the second pressure switch is in the correct state when normal and unpressurized.
8. Turn the key switch to the “Bypass” position.
9. Verify the second pressure switch is in the correct state for when bypassed and unpressurized.
10. Connect the multi-meter to the leads of the first pressure switch.
11. Verify the first pressure switch is in the correct state for when bypassed and unpressurized.
12. Pressurize the detection network.
13. Verify the first pressure switch is in the correct state for when bypassed and pressurized.
14. Connect the multi-meter to the leads for the second pressure switch.
15. Verify the second pressure switch is in the correct state for when bypassed and pressurized.
16. Turn the key switch to the “Normal” position.
17. Verify the second pressure switch is in the correct state for when normal and pressurized.
18. Connect the multi-meter to the leads of the first pressure switch.
19. Verify the first pressure switch is in the correct state for when normal and pressurized.
Table 4 – Testing Reference | With Bypass
Module
Config #
Key Switch
Position
PS1
(Unpressurized)
PS2
(Unpressurized)
PS1
(Pressurize
d)
PS2
(Pressurized)
1 Normal Closed Closed Open Open
Bypass Open Open Open Open
2 Normal Closed Open Open Closed
Bypass Open Closed Open Closed
3 Normal Open Open Closed Closed
Bypass Closed Closed Closed Closed
4 Normal Open Closed Closed Open
Bypass Closed Open Closed Open
5 Normal Closed Closed Open Open
Bypass Open Closed Open Closed
6 Normal Closed Open Open Closed
Bypass Open Open Open Open
7 Normal Open Open Closed Closed
Bypass Closed Open Closed Open
8 Normal Open Closed Closed Open
Bypass Closed Closed Closed Closed
9 Normal Closed Closed Open Open
Bypass Open Closed Open Open
10 Normal Closed Open Open Closed
Bypass Open Open Open Closed
11 Normal Open Open Closed Closed
Bypass Closed Open Closed Closed
12 Normal Open Closed Closed Open
Bypass Closed Closed Closed Open
13 Normal Closed Closed Open Open
Bypass Closed Closed Open Open
14 Normal Closed Open Open Closed

DIOM 800095-A 8 7/22/2022
Bypass Closed Open Open Closed
15 Normal Open Open Closed Closed
Bypass Open Open Closed Closed
16 Normal Open Closed Closed Open
Bypass Open Closed Closed Open
Table 5 – Testing Reference | Standard
Module
Config #
PS1
(Unpressurized)
PS2
(Unpressurized)
PS1
(Pressurized)
PS2
(Pressurized)
1 Closed Closed Open Open
2 Closed Open Open Closed
3 Open Open Closed Closed
4 Open Closed Closed Open
3.4 Closing the Module
3.4.1 With Bypass Switch
Reference Figure 6 in Section 3.1.1 above for part callouts
1. Place lid on top of the box
2. Partially screw cover screws (5) in place
3. Lube bonded washer (3)
4. Install bonded washer (3) over EOL (4) threads, seat to cover
5. Thread retaining nut (2) to hand tight then screw one more full turn with wrench
6. Tighten all four cover screws (5)
7. Install gauge (1)
3.4.2 Standard (without Bypass)
Reference Figure 7 in Section 3.1.2 above for part callouts.
1. Place lid on top of the box
2. Tighten all four cover screws (1)
3.5 Mounting the Module
The Dual Pressure Switch Module can be mounted in several different ways using the M4 SS threaded inserts located on the back of the box (see
Figure 10 below). The module can be mounted threading directly to the inserts, attaching flanges to allow for the use of self-tapping screws, or by
attaching magnets to the box to secure the module in its mounting location. Tighten screws to hand tight to avoid stripping the threaded inserts away
from the box. Thread locker should be used in higher vibration environments.
If mounted in a vertical orientation, remove the nameplate from the module and apply the supplied nameplate so that the content is readable.
Figure 10 – Threaded Insert

DIOM 800095-A 9 7/22/2022
CAUTION
Overtightening the screws threaded into the threaded inserts can result in stripping the threaded inserts away from the box.
The use of stainless-steel screws can result in seizing of screw in the threaded insert. Leading to overtightening.
3.5.1 Direct Mounting
Holes will need to be predrilled at the mounting location to allow for screws to be threaded in from behind. Figure 10 below gives the hole location
dimensions of the threaded inserts. Appendix A also contains a printable drill guide to aid in the mounting process. Do not use stainless-steel
screws. Seizing of the screw inside the threaded insert can occur, resulting in overtightening, and the potential stripping of the threaded inserts away
from the box
Figure 11 – Threaded Insert Dimensions
3.5.2 Flange Mounting Kit
Option to attach flanges to the box to allow r the use of self-tapping screws. The flanges are secured to the module using the supplied hardware. Adjust
flange so that the lip is flush with the side of the box. Figure 12 below highlights what is provided in the Flange Mounting Kit (P/N 111152). Figure 13
below shows the flanges installed on the module.
Figure 12 – Flange Mounting Kit

DIOM 800095-A 10 7/22/2022
Figure 13 – Flanges Installed
3.5.3 Magnetic Mounting Kit
The magnets are secured to the module using the supplied hardware. Magnets are a non-destructive option for mounting the module in place. The
non-permanent nature of this option allows for minor adjustments of the box during installation. Figure 14 below highlights what is provided in the
Magnetic Mounting Kit (P/N 111151). Figure 15 below shows the magnets installed on the module.
Figure 14 – Magnetic Mounting Kit
Figure 15 – Magnets Installed
3.6 Wiring the Module
The cable harness (P/N 203210) needs to be properly secured to the box when installed. Ensure the female connector on the harness is pushed all
the way in before tightening the connector body to the male connector on the box. Tighten to finger tight. Figure 17 below details the pin locations on
the harness. Table 6 indicates the relationship between each pin and wire and the pressure switch associated with them.
Cable shielding can be utilized by connecting directly to the shielding in the cable, if needed.

DIOM 800095-A 11 7/22/2022
CAUTION
Cross threading can occur on the harness connector if connection is forced
Figure 16 – Cable Harness Install | Exploded View
Figure 17 – Harness Pinout Diagram
Table 6 – Pinout Details
Pin
Wire Color
Pressure Switch
1 White Supervisory / Activation (PS2)
2 Brown Supervisory / Activation (PS2)
3 Green Activation (PS1)
4 Yellow Activation (PS1)
Shield Green/Yellow N/A
3.7 System Activation
1. Install the detection tubing throughout the enclosure. Ensure all necessary fittings and accessories are installed in accordance with the
procedures specified in the DIOM of the Firetrace suppression unit being installed
2. With the unit ball valve in the closed position, thread the tube fitting into the ball valve attached to the top of the cylinder valve.
3. Install one end of the Firetrace detection tubing into the fitting.
4. Ensure the end of line adapter is installed at the opposite end of the detection tubing. Verify no accessories are installed in the end of line
adapter.
a. If using the Dual Pressure Switch Module with the integrated end-of-line adapter, no end-of-line adapter needs to be installed as
part of the detection network.
5. Attach the filling adapter into the end-of-line adapter.
6. Attach a regulated nitrogen supply onto the filling adapter.
7. Pressurize the detection tubing to the suppression unit’s operating pressure.
8. Remove the nitrogen supply and filling adapter from the end-of-line adapter.
9. Thread the pressure gauge into the end of line adapter and verify that the tubing is pressurized to the correct pressure.
10. With the gauge still installed in the end-of-line adapter, test for leakage:

DIOM 800095-A 12 7/22/2022
a. Apply a soapy water solution to the cylinder valve connection, end of line adapter connection, and the pressure gauge connection.
b. Observe for bubble leaks.
c. After approximately 30 minutes, verify the pressure gauge reading. Any decrease in pressure is an indication of a leak.
d. If the system is determined to contain a leak, verify the installation procedures were properly followed for all fittings and accessories.
11. After confirming that there is no leakage within the detection tubing, SLOWLY rotate the ball valve lever counterclockwise, to the “ON”
position.
4 SERVICE AND MAINTENANCE
4.1 General
A regular program of systematic maintenance must be established for continuous, proper operation of all Dual Pressure Switch Modules, and to avoid
violating the warranty. A periodic maintenance schedule must be followed, and an inspection log maintained for ready reference. As a minimum, the
log must record: (1) inspection interval, (2) inspection procedure performed, (3) maintenance performed, if any, as a result of inspection, and (4) name
of inspector performing task. For any deficiencies that are found, appropriate corrective actions shall be taken immediately. Inspections should be
taken on a weekly, monthly, semi-annual basis according to the connected Firetrace Suppression unit’s manual.
1. Make a general visual inspection of the unit(s) for damaged or missing parts.
2. Ensure access to hazard areas and cylinders are unobstructed and that there are no obstructions to the operation of the equipment.
3. Inspect detection tubing in hazard area for abrasion, distortion, cuts, or dirt accumulation, and that there are no obstructions preventing
tubing from sensing a fire should one occur.
4. The Pressure Gauge(s) are in the operable range.
5. Neither the Protected Equipment nor the Hazard has been replaced, modified, or relocated.
6. Ensure that the proper electrical connections are not damaged, missing, or modified.
4.2 Post Discharge, System Recharge, and Return to Service
An authorized Firetrace distributor must be consulted after a system has discharged. The units must be removed and recharged. To remove the
connected Firetrace Suppression unit(s) please refer to that unit’s manual to return to service.

DIOM 800095-A 13 7/22/2022
5 APPENDIX A
Direct Mounting Hole Location Print Out

DIOM 8000
95
-
A
1
7
/
22
/2022
Table of contents
Popular Control Unit manuals by other brands
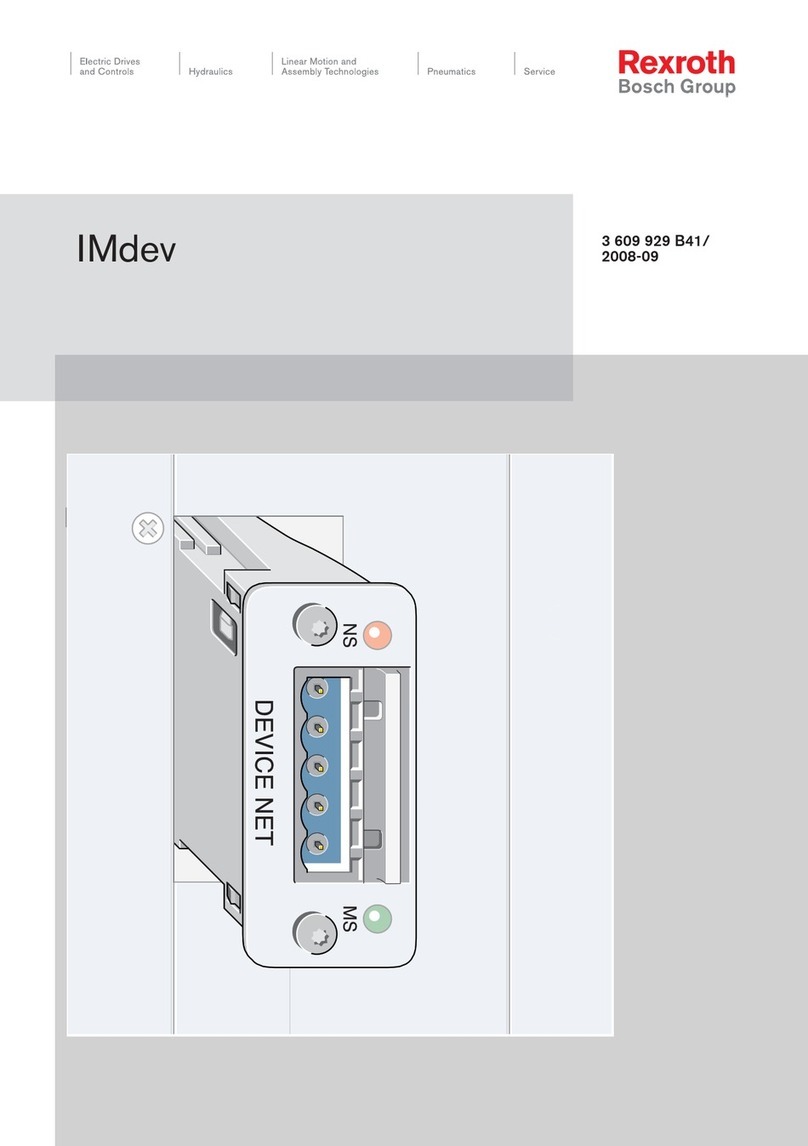
Bosch
Bosch Rexroth IMdev manual
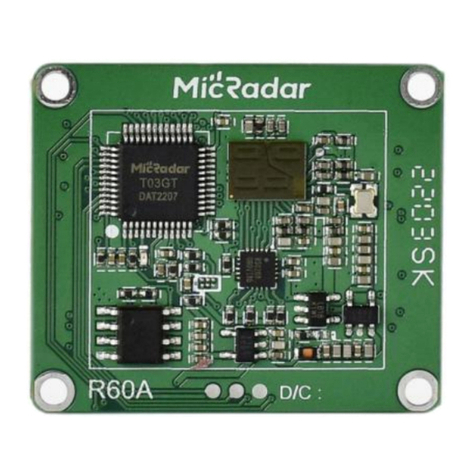
MicRadar
MicRadar R60AFD2 Using Guide
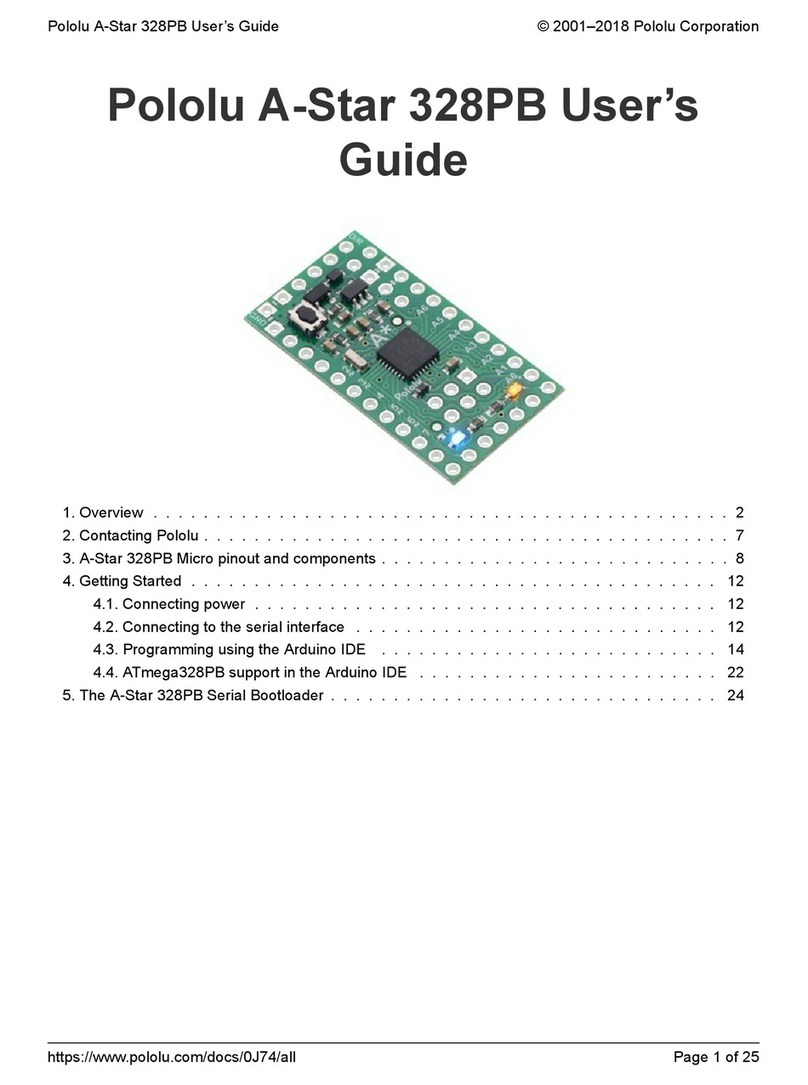
Pololu Corporation
Pololu Corporation A-Star 328PB user guide
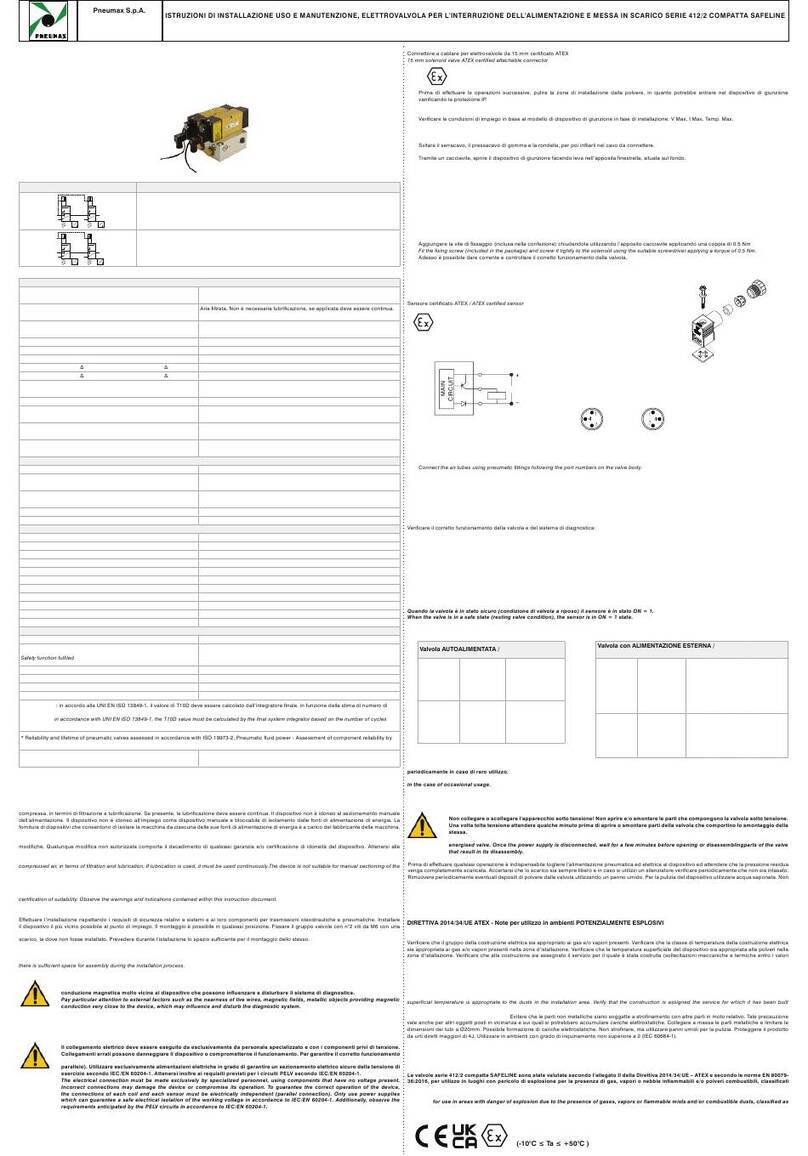
Pneumax
Pneumax 2 SAFELI 412/2 Series Installation, Use and Maintenance Instruction
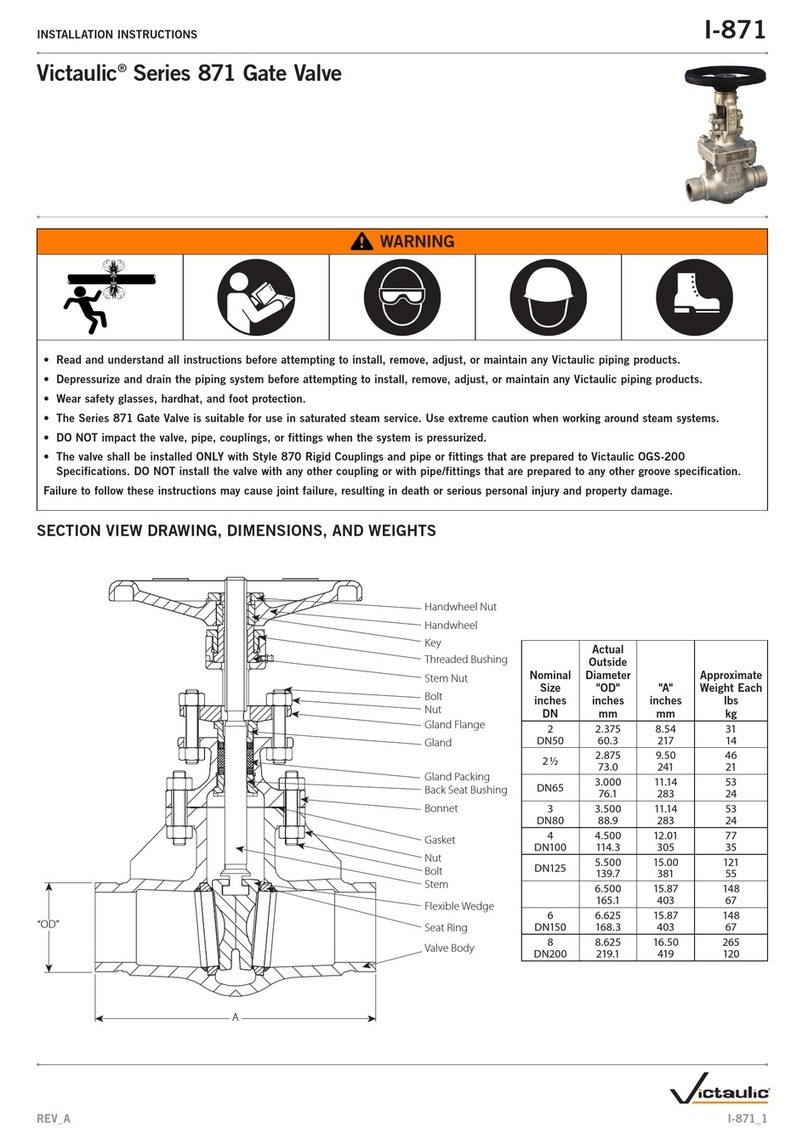
Victaulic
Victaulic 871 Series installation instructions
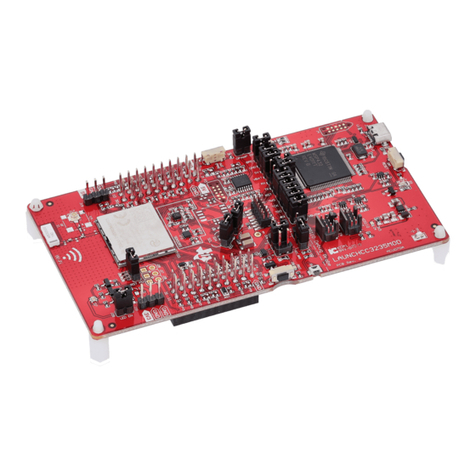
Texas Instruments
Texas Instruments SimpleLink CC3235MODS manual