HAUVREX HFL4140E Manual

MODEL: HFL4140E
Please read through this manual before operation. You must read and understand the
precautions for safety to protect your safety
and any damage to your property.
ELECTRO-HYDRAULIC 4-POST LIFT
Installation/Operation & Maintenance Manual
Version: HR201408.2.0


NOTE TO THE USER
Thank you for purchasing our products.
Please read this instruction carefully for safe and proper use
of the car lift, and keep it handy for future reference.
■This Manual is for model: HFL4140E
■As for the assurance of safety in design and construction of
car lift, read this Manual first.
■Please make sure that this manual is delivered to end users
for their implementation of safety.
■Don't use the car lift in a potentially explosive atmosphere.
ANY PART OF THIS PRINT MUST NOT BE REPRODUCED
IN ANY FORM WITHOUT PERMISSION.
THIS PRINT IS SUBJECT TO CHANGE WITHOUT NOTICE.


i
Installation/Operation & Maintenance Manual
HFL4140E 4-POST ALIGNMENT LIFT
Chapter 1 DESCRIPTION OF THE MACHINE
1.1 FIXED STRUCTURE ASSEMBLY
1.2 MOVABLE STRUCTURE
Chapter 2 SPECIFICATIONS
2.1 OVERALL DIMENSIONS
2.2 TECHNICAL SPECIFICATION
2.3 ELECTRIC MOTOR
2.4 HYDRAULIC PUMP
2.5 OIL
2.6 TYPES OF VEHICLES SUITABLE FOR BEING LIFTED AND
OVERALL DIMENSIONS
Chapter 3 SAFETY
Chapter 4 INSTALLATION
4.1 ASSEMBLY OF MOVABLE STRUCTURE (PLATFORM)
4.2 POST ASSEMBLY
4.3 HYDRAULIC SYSTEM CONNECTION
4.4 ELECTRICAL SYSTEM CONNECTION
4.5 CABLE PRE-ADJUSTMENT
4.6 SECURE THE POSTS TO THE GROUND
4.7 INSTALLING THE VEHICLE RAMPS AND THE WHEEL
STOPS
4.8 ADJUSTING THE LIFTING CABLES
4.9 PRELIMINARY TESTS AND INSPECTIONS BEFORE
STARTING
Chapter 5 OPERATING PRINCIPLES AND USE
5.1 MAIN MACHINE OPERATION
5.2 ROLLING JACK OPERATION
Chapter 6 MAINTENANCE
Chapter 7 TROUBLESHOOTING
APPENDIX A SPECIAL INFORMATION
TABLE OF CONTENTS
1
1
2
4
4
5
5
5
5
6
7
12
13
13
15
15
15
16
16
17
17
18
18
19
19
22
23
TABLE OF CONTENTS

ii
Installation/Operation & Maintenance Manual
HFL4140E 4-POST ALIGNMENT LIFT
APPENDIX B HYDRAULIC DIAGRAM
APPENDIX C ELECTRICAL WIRING DIAGRAM
APPENDIX D SPARE PARTS
24
25
26
TABLE OF CONTENTS

1
Installation/Operation & Maintenance Manual
HFL4140E 4-POST ALIGNMENT LIFT
Chapter 1 DESCRIPTION OF THE
MACHINE
Four-post lifts are fixed installations, i.e. anchored to
the floor; the units are designed and built for lifting
cars and vans and holding them in an elevated
position.
The units are essentially made up of a fixed part that
is anchored to the floor (posts) and a moving part
(cross-pieces and platforms). The operation is
electro-hydraulic.
■There are four basic parts of the lifts:
■Fixed structure assembly;
■Movable structure assembly;
■Lifting assembly;
■Safety devices.
Fig. 1 shows the various parts of the lift and the
operating zones in the surrounding area.
Fig. 1
The lift is composed of the following main parts:
Control side post (conventionally the front right-hand
post) (Fig. 1-1)
■Front left post (Fig. 1-2)
■Rear left post (Fig. 1-3)
■Rear right post (Fig. 1-4)
■Control side cross-piece (front cross-piece)
(Fig. 1-5)
■Rear cross-piece (Fig. 1-6)
■Right fixed platform (Fig. 1-7)
■Left moving platform (Fig. 1-8)
Operator side: this is the front of the lift, including
the area reserved for the operator with the control
panel. The operator side is opposite the vehicle
access side.
Rear side: it is the side opposed the operator’s one,
with the lift access ramps.
Right and left sides: the right and left is considered
from the operator’s standpoint when facing the lift.
Danger zone: an area that must be kept clear of
persons when the lift is in use; refer to Chapter
“Safety devices” for details.
1.1 FIXED STRUCTURE ASSEMBLY
The structure includes the four vertical posts in bent
steel plate with a pre-drilled base plate for
expansion anchors to secure the unit to the floor
(see Chapter 4 “Installation”).
Each post houses:
■A safety rod with slots (Fig.2-2) to engage the
safety wedges;
■A steel cable for lifting (Fig. 2-1);
■A guide for the cross-piece vertical sliding (Fig.
2-3).
Fig. 2
The following parts are anchored to the top of each
post:
■End of safety rod (Fig. 3-2), (secured with M20
nut and lock nut, class 8.8);
■The end of the steel cable (Fig. 3-1), which is
fitted with an M20 threaded shank (fixed with
M20 nut and lock nut, class 6S).
The length of the cables can be perfectly adjusted,
also to take up slack due to stretching, thanks to the
length of the threaded shanks on the ends of the
cables.

2
Installation/Operation & Maintenance Manual
HFL4140E 4-POST ALIGNMENT LIFT
Fig. 3
The drive post mounts the hydraulic power unit (Fig.
4).
Fig. 4 Hydraulic Power Unit
The hydraulic power unit comprises:
■An electric motor (Fig. 4-1);
■A geared hydraulic pump (Fig. 4-2);
■Descent hand-valve equipped with a manual oil
drain valve; (Fig. 4-3) (see the use and
maintenance chapter)
■A maximum pressure valve;
■Oil tank (Fig. 4-4);
■An oil delivery and return flexible pipe to the
cylinders feeding circuit.
1.2 MOVABLE STRUCTURE
The movable structure consist of two cross-pieces
and two platforms.
Each cross-piece translates vertically between two
posts.
Fig. 5
As shown in Fig. 5, the ends of the cross-pieces are
fitted with the following parts:
■Return pulleys (Fig. 54) for the lift cable
■Mechanical safety devices (wedges) (Fig. 5-1
and Fig. 5-2)
The wedge (Fig. 5-2) will engage automatically
during lifting and when the lift is raised. To start the
LOWERING cycle the wedges must be disengaged
by hand or using an electro-pneumatic control
(optional) when lowering.
The safety wedge (Fig. 5-1) take the weight in the
event of a cable failure; the wedge automatically
engages with the safety rods and immediately stops
the movable section of the lift together with the
vehicle; the cable micro-switch disconnects the
electrical parts.
The two platforms (Fig. 6) are supported on the
cross-pieces.
Fig. 6
The right platform (Fig. 6-6) has no adjustment; the
left platform (Fig. 6-2) is free to slide across the
width of the lifting area to adapt to the track width of
the vehicle being lifted.

3
Installation/Operation & Maintenance Manual
HFL4140E 4-POST ALIGNMENT LIFT
Both platforms have inside rails (Fig. 6-6) for rolling
jack, and fixed wheel stops (Fig. 6-7) to stop the
vehicle from going beyond the ends of the platforms.
The access ramps (Fig. 6-4), pivoted to the
platforms, automatically reach a vertical position
when the platforms lift, thereby securing the vehicle
also from the access end.
The following components are located beneath the
fixed platform (Fig. 7), and are accessible only from
underneath:
■Hydraulic lift cylinder (Fig. 7-3)
■Parachute safety valve (Fig. 7-2)
■Clevis coupling (Fig. 7-1) for the steel cables
■Two cable return pulley assemblies (Fig. 7-4)
Fig. 7

4
Installation/Operation & Maintenance Manual
HFL4140E 4-POST ALIGNMENT LIFT
Chapter 2 SPECIFICATIONS 2.1 OVERALL DIMENSION
Fig. 8 Overall Dimension

5
Installation/Operation & Maintenance Manual
HFL4140E 4-POST ALIGNMENT LIFT
2.3 ELECTRIC MOTOR
Type ....................................................................C90
Power .............................................................2.2 Kw
Voltage ...................................230-400V 3ph. +/-5%
Frequency ........................................................50 Hz
Poles .......................................................................4
Speed.........................................................1400 rpm
Building shape....................................................B 14
Insulation class........................................................F
Absorption ............................................230V: 10,7A
..............................................400V: 6,2A
When connecting the motor refer to the enclosed
wiring diagrams, the motor has left-handed rotation
(counter-clockwise) as shown on the data plate on
the casing.
2.4 HYDRAULIC PUMP
Type ......................................................................18
Model ........................................................10A5x348
Displacement ..............................................5 cc/rev.
Relief valve set-up .........................................160 bar
2.5 OIL
The hydraulic oil reservoir is filled with mineral oil to
ISO/DIN 6743/4, contamination category no higher
than class 18/15 according to ISO 4406, such as IP
2.2 TECHNICAL SPECIFICATION
Driving Mode Electro-hydraulic
Capacity 4000kg
Max. Lifting Height 1800mm
Min. Height 135mm
Platform Length 4500mm
Platform Width 500mm
Lifting Time ≤60S
Lowing Time ≤50s
Overall Width 3254mm
Overall Length 4677mm
Overall Weight 1200kg
Power AC 110V、220V、230V or 380V 50 Hz/ 60 Hz
Hydraulic Oil 16 L 20# high abrasive hydraulic oil
Working Temperature 5-40℃
Working Humidity 30-95%
Noise Level <76db
Installation Altitude ≤1000M
Storage Temperature -25-55℃
Rolling Jack Capacity 2000kg
Max. Lifting height of Rolling Jack 454mm
Table 1

6
Installation/Operation & Maintenance Manual
HFL4140E 4-POST ALIGNMENT LIFT
HYDRO OIL 32; SHELL TELLUS T37 or an
equivalent oil.
2.6 TYPES OF VEHICLES SUITABLE FOR
BEING LIFTE D A N D O V E R ALL
DIMENSIONS
The lift is suitable for virtually all vehicles with total
weight of no more than 4000 kg.
The vehicle dimension shall not exceed the below
data:
Max. width: 2400 mm.
Max. wheelbase: 3000 mm.
Max. distance between outer wall of tyres, inclusive
of bulge caused by weight of vehicle on ground:
2000 mm.
Min. distance between inner walls of tyres, inclusive
of bulge caused by weight of vehicle on ground: 900
mm.
Caution: the lower parts of the vehicle underbody
could interfere with structural parts of the lift.
Take particular care in the case sports-cars.
The lift will also handle customized or non-standard
vehicles provided they are within the maximum
specified carrying capacity.
Also the personnel danger zone must be defined in
relation to vehicles with unusual dimensions.
The following diagrams illustrate criteria used to
define the operating limits of the lift.
Fig. 9
Table 2
FOR LARGER DIMENSIONS CHECK THE
MAXIMUM LOAD AND POSSIBLE UNBALANCE.
MAXIMUM WEIGHTS OF VEHICLES BEING
LIFTED
Fig. 10 Weight Distribution
Min. (mm) Max. (mm)
A 2300 4500
B 200
C 2000
D 900

7
Installation/Operation & Maintenance Manual
HFL4140E 4-POST ALIGNMENT LIFT
Chapter 3 SAFETY
It is extremely important to read this chapter of
the manual carefully and from beginning to end
as it contains important information regarding
the risks the operator or maintenance fitter may
be exposed to if the lift is used incorrectly.
In the following text there are clear explanations
regarding certain situations of risk or danger
that may arise during the operation or
maintenance of the lift, the safety devices
installed and the correct use of such systems,
residual risks and operative procedures to use
(general and specific precautions to eliminate
potential hazards).
WARNING:
The lifts are designed and built to lift vehicles
and hold them in the elevated position in an
enclosed workshop. All other uses of the lifts
are unauthorized. In particular, the lifts are not
suitable for:
■Washing and respray work;
■Creating raised platforms for personnel or lifting
personnel;
■Use as a press for crushing purposes;
■Use as elevator;
■Use as a lift jack for lifting vehicle bodies or
changing wheels.
During lifting and lowering movements the
operator must remain in the control station as
defined in Fig. 11.
The presence of persons beneath the cross-
pieces and/or the platforms when they are
moving, or the presence of persons inside the
danger zone indicated in Fig. 11 is strictly
prohibited.
The area occupied from the lift and perimetral
band of width 1÷ 2 mt of the lift are defined as
"DANGER ZONE".
The operator parking area, only for actioning the
lift, is defined as "ZONE OPERATOR".
Fig. 11
During operations persons are admitted to the
area beneath the vehicle only when the vehicle
is already in the elevated position, when the
cross-pieces and platforms are stationary, and
when the mechanical safety devices (wedges)
are firmly engaged in the slots on the safety
rods.
DO NOT USE THE LIFT WITHOUT PROTECTION
DEVICES OR WITH THE PROTECTION DEVICES
INHIBITED.
FAILURE TO COMPLY WITH THESE
REGULATIONS CAN CAUSE SERIOUS INJURY
TO PERSONS, AND IRREPARABLE DAMAGE TO
THE LIFT AND THE VEHICLE BEING LIFTED.
GENERAL PRECAUTIONS
The operator and the maintenance fitter are required
to observe the prescriptions of safety regulation in
force in the country of installation of the lift.
Furthermore, the operator and maintenance fitter
must:
■Always work in the stations specified and
illustrated in this manual;
■Never remove or deactivate the guards and
mechanical, electrical, or other types of safety
devices;
■Read the safety notices placed on the machine
and the safety information in this manual.
In the manual all safety notices are shown as
follows:

8
Installation/Operation & Maintenance Manual
HFL4140E 4-POST ALIGNMENT LIFT
DANGER: indicates imminent danger that can result
in serious injury to people or death.
WARNING: indicates situations and/or types of
maneuvers that are unsafe and can cause more or
less harmful injuries or death.
CAUTION: indicates situations and/or types of
maneuvers that are unsafe and can cause minor
injury to persons and/or damage the lift, the vehicle
or other property.
RISK OF ELECTRIC SHOCK: a specific safety
notice placed on the lift in areas where the risk of
electric shock is particularly high.
RISKS AND PROTECTION DEVICES
We shall now examine the risks that operators or
maintenance fitters may be exposed to when the
vehicle is standing on the platforms in the raised
position, together with the various safety and
protection devices adopted by the manufacturer to
reduce all such hazards to the minimum:
LONGITUDINAL MOVEMENTS
Longitudinal movements refer to forward and
backward movement of the load (vehicle).
To protect against the consequences of longitudinal
movement, the lift is installed with fixed wheel stops
at the front of the lift, and pivoting stops at the rear.
The stops are integral with the platforms and serve
to secure the vehicle during lifting and lowering
movements and when the vehicle is at a standstill in
the raised position, thus preventing any potentially
dangerous movement.
SIDE MOVEMENTS
Side movements refer to shifting of the vehicle
toward the left or right of the lift, especially during
the lifting cycle.
Fig. 12
Fig. 13
For optimal personal safety and safety of vehicles,
observe the following regulations:
Do not enter the danger zone while vehicles are
being lifted (see Fig. 11);
Switch off the engine of the vehicle, engage a gear
and engage the hand brake;
Make sure the vehicle is positioned correctly
(Fig.14);
Fig. 14
Be sure to lift only approved vehicles, never exceed
the specified carrying capacity, maximum height,
and projections (vehicle length and width);
Make sure that there are no persons on the
platforms during up and down movements and
during standing (Fig. 15).

9
Installation/Operation & Maintenance Manual
HFL4140E 4-POST ALIGNMENT LIFT
Fig. 15
POTENTIAL RISKS DURING LIFTING
The following safety devices are installed to protect
against overloads and possible mechanical failures:
In the case of excess weight on the lift the relief
valve on the hydraulic power unit will open (Fig. 16).
Fig. 16
If one or more hoses in the hydraulic circuit should
break, a cylinder locking valve will operate (Fig.
17).
Fig. 17
If the movable part of the lift should go in overstroke,
there is an electric limit switch (Fig. 18) in the
control post and a steel locking plate on the top of all
four posts.
Fig. 18
Should the steel cables slacken or break, the safety
wedges will stop the movable part of the lift and the
vehicle in its current position (Fig. 19).
Fig. 19
RISKS FOR PERSONNEL
This heading illustrates potential risks for the
operator, maintenance fitter, or any other person
present in the area around the lift, resulting from
incorrect use of the lift.
RISK OF CRUSHING (OPERATOR)
Possible if the operator controlling the lift is not in
the specified position at the control panel.
When the platforms (and vehicle) are lowering the
operator must never be partly or completely
underneath or near of the movable structure. Always
remain in the operator zone (Fig. 11).
RISK OF CRUSHING (PERSONNEL)
When the platforms and the vehicle are lowering,
personnel are prohibited from entering the area
beneath the movable parts of the lift (Fig. 20). The
lift operator must not start the maneuver until it has
been clearly established that there are no persons in
danger zone.

10
Installation/Operation & Maintenance Manual
HFL4140E 4-POST ALIGNMENT LIFT
Fig. 20
RISK OF IMPACT
Caused by the parts of the lift or the vehicle that are
positioned at head height.
When, due to operational reasons, the lift is stopped
at relatively low elevations (less than 1.75 m from
the ground) personnel must be careful to avoid
impact with parts of the machine not marked with
special colors (Fig. 21).
Fig. 21
RISK OF VEHICLE MOVING
Caused by operations involving the application of
force sufficient to displace the vehicle.
In the case of large or particularly heavy vehicles,
sudden movement could create an unacceptable
overload or uneven loadsharing.
Therefore, before lifting the vehicle and during all
operations on the vehicle
MAKE SURE THAT IT IS PROPERLY STOPPED
BY THE HAND BRAKE.
Fig. 22
RISK OF VEHICLE FALLING FROM LIFT
This hazard may arise in the case of incorrect
positioning of the vehicle on the platforms, incorrect
stopping of the vehicle, or in the case of vehicles of
dimensions that are not compatible with the capacity
of the lift.
NEVER ATTEMPT TO PERFORM TESTS BY
DRIVING THE VEHICLE WHILE IT IS ON THE
PLATFORMS (e.g. reversing, etc.).
Fig. 23
RISK OF SLACKENING OF LIFT CABLES
Caused by objects left leaning against the posts or
on the platforms (Fig. 24).
NEVER LEAN OBJECTS AGAINST THE POSTS
OR LEAVE THEM IN THE LOWERING AREA OF
THE MOVABLE PARTS OF THE LIFT.
If you leave objects that interfere with the free
lowering of the platforms, the lowering movement
will be interrupted.
Fig. 24
RISK OF SLIPPING
Caused by lubricant contamination of the floor
around the lift (Fig. 25).
THE AREA BENEATH AND IMMEDIATELY
SURROUNDING THE LIFT AND ALSO THE
PLATFORMS MUST BE KEPT CLEAN. Remove
any oil spills immediately.
When the lift is fully down, do not walk over the
platforms or the cross-pieces in places that are
lubricated with a film of grease for functional

11
Installation/Operation & Maintenance Manual
HFL4140E 4-POST ALIGNMENT LIFT
requirements. Reduce the risk of slipping by wearing
safety shoes.
Fig. 25
RISK OF ELECTRIC SHOCK
Risk of electric shock in areas of the lift housing
electrical wiring.
Do not use jets of water, steam (high pressure
washers units), solvents or paint next to the lift, and
take special care to keep such substances clear of
the electrical control panel.
RISKS RELATED TO INAPPROPRIATE LIGHTING
The operator and the maintenance fitter must be
able to assure that all the areas of the lift are
properly and uniformly illuminated in compliance
with the laws in force in the place of installation.
RISK OF COMPONENT FAILURE DURING
OPERATION
The manufacturer has used appropriate materials
and construction techniques in relation to the
specified use of the machine in order to manufacture
a reliable and safe lift. Note however, that the lift
must be used in conformity with manufacturer’s
prescriptions, and the frequency of inspections and
maintenance works recommended in Chapter 6
“MAINTENANCE” must be observed.
RISKS RELATED TO IMPROPER USE
Persons are not permitted to stand or sit on the
platforms during the lift maneuver or when the
vehicle is already lifted.
All uses of the lift other than the uses for which it
was designed are liable to give rise to serious
accidents involving the persons working nearby.
It is therefore essential to adhere scrupulously to all
regulations regarding use, maintenance and safety
contained in this manual.
Fig. 26

12
Installation/Operation & Maintenance Manual
HFL4140E 4-POST ALIGNMENT LIFT
Chapter 4 INSTALLATION
THE FOLLOWING OPERATIONS MUST BE
PERFORMED EXCLUSIVELY BY SPECIALISED
TECHNICAL STAFF WITH AUTHORISATION
FROM THEMANUFACTURER OR LICENSED
DEALER.
IF THESE OPERATIONS ARE PERFORMED BY
OTHER PERSONS, SERIOUS PERSONAL
INJURY AND/OR IRREPARABLE DAMAGE TO
THE LIFT UNIT MAY RESULT.
INSTALLATION REQUIREMENT CHECK
MAKE SURE THAT THE INTENDED PLACE OF
INSTALLATION IS SUITABLE.
The lift is designed for installation in enclosed areas
suitably protected from weather. The place of
installation must be well clear of areas in which
washing or painting work is performed, and away
from solvent or paint storage areas or areas, where
there is a risk of potentially explosive atmosphere.
CHECK OF ROOM SUITABILITY AND SAFETY
CLEARANCES.
The lift must be installed in compliance with the
clearances between walls, pillars, other machines,
etc. indicated in Fig. 27 and in compliance with any
law requirements in the country of installation.
Fig. 27
In any event, there must be a minimum clearance of
800 mm between all movable parts of the lift and the
vehicle itself and the nearest fixed or mobile
structures in the workshop.
Check:
■Height: 5000 mm min. (calculate also the height
of the vehicles you intend to lift)
■Distance from walls: 800 mm min.
■Working space: 800 mm min.
■CONTROL POSITION area
■Maintenance area
■Access
■Escape routes for emergency situations
■Position in relation to other machines
■Rational orientation of the lift
■Possibility of electrical connection
LIGHTING
All parts of the machine must be uniformly lit with
sufficient light to make sure that the adjustment and
maintenance operations specified in the manual can
be performed safely, and without areas of shadow,
reflected light, glare and avoiding all situations that
could give rise to eye fatigue.
The lighting must be installed in accordance with
the laws in force in the place of installation
(responsibility lies with the lighting equipment fitter).
FLOOR
The lift must be installed on a horizontal platform
with suitable load capacity.
The platform and the foundations must be suitable
to resist the maximum stress values that the lift can
transmit to the ground envisaging the worst
operating conditions: specific ground pressure
exerted by the lift in the prescribed conditions of use
is approximately 5 kg/cm2.
■Vertical load: 1850 kg
■Shear force: negligible
The floor must be flat and without gradients
(maximum of 10 mm tolerance)
INSTALLING WITH EXPANSION ANCHORS
Example of installation on industrial floor in average
mix concrete with embedded electrowelded

13
Installation/Operation & Maintenance Manual
HFL4140E 4-POST ALIGNMENT LIFT
reinforcing mesh, thickness min. 180 mm and
properly leveled.
Fig. 28
4 . 1 A S S E M B L Y O F M O V A B L E
STRUCTURE (PLATFORM)
Fig. 29
1 - Place 4 trestles of the same height and suitably
sturdy to hold 250 kg each, in the area where you
intend to install the lift. Position the trestles as
shown in the Fig. 29-A/B/C/D.
2 - Remove the posts from the packing (Fig. 29-
1/2/3/4), together with the movable platform (Fig. 29
-7), the hydraulic power unit and accessories.
3 - Place the fixed platform (Fig. 29-8) on two
trestles (Fig. 29-B/C) together with the two cross-
pieces (Fig. 29-5/6).
4 - Place the cross-piece (Fig. 29-5) on trestle (Fig.
29-A) and secure it to the fixed platform (Fig. 29-8).
During these operations check that the steel cables
are correctly positioned (Fig. 30).
Fig. 30
5 - Place the movable platform (Fig. 29-7) on the
cross-pieces (Fig. 29-5/6).
6 - Check squaring and the diagonals of the cross-
piece - platform assembly; check also that the
movable platform runs smoothly between the cross-
pieces; then, fully tighten the screws securing the
fixed platform.
Fig. 31
Repeat this operation for the cross-piece (Fig. 29-6).
4.2 POST ASSEMBLY
Remove the safety rods from the top of the posts as
shown in Fig. 32.

14
Installation/Operation & Maintenance Manual
HFL4140E 4-POST ALIGNMENT LIFT
Fig. 32
Preparation of the control post
The control post is distinguished from the others
because it has drilled holes to receive the control
panel and the hydraulic power unit.
Secure the hydraulic power unit and control panel to
the control post. (Fig. 33)
Fig. 33
Install the lift limit switch on the top inside of the post
according to Fig. 34.
Fig. 34
Position the posts at the end of the cross-pieces
observing the numbering and the lay-out shown in
Fig. 29.
Fit the safety rods (Fig. 35-1) from the top of the
posts, inserting them between the rear face of the
cross-pieces and the guide pins (Fig. 35-2) as
shown in Fig. 35.
Fig. 35
Check the Safety rods are straight.
Fit the Safety rods with the rounded edges of the
slots towards the front of the posts.
Now secure the bottom end of the rods as shown in
Fig. 36.
Fig. 36
Remove the nuts and washers from the ends of the
lifting cables and install the terminal blocks in the
relevant holes on the top plates of the posts (Fig.
37).
Fig. 37
Table of contents
Other HAUVREX Lifting System manuals
Popular Lifting System manuals by other brands

K Tool International
K Tool International XD KTI62115 owner's manual
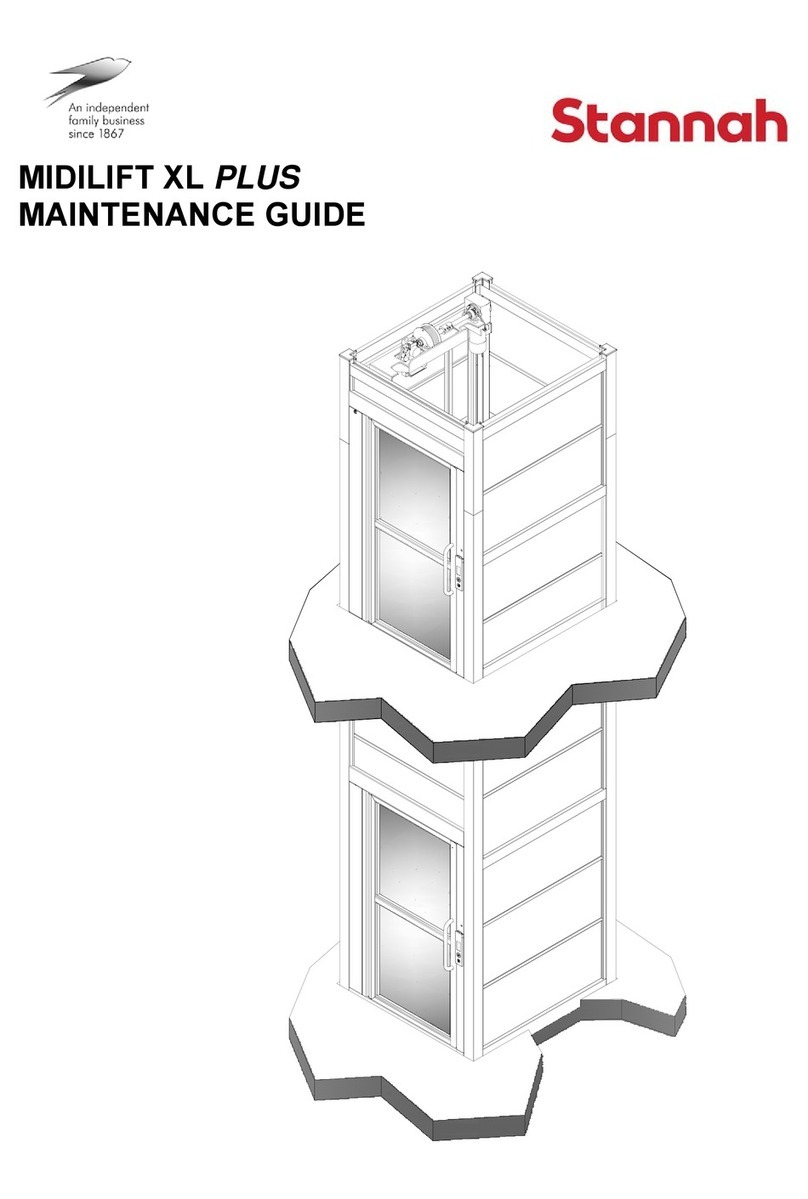
Stannah
Stannah MIDILIFT XL PLUS Maintenance Guide
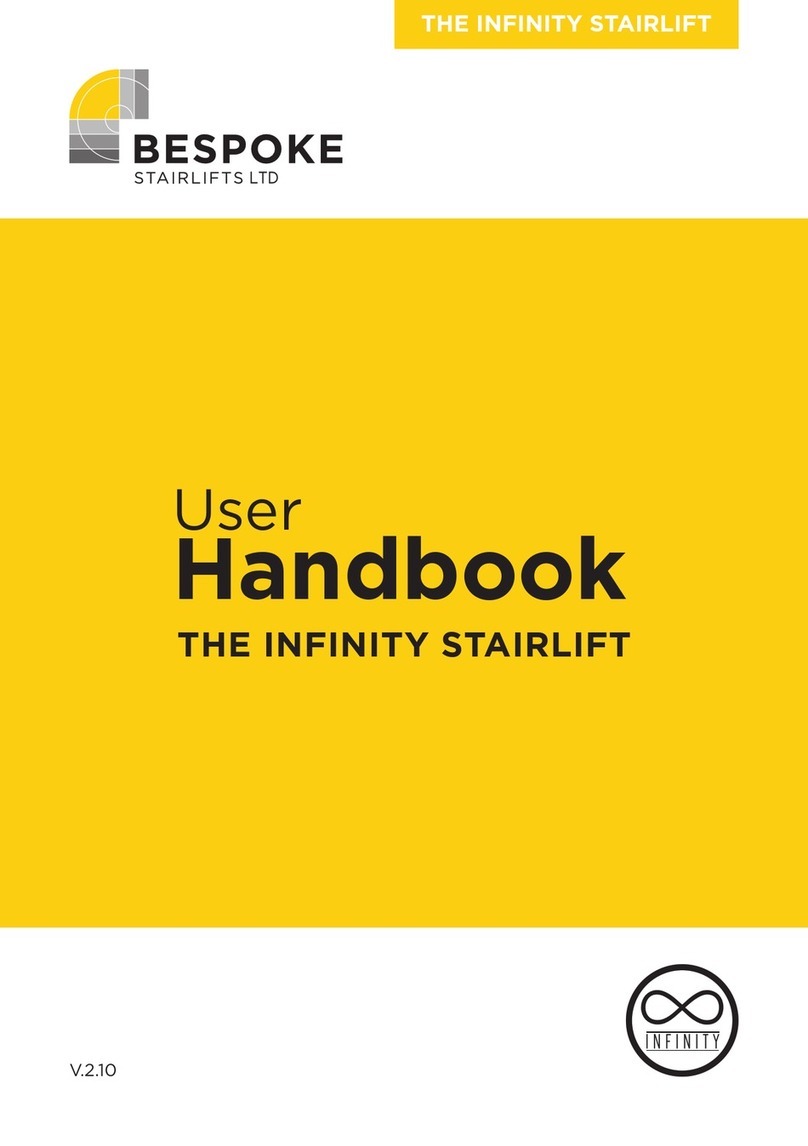
Bespoke
Bespoke Infinity User handbook

Braun Corporation
Braun Corporation Century 2 Series Service manual

Genie
Genie GS-3384 Operator's manual

Artweger
Artweger ARTLIFT ALWA0 Series Assembly instructions