InPOWER 1IPSE1A33-60 Guide

TECHNICAL DOCUMENTATION
DIGITAL, PROGRAMMABLE, PLUG & PLAY,
IGBT DRIVER
1IPSE1A33-60
FOR MEDIUM AND HIGH POWER IGBTS
MANUAL
InPower Systems GmbH
Am Kornfeld 11
D-86932 Pürgen, Germany
Tel: +49-(0)8196-93000
Fax: +49-(0)8196-930020
Email: info@inpower-sys.com
VAT-Id: DE 221021830
Prepared by:
Approved by:
Date of publication:
Revision:
Status: production

www.inpower-sys.com 1IPSE1A33-60
TECHNICAL DOCUMENTATION
Preliminary
2
T
ABLE
OF
C
ONTENTS
1. S
AFETY
N
OTICE
3
2. H
ANDLING
AND
M
OUNTING
A
DVICES
4
3. M
AIN
F
EATURES
5
4. M
ECHANICAL
D
IMENSIONS
5
5. K
EY
D
ATA
6
6. I
NTERFACES
6
7. C
OMMISSIONING
S
UPPORT
7
8. I
NPUTS
AND
O
UTPUTS
9
9. C
ONNECTIONS
10
10. LED D
IAGNOSTICS
12
11. E
XCLUSION
C
LAUSE
13

TECHNICAL DOCUMENTATION
3
www.inpower-sys.com 1IPSE1A33-60
Preliminary
SAFETY NOTICE1.
Prior to installation and commissioning please read this document thoroughly.
The driver may only be used for the purposes determined by the manufacturer. Unauthorized alterations
and use of spare parts and accessories not recommend by the manufacturer of the driver can cause re,
electric shock and injuries.
It must be prevented that children and the general public have access to or come into contact with the
installed driver!
This document has to be at the disposal of all users, developers and qualied personnel who are to work
with the driver.
If measurements and tests on the live device have to be carried out, then the regulations of the Safety
Code VBG 4.0 are to be observed, in particular § 8 “Admissible deviations during work on live parts“.
Commissioning is prohibited if there is visible damage•
by inappropriate handling or transport.
Contact while uninstalled is permitted only with ESD•
protection.
Install only without supply voltage.•
Use only suitable electronic devices.•
Always keep sucient safety distance during commis-•
sioning when protective housing is not closed.
Contact under live condition is strictly prohibited.•
CAUTION: All handling with high voltage is at the risk of•
one’s life. Denitely comply with the respective safety
regulations!
Work after turn-o is not admissible until the absence•
of supply voltage has been veried.
During work after turn-o, it must be observed that•
components heat up during operation. Contact with
these can cause burns.
The drivers are mounted electrically and mechanically•
close onto the IGBT module using screws. The mechan-
ical strength has to be veried by the user and, if neces-
sary, assured with appropriate tests.
Any handling of drivers is subject to the specications•
for protecting electrostatic-sensitive devices accord-
ing to the valid international standard (e.g. IEC 747-1,
EN 100015). When ignoring these specications, both
IGBTs and drivers may be destroyed or damaged.

TECHNICAL DOCUMENTATION
4
Preliminary
www.inpower-sys.com 1IPSE1A33-60
HANDLING AND MOUNTING ADVICES2.
Any parasitic inductances within the DC-link are to be avoided or at least minimised.•
As long as the driver main board and the adaptation board are not completely assembled, the inputs•
have to be short-circuited.
Electrostatic discharge (ESD) protection must be provided during handling. ESD is avoided by preven-•
ting the build-up of static electricity. Before opening the boxes, place the them on an ESD protected
workstation. Persons working with devices have to wear their own wrist straps which they should test
before use. Human hands contain oil and this oil can contaminate the contacts and can generate dys-
functions on devices. Therefore, it is recommended to handle a device with protection gloves and al-
ways touch it by the sides.
Humidity is an important factor for the generation of static charges. Humidity between 40 and 60 per•
cent is the best choice for an assembly area.
The input terminals of the main driver board are sensitive to over-voltages. Therefore, please avoid•
over-voltages of the control input signal in order to prevent destruction.
Some driver functions should be checked before installation. Check the gate voltage of the driver for•
the on-state (+15V) and the gate voltage for the o-state (-15V). We also recommend to check the input
current consumption of the driver at the required switching frequency and without clock signals.
The connecting cable between the driver board and the IGBT module should be as short as possible.•
Max. length of coaxial cable should not exceed 30cm. Max. length of simple cable should not exceed
7cm.
For the gate and auxiliary emitter connections it is recommended to use coaxial cable RG58 C/U with•
auxiliary emitter connected to the shielding. For power emitter and auxiliary collector it is recommen-
ded to use HV insulation cable, for instance Radox 9 GKW-AX, 1.5mm, order no. 12 537 829.
The driver should be connected to the control electronics, and feedback status signals should be fed to•
the control circuit. In failure events the device must be turned-o immediately.
When rst operating the assembled circuit we advice to apply a low collector voltage and load current•
in the beginning and then to increase their values step by step, observing the behaviour of the free-
wheeling diode and voltage peaks of the IGBT during turning-o.
Short-circuit tests should not be done until the correct function of the device has been checked under•
rated operation conditions. When executing these tests start with low collector voltage as well.
Observation with an oscilloscope and thermal monitoring will be necessary.•
Do not switch-on the IGBT-module repeatedly into a short circuit. It may destroy the device.•
In applications with parallel connection of IGBT-modules we recommend to check each logical switch•
under power-cycling conditions before starting-up the whole system. Usually it is sucient to switch
with single or double pulses.
As the specic inverter construction determines many parameters, we recommend to check the IGBT•
modules in the worst case conditions to be sure that they are within the SOA.
When testing, please be aware that the gate drivers for all IGBTs of the system must be supplied with•
energy – in order to hold the turn-o stage by applying negative gate voltage – even if only individual
IGBTs are tested.

TECHNICAL DOCUMENTATION
5
www.inpower-sys.com 1IPSE1A33-60
MAIN FEATURES3.
Single channel for dual- and multilevel topology•
Smart switching with variable gate resistors•
Tuned according to the application•
Reliable protection against•
- over-current in all short circuit conditions
- over-voltage during turn-o
Advanced control and protection functions•
- four level desaturation monitoring
- two level di/dt monitoring
- feedback clamping with active function
- multiple soft shut down
- supply voltage monitoring
- digital input lter for switching signals
DC/DC converter included•
Cable connection with adaptation board matched•
for every type of IGBT module
MECHANICAL DIMENSIONS4.

TECHNICAL DOCUMENTATION
6
www.inpower-sys.com 1IPSE1A33-60
KEY DATA5.
Parameter Symbol Value (at +25°C)
Max. collector-emitter voltage VCE 3300V
Input supply voltage range VDC +14 to +30V
Output voltage: ON/OFF voltage VON/VOFF ±15V
Isolation testing voltage (VAC RMS 50Hz / 1 min) VISOL 6000V
Switching frequency (max.) fS max 120kHz
Peak output current IG±70A
Peak output power PDC/DC 3W
Quiescent current typically IDC 0.25A (at 15V)
Max. input current at max. load IDC max 0.50A (at 15V)
Coupling capacitance primary/secondary side (max.) Cio 2pF
Switching frequency of isolated converter fSMPC max 0.5MHz
Creepage distance >30mm
Frequency of logic controller f 20MHz
Operating temperature (measured on driver surface) TOP -40 to +85°C
Storage temperature TST -40 to +85°C
Input driving and output error signal optical 660nm
Turn-on delay time tpdON 400nsec
Turn-o delay time tpdOFF 400nsec
Typical time of soft shut down tSSD 1-2µsec
Max. system time between fault detection and error notication tSYS 100nsec
Time between detection of desaturation and gate voltage falling edge tpDES 300nsec
INTERFACES6.
Interface Part Type Remarks
Optical Receiver HFBR-2531Z (Avago) For suitable connectors see
www.avagotech.com
Optical Transmitter HFBR-1531Z (Avago)
DC supply on PCB FKC 2,5/2-STF-5,08 (Phoenix ) Connector: MSTBV 2,5/2-GF-5,08 (Phoenix)
CABLE LENGTH7.
Max. length of coaxial cable: 30cm. Max. length of simple cable: 7cm.
For gate and auxiliary emitter connections use coaxial cable RG58 C/U with auxiliary emitter connected
to the shielding. For power emitter and auxiliary collector it is recommended to use HV isolation cable, for
instance Radox 9 GKW-AX, 1.5mm.

TECHNICAL DOCUMENTATION
Preliminary
7www.inpower-sys.com 1IPSE1A33-60
COMMISSIONING SUPPORT8.
The IPS drivers are delivered to match the exact type of the IGBT-module used and according to the
application information given in your order, i.e. the settings of the drivers comply with the key features of
your system such as:
Inverter topology•
Nominal DC-link voltage•
Maximum collector current in nominal operation•
Switching frequency•
NOTE: You do not have to change any settings before you start your rst tests!
Preparation
Make sure all supplies are turned o and the DC-bus is fully discharged!
Connect the driver to the IGBT-module as shown in chapter CONNECTIONS. Observe all tips and instructions
given in chapters HANDLING AND MOUNTING ADVICES and SAFETY NOTICE.
Connect the DC low voltage supply for the driver. Do not turn it on.
Connect the control signals from the double pulse tester.
Once you have double-checked that all the connections are correct, no wires inter-changed, all the bolts
are tightened to the correct torque and no conductive materials or swarf interfering with the required
clearance and creepage distances, the preliminary test can be started.
Pre-test
Turn on the DC low voltage supply for the driver. Make sure that there is no strange noise, smell, heat or
otherwise originating from the driver. The voltage supply LEDs should now light up green which means
that the system is working in nominal operation.
If something does not seem right, stop the test straight away and check for the reason! If there has been
an incorrect connection, make sure the driver is not damaged!
As with any electrical equipment, here too we begin with a much lower than nominal voltage. The DC-bus
voltage can be slowly increased to around 100V.
Make sure that there is no strange noise, smell, heat or otherwise originating from the driver or any other
part of the inverter section under test.
Take extreme care to protect yourself and any other persons and equipment from unexpected action or
reaction from the device under test and the connected test equipment.
DO NOT TOUCH ANY LIVE PARTS!
If all is well so far, continue to increase the voltage slowly to half the nominal DC-bus voltage. If something
does not seem right, stop the test straight away and check for the reason!
If all is well , continue to increase the voltage slowly to the nominal DC-bus voltage.
Make sure to remain at a safe distance to the equipment, in particular to the DC-bus, which now has a very
dangerous fault energy level. If something does not seem right, stop the test straight away and check for
the reason!

TECHNICAL DOCUMENTATION
Preliminary
8www.inpower-sys.com 1IPSE1A33-60
Double pulse switching test
Run a double pulse test on the channel under test. Use half the nominal DC-bus voltage at rst. Once that
is okay, repeat the test with the nominal DC-bus voltage.
Make sure to capture the input and output signals on the oscilloscope and save the images. If something
does not seem right, stop the test straight away and check for the reason!
Oncethesetestshavebeen successful,turnotheDC-bussupplyandwaituntiltheDC-bushasCOMPLETELY
DISCHARGED. Then turn o the low voltage supply to the driver.
Normal switching test
Connect the application controller to the input of the driver. Make sure all the connections are correct, no
wires inter-changed, all the bolts are still tight and no conductive materials or swarf is interfering with the
required clearance and creepage distances
Now the full switching test can be conducted.
Proceed by turning on the low voltage supply to the driver and then slowly turning up the DC-bus voltage
as with the pre-test. If something does not seem right, stop the test straight away and check for the reason!
If there has been an incorrect connection, make sure the driver is not damaged!
Once the nominal DC-bus voltage is present, turn on the controller, thereby applying the application
switching signals. Make sure to capture the input and output signals on the oscilloscope and save the
images.
If all is well, you have got the system working correctly. If something does not seem right, stop the test
straight away and check for the reason!
The voltage and current waveforms may not precisely look like the expected result. This will be due to
specics of the inverter design such as stray or leakage inductances and bus-bar or cable runs.
Short circuit test
If the results you have achieved so far are of sucient quality, you can proceed with the short circuit
tests.
This is carried out just like the double pulse test described above, except with a short circuit applied at the
appropriate terminals.
Again start with half the nominal DC-bus voltage. Due to the fact that much higher currents can be
expected with this test, take extreme caution in protecting all personnel and equipment from inadvertent
action or explosion!
Finally use the full nominal DC-bus voltage and repeat the test, capturing the signals on the oscilloscope.
Re-programming of the IPS driver
To get the driver tuned to the optimum result, it may require the IPS application support. Please forward
the scope images to IPS together with any relevant information on the application test.
TheengineeringteamoftheInPowerSystemswillevaluateyourtestsresultsandsendyouare-programming
software tuned exactly to the real conditions of your inverter.
NOTE: We can only retune the driver according to your real conditions if we receive from you all relevant
information of your inverter including tests results.

TECHNICAL DOCUMENTATION
9
Preliminary
www.inpower-sys.com 1IPSE1A33-60
INPUTS AND OUTPUTS9.
There are 5 mounting holes for M4 screws. It is possible to use plastic or metal screws. Mounting holes
have dierent potentials.
The auxiliary adaptation board is including an addi-
tional gate capacitor (C3, C2 or C1) if it is required by
IGBT module producer.
Driver with cable connector
Driver without cable connector
Adaptation board

TECHNICAL DOCUMENTATION
10
Preliminary
www.inpower-sys.com 1IPSE1A33-60
CONNECTIONS10.
Driver without cable connector
Driver with cable connector
Max. length of coaxial cable: 40cm.
For gate and auxiliary emitter connections use coaxial cable RG58 C/U with auxiliary emitter connected
to the shielding. For power emitter and auxiliary collector it is recommended to use HV isolation cable, for
instance Radox 9 GKW-AX, 1.5mm.

TECHNICAL DOCUMENTATION
11
Preliminary
www.inpower-sys.com 1IPSE1A33-60
Max. length of coaxial cable: 30cm. Max. length of simple cable: 7cm.
For gate and auxiliary emitter connections use coaxial cable RG58 C/U with auxiliary emitter connected
to the shielding. For power emitter and auxiliary collector it is recommended to use HV isolation cable, for
instance Radox 9 GKW-AX, 1.5mm, order no. 12 537 829.
The adapter board has to be screwed to the IGBT-module and connected to the driver as in gure below.
Driver and adaptation board are connected to the IGBT module

TECHNICAL DOCUMENTATION
12
Preliminary
www.inpower-sys.com 1IPSE1A33-60
LED DIAGNOSTICS11.
The system status during normal operation or fault is indicated by eight LEDs. All LEDs are on the driver
board.
The LEDs indicate the following conditions:
LED Description
Switch D 15 no light: the driver is receiving switch OFF signal
red light: the driver is receiving switch ON signal
is blinking: input lter detected problem with input switching signal, i.e. too high
frequency, second switching pulse very close to the rst one or
incorrect delay between two pulses
U sat D 16 no light: system is working in nominal operation
red light: U sat – protection was operating
U sat D 17 no light: system is working in nominal operation
red light: U sat – protection was operating
U sat D 18 no light: system is working in nominal operation
red light: U sat – protection was operating
U sat – D 19 no light: system is working in nominal operation
red light: U sat – protection was operating
di/dt D 1 no light: system is working in nominal operation
red light: di/dt protection was operating
Reset D 14 no light: system is working in nominal operation
red light: reset of the driver or secondary voltage is below 11V
Voltage
supply
D 20 no light: secondary supply voltage is missing
green light: system is working in nominal operation
The failure indications are illuminated until the driver is reset (switch-o of the driver power supply).

TECHNICAL DOCUMENTATION
13
www.inpower-sys.com 1IPSE1A33-60
EXCLUSION CLAUSE12.
Passing on of this document or its contents to company external personnel requires written consent. Us-
age and copying of the contents to other media is prohibited. Violations will be prosecuted for damages.
All rights reserved, including such arising from issue of patents or registration of trade marks or design.
© InPower Systems GmbH 2011. All rights reserved.
The contents of this document correspond with the described hardware has been checked. Discrepancies
may exist nevertheless; no guaranty is assumed for total congruence. The information contained in this
document is subject to regular revision. Any alterations required will be incorporated in the next issue.
Suggestions for improvement are welcome. Changes of the document may occur without prior notice.
These instructions are part of the InPower Systems driver 1IPSE1A33-60. To guaranty safe and fault free
operation it is necessary to have read and understood these instructions. In this context InPower Systems
GmbH retains the right to change technical data and product specications without prior notice to the
course of improvement.
Table of contents
Other InPOWER Computer Hardware manuals
Popular Computer Hardware manuals by other brands
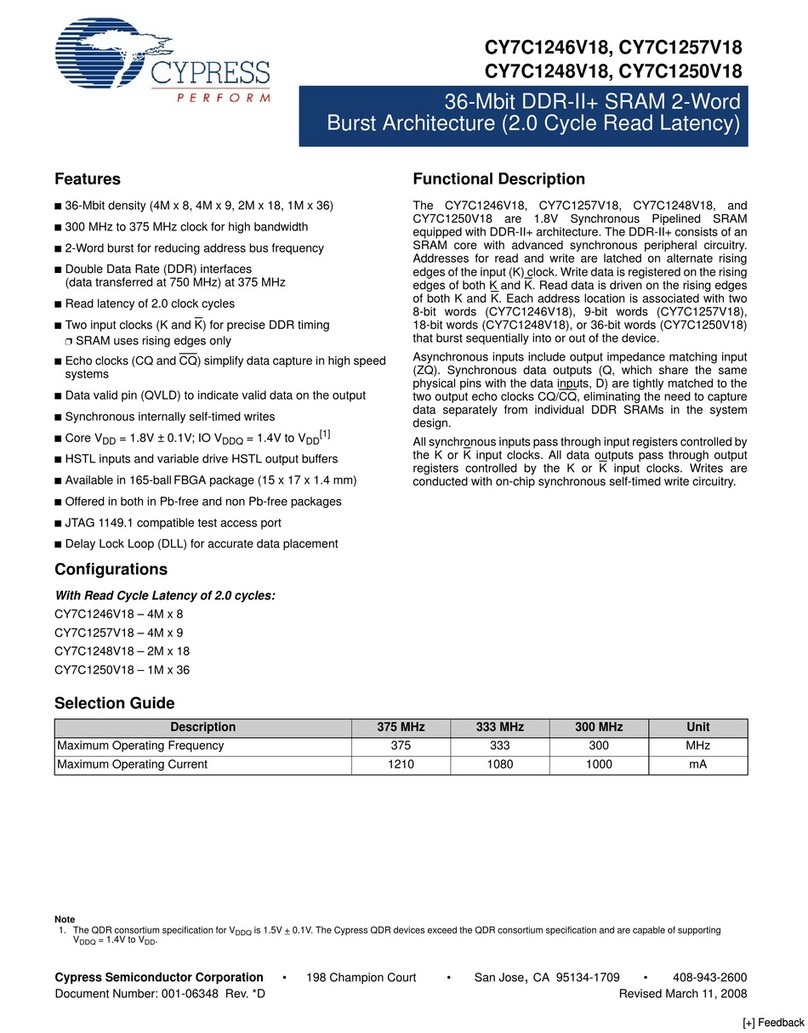
Cypress Semiconductor
Cypress Semiconductor CY7C1246V18 Specification sheet
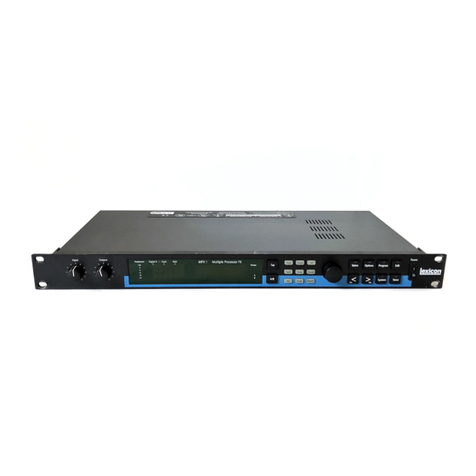
Lexicon
Lexicon MPX - ADDENDUM REV 1 Quick reference guide

Nuvoton
Nuvoton N9H30 Series Hardware development guide
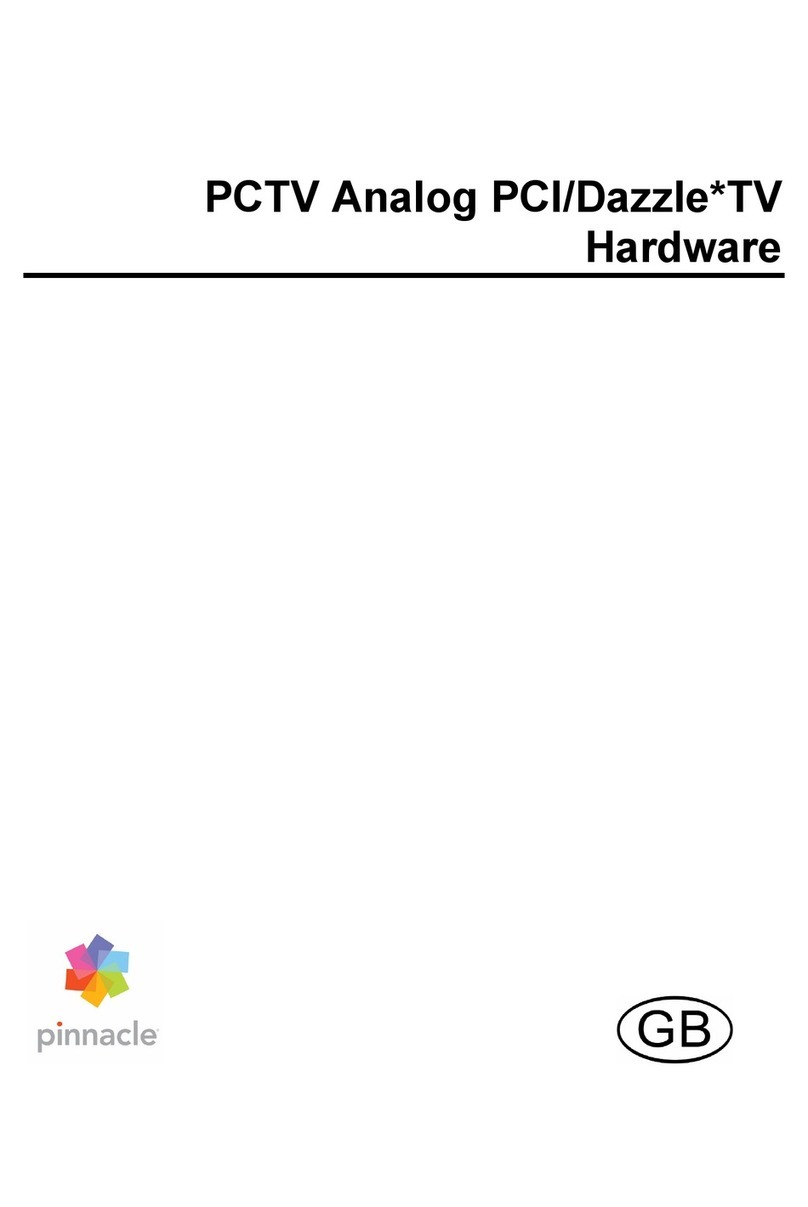
Pinnacle
Pinnacle PCTV ANALOG PCI user manual
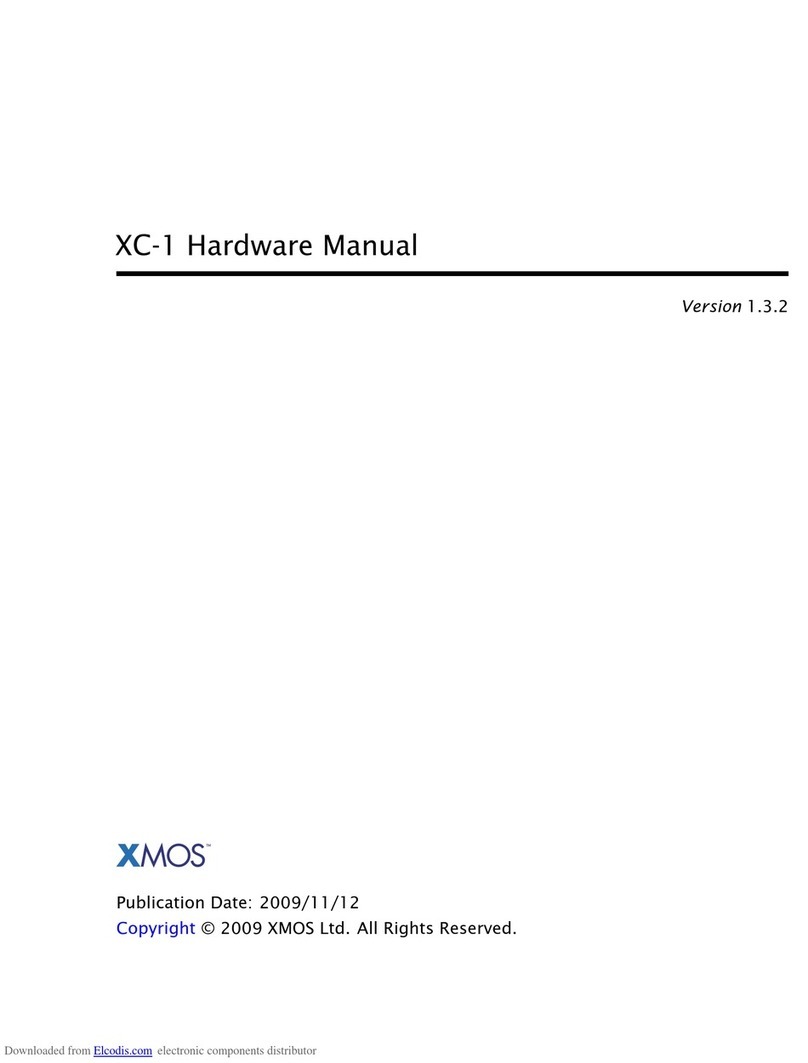
XMOS
XMOS XC-1 Hardware manual
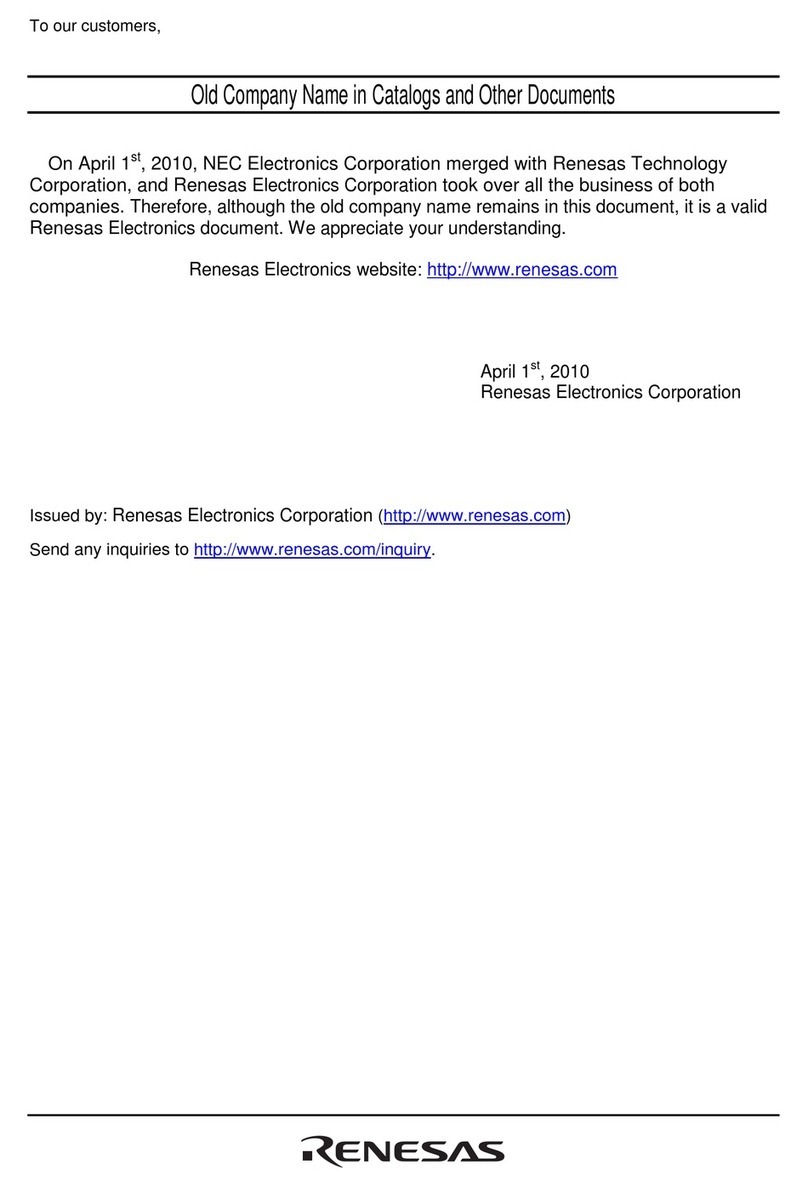
Renesas
Renesas Converter Board M37530T-PTCB user manual