Wabtec Ricon TITANIUM S Series User manual

Service Manual
06-11-2021 2021 RICON CORPORATION
All Rights Reserved
TITANIUM LINE
S-SERIES AND K-SERIES
DOT – PUBLIC USE LIFT
™
®
®
-
PRIN
T
-
32DSKF02.D
-
HOME
-
U.S. Patent Nos: 4,534,450; 5,308,215; 5,445,488; 5,605,431; 5,944,473;
Australia Patent Nos: 661127;687066;
Canadian Patent Nos: 1,245,603; 2,168,761
Other U.S. and foreign patents pending

i
TABLE OF CONTENTS
JUNE 2021
32DSKF02.D
TITANIUM S-SERIES AND K-SERIES
PUBLIC USE SERVICE MANUAL
This Ricon service manual is for use by qualified service technicians, and
is not intended for use by non-professionals (do-it-yourselfers). The man-
ual provides essential instructions and reference information, which sup-
ports qualified technicians in the correct installation and maintenance of
Ricon products.
Qualified service technicians have the training and knowledge to perform
maintenance work properly and safely. For the location of a service tech-
nician in your area, call Ricon Product Support at 1-800-322-2884.
“DOT – Public Use Lift” verifies that this platform lift meets the public use
lift requirements of FMVSS no. 403. This lift may be installed on all vehi-
cles appropriate for the size and weight of the lift, but must be installed on
buses, school buses, and multi-purpose passenger vehicles other than
motor homes with a gross vehicle weight rating (GVWR) that exceeds
10,000 lbs (4,536 kgs).
Customer Name:
Installing Dealer:
Date Installed:
Serial Number:

ii
TABLE OF CONTENTS JUNE 2021
32DSKF02.D.C
TITANIUM S-SERIES AND K-SERIES
PUBLIC USE SERVICE MANUAL
REVISION RECORD

iii
TABLE OF CONTENTS
JUNE 2021
32DSKF02.D
TITANIUM S-SERIES AND K-SERIES
PUBLIC USE SERVICE MANUAL
CHAPTER PAGE
I. INTRODUCTION ....................................................................................................................1-1
A. RICON PRODUCT SUPPORT........................................................................................................1-1
B. RICON TITANIUM LIMITED WARRANTY......................................................................................1-2
C. SHIPMENT INFORMATION............................................................................................................1-3
D. GENERAL SAFETY PRECAUTIONS.............................................................................................1-3
E. MAJOR LIFT COMPONENTS.........................................................................................................1-4
II. INSTALLATION .....................................................................................................................2-1
A. GENERAL MECHANICAL INSTALLATION...................................................................................2-1
1. LIFT LOCATION.........................................................................................................................................2-1
2. VEHICLE DIMENSIONAL REQUIREMENTS............................................................................................2-1
3. LIFT INSTALLATION GUIDELINES ..........................................................................................................2-2
4. LIFT INSTALLATION INTO BUSES ..........................................................................................................2-3
B. ELECTRICAL INSTALLATION.......................................................................................................2-5
1. INSTALL MAIN CIRCUIT BREAKER.........................................................................................................2-6
2. ROUTE AND CONNECT MAIN POWER CABLE......................................................................................2-6
3. GROUND CONNECTIONS........................................................................................................................2-7
4. CONTROL PENDANT ...............................................................................................................................2-7
5. INSTALLATION OF INTERLOCK DEVICE ...............................................................................................2-9
C. FINAL ADJUSTMENTS ................................................................................................................2-10
1. LIMIT SWITCH ADJUSTMENT................................................................................................................2-10
2. PLATFORM TILT ADJUSTMENT............................................................................................................2-11
3. K-SERIES PLATFORM FOLDING LINKAGE ADJUSTMENT.................................................................2-12
4. K-SERIES OUTER ROLLSTOP BARRIER ADJUSTMENT....................................................................2-13
5. PLATFORM PRESSURE SWITCH CHECK AND ADJUSTMENT..........................................................2-13
D. VERIFY INSTALLATION...............................................................................................................2-16
E. SAFETY CHECKLIST FOR VEHICLE MANUFACTURER ..........................................................2-16
III. MAINTENANCE AND REPAIR..............................................................................................3-1
A. LUBRICATION................................................................................................................................3-1
B. CLEANING......................................................................................................................................3-1
C. MAINTENANCE SCHEDULE..........................................................................................................3-2
D. TROUBLESHOOTING ....................................................................................................................3-3
1. LIFT TROUBLESHOOTING.......................................................................................................................3-3
2. PUMP SOLENOID LED STATUS INDICATOR.........................................................................................3-4
3. BRIDGEPLATE CABLE ASSEMBLY REPLACEMENT.............................................................................3-4
4. S-SERIES AND K-SERIES LIMIT SWITCH STATES ...............................................................................3-5
5. BRIDGEPLATE ADJUSTMENT.................................................................................................................3-6
6. STOW LOCK ADJUSTMENT ....................................................................................................................3-7
7. REAR SPRING REPLACEMENT ..............................................................................................................3-8
8. HYDRAULIC CYLINDER GLAND NUT AND PISTON REPLACMENT ....................................................3-9
E. HYDRAULIC CIRCUIT DIAGRAM................................................................................................3-11
F. ELECTRICAL WIRING DIAGRAM................................................................................................3-12
1. DIAGRAM LEGENDS..............................................................................................................................3-12
2. WIRING DIAGRAM..................................................................................................................................3-14
IV. PARTS DIAGRAMS AND LISTS ........................................................................................... 4-1
Appendix: Lift Specifications..........................................................................................................4-30

iv
TABLE OF CONTENTS JUNE 2021
32DSKF02.D
TITANIUM S-SERIES AND K-SERIES
PUBLIC USE SERVICE MANUAL
Thispageintentionallyleftblank.

1 - 1
I
N
TRODU
C
TIO
N
JUNE 2021
32DSKF02.D
TITANIUM S-SERIES AND K-SERIES
PUBLIC USE SERVICE MANUAL
I. INTRODUCTION
he RICON Titanium™S-Series®and K-Series® Public Use wheelchair lift provides wheelchair access to vans and
buses. The patented movement provides smooth, safe entry and exit and lifts up to 1,000 pounds (454kg). It is
to be operated by a trained attendant. The lift contains a powerful electro-hydraulic pump that includes a built-in
manual backup pump. If the lift loses electrical power, it can be raised or lowered manually.
By using the lift control switches, the lift is unfolded out from the vehicle (deployed). The user boards the large non-skid
platform and the operator uses the control switches to gently lower the platform to the ground. After the user departs,
the platform is raised and folded into the vehicle (stowed). The lift is also available with a platform that splits and folds
when stowed, providing easy vehicle access through the lift.
This manual contains installation instructions; maintenance and repair instructions; troubleshooting guide; parts and di-
agram lists. It is important to user safety that the lift operator be completely familiar with the operating instructions.
Once the lift is installed, it is very important that the lift be properly maintained by following the Ricon recommended
cleaning, lubrication, and inspection instructions.
A. RICON PRODUCT SUPPORT
If you have questions about this manual, or additional copies are needed, please contact Ricon Product Support at one
of the following locations:
Ricon Corporation
1135 Aviation Place
San Fernando, CA 91340 ..........................................................................................................(818) 267-3000
Outside (818) Area Code...........................................................................................................(800) 322-2884
Website................................................................................................................................. www.wabtec.com
Vapor Ricon Europe Ltd.
Meadow Lane
Loughborough, Leicestershire ....................................................................................0044 (9) 1509 635 920
LE 1HS United Kingdom
Website................................................................................................................................. www.wabtec.com
T

1 - 2
INTRODUCTION JUNE 2021
32DSKF02.D
TITANIUM S-SERIES AND K-SERIES
PUBLIC USE SERVICE MANUAL
B. RICON TITANIUM LIMITED WARRANTY
RICON CORPORATION
TITANIUM™LIMITED WARRANTY
Ricon Corporation (Ricon) warrants to the original purchaser of this product that Ricon will repair or replace,
at its option, any part that fails due to defective material or workmanship as follows:
• Repair or replace parts for a period of three (3) years from the date of lift purchase.
• Labor costs for specified parts replaced under this warranty for a period of three (3) years from the date of
lift purchase. A Ricon rate schedule determines parts covered and labor allowed.
• Repair or replace only power train parts for a period of five (5) years from the date of lift purchase. A com-
plete list of parts covered under the power train warranty can be obtained from your Ricon dealer or Ricon
Corporation.
(Note: See specified labor costs for explanation of when labor is covered under this warranty.)
If you need to return a product: Return this product to Ricon, following the Ricon RMA procedure. Please
give as much advance notice as possible, and allow a reasonable amount of time for repair.
This warranty does not cover: Malfunction or damage to product parts caused by accident, misuse, lack of
proper maintenance, neglect, improper adjustment, modification, alteration, the mechanical condition of the ve-
hicle, road hazards, overloading, failure to follow operating instructions, or acts of nature (i.e., weather, light-
ning, flood).
Note: Ricon recommends that this product be inspected by a Ricon dealer or qualified service technician at
least once every six months, or sooner if necessary. Required maintenance should be performed at that time.
WARNING
THIS PRODUCT HAS BEEN DESIGNED AND MANUFACTURED TO EXACT SPECIFICATIONS.
ANY MODIFICATION OF THIS PRODUCT IN ANY RESPECT CAN BE DANGEROUS.
This warranty is void if:
•The product has been installed or maintained by someone other than a Ricon dealer or qualified service
technician.
•The product has been modified or altered in any respect from its original design without written authoriza-
tion by Ricon.
Ricon disclaims liability for any personal injury or property damage that results from opera-
tion of a Ricon product that has been modified from the original Ricon design. No person or
company is authorized to change the design of this Ricon product without written authoriza-
tion by Ricon.
Ricon's obligation under this warranty is exclusively limited to the repair or exchange of parts
that fail within the applicable warranty period and the authorized labor to accomplish said re-
pair.
Ricon assumes no responsibility for expenses or damages, including incidental or conse-
quential damages. Some states do not allow the exclusion or limitation of incidental or con-
sequential damages, so the above limitation or exclusion may not apply.
Important: The warranty registration card must be completed and returned to Ricon within 20
days after installation of this Ricon product for the warranty to be valid. The warranty is not
transferable.
The warranty gives specific legal rights. There may be other rights that vary in each state.

1 - 3
I
N
TRODU
C
TIO
N
32DSKF02.D
TITANIUM S-SERIES AND K-SERIES
PUBLIC USE SERVICE MANUAL
JUNE 2021
C. SHIPMENT INFORMATION
• When the product is received, unpack the product and check for freight damage. Claims for damage should be
made to the freight carrier immediately.
• Be sure the installation kit contains all items listed on the kit packing list. Please report any missing items immedi-
ately to Ricon Product Support.
• The warranty and owner registration cards must be completed and returned to Ricon within 20 days to validate the
warranty.
NOTE: The Sales or Service personnel must review the Warranty and this Operator Manual with the user to be certain
that they understand how to safely operate the product and instruct the user to follow the operating instructions
without exception.
D. GENERAL SAFETY PRECAUTIONS
The following general safety precautions must be followed during installation, operation, and maintenance:
• Under no circumstances should installation, maintenance, repair, and adjustments be attempted without the imme-
diate presence of a person capable of rendering aid.
•An injury, no matter how slight, should always be attended. Always administer first aid or seek medical attention
immediately.
•Protective eyeshields and appropriate clothing should be worn at all times.
•To avoid injury, always exercise caution when operating and be certain that hands, feet, legs, and clothing are not
in the path of product movement.
•Batteries contain acid that can burn. If acid comes in contact with skin, flush affected area with water and wash with
soap immediately.
•Always work in a properly ventilated area. Do not smoke or use an open flame near a battery.
• Do not lay anything metallic on top of a battery.
•Check under vehicle before drilling to avoid drilling into frame, subframe members, wiring, hydraulic lines, fuel lines,
fuel tank, etc.
•Read and thoroughly understand the operating instructions before attempting to operate.
•Inspect the product before each use. If an unsafe condition is noted, such as unusual noises or movements, do not
use lift until the problem is corrected.
•Never load or stand on the platform until installation is complete. Upon completion of installation, test load the lift to
100% of its rated load capacity.
•Stand clear of doors and platform and keep others clear during operation.
•The product requires regular periodic maintenance. Inspections are recommended at the intervals prescribed in
chapter three. The product must be maintained at the highest level of performance.
•Only one (1) control pendant can safely operate the wheelchair lift at any time. Do not control wheelchair lift with
two control pendants simultaneously.

1 - 4
INTRODUCTION JUNE 2021
32DSKF02.D
TITANIUM S-SERIES AND K-SERIES
PUBLIC USE SERVICE MANUAL
E. MAJOR LIFT COMPONENTS
The references used throughout this manual are illustrated in Figures 1-1, 1-2 and defined in the Tables 1-1, 1-2. Re-
fer to Chapter IV “Parts Diagrams and Lists” for more details.
1
2
3
4
6
7
8
9
16
10
11
12
13
14
15
17
18
21
22
24
5
11
12
17
23
22
19
20
RSM0052200
FIGURE 1-1: TITANIUM S-SERIES MAJOR COMPONENTS

1 - 5
I
N
TRODU
C
TIO
N
JUNE 2021
32DSKF02.D
TITANIUM S-SERIES AND K-SERIES
PUBLIC USE SERVICE MANUAL
TABLE 1-1: TITANIUM S-SERIES PUBLIC USE LIFT COMPONENT TERMS
REF NAME DESCRIPTION
1, 2,
3, 4 Left, right,
front, rear Position references when lift is viewed from outside of vehicle.
5 Audible alarm (inside housing for hydraulic unit) Announces when something has
passed over threshold. Activated by threshold beam.
6 Baseplate
assembly Bolts to vehicle floor; provides secure foundation for lift.
7 Bridgeplate
(inboard rollstop) Plate bridges gap between platform and baseplate when platform is at
floor level. Acts as barrier to prevent wheelchair from rolling off of the plat-
form during "Up" and "Down" platform motions.
8 Control pendant Water resistant, hand-held device controls platform motions.
9 Cycle counter Visible at rear of housing, it records number of times platform has moved
from floor to ground and back to floor.
10 Front rollstop Front barrier prevents the wheelchair from inadvertently rolling off of the
platform during lift operation.
11 Handrail (left and right) Provides a handhold for standing passenger.
12 Hydraulic cylinder (left and right) Telescoping single-acting cylinders convert
hydraulic pressure into platform lifting and folding force.
13 Hydraulic power unit Contains hydraulic pump driven by electric motor that produces pressure
to raise and fold platform, and a pressure release valve to unfold and lower
it.
14 Manual backup pump
handle Used to operate manual back up-pump (located on hydraulic power unit
cover).
15 Occupant restraint
belt Electrically interlocked safety belt that is intended to prevent acceleration
of wheelchair from platform. Lift will not operate unless belt is properly
connected.
16 Platform Component of lift where the wheelchair and occupant are situated during
"Up" and "Down" lift motions.
17 Platform light (left and right) Directs light onto platform surface.
18 Serial number Location of serial number decal.
19 Stow-Lock catch Engages latch located on bottom of bridgeplate when platform is fully
stowed.
20 Switch - Bridgeplate
load sensor Senses if weight is present on the lowered bridgeplate.
21 Threshold beams Light-beams detect presence of objects in threshold area.
22 Top and bottom arms (left and right) Upper and lower links connecting vertical arm to base as-
sembly.
23 Vertical arm (left and right) Connects platform to top and bottom arms.
24 Visual alarm Flashing light makes it known when something has passed over threshold.
Activated by threshold beams.
END OF TABLE

1 - 6
INTRODUCTION JUNE 2021
32DSKF02.D
TITANIUM S-SERIES AND K-SERIES
PUBLIC USE SERVICE MANUAL
1
2
3
4
6
7
8
9
16
10
11
12
13
14
15
18
20
23
24
26
5
11
12
17
25
22
21
22
19
19
RSM0052300
FIGURE 1-2: TITANIUM K-SERIES MAJOR COMPONENTS

1 - 7
I
N
TRODU
C
TIO
N
JUNE 2021
32DSKF02.D
TITANIUM S-SERIES AND K-SERIES
PUBLIC USE SERVICE MANUAL
TABLE 1-2: TITANIUM K-SERIES PUBLIC USE LIFT COMPONENT TERMS
REF NAME DESCRIPTION
1, 2,
3, 4 Left, right,
front, rear Position references when lift is viewed from outside of vehicle.
5 Audible alarm (inside housing for hydraulic unit) Announces when something has
passed over threshold. Activated by threshold beam.
6 Baseplate
assembly Bolts to vehicle floor; provides secure foundation for lift.
7 Bridgeplate
(inboard rollstop) Plate bridges gap between platform and baseplate when platform is at
floor level. Acts as barrier to prevent wheelchair from rolling off of the plat-
form during "Up" and "Down" platform motions.
8 Control pendant Water resistant, hand-held device controls platform motions.
9 Cycle counter Visible at rear of housing, it records number of times platform has moved
from floor to ground and back to floor.
10 Front rollstop Front barrier prevents the wheelchair from inadvertently rolling off of the
platform during lift operation.
11 Handrail (left and right) Provides a handhold for standing passenger.
12 Hydraulic cylinder (left and right) Telescoping single-acting cylinders convert
hydraulic pressure into platform lifting and folding force.
13 Hydraulic power unit Contains hydraulic pump driven by electric motor that produces pressure
to raise and fold platform, and a pressure release valve to unfold and lower
it.
14 Manual backup pump
handle Used to operate manual back up-pump (located on hydraulic power unit
cover).
15 Occupant restraint
belt Electrically interlocked safety belt that is intended to prevent acceleration
of wheelchair from platform. Lift will not operate unless belt is properly
connected.
16 Platform (Front) Front portion of platform that unfolds during deploy and folds during stow.
See “Platform folding linkage”.
17 Platform (Rear) Rear portion of platform that is folded by linkage located within the vertical
arms.
18 Platform LED Light (left and right) Directs light onto platform surface.
19 Platform Folding
Linkage (left and right) Directs light onto platform sur-face.
20 Serial Number Location of lift serial number decal.
21 Sto-Loc Catch Engages latch located on bottom of bridgeplate when platform is fully
stowed.
22 Switch (Bridgeplate
Load Sensor) Senses if weight is pre-sent on the lowered bridgeplate.
23 Threshold Warning
System (TWS) Light-beams detect some-thing passing through the threshold area while
platform is below floor level.
24 Top and Bottom
Arms (left and right) - Upper and lower links that connect vertical arms to
baseplate.
25 Vertical Arm left and right) - Connects platform to top and bot-tom arms.
26 Visual Alarm Flashing light makes it known when something passes through threshold
area. Activated by threshold beams.
END OF TABLE

1 - 8
INTRODUCTION JUNE 2021
32DSKF02.D
TITANIUM S-SERIES AND K-SERIES
PUBLIC USE SERVICE MANUAL
Thispageintentionallyleftblank.

2 - 1
INSTALLATIO
N
JUNE 2021
32DSKF02.D
TITANIUM S-SERIES AND K-SERIES
PUBLIC USE SERVICE MANUAL
II. INSTALLATION
his chapter contains instructions for installing the Ricon Titanium™S-Series®and K-Series®Public Use wheel-
chair lift into most vans and busses, although custom installations are also possible in other types of vehicles.
Due to the wide range of lift applications, specific information for every possible application is not available. The
following general procedures will apply to most installations. Contact Ricon Product Support for instruction concerning installations
not covered. To install lift, refer to following sections and perform procedures carefully and in the order that they are presented. Be
certain that installation instructions are followed exactly and do not eliminate any steps or modi-fy product.
NOTE: Please review carefully the installation instructions (32ii463e) that are supplied with this lift before beginning the
following procedures. Where theseprocedures conflict, the installation instructions take precedence.
Public use vehicle manufacturers are responsible for complying with the lift lighting requirements in Federal
Motor Vehicle Safety Standard No. 404, Platform Lift Installations in Motor Vehicles (49 CFR 571.404)
A. GENERAL MECHANICAL INSTALLATION
1. LIFT LOCATION
The installation surface must be flat and level. It is recommended that lift be installed on a ½", minimum, high-grade plywood
sub-floor. However, this additional installation height may not be acceptable in cases where over-head clearance is limited.
Refer to Figure 2-1.
NOTE: Check for proper travel clearance through doorway.
a. With doors fully open, place/position lift in vehicle doorway as close as possible to door, with lift's baseplate assembly
parallel to side of vehicle.
b. Allow a distance of 3/4", if possible, between door and the part of lift closest to it. Adjust lift left and right-side locations
to accommodate subframe members.
c. Verify proper clearance of door frame, passenger seats, and outer edge of vehicle floor and possible inter-ference with
wires, fluid lines, subframe members, etc.
2. VEHICLE DIMENSIONAL REQUIREMENTS
The following figures and text provide installation guidelines for the RICON Titanium S-Series and K-Series Public Use
wheelchair lift into most vans and busses. Adherence to these requirements will verify that the lift installation conforms to the
requirements of FMVSS 403 and 404.
a. VEHICLE DOOR OPENING DIMENSIONAL REQUIREMENTS in inches and [millimeters].
MODEL A(Width) B(Height) C(Floor-To-Ground)
S2005 40.5 [1029] 55.0 [1397] 42.0 [1067]
S2010 43.0 [1092] 55.0 [1397] 42.0 [1067]
S5505 40.5 [1029] 58.0 [1473] 51.0 [1295]
S5510 43.0 [1092] 58.0 [1473] 51.0 [1295]
K2005 40.5 [1029] 55.0 [1397] 37.0 [940]
K2010 43.0 [1092] 55.0 [1397] 37.0 [940]
K5505 40.5 [1029] 58.0 [1473] 48.0 [1219]
K5510 43.0 [1092] 58.0 [1473] 48.0 [1219]
RSM0050300
A
B
C
VEHICLE FLOOR LEVEL
GROUND LEVEL
VEHICLE DOOR OPENING
FIGURE 2-1: DOOR OPENING REQUIREMENTS
T

2 - 2
INSTALLATIO
N
JUNE 2021
32DSKF02.D
TITANIUM S-SERIES AND K-SERIES
PUBLIC USE SERVICE MANUAL
b. VEHICLE FLOOR STRENGTH REQUIREMENTS
NOTE: The Ricon Titanium™model lift structure has been bench tested to four (4) times its rated load. Con-
sistent with the requirements of FMVSS 404, Ricon recommends that the vehicle structure be tested to
three (3) times the rated load of the lift (3,000 lbs.) to ensure sufficient capacity exists in the
NOTE: The Ricon Titanium™lift is shipped with a 1,000 lbs. capacity rating. Ricon understands that the 1,000
lbs. rating is not required to meet the minimum requirements of FMVSS 404. In the event the aforemen-
tioned recommended test load for the Titanium™lift cannot be met, the vehicle manufacturer may de-rate
the installation to 800 lbs. using new decals available from Ricon (Ricon P/N 26201).
NOTE: The table below illustrates the reaction forces present when the lift platform is loaded to three (3) times
the rated capacity or three thousand pounds (3,000 lbs.)
MODEL L1 L2 A * B ** C
S/K-20XX w/51” platform 11.00 36.25 -9,886 12,886 -3,000
S/K-20XX w/54” platform 11.00 37.75 -10,295 13,295 -3,000
S/K-50XX w/51” platform 11.00 41.50 -11,318 14,318 -3,000
S/K-50XX w/54” platform 11.00 43.00 -11,727 14,727 -3,000
*
Negative numbers (column A) indicate tensile load pulling upward at the inboard edge mounting holes of
the base plate.
** Positive numbers (column B) indicate compressive load pushing floor downward at the outboard edge
mounting holes of the base plate.
RSM0050400
L1 L2
C
BA
FIGURE 2-2: FLOOR STRENGTH REQUIREMENTS
3. LIFT INSTALLATION GUIDELINES
The lift mounting is a very important step. Improper mounting or fastening of baseplate can adversely affect lift per-
formance. Although fastening details may vary from one vehicle to the next, these general principles apply:
Be certain that all mounting bolts are properly installed and tightened. Bolts used to fasten baseplate assembly
to vehicle floor must have a minimum strength rating of SAE Grade 5 and be torqued to 28 ft lbs, dry. Recog-
nize that the most important bolts are those along the rear of lift, since these bolts retain the majority of the
load.
Refer to Figures 2-3 and 2-7. Improper torqueing sequence of baseplate bolts may result in a warped or
bowed baseplate, which can cause platform to move erratically.

2 - 3
INSTALLATIO
N
JUNE 2021
32DSKF02.D
TITANIUM S-SERIES AND K-SERIES
PUBLIC USE SERVICE MANUAL
RSM0004800
CORRECT BOWED UP
TIGHTEN HERE
LOOSE N HERE TIGHTEN HERE
LOOSEN HERE
BOWED DOWN
FIGURE 2-3: FORD VAN CLAMPING BAR ARRANGEMENT
4. LIFT INSTALLATION INTO BUSES
Refer to Figure 2-9. Clamping bars are used on most bus installations to help distribute floor loading, and should
only be cut if needed to clear a subframe member. A subframe member should be used to support clamping bar.
RSM0004500
12”
CLAMPING BAR
MINIMUM UNSUPPORTED
CLAMPING BAR LENGTH
CLAMPING BAR SUPPORTED BY
SUBFRAME WHERE POSSIBLE
SUBFRAME MEMBER
VEHICLE FLOOR
FIGURE 2-9: BUS CLAMPING BAR ARRANGEMENT
WARNING
LIFT WEIGHT IS APPROXIMATELY 400-425 LBS. TAKE EXTREME CARE WHEN POSITIONING BECAUSE
STEPWELL BRACKETS MAY TIP. THIS PROCEDURE MUST NOT BE ATTEMPTED BY ONE PERSON.
a. Open doors fully and position lift so that it is centered in vehicle doorway. Close doors and move lift out-
ward until it clears doors by a minimum of ½”. The baseplate must be parallel to side of bus. Open manual
pump release valve (CCW) and allow folded platform to fully settle against latch on baseplate. Verify that
interference is not present between lift and doors. Reposition lift, if necessary. Close pump release valve;
do not over tighten valve.
b. Refer
to Figure 2-10. Mark and drill ten 25/64" baseplate mounting holes (1 thru 10) through vehicle floor.

2 - 4
INSTALLATIO
N
JUNE 2021
32DSKF02.D
TITANIUM S-SERIES AND K-SERIES
PUBLIC USE SERVICE MANUAL
RSM0004600
FIGURE 2-10: BUS BASEPLATE HOLES
CAUTION
Before drilling holes, verify that underlying wires and tubing will not be damaged.
c. Fasten Lift:
1) Insert ten 4" x 3/8" carriage bolts through baseplate and vehicle floor.
2) Refer
to Figure 2-9. Install five clamping bars on bolts underneath vehicle floor (across baseplate), i.e.,
from 1 to 6, 2 to 7, etc, and secure lift to vehicle floor with 3/8" washers, lock washers and hex-nuts.
3) Use care when tightening carriage screws to prevent baseplate warpage. If baseplate assembly warps,
vertical arms will not be parallel. Make corrections by shimming at appropriate locations. To help pre-
vent warping, tighten the eight carriage bolts to 28 ft. lbs. in the following sequence:
3, 8, 2, 4, 7, 9, 1, 5, 6, 10
NOTE: Vertical arms must be parallel for proper operation. Adjust bolts as required. Best results are obtained
when lift is mounted on plywood. Shims, although best avoided, may be used if required.

2 - 5
INSTALLATIO
N
JUNE 2021
32DSKF02.D
TITANIUM S-SERIES AND K-SERIES
PUBLIC USE SERVICE MANUAL
B. ELECTRICAL INSTALLATION
CAUTION
Do not route any wire while it is connected to the battery.
Route wires clear of moving parts, brake lines, and the exhaust system. Secure to the vehicle.
When routing an electrical wire through vehicle floor or walls, use a grommet to protect wires from chafing.
Check underside of vehicle before drilling to avoid damage to fuel lines, vent lines, brake lines, or wiring.
B
4 AWG POWER CABLE:
SHORT CABLE NOT TO EXCEED 12”,
CONNECTED BETWEEN BATTERY (OR
MAIN POWER SOURCE) AND MAIN
CIRCUIT BREAKER
90 AMP MAIN
CIRCUIT BREAKER
BUS BAR
GROUND
SPOOL VALVE
(DECELERATION) 4 AWG POWER CABLE:
LONG CABLE CONNECTED
BETWEEN MAIN CIRCUIT
BREAKER AND POSITIVE
CONNECTION BLOCK
POSITIVE CONNECTION
BLOCK
PRESSURE SWITCH
MAIN POWER HARNESS
CONNECTED TO
SOLENOID
SIDE PUMP
SOLENOID
BUS BAR
(RH SOLENOID)
8 AMP CIRCUIT
BREAKER
TOP PUMP SOLENOID
4 AWG GROUND CABLE
FROM BATTERY TERMINAL
A
MOTOR TERMINAL BOOT
FACTORY INSTALLED ON PUMP
A
MOTOR TERMINAL BOOT
KIT P/N 37152 SHIPPED WITH PUMP HANDLE
ATTACH TO TERMINAL
B
8 AMP CIRCUIT
BREAKER
RSM0050501
HYDRAULIC POPPET
VALVE (DOWN)
FIGURE 2-11: ELECTRICAL INSTALLATION DIAGRAM

2 - 6
INSTALLATIO
N
JUNE 2021
32DSKF02.D
TITANIUM S-SERIES AND K-SERIES
PUBLIC USE SERVICE MANUAL
1. INSTALL MAIN CIRCUIT BREAKER
a. Disconnect battery.
b. Mount main circuit breaker inside engine compartment within 12 inches of battery (to minimize length of un-
protected cable). Avoid installing near a heat source.
2. ROUTE AND CONNECT MAIN POWER CABLE
CAUTION
Check under-side of vehicle before drilling to avoid damage to fuel lines, vent lines, brake lines, or wiring.
NOTE: For applications where power cable is to pass through sheet metal, drill a 3/4" hole and use wire clamp pro-
vided. For applications where cable is to pass through plywood, drill a 1" hole and use black plastic grom-
met provided.
a. Refer
to Figure 2-11 and 2-12. Drill a hole through vehicle floor near positive connection block so power
cable can reach stud of positive connection block. Drill hole where the installed pump cover will cover it.
RSM0050601
A
A
B
MAIN POWER
CABLE
POSITIVE CONNECTION
BLOCK
VEHICLE CHASSIS
GROUND STRAP
1.88”
0.75” DIAMETER HOLE FOR FLOOR METAL.
1.00” DIAMETER HOLE FOR OTHER FLOOR MATERIAL
30” PLATFORM WIDTH = 1.25” DISTANCE
32” PLATFORM WIDTH = 2.25” DISTANCE
B
FIGURE 2-12: POWER CABLE ACCESS HOLE
b. Refer to Figure 2-11. Install supplied heavy ring terminals to each end of the short (12" long) 4 AWG pow-
er cable. Install one ring terminal, only, to one end of long power cable. Use an appropriate crimp tool
(such as Ricon hammer tool, part of kit P/N 01243).
c. Connect ring terminal end of long 4 AWG power cable to 90A main circuit breaker, then route power cable
underneath vehicle floor and up through hole in floor.
d. Refer
to Figure 2-11. Detach Kit P/N 37152 (Shipped with pump handle) then install onto ring terminal
connector before installing ring terminal onto positive connection block.
e. Tie power cable to vehicle chassis, and to pump assembly harness using cable ties. Avoid pinch points,
exhaust system, moving parts, and brake lines. Verify that power cable is secure.
CAUTION
Be sure that there is no interference with any parts that
could damage power cable or other wires in any way.

2 - 7
INSTALLATIO
N
JUNE 2021
32DSKF02.D
TITANIUM S-SERIES AND K-SERIES
PUBLIC USE SERVICE MANUAL
f. Refer to Figure 2-13. Cut excess wire from long cable, install heavy ring terminal, and then connect to pos-
itive connection block. Verify that red wire from main circuit breaker (if applicable) is securely connected to
positive connection block. CAUTION
Ensure that shrink tube and black boots are secure and
properly installed on both wire connections near the
positive connection block.
RSM0050701
POSITIVE
CONNECTION
BLOCK
4 AWG POWER
CABLE CONNECTION
TO BATTERY
VEHICLE CHASSIS
GROUND STRAP
MAIN POWER
CABLE CONNECTION
TO PUMP MOTOR
FIGURE 2-13: CABLE ROUTING
g. Refer to Figure 2-11. Connect 12" cable, with ring terminals, from positive battery terminal to main circuit
breaker terminal.
3. GROUND CONNECTIONS
a. Refer
to Figure 2-13. Locate 4GA vehicle chassis ground cable that is pre-installed then install ground ca-
ble to vehicle chassis. Avoid pinch points, exhaust system, moving parts, and brake lines. Verify that
ground cable is secure.
b. Ensure other wires that are fasted with the ground cable are secure and remain connected after installation.
c. 12 VDC Systems
12 VDC powered lifts are chassis grounded and do not require a separate ground cable connection to bat-
tery. However, if the common side of the lift electrical system is connected to chassis with a cable, the ca-
ble must be attached in a manner that provides a reliable electrical connection. If ground cable is attached
to an existing ground circuit, the circuit must be capable of conducting an additional 90 amps.
4. CONTROL PENDANT
The water resistant control pendant can be connected on either the left hand or right hand side of the
wheelchair lift. Connections for the control pendant are located on the pump chassis, close to the connec-
tion block. An alternate control pendant connection is located opposite the pump chassis, near the stow
lock cover. CAUTION
Only one control pendant can safely operate the
wheelchair lift at any time. Use of more than one control
pendant at the same time is not permitted.
a. Press Power switch to OFF position on control pendant. Illuminated lights will turn off.
b. Refer to Figure 2-14. Locate control pendant connector installed on pump chassis side of wheelchair lift.
c. Twist and unlock connector then remove from pump chassis.
This manual suits for next models
9
Table of contents
Other Wabtec Lifting System manuals
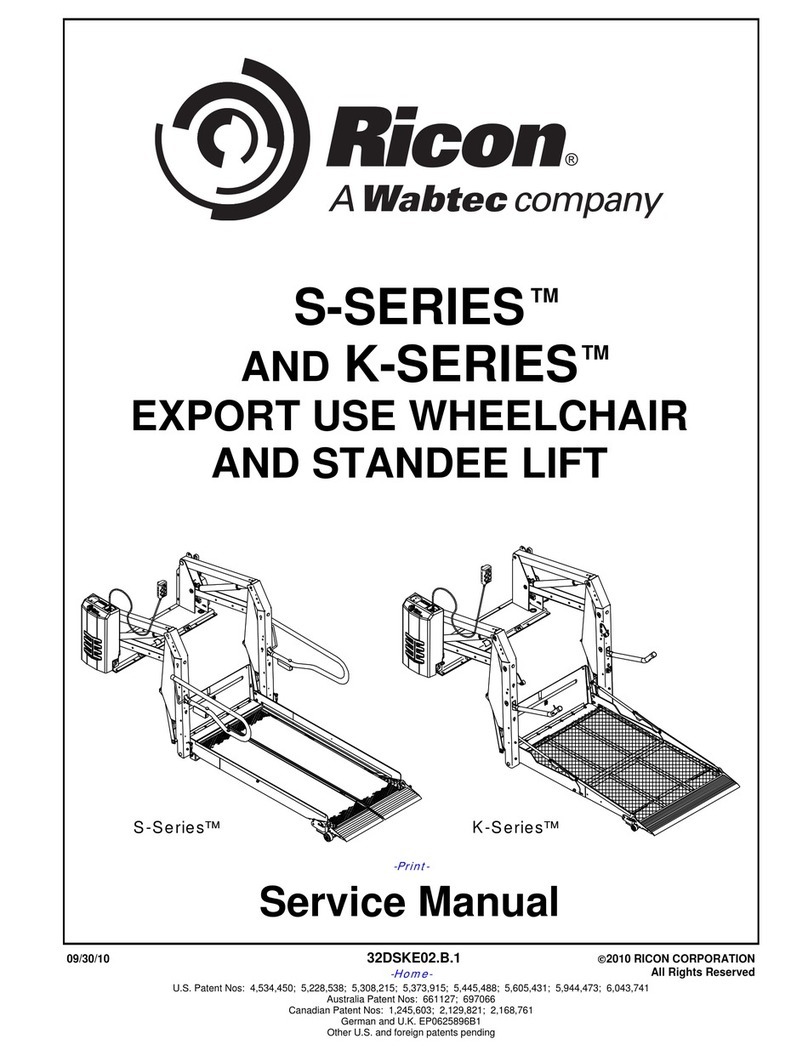
Wabtec
Wabtec Ricon S Series User manual

Wabtec
Wabtec Ricon S Series User manual

Wabtec
Wabtec R-290 User manual
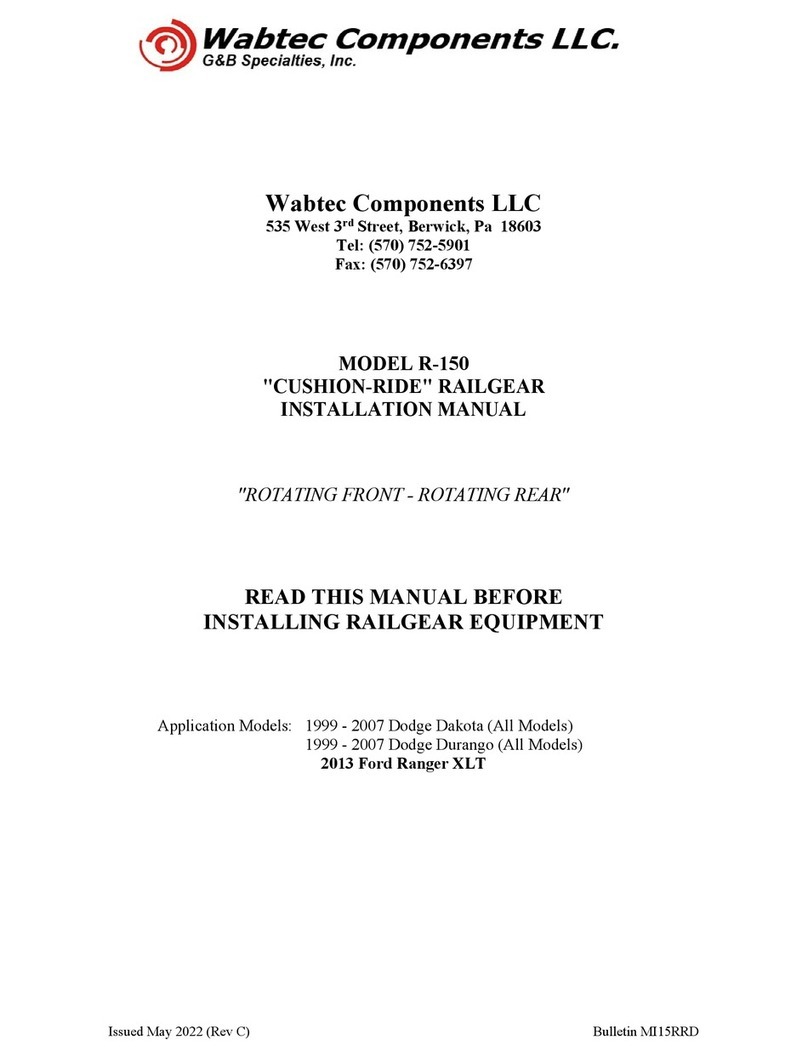
Wabtec
Wabtec R-150 User manual

Wabtec
Wabtec Ricon S Series User manual

Wabtec
Wabtec Ricon S Series User manual
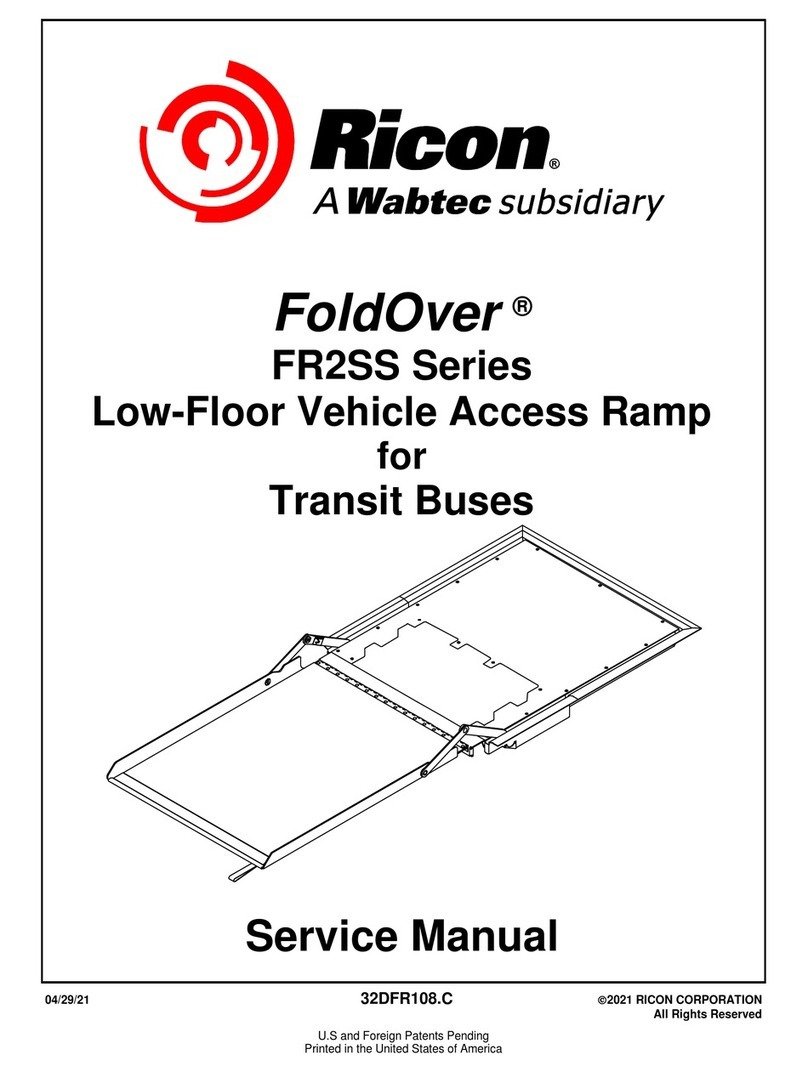
Wabtec
Wabtec Ricon FoldOver FR2SS Series User manual
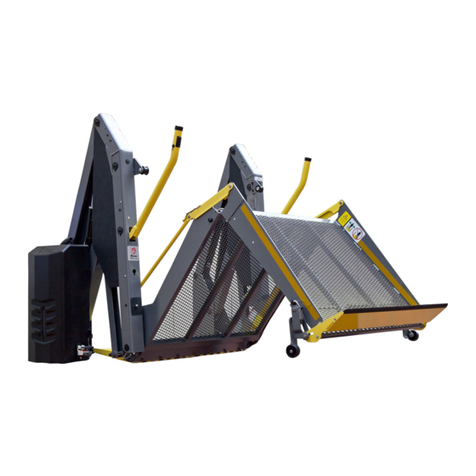
Wabtec
Wabtec Ricon K Series User manual
Popular Lifting System manuals by other brands
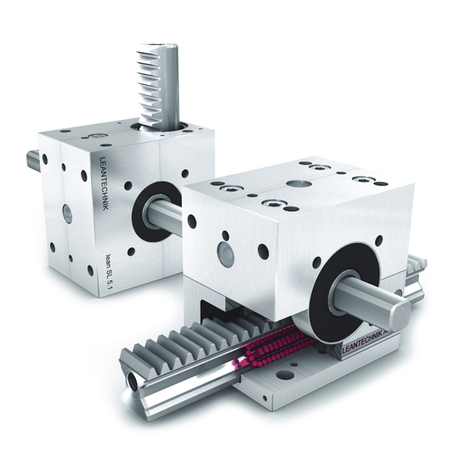
Leantechnik
Leantechnik Lifgo Series INSTRUCTIONS FOR INSTALLATION, COMMISSIONING AND MAINTENANCE
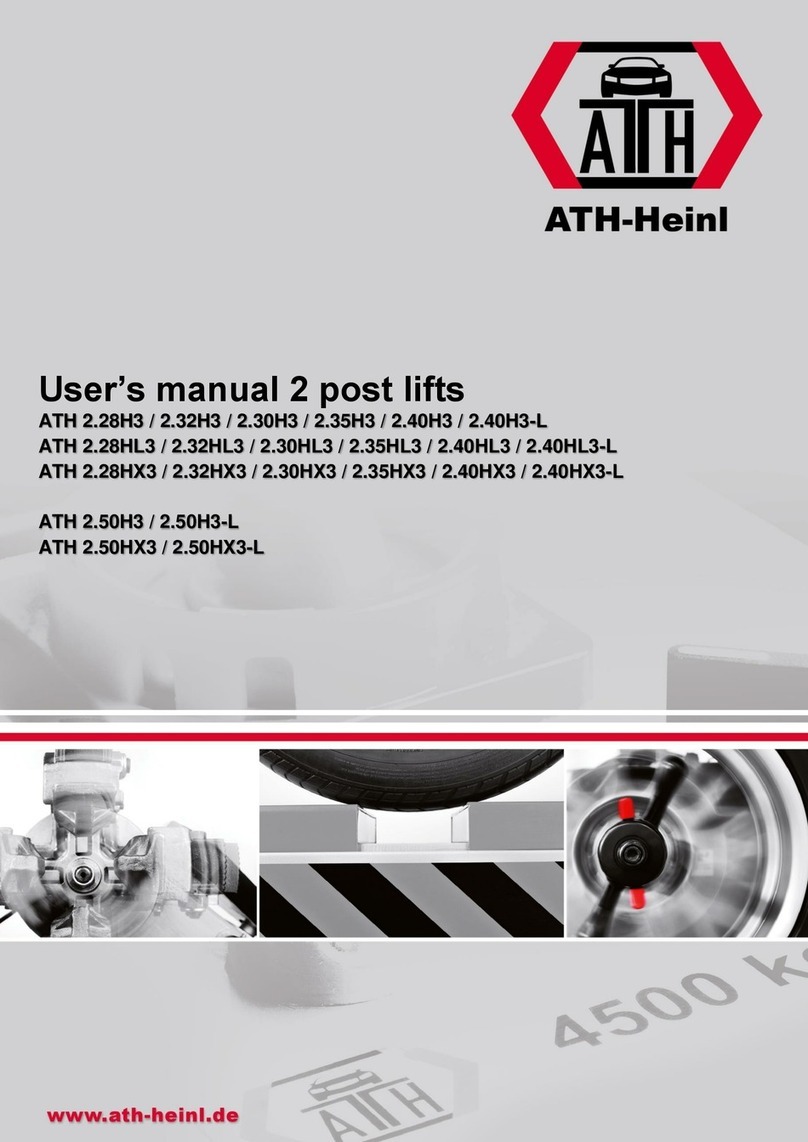
ATH-Heinl
ATH-Heinl ATH 2.28H3 user manual
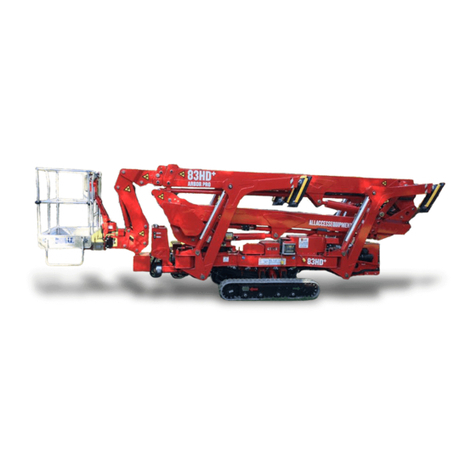
CMC
CMC 83 HD+ ARBOR PRO manual
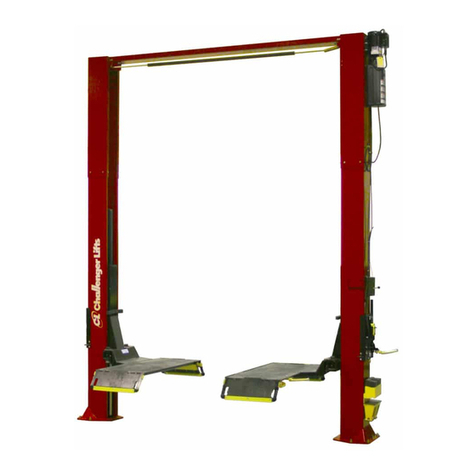
Challenger Lifts
Challenger Lifts CL10 Installation, operation & maintenance manual
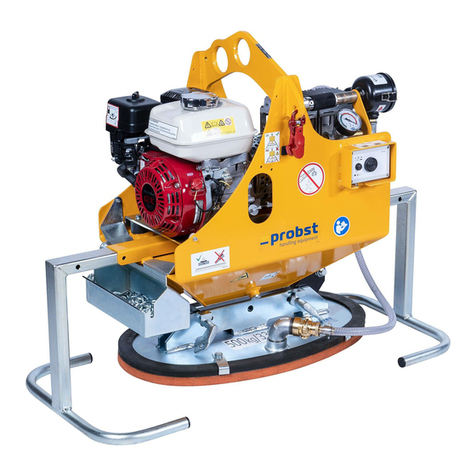
probst
probst SH-1000-MINI operating instructions
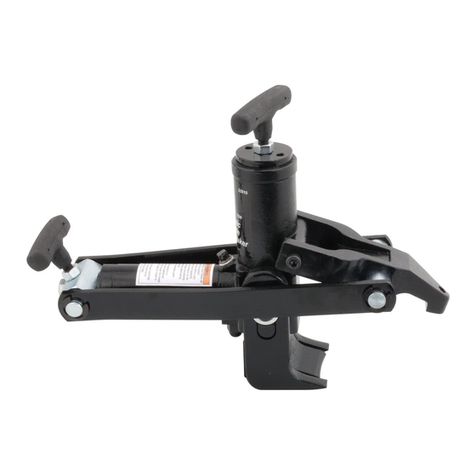
Omega
Omega 22910 Operating instructions manual