HELI gleen Series Installation and operating instructions

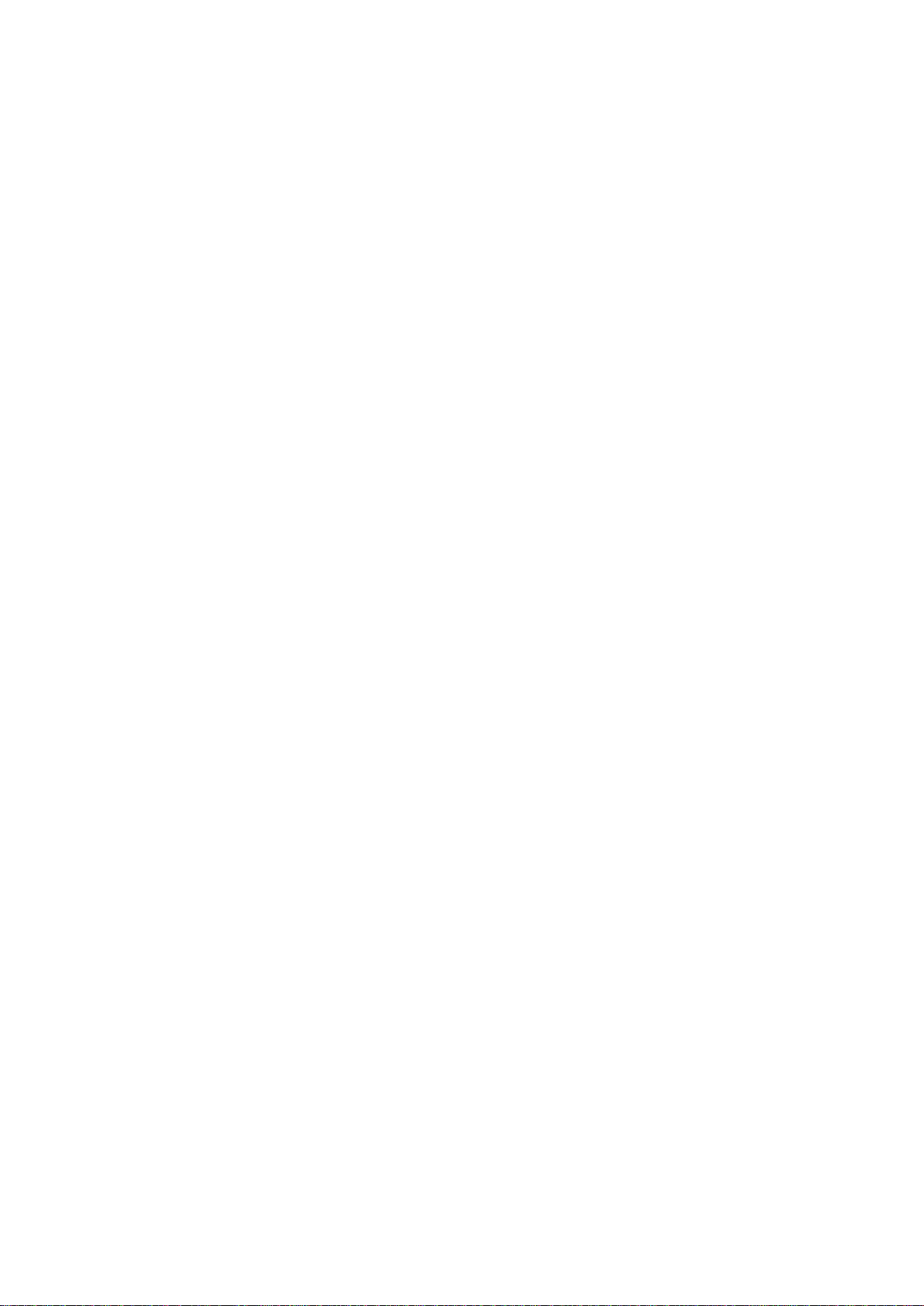
FOREWORD
AC type three wheeled forklift truck with front drive is designed on the base of
advantages of some trucks made by domestic and foreign manufacturers and
developed in introduced technology from abroad to meet the market needs. These
trucks are all suited for handling and stacking packed goods in stations, ports, goods
yards, warehouses, food processing factory, light and textile industries and other
factories. Because the AC type three wheeled forklift truck with front drive has small
turning radius so it is more suitable for narrow working space such as supermarket
and enterprise with high requirement on land usage rate. With some of attachments
fitted, the trucks can be applied more and more.
These trucks feature a wide-visible hoisting system, full powered steering unit,
drive axle with automatic brake, continuous speed control, overhead guard with
opened port, high quality motor, battery, MOSFET electric controller and liquid
crystal combined meter with large screen so they have a lot of advantages such as
good performance, easy operation, wide visibility of operator, flexible steering,
reliable braking, powerful and smooth power, low noise, no contamination to
environment and beautiful contour.
This manual states the trucks’specifications, operation, maintenance, service,
main assemblies’constructions and working principles so as to help operators to use
the trucks correctly and attain the highest functions. It is necessary to read over the
manual before they operate the trucks or service personnel serve these trucks. The
rules and notices in the manual should be abided seriously by relative personals to
enable trucks in optimized working state for long period and bring highest efficiency.
Because of the limit of space and editing, the figures, drawings, parts and such
diagram illustration used in the manual do not have actual proportion. So size or mass
can not be gained from diagram accurately.
This manual content might not correspond with the actual condition because of
the improving of our products. Our products are subject to improvements and changes
without notice.

1
CONTENTS
I. Safety Rules for Opeartion and Daily Maintenance of Forklift Truck.......................2
II. Main Specifications of Forklift Truck.......................................................................7
III. Construction, Priciple,Adjustment and Maintenance of Forklift Truck................11
1. Transmission System .......................................................................................11
2. Brake System...................................................................................................17
3. Steering System ...............................................................................................19
4. Electric System ................................................................................................23
5. Hydraulic System.............................................................................................54
6. Lifting System..................................................................................................68

2
Ι. Safety Rules for Operation and Daily Maintenance of Forklift Truck
It is important that driver and manager for forklift trucks remember the principle
of the “first safety” and ensure the safety operation as the description in
《OPERATION AND SERVICE MANUAL》&《OPERATION MANUAL》.
1. Delivery of Forklift Truck
It must be pay attention to the following items when you deliver forklift trucks
with container or trucks.
(1) Apply the parking brake.
(2) Fix the mast and the balance weight with steel wire. Wedge up all wheels.
(3) Sling points should be always at the positions specified in sling index plate when
hoisting up the forklift truck.
2. Storage of Forklift Truck
(1) Drain off fuel completely. Don’t drain off the cooling water containing antifreeze
and rustproof agent.
(2) Apply antirust to the surface of the parts not painted. Apply lubrication oil to the
lift chain.
(3) Lowing the mast to the lowest position.
(4) Apply the parking brake.
(5) Wedged up the wheels.
3. Precautions Before Operation
(1) Don’t check fuel leakage and lever or instruments at the place where there is open
flame. Never fill the fuel tank with the truck running.
(2) Check the tire inflation pressure.
(3) The forward-reverse lever should be in neutral.
(4) Check all the levers and pedals.
(5) Complete the provisions before starting.
(6) Release the parking lever.

3
(7) Make trying operation of the mast for lifting, lowing and Fwd/Bwd tilting and the
truck for steering and braking.
4. Operation of Forklift Truck
(1) Only trained and authorized operator shall be permitted to operate the truck.
(2) Wear all the safety guards, such as shoes, helmet, clothing and gloves while
operating the truck.
(3) Check all the control and warning devices before starting the truck. If any
damages or defects are found, operate it after repairing.
(4) At the rated loading center, either overload or overload operation is strictly
prohibited. The center of cargo should be in line with the frame center, not out of the
line. The fork should insert completely under the cargo and make the cargo placed on
it evenly. Do not raise an object with one fork end.
(5) The starting, turning, driving, braking and stopping operation of the truck should
be done smoothly. When steering on the humid or low friction road, the truck should
be decelerated.
(6) Travel with loads as low as possible and tilted backward.
(7) Be careful when traveling on a slope. When climbing grades with a slope of more
than 10%, the truck should forward travel, and when descending so grades, backward
travel. Never turning on a slope. Avoid loading and unloading operation when
descending.
(8) Pay attention to pedestrian, obstacle and bumpy road when driving. Pay attention
to the clearance over forklift truck.
(9) Never allow any persons to stand on the forks or the truck to carry persons.
(10)Never permit anyone to stand or walk under upraised forks.
(11)Don’t operate truck and attachment of it at any position out of the drive seat.
(12)On the high lift forklift truck, when the lift high more than 3m, it is noted that the
goods on it should not fall down or the protection measures must be taken if

4
necessary.
(13) Tilt the mast of the high lift forklift truck as backward as possible while the truck
working. Use minimum forward tilt angle and Min. reverse tilt when loading and
unloading.
(14) Be careful and slowly driving over a dockboard or bridge-plate.
(15) Shut down the truck and don’t stay on the truck when checking battery or fuel
lever.
(16) The unloaded forklift truck with attachments should be operated as a loaded
truck.
(17) Don’t handle unfixed stacked goods. Be careful to bulky goods to be handled.
(18) If leaving the truck, lower the forks on the ground and let the shift lever to
neutral, shut down the engine or cut down electric supply. If parking on a slope is
unavoidable, apply the parking brake and block the wheels.
(19) Don’t adjust the control valve and relief valve at will to prevent the damage of
hydraulic system and its components because of excessive pressure passing them.
(20) Inflate a tyre according to it’s stated air pressure. Never over inflate a tyre.
(21) According to the measure method specified in JB/T 3300, the max. noise at the
outboard of the truck should be not more than 80dB(A).
(22) Be familiar with and pay attention to the functions of the decals on the forklift
trucks.
5.Application environment
1) Environment temperature: -25ºC ~ +40ºC;
2) Relative humidity: <90%;
3) Altitude: <1200m.
6. Daily Maintenance of Forklift Trucks
(1) Inspection before startup
a) Hydraulic oil volume: oil level should stay in the middle of oil meter scale;

5
b) Check piping, joints, pumps and valves for leaks or damages;
c) Check parking brake. The unladen truck can park on the 15% grade ramp,
when the parking lever is pulled to the bottom;
d) Check instruments, lighting, switches and wiring to see if they work normally
or not.
(2) Oil used for forklift trucks
Name
Recommended
brand
Brand and temperature of using
Hydraulic oil
Chang cheng
Sticky grade
L-HM32
wearable
hydraulic oil
L-HV32 low
temp. wearable
hydraulic oil
Temp. of
using (℃)
≥-5
≥-20 (cold
region)
Lubricating
grease
Chang cheng
3# lithium base grease (-20℃~+120℃)
Gear oil of
heavy-laden
truck
Hai pai
Sticky grade
85W/90GL-5
80W/90GL-5
Temp. of
using (℃)
-15~+49
-25~+49

6
(3)Lubrication chart
Note: for the truck without brake liquid, it is not necessary to refer to the chart for
relative operation.

7
Ⅱ. Main Specifications of Forklift Truck
Enternal view of forklift trucks

8
Main specifications
Model
Unit
CPD15SQ
CPD18SQ
CPD20SQ
GB
GB
GB
Rated capacity
lb
kg
3000
1500
3500
1750
4000
2000
Load center
in/mm
24/500
Lifting height
in/mm
130/3300
Free lifting height
in/mm
3.5/90
Mast tilt
angle(front/rear)
(K/T)
deg.
5/7
Fork size(L*S*E)
in/mm
42.1×3.9×1.4/ 1070×100×35
42.1×4.8×1.6/
1070×122×40
wheel base F
in/mm
51/1292
55/1400
55/1400
Front tread (b10)
in/mm
35.8/910
36.2/920
36.2/920
Rear tread(b11)
in/mm
6.4/163
7.1/180
7.1/180
Overall length
(without fork)l2
in/mm
114.6/2912
118.8/3020
118.8/3020
Overall width (b1)
in/mm
42/1060
44/1120
44/1120
Overall height
(mast h1)
in/mm
84/2160
86/2175
86/2175
Overall height
(overhead guard
h6)
in/mm
80/2040
Seat height h7
in/mm
370/940
Underground
clearance (at mast)
m1
in/mm
3.3/85
3.5/90
3.5/90
Underground
clearance(truck
frame) m2
in/mm
3.9/100
3.9/100
3.9/100
Min. steering
radius Wa
in/mm
58/1477
62/1585
62/1585
Travelling
speed(loaded/ulo
aded)
36
V
mp
h
km/h
8.7/8.7
14/14
8.7/8.7
14/14
8.7/8.7
14/14
48
V
9.9/10.
5
16/17
9.9/10.5
16/17
9.9/10.5
16/17
Lifting
speed(loaded/unlo
aded)
36
V
fpm
mm/s
66.9/9
8.4
340/500
64.9/98.
4
330/500
63/98.4
320/500
48
V
84.6/1
18
430/600
84.6/118
430/600
78.4/118
400/600
Lowering
speed(loaded/unlo
aded)
fpm
mm/s
98.4/78.4
400/500
Gradeability
(loaded/unloaded)
%
20/33
Tyre size
Front
18x7-8
200/50-10
Rear
140/55-9
140/55-9
Traction motor
HP
kW
4.7X2(AC)
4.7X2(AC)

9
Oil pump motor
HP
kW
11 (AC)
Battery capacity
36
V
A
h
Kwh
880
30.6
1100
38.2
1100
38.2
48
V
A
h
Kwh
660
30.5
770
35.8
770
35.8
Min. battery
weight
lb
Kg
1700
772
2100
953
2100
953
Service mass( with
min. battery)
lb
Kg
6925
3144
7612
3456
8088
3672

10
Dimensions and weight of main removable parts
Truck model
Items
Unit
CPD15SQ
CPD18SQ
CPD20SQ
GB
GB
GB
Counterweight
Max. outline
dimensions
mm
425×1060×775
Weight
kg
750
890
950
Overhead guard
Max. outline
dimensions
mm
1238×1030×1541
1292×1030×1541
Weight
kg
65
75
Mast (lifting height
3300mm)
Max. outline
dimensions
mm
1267×1010×2075
1267×1086×2075
Weight
kg
577
604

11
Ⅲ. Construction, Principle,Adjustment and Maintenance of Forklift Trucks
1. Transmission system
1.1 General description
The transmission system of the three wheeled forklift truck includes transmission
system we call traditionally and brake system. Front wheel dual driving motor structure
makes the right and left wheel of three wheeled truck has drive axle, redactor, brake and
driving motor independently to improve working efficiency. Transmission unit is
assembled inside of drive axle housing while brake is assembled on motor shaft. The
structure is compact.
Truck travelling speed is increased with the increase of motor speed; travelling
direction is changed with motor rotation direction; The sensor installed on rear wheel
sends information to drive motor controller on right and left front wheel, after receiving
different information, right and left front wheel give out different speed and thus steering
of the truck is realized. The steering of the three wheeled truck is realized through electric
differential. The system has no bevel gear which thus not only improves working
efficiency but also reduce bevel gear noise.
1.1.1 Front wheel assembly
Front wheel is made up of solid tyre and rim. Refer to the following for front wheel
and rim model:
Model
Tyre parameters
CPD15SQ
CPD18SQ
CPD20SQ
Model
Super
elasticity
18×7-8
200/50-10
200/50-10
Rim
4.33R
6.50F
6.50F

12
1.2 Disassembling of transmission system
Disassemble the front wheel assembly and travelling motor first before disassemble
transmission box. Then parts inside of the transmission box can be repaired or
maintenance.
1.2.1 Removal of the wheels
Drain off the gear oil inside of the transmission box before disassembling. Loose 6
drive nut and remove drive wheel. Then loose the 7 bolts on frame (2 are M14 x1.5x 50
bolts and 5 are M14x1.5x100 hexagon socket bolts and remove transmission box
connected with travelling motor from frame. Refer to figure 1-1.
Figure 1-1
1.2.2 Removal of travelling motor
Refer to figure 1-2 to remove the bolts fixing travelling motor (one is M8 x50, and
two are M8 x75).

13
Figure 1-2
NOTE: Take care when removing motor from transmission box.
Take care not to damage the sealing surface for the O-ring in the housing! If only the
motor is removed, the released transmission opening is to be sealed in order to avoid that
dirt can get inside the transmission.
1.2.3 Disassembling and assembling of transmission box
It is not necessary to disassemble this part normally. If has to, please contact HELI
sales company.
1.3Assembling of transmission system
1.3.1 Assembling of travelling motor
Before assembling, clean the contacting face between transmission box and motor
with cleanser (for example loctite 706 or alcohol) then make it dry. Check if the contactor
is damaged, if there is slight damage, remove it with oil stone. Refer to figure 1-3.
Note: cleansers can not come into contact with the skin ,they must not be swallowed
and their vapors must not be inhaled. Always use protective gloves and goggles. If a
cleanser has been swallowed inadvertently, call medical help immediately. Pertinent
instructions of the manufacturer should be duly noted.
(1) Clean motor shaft (part1) and taper bore of drive pinion (part 2) carefully
(2) Insert woodruff key (part 3) into motor shaft and push drive pinion on.

14
(3) Screw a new stopping nut (part 4) on and tighten with socket wrench. Tightening
torque:55 Nm(M20 ×1,taper φ25);68 Nm(M14 ×1.5,taper φ20)
(4) Coat O-ring (part 5) slightly with transmission fluid and push it onto centering seat of
motor.
(5)Place the motor carefully on the transmission and join the gearings of motor pinion
and helical gear carefully.
Attention: Do not knock with the drive pinion against the helical gear while
installing the motor. This can cause knocking noise.
(6) Turn motor to coincide bore pattern of transmission with bore pattern of motor.
(7)Screw motor to transmission with three hexagon bolts.(parts1 and 2)(1×M8×50 and
2×M8×75) Tightening torque: 23 Nm.
Figure 1-3
1.3.2 Mounting the transmission unit to the truck frame
Check the frame surface for damage and irregularities. The maximum admissible
irregularity in the area of the transmission contour shall be no more than0.1mm.Screw
drive unit with 7 hexagon bolts M14 and shims to frame. Refer to figure 1-1.
1.3.3 Assembling of wheels
The axle is applicable to solid tyre.

15
(1) Clean mating surfaces on wheel shaft and wheel thoroughly and check if it is
damaged.
(2)The bore pattern in the rim should be in line with the bolts of the wheel shaft;
then push the wheel on.
(3) Install hub nuts and tighten them. The tightening torque of it is 140Nm.(see
Fig.1-4).
Figure 1-4
1.4 Replenishing with Transmission Fluid
When a truck has been used for 1000 hours or one year, (The accurate time is
according to the first reached time.) replace gear oil in differential and main reducer.
(1) Unscrew fluid filling plug (part 3) with sealing ring (part1), and let the gear oil
out completely. Before screw fluid filling plug again, remove the dust on the plug. It is
necessary to replace the sealing ring if it is damaged.
(2) Unscrew fluid filling plug (part 4) with sealing ring (part 2).
(3) Add gear oil to transmission box. During adding, air is not permitted to enter for
bubble may be produced in the transmission box.
(4) Fluid capacity approx. 0.45 liters (standard value).The exact oil amount is
determined by funnel.
(5) Gear oil model may be MOBIL ATF200 or ATF210 or ATF220;SHELL
DONAXTM or ATFDEXRONⅡD-21666 or DONAXTG PLUSD-22543 or DONAXTG

16
D-21126;ESSO TYPESUFFIXA or ATF D-21065 or ATF D-21611 or ATF D-22079.
(6)Screw fluid filling plug (part 1) with the sealing ring (part 2).Tightening torque:
22Nm. Refer to figure 1-5.
Figure 1-5

17
2. Brake system
2.1 General description
Brake system is made up of service brake and parking brake.
2.1.1Serivce brake
The service brake is made up of accelerating pedal, brake pedal, traction controller
and traction motor.
During travelling, releasing the accelerating pedal slowly or quickly can reduce
truck speed quickly and achieve brake effect. Brake effect in normal condition can be
realized.
During travelling, Step the brake pedal (2) can achieve brake effect flexibly.
Different brake effect can be achieved.
Note:
It is suggest for driver to getting familiar with the brake effect and functioning
without load.
2.1.2 Parking brake
Electromagnetic parking brake which is installed on traction motor shaft is applied
on three wheeled truck.
1) Automatic parking brake

18
When truck is braked or is stopped, electromagnetic parking brake is applied to lock
traction motor output shaft. And thus the truck is stopped with parking brake.
When truck is stopped on a slope, the truck keep stopping through electric method
ant then parking brake is started. And thus the truck is stopped with parking brake.
When operating direction switch and stepping on accelerating pedal at the same time,
the electromagnetic parking brake is loosed automatically and truck can be operated
normally.
2) Power-off parking brake
When key switch is turned off, emergency button is turned off or truck main
power is disconnected, electromagnetic parking brake starts automatically. And thus the
truck is stopped with parking brake.
Danger:
Except under emergency case, it is prohibited to start electromagnetic parking
brake through power-off parking brake. When electromagnetic parking brake is
applied, do not tow the truck.
This manual suits for next models
4
Table of contents
Other HELI Forklift manuals
Popular Forklift manuals by other brands

Xtreme
Xtreme XR1555 Operation and safety manual

Baoli
Baoli EP16-N01 Service maintenance manual
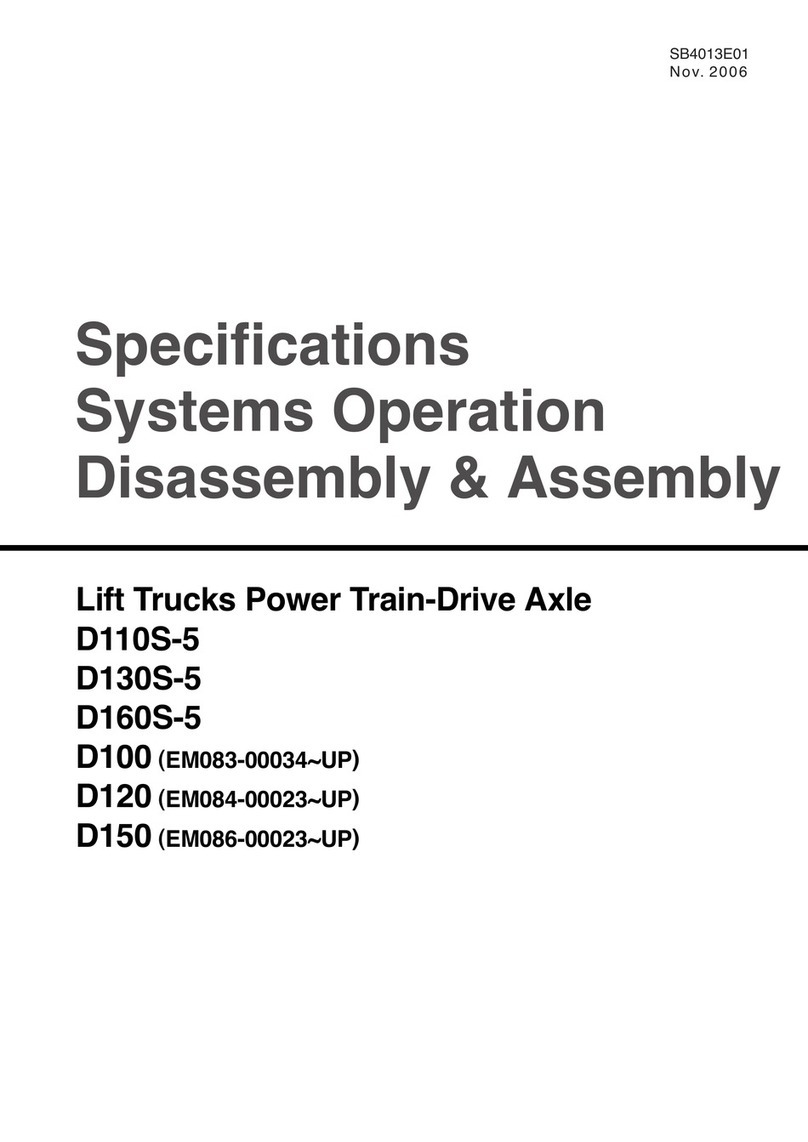
Doosan
Doosan D110S-5 with OCDB Specifications, Systems Operation, Disassembly & Assembly
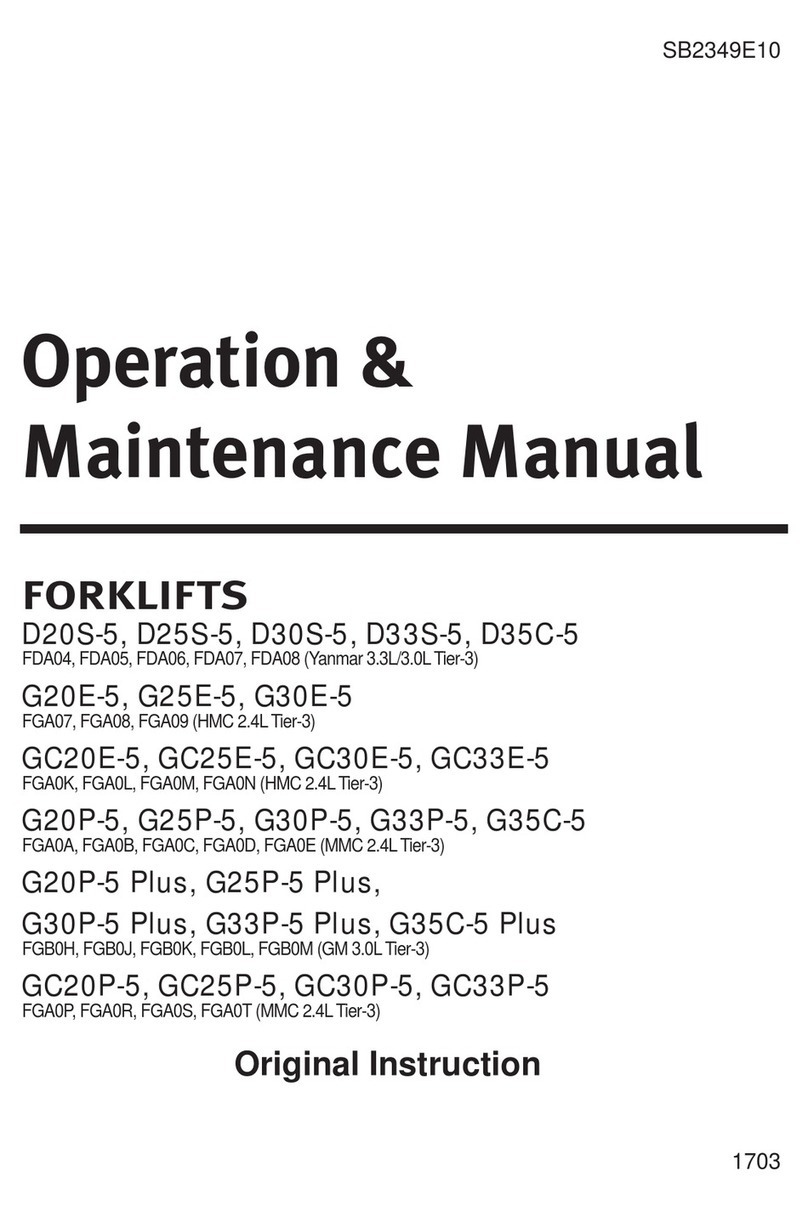
Doosan
Doosan D35C-5 FDA04 Operation & maintenance manual
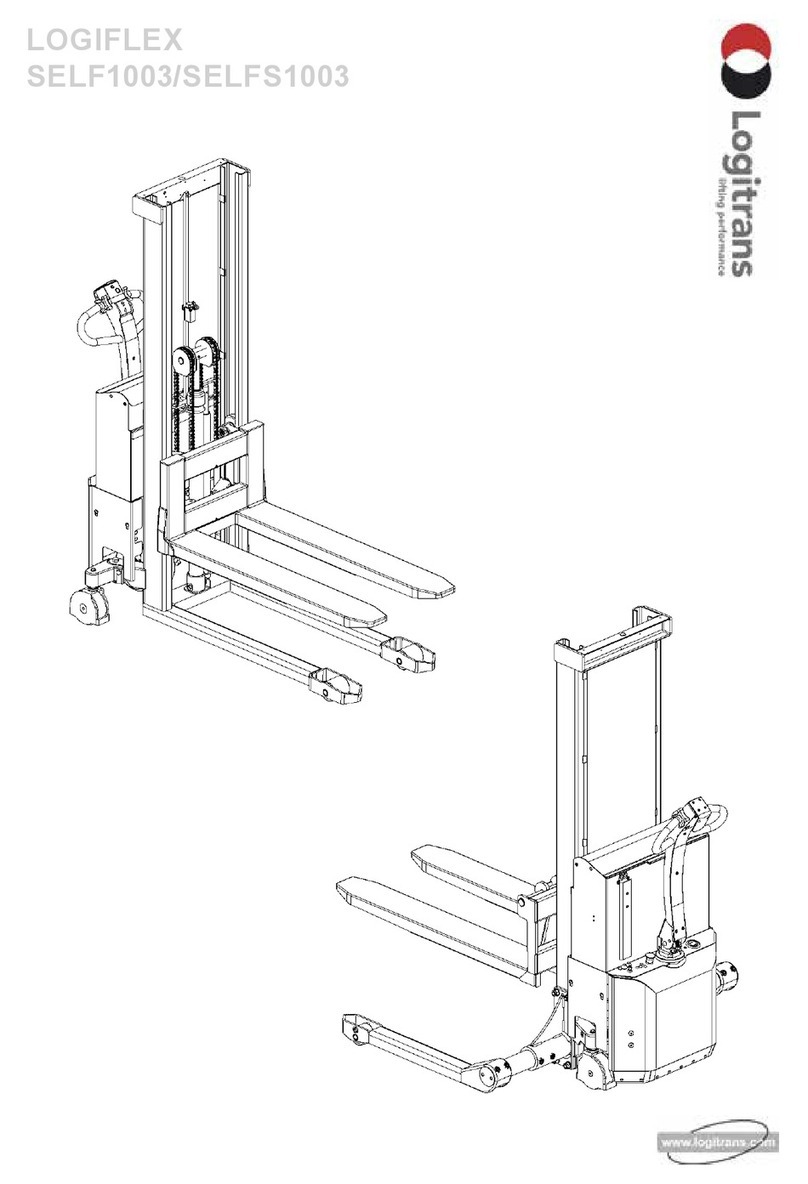
logitrans
logitrans LOGIFLEX SELF1003 manual

Hyster
Hyster B262 Service & repair manual