GEIGER GJ56 E07 SMI Series User manual

1
www.geiger.de EN
EN
Original-Montage- und
Betriebsanleitung
Original assembly and
operating instructions
Notice originale de montage
et d’utilisation
Instrucciones originales de
instalación y funcionamiento
Istruzioni originali di installazione
e funzionamento
DE
EN
FR
ES
IT
Venetian blind motor:
GEIGER GJ56.. E07 SMI
For Venetian blinds

2Gerhard Geiger GmbH & Co. KG | 100W1549 0623V001en
EN
EN
1. General information
Dear customer,
By purchasing a GEIGER motor you have decided on a quality product from GEIGER.
Thank you very much for your decision and the condence placed in us.
Before you put this drive into operation please observe the following safety instructions. It
serves for the prevention of danger and for the avoidance of personal injury and damage to
property.
The installation and operating instructions contain important information for the installer, the
specialist electrician and the user. Please pass on these instructions if you transfer the product.
These instructions should be kept by the user.
2. Guarantee
In the case of incorrect installation contrary to the installation and operating instructions and/
or constructional modication, the legal and contractual guarantee for property damage and
product liability lapses.
Index
1. General information ............................................................................2
2. Guarantee.............................................................................................2
3. Intended use ........................................................................................3
4. Safety instructions ..............................................................................3
5. Safety instructions for assembly.......................................................3
6. Identicationnumber..........................................................................5
7. Assembly note.....................................................................................5
8. Installation instructions......................................................................6
9. Information for the specialist electrician ..........................................8
10. Conductor assignment for SMI drives for mains voltage................9
11. SMI drives on different AC phases ..................................................10
12. For your notes …............................................................................... 11
13. Setting of the end stops ...................................................................12
14. Activate the programming mode ....................................................12
15. Programming/changing the end stops............................................13
16. Referencing on the limit stop switch...............................................13
17. Enable/disable reference cycles ......................................................14
18. Resetting to factory settings............................................................14
19. Obstacle detection and anti-freeze protection ...............................14
20. What to do if… ...................................................................................14
21. Declaration of conformity.................................................................15
22. Maintenance.......................................................................................16
23. Technical data....................................................................................16
24. Notes on waste disposal ..................................................................16

3
www.geiger.de EN
EN
3. Intended use
The motors of the model range GJ56.. E07 SMI with electronic end stop are designed exclusi-
vely for the operation of Venetian blinds.
The motors may not be used for the operation of roller grilles, garage doors, furniture and lifting
tools.
GJ 56 xx x
Design options
Torque in Nm
For head rails at least 56 mm
GEIGER Venetian blinds motor
4. Safety instructions
I ATTENTION: Important safety instructions. For personal safety,
it is important to follow these instructions. Please keep these
instructions for future reference.
fDo not allow children to play with stationary controls. Keep remote controls away
from children.
fThe installation is to be checked regularly for defective balance, signs of wear or
damaged cables and springs, if relevant.
fDo observe the moving sun protection system and keep persons away until it has
closed completely.
fWhen operating the manual release with the sun protection system open, please be
cautious as it can fall down quickly if springs or tapes wear off or are broken.
fDo not operate the device if operations such as, for example, window cleaning are to
be carried out in the vicinity.
fDisconnect the automatic controlled device from the mains power supply if opera-
tions such as, for example, window cleaning are being carried out in the vicinity.
fDuring operation observe the danger zone.
fDo not use the installation if people or objects are in the danger zone.
fUrgently shut down damaged installations until repair.
fUnconditionally shut down the unit during maintenance and cleaning operations.
fPinching and shearing points are to be avoided and must be secured.
fThis appliance can be used by children aged 8 and above and persons whose
physical, sensorial or mental capacities are impaired, or who have no experience or
know-how if they have been supervised or been given instructions on the use of the
appliance and if they understand the possible resulting dangers. Children are not
permitted to play with the device. Cleaning and maintenance should not be carried
out by children.
fThe rated sound pressure level is less than 70 dB(A).
fDisconnect the device from the mains power supply for maintenance and replace-
ment of parts.
If the motor is disconnected via a plug connection the operator must be able to
control - from any place to which it has access – that the plug is removed.
If this is not possible - due to design or installation - the disconnection from the
power supply must be ensured via locking in the disconnected position (e.g. isolator).
fThe motor tube can get very hot during prolonged use.
When working on the unit, do not touch the tube before it has cooled down.
5. Safety instructions for assembly
I ATTENTION: Important safety instructions. Follow all installation
instructions, as incorrect installation can lead to serious injuries.
fWhen mounting the motor without any mechanical protection of the driven parts and
of the tube which may become hot, the motor must be installed at a height of at least
2.5 m above the ground or of another level which provides access to the drive.

4Gerhard Geiger GmbH & Co. KG | 100W1549 0623V001en
EN
EN
fBefore the motor is installed, all cables which are not needed are to be removed and
all equipment which is not needed for power-operated actuation is to be put out of
operation.
fThe actuating element of a manual release must be mounted at a height of less than
1.8 m.
fIf the motor is controlled by a switch or pushbutton, the switch or pushbutton must
be mounted within eyeshot of the motor. The switch or pushbutton must not be
located in the vicinity of moving parts. The height of installation must be at least
1.5mabovetheoor.
fPermanently installed control devices must be attached visibly.
fIn case of devices extending horizontally, a horizontal distance of at least 0.4 m must
berespectedbetweenthefullyextendedpartandanyotherxedelement.
fThe rated speed and the rated torque of the motor must be compatible with the
device.
fThe mounting accessories that are used must be designed in accordance with the
selected rated torque.
fGood technical knowledge and good mechanical skills are necessary for the motor
installation. Incorrect installation can lead to serious injury.
Electricalworkmustbecarriedoutbyaqualiedelectricianinaccordancewiththe
regulations in force locally.
fOnly use connecting cables that are suitable with the environmental conditions and
which meet the construction requirements. (see accessories catalogue)
fIf the device is not equipped with a connecting cable and a plug, or other means for
disconnecting from the mains with a contact opening on each pole according to the
conditions of the overvoltage category III for full disconnection, a disconnecting
device of this type must be incorporated into the permanently installed electrical
installation according to the wiring rules.
fDo not mount the connecting cables near hot surfaces.
fA plug for the disconnection of the motor from the power supply must be accessible
after installation.
fDamaged connecting cables must be replaced by GEIGER connecting cables of the
same type.
fThe device must be mounted as described in the installation instructions. Fixations
shall not be made with adhesives since they are regarded as unreliable.

5
www.geiger.de EN
EN
6. Identicationnumber
Four removable ID stickers are applied on the connecting cable
of the motor GJ56.. E07 SMI. The printed number SMI-KEY-ID
clearly identies the motor in the bus system.
The stickers and / or the connecting cable must not be
interchanged.
The stickers are useful if you want to note the installation location
for a later bus integration of each motor (see “for your notes”).
7. Assembly note
When viewed from inside the room, the
power supply connection of the GJ56..
E07 SMI is located on the left side. The
straps are wound on the winding rollers
from the outside.
The GJ56.. E07 SMI must be installed in
alignment with the turning bars.
It is important that the GJ56.. E07 SMI is
installed centrally. Please make sure that
the load is evenly distributed.
Inclined installation:
The inclined installation is permitted till
45° maximum to level.
SMI-KEY-ID: 1114166510
SMI-KEY-ID: 1114166510
SMI-KEY-ID: 1114166510
SMI-KEY-ID: 1114166510
SMI-KEY-ID: 1114166510
Electric mains
Inside the room
Direction OPEN

6Gerhard Geiger GmbH & Co. KG | 100W1549 0623V001en
EN
EN
8. Installation instructions
I Prior to installation please check to ensure there is no visible damage
to the motor like cracks or open cables.
I Beforexingpleasecheckthestrengthofthemasonryandofthe
surface.
Head rail opening at top:

7
www.geiger.de EN
EN
Head rail opening at bottom:
i

8Gerhard Geiger GmbH & Co. KG | 100W1549 0623V001en
EN
EN
9. Information for the specialist electrician
H Caution: Important installation instructions. Please follow all
installation instructions since incorrect installation can lead to the
destruction of the motor and the switching unit.
H Attention! The bus voltage is not a safe low voltage. The bus is not
galvanically isolated from the supply voltage.
H ThemotorcanonlybeoperatedwithSMIcertiedactuators.
• For the operation with a setting switch, a locking switch is necessary (no simultaneous
UP and DOWN commands).
• The operations with the service clamps may be accomplished only by an electrical
specialist.
• The number of motors which can be connected to an actuator depends on the actuator.
Please observe the instructions of the actuator manufacturer.
• In case of parallel connection, the maximum load of the electrical installation must not be
exceeded.
• By push-button operation the switchover must be effected through an off position.
• By push-button operation the switchover time must be at least 0.2 s.
• Connecting cables with plug connectors of the Hirschmann Company are tested and
approved with couplings of the Hirschmann Company.
• A 5-pole connecting cable with continuous power supply must be used for SMI motors.
(GEIGER Flat5 with dark blue ring)
• In order to prevent a malfunction caused by coupling, the supply line (ref. NYM) from the
actuator/switch to the motor must not exceed 100m in case of motors with electronic end
stops.

9
www.geiger.de EN
EN
10. Conductor assignment for SMI drives for mains voltage
12 34
l+
l+: Control wire +
l-: Control wire -
PE: Protective earth conductor
L: Live
N: Neutral wire
Names
PEl- LN
l+
Ab
Auf
PEl- LN
Drive
12 34
Push button operation
Drive
l+ PEl- LN
12 34
Telegram operation
Drive
Changing the operating mode from telegram operation to pushbutton operation is done by
switching the power supply off and on.
Connector on drive cables The STAS4 connector from Hirschmann
is recommended.
Cable connections and connector
assignment for the STAS4/STAK4
connection system with cables
having black, grey, brown, blue
and yellow-green wires
STAS 4 / STAK 4 Wire colour Name
1
2
3
4
5 (PE)
black
grey
brown
blue
green-yellow
I+
I-
L
N
PE
Cable connections and connector
assignment for the STAS4/STAK4
connector system with cables
having 2 black wires
STAS 4 / STAK 4 Wire colour Name
1
2
3
4
5 (PE)
black 1
black 2
brown
blue
green-yellow
I+
I-
L
N
PE
Definition of the black wires:
black 1: between blue and green-yellow
black 2: between brown and green-yellow
Note on laying SMI wires in
custom cables
The I+ and I- SMI wires can be laid in the motor connec-
tion line of the SMI drive (as above) or in their own cable.
It is not permitted to lay SMI wires together with wires
carrying other signals in one cable.
If SMI drives wired in parallel are supplied with electrical
power from different phases, the SMI I+ and I- wires
must be laid in a separate cable.

10 Gerhard Geiger GmbH & Co. KG | 100W1549 0623V001en
EN
EN
11. SMI drives on different AC phases
Parallel connection to the control lines I+ and I- while supplying power to the drives from
different phases, is only permissible in telegram operating mode.
Drive
l+ PEl- NL1
L1
L2
L3
l+
l-
l+
l-
Actuator
(Telegram operation)
N
PE
Drive
l+ PEl- NL2
Drive
l+ PEl- NL3
Drive
l+ PEl- NL1
L1
L2
L3
N
PE
Drive
l+ PEl- NL2
Drive
l+ PEl- NL3
Telegram operation with power supply from different phases
permitted
Push button operation with power supply from different phases
not
permitted

11
www.geiger.de EN
EN
12. For your notes …
SMI-KEY-ID (sticker) Place of installation
e.g.: 1st floor, left side, third room, 1st window etc.

12 Gerhard Geiger GmbH & Co. KG | 100W1549 0623V001en
EN
EN
13. Setting of the end stops
General information
In order to set the end positions of the GJ56.. E07 SMI motors, any setting switch – with
continuous power supply – can be used that has a programming key or that allows a
simultaneous UP/DOWN command. In this case, the UP/DOWN keys must be activated
simultaneously instead of the programming key.
Article number / GEIGER setting switch
M56F152 with service terminal (D), 5 wires, SMI compatible
M56F153 with service terminal (CH), 5 wires, SMI compatible
I Important: please observe the connecting diagram on the back of the
setting switch.
Factory setting
• The motor is set on the lower end position at the factory. The upper end stop is at the very
other end. (at least lower end stop + 200 motor rotations).
• The motor command is in normal operation.
• The referencing is enabled on delivery.
✎Note: If the motor is installed in a closed Venetian blind and if the
limit stop switch is used the motor can be operated without further
settings.
I If the factory setting has been carried out and if the programming
mode is activated, max. 100 revolutions can be done downwards.
Reset to factory settings for a further run downwards.
14. Activate the programming mode
I Prerequisite: The motor is positioned between the upper and the
lower end position. The limit stop switch should not be pressed.
I The GJ56.. E07 SMI can be set with any setting switch that permits a
simultaneous UP/DOWN command. In this case, the UP/DOWN keys
must be simultaneously pressed instead of the programming key.
Activate the programming mode
via limit stop switch
In order to activate the programming mode, the motor
must be connected according to the diagram “push
button operation” (see point 10).
Press the programming key of the limit stop switch or the
UP/DOWN keys simultaneously until, after about 3 seconds,
the motor conrms “end position programming activated”
with 1 x click-clack. Then release the key.
1 x
Press programming
key for about
3 seconds
waving
PROG
PROG

13
www.geiger.de EN
EN
15. Programming/changing the end stops
The upper and lower end stops can be programmed and changed independently
of each other.
• Activate the programming mode.
• Run the motor in the direction of the desired end
position. The motor interrupts its run just to show that it
is in the programming mode:
• The direction in which the motor moves after the break*
determines the end stop to be programmed.
(UP = upper end stop, DOWN = lower end stop)
• When the desired end position is reached, move the
motor in the opposite direction until 2 short breaks*
show the last saved position.
• The programming is completed.
* As long as the interruption of movement has not yet
occurred, corrections can be done.
Start the setting process again to adjust another end position.
The referencing is automatically activated if the upper end position is programmed.
Note: when referencing, the motor runs over the set upper end position until the limit
stop switch.
I If the upper end position is reprogrammed on position, after the
end position had been programmed on the limit stop switch, the
referencing is automatically switched on. If the upper end position
is programmed on position again, the referencing remains switched
off or on.
Limit stop switch instead of upper end position
• If the direction UP should be turned off by the limit stop switch, there is no need to program
the upper end stop. The blind moves every time against the limit stop switch.
• If an upper end position is already programmed and you now want to switch off with the limit
stop switch, the programming mode must be activated and the blind moved against the limit
stop switch. The lower end position is unchanged and the programming is completed.
• The motor is now always turned off by the limit stop switch.
Cancel the programming mode:
In order to cancel the programming mode, press the PROG key or press simultaneously the
UP/DOWN keys until the motor conrms the cancellation of the programming mode after about
3 seconds with 2 x click-clack.
16. Referencing on the limit stop switch
The referencing on the limit stop switch can compensate a possible drifting of the upper end
position due to the modied winding behaviour of the lifting tapes.
If the referencing has been activated (see below), the next UP run is done till the limit stop
switch or after the programming of the upper end position.
The variation in distance between the upper limit position and the limit stop switch is stored.
After 1, 5, 20 and then every 50 cycles on the upper end stop, the motor runs against the limit
stop switch in order to test if the variations in distance have changed. If this is the case, the
upper end position is readjusted.
The motor stops on the limit stop switch by the reference runs.
PROG
PROG

14 Gerhard Geiger GmbH & Co. KG | 100W1549 0623V001en
EN
EN
17. Enable/disable reference cycles
The referencing is enabled at the factory. The referencing can only be effective if the upper
end position is set on position.
Switching on/off referencing:
Press the programming keys (programming key/UP/DOWN keys/limit stop switch and DOWN
key) until the motor jerks 1 x after about 3 seconds and another time after 6 seconds for
feedback “Switching on/off referencing”.
A subsequent UP command with 1 x jerking enables the referencing, a DOWN command with
2 x jerking disables it.
Automatic activation of the referencing
The referencing is automatically activated when the upper limit position was rst learned on the
limit stop switch and the referencing was disactivated.
If the upper end position is learned again on position and the referencing was not on, the
referencing remains off
18. Resetting to factory settings
Press the programming keys (programming key/UP/DOWN keys/limit stop switch and DOWN
key) about 10 seconds until the motor jerks 1 x after 3 seconds, 1 x after 6 seconds and 4 x
after 10 seconds. Then the motor is reset to factory settings and the referencing is activated.
Note: the position at which the drive has been reset to the factory setting is now dened as the
lower end position and can be adjusted by activating the learning mode.
19. Obstacle detection and anti-freeze protection
For an optimal operation of the obstacle detection function, move the blind from bottom to top
without interruption, after the programming has been completed.
After an obstacle detection (e.g. obstacle or blind frozen to the window sill), the UP direction is
blocked.
A short command in the DOWN direction releases the UP direction.
20. What to do if…
Problem Solution
Motor does not run. • Motor not plugged in.
Please check the plug connection.
• Check connecting cable for possible
damage.
• Check the mains voltage and allow the
cause of the voltage breakdown to be
tested by a specialist
electrician.
Instead of in the downwards direction,
motor runs upwards.
• The control leads are interchanged.
Exchange black/grey control leads.
Motor only runs in one
direction.
• Motor in the end position.
Run motor in the opposite direction.
Readjust the end positions, if necessary.
After running several times,
the motor breaks down and
no longer responds.
• The motor became too hot and has
switched off.
Try it again after a cooling time of about
15 min.
The blind is in the upper position,
actuates the limit stop switch and can
no longer be moved downwards.
• The motor was installed upside down or the
lower end position has been overrun and
the lift tapes were wound up incorrectly.
Allow free mobility of the limit stop switch.
Reset the end stops.

15
www.geiger.de EN
EN
21. Declaration of conformity
Current declarations of conformity are available under www.geiger.de
Schleifmühle 6 |D-74321 Bietigheim-Bissingen
Sitz Bietigheim-Bissingen |Amtsgericht Stuttgart HRA 300591 | USt-IdNr. DE145002146
Komplementär: Geiger Verwaltungs-GmbH |Sitz Bietigheim-Bissingen |Amtsgericht Stuttgart HRB 300481
Geschäftsführer: Roland Kraus |WEEE-Reg.-Nr. DE47902323
Gerhard Geiger GmbH & Co. KG
300H0204
EU Declaration of Conformity
Bietigheim-Bissingen, 20.04.2022 Roland Kraus (General Manager)
Product designation:
Venetian blinds motor, motor for rolling shutters, motor for awnings
Type designation:
GJ56.., GR45.., GU45.., GSI56.., GB45.., GB35..
Applied directives:
2006/42/EG
2014/53/EU
2011/65/EU + (EU)2015/863 + (EU)2017/2102
Applied standards:
EN 60335-1:2012
EN 60335-1:2012/AC:2014
EN 60335-1:2012/A11:2014
EN 60335-1:2012/A13:2017
EN 60335-1:2012/A1:2019
EN 60335-1:2012/A14:2019
EN 60335-1:2012/A2:2019
EN 60335-2-97:2006+A11:2008+A2:2010+A12:2015
EN 62233:2008
EN 62233 Ber.1:2008
EN 55014-1:2017
EN 55014-2:2015
EN 61000-3-2:2019
EN 61000-3-3:2013
ETSI EN 301 489-1 V2.2.0(2017-03)
ETSI EN 301 489-3 V2.1.1(2019-03)
ETSI EN 300 220-2 V3.1.1(2017-02)
DIN EN IEC 63000:2019-05
Authorized representative for technical data:
Gerhard Geiger GmbH & Co. KG
Address:
Schleifmühle 6, D-74321 Bietigheim-Bissingen
en
Gerhard Geiger GmbH & Co. KG
Antriebstechnik
Schleifmühle 6
D-74321 Bietigheim-Bissingen
0422100W1518

16 Gerhard Geiger GmbH & Co. KG | 100W1549 0623V001en
EN
EN
For technical questions, please call our service team at: +49 (0) 7142 938 333.
They will be happy to assist you.
Gerhard Geiger GmbH & Co. KG
Schleifmühle 6 | D-74321 Bietigheim-Bissingen
T +49 (0) 7142 9380 | F +49 (0) 7142 938 230
info@geiger.de | www.geiger.de
22. Maintenance
The drive is maintenance-free.
23. Technical data
Technical data GJ56.. E07 with electronic end stop
GJ5603k GJ5606k GJ56061) GJ5610 GJ5620
Voltage 230 V~/50 Hz
Current 0,40 A 0,40 A 0,40 A 0,60 A 0,85 A
Cos Phi (cosj)> 0,95
Inrush current (factor) x 1,2
Power 90 W 93 W 90 W 135 W 190 W
Torque 3 Nm 6 Nm 6 Nm 10 Nm 2 x 10 Nm
Speed 26 rpm
Protection class IP 54
Limit switch range 200 rotations
Operating mode S2 4 min. S2 4 min. S2 6 min. S2 4 min. S2 4 min.
Length 319,5 mm 319,5 mm 324,5 mm 329,5 mm 356,7 mm
Diameter 55 mm
Weight ca. 1,50 kg ca. 1,50 kg ca. 1,60 kg ca. 1,70 kg ca. 2,20 kg
Air humidity dry and non-condensing place
Storage temperature T = -15°C .. +70°C
1) Run-time optimized version
Subject to technical modifications. Please find information to the ambient temperature range of our
GEIGER motors under www.geiger.de
24. Notes on waste disposal
Recycling of packaging materials
In the interest of environmental protection, please contact your local government’s recycling or
solid waste management department to learn more about the services it provides.
Waste disposal of electric and electronic equipment
Electrical and electronic equipment must be collected and disposed of separately in accordance
with EU regulations.
Table of contents
Other GEIGER DC Drive manuals
Popular DC Drive manuals by other brands
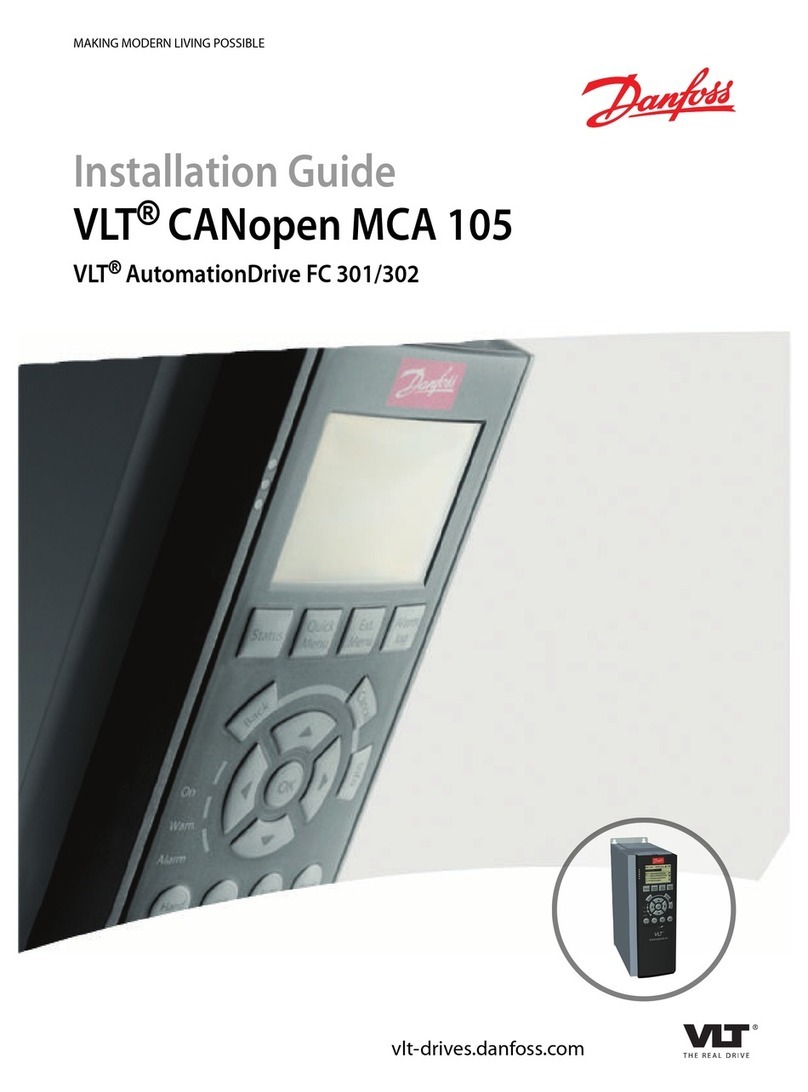
Danfoss
Danfoss VLT AutomationDrive FC 301 installation guide

Honeywell
Honeywell QM100A1009 instruction sheet
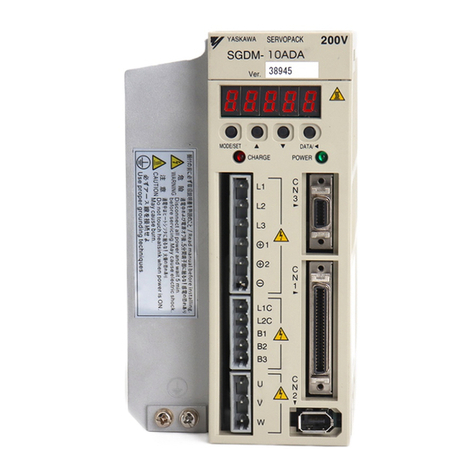
YASKAWA
YASKAWA E-II Series Safety precautions

Aquagem
Aquagem iSAVER 1100 Installation & user guide
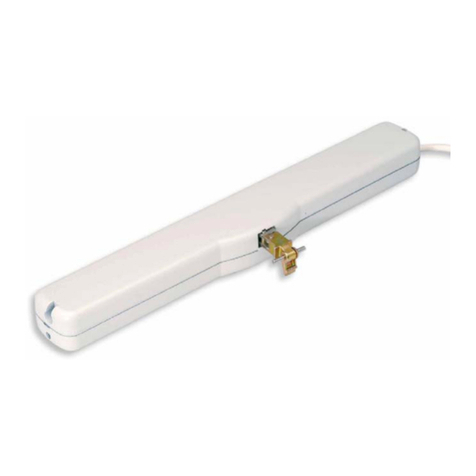
G-U
G-U ELTRAL KS 30/40 Remote Assembly and operating instructions
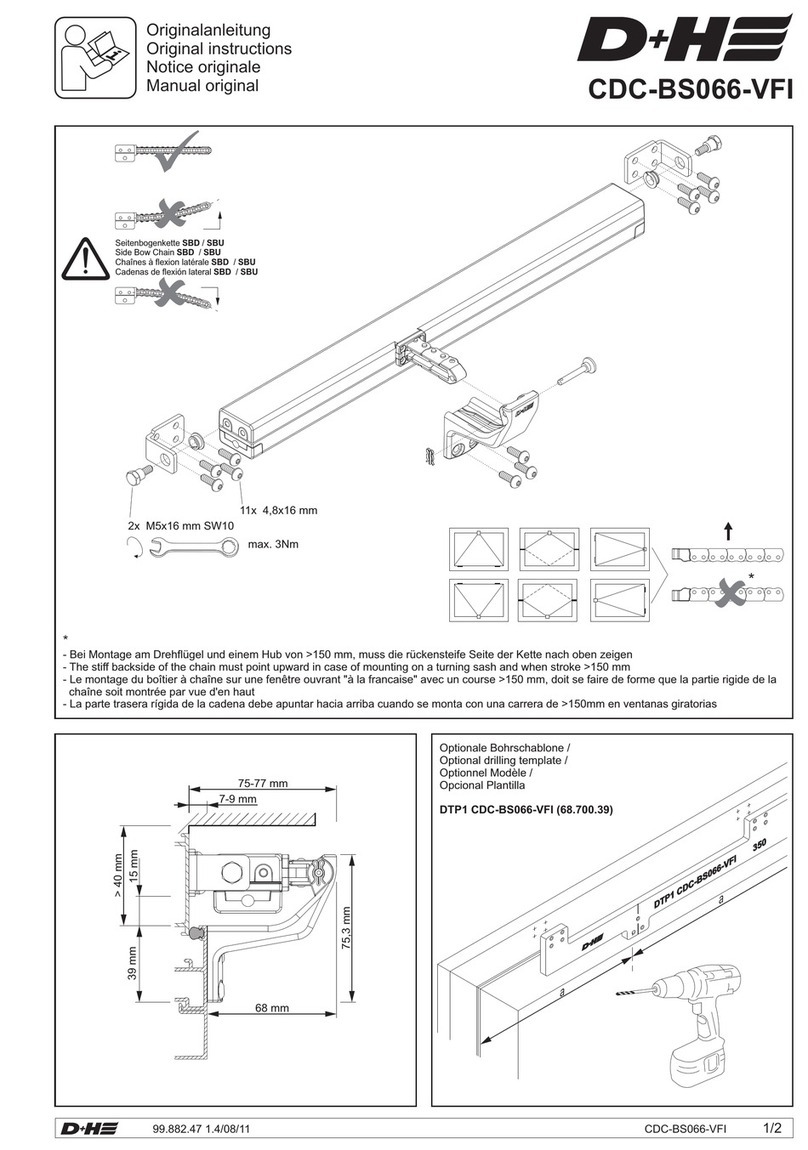
D+H
D+H CDC-BS066-VFI Original instructions

Siemens
Siemens SINAMICS SM150 Operating and installation instructions
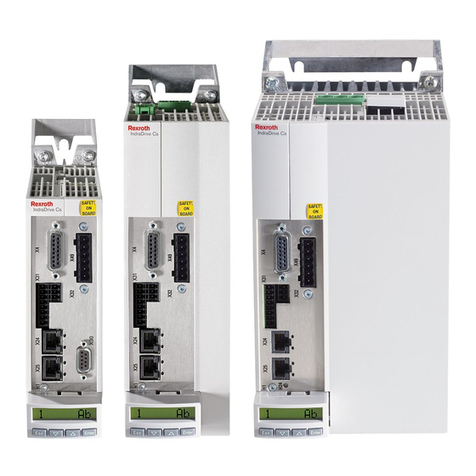
Bosch
Bosch Rexroth IndraDrive CsDrive System with HCS01 Project planning manual
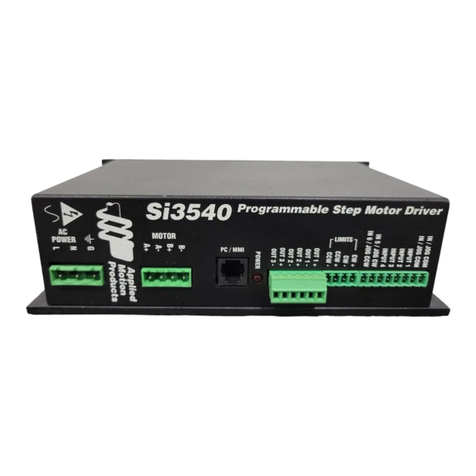
Applied Motion Products
Applied Motion Products Si3540 Hardware manual
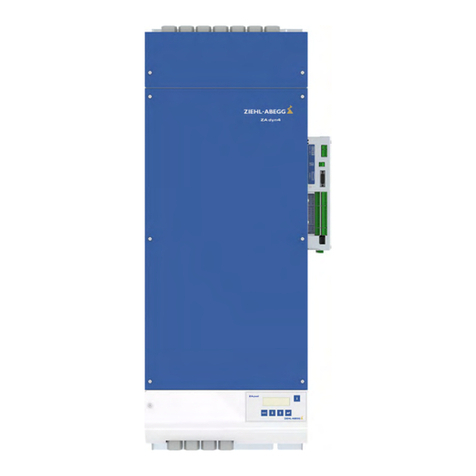
ZIEHL-ABEGG
ZIEHL-ABEGG ZA dyn 4B 110 Original operating instructions
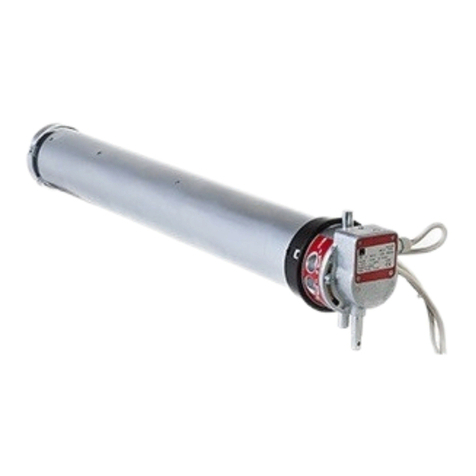
Simu
Simu T835/8 manual

Danfoss
Danfoss MCD 500 Service manual