Helm Trend Series User manual

Helm Instrument Company, Inc.
361 West Dussel Drive
Maumee, Ohio 43537 USA
419/ 893-4356
Fax: 419/ 893-1371
www.helminstrument.com
Trend Series
TLG2300 / TLG4500 Loadgard
Operating Instructions
Force Measurement and Control Solutions

OPERATING INSTRUCTIONS TREND SERIES
ii
LIMITED WARRANTY
Helm Instrument Co., Inc. (”HELM”) hereby warrants that the instruments and
sensors (collectively the ”Product”) manufactured by it and sold to customer, are
free from defects in material and/or workmanship under normal use subject to the
following conditions. This warranty shall not apply to any Product which has been
subjected to improper installation, misuse, negligence, accident, alteration, where
service has been performed by other than an authorized Helm serviceman, o
r
where the serial number has been defaced or altered. This warranty shall extend
for the one (1) year period from date of shipment from our factory or authorized
dealer, provided that the product is returned, freight prepaid, to Helm within the
one (1) year warranty period within specific written authorization to perform
repairs. Helm’s obligations and the exclusive remedy of customer under this
warranty are limited to repairing or replacing any defective Product at no
additional charge and returning Product to customer freight paid. Repair parts
and replacement Products shall be furnished on an exchange basis and shall be
either new or reconditioned. All replaced parts and Products shall become the
property of Helm.
EXCEPT AS SPECIFICALLY STATED HEREIN, HELM MAKES NO
WARRANTIES EXPRESSED OF IMPLIED, OF THIS PRODUCT INCLUDING
BUT NO LIMITED TO WARRANTIES OF MERCHANTABILITY OR FITNESS
FOR A PARTICULAR PURPOSE, OR AS TO THE QUALITY, UTILITY OR
PERFORMANCE, ALL QF WHICH ARE HEREBY EXPRESSLY EXCLUDED. IN
NO EVENT SHALL THE LIABILITY OF HELM EXCEED THE PURCHASE
PRICE OF THIS PRODUCT. NOR SHALL HELM BE LIABLE FOR ANY
DAMAGES WHATSOEVER, INCLUDING BUT NOT LIMITED TO SPECIAL,
INDIRECT, INCIDENTAL OR CONSEQUENTIAL CHARGES, EXPENSE OR
DAMAGES, ARISING OUT OF THE USE OR INABILITY TO USE THIS
PRODUCT OR FOR ANY CLAIM BY ANY OTHER PARTY.
Should you have any questions concerning this Warranty, you may contact Helm
by writing or calling:
HELM INSTRUMENT COMPANY, INC.
CUSTOMER SERVICE
361 WEST DUSSEL DRIVE
MAUMEE, OHIO 43537
(41 9) 893-4356

OPERATING INSTRUCTIONS TREND SERIES
EXPLANATION OF SYMBOLS
~
Ω
Alternating Currrent
Earth (ground) TERMINAL
On (Supply)
Off (Supply)
Caution, risk of electric shock
Caution (refer to accompanying
documents)
iii

OPERATING INSTRUCTIONS TREND SERIES
Introduction........................................................................................................................................................ 1
Trend System Operation ................................................................................................................................... 1
The Strain Gain Transducer Operation ............................................................................................................. 1
Trend Loadgard Installation............................................................................................................................... 2
Enviromental Conditions ................................................................................................................................... 2
Strain Gain Installation And Wiring ................................................................................................................... 2
Sensor Wiring Connections............................................................................................................................... 2
Instrument Power And Relay Wiring ................................................................................................................. 3
Electrical Specifications..................................................................................................................................... 3
Replacement Fuses .......................................................................................................................................... 3
Instrument Calibration ....................................................................................................................................... 5
Preliminary Calibration Adjustment Procedures ............................................................................................... 6
Individual Channel Adjustments........................................................................................................................ 6
Manual Zero Adjust ........................................................................................................................................... 6
Gain Adjust........................................................................................................................................................ 7
Meter Calibrate Switches .................................................................................................................................. 8
Setting Meter Calibrate Switches On Two Channel Systems ........................................................................... 9
Alarm Set Procedures ..................................................................................................................................... 10
Setting Capacity Alarm.................................................................................................................................... 11
Setting High - Low Tolerance Limits ............................................................................................................... 12
Establishing Optimum Tolerance Settings ...................................................................................................... 12
Job Data Control (Jdc) .................................................................................................................................... 13
Initial Storing Of Capacity And Tolerance Settings ......................................................................................... 13
Storing Of Target Loads .................................................................................................................................. 13
Testing For Open Job Number........................................................................................................................ 14
Calling Stored Job Data For Die Setup ........................................................................................................... 14
Front Panel Controls - Operating Instructions................................................................................................. 15
Three Position Function Selector .................................................................................................................... 15
Setup (Clear) Keyswitch Position.................................................................................................................... 15
Monitor Parts Keyswitch Positions .................................................................................................................. 16
Alarm Set Status ............................................................................................................................................. 17
Digital Meter Display ....................................................................................................................................... 17
Trend Display-Quality Window........................................................................................................................ 18
Recorder Output Jacks.................................................................................................................................... 19
Front Panel Push Buttons ............................................................................................................................... 20
Alarm Reset ................................................................................................................................................. 20
Capacity Alarms........................................................................................................................................... 20
Strokes Per Minute ...................................................................................................................................... 20
Tolerance Alarms......................................................................................................................................... 20
Reverse Load .............................................................................................................................................. 20
Target Load ................................................................................................................................................. 20
Cleaning .......................................................................................................................................................... 21
Computer Interface And Filter Card Wiring .......................................................................................Appendix A
a

OPERATING INSTRUCTIONS TREND SERIES
INTRODUCTION
You have just purchased the most advanced load monitoring system available. In addition to this system,
HELM INSTRUMENT CO., INC. manufactures a complete line of load monitoring control systems for use
on metal stamping, forging, compaction and assembly presses; cold forming, cold heading, injection molding
and die cast machines.
Standard or custom transducers and load cells are available for in-die monitoring or transfer or progressive
tooling. Easy to use software systems designed for your specific plantwide SPC programs are also
available.
At HELM, quality is inherent not only in the design of our products but in the attitudes of our employees as
well. We're working together to give you the best. After all, that's what our business is all about - providing
innovative instrumentation to help make your manufacturing process more productive and your operation
more effective.
TREND SYSTEM OPERATION
The HELM TREND LOADGARD control system provides protection for the die, the product and the machine
with minimal operator involvement. The Loadgard takes a sample of the forming force of an ideal part,
stores this level in memory and compares each subsequent force level against the ideal.
In addition to capacity alarms for overload protection, the TREND Loadgard features high and low tolerance
limits, set automatically for each channel based on a pre-established setting.
Digital meters display load, machine speed, alarm settings and capacity alarms. Machine stop is initiated
when an off tolerance part is produced.
THE STRAIN GAIN TRANSDUCER OPERATION
The basic function of the HT-400 Strain Gain is to detect the amount of the deflection imposed on the press
as parts are being formed. All Strain Gain sensors are matched to within 1% and therefore can be replaced
without re-calibration of the machine.
The HT-400 Strain Gain sensors are mounted to strategic high stress areas of the machine frame. Signals
from these sensors are routed to the TREND Loadgard for processing. The HT-400 is capable of measuring
either a tension or compression signal.
1

OPERATING INSTRUCTIONS TREND SERIES
INSTALLATION GUIDELINES
TREND LOADGARD INSTALLATION
WARNING
If this unit is modified in a manner not specified by the manufacturer, protection provided may be impaired.
Repair or calibration of this equipment is to be done by authorized personnel only. This unit contains no
serviceable parts other than those outlined in this manual. Return unit to manufacturer for repair.
For purposes of safety, this unit is to be permanently installed. Electrical lines will be housed in conduit so
that wiring is not subject to mechanical stress. A means of electrical disconnect (switch or circuit breaker)
shall be included in the permanent power installation. This disconnect device will be in close proximity to the
equipment and within easy reach of the operator. The device will be clearly marked as the disconnect for
the equipment (ref. Drawing T-2227 Appendix A).
For best results, mount the TREND Loadgard at eye level and within operators' reach. Use the supplied
rubber shock mounts to isolate the unit from vibration. Care should be taken to insure that the instrument
chassis ground Ωis the same potential as the machine ground. See Mounting Detail Illustration in
Appendix A.
ENVIROMENTAL CONDITIONS
This unit is designed for indoor use only. Operating temperature range is from 5ºC up to 55ºC.
STRAIN GAIN INSTALLATION AND WIRING
Specific sensor location and mounting instructions are described in the “Installing Strain Gain Transducers”
manual. Refer to this manual for proper location and installation. Sensor nominal resistance values should
check out in accordance with HELM drawing number T-2344-51 in Appendix A. For proper wiring, use
separate conduit or sealtite for transducer cables and avoid running these cables with any press control or
high power motor circuits. Transducer cables should never be run near high voltage (220VAC, 440VAC)
circuits.
SENSOR WIRING CONNECTIONS
The Sensor Terminal Strips are located inside the box, above the circuit board card rack.
NOTE: Always route power and sensor cables through proper holes as designated inside the
LOADGARD enclosure.
TENSION COMPRESSION
+G (gage positive) green black
-G (gage negative) black green
-S (signal negative) red red
(shield) shield shield
+S (signal positive) white white
2

OPERATING INSTRUCTIONS TREND SERIES
INSTRUMENT POWER AND RELAY WIRING
Trend Loadgard supply wiring connections shall be made with 14 ga. THHN wire or equivalent.
Electrical Specifications
Unit marked for 120V~ operation 120V~ ±10%
50-60 Hz 500 mA Max.
Unit marked for 220V~ operation 220V~ ±10%
50-60 Hz 250 mA Max.
Installation Class III
Replacement Fuses
Replace fuses with main power OFF! (o)
Replace fuses with "TT" time delay fuses of specified rating only!
TLG-4500 models marked for 120V~ operation require a .5A 20mm x 5mm type TT fuse.
TLG-4500 models marked for 220V~ operation require a .25A 20mm x 5mm type TT fuse.
3

OPERATING INSTRUCTIONS TREND SERIES
A mechanical relay is provided to activate machine stop when an alarm condition occurs. This relay is wired
“fail-safe” and will pass current through the normally closed and common contacts when the instrument is
turned on and no alarms are tripped. Current rating for these contacts is 10 amps at 120VAC. Cam switch
connections are supplied, if applicable.
CARD RACK - Channel Boards
The steel cabinet (card rack) inside the instrument holds all the circuit boards. Slot #1 is reserved for the
optional computer interface card. Slot #2 contains the microprocessor board that controls all instrument
logic. Slot #3 is open.
Slots #4 through 7 are reserved for channel boards. Refer to the illustrations below for the proper location of
each channel board in your instrument(s).
Channel boards are interchangeable. Use the jumper plugs on the individual
channel boards for setting the proper channel board number.
NOTE: Jumpers are factory set prior to shipment. Adjust this jumper only if
you switch channel board locations.
4

OPERATING INSTRUCTIONS TREND SERIES
INSTRUMENT CALIBRATION
This section details calibration procedures. If this system has been calibrated by a HELM Field Service
Engineer or by the machine manufacturer, the calibration numbers will be noted on a tag inside the
instrument. Once calibrated, it is not necessary to re-calibrate unless the machine is moved, dismantled or
otherwise structurally changed. If you have any questions or need a HELM Field Engineer for calibration,
please contact our Field Service Department at 419-893-4356.
The illustration below details the locations of switches and potentiometers used during calibration.
5

OPERATING INSTRUCTIONS TREND SERIES
PRELIMINARY CALIBRATION ADJUSTMENT PROCEDURES
1. Turn function keyswitch to SETUP position.
2. Open enclosure door, turn power on.
3. Set MONITOR/CALIBRATE switch, located
on inside of door, to the CALIBRATE position.
INDIVIDUAL CHANNEL ADJUSTMENTS
MANUAL ZERO ADJUST
1. Push AUTO ZERO switch to the OFF
(back) position.
2. Pull CALIBRATION switch to the OFF
(forward) position.
3. Adjust the ZERO BALANCE
The zero balance (BALANCE ADJUST) controls are the small
multi-turn potentiometers at the extreme right of each channel
board.
Watch the outside meter and turn the BALANCE ADJUST
control of the first channel board until the meter displays all
zeros. Repeat for all channels.
NOTE: On models TLG-4100 & TLG-2100, push LEFT or RIGHT DISPLAY button to display individual
channel readings.
6

OPERATING INSTRUCTIONS TREND SERIES
GAIN ADJUST
The GAIN ADJUST control is a small multi-turn control located on the extreme left of each channel board.
This control is used to adjust the instrument to display the proper CAL (calibration) number on the digital
meter(s).
1. Push CALIBRATION SWITCH to the ON (back)
position. This switch puts the CAL resistor
(simulated load) across the sensor for that channel.
2. Set the GAIN ADJUSTMENT
If the press has been calibrated, use the CAL
numbers that are recorded for each channel. If the
press has not been calibrated, use 50 as a
temporary cal number.
Watch the digital meter and turn the GAIN ADJUST
control until the meter displays the correct CAL
number. Repeat for all channels.
3. Turn AUTO ZERO on by moving the AUTO
ZERO switch to the ON (forward) position. Pull
CALIBRATION switch to the OFF (forward) position
to remove simulated load.
4. Set MONITOR/CALIBRATE switch back to
“MONITOR” position.
During normal operation, Auto Zero and Calibration switches must be in the forward position.
Monitor/Calibrate switch must be in Monitor position.
7

OPERATING INSTRUCTIONS TREND SERIES
METER CALIBRATE SWITCHES
These switches, located on the microprocessor board (slot #2), are used to set meter scale based on rated
machine capacity. Pull the microprocessor board out of the card rack for this adjustment. Make sure power
to the instrument is OFF before pulling any boards from the rack.
SETTING METER CALIBRATE SWITCHES ON FOUR CHANNEL SYSTEMS
• FOR MACHINES UP TO AND INCLUDING 500 TON TOTAL CAPACITY
Put the METER RANGE selector to the LOW position. Calculate the capacity of one corner by dividing the
total machine capacity by the number of channels (4).
Set the METER CALIBRATE switches to the capacity of one corner using the red switches labeled SW1,
SW2, SW3.
• FOR MACHINES OVER 500 TONS TOTAL CAPACITY
PRESS SWITCH PRESS SWITCH PRESS SWITCH
CAPACITY SETTING CAPACITY SETTING CAPACITY SETTING
550 014 900 023 3500 088
600 015 950 024 4000 100
650 016 1000 025 4500 113
700 018 1500 038 5000 125
750 019 2000 050 5500 138
800 020 2500 063 6000 150
850 021 3000 075 6500 162
8

OPERATING INSTRUCTIONS TREND SERIES
METER CALIBRATE SWITCHES (cont.)
SETTING METER CALIBRATE SWITCHES ON TWO CHANNEL SYSTEMS
• FOR MACHINES UP TO AND INCLUDING 250 TONS TOTAL CAPACITY
Put the METER RANGE selector to the LOW position. Calculate the capacity of one side by dividing the
total machine capacity by the number of channels (2).
Set the METER CALIBRATE switches to the capacity of one side using red switches labeled SW1, SW2 and
SW3.
EXAMPLE: For a 100 ton machine rated at 50 tons per side, set switches to 050 by setting left switch
(SW1) to 0, middle switch (SW2) to 5 and right switch (SW3) to 0. Re-install board.
• FOR PRESS OVER 250 TONS TOTAL CAPACITY
Put the METER RANGE selector to the HIGH position. Set METER CALIBRATE switches based on the
following table.
PRESS SWITCH PRESS SWITCH PRESS SWITCH
CAPACITY SETTING CAPACITY SETTING CAPACITY SETTING
300 015 600 030 900 045
350 018 650 033 950 048
400 020 700 035 1000 050
450 023 750 038 1500 075
500 025 800 040 2000 100
550 028 850 043 2500 125
3000 150
9

OPERATING INSTRUCTIONS TREND SERIES
INSIDE CONTROLS
ALARM SET PROCEDURES
Capacity and tolerance alarm adjustments are located on the inside door panel. Capacity alarms provide
press overload protection. Tolerance alarms provide tooling and die protection as well as providing part
quality assurance.
10

OPERATING INSTRUCTIONS TREND SERIES
SETTING CAPACITY ALARM
1. Turn Function Selector to SETUP position.
2. Open enclosure door and locate slide
switches on inside door.
3. Slide top switch on inner door to CALIBRATE
position (right) and center switch marked CAPACITY
ALARMS to the right.
4. Unlock Capacity Alarm control knob by turning the locking ring counter clockwise.
5. Calculate capacity alarm for each channel by dividing total press capacity by the number of channels on
the instrument. Divide by four (4) for four channel systems. Divide by two (2) for two channel systems.
6. Watch the digital meter(s) and adjust capacity for each channel. Models 2100 & 4100 use the LEFT or
RIGHT DISPLAY button for displaying individual channel settings on the digital meter.
7. Turn locking ring clockwise to lock Capacity Alarm sets.
8. Return top and center slide switches to left position. For normal operation, these two slide switches must
be in the left position.
EXAMPLE: For a press with a four channel system and a total rated capacity of 500 tons, calculate the per
channel capacity. Divide press capacity by the number of channels (500/4 = 125 per corner). Turn the
control to make the meter display 125 tons.
11

OPERATING INSTRUCTIONS TREND SERIES
SETTING HIGH - LOW TOLERANCE LIMITS
Every TREND system features tolerance alarms which are used to establish a “quality window” that the
process will operate within. These alarms are set as a percentage of the forming force and automatically
adjusted each time a sample is taken or a new job is started.
The ability to establish alarms in percent eliminates the need to re-adjust settings for each job change. For
example, with high and low tolerance settings of 10%, a 100 ton job has alarms automatically set at 110 tons
high and 90 tons low. A 40 ton job has alarms automatically set at 44 tons high and 36 tons low.
There are two switches for each channel of monitoring; one to establish the LOW alarm setting and one for
the HIGH alarm setting. Each switch is selectable from 5% to 45%, in increments of 5%. There is also a
position to turn the alarms off.
A tolerance setting of plus 5% on an individual channel will cause an alarm when the load level increases
5% above the sampled load.
A tolerance setting of minus 45% on a particular channel will cause an alarm when the load decreases 45%
from the sampled load.
ESTABLISHING OPTIMUM TOLERANCE SETTINGS
A good baseline starting point is 25%, high and low. With the instrument in Monitor Parts mode, watch the
trend lights during a production run. Begin lowering tolerance percents until the center green (GOOD) LED
starts flashing one LED up and down from center.
12

OPERATING INSTRUCTIONS TREND SERIES
JOB DATA CONTROL (JDC)
The JED feature provides memory storage of up to 100 different job numbers per LOADGARD. The
following data is stored for each job:
• Capacity alarm settings
• Tolerance alarm settings
• Target (optimum) load values
INITIAL STORING OF CAPACITY AND TOLERANCE SETTINGS
1. Put JDC switch in manual mode.
2. Set selector switches to desired job
number (0-99).
3. Check capacity and tolerance settings;
readjust if necessary.
4. Press STORE button
5. Green LED on JDC panel will flash, indicating data is being stored.
6. To over-ride and store new settings, follow steps 1-5.
STORING OF TARGET LOADS
1. Put JDC switch in Auto mode.
2. Turn front panel keyswitch to monitor parts mode.
3. TARGET values are automatically stored during initial setup when front panel keyswitch is
turned to Monitor Parts mode. The TARGET value is current peak tonnage as displayed on
digital meters.
4. To over-ride and store new TARGET values, put JDC switch in Auto Mode and press store
button. Peak loads as displayed on the digital meters will be stored as new target loads.
5. Green LED will flash, indicating data is being stored.
Capacity and Tolerance settings are stored in MANUAL mode. Target loads are stored in AUTO
mode.
13

OPERATING INSTRUCTIONS TREND SERIES
JOB DATA CONTROL (cont.)
TESTING FOR OPEN JOB NUMBER
1. Put JDC switch in AUTO mode.
2. Select job number.
3. Yellow LED will flash if job number is available.
CALLING STORED JOB DATA FOR DIE SETUP
1. Select job number to be recalled.
2. Put JDC switch in auto mode.
3. Capacity and Tolerance settings are activated for first hit protection.
4. Press Target Load button on front panel to display target values on each channel.
Job number is displayed on center meter.
5. With front panel function selector switch in SETUP mode, Trend columns are used to indicate if
the current peak load value is above or below the stored target value.
14

OPERATING INSTRUCTIONS TREND SERIES
FRONT PANEL CONTROLS - OPERATING INSTRUCTIONS
THREE POSITION FUNCTION SELECTOR
• A position marked SETUP (Clear)
• A monitoring position marked MONITOR PARTS (RESET BUTTON NOT ACTIVE)
• A monitoring position marked MONITOR PARTS (RESET BUTTON ACTIVE)
SETUP (CLEAR) KEYSWITCH POSITION
Use this position for machine and die set up. The following conditions are present in SETUP mode:
• Machine capacity alarms are active. Press button labeled “CAPACITY ALARMS” to display
• alarm settings on each channel.
• The alarm RESET button will initiate a PEAK reset.
• The REVERSE LOAD and strokes per minute buttons are not active.
• The TREND display and the TREND alarms are turned OFF.
• Parts counter is not updated.
NOTE: Always power on the instrument in the SETUP position. If the instrument is powered on in either
MONITOR PARTS position, the machine stop relay will prevent the machine from running and the digital
display will flash zeroes. Turn the function switch to SETUP to reset machine stop relay.
15

OPERATING INSTRUCTIONS TREND SERIES
MONITOR PARTS KEYSWITCH POSITIONS
During production, the keyswitch should be in one of these MONITOR PARTS positions.
Once the machine is set up and producing good parts, turn the switch to one of these positions. The
instrument will take a sample of the forming loads and store this sample in memory. Each subsequent hit is
compared to this sample. The TREND lights will display any changes in the forming loads.
Tolerance alarms are automatically adjusted when this sample is taken. Any load change that meets or
exceeds the tolerance settings will cause an alarm condition and activate the machine stop relay.
In Monitor Parts/Reset Not Active, the ALARM RESET button is inactive and the keyswitch must be turned
to Reset Active before alarms can be reset.
The following conditions are present in MONITOR PARTS position:
• Capacity alarms are active.
• The TREND display and the TREND alarms on ON.
• All front panel switches are active.
NOTE: The sample loads are erased whenever the function switch is turned to the SETUP position. To
stop the machine for a break, leave the instrument in MONITOR PARTS-RESET ACTIVE position. When
restarting the machine, push ALARM RESET button to clear any alarms.
16
This manual suits for next models
2
Table of contents
Other Helm Control System manuals
Popular Control System manuals by other brands
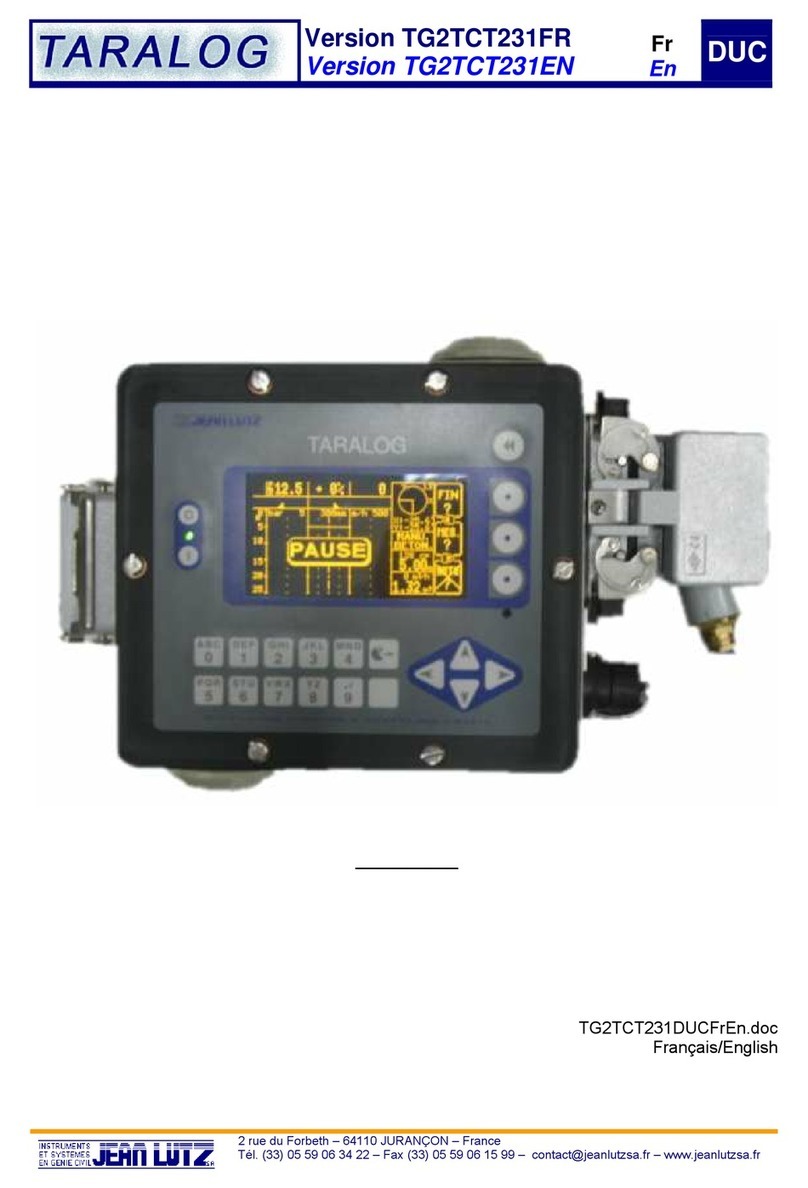
JEAN LUTZ
JEAN LUTZ TARALOG instruction manual
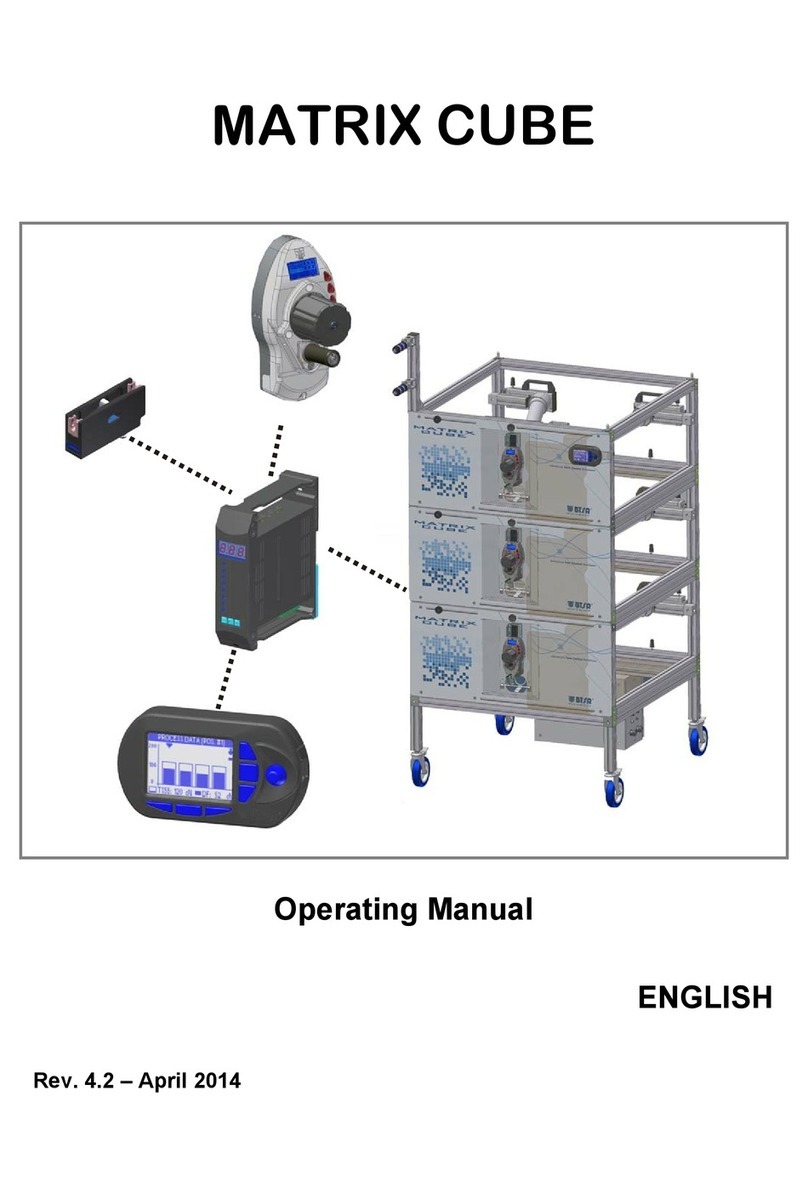
btsr
btsr MATRIX CUBE operating manual
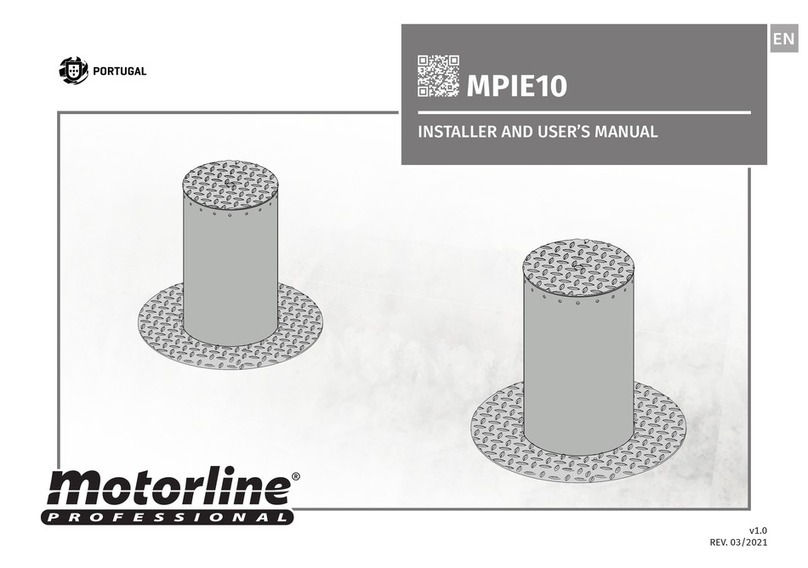
Motorline professional
Motorline professional MPIE10 installer and user manual
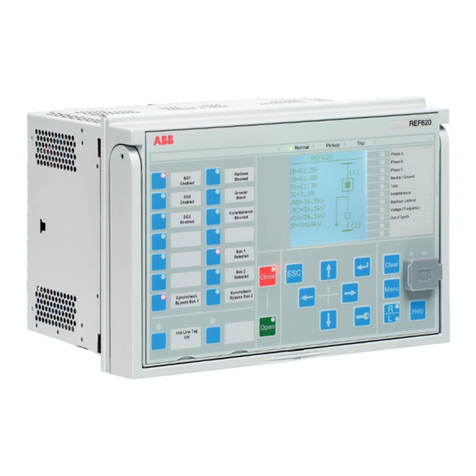
ABB
ABB 620 Series ANSI installation manual
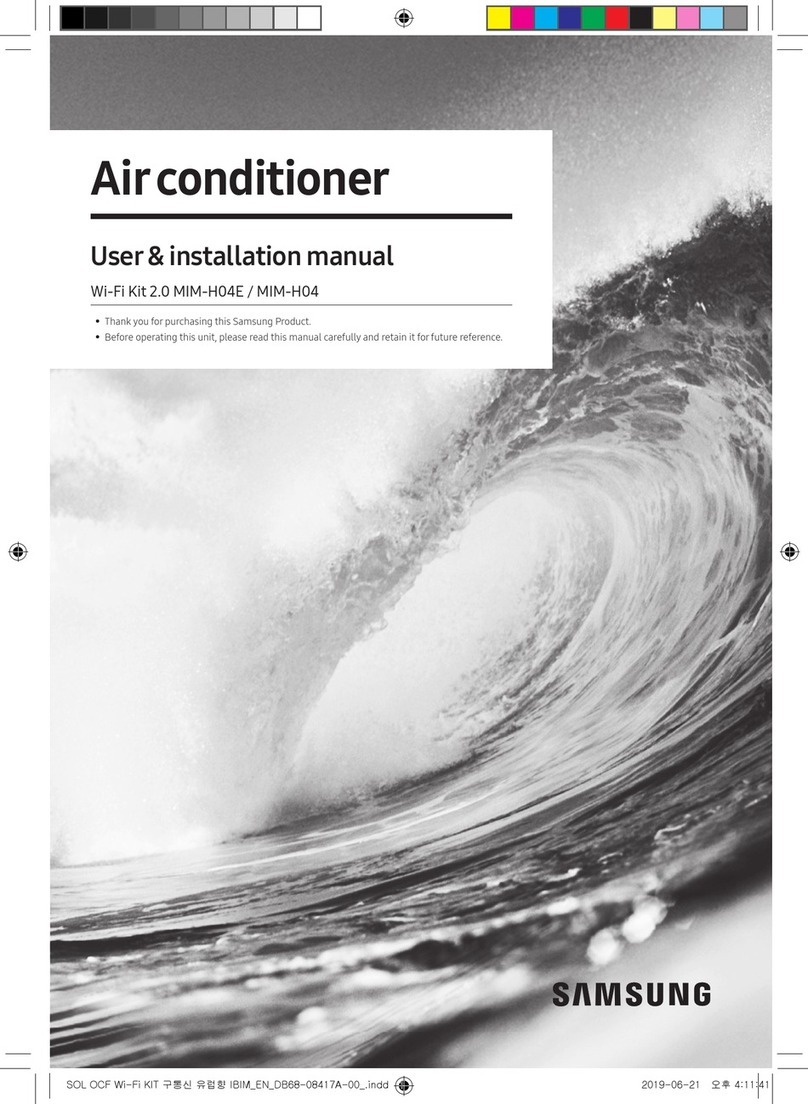
Samsung
Samsung Wi-Fi Kit 2.0 User & installation manual
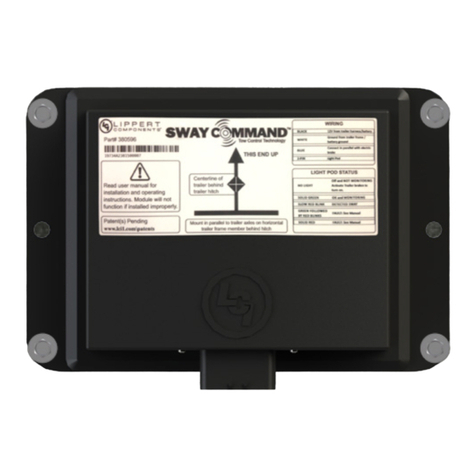
Lippert Components
Lippert Components Sway Command Install manual