Jäger ADwin-Pro Operating and installation instructions

ADwin-Pro, -Pro II
System and hardware description
ADwin-Pro Hardware, manual version 2.9, June 2006

ADwin-Pro Hardware, manual version 2.9, June 2006
Jäger Computergesteuerte
Messtechnik GmbH
Rheinstraße 2-4
D-64653 Lorsch
Germany
For any questions, please don’t hesitate to contact us:
Hotline: +49 6251 96320
Fax: +49 6251 5 68 19
E-Mail: [email protected]
Internet www.ADwin.de

ADwin-Pro Hardware, manual version 2.9, June 2006 III
ADwin
Table of contents
Typographical Conventions . . . . . . . . . . . . . . . . . . . . . . . . . . . . . . . . . . . . . . . . . . . . . . . IV
1 The ADwin-Pro system . . . . . . . . . . . . . . . . . . . . . . . . . . . . . . . . . . . . . . . . . . . . . . . . . . 1
2 How to Install an ADwin-Pro System . . . . . . . . . . . . . . . . . . . . . . . . . . . . . . . . . . . . . . . .2
3 Operating Environment . . . . . . . . . . . . . . . . . . . . . . . . . . . . . . . . . . . . . . . . . . . . . . . . . . . 3
4 Enclosures for the ADwin-Pro System . . . . . . . . . . . . . . . . . . . . . . . . . . . . . . . . . . . . . . 4
4.1 ADwin-Pro. . . . . . . . . . . . . . . . . . . . . . . . . . . . . . . . . . . . . . . . . . . . . . . . . . . . . . . . .5
4.2 ADwin-Pro-DC . . . . . . . . . . . . . . . . . . . . . . . . . . . . . . . . . . . . . . . . . . . . . . . . . . . . . 7
4.3 ADwin-Pro-BM . . . . . . . . . . . . . . . . . . . . . . . . . . . . . . . . . . . . . . . . . . . . . . . . . . . . . 8
4.4 ADwin-Pro-light . . . . . . . . . . . . . . . . . . . . . . . . . . . . . . . . . . . . . . . . . . . . . . . . . . . .9
4.5 ADwin-Pro-mini . . . . . . . . . . . . . . . . . . . . . . . . . . . . . . . . . . . . . . . . . . . . . . . . . . .10
5 ADwin-Pro Modules . . . . . . . . . . . . . . . . . . . . . . . . . . . . . . . . . . . . . . . . . . . . . . . . . . . .11
5.1 Setting the module’s addresses. . . . . . . . . . . . . . . . . . . . . . . . . . . . . . . . . . . . . . . .11
5.2 Processor modules. . . . . . . . . . . . . . . . . . . . . . . . . . . . . . . . . . . . . . . . . . . . . . . . . 13
5.3 Pro II: Analog Input Modules. . . . . . . . . . . . . . . . . . . . . . . . . . . . . . . . . . . . . . . . . . 23
5.4 Pro II: Analog Output Modules. . . . . . . . . . . . . . . . . . . . . . . . . . . . . . . . . . . . . . . . .33
5.5 Pro I: Analog Input Modules. . . . . . . . . . . . . . . . . . . . . . . . . . . . . . . . . . . . . . . . . . . 38
5.6 Pro I: Analog Output Modules. . . . . . . . . . . . . . . . . . . . . . . . . . . . . . . . . . . . . . . . . 77
5.7 Pro I: Analog Input and Output Modules. . . . . . . . . . . . . . . . . . . . . . . . . . . . . . . . . 90
5.8 Pro I: Digital-I/O- and Counter Modules. . . . . . . . . . . . . . . . . . . . . . . . . . . . . . . . . . 93
5.9 Pro I: Signal Conditioning and Interface Modules. . . . . . . . . . . . . . . . . . . . . . . . . 155
6 Calibration . . . . . . . . . . . . . . . . . . . . . . . . . . . . . . . . . . . . . . . . . . . . . . . . . . . . . . . . . . 191
6.1 General information. . . . . . . . . . . . . . . . . . . . . . . . . . . . . . . . . . . . . . . . . . . . . . . .191
6.2 Calculation basis. . . . . . . . . . . . . . . . . . . . . . . . . . . . . . . . . . . . . . . . . . . . . . . . . . 192
6.3 Calibrating a module. . . . . . . . . . . . . . . . . . . . . . . . . . . . . . . . . . . . . . . . . . . . . . . 194
6.4 Calibration with ADbasic Programs. . . . . . . . . . . . . . . . . . . . . . . . . . . . . . . . . . . . 197
6.5 Programs for calibration. . . . . . . . . . . . . . . . . . . . . . . . . . . . . . . . . . . . . . . . . . . . . 199
7 Accessories . . . . . . . . . . . . . . . . . . . . . . . . . . . . . . . . . . . . . . . . . . . . . . . . . . . . . . . . .203
7.1 Cable Sets for ADwin-Pro Systems. . . . . . . . . . . . . . . . . . . . . . . . . . . . . . . . . . . 203
7.2 Adapter sets. . . . . . . . . . . . . . . . . . . . . . . . . . . . . . . . . . . . . . . . . . . . . . . . . . . . . . 203
7.3 Reference addresses. . . . . . . . . . . . . . . . . . . . . . . . . . . . . . . . . . . . . . . . . . . . . . . 203
Annex. . . . . . . . . . . . . . . . . . . . . . . . . . . . . . . . . . . . . . . . . . . . . . . . . . . . . . . . . . . . . . . A-1
A.1 Table of Figures. . . . . . . . . . . . . . . . . . . . . . . . . . . . . . . . . . . . . . . . . . . . . . . . . . . A-1
A.2 Alphabetic List of Modules. . . . . . . . . . . . . . . . . . . . . . . . . . . . . . . . . . . . . . . . . . . A-9

Typographical Conventions ADwin
IV ADwin-Pro Hardware, manual version 2.9, June 2006
Typographical Conventions
"Warning" stands for information, which indicate damages of hardware or soft-
ware, test setup or injury to persons caused by incorrect handling.
You find a "note" next to
– information, which have absolutely to be considered in order to guaran-
tee an operation without any errors
– advice for efficient operation
"Information" refers to further information in this documentation or to other
sources such as manuals, data sheets, literature, etc.
<C:\ADwin\ …> File names and paths are placed in angle brackets and characterized in the
font Courier New.
Program text Program instructions and user inputs are characterized by the font Courier
New.
Var_1 ADbasic source code elements such as INSTRUCTIONS, variables, com-
ments and other text are characterized by the font Courier New and are
printed in color (see also the editor of the ADbasic development environment).
Bits in data (here: 16 bit) are referred to as follows:
BitNo. 151413…0100
Bit value 215 214 213 …21=2 20=1
Synonym MSB - - - - LSB

ADwin-Pro Hardware, manual version 2.9, June 2006 1
The ADwin-Pro system
ADwin
1TheADwin-Pro system
The ADwin-Pro system is an external processing system with modular expan-
sion options. Depending on applications, the different enclosures can be
equipped with ADwin-Pro modules.
Since middle of 2005 there are 2 versions of ADwin-Pro:
–ADwin-Pro I: The classic ADwin-Pro system for approved Pro I modules
and the processors T9 and T10.
–ADwin-Pro II: The new ADwin-Pro system for existing Pro I modules,
new Pro II modules and the processor T11.
When the ADwin-Pro system was developed great attention was paid to the
electromagnetic compatibility. The ADwin-Pro system and all available input
and output modules have the CE sign and can therefore be configured differ-
ently later if necessary.
Applicable modulesEach ADwin-Pro system needs a processor module. It communicates via Eth-
ernet or USB with the PC or notebook; previous versions used a serial link con-
nection.
In order to meet the various requirements for measurement and control tasks
the system can be equipped with the following modules:
– analog input modules and analog output modules
– digital input modules and digital output modules
– counters
– filters, isolation amplifiers
– amplifiers for thermocouples and PT100 resistors
– serial communication interfaces (CAN, RSxxx, Fieldbus)
– storage / read module for PCMCIA storage media
Revision IdentifierSince middle of 2002 all modules have a revision identifier written on the mod-
ule front, e.g. Rev. A2, Rev. B3, Rev. C3. Earlier delivered modules have no
identifier; they are to be considered as revision "Rev. A".
Different revision characters mean different module properties and are
described separately.
The revision identifier is followed by a minor counting number, which is mainly
used for internal purposes of Jaeger Computergesteuerte Messtechnik GmbH.
All modules for ADwin-Pro II have the revision identifier Rev. E1 or higher. This
is true for both advancements out of Pro I modules and for newly developped
modules.

How to Install an ADwin-Pro System ADwin
2ADwin-Pro Hardware, manual version 2.9, June 2006
2 How to Install an ADwin-Pro System
Please keep strictly to the following order:
1. Start with the manual "ADwin installation":
• Installation of software and interface drivers from the
ADwin-CDROM.
• Initialization of data connection from PC to ADwin system as well
as operational test.
2. First steps with the ADbasic Tutorial .
3. Programming in ADbasic.
The ADbasic manual describes the real-time development environment,
the structure of an ADbasic program and gives hints for optimizations.
You also find all this information in the ADbasic online help.
The ADbasic instructions are described in these documents:
For operation, please pay attention to the notes in this manual concerning the
respective modules.
•ADbasic manual: Basic instructions for calculation, pro-
gram structure and process control.
•ADwin-Pro software
manual:
Instructions and hints for accessing
the Pro modules.
• Online help: Instructions from both ADbasic man-
ual and ADwin-Pro software manual.
Please note:
For ADwin systems to function correctly, adhere strictly to the information pro-
vided in this documentation and in other mentioned manuals.
Qualified personnel Programming, start-up and operation, as well as the modification of program
parameters must be performed only by appropriately qualified personnel.
Qualified personnel are persons who, due to their education, experience
and training as well as their knowledge of applicable technical stan-
dards, guidelines, accident prevention regulations and operating condi-
tions, have been authorized by a quality assurance representative at the
site to perform the necessary acivities, while recognizing and avoiding
any possible dangers.
(Definition of qualified personnel as per VDE 105 and ICE 364).
Availability of the
documents
This product documentation and all documents referred to, have always to be
available and to be strictly observed. For damages caused by disregarding the
information in this documentation or in all other additional documentations, no
liability is assumed by the company Jäger Computergesteuerte Messtechnik
GmbH, Lorsch, Germany.
Legal information This documentation, including all pictures is protected by copyright. Reproduc-
tion, translation as well as electronical and photographical archiving and mod-
ification require a written permission by the company Jäger Computergesteu-
erte Messtechnik GmbH, Lorsch, Germany.
OEM products are mentioned without referring to possible patent rights, the
existence of which, may not be excluded.
Subject to change.

ADwin-Pro Hardware, manual version 2.9, June 2006 3
Operating Environment
ADwin
3 Operating Environment
Earth protectionThe ADwin-Pro device must be earth-protected, in order to
– build a ground reference point for the electronic
– conduct interferences to earth.
Connect the GND clamp / plug via a short low-impedance solid-type cable to
the central earth connection point of the controlled system. The GND plug is
internally connected with ground and the enclosure.
Galvanic connectionIn the Ethernet cable the data lines are galvanically isolated, but the ground
potentials are connected, because the shielding of the Ethernet connector
(RJ-45) is connected to GND.
Excluding transient
currents
Transient currents, which are conducted via the aluminum enclosure or the
shielding, have an influence on the measurement signal.
Please, make sure that the shielding is not reduced, for instance by taking
measures for bleeding off interferences, such as connecting the shielding to
the enclosure just before entering it. The more frequently you earth the shield-
ing on its way to the controlled system the better the shielding will be.
Use cables with shielding on both ends for signal lines. Here too, you should
reduce the bleeding off of interferences via the enclosure by using screen clips.
Supply voltageOperate the device with the defined and fitting supply voltage. For operation
with an external power supply, the instructions of the manufacturer apply.
Close the device for operation, use cover plates to cover gaps between built-in
modules.
Ambient atmosphereADwin-Pro is designed for operation in dry rooms with an ambient temperature
of +5°C … +50°C and a relative humidity of 0 … 80% (no condensation). The
device may be operated in a control cabinet or mobile (e.g. in a car).
Chassis temperatureThe temperature of the chassis (surface) must not exceed +60°C, even under
extreme operating conditions – e.g. in a control cabinet or if the system is
exposed to the sun for a longer period of time. You risk damages at the device
or not-defined data (values) are output which can cause damages at your mea-
surement device under unfavorable circumstances.
For use in a control cabinet, please note:
– The device shall not pe placed above strong heat sources, e.g. a high
power transformer.
– Ventilation inside the control cabinet towards and from the ADwin-Pro
device mus be provided.
Especially, the ventilation slots of the device must be kept free, so that
the device can lead off its generated heat completely.

Enclosures for the ADwin-Pro System ADwin
4ADwin-Pro Hardware, manual version 2.9, June 2006
4 Enclosures for the ADwin-Pro System
The different sizes for the enclosures depend on the number of slots and the
kind of power supply.
Each enclosure type is available for both the classic ADwin-Pro I and the new
ADwin-Pro II:
With ADwin-Pro II systems, the number of slots is given for Pro II modules. If
Pro I modules be used – in combination with Pro II modules or not – less mod-
ules fit into the enclosure
For the slot area (including power supply slot) the following dimensions apply:
The slots mostly have a width of 5 HP = 1 inch.
Plug-in a module You plug-in a module into the enclosre like this:
– Switch off the ADwin device! A module may sustain damage if you plug
it in or out with the power supply switched on.
– Remove one or more cover plates at the wanted position, until the bear-
ings be seen at the left edge: one upper and one lower bearing.
Specific features for ADwin-Pro II enclosures:
• Pay attention to the color of the bearings. There are different,
offset bearings for Pro I and Pro II modules:
White bearings: Pro II modules.
Black bearings: Pro II modules.
• The processor module has a fixed position, no other position can
be used.
– Insert the board carefully into both bearings, plug ahead. If positioned
correctly the module cannot be skewed.
– Push the module into the enclosure. At the end the push gets harder
while the module plug slides into the socket of the back plane.
The module’s front panel should butt against the enclosure.
– Fix the module with the screws at top and bottom of the front panel.
– If there are, close the gaps between plugged-in modules using the cover
plates. There are plates with 2, 3 or 5 HP width.
Enclosure Number of
Slots Power supply
ADwin-Pro 16 100V…240V AC
ADwin-Pro-DC 16 10V…35V DC
ADwin-Pro-BM 15 100V…240V AC
ADwin-Pro-light 7100V…240V AC
ADwin-Pro-mini 55V DC
ADwin-Pro-mini-2 510V…18V DC
ADwin-Pro-mini-3 520V…36V DC
1 HP = 1/5 inch = 5.08mm 1 U = 5/3 inch = 42.3mm

ADwin-Pro Hardware, manual version 2.9, June 2006 5
ADwin-Pro
ADwin
4.1 ADwin-Pro
Pro with 16 slotsThe standard enclosure for the ADwin-Pro systems. The backplane of the
enclosure connects the processor module with the ADwin-Pro modules.
The system fuse is located in a slot in the power supply unit above the socket
for the power supply cable (rear of the enclosure).
At the rear of the enclosure, above the power supply connector you will find a
label with the revision number:
4.1.1 ADwin-Pro I
The processor module (T9 or T10) can be plugged-in at any position.
Fig. 2 – Enclosure ADwin-Pro I (up to Rev. B3)
4.1.2 ADwin-Pro I
The Pro II enclosure is designed for both Pro I and Pro II modules: The back
plane comprises the Pro I bus as well as the Pro II bus. The processor module
runs both buses in parallel.
Number of Slots 16
Main dimensions (l x w x h)
Slot area (w x h)
336mm × 447.5mm × 146mm
84 HP × 3 U
Power supply unit min. 70W, 100V…240VAC at 50/60Hz
switching power supply
Fuse 5A, delayed-action fuse
Fig. 1 – Enclosure ADwin-Pro: Specification
Revision Release Previous versions
A 1997 First version with linear power supply.
B1 Sep. 1999 Prototype (internal use only, not delivered to cus-
tomers)
B2 Jun. 2003 Internal structure modified, function unchanged.
B3 Jun. 2004 New power supply (switching power supply) with
automatical voltage adaptation.
E1 Jun. 2005 ADwin-Pro II: New enclosure design and new back
plane with Pro I and Pro II bus.
74 5 61 2 3 8 1512 13 14910 11 16
POWER
ON
ADwin-Pro
GND

ADwin-Pro I ADwin
6ADwin-Pro Hardware, manual version 2.9, June 2006
Fig. 3 – Enclosure ADwin-Pro II (up from Rev. E1)
Please note that modules for Pro I bus (grey in fig. 3) and for Pro II bus have
different plug-in positions. You recognize the right position easily by the color
of the bearings:
– White bearings: Modules for Pro II bus.
– Black bearings: Modules for Pro I bus.
Output modules Pro-AOut-x with Rev. A may not be used for technical
reasons.
The processor module must be plugged-in at the middle position (white bear-
ings).
There is a gap of half a slot between processor module and Pro I modules
(cover plates accompanied), while Pro II modules fit directly besides the pro-
cessor module.
74 5 61 2 3 1411 12 138 9 10 15
POWER
ADwin-Pro II
8641235 7910111213
CPU-T11
ADwin-Pro
DIG I/O 0
EVENT IN
ST BU
AC LI
ETHERNET
DIG I/O 1
Modules for Pro II-BusModules for Pro II-Bus
Modules for Pro I-Bus Modules for Pro I-Bus

ADwin-Pro Hardware, manual version 2.9, June 2006 7
ADwin-Pro-DC
ADwin
4.2 ADwin-Pro-DC
Pro-DC
with 16 slots
The ADwin-Pro-DC enclosure is similar to the standard enclosure ADwin-Pro,
but is equipped with a DC power supply.
If a current-limited power supply unit is used, it should be able to supply a mul-
tiple of the idle current during power-up to maintain proper performance of the
system.
Fig. 4 – Enclosure ADwin-Pro-DC:
Detailed view of the pin assignment
At the rear of the enclosure, above the power supply connector you will find a
label with the revision number:
Number of Slots 16
Main dimensions (l x w x h)
Slot area (w x h)
336mm × 447.5mm × 146mm
84 HP × 3 U
Power supply unit min. 80W, DC-DC converter 10V…35V
Fig. 5 – Enclosure ADwin-Pro-DC: Specification
Revision Release Änderung zur Vorgänger-Version
A 1997 First version with linear power supply.
B1 Sep. 1999 Prototype
(internal use only, not delivered to customers)
B2 Jun. 2003 Internal structure modified, function unchanged.
B3 Nov. 2003 Various improvements
E1 Jun. 2005 ADwin-Pro II: New enclosure design and new back
plane with Pro I and Pro II bus.
3
4
2
1
V
CC
V
CC
GND
GND
PE

ADwin-Pro-BM ADwin
8ADwin-Pro Hardware, manual version 2.9, June 2006
4.3 ADwin-Pro-BM
Pro "backmounted" with
15 slots
In the version "backmounted" of the standard enclosure, the modules are
plugged-in at the rear of the enclosure.
The revisions are similar to those of the ADwin-Pro enclosure.
Fig. 6 – Enclosure of ADwin-Pro I-BM (rear panel)
Fig. 7 – Enclosure of ADwin-Pro II-BM (rear panel)
The system fuse is located in a slot in the power supply unit above the socket
for the power supply cable (rear of the enclosure).
At the rear of the enclosure, above the power supply connector you will find a
label with the revision number:
Number of Slots 16
Main dimensions (l x w x h)
Slot area (w x h)
336mm × 447.5mm × 146mm
84 HP × 3 U
Power supply unit min. 70W, 100V…240VAC at 50/60Hz
switching power supply
Fuse 5A, delayed-action fuse
Fig. 8 – Enclosure of the ADwin-Pro-BM: Specification
Revision Release Previous versions
A 1997 First version with linear power supply.
B1 Sep. 1999 Prototype
(internal use only, not delivered to customers)
B2 Jun. 2003 Internal structure modified, function unchanged.
B3 Nov. 2003 New power supply (switching power supply) with
automatical voltage adaptation.
E1 Jun. 2005 ADwin-Pro II: New enclosure design and new back
plane with Pro I and Pro II bus.
63 4 51 2 7 1411 12 138 9 10 15
POWER
ON
230V
115 / 230 VAC
GND
63 4 51 2
POWER
ON
230V
115 / 230 VAC
GND
CPU-T11
ADwin-Pro
DIG I/O 0
EVENT IN
ST BU
AC LI
ETHERNET
DIG I/O 1
71411 12 138 9 10
4123 5 75 6 8 9 10 11 12

ADwin-Pro Hardware, manual version 2.9, June 2006 9
ADwin-Pro-light
ADwin
4.4 ADwin-Pro-light
Pro-light with 7 slots
The ADwin-Pro-light enclosure. The backplane of the enclosure connects the
processor module with the ADwin-Pro modules.
At the rear of the enclosure, above the power supply connector you will find a
label with the revision number:
Enclosure ADwin-Pro I-light Enclosure ADwin-Pro II-light
Number of Slots 7
Main dimensions (l x w x h)
Slot area (w x h)
336mm × 234mm × 146mm
42 HP × 3 U
Power supply unit min. 40W, 100…240VAC at 50/60Hz
switching power supply
Fuse 2A, delayed-action fuse
Fig. 9 – Enclosure ADwin-Pro-light: Specification
Revision Release Previous versions
A1 1997 First version with linear power supply.
A2 Jun. 2004
New power supply (switching power supply) with
automatical voltage adaptation.
Internal structure modified.
A3 Aug. 2004 Various improvements
E1 Jun. 2005 ADwin-Pro II: New enclosure design and new back
plane with Pro I and Pro II bus.
74 5 61 2 3
POWER
ON
ADwin-Pro
GND
4 5 61 2 3
POWER
ADwin-Pro II
213456
CPU-T11
ADwin-Pro
DIG I/O 0
EVENT IN
ST BU
AC LI
ETHERNET
DIG I/O 1

ADwin-Pro-mini ADwin
10 ADwin-Pro Hardware, manual version 2.9, June 2006
4.5 ADwin-Pro-mini
The ADwin-Pro-mini enclosure is available in 3 versions, each of which works
with a different power supply voltage. In any case an external power supply unit
is required.
The enclosure type ADwin-Pro-mini for Pro II is being developped.
Pro-mini with 5 slots
Fig. 10 – Enclosure ADwin-Pro-mini
The required power of the external power supply unit depends on the type and
number of the used modules; we recommend a power of at least 20W.
The connector for the external power supply unit as well as a 4A fuse can be
found at the rear of the ADwin-Pro-mini enclosure (see fig. 12).
Fig. 12 – Enclosure ADwin-Pro-mini:
Rear and detail of the pin assignment
At the rear of the enclosure you will find a label with the revision number:
Number of Slots 5
Main dimensions (l x w x h)
Slot area (w x h)
253mm × 147.3mm × 146mm
20 HP × 3 U
Fuse 4A, delayed-action fuse
External power supply unit external power supply unit required
mini 5V DC, 4A
mini-2 10V…18V DC
mini-3 20V…36V DC
Fig. 11 – Enclosure ADwin-Pro-mini Specification
Revision Release Previous versions
A 1998 First version
41 2 3 5
1 2 3
1 2 3
JÄGER MESSTECHNIK GmbH LORSCH
FUSE POWER
5 VDCT 4A
1 2 3
1 2 3
V
CC
GND PE

ADwin-Pro Hardware, manual version 2.9, June 2006 11
ADwin-Pro Modules
ADwin
5ADwin-Pro Modules
An ADwin-Pro module needs one slot (5 HP) in an ADwin-Pro system, some
modules need 2 slots.
All technical data of the module refer to a device which is powered-up.
For pluggin-in a module into the enclosure please note the description on
page 4, especially with ADwin-Pro II enclosures.
5.1 Setting the module’s addresses
Any ADwin-Pro module (except CPU modules) is addressed in an ADbasic
program via its module address. The module address is free selectable.
Selecting a module’s address
Note the following rules for selecting a module’s address:
– A module address mut be unique inside its module group.
Each module is member of a module group:
• Pro I modules, functional group CPU: processor modules.
• Pro I modules, functional group ADC: analog input modules.
• Pro I modules, functional group DAC: analog output modules.
• Pro I modules, functional group DIO: digital input/output modules,
relays and counter modules.
• Pro I modules, functional group EXT: special modules of all kind.
• All Pro II modules.
– A module address must be within the following limits:
• Pro I modules: 1 … 255.
• Pro II modules: 1 … 15.
There are special limits for RSxxx- and fieldbus modules (see below)
It is true that you can select the same module address for modules of different
groups. Nevertheless we recommend to use unique adresses in order to pre-
vent a mix-up.
Setting the module’s adress: Pro II modules
With Pro II modules you set the module address with the program ADpro. Set-
tin the address also resets the Pro modules to initial state.
Switch off the power supply of the ADwin system and insert the Pro II modules
into the casing; please note the description on page 4. Power up the ADwin
system again.
Afterwards you start the program ADpro from the Windows Start menu under
Programs ADwin. Select the module address with the menu entry Edit
Set module adresses.
Setting the module’s adress: Pro I modules
With Pro I modules you set the module address manually via DIP-switches.
The on-board block of DIP-switches is located right to the bottom.
Wit 8 DIP switches the address is selectable between 1 and 255 (see fig. 13).
Each module of the same group needs to have a different address.

Setting the module’s addresses ADwin
12 ADwin-Pro Hardware, manual version 2.9, June 2006
Please note:
– A RSxxx module with 4 serial interfaces uses 2 addresses (group EXT):
the set address and the following address.
– A fieldbus module uses 32 addresses (group EXT); the address alloca-
tion is shown in fig. 14.
Module no. Settings of DIP switches
1 2 3 4 5 6 7 8
1 10000000
2 01000000
3 11000000
4 00100000
5 10100000
6 01100000
7 11100000
8 00010000
……
254 01111111
255 11111111
Fig. 13 – Address settings of the ADwin-Pro modules with DIP switches
ON
12345678
A0 A1 A2 A3A4 A5 A6 A7
ON
12345678
DIP-switch block
Set module
address
Addit. allocated
addresses
Settings of DIP switches
1 2 3 4 5 6 7 8
1 160…191 10000000
2 192…223 01000000
3 224…255 11000000
4 128…159 00100000
Fig. 14 – Address settings of fieldbus modules with DIP switches

ADwin-Pro Hardware, manual version 2.9, June 2006 13
Processor modules
ADwin
5.2 Processor modules
For each ADwin-Pro system one processor module is required. This processor
module is the center of a Pro system and performs the following tasks:
– Communication with PC or laptop.
The data connection is established via USB or Ethernet; former version
used a serial link connection.
– Communication with other ADwin-Pro modules via internal Pro bus.
– Srarting and runing the user defined processes.
The processor module provides the memory for data and programs, divided
into a fast internal memory (SRAM) and an external memory (DRAM).
Overview CPU modulesThe processor modules differ mainly in computing power (clock rate):
Input Event InThe external trigger input (Event In) enables the processor module to recog-
nize an external signal as trigger for an event and trigger a process, that is pro-
cessed immediately and completely (see ADbasic manual, chapter: Structure
of the ADbasic program).
The event signal has to be present for 50ns to be recognized (specified value
for CPU-T9 in basic version; 25ns are typical).
Alternatively, the event input of an other module may be used. All event signals
arrive at the same signal line of the processor module as the input Event In
does.
Module Pro-CPU-T9 Pro-CPU-T9-
ENET / -USB
Pro-CPU-T10-
ENET
System Pro I Pro I Pro I
Processor ADSP 21062 ADSP 21062 ADSP 21162
Clock rate 40MHz 40MHz 80MHz
Data connection Link Ethernet, USB Ethernet, USB
Internal
memory
256kB
opt. 512kB
256kB
opt. 512kB 512kB
External
memory
4MB
opt. 16 / 32MB
16MB
opt. 64MB 128MB
Inputs Event In Event In
opt. Digin 0
Event In
Digin 0
Module Pro-CPU-T11
System Pro II
Processor ADSP
TS101S
Clock rate 300MHz
Data connection Ethernet
Internal
memory 768kB
External
memory 256MB
Inputs Event In
DigIO 0,
DigIO 1
Fig. 15 – Overview Pro CPU modules

Processor modules ADwin
14 ADwin-Pro Hardware, manual version 2.9, June 2006
5.2.1 Pro-CPU-T9
Fig. 16 – Pro-CPU-T9: Block diagram
Fig. 18 – Pro-CPU-T9: Pin assignment
Fig. 19 – Pro-CPU-T9: Board and front panel
To be used for Pro system Pro I
Processor ADSP 21062
Clock rate 40MHz
Data connection Link
Internal memory 256kB, optional 512kB
External memory 4MB, optional 16 oder 32MB
TTL-signal inputs Event In
Fig. 17 – Pro-CPU-T9: Specifikation
DATA
ADDRESS
ADwin-Pro bus
ext. Memory
SRAM
3 MB
DRAM
4/16/32/64 MB
EVENT IN
Link 0
Data
Address
SHARC
™
ADSP 21062
from Analog Devices with
2 MBit internal SRAM
/RESET
LINK OUT (-)
/ERROE
LINK IN (-)
GND
LINK OUT (+)
/ANALYSE
LINK IN (+)
nc
1
2
3
4
5
6
7
8
9
8921
721
721
721
LS09
ON
12
19DSPIF01
DC-DC-converter
LS19
706
FPGA
FPGA
FPGA
ADSP-21062
IMSC011
OCX
CPU-T9
ADwin-Pro
0
LINK
EVENT IN

ADwin-Pro Hardware, manual version 2.9, June 2006 15
Processor modules
ADwin
5.2.2 Pro-CPU-T9-ENET / -USB
The processor module is available with data connection Ethernet or USB.
Fig. 20 – Pro-CPU-T9-ENET / -USB: Block diagram
Fig. 22 – Pro-CPU-T9-ENET: Board and front panel
To be used for Pro system Pro I
Processor ADSP 21062
Clock rate 40MHz
Data connection Ethernet or USB
Internal memory 256kB, optional 512kB
External memory 16MB, optional 64MB
TTL-signal inputs Event In
DigIn 0 (optional)
Fig. 21 – Pro-CPU-T9-ENET / -USB: Specifikation
Daten
Adressen
Daten
AdressenDSP-Link
ADwin-Pro-Bus
SHARC
™
ADSP 21062
von Analog Devices mit
2 MBit internem SRAM
ext. Speicher
SDRAM
16 / 64 MB
EVENT IN
LM3940IS
-3.3
ADM
706
74LS125A
OCX
24MHz
OCX
40MHz
ICSI
IS42S16400-7
ICSI
IS42S16400-7
ADSP-21062
FPGA
24LC01B
74LVT1624574LVT16245
LM2937ES
-2.5
Xilinx
SPARTAN
XC2S50
74AC08 74AC08 74AC08
ADM
706
ADM
706
19ADSP03
17S50
ON DIP
123456 78
19ARM12
CPU-T9
ETHERNET
STAT BUSY
ACT LNK
EVENT IN
ADwin-Pro

Processor modules ADwin
16 ADwin-Pro Hardware, manual version 2.9, June 2006
Fig. 23 – Pro-CPU-T9-USB: Board and front panel
LM3940IS
-3.3
ADM
706
74LS125A
OCX
24MHz
OCX
40MHz
AT17LV010
ICSI
IS42S16400-7
ICSI
IS42S16400-7
ICSI
IS42S16400-7
ICSI
IS42S16400-7
ADSP-21062
FPGA
Cypress
AN2135
USB-
Hub
24LC01B
74LVT1624574LVT16245
LM2937ES
-2.5
Xilinx
SPARTAN
XC2S50
74AC08 74AC08 74AC08
ADM
706
ADM
706
CPU-T9
USB
EVENT IN
ADwin-Pro
Other manuals for ADwin-Pro
1
This manual suits for next models
1
Table of contents
Other Jäger Control System manuals
Popular Control System manuals by other brands
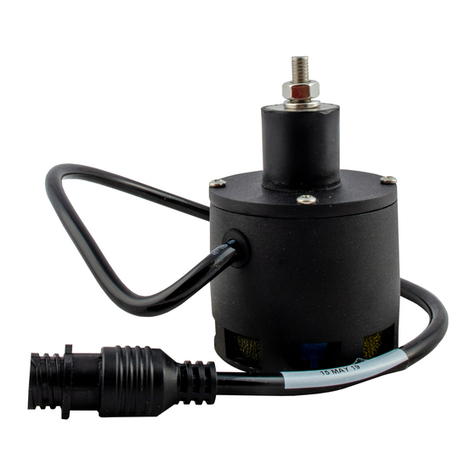
Norac
Norac UC4 Total Control installation manual
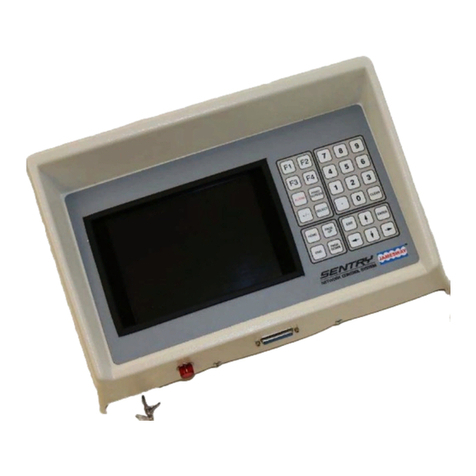
Jamesway
Jamesway Sentry Guide

ASA Electronics
ASA Electronics iN-Command JRVCS105 troubleshooting guide
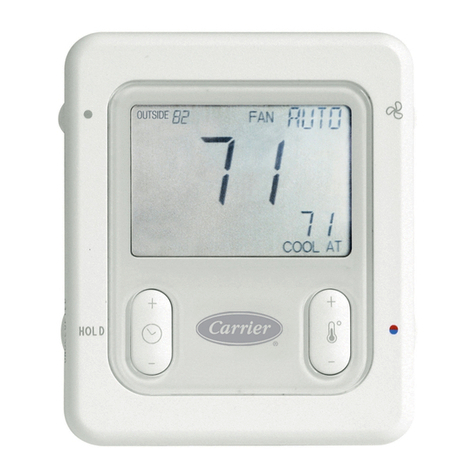
Carrier
Carrier SYSTXCCSMS01-A installation instructions

TLS Electronics
TLS Electronics 875760 manual
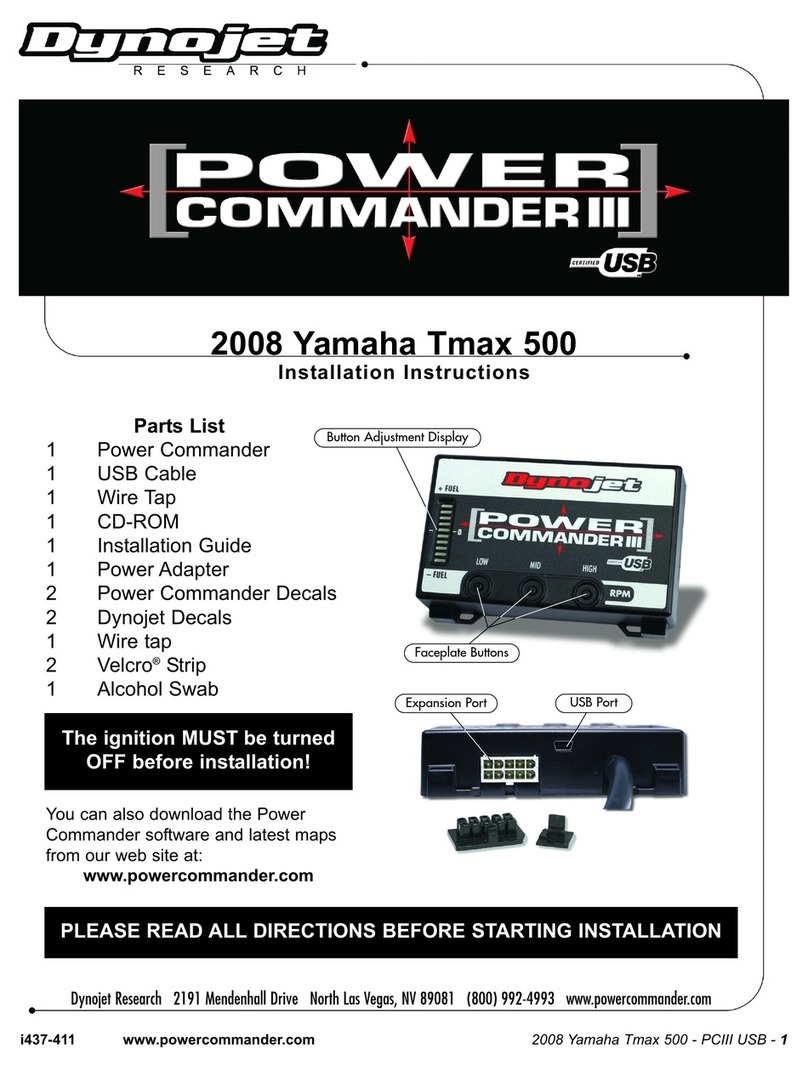
Dynojet
Dynojet POWER COMMANDER 3 Installation Instructions and Technical Information