Simu SIMUDRIVE SD510 User manual

EN 1/28
CONTROL BOX
SIMUDRIVE SD510
5136983C
EN - READ THIS NOTICE
CAREFULLY BEFORE USE
1.1 Caution – Important safety instructions
For reasons of personal safety, it is important to follow all the instructions, as incorrect installation can lead
to serious injury. The control box must be installed and adjusted by a professional motorization and building
automation installer, in compliance with the regulations of the country in which it is going to be used.
The installation and user manual must be given to the end user, explicitly stating that installation, adjustment
and maintenance of the motorization must be performed by a professional motorization and building
automation installer.
1.2 Introduction
This control box is designed to control three-phase SIMU motors (<1250W) roll-up or sectional doors in
commercial or industrial use.It is provided with 3 push buttons (open / close / stop).
A LED screen allows to check and detect any operating anomalies in the control unit or on the connected
devices. This product, installed according to these instructions, complies with EN 12453 et EN 12445.
These instructions are especially designed to ensure the safety of property and people.
1.3 Safety instructions relating to installation
WARNING! An incorrect installation or improper use of the product can cause damages to people,
animal or things.
• Scrap packing materials (plastic, cardboard, polystyrene etc.) according to the provisions set out by
current standards. Keep nylon or polystyrene bags out of children’s reach.
• Keep the instructions together with the technical brochure for future reference.
• This product was exclusively designed and manufactured for the use specied in the present documentation.
Any other use not specied in the documentation could damage the product and be dangerous.
• SIMU declines all responsibility for any consequences resulting from improper use of the product, or use
which is dierent from that expected and specied in the present documentation.
• Do not install the product in explosive atmosphere.
• The installation must comply with the provisions set out by the country in which it is going to be used.
• Disconnect the electrical power supply before carrying out any work on the installation. Also disconnect
any buer batteries, if tted.
• The actuating member of a biased-o switch is to be located within direct sight of the driven part but away
from moving parts. It is to be installed at a minimum height of 1,5 m and not accessible to the public.
• For door and gate motors tted with emergency opening/closing controls, switches must not be positioned
higher than 5 feet above ground level.
• If the drive is tted with a manual release, install its actuating member at a height less than 1,8 m.
• Fit an omnipolar or magneto-thermal switch on the main power supply, having a contact opening distance
equal to or greater than 3mm.
• Make sure that there is no crushing between the driven part and the surrounding xed parts due to the
opening movement of the driven part.
SAFETY INSTRUCTIONS
1
SIMU S.A.S. au capital de 5 000 000 € - Zone Industrielle Les Giranaux - 70100 ARC-LÈS-GRAY - FRANCE - RCS VESOUL B 425 650 090 - SIRET 425 650 090 00011 - n° T.V.A CEE FR 87 425 650 090

EN
2/28
• Check that a dierential switch with a 0.03 threshold is tted just before the power supply mains.
• Check that earthing is carried out correctly: connect all metal parts for closure (doors, etc.) and all system
components provided with an earth terminal.
• SIMU declines all responsibility with respect to the automation safety and correct operation when other
manufacturer’s components are used.
• Only use original parts for any maintenance or repair operation.
• Do not modify the automation components, unless explicitly authorized by SIMU.
• Instruct the product user about the control systems provided and the manual opening operation in case
of emergency.
• Do not allow people or children to stay in the automation operation area.
• Keep radio control or other control devices out of children’s reach, in order to avoid unintentional automation
activation.
• The user must avoid any attempt to carry out work or repair on the automation system, and always request
the assistance of qualied people.
• Anything which is not expressly provided for in the present instructions is not allowed.
1.4 Safety instructions relating to use and maintenance
WARNING: Important safety instructions. It is important for the safety of people to follow these instructions.
Save these instructions.
WARNING: The drive has to be disconnected from its power source during cleaning, maintenance and
when replacing parts.
• This system can be used by children aged from 8 years and above and people with reduced physical,
sensory or mental capabilities or lack of experience and knowledge if they have been given supervision or
instruction concerning use of the appliance in a safe way and understand the hazards involved. Children
must not play with the appliance. Cleaning and user maintenance should not be made by children without
supervision.
• Do not allow children to play with xed controls. Keep remote controls away from children.
• Frequently examine the installation for imbalance and signs of wear or damage to cables and springs. Do
not use if repair or adjustment is necessary.
• Watch the motorised installation while it is moving and keep people away until the motorised installation
is fully extended.
• For drives powered by a very low voltage removable power supply, only the power supply provided with
the drive must be used.
• For drives tted with a manual release, operating conditions are given in the drive instructions.
• All wiring has do be done with power o.
• PCB protective cover has to be placed before powering on.

EN 3/28
1.5 Risk prevention
Risk areas : measures to be taken to eliminate risks
Installation which cannot lift a person or a child Installation which could lift a person or a child
Areas to protect Areas to protect
• Risk of crushing between the ground and the lower
edge of the door during closing.
Solution :
• Obstacle detection using safety edge solution and
photocells.
Warning : in the case of not self-tested photocells,
they must be checked every 6 months.
• Risk of crushing between the ground and the lower
edge of the door during closing.
• Risk of jamming between the case and the door.
• Risk of jamming between guides and door.
Solution :
• Photocells ( connection on not self-tested input to
check every 6 months )
• Obstacle detection on the top with self-tested
photocells.
DESCRIPTION OF SIMUDRIVE SD510 CONTROL BOX
2
2.1 Reference
DESIGNATION REF.
SIMUDRIVE SD510 2008779
2.2 Technical datas
- Three-phase supply :
• 230V 3~ 50/60Hz
• 380-415V 3N~ 50/60Hz
- Maximum power : 1250W
-Accessories power :
24Vdc / 0.5A - 230Vac / 250mA
-Ambient working temperature:
+5°C +40°C
- Protection index: IP54
- Dimensions : 262 x 193 x 100 mm
- Weight : 3.2 kg

EN
4/28
2.3 Board layout
Protective cover : To be used for any handling with power on (settings).
SW1: 230-400: Supply voltage conguration.
and buttons: Navigator menu buttons.
F1: Slow blow fuse 0.8A high breaking capacity / Transformer primary winding protection (H.B.C: High breaking
Capacity / 1500A mini).
F2: Slow blow fuse 0.8A / 24 Vdc output protection .
AFF.1: Display shows the operating phase.
AFF.2: Display indicates errors if any, otherwise indicates door position.

EN 5/28
B1: Motor encoder output (not used) , End limit contact.
B2: 3 command input (CMD1, CMD2, AUX) , Stop.
B3: Safety edge inputs.
B4: Photocell inputs and 24Vdc 20% / 0.5A global outputs.
B5: Auxiliary outputs
Low power (dry contact). Switchable maximum current: 0.8A at 230Vac or 1.6A at 24Vdc.
2 auxiliary power outputs (dry contact). Maximum voltage and current for change-over switching: 400Vac / 1A
B6: Power supply
B7: Motor output
Led 1 & 2: not used
Led 3: O if opening limit control input switch is activated
Led 4: O if closing limit control input switch is activated
Led 5: O if partial limit switch control input is activated
Led 6: O if pre-closing limit switch control input is activated
Led 7: On if command 1 control input is activated
Led 8: On if command 2 control input is activated
Led 9: On if auxiliary control input is activated
Led 10: O if stop or emergency stop control input is activated
Led 11: O if photocell 1 control input is activated
Led 12: O if photocell 2 control input is activated
2.4 Description of external programming interface
Red light, error indicator or maintenance.
Blinks to indicate an error (see chapter 4, page 26).
Stay on to indicate the necessity of a maintenance.
To open the door.
To stop the door.
To close the door.
2.5 Compatibility and standard installation diagram
The SD510 control box has been designed to control the SIMU T9 and SIMUBOX three-phase motors as well as to be
used exclusively with the following SIMU accessories: OSE safety edge, cell barrier, reex sensor, signalling light, SA Hz
standard receiver + TSA + remote control, universal key box, unstable key box, inverters.

EN
6/28
Power o, unscrew the protective cover to access to the PCB.
3.1 Control box supply
•Set up power supply with the switch SW1.
•Connect power supply.
All wiring has to be done with power o.
POWER SUPPLY CONFIGURATION
3~230V
SW1
POWER SUPPLY CONNECTION
3 ~ 230V
B6
39 40 41 42
L1 L2 L3
POWER SUPPLY CONFIGURATION
3 ~ 400V
SW1
POWER SUPPLY CONNECTION
3 ~ 400V + N
B6
39 40 41 42
L1 L2 L3N
3.2 Motor and safety brake wiring
•Three-phases T9
MOTOR AND CONTROL BOX CONNECTION
3
1
2
3
4
5
6
7
8
9
10
11
12
B1
B7
U V W
1234
Moteur
Antichute
5
6
8
7
U
V
W
moteur triphasé
bleu
U
moteur triphasé
gris
V
moteur triphasé
rouge
W
terre
jaune/vert
fin de course 1
violet
fin de course 1
violet
2
1
fin de course 2
noir
3
fin de course 2
noir
4
sonde thermique
beige
5
manœuvre de dépannage
bleu
6
manœuvre de dépannage
marron
7
sonde thermique
gris
8
ENCODER
MOTOR
SAFETY CHAIN
OPEN
LS
PARTIAL
LS
PRE
CLOSING
LS
CLOSE
LS
A
B
+
_
* Connecter ici le fil 8
en cas de moteur
sans manœuvre de dépannage
*
B7
B1

EN 7/28
•SIMUBOX three-phase
•Connect motor to control box.
•Connection has to be done in a connection box in order not to apply tensile on the cable.
•For a three-phase motor, connect safety brake (compulsory device) in series with motor safety chain and emergency
stop (terminals 5 and 6) and connect end limits (terminals 7/8/9).
• Refer to the motor instruction manual for end limits wiring : wires 1/2 from the motor can correspond to opening or
closing end limits depending on motor installation (same as wires 3/4).
• Connect an external stop button. Otherwise, use a shunt between 18 and 19. Motor won’t work if STOP is not
connected.
1
2
3
4
5
6
7
8
9
10
11
12
B1
B7
U V W
1234
Antichute
5
8
U
V
W
moteur triphasé
bleu
U
moteur triphasé
gris
V
moteur triphasé
rouge
W
terre
jaune/vert
fin de course 1
violet
fin de course 1
violet
2
1
fin de course 2
noir
3
fin de course 2
noir
4
sonde thermique
beige
5
sonde thermique
gris
8
ENCODER
MOTOR
SAFETY CHAIN
OPEN
LS
PARTIAL
LS
PRE
CLOSING
LS
CLOSE
LS
A
B
+
_
U V W Fdc
S1
Fdc
S1
Fdc
S2
Fdc
S2
Secu
Mot
Secu
Mot
U V W Fdc
S1
Fdc
S1
Fdc
S2
Fdc
S2
Secu
Mot
Secu
Mot
B1

EN
8/28
3.3 Checking motor rotation
Replace the PCB protective cover before powering on.
Press and hold the key « up »
to open the door.
Press and hold the key « down »
to close the door.
If the operation is reversed, power o the product and reverse the motor’s power supply.
3.4 End limit settings
The control box is now in dead man mode. Set up end limits with up and down buttons.
Check end limit leds lighting.
KEY SWITCH CONNECTION
4
Check the rotation direction. If the axis rotates in the opposite direction to the desired one:
• Stop the movement immediately.
• Turn o power.
• Reverse 13 and 15 on terminal block B2.
• Switch on the system again and repeat the rotation direction check operation.
Description Reference
UNIVERSAL KEY SWITCH 9012888
All wirings have to be done with power off.

EN 9/28
SAFETY ACCESSORIES WIRING
5
Connections
B3 OPTICAL SAFETY EDGE
22 BROWN
23 GREEN
24 WHITE
5.1 Optical safety edge wiring
SIMU advices about safety.
KIND OF DOOR
OPERATIN
MODE
SHUTTER WHICH CANNOT
LIFT A PERSON
SHUTTER WHICH CAN
LIFT A PERSON
MAINTAINED PRESSURE No accessories required. No accessories required.
MIXED No accessories required. 2 sets of self-tested photocells in up position.
IMPULSE/AUTOMATIC
• safety edge.
• 2 sets of photocells in down
position.
• flashing light if there is an
access to the road.
• safety edge.
• 2 sets of photocells in down position.
• 2 sets of self-tested photocells in up position.
• flashing light if there is an access to the road.
5.2 Photocell wiring
5.2.1 In the case of a shutter which cannot lift a person
2 sets of not self-tested photocells in down position.
When photocells are not self-tested, they must be checked every 6 months.
Connections
B4:25 RX1:3
B4:26 RX1:5
B4:27 RX2:3
B4:28 RX2:5
B4:29 TX1:1
B4:29 RX1:1
B4:30 TX1:2
B4:30 RX1:2
B4:31 RX2:1
B4:31 TX2:1
B4:32 TX2:2
B4:32 RX2:2
BLUE
BLUE
DARK
BLUE
BROWN
BROWN
GREEN
GREEN
DARK
BLUE
DARK
BLUE
DARK
BLUE
GREEN
GREEN
OUTPUT
OUTPUT
Description Reference
Cell Master Pro Bitech 5115929

EN
10/28
5.2.1 In the case of a shutter which can lift a person
2 sets of not self-tested photocells in down position.
When photocells are not self-tested, they must be checked every 6 months.
2 sets of self-tested photocells in up position.
Connections
B3:20 RX1:3
B3:21 RX2:5
B4:29 TX1:1
B4:29 RX1:1
B4:30 TX1:2
B4:30 RX1:2
B4:31 TX2:1
B4:31 RX2:1
B4:32 TX2:2
B4:32 RX2:2
B4:30 TX1:2
B4:30 RX1:2
B4:31 RX2:1
B4:32 TX2:2
B4:32 RX2:2
RX1:5 RX2:3
BLUE
DARK
BLUE
BROWN
GREEN
GREEN
DARK
BLUE
DARK
BLUE
DARK
BLUE
BLACK
GREEN
GREEN
OUTPUT
OUTPUT
Description Reference
Cell Master Pro Bitech 5115929
Connections
B5:34 B4:29
B5:34 B4:31
B5:33 TX1:1
B5:33 TX2:1
B4:25 RX1:3
B4:26 RX1:5
B4:27 RX2:3
B4:28 RX2:5
B4:29 RX1:2
B4:30 TX1:2
B4:30 RX1:1
B4:31 RX2:2
B4:32 TX2:2
B4:32 RX2:1
BLUE
BLUE BLUE
BROWN
BROWN
BLACK
GREEN
GREEN
RED
BLACK
GREEN
GREEN
GREEN
Description Reference
Cell Master Pro Bitech 5115929

EN 11/28
FIRST POWER UP
6
Eclairage de zone
Charge max 200W
(2x100W)
5.3 Flashing light wiring
Description Reference
Orange ashing light 9019453
Wiring in 24 Vdc
Connections
B4 : 32 B5 : 37
B5 : 38 J2:1
B4 : 31 J2:2
Congure the High power output 2 :
Flashing output J2 = 04
5.4 Lighting wiring
Congure the high power output 1 :
• Flashing output, J1 = 04
• J4=02 (expert mode needed : see
chapter 4 p.18)
If a ashing light is also connected
place its switch on « FLASH »
200W maximum
(2x100W)
When all wirings are done, replace the protective cover before powering on.
6.1 Display
The 2 digits on the left
display the current phase :
The 2 digits on the right display :
-The default if there is one
-The door position in other case
OPERATING PHASE DISPLAY
Waiting for a command AC
Total internal opening
(complete opening phase with priority to inside panel) OU
Total external opening
(complete opening phase with priority to outside panel) OE
Closing (Closing phase in progress) FE
Waiting to close
(Door open, on standby for closing) AF
Reopening after safety close detection LO
Reclosing after safety open detection LF
DOOR POSITION DISPLAY
Door is opened
Door is neither opened or closed
Door is closed

EN
12/28
6.2 First power up procedure
Motor rotation direction has to be checked and the end limits have to be set.
If ATEE error code appears, check end limit wiring (7-8-9), motor safety chain wiring (5-6), stop wiring (18/19) as well
as front face button wiring (CM1).
Move the door in main-
tained pressure mode until
the downward end limit.
Open the door with 1 impulse the door goes to
the upward end limit.
Note that pushing on any button will stop the door.
Close the door with 1 impulse the door goes to
the downward end limit.
Note that pushing on any button will stop the door.
Safety edge configuration
01 : Resistive 8.2kohms
02 : Optical
03: Pneumatic
For mixed mode,
validate directly.

EN 13/28
6.3 Button and display operation
Changes have to be done when the curtain is closed.
Example to modify d1 parameter in « 03 »

EN
14/28
6.4 End limit self learning
Use self-learning if you want to change closed and opened position or learn new operation time. Before starting self-
learning process, the installation has to be nished (door installed).
Current phase
and error display
The door opens
until the upward end limit.
The door closes
until the downward end limit.

EN 15/28
Below tables show pre-programmed parameters. To modify them, refer to 6.3 paragraph (page 13). To make a more
advanced programming, refer to Expert parameters (page 18).
7.1 Generic parameters
d0 GENERIC PARAMETERS
Parameters Value Impulse 2BP Mixed Automatic
d1 Operating mode
00 Deadman
01 Mixed (automatic open / deadman close) X
02 Impulse open and close X X
d2 AUX Command
conguration
00 Step by step command X
01 Partial / complete opening selection for CMD1
02 Partial open command X
03 Trac management external command
04 Input photocell blanking X
05 Automatic interlocking input
d3 Closing on
photocell activation
On Closing after photocell activation X
OF No closing after photocell activation X X
d4 Closing on timer
end
On Closing after end of the timer
OF No closing after end of the timer X X X
d5 With or without
clock system
On With clock system
OF Without clock system X X X
d6 Number of closing
attempts
00 to
50 Closing attempts 03 00 03
d1 : Operating mode is preprogrammed during 1st power up procedure. It can be changed in deadman, mixed or
impulse. This mode is allowed only with necessary security devices.
d2 : Step by step command allows to control the shutter from a SIMU remote control (installation of the SAHz
receiver below).
Connection of SIMU radio receiver:
OUTPUT
24 VDC
Description Reference
SA Hz standard receiver 2006380
Connections
B2:16 Receiver : 3
B2:17 Receiver : 4
B4:29 Receiver : 1
B4:30 Receiver : 2
SETTINGS IN LEVEL 1
7

EN
16/28
d3 : Possibility to program closing on cell-activation. This mode is only allowed with necessary security devices.
d4 : Shutter can close automatically after a dwell-time. This mode is only allowed with necessary security devices. In
this case, check tA in t0 menu:
t0 TIMER PARAMETERS
Parameters Value Impulse 2BP Mixed Automatic
tF Opening / closing timer 00 00 second to 4.0 minutes 1.0 1.0 30
tA Re-closing timer 01 00 second to 4H00 10 10 05
tU Warning timer before starting 02 00 second to10 seconds 03 03 03
SETTING TIME ta PROCEDURE
Between 0 sec and 1 min press the button or
to increase or decrease the timer by 1s.
Between 1 min and 10 min press the button or
to increase or decrease the timer by 5s.
Between 10 min and 1 hour press the button or
to increase or decrease the timer by 10 s.
Between 1hour and 4 hour press the button or
to increase or decrease the timer by 10 min.

EN 17/28
7.2 Input parameters
In the mixed mode, safety devices are not compulsory. As a result, input parameters can only be changed in expert
mode (chapter 4).
E0 INPUT PARAMETERS
Parameters Value Impulse 2BP Mixed Automatic
E1 Photocell 1 input EXPERT MODE to modify
Safety input
on CLOSING
without self-test
with complete
reopening
Inactive
Safety input
on CLOSING
without self-test
with complete
reopening
E2 Photocell 2 input EXPERT MODE to modify
Safety input
on CLOSING
without self-test
with complete
reopening
Inactive
Safety input
on CLOSING
without self-test
with complete
reopening
E3 8.2k safety edge
input conguration
00 Inactive
Programmed during 1st installation procedure
01 8.2k safety edge only
02 Air pressure safety edge without 8.2k
03 Air pressure safety edge with 8.2k
04 Pass-door function
E4 8.2k safety edge
function
01 Safety input on CLOSING with COMPLETE re-
opening X X X
02 Safety input on CLOSING with 2 SECONDS re-
opening
E5 OSE safety edge
function
00 Inactive
Programmed during 1st installation procedure
01 Safety input on CLOSING with COMPLETE re-
opening
02 Safety input on CLOSING with 2 SECONDS re-
opening
E6 End limit type
00 Mechanical end limit
Programmed during 1st installation procedure
01 Electronic end limit
02 No end limit
EF
Radio channel
reaction during
opening
EXPERT MODE to modify Reverse
EH Function not used
EJ Function not used
In the case of a shutter which can lift a person, the 5 safety accessories have to set like this :
•
Bottom photocells are connected on safety edge input : program E3 on 02 (air pressure safety edge without 8.2k).
•
Top photocells are self-tested : program E1 and E2 on 04 (cf Chapter 4 to go in expert mode)
.

EN
18/28
7.3 Output parameters
J0 OUTPUT PARAMETERS
Parameters Value Impulse 2BP Mixed Automatic
J1 High power output 1
function
00 Electric strike door release
01 Electromagnetic door lock
02 Brake contact NO X X X
03 Brake contact NC
04 Flashing output
05 Door closed indication
J2 High power output 2
function
00 Electric strike door release X
01 Electromagnetic door lock
02 Brake contact NO
03 Brake contact NC
04 Flashing output X X
05 Door closed indication
J3 Function not used
J5 Warning before starting
00 No warning before starting
01 Warning before start closing only X
02 Warning before start opening and closing X X
J6 Low power output 1
function
00 Alarm
01 Timer
02 Door position X
03 Self-test output NC
04 Self-test output NO
05 Automatic interlocking output
06 Buzzer output
07 Service point output
08 Service point output + deadman operating
09 Opened door indication X X
10 Closed door indication
11 Function not used
12 Function not used
JE Red trac lights ashing
conguration EXPERT MODE to modify Red lights are ashing on the two way
JF Red light waiting
command conguration EXPERT MODE to modify Red lights are o during waiting command
phase
J2 : in impulse mode, change it in 04 to make the signaling light working.
8.1 Expert level activation
EXPERT LEVEL PARAMETERS
8

EN 19/28
8.2 Expert parameters
d0 GENERIC PARAMETERS
Parameters Value Impulse 2BP Mixed Automatic
d1 Operating mode
00 Deadman
01 Mixed (automatic open / deadman close) X
02 Impulse open and close X X
d2 AUX Command
conguration
00 Step by step command X
01 Partial / complete opening selection for CMD1
02 Partial open command X
03 Trac management external command
04 Input photocell blanking X
05 Automatic interlocking input
d3 Closing on photocell
activation
On Closing after photocell activation X
OF No closing after photocell activation X X
d4 Closing on timer end
On Closing after end of the timer
OF No closing after end of the timer X X X
d5 With or without clock
system
On With clock system
OF Without clock system X X X
d6 Number of closing
attempts 00 to 50 Closing attempts 03 00 03

EN
20/28
E0 INPUT PARAMETERS
Parameters Value Impulse 2BP Mixed Automatic
E1 Photocell 1
input
00 Inactive X
01 OPEN safety input without self-test with COMPLETE re-closing
02 OPEN safety input without self-test with 2 SECONDS re-closing
03 OPEN safety input with self-test with COMPLETE re-closing
04 OPEN safety input with self-test with 2 SECONDS re-closing
05 CLOSE safety input without self-test with COMPLETE re-opening X X
06 CLOSE safety input without self-test with 2 SECONDS re-opening
07 CLOSE safety input with self-test with COMPLETE re-opening
08 CLOSE safety input with self-test with 2 SECONDS re-opening
E2 Photocell 2
input
00 Inactive X
01 OPEN safety input without self-test with COMPLETE re-closing
02 OPEN safety input without self-test with 2 SECONDS re-closing
03 OPEN safety input with self-test with COMPLETE re-closing
04 OPEN safety input with self-test with 2 SECONDS re-closing
05 CLOSE safety input without self-test with COMPLETE re-opening X X
06 CLOSE safety input without self-test with 2 SECONDS re-opening
07 CLOSE safety input with self-test with COMPLETE re-opening
08 CLOSE safety input with self-test with 2 SECONDS re-opening
E3
8.2k safety
edge
conguration
00 Inactive
Programmed during 1st installation
procedure
01 8.2k safety edge only
02 Air pressure safety edge without 8.2k
03 Air pressure safety edge with 8.2k
04 Pass-door function
E4 8.2k safety
edge function
01 Safety input on CLOSING , with COMPLETE re-opening without self-test X X X
02 Safety input on CLOSING with 2 SECONDS re-opening without self-test
03 Safety input : OPENING→ STOP, CLOSING → COMPLETE re-opening
04 Safety input : OPENING→ STOP, CLOSING → 2 SECONDS re-opening
05 CLOSE safety input with COMPLETE re-opening and BLANKING
06 CLOSE safety input with 2 SECONDS re-opening and BLANKING
E5 OSE safety
edge function
00 Inactive
Programmed during 1st installation
procedure
01 Safety input on CLOSING, with COMPLETE re-opening without self-test
02 Safety input on CLOSING with 2 SECONDS re-opening without self-test
03 Safety input : OPENING→ STOP, CLOSING → COMPLETE re-opening
04 Safety input : OPENING→ STOP, CLOSING → 2 SECONDS re-opening
05 CLOSE safety input with COMPLETE re-opening and BLANKING
06 CLOSE safety input with 2 SECONDS re-opening and BLANKING
E6 End limit type
00 Mechanical end limit
Programmed during 1st installation
procedure
01 Electronical end limit
02 No end limit
E7 Function not used
E8 Function not used
E9 Function not used
EA Function not used
EC Function not used
ED Function not used
EE Function not used
EF
Radio
channel
reaction
during
opening
00 Stop
01 Inversion X X X
EH Function not used
EJ Function not used
Table of contents
Other Simu Control System manuals
Popular Control System manuals by other brands
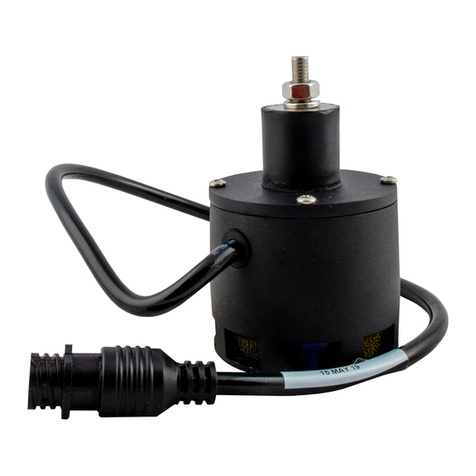
Norac
Norac UC4 Total Control Operator's manual
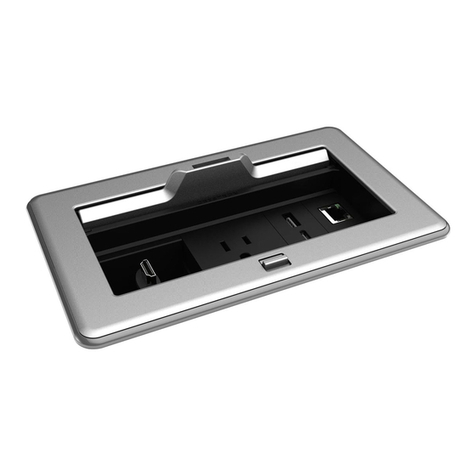
Crestron
Crestron FlipTop FT2-202-ELEC Series manual
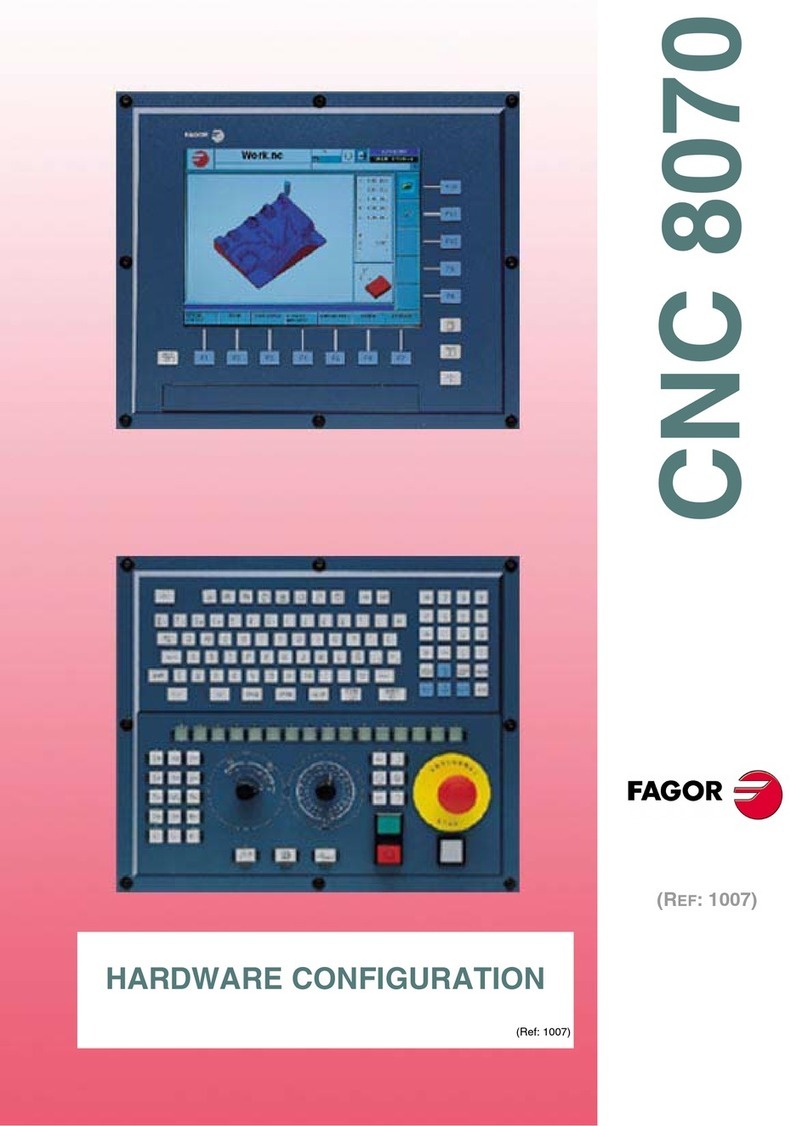
Fagor
Fagor CNC 8070 Hardware configuration
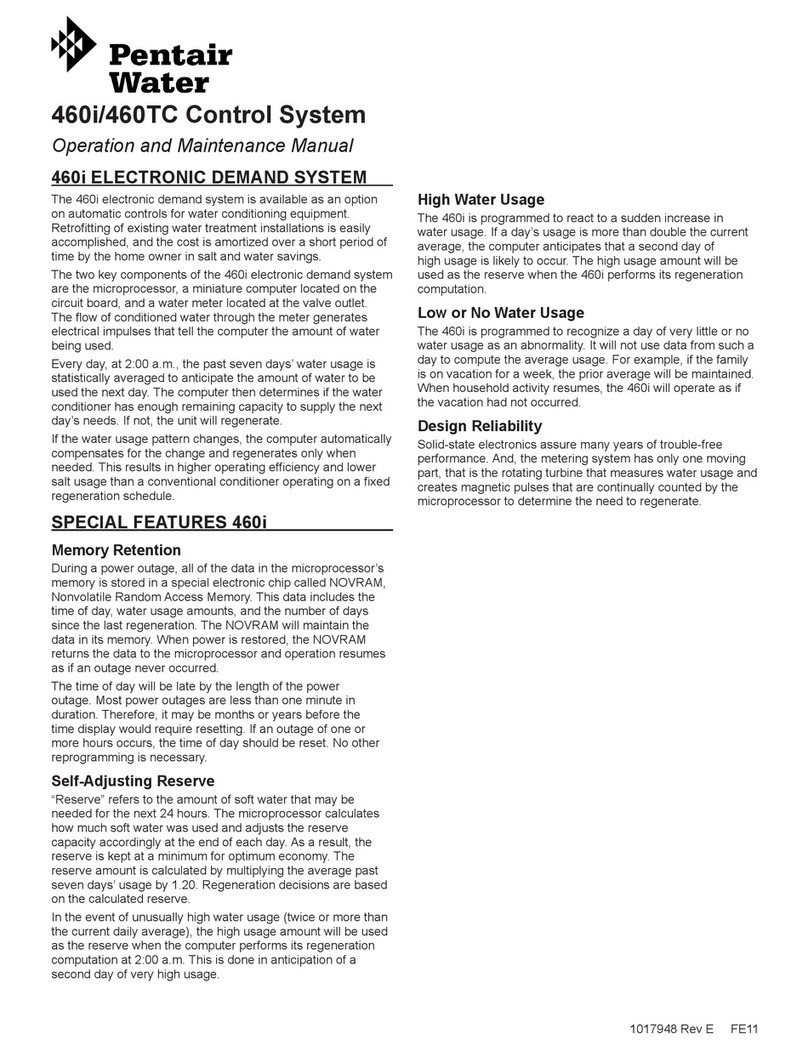
Pentair Pool Products
Pentair Pool Products 460TC Operation and maintenance manual
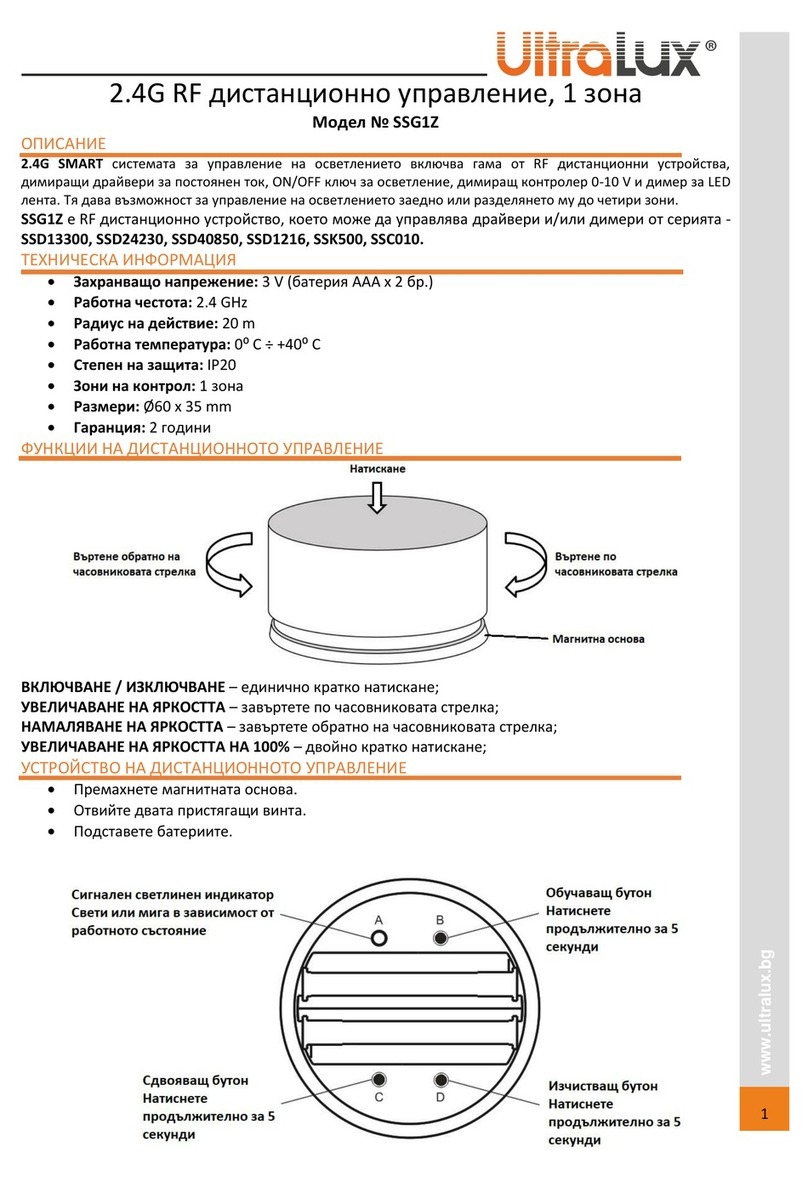
UltraLux
UltraLux SSG1Z instruction manual

Monacor
Monacor security DA-8000 installation instructions