FoamFly XPG User manual

TM
XPG
(XPERIMENTAL PUSHER GYRO)
Instruction Manual
Electric Parkflyer AutoGyro
Designed By: Dan Schwartz
Available Exclusively from:
www.FoamFly.com
4077 WoodCreek Dr.
Ypsilanti MI. 48197
USA
© 2007 FoamFly.com
!

©2007 FoamFly.com 2
Thank you for purchasing the XPG! If you’re reading this, you’ve probably
already been charmed and cannot resist building and flying one. You may be the
only one you know who flies a Gyro in your entire state.
All the pieces are specially designed to interlock, and are computer cut so that
they fit perfectly every time.
XPG Specs:
•Rotor Diameter: 36”
•Ready To Fly Weight 16 Oz.
•Motor: Included Brushless Outrunner
•Propeller: APC 8x3.8 Included
•Batteries: 3 cell 1000 – 1350 Lithium Polymer,
Basically any 3 - 4 Oz battery.
•Receiver: Berg (or other 4 Channel, 5+ w/pre-rotator)
•Servos: GWS Naro
•ESC: Castle Thunderbird 18 (or equivalent)
Introduction:
FoamFly.com is more than just a hobby company. It’s a community too!
With pilots and designers from all over. Please take pictures and videos of your
XPG, and I’ll put them in the photo gallery. Feel free to drop by and see what all
the other foam junkies have been building. There are free plans, and lots of tips
and ideas as well as unique new planes that you won’t find anywhere else.
NEW!! FoamFly kits are now easier to assemble. New techniques make all the
most tedious steps unnecessary.
Okay, you’ve got your XPG kit spread out in front of you. I know it looks
complicated, but take it one step at a time, and you won’t find it very difficult.
(They always say this but, “I highly recommend that you read the entire
instruction manual before beginning.”) Just remember to test fit each piece
before gluing, and if you get frustrated, just take a break, and have a soda. You
don’t have to finish this project in one sitting.
There are some techniques you’ll need to be familiar with to make the most
of your kit. I’ll refer to them as they’re needed, but the details of those
techniques will be in the Appendix at the end of this manual.

3
1) The wooden parts:
a) Take a look at the parts layout sheets.
b) Your kit will have two sheets of plywood, one 1/16” thick, and the other
1/32” thick. (If you bought the pre-rotator, you’ll also have another
smaller 1/16” sheets)
c) You’ll find the two 1/8” ply parts in one of the smaller parts bags.
d) The layout sheets give you part numbers, so it’s probably best to only
punch out the parts you’re using in a given step so that you can still tell
what’s what.
e) When you punch out a part, cut or sand off the small tabs that were
holding it in place. These can sometimes get in the way of the parts
fitting well.
f) Assemble the wooden parts following the instructions on the layout
sheets.
2) Assembly:
a) Find the longer 3/8” Basswood stick. The narrowed end is the back,
and the curved section goes on the bottom.
b) Glue the battery tray on the stick so that the nosewheel mounting block
is pressed against the front end of the stick.
c) The main crutch goes on the stick with the landing gear mounts facing
towards the back end.
d) Leave 11/16” between the
back end of the battery tray
and the front end of the main
crutch. Then glue it in place.
e) Glue the motor mount onto
the stick, leaving 4 7/16””
between the bottom of the
motor mount, and the bottom
end of the short stick.
f) Glue the short stick into the
top of the main crutch.
g) Glue the bottom half of the
head unit to the top of the
stick. Make sure to have the
notched side facing forward.
3) Head Unit:
a) Slide the black aluminum crossbar through the arms on the top half of
the head, slip the brass rings over the ends as reinforcement, and glue
in place.
b) Press the bearings into the holes in the top and bottom of the tower.
c) Clip the larger E-Clip onto the 3mm shaft and slide it into the tower from
the bottom.
d) Place the U-Joint block between the arms of the bottom half of the joint.
Slide the larger shaft through. Align the top half with the arms facing
forward, and slide the smaller shaft through the holes. Apply the small
washers and e-clips on either side of the U-Joint.

©2007 FoamFly.com 4
e) Using the short 2mm bolts, attach the ball joints to the crossbar. Use
thread locker, you don’t want this part to fall off in flight.
f) Check the position that the nut shaped prop adapter will sit on the shaft.
You might want to file a flat in the side of the shaft so the adapter
cannot slip off accidentally in flight. Press the adapter onto the shaft,
and tighten the set screws. Again, use thread locker.
4) Blades:
a) Cut a short length of plastic tubing the height of each blade. Slide the
tubing into the hole in the blade, and glue in place.
b) Using one of the longer 2mm bolts as an alignment pin, push the bolt
through the tubing, and then glue the blade topper (P5023) onto the top
of the blade using the bolt to keep the hold aligned. Do not glue the bolt
in place.
c) Again using the bolt to keep the holes aligned, glue one of the blade
bottoms (P5025) onto the bottom of the blades. Keep the bottom
straight so that the edges are parallel to the length of the blades.
d) Glue a wedge (P5022) in place on the bottom. The wedge will line up
with the bottom blade support, and should be on the trailing edge of the
bottom support so that the blade will pitch down in flight.
e) Glue the second bottom blade support (P5025) in place over the bottom
of the previous one. Use the bolt to keep the holes lined up.
f) Do not glue the bolt into the hole ;)
g) Glue on the Blade alignment tab (P5024). Keep it lined up with the
bottom blade support, so that the forked end points toward the hole.
This will keep the blades lined up with the hub, but still allow them to
fold back in an “emergency.”
5) Blade finishing:

5
a) Seriously consider coating the last 1/4” of the trailing edge of the blades
in thin CA. It really helps to make them more durable.
b) Finish the blades with Lacquer Paint, Dope, Polyurethane, whatever you
can use to seal the grain, and make the blade a little more solid. I
prefer the Lacquer paint, it dries quickly, and makes balancing a quicker
easier task.
c) Apply several coats, sanding after each coat.
d) Apply a final coat to leave a glossy finish.
e) Add more paint to the leading or trailing edges of the blades until they
hang straight down when hung from the mounting hole.
f) Weigh each blade on the most accurate scale you can find. If you really
need to you can probably fashion a crude balance scale to at least
compare the weights of the blades to each other. I’ve pre-weighed the
blades, they should all be within a gram of each other to begin with.
g) Balance the heaviest blade on a ruler, or knife edge etc. to see where
along it’s length it balances.
h) When you add weight to the lighter blades, place it so that they balance
at the same points as well as weighing the same.
i) You can add weight by adding more paint to the ends of the lighter
blades as necessary. If you still can’t get all the blades to balance in
the same place, and they weigh the same. Add weigh to the lighter
blades till they balance, and then add extra weight right on the balance
point of the original heavier blade (now lighter) until it weighs the same
as the others.
j) Strongly consider covering the blades in Monokote, Econocote, etc.
This will make them dramatically more durable.
i) If you can cover the complete blade, root to tip, then do it. I can’t
really, so I just covered the middle.
ii) Start the covering on the bottom right near the trailing edge, with
about 1/8” overlap, and work over the edge, across the top, and
around the front. Continue on the bottom to the trailing edge, and
trim off the excess.
iii) Once all the blades are covered the same way, weigh them again.
iv) Add clear tape if necessary at their balance points until they weigh
the same again. (This isn’t as critical as it sounds, but you really
should get the blades in balance as closely as you can, without
driving yourself nuts about it)
k) Using a knife or file, just barely bevel the tops of the tips of the hub
triangle. This will make it easier for the blades to fold up in an
emergency. When the blades are on, test. They should have a little
movement, then be firm. A reasonable push should fold the blade back.
If it seems like too much effort, bevel the plastic some more.
l) Mount the blades to the center hub with the 2mm bolts, and nylon insert
nuts. The hinge lines on the hub must be angled back against the
counter-clockwise direction of spin. Flip over the hub if need be. When
aligned properly, then hinges will force the blades to pitch down when
lifted, and to pitch up when lowered. This greatly increases the
responsiveness and stability of the whole gyro.
6) Landing Gear:
a) Take the two pieces of 4mm carbon tube, and File/sand them till the
ends are smooth, and they’re the same length.

©2007 FoamFly.com 6
b) Drill out the holes in the landing gear mounts with a 5/32” or 11/64” drill
bit. (Try the 5/32” first, you want the tube to fit snug, but not tight.)
c) Glue the tubes into the landing gear mounts, pushing them all the way
in.
d) Cut two 1” sections of the 3mm tube.
e) Cut two 2.5” sections of the 1/16” wire.
f) At the halfway point, bend the wire so that when protruding from the
carbon tube, the wheels will sit at the angle you prefer. I like them to
lean inboard a tiny bit for ground stability.
g) Glue one end of the wire firmly in the section of 3mm tube. Then glue
the 3mm tube inside the 4mm tube, taking care to keep the wires
straight, so the wheels will point straight ahead.
h) If you’d like a little extra security, you can wrap the exposed end of the
4mm tube with some thread, or unwaxed dental floss, tightly, and then
soak the thread with CA.
i) Cut a small length of the plastic tubing to set the wheels away from the
carbon tube. Leave enough wire exposed to put on the wheels, and the
wheel collar.
j) Put on the wheels and wheel collars. ;)
k) Nose Wheel:
i) Position the two plastic straps, one above the other, on the
nosewheel mounting block. Drill small holes for the screws on the
straps, and screw them into place.
ii) A short length of 3mm tube will fill the gap between the wire and the
straps.
iii) Bend a section of the 1/16” wire into the nosewheel shape.

7
(1) Leaving about 1” of wire, make a Z-bend, and then continue
down making the 45 degree bend, and then aside for the
wheel, and so on, like in the pictures. (Those are 1/2” Squares)
(2) Cut a small piece of the plastic tubing
(about 1/4”) Cut or file a notch into the
bottom half, so that the notch fits over the
Z-bend in the wire, and the top half into
tan extra servo horn, as shown. Glue the
tube and servo horn in place.
(3) Use a small piece
of the plastic
tubing to center
the wheel, and
then hold it in
place with the
wheel collar.
(4) Use a second wheel collar at the top to keep the wire from
falling out. Cut the excess wire short, or slip a piece of plastic
tube on it to prevent poking out eyes, batteries.
7) Tails:
a) Cut the foam parts free from the sheet.
b) The trapezoid with the arrow is an alignment jig.
c) Crease the horizontal stabilizer along the groove cut into it’s surface.
d) Slide the vertical stabilizer into the slot.

©2007 FoamFly.com 8
e) Fit one of the vertical fins on the end of the horizontal stabilizer.
f) Holding the Jig in place, Hot Glue Weld (See Appendix) the verticals to
the horizontal. Do the center first, then the tiplets. Do NOT glue the jig
in place.
g) Repeat the process for the other side.
h) The Proper orientation will have some dihedral in the horizontal, and the
tip canted outward slightly. The flat side of the tiplets faces forward.
i) Use heavy packing tape,
or other hinge tape to
attach the rudder to the
vertical stabilizer. Trim
the tape as necessary to
fit around the horizontal
stabilizer.
j) Fit the tails flush against
the main fuselage stick,
and glue the side panels.
(P5036 & P5037) on
either side to match. Use a foam safe glue to attach the wood to the
foam. Hot Glue Weld the horizontal stabilizer to the side panels. The
false tailwheel can be on either side.
8) Electronics:
a) Install the servos using the grommets and things that come with them.
Drill small holes in the servo mount tabs to accept the screws.
b) Assemble the pushrods by screwing the threaded rod into the ball joints,
and cut them to length so that the links can go on the other end. Be
careful not to mash the threads so that the links can still screw on, and
leave enough extra that you can make some adjustments in either
direction.
c) The proper position for the head should be tilted back about 2-3
degrees relative to the stick it’s attached to.
d) The Rudder pushrod needs to attach to the rudder on the opposite side
from the nosewheel, so that they will both turn in the correct direction.
i) Make a z-bend in one piece of .032” wire, and attach to the servo
arm. The other end goes to the nosewheel arm, using one of the
small adjustable connectors.
ii) Trim off the excess wire.
iii) Make a z-bend in the other piece of .032” wire, and attach it to the
servo arm using one of the small adjustable connectors.

9
iv) Run the wire straight back to see where the rudder control horn
needs to be. Once you’ve got a place picked out, make a slit with a
knife, insert the plastic control horn, and Hot Glue Weld it into
place.
(1) Make sure that the hole in the control horn is lined up over the
hinge line for even control throws.
(2) Slip the Z-bend into the control horn, and then run it back
through the connector.
e) The servo wires can be neatly
stowed by tucking them
through the center crutch.
f) Attach the speed control to
the opposite side of the main
crutch from the rudder.
g) Attach the receiver wherever
it fits conveniently.
h) Remove the base from the
motor by loosening the set
screw.
i) Drill 4 pilot holes that match the motor
base.
ii) Install the base using the 4 woodscrews.
iii) Re-attach the motor to the base, and
tighten the set screw.
iv) Use the supplied prop adapter, and the
appropriate sized spacer ring to attach the pro to the motor. The
numbers and writing on the
prop should face forward.
9) Finishing Up:
a) Set your trims so that the rudder
and nosewheel are straight ahead.
b) You’ll need V-tail, Delta, Elevon,
whatever mixing for the two servo
head. If your radio doesn’t have it, a
small on board mixer is lightweight
and inexpensive. You want the
servos to work together, so that:
i) Up elevator tilts the head back.
ii) Down elevator tilts the head
forward.
iii) Right Aileron tilts the head right.
iv) Left Aileron tilts the head left.
c) Set up the head so that it is tilted
back from the mast by about 3
degrees.
d) Position the battery so that (when
held from the pins on the u-joint) the
gyro hangs nose down about 10
degrees. The mast will be hanging
back by about 2-3 degrees. The

©2007 FoamFly.com 10
head should be almost level when the Gyro is balanced right.
e) Velcro is recommended to keep the battery in place. A Velcro strap can
easily be put through the holes in the battery tray for extra security.
f) Put the blades and hub onto the adapter. Use the plastic washers. One
washer, the hub, then the second washer. Tighten down the nut
securely.
g) Adjust your control throws:
i) Maximum forward should bring the head level with the horizontal
stabilizer, but not more forward than that.
ii) You only need about 15-25 degrees side to side tilt in either
direction. You can adjust to taste after a few flights.
iii) Rear tilt should be about as far back as can without the blades
hitting the tails, or the ground (when the Gyro is tilted back on the
false tailwheel) The hub flexes, so make sure to leave an inch or
so safe zone.
10) Flying – General Tips:
a) If you’ve never flown a Gyro before it’s kind of hard to describe. It’s kind
of like flying a throttle rudder plane. But it also has Ailerons, and you
use a little up elevator in turns.
b) You will need to be able to fly a 4-channel plane or helicopter. You
need to be able to work Ailerons, Elevator, Throttle, and Rudder all at
the same time.
c) Basically, on the straight and level, you climb/descend with throttle, not
elevator.
d) In turns, you bank with Ailerons, hold the turn with Rudder, straighten
the Ailerons, and increase throttle, pull a little up elevator.
e) You might need to hold opposite aileron to keep the bank angle that you
want.
f) When the turn is complete, level the gyro, let off the rudder, decrease
the throttle, let off the up elevator. The gyro should slow down and
resume level flight.
g) Since you climb and descend with throttle, you can use elevator trim to
set level flight a little faster or slower. A few clicks down elevator to fly
faster, and a few up to fly slower. Then proceed to fly on throttle as
necessary.
11) Flying –First Flights: Since you are an experienced airplane flyer, you’re
ready for everything, right? What you need to know is how a Gyro handles
differently than a plane…
a) Takeoff:
i) Find a smooth area to take off from. The smoother the better, but
with all those spinning blades, Pavement scares me. Short grass,
or dirt is probably best. Golf course, Baseball diamond, well cared
for club field, etc.
ii) Hope for a little wind. I know this is the opposite of planes, but wind
is going to make takeoffs and landings easier. Look for 5-10mph
winds. 10 might be a bit high for a first flight, but it’s okay if it’s
steady.
iii) Point the Gyro directly into the wind. Give the blades a twirl, or
“wind them up” with one finger etc.

11
iv) Hold full up elevator, the blades will spin up more easily. If there’s
enough wind they might spin up all the way. Listen for the
distinctive “swish swish swish” sound.
v) When the Blades have spun up as much as they’re going to by
wind alone, let off half the up elevator, and go full throttle.
vi) When the gyro reaches full speed, about 5-10ft. (The more wind,
the less distance) Let the elevator back to neutral. Then just hang
on and wait for it to lift off. Once you break ground, you can reduce
the throttle a little bit, and begin a flight.
vii) Don’t let the gyro take off prematurely. If you have too much up
elevator or up trim, it might try to take off before the blades are up
to speed, then it will just roll over on you. You need full rotor RPM,
or abort the takeoff.
b) Takeoff with Pre-Rotator:
i) This is a little simpler, especially if you don’t have a good runway,
or there’s no wind.
ii) Bring up the Pre-Rotator throttle slowly, over about 5 seconds. You
should only need about 75-80% throttle to reach flight RPM.
iii) Turn off the Pre-Rotator, and Hit full throttle directly into the wind.
Liftoff will occur in a very short distance.
iv) Proceed normally.
c) Landing:
i) Not as hard as it seems.
ii) You approach the landing pretty much the same as with a normal
plane, but it will look different. I tried to make my first Gyro
approach with far too much ground speed, and flipped it over.
iii) On a normal landing, you’ll point into the wind, reduce throttle, hold
a little up elevator, and just before touchdown flare with more up
elevator.
(1) What that looks like on a plane: Plane begins descending,
reduce speed slightly, bring nose up just prior to touchdown,
roll out.
(2) On a Gyro: Gyro nearly stops in place, descends almost
vertically (depending on wind). During Flare, almost all forward
speed goes, Gyro settles the last few inches slowly and softly.
iv) The mistake is to come in with too much power, at normal flight
speeds, because that’s what you’re used to feeling. You wouldn’t
land a plane at high throttle settings.
v) Because the Gyro swings under it’s blades like a pendulum, you
might want to add throttle as the end of the flare to bring the
nosewheel up prior to touchdown. This is something you would
only do at the last second.
vi) On windy days: After landing, apply down elevator so that the wind
doesn’t tip you over. As you taxi, try to keep the blades tilted
toward the wind a little.
That’s it!
Now, double check everything. Make sure all the nuts and set screws are tight,
and check your control directions and throws for a third and fourth time.. ;)

©2007 FoamFly.com 12
The blades can be folded two on one side, one on the other and they’ll notch
into place, making transport easier. I usually remove the blade hub with the
blades on it for transport.
Have Fun!

13
Appendix:
1) Pre-Rotator Assembly:
a) Assemble the Pre-Rotator. (Silly question)
b) Follow the diagram on the Parts Layout Page.
c) Drill out the center of the plastic gear with a 9/32” drill.
d) Remove the Prop Adapter (If it was already on there.) Slip the Pre-
Rotator over the top tower until it sits flush against the arm doublers.
e) CA Glue the Bearing into the gear:
f) Make sure the bearing has the writing facing up.
g) Press the gear and bearing against a flat surface while gluing to make
sure they are straight relative to each other.
h) Don’t glue the gear to the table.
i) File off the small end of the gearbox until it fits into the hole in the Pre-
Rotator mount with the gearbox flush against the back end of the tower.
j) Cut off the excess shaft from the gearbox.
k) Fit the gearbox into the mount.
l) Slide the gear/bearing combo over the shaft, with the writing on the
bearing facing down. Double check that the shaft spins freely counter
clockwise, and the gear drives the shaft counter clockwise. If not, flip it.
m) Make any small adjustments necessary for the gears to mesh cleanly.
A good gear mesh is not a tight fit. There’s a little wiggle room, but no
chance of the teeth slipping.
n) When it looks good, screw or glue the gearbox to the mount. Glue the
mount to the tower.
2) Pre-Rotator Setup:
a) The pre-rotator needs a brushed speed controller. You’ll want to solder
the brushed controller to the same plug as the main motor controller.
Any Y-connectors can introduce too much resistance, and rob you of
power.
b) The easiest way to set up the pre-rotator is to put it on an additional
variable (that is, not just on/off) channel, like flaps. This will allow you to
bring up the throttle gradually, and cut it off quickly.
c) The next easiest is to use a programmable radio. Especially one that
lets you program a switch flip for slow response (like a more scale
landing gear effect) About 5 seconds from 0 to full is enough. The
Multiplex radios have this feature. Some others do too.
d) In the same vein, an add-on slower will let you use an switch on your
transmitter.

©2007 FoamFly.com 14
i) I used this: http://www.firmtronics.com/rc-products/digislower.php
ii) This one is simpler. It’s not programmable, but easier to setup:
http://www.dionysusdesign.com/product_info.php?products_id=164
it’s called Servo Rate Reducer (Extra Slow), only $10
e) Slightly less easy, is to set up your transmitter as a collective pitch
helicopter. You need to program both regular, and idle up modes. Set
regular modes curves to: Throttle 0-100%, Pitch 0-0%, and idle up
mode to: Throttle 0-0%, Pitch 0-100%. Plug the pre-rotator motor into
the “pitch” servo channel. This results in the throttle stick controlling the
main motor in regular mode, and the pre-rotator motor in idle up mode.
You can then use the throttle stick to gradually bring up the pre-rotator
throttle, then flip back to regular mode for flight.
i) If you do this, you’ll probably have to use programmed mixes to re-
create the V-Tail/Elevon effect for proper mixing of elevator and
ailerons. If you can do that this might be the most desirable setup
for you.
3) The Techniques: You’ll probably want to practice these on a piece of the
scrap foam.
1) Gluing:
a) Hot Glue Welding:
Although the hot glue gun can be used to attach flat sections, it
dries too quickly to give you much time. The glue gun works best when
the parts are already assembled, and you simply need to make the fit
permanent.
Rather than continually pulling back the gun, leaving a glob of glue
behind, move the gun forward, keeping just enough glue flowing that the
tip slides easily, and leaves a seam of glue pressed deep into the corner
of the joint. This takes a little practice, but leaves an unobtrusive glue
joint that is incredibly strong. Quick and easy too!
Other FoamFly Toy manuals
Popular Toy manuals by other brands

LEGO
LEGO 60022 CiTY Building instructions

Black Horse Model
Black Horse Model BH169 instruction manual

Extreme Flight
Extreme Flight VANQUISH MKII instruction manual
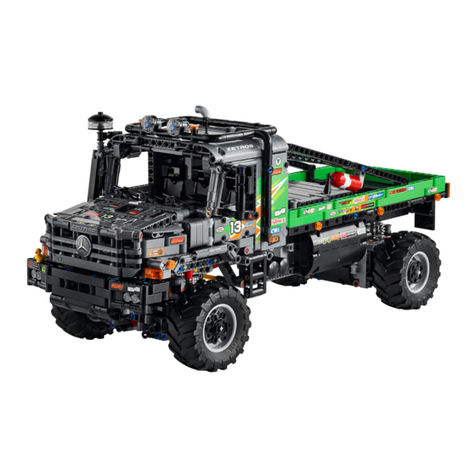
GAME OF BRICKS
GAME OF BRICKS 42129 instruction manual

TP active fun
TP active fun Muddy Madness Kitchen TP612 manual
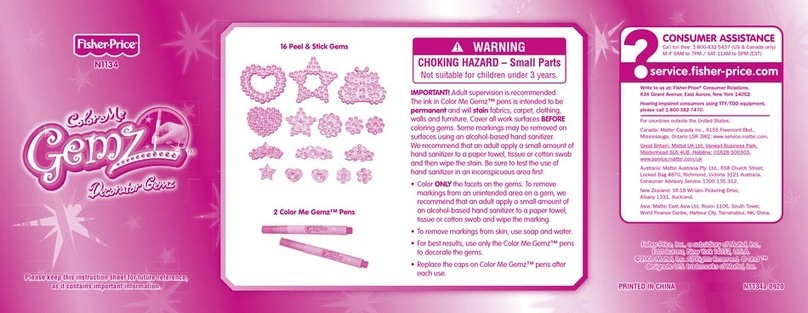
Fisher-Price
Fisher-Price N1134 quick start guide