WIFO K75A Operator's manual

WIFO-Anema B.V.
Hegebeintumerdyk 37 – 9172 GP Ferwert – Holland
Telefoon (0031) 518411318 – Telefax (0031) 518411563
www.wifo.nl – email: [email protected]
Manual and safety instructions
K75A/K75B/K80/K85
Forward tipping box rotator
GB
K75A K75B
K80 K85


1
English
Table of contents
1. TO THE USER ...................................................................................................................................................................... 2
1.1 INTRODUCTION ...................................................................................................................................................................... 2
1.2 SAFETY PRECAUTIONS AND WARNINGS........................................................................................................................................ 3
1.2.1 Safety precautions .................................................................................................................................................... 3
1.2.2 Saftey stickers and warning signs............................................................................................................................. 6
1.2.3 Location of the safety stickers on the machine......................................................................................................... 6
1.3 PURPOSE OF USE .................................................................................................................................................................... 7
1.4 LIABILITY............................................................................................................................................................................... 8
1.5 WARRANTY ........................................................................................................................................................................... 8
2. TECHNICAL DATA ............................................................................................................................................................... 9
2.1 GENERAL TECHNICAL DATA....................................................................................................................................................... 9
2.2 K75A ................................................................................................................................................................................ 11
2.2.1 Parts list .................................................................................................................................................................. 11
2.3 K75B................................................................................................................................................................................. 12
2.3.1 Parts list .................................................................................................................................................................. 12
2.3.2 Commissioning the K75A and K75B box rotators................................................................................................... 13
2.4 K80................................................................................................................................................................................... 15
2.4.1 Parts list .................................................................................................................................................................. 15
2.5 K85................................................................................................................................................................................... 16
2.5.1 Parts list .................................................................................................................................................................. 16
2.5.2 Commissioning the K80 and K85 box rotators........................................................................................................ 17
2.6 PROVISIONS FOR CONNECTING K75A/K75B/K80/K85 .............................................................................................................. 19
2.7 REPLACEMENT COMPONENTS.................................................................................................................................................. 20
3. MAINTENANCE AND TROUBLESHOOTING ........................................................................................................................ 21
3.1 PREVENTIVE MAINTENANCE AND LUBRICATION ........................................................................................................................... 21
3.2 TROUBLESHOOTING .............................................................................................................................................................. 22
3.2.1 Adjustment of electrical limit switch....................................................................................................................... 22
3.2.2 Adjustment of hydraulic limit switch ...................................................................................................................... 23

2
1. To the user
1.1 Introduction
The aim of this manual is to inform users about the commissioning, use and maintenance of their new WIFO forward
tipping box rotator. Also included in this manual are a number of safety instructions to create a safe working
environment.
At WIFO-Anema B.V. we aim to continuously improve our products. WIFO-Anema B.V. reserve the right to introduce
any changes and improvements deemed necessary without prior notice.
Please read the manual thoroughly and observe the safety procedures before putting the unit into operation.
Contact your dealer for any further questions or concerns you may have.
We trust that your WIFO forward tipping box rotator will provide many years of useful service.
Keep this manual in a safe place for future reference!
WIFO-Anema B.V.
Dealer:
ATTENTION:
Carefully read this manual before you put the machine into operation and act upon all directions that are
given. This is to guarantee its safe, trouble-free operation.

3
1.2 Safety precautions and warnings
Please read this manual before you put the machine into operation for the first time, and observe the safety
instructions at all times. The most important instructions are marked with a symbol.
Any person in charge of the commencement of operation, the operation itself or the maintenance of the machine is
urged to carefully read and observe the following instructions.
1.2.1 Safety precautions
The following safety instructions apply to all types of WIFO forward tipping box rotators. No distinction is made with
regard to the type of lifting vehicle used.
This symbol is used for all important actions that should not be carried out under any circumstances.
Carefully observe these prohibitions.
Do not allow anyone to hitch a ride.
Persons must not stand below the load, and must
remain outside the tipping range of the equipment. Bear
in mind that items may fall from the box.
This symbol is used for all important safety instructions throughout this manual. Carefully observe the
instructions and be very cautious.

4
Adjust the upper clamp to take account of the height
and depth of the boxes to be tipped.
Raise the upper clamp using the clamping cylinder
before picking up the box with the box rotator.
Distribute the load as evenly as possible over the forks.
Keep the load as low as possible during transportation
to maximise the stability of the lifting vehicle. Boxes
must always be clamped during transportation.

5
Make sure the hydraulic hoses and any power cables do not get jammed and that the box rotator is able to
move freely.
Only sound boxes must be used for tipping operations.
The tipper must be placed in its lowest position when parking the lifting vehicle. Ensure that the
clamp/vehicle combination cannot make any unintended movements while the vehicle is not in use. Place the
rotator on its back on a flat, stable surface after it has been removed from the forklift truck / mast for
storage.
Ensure that the operating levers for tipping and clamping cannot be confused with each other or with other
controls, in order to prevent unintended operation. Only the rotating cylinder function remains in the event
of a power cut while operating an electrically controlled valve.
T
he box rotator must only be operated from the driver's position in the vehicle. Ensure that there is adequate
visibility of the work activities from this position

6
1.2.2 Saftey stickers and warning signs
Several safety stickers have been put onto the machine. The meaning of the stickers on this machine is as follows:
1.2.3 Location of the safety stickers on the machine
A safe working environment also requires personnel to be well-informed about the various safety stickers
on the machine. Be aware of the hazards they warn you to look out for.
Replace any loose, illegible or missing stickers.
Figure 1.2.1-Location of safety stickers for K75A Figure 1.2.2-Location of safety stickers for K75B
N.B.:
Please read the instruction manual prior to any maintenance to the machine.
Turn off the engine and remove the key from the ignition while maintenance
is carried out on the machine!
1
1 2 1 2
Danger:
Always keep at a safe distance from the machine!
2

7
1.3 Purpose of use
WIFO K75A and K75B forward tipping box rotators are suitable only for the transportation and forward tipping of
boxes, provided the total weight of the box and its load does not exceed 1750kg for the K75A and 2750kg for the
K75B.
WIFO K80 and K85 forward tipping box rotators are suitable only for the transportation and forward tipping of
boxes, provided the total weight of the box and its load does not exceed 2500kg. These box rotators are suitable
only for attachment to the FEM II or FEM III fork carrier of a forklift truck or lifting mast.
The box rotator must in no circumstances be used for the carriage of persons!
ATTENTION:
The capacity of the reach truck must exceed the total mass of the forward tipping box rotator, the box and
its load. The reach truck must be equipped with a double action hydraulic connection on the telescopic
boom.
Figure 1.2.3-Location of safety stickers for K80 Figure 1.2.4-Location of safety stickers for K85
ATTENTION:
The capacity of the forklift truck or lifting mast must exceed the total mass of the forward tipping box
rotator, the box and its load. The forklift truck or lifting mast must be equipped with a double action
hydraulic connection at the fork carrier, as a minimum. The format will depend on the width of the boxes
to be tipped.
1 2 1 2

8
1.4 Liability
Any person working with or on the machine must have read this manual. The machine is to be used for its intended
purpose only. Included in the intended purpose are, among other things:
1. Work must be carried out in accordance with the directions and within the functional restrictions (e.g.
maximum hydraulic working pressure) as outlined in the regulations. Use only sound and appropriate tools.
2. Electric/electronic equipment and accessories (e.g. cables) must be treated in accordance with the general
accepted policy for using non-waterproof portable electric and electronic equipment, such as:
a) Storing and keeping in a clean, dry environment away from rodents and the like; and
b) Protecting the equipment against severe, uncushioned schocks and water (precipitation).
3. Use only original or compatible spare parts. Such parts must be assembled as directed (e.g. by observing the
recommended tightening moments). Spare parts (as well as lubricants) are considered compatible only if
explicitly approved by WIFO or in the event that the customer is able to prove they possess the required
properties for the purpose(s) they are used.
4. Use only lubricants that meet the specifications as described in the directions.
5. Always observe the local regulations in terms of accident prevention, safety, traffic and transport.
6. Only trained personnel with knowledge of the possible hazards have permission to work with/on the
machine.
7. WIFO-Anema B.V. will assume no liability in any shape or form for losses or damage caused following
modifications to the machine, which have not been explicitly approved by WIFO.
1.5 Warranty
WIFO-Anema B.V. guarantees the soundness of its products in terms of materials used and/or structural defects.
However, in any event this warranty is limited to the free-of-charge replacement or repairs of the defect product, or
part thereof. WIFO-Anema B.V. assumes no liability for any loss or damage arising from faulty deliveries and/or the
breakdown of purchased goods before the warranty period has expired. The warranty period for this product is
twelve months.
Noncompliance with the rules and directions from this manual will be considered as serious negligence, for
the consequences of which WIFO-Anema B.V. accepts no liability whatsoever. In such cases, the user will
bear the full risk of his actions!
WIFO-Anema B.V. is continuously working on the improvement of its products. For that reason, WIFO-
Anema B.V. reserves the right to introduce any changes and improvements deemed necessary without
prior notice. However, it does not imply an obligation to make any such changes or improvements to
machines bought by customers in the past!

9
2. Technical data
2.1 General technical data
1Without inclination of reach truck or shovel frame/with inclination of reach truck or shovel frame.
The K75A and K75B are suitable for attachment to reach trucks and heavy front loaders.
The K80 forward tipping box rotator is suitable for attachment to FEM II (407mm) and FEM III (508mm) fork carriers.
Table 2.1.1-K75A and K75B forward tipping box
Type K75A K75B
Max. carrying capacity
1750 kg 2750 kg
Weight 615 kg 725 kg
Max. working pressure 18 Mpa (180 bar) 18 Mpa (180 bar)
Centre of gravity 500 mm 531 mm
Frontal extension length 500 mm 500 mm
Transport width 1300 mm 1600 mm
Tipping angle
1
± 110°/180° ±110°/180°
Type K80-1200 K80-1400 K80-1600 K80-1800
Max. carrying capacity 2500 kg 2500 kg 2500 kg 2500 kg
Weight 580 kg 610 kg 640 kg 670 kg
Max. working pressure 18 Mpa (180 bar) 18 Mpa (180 bar) 18 Mpa (180 bar) 18 Mpa (180 bar)
Centre of gravity 560 mm 560 mm 560 mm 560 mm
Frontal extension length 440 mm 440 mm 440 mm 440 mm
Transport width 1586 mm 1786 mm 1986 mm 2186 mm
Tipping angle 135° 135° 135° 135°
Type K80-2000 K80-2240 K80-2400
Max. carrying capacity 2500 kg 2500 kg 2500 kg
Weight 700 kg 730 kg 955 kg
Max. working pressure 18 Mpa (180 bar) 18 Mpa (180 bar) 18 Mpa (180 bar)
Centre of gravity
560 mm
560 mm
560 mm
Frontal extension length 440 mm 440 mm 440 mm
Transport width 2386 mm 2626 mm 2786 mm
Tipping angle 135° 135° 135°
Table 2.1.2-K80 forward tipping box

10
The K85 forward tipping box rotator is suitable for attachment to FEM II (407mm) and FEM III (508mm) fork carriers.
Type Letter Description
K75A/K75B/K80/K85 E Electrically controlled switching valve
S 4-hose connection
Table 2.1.4-Description data on model plate
The box rotators are equipped with an electric or hydraulic limit switch to prevent unintended opening of the upper
clamp during tipping. The upper clamp can only be opened when the tipping frame is horizontal.
Type K85-1200 K85-1400 K85-1600 K85-1800
Max. carrying capacity 2500 kg 2500 kg 2500 kg 2500 kg
Weight 700 kg 725 kg 745 kg 765 kg
Max. working pressure 18 Mpa (180 bar) 18 Mpa (180 bar) 18 Mpa (180 bar) 18 Mpa (180 bar)
Centre of gravity 625 mm 625 mm 625 mm 625 mm
Frontal extension length 440 mm 440 mm 440 mm 440 mm
Transport width 1656 mm 1856 mm 2056 mm 2256 mm
Tipping angle 180° 180° 180° 180°
Type K85-2000 K85-2240 K85-2400
Max. carrying capacity 2500 kg 2500 kg 2500 kg
Weight 790 kg 815 kg 1010 kg
Max. working pressure 18 Mpa (180 bar) 18 Mpa (180 bar) 18 Mpa (180 bar)
Centre of gravity 625 mm 625 mm 625 mm
Frontal extension length 440 mm 440 mm 440 mm
Transport width
2456 mm
2696 mm
2856 mm
Tipping angle 180° 180° 180°
Table 2.1.3-K85 forward tipping box

11
2.2 K75A
2.2.1 Parts list
Number Description Number Description
1 Main frame 11 Tipping cylinder bush side pin
2 Tipping frame 12 Tipping axle washer
3 Upper clamp height adjustment 13 Tipping cylinder piston rod side pin
4 Upper clamp 14 Tipping cylinder piston rod side washer
5 Upper clamp valve 15 Clamping cylinder bush side pin
6 Upper clamp slide tube 16 Clamping cylinder piston rod side pin
7 Support leg 17 Height adjustment pin
8 Tipping axle 18 Support leg pin
9 Rotating cylinder DW 70-40-410 19 Bronze bearing bush
10 Clamping cylinder DW 50-30-330 20 Stripper R50
Table 2.2.1-Parts list for K75A

12
2.3 K75B
2.3.1 Parts list
Number Description Number Description
1 Main frame 11 Tipping cylinder bush side pin
2 Rotating frame 12 Tipping pin washer
3 Upper clamp height adjustment 13 Tipping cylinder piston rod side pin
4 Upper clamp 14 Tipping cylinder piston rod side washer
5 Upper clamp valve 15 Clamping cylinder bush side pin
6 Upper clamp slide tube 16 Clamping cylinder piston rod side pin
7 Support leg 17 Height adjustment pin
8 Tilting pin 18 Support leg pin
9 Rotating cylinder DW 70-40-410 19 Bronze bearing bush
10 Clamping cylinder DW 70-40-410 20 Upper clamp rotation point pin
Table 2.3.1-Parts list for K75B

13
2.3.2 Commissioning the K75A and K75B box rotators
Type K75A and K75B forward tipping box rotators can be supplied with the necessary fitting components or
without (bare machine). In the former case users must make their own arrangements for the attachment. In
the latter case, the type of machine to which the K75A or K75B is to be fitted should be specified. Where
available fitting can take place in the factory, and the normal guarantee provisions will apply.
1. Bear in mind that with an electrically controlled switching valve, 1 double action hydraulic connection must
be present on the lifting vehicle, and with a 4-hose connection, 2 double action hydraulic connections.
Connection of hydraulic hoses
Depending on the model, the following hydraulic hoses are connected:
a) Electrically controlled reversing valve
Connect the hydraulic supply/discharge hoses to the dual-action connection on the fork carrier.
Install the supplied switch so that the machine driver is able to operate it from his driving position and
cannot confuse it with other controls. For a safe working environment, avoid situations such as inadvertently
starting the machine or not being able to control it.
Keep an eye on the correct voltage of the lifting device and the valve. The voltage is shown on the coil.
Connect a twin core cable in accordance with the circuit diagram. Include a warning light, fuse and/or plug
socket in the circuit if required.
b) Four-hose connection
Connect the two pairs of hydraulic supply/discharge hoses to the dual-action connection on the fork carrier.
ATTENTION:
WIFO-Anema B.V. can accept no liability for the construction and mounting of fitting equipment
attached by users themselves.

14
1. If the box is raised at all, the upper clamp should be horizontal or sloping on the box in the direction of the
valve front plate. This can be adjusted as follows:
Adjusting the upper clamp
-Remove the pins and securing clips from the upper clamp and the pin and securing clip from the
clamping cylinder.
-Using the box and the pins with their securing clips, adjust the height of the upper clamp.
-Set the upper clamp vertically, slide the clamping cylinder(s) fully home and secure to the tipping
frame using the pin. With the clamping cylinder in its extended position, the upper clamp will now
pass around 10° through the 90° position. This is sufficient to clamp the box.
2. With the back of the box against the tipping frame, the front plate of the upper clamp should be just on the
edge of the box, against the front of the box. This can be adjusted as follows:
-Loosen the upper clamp securing bolts.
-Slide the valve up against the box and retighten the upper clamp using the securing bolts and
locknuts (105Nm).
-The slide out tubes should be adjusted so that they fit just within the width of the box.
The WIFO forward tipping box rotator is now ready for use.
Ensure that the hydraulic hoses and electrical cables cannot become trapped during use.

15
2.4 K80
2.4.1 Parts list
Number
Description
Number
Description
1 Fixed frame 11 Clamping plate FEM II/III
2 Rotating frame 12 Rotary pin
3 Adjusting tube 13 Cylinder pin
4 Upper clamp slide-in frame 14 Rotating point pin
5 Upper clamp 15 Cylinder washer
6 Clamping cylinder DW 50-30-330 16 Rotary pin
7 Category II top pin 17 Bump rubber
8 Clamping cylinder pin 18 Bump rubber
9 Rotating cylinder DW 60-30-410 19 Bronze bushing
10 FEM II/III mounting block 20 Bronze tipping cylinder bushing
Table 2.4.1-Parts list for K80 forward tipping box rotator

16
2.5 K85
2.5.1 Parts list
Number Description Number Description
1 Fixed frame 14 Cover plate
2 Rotating frame 15 Cover plate
3 Slide-in upper clamp 16 Gear wheel
4 Upper clamp 17 Bearing
5 FEM II/III clamp pin 18 Cover plate
6 Upper clamp adjustment beam 19 Tipping cylinder pin
7 Tipping cylinder DW 60-35-280 20 Washer
8
Clamping cylinder DW 50-30-330
21
Locking ring
9 Locking plate 22 Rack
10 FEM II/III mounting block 23 Clamping plate
11 Bump rubber 24 Rotary pin
12 Bearing plate, complete 25 Guide block
13 Category II top pin 26 Clamping cylinder pin
Table 2.5.1-Parts list for K85 forward tipping box rotator

17
2.5.2 Commissioning the K80 and K85 box rotators
Different methods are used to fit the mounting blocks and clamping plate, depending on the type of fork
carrier used. These are described below.
FEM II fork carrier
1. Loosen the FEM II/III mounting block bolts and remove the mounting blocks.
2. Reattach the mounting blocks using the bolts, so that the FEM II is underneath. Tighten the bolts securely
(200Nm).
3. Remove the clamping plate with the pins and retaining clips.
4. Remove the forks from the forklift truck or forklift mast.
5. Make sure the fork carrier is straight and clean.
6. Place the box rotator on the forklift truck or lifting mast fork carrier, depending on the box dimensions.
7. Make sure the locking cam slots into the recess in the centre of the fork carrier. If no recess is available:
a) Grind such a recess; or
b) Grind the locking cam from the box rotator and attach a sound locking cam on the spot of an existing recess
in the fork carrier. In doing so, make sure the box rotator sits secure in the centre in front of the fork carrier,
so it is unable to slide sideways
8. Attach the clamping plate to the fork carrier profile with the FEM II profile above, using the 9x11 pins and
retaining clips.
9. Check to make sure the hydraulic hoses are clean before connecting them to the rapid-action couplings to
prevent any debris from entering the hydraulics of the machine.
10. Depending on the model, the following hydraulic hoses are connected:
a) Electrically controlled switching valve
Connect the hydraulic supply/discharge hoses to the dual-action connection on the fork carrier.
Install the supplied switch so that the machine driver is able to operate it from his driving position and
cannot confuse it with other controls.
For a safe working environment, avoid situations such as inadvertently starting the machine or not being
able to control it.
Keep an eye on the correct voltage of the lifting device and the valve. The voltage is shown on the coil.
Attach a twin core cable in accordance with the circuit diagram. Include a warning light, fuse and/or plug
socket in the circuit if required.
b) Four-hose connection
Connect the two pairs of hydraulic supply/discharge hoses to the dual-action connection on the fork carrier.
FEM III fork carrier
1. See FEM II fork carrier, however the mounting blocks must be fitted with the FEM III profile below, while the
clamping plate should have its FEM III profile above.

18
1. If the box is raised at all, the upper clamp should be horizontal or sloping on the box in the direction of the
valve front plate. This can be adjusted as follows:
Adjusting the upper clamp
-Remove the pins and securing clips from the upper clamp and the pin and securing clip from the
clamping cylinder.
-Using the box and the pins with their securing clips, adjust the height of the upper clamp.
-Set the upper clamp vertically, slide the clamping cylinder(s) fully home and secure to the tipping
frame using the pin. With the clamping cylinder in its extended position, the upper clamp will now
pass around 10° through the 90° position. This is sufficient to clamp the box.
2. With the back of the box against the tipping frame, the front plate of the upper clamp should be just on the
edge of the box, against the front of the box. This can be adjusted as follows:
-Loosen the upper clamp securing bolts.
-Slide the valve up against the box and retighten the upper clamp using the securing bolts and
locknuts (105Nm).
-The slide out tubes should be adjusted so that they fit just within the width of the box.
The WIFO forward tipping box rotator is now ready for use.
Ensure that the hydraulic hoses and electrical cables can not become trapped during use.
This manual suits for next models
3
Table of contents
Other WIFO Lifting System manuals
Popular Lifting System manuals by other brands
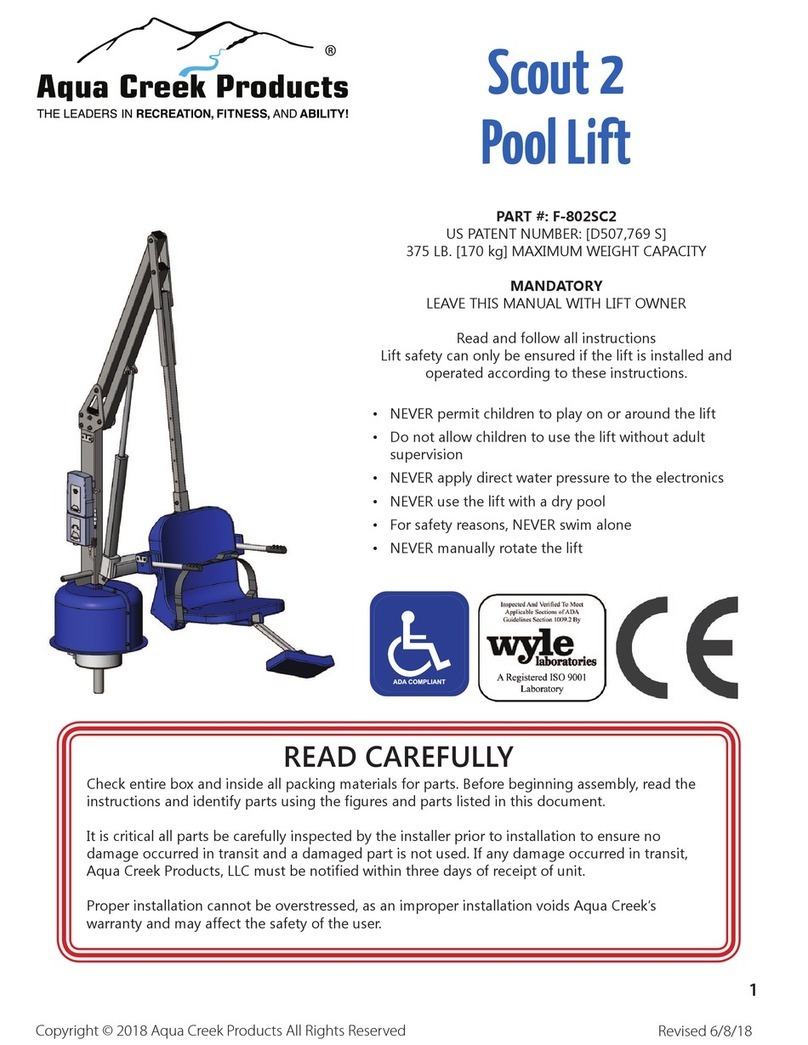
Aqua Creek
Aqua Creek Scout 2 user manual

SYSTEMS
SYSTEMS McGuire VSH Series Owner & user manual

JLG
JLG G6-42A Replacement instructions
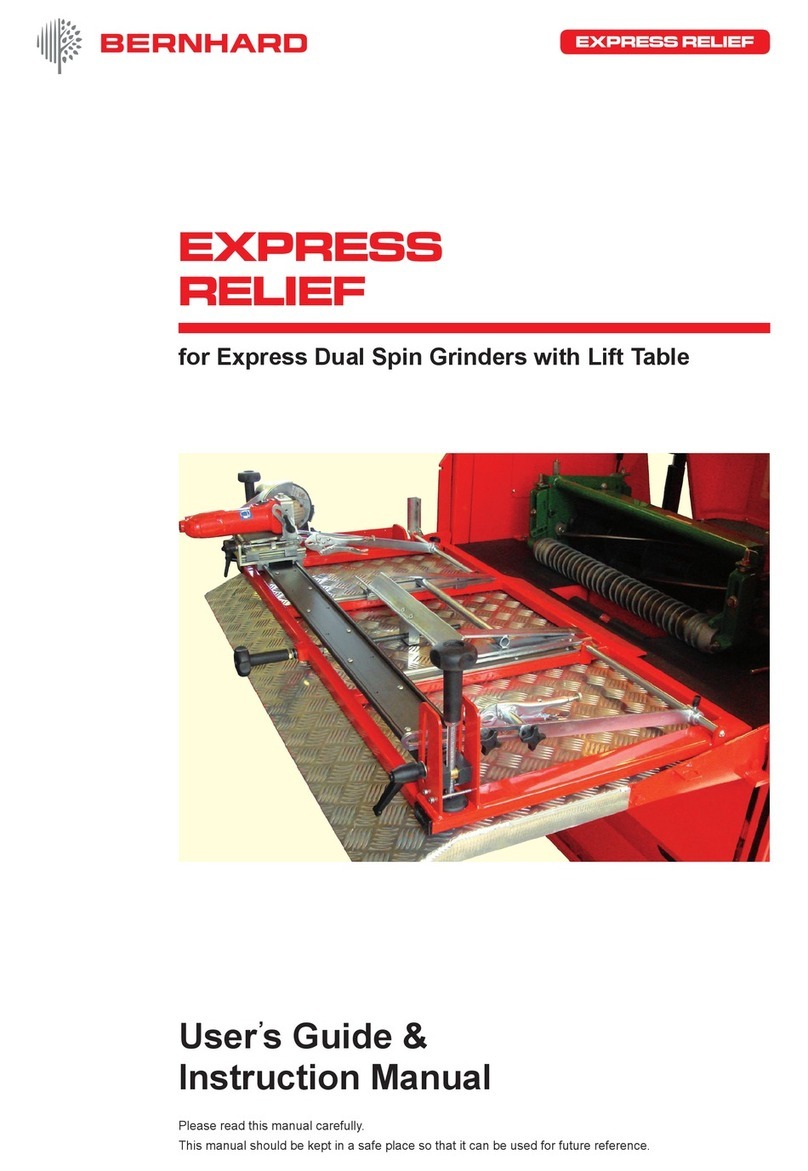
Bernhard
Bernhard EXPRESS RELIEF User guide/instruction manual
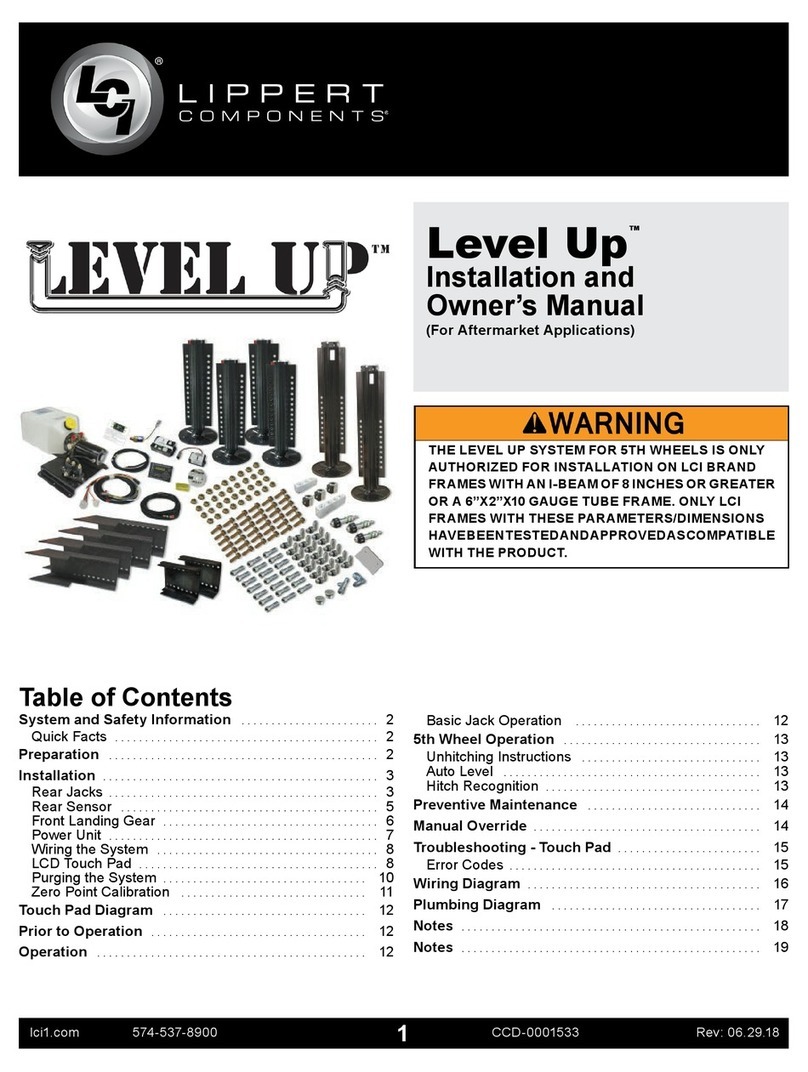
Lippert Components
Lippert Components Level-Up Installation and owner's manual
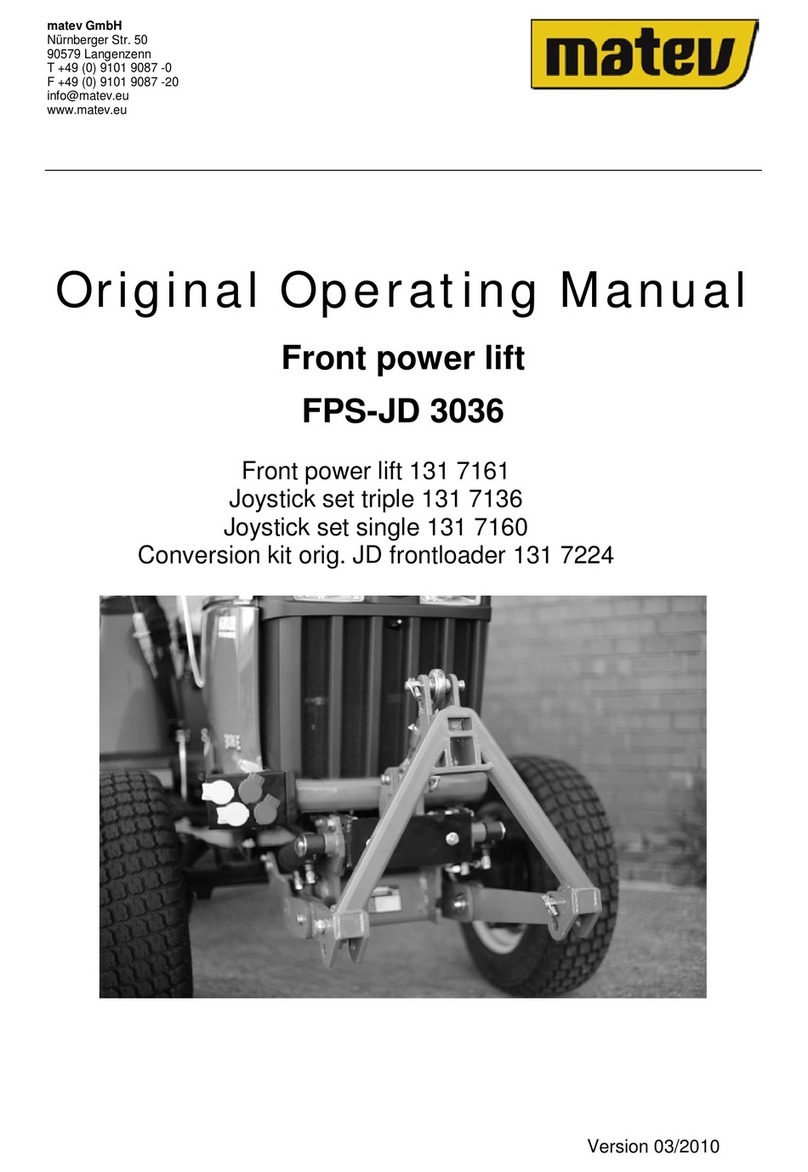
matev
matev FPS-JD 3036 Original operating manual