Inca PVJ3 User manual

PVJ3 page 1
1
INCA
CONTROL PTY LTD Phone:(02) 9675 3815
UNIT 14/62 OWEN ST Fax: (02) 9675 1381
GLENDENNING NSW 2761 Email: sales@incacontrol.com.au
A.B.N 54 131 353 636 Web: www.incacontrol.com.au
Design & Manufacture of:
Custom-built switchboards
Electronic control equipment
AC/DC pumping controls
Installation & service
INCA MODEL
PVJ3
TRIPLEX PRESSURE SYSTEM VARIABLE
SPEED CONTROLLER
USER MANUAL
Inca Reference PVJ3
Software Version 1.7
Technical Support
Pumps & Mechanicals –Pump supplier
Controls –Inca Control Pty Ltd
Phone 02 9675 3815

PVJ3 page 2
2
TABLE OF CONTENTS
1.0 Control Panel Overview………………………………………………. 3
1.1 Features………………………………………………………… 3
1.2 Description……………………………………………………... 3
2.0 Installation…………………………………………………………….. 5
2.1 Mechanical installation………………………………………… 5
2.2 Sensor installation……………………………………………… 5
2.3 Electrical installation…………………………………………… 5
2.4 Maintenance…………………………………………………….. 6
3.0 Start up………………………………………………………………… 7
3.1 Notes on value entry…………………………………………... 7
3.2 Power up display………………………………………………. 7
3.3 Screen display layout………………………………………….. 7
4.0 Calibration……………………………………………………………. 8
4.1 Pressure Sensor Calibration……………………………………. 8
4.2 Setting low pressure shutdown…………………………………. 8
4.3 Setting low pressure time delay………………………………… 8
4.4 Set Point Pressure Setting……………………………………… 8
4.5 Start pressure Setting…………………………………………… 9
4.6 Pump Stop Minimum Speed…………………………………… 9
4.7 Sleep Shutdown Time Setting………………………………….. 9
4.8 Standby Start Time Setting.…………………………………….. 9
4.9 Standby Stop time Setting……………………………………… 10
4.10 2nd Standby Start Time Setting.……………………………….. 10
4.11 2nd Standby Stop time Setting………………………………… 10
4.12 Maximum continuous running time ……………………………. 10
4.13 Hour run meter………..……………………………………… 10
4.14 Data Logger.............................................................................. 10
4.15 Auto Tune.................................................................................. 11
5.0 Operation……………………………………………………………… 12
5.1 System operation……………………………………………….. 12
5.2 Manual/off/auto selector………………………………………. 13
6.0 Warranty Statement…………………………………………………… 14
Drawing supplied separately

PVJ3 page 3
3
1.0 Control Panel Overview
1.1 Features
PVJ3 controller with user friendly setup & display
Display of system Pressure
Low pressure pump shutdown
Low level pump shutdown with automatic reset
Manual/off/auto selectors on panel Face
Hour run meter (resetable)
Microprocessor controlled
Useable with any 4-20mA loop powered Pressure Transducer
1.2 Description
The pressure control panel is designed to maintain a system discharge
pressure via adjustable control points entered by the operator. The display
shows the actual live pressure input received from the system discharge
pressure transducer. It also displays the pump operating condition & alarm
conditions.
User Interface
Display An LCD screen displaying 2 lines of text, each 16
characters long.
Keypad Operator keyboard, 16 sealed membrane keys.
Performance
Range 0 –1000kpa generally, programmable to suit
transducer range.
Inputs 2 wire plus shield connected to terminals located on
panel base plate for pressure transducer.
2 wire connected to terminals for Low Level float
switch.
Outputs
Motors 3 wire plus earth sized to suit motor FLC connected
directly to motor starters overload terminals.
Power Supply 415V 3phase neutral & earth power supply sized to
suit the total load of the three motor & must have a
protection circuit breaker sized to suit the starting
characteristics of the motor.

PVJ3 page 4
4
Mechanical Specification
Enclosure Mild steel powder coated IP54.
Pump Unit See Pumping detail by Pump supplier.
Environmental Specification
Operating Temp -10 to 50deg C
Relative Humidity Do not install in areas of high humidity.
Locate control panel internally where possible to help
reduce heat & weather damage & increase mechanical
life.
Vibration Do not install in a location that is subject to large
amounts of vibration.

PVJ3 page 5
5
2.0 Installation
Note: If any damage to control panel if found, please notify Inca Control
Pty Ltd as soon as possible prior to installation.
The control panel can be wall mounted separately from the pumping unit;
distance is governed by the cable sizing to the motor.
It is recommended that the control panel is within view of the pumping unit for
safety reasons. If not in view lockable isolating switches must be installed at
the pump motors.
2.1 Mechanical Installation
Mount the control panel via the mounting holes in each corner at the back of
the enclosure using minimum 6mm screws, nuts & locking washers, or
masonry anchors.
Install in a dry well ventilated location that matches with environmental
specification in 1.2 above.
2.2 Sensor Installation
Locate the pressure transducer in the discharge pipe work as close as
practical to the control panel.
2.3 Electrical Installation
Note: All cable entries must enter via the bottom of the cabinet. If cables
are entered via the roof Inca Control Pty Ltd reserve the right to
withdraw warranty because of the possibility of shaving entering
sensitive electronic equipment.
Transducer wiring
The pressure transducer must be wired in 1 pair overall screened data cable.
This type of cable provides the most protection against electrical noise &
allows a more accurate outcome.
Connect to the sensor as per data supplied by the sensor supplier
At the control panel connect the positive lead to terminal No10 & the return
signal to terminal No12.
The screen must be solidly earthed, with a saddle clamp providing the best
screening earth.
Float switch wiring
The float switch is wired in the cable supplied with switch. The cable to be
connected must close the circuit when water in the suction tank falls
Connect the float switch as per data supplied by the float switch supplier
At the control panel connect the float switch lead to terminal No10 & terminal
No11.

PVJ3 page 6
6
Motor Wiring
The motor must be wired in cabling sized to suit the motor power requirement.
The motor is to be connected in star or delta as instructed by the nameplate
on the motor.
The cabling entering into the motor terminal box shall be glanded unless a
submersible motor is being used in this case the pump lead is supplied by the
pump manufacturer.
The cable entering the control panel end can be glanded using standard nylon
glands & run directly to the VSD terminals T1, T2, T3. The cables screen must
be earthed via the supplied screening saddle.
2.4 Maintenance
Check that all connections are tight as copper is soft & can work loose.
Check that all controls are functioning as intended.
Check & ensure that the ventilation mats are regularly cleaned as reduced air
flow will damage drives.

PVJ3 page 7
7
3.0 Start up
3.1 Notes on Value Entry
When entering a numeric value, the cursor can be backspaced to correct
mistakes by pressing the LEFT ARROW button.
Decimal points can only be entered on entries with decimal points in the
display line. The decimal point is entered by pressing the +/- . down arrow key
on the bottom of the blue buttons.
You can only enter a value of as many digits as is displayed on the screen.
Example an input that displays 3 digits can only have 3 digit entered.
3.2 Power Up Display
On power up the screen will display the main page including the system
pressure, & Pump motor speeds in %.
3.3 Screen Display Layout
The screen displays two lines of information
The top line displays the live discharge pressure in kPa.
The bottom line displays each Pump motor speed in %. (P1S for Pump 1 &
P2S for Pump 2)

PVJ3 page 8
8
4.0 Calibration
The calibration of the controller is carried out on pages accessed by pressing
& holding in the RIGHT ARROW Button for 5seconds. The first calibration
page will appear. You can move through the calibration pages by pressing the
RETURN ARROW button & then the RIGHT ARROW button to move on.
Continuing this process will move you through the pages with out making any
changes. If changes are made the inputted value is recorded once the enter
button has been pressed. The enter button is the return arrow located at the
bottom right corner of the facia. To get out of calibration pages press the
RETURN ARROW button twice & return to the main page.
4.1 Pressure Sensor Calibration
Calibrate Sensor will now be displayed.
The Cursor will be flashing under the first digit of the SENSOR CALIBRATE
setting. Simply type in the 20mA scale off the pressure transducer to be used,
example 1000kPa (10bar) Press 1, Press 0, press 0, press 0 & then press
Return Arrow button.
Press the RIGHT ARROW Button to move onto the next Page.
4.2 Setting Low Pressure Shutdown
Low pressure will now be displayed.
The Cursor will be flashing under the first digit of the LOW PRESSURE
setting. Simply type in the appropriate pressure you want the low pressure
shutdown to operate at, example 200kPa Press 2, press 0, press 0 & then
press Return Arrow button.
Press the RIGHT ARROW Button to move onto the next Page.
4.3 Setting Low Pressure Time Delay
Low pressure time will now be displayed.
The Cursor will be flashing under the first digit of the LOW PRESSURE TIME
setting. Simply type in the appropriate delay time you want after the low
pressure set point has been reached, example 45sec Press 0, press 0, press
4, Press 5, & then press Return Arrow button.
Press the RIGHT ARROW Button to move onto the next Page.
4.4 Set point Pressure Setting
Set point pressure will now be displayed.
The Cursor will be flashing under the first digit of the SETPOINT PRESSURE
setting. Simply type in the appropriate pressure you want the pumps to
maintain the System at, example 400kPa Press 4, press 0, press 0 & then
press Return Arrow button.
Press the RIGHT ARROW Button to move onto the next Page.

PVJ3 page 9
9
4.5 Start Pressure Setting
Start pressure will now be displayed.
The Cursor will be flashing under the first digit of the START PRESSURE
setting. Simply type in the appropriate pressure you want the Pump to restart
at once it has gone to sleep, example 375kPa Press 3, press 7, press 5 &
then press Return Arrow button.
Press the RIGHT ARROW Button to move onto the next Page.
4.6 Pump Stop Minimum Speed Setting
Pump Stop Minimum Speed will now be displayed.
The Cursor will be flashing under the first digit of the PUMP STOP MINIMUM
SPEED setting. The pump stop minimum speed is the speed at which the
standby pump is turned off after the duty pump has reached the pump stop
minimum speed plus a short time delay. This set point is critical to be set
correctly so as to prevent short cycling.
To set the Pump stop Min Speed you must first operate 1-off pump in
manual with a closed discharge to find out the pump speed required to
maintain set point pressure. Add 2% to ensure the system will get to the
setpoint. This speed value is then entered. Example say 67%. Press 6,
press 7, the Return arrow button to accept.
Press the RIGHT ARROW Button to move onto the next Page.
4.7 Sleep Shutdown Time Setting
Sleep Shutdown Time will now be displayed.
The Cursor will be flashing under the first digit of the SLEEP SHUTDOWN
TIME setting. Simply type in the appropriate time value in minutes & seconds
you want the duty pump to run on for before going to sleep, example
20seconds Press 0, press 0, press 2, press 0 & then press Return Arrow
button.
Press the RIGHT ARROW Button to move onto the next Page.
4.8 Standby Start Time Setting
Standby Start Time will now be displayed.
The Cursor will be flashing under the first digit of the STANDBY START TIME
setting. Simply type in the appropriate time value in minutes & seconds you
want the standby pump to be delayed from starting once the Standby Start
Speed has been reached, example 20seconds Press 0, press 0, press 2,
press 0 & then press Return Arrow button.
Press the RIGHT ARROW Button to move onto the next Page.

PVJ3 page 10
10
4.9 Standby Stop Time Setting
Standby Stop Time will now be displayed.
The Cursor will be flashing under the first digit of the STANDBY STOP TIME
setting. Simply type in the appropriate time value in minutes & seconds you
want the standby pump to be delayed from stopping once the Standby Stop
Speed has been reached, example 20seconds Press 0, press 0, press 2,
press 0 & then press Return Arrow button.
Press the RIGHT ARROW Button to move onto the next Page.
4.10 2nd Standby Start Time Setting
2nd Standby Start Time will now be displayed.
The Cursor will be flashing under the first digit of the 2nd STANDBY START
TIME setting. Simply type in the appropriate time value in minutes & seconds
you want the 2nd standby pump to be delayed from starting once the Standby
Start Speed has been reached, example 20seconds Press 0, press 0, press 2,
press 0 & then press Return Arrow button.
Press the RIGHT ARROW Button to move onto the next Page.
4.11 2nd Standby Stop Time Setting
2nd Standby Stop Time will now be displayed.
The Cursor will be flashing under the first digit of the 2nd STANDBY STOP
TIME setting. Simply type in the appropriate time value in minutes & seconds
you want the 2nd standby pump to be delayed from stopping once the Standby
Stop Speed has been reached, example 20seconds Press 0, press 0, press 2,
press 0 & then press Return Arrow button.
Press the RIGHT ARROW Button to move onto the next Page.
You will now be returned to the main screen.
4.12 Maximum Continuous Running Time
This setting allows you to limit the total continuous running time of either pump
to a maximum of 24 hours before alternating to the opposite pump. This
function is only available if both pumps are selected in AUTO.
4.13 Hours Run Meters
To view ‘hours run’press the FUNCTION (Up arrow) button. The first two
pump hours run meters will be displayed. Press the function button again will
transfer you to the Data logger.
4.14 Data Logger
The data logger logs the last 6 fault events which are number from 1-6 &
display the fault the time of the fault & the date of the fault to view the logger
you enter via the hour meters, press the FUNCTION (Up arrow) button. The
first two pump hours run meters will be displayed. Press the function button
again & the 3rd pump hours run meter is displayed, press the function button

PVJ3 page 11
11
again & the logger will be displayed. Press the down arrow to run through the
last 6 logged events.
Press the function button to return to the main page.
4.15 Auto Tuning
After setting all the calibration setting above (which may need small
adjustments once auto tuning has been carried out), carry out an auto tune
which will set up the controller PID parameters to suit the live input from the
field pressure transducer.
It is critical that the following is observed: -
1) Make shore pump is running at set point pressure & is not wanting to call
other pump online.
2) Use only one pump in automatic, Turn the remainder off.
Auto tuning takes from 5 to 20 seconds & is a three stage process.
To carry out an auto tune ensure that 1-off selector is in auto, press& hold the
LEFT ARROW button for 5seconds the display will flash AUTO-TUNE IN
PROGRESS until auto tune is complete. During this time you cannot access
other screens.

PVJ3 page 12
12
5 Operation
5.1 System Operation
The system is designed to maintain a constant pressure in the discharge line
of a pumping system. The duty pump will start & ramp up & down in speed
maintaining the set point pressure until this duty pump reaches & maintains
100% speed for a short time delay. At this point the standby pump will start.
Both pumps will then ramp up & down maintaining the set point pressure until
the pumps reach & maintains (Standby stop speed) for a short time delay. At
this point the standby pump will be turned off & the duty pump will take over
by itself.
The duty pump will then ramp up & down to maintain the set point pressure
until this pump reaches & maintains the pump stop criteria plus a delay set in
(pump shutdown delay) & will then turn off stopping all pump operation until
the wake-up pressure is again reached.
The pressure will fall to the wake-up pressure set point where the duty pump
will then start the cycle once again.
Each time the system goes to sleep the duty pump will be alternated to the
next pump ready for the next operation.
If a motor fails the standby pump will be started & will remain as duty until the
faulted pump is put back on line.
Pump Stop Criteria
Duty Pump –The duty pump requires 3 things to shut down-
1. The system pressure has reached & maintains set point pressure less
5kPa.
2. The motor speed is less & maintains less than the speed set in PUMP
STOP MINIMUM SPEED.
3. And the time value entered into LOW STOP TIMER parameter has timed
out.
Standby Pump –The standby pump requires 3 things to shut down-
1. The system pressure has reached & maintains set point pressure less
5kPa.
2. The motor speed is less & maintains less than the speed set in PUMP
STOP MINIMUM SPEED.
3. And the time value entered into parameter STANDBY STOP TIMER.

PVJ3 page 13
13
5.2 Manual/Off/Auto Selector Switches
Each pump has a Manual/Off/Auto selector switch. Each function of the switch
is selected by operating the appropriate selector on the Panel facia.
Manual Selecting MANUAL will turn the pump on continuously at a fixed
full speed.
Off Selecting OFF will turn the pump off.
Auto Selecting AUTO will select the pump on automatic & is then
controlled via the set points within the PVJ3 controller.

PVJ3 page 14
14
6.0 Warranty Statement
The Products manufactured by Inca Control Pty Ltd is guaranteed against faulty
workmanship for a period of 12months from the date of delivery.
Our obligation assumed under this guarantee is limited to the replacement of parts
which, by our examination are proved to be defective & have not been misused,
carelessly handled, defaced or damaged. This guarantee is VOID where the
purchaser has modified or repairs have been made or attempted by anyone except
an authorised representative of Inca Control Pty Ltd.
Products for attention under guarantee (unless otherwise agreed) must be returned
to the factory freight paid and, if accepted for free repair, will be returned to the
customers address in Australia free of charge.
Equipment supplied by Inca Control Pty Ltd, but manufactured by others is covered
by their manufacturers warranty only.
When returning the product for service or repair, a full description of the fault must
be given and the mode of operation used when the product failed.
In addition to the above, equipment manufactured, installed & commissioned by
Inca Control Pty Ltd, within the Sydney Metropolitan Area, includes onsite
replacement.
In any event Inca Control Pty Ltd has no other obligation or liability beyond
replacement or repair of this product.
NOTES:
Table of contents
Other Inca Control Panel manuals
Popular Control Panel manuals by other brands
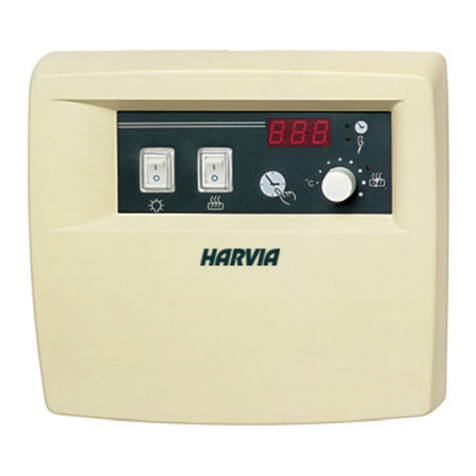
Harvia
Harvia C90 quick start guide
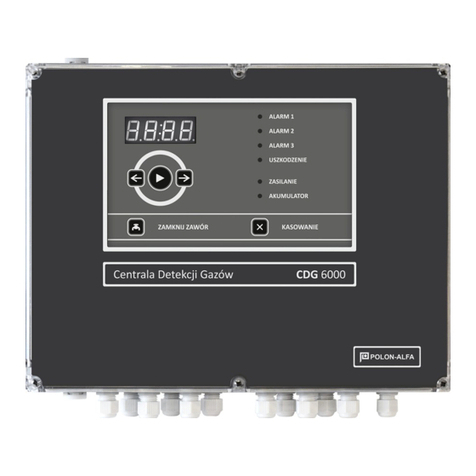
Polon-Alfa
Polon-Alfa CDG 6000 Operation and Maintenance Documentation
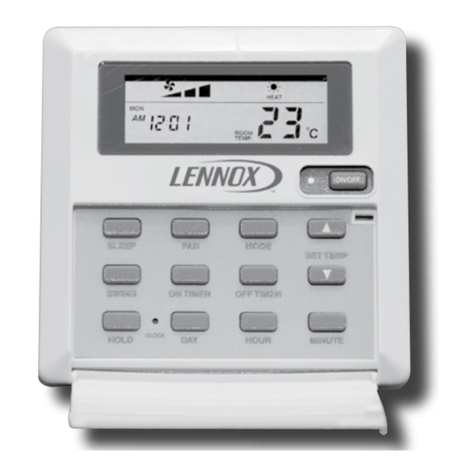
Lennox
Lennox OLT-1X user manual
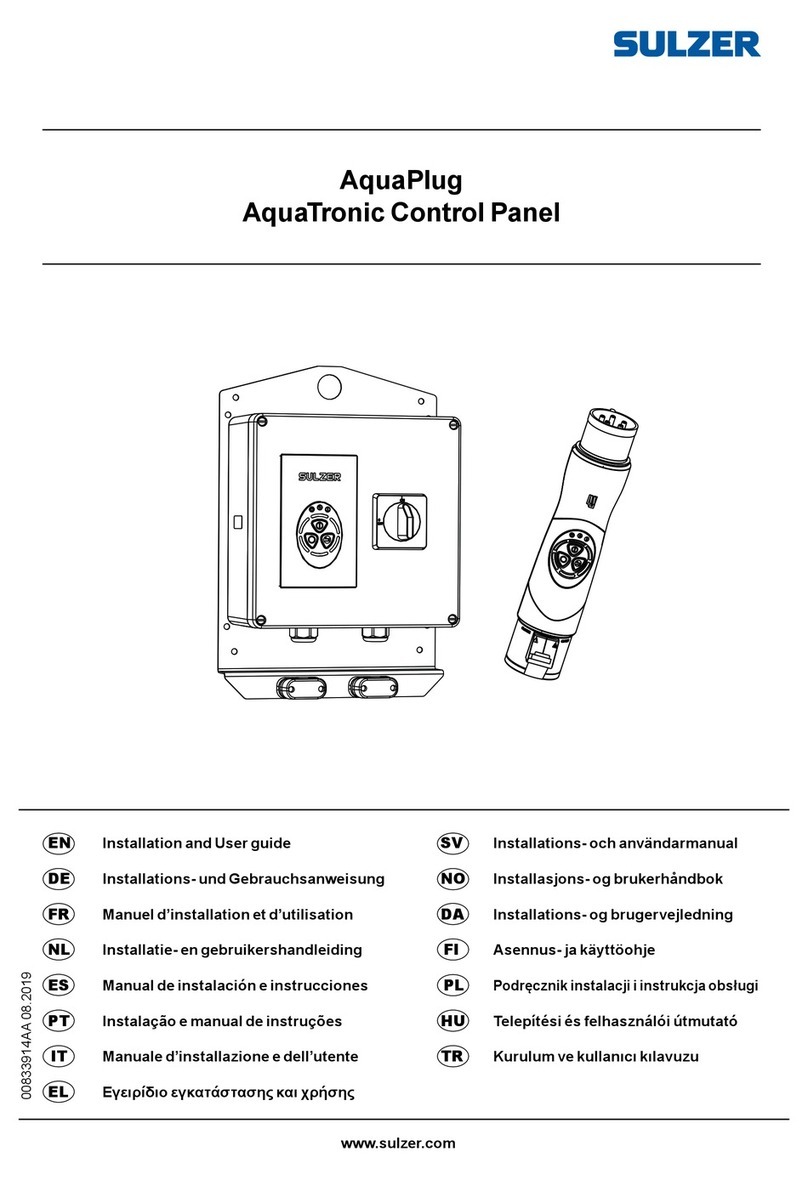
Sulzer
Sulzer AquaTronic Control Panel Installation and user guide

Johnson Controls
Johnson Controls FC-2000 Installing

JCM Technologies
JCM Technologies ROLL868 DMR quick start guide