GHM GREISINGER GIR 300 Technical document

E44.X.01.6C-04
GHM Messtechnik GmbH • Standort Greisinger
Hans-Sachs-Str. 26 • 93128 Regenstauf • GERMANY
+49 (0) 9402 / 9383-0
+49 (0) 9402 / 9383-33
info@greisinger.de
Mounting- and Operating Manual
Universal displaying and controlling device
as of version 1.1
GIR 300
Please read these instructions
carefully before use!
WEEE-Reg.-Nr. DE 93889386
Please consider the safety instructions!
Please keep for future reference!

E44.X.01.6C-04 Mounting- and Operating Manual GIR 300 page 2 of 34
Contents
1SAFETY.................................................................................................................................................3
1.1 GENERAL NOTE.................................................................................................................................3
1.2 INTENDED USE...................................................................................................................................3
1.3 SKILLED PERSONNEL .........................................................................................................................3
1.4 TYPE-LABEL......................................................................................................................................4
1.5 SAFETY SIGNS AND SYMBOLS.............................................................................................................4
1.6 REASONABLY FORESEEABLE MISUSEE ................................................................................................5
1.7 SAFETY GUIDELINES ..........................................................................................................................5
2PRODUCT DESCRIPTION....................................................................................................................5
2.1 SCOPE OF SUPPLY.............................................................................................................................5
2.2 FUNCTION.........................................................................................................................................6
3MOUNTING IN PANELS / HOUSINGS..................................................................................................6
4DISPLAY AND OPERATING ELEMENTS ............................................................................................7
4.1 DISPLAY ELEMENTS ...........................................................................................................................7
4.2 OPERATING ELEMENTS ......................................................................................................................7
5ELECTRIC CONNECTION ....................................................................................................................8
5.1 TERMINAL ASSIGNMENT .....................................................................................................................8
5.2 CONNECTION DATA............................................................................................................................8
5.3 CONNECTING AN INPUT SIGNAL...........................................................................................................9
5.4 CONNECTING SWITCHING OUTPUTS ..................................................................................................13
5.5 COMMON WIRING OF SEVERAL DEVICES ............................................................................................13
6CONFIGURATION...............................................................................................................................13
6.1 GENERAL DESCRIPTION AND NOTES TO THE OPERATING OF THE MENU................................................13
6.2 SELECTING AN INPUT SIGNAL TYPE ...................................................................................................14
6.3 MEASURING VOLTAGE OR CURRENT (0-50MV, 0-1V, 0-2V, 0-10V, 0-20MA, 4-20MA)..........................16
6.4 MEASURING TEMPERATURE (PT 100, PT 1000 RTD PROBES AND THERMOCOUPLES TYPE J, K, N, SOR T) ...............17
6.5 MEASURING OF FREQUENCY (TTL, SWITCHING-CONTACT)..................................................................18
6.6 MEASURING OF ROTATION SPEED (TTL, SWITCHING-CONTACT)..........................................................20
6.7 UP-/DOWNWARDS COUNTER ............................................................................................................21
6.8 INTERFACE MODE ............................................................................................................................23
6.9 SELECTION OF THE OUTPUT FUNCTION..............................................................................................23
7SWITCHING POINTS AND ALARM-BOUNDARIES...........................................................................24
7.1 2-POINT-CONTROLLER,3-POINT-CONTROLLER...................................................................................25
7.2 2-POINT-CONTROLLER WITH ALARM FUNCTION...................................................................................26
7.3 MINIMUM/MAXIMUM ALARM (INDIVIDUAL OR COMMON) ........................................................................27
8OFFSET- AND SLOPE-ADJUSTMENT...............................................................................................28
9MIN-/MAX-VALUE MEMORY..............................................................................................................29
10 SERIAL INTERFACE .......................................................................................................................29
11 ERROR CODES...............................................................................................................................30
12 DECOMMISSIONING, RESHIPMENT AND DISPOSAL ..................................................................31
12.1 DECOMMISSIONING ......................................................................................................................31
12.2 RESHIPMENT AND DISPOSAL .........................................................................................................31
13 SPECIFICATION..............................................................................................................................32

E44.X.01.6C-04 Mounting- and Operating Manual GIR 300 page 3 of 34
1 Safety
1.1 General note
Read this document carefully and get used to the operation of the device before you use it.
Keep this document within easy reach near the device for consulting in case of doubt.
Mounting, start-up, operating, maintenance and removing from operation must be done by qualified, spe-
cially trained staff that have carefully read and understood this manual before starting any work.
The manufacturer will assume no liability or warranty in case of usage for other purpose than the intended
one, ignoring advices of this manual, operating by unqualified staff as well as unauthorized modifications
to the device.
1.2 Intended use
The device is a universal microcontroller based display -, monitoring - and controlling device.
The device has 1 universal-input, 2 relay outputs and an EASY Bus-interface. It can be used by measure-
ment and –regulation, limit monitoring, etc.
Prior to fulfil the referring requirements, the device has to be configured on the base of this manual. Wrong
configuration may lead to malfunction in the application. The commissioning expert / the operator is liable
for a suitable configuration.
The device is only to be operated in control panels ore suitable electric housings, where the connection
terminal area is sufficiently protected against touch.
The device is designed for industrial or commercial use.
Outdoor installation without suitable means of protection is not allowed.
The counting function is not to be used for e.g. consumption metering in the sense of the measuring in-
struments directive 2014/32/EU.
The safety guidelines of the manual are followed!
The unit does not contain any components that you can service or repair yourself.
All the described operations are only to be performed of skilled personnel that are authorized by the opera-
tor.
Any other use or use exceeding this is considered as non-conforming and leads to the expiration of any
liability or guarantee claims from the manufacturer.
Note: Combination / connection to other electrical equipment with CE marking does not automatically de-
liver a conform system. A new evaluation of the system’s conformity to the low voltage directive
(2014/35/EU) and EMC directive (2014/30/EU) by the manufacturer may be necessary, eventually others
have to be considered (e.g. machinery directive).
1.3 Skilled personnel
The mounting, electrical installation, start of operation, maintenance and decommissioning must only per-
formed by a skilled electrician.
Users of the readily installed device have to be sufficiently skilled in the operation of the device and able to
avoid risks. The operator of the arrangement is responsible for sufficient qualification the operators.

E44.X.01.6C-04 Mounting- and Operating Manual GIR 300 page 4 of 34
1.4 Type-Plate
Type
Manufacturer address
Production date code
CE mark: see below
Disposal: refer Chapter 12.2
Please refer to manual
Serial number
Warning sign: Electrical risk, see below
Electric connections, refer chapter 5.1
Symbol explanation
Electrical risk:
At electrical connections and components signed with this symbol there is a
risk of electrical shock.
Please refer to manual:
Read the mounting- and operating manual carefully, before you connect and
use the device.
CE mark:
With the CE-Sign declares the manufacturer, that the Product is conform with
the prevailing requirements of EG.
1.5 Safety signs and symbols
Warnings are labelled in this document with the followings signs:
Caution!
This symbol warns of imminent danger, death, serious injuries and sig-
nificant damage to property at non-observance.
Attention!
This symbol warns of possible dangers or dangerous situations which
can provoke damage to the device or environment at non-observance.
Note!
This symbol point out processes which can indirectly influence opera-
tion, possibly cause incorrect measurement or provoke unforeseen re-
actions at non-observance.

E44.X.01.6C-04 Mounting- and Operating Manual GIR 300 page 5 of 34
1.6 Reasonably foreseeable misusee
1.
This device must not be used at potentially explosive areas!
Do not use these products as safety or emergency stop devices or in any other
application where failure of the product could result in personal injury or material
damage.
Failure to comply with these instructions could result in death or serious injury
and material damage.
2.
This device must not be used at a patient for diagnostic or other medical
purpose.
1.7 Safety guidelines
1.
Faultless operation and reliability in operation of the measuring device can only be assured if
the device is used within the climatic conditions specified in the chapter 0
2.
Always disconnect the device from its supply before opening it. Take care that nobody can
touch any of the unit‘s contacts after installing the device.
3.
Standard regulations for operation and safety for electrical, light and heavy current equipment
have to be observed, with particular attention paid to the national safety regulations
(e.g. VDE 0100).
4.
When connecting the device to other devices (e.g. the PC) the interconnection has to be de-
signed most thoroughly, as internal connections in third-party devices (e.g. connection of
ground with protective earth) may lead to undesired voltage potentials.
5.
The device must be switched off and must be marked against using again, in
case of obvious malfunctions of the device which are e.g.:
- Visible damage.
- Device does not work like prescribed.
- Storing the device under inappropriate conditions for longer time.
When not sure, the device should be sent to the manufacturer for repairing or
servicing.
6.
Modifications or repairs of the device may not be performed by the customer. For maintenance
or repair the device must be sent to the manufacturer.
2 Product description
2.1 Scope of supply
monitoring- / controlling device
2 mounting brackets
screw-in/plug-in clamps (according to the model)
mounting and operating manual

E44.X.01.6C-04 Mounting- and Operating Manual GIR 300 page 6 of 34
2.2 Function
It is a universally applicable microprocessor controlled displaying, monitoring and controlling device.
The device is supporting one universal interface for the connection of:
- Standard transmitter signals (0-20 mA, 4-20 mA, 0-50 mV, 0-1 V, 0-2 V
and 0-10 V),
- RTD (Pt 100 and Pt 1000),
- Thermocouple probes (type K, J, N, T and S)
- Frequency (TTL and switching contact)
As well as rotation measuring, counting, etc...
Additionally two switching outputs, which can be configured as 2-point-controller, 3-point-controller, 2-point-
controller with min./max. alarm common or individual min./max. alarm. The state of the switching outputs is
displayed with 2 LED, whereby the LED (label 1) is displayed the state of the contact from relay 1 and the
LED (label 2) the state of the contact from relay 2.
(LED on = contact connected).
Furthermore both devices support one EASY Bus-interface for communicating with a host computer that
makes the device to a EASY Bus-module.
The device is being examined and completely calibrated.
Before the device can be used, it has to be configured for the customer’s application.
In order to avoid undefined input states and unwanted or wrong switching
processes, we suggest to connect the device’s switching outputs after You
have configured the device properly.
By calling a configuration menu (configuration of the measuring input, con-
figuration of the analog output, configuration of the output function, offset-
and slope-adjustment) the measurement and regulation of the device will be
deactivated.
By leaving the menu the device will be reinitialised and the measur-
ing/regulation will be started again.
At the input function “counter” the counter state will be reset by leaving the
menu.
3 Mounting in panels / housings
Panel cut-out:
Mounting:

E44.X.01.6C-04 Mounting- and Operating Manual GIR 300 page 7 of 34
4 Display and operating elements
4.1 Display elements
Main display:
Display element to show minimum / maximum and measuring value.
It also displays errors and parameters.
LED 1:
Indicates the state of output 1
LED 2:
Indicates the state of output 2
4.2 Operating elements
Button 1:
activates menu "Switching points and alarm boundaries"
Button 1 + 5, >2s: activates menu "Configuration of Output functions"
Menu: save value or step to next parameter
Button 2:
display max. value
button 2 + 5, >2s: activates menu „Select input signal“
button 2 + 3, >2s: reset min-/max. value
Menu: press short = increase value
press long = roll-function with overflow-function *)
Button 3:
display min. value
button 3 + 5, >2s: activates menu „Offset- and slope adjustment“
button 3 + 2, >2s: reset min-/max. value
Menu: press short = decrease value
press long = roll-function with overflow-function *)
*) The input is made with the buttons 2 and 3. When pressing the button once the value will be raised (but-
ton 2) by one or lowered (button 3) by one.
When holding the button pressed for longer than 1 sec. the value starts counting up or down, the count-
ing speed will be raised after a short period of time. The device also features a ‘overflow-function‘, when
reaching the upper limit of the range, the device switches to the lower limit, vice versa.

E44.X.01.6C-04 Mounting- and Operating Manual GIR 300 page 8 of 34
5 Electric connection
Wiring and commissioning of the device must be carried out by skilled personnel only.
Use the device only for panel mounting or with suitable electrically
housings
The electrical connections must be protected against direct contact.
Other way, the risk of an electric shock exists.
In case of wrong wiring the device may be destroyed. We cannot as-
sume any warranty in case of wrong wiring of the device.
5.1 Terminal assignment
1
EASY Bus-Interface
2
EASY Bus-Interface
3
Input: 0-10V
4
Input: 0-50mV, thermocouples, Pt100
5
Input: 0-1V, mA, frequency, Pt100, Pt1000
6
Input: GND, Pt100, Pt1000
7
Supply voltage GND
8
Supply voltage +Uv
9
Output 2: relay, break contact
10
Output 2: relay, input
11
Output 1: relay, input
12
Output 1; relay, make contact
5.2 Connection data
These limits must not be exceeded (not even for a short time)!
between
terminals
typical
limitations
Note
min.
max.
min.
max.
Power supply voltage
7 and 8
9
28
0
30
or corresponding designa-
tion on the type plate
Output 1:
relay: make contact
11 and 12
253 VAC
5A
ohmic load
or corresponding designa-
tion on the type plate
Output 2
relay: break contact
9 and 10
253 VAC
5A
ohmic load
or corresponding designa-
tion on the type plate
Input 0-50mV, TC, ...
4 and 6
0 V
3.3 V
-1 V
10 V,
I<10mA
Input mA
5 and 6
0 mA
20 mA
0 mA
30 mA
Input 0-1(2)V, freq., ...
0 V
3.3 V
-1 V
30 V,
I<5mA
Input 0-10V
3 and 6
0 V
10 V
-1 V
20 V
Input Pt100 (Pt1000)
4, 5 and 6
0 Ω
∞Ω
active signal not allowed
EASYBus-Interface
1 and 2
12 V
36 V
0 V
42 V
12 10

E44.X.01.6C-04 Mounting- and Operating Manual GIR 300 page 9 of 34
5.3 Connecting an input signal
Please take care not to exceed the limitations of the inputs when connecting the de-
vice as this may lead to destruction of the device.
5.3.1 Connection a Pt 100 or Pt 1000 RTD probe or a thermocouple probe
Pt100
6
5
4
Pt100
6
5
4
Pt100
6
5
4
Pt100-RTD probe (3-wire)
Pt100- RTD probe (2-wire)
Pt100- RTD probe (4-wire)
Pt1000
6
5
-
+TC
6
4
Pt1000- RTD probe (2-wire)
Thermocouple probe
5.3.2 Connecting a 4 - 20 mA transmitter in 2-wire-technology
+
_
9-28 VDC
Supply:
-Uv
+Uv Transmitter
4-20mA
_
+for transmitter
Supply:
8
7
6
5
+
_
9-28 VDC
Supply:
-Uv
+Uv Transmitter
4-20mA
8
7
5
with individual transmitter supply
without separate transmitter supply
5.3.3 Connecting a (0)4 - 20 mA transmitter in 3-wire-technology
+
_
9-28 VDC
Supply:
-Uv
Sig.
+Uv
Transmitter
0(4)-20mA
_
+for transmitter
Supply:
8
7
6
5
+
_
9-28 VDC
Supply:
-Uv
Sig.
+Uv
Transmitter
0(4)-20mA
8
7
5
with individual transmitter supply
without separate transmitter supply
set link
non-connected

E44.X.01.6C-04 Mounting- and Operating Manual GIR 300 page 10 of 34
5.3.4 Connecting a 0-1V, 0-2V or 0-10V transmitter in 3-wire-technology
+
_
9-28 VDC
Supply:
10V
1V / 2V
-Uv
Sig.
+Uv
Transmitter
0-1(10)V
_
+for transmitter
Supply:
8
7
6
5
3
+
_
9-28 VDC
Supply:
10V
1V / 2V
-Uv
Sig.
+Uv
Transmitter
0-1(10)V
8
7
5
3
with individual transmitter supply
without separate transmitter supply
5.3.5 Connecting a 0-1/2/10V or 0-50 mV transmitter in 4-wire-technology
+
_
9-28VDC
Supply:
10V
50mV
1V / 2V
-Uv
Sig-
Sig+
+Uv
Transmitter
_
+for transmitter
Supply:
8
7
6
5
4
3
+
_
9-28 VDC
Supply:
10V
50mV
1V / 2V -Uv
Sig-
Sig+
+Uv
Transmitter
8
7
6
5
4
3
with individual transmitter supply
without separate transmitter supply
(Note: Sig- and -Uv of the Transmitter must be the same potential)
5.3.6 Connecting a frequency- or rotation-signal
When measuring frequency or rotation three different input signals can be selected in the device’s con-
figuration. There is the possibility of connecting an active signal (= TTL, ...), a passive sensor-signal
with NPN
(= NPN-output, push-button, relay, ...) or PNP (= a PNP output switching to +Us, high-side push-button,
...)
When configuring the device with a NPN switching output, a pull-up-resistor (~7 kΩreferring to +3.3V)
is connected internally. So when you use a device with NPN output you don‘t need to connect a resistor
externally.
When configuring the device with a PNP switching output, a pull-down resistor (~7 kΩreferring to GND) is
connected internally. So when you use a device with PNP output You don‘t need a resistor externally.
It may be that your measuring-signal source needs the connection of an external resistor e.g. the pull-
up-voltage of 3.3V is not enough for the signal source, or you want to measure in the top level fre-
quency range. In this case the input signal has to be treated like an active signal and you have to con-
figure the device as „TTL“.
When connecting the device You have to take care not to exceed the limits of the input
voltage respective the input current of the frequency-input.

E44.X.01.6C-04 Mounting- and Operating Manual GIR 300 page 11 of 34
+
_
9-28 VDC
Supply:
-Uv
Sig.
+Uv
Transducer
_
+for transducer
Supply:
8
7
6
5
+
_
9-28 VDC
Supply:
-Uv
Sig.
+Uv
Transducer
8
7
5
Connection of a transducer (with separate power
supply) with TTL or PNP output
Connection of a transducer (without separate power
supply) with TTL or PNP output
+
_
9-28 VDC
Supply:
-Uv
Sig.
+Uv Transducer
_
+for transducer
Supply:
8
7
6
5
+
_
9-28 VDC
Supply:
-Uv
Sig.
+Uv Transducer
8
7
5
Connection of a transducer (with separate power
supply) with NPN output
Connection of a transducer (without separate power
supply) with NPN output
+
_
9-28 VDC
Supply:
Rv
-Uv
Sig.
+Uv Transducer
_
+for transducer
Supply:
8
7
6
5
+
_
9-28 VDC
Supply:
Rv -Uv
Sig.
+Uv Transducer
8
7
5
Connection of a transducer (with separate power
supply) with NPN output and necessary external
resistor
Connection of a transducer (without separate power
supply) with NPN output and necessary external
resistor
Connection note: Rv = 3 kΩ(with power supply voltage =12 V) or 7 kΩ(at 24 V), device configuration: Sens = TTL
+
_
9-28 VDC
Supply:
Rv2
Rv1
-Uv
Sig.
+Uv
Transducer
_
+for transducer
Supply:
8
7
6
5
+
_
9-28 VDC
Supply:
Rv2
Rv1
-Uv
Sig.
+Uv
Transducer
8
7
6
5
Connection of a transducer (with separate power
supply) with PNP output
and necessary external resistor wiring.
Connection of a transducer (without separate power
supply) with PNP output
and necessary external resistor wiring.
Connection note: Rv2 = 600Ω, Rv1 = 1.8kΩ(with power supply voltage =12V) or 4.2kΩ(at 24V), device configuration: Sens = TTL
(Rv1 is a current limiting resistor and may be shorted if necessary. It should never exceed the mentioned value)

E44.X.01.6C-04 Mounting- and Operating Manual GIR 300 page 12 of 34
5.3.7 Connecting a counter signal
When configuring the device you can select 3 different input signal modes similar to the connection of
frequency- and rotation-signals.
The connection of a sensor-signal for a counter-signal is the same used for the frequency- and rotation-
signal.
Please use the wiring diagram given in this chapter.
There is the possibility to reset the counter. When connecting contact 4 with GND (e.g. contact 6) the
counter will be reset. You can do this manually (e.g. with the help of a push-button) or automatically
(with one switching output of the device).
When connecting the device, take care not to exceed the limits of the input-
voltage or the input-current of the frequency input.
+
_
9-28 VDC
Supply:
-Uv
Sig.
+Uv
transducer
Impulse
8
7
6
5
4Reset-
button
-Uv
Sig.
+Uv
transducer
Impulse
_
+9-28 VDC
Supply:
no.2
device
8
7
5
no.1
device
12
11
8
7
5
4
Manually reset the device
with the help of an push-button
+
_
9-28VDC
Supply:
-Uv
Sig.
+Uv
transducer
Impulse
12
11
8
7
6
5
4Reset-
button
automatically resetting with the help of output 1 and
additional resetting the device via push-button
Connection note: output 2 can only be used to
switching of low voltage potential!
Cascading of GIR 300
(Configuration note for the GIR 300:
device 1 –input signal like impulse transducer
device 2 –input signal = switching-contact

E44.X.01.6C-04 Mounting- and Operating Manual GIR 300 page 13 of 34
5.4 Connecting switching outputs
In order to avoid unwanted or wrong switching processes, we suggest to connect the de-
vice’s switching outputs after you have configured the device’s switching outputs properly.
The device have 2 outputs:
•Output 1: Relay, make contact
• Output 2: Relay, break contact
Please take care that you must not exceed the limits of the voltage and of the
maximum current of the switching outputs (not even for a short period of time).
Please take extreme care when switching inductive loads (like relays, coils etc.).
Because of their high voltage peaks, protective measures (e.g. RC-element) to
limit these peaks have to be taken.
More information about switch states from the output functions, see chapter Feh-
ler! Verweisquelle konnte nicht gefunden werden.
In case of configuring one output as an alarm output, the output will be closed in
idle state (no alarm present). The output relay opens when an alarm condition oc-
curred. See chapter7.2 and 7.3
5.5 Common wiring of several devices
The inputs of the device are not electrically isolated to the power supply.
When interconnecting several of these devices you have to make sure that there is no potential displace-
ment.
Especially consider the following points:
- If several encoders are supplied with the same voltage (sensors, transducers), it is advisable to isolate
each other electrically.
- If encoders have an electrical connection, the supply voltage should be electrically isolated. Please note
that electrical connection of the encoders also can be arising with the measuring medium (e.g. liquid).
6 Configuration
6.1 General description and notes to the operating of the menu
Selection of parameters:
Switch to the next parameter with Button1 resp. save after the last pa-
rameter.
Parameter adjustment:
With button 2 or button 3you can adjust its value.
The buttons 2 and 3 are featured with a ‘roll-function‘. When pressing the button once
the value will be raised (button 2) by one or lowered (button 3) by one.
When holding the button pressed for longer than 1 sec. the value starts counting up or
down, the counting speed will be raised after a short period of time. The device also
features a ‘overflow-function‘, when reaching the upper limit of the range, the device
switches to the lower limit, vice versa.
Button 1 Button 2 Button 3

E44.X.01.6C-04 Mounting- and Operating Manual GIR 300 page 14 of 34
If no key is pressed > 60 sec. the menu will be automatically closed.
When changing the measuring mode “FUNC“ the values for the offset and slope-
adjustment will be reset. Furthermore a change of the device scaling for standard sig-
nals (di.Lo, di.Hi, dP) or of the resolution can possibly influence the values of the offset
and slope-adjustment. Therefore you may check your offset and slope-adjustment after
changing the input configuration.
The change of the device scaling for standard signals (di.Lo, di.Hi, dP) can possibly
change the switching and alarm points. Therefore you may check your output settings
afterwards!
The alarm-output is inverted!
This means, that the output will be active when there is no alarm!
6.2 Selecting an input signal type
- Turn the device on and wait until it completed its built-in segment
test.
- Press button 2 for >2 sec. (e.g. with a small screw driver)
The device displays “InP“ ('INPUT').
- Use button 2 or button 3 (middle or right button) to select the in-
put
signal (see table below).
- Validate the selection with button 1 (the left button). The display
will show “InP“ again
Depending on the selected input signal, additional configurations will be needed.
Input type
Input Signal
To select as
input
proceed in chap-
ter
Voltage signal
0 –10 V
U
6.3
0 –2 V
0 –1 V
0 –50 mV
Current signal
4 –20 mA
I
6.3
0 –20 mA
RTD
Pt 100
T.RES
6.4
Pt 1000
Thermocouples
NiCr-Ni (type K)
T.TC
6.4
Pt10Rh-Pt (type S)
NiCrSi-NiSi (type N)
Fe-CuNi (type J)
Cu-CuNi (type T)
Frequency
TTL-signal
FREQ
6.5
Switch-contact NPN,
PNP
Rotation
TTL-signal
RPN
6.6
Switch-contact NPN,
PNP
Counter up
TTL-signal
[O.VP
0

E44.X.01.6C-04 Mounting- and Operating Manual GIR 300 page 15 of 34
Switch-contact NPN,
PNP
Counter down
TTL-signal
[O.DN
0
Switch-contact NPN,
PNP
Interface mode
Serial interface
SER,
6.8
Please note: When changing the measuring mode “InP“, the input signal “SEnS“ and the display-
unit “Unit“ all settings will be changed to factory default. You have to set all the other
settings.
This also regards the settings for offset and slope-adjustment as well as the switching
points!
Parameter Overflow for the available measuring types:
Measuring type
U
I
T.RES
T.TC
FREQ
RPN
[O.VP
[O.DN
SER,
Input signal / sensor
X
X
X
X
X
X
X
X
-
Signal edge
-
-
-
-
-
-
X
X
-
Devisor
-
-
-
-
-
X
X
X
-
Input signal low
-
-
-
-
X
-
-
-
-
Input signal high
-
-
-
-
X
-
X
X
-
Decimal point
X
X
X
-
X
X
X
X
-
Display low
X
X
-
-
X
-
-
-
-
Display high
X
X
-
-
X
-
X
X
-
Temperature unit
-
-
X
X
-
-
-
-
-
Limit
X
X
-
-
X
-
X
X
-
Filter
X
X
X
X
X
-
-
-
-
Address
-
-
-
-
-
-
-
-
X
Output
X
X
X
X
X
X
X
X
X

E44.X.01.6C-04 Mounting- and Operating Manual GIR 300 page 16 of 34
6.3 Measuring voltage or current (0-50mV, 0-1V, 0-2V, 0-10V, 0-20mA, 4-20mA)
This chapter describes how you configure the device for measuring voltage- or current-signals from an ex-
ternal transmitter. This instruction demands that you selected “U“ or “I“ as your desired input type like it is
explained in chapter 6.2. The display has to show “InP“.
- Press Button 1. The display shows “SEnS“.
- Select the desired input signal using button 2 or button 3 (middle or right button).
Display
Input signal
(voltage measuring)
Notes
10.00
0 –10 V
2.00
0 –2 V
1.00
0 –1 V
0.050
0 –50 mV
Display
Input signal
(current measuring)
Notes
4-20
4 –20 mA
0-20
0 –20 mA
- Validate the selected input signal by pressing button 1. The display shows “SEnS“ again.
- Press button 1 again, The display will show “dP“ (decimal point).
- Select the desired decimal point place by pressing button 2 or button 3.
- Validate the selected decimal position by pressing button 1. The display shows “dP“ again.
- Press button 1 again, the display will show “di.Lo“ (Display Low = low display value).
- Use button 2 and button 3 to select the desired value the device should display when a 0mA,
4mA or 0V input signal is attached.
- Validate the selected value by pressing button 1. The display shows “di.Lo“ again.
- Press button 1 again, the display will show “di.Hi“ (Display High = high display value).
- Use button 2 and button 3 to select the desired value the device should display when a
20mA, 50mV, 1V, 2V or 10V input signal is attached.
- Validate the selected value by pressing button 1. The display shows “di.Hi“ again.
- Press button 1 again. The display will show “Li“ (Limit = Measuring range limit).
- Use button 2 and button 3 to select the desired measuring range limit.
Display
Measuring range limit
Notes
off
Deactivated
Exceeding of the measuring range limit is
tolerable for about 10% of the selected
input signal.
on.Er
Active, (displays error)
The measuring range limit is exactly
bounded by the input signal. When ex-
ceeding or shortfalling the input signal the
device will display an error message.
SENS
DP
D,.K,
D,.LO
L,

E44.X.01.6C-04 Mounting- and Operating Manual GIR 300 page 17 of 34
on.rG
Active, (displays the selected limit)
The measuring range limit is exactly
bounded by the input signal. When ex-
ceeding or shortfalling the input signal the
device will display the selected
lower/upper display value.
[e.g. humidity: when shortfalling or ex-
ceeding, the device will display 0% or
100%]
Hint: When exceeding the measuring range limit > 10% independently from the setting, the device
will always display an error message (“Err.1“ or “Err.2“).
- Press button 1 to validate the selection, the display shows “Li“ again.
- When pressing button 1 again, the display will show “FiLt“ (Filter = digital filter).
- Use button 2 and button 3 to select the desired filter [in sec.].
Selectable values: 0.01 ... 2.00 sec.
Explanation: this digital filter is a digital replica of a low pass filter.
Note: when using the input signal 0-50 mV a filter value of at least 0.2 is recommended
- Press button 1 to validate your value, the display shows “FiLt“ again.
Now your device is adjusted to your signal source. Now the only thing left to do is to adjust the outputs of
the device. - When pressing button 1 again, the display shows “outP“. (output)
For configuring the outputs of the device, please follow the instructions given in chapter 6.9.
6.4 Measuring temperature (Pt 100, Pt 1000 RTD probes and thermocouples type J, K, N, S or T)
This chapter describes how to configure the device for temperature measuring with the help of external
platinum RTD probes or thermocouple probes. This instruction demands that you selected “t.res“ or “t.tc“
as your desired input type like it is explained in chapter 6.2. The device has to display “InP“.
- When pressing button 1 the display shows “SEnS “.
- Use button 2 or button 3 (middle or right button) to select your desired input signal.
Display
Input signal
(thermocouples)
Notes
niCr
NiCr-Ni (type K)
Meas. range: -270 ... +1350 °C (-454 ... + 2462 °F)
S
Pt10Rh-Pt (type S)
Meas. range: -50 ... +1750 °C (- 58 ... + 3182 °F)
n
NiCrSi-NiSi (type N)
Meas. range: -270 ... +1300 °C (-454 ... + 2372 °F)
J
Fe-CuNi (type J)
Meas. range: -170 ... + 950 °C (-274 ... + 1742 °F)
t
Cu-CuNi (type T)
Meas. range: -270 ... + 400 °C (-454 ... + 752 °F)
- Validate the selected input signal by pressing button 1. The display shows “SEnS“ again.
- Press button 1 again, the display will show “dP“ (decimal point, for the resolution).
This menu parameter is only available at input signal Pt 100 and Pt 1000!
Display
Input signal
(RTD)
Notes
P100
Pt100 (3-wire)
Meas. range: -50.0 ... +200.0 °C (-58.0 ... + 392.0
°F)
Meas. range: -200 ... + 850 °C (-328 ... + 1562 °F)
1000
Pt1000 (2-wire)
Meas. range: -100.0 ... +200.0 °C (-148.0 ... +
392.0 °F)
Meas. range: -200 ... + 850 °C (-328 ... + 1562 °F)
F,LT
OVTP
SENS
DP

E44.X.01.6C-04 Mounting- and Operating Manual GIR 300 page 18 of 34
- Use button 2 and button 3 to select whether the temperature is displayed with 0.1° or 1°.
- Validate the selected decimal position by pressing button 1. The display shows “dP“ again.
- Press button 1 again, the display will show “Unit“ (the unit you want to display).
- Use button 2 and button 3 to select whether you want to display °C or °F.
- Press button 1 to validate the selected unit, the display shows “Unit“ again.
- Press button 1 again, the display will be showing “FiLt“ (Filter = digital filter).
- Use button 2 and button 3 for setting the desired filter-value [in sec.].
Selectable values: 0.01 ... 2.00 sec.
Explanation: this digital filter is a digital replica of a low pass filter.
- Press button 1 to validate your selection, the display shows “FiLt“ again.
Now your device is adjusted to your signal source. Now the only thing left to do is to adjust the outputs of
the device. - When pressing button 1 again, the display shows “outP“. (output)
For configuring the outputs of the device, please follow the instructions shown in chapter 6.9.
For setting the offset and for setting the slope-adjustment, please follow the instructions given in chapter 8.
6.5 Measuring of frequency (TTL, switching-contact)
This chapter describes how to configure the device for measuring frequency.
This instruction demands that you selected “FrEq“ as your desired input type like it is explained in chapter
6.2. The device has to display “InP“.
- When pressing button 1 the display will show “SEnS“.
- Use button 2 or button 3 (middle or right button) to select the desired input signal.
Display
Input signal
Notes
ttL
TTL-signal
nPn
Switching contact, NPN
For direct connection of a passive switch-
ing contact (e.g. push button, relay) or
Transmitter with NPN output.
A pull-up-resistor is internally connected.
Hint: when using push-buttons or relays, they
must be bounce-free!
PnP
Switching contact, PNP
For direct connection of a transmitter with
PNP output.
A pull-down-resistor is internally con-
nected.
Hint: For the connection of a frequency-transmitter, please follow the instructions given in chapter.
When connecting a switching-contact-transmitter with increased frequency range (= with external
circuitry) you have to select TTL as your desired input signal.
- Validate your selected input signal by pressing button 1. The display shows “SEnS“ again.
- When pressing button 1 again, the display will show “Fr.Lo“ (frequency low = lower frequency
range limit).
- Use button 2 and button 3 to select the lowest frequency that may occur when measuring.
- Press button 1 to validate your selection. The display shows “Fr.Lo“ again.
UN,T
F,LT
OVTP
SENS
FR.LO

E44.X.01.6C-04 Mounting- and Operating Manual GIR 300 page 19 of 34
- When pressing button 1 again, the display will show “Fr.Hi“ (frequency high = upper frequency
range limit).
- Use button 2 and button 3 to select the highest frequency that may occur when measuring.
- Press button 1 to validate your selection. The display shows “Fr.Hi“ again.
- When pressing button 1 again, the display will show “dP“ (decimal point).
- Use button 2 and button 3 to select the desired decimal point position.
- Press button 1 to validate your selection. The display shows “dP“ again.
- When pressing button 1 again, the display will show “di.Lo“ (display low = display at lower frequency
range limit).
- Set the value the device shall display at the lower frequency range limit by pressing button 2 or
button 3.
- Press button 1 to validate your selection. The display shows “di.Lo“ again.
- When pressing button 1 again, the display will show “di.Hi“ (display high = display at upper frequency
range limit).
- Set the value the device shall display at the upper frequency range limit by pressing button 2 or
button 3.
- Press button 1 to validate your selection. The display shows “di.Hi“ again.
- When pressing button 1 again, the display will show “Li“ (limit = measuring range limitation).
- Use button 2 and button 3 to select the desired measuring range limitation.
Display
Measuring range limit
Notes
off
Inactive
Exceeding of the measuring-frequency is
tolerable until you reach the maximum
measuring range limit.
on.Er
Active, (displays error)
The measuring range is exactly bounded
by the selected frequency-measuring-
range-limit. When exceeding or shortfal-
ling of the limit the device will display an
error message.
on.rG
Active, (displays the selected limit)
The measuring range is exactly bounded
by the selected frequency-measuring-
range-limit. When exceeding or shortfal-
ling of the limit the device will display the
lower or upper display-range-limit.
[e.g. for humidity: when shortfalling or
exceeding the device will display 0% or
100%]]
Hint: When exceeding the maximum range limit (10 kHz) independently from the limit setting an error message
will be displayed (“Err.1“).
- Press button 1 to validate your selection. The display shows “Li“ again.
- When pressing button 1 again, the display will show “FiLt“ (Filter = digital filter).
- Use button 2 and button 3 to select the desired filter value [in sec.].
Usable values: 0.01 ... 2.00 sec.
Explanation: this digital filter is a digital replica of a low pass filter.
- Press button 1 to validate your selection. The display shows “FiLt“ again.
Now your device is adjusted to your signal source. The only thing you left do is to adjust the outputs of the
device. - When pressing button 1 again, the display will show “outP“. (Output)
For configuring the outputs of the device, please follow the instructions shown in chapter 6.9.
DP
FR.K,
D,.LO
D,.K,
L,
F,LT
OVTP

E44.X.01.6C-04 Mounting- and Operating Manual GIR 300 page 20 of 34
6.6 Measuring of rotation speed (TTL, switching-contact)
This chapter describes how to configure the device for measuring rotation speed.
This instruction demands that you selected “rPn“ as your desired input type like it is explained in chapter
6.2. The device has to display “InP“.
- When pressing button 1 the display will show “SEnS“.
- Use button 2 or button 3 (middle or right button) to select the desired input signal.
Display
Input signal
Notes
ttL
TTL-signal
nPn
Switching contact, NPN
For direct connection of a passive switch-
ing contact (e.g. push button, relay) or
Transmitter with NPN output.
A pull-up-resistor is internally connected.
Hint: when using push-buttons or relays, they
must be bounce-free!
PnP
Switching contact, PNP
For direct connection of a transmitter with
PNP output.
A pull-down-resistor is internally con-
nected.
Hint: For the connection of a frequency-transmitter, please follow the instructions given in chapter 5.3.6.
When connecting a switching-contact-transmitter with increased frequency range (= with external
circuitry) you have to select TTL as your desired input signal.
- Validate your selected input signal by pressing button 1. The display shows “SEnS“ again.
- When pressing button 1 again, the display will show “diu“ (divisor).
- Use button 2 and 3 to select your desired divisor.
Set the divisor to the pulses per rotation the transmitter supplies.
- Press button 1 to validate your selection. The display shows “diu“ again.
- When pressing button 1 again, the display will show “dP“ (decimal point).
- Use button 2 and button 3 to select the desired decimal point position.
Use the decimal point position to change the resolution of your measurement.
The more the decimal point position is on the left, the finer the resolution will become. Please
note that you lower the maximum value that can be displayed, either.
Example: your engine runs with 50 rotations per minute.
With no decimal point the device will display something like 49 –50 –51, the maximum
value that can be displayed is 9999 rotations per minute.
With the decimal point position on --.-- the device will display something like 49.99 –50.00 –
50.01, but the maximum value that can be displayed is 99.99 rotations per minute.
- Press button 1 to validate your selection. The display shows “dP“ again.
Now your device is adjusted to your signal source. The only thing left to do is to adjust the outputs of the
device. - When pressing button 1 again, the display will show “outP“. (Output)
For configuring the outputs of the device, please follow the instructions shown in chapter 6.9.
SENS
D,V
DP
OVTP
This manual suits for next models
1
Table of contents
Popular Control Panel manuals by other brands

Carrier
Carrier INFINITY ZONING CONTROL installation instructions
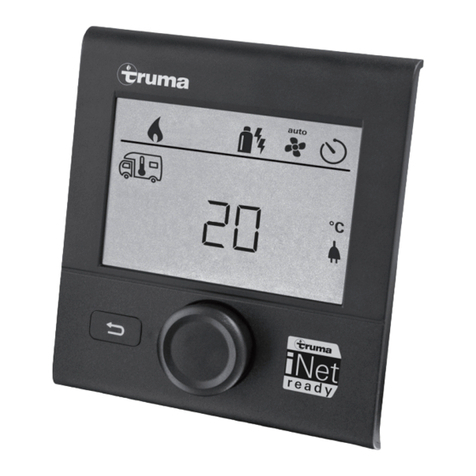
Truma
Truma CP plus VarioHeat operating instructions

Well SEC
Well SEC WL1014 user manual
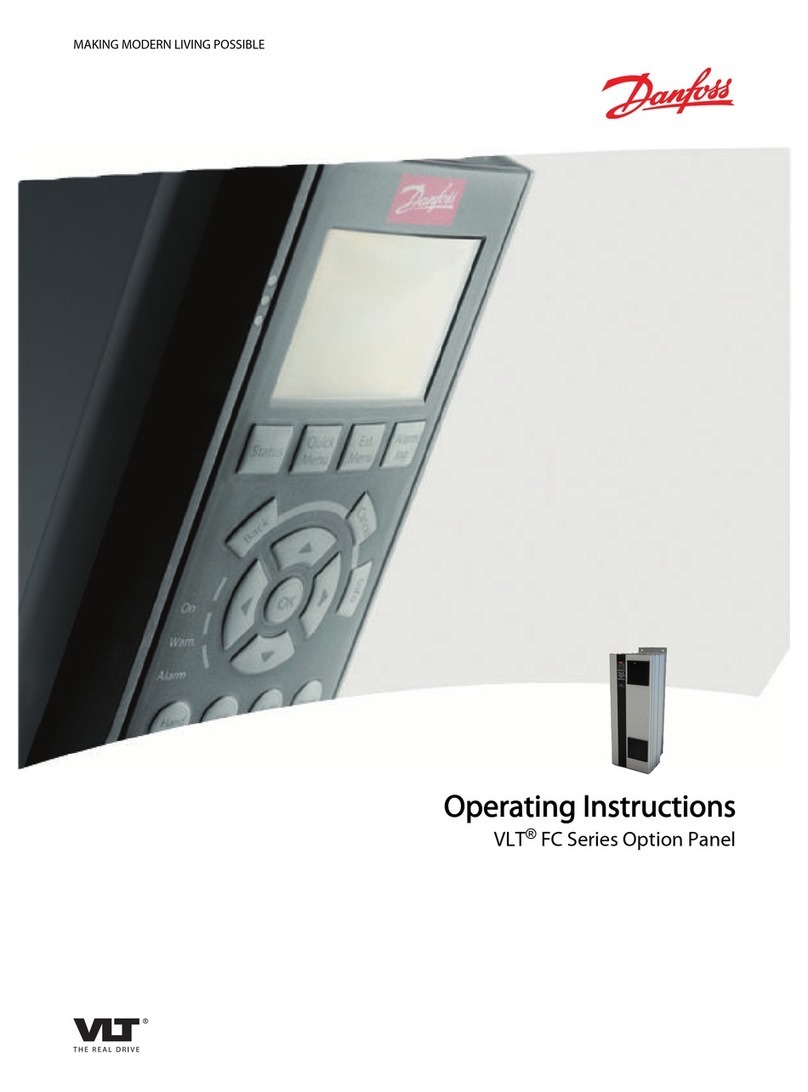
Danfoss
Danfoss VLT FC Series operating instructions
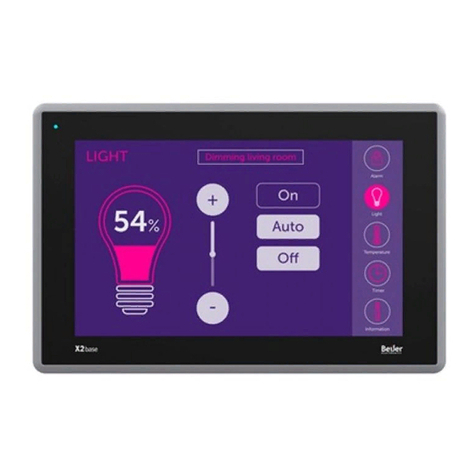
Beijer Electronics
Beijer Electronics X2 control user guide
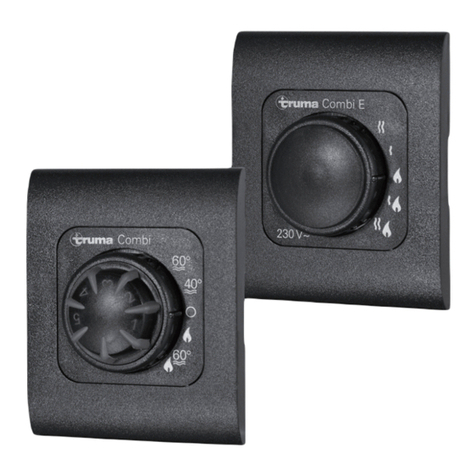
Truma
Truma CP E classic Operating instructions & installation instructions