Heyl Testomat Modul TH Operating instructions

1
Testomat®Modul TH
Service Instructions
These operating instructions are the copyrighted property of Heyl Analysen-
technik GmbH & Co. KG.
It is intended for customer service and should only be used by authorised ser-
vice staff.
No part of this publication may be reproduced or transmitted in any form or by
any means to a third party, in particular to our competitors, without express
prior permission of Heyl Analysentechnik GmbH & Co. KG.

Contents
2
Contents
Contents...............................................................................................2
Important safety information.............................................................3
Qualification of the staff ........................................................................3
Warning notices in these instructions ...................................................3
Further documents................................................................................4
General instructions...........................................................................4
Prior to carrying out maintenance work ................................................6
Permissible tools...................................................................................6
Carrying out maintenance..................................................................7
Removing and installing the measuring chamber holder......................7
Cleaning of clogged solenoid valves ....................................................8
Additional cleaning instructions...........................................................10
Repairing or replacing the dosing pump.............................................11
Replacing the dosing pump valves.....................................................12
Checking the dosing pump .................................................................12
Replacing the backup battery .............................................................13
Replacing the fuse ..............................................................................14
Troubleshooting................................................................................15
Error message “36 Fault analysis”......................................................15
Error message “38 Water low” ............................................................17
Error message “„33 Fault optics LED1” and „27 Fault optics LED2” ..18
Error message “34 Fault turbid”..........................................................18
Error due to defective hardware .........................................................18
Spare parts for Testomat®Modul TH ..............................................19
Component positions.......................................................................20
Checklist Testomat®Modul.................................................................24

Important safety information
3
Important safety information
Please read the operating instructions and maintenance instruc-
tions carefully and completely prior to carrying out maintenance
work at Testomat instruments.
Observe the warning notices in these maintenance instructions
and the operating instructions of the respective instrument.
Always adhere to hazard warnings and safety tips when using
reagents, chemicals and cleaning agents. Please adhere to the re-
spective safety data sheet! Download the safety data sheets for
the supplied reagents at http://www.heylanalysis.de.
Qualification of the staff
Maintenance work requires fundamental electrical and process engi-
neering knowledge as well as knowledge of the respective technical
terms. Assembly and commissioning should therefore only be carried
out by a specialist or by an authorised individual supervised by a
specialist.
A specialist is someone who due to his/her technical training, know-
how and experience as well as knowledge of relevant regulations can
assess assigned tasks, recognise potential hazards and ensure ap-
propriate safety measures. A specialist should always adhere to the
relevant technical regulations.
Warning notices in these instructions
The warning notices in these instructions warn the user about poten-
tial dangers to individuals and property resulting from incorrect han-
dling of the instrument. The warning notices are structured as follows:
Description of the type or source of danger
Description of the consequences resulting from non-observance
Preventive measures. Always adhere to these preventive
measures.
“DANGER” indicates an immediate hazardous situation which, if not
avoided, will result in death or serious injury.
“WARNING” indicates a potentially hazardous situation which, if not
avoided, could result in death or serious injury.
“CAUTION” indicates a potentially hazardous situation which, if not
avoided, could result in minor or moderate injuries or property dam-
age.
“NOTE” indicates important information. If this information is not ob-
served, it may result in an undesirable result or state.
DANGER
!
WARNING
!
CAUTION
!
SIGNAL WORD!
NOTE

General instructions
4
Further documents
Testomat instruments are plant components. Therefore, always ob-
serve the documentation of the plant manufacturer.
General instructions
Regular maintenance is necessary to ensure trouble-free operation of
the Testomat instrument. Regular visual inspections also increase
operational reliability. Also refer to the notes in the operating instruc-
tions!
Fix errors by yourself.
Experience has shown that many errors that occur in day-to-day op-
erations you can fix by yourself.
This ensures that the instrument is soon working again. In this
maintenance manual you will find possible causes of malfunctions
and helpful hints for their elimination.
Overview of maintenance work to be executed
The maintenance intervals may vary depending on the water and
pipeline quality.
Maintenance work
Quarterly
Semi-
annually
Annually
Biennially /
Triennially
Cleaning sight-glass windows
X
Cleaning measuring chamber / measur-
ing chamber holder
X
Cleaning the receiver optics
X
Cleaning the controller/filter housing
X
Cleaning the waste water line
X
Checking the dosing pump incl. suction
and pressure hoses
X
Electrical and hydraulic connections
X
Renewing the sealing kit (40124) and
sight-glass windows
X
Recommendation:
Allow the manufacturer to overhaul the
dosing pump
X
NOTE

General instructions
5
•Clean the measuring chamber at regular intervals (approx. every 6
months) and, if possible, replace the two seals of the measuring
chamber holder and the sight-glass windows.
•If the water has high iron content, cleaning might be necessary
more often.
•Only use a dry, lint-free cloth for cleaning.
•To carry out maintenance work after the error message “35 Fault
soiling” or “33. Fault optics”, always confirm the error message with
the Alarm function key.
•If maintenance is carried out after an instrument maintenance
message (maintenance interval), maintenance must be confirmed
with the Alarm function key.
•Wait at least 5 seconds before switching the instrument on and
then off again at the main switch.
•A defective device, regardless of the guarantee period, can be
serviced only when the device is dismantled and the error is de-
scribed. Please also inform us of the indicator type currently in use,
the batch number and the measured medium. Make no changes or
modifications to the device that go beyond the scope of use speci-
fied in these instructions. Doing so will void the warranty. This ap-
plies particularly to the measuring chamber holder, the seal of
which must remain undamaged. If you send the device in for re-
pair, please completely empty the measuring chamber and remove
the indicator bottle and the drain funnel.
Before dismantling, the type of error must be noted (error number,
error effect, log file of the SD card).
•Once a protective device has been triggered (safety fuse), initially
try resolving the cause of error (e.g. by replacing a defective
valve), before reactivating the protective device. Frequent trigger-
ing always signifies an error, which under certain circumstances
may also damage the device.

General instructions
6
Prior to carrying out maintenance work
Carry out a visual inspection of the instrument:
•Is the cover of the unit (if present) always carefully closed?
•Is the instrument heavily soiled?
•Is there air inside the dosing hoses?
•Is the DosiClip®pump properly vented?
•Are the hose connections of the dosing pump free of leaks?
•Has the use-by date of the indicator expired?
Always make sure that the sight-glass windows are clean before in-
serting a new indicator bottle.
Cleaning agents
Never use organic solvents to clean the measuring chamber or
other plastic parts!
Use an acidic cleaning agent for cleaning.
Please observe the safety regulations when handling cleaning
agents!
Permissible tools
Only use suitable tools for the work described, e.g., our tool set
T2000 (Art. No. 40138) and our maintenance case T2000 (Art. No.
270338) with all necessary spare parts for regular maintenance.
Content of the tool kit T2000 (Art. no. 40138)
Size
Application
Art. no.
Torx, TX 20x100
Measuring chamber, snap-on installa-
tion
30991
Torx, TX 10x80
Measuring chamber holder
30992
Torx, TX 8x60
Display circuit board , measuring
chamber holder
30993
CAUTION
!

Carrying out maintenance
7
Carrying out maintenance
This service manual describes maintenance work that goes beyond
the regular maintenance work described in the “Maintenance and
repairs” chapter of the operating manual.
see Operating manual
- Cleaning the measuring chamber and the viewing
window Page 41
- Cleaning the filter housing Page 41
- Changing an empty indicator bottle Page 42
- Firmware update Page 43
Removing and installing the measuring chamber
holder
(Required tool: Torx 10, Tensioning and release aid, for John
Guest connector, John Guest ICLT/2)
Switch off the device and disconnect it from the power supply.
Stop the water supply to the instrument.
Drain the measuring chamber, if water has remained in it.
Unhook the toggle type fastener.
Tilt the measuring chamber upwards and remove it.
Remove the stirring bar.
Loosen the pressure hose .
Loosen the four fastening screws of the measuring chamber holder
.
Loosen the valve block from the measuring chamber holder
(two fastening screws).
Disconnect the plug from the flexible cable connection on the
base circuit board by pressing together and raising the two lateral
levers.
Unplug the flexible cable.
Remove the measuring chamber holder from the front. To achieve
this, remove the drain pipe from the hose connection of the
measuring chamber holder (see fig. push locking ring upwards).
Install the new measuring chamber holder in reverse order.
Ensure that the plug is locked into position after inserting the flexi-
ble cable connection.
Push locking
ring upwards

Carrying out maintenance
8
Cleaning of clogged solenoid valves
When the solenoid valve is clogged with impurities, the measuring
chamber is not properly emptied. In this case, the solenoid valve can
be carefully cleaned.
For dismantling all Testomat devices, please proceed as follows:
Switch off the device and disconnect it from the power supply.
Shut off the water supply in the supply line to the Testomat device.
Open the cover if present.
Loosen the hose from the plug connector
Loosen the 4 cable connectors from the coils of the solenoid
valve.
Loosen the 2 screws that hold the solenoid valve in the housing.
(Torx 10)
Remove the solenoid valve forwards out of the housing.
To clean the solenoid valve, disassemble each side separately as
follows:
Start with the outlet side. On this side, the membrane of the valve
core may get stuck in the drill hole when the valve is contaminated.
The problem can be resolved mostly by loosening the membrane and
cleaning the drill hole.
Unscrew the knurled nut
Pull off the coil
Unscrew the anchor sleeve (SW 13)
Carefully extract the valve core, also called the anchor. Ensure
that the spring is not released.
If the membrane does not come loose and the anchor cannot be
extracted, blow compressed air into the hole so that the membrane
comes loose.
When you blow compressed air through the valve and the valve
block, make sure that the O-ring is not lost from the drill hole to
the measuring chamber. Therefore, remove the O-ring before eve-
ry cleaning operation.
Blow in compressed air here

Carrying out maintenance
9
When microbial contamination or deposits are present, clean the
valve chamber and the parts of the valve with a small brush
(e.g. from our cleaning brush set, Art. No. 32287).
Carry out assembly by following the steps for dismantling of the
same in reverse.
Make sure that you place the coil the right way round on to the an-
chor sleeve, as shown in the image above. The coil can be easily
placed on to the anchor sleeve in only one direction.
Now disassemble the inlet side in the same way, as described for
the outlet side.
Clean the inlet side, as described above.
After cleaning, reassemble all parts.
Risk of interchanging parts
Do not interchange the inlet and outlet sides when mounting! The
springs are not identical. The solenoid valve no longer works when it
is incorrectly assembled.
Do not interchange the cable connectors of the inlet and outlet sides
when reconnecting (inlet: yellow-green cable; outlet: brown-white
cable). If necessary, take a photo prior to removal.
Ensure that the drill hole appears in the solenoid valve to the
measuring chamber.
Do not attempt to forcibly install the solenoid valve. If there are prob-
lems, check whether the solenoid valve has been properly assembled
and screw on to the measuring chamber using the correct side.
Reconstruct the solenoid valve by following the steps for disman-
tling of the same in reverse.
NOTE

Carrying out maintenance
10
Additional cleaning instructions
Procedure in the event of corrosion:
Temporarily place the tie rod in a metal cleaning solution (no longer
than 5 minutes, depending on the concentration). Subsequently, neu-
tralise with plenty of clear water.
Under no circumstances must sandpaper be used!
It is far better to use metal-free cleaning fleece, e.g. from the compa-
ny Rothenberger
Procedure in the event of crystalline deposits:
Place the tie rod in either vinegar essence, pre-dissolved granulated
citric acid, or some limescale remover. In this case also, allow it to
take effect for no longer than 5 minutes. Subsequently, neutralise
with plenty of clear water, and, where appropriate, rework using met-
al-free cleaning fleece.
Prior to assembly:
Please wet the parts in direct contact with the medium with a fine
water-repellent silicone grease or spray, e.g. Baysilone
It is resistant to water vapour, sulphur dioxide, dilute acids and alka-
lis, and also is physiologically indifferent, skin-friendly and has excel-
lent dielectric properties.
When all of these instructions are implemented, older valves will also
work again properly for a long time.

Carrying out maintenance
11
Repairing or replacing the dosing pump
Maintenance rate
The dosing pump DOSIClip®is a high-precision piston dosing pump,
which makes up to 400 000 pump strokes per year depending on the
settings (a measurement all 10 minutes x 4 pump strokes every day).
To ensure proper operation for many years, we recommend sending
in the pump for servicing every 2-3 years.
Calibration on-site not possible!
We would like to point out that a repair of the dosing pump should be
performed only marginally, because calibration of the dosing pump
on-site is not possible.
We recommend exchanging a defective pump and sending it in for
servicing to the factory.
A pump which does not function properly results in incorrectly meas-
ured values (e.g. error message "36 Fault Analysis"). If you have
problems with the dosing pump, we recommend replacing it.
Proceed as follows to replace it:
Switch off the device and disconnect it from the power supply
Loosen the five cables of the terminal connections using a suitable
screwdriver.
Loosen the hose connections at the indicator bottle and at the
measuring chamber holder.
Collect the indicator in a container!
Use a screwdriver to push the lock of the pump housing down-
wards and remove the housing from the top
At first, place the replacement pump on top of the DIN rail and
push the housing downwards until the lock engages
Reconnect the cables (observe the colour sequence!)
Reconnect the hose connections (note the suction and pressure
side!)
CAUTION
!
NOTE

Carrying out maintenance
12
Replacing the dosing pump valves
In certain cases and with an obvious cause of malfunctioning, it is
also possible to replace the pump valves. Please proceed as follows:
Remove the transparent cover.
Use a suitable screwdriver to remove the electronics from the
housing (snap-on installation).
Replace the hoses or valves (observe the direction of installation.
Re-assemble the pump in reverse order. Please make sure that
wires and hoses are not trapped.
Checking the dosing pump
Proceed as follows to check correct functioning and the dosing quan-
tity of the dosing pump:
Press the “HAND” key.
Make sure that the measuring chamber is empty.
Remove the pressure hose from the measuring chamber holder.
Subsequently press the "Manual" key on the dosing pump.
The dosing quantity must be a single drop (30 μl) and should drip
from the pressure hose
Collect the indicator in a container!
2.
1.
3.

Carrying out maintenance
13
Replacing the backup battery
When the device is switched off the internal clock is powered by a
lithium backup battery (CR2032 type), which is designed to have a
service life of 10 years. After this period, it should be replaced for
preventive reasons, and always ensuring a measured voltage <2.3V.
Change the battery on the controller board as follows:
Switch off the device and disconnect it from the power supply
Open the unit cover if present.
Open the transparent cover to the board room.
Using a non-conductive tool, carefully prise the used battery out of
its mounting ①. Avoid damaging the circuit board with the sharp
edge of a screwdriver.
Insert a new battery and pay attention to the polarity.
Close the transparent cover to the board compartment.
Disposal of batteries
Batteries must be disposed of separately from the unit! Dispose of
the batteries according to the guidelines of your country.
Observe ESD safety
precautions!
NOTE

Carrying out maintenance
14
Replacing the fuse
This fuse protects the Testomat® Modul TH device or outputs against
overload and short circuit.
The main fuse F1 (1 A MT) for outputs and equipment is located on
the motherboard (behind the controller board).
F1

Troubleshooting
15
Troubleshooting
In this section, you will find the most common error messages, possi-
ble causes and how to resolve them.
A complete table with all error messages, possible causes and trou-
bleshooting measures can be found from page 35 onwards in the
operating manual.
Operation without cover / Measurement error under strong inci-
dence of light
When installing and operating without the instrument cover (Art. No.
37798), avoid direct sunlight or strong incidence of light, as this may
impair the measurement.
Error message “36 Fault analysis”
A measuring fault analysis occurs when the water in the measuring
chamber is too “light” after the second dosing.
Check the following points if “36 Fault analysis”is displayed in the
Service Monitor:
1. The indicator’s expiry date has been exceeded.
Remedy:
There is insufficient dye in the indicator. Use a new indicator.
When using an indicator that is not from Gebr. Heyl, replace it with
the one recommended by us.
2. The stirring bar in the measuring chamber holder fails to
rotate, resulting in an insufficiently mixed indicator.
Remedy:
The stirring bar is stuck due to soiling in the stirring area of the
measuring chamber holder. Clean the measuring chamber.
The measuring chamber holder is leaky, entered water has de-
stroyed the electronics on the circuit board. Change the measuring
chamber holder.
The plug connector of the flexible cable is not locked (loose con-
tact). Insert the plug properly into the socket.
The magnet in the stirring bar is too weak. Change the stirring bar.
If necessary, insert a stirring bar.
Check the plug contact of the flexible printed circuit board. If nec-
essary, replace the measuring chamber holder.
3. The pump doses insufficient indicator.
Remedy:
Check the dosing pump (see Checking the dosing pump on page
12). If necessary, replace the dosing pump.
NOTE

Troubleshooting
16
4. Air is trapped in the indicator hose.
Remedy:
Bleed the dosing hoses by pressing the “Manual” button on the
dosing pump several times.
Make sure that all the indicator hoses are fitted correctly. If not, air
may enter the hoses!
If the error re-occurs, replace the bottle insert for a screw cap with
a suction tube (art. no.: 40135).
Make sure that the suction and pressure hose set is not kinked or
trapped. If necessary, replace the hoses. Complete suction hose
(art. no. 40011), complete pressure hose (art. no. 40016).
5. The water pressure is insufficient. Water is supplied, but the
water level inside the measuring chamber remains too high
after closing the inlet valve.
Remedy:
The water level should be approx. 32 mm above the lower edge of
the transparent measuring chamber block.
Make sure that the water pressure is within the valid range of 0.3 -
1 bar (without valve body) and 1 - 8 bar (with valve body).
Make sure all the dummy plugs are in place at the measuring
chamber (e.g. after maintenance). Make sure all the dummy plugs
are fitted correctly, thus preventing air leaks.
6. The drain pipe is blocked. Water may collect and stand in the
pipe.
Remedy:
Make sure the water outlet is not blocked. If necessary, clean it.
7. The measuring chamber is soiled.
Remedy:
All the channels in the measuring chamber and the measuring
chamber sight-glass windows must be free of indicator residue or
any other type of contamination.
Dirt can be removed with either ethyl alcohol or another commer-
cially available plastic cleaner.
Also clean the receiver optics.
8. The measuring water must be completely free of bubbles
when carrying out measurements and should not have a
milky appearance.
Remedy:
Make sure there are neither air bubbles nor more than 20 mg/l CO2
in the measuring water.
Air bubbles or milky measuring water may be the result of incorrect
regeneration of the softening plant or residual salt in the soft water.
Use our aerator R (art. no. 130010).

Troubleshooting
17
9. Iron (< 0.5 mg/l), copper and aluminium ions (<0.1 mg/l) may
impair the measurement.
Remedy:
This is probably caused by old iron pipes, new copper pipes or
changes to the well water. Pay attention to the composition of the
measuring water.
Use our colourimetric test kits for iron (art. no. 410547) and copper
(art. no. 410562) when carrying out checks.
10. Oxidation on the flex film in the measuring chamber holder.
Remedy:
Replace the measuring chamber holder.
11. Measuring chamber was not correctly filled.
Remedy:
Check if the closing plugs in the measuring chamber fit tightly. Pay
special attention to the rear plug. If it doesn’t fit, air is sucked
through and the measuring chamber cannot siphon correctly. This
leads to low water in the measuring chamber or overflowing.
Replace old or missing closing plugs with new. If you don't have
these on hand, use a tape to help, until you've got the spare part.
Check the inlet solenoid valve. Excessive or insufficient water in
the measuring chamber indicates incorrect opening/closing of the
solenoid valve.
( foreign particles / wear )
Indicator and water quantity must be correct. Otherwise it will result
in incorrect measurements.
Error message “38 Water low”
Remedy:
Check the inlet water (filter strainer, etc.) for foreign particles. If
necessary, clean the filter strainer.
The inlet pressure is too low (less than 1 bar). Remove the pres-
sure valve body (see “Cleaning the controller/filter housing” on
page 41).
Typically 400 ml/min must flow through the measuring chamber to
flush and fill the measuring chamber.
Oxidation on the flex film in the measuring chamber holder. Re-
place the measuring chamber holder.
closing plugs
Water level
too high
Water level
too low
Water level
correct

Troubleshooting
18
Error message “„33 Fault optics LED1” and „27
Fault optics LED2”
Remedy
There is an error at the optical component. The receiver is defec-
tive. Replace the measuring chamber holder.
Cold water (<8°C) combined with a warm and humid ambient tem-
perature (>28-30°C) can lead to the formation of water drops on
the sight-glass windows.
Error message “34 Fault turbid”
Remedy:
Check whether the supplied measuring water is very turbid or
soiled.
Check whether the sight-glass windows are soiled and, if neces-
sary, clean them.
Make sure the flex film is dry. If you detect water damage, replace
the measuring chamber holder.
If necessary, install a filter (art. no. 11217) in the inlet of the in-
strument.
Cold water (<8°C) combined with a warm and humid ambient tem-
perature (>28-30°C) can lead to the formation of water drops on
the sight-glass windows.
Error due to defective hardware
1. The dosing pump runs permanently.
Remedy:
Check whether the broadband cable at the main and front board is
loose or defective.
2. The inlet valve allows water to flow through it.
Remedy:
Check whether the inlet valve is soiled.
3. The outlet valve allows water to flow through it.
Remedy:
Check whether the outlet valve is soiled. Is there a permanent
voltage on the valve?
Carry out a reset (see operating instructions on page 20).
If this fails to eliminate the error, replace the valve.

Spare parts for Testomat® Modul TH
19
Spare parts for Testomat® Modul TH
Art. no.
Pressure controller
40125
Controller / Filter receiver, complete
40120
Controller / Filter receiver
40129
Controller plug T2000, complete
11225
Flow controller valve body
11270
Retaining pin 3x50 / 135 degree
11217
Inlet filter 19,5dx25
11218
Spring for inlet filter
40121
Inlet connector
40153
Screw-in connector G 1/4"
40150
Screw-in connector G 1/8"
Measuring chamber
40173
Sight-glass window with seal
40170
Sight-glass window 30x3
40176
Sight-glass holder
33253
Bolt M3x40, A2, DIN 965
40032
Latch fastener TL-17-201-52
11210
Plug for measuring chamber
40022
Measuring chamber T2000 complete.
Measuring chamber holder
40392
Measuring chamber holder Testomat®Modul TH
40050
Magnetic stirrer
40156
Screw-in connector 3/8" -10
40056
Solenoid valve, 2/2-way, Testomat®ECO
Dosing pump DOSIClip®
270470
Dosing pump DOSIClip
Bottle connection/Suction device
37644
Screw cap with insert for 500 ml bottle
Instrument spare parts
31271
Fuse G-M, 5x20mm, M 1 A
37896
Base circuit board Testomat®Modul TH
37805
Control circuit board Testomat®Modul TH
37734
Cable gland M16 x 1,5
37735
Nut M16x1,5 for cable gland
37832
Ribbon cable 2 x 7 pole
40060
Cable loom 2V for T2000
40062
Cable loom 2P for T2000
32187
Outlet funnel with snap lug
37774
Spacer ring for drain funnel
37798
Cover
Installation
40153
Inlet for Testomat®Modul TH D=6
37581
Pipe, PE, D=6 d=4 L=5 m (5 m supply hose with 6
mm external diameter)
35715
Outlet hose 12 x 15 x 2000 mm (2 m outlet hose with
12 mm internal diameter)
Caution!
Should you send your Tes-
tomat®Modul TH in for
maintenance, please make
sure that the measuring
chamber has been emptied
and the reagent bottles
have been removed from
the device. In addition,
rinse the DOSIClip pump
with water to remove resid-
ual indicator.

Component positions
20
Component positions
Motherboard 37896 (behind)
Controller board 37805
Cable loom 2V 40060
Cable loom 2P 40062
Valve block 40056
Screw cap with insert
37644
Measuring chamber
40022
Measuring cham-
ber holder 40392
Controller/filter
mounting 40125
Plug-in connector
40156
Dosing pump 270470
Sight glass window
with seal 40173
Sight glass holder
40176
Other manuals for Testomat Modul TH
1
Table of contents
Other Heyl Measuring Instrument manuals
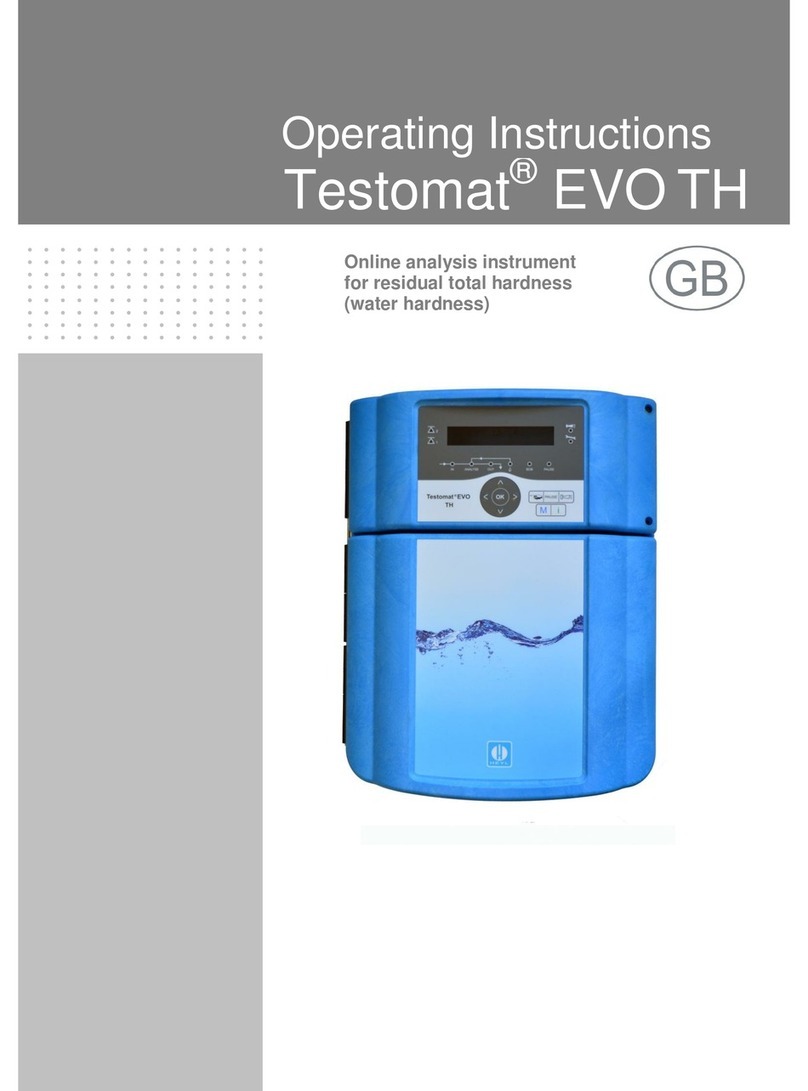
Heyl
Heyl Testomat EVO TH series User manual
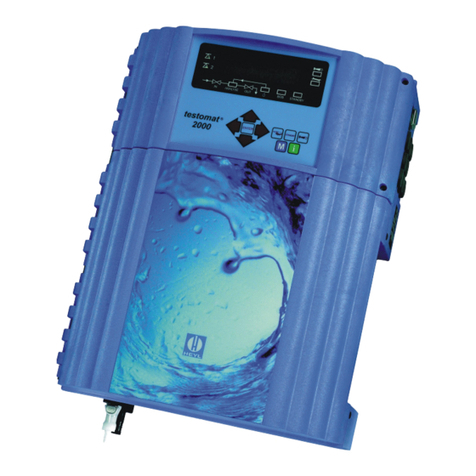
Heyl
Heyl Testomat 2000 User manual
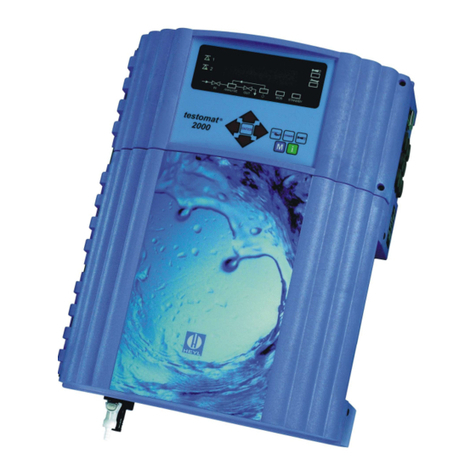
Heyl
Heyl Testomat 2000 THCL User manual
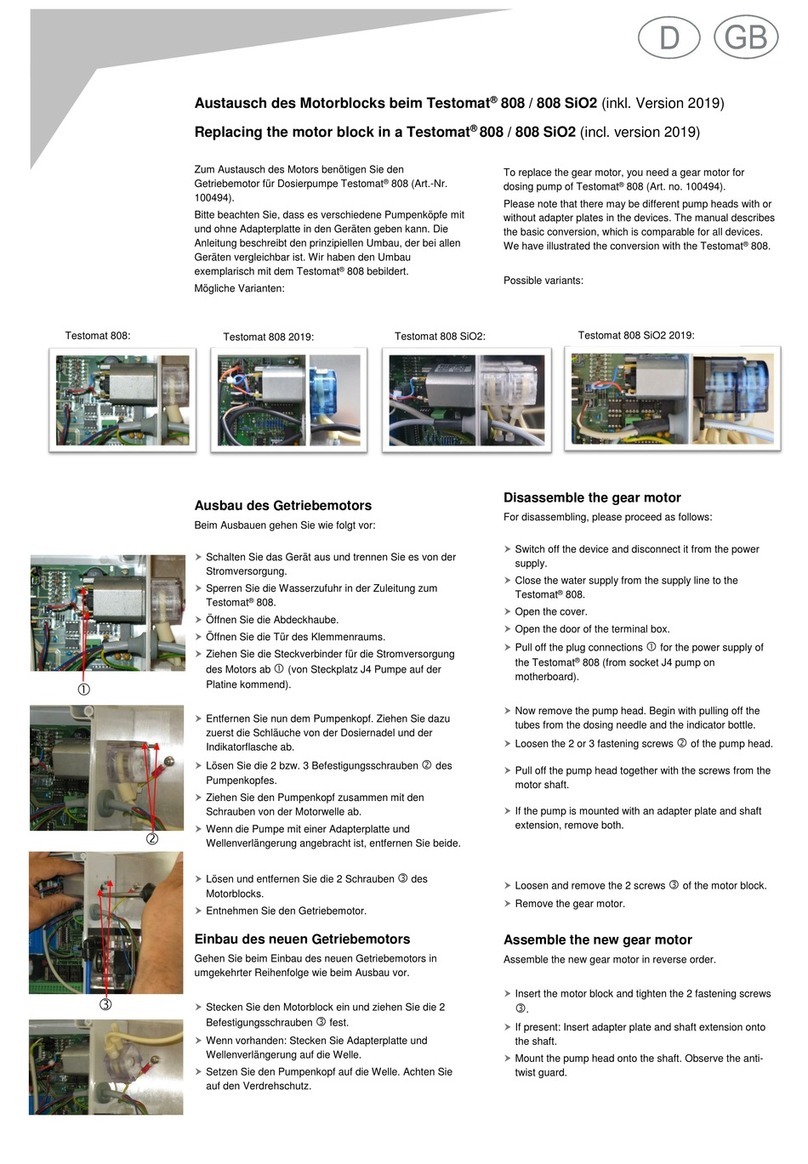
Heyl
Heyl Testomat 808 User manual
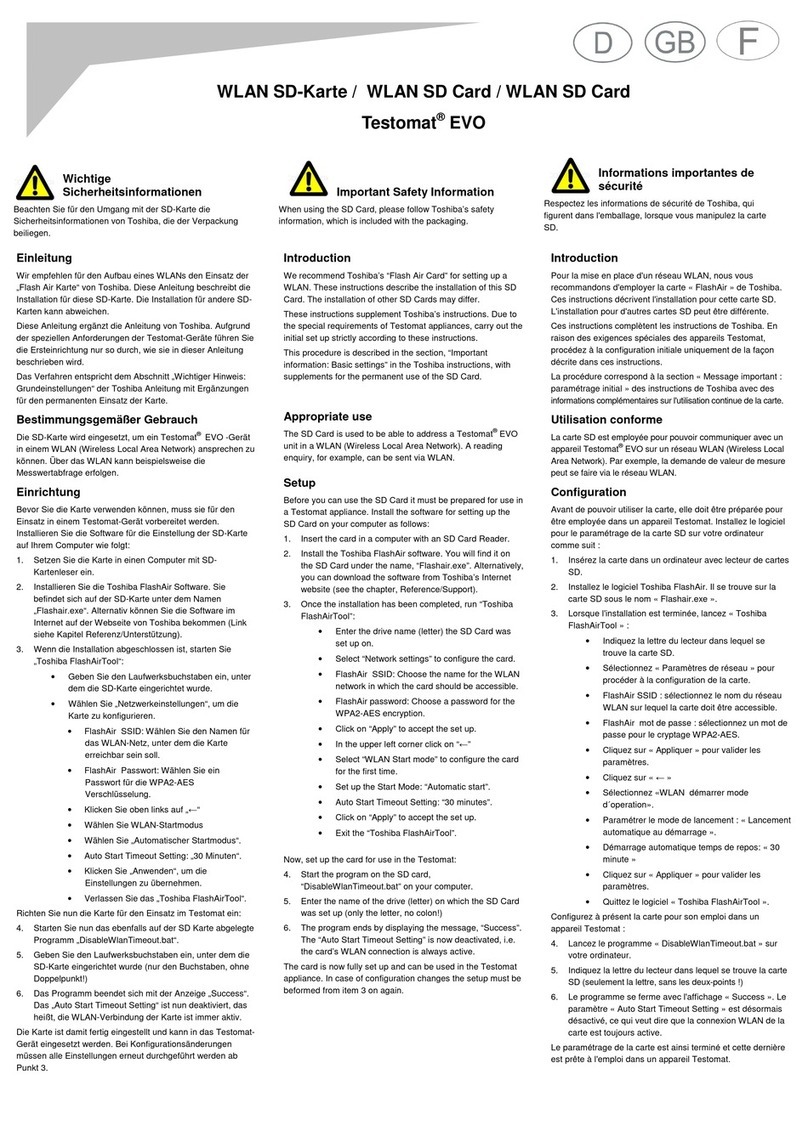
Heyl
Heyl Testomat EVO User manual

Heyl
Heyl Testomat ECO User manual

Heyl
Heyl Testomat EVO TH Operating instructions
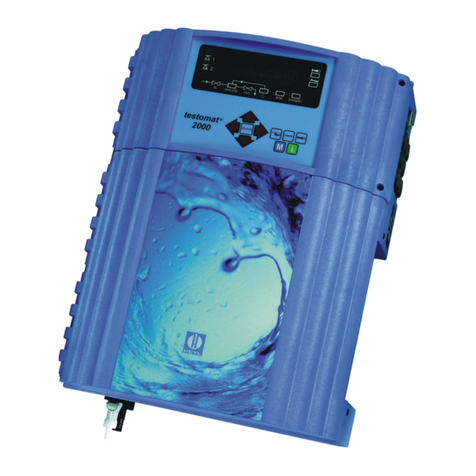
Heyl
Heyl Testomat 2000 PO4 User manual
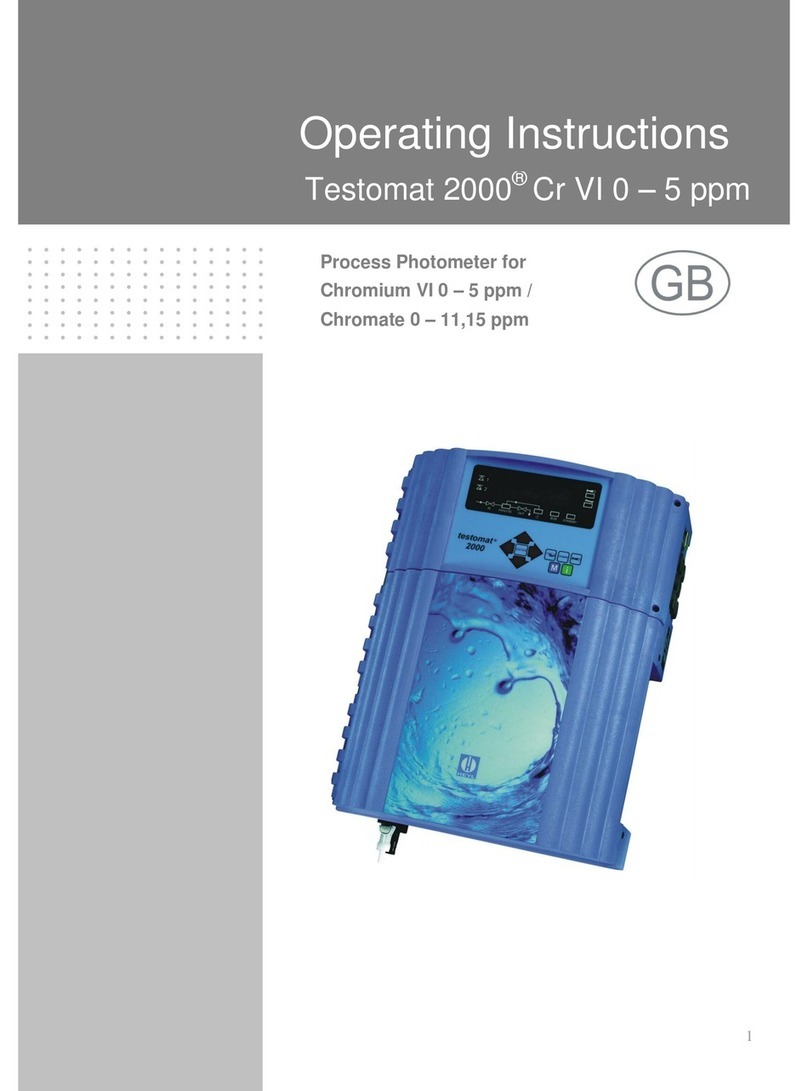
Heyl
Heyl Testomat 2000 Cr VI 0 - 5 ppm User manual
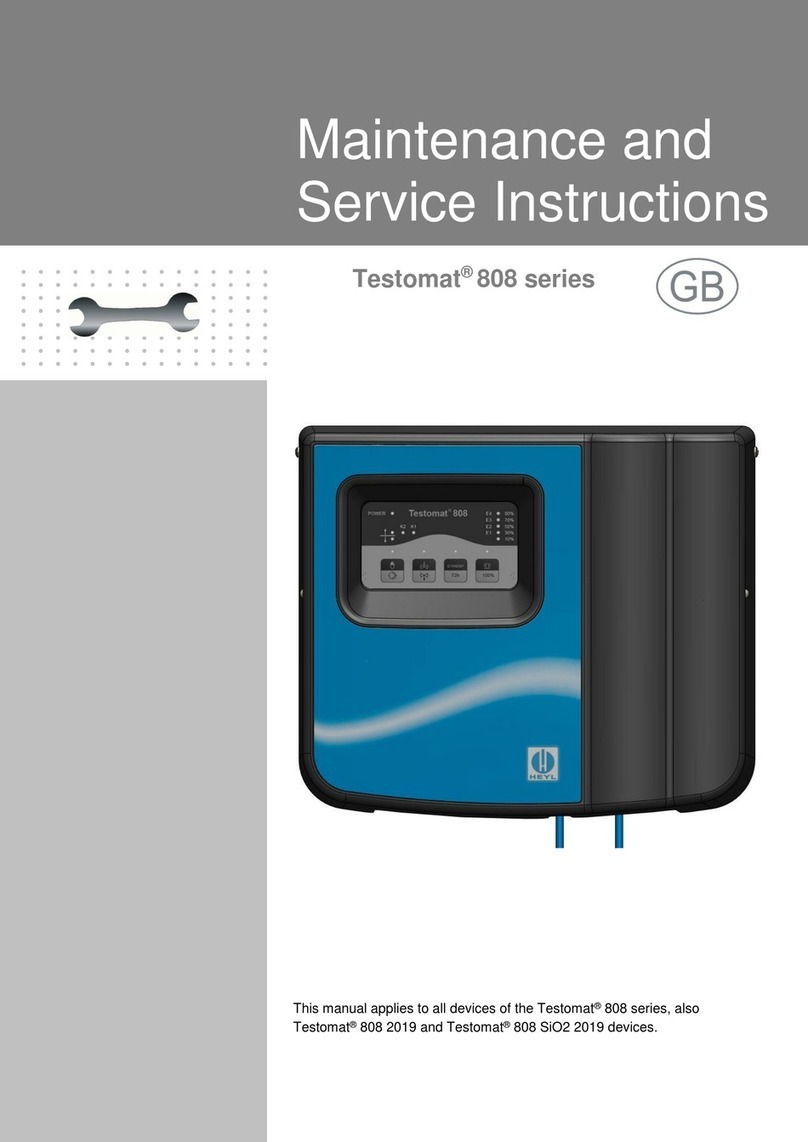
Heyl
Heyl Testomat 808 Series Manual