Festo CMCA-...-B Series User manual

Description
Electrical
Installation
8036667
1405NH
[8036661]
Control system
CMCA-...-B...

CMCA-...-B...
2 Festo – GDCP-CMCA-B-INST-EN – 1405NH – English
Translation of the original instructions
GDCP-CMCA-B-INST-EN
Codesys
®
is a registered trademark of its respective trademark holder in certain countries.
Identification of hazards and instructions on how to prevent them:
Warning
Hazards that can cause death or serious injuries.
Caution
Hazards that can cause minor injuries or serious material damage.
Other symbols:
Note
Material damage or loss of function.
Recommendations, tips, references to other documentation.
Essential or useful accessories.
Information on environmentally sound usage.
Text designations:
• Activities that may be carried out in any order.
1. Activities that should be carried out in the order stated.
– General lists.

CMCA-...-B...
Festo – GDCP-CMCA-B-INST-EN – 1405NH – English 3
Table of Contents – CMCA-...-B...
1 Safety and requirements for product use 5......................................
1.1 Safety 5..................................................................
1.1.1 General safety information 5..........................................
1.1.2 Intended use 5.....................................................
1.1.3 Foreseeable misuse 6...............................................
1.2 Requirements for product use 6...............................................
1.2.1 Qualification of specialized personnel 6.................................
1.2.2 Range of application and certifications 6................................
2 Transport and storage 7.....................................................
2.1 Transport 7................................................................
2.1.1 Dimensions and weights 7...........................................
2.2 Storage conditions 8........................................................
2.3 Unpacking 8...............................................................
2.3.1 Mounting plate 9...................................................
2.3.2 Control cabinet 10...................................................
2.4 Check the scope of delivery 13.................................................
3Overview 14................................................................
3.1 Function and application 14....................................................
3.2 Design 14..................................................................
3.2.1 External control elements and connections 14.............................
3.2.2 Internal components and connections 16.................................
3.2.3 Terminal strips 17...................................................
3.2.4 Circuit breakers 18..................................................
4 Mounting and installation 19..................................................
4.1 Mounting 19................................................................
4.1.1 Mounting plate 19...................................................
4.1.2 Control cabinet without base 20........................................
4.1.3 Control cabinet with base 21..........................................

CMCA-...-B...
4 Festo – GDCP-CMCA-B-INST-EN – 1405NH – English
4.2 Electrical installation 22.......................................................
4.2.1 Safety instructions 22................................................
4.2.2 Design of the double-stack terminals 24.................................
4.2.3 Supply voltage 25...................................................
4.2.4 Power switch (mounting plate design) 25................................
4.2.5 Emergency stop switch (mounting plate design) 26.........................
4.2.6 External emergency stop circuits 27.....................................
4.2.7 Protective door switch 27.............................................
4.2.8 Control and signal elements 28.........................................
4.2.9 Mode selector 30....................................................
4.2.10 Kinematic drives 31..................................................
4.2.11 Connect limit switches 31.............................................
4.2.12 Rod loss detection (only for parallel kinematic system EXPT) 32...............
4.2.13 Axis of rotation reference sensor 32.....................................
4.2.14 Camera system 32...................................................
4.2.15 Lighting 32.........................................................
4.2.16 Freely usable outputs 33..............................................
4.2.17 Additional peripheral modules for the multi-axis controller 34................
5 Commissioning 35...........................................................
5.1 Checks before commissioning 35.......................................
6 Operation and diagnostics 36..................................................
6.1 Operation 36...............................................................
6.2 Maintenance and care 36......................................................
6.2.1 Control cabinet fan 36................................................
7 Module replacement and repair 37.............................................
7.1 Module replacement 37.......................................................
7.2 Repair 37..................................................................
7.3 Disposal 37................................................................
A Technical appendix 38........................................................
A.1 Technical data 38............................................................
A.1.1 Safety engineering 38................................................
A.1.2 General 38.........................................................
A.1.3 Electrical data 39....................................................
A.1.4 Operating and environmental conditions 39...............................

1 Safety and requirements for product use
Festo – GDCP-CMCA-B-INST-EN – 1405NH – English 5
1 Safety and requirements for product use
1.1 Safety
1.1.1 General safety information
Warning
Danger of electric shock even if power switch is shut off.
The control system is only completely voltage-free if all supply lines have been switched
voltage-free.
• Switch off all supply lines (also external voltage) prior to assembly, installation and/
or maintenance work and secure them from being restarted accidentally.
• Switch the voltages back on only after completion of work.
Note
Damage to the product from incorrect handling.
• Never pull or plug in the plug connectors and interfaces when powered.
• Observe the handling specifications for electrostatically sensitive devices.
1.1.2 Intended use
The control system CMCA-...-B... is intended to operate a kinematics system in the environment of a
machine or automated system.
• Use system only as follows:
– in perfect technical condition
– in original status, without unauthorised modifications
– within the limits of the product defined through the technical data (A.1 Technical data)
– in an industrial environment
The safety circuit of the control solution CMCA-...-B... is only one part of the safety concept for a ma-
chine, whereby the safety concept must be based on a risk assessment of the entire machine to be
performed by the machine manufacturer.
Note
In the event of damage caused by unauthorised manipulation or other than intended
use, the guarantee is invalidated and the manufacturer is not liable for damages.

1 Safety and requirements for product use
6 Festo – GDCP-CMCA-B-INST-EN – 1405NH – English
1.1.3 Foreseeable misuse
– The safety circuit of the control system CMCA-...-B... is changed in its function.
– With the control system CMCA-...-B..., safety functions are implemented that are not described in
this documentation.
– A sufficient risk assessment has not been performed for the machine.
– There is no safety concept for the machine available.
– The safety circuit is not appropriate for the application.
– No verification and no validation of the switch in the machine have been performed.
1.2 Requirements for product use
• Provide this documentation to the following persons:
– design engineer
– assembler
– commissioner of the machine or system
• Comply with the specifications of the documentation. Follow all accompanying documentation and
the documentation of any associated accessories.
• Take the following into consideration for the destination:
– applicable legal regulations
– regulations and standards
– regulations of the testing organizations and insurers
– national specifications
For correct and safe use:
• Observe all warnings and notes.
• Comply with all load limits of the product and the connected components (A.1 Technical data).
1.2.1 Qualification of specialized personnel
• The product should only be installed by specialized personnel with corresponding qualifications.
The following knowledge is required:
– installation and operation of electrical control systems
– applicable regulations for operating safety-engineering systems
– applicable regulations for accident protection and operational reliability
– documentation and mode of operation of the product
1.2.2 Range of application and certifications
Standards and test values that the product complies with and fulfills (A.1 Technical data).
Certificates and declaration of conformity (www.festo.com/sp).

2Transportandstorage
Festo – GDCP-CMCA-B-INST-EN – 1405NH – English 7
2 Transport and storage
2.1 Transport
The control system is delivered on a pallet and is protected with a cover made of plates. The mounting
plate design is also screwed to the pallet.
2.1.1 Dimensions and weights
CMCA-…-B... C- CC- CS-
Dimensions [mm]
H565 868 1018
L1010 1140 1140
B640 510 510
Maximum weight
1)
[kg]
Control system 43 81 91
Overall weight 87 127 144
1) Dependent on the design and accessories
Tab. 2 .1
Note
• For transport, observe the marking on the upper side on the transport box.
1. Transport the pallet with the control system to the mounting/storage location.
2. Set the pallet down on a fixed and flat base at the mounting/storage location.

2 Transport and storage
8 Festo – GDCP-CMCA-B-INST-EN – 1405NH – English
2.2 Storage conditions
• For safe later use, the following storage conditions must be complied with.
Storage conditions
Storage temperature [°C] –20 … +60
Relative air humidity [%] 10 … 95 (non-condensing)
Max. storage time 60 months
Requirements of storage location dry, solid and flat base
Tab. 2 .2
2.3 Unpacking
Note
Damage to the product from incorrect dismounting of the transport packaging.
• Use the correct tool to loosen the screws.
• Do not let packaging parts fall onto the control system.
• Observe product weight.(2.1.1 Dimensions and weights).
• Keep the packaging for later use or dispose of it in accordance with the notes
(7.3 Disposal).

2Transportandstorage
Festo – GDCP-CMCA-B-INST-EN – 1405NH – English 9
2.3.1 Mounting plate
Remove transport packaging
1. Loosen and remove the lower cover screws.
2. Pull cover off upwards.
Fig. 2.1
Remove the packaging foil
3. Cut the plastic sheet parallel to the contour of
the product with an appropriate tool. When
cutting, make sure that you do not damage or
scratch the components of the control system.
4. Pull the plastic sheet upward and away. Care-
fully remove the bag with drying agent and dis-
pose of it in accordance with the instructions
(7.3 Disposal).
Fig. 2.2
Loosen mounting plate
5. Loosen and remove the screws with which the
mounting plate is screwed to the pallet.
6. With two people, lift the control system off the
pallet and bring it to the installation site.
Fig. 2.3

2 Transport and storage
10 Festo – GDCP-CMCA-B-INST-EN – 1405NH – English
2.3.2 Control cabinet
Warning
Danger of injury/damage due to falling loads.
The device to lift the control cabinet out of the transport packaging must be sufficiently
dimensioned.
• Observe product weight (2.1.1 Dimensions and weights).
Remove transport packaging
1. Loosen and remove all screws from the cover.
2. Remove transport packaging covers upward.
Fig. 2.4
3. Loosen and remove all screws of the side wall
near the control cabinet doors.
4. Pull the side wall forward and off.
Fig. 2.5

2Transportandstorage
Festo – GDCP-CMCA-B-INST-EN – 1405NH – English 11
5. Mount an appropriate lifting device to the
transport lugs of the control cabinet.
Fig. 2.6
6. Lift the control cabinet out of the transport
packaging.
Fig. 2.7

2 Transport and storage
12 Festo – GDCP-CMCA-B-INST-EN – 1405NH – English
Unpack filter mats
Caution
Fire risk from overheating.
At delivery, the filter mats for control cabinet fans and outlet filters are packed in plastic
and placed in the filter cassettes.
Operation of the control system with packaged filter mats results in overheating and
related consequential damage.
• Remove the plastic packaging from both filter mats as described subsequently.
1. Pull the covers of the filter housing off to the
front.
2. Take out the packaged filter mats.
3. Remove the packaging.
Fig. 2.8
4. Place the unpackaged filter mats in the filter
housing.
5. Install covers again.
Fig. 2.9
Remove drying agent
The control cabinet includes several bags with drying agent to protect against damage
due to moisture.
Before installation of the control system:
• Carefully remove the drying agent from the control cabinet and dispose of it in
accordance with the instructions (7.3 Disposal).

2Transportandstorage
Festo – GDCP-CMCA-B-INST-EN – 1405NH – English 13
2.4 Check the scope of delivery
1. After unpacking, check whether the product corresponds to the version you ordered.
2. Check accompanying user manual of the individual components for completeness.
Documentation No.
Electrical installation control system CMCA-...-B... 1
Circuit diagram, control system CMCA-...-B... 1
Multi-axis controller CMXR-C1/CMXR-C2 1
Motor controller + CD-ROM 1
I/O module CECX-D-8E8A-NP-2 1
Power supply CACN 1
Subcon cable interface 1
Ethernet switch SFNB 1
Controller PNOZ S7 + supplement 1
Controller PNOZmulti Mini + DVD 1
Buffer module 1 (for characteristic S2)
Terminals with filter 1, 21108-2EN-04 1
Tab. 2 .3
Only for control cabinet version:
3. Check accompanying accessories for completion.
Accessories No.
Keyforkeyswitch 2 each
Key for control cabinet doors 1
Inscription labels for control elements, German 6
Tab. 2 .4

3Overview
14 Festo – GDCP-CMCA-B-INST-EN – 1405NH – English
3Overview
3.1 Function and application
The control system CMCA-...-B... serves to control and monitor a connected kinematics system with several
axes. Each axis of the kinematics system is controlled by a motor controller. The higher-order multi-axis con-
troller coordinates the movements of the individual axes through the corresponding motor controller.
3.2 Design
3.2.1 External control elements and connections
5
6
2
3
4
1
79
8
aJ
aA
1Base (option)
2Control cabinet door, left
3Control cabinet fan cover
4Power switch
5Connection for operator unit CDSA or
enabling button CACS-Z-...
6Control and signal elements (Fig. 3.2)
7Emergency stop switch (S1)
8Transport lugs
9Outlet filter cover
aJ Control cabinet doors interlock
aA Control cabinet door right
Fig. 3.1

3Overview
Festo – GDCP-CMCA-B-INST-EN – 1405NH – English 15
562341
1Illuminated push-button (S20/P20) “acknowledge emergency stop”: confirms unlocking of the
emergency stop circuit
2Indicator light (P21) “external emergency stop”: external emergency stop triggered
3Indicator light (P4) “automatic control”: automatic operation active
4Key switch (S2) “automatic/manual”: Switches between automatic and manual override
The switch is only active when the “local” operating mode has been selected by means of link
plugs (Tab. 4.18). In case of “external” operating mode, the switch is without effect.
5Indicator light (P5) “manual control”: manual override active
6Key actuator (S3) “brake release”: releases the motor brakes
Only possible in manual override and in combination with one of the enabling buttons on the oper-
ator unit CDSA or the enabling button CACS-Z-....
Fig. 3.2
Note
The labels for marking the control elements in German as well are included in the con-
trol cabinet.

3Overview
16 Festo – GDCP-CMCA-B-INST-EN – 1405NH – English
3.2.2 Internal components and connections
The design can deviate from the illustration, depending on the version.
5
6
2
4
1
3
789aJaA
aB
aC
aD
aE
aF
1Terminal strips X0 … X6
2Monitoring module for mains failure detection (only for characteristic S2)
3Controller, safety control circuit PNOZ S7
4Circuit breakers F1 … F22
5Protective contact socket type F (230 V AC, max. 6 A) for PC
6Multi-axis controller
7Controller, safety control circuit extension PNOZmulti
8Connection for operator unit CDSA or enabling button CACS-Z-...
(with control cabinet design on the left door)
9Buffer module 24 V DC (only for characteristic S2)
aJ Power supply unit 24 V DC
aA Ethernet switch
aB Motor controller for axis 4 (only for characteristic B3, B5, B8)
aC Motor controller for axis 3 (only for characteristic B2, B3, B4, B5, B7, B8)
aD Motor controller for axis 2
aE Motor controller for axis 1
aF Terminals with filter
Fig. 3.3

3Overview
Festo – GDCP-CMCA-B-INST-EN – 1405NH – English 17
3.2.3 Terminal strips
5623 41
1X0: Feed upstream of power switch
2X1: Feed downstream of power switch
3X2: Control circuit 24 V DC
4X3: Emergency stop
5X4: External emergency stop
6X6: Control and signal elements
Fig. 3.4

3Overview
18 Festo – GDCP-CMCA-B-INST-EN – 1405NH – English
3.2.4 Circuit breakers
5623417 8 9 aJ aA aB aC
1F1 (B16 A):
power supply 230 V AC, power supply unit 24 V DC
2F2 (B16 A):
power supply 230 V AC, load circuit motor controller axis 1
(three-phase for characteristics A6, A7 and A8)
3F3 (B16 A):
power supply 230 V AC, load circuit motor controller axis 2
(three-phase for characteristics A6, A7 and A8)
4F4 (B16 A):
power supply 230 V AC, load circuit motor controller axis 3
(only for characteristics B2, B3, B4, B5, B7, B8)
5F5 (B16 A):
power supply 230 V AC, load circuit motor controller axis 4
(only for characteristics B3, B5, B8)
6F6 (B6 A):
power supply 230 V AC, plug socket
7F10 (B2 A):
power supply 230 V AC, control cabinet fan
8F11 (B2 A):
power supply 230 V AC, control cabinet lighting
9F12 (B4 A):
external emergency stop
aJ F13 (B4 A):
external emergency stop
aA F20 (B6 A):
power supply 24 V DC
aB F21 (B4 A):
power supply 24 V DC
aC F22 (B2 A):
power supply 24 V DC
Fig. 3.5

4 Mounting and installation
Festo – GDCP-CMCA-B-INST-EN – 1405NH – English 19
4 Mounting and installation
4.1 Mounting
Warning
Danger of injury/damage risk due to falling loads.
If incorrectly mounted, the control system can become loose and fall.
• Observe the product weight in selection of the mounting surface and mounting
material (A.1 Technical data).
4.1.1 Mounting plate
The control system on the mounting plate must be mounted to the 6 mounting points on a vertical and
sufficiently stable surface.
Mounting points
L3
L1
L2
Fig. 4.1
Dimensions [mm]
L1 925
L2 518
L3 462.5
Tab. 4.1

4 Mounting and installation
20 Festo – GDCP-CMCA-B-INST-EN – 1405NH – English
4.1.2 Control cabinet without base
The control system with its own control cabinet must be mounted as follows:
– upright on a sufficiently strong wall bracket
– upright on horizontal cross braces in a frame with sufficient bearing capacity
– with a free space below the control cabinet of at least 200 mm for the cable throughfeed
Note
A wall bracket is not included in the scope of delivery.
Note
Screws and mounting accessories are not included in the scope of delivery.
• Observe the product weight in selection of the mounting surface and mounting ma-
terial (A.1 Technical data).
Mounting points, control cabinet bottom for mounting on wall bracket
Fig. 4.2
Dimensions [mm]
L1 940
L2 239.4
D1 ∅9
Tab. 4.2
Table of contents
Other Festo Control System manuals

Festo
Festo CMCA series User manual
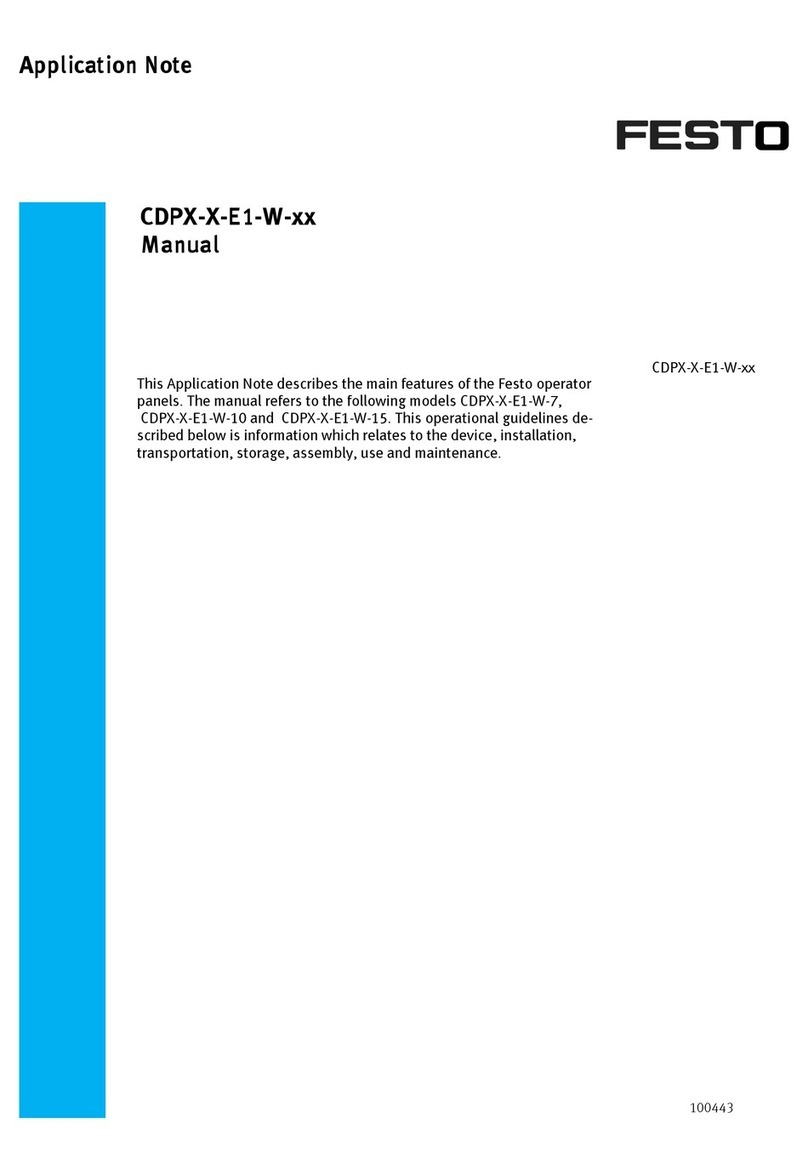
Festo
Festo CDPX-X-E1-W Series User manual
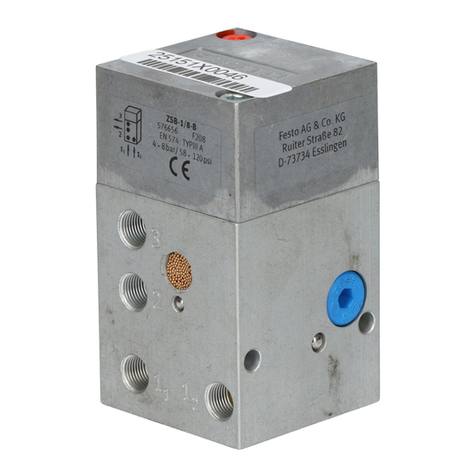
Festo
Festo ZSB-1/8-B User manual
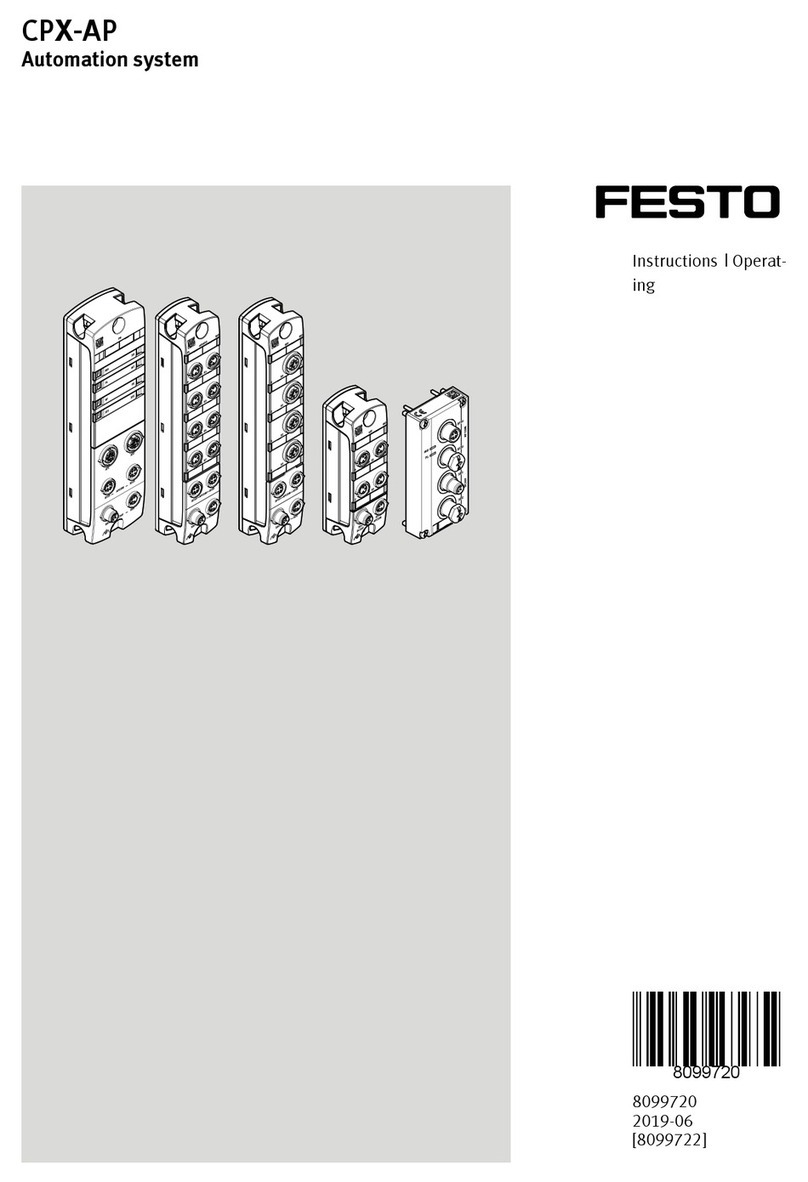
Festo
Festo CPX-AP Series User manual
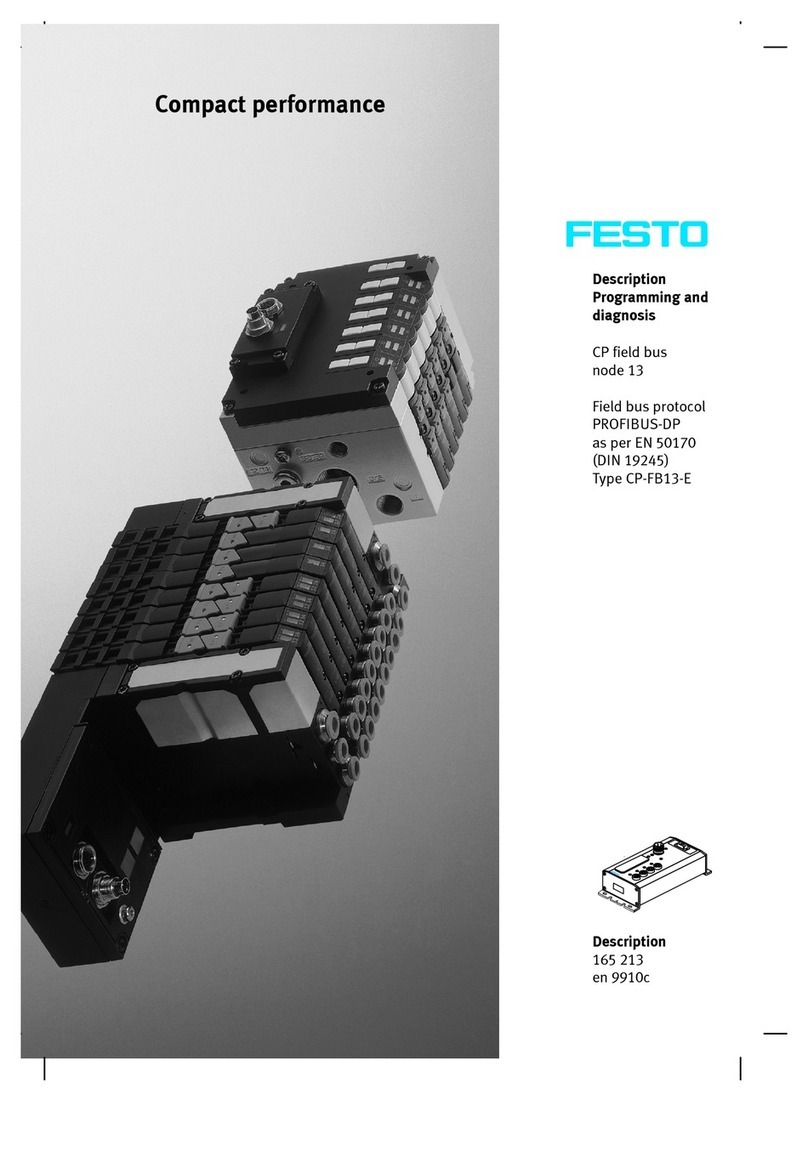
Festo
Festo CP-FB13-E User manual
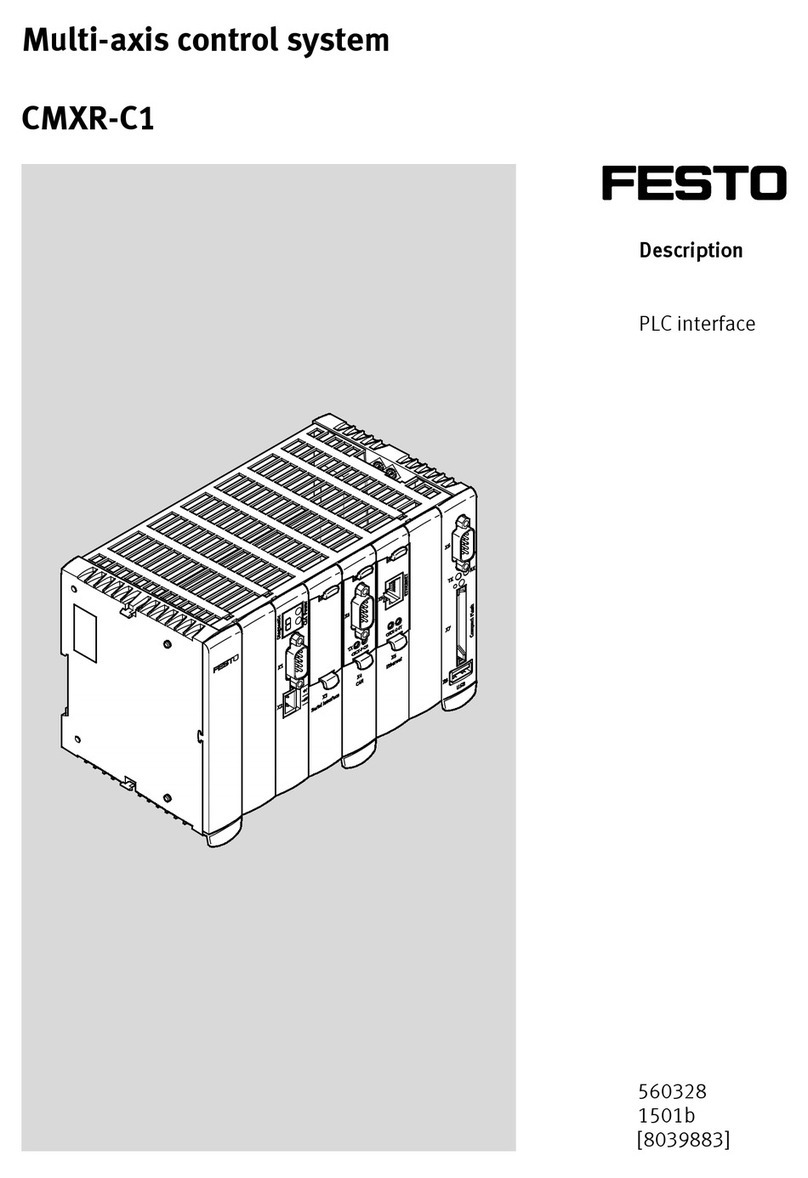
Festo
Festo CMXR-C1 Operating and installation instructions
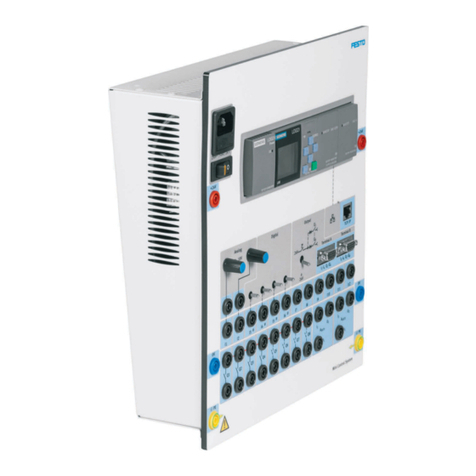
Festo
Festo EduTrainer 8071407 User manual
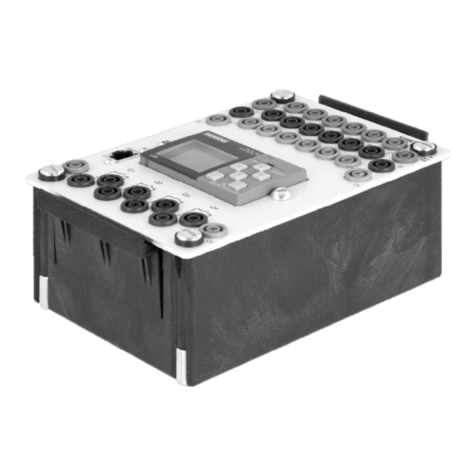
Festo
Festo LOGO! 8 TP EduTrainer User manual
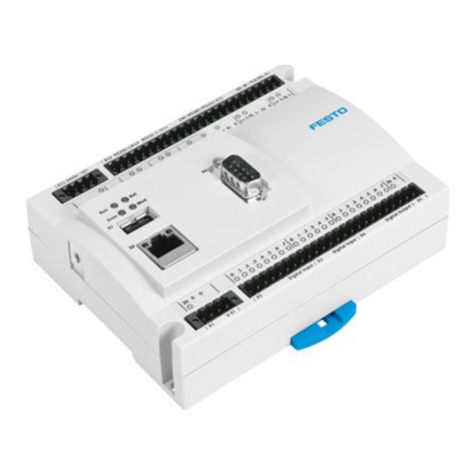
Festo
Festo Controller CECC-LK Parts list manual
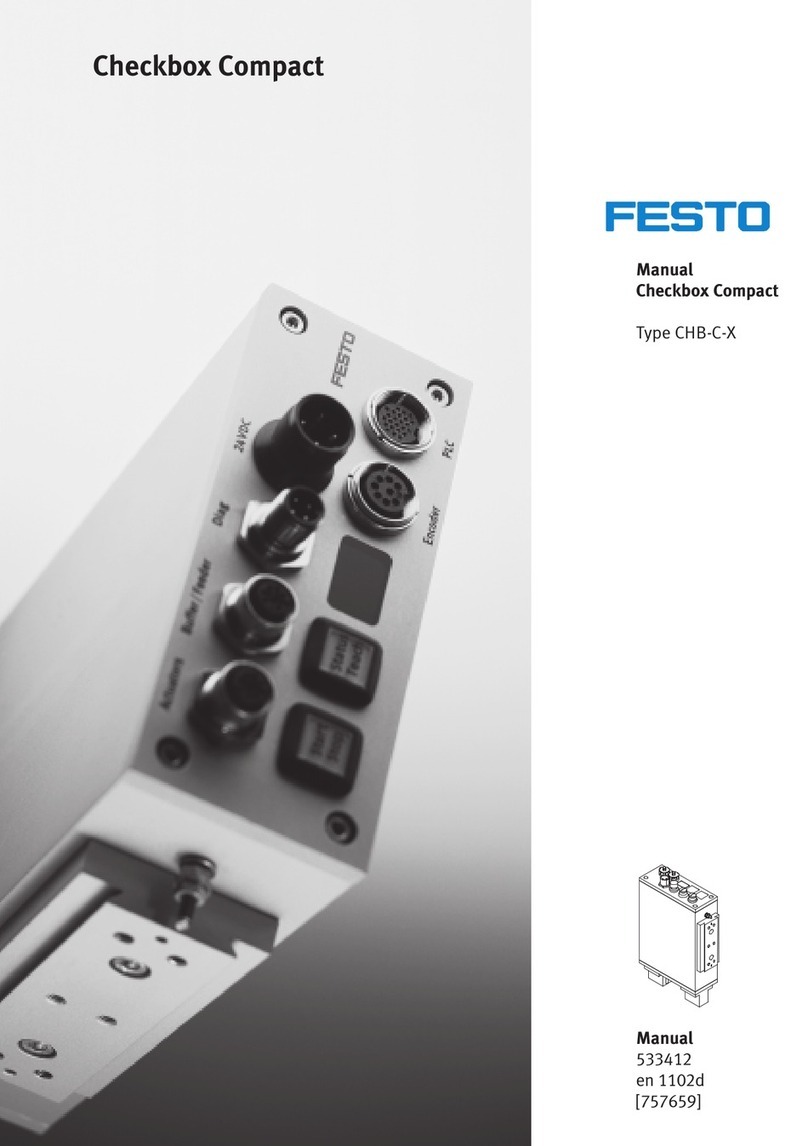
Festo
Festo Checkbox Compact CHB-C-X User manual