INDELAC CONTROLS 22018-DH Instruction manual


PART #22018-DH - High-Resolution Positioner
Page 2
INTRODUCTION:
The Indelac 22018-DH, also known as DHC-400,
is a high performance digital positioner intended
to control DC actuators, providing 450 points of
resolution with quarter turn actuators ranging
from 2 sec to 120 sec. The DHC-400 has many
automatic advanced features that will enhance
any actuator while making it easy to install and
set up. The DHC-400 can replace a DMC-100
standard size controller in most applications to
upgrade performance.
The simple three button control is used to
configure all parameters the unit needs for a wide
variety of applications, and allows the open and
closed positions to be easily set for direct or
reversing acting without any rewiring. The unit
can be configured for various command types (4-20mA, 1-5V, 0-5V, 0-10V, 2-10V, or a digital
command) and its default operation upon loss of command. The multicolor LED Fault indication
displays up to 15 different conditions (including "Low Battery Voltage").
Various option modules are easily plugged into the unit, providing other features such as a position
feedback signal, auxiliary switches, fault relay contact, or digital communications. A wide range of
data is accessible through a digital communications module, providing additional control or
information.
ADDITIONAL FEATURES:
10 to 30 VDC operatingvoltage range with motors rated up to 60A locked rotor or 10A running
current.
Solid state motor driver with thermal and overcurrent protection provides reliable service
beyond the life of the actuator motor.
Positions to ±0.1° with quarter-turn actuators ranging from 2 sec to 120 sec (with or without
a mechanical brake). Electronic Brake feature can eliminate mechanical brake.
Adaptive Control feature continuouslyadjusts for load and actuator conditions and eliminates
calibration procedures and auto-cal operations.
Polarity Detection feature allows direct or reverse acting operation without re-wiring.
Stall Detection feature protects actuator motor from a stall condition.
Adjustable Motor Current Trip (0-12A) setting limits actuator torque and battery/power supply
current requirements.
Electronic Surge Limiting reduces wire size and battery/power supply requirements to 20%
of locked rotor current.
Automatic Duty Cycle Control feature prevents motor damage due to overheating and
prevents shutdown of a process due to a thermal overload switch.
Operating temperature range of 0 to 60°C

PART #22018-DH - High-Resolution Positioner
Page 3
BOARD OUTLINE:

PART #22018-DH - High-Resolution Positioner
Page 4
BLOCK DIAGRAM:
DESCRIPTION:
The DHC-400 is rated for motors with up to 60A locked rotor or 10A running currents and has an
operating voltage range from 10VDC to 30VDC. The unit is easily mounted with 2 screws and is
equipped with removable screw terminals that provide for easy field wiring. The unit's size and
mounting allows the DHC-400 to replace the DMC-100 series controllers in most applications with
minimal rewiring.
The simple three button control (MODE, ▲, and ▼) allows the user to perform a complete set-up
from the unit itself without the need for any instrumentation. The adaptive control feature of the
DHC-400 eliminates the need for any calibration steps. In the simplest application, only the closed
and open positions need to be set and the unit automatically and continuously sets all other
parameters when placed in the AUTO mode.

PART #22018-DH - High-Resolution Positioner
Page 5
POWER / SIGNAL: (J2):
The positive terminal of the DC power source is connected to pin 1 while the negative terminal
connects to pin 2. When the DHC-400 is mounted to a metal bracket or directly to the actuator case,
pin 3 provides a terminal for an earth ground connection to the actuator body. In applications where
the actuator body is non-metallic or is electrically isolated from earth ground, pin 3 must be
connected to earth ground to prevent static voltage buildups.
Transferring DC power can be inefficient, therefore care should be taken to use appropriate wire
sizes. The size wire required depends on the locked rotor motor current and the length of wire to be
used. See the Wire Table for more information.
An appropriate command signal, either 0-5V, 0-10V, 1-5V, 2-10V, or 4-20mA, should be connected
to pin 5 (as shown in the Block Diagram) while using pin 4 as the return signal ground. See Wiring
Diagrams, Input Configurations, for wiring details. The DHC-400 must be configured for the type of
command signal that is to be used (see COMMAND TYPE).
Pin 6 of J2 provides an auxiliary +5V output which can be used to connect a command
potentiometer. By connecting one end of a potentiometer to pin 6, the other end to pin 4, and the
wiper to pin 5, a local control knob can be implemented. Pin 4 will also need to be connected to pin
2 (BAT NEG) for this application.
ACTUATOR (J1):
The actuator motor and feedback potentiometer are connected to J1 as shown in the Block Diagram.
The feedback potentiometer wiper must be connected to pin 5, while one end is connected to pin 4
and the other end to pin 6. The Polarity Detection feature of the DHC-400 automatically determines
which polarity to apply to the motor based on where the open and closed positions are set; this
feature also eliminates the need to rewire the unit for direct or reverse acting applications.
Many actuators include limit switches that are used to turn off the motor when the extreme ends of
travel have been reached. Limit switches should be wired to pins 6, 7, and 8 as shown in the Block
Diagram. If limit switches are not used, pins 7 and 8 must be connected to pin 6 (note, if pins 7 and
8 are not connected to pin 6, the DHC-400 will not be able to control the motor outputs).
When the ▲ and ▼ buttons are used to control the actuator, the ▲ button will connect pin 4
(MOTOR 1) to BAT POS (J2-1) and pin 5 (MOTOR 2) to BAT NEG (J2-2) as long as pin 7 (LIMIT
SW1) is connected to pin 6 (LIMIT COMMON). Likewise, the ▼ button will connect pin 5 to BAT
POS and pin 4 to BAT NEG as long as pin 8 (LIMIT SW2) is connected to LIMIT COMMON.
Since pins 4 and 5 are alternately connected to BAT POS (J2-1) and BAT NEG (J2-2), care should
be taken not to connect the motor output pins to any other terminals. See MANUAL/FB POT CAL
for more details.
The DHC-400 provides a dynamic braking feature that can eliminate the need for a separate brake.
When the DHC-400 turns off the motor outputs, pins 4 and 5 are internally connected to the BAT
NEG pin (J2-2); this has the effect of shorting the motor leads together, thus braking the motor

PART #22018-DH - High-Resolution Positioner
Page 6
motion. When power is removed from the DHC-400, the electronic braking feature is disabled. In
some applications, a brake is required for mechanical reasons, such as avoiding back driving the
motor; the DHC-400 is suitable for powering most brakes, however, consult the actuator
manufacturer for more information.
OVERRIDE (J7):
J7 provides a simple 2-wire connection that can override the DHC-400 to perform a variety of
external control functions. Using an appropriate interface module, commonly used auto/manual
station switches are easily implemented with low voltage/low current switches. See Special
Applications for more details. The factory installed jumper between pins 1 and 2 enables normal
operation of the DHC-400 and must be installed if the external override functions are not used.
MODE:
The MODE button is used to select the desired function of operation. When the MODE button is
pressed, the unit will switch to the next function and the appropriate LED indicator will turn on to let
the user know which function is selected. Except for the MANUAL/FB POT CAL mode, the
associated mode indicator will be steady on; for some of the modes other indicators will flash to
indicate specific settings associated with the mode. Each of the modes are described in more detail
in the following sections.
If a 0-5V or 0-10V command signal is used, the LOSS OF COMMAND function cannot be used. The
MODE button will skip over the LOSS OF COMMAND mode when the unit is configured for a 0-5V
or 0-10V command signal (see COMMAND TYPE). When the OVERRIDE mode is enabled (see
OVERRIDE MODE), the MODE button is disabled and the Manual/Pot Cal indicator will turn on
steady.
ADJUST UP (▲) and ADJUST DOWN (▼):
The adjust up (▲) and adjust down (▼) buttons are used to adjust the setting of any given function.
When a function is selected by the MODE button, the adjust buttons will affect that function only.
Note, that the AUTO mode does not have any adjustable settings, and therefore, the adjust up (▲)
and adjust down (▼) buttons have no effect. Also, the adjust buttons are disabled in the OVERRIDE
mode.
OVERRIDE MODE:
The OVERRIDE mode is not selected by the MODE button and can be enabled at any time by
connecting a resistance greater than 250 ohms to the Override Input (J7 pin 1 and pin 2). While the
OVERRIDE mode is enabled, the MODE button and adjust buttons are disabled, and the
Manual/Pot Cal indicator will turn on steady to indicate that the unit is being controlled by the
Override Input. Shorting J7 pin 1 to pin 2 returns the unit to normal operation and the previously
selected mode.

PART #22018-DH - High-Resolution Positioner
Page 7
Controlling the DHC-400 from the Override Input is accomplished by connecting a specific
resistance to select a specific operation. The table belowdefines the operations and their associated
resistance. See Special Applications for details on using the Override Input for an Auto/Manual
Station.
RESISTANCE OPERATION
> 4.3K ohms OFF
3.3K ohms ±5% LATCH
2K ohms ±5% OPEN
1.2K ohms ±5% CLOSE
510 ohms ±5% STOP
The OPEN function will operate the motor in the open direction as set by the OPEN mode, while
the CLOSE function operates the motor in the closed direction as set by the CLOSE mode. The
LATCH function will maintain the previously selected function; this allows momentary switches to
be used for the OPEN and CLOSE functions. The OFF and STOP functions turn the motor off, which
also unlatches the OPEN or CLOSE functions.
Note that the OPEN and CLOSE functions may work in reverse until the open and closed positions
are set by the OPEN and CLOSE modes. The DHC-400 will automatically turn the motor off when
the open or closed positions are reached. However, if a feedback fault occurs (see FAULT
INDICATOR), the motor will be turned on for a period of 15 minutes in the selected direction. For
this reason, limit switches should be used when using the OVERRIDE mode, and should be set to
a position acceptable for the application. The 15 minute period can also be terminated using the
OFF or STOP function.
The motor is also automatically turned off if the DHC-400 detects a stall (see STALL DETECTION).
An OPEN or CLOSE operation can be attempted again after switching to the OFF, LATCH, or STOP
functions first.
The motor is also turned off if a motor current trip is detected (see TRIP SETTING). If the trip
occurred during an OPEN operation, the OPEN operation is disabled until the trip condition is
corrected. The CLOSE operation may be used to attempt to clear the trip condition (by causing a
certain amount of motion in the closeddirection).Likewise, if atrip occurs duringa CLOSE operation,
the OPEN operation can be used for clearing the trip. If a trip occurs in both directions (i.e., before
the first trip can be cleared), the trip can only be cleared by a mechanical override mechanism, or
by using the MANUAL mode from the DHC-400 front panel, or by powering the DHC-400 down and
back up.

PART #22018-DH - High-Resolution Positioner
Page 8
AUTO:
The AUTO function is the normal mode of operation for the DHC-400; all the other functions are
used to set up the unit. While in AUTO, the unit can be controlled by various external signals, some
of which can be selected by the COMMAND INPUT function. When the unit is not in the AUTO
mode, all external control signals described below will be disabled.
Once the open and closed positions have been set, the AUTO mode will control the position of the
actuator according to the command input signal. For an input signal of 0V (for 0-5V or 0-10V input),
1V (for 1-5V input), 2V (for 2-10V input), 4.0 mA (for 4-20mA input), or 0% (for a digital input), the
DHC-400 will position the actuator to the closed position as set by the user. Conversely, an input of
5V, 10V, 20mA, or 100% will position the actuator to the defined open position.
When the DHC-400 is configured to use a 0-5V, 0-10V, 1-5V, 2-10V, or 4-20mA command, the
command signal should be connected to the appropriate pins on J2. When the DHC-400 is
configured for a Digital command type, an appropriate communications option module must be
installed. A communications module may be installed when using one of the analog command types
and can be used to override the analog command. The AUTO indicator will flash whenever the unit
is being controlled by the communications module.
MANUAL/FB POT CAL:
The MANUAL/FB POT CAL function allows manual operation of the actuator by using the adjust
buttons (▲ and ▼) without affecting any other settings within the DHC-400. When the ▲ button is
pressed, the MOTOR 1 (J1-4) output is connected to BAT POS (J2-1), and the MOTOR 2 (J1-5)
output is connected to BAT NEG (J2-2). The ▼ button connects MOTOR 1 to BAT NEG and
MOTOR 2 to BAT POS. Whether the actuator moves toward the open or closed position depends
on which motor wire is connected to J1-4 and J1-5.
The POT CAL feature provides an indication of the feedback potentiometer's setting. When the
MANUAL/POT CAL function is selected, the Manual/Pot Cal indicator will turn on - it may flash or
be on steady, depending on the actuator position. The indicator will be on steady whenever the
DHC-400 detects that the feedback potentiometer is at midrange of its rotation. As the actuator
moves, causing the feedback potentiometer to move away from midrange, the indicator will begin
to flash, and the indicator will flash at a decreasingly slower rate as the actuator moves further away
from midrange.
By using the adjustbuttons to position theactuator to mid-stroke (half way point between the desired
open and closed positions), the feedback potentiometer can then be adjusted until a steady light
occurs. This insures that the feedback potentiometer has maximum range to reach the open and
closed positions.
CLOSE:
The CLOSE function is used to set the desired closed position; however, prior to doing this, the
feedback potentiometer should be checked for optimum position (see MANUAL/POT CAL), and the
limit switches should be set outside of the operating range (see LIMIT SWITCHES). In the CLOSE

PART #22018-DH - High-Resolution Positioner
Page 9
function, the adjust buttons are used to set the actuator to any desired position, and upon pressing
the MODE button (to select the next function, OPEN), the DHC-400 will retain the setting as the
defined closed position.
Upon selecting the CLOSE function, the DHC-400 will begin moving the actuator to the previously
set closed position; it is not necessary to make an adjustment if the unit has been previously set to
the desired position. A command signal input of 0V, 1V, 2V, 4mA, or 0% automatically corresponds
to the defined closed position.
OPEN:
The OPEN function works the same way as the CLOSE function with the exception that the adjust
buttons are used to set the desired open position. As with the CLOSE function, upon selecting the
OPEN function, the actuator will move to the previously set open position. Once the desired position
is set, the DHC-400 will automatically associate a command signal input of 5V, 10V, 20mA, or 100%
to the open position.
AUX CLOSE OUTPUT:
The AUX CLOSE OUTPUT function is used to set an optional output setting that is associated with
the closed position - an appropriate relay option module is required to use this output. The adjust
buttons are used to set the actuator to a desired position. Whenever the actuator position falls
between the defined closed position and the Aux Close position, the Aux Close Output indicator will
flash. Additionally, the DHC-400 will turn on a relay output on the optional relay module - the output
can be used to drive an alarm or merely act as an auxiliary limit switch.
Upon selecting the AUX CLOSE OUTPUT function, the DHC-400 will begin moving the actuator to
the previously set position. It is not necessary to make an adjustment if the unit has been previously
set to the desired position.
AUX OPEN OUTPUT:
The AUX OPEN OUTPUT function is used to set an optional output setting that is associated with
the open position - an appropriate relay option module is required to use this output. The adjust
buttons are used to set the actuator to a desired position. Whenever the actuator position falls
between the defined open position and the Aux Open position, the Aux Open Output indicator will
flash. Additionally, the DHC-400 will turn on a relay output on the optional relay module - the output
can be used to drive an alarm or merely act as an auxiliary limit switch.
Upon selecting the AUX OPEN OUTPUT function, the DHC-400 will begin moving the actuator to
the previously set position. It is not necessary to make an adjustment if the unit has been previously
set to the desired position.

PART #22018-DH - High-Resolution Positioner
Page 10
COMMAND TYPE:
The COMMAND TYPE function is used to configure the command signal input for either 4-20mA,
1-5V, 0-5V, 0-10V, 2-10V, or digital so as to match the type of command signal being used. Upon
selecting the COMMAND TYPE function, the Command Input indicator will turn on steady, while the
indicator for the selected type will flash. Use the adjust buttons (▲ or ▼) to select the desired input
type. The selection will be saved when the MODE button is pressed, which will also advance the
unit to the LOSS OF COMMAND function.
LOSS OF COMMAND:
When using 1-5V, 2-10V, 4-20mA, or a Digital input type for the command signal, the DHC-400 will
detect when the command signal is lost or out of range. A loss of command condition is detected
whenever the input is disconnected, the input becomes less than 0.75V (for 1-5V input), 1.5V (for
2-10V input) or 3mA, or the input is connected backwards. An out of range condition is detected
whenever the input becomes greater than 5.25V (for 1-5V input), 10.5V (for 2-10V input), or 21mA.
If the DHC-400 detects a loss of command, a fault will be indicated (see FAULT INDICATORS), and
the actuator will be moved to one of three preset positions: the open position, the closed position,
or the position last attained prior to losing the command signal. The LOSS OF COMMAND function
is used to set the desired default position.
When the LOSS OF COMMAND function is selected, the adjust buttons are used to set the default
position. The DHC-400 indicates the selected default setting by flashing the Open function indicator
for the open default position, or it will flash the Close function indicator for the closed default position.
When neither indicator is on, then the "last position" default is selected.
When a 0-5V or 0-10V command signal is used, a loss of command signal cannot be reliably
detected. Therefore, if the unit is configured for a 0-5V or 0-10V command signal (see COMMAND
INPUT), the MODE button will not select the LOSS OF COMMAND function. However, the DHC-
400 can detect when a 0-5V or 0-10V command signal is out of range (i.e., greater than 5.25V or
greater than 10.5V) or connected backwards. When an out of range condition is detected for a 0-
5V or 0-10V input, the motor is turned off (leaving the actuator in its "last position") and a fault will
be indicated (see FAULT INDICATORS).
POSITION OUT CAL:
The POSITION OUT CAL function is used to calibrate an optional feedback transmitter output. An
appropriate transmitter option module is required to use this feature. When the POSITION OUT
CAL function is first selected (by pressing the MODE button while in the LOSS OF COMMAND
function), the CLOSE indicator will flash, and the current associated with the closed position will
appear at the option module output. If desired, the output can be adjusted (using the adjust buttons)
to any value from 4 to 20mA. The new setting is saved when the MODE button is pressed.
Pressing the MODE button will leave the unit in the POSITION OUT CAL function except that the
OPEN indicator will flash, and the output current associated with the open position will appear at
the option module output. Like the closed setting, the output can be adjusted to any current from 4

PART #22018-DH - High-Resolution Positioner
Page 11
to 20mA. The new setting is saved when the MODE button is pressed, which also selects the AUTO
mode.
FAULT INDICATORS:
The DHC-400 detects various fault conditions that prohibit the unit from controlling the actuator. A
combination of the three Fault indicators (red, yellow, and green) will turn on or flash to indicate a
specific detected fault. If an appropriate relay option module is installed, the Fault relay output on
the option module will turn off (indicating a fault) when any of the Fault indicators turn on or flash. A
communications option module can also read the specific conditions causing a fault. Note that a
fault condition DOES NOT disable the motor outputs when manually controlling the actuator with
the adjust buttons; while useful for troubleshooting, care should be exercised when operating the
motor under a fault condition. The OVERRIDE mode can also operate the motor when a fault
condition exists - see OVERRIDE MODE for details.
Note that the indicators may not indicate all the fault conditions that may exist. This means that
when the indicated fault is corrected, the unit may display another fault that has not been corrected.
The table below provides a summary of the Fault indications which is followed by a description of
each fault.
RED YEL GRN FAULT
flash OFF OFF Low Battery Voltage
flash flash OFF Motor 1 Stall
flash OFF flash Motor 2 Stall
flash flash flash Double Stall
flash ON OFF Motor 1 Current Trip
flash OFF ON Motor 2 Current Trip
flash ON ON Double Current Trip
ON OFF OFF Battery Over Voltage
ON flash OFF Motor 1 No Motion
ON OFF flash Motor 2 No Motion
ON flash flash Double No Motion
OFF OFF flash Feedback Alarm
OFF flash OFF Loss of Command
OFF ON OFF Command Out of Range
OFF flash flash Feedback Alarm and Loss of Command
OFF ON flash Feedback Alarm and Command Out of Range

PART #22018-DH - High-Resolution Positioner
Page 12
Low Battery Voltage - When the DHC-400 detects that the battery/power supply voltage connected
to BAT POS (J2-1) and BAT NEG (J2-2) drops below 10V, the motor outputs are turned off and the
DHC-400 suspends all other operations until the voltage returns to 10V or more. However, the Low
Battery Voltage fault indication will maintain for 3 seconds after voltage returns. Since DC motors
present a large load (from in-rush currents) when turned on, a weak battery or insufficient power
supply may experience a short voltage drop below 10V until the motor begins to move. Therefore,
the Low Battery Voltage indication provides warning of batteries in need of recharge or power
supplies that have insufficient current for the application.
Motor 1 Stall - A stall condition is detected when no actuator motion is detected while the Motor 1
output is turned on and drawing more than 0.5A of motor current. The fault condition will disable the
Motor 1 output only, and the fault is cleared when the DHC-400 detects a motion greater than 1.5°
in either direction. The fault canbe cleared if 1) the command signal commands a Motor 2 operation,
2) manual operation with the adjust buttons results in a motion greater than 1.5°, or 3) a mechanical
manual override forces the 1.5° motion, provided the mechanical motion is monitored by the
feedback pot.
Motor 2 Stall - A stall is detected when no actuator motion is detected while the Motor 2 output is
turned on and drawing more than 0.5A of motor current. The fault can be cleared in the same
manner as previously described for a Motor 1 Stall.
Double Stall - If the DHC-400 detects a stall condition in both directions, both motor outputs will be
disabled. The command signal cannot clear this condition; only manual operation or a mechanical
override can clear the fault. Alternatively, the DHC-400 can be powered off and then on to
temporarily clear the fault; however, this practice should be avoided without permanently correcting
the cause of such a fault.
Motor 1 Current Trip - A current trip fault is detected when the motor current exceeds the current
trip setting (see TRIP SETTING) while the Motor 1 output is turned on. The fault can be cleared in
the same manner as previously described for a Motor 1 Stall. NOTE: Successive attempts with
manual operation using the adjust buttons can exceed the torque limit set by the Trip Setting.
Motor 2 Current Trip - A current trip fault is detected when the motor current exceeds the current
trip setting (see TRIP SETTING) while the Motor 2 output is turned on. The fault can be cleared in
the same manner as previously described for a Motor 1 Current Trip.
Double Current Trip - If the DHC-400 detects a current trip fault in both directions, both motor
outputs will be disabled. The fault can be cleared in the same manner as previously described for a
Double Stall.
Battery Over Voltage - Other inductive loads (such as motors or solenoids) sharing the
battery/power supply connected to BAT POS (J2-1) and BAT NEG (J2-2) can generate short
transient voltages that may cause the supply voltage to exceed 30V. To prevent damage to the
DHC-400 or the actuator motor, the motor outputs are turned off whenever the supply voltage
exceeds 30V. Upon detecting a voltage above 30V, the Battery Over Voltage fault indication will
turn on and will maintain for 3 seconds after voltage returns. If an over voltage condition lasts less
than 1 second, the Fault relay output will not turn off. If the Fault relay output turns off (indicating an
over voltage lasting longer than 1 second), the output will turn back on when the voltage returns to

PART #22018-DH - High-Resolution Positioner
Page 13
30V or less. Note, earlier versions of the DHC-400 may not have this feature. Contact Indelac, Inc.
for more information.
WARNING! Exposing the DHC-400 to frequent or continuous voltages above 30V can damage the
unit. The user should take steps to suppress or eliminate possible supply voltage conditions above
30V.
Motor 1 No Motion - A no motion fault is detected when no actuator motion is detected while the
Motor 1 output is turned on and drawing less than 0.5A of motor current. The fault can be cleared
in the same manner as previously described for a Motor 1 Stall. A stall usually indicates a heavy
mechanical load or stall, while a no motion fault usually indicates a broken motor wire or disengaged
feedback pot. Note that a stall cannot be detected in applications using very small motors (locked
rotor currents less than 0.5A); only a no motion fault can be detected.
Motor 2 No Motion - A no motion fault is detected when no actuator motion is detected while the
Motor 2 output is turned on and drawing less than 0.5A of motor current. The fault can be cleared
in the same manner as previously described for a Motor 1 Stall. A no motion fault differs from a stall
as previously describe for a Motor 1 No Motion fault.
Double No Motion - If the DHC-400 detects a no motion fault in both directions, both motor outputs
will be disabled. The fault can be cleared in the same manner as previously described for a Double
Stall.
Feedback Alarm - A fault condition is detected whenever the feedback signal is out of range (that
is, less than 5% of the potentiometer value or more than 95% of the potentiometer value), or when
any of the potentiometer connections are broken. Normal operation resumes when the
potentiometer is reconnected or back in range.
Loss of Command - If the command signal is disconnected, the fault indication will remain on until
the signal is reconnected. See LOSS OF COMMAND for details.
Command Out of Range - If the command signal goes out of range, the fault indication will remain
on until the signal is back in range. See LOSS OF COMMAND for details.
LIMIT SWITCHES:
The actuator's limit switches should be connected to J1 as described in ACTUATOR (J1) - also see
OUTLINE and BLOCK DIAGRAM. The limit switches must be closed throughout the operating range
from closed to open. When Limit Switch 1 opens, Motor 1 operations are disabled. Likewise, when
Limit Switch 2 opens, Motor 2 operations are disabled.
Note that the actuator's limit switches should be set outside of the operating range set by the CLOSE
and OPEN functions. Limit switches exhibit wide variations, and the DHC-400 can position the
actuator more precisely at closed and open than the limit switches. A limit switch better serves as a
fail-safe device.
After setting the open and closed positions, the DHC-400 automatically determines which limit
switch is associated with open and closed. When a limit switch is reached, the appropriate indicator

PART #22018-DH - High-Resolution Positioner
Page 14
light (CLOSE or OPEN) will flash. If an appropriate relay option module is installed, the Fault relay
output on the option module will turn off (indicating a fault) when either of the limit switches is
reached.
TRIP SETTING:
The Trip Setting is used to limit the motor current and is set using the TRIP ADJUST pot (see
OUTLINE) as shown below.
The setting should be adjusted to a comfortable level
above the running current expected for the actuator and
its load. When the motor current exceeds the trip setting,
the motor is turned off and a fault condition is indicated
(see FAULT INDICATORS).
While the Electronic Surge Limiting feature of the DHC-
400 reduces the high in-rush currents during motor starts,
the trip setting is used to reduce the current required from
the battery/power supply when the motor stalls or
encounters an excessive load. Without the trip setting, a
costly high capacity battery/power supply would be
needed to avoid collapse of the battery/power supply voltage. The combination of the trip setting
and electronic surge limiting allows the use of a more moderate battery/power supply and smaller
gauge wires for a given length (see WIRE TABLE).
The trip setting essentially performs the same function as commonly used torque switches.
However, it should be noted that the actuator and valve components (gears, couplings, seats, etc.)
also place a load on the motor. These components will vary with temperature and age, and therefore
the torque on the load will vary accordingly.
STALL DETECTION FEATURE:
The Stall Detection feature of the DHC-400 detects when there is no motion after a certain amount
of time while the motor is turned on (see FAULT INDICATORS). This condition can arise if the
motor's stall current is less than the current trip setting (see TRIP SETTING). If the motor current is
greater than 0.5A when no motion is detected, a stall fault is indicated.
When one of the motor wires is disconnected, no motion will be detected, but the motor current will
be zero. Therefore, if the motor current is less than 0.5A when no motion is detected, a no motion
fault is indicated.
If the feedback pot is mechanically disengaged, no motion will be detected, but the motor current
will be the normal running current. Therefore a stall or a no motion fault may be indicated,depending
on whether the running current is greater or less than 0.5A.

PART #22018-DH - High-Resolution Positioner
Page 15
ELECTRONIC BRAKE FEATURE:
The Electronic Brake feature of the DHC-400 provides highly reliable and accurate braking of the
motor, and it is a key element in achieving high resolution. A mechanical brake can still be
implemented without interfering with the DHC-400 operation. The Adaptive Control feature of the
DHC-400 automatically compensates for changes in a mechanical brake's performance due to
temperature or age.
Mechanical brakes can be useful for providing a holding brake in the event power to the actuator is
lost. However, mechanical brakes require time to release on motor start up, and this may cause an
increased surge current that counteracts the Electronic Surge Limiting feature. Also, a mechanical
brake may not release at lower voltages, in which case a stall or current trip fault may occur.
The Electronic Brake feature remains on as long as the DHC-400 is powered. This could make a
mechanical override mechanism difficult to turn. For this reason, the electronic brake is disabled
when the DHC-400 is placed in the Override Mode via J7 (see Special Applications).
CAUTION! When using the DHC-400 with a spring return actuator, the return spring can generate
high electrical energies while back driving the motor that can damage the DHC-400 motor outputs.
In this application, the motor must be disconnected (usually with a relay) from the DHC-400 during
a spring return operation.
DUTY CYCLE CONTROL FEATURE:
The Duty Cycle Control feature of the DHC-400 allows the actuator to be safely used when a
process becomes unstable, a control loop is not properly set, or when the motor is subjected to
excessive loading. The DHC-400 accurately monitors the relative heating of the motor and
automatically duty cycles the unit at a safe level.
The Duty Cycle Control feature allows continuous operation of the motor until it detects an excess
heat buildup in the motor. At that time, duty cycle operation is automatically enabled and continues
until the motor cools enough to resume continuous operation. The dutycycle period is approximately
2 seconds with an on time that automatically varies depending on the heating of the motor. While
this operation slows down the actuator's operation, it does not impact the resolution performance of
the DHC-400, and it allows control of the process to be maintained without damage to the motor.
SPECIFICATIONS:
POWER REQUIREMENTS
Operating Voltage: 10 to 30 VDC
Operating Current, typical: 70mA (not including option module)
Fuse Type: 10A TR5 Time Lag 374 (replaceable)

PART #22018-DH - High-Resolution Positioner
Page 16
COMMAND SIGNAL INPUT
Common Mode Voltage (both inputs): -9 to +30 VDC
Input Impedance
10.25K ohms (1-5 VDC, 0-5 VDC, 0-10 VDC, 2-10 VDC Input)
250 ohms ±1% (4-20 mA Input)
Loss of Command threshold
< 0.75V (1-5 VDC input)
< 1.5V (2-10 VDC input)
< 3mA (4-20mA input)
Command Out of Range threshold
> 5.25V (0-5 VDC, 1-5 VDC input)
> 10.5V (0-10 VDC, 2-10 VDC input)
> 21mA (4-20mA input)A
FEEDBACK SIGNAL INPUT
Input Voltage: 0 to 2.5 VDC
External Feedback Potentiometer: 1K ohm
COMMAND POTENTIOMETER POWER OUTPUT (J2-6)
+5V OUT: 5mA maximum
NOTE: Do not connect this output to other power supplies..
DC MOTOR OUTPUTS
Maximum Running Current: 10 A
Motor Current Trip: 0 to 12 A (adjustable)
Motor Current Measurement Resolution: 85mA typical
ENVIRONMENTAL
Operating Temperature Range: 0 °C to 60 °C
Storage Temperature Range: -40 °C to 85 °C
Relative Humidity Range: 0 to 90 % (noncondensing)
.

PART #22018-DH - High-Resolution Positioner
Page 17
WIRING DIAGRAMS (Output Configurations):

PART #22018-DH - High-Resolution Positioner
Page 18
WIRING DIAGRAMS (Input Configurations):

PART #22018-DH - High-Resolution Positioner
Page 19
WIRING DIAGRAMS (Special Applications):

PART #22018-DH - High-Resolution Positioner
Page 20
WIRING DIAGRAMS (Special Applications):
This manual suits for next models
1
Table of contents
Popular Valve Positioner manuals by other brands
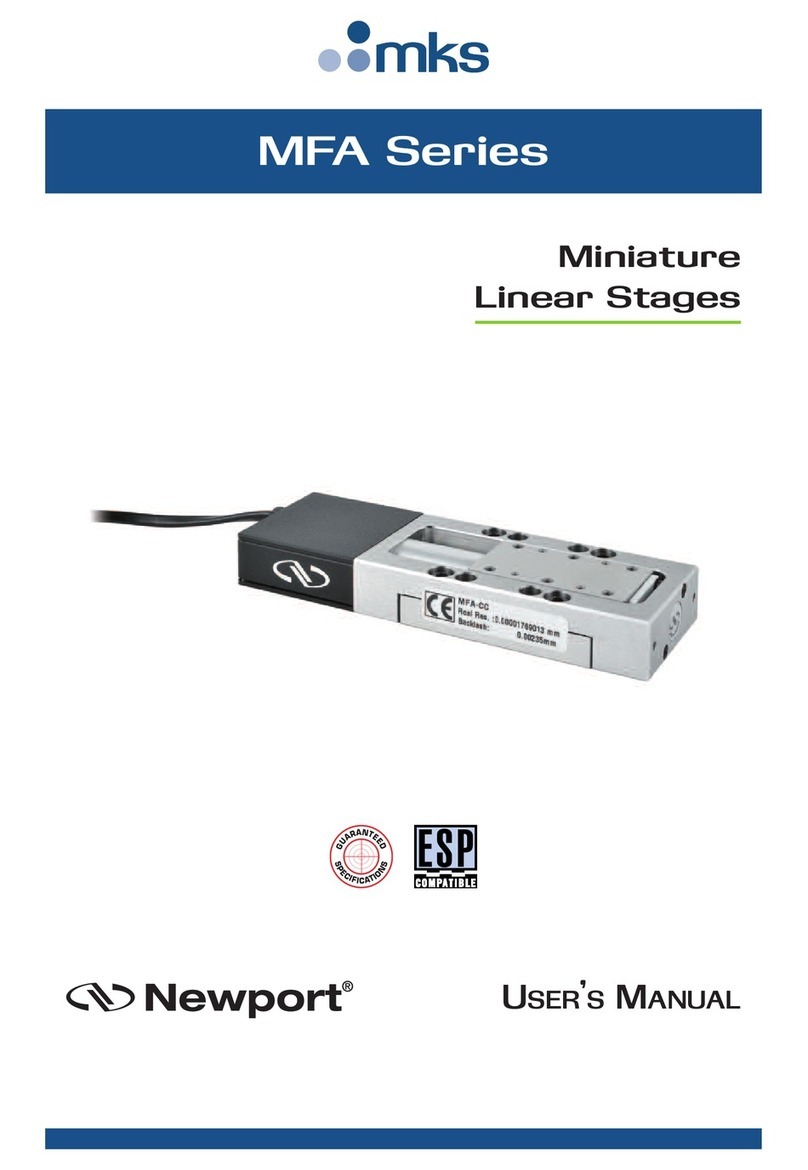
Newport
Newport MFA Series user manual
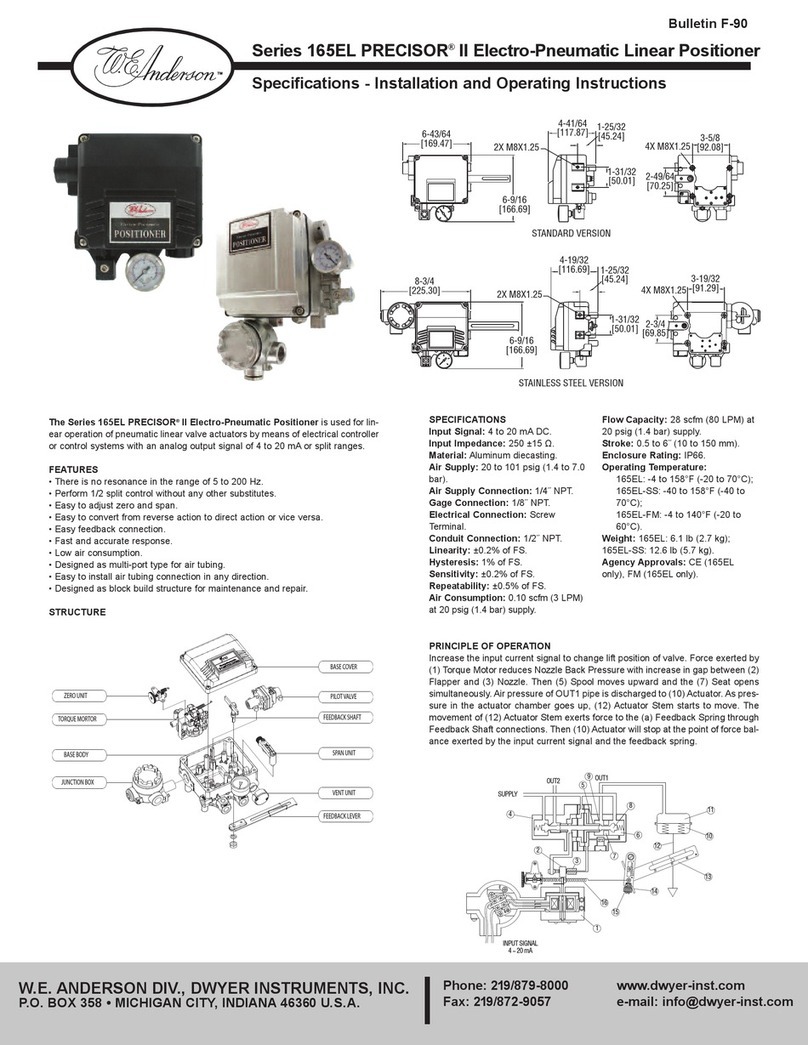
W.E. Anderson
W.E. Anderson PRECISOR II 165EL Series Installation and operating instructions

Baker Hughes
Baker Hughes Masoneilan SVI3 Special instructions
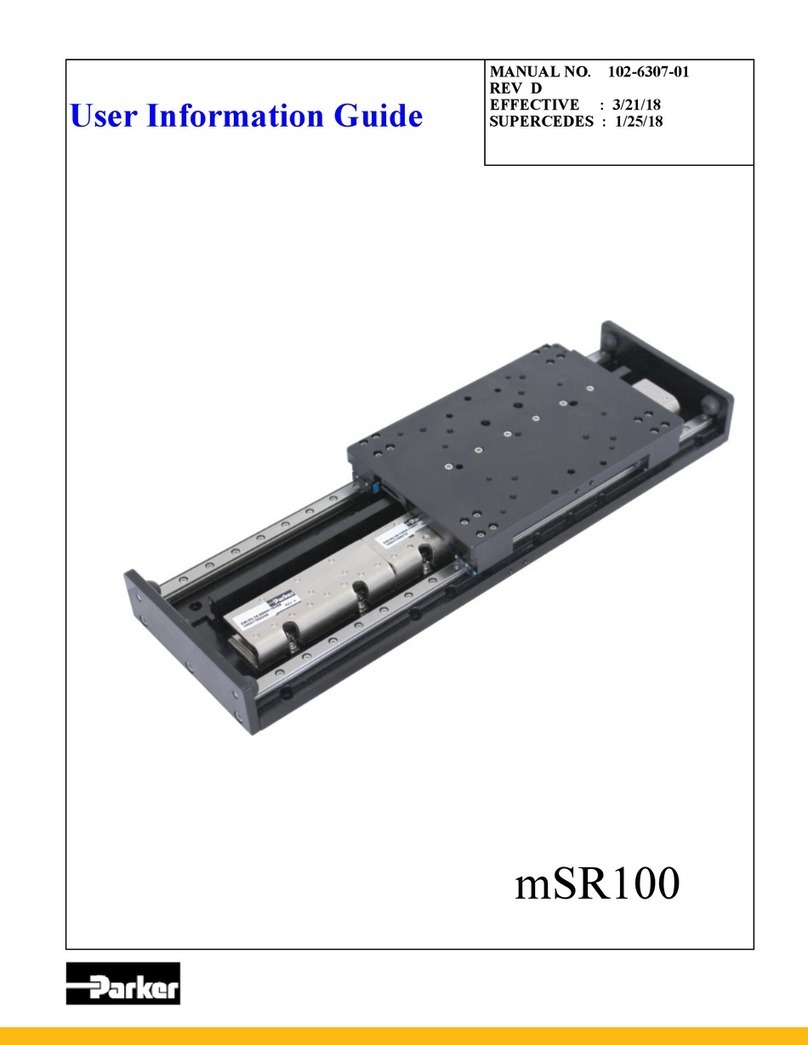
Parker
Parker MSR Series User's information guide
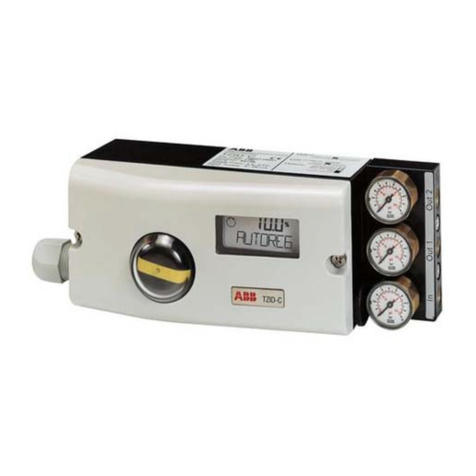
ABB
ABB HART Industrial IT enabled TZIDC operating instructions
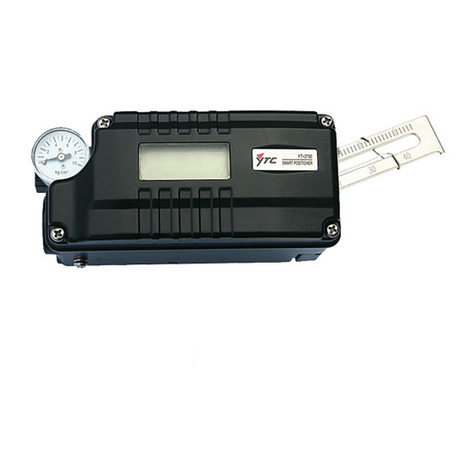
Ytc
Ytc YT-2700L installation manual