Global IFS FDU-1-1 User manual

Page: 1 of 9Global IFS Fan Powered Box
Global IFS Fan Powered Box
Installation Instruction
Tool Check List
#2
Fan Powered Box & Terminal Unit (FPB & TU)

Page: 2 of 9Global IFS Fan Powered Box
1290 Barrow Ind. Parkway
Winder, GA 30680-5704
Phone: (678) 425-6640
Fax: (678) 425-6659
1462263
FDU-1-X
PRICE RESEARCH CENTER
VAV-101
Configuration = B; Fan Volume = 300 CFM
1 FDU-1-1 20 FLD /
6000 FG50 ECM
115 Volts
0 CFM 0 CFM
4P-RE,
HWC,
CWC
LH-HEAT, 1H, LH-COOL, 1C, GALV DC, SB-E
0 L/S 0 L/S
REPRINTED
O1462263000100010001 Printed on 10/08/2018
1462263 1 FDU-1-1 20
1462263 1 FDU-1-1 20
Min.0 CFM Max.0 CFM
Min. 0 L/S Max. 0 L/S
Control Assembly Label
All Global IFS fan powered terminal units are tagged with a control assembly label as shown on the left. This label
identifies the model number, location tag #, controller type, actuator type, thermostat action, application and
controller setpoints. Options, accessories and appropriate control diagrams are also identified. If field adjustment of
the controller factory setpoints should become necessary, follow the appropriate procedure outlined in the manual.
All factory supplied controllers are tagged with a controller label as shown below. This label identifies the required
sensor velocity pressure for both the minimum and maximum controller setpoints.
FAN POWERED BOX & TERMINAL UNIT

Page: 3 of 9Global IFS Fan Powered Box
INSTALLATION OVERVIEW
Fan Terminal Installation
Instructions
Mounting The Unit
1. Global IFS Fan Powered Terminal Units are designed to be mounted in the direction indicated by the Control
Assembly Label found on the protective shroud.
2. Mount the unit directly on the sub-floor, beneath the raised floor. Ensure the area where the unit is to go is clear of
cables, wires, etc.
3. Position the unit so that there is no interference with the raised floor support members.
4. Install the unit in a location that allows free access to the unit as well as all control components.
5. Ensure main power to the terminal and electrical coil has been disconnected prior to performing any electrical
work or inspection of the circuitry.
WARNING: Do not tamper with control components.
Fan Terminal Duct Connection
1. To prevent excessive air leakage, all cleat joints should be sealed with an approved duct sealer. This applies to all
accessory connections as well as the basic fan box.
2. Holes that are drilled in the duct for testing or balancing purposes are to be sealed with duct tape or duct sealer.
3. A minimum of 0.10 inches W.G. downstream static pressure is required to prevent overheating of the fan motor.
Fan Terminal Electrical Connection
1. All field wiring is to be in accordance with the National Electrical Code ANSI/NFPA No. 70 or the Canadian Electrical
Code , Part 1, CSA Standard C 22.1 and local codes and standards.
2. Refer to the product identification label on each unit for information to determine the field wire size.
CAUTION: Check voltage requirements prior to power supply connection. Refer to the electrical label located near the electrical
control box and also refer to the schematic drawing provided on the underside of the electrical control box cover.
3. If upon energizing the electric motor(s), excessive noise is apparent, shut down the unit. Determine the cause by
checking for packing materials, etc. and re-energize after corrective action has been taken.
4. If an Electric Reheat Coil has been supplied, refer to the electrical schematic which is permanently affixed to the
topside of the electrical control cabinet cover, prior to hook-up.
CAUTION: Check the voltage requirements to ensure proper voltage supply is used
FAN POWERED BOX & TERMINAL UNIT

Page: 4 of 9Global IFS Fan Powered Box
FAN POWERED BOX & TERMINAL UNIT
START UP & OPERATION
Air System Balancing
Overview
All ductwork must be complete and connected, and all grilles, filters, access doors and panels must be properly installed to
establish actual system operating conditions BEFORE beginning air balancing operations. Each individual unit and attached
ductwork is a unique system with its own operating characteristics. For this reason, air balancing is normally done by balance
specialists who are familiar with all procedures required to properly establish air distribution and fan system operating
conditions.
These procedures should not be attempted by unqualified personnel.
After the proper system operation is established, the actual unit air delivery and the actual fan motor amperage draw for each
unit should be recorded in a convenient place for future reference such as the inspection, installation, & start-up check sheet, a
copy of which is provided on the back of this manual. Contact the sales representative or the factory for additional copies of
this sheet.
The manufacturer assumes no responsibility for undesirable system operation due to improper design, equipment or
component selection, and/or installation of ductwork, grilles, and other field supplied components.
Air Balancing Procedure
Before Air Balancing the terminal unit, the following general items should be verified.
1. The primary fan system is operating at the specified volume, static pressure, RPM and current.
2. Return filters (if supplied) are clean.
3. All balancing dampers are adjusted and locked. Dampers downstream of the terminal unit should be proportionally
balanced.
4. Thermostats are calibrated and operational.
5. All duct work and connections are free from leaks.
6. Sufficient duct static pressure is available at the terminal primary air inlet.
7. All diffusers are installed and adjusted for the proper air pattern.
NOTE: Since fan powered terminals are typically operating within a pressurized plenum, all flooring tiles must be replaced prior to
verifying outlet flows.
8. A fan powered terminal unit should never be operated if the downstream duct work has not been installed. A
minimum downstream static pressure resistance of 0.1 in. w.g. is recommended.
9. If field adjustment of the primary air valve should be necessary, follow the appropriate calibration procedures for
the controller type supplied with the unit. If DDC controls are supplied, refer to the control contractor’s
documentation for calibration instructions.
10. Set the thermostat to full cooling. The fan should be on and the primary air valve (if present) at maximum air flow.
Verify the air flow with the sensor tube or pitot tube traverse. Adjust if necessary.
11. The fan volume must be field adjusted with the fan speed controller. Fan curves (available at priceindustries.com)
indicate the volume range of each size unit. Adjust the speed control until the desired air flow is measured at the
outlet.
12. Set the thermostat to full heating. The fan should be on and the primary air valve (if present) at minimum flow.
Verify the primary air volume with sensor taps or pitot tube traverse. Adjust if necessary.
13. Always set the fan volume at full cooling.

Page: 5 of 9Global IFS Fan Powered Box
FAN POWERED BOX & TERMINAL UNIT
START UP & OPERATION
Electronically Commutated Motor (ECM) Information
Do not switch 120/208/240/277 VAC power to turn ECM motor on and off. Instead control the 24VAC signal or BAS
signal to turn the ECM motor on and off. The ECM motor has large capacitors that charge quickly on mains power up.
Switching on several motors frequently could reduce building power quality and is not recommended.
Standard ECM Speed Controller
The Global IFS standard speed controller allows manual adjustment of the fan flow using the adjustment dial on the
control board and a voltmeter. Remote control of the fan speed is also possible with the BAS input. The following chart
describes the controller response to a 0-10 VDC input.
Input Voltage Mode of Operation
0-1 VDC Manual Control
1-2 VDC Fan Off (1.5V Recommended)
2-10 VDC Remote Control 0 - 100%
Note: Refer to “Fan Curves” performance data documents for fan
curves. Pressure Independent Flow (PIF) Motor Program Voltage
Equations Box Con iguration:
Size 115V 208/240V 277V
10 CFM = (175.57 X VDC) - 159.00 CFM = (173.93 X VDC) - 153.79 CFM = (171.07 X VDC) - 145.50
20 CFM = (272.79 X VDC) - 228.79 CFM = (272.57 X VDC) - 224.57 CFM = (271.36 X VDC) - 220.21
30 CFM = (347.14 X VDC) - 305.86 CFM = (347.21 X VDC) - 306.21 CFM = (346.29 X VDC) - 300.14
40 CFM = (521.93 X VDC) - 447.93 CFM = (522.86 X VDC) - 445.71 CFM = (526.5 X VDC) - 471.07
50 CFM = (640.00 X VDC) - 378.86 CFM = (636.79 X VDC) - 373.50 CFM = (615.07 X VDC) - 331.93
60 CFM = (1018.14 X VDC) - 885.71 CFM = (1029.07 X VDC) - 893.50 CFM = (1015.93 X VDC) - 897.93
Terminal Configuration:
Size 115V 208/240V 277V
10 CFM = (155.50 X VDC) - 50.79 CFM = (152.86 X VDC) - 45.29 CFM = (178.57 X VDC) - 167.29
20 CFM = (249.79 X VDC) - 207.64 CFM = (253.36 X VDC) - 211.50 CFM = (246.36 X VDC) - 197.64
30 CFM = (298.00 X VDC) - 216.86 CFM = (297.29 X VDC) - 214.43 CFM = (314.79 X VDC) - 277.79
40 CFM = (478.36 X VDC) - 347.50 CFM = (474.71 X VDC) - 341.00 CFM = (475.86 X VDC) - 350.00

Page: 6 of 9
ECM Adjustment
1. Remove the electrical control cover and connect the leads from a DC
voltmeter to the terminals indicated.
2. Determine test point voltage from the formula based on the desired airflow.
3. Adjust the manual speed control dial on the outside of the box with a screwdriver until the test point voltage is achieved.
4. Wait a few seconds for the motor to adjust its speed and then verify fan flow with measurements at the supply outlets.
5. If necessary, fine tune the speed control in accordance with the measured outlet flow.
MANUAL SPEED
CONTROL DIAL
DC VOLTMETER
WIRING
HARNESS
24VAC
POWER
SUPPLY
SPEED CONTROL
NEUTRAL SIGNAL
24VAC COMMON
CONTROL ASSEMBLY LABEL ECM CABLE CONNECTION
ECM Deluxe Speed Controller Adjustment
The Global IFS Deluxe ECM speed controller works with a high
efficiency ECM motor. This low voltage (24 VAC) speed control
allows full manual (push button adjust) or BAS (2-10 VDC signal)
control of the ECM motor. The deluxe speed controller also has a
digital screen and BAS RPM feedback (2-10 VDC) which is
proportional to motor RPM.
NOTE: 24 VAC COM, BAS COM, ANALOG OUTPUT COM are all
connected together. Please observe 24 VAC polarity
NOTE: Local setpoints are stored to EEPROM and will remain set
after power failures.
Local control:
To change modes press both up and down buttons at the same time
until L.SET appears on display
Use up and down to adjust fan speed.
BAS control:
To change modes press both up and down buttons at the same time
until bAS.r appears on display
The BAS input voltage is a 2-10 VDC scale, and therefore VDC
calculated for a given CFM using the equation must
be doubled to achieve that CFM using the BAS input. See standard
speed controller BAS section for an example of calculating the
voltage required for a specific CFM. Example found in the BAS Input
Signal section below.
NOTE: For further troubleshooting information on ECM motors,
ECM Speed Controllers, and ECM Deluxe Speed Controllers, please
refer to the ECM motor manual.
ECM DELUXE SPEED CONTROLLER
POT Voltage Motor
0 -1 VDC Off
1 - 4.5 VDC 0-100% Control
4.5 - 5 VDC 100%
ECM SPEED CONTROLLER
Global IFS Fan Powered Box
FAN POWERED BOX & TERMINAL UNIT

Page: 7 of 9Global IFS Fan Powered Box
FAN POWERED BOX & TERMINAL UNIT
MAINTENANCE
Troubleshooting Guide
1. The terminal is louder than expected. What might be causing
this?
a. The first thing to look for is any foreign material in the fan or
terminal casing, like packing material or small parts shipped
with the unit. Ensure the power is off, and spin the fan wheel
to make sure it is balanced so it is not making contact with
the fan housing.
b. Once it’s confirmed that the fan and terminal casing are free
of foreign material and balanced, ensure the terminal is the
correct size. Check the label for the model and size, and
match that against the schedule to ensure the correct size
was selected and installed. A terminal that is too small for the
application will cause high air velocity and excessive noise.
c. If an electric coil is present, ensure there is sufficient
downstream static pressure of 0.2 inches water gauge to
prevent any chatter of the air proving switch.
2. The terminal is not providing the specified primary air
volume. How do I adjust the primary air volume?
a. First, the airflow may simply need to be balanced correctly to
ensure the primary airflow isn’t short circuiting into the
plenum. See page 6 for air balancing procedures.
b. Check the controller. Make sure it is set up according to the
wiring diagram. There should be a wiring diagram mounted
inside the door of the controls enclosure, or contact
airmovement@priceindustries. com for assistance.
c. Next, ensure the following items are operating correctly:
i. Cycle the thermostat to see if a signal is being sent to
the controller and the controller is reacting
appropriately.
ii. Check the operation of the damper actuator and the
linkage.
iii. Check the flow sensor and tubing for block
3. The fan air volume is too low. How do I adjust the fan air
volume?
a. Measure the downstream static pressure. It needs to be at
least 0.1 in wg (0.2 in wg for a Size 60 FDC or if an electric coil
is present). If the downstream static pressure is too low, the
blower motor will overheat, turn off, and restart after it
cools, and will continue in this cycle.
b. Once the downstream static pressure is confirmed, check the
supply voltage is the same as stated on the wiring diagram.
The supply voltage must be identical to the wiring diagram.
c. For ECM applications, the motor will be furnished with one
of two programs:
i. High Turndown flow program: This program will maintain
constant motor torque to vary the airflow with
fluctuations in static pressure.
ii. Pressure Independent program: This program
will maintain the desired airflow by varying the motor
torque to compensate for changes in static pressure.
Check the product label to confirm which program was
supplied with your motor, and determine if the program
matches the behavior of the fan with respect to duct
static pressure. If it is not operating as described for the
appropriate program, contact
airmovement@priceindustries for assistance.
ci. Next, check the filter for excessive dust build-up, and then
check the fan, any coils, and the inside of the terminal casing
for particle blockage, or loose insulation. If needed, changed
the filter and clear any blockages.
cii. Check the fan rotation to ensure it is spinning in the
direction marked on the blower casing. If the fan is not
energized for morning warm-up, for example, the warm
primary air may short-circuit through the return opening to
the plenum, inducing the fan to spin in the wrong direction.
When the fan is energized, it will continue to spin in the
wrong direction, which will sharply decrease fan flow.
ciii. Finally, inspect the ductwork for leaks or obstructions, sharp
elbows near the fan inlet, or improperly designed turning
vanes. Any of these items can decrease the fan’s efficiency.
4. The fan will not operate. How do I get it to start?
a. Check the wiring diagram provided with the terminal unit.
Make sure that all the wiring inside the electrical
enclosure matches the wiring diagram exactly.
b. If the fan is cycling on and off, it may be insufficient
downstream static pressure causing the motor to
overheat and cycle. Ensure the downstream static
pressure is a minimum of 0.1 in wg (0.2 in wg for a Size 60
FDC or if an electric heater is installed).
c. Cycle the thermostat to full heating and verify the signal
output from the thermostat to the controller.
d. Check the disconnect switch or breaker.
e. Ensure the fan wheel is not touching the blower casing.

Page: 8 of 9Global IFS Fan Powered Box
FAN POWERED BOX & TERMINAL UNIT
MAINTENANCE
Typical Wiring Diagram
NOTE: The ECM motor is turned ON/OFF by switching 24 VAC power to the ECM speed controller. It is not
recommended to switch the main (120/240/277 VAC) power on and off. This is because the ECM motor has large
capacitors that cause a current surge when turned on. This could cause a significant power spike if many units are
turned on at once.
For reference only. For actual wiring specific to the supplied units please refer to the wiring diagram supplied with
each unit.
=
=
=
i
OPONAL VIPMENT·
MERCURY CONTACTORS {MC)
□
□DOOR INTERLOCK
DISCONNECT STCH {IDSW)
CONTROL CKT. FUSE {CCF)
MAIN LINE FUSE {FUS)
□
□
□MOTOR FUSE {MFUS)
'
i
'i
I
i
i'
i'
RED
0 Cl
YL
-
I HOT I

Page: 9 of 9Global IFS Fan Powered Box
FAN POWERED BOX & TERMINAL UNIT
MAINTENANCE
Replacement Parts
Component Part# Description
ECM Fan Motors
019178-006 120V/240V - 1/3 HP (FDU Size 10, 20)
019179-006 277V - 1/3 HP (FDU Size 10, 20)
019178-007 120V/240V - 1/2 HP (FDU Size 30, 50)
019179-007 277V - 1/2 HP (FDU Size 30, 50)
019178-008 120V/240V - 3/4 HP (FDU Size 40)
019179-008 277V - 3/4 HP (FDU Size 40)
ECM Speed Controller 232952-100 Standard Fan Speed Controller (All Sizes)
232952-200
Deluxe Fan Speed Controller (All Sizes)
Blowers
100186-011 FDU Size 10, 20
100185-002 FDU Size 30, 50
100185-003 FDU Size 40
Actuators 019917-001 FDU Terminal & Box w/ ID (Sizes 10-40)
Thermostats Reference UMCB Underfloor Modulating Controller with BACnet Manual5 mfd
Transformers
019436-001 115V-24V, 50 VA Transformer
019436-011 208V/240V-24V, 50 VA Transformer
019439-001 277V-24V, 50 VA Transformer
Disconnect Switch 019903-001 115V/277V Single Pole
019903-003 240V Two Pole
Drain Pan Part# Reference (506274-XXX)
2 Pipe 1 or 2 Row 2 Pipe 3 or 4 Row 2 Pipe 5 or 6 Row
Galvanized Stainless Steel Galvanized Stainless Steel Galvanized Stainless Steel
001 101 002 102 003 103
4 Pipe 1/2 Cool - 1/2 Heat 4 Pipe 3/4 Cool - 1/2 Heat 4 Pipe 5/6 Cool - 1/2 Heat
Galvanized Stainless Steel Galvanized Stainless Steel Galvanized Stainless Steel
004 104 005 105 006 106
Discharge Attenuator Part# Reference (506271-XXX)
Unit Size Configuration XXX
10 STD BOX/EC 001
20 STD BOX/EC 002
30 STD BOX/EC 003
40 STD BOX/EC 004
50 STD BOX/EC/WC 005
10 BOX W/ CWC 101
10/20 BOX W/ HWC(10), CWC/HWC (20)
102
30 BOX W/ WC 103
40 BOX W/ WC 104
This manual suits for next models
1
Table of contents
Popular Fan manuals by other brands
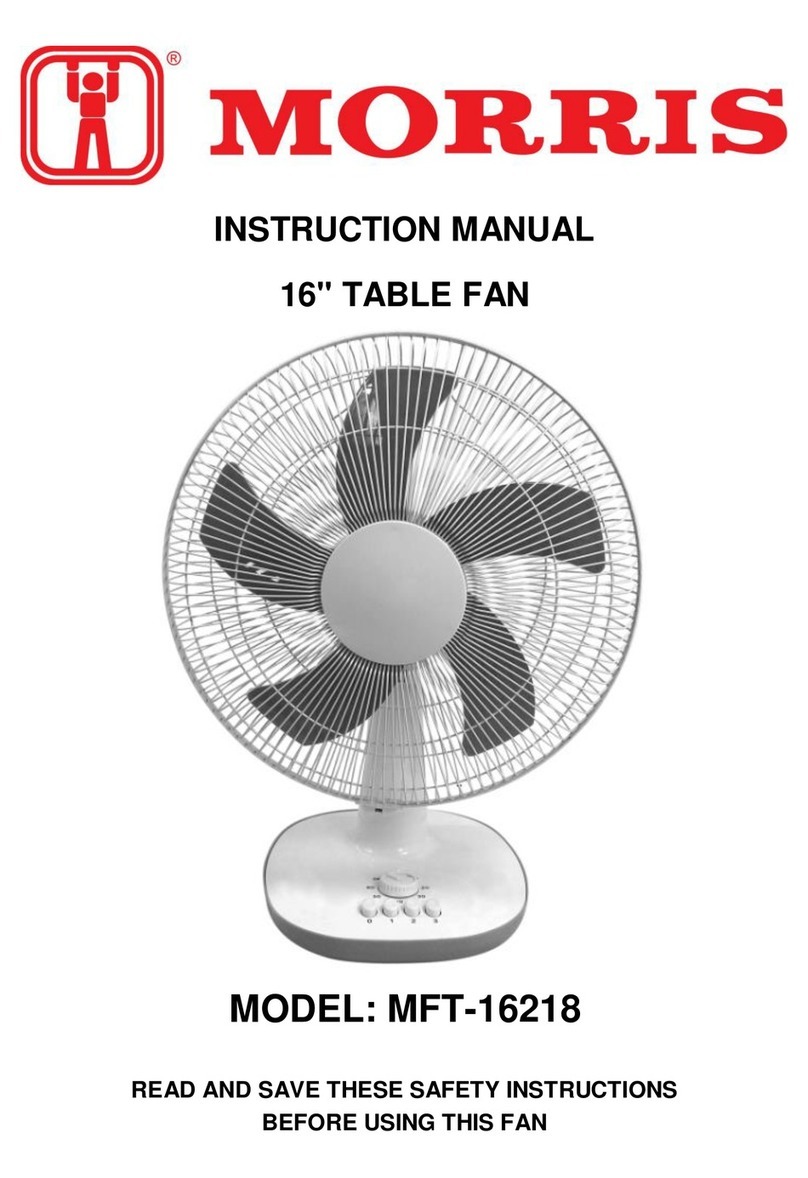
Morris
Morris MFT-16218 instruction manual

Vortice
Vortice GORDON EVO C 40 Instruction booklet
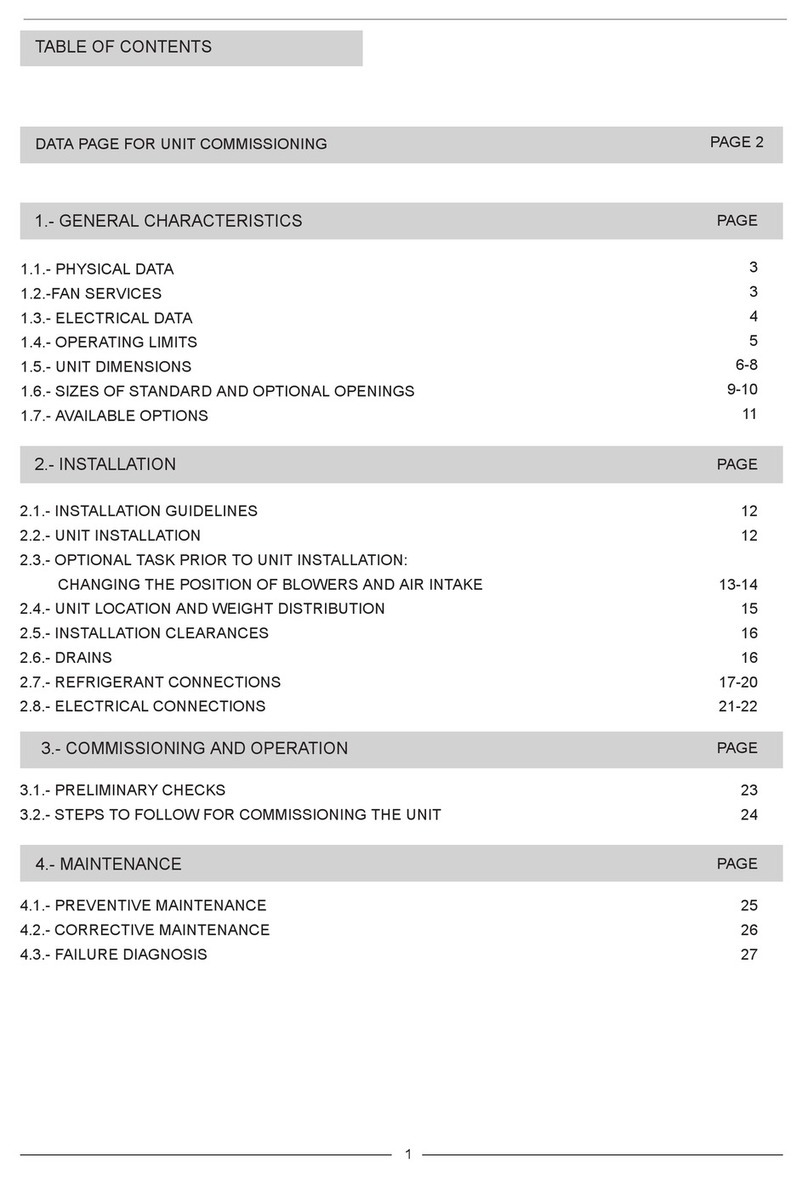
Lennox
Lennox FLATAIR KFC Series Installation and operating manual

NuAire
NuAire Sunwarm Air Installation and Maintenance Details

Vitek
Vitek VT-2073 Manual instruction

BALMUDA
BALMUDA GreenFan EGF-1400 Series instruction manual