Gis GCH250 Series User manual

INSTRUCTION MANUAL
Electric chain hoist GCH 250/500 • GCH 1000 • GCH 1600/2000/2500
SWISS QUALITY
GCH
GCHK
GCHS
GCHH
GCHR
GIS CHAIN HOIST
07.11 Original document 9401.9000.1.doc

GIS CHAIN HOIST SWISS QUALITY2
Table of contents 0 General information..................................................................4
0.1 General safety information .................................................................................. 4
0.1.1 Safety and hazard precautions............................................................................ 4
0.2 General safety specifications and procedures..................................................... 4
0.2.1 Warning paint / Marking / Danger signs .............................................................. 4
0.3 Special safety directions...................................................................................... 4
0.4 Notes on hazard protection ................................................................................. 5
0.4.1 Hazards caused by mechanical influences ......................................................... 5
0.4.2 Hazards caused by electrical energy / power supply .......................................... 5
0.4.3 Sound level (SPL)................................................................................................ 6
0.5 Technical status .................................................................................................. 6
0.5.1 Technical data ..................................................................................................... 6
0.5.2 Recurrent checks................................................................................................. 6
0.5.3 Warranty .............................................................................................................. 7
0.6 Operational parameters....................................................................................... 7
0.6.1 Directions for using the instruction manual ......................................................... 7
1 Description ................................................................................8
1.1 Operating conditions............................................................................................ 8
1.2 General description ............................................................................................. 9
1.3 Special models .................................................................................................. 10
2 Start-up ....................................................................................11
2.1 Transport and assembly.................................................................................... 11
2.2 Connection ........................................................................................................ 11
2.2.1 Electrical connection ......................................................................................... 11
2.2.2 Load chain......................................................................................................... 12
2.2.3 Limit switch........................................................................................................ 14
2.2.4 Chain bucket...................................................................................................... 15
3 Service and maintenance.......................................................15
3.1 General regulations for service and maintenance work .................................... 15
3.2 Service and maintenance.................................................................................. 16
3.2.1 Maintenance overview....................................................................................... 16
3.2.2 Service overview ............................................................................................... 16
3.2.3 Brake system..................................................................................................... 16
3.2.4 Load chain......................................................................................................... 17
3.2.5 Limit stop assembly........................................................................................... 17
3.2.6 Gearbox............................................................................................................. 17
3.2.7 Slip clutch .......................................................................................................... 17
3.2.8 Suspension parts............................................................................................... 18
3.3 Ordering spare parts.......................................................................................... 18
4 Measures for obtaining a safe period of operation.............18
4.1 Determining the actual utilization period S ........................................................ 18
4.2 General overhaul ............................................................................................... 18
5 Appendix .................................................................................19
5.1 Technical data ................................................................................................... 19
5.2 EC Declaration of conformity............................................................................. 21
5.3 EC Declaration of incorporation......................................................................... 22

GIS CHAIN HOIST SWISS QUALITY 3
Spare parts / Ordering spare parts The correct order numbers for original spare parts can be obtained from the relevant
spare parts list. Please ensure that you have the following data on your chain hoist to
hand. This will enable the correct spare parts to be supplied without delay.
Electric chain hoist type : ..........................................................................................
Manufacture number : ..........................................................................................
Year of manufacture : ..........................................................................................
Load capacity : ..........................................................................................
Original spare parts for the electric chain hoist can be acquired from the following
addresses:
1. Manufacturer
GIS AG
Hebe- und Fördertechnik
Luzernerstrasse 50
CH-6247 Schötz
Tel. +41 (0)41 984 11 33
Fax +41 (0)41 984 11 44
www.gis-ag.ch
2. Agent
............................................................................................................................................
............................................................................................................................................
............................................................................................................................................
............................................................................................................................................
............................................................................................................................................
............................................................................................................................................

GIS CHAIN HOIST SWISS QUALITY4
0 General information
0.1 General safety information
0.1.1 Safety and hazard precautions
0.2 General safety specifications
and procedures
0.2.1 Warning paint / Marking /
Danger signs
The following symbols and terms are used in this instruction manual for safety and
hazard instructions:
DANGER !
Non-compliance, either in part or full, with operating instructions marked
with this symbol can result in serious personal injury or even death.
Danger notices must be strictly complied with.
CAUTION !
Non-compliance, either in part or full, with operating instructions marked
with this symbol can result in major damage to machinery, property or
material.
Cautionary notices must be strictly adhered to.
NOTE
Following the instructions marked by this symbol will lead to more effective
and straightforward operation.
"Note" directions make work easier.
The instruction manual for the electric chain hoist must always be available within the
operating area of the hoist. The instructions mentioned in this manual must be strictly
adhered to.
Furthermore, supplementary to the instruction manual, the statutory regulations
governing general accident prevention and environmental protection are to be enforced.
Operating and service personnel must have read and understood the operating
instructions, in particular the safety instructions, before commencing work. Protective
equipment must be made available for operating and service personnel and worn at all
times.
The operator or his representative is responsible for supervising operating personnel
and ensuring they are aware of the hazards and safety implications of working with the
electric hoist.
Lubricate chain....................figure 0-1
CE symbol...........................figure 0-2
Model plate .........................figure 0-3
Data plate............................figure 0-4
Voltage................................figure 0-5
Figure 0-1 Figure 0-2 Figure 0-3 Figure 0-4 Figure 0-5
0.3 Special safety directions
Transport and assembly:
Electric chain hoists, single parts and large components should be carefully affixed
to suitable and technically acceptable hoisting apparatus / load lifting members
Connection:
Connection work is only to be performed by personnel specifically designated and
trained for the job
Start-up / operation:
Before initial start-up, as well as daily start-up, carry out a visual check and carry out
the predefined user-checks routine
Only operate the electric chain hoist if the protective and safety equipment provided
is ready and working
Damage to the electric chain hoist and changes in its operational characteristics
must be reported immediately to the person responsible
After use, or when in a non-operational mode, the chain hoist should be secured
against unauthorised and unintentional use
Refrain from hazardous procedures
See also operational parameters (chapter 0.6)

GIS CHAIN HOIST SWISS QUALITY 5
0.4 Notes on hazard protection
0.4.1 Hazards caused by mechanical
influences
0.4.2 Hazards caused by electrical
energy / power supply
Cleaning / service / repair / maintenance / refitting:
Use the working platforms and ladders provided for assembly work above body
height
Do not use machine parts for this purpose
Check electrical cables for damage or wear
Ensure any oils or other agents used are discharged, collected and disposed of
safely and in an environmentally sound manner
Reassemble and check safety apparatus that has been disassembled for servicing
or repairing the hoist once service and repair work has been completed
Adhere to predefined testing and service intervals specified in the instruction
manual
Follow the directions in the instruction manual regarding exchanging parts
Operating personnel should be informed before commencing special or refitting
work
Secure the repair working area
Prevent the electric chain hoist from being inadvertently switched on during service
or repair work
Erect warning signs
Disconnect the power cable and ensure it cannot be inadvertently switched on again
Retighten screw connections that have been loosened for repair or service work
Replace parts that are not reusable, such as O-rings, gaskets, self locking nuts,
split-pins and washers
Shut down / storage:
Clean and preserve (lubricate/grease) the chain hoist before long periods of
inactivity or storage
Hazardous areas must be clearly marked by warning signs and cordoned off. It must be
ensured that warnings regarding hazardous areas are given due attention.
Hazards can stem from:
incorrect application
not following safety directions properly
not carrying out test and service work thoroughly
Physical injury:
DANGER !
Unconsciousness and injury through:
crushing, shearing, cutting and twisting
drawing in, ramming, piercing and rubbing
slipping, stumbling and falling
Causes:
crush, shear and twist area
parts rupturing or bursting
Safety options:
keep floor, equipment and machinery clean
eliminate leakages
observe the required safety distance
Work on electrical apparatus or machinery may only be performed by qualified
electricians or persons under the supervision and guidance of qualified electricians,
in accordance with predefined electrotechnical regulations.
Physical injury:
DANGER !
Death from electrical shock, injury and burns through:
contact
faulty insulation
faulty servicing or repair work
short circuit

GIS CHAIN HOIST SWISS QUALITY6
0.4.3 Sound level (SPL)
0.5 Technical status
0.5.1 Technical data
0.5.2 Recurrent checks
Causes:
contact with, touching or standing too close to uninsulated power and voltage supply
terminals
use of uninsulated tools
exposed electricity supply terminals following insulation failure
inadequate safety checks following repair work
incorrect fusing
Safety options:
isolate machinery and equipment designated for repair or service work before
commencing such work
first check isolated parts for voltage
regularly check electrical fittings
replace loose or damaged cables immediately
always replace blown fuses with fuses of the correct value
avoid contact with or touching live terminals
only use insulated tools
Tests on the chain hoist sound level are performed at a range of 1, 2, 4, 8 and 16
metres from the centre of the chain hoist motor to the measuring device.
Measurement of SPL according to DIN 45 635.
The SPL was measured:
a) during operation of electric chain hoists on factory site
b) during open-air operation
Table 0-1 Sound level
Types Measuring
distance
1 m 2 m 4 m 8 m 16 m
Measurement dBA
GCH 250/500 a)
b)
75
75
72
69
69
63
66
57
63
51
GCH 1000 a)
b)
72
72
69
66
66
60
63
54
60
48
GCH 1600/2000/2500 a)
b)
75
75
72
69
69
63
66
57
63
51
The present document was written in 2010. It corresponds to directive 2006/42/EC of
the European Parliament and of the Council of 17 May 2006.
0.5.1.1 Models GCH ..............................table 0-2, page 19
0.5.1.2 Models GCHK............................table 0-3, page 19
0.5.1.3 Models GCHS............................table 0-4, page 20
0.5.1.4 Models GCHHK .........................table 0-5, page 20
0.5.1.5 Models GCHHTD.......................table 0-6, page 20
0.5.1.6 Models GCHR ...........................table 0-7, page 20
Each device/ unit operator should adequately note all checks, maintenance and
inspections performed in the log book, and have these confirmed by the competent
person in charge.
Incorrect or missing entries will lead to forfeiture of the manufacturer's warranty.
CAUTION !
Equipment and cranes should be periodically tested by an expert. Basically,
visual and functional checks should be performed to determine the
condition of components as regards damage, wear, corrosion or other
modifications. In addition, safety equipment is assessed for completeness
and efficiency. It may be necessary to dismantle the equipment under
inspection to correctly assess expendable parts.
CAUTION !
Suspension apparatus must be inspected over its entire length, including
covered or hidden parts.
CAUTION !
All periodical inspections should be arranged by the operator.

GIS CHAIN HOIST SWISS QUALITY 7
0.5.3 Warranty
0.6 Operational parameters
0.6.1 Directions for using the
instruction manual
the warranty is void if the installation, operation, testing or maintenance is not
carried out according to these instructions
troubleshooting and repair under warranty may only be carried out by qualified
persons and only after consultation and agreement with the manufacturer / supplier.
Any modifications to the product or the use of non-original replacement parts will
void the warranty
Electric chain hoists of the series GCH are hoists of differing load capacities. They can
be installed as stationary or mobile units. Electric chain hoists are manufactured in
accordance with the latest technical developments and recognised safety standards,
and are tested for safe operation by the manufacturer.
Electric chain hoists are approved by various international institutes such as BG and
others.
Electric chain hoists of the above series may only be used when in an acceptable
technical condition, in accordance with their operating parameters, by trained personnel
in a safe and responsible manner.
The operational parameters of the electric chain hoist also encompass compliance with
the pre-defined operating, service and maintenance requirements laid down by the
manufacturer.
The operational parameters do not include:
exceeding the defined load capacity
pulling the load diagonally (see figure 0-5)
heaving, pulling or dragging the load
transporting persons
transporting loads when personnel are underneath
standing under suspended loads (see figure 0-6)
transporting excessive loads
pulling on the control cable
failing to observe the load hook constantly
running the chain over edges
failing to observe the load constantly
allowing the load to fall due to a slack chain
use at temperatures below -15° C or above +50° C
use in an explosive environment
See also chapter 0.3.
Figure 0-5 Figure 0-6
Inching operations, ground mooring and driving against the limit switches should be
avoided. The manufacturer accepts no responsibility for damage to equipment and third
parties ensuing from such action.
This instruction manual includes the following chapters:
0 General information 4 Measures for obtaining a safe
1 Description period of operation
2 Start-up 5 Appendix
3 Service and maintenance

GIS CHAIN HOIST SWISS QUALITY8
1 Description
1.1 Operating conditions
Supplementary to the instruction manual, the following documentation from the operator
must be noted:
Declaration of conformity
Log book
Spare parts list(s)
Circuit diagrams
Page and figure numeration:
The pages are consecutively numbered. Blank pages are not numbered, however are
calculated together with the consecutive pages.
Figures are numbered consecutively by chapter.
Example:
Figure 3-1 means: in chapter 3, figure 1
General:
The GCH series consist of the following models:
GCH, GCHK, GCHS, GCHHK, GCHHTD, GCHR
Classification according to application requirements:
Electric chain hoists and travelling gears are classified according to the following
regulations into ISO Groups:
DIN EN 14492-2
DIN 15400 (load hook)
FEM calculation regulations for series lifting equipment
(chain drive, motor, full load-life span)
ISO 4301-1: D (M3) = 400 h
Remarks about general revision (see chapter 4)
There is differing coefficient data for the ISO Groups that must be adhered to in
operation.
CAUTION !
The travelling gear is always classified as the same ISO Group as the
corresponding electric chain hoist.
NOTE
The ISO Group registration number of the electric chain hoist can be found
on the data plate.
The manufacturer will only guarantee the safety and lasting operation of the electric
chain hoist when used for applications that fall within its valid ISO Group coefficient
data.
Before the first start-up, the user must estimate according to the features in table 1-1,
which of the four types of load is applicable to the use of the electric chain hoist during
its whole service life. Table 1-2 shows standard values for the operating conditions of
the ISO Groups depending on the type of load and the time of operation.
Ascertaining the correct type of application for an electric chain hoist:
Either the running time or expected type of load can be used as a basis for ascertaining
the correct type of application for the electric chain hoist.
CAUTION !
Before starting up the electric chain hoist for the first time, it must be
determined with which of the load types shown in table 1-1 the electric chain
hoist is to operate. Assignment to a load type or a load collective (k) applies
for the entire operational life of the equipment and may not be altered for
operational safety reasons.
Example 1: Ascertaining permissible running time of the electric chain hoist:
An electric chain hoist of the ISO Group M4 is to be used for medium stress load tasks
throughout its entire service life. This corresponds to load type <3 heavy> (see table
1-1). According to the values in table 1-2, the electric chain hoist should not be used for
longer than 0.5 - 1 hour per working day.

GIS CHAIN HOIST SWISS QUALITY 9
Example 2: Ascertaining permissible load type:
An electric chain hoist of the ISO Group M5 is to be used for approximately 6 hours per
working day, throughout its complete service life. Consequently the electric chain hoist
should be operated in accordance with the characteristics of the load type <1 light> (see
table 1-1).
Table 1-1 Load collectives
Load type 1
light
k < 0.50
k = 0.50
Load type 2
medium
0.50 < k < 0.63
k = 0.63
Load type 3
heavy
0.63 < k < 0.80
k = 0.80
Load type 4
very heavy
0.80 < k < 1.00
k = 1.00
% of bearing
capacity
% of bearing
capacity
% of bearing
capacity
% of bearing
capacity
% of running time % of running time % of running time % of running time
Full load by way of an
exception, however,
predominantly
low loads
Frequently fully loaded,
however continuously
lightly loaded
Frequently fully loaded,
continuous average
loading
Regularly fully loaded
k = Load collective (type of load)
Table 1-2 Operating conditions
ISO Group according
to ISO 4301-1
M3 M4 M5 M6 M7
Load collective Average running time per working day [h]
1 - light
k < 0.50
up to
2 2 - 4 4 - 8 8 - 16 over
16
2 - medium
0.50 < k < 0.63
up to
1 1 - 2 2 - 4 4 - 8 8 - 16
3 - heavy
0.63 < k < 0.80
up to
0.5 0.5 - 1 1 - 2 2 - 4 4 - 8
4 - very heavy
0.80 < k < 1.00
up to
0.25
up to
0.5 0.5 - 1 1 - 2 2 - 4
1.2 General description
Figure 1-1
10 40 50
100
0~
40
16.7 50
100
0~
40
16.716.7
70
50 50
100
33
10
90
100
80
1
4
3
2 5
6
7
1 Housing
2 Motor and brake
3 Rotor shaft with integrated
slip clutch
4 Limit switch
5 Electrical controller
6 Chain drive
7 Gearbox
Control switch
single fall double fall

GIS CHAIN HOIST SWISS QUALITY10
The electric chain hoist meets the requirements of the EC Machinery Directive and the
relevant EN and FEM standards.
Housing and cover are made of a sturdy aluminum die casting. Fins on the motor
ensure optimum cooling. The chain box can be attached to the compactly constructed
housing. A drilled hole is provided for both the power supply cable gland and the control
cable. The lugs, or optionally the suspension hooks, are attached to the flange ring.
GIS electric chain hoists are driven by asynchronous motors. For two-speed models a
pole switching version of the motor is fitted.
The braking system consists of a DC-operated spring loaded brake. When there is no
current, the pressure spring generates the braking torque.
For functional reasons, the slip clutch is installed in front of the brake system and
integrated into the rotor shaft. It protects the hoist from overload and takes on the
function of an emergency end stop for the highest and lowest hook positions.
A gear-type limit switch is fitted to limit the highest and lowest hook position. As an
option, emergency stop contacts with positive separation can be retrofitted downstream.
Electric chain hoists are fitted with a 42 V contactor control as standard. The emergency
stop contactor that is usually installed separates all three mains power phases when the
red button is pressed.
The high-strength round steel chain meets the requirements of grade DAT (8SS) to DIN
EN 818-7. Sprocket and pulley are hardened. The load hook, which complies with DIN
15400, is fitted with a safety latch.
The two-or three-stage, closed spur gear units are usually helically cut. The gears are
mounted on roller bearings and run greased.
The standard equipment fitted to the electric chain hoist includes a control switch (up/
down with emergency stop).
1.3 Special models
Figure 1-2
Low headroom hoist GCHK
Synchron hoist GCHS
Handy chain hoist GCHHK
Handy double telescopic
hoist GCHHTD

GIS CHAIN HOIST SWISS QUALITY 11
2 Start-up
2.1 Transport and assembly
2.2 Connection
2.2.1 Electrical connection
DANGER !
Mechanical adjustments may only be performed by authorised specialists.
CAUTION !
Operating staff must carefully read the operating instructions of the electric
chain hoists before its initial operation and carry out all checks. Only when
safe operation has been established may the device be put into operation.
Unauthorised persons may not operate the device or carry out work with it.
The safety directions for handling with loads should be followed (see chapter 0.3) when
transporting and assembling the electric chain hoist.
Electric chain hoists must be assembled by qualified staff, always bearing in mind the
accident prevention directions in chapter 0.2. Before assembly the electric chain hoist
must be stored in an enclosed room or covered area.
Should the electric chain hoist be destined for operation outdoors, then it is
recommended that a protection cover is erected to shield it from the effects of the
weather.
Wherever possible, the electric chain hoist should be transported in its original
packaging. The goods delivered should be checked for completeness and the
packaging disposed of in an environmentally sound manner. It is recommended that the
electric chain hoist is assembled and connected on-site by our qualified customer
service personnel.
DANGER !
Electrotechnical adjustments may only be performed by authorised
specialists.
The mains connection cable, the mains connection fuse and the main switch for
connecting the electric chain hoist to the mains power supply must be installed
beforehand by the customer.
A 4-wire cable with a PE protective conductor is needed to provide the power supply for
three-phase models. A 3-wire cable with a protective conductor is adequate for single-
phase models. The length and cross-section must be appropriate for the power
consumption of the electric chain hoist.
Before connecting the electric chain hoist, check whether the operating voltage and
frequency that are specified on the name plate correspond to the available power
supply
Remove cover on electrical side
Insert connecting cable with M25 x 1.5 screwed cable connection into hole at side
and connect to terminals L1, L2, L3 and PE in accordance with supplied circuit
diagram (see figure 2-1)
Insert control cable with M20 x 1.5 screwed cable connection through hole in
underside of housing and connect to terminals 1, 2, 3, 4 and 10 (see figure 2-2)
Attach strain relief to housing (see figure 2-3)
CAUTION !
The control switch must be attached to the strain relief cord and not to the
cable.
Figure 2-1 Figure 2-2 Figure 2-3
Not Aus
1 speed
2 speed
1 speed
2 speed
1 2
43
34
43
34
321 54
L3
L2
L1
PE
PE
1
2
1
2
3
4
10
5
6
7
1
2
3
4
1
0

GIS CHAIN HOIST SWISS QUALITY12
2.2.2 Load chain
DANGER !
The protective conductor should not carry any power. With motor carriage
operation, the power supply is enclosed in a terminal box of the drive motor.
With the installation of a motor protector, the load plate voltage of the
electric chain hoist must be observed.
CAUTION !
Checking direction of rotation: If the direction of rotation does not
correspond to the button symbols on the control switch, power supply
wires L1 and L2 must be swapped round
Inching operations on single-phase models can cause interference
NOTE Figure 2-4
Open the terminal that is used in
accordance with figure 2-4.
CAUTION !
Only use original chains
Welded seam of the chain links must face inward on the chain wheel
(see figure 2-5)
The gearbox limit switch must be mechanically disabled in order to pull
in the chain, see chapter 2.2.3
Before start-up and during operation the load chain must be oiled along its full length.
Oil must constantly be present on the internal, contacting and rubbing surfaces of the
chain links. Lubrication is carried out by submersion or with an oil can, using a creeping
gear oil.
The end of the chain should be attached to a flexible piece of wire (1) and fed through
the chain wheel (2) of the electric chain hoist. Through short switching impulses, the
chain (3) will be housed correctly in accordance with figure 2-5.
The lifting height must be adjusted such that the hook fittings lie on the ground in the
lowest hook position.
Figure 2-5
8-9 mm
2
3
1

GIS CHAIN HOIST SWISS QUALITY 13
Figure 2-8
Single fall operation: The load hook (1) is connected to the chain using a shim
(2). Bolt (3) installation is important for power transmission
(see figure 2-6).
CAUTION !
Pay attention to correct arrangement of suspension (see figure 2-7)! Grease
the bearings thoroughly.
Figure 2-6 Figure 2-7
Double fall operation: Connect load side of chain end to chain retainer (3) and fix in
housing guide rail. Assemble bottom sheave (1) with load hook
(2) in accordance with figure 2-9.
CAUTION !
Pay attention to correct arrangement of suspension (see figure 2-10)!
Do not twist chain lengthwise (see figure 2-8)! Grease the bearings
thoroughly.
Chain end: The chain end must be attached to the housing in accordance with figure 2-
11.
The section of chain after the end stop (1) must be adjusted to the height of the chain
bucket. The length of the section of chain must be selected so that the end stop lies on
the floor of the magazine when the chain runs into it (see figure 2-11).
Figure 2-9 Figure 2-10 Figure 2-11
3
2
1
1
2
3
1
Types k1 [mm]
GCH 250/500 41.0
GCH 1000 43.0
GCH 1600/2000/2500 49.0
... kg
k1
... kg
k2
Types k2 [mm]
GCH 250/500 52.0
GCH 1000 62.0
GCH 1600/2000/2500 69.0

GIS CHAIN HOIST SWISS QUALITY14
2.2.3 Limit switch The electric chain hoist is equipped with a gearbox limit switch as standard. This is also
suitable for normal limit switch operation with a high degree of accuracy. The operation
of the limit switches (highest and lowest hook position) must be checked during
start-up.
Three different transmissions are available that are adapted to the lift:
GCH 250/500
Transmission Colour Single fall lift [m] Double fall lift [m]
i = 1:1 black 20 10
i = 1:3 yellow 60 30
i = 1:6 blue 120 60
GCH 1000
Transmission Colour Single fall lift [m] Double fall lift [m]
i = 1:1 black 30 15
i = 1:3 yellow 80 40
i = 1:6 blue 180 90
GCH 1600/2000/2500
Transmission Colour Single fall lift [m] Double fall lift [m]
i = 1:1 black 36 18
i = 1:3 yellow 110 55
i = 1:6 blue 220 110
Description of settings (see figure 2-12):
Before pulling in the chain or changing the chain, the gearbox limit switch must be
mechanically disabled by securing the rocker (1)
Pull in the chain
Move to highest hook position, rotate red ratchet wheel (front) (2) to switching cam
of top limit switch (3); (rotate clockwise for higher hook position and anticlockwise
for lower hook position)
Activate rocker, move to lowest hook position, rotate green switching wheel (rear)
(4) to switching cam of bottom limit switch (5); (rotate anticlockwise for higher hook
position and clockwise for lower hook position)
Activate rocker (must engage in switch wheel)
Check operation of limit switch; the end stop and the hook fittings must not touch
the housing
Figure 2-12
3
2
1
4
5

GIS CHAIN HOIST SWISS QUALITY 15
2.2.4 Chain bucket Move chain out at load side until limit switch is activated
Attach free end of chain to housing (see chapter 2.2.2)
Attach chain bucket and allow chain to run in (see figure 2-13)
DANGER !
All steel plate chain buckets must be equipped with an additional wire cable
with a minimum diameter of 2 mm (see figure 2-14).
Figure 2-13 Figure 2-14
3 Service and maintenance
3.1 General regulations for service
and maintenance work
Operating failures in electric chain hoists affecting the safe operation of the device
should be remedied immediately.
CAUTION !
Maintenance and repair work on the electric chain hoist may only be carried
out by qualified and trained personnel.
CAUTION !
If the operator performs maintenance work on an electric chain hoist on his
own account, the type of maintenance performed together with the date
carried out must be entered in the log book.
Alterations to, as well as modifications and supplements to electric chain hoists which
may affect safety must be authorized by the manufacturer in advance. Structural
alterations to chain hoists not authorized by the manufacturer exempt the manufacturer
from liability in case of damage.
Material warranty claims will only be recognized if solely manufacturer’s genuine spare
parts have been used.
We explicitly wish to point out that those original parts and accessories not supplied on
our behalf cannot be inspected or released by us.
General:
Service and maintenance are preventive measures designed to preserve the full
functionality of electric chain hoists. Non-compliance with service and maintenance
routines can result in reduction in the useful function of and/ or damage to electric
chain hoists.
Service and maintenance work should be carried out at the predefined time intervals,
in accordance with the instruction manual (table 3-1 and 3-2).
... kg

GIS CHAIN HOIST SWISS QUALITY16
3.2 Service and maintenance
3.2.1 Maintenance overview
During service and maintenance work, general accident prevention directions, special
safety directions (chapter 0.3) as well as hazard protection instructions (chapter 0.4)
should be followed.
DANGER !
Service and maintenance work should only be performed on unloaded
electric chain hoists. The main switch must be off. The lower sheave or
hook fittings must be lying on the floor or a maintenance platform.
Maintenance work encompasses visual checks and cleaning routines. Service work
includes additional functional checks. During the functional checks, all securing
elements and cable clamps must be checked for secure seating.
Cables must be inspected for dirt, discoloration and arc spots.
CAUTION !
Used operating materials (oil, lubricants, etc.) should be safely collected
and disposed of in an environmentally friendly manner.
Service and maintenance intervals are defined as follows:
t ............ : daily
3 M ....... : quarterly
12 M ..... : annually
The predefined service and maintenance intervals should be reduced when the loading
of the electric chain hoist is exceptionally large and when frequently operated in adverse
conditions (dust, heat, humidity, steam, etc.).
See table 3-1.
Table 3-1 Maintenance overview
Term t 3 M 12 M Activity Notes
1. Load chain X visual check
clean and lubricate as needed
see chapter 2.2.2
2. Hoist and carriage X abnormal noise check
seal check
3. Power supply cable X visual check
4. Limit switch X function check see chapter 2.2.3
5. Seal X visual check
6. Cable discharging device control cable X visual check
3.2.2 Service overview
See table 3-2.
Table 3-2 Service overview
Term t 3 M 12 M Activity Notes
1. Load chain X
X
lubricate
measure wear
see chapter 2.2.2 / 3.2.4
2. Brake system X X function check with load see chapter 3.2.3
3. Electrical fittings X function check
4. Securing screws on suspended parts
and load hook with accessories
X check for cracks
check screw movement
see chapter 3.2.8
5. Gearing X visual check wear see chapter 3.2.6
6. Limit switch X check switching elements see chapter 2.2.3
7. Slip clutch X function check see chapter 3.2.7
3.2.3 Brake system
The spring-loaded brake is a solenoid operated single disk brake with two friction
surfaces. The braking force is applied by compression springs. The braking torque is
generated when no current is applied. The ventilation is electromagnetic. The brake
operates with DC current.
The brake must be able to hold the nominal load in power free mode without any
problems.
CAUTION !
The brake coil voltage must be the same as the operating voltage.

GIS CHAIN HOIST SWISS QUALITY 17
NOTE
The brake has no air gap adjustment. If the air gap (a max., table 3-3 and
figure 3-1) reaches maximal value, the brake pad needs changing.
Table 3-3 Air gap
GCH 250/500 GCH 1000 GCH 1600/2000/2500
Air gap (a) [mm] 0.4 0.15
0
0.5
0.2
0
0.5
0.2
0
Air gap (a max.) [mm] 0.7 0.9 0.9
Torque value [Nm] 3 10 10
Figure 3-1
3.2.4 Load chain
The load chain should be periodically checked for abrasion. The check is based upon
three measurements: see accepted wear factors (table 3-4) and measurement points
(figure 3-2).
CAUTION !
The chain should be replaced when the measurements exceed or fall short
of those defined in the table. The chain wheel and chain guide should be
checked for wear at the same time and, where necessary, be replaced. Only
use original chains. The chain links should not be welded.
The new chain is installed in accordance with chapter 2.2.2.
NOTE
For ease of installation, the old chain and new chain can be connected by a
piece of flexible wire.
Table 3-4 Wear factors load chain
GCH 250 GCH 500 GCH 1000 GCH 1600 GCH 2000/2500
Chain type d x t [mm] 4 x 12.3 5 x 15.3 7 x 22 9 x 27 10 x 28
Tolerances in accordance with: DIN 685, part 5
DIN EN 818-7
1. Measurement over 11 chain links; a = 11t
[mm]
138.0
171.6
246.8
302.9
314.2
2. Measurement over 1 chain link 1t [mm] 12.9 16.0 23.1 28.35 29.4
3. Measurement of the chain link diameter
dm =
2
d2d1
; (dm min. = 0.9 x d)
[mm]
3.6
4.5
6.3
8.1
9.0
Figure 3-2
3.2.5 Limit stop assembly
3.2.6 Gearbox
3.2.7 Slip clutch
CAUTION !
A damaged buffer plate, underneath the housing, must be replaced.
Screw connections at the limit stop and shims or lower sheaves should be checked and,
where necessary, tightened to the right torque. For coefficient data see chapter 3.2.8.
The gearing has continual lubrication.
Lubricant........................ : Strub N1424
Can be mixed and is compatible with all other similar brand
name grease (DIN 51502: GP OM-20)
Lubricant quantity .......... : GCH 250/500 ................. : 0.4 kg
GCH 1000 ...................... : 1.0 kg
GCH 1600/2000/2500 .... : 1.8 kg
The slip clutch is set at 125% at the factory and can be relied on to prevent the chain
hoist from being overloaded (the force limiting factor according to DIN EN 14492-2 is
ΦDAL = 1.4). The coating is wear resistant.
CAUTION !
Adjustment and testing of the slip clutch may only be carried out by
authorized personnel and must be recorded in the log book.
d
d1
d2
t
a = 11t
b
a

GIS CHAIN HOIST SWISS QUALITY18
3.2.8 Suspension parts
3.3 Ordering spare parts
4 Measures for obtaining a
safe period of operation
4.1 Determining the actual
utilization period S
4.2 General overhaul
All statically loaded parts are considered suspension parts. The bearing surfaces of the
slewing suspension parts must be periodically greased.
Torque values for screws of property class 8.8 according to DIN ISO 898:
M 5 M 6 M 8 M 10 M 12
6 Nm 10 Nm 24 Nm 48 Nm 83 Nm
Information on how to order spare parts can be found on page 3.
The statutory and health requirements of the EU regulations stipulate that specific
dangers which may arise from fatigue or ageing must be prevented.
Accordingly, operators of standard hoist gear are obliged to determine the actual
utilization. The actual utilization period is determined and recorded as part of the annual
inspection by customer service engineers. A general overhaul must be carried out when
the theoretical utilization limit is reached, or after no more than 10 years.
All checking and the general overhaul itself must be arranged by the operator of the
hoist gear. The following theoretical utilization periods apply to electric chain hoists that
are categorized according to ISO 4301-1 (converted into full-load hours):
M3 M4 M5 M6 M7
400 h 800 h 1600 h 3200 h 6300 h
The actual utilization period depends on the daily operating time and the load collective.
Running time is determined from information provided by the operator or recorded using
a meter that counts the number of operating hours. The load collective is determined in
accordance with table 1-1, page 9. These two items of information are used to calculate
the annual utilization period from table 4-1.
If an operating data acquisition system (BDE) is used, the actual utilization can be read
out directly by our experts during the annual inspection.
CAUTION !
The values periodically calculated or read-off must be recorded in the log
book.
On reaching the theoretical service life (no later than 10 years for recording without
BDE), a general overhaul should be performed. This enables the equipment to continue
operating safely for a further period of utilization (service life). Components must be
inspected and/ or replaced in this overhaul according to table 4-2. Inspection and
approval for further use must be performed either by a specialist company authorized by
the manufacturer, or by the manufacturer personally.
The inspector determines: – the new theoretical utilization possible
– the maximum period until the next general overhaul
This data should be recorded in the log book.
Table 4-1 Annual service life
Utilization
per day [h]
<= 0.25
(0.16)
<= 0.50
(0.32)
<= 1.0
(0.64)
<= 2.0
(1.28)
<= 4.0
(2.56)
<= 8.0
(5.12)
<= 16.0
(10.24)
> 16.0
(20.48)
Load
collective Annual service life [h]
k = 0.50 6 12 24 48 96 192 384 768
k = 0.63 12 24 48 96 192 384 768 1536
k = 0.80 24 48 96 192 384 768 1536 3072
k = 1.00 48 96 192 384 768 1536 3072 6144
Table 4-2 General overhaul
Components of GCH-models
all types Check for wear * Replace
Brake x
Motor shaft x
Gear teeth x
Antifriction bearing x
Washers x
Chain x **
Chain wheel, chain guide x
Deflection wheels x
Suspension x
Load hook x
Travelling gear, running wheel x
Contactor, limit switch x
* replace when worn ** replace no later than at general overhaul

GIS CHAIN HOIST SWISS QUALITY 19
5 Appendix
Table 0-2 GCH technical data
ISO (FEM)
classification
M3 (1Bm)
150 s/h
25% duty
M4 (1Am)
180 s/h
30% duty
M5 (2m)
240 s/h
40% duty
M6 (3m)
300 s/h
50% duty
M7 (4m)
360 s/h
60% duty
Lifting
speed
Motor power
(M3)
3 x 400V
50Hz
(M3)
1 x 230V
50Hz
(M3)
No. of
chain falls
Dead
weight
3 m lift
Connection
fuse
Types Capacity [kg] [m/min] [kW] [A] [A] [kg] [A]
GCH 250/1N
GCH 250/1NF
GCH 250/1SF
GCH 250/1HF
GCH 250/1N 1Ph
250
250
160
100
160
200
200
125
100
-
160
160
100
100
-
125
125
100
100
-
100
100
100
100
-
8
8/2
12.5/3
20/5
8
0.36
0.36/0.09
0.36/0.09
0.36/0.09
0.23
1.3
2.7/3.0
2.7/3.0
2.7/3.0
-
-
-
-
-
8.9
1
1
1
1
1
19
22
22
22
19
10
10
10
10
10
GCH 250/2N
GCH 250/2NF
GCH 250/2SF
GCH 250/2N 1Ph
500
500
320
320
400
400
250
-
320
320
200
-
250
250
200
-
200
200
200
-
4
4/1
6.25/1.5
4
0.36
0.36/0.09
0.36/0.09
0.23
1.3
2.7/3.0
2.7/3.0
-
-
-
-
8.9
2
2
2
2
22.5
23
23
22.5
10
10
10
10
GCH 500/1N
GCH 500/1NF
GCH 500/1SF
GCH 500/1HF
GCH 500/1N 1Ph
500
500
320
200
250
400
400
250
160
-
320
320
200
125
-
250
250
160
100
-
200
200
125
100
-
8
8/2
12.5/3
20/5
8
0.72
0.72/0.18
0.72/0.18
0.72/0.18
0.36
2.1
2.9/3.0
2.9/3.0
2.9/3.0
-
-
-
-
-
8.9
1
1
1
1
1
20
22.5
22.5
22.5
20
10
10
10
10
10
GCH 500/2N
GCH 500/2NF
GCH 500/2SF
GCH 500/2N 1Ph
1,000
1,000
630
500
800
800
500
-
630
630
400
-
500
500
320
-
400
400
250
-
4
4/1
6.25/1.5
4
0.72
0.72/0.18
0.72/0.18
0.36
2.1
2.9/3.0
2.9/3.0
-
-
-
-
8.9
2
2
2
2
24.5
25
25
24.5
10
10
10
10
GCH 1000/1N
GCH 1000/1NF
GCH 1000/1SF
GCH 1000/1N 1Ph
1,000
1,000
500
500
800
800
400
-
630
630
320
-
500
500
250
-
400
400
200
-
8
8/2
16/4
8
1.45
1.45/0.36
1.45/0.36
0.73
3.7
4.0/2.8
5.8/2.6
-
-
-
-
6.0
1
1
1
1
45
46
48
46
10
10
10
10
GCH 1000/2N
GCH 1000/2NF
GCH 1000/2SF
GCH 1000/2N 1Ph
2,000
2,000
1,000
1,000
1,600
1,600
800
-
1,250
1,250
630
-
1,000
1,000
500
-
800
800
400
-
4
4/1
8/2
4
1.45
1.45/0.36
1.45/0.36
0.73
3.7
4.0/2.8
5.8/2.6
-
-
-
-
6.0
2
2
2
2
50
51
53
51
10
10
10
10
GCH 1600/1N
GCH 1600/1NF
GCH 1600/1SF
1,600
1,600
1,000
1,250
1,250
800
1,000
1,000
630
800
800
500
630
630
400
8
8/2
12.5/3
2.44
2.44/0.61
2.39/0.58
6.0
6.6/4.2
6.6/4.2
-
-
-
1
1
1
63
65
65
16
16
16
GCH 1600/2N
GCH 1600/2NF
GCH 1600/2SF
3,200
3,200
2,000
2,500
2,500
1,600
2,000
2,000
1,250
1,600
1,600
1,000
1,250
1,250
800
4
4/1
6.25/1.5
2.44
2.44/0.61
2.39/0.58
6.0
6.6/4.2
6.6/4.2
-
-
-
2
2
2
73
75
75
16
16
16
GCH 2000/1N
GCH 2000/1NF
GCH 2000/1SF
2,000
2,000
1,250
1,600
1,600
1,000
1,250
1,250
800
1,000
1,000
630
800
800
500
8
8/2
12.5/3
3.05
3.05/0.77
2.98/0.72
7.3
8.0/4.5
8.0/4.5
-
-
-
1
1
1
65
67
67
16
16
16
GCH 2000/2N
GCH 2000/2NF
GCH 2000/2SF
4,000
4,000
2,500
3,200
3,200
2,000
2,500
2,500
1,600
2,000
2,000
1,250
1,600
1,600
1,000
4
4/1
6.25/1.5
3.05
3.05/0.77
2.98/0.72
7.3
8.0/4.5
8.0/4.5
-
-
-
2
2
2
76
78
78
16
16
16
GCH 2500/1N
GCH 2500/1NF
GCH 2500/1SF
2,500
2,500
1,600
2,000
2,000
1,250
1,600
1,600
1,000
1,250
1,250
800
1,000
1,000
630
6.4
6.4/1.6
10/2.5
3.05
3.05/0.77
3.05/0.77
7.7
8.2/4.4
8.2/4.4
-
-
-
1
1
1
65
67
67
16
16
16
GCH 2500/2N
GCH 2500/2NF
GCH 2500/2SF
5,000
5,000
3,200
4,000
4,000
2,500
3,200
3,200
2,000
2,500
2,500
1,600
2,000
2,000
1,250
3.2
3.2/0.8
5/1.25
3.05
3.05/0.77
3.05/0.77
7.7
8.2/4.4
8.2/4.4
-
-
-
2
2
2
76
78
78
16
16
16
Table 0-3 GCHK technical data
ISO (FEM)
classification
M3 (1Bm)
150 s/h
25% duty
M4 (1Am)
180 s/h
30% duty
M5 (2m)
240 s/h
40% duty
M6 (3m)
300 s/h
50% duty
M7 (4m)
360 s/h
60% duty
Lifting
speed
Motor power
(M3)
3 x 400V
50Hz
(M3)
1 x 230V
50Hz
(M3)
No. of
chain falls
Dead
weight
3 m lift
Connection
fuse
Types Capacity [kg] [m/min] [kW] [A] [A] [kg] [A]
GCHK 250/1NF
GCHK 250/1SF
200
125
160
100
125
100
100
100
100
100
8/2
12.5/3
0.29/0.07
0.28/0.07
2.7/3.0
2.7/3.0
-
-
1
1
40
40
10
10
GCHK 250/2NF
GCHK 250/2SF
400
250
320
200
250
200
200
200
200
200
4/1
6.25/1.5
0.29/0.07
0.28/0.07
2.7/3.0
2.7/3.0
-
-
2
2
41
41
10
10
GCHK 500/1NF
GCHK 500/1SF
400
250
320
200
250
160
200
125
160
100
8/2
12.5/3
0.58/0.14
0.57/0.14
2.9/3.0
2.9/3.0
-
-
1
1
40.5
40.5
10
10
GCHK 500/2NF
GCHK 500/2SF
800
500
630
400
500
320
400
250
320
200
4/1
6.25/1.5
0.58/0.14
0.57/0.14
2.9/3.0
2.9/3.0
-
-
2
2
43
43
10
10
GCHK 1000/1NF
GCHK 1000/1SF
800
400
630
320
500
250
400
200
320
160
8/2
16/4
1.16/0.29
1.16/0.29
3.3/2.8
5.4/2.4
-
-
1
1
88
90
10
10
GCHK 1000/2NF
GCHK 1000/2SF
1,600
800
1,250
630
1,000
500
800
400
630
320
4/1
8/2
1.16/0.29
1.16/0.29
3.3/2.8
5.4/2.4
-
-
2
2
94
96
10
10
GCHK 1600/1NF
GCHK 1600/1SF
1,250
800
1,000
630
800
500
630
400
500
320
8/2
12.5/3
1.91/0.48
1.91/0.46
5.5/4.1
5.5/4.1
-
-
1
1
127
127
16
16
GCHK 1600/2NF
GCHK 1600/2SF
2,500
1,600
2,000
1,250
1,600
1,000
1,250
800
1,000
630
4/1
6.25/1.5
1.91/0.48
1.91/0.46
5.5/4.1
5.5/4.1
-
-
2
2
139
139
16
16
GCHK 2000/1NF
GCHK 2000/1SF
1,600
1,000
1,250
800
1,000
630
800
500
630
400
8/2
12.5/3
2.44/0.61
2.38/0.57
6.6/4.2
6.6/4.2
-
-
1
1
129
129
16
16
GCHK 2000/2NF
GCHK 2000/2SF
3,200
2,000
2,500
1,600
2,000
1,250
1,600
1,000
1,250
800
4/1
6.25/1.5
2.44/0.61
2.38/0.57
6.6/4.2
6.6/4.2
-
-
2
2
142
142
16
16
GCHK 2500/1NF
GCHK 2500/1SF
2,000
1,250
1,600
1,000
1,250
800
1,000
630
800
500
6.4/1.6
10/2.5
2.44/0.61
2.38/0.60
6.2/4.1
6.2/4.1
-
-
1
1
129
129
16
16
GCHK 2500/2NF
GCHK 2500/2SF
4,000
2,500
3,200
2,000
2,500
1,600
2,000
1,250
1,600
1,000
3.2/0.8
5/1.25
2.44/0.61
2.38/0.60
6.2/4.1
6.2/4.1
-
-
2
2
142
142
16
16

GIS CHAIN HOIST SWISS QUALITY20
Table 0-4 GCHS technical data
ISO (FEM)
classification
M3 (1Bm)
150 s/h
25% duty
M4 (1Am)
180 s/h
30% duty
M5 (2m)
240 s/h
40% duty
M6 (3m)
300 s/h
50% duty
M7 (4m)
360 s/h
60% duty
Lifting
speed
Motor power
(M3)
3 x 400V
50Hz
(M3)
1 x 230V
50Hz
(M3)
No. of
chain falls
Dead
weight
3 m lift
Connection
fuse
Types Capacity [kg] [m/min] [kW] [A] [A] [kg] [A]
GCHS 500/1NF
GCHS 500/1SF
2x200
2x125
2x160
2x100
2x125
2x80
2x100
2x60
2x80
2x50
8/2
12.5/3
0.58/0.14
0.57/0.14
2.9/3.0
2.9/3.0
-
-
1
1
44.5
44.5
10
10
GCHS 500/2NF
GCHS 500/2SF
2x400
2x250
2x320
2x200
2x250
2x160
2x200
2x125
2x160
2x100
4/1
6.25/1.5
0.58/0.14
0.57/0.14
2.9/3.0
2.9/3.0
-
-
2
2
47
47
10
10
GCHS 1000/1NF
GCHS 1000/1SF
2x400
2x200
2x320
2x160
2x250
2x125
2x200
2x100
2x160
2x80
8/2
16/4
1.16/0.29
1.16/0.29
3.3/2.8
5.4/2.4
-
-
1
1
87
89
10
10
GCHS 1000/2NF
GCHS 1000/2SF
2x800
2x400
2x630
2x320
2x500
2x250
2x400
2x200
2x320
2x160
4/1
8/2
1.16/0.29
1.16/0.29
3.3/2.8
5.4/2.4
-
-
2
2
93
95
10
10
GCHS 2000/1NF
GCHS 2000/1SF
2x800
2x500
2x630
2x400
2x500
2x320
2x400
2x250
2x320
2x200
8/2
12.5/3
2.44/0.61
2.38/0.57
6.6/4.2
6.6/4.2
-
-
1
1
151
151
16
16
GCHS 2000/2NF
GCHS 2000/2SF
2x1'600
2x1'000
2x1'250
2x800
2x1'000
2x630
2x800
2x500
2x630
2x400
4/1
6.25/1.5
2.44/0.61
2.38/0.57
6.6/4.2
6.6/4.2
-
-
2
2
168
168
16
16
Table 0-5 GCHHK technical data
ISO (FEM)
classification
M3 (1Bm)
150 s/h
25% duty
M4 (1Am)
180 s/h
30% duty
M5 (2m)
240 s/h
40% duty
M6 (3m)
300 s/h
50% duty
M7 (4m)
360 s/h
60% duty
Lifting
speed
Motor power
(M5)
3 x 400V
50Hz
(M5)
1 x 230V
50Hz
(M5)
No. of
chain falls
Dead
weight
3 m lift
Connection
fuse
Types Capacity [kg] [m/min] [kW] [A] [A] [kg] [A]
GCHHK 500/NF
GCHHK 500/SF
GCHHK 500/HF
-
-
-
-
-
-
250
200
125
250
160
100
200
125
100
8/2
12.5/3
20/5
0.36/0.09
0.45/0.11
0.45/0.11
2.7/3.0
2.7/3.0
2.7/3.0
-
-
-
1
1
1
27
27
27
10
10
10
Table 0-6 GCHHTD technical data
ISO (FEM)
classification
M3 (1Bm)
150 s/h
25% duty
M4 (1Am)
180 s/h
30% duty
M5 (2m)
240 s/h
40% duty
M6 (3m)
300 s/h
50% duty
M7 (4m)
360 s/h
60% duty
Lifting
speed
Motor power
(M6/M4)
3 x 400V
50Hz
(M6/M4)
1 x 230V
50Hz
(M6/M4)
No. of
chain falls
Dead
weight
2 m lift
Connection
fuse
Types Capacity [kg] [m/min] [kW] [A] [A] [kg] [A]
GCHHTD 500/NF
GCHHTD 500/SF
-
-
-
250
-
200
250
160
200
125
8/2
12.5/3
0.36/0.09
0.57/0.14
2.7/3.0
2.7/3.0
-
-
1
1
35
35
10
10
Table 0-7 GCHR technical data
ISO (FEM)
classification
M3 (1Bm)
150 s/h
25% duty
M4 (1Am)
180 s/h
30% duty
M5 (2m)
240 s/h
40% duty
M6 (3m)
300 s/h
50% duty
M7 (4m)
360 s/h
60% duty
Lifting
speed
Motor power
(M4)
3 x 400V
50Hz
(M4)
1 x 230V
50Hz
(M4)
No. of
chain falls
Dead
weight
3 m lift
Connection
fuse
Types Capacity [kg] [m/min] [kW] [A] [A] [kg] [A]
GCHR 500/1N
GCHR 500/1NF
-
-
320
320
250
250
-
-
-
-
8
8/2
0.46
0.46/0.12
2.1
2.9/3.0
-
-
1
1
20
22.5
10
10
GCHR 500/2N
GCHR 500/2NF
-
-
630
630
500
500
-
-
-
-
4
4/1
0.46
0.46/0.12
2.1
2.9/3.0
-
-
2
2
24.5
25
10
10
GCHR 1000/1N
GCHR 1000/1NF
-
-
630
630
500
500
-
-
-
-
8
8/2
0.91
0.91/0.23
3.7
4.0/2.8
-
-
1
1
45
46
10
10
GCHR 1000/2N
GCHR 1000/2NF
-
-
1'250
1'250
1'000
1'000
-
-
-
-
4
4/1
0.91
0.91/0.23
3.7
4.0/2.8
-
-
2
2
50
51
10
10
This manual suits for next models
97
Table of contents
Popular Lifting System manuals by other brands
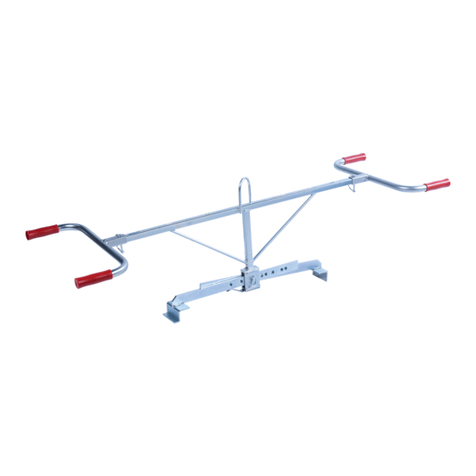
probst
probst VZ-II operating instructions
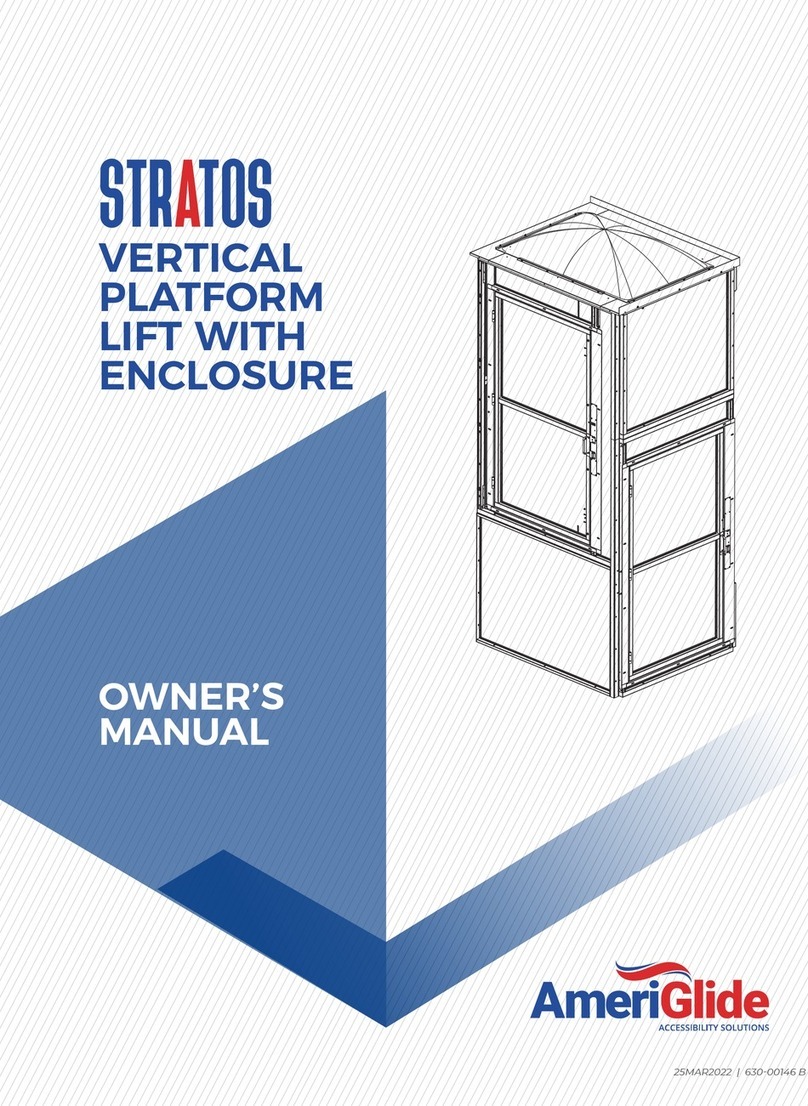
AmeriGlide
AmeriGlide STRATOS owner's manual

Discount Equipment
Discount Equipment SKYJACK SJ3013 Operation manual
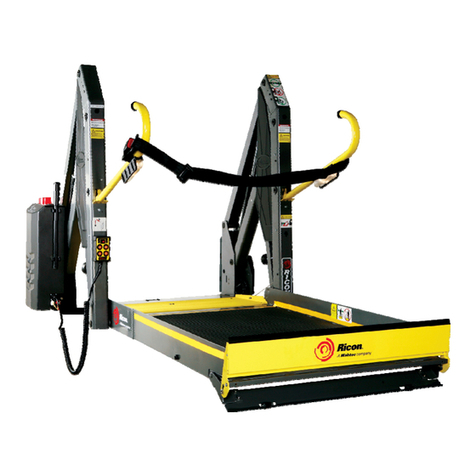
Wabtec
Wabtec Ricon TITANIUM S Series Service manual
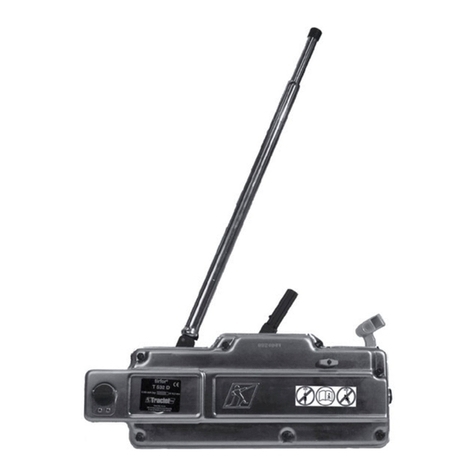
Tractel
Tractel tirfor TU-8 Operating and maintenance instruction
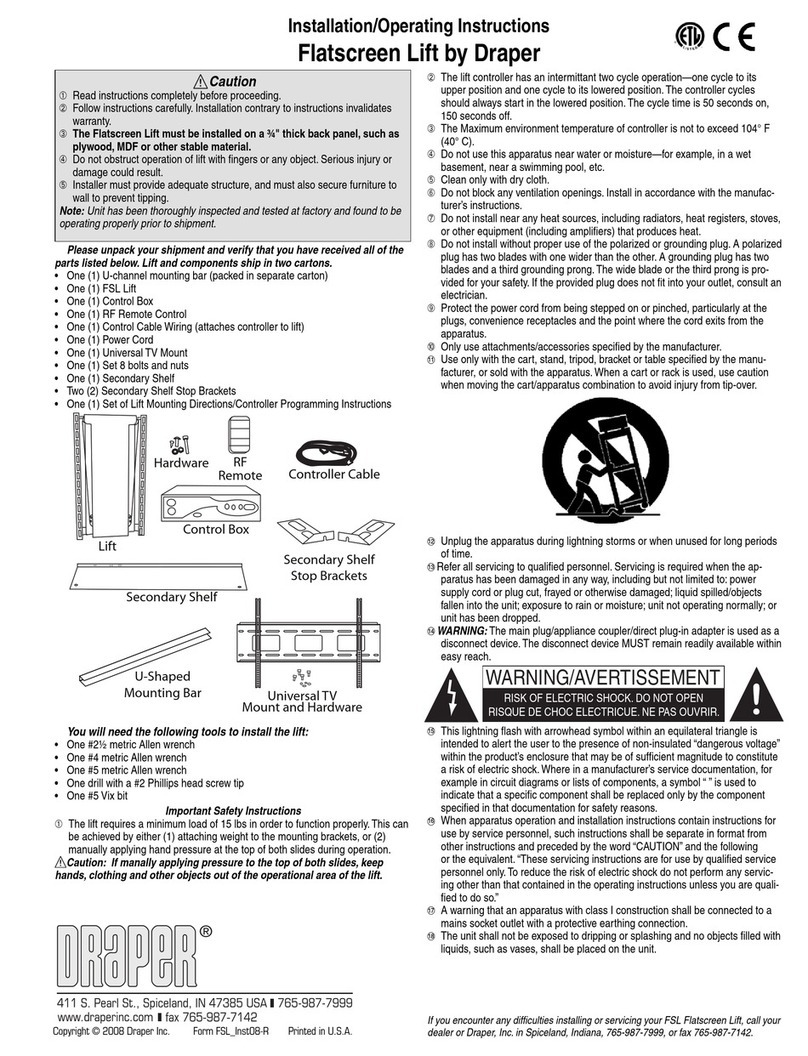
Draper
Draper Flatscreen Lift FSL-F-42 Installation & operating instructions