GDS XDI-XDIwin/30J Instruction Manual

TECHNOLOGIES
GDS TECHNOLOGIES LTD |FUSION POINT |ASH LANE |GARFORTH |LEEDS |LS25 2GA |UK www.gds-technologies.co.uk
Technical Sheet
ref C1518B
XDI-XDIwin / 30J
PID SENSOR
Set-up procedure: 292 D6C Issue Bv5
• NEW SENSORS ARE SUPPLIED READY TO CONNECT AND GO
BUT NEED 15 MINUTES POWER STABILISATION. The following procedure is
for full set up using a PC but onsite calibration without PC/LCD requires only
sections 18, 19, 20.
Note: If a new cell is fitted then full calibration is required. PID lamp has an approximate lifetime of 6 months.
Replacement bulb and extractor tool can be purchased using part numbers 010-644 and 010-647 respectively.
PC setup
The auto zero adjust is continuous during power up inhibit period and PCB fault LED flashes to indicate this,
do not apply any gas at this time because zero adjust will try to offset the measurement.
Thereafter zero is adjusted every 60 seconds. D1 flickers orange at the zero point. This function can be toggled on/off
by using command ‘Y’ in hyperterminal. ‘Auto zero’ is only active if gas reading is below 5% of full scale.
1. Insert jumpers J20 and J6 position SO for 4-20mA source output
2. Turn sensor voltage potentiometer RV4 fully anticlockwise (minimum voltage)
3. Connect sensor to J2 terminal (W) white (P) pink (Y) yellow
4. Connect 24v + and 0V to J10, insert test link at J9 to bypass 4-20mA terminal
5. Set the sensor voltage to 5.0V measured across SV and 0V, adjust by slowly turning RV4 clockwise.
DO NOT EXCEED THE REQUIRED VOLTAGE OTHERWISE PERMANENT DAMAGE WILL OCCUR
6. Insert jumper G2 for a nominal gain value (G1 is lowest gain, G5 is highest or a combination
G1 to G5)
7. Connect a PC to J3 with a sensor programming module and a USB to RS232 converter (part no. 160510 and
part no. 160520) use hyperterminal set to 4800/1stop/8bit and initialise the sensor using (C) calibration mode,
then shift + ($) command from the keyboard. The default gas is Isobutylene 200ppm.
8. The typical hyperterminal display is (also see appendix 1)
60 C4H8 200ppm
O H L D F I
^ ^ ^
- - - - - - PPM=0 A=010 R=010 Adj=500 Pinh=0 adj=4 CG=100 CGADC = 222
PPM is the gas value
Ais the processor raw measurement
Ris the zero point of the sensor (10 ± 2)
Adj is the adjustment value of autozero circuit, it can be between 0 and 1000 but 500 is ideal.
Pinh is the number of seconds left of powerup inhibit (autozero is active during this time)
adj is the number of seconds until a 1 second autozero will occur.
CG is the calibration gas value PPM.
CGADC is the number A must reach to display the value CG as the correct PPM gas reading
9. Sensor Zero is true when D1 flashes orange and potentiometer VR2 is adjusted to ensure Adj (screen text) is
between 400 and 600. Turning VR2 clockwise will increase Adj. Note: pressing (R) or J28 short will reset sensor
and give 1 min adj time (when in clean air).
10. Press F to adjust the 4mA output by measuring the mV across TP8 and TP9. Press H or L to adjust then press
SPACE to set and exit.

11. Press T to adjust the 20mA output by measuring the mV across TP8 and TP9. Press H or L to adjust and then press
SPACE to set and exit.
12. Before using span gas, ensure that an autozero is not about to take place. This is indicated by the MPU LED
flashing at 1 Hz. The MPU LED on the PCB will flash normally at 1 Hz but when there is less than 30 seconds to an
autozero flash rate will increase to 2Hz i.e faster flash.
13. Apply a test gas to the sensor (typical - 100ppm Isobutylene) for 1 minute at a flow rate of 1 litre/min. Use the
UP and DOWN buttons on the PCB to give correct 4-20mA level. (ie. 5.6mA for 100ppm). Remove gas and wait
5 minutes. If a maximum range gas is available, apply for 1 minute and note the value of A. This can then be
entered via Hyperterminal using the M command giving better accuracy across the range. Remove gas and wait 2
minutes.
14. Connect the sensor to a Combi alarm panel and ensure that it reports in correctly.
Note: Fit the end of line (EOL) link J1 if the sensor is to be installed at the end of the sensor cable.
15. If a display board is fitted via connector J5 and U12 adjust VR1 for LCD contrast.
16. Remove J9 test link for normal operation.
17. Ensure J29 address link is removed (this is only used when changing address from a panel)
Manual calibration (without PC or LCD)
18. Zero - with no gas applied, measure between Ag and Sig (Y) and adjust VR2 to give 50mv.
With J9 test link inserted, check the 4-20mA output to be 4mA as measured at TP8 to TP9 = 4mV
19. Span - apply test gas (typical 50% of range) and use UP and DOWN buttons on the PCB to give correct 4-20mA
output. (50% gas = 12mA).
20. Remove gas and ensure the output returns to the 4mA level and then remove the J9 test link
Setup using magnets - LCD
WIN versions of the sensor have an LCD display which shows the Gas and range together with the sensor address and
a display of the number of seconds until an autozero will occur.
Also incorporated are 3 reed switches which can be activated using external magnets through the glass window of the
flameproof XDIwin enclosure. These magnets do not act instantly and have to be in close proximity to L, M and R on the
front display for a few seconds to activate a software setup function.
The right magnet allows the CAN address of the sensor to be changed. When the address menu is displayed with a
prompt to remove the magnet, and then the display shows the address and that the right magnet will decreases it whilst
the left magnet will increase it. This is then stored in internal non-volatile memory and the display will automatically
revert to normal operation.
The centre magnet is used to inhibit the sensor. As with the left and right magnet functions the display requests that you
remove the magnet and then the state of inhibit appears on the LCD.
The left magnet then puts the sensor into inhibit whilst the right magnet removes it. The amber LED on the front panel
under the LCD flashes when the sensor is inhibited. When all magnets are removed, the display will revert to normal
operation. The direction of the alarms is displayed as ^ for rising and v for falling but these can be changed using left
and right magnets together.
The left and right magnets together allow the calibration menu to be used. Removing both magnets as instructed on
the LCD presents the first part of this multi menu which is ZERO. With no gas present the display shows the PPM value
but also typically [0.02] This number between the square brackets shows how close the autozero has achieved. [0.00] is
definite zero and the PCB led D1 will be flickering orange.
A 15 second timer is displayed and is reset back each time a magnet is near. Waiting till timeout is acceptable but this
timeout can be speeded up by placing a magnet near to the centre position.
SPAN is the next part of the menu and gas should be applied to the sensor at this time (recommended - 100ppm
Isobutylene - see GDS application notes C645). A 2 minute counter is displayed before the next part of menu is
activated. The left magnet now increases the PPM reading and the right magnet reduces.

The actual sensor value can be seen on the display rising or falling respectively. The magnets are the equivalent of the
PCB UP and DOWN push buttons.
LOW ALARM is the next menu and left and right magnets increase and decrease this value.
HIGH ALARM is next followed by OVER RANGE alarm.
The direction of the alarms is displayed as ^ for rising and v for falling but these can be changed using left and right
magnets together.
Appendix 1
Hyperterminal Display OHLDFI
• OHand Lrepresent the Over Range, High and Low alarms respectively ^^v shows the direction of alarms
• Dindicates if a duplicate address is detected
• Findicates a fault
• Iindicates alarms inhibited
Pressing (R) when in normal runtime display causes a sensor reset to occur. Gas type with address and serial number
are then output to the PC together with alarms and calibration date, etc.
This also starts 1 minute autozero, which is useful when adjusting VR2 zero potentiometer.
Pressing (C) on the PC will list the available commands
(V) Allows a view of the gas log taken at one minute intervals over 48 hours
(A) To set the sensor address
(G) Select gas type Select the gas type from a list
(Z) Prompts to use the zero potentiometer
(S) Prompts to use the PCB buttons
($) Initialise the sensor
(%) Clear the log of sensor readings, (this takes a minute to perform)
(U) Alarm directions, Rising or falling
(D) Enter calibration date
(R) Enter the range of the gas x 10
(F) Set 4mA level Use H and L and space
(T) Set 20mA level Use H and L and space
(O) (H) (L) Set over, high and low alarm levels x 10
(M) Set the value of full range raw processor measurement value when maximum gas was applied
(E) Allows the editing of the 8 character user gas description
(X) Exit to normal display

TECHNOLOGIES
GDS TECHNOLOGIES LTD |FUSION POINT |ASH LANE |GARFORTH |LEEDS |LS25 2GA |UK www.gds-technologies.co.uk
This document is not contractual and the equipment specification may be modified at any time without prior notice.
Technical Sheet
ref C1518B
XDI-XDIwin / 30J
PID SENSOR
Set-up procedure: 292 D6C Issue Bv5
Figure 1
Figure 2 Figure 3
Appendix 2
The PID sensor can react to gas flow and humidity. When gas is removed from the sensor, the displayed
PPM gas value may rise and take some time to return to normal. Autozero is therefore delayed by 2 minutes
after the reading has fallen below 5% of range.
Table of contents
Other GDS Gas Detector manuals
Popular Gas Detector manuals by other brands
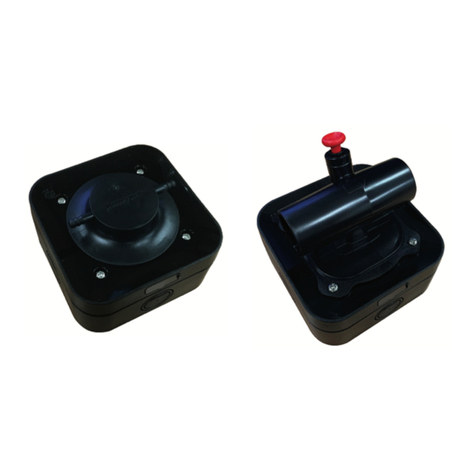
Xtralis VESDA
Xtralis VESDA Sensepoint XCL Frequently asked questions

Berner
Berner D640 instruction manual
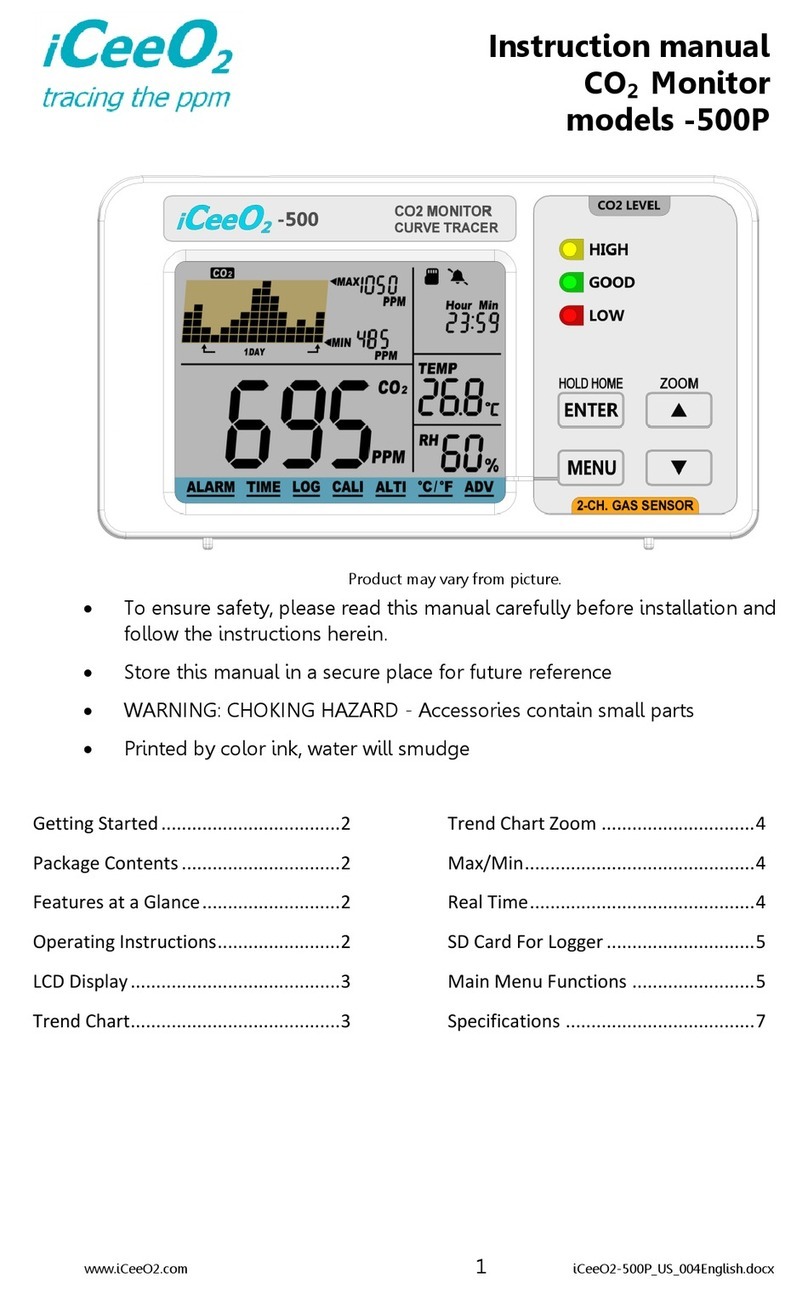
iCeeO2
iCeeO2 500P instruction manual

Bühler technologies
Bühler technologies GAS 222.35 AMEX Brief instructions
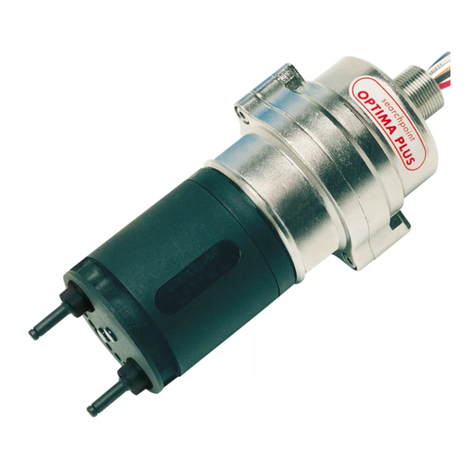
Honeywell
Honeywell Searchpoint Optima Plus Safety manual

eLICHENS
eLICHENS AVOLTA quick start guide

Tellur
Tellur TLL331291 user manual
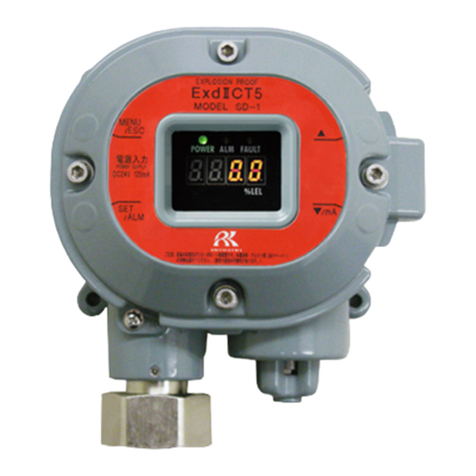
Riken Keiki
Riken Keiki SD-1D-AS operating manual

BW Technologies
BW Technologies GasAlertClip Extreme instruction sheet
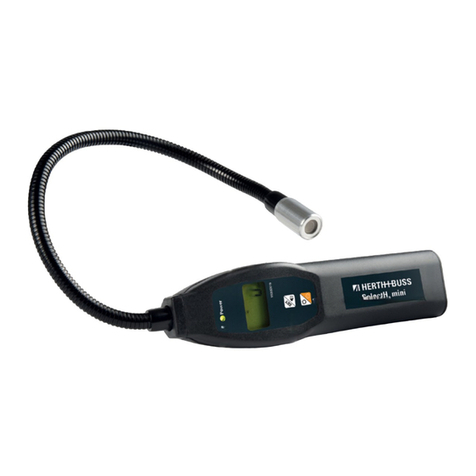
Herth+Buss
Herth+Buss ELPARTS SelectH2 mini operating instructions

Dräger
Dräger X-am 3500 Instructions for use

GASTRON
GASTRON GTD-2000Ex instruction manual