Gantner Q Series User manual

Manual
Q.brixx
Vers. No. 1.0

Vers. No. 1.0
2Released: 2/12/2011
© 2011 Gantner Instruments Test & Measurement GmbH
Operating instructions, manuals and software are protected by
copyright. Copying, duplicating, translating, conversion into any
electronic medium or into machine readable form, completely or
partially, is only permissible with the expressed consent of
Gantner Instruments Test & Measurement GmbH. An exception
is the making of a copy of software for one's own use for backup
purposes, where this is technically possible and recommended by
us. Infringements will be pursued in law and will be subject to
compensation claims.
All trademarks and brand names used in this document only indi-
cate the respective product or the proprietor of the trademark or
brand name. The naming of products which are not from Gantner
Instruments Test & Measurement GmbH is made exclusively for
informative purposes. Gantner Instruments Test & Measurement
GmbH makes no claims on trademarks or brand names other
than its own.

Q.series
Gantner Instruments Test & Measurement GmbH 1
Table of Contents
Table of Contents
1Safety Information .................................................5
1.1 Intended use ...........................................................................5
1.2 Checking for damage in transit...............................................5
1.3 Personnel.................................................................................5
1.4 Special risks ............................................................................6
1.5 Siting locations .......................................................................6
1.6 Modifications...........................................................................6
1.7 Servicing and cleaning............................................................7
1.8 Disposal...................................................................................7
1.9 General hazards due to non-observance of the safety
information..............................................................................7
2Labels and warning information............................8
2.1 Warning information ...............................................................8
2.2 Labels on the modules ............................................................8
2.3 Labels in this manual ..............................................................9
3Introduction .........................................................11
3.1 The documentation in the Q.brixx family..............................12
3.2 About this manual .................................................................12
3.3 System description................................................................13
4Connection ...........................................................15
4.1 Connecting the power supply ...............................................15
4.2 Connecting interfaces ...........................................................16
4.2.1 Connecting Q.gate via Ethernet to a PC/PLC ........................16
4.2.2 Using the RS-232 interface of Q.gate....................................17
4.3 Synchronization of several systems ......................................19
4.3.1 Connection of a radio receiver for time signals ....................21
4.3.2 Connection of a GPS receiver................................................22
4.4 Module flashing frequency....................................................22
4.4.1 SOS........................................................................................22
4.4.2 Firmware download...............................................................22
4.4.3 FPGA download .....................................................................23
4.4.4 Problems during data transmission.......................................23
4.4.5 LED displays in normal operation .........................................23
4.5 The modules and their connection options ...........................24

Vers. No. 1.0
2Released: 2/12/2011
Table of Contents
4.6 Q.brixx A101: Connecting sensors and I/O...........................26
4.6.1 Voltage.................................................................................. 26
4.6.2 Current.................................................................................. 27
4.6.3 Potentiometer ....................................................................... 27
4.6.4 Resistance, Pt100, Pt1000 .................................................... 27
4.6.5 Thermocouple ....................................................................... 28
4.6.6 Full and half-bridge transducers........................................... 28
4.6.7 Strain-gauge quarter bridges ............................................... 29
4.6.8 IEPE/ICP®sensor ................................................................. 29
4.6.9 Digital input and output........................................................ 30
4.7 Q.brixx A102: Connecting sensors and I/O...........................31
4.7.1 Voltage.................................................................................. 31
4.7.2 Current.................................................................................. 32
4.7.3 Full and half-bridge transducers........................................... 32
4.7.4 Strain-gauge quarter bridges ............................................... 33
4.7.5 IEPE/ICP®sensor ................................................................. 33
4.7.6 Analog output........................................................................ 33
4.7.7 Digital input and output........................................................ 34
4.8 Q.brixx A104: Connecting sensors........................................35
4.8.1 Voltage.................................................................................. 36
4.8.2 Thermocouple ....................................................................... 36
4.9 Q.brixx A106: Connecting sensors and I/O...........................37
4.9.1 Full and half-bridge transducers .......................................... 37
4.9.2 Strain-gauge quarter bridges ............................................... 38
4.9.3 Inductive full and half bridges .............................................. 38
4.9.4 LVDT, RVDT........................................................................... 39
4.9.5 Analog output........................................................................ 39
4.9.6 Digital input and output........................................................ 40
4.10 Q.brixx A107: Connecting sensors........................................41
4.10.1 Voltage .................................................................................. 42
4.10.2 Current.................................................................................. 43
4.10.3 Potentiometer ....................................................................... 43
4.10.4 Resistance, Pt100, Pt1000 .................................................... 43
4.10.5 Thermocouple (only with terminal version).......................... 44
4.10.6 Full-bridge transducer .......................................................... 44
4.10.7 Strain-gauge half and quarter bridges ................................. 45
4.11 Q.brixx A108: Connecting sensors and I/O...........................47
4.11.1 Voltage.................................................................................. 48
4.11.2 Current.................................................................................. 48
4.11.3 Digital input and output........................................................ 48
4.12 Q.brixx A109: Connecting I/O and outputs ...........................49
4.12.1 Digital input and output, Plug 1............................................ 49
4.12.2 Analog output, Plug 2 ........................................................... 50

Q.series
Gantner Instruments Test & Measurement GmbH 3
Table of Contents
4.13 Q.brixx A123: Connecting sensors........................................51
4.13.1 Voltage...................................................................................52
4.13.2 Current ..................................................................................52
4.14 Q.brixx A124: Connecting sensors........................................53
4.14.1 Voltage...................................................................................54
4.14.2 Thermocouple........................................................................54
4.15 Q.brixx A128: Connecting sensors........................................55
4.15.1 Voltage...................................................................................56
4.16 Q.brixx D101: Connecting I/O...............................................57
4.16.1 Digital input and output ........................................................57
4.17 Q.brixx S104: Supply Module ...............................................60
4.18 Replacing a module...............................................................61
4.19 Replacing/changing the module type....................................62
5Configuration .......................................................65
5.1 Installing the test.commander ..............................................66
5.2 Using test.commander ..........................................................67
5.2.1 Linking test.commander via Ethernet (TCP/IP).....................67
5.2.2 test.commander and the serial (service) interface................68
5.2.3 Creating a project for configuration......................................69
5.3 Setting sensor parameters....................................................71
5.4 Specifying digital input/outputs............................................74
5.5 Defining analog outputs........................................................76
5.6 Defining computations ..........................................................78
5.7 Specifying the alarm monitoring...........................................79
5.8 Q.gate settings ......................................................................80
5.8.1 Slave interface.......................................................................81
5.8.2 Host interface ........................................................................81
5.8.3 Settings..................................................................................82
5.8.4 System variable .....................................................................84
5.8.5 Virtual variable ......................................................................85
5.9 Online tools ...........................................................................88
5.9.1 Read data buffer (with measurements) .................................88
5.9.2 Displaying measurements .....................................................88
5.9.3 Reading module information .................................................89
5.9.4 Reading status information ...................................................90
5.10 Firmware update...................................................................91
5.10.1 Firmware update for a Test Controller..................................91
5.10.2 Firmware update for modules ...............................................92

Vers. No. 1.0
4Released: 2/12/2011
Table of Contents
6Functional Procedures .........................................93
6.1 Ethernet on the PC ...............................................................93
6.1.1 Finding the IP address and subnet mask of the PC .............. 93
6.1.2 Setting the IP address on the PC .......................................... 94
6.1.3 Allowing access to network devices (firewall) ...................... 96
6.2 Connecting sensors with sensing leads ................................98
6.3 Sensor scaling.......................................................................99
6.3.1 Scaling of stress signals and strain-gauge bridges............... 99
6.3.2 Scaling of strain gauges...................................................... 100
6.4 Current measurement with an external shunt....................101
6.5 Measuring with thermocouples ..........................................102

Q.series
Gantner Instruments Test & Measurement GmbH 5
1Safety Information
1Safety Information
Before starting installation, setting up, operation and before
maintenance work is carried out, it is essential to read and follow
the appropriate warning and safety information given in this
manual.
Installation, setting up, operation and maintenance of the mod-
ules or devices must take place as intended, i.e. under the condi-
tions of use laid down in this manual and in the technical data for
the relevant module or device.
1.1 Intended use
The products in the Q.series range are intended for use in indus-
trial and experimental test engineering and for monitoring
assembly and production processes. Transducers (sensors) for
the acquisition of physical quantities such as voltage, current,
resistance, temperature, force, displacement, torque, mass,
strain and pressure can be connected. The modules are used
exclusively for these kinds of measurement and control applica-
tions. Any application which goes beyond this scope does not fall
within the intended use of the modules.
To ensure safe operation the modules and devices must only be
operated according to the details given in the manuals and tech-
nical data sheets. In addition, the required legal and safety regu-
lations covering the respective application must be followed. This
applies in particular to the modules A123, A124 and A128 with
which input voltages of up to 1200VDC can be used.
1.2 Checking for damage in transit
On receipt of the goods visually check that the packaging and the
module or device together with the data medium are intact. Also
check the shipment for completeness (accessory parts, documen-
tation, auxiliary aids, etc.). If the packaging has been damaged in
transit or if you suspect that the product is damaged or may mal-
function, the product must not be put into operation. In this case
contact your customer consultant or Gantner Instruments Test &
Measurement GmbH.
1.3 Personnel
The installation, operation and maintenance of the modules or
devices must only be carried out by competent persons. Compe-
tent persons are those who through their professional education
have sufficient knowledge in the required field and are familiar

Vers. No. 1.0
6Released: 2/12/2011
1Safety Information
with the relevant national occupational protection regulations,
accident prevention regulations, guidelines and accepted engi-
neering rules. They must be able to reliably assess the results of
their work and must be familiar with the contents of this manual.
Electrical connections must only be carried out by specialist per-
sonnel trained for the task.
In particular, pay attention to the following:
• the national installation and erection regulations (e.g. ÖVE,
VDE, etc.)
• generally accepted engineering rules
• the details on transport, installation, operation, servicing,
maintenance and disposal in this manual.
• the parameters, limits and the details about the operating and
ambient conditions on the name-plates and in the data sheets.
1.4 Special risks
The modules A123, A124 and A128 are specially designed for
measurements at high voltages. Consequently, on the modules a
voltage of up to 1200V may be present, which can lead to fatal or
severe injury on touching the terminal contacts or bare parts of
the connecting cables. Therefore, make sure that only qualified
personnel have access to the modules or devices and that the
voltages on modules can be switched off by a switch-disconnector
or similar device for service purposes.
1.5 Siting locations
The devices in the Q.series range are protected to IP20 against
water, dirt and small parts. If the ambient conditions require it,
the modules can be fitted in water-protected or watertight hous-
ings.
Please note the admissible ambient temperatures specified in the
technical data.
1.6 Modifications
Making modifications to the modules or devices is not permitted.
Dirt and shrouding covers may only be removed for service and
maintenance purposes.

Q.series
Gantner Instruments Test & Measurement GmbH 7
1Safety Information
1.7 Servicing and cleaning
The modules or devices do not need any servicing. Cleaning may
only take place in the voltage-free state. Therefore follow the
points below:
• Before cleaning, disconnect all connectors.
• Clean the housing with a soft, slightly moistened cloth. Never
use any solvents, because these may attack the labels.
• When cleaning, make sure that no liquid enters into the
device or goes onto the terminals.
Never attempt to repair nor to again operate devices which are
defective, have developed a fault or are damaged. In this case it
is essential to contact your customer consultant or Gantner
Instruments Test & Measurement GmbH.
1.8 Disposal
Old devices which are no longer usable must be disposed of
according to national and local regulations regarding environ-
mental protection and raw-material recycling. Electronic compo-
nents must not be disposed of with the household refuse. The
packaging can be recycled and should therefore be passed into
the recycling system. However, we recommend that the packag-
ing is kept until the end of the warranty period so that you can
pack faulty devices or modules properly.
1.9 General hazards due to non-observance of the
safety information
The modules or devices conform to the state of the art and are
operationally safe. However residual risks may arise when they
are used and operated improperly by untrained personnel.
Any person commissioned with the task of siting, operating, ser-
vicing or repairing a module or device in the Q.series must have
read and understood the operating manual and in particular the
information relating to safety.

Vers. No. 1.0
8Released: 2/12/2011
2Labels and warning information
2Labels and warning infor-
mation
2.1 Warning information
To prevent personal injury and damage to property it is essential
that you follow the warning and safety information given in this
operating manual.
Indicates a directly threatening hazard. If it is not pre-
vented, the consequence will be fatal or serious injuries.
Indicates a possibly hazardous situation. If it is not prevented, the
consequence may be fatal or serious injuries.
Indicates a possibly hazardous situation. If it is not prevented, the
consequence may be injuries of slight or medium severity.
Indicates a situation in which the consequence may be property
damage if the information is not followed.
2.2 Labels on the modules
Symbol:
Meaning: This symbol is the CE marking. This shows that we
guarantee that our product meets the requirements of the rele-
vant EC directives.
Symbol: CAT II
Meaning: Modules with this symbol are intended for the connec-
tion of high voltage. The maximum admissible voltage is also
given.

Q.series
Gantner Instruments Test & Measurement GmbH 9
2Labels and warning information
2.3 Labels in this manual
To simplify reading this manual we use the following labels and
notation:
IMPORTANT
Paragraphs with this symbol give important information about
the product or about using the product.
Tip
Contains application hints and other particularly useful informa-
tion.
italics signifies highlighted text
interface signifies entries and entry fields in program
user interfaces
Options signifies menu items in the program user
interfaces
>signifies a sequence of menu items, e.g. in
Options > Settings
➡indicates special features or restrictions

Vers. No. 1.0
10 Released: 2/12/2011
2Labels and warning information

Q.series
Gantner Instruments Test & Measurement GmbH 11
3Introduction
3Introduction
Dear Customer,
thank you purchasing a product in the Q.series from Gantner
Instruments Test & Measurement GmbH. We are sure that you
have obtained an excellent product which will enable you to make
fast and reliable measurements with low measurement uncertain-
ties.
The manual is included in the items supplied. Keep the manual
safe or download the latest version from our web site. To prevent
personal injury and damage to property it is essential that you fol-
low the warning and safety information given in this manual
(Chapter 1, Page 5). Please contact us if you do not know how to
proceed even after reading the manual thoroughly.
If you find faults on the product or errors in the accompanying
documentation or if you have suggestions for improvement,
please contact your customer consultant or Gantner Instruments
Test & Measurement GmbH directly. We would be glad to receive
your comments and ideas.
Austria Gantner Instruments Test & Measurement GmbH
Silvrettastr. 11-13
6780 Schruns/Austria
Tel.: +43 (0) 5556 77463-0
Fax: +43 (0) 5556 77463-300
e-mail: [email protected]
Web: www.gantner-instruments.com
Germany Gantner Instruments Test & Measurement GmbH
Heidelberger Landstr. 74
64297 Darmstadt
Tel.: +49 (0) 6151 95136-0
Fax: +49 (0) 6151 95136-26
e-mail: [email protected]
Web: www.gantner-instruments.com

Vers. No. 1.0
12 Released: 2/12/2011
3Introduction
3.1 The documentation in the Q.brixx family
The documentation for the Q.brixx consists of this manual about
the Q.brixx modules A101, A102, A104, A106, A107, A108, A109,
A123, A124, A128, D101, D104, D105 and S104 as well as the
Q.gate Test Controller. Detailed descriptions on special settings
for Q.gate can be found in other Gantner Instruments Test &
Measurement GmbH documentation on the Gantner CD or on our
home page www.gantner-instruments.com.
You will find this manual also as a PDF file on our home page and
on the Gantner CD enclosed with your system or which you can
order free of charge from Gantner Instruments Test & Measure-
ment GmbH.
3.2 About this manual
This manual describes the installation, initial operation and the
configuration of the modules Q.brixx A101, A102, A104, A106,
A107, A108, A109, A123, A124, A128, D101, D104, D105 and
S104 with the Q.gate Test Controller using the program test.com-
mander. The modules are differentiated through the number of
their analog and/or digital inputs and outputs as well as by the
maximum possible measuring rate.
The manual is divided into several chapters:
• Safety information in Chapter 1, from Page 5 onwards.
• A description of the labels and symbols used on the modules
and in this documentation can be found in Chapter 2 from
Page 8 onwards.
• You will find a description of the system and the main combi-
nation and expansion options in the next section.
• The description of the connection variants and the pin assign-
ments on the inputs and outputs can be found in Chapter 4,
Connection, from Page 15 onwards.
• A comprehensive introduction to the configuration of the
modules using the program test.commander is given in
Chapter 5, Configuration, from Page 65 onwards.
• Comprehensive explanation of the module measurement tech-
nology and background information about working proce-
dures can be found in Chapter 6, Functional Procedures, from
Page 93 onwards.

Q.series
Gantner Instruments Test & Measurement GmbH 13
3Introduction
3.3 System description
The modules in the Q.brixx series have been developed for indus-
trial and experimental measurement and test engineering, in par-
ticular for multi-channel measurements of electrical, mechanical
and thermal signals on engine and component test-rigs as well as
for monitoring processes and long-term supervision. The modules
A123, A124 and A128 are specially designed for measurements at
high voltages.
Voltages of up to 1200V may be present on the connections
of the modules A123, A124 and A128.
Before connecting or disconnecting cables on these mod-
ules check that the cables to be connected or disconnected
are no longer live.
The individual modules can be combined to form one system as
required. You can connect up 16 modules to the Q.gate Test Con-
troller and then address them from a PC or PLC via a single inter-
face.
On all modules the power supply, bus interface and the inputs
and outputs are electrically isolated from one another.
Operating the modules via Q.gate
The Q.gate Test Controller can be operated to the far left or far
right next to the Q.brixx modules (first or last slot). It cannot how-
ever be installed between the modules.
Fig. 3-1 Q.gate with 8 modules.
Depending on the operating mode of the modules, transmission
rates of 1kHz with up to 128 variables (transferred values with
four byte resolution, real variables) are possible over Ethernet.
max. 16 modules, here: 8 modulesQ.gate

Vers. No. 1.0
14 Released: 2/12/2011
3Introduction
UART data throughput at 24MBd
Measuring rate 1kHz
Measuring rate 10kHz
Measuring rate 100kHz
200 real variables
20 real variables
2 real variables
Ethernet data throughput (transmission rate with block transfer) 128 real variables (1kHz)
16 real variables (10kHz)
Ethernet data throughput (transmission rate with online transfer) 64 real variables (300Hz)
Interfaces Ethernet, USB, RS-232,
2UARTs
Max. number of slaves (Q.brixx) 16

Q.series
Gantner Instruments Test & Measurement GmbH 15
4Connection →Connecting the power supply
4Connection
This chapter contains the description of the connection variants
and pin assignments.
4.1 Connecting the power supply
For the power supply an unregulated direct voltage between 10
and 30volts is required, which is connected to the socket right at
the bottom in the Q.gate. Fig. 4-1 shows the pin assignment.
Each module requires a power of approx. 2W in addition to the
power supplied for the connected transducers. The power
required is almost constant over the complete voltage range.
Fig. 4-1 Assignment for power supply socket contacts.
IMPORTANT
When the modules are switched on, there is an increase current
demand until the modules are operating in a stable manner: In
the start-up phase up to 700mA (10ms) per module is needed
depending on the supply voltage. Thereafter, you should expect
approx. 500mA per module for a 10V supply voltage, with a 30V
supply voltage approx. 170mA. You should therefore either use
power supplies which can deliver the required peak power when
the voltage is switched on or – with many modules – switch the
modules on in several groups.
The modules have an internal self-healing (reversible) fuse for
protection against overvoltages, overcurrents and incorrect
polarity.
➡Do not use cable which is too thin for the connection so that the
required power can be transferred to the module without signifi-
cant losses.
Power supply +
(upper pin)
Power supply –
(lower pin)

Vers. No. 1.0
16 Released: 2/12/2011
4Connection →Connecting interfaces
4.2 Connecting interfaces
For communication (configuration and data interchange) with the
modules you must connect the Q.gate Test Controller via Ether-
net (Section 4.2.1, Page 16) to a PC or PLC. The configuration is
carried out exclusively via the Ethernet interface.
We recommend the use of cables to Cat-5e or better.
For setting an IP address or for logging purposes you can also
use the RS-232 interface of the Q.gate Test Controller
(Section 4.2.2, Page 17).
4.2.1 Connecting Q.gate via Ethernet to a PC/PLC
The Q.gate Test Controller uses DHCP (Dynamic Host Configura-
tion Protocol) to obtain an address from a server in the network.
In this case you only have to connect the Test Controller to an
Ethernet switch. An IP address is assigned automatically.
Tip
We recommend the use of industrial Ethernet switches. Q.gate
uses autonegotiation and operates, if available, with 100Mbit/s
and full duplex for the transmission.
Connection without a server If you are not connected to a network or there is no server in the
network, you should set your PC to DHCP (Control Panel > Net-
work) and connect to the Q.gate Test Controller. Windows XP or
Windows Vista then negotiates a suitable address so that you can
communicate with the module and can set a fixed Ethernet
address. Consequently, set your PC also to a fixed IP address
from the same address range, because otherwise no link can be
established to the module.
Tip
Refer also to Section 6.1, Ethernet on the PC, on Page 93 for the
display and setting of the PC IP address.
If the Test Controller does not receive an IP address from a
server, then it adjusts to its static IP address after a few seconds.
The factory setting of the static IP address of the Test Controller
is 192.168.1.28.
Connection in a network
with a server
In the factory setting the Test Controllers use DHCP, i.e. they
receive a valid network address from a server which is present in
the network. Connect the PC or the PLC to the same network.
Then you can establish the link immediately via test.commander
and can therefore also assign a fixed address to the Test Con-
troller. Refer also to Section 6.1 on Page 93.

Q.series
Gantner Instruments Test & Measurement GmbH 17
4Connection →Connecting interfaces
Procedure Setting an Ethernet address (IP address)
1. Make sure that the current version of the test.commander
software is installed on your PC.
You will find the current version in the download section of
our home page. If necessary, install the current version; refer
to Section 5.1 on Page 66.
2. Start the software.
3. Using the menu Utilities > Controller network terminal
call the dialog for finding Test Controllers.
4. Click on Configure IP settings.
5. Select Manually configure network settings and specify
the required IP address (IP address), the subnet mask (Sub-
net mask) and – if necessary – the gateway address (Default
gateway). If in doubt, details can be obtained from your net-
work administrator.
6. Click on Apply to accept the changes.
Example
Selected new IP address for the Test Controller: 192.168.169.85
Possible PC IP address: 192.168.169.10
Subnet masks of the PC and module: 255.255.255.0
Tip
Alternatively, you can also use the wizard for the initial operation
in the test.commander program.
Section 6.1, Ethernet on the PC on Page 93 contains further
information about the use of Ethernet addresses and subnet
masks.
4.2.2 Using the RS-232 interface of Q.gate
The RS-232 interface is used for the output of protocol informa-
tion and for setting the IP address if this is not possible else-
where.
The RS-232 interface of the Q.gate Test Controller is located
below the USB interface at the front. For the link to a PC you
require the supplied cable with the 3.5mm stereo jack plug.
Fig. 4-2 Pin assignment for RS-232 on the jack plug.
TxGND,
Ground
Rx

Vers. No. 1.0
18 Released: 2/12/2011
4Connection →Connecting interfaces
Procedure Setting an Ethernet address (IP address) via RS-232
1. Make sure that the current version of the test.commander
software is installed on your PC.
You will find the current version in the download section of
our home page. If necessary, install the current version; refer
to Section 5.1 on Page 66.
2. Start the software.
3. Using the menu Utilities > Controller serial terminal call
the dialog for finding Test Controllers.
4. Specify the required IP address (IP address), the subnet
mask (Subnet mask) and – if necessary – the gateway
address (Default gateway). If in doubt, details can be
obtained from your network administrator.
5. Click on Apply to accept the changes.
Example
Selected new IP address for the Test Controller: 192.168.169.85
Possible PC IP address: 192.168.169.10
Subnet masks of the PC and module: 255.255.255.0
Section 6.1, Ethernet on the PC on Page 93 contains further
information about the use of Ethernet addresses and subnet
masks.
4.2.2.1 Establishing connection with the test.commander setup wizard
1. Make sure that the current version of the test.commander
software is installed on your PC.
You will find the current version in the download section of
our home page. If necessary, install the current version; refer
to Section 5.1 on Page 66.
2. Start the software and select the Utilities > Module setup
assistant
Another program window opens.
3. Select Options > Communication settings.
4. Under Interface type select the RS-232 direct connection
and under ComPort the PC connection you are using.
5. Close the dialog with OK.
Further interface parameters are not needed.
6. Click on Find modules.
The program searches the specified interface for connected
modules and displays all the modules found in the program
window. If there are addressing conflicts, they are also dis-
played. Specify unique addresses for the modules; refer to
Section 5.2 on Page 67.
Other manuals for Q Series
5
This manual suits for next models
15
Table of contents
Other Gantner Control Unit manuals
Popular Control Unit manuals by other brands

Triax
Triax 692855 Configuration guide
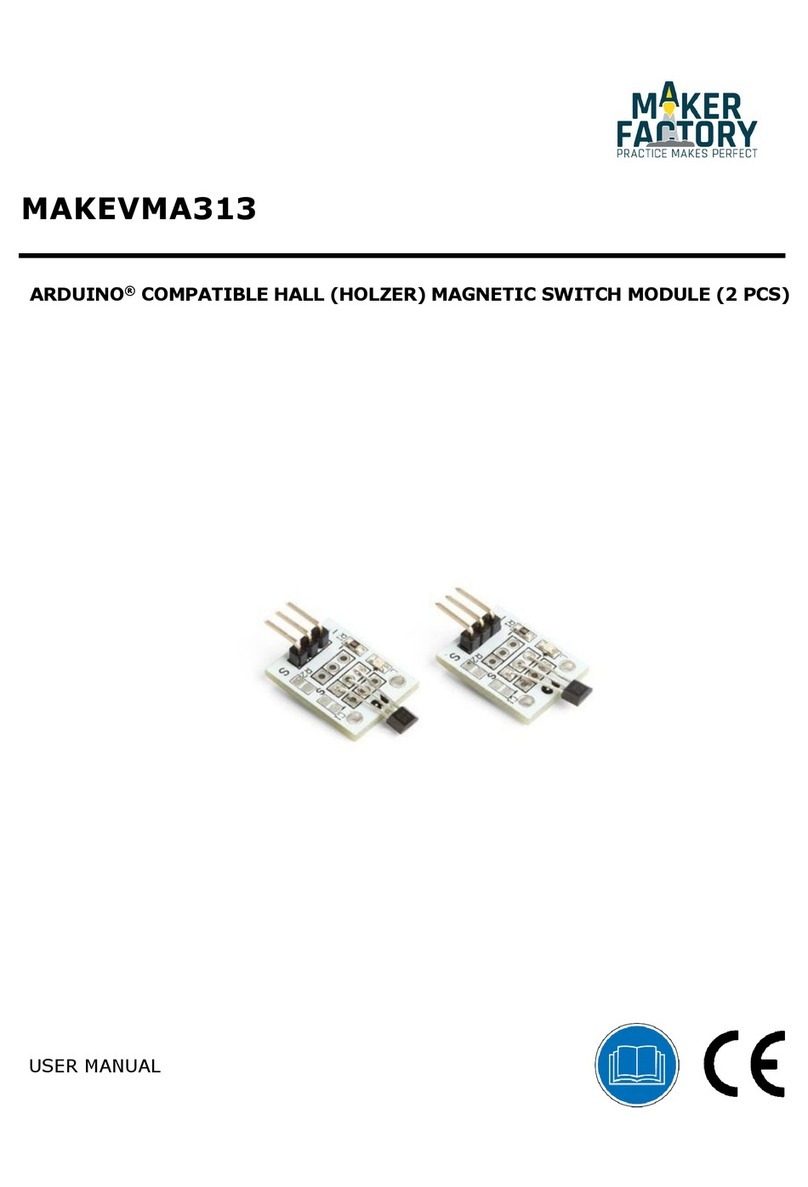
Maker Factory
Maker Factory ARDUINO MAKEVMA313 user manual
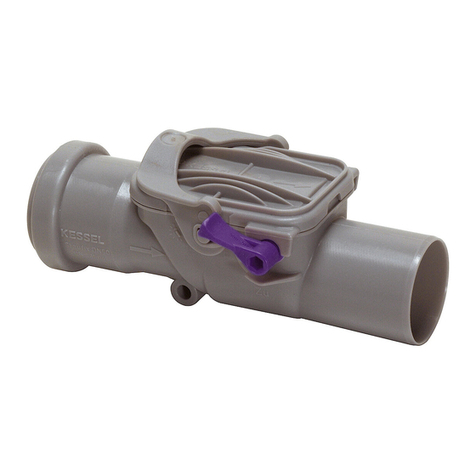
Kessel
Kessel Staufix Series Installation and operating instructions
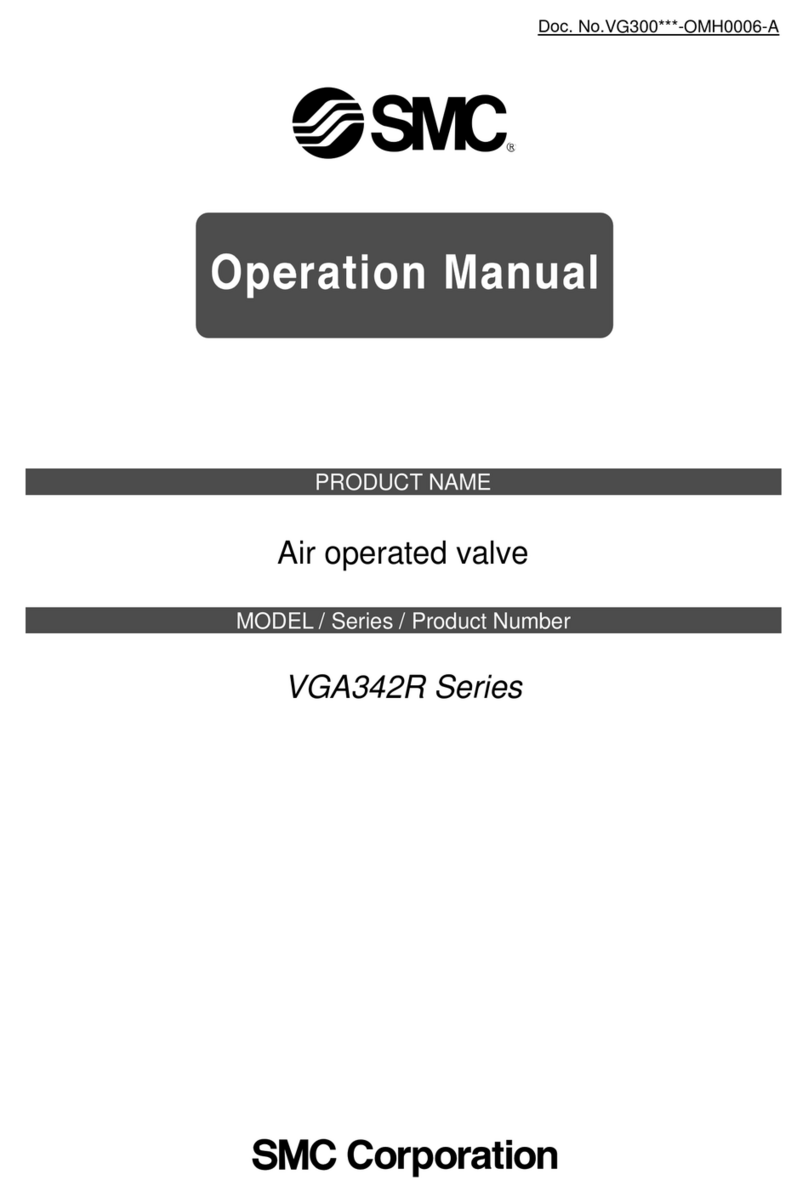
SMC Networks
SMC Networks VGA342R Series Operation manual
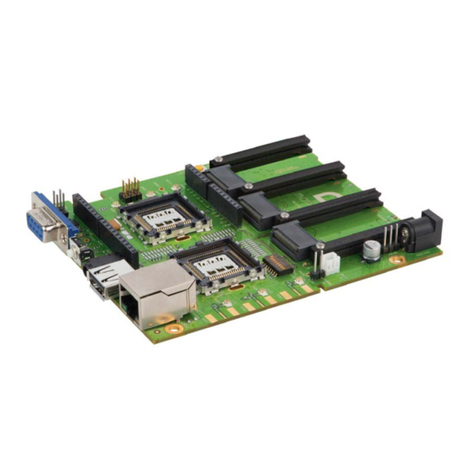
Sierra Wireless
Sierra Wireless mangOH Green DV4 user guide
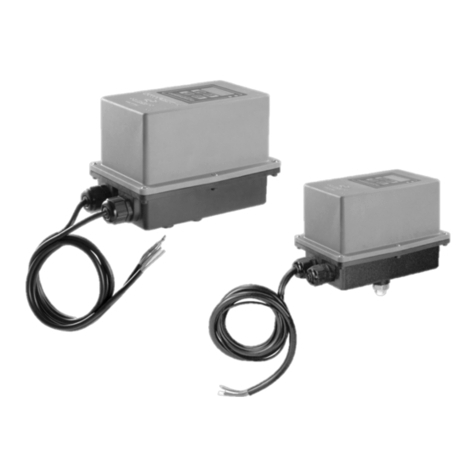
Comparato
Comparato COMPACT CRONO installation manual