ISB RBPC User manual

Rev. 22
March 2019
P/N: 60 0140 01
RBPC – Resolver Based Press Control
Installation Manual
Complementary to the RBPC User's Manual

Table of contents
1 . Installation Procedure............................................................................................................................................ 3
2 . Installation tips....................................................................................................................................................... 5
2.1 . Front panel mounting..................................................................................................................................... 5
2.2 . Heat considerations....................................................................................................................................... 5
2.3 . Wiring guidelines............................................................................................................................................ 5
2.4 . Grounding essentials..................................................................................................................................... 5
2.5 . Noise considerations...................................................................................................................................... 6
2.6 . Understanding t e fault messages (w at to do?)...........................................................................................6
2.7 . PLS Outputs................................................................................................................................................... 6
3 . System overview.................................................................................................................................................... 7
3.1 . RBPC at first glance....................................................................................................................................... 7
3.2 . Front panel..................................................................................................................................................... 8
3.2.1 . Main mode selector switc ..................................................................................................................... 8
3.2.2 . LED circular array (LCA)........................................................................................................................ 8
3.2.3 . LCD display........................................................................................................................................... 8
3.2.4 . Keypad................................................................................................................................................... 9
3.3 . Rear panel................................................................................................................................................... 10
4 . Connection tables................................................................................................................................................. 11
4.1 . Optional connections................................................................................................................................... 12
5 . Mec anical dimensions........................................................................................................................................ 13
6 . Part c eck list....................................................................................................................................................... 14
7 . Specifications....................................................................................................................................................... 14
8 . Function key......................................................................................................................................................... 14
9 . Outputs................................................................................................................................................................ 14
10 . Troubles ooting................................................................................................................................................. 15
10.1 . Backwards movement detected................................................................................................................. 15
10.2 . Resolver c eck not found........................................................................................................................... 15
10.3 . Brake time exceeded................................................................................................................................. 15
This installation manual is a complement to the RBP User's manual. Please read both documents carefully before
installing and using the RBP
Page 2 of 15

1 Installation Procedure
⚠ IMPORTANT
Before applying power to t e control, make sure t at t e following is connected:
✔ Resolver and proximity switc
✔ J6-9 Top stop switc
✔ J7-4 Aux top stop
✔ J7-5 Aux E-Stop stop
✔ J3-1 Safety lig t curtain input
✔ J3-2 Emergency stop input
T e control as to see t ese inputs, ot erwise faults will be generated and t e setup process will take more time.
Page 3 of 15

STEP1: T e first step is to cut out t e area for t e control
STEP2: Mount t e resolver wit t e spring bracket, t e proximity switc and t e RBPC.
STEP3: Wire t e RBPC as per t e included wiring diagram
STEP4: Put t e mode key-switc in PROG position
STEP5: Clear all t e faults on screen (see section 2.6)
STEP 6: Once t e control states “Press EXIT to Conf.” in t e fourt line of t e display, t en proceed.
STEP 7: Now t e resolver offset must be programmed. Refer to t e Resolver Settings section of t e RBPC User's
Manual for step-by-step instructions.
Page 4 of 15
RESOLVER
RESOLVER CHAIN LINK
PROXIMITY SWITCH AND
MOUNTING BRACKET
Resolver mounted wit a c ain and
sprocket from t e existing cam s aft.
A resolver spring bracket must be
used to avoid damaging t e resolver
due to improper axial load.
T e proximity switc is mounted so t at
it is directly actuated by t e cam of t e
press. T e proximity as to be mounted
so t at it is activated w en t e mac ine
is a t e top dead centre.
Mount t e resolver on t e spring bracket
as s own in t e drawing.
W en t e c ain link is in place, t e
bracket s ould be compressed alf way
in. T is will provide proper load
absorption and will allow an easy removal
of t e c ain if required.

2 Installation tips
2.1 Front panel mountin
T e Front Panel Mounting unit as a sealed front plate and is provided wit four #10-32 bolts for mounting. #10-32
nuts are required to secure t e panel.
2.2 Heat considerations
T e installation enclosure for t e RBPC s ould be at least 76 mm (3”) deep and ave a minimum of 50 mm (2”)
clearance on all sides. No eat producing control or ardware s ould be mounted directly underneat t e RBPC.
2.3 Wirin uidelines
•T e RBPC must be powered from a dedicated 120 V AC line wit an appropriate fuse and power switc .
•Do not wire any ot er devices in series wit wit t e AC power input of t e RBPC (J3-3), suc as air or oil
pressure switc es, counterbalance, die block or any ot er monitoring switc es.
•If ot er s ut-off monitoring devices like t ose mentioned above are required, t ey s ould be wired in line wit
t e E-Stop monitoring input of t e RBPC (J3-2.).
•T e lig t curtain input (J3-1) and E-stop input (J3-2) of t e RBPC are not safety-related and can only be used
for monitoring purposes.
•Do not install 12 V or 24 V wiring in t e same conduits or raceways as t e mac ine ig voltage wiring,
including motor wiring.
•Connect all t e inputs, outputs, resolver and proximity switc es before applying power.
•Appropriate transient suppressor devices must be connected (in parallel) to eac solenoid of t e clutc safety
valve and as close as possible to t e solenoid terminals (see V1 & V2 in figure below). Suitable suppressor
devices can be ordered from ISB (e.g. P/N 56000502).
2.4 Groundin essentials
A proper grounding is essential to t e RBPC operation. Please observe t e following grounding guidelines w en
wiring t e RBPC:
•Use a t ick grounding wire to connect t e c assis GND terminal of t e RBPC to t e eart ground point in t e
control panel.
•T e enclosure itself s ould ave a good eart ground connection. A separate 1.5 mm2 (16 AWG) or t icker
ground wire is essential.
•A star was er s ould be used toget er wit a mounting bolt to ensure a good electrical connection between t e
RBPC c assis and t e enclosure.
•Before finis ing t e installation, measure t e electrical reistance of t e ground wiring to ensure t at it complies
wit t e local electrical codes and regulations.
Page 5 of 15
Figure 1: Connection of transient suppressor devices
CLUTCH DUAL
SAFETY VALVE
V2
V1

2.5 Noise considerations
All motor starters, contactors or any ot er inductive or noise generating devices s ould be mounted in eit er a
separate control panel or in a separate section of t e RBPC enclosure, at least 305 mm (12”) away.
W en t e RBPC is mounted in an enclosure or a control panel, use separate conduit entrances for low voltage
wiring and 120 V AC wiring.
2.6 Understandin the fault messa es (what to do?)
T e faults in t e RBPC are generated one at a time. If a fault occurs, t e fault as to be corrected first and t en it
as to be reset on t e main screen. T e faults are generated and stored like a deck of cards, one on top of anot er.
If multiple faults ave occurred t en once t e first fault is cleared t e next one will appear instantly after t e first. All
errors are saved in memory. If a power down occurs t ose same faults will re-appear t e next time t e control
powers up. Please refer to Appendix 1 in t e RBPC User’s Manual for a detailed listing and explanation of all faults
messages.
2.7 PLS Outputs
In order to cover a wider range of applications wit t e standard configuration, t e PLS outputs of t e RBPC are
factory equipped wit general purpose electromec anical relays. However, it is important to note t at t e service
life of electromec anical relays is inversely proportional to t e load current and to t e number of operations; t at is,
t e greater t e number of cycles t at an electromec anical relay is actuated and t e ig er t e current t roug its
contacts, t e s orter its service life.
T is wear mec anism can be particularly significant w en t e PLS outputs are programmed to operate at relatively
ig speeds (e.g. > 100 cycles per minute), as t ese operating conditions can lead to a premature failure of t e
relay w ic , ultimately, must be replaced.
To address t is problem, ISB recommends t e use of optional solid-state relays, w ic , aving no moving parts,
provide a longer lifetime and trouble free operation.
However, unlike t eir electromec anical counterparts, w ic can be used in a wider range of applications, solid-
state relays must be selected according to t e specific loading conditions (AC or DC, voltage and current) of eac
particular application. Please use t e information in t e table below to select and order optional ISB solid-state
relays:
ISB Part number Description
22 0240 00 Solid-state relay, AC output, 1 A @ 250 V AC (black colour)
22 0242 00 Solid-state relay, DC output, 1 A @ 60 V DC (red colour)
Please also note t at t e load ratings of t e solid-state relays is lower t an t e standard relays provided wit t e
RBPC.
⚠WARNING: Exceeding t e maximum ratings of t e solid-state relays may cause permanent damage
to t e device and may also lead to damage to t e internal circuitry of t e RBPC
Page 6 of 15

3 System overview
3.1 RBPC at first lance
T e RBPC Resolver Based Press Control is a full clutc control wit t e following features:
•Punc Press and Press Brake control modes.
•Built-in brake monitor t at displays stopping time & stopping angle
•Automatically compensates to stop press at top of stroke even wit varying press speed or die weig t.
•Multi-colour LED circular display array s ows press position and displays PLS & Die protection settings.
•Built-in PLS C annels (4), eac wit 4 dwell settings t at are angle on / angle off and include a maximum time
setting and speed compensation feature.
•Built-in Die protection c annels (4), eac wit multiple dwell inputs t at are universally programmable for
function and stop type.
•Additional PLS and die protection c annels available using external circuit boards.
•Built-in 300 jobs storage capability. Eac job stored will contain press parameters suc as operating mode, PLS
settings, die protection settings, brake settings, counter info and muc more!
•Multi-level password protection; Operator level, set-up level, and supervisor level.
•Numerous built-in counters; total strokes, batc , quality, total faults, running time, etc.
•Fault messages and working conditions recording. Fault codes, our meters, last stopping times and a variety of
ot er faults are stored internally for troubles ooting, etc.
•Message center wit 4-line LCD prompts operator and display user information and settings.
•Durable keypad, 27 keys.
•Standard built-in operating modes; Inc , Single Stroke, Continuous, Auto Single Stroke and Timed inc .
•Standard built-in actuating modes; 2 and controls (2 sets), electric foot switc (2) Kwik-Trip, PSDI Mode 1, and
PSDI Mode 2.
•All modes selectable t roug keypad.
•All electrical connections made from t e back of t e panel using plug-in terminal blocks.
•Compact design is easy to install and user friendly.
•Contains many features t at are normally found in ig -end controllers.
Page 7 of 15

3.2 Front panel
3.2.1 Main mode selector switch
T e main selector switc is used to select t e RUN/Program and OFF modes of t e control. T is feature is used for
supervisory purposes. T e unit can be locked out by putting t e key switc in OFF mode and removing t e key.
T e key is also used to lock out programmable features of t e unit during operation.
3.2.2 LED circular array (LCA)
T is is a circular visual interface to allow t e user to know t e angular position of t e w eel of t e mac ine. It also
s ows t e angles in PLS and DIE protection settings. See t e RBPC User’s Manual for furt er details.
3.2.3 LCD display
T e Press control screen s ows ow t e mac ine is operated. It provides t e following information to t e user:
•Current Strokes per minute
•Angular position of t e cranks aft
•Current operation mode
•Current Actuating mode
T e message line at t e bottom of t e LCD screen is used for:
•S owing messages w en an action is required from t e user
•S owing warning and fault messages
T e control tells you ow to operate and run t e mac ine, also it will tell you exactly w at fault as occurred if
anyt ing goes wrong wit t e operation of t e press.
Page 8 of 15

3.2.3.1 Main screen fi ure
3.2.4 Keypad
T e 27-key keypad provides “hot keys” for direct and easy access to t e desired functions. All jobs and settings are
keyed in using t is durable keypad.
Page 9 of 15

3.3 Rear panel
T e rear panel of t e RBPC looks like t is. T e connector positions mig t be different depending on t e version on
t e RBPC. All connections are made to t e appropriate connector directly to t e back of t e panel. T e Die
Protection Inputs2 and t e PLS outputs2 require extra ardware to be purc ased from ISB.
At t e top of t e back panel t ere are eig t relays. T e first four small relays to t e left are t e PLS output relays
and t e four large relays on t e rig t are t e output relays for t e load.
Page 10 of 15
PLS outputs1
Die protection
Inputs1
Inputs1
(palm, FS etc)
Inputs2
(palm, FS etc)
Communications
TIA-232
Resolver
Power (90-250 V AC/DC)
Main outputs
PLS outputs 2
Die protection
Inputs 2
DIP-switc
(for ISB)
Lig t curtain and
valve reference (V)
LEDs description
table
Extra power/GND
Power/fault
LEDs

4 Connection tables
J1: Outputs J2: PLS Outputs
Terminal Function Terminal Function
1 Mute relay (K1, NO) 1 PLS C annel 1 (K2, NO)
2 Mute relay (K1, COM) 2 PLS C annel 1 (K2, COM)
3 Safety relay 1 (K3, NO) 3 PLS C annel 2 (K4, NO)
4 Safety relay 1 (K3, COM) 4 PLS C annel 2 (K4, COM)
5 Safety relay 2 (K5, NO) 5 PLS C annel 3 (K6, NO)
6 Safety relay 2 (K5, COM) 6 PLS C annel 3 (K6, COM)
7 Mute / Fault relay (K7, NO) 7 PLS C annel 4 (K8, NO)
8 Mute / Fault relay (K7, COM) 8 PLS C annel 4 (K8, COM)
J3: Power / Inputs J17: E-Stop and ligtht curtain monitoring inputs
Terminal Function Terminal Function
1 Lig t curtain monitoring input (H) * 1 Neutral (internally connected to J3-4)
2 E-Stop monitoring input (H) * 2 E-Stop monitoring input (L) *
3 Power input, Line ( ot) 3 Lig t curtain monitoring input (L) *
4 Power input, Neutral
5 Protective eart
J4: Resolver J6: Sensor inputs
Terminal Function Terminal Function
1 S4 / A 1 +12 V (ISO) **
2 S2 / B 2 Station 1, button 1
3 S3 / C 3 Station 1, button 2
4 S1 / D 4 Station 2, button 1
5 R2 / E 5 Station 2, button 2
6 R1 / F 6 Foot-switc 1
7 S ield 7 Foot-switc 2
Use cable 55 0556 xx (twisted pairs: R1/R2, S1/S3, S2/S4)
To c ange t e resolver ascending count direction, go to t e
resolver settings in supervisor menu
8 Preset
9 Top stop (NC) *
J5: ommunication interface J7: Inputs
Terminal Function Terminal Function
1 TIA-232 Transmit data 1 (TX1) 1 +12 V (ISO) **
2 TIA-232 Receive data 1 (RX1) 2 Kwik-Trip
3 Signal ground 3 Proximity switc (Resolver c eck, NC) *
4 TIA-232 Transmit data 2 (TX2) 4 Auxiliary Top Stop (NC) *
5 TIA-232 Receive data 2 (RX2) 5 Auxiliary E-Stop (NC) *
6 No connection 6 Reset
J9: Die protection inputs J16: Isolated power output **
Terminal Function Terminal Function
1 0 V (ISO) 1 +12 V (ISO)
2 Die input 1 2 +12 V (ISO)
3 Die input 2 3 +12 V (ISO)
4 Die input 3 4 0 V (ISO
5 Die input 4 ** Total maximum load at +12 V (ISO) < 100 mA
* These signals must be connected in order to run the press. Refer to the RBP wiring diagram for further details.
Page 11 of 15

4.1 Optional connections
J13: Die Protection Inputs 2 J14: PLS Outputs 2
Terminal Function Terminal Function Terminal Function Terminal Function
1 0 V DC ISO 11 DIE11 21 DIE21 1 PLS5
2 0 V DC ISO 12 DIE12 22 DIE22 3 PLS6
3 12 V DC ISO 13 DIE13 23 DIE23 5 PLS7
4 12 V DC ISO 14 DIE14 24 DIE24 7 PLS8
5 DIE5 15 DIE15 25 DIE25 9 PLS9
6 DIE6 16 DIE16 26 DIE26 11 PLS10
7 DIE7 17 DIE17 13 PLS11
8 DIE8 18 DIE18 15 PLS12
9 DIE9 19 DIE19 2, 4, 6, 8 0 V DC ISO
10 DIE10 20 DIE20 10, 12, 14, 16 0 V DC ISO
Page 12 of 15

5 Mechanical dimensions
T e RBPC control is designed to fit in a 261.6 mm (10.3”) long and 167.6 mm (6.6”) wide cut out in an existing
control box or enclosure.
T e outside dimensions are 305 mm (12”) long x 185 mm (7.3”) wide x 46 mm (1.8”) deep.
Leave yourself 75 mm (3”) from t e front panel for wiring and space for t e safety relays on t e back of t e control.
Page 13 of 15

6 Part check list
RBPC-SYS1 or RBPC-SYS2:
Item Description ISB Part Number
1 RBPC Control 56 0774 01
2 Resolver mounting bracket 02 0399 00
3 Proximity switc , PNP, M12 wit integral cable 18 0223 00
4 Proximity switc mounting bracket 02 0202 11
5 Resolver 3/8” s aft (SYS1) or 3/4”s aft (SYS2) 30 0018 01 or 30 0018 02
6 or 3/4” s aft adapter for 30 0018 01 (SYS2) 02 0889 00
7 Resolver cable, 6.1 m (20 ft) 55 0556 20
8 Strap CAM assembly wit lobe 50 0200 00
7 Specifications
Input power 90-250 V DC or AC 50/60 Hz, 48 W max. (internally compensates for fluctuations)
Safety relay output rating 5 A @ 250 V AC, unfused
PLS output relay rating
4 A @ 250 V AC, unfused (standard relays)
1 A @ 250 V AC, unfused (optional AC solid state relay, P/N 22 0240 00)
1 A @ 60 V DC, unfused (optional DC solid state relay, P/N 22 0242 00)
Operating ambient temperature 0 C to 40 C (32 F to 104 F)
Dimensions (H x W x D) 305 mm x 186 mm x 46 mm (12” x 7.3” x 1.8”)
8 Function key
Program Mode
(Key-switc in PROG position) Allows programming of parameters.
OFF Mode
(Key-switc in OFF position) All outputs disabled (de-energized). No programming can occur
RUN Mode
(Key-switc in RUN position) Access to Counters and view Operator settings/ Run t e Press
9 Outputs
Mute / Fault Output
(Safety relay K7)
Used for connecting across t e lig t curtain contacts for t e mute function.
Optionally, it can be used to control external devices or an indicator lig t. T is relay
can be used in conjunction wit t e die protection inputs.
Main Output 1 SR1
(Safety relay K3)
Used for connecting to t e safety switc ing device of t e mac ine (e.g. t e activation
valve of t e press).
Main Output 2 SR2
(Safety relay K5)
Used for connecting to t e safety switc ing device of t e mac ine (e.g. t e activation
valve of t e press).
Mute Output
(Safety relay K1) Used for connecting across t e lig t curtain contacts for t e mute function.
Page 14 of 15

10 Troubleshootin
T e following guidelines will elp you to troubles oot some of t e most common fault messages t at appear during
t e initial installation of t e RBPC:
10.1 Backwards movement detected
If t is fault occurs w ile doing t e initial setup it means t at t e resolver is not set to turn in t e correct direction.
C ange t e direction of t e resolver signals in t e supervisor menu. T is feature can be c anged in t e Supervisor
Menu → Resolver Settings → Set Work Direction.
If t is fault occurs after t e setup and running of t e press is complete, it could be cause by a loose gear on t e
resolver. A temporary fix would be to increase t e Backwards detection window. T is is done in t e Supervisor Menu
→ Resolver Settings → Movement Detection.
Please refer to t e Resolver settings section of t e RBPC User's Manual for furt er details and step-by-step
instructions.
10.2 Resolver check not found
T is fault could occur because t e resolver offset or zero position is not set correctly. To set t e resolver offset go to
t e Supervisor menu → Resolver settings → Resolver offset.
T is fault also could be generated because t e Proximity switc , w ic is used for t e top dead center c eck,
(resolver c eck) is not being activated properly. C eck t e proximity switc and input on J7-3. T ere are small LED
above t e inputs used to verify activation of t e sensor.
Please refer to t e Resolver settings section of t e RBPC User's Manual for furt er details and step-by-step
instructions.
10.3 Brake time exceeded
T is fault is generated because t e stopping time of t e press exceeds t e programmed value in t e RBPC. C eck
t e stopping time of t e press using t e Brake Wear ot key and c ange t e parameters of t e brake settings in t e
supervisor menu to correspond to t e viewed value. T is can be done t roug t e Supervisor menu → Braking
settings. View section 14 of t e User’s Manual on all t e details for t e brake settings.
Please refer to t e Braking settings section of t e RBPC User's Manual for furt er details and step-by-step
instructions.
✎If you have any other problems or questions, please call your local ISB representative
Page 15 of 15
Other manuals for RBPC
1
Table of contents
Popular Control Unit manuals by other brands
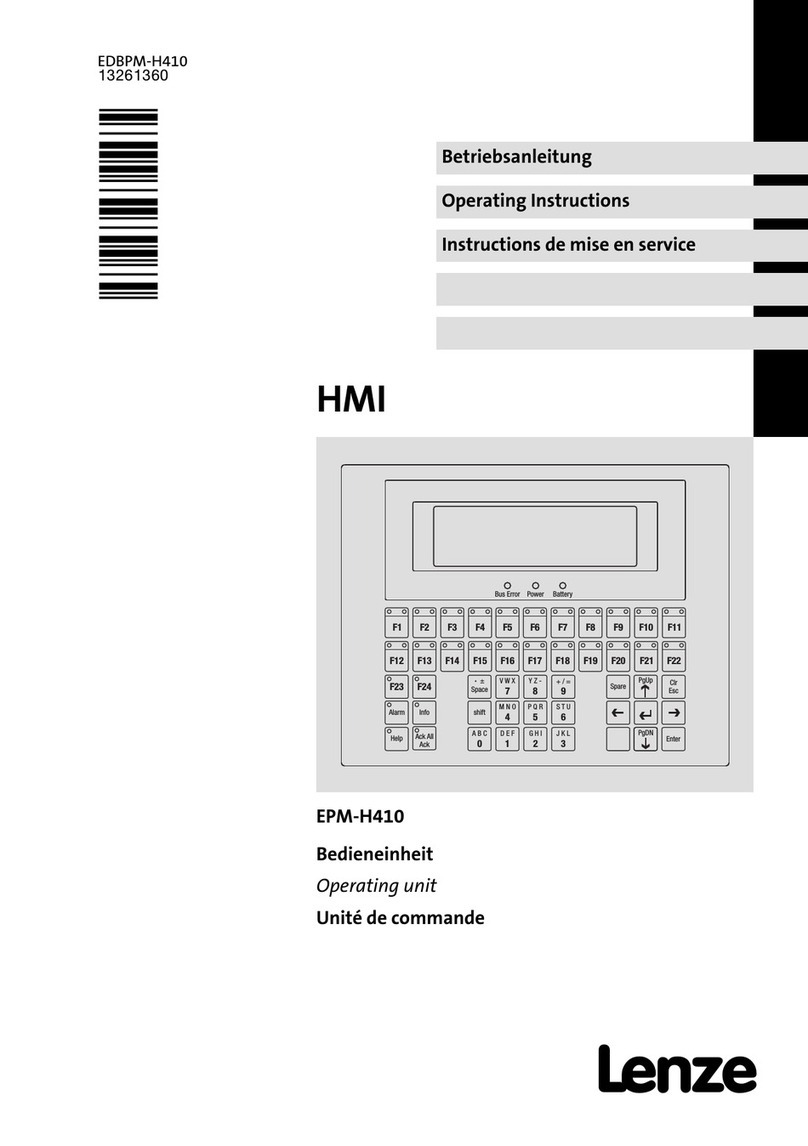
Lenze
Lenze EPM-H410 operating instructions
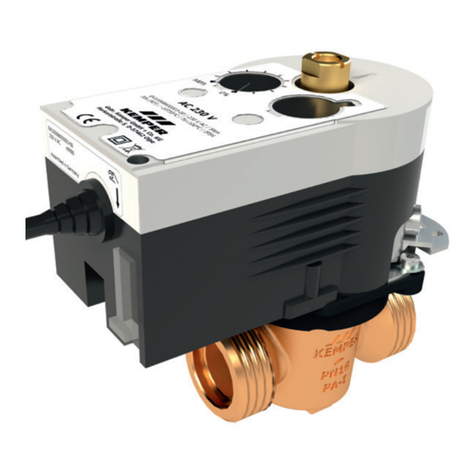
Kemper
Kemper kHS 686 00 Installation and operating instructions
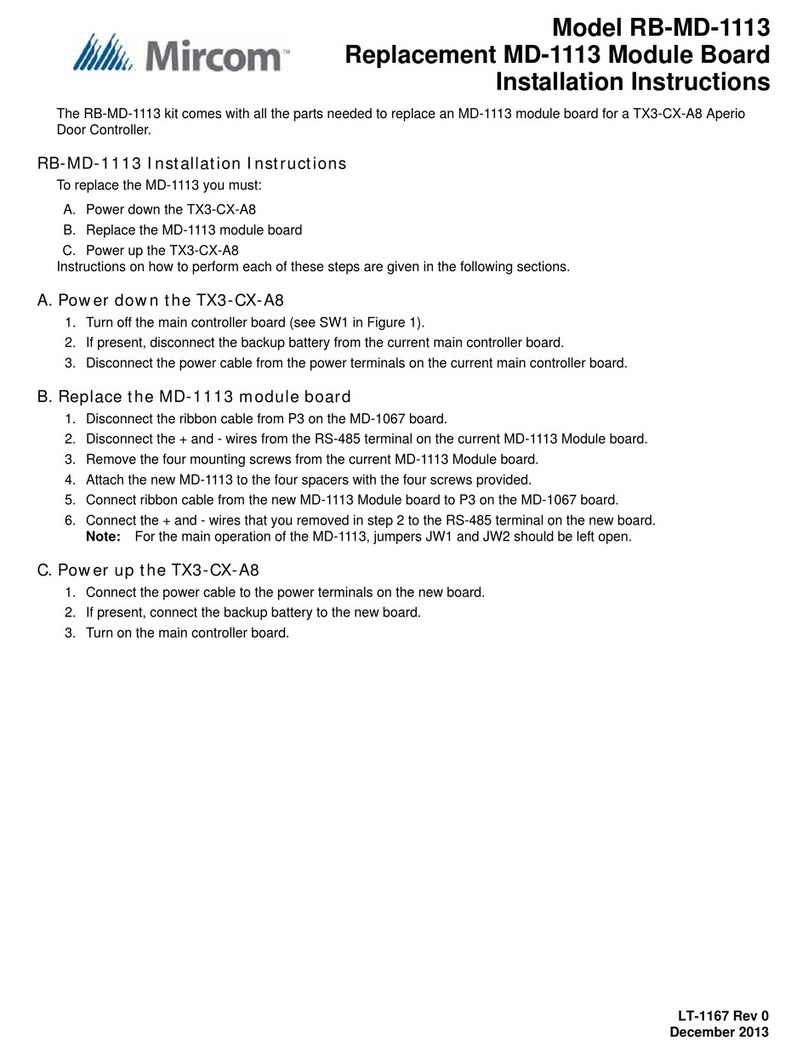
Mircom
Mircom RB-MD-1113 installation instructions
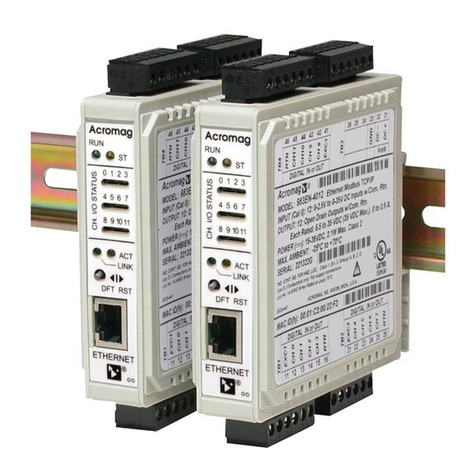
Acromag
Acromag BusWorks 900EN Series user manual
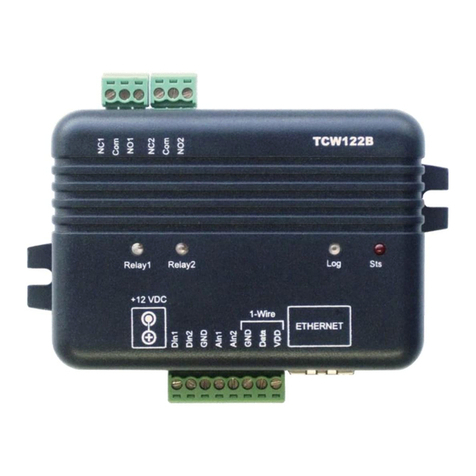
Teracom
Teracom TCW122B-CM user manual
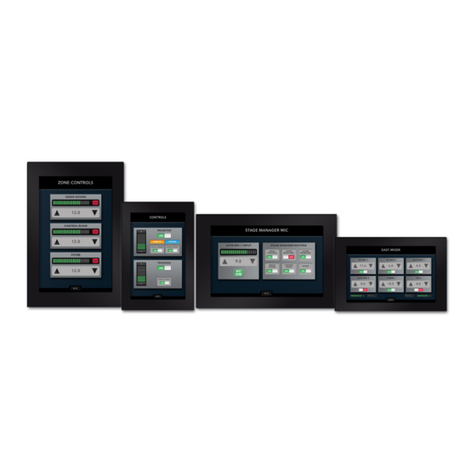
Xilica Audio Design
Xilica Audio Design XTouch Series: XTouch50 user manual