HM Electronics SUPERFLEX HS-2A-3SH User manual

Industrivej 3-9
DK-9460 Brovst
Denmark
Tel.: +45 9823 6088
Fax: +45 9823 6144
Manual for: 13.03.12
Bending Machines
HS-2A-3SH SUPERFLEX
HS-3-3SH SUPERFLEX

2
EC Declaration of Conformity
hereby declares that
HM HS-2A-3SH Superflex Bending Machine are manufactured in accordance with the
provisions of the COUNCIL DIRECTIVE of 17. May 2006 (2006/42/EC) – The Machinery
Directive (order no. 561 of 25 June 1994 with subsequent amendments)
Also on accordance with:
The council directive of 19 February 1973 (73/23/EEC) – The Low Voltage Directive – with
later amendments (order no. 797 of 30 August 1994)
The council directive of 3 May 1989 (89/336/EEC) – The EMC Directive – with later
amendments (order no. 796 of 5 December 1991 with subsequent amendments)
HM MACHINERY A/S
Industrivej 3-9
9460 Brovst
Denmark
www.scantool-group.com
Tlf: +45 98 23 60 88
Fax.: +45 98 23 61 44

3
Table of contents
1. SET UP 4
1.1 INSTALLATION 4
1.2 LOOSENING THE BENDING STOP 4
1.3 ADJUSTING THE LOWER BEAM 4
2. OPERATING INSTRUCTIONS 5
2.1 SETTING THE ANGLE 5
2.2 BENDING 5
2.3 MAINTENANCE 5
2.4 CLEANING 5
2.5 OPERATION IN PICTURES 6
2.6 MAINTENANCE IN PICTURES 7
3. SAFETY RULES FOR STATIONARY POWER TOOLS. 7
3. SPARE PARTS 10
3.1 EXPLODED DRAWING 10
3.2 SPARE PART LIST 10
3.3 EXTRA ACCESSORIES 11
3.4 SPARE PARTS BACK GAUGE 11
3.5 SPARE PARTS SEGMENTS 12
3.6 PRESS PIECE HM F/QUICK-CHANGE 13
4. TECHNICAL DATA 13
4.1 EXTERIOR DIMENSIONS 13
4.2 MACHINE SPECIFICATIONS14
4.3 WARRANTY 14

4
1. Preparations
1.1 Installation
The machine is delivered on a pallet and packed in protective wrapping. When the
machine is delivered it has been pre-treated with an anti corrosive. Use an ordinary
detergent when cleaning. Do not use thinner. The machine must be placed on a firm and
level ground. Bolt it to the floor using the anchoring holes.
It is important that this machine is bolted to the floor.
Before the machine is bolted to the floor the machine it is necessary to level out the
machine. It might be necessary to make adjustment with distance pieces underneath the
machine if the floor is not in level. The adjustment is necessary to avoid the machine for
twisting and then pull uneven.
1.2 Loosening the bending stop
Before usage you will need to loosen the bending stop (Fig. 2.1 no. 7). The camber is from
the factory adjusted to 1mm sheets, if another setting is needed to e.g. Bending of a
thicker sheet, you will need to adjust this using the handle (Fig2.1 no. 8) to the thickness
of the sheet + 25% so the sheet can be bend without ruining the segments. The camber is
adjusted using handles (Fig. 2.1 no 6) until you can lock the foot pedal.
1.3 Adjusting the lower beam
If the bend is not satisfactory in the middle of the sheet, it can be caused by the bending
beam not having an adequate bombarding (crowning). This can be solved by tightening
the two nuts (Fig 2.1 no. 5), giving the bending beam a bigger bombarding. This should
normally only be needed after the machine has been in use for a while.

5
2. Operating Instructions
The machine consists of the following mechanisms:
1. Foot clamp with locking mechanism
2. Lower beam segments
3. Upper beam segments
4. Bending beam segments
5. Adjustment nut for bombarding of the bending beam
6. Handle for adjustment of the upper beam
7. Bending stop
8. Adjustment handle for adjusting the bending beam to the sheet thickness
6
6
2
3
4 7
8 8
5
5
1
Fig. 2.1 The machine
2.1 Setting the angle
The bending stop (nr 7) is set to the wanted angle using the degree measure on the side
of the machine. A test bend is performed and the bending stop adjusted if needed.
2.2 Bending
The bending beam is lowered to a minimum of the sheet thickness e.g. the sheet is 2 mm
thick, then the bending beam needs to be lowered by 2 mm. If the bend is over 90
degrees the distance needs to be bigger.
2.3 Maintenance
Normal cleaning and lubrication of movable parts should be done for every 100 working
hours.
2.4 Cleaning
Machine anticorrosive parts should only be cleaned with kerosene in a rapid workflow.

6
2.5 Operation in pictures
The machine is operated as shown below

7
2.6 Maintenance in pictures
3. Safety rules for stationary power tools.
Follow them to achieve best results and full benefit from your new machine.
The good craftsman respects
the tools with which he works.
He knows they represent years
of constantly improved design.
He also knows that they are
dangerous if misused.
The safety rules are based on
approved practices in industrial
and home shops.
1. Know your power
tool. Read the
owner’s manual
carefully. Learn its
applications and
limitations, as well
as the specific
potential hazards
peculiar to this tool.
2. Keep guard in place
and in working order.
3. Ground all tools. If tool is equipped with three-
prong plug, it should be plugged into a three-hole
electrical receptacle. If an adapter is used to
accomodate a two-
prong receptacle, the
adapter wire must be
attached to a known
ground. Never
remove the third
prong.

8
4. Remove adjusting keys
and wrenches. Form
habit of checking to see
that keys and adjusting
wrenches is removed
before turning it on.
5. Cluttered areas and benches invite accidents.
6. Avoid dangerous
environment. Don’t use
power tools in damp or wet
locations or expose them to
rain. Keep your work area
well lighted.
6. Keep children away.
All visitors should be
kept in a safe distance
from work area.
8. Make workshop
kidproof with
padlocks, master
switches, or by
removing starter keys.
9. Don’t force tool. It will do the job better and be
safer at the rate for
which it was designed.
.
10. Use right tool.
Don’t force tool or
attachment to do
a job it was not
designed for.
11. Wear proper apparel. Wear no loose clothing,
gloves, neckties, rings,
bracelets, or other
jewelry which may get
caught in moving parts.
Non-slip footwear is
recommended. Wear
protective hair covering
to contain long hair.
12. Always use safety
glasses. Also use face or
dust mask if cutting
operation is dusty.
Everyday eyeglasses only
have impact resistant
lenses. They are NOT
safety glasses.
13. Secure works. Use
clamps or vise to hold
works, when pratical. It’s
safer than using your
hands and it frees both
hands to operate tool.

9
14. Don’t
overreach.
Keep proper
footing and
balance at
all times.
15. Maintain tools with care. Keep tools sharp and
clean for best and safest
performance. Follow
instructions for lubricating
and changing accessories.
16. Disconnect tools before
servicing and when changing
accessories such as grinding
wheels, polishing mops,
grinding belts, blades, bits,
cutters, etc. Never leave a
running maschine, wait till the
Machine has stopped. If parts
of the machine are out of order
the Machine shold not be used
befour it has been repaired.
17. Reduce the risk of
unintentional starting.
Make sure switch is in off
position before plugging
in.
18. Use recommended accessories. Consult owner’s
manual for recommended accessories. Use of
improper accessories may cause risk of injury to
persons.
19.Never work in a way that can hurt you. Do not
stand in a bent position. Stand straight. Alkohol and
other drugs are not to be taken while working with
the machine.

10
3. Spare parts
3.1 Exploded drawing
3.2 Spare part list
00313350 HM HS-3-3SH Superflex - 1270x2,00mm
00312650 HM HS-2A-3SH Superflex - 1020x2,50mm Order number
Pos. Description 1270 1020
1 Arm trykbom højre 1056783 =
2 Arm trykbom venstre 1056780 =
3 Trykbom komplet 1056771 1056772
4 Skærm komplet højre 1056703 =
5 Skærm komplet venstre 1056704 =
6 Aksel + kødben V. 1056843 =
7 Aksel + kødben H. 1056844 =
8 Glidering 1056795 =
9 Vippearm Komplet 1056802 =
10 Grundstel 1056770 1056769
11 Overvange komplet 1056748 1056745

11
12 Bukkevange komplet 1056756 1056757
13 Trækstang kpl 1056820 =
14 Trækfjeder 8x49,5xtæt vx405 indv. i øjet 9014362 =
15 Trykfjeder 7x53,5x295x18,5 V TES 9014358 =
16 Håndtag Lang Møtrik 1056830 =
17 Håndtag Kort Møtrik 1056833 =
18 Press Piece HM f/quick-change Se nedenfor =
19 Holder for fjeder 1056836 =
20 Ring for grademåler 1056865 =
21 Pinolskrue M6x50 0105027 =
22 Stop for bukkevinkel 1056867 =
23 Unbracobolt M10x25 5431215 =
24 Mellemlæg for fjeder 1056870 =
25 Vinkelmåler digital 10436151 =
26 Fodpedal komplet 1056875 =
27 Fjederholder 1056880 =
28 Bolt for forspænd 1056885 1056884
29 Juster for trykfjeder indre 1056888 =
30 Muffe sort 3/4" V V S 1056889 =
31 Polyamidskive ø21 0101697 =
32 Støddæmper v/fodpedal 1056892 =
33 Møtrik M16, højre 0928641 =
34 Facetskive ø21 0231337 =
35 Bræddebolt M10x35 5490098 =
36 Møtrik M10 5438761 =
37 Skærmskive A2 ø10,5x30x2,5 2323212 =
38 Låsemøtrik M10 1943643 =
39 Segmentstøtte undervange 1056894 =
40 Unbracobolt M5x16 0120626 =
41 Maskinskrue M5x10 m/cyl. hoved og kærv 0120630 =
42 Stålsætbolt M10x16 0300133 =
43 Møtrik M8 0231350 =
44 Topmøtrik M8, messing 0232304 =
45 Låsering Ø30 udv. 0111330 =
46 Låsering Ø25 udv. 0111325 =
47 Støddæmperring pur skive 0100072 =
48 Smørenippel M8 2005976 =
49 Stålafstandsskive ø42ø30x0,5 0101698 =
50 Segmentsæt kpl UV 10312665 10313365
51 Segmentsæt kpl OV 10312663 10313363
52 Segmentsæt kpl BV 10312667 10313367
53 Bolt m/kugle og fjeder inkl. møtrik. 10310055 =
54 Møtrik M20, sort 0928645 =
55 Værktøj til skift af segment 10311062 =
56 Stålsætbolt M10x55 0110107 =
57 Stålsætbolt M8x40 FZB 0207969 =
3.3 Extra accessories
·You can get a Back gauge for the Superflex bending machine. Order number:
10311005.
·It can be an advantage to get an extra set of the right and left segments also called
Corner Segments. When you have the extra segments you have more possibilities
to bend special bents.
3.4 Spare parts Back gauge
Benævnelse 1270 og 1020
Kibgreb M8x20 0105134
Svingarm f/anslag 46010007

12
Skinne f/anslag 46010106
C-profil f/anslag 46010005
Klods f/anslag t/superflex 46010010
Unbracobolt M8x55 0350014
Møtrik f/anslag 10306067
Unbracobolt M8x10 Buttonhead 0120500
3.5 Spare parts segments
Segments can be purchased either as a complete set or as individual parts. In this section
lists the various items. Abbreviations: OV = Clamping beam, BV = bending beam, UV =
Lower beam.
Benævnelse 1270
1020
Segment set kpl UV (stykliste) 10313365 10312665
Segment set kpl UV (vare) 10313369 10312669
Segment set kpl OV (stykliste) 10312671 10312670
Segment set kpl OV (vare) 10313363 10312663
Segment set kpl BV (stykliste) 10313367 10312667
Segment set kpl BV (vare) 10313368 10312668
Segment set Right/Left UV 10312659 =
Segment set Right/Left OV 10312661 =
Segment set Right/Left BV 10312660 =
Lower Beam segments
Segment 25 mm UV 10312730 =
Segment 30 mm UV 10312731 =
Segment 35 mm UV 10312732 =
Segment 40 mm UV 10312733 =
Segment 45 mm UV 10312734 =
Segment 50 mm UV 10312735 =
Segment 75 mm UV 10312736
Segment 100 mm UV 10312737 =
Segment 200 mm UV 10312738 =
Segment 250 mm UV 10312739
Segment 270 mm UV 10312740 =
Cornersegment Left UV 10311065 =
Cornersegment Right UV 10311066 =
Clamping beam segments
Segment 25 mm OV 10312687 =
Segment 30 mm OV 10312688 =
Segment 35 mm OV 10312689 =
Segment 40 mm OV 10312690 =
Segment 45 mm OV 10312691 =
Segment 50 mm OV 10312692 =
Segment 75 mm OV 10312695 =
Segment 100 mm OV 10312696 =
Segment 200 mm OV 10312697 =
Segment 250 mm OV *) 10312698
Segment 270 mm OV 10312699 =
Corner segment v OV 10312662 =
Corner segment h OV 10312664 =
Bending beam segments
Segment 25 mm BV 10312705 =
Segment 30 mm BV 10312706 =
Segment 35 mm BV 10312707 =
Segment 40 mm BV 10312708 =

13
Segment 45 mm BV 10312709 =
Segment 50 mm BV 10312710 =
Segment 75 mm BV 10312711 =
Segment 100 mm BV 10312712 =
Segment 200 mm BV 10312713 =
Segment 250 mm BV *) 10312714
Segment 270 mm BV 10312715 =
Corner segment v BV 10311068 =
Corner segment h BV 10311069 =
Note: *) Segments of width 250 mm, only the HS-3-3SH is 250 mm wider than the HS-2A-3SH
3.6 Press Piece HM f/quick-change
The Press Piece HM f / quick change segment mentioned in the parts list consists of the
following parts:
1) 1 unit Pressure Piece / Hose Iron No.: 1056886
2) 1 piece O-ring cords f / quick change No.: 10312685
3) 3 pieces Unbracobolt M8x25 No.: 0105052
4. Technical Data
4.1 Exterior Dimensions
The machine's exterior dimensions in mm:
Type
A
B
C
D
E
F
HS-2A-3SH 305 1335 550 730 1240 1450
HS-3-3SH 305 1335 550 730 1240 1700
Fig.: 5.1 Exterior dimensions

14
4.2 Machine specifications
The technical specifications are given for bending ordinary steel St37.
Type
Work length
[mm]
Plate
thickness
[mm]
Max. Lifting
heigth
[mm]
Bending angle
[grader]
Weight
[kg]
HS-2A-3SH
1020
2,50
50
135°
430
HS-3-3SH
1270
2,00
50
135°
477
4.3 Warranty
Guarantee
If within 2 year of purchase this machine supplied by Scantool A/S becomes defective due
to faulty materials or workmanship we guarantee to repair or replace the machine or
defective part or parts free of charge provided that:
1. The product is returned complete to one of our Service Branches or Official Service
Agents.
2. The product has not been misused or carelessly handled and in particular has not
been used in a manner contrary to the operating instructions.
3. Repairs have not been made or attempted by other than our own Service Staff or
the staff of our Official Service Agents.
4. The invoice copy attached, when sent for repair.
5. Wear parts are not covered by the warranty
This manual suits for next models
1
Table of contents
Popular Cutter manuals by other brands

Rose electronics
Rose electronics TUBING CUTTER owner's manual
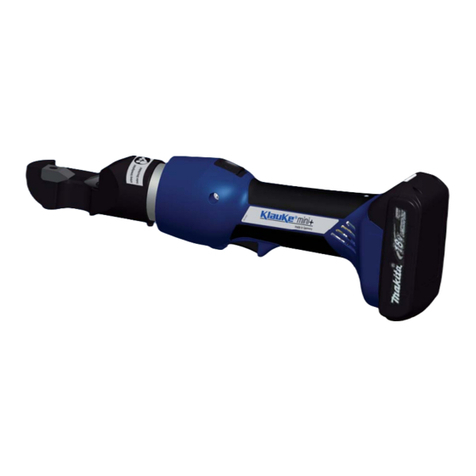
Textron
Textron Klauke Mini+ EBS 12-L instruction manual
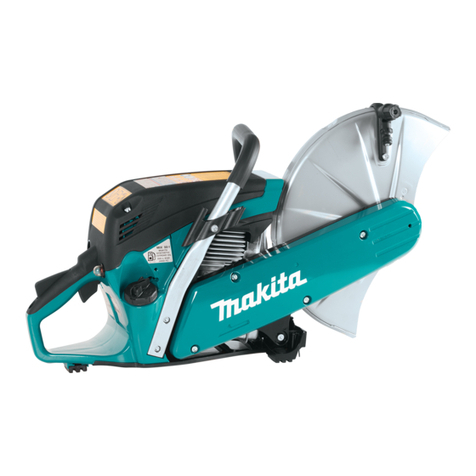
Makita
Makita EK6100 Operator's and safety manual
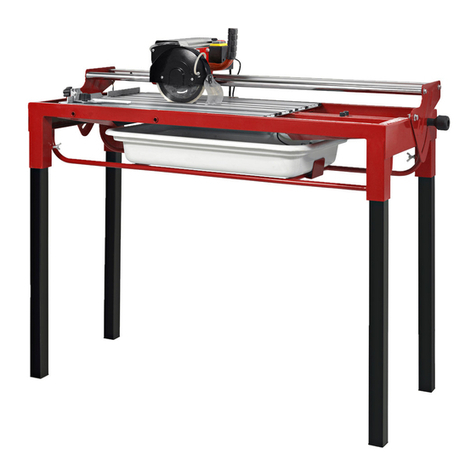
Jula
Jula Meec tools B-850 operating instructions
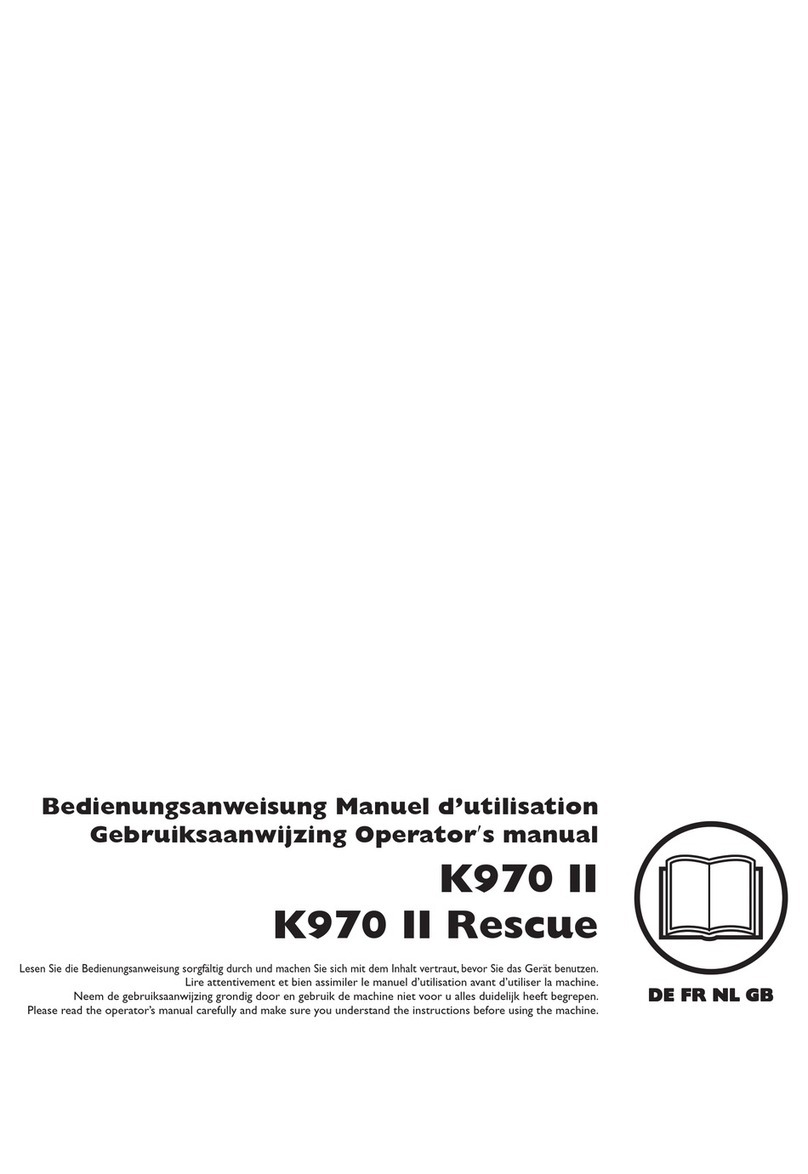
Husqvarna
Husqvarna K970 II Rescue Operator's manual

START International
START International zcM1500 manual

Würth
Würth EMS 12-A Translation of the original operating instructions

Hallde
Hallde CC-32S User instructions
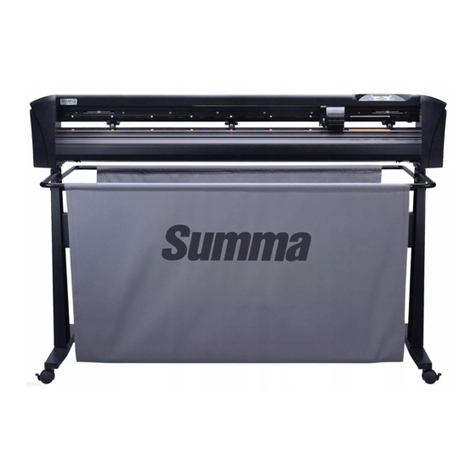
Summa
Summa SummaCut D120 user manual

CORTAG
CORTAG INFINITY LARGE FORMAT TILE CUTTING SYSTEM instruction manual
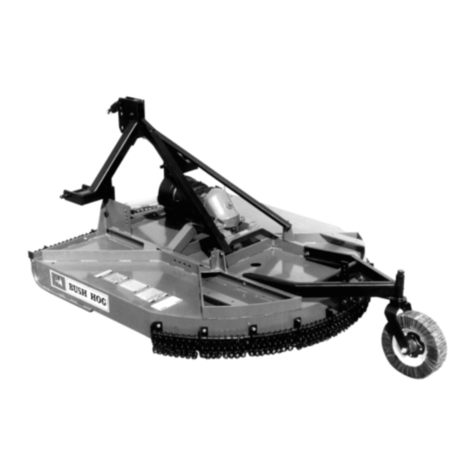
Bush Hog
Bush Hog 305 Series Operator's manual

RIDGID
RIDGID 1390M operating instructions