Inxpect SBV System Series User manual

Copyright © 2021, Inxpect SpA
All rights reserved in all countries.
Any distribution, alteration, translation or reproduction, partial or total, of this
document is strictly prohibited unless with prior authorization in writing from
Inxpect SpA, with the following exceptions:
lPrinting the document in its original format, totally or partially.
lTransferring the document on websites or other electronic systems.
lCopying contents without any modification and stating Inxpect SpA as
copyright owner.
Inxpect SpA reserves the right to make modifications or improvements to the
relative documentation without prior notice.
Requests for authorizations, additional copies of this manual or technical
information about this manual must be addressed to:
Inxpect SpA
Via Serpente, 91
25131 Brescia (BS)
Italy
+39 030 5785105

Contents
Glossary of terms iv
1. This manual 6
1.1 Information on this manual 6
2. Safety 8
2.1 Safety information 8
2.2 Conformity 11
3. Get to know SBV System Series 12
3.1 SBV System Series 12
3.2 SBV System Series control units 14
3.3 SBV-01 sensors 20
3.4 Inxpect Safety application 21
3.5 Fieldbus communication 23
3.6 Modbus communication 24
3.7 System configuration 25
4. Functioning principles 27
4.1 Sensor functioning principles 27
4.2 Detection fields 28
4.3 Safety working modes and safety functions 32
4.4 Safety working mode: Both (default) 32
4.5 Safety working mode: Always access detection 33
4.6 Safety working mode: Always restart prevention 33
4.7 Restart prevention function: static object detection option 34
4.8 Features of the restart prevention function 34
4.9 Muting 37
4.10 Anti-tampering functions:anti-rotation around axes 38
4.11 Anti-tampering functions:anti-masking 39
5. Sensor position 42
5.1 Basic concepts 42
5.2 Sensor field of view 43
5.3 Dangerous area calculation 45
5.4 Calculation of range of distances 46
5.5 Sensor position recommendations 47
5.6 Installations on moving elements 48
5.7 Outdoor installations 49
6. Installation and use procedures 51
6.1 Before installation 51
6.2 Install and configure SBV System Series 52
6.3 Validate the safety functions 59
6.4 Manage the configuration 61
6.5 Other functions 62
7. Maintenance and troubleshooting 64
7.1 Troubleshooting 64
7.2 Event log management 67
7.3 INFOevents 71
7.4 ERRORevents (control unit) 73
7.5 ERRORevents (sensor) 75
7.6 ERRORevents (CANbus) 76
7.7 Cleaning and spare parts 77
8. Technical references 78
8.1 Technical data 79
8.2 Terminal blocks and connector pin-outs 82
8.3 Electrical connections 84
8.4 Parameters 91
8.5 Digital input signals 94
9. Appendix 99
9.1 System software 99
9.2 Disposal 100
9.3 Service and warranty 100
SBV System Series| Instruction manual v1.2 DEC 2021|SAF-UM-SBVBus-en-v1.2|© 2021 Inxpect SpA iii

iv SBV System Series| Instruction manual v1.2 DEC 2021 |SAF-UM-SBVBus-en-v1.2|© 2021 Inxpect SpA
Glossary of terms
A
Activated output (ON-state)
Output that switches from OFF to ON-state.
Angular coverage
Property of the field of view that corresponds to the coverage on the horizontal plane.
D
Dangerous area
Area to be monitored because it is dangerous for people.
Deactivated output (OFF-state)
Output that switches from ON to OFF-state.
Detection distance x
Depth of the field of view configured for detection field x.
Detection field x
Portion of the field of view of the sensor. Detection field 1 is the field closer to the sensor.
Detection signal x
Output signal that describes the monitoring status of the detection field x.
E
ESPE (Electro-Sensitive Protective Equipment)
Device or system of devices used for the safety-related detection of people or parts of the body. ESPEs
provide personal protection at machines and plants/systems where there is a risk of physical injury.
These devices/systems cause the machine or plant/system to switch over to a safe status before a
person is exposed to a dangerous situation.
F
Field of view
Sensor area of vision characterized by a specific angular coverage.
Fieldset
Structure of the field of view which can be composed of up to four detection fields.
FMCW
Frequency Modulated Continuous Wave

I
Inclination
Sensor rotation around the x-axis. The sensor inclination is the angle between the center of the field of
view of the sensor and a line parallel to the ground.
M
Machinery
The system for which the dangerous area is monitored.
Monitored area
Area that is monitored by the system. It is composed of all the detection fields of all the sensors.
O
OSSD
Output Signal Switching Device
R
RCS
Radar Cross-Section. Measure of how detectable an object is by radar. It depends, among other factors,
on the material, dimension and position of the object.
T
Tolerance area
Area of the field of view where detection or not of a moving object/person depends on the
characteristics of the same object itself.
SBV System Series| Instruction manual v1.2 DEC 2021|SAF-UM-SBVBus-en-v1.2|© 2021 Inxpect SpA v

6SBV System Series| Instruction manual v1.2 DEC 2021 |SAF-UM-SBVBus-en-v1.2|© 2021 Inxpect SpA
1. This manual
1.1 Information on this manual
1.1.1 Objectives of this instruction manual
This manual explains how to integrate SBV System Series for safeguarding machinery operators and how to
install it, use it and maintain it safely.
This document includes all the information as Safety Manual according to IEC 61508-2/3 Annex D. Please refer in
particular to"Safety parameters" on page79 and to "System software" on page99.
The functioning and safety of the machinery to which SBV System Series is connected is out of the scope of this
document.
1.1.2 Obligations with regard to this manual
NOTICE: this manual is an integral part of the product and must be kept for its entire working life.
It must be consulted for all situations related to the life cycle of the product, from its delivery to
decommissioning.
It must be stored so that it is accessible to operators, in a clean location and in good condition.
In the event of manual loss or damage, contact Customer Assistance Service.
Always enclose the manual when the equipment is sold.
1.1.3 Provided documentation
Document Code Date Distribution format
Instruction manual (this
manual)
SAF-UM-SBVBus-
en-v1.2
DEC
2021
online PDF
PDF downloadable from the site
www.inxpect.com/industrial/tools
PROFIsafe communication
Reference guide
SAF-RG-
PROFIsafe-en-v16
JUL
2021
online PDF
PDF downloadable from the site
www.inxpect.com/industrial/tools
Modbus communication
Reference guide
SAF-RG-Modbus-
en-v1
JUL
2021
online PDF
PDF downloadable from the site
www.inxpect.com/industrial/tools
National configuration
addendum
SAF-SN-SBVBus-
en-v1.0
DEC
2021
online PDF
PDF downloadable from the site
www.inxpect.com/industrial/tools
Cable validator online Excel
Excel downloadable from the site
www.inxpect.com/industrial/tools

1.1.4 Instruction manual updates
Publication
date Code Hardware
version
Firmware
version Updates
DEC 2021 SAF-UM-
SBVBus-
en-v1.2
lISC-B01,
ISC-02 and
ISC-03: 2.1
lSBV-01:
2.1
lISC-B01,
ISC-02 and
ISC-03:
1.5.0
lSBV-01: 3.0
Added static object detection option
Added reference to the "National configuration
addendum" document
Added "Muting activation conditions" on page37
SEP 2021 SAF-UM-
SBVBus-
en-v1.1
lISC-B01,
ISC-02 and
ISC-03: 2.1
lSBV-01:
2.1
lISC-B01,
ISC-02 and
ISC-03:
1.4.0
lSBV-01: 1.1
Changed system denomination in SBV System
Series
Changed application denomination in Inxpect
Safety
Added ISC-02 and ISC-03 control units
Added topics: "Modbus communication" on
page24, "System software" on page99
Added event log (Fieldbus connection, Modbus
connection, Session authentication, Validation, Log
download)
Other minor changes
JAN 2021 SAF-UM-
SBVBus-
en-v1.0
lISC-B01:
2.1
lSBV-01:
2.1
lISC-B01:
1.3.0
lSBV-01: 1.0
First publication
1.1.5 Intended users of this instruction manual
The recipients of the instruction manual are:
lThe machinery manufacturer onto which the system will be installed
lSystem installer
lMachinery maintenance technician
1. This manual
SBV System Series| Instruction manual v1.2 DEC 2021|SAF-UM-SBVBus-en-v1.2|© 2021 Inxpect SpA 7

8SBV System Series| Instruction manual v1.2 DEC 2021 |SAF-UM-SBVBus-en-v1.2|© 2021 Inxpect SpA
2. SAFETY
2.1 Safety information
2.1.1 SAFETY MESSAGES
Warnings related to the safety of the user and of the equipment as envisaged in this document are as follows:
WARNING! indicates a hazardous situation which, if not avoided, may cause death or serious injury.
NOTICE: indicates obligations that if not observed may cause harm to the equipment.
2.1.2 SAFETY SYMBOLS ON THE PRODUCT
This symbol marked on the product indicates that the manual must be consulted. In particular, pay
attention to the following activities:
lwiring of the connections (see "Terminal blocks and connector pin-outs" on page82 and "Electrical
connections" on page84)
lcable operating temperature (see "Terminal blocks and connector pin-outs" on page82)
lcontrol unit cover, which was subjected to a low energy impact test (see "Technical data" on page79)
2.1.3 PERSONNEL SKILLS
The recipients of this manual and the skills required for each activity presented herein are as follows:
Recipient Assignments Skills
Machinery
manufacturer
lDefines which protective devices should
be installed and sets the installation
specifications
lKnowledge of significant hazards of the
machinery that must be reduced based on
risk assessment.
lKnowledge of the entire machinery safety
system and the system on which it is
installed.
Protection
system installer
lInstalls the system
lConfigures the system
lPrints configuration reports
lAdvanced technical knowledge in the
electrical and industrial safety fields
lKnowledge of the dimensions of the
dangerous area of the machinery to be
monitored
lReceives instructions from the machinery
manufacturer
Machinery
maintenance
technician
lPerforms maintenance on the system lAdvanced technical knowledge in the
electrical and industrial safety fields
2.1.4 SAFETY ASSESSMENT
Before using a device, a safety assessment in accordance with the Machinery Directive is required.
The product as an individual component fulfills the functional safety requirements in accordance with the
standards stated in "Standards and Directives" on page11. However, this does not guarantee the functional
safety of the overall plant/machine. To achieve the relevant safety level of the overall plant/machine’s required
safety functions, each safety function needs to be considered separately.

SBV System Series| Instruction manual v1.2 DEC 2021|SAF-UM-SBVBus-en-v1.2|© 2021 Inxpect SpA 9
2.1.5 INTENDED USE
SBV System Series is certified SIL 2 according to IEC/EN 62061, PL d according to EN ISO 13849-1 and
Performance Class D according to IEC/TS 62998-1.
It performs the following safety functions:
lAccess detection function: access to a hazardous area deactivates the safety outputs to stop the moving
parts of the machinery.
lRestart prevention function: prevents unexpected starting or restarting of the machinery. Detection of
motion within the dangerous area maintains the safety outputs deactivated to prevent machinery starting.
It performs the following optional safety functions:
lStop signal: force all the safety outputs to OFF-state.
lRestart signal: enables the control unit to switch to ON-state the safety outputs related to all the detection
fields with no motion detected.
lMuting (see "Muting" on page37).
SBV System Series is suitable for protecting the entire body for the following applications:
ldangerous area protection
lmobile dangerous area protection
lindoor and outdoor applications
SBV System Series meets requirements of applications safety functions that require a risk reduction level of:
lUp to SIL 2, HFT = 0 according to IEC/EN 62061
lUp to PL d, Category 3 according to EN ISO 13849-1
lUp to Performance Class D according to IEC/TS 62998-1
SBV System Series, in combination with additional risk reduction means, can be used for applications safety
functions that require higher risk reduction levels.
The following is deemed improper use in particular:
lAny component, technical or electrical modification to the product,
lUse of the product outside the areas described in this document,
lUse of the product outside the technical details, see "Technical data" on page79.
2.1.6 EMC-COMPLIANT ELECTRICAL INSTALLATION
NOTICE: The product is designed for use in an industrial environment. The product may cause interference if
installed in other environments. If installed in other environments, measures should be taken to comply with the
applicable standards and directives for the respective installation site with regard to interference.
2.1.7 GENERAL WARNINGS
lIncorrect installation and configuration of the system decreases or inhibits the protective function of the
system. Follow the instructions provided in this manual for correct installation, configuration and validation of
the system.
lChanges to the system configuration may compromise the protective function of the system. After any
changes made to the configuration, validate correct functioning of the system by following the instructions
provided in this manual.
lIf the system configuration allows access to the dangerous area without detection, implement additional
safety measures (e.g. guards).
lThe presence of static objects, in particular metallic objects, within the field of view may limit the efficiency of
sensor detection. Keep the sensor field of view unobstructed.
lThe system protection level (SIL 2, PL d) must be compatible with the requirements set forth in the risk
assessment.
lCheck that the temperature of the areas where the system is stored and installed is compatible with the
storage and operating temperatures indicated in the technical data of this manual.
lRadiation from this device does not interfere with pacemakers or other medical devices.
2. Safety

10 SBV System Series| Instruction manual v1.2 DEC 2021 |SAF-UM-SBVBus-en-v1.2|© 2021 Inxpect SpA
2.1.8 WARNINGS FOR THE RESTART PREVENTION FUNCTION
lThe restart prevention function is not guaranteed in blind spots. If required by the risk assessment, implement
adequate safety measures in those areas.
lMachinery restarting must be enabled only in safe conditions. The button for the restart signal must be
installed:
ooutside of the dangerous area
onot accessible from the dangerous area
oin a point where the dangerous area is fully visible
2.1.9 RESPONSIBILITY
The machinery manufacturer and system installer are responsible for the operations listed below:
lProviding adequate integration of the safety output signals of the system.
lChecking the monitored area of the system and validating it based on the needs of the application and risk
assessment. Following the instructions provided in this manual.
2.1.10 LIMITS
lThe system cannot detect the presence of people who are immobile and not breathing or objects within the
dangerous area.
lThe system does not offer protection from pieces ejected from the machinery, from radiation, and objects
falling from above.
lThe machinery command must be electronically controlled.
2.1.11 DISPOSAL
In safety-related applications, comply with the mission time reported in "General specifications" on page79.
For decommissioning follow the instructions reported in "Disposal" on page100.
2. Safety

SBV System Series| Instruction manual v1.2 DEC 2021|SAF-UM-SBVBus-en-v1.2|© 2021 Inxpect SpA 11
2.2 Conformity
2.2.1 STANDARDS AND DIRECTIVES
Directives 2006/42/EC (MD - Machinery)
2014/53/EU (RED - Radio equipment)
Standards IEC/EN 62061: 2005, A1:2013, A2:2015, AC:2010 SIL 2
EN ISO 13849-1: 2015 PL d
EN ISO 13849-2: 2012
IEC/EN 61496-1: 2013
IEC/EN 61508: 2010 Part 1-7 SIL 2
IEC/EN 61000-6-2:2019
ETSI EN 305 550-1 V1.2.1
ETSI EN 305 550-2 V1.2.1
ETSI EN 301 489-1 v2.2.3 (only emissions)
ETSI EN 301 489-3 v2.1.1 (only emissions)
IEC/EN 61326-3-1:2017
IEC/EN 61010-1: 2010
IEC/TS 62998-1:2019
UL/CSA 61010-1
IEC/EN 61784-3-3 for the PROFIsafe Fieldbus
Note: no type of failure has been excluded during the system analysis and design phase.
The EUDeclaration of Conformity can be downloaded from www.inxpect.com/en/resources/downloads/.
2.2.2 CE
The manufacturer, Inxpect SpA, states that SBV System Series SRE (Safety Radar Equipment) complies with the
2014/53/EU and 2006/42/EC directives. The full EU declaration of conformity text is available on the company's
website at the address: www.inxpect.com/en/resources/downloads/.
At the same address all updated certifications are available for download.
2.2.3 OTHER CONFORMITIES AND NATIONAL CONFIGURATIONS
For a complete and up-to-date list of product conformities and any national configurations, please refer to the
National configuration addendum document. The PDFcan be downloaded from the site
www.inxpect.com/industrial/tools.
2. Safety

12 SBV System Series| Instruction manual v1.2 DEC 2021 |SAF-UM-SBVBus-en-v1.2|© 2021 Inxpect SpA
3. Get to know SBV System Series
Contents
This section includes the following topics:
3.1 SBV System Series 12
3.2 SBV System Series control units 14
3.3 SBV-01 sensors 20
3.4 Inxpect Safety application 21
3.5 Fieldbus communication 23
3.6 Modbus communication 24
3.7 System configuration 25
Product label description
The following table describes the information contained in the product label:
Part Description
SID Sensor ID
DC "yy/ww" : year and week of the product manufacture
SRE Safety Radar Equipment
Model Product model (e.g. SBV-01, ISC-B01)
Type Product variant, used for commercial purposes only
S/N Serial number
3.1 SBV System Series
3.1.1 Definition
SBV System Series is an active protection radar system that monitors the dangerous areas of machinery.
3.1.2 Special features
Some of the special features of this protection system are the following:
ldetection of current distance and angle of the targets detected by each sensor
lup to four safe detection fields to define different behaviors of the machines
lprogrammable coverage angle for each detection field
lrotation on three axes during installation to allow better coverage of detection areas
lEthernet safety Fieldbus to safely communicate with the PLC of the machinery (if available)
lpossibility to switch dynamically between different preset configurations (max 32 through Fieldbus, if
available, and max 4 with digital inputs) to adapt to the surrounding reality
lmuting on the entire system or only on some sensors
limmunity to dust and smoke
lreduction of undesired alarms caused by the presence of water or processing waste
lcommunication and data exchange through Modbus (if available)

3.1.3 Main components
SBV System Series is composed of a control unit and up to six sensors. The Inxpect Safety application allows
system operation configuration and checks.
3.1.4 Control unit - sensor communication
The sensors communicate with the control unit via CAN bus using diagnostic mechanisms in compliance with
standard EN 50325-5 to guarantee SIL 2 and PL d.
For correct functioning, each sensor must be assigned an identification number (Node ID).
Sensors on the same bus must have different Node IDs. By default, the sensor does not have a pre-assigned
Node ID.
3.1.5 Control unit - machinery communication
The control units communicate with the machinery via I/O ("Inputs" on page16 and "Outputs" on page17).
The ISC-B01 control unit is provided with a safety communication on a Fieldbus interface. The Fieldbus interface
allows the ISC-B01 control unit to communicate in real-time with the PLC of the machinery in order to do the
following:
lsend information about the system to the PLC (e.g. the position of the detected target)
lreceive information from the PLC (e.g. to change the configuration dynamically)
See "Fieldbus communication" on page23.
The ISC-B01 and ISC-02 control units are provided with an Ethernet port that allows an unsafe communication
on a Modbus interface. See "Modbus communication" on page24.
3.1.6 Applications
SBV System Series integrates with the machinery control system: when performing safety functions or detecting
failures, SBV System Series deactivates the safety outputs and keeps them deactivated, so the control system
can put the area into a safe condition and/or prevent restarting of the machinery.
In the absence of other control systems, SBV System Series can be connected to the devices that control the
power supply or machinery start-up.
SBV System Series does not perform normal machinery control functions.
For connection examples, see "Electrical connections" on page84.
3. Get to know SBV System Series
SBV System Series| Instruction manual v1.2 DEC 2021|SAF-UM-SBVBus-en-v1.2|© 2021 Inxpect SpA 13

14 SBV System Series| Instruction manual v1.2 DEC 2021 |SAF-UM-SBVBus-en-v1.2|© 2021 Inxpect SpA
3. Get to know SBV System Series
3.2 SBV System Series control units
3.2.1 Control units supported
The SBV System Series supportsthree different control units. The main difference among them are the
connection ports and therefore the communication interfaces available:
lISC-B01: two Ethernet ports for Fieldbus, an Ethernet port for system configuration and Modbus
communication and a micro-USB port
lISC-02: an Ethernet port for system configuration and Modbus and a micro-USB port
lISC-03: a micro-USB port
Safe
Unsafe
ISC-B01 communication architecture. ISC-02 communication architecture.
ISC-03 communication architecture.
3.2.2 Functions
The control unit performs the following functions:
lCollects information from all the sensors via CAN bus.
lCompares the position of detected motion with the set values.
lDeactivates the dedicated safety output when at least one sensor detects motion in the detection field.
lDeactivates all the safety outputs if a failure is detected in one of the sensors or the control unit.
lManages the inputs and outputs.
lCommunicates with the Inxpect Safety application for all configuration and diagnostic functions.
lAllows dynamically switching between different configurations.
lCommunicates with a safety PLC through the safe Fieldbus connection (if available)
lCommunicates and exchanges data through Modbus protocol (if available)

3.2.3 Structures
ISC-B01 ISC-02
ISC-03
Part Description Control unit
AI/O terminal block ISC-B01, ISC-02, ISC-03
BSystem status LEDs ISC-B01, ISC-02, ISC-03
CNetwork parameter reset button ISC-B01, ISC-02, ISC-03
DReserved for internal use. Output reset button ISC-B01, ISC-02, ISC-03
EMicro-USB port for connecting the PC and
communicating with the Inxpect Safety application
ISC-B01, ISC-02, ISC-03
FMicro-USB port (reserved) ISC-B01
GFieldbus status LEDs
See "Fieldbus status LEDs" on the next page
ISC-B01
HEthernet port with LEDs for connecting the PC,
communicating with the Inxpect Safety
application, and for Modbus communication
ISC-B01, ISC-02
IPower supply terminal block ISC-B01, ISC-02, ISC-03
JPower supply LEDs (steady green) ISC-B01, ISC-02, ISC-03
KCAN bus terminal block for connecting the first
sensor
ISC-B01, ISC-02, ISC-03
LDIP switch to turn on/off the bus termination
resistance:
lOn (top position, default) =resistance included
lOff (bottom position)= resistance excluded
ISC-B01, ISC-02, ISC-03
3. Get to know SBV System Series
SBV System Series| Instruction manual v1.2 DEC 2021|SAF-UM-SBVBus-en-v1.2|© 2021 Inxpect SpA 15

16 SBV System Series| Instruction manual v1.2 DEC 2021 |SAF-UM-SBVBus-en-v1.2|© 2021 Inxpect SpA
3. Get to know SBV System Series
Part Description Control unit
MCPU LEDs:
lon the right: status of hardware functions of the
primary micro-controller
loff: normal behavior
lsteady red: contact assistance service
lonly for ISC-B01 and ISC-02, on the left: status
of hardware functions of the secondary micro-
controller
oslow flashing orange: normal behavior
oother status: contact assistance service
ISC-B01, ISC-02, ISC-03
NEthernet Fieldbus port n. 1 with LEDs ISC-B01
OEthernet Fieldbus port n. 2 with LEDs ISC-B01
3.2.4 System status LEDs
The LEDs are each dedicated to a sensor, and can display the following statuses:
Status Meaning
Steady green Normal sensor function and no motion detected
Orange Normal sensor function and some motion detected
Flashing red Sensor in error. See "Control unit LED" on page64
Steady red System error. See "Control unit LED" on page64
Flashing green Sensor in boot status. See "Control unit LED" on page64
3.2.5 Fieldbus status LEDs
The LEDs reflect the status of the PROFINET/PROFIsafe Fieldbus and their meaning is reported below.
Note: F1 is the LEDat the top, F6 is the LED at the bottom.
LED Status Meaning
F1 (power) Steady green Normal behavior
Flashing green or
off
Contact assistance service
F2 (boot) Off Normal behavior
Steady or flashing
yellow
Contact assistance service
F3 (link) Off Data exchange is running with the host
Flashing red No data exchange
Steady red No physical link
F4 (not used) - -
F5 (diagnosis) Off Normal behavior
Flashing red DCP signal service is initiated via the bus
Steady red diagnostic error at PROFIsafe layer (wrong F Dest Address, watchdog
timeout, wrong CRC) or diagnostic error at PROFINET layer (watchdog
timeout; channel, generic or extended diagnosis present; system
error)
F6 (not used) - -
3.2.6 Inputs
The system has two type 3 digital inputs (according to IEC/EN 61131-2). Each digital input is dual channel, and
the ground reference is common for all the inputs (for details, see "Technical references" on page78).
When using digital inputs, it is mandatory that the additional SNS input "V+ (SNS)" is connected to 24 V dc and
that the GND input "V- (SNS)" is connected to the ground in order to:

lperform the correct input diagnostic
lassure the system safety level
The function of each digital input must be programmed through the Inxpect Safety application. The available
functions are the following:
lStop signal: optional safety function, manages a specific signal to force all the safety outputs (detection
signals, if present) to OFF-state.
lRestart signal: optional safety function, manages a specific signal which enables the control unit to switch to
ON-state the safety outputs related to all the detection fields with no motion detected.
lMuting group “N”: optional safety function, manages a specific signal which allows the control unit to ignore
the information coming from a selected group of sensors.
lActivate dynamic configuration: allows the control unit to select a specific dynamic configuration.
lFieldbus controlled (if available): monitors the input status through Fieldbus communication. For example, a
generic ESPE can be connected to the input, respecting electrical specifications.
For details about digital input signals, see "Digital input signals" on page94.
3.2.7 Input variable behavior
If neither digital input nor OSSD is configured as Fieldbus controlled, the behavior of the input variables is as
described below:
Condition Input variable behavior Output behavior
IOPS (PLCprovider status)
=bad
the last valid value of the input
variable is retained
the system keeps working in its
normal operating state
Connection loss the last valid value of the input
variable is retained
the system keeps working in its
normal operating state
After power-up the initial values (set to 0) are used
for the input variables
the system keeps working in its
normal operating state
If at least one digital input or OSSD is configured as Fieldbus controlled, the behavior of the input variables is as
described below:
Condition Input variable behavior Output behavior
IOPS (PLCprovider status)
=bad
the last valid value of the input
variable is retained
the system keeps working in its
normal operating state
Connection loss the last valid value of the input
variable is retained
the system transits to safe state,
deactivating the OSSDs, until the
connection is re-established.
After power-up the initial values (set to 0) are used
for the input variables
the system remains in a safe state
with the OSSDs deactivated, until the
input data are passivated.
3.2.8 SNS input
The control unit also has an SNS input (high logic level (1) = 24 V) to check the correct functioning of the chip that
detects the status of the inputs.
NOTICE: if at least one input is connected, the SNS input "V+ (SNS)" and the GND input "V- (SNS)" must also be
connected.
3.2.9 Outputs
The system has four digital OSSD short-circuit protected outputs that can be used individually (non safe) or can
be programmed as dual channel safety outputs (safe) in order to ensure the system safety level.
An output is activated when it switches from OFF to ON-state and it is deactivated when it switches from ON to
OFF-state.
The function of each digital output must be programmed through the Inxpect Safety application.
The available functions are the following:
lSystem diagnostic signal: switches the selected output to OFF-state when a system fault is detected and
switches all the OSSD related to detection signals, if any, to OFF-state.
3. Get to know SBV System Series
SBV System Series| Instruction manual v1.2 DEC 2021|SAF-UM-SBVBus-en-v1.2|© 2021 Inxpect SpA 17

18 SBV System Series| Instruction manual v1.2 DEC 2021 |SAF-UM-SBVBus-en-v1.2|© 2021 Inxpect SpA
3. Get to know SBV System Series
lMuting enable feedback signal: switches the selected output to ON-state in the following cases:
owhen a muting signal is received over the configured input and at least one group is in muting
owhen a muting command is received through Fieldbus communication (if available) and at least one
sensor is in muting
lDetection signal 1: (e.g. alarm signal) switches the selected output to OFF-state when a sensor detects a
motion in detection field 1, when a stop signal is received from the related input or when there is a system
failure. The selected output remains in OFF-state for at least 100 ms.
Note: when an OSSD is configured as detection signal 1, a second OSSD is automatically assigned to it to
provide a safe signal.
lDetection signal 2: switches the selected output to OFF-state when a sensor detects a motion in detection
field 2, when a stop signal is received from the related input or when there is a system failure. The selected
output remains in OFF-state for at least 100 ms.
Note: when an OSSD is configured as detection signal 2, a second OSSD is automatically assigned to it to
provide a safe signal.
lDetection signal 3: switches the selected output to OFF-state when a sensor detects a motion in detection
field 3 or when a stop signal is received from the related input or when there is a system failure. The
selected output remains in OFF-state for at least 100 ms.
Note: when an OSSD is configured as detection signal 3, a second OSSD is automatically assigned to it to
provide a safe signal.
lDetection signal 4: switches the selected output to OFF-state when a sensor detects a motion in detection
field 4 or when a stop signal is received from the related input or when there is a system failure. The
selected output remains in OFF-state for at least 100 ms.
Note: when an OSSD is configured as detection signal 4, a second OSSD is automatically assigned to it to
provide a safe signal.
lFieldbus controlled (if available): allows the specific output to be set through the Fieldbus communication.
lRestart Feedback signal: switches the selected output to ON-state when it is possible to restart at least
one detection field (Restart signal).
oIf all the used detection fields are configured as automatic restart prevention (in Settings >Restart
parameters), the dedicated output is always in OFF-state;
oIf at least one detection field in use is configured as manual or safe manual restart prevention (in
Settings >Restart parameters), the dedicated output remains in OFF-state as long as motion is
detected; then it is activated (ON-state) if there is no more motion within at least one detection field.
The ON-state lasts as long as the absence of motion within one or more detection field does and until
the restart signal is activated on the dedicated input.
Each output status can be retrieved by Fieldbus communication (if available).
The system installer can decide to configure the system as follows:
ltwo dual channel safety outputs (e.g. Detection signal 1 and Detection signal 2, usually alarm and warning
signals), or
lone dual channel safety output (e.g. Detection signal 1) and two single channel output (e.g. System
diagnostic signal and Muting enable feedback signal), or
leach output as a single output (e.g. System diagnostic signal,Muting enable feedback signal and a Restart
Feedback signal).
WARNING! To use SBV System Series for a category 3 safety system, both the channels of a safety
output must be connected to the safety system. Configuring a safety system with only one channel
safety output may result in serious injuries due to an output circuit fault and a failure of the machine
to stop.
The dual channel safety output is automatically obtained by the Inxpect Safety application and it only matches
the single OSSD outputs as follows:
lOSSD 1 with OSSD 2
lOSSD 3 with OSSD 4
In the dual channel safety output, the output status is the following:
lactivated output (24 V dc): no motion detected and normal functioning
ldeactivated output (0 V dc): motion detected in the detection field or failure detected in the system

Idle signal is 24 V dc, periodically shortly pulsed to 0 V (pulses are not synchronous) for the receiver to detect
shortcut to either 0 V or 24 V.
The pulse duration at 0 V (TL) can be set at 300 μs or 2 ms through the Inxpect Safety application (Settings >
Digital Input-Output >OSSD Pulse width).
For details, see "Technical references" on page78.
3.2.10 External resistor for OSSD outputs
To guarantee the correct connection between the OSSDs of the control unit and an external device, it may be
necessary to add an external resistor.
If the pulse width set (OSSD Pulse width) is 300 μs, it is strongly recommended to add an external resistor to
guarantee the discharge time of the capacitive load. If it is set at 2 ms, an external resistance must be added if
the resistor of the external load is greater than the maximum resistive load allowed, see "Technical data" on
page79.
Below are some standard values for the external resistor:
OSSD Pulse width value External resistor (Re)
300 μs 1 kΩ
2 ms 10 kΩ
3. Get to know SBV System Series
SBV System Series| Instruction manual v1.2 DEC 2021|SAF-UM-SBVBus-en-v1.2|© 2021 Inxpect SpA 19

20 SBV System Series| Instruction manual v1.2 DEC 2021 |SAF-UM-SBVBus-en-v1.2|© 2021 Inxpect SpA
3. Get to know SBV System Series
3.3 SBV-01 sensors
3.3.1 Functions
The sensors perform the following functions:
lDetect motion in their field of view.
lSend the motion detection signal to the control unit through CAN bus.
lSignal to the control unit through CAN bus the failures or faults detected on the sensor during diagnostics.
3.3.2 2-axes structure
Part Description
ASensor
BStatus LED
CTamper-proof screws to position the sensor at a specific angle around x-axis (tilt 10° steps)
DMounting bracket
EScrew to position the sensor at a specific angle around y-axis (pan 10° steps)
FConnectors for connecting the sensors in a chain and to the
3.3.3 3-axes structure
Part Description
ASensor
BStatus LED
CTamper-proof screws to position the sensor at a specific angle around x-axis (tilt 10° steps)
Table of contents
Popular Radar manuals by other brands
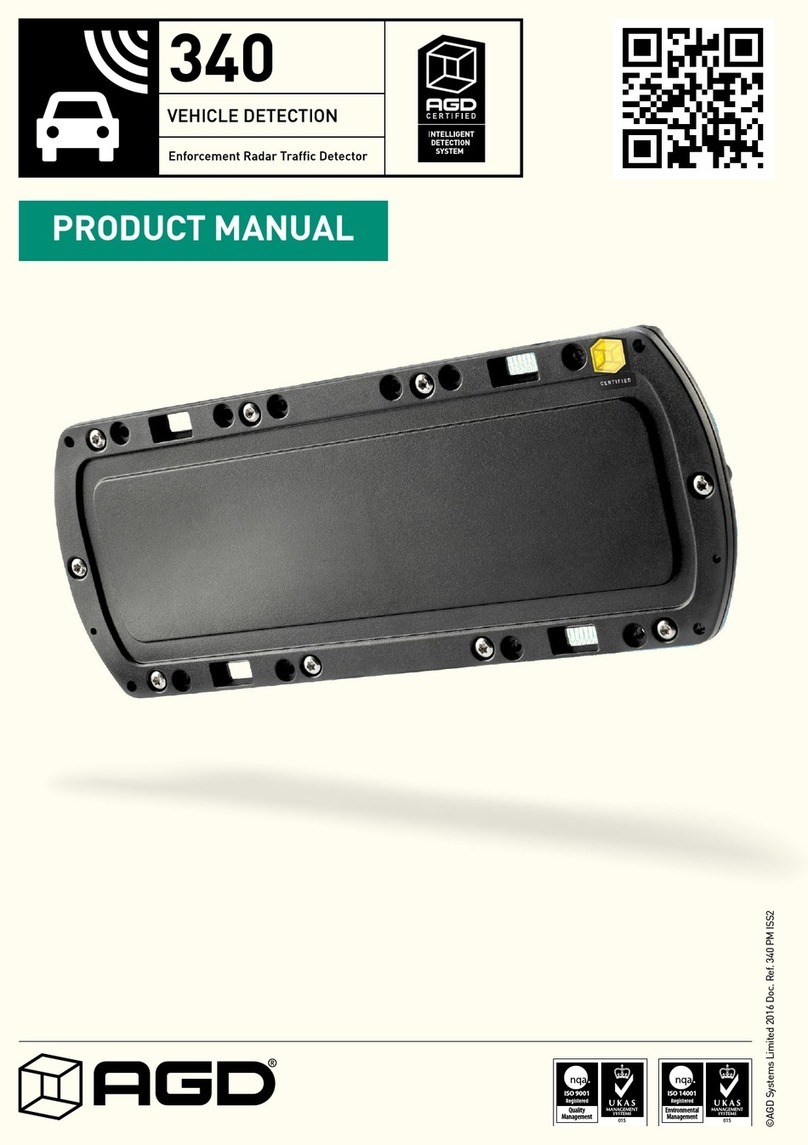
AGD
AGD 340 product manual
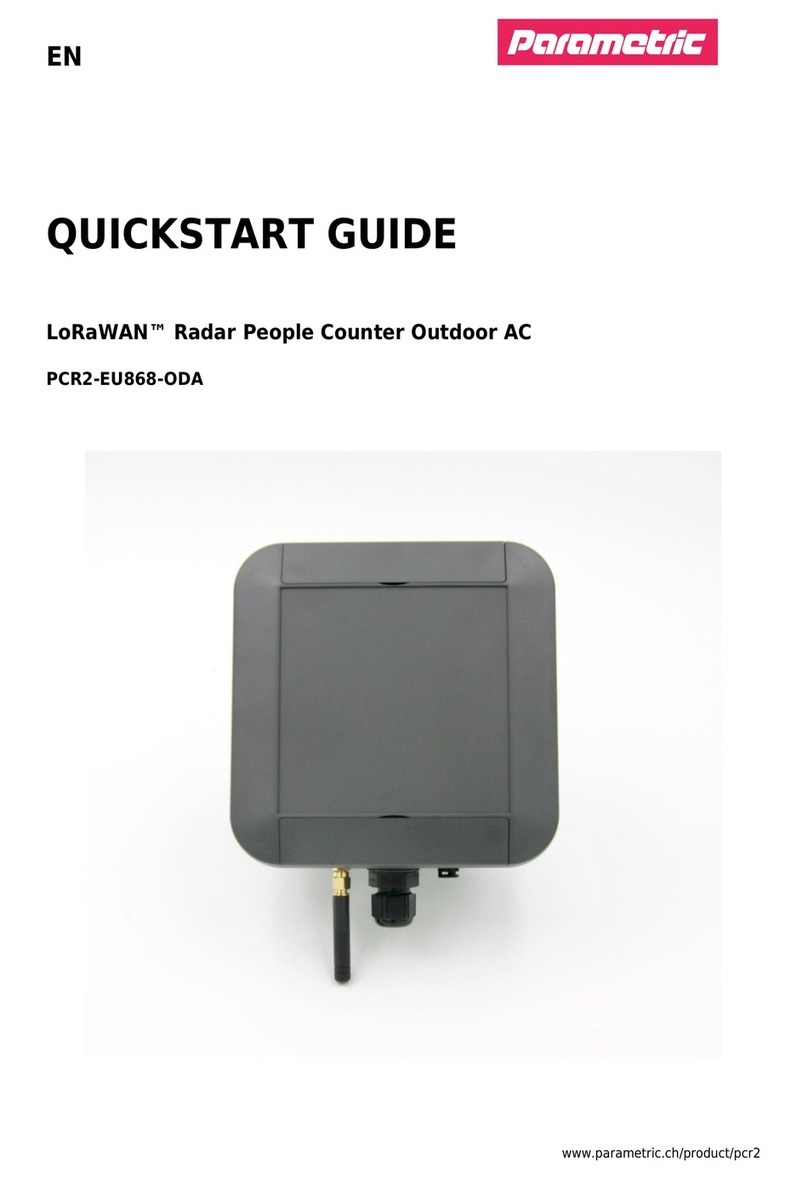
Parametric
Parametric PCR2-EU868-ODA quick start guide
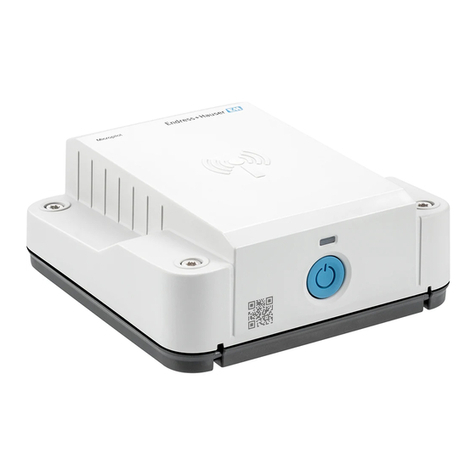
Endress+Hauser
Endress+Hauser Micropilot FWR30 operating instructions
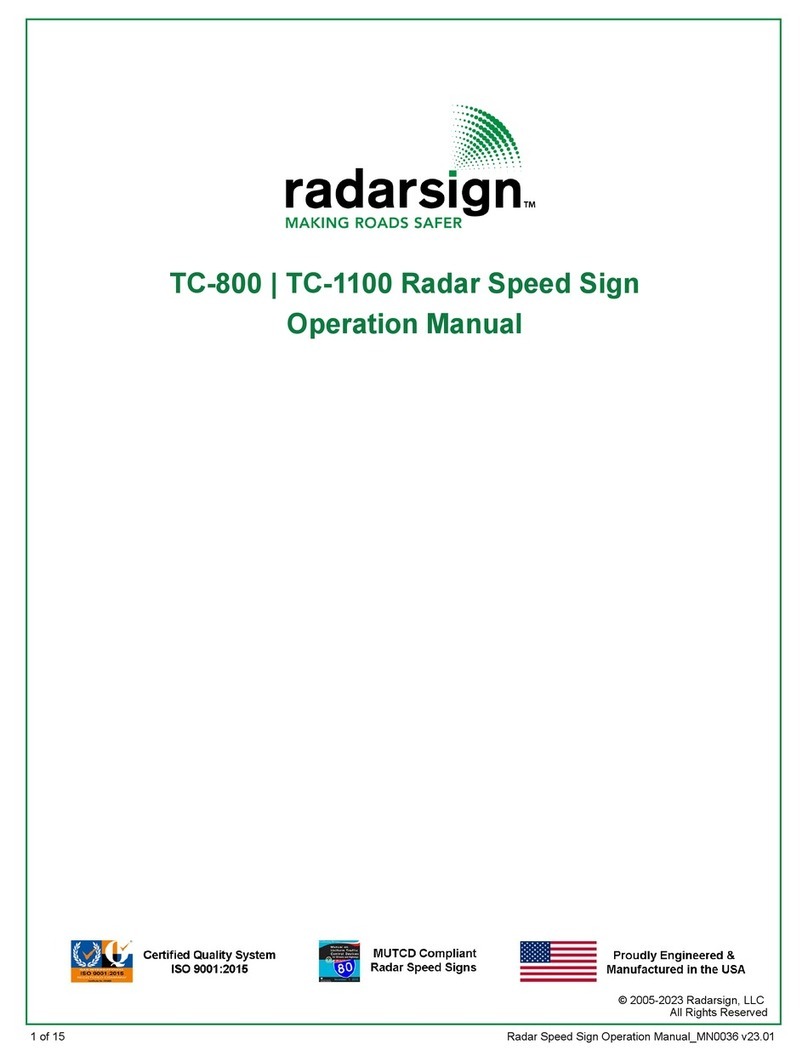
Radarsign
Radarsign TC-800 Operation manual
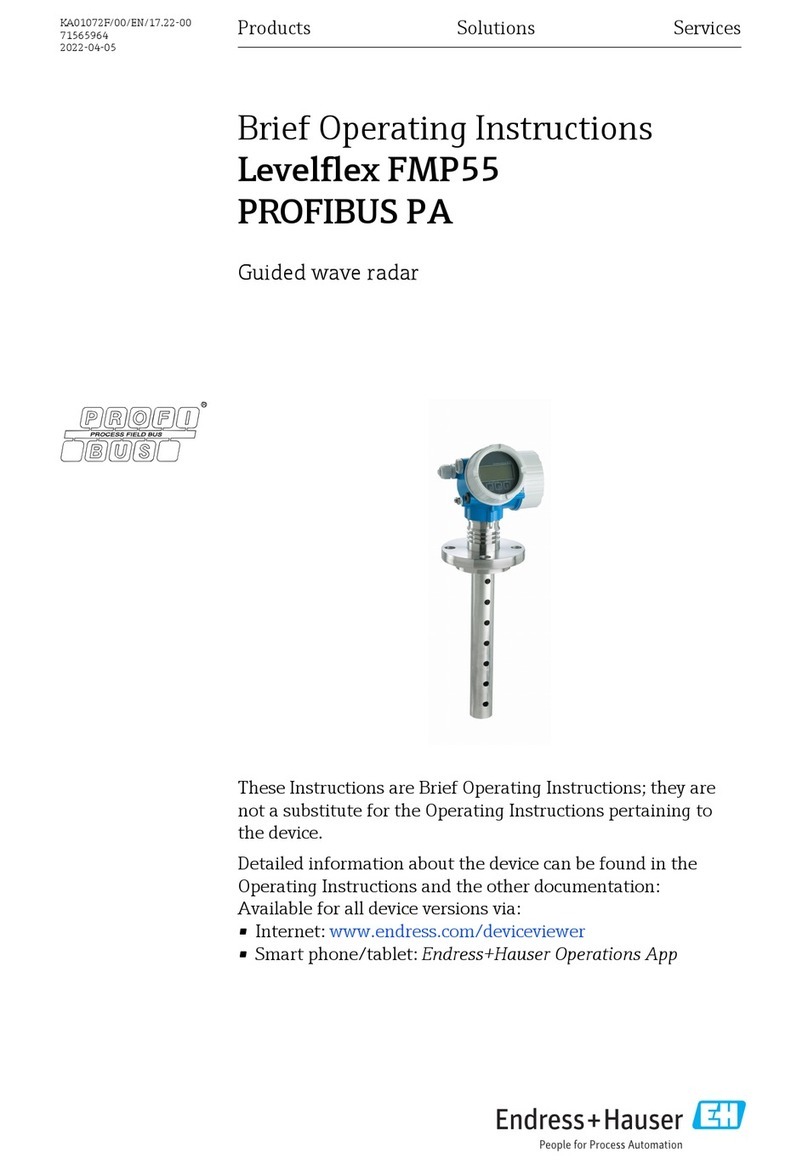
Endress+Hauser
Endress+Hauser Levelflex FMP55 PROFIBUS PA Brief operating instructions
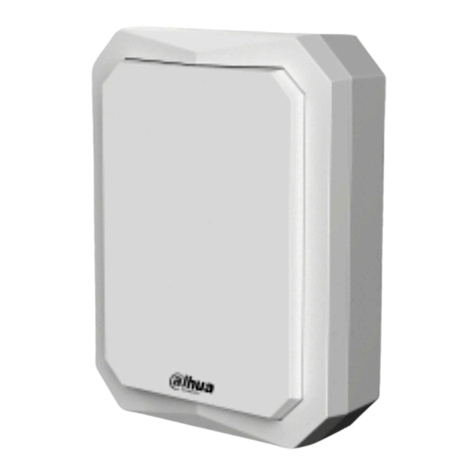
Dahua Technology
Dahua Technology DH-PFR4K-E50 user manual
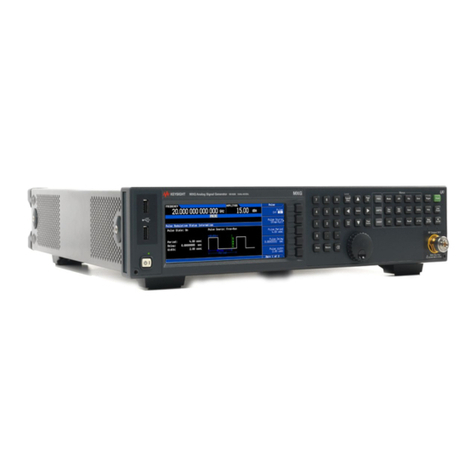
Keysight Technologies
Keysight Technologies E8740A-070 Startup guide
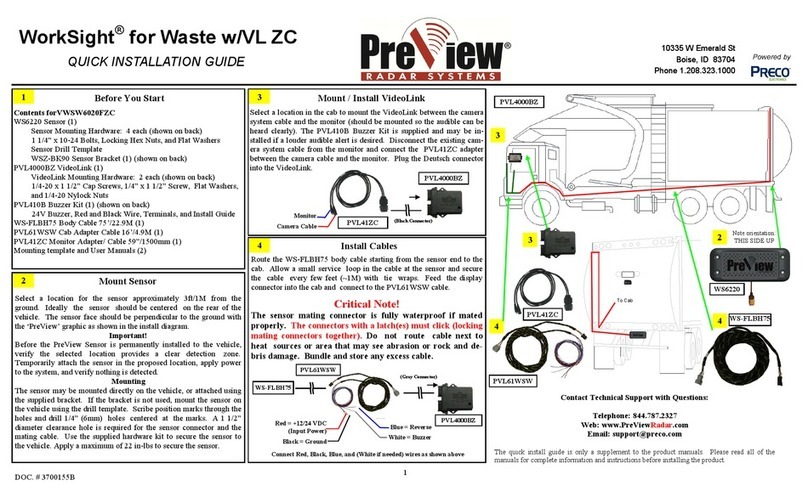
Preco
Preco PreView WorkSight for Waste w/VL ZC Quick installation guide
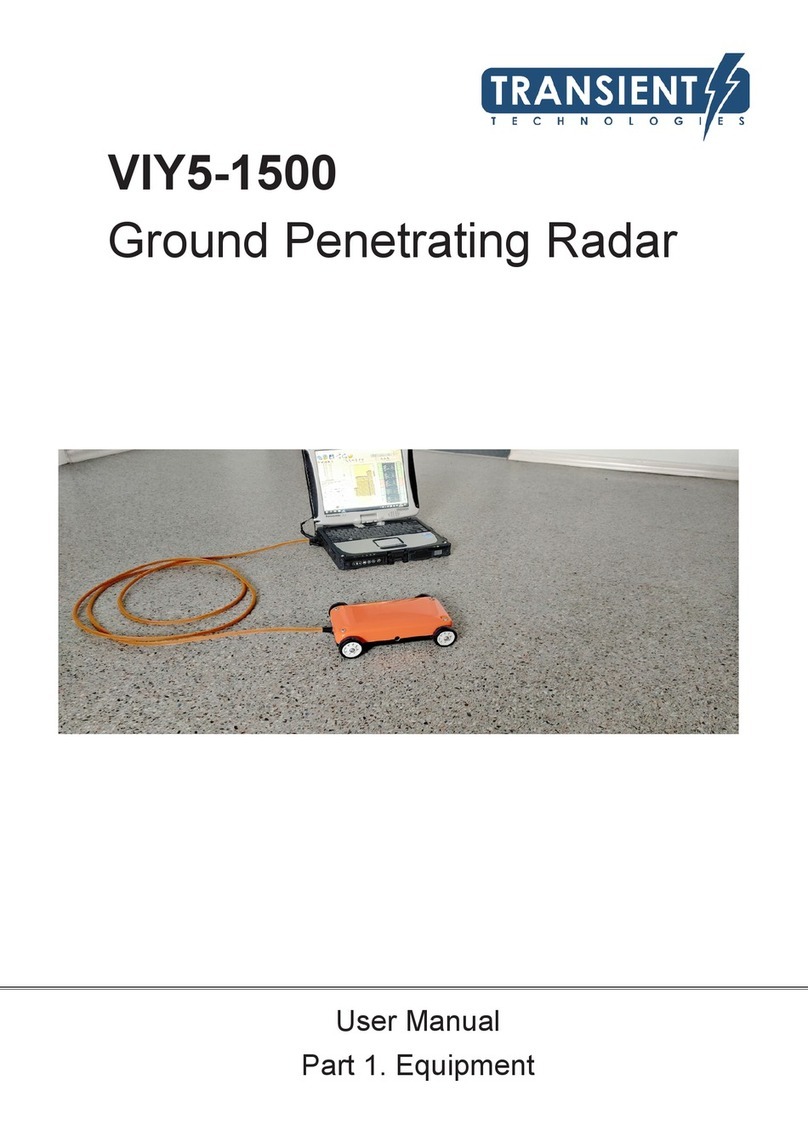
TRANSIENT
TRANSIENT VIY5-1500 user manual
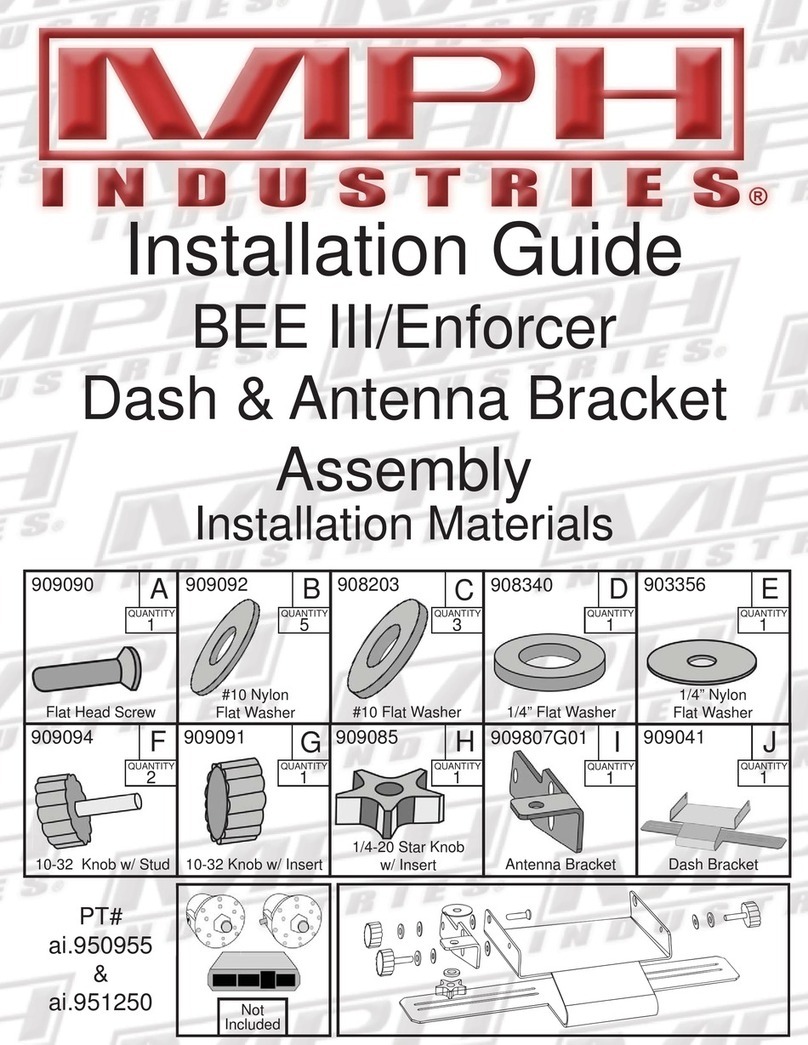
MPH Industries
MPH Industries BEE III installation guide

Endress+Hauser
Endress+Hauser Micropilot FMR51 operating instructions
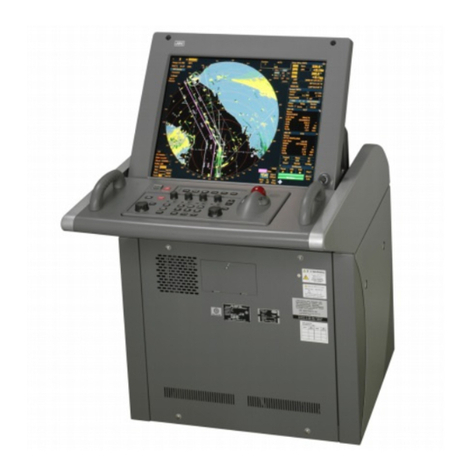
JRC
JRC JMA-933B installation manual