Johnson Controls TVS User manual

Installation Instructions
Issue Date October 29, 2004
© 2004 Johnson Controls, Inc. 1
Parallel Flow Fan Powered Terminal (Model TVS)
In conjunction with the use of these instructions, obtain
and refer to the construction, fan performance, and
control wiring drawings submitted for the specific
project.
The equipment covered in this document is designed
for safe and reliable operation when installed and
operated within its design specification limits. Observe
the following cautionary statements.
!
DANGER: Electrical Shock Hazards. All
power must be disconnected prior to installation and
servicing this equipment. More than one source of
power may be present. Disconnect all power
sources to avoid electrocution or shock injuries.
!
DANGER: Moving Parts Hazards. Motor
and blower must be disconnected prior to opening
access panels. Motors can start automatically;
disconnect all power and control circuits prior to
servicing to avoid serious crushing or
dismemberment injuries.
!
DANGER: Hot Parts Hazard. Electric
resistance heating elements must be disconnected
prior to servicing. Electric heaters may start
automatically; disconnect all power and control
circuits prior to servicing to avoid burns.
!
WARNING: Check that the unit assembly
and component weights can be safely supported by
rigging and lifting equipment.
!
WARNING: All assemblies must be
adequately secured during lifting and rigging by
temporary supports and restraints until equipment is
permanently fastened and set in its final location.
!
WARNING: All unit temporary and
permanent supports must be capable of safely
supporting the equipment's weight and any
additional live or dead loads that may be
encountered. All supports must be designed to meet
applicable local codes and ordinances.
!
WARNING: All fastening devices must be
designed to mechanically lock the assembly in place
without the capability of loosening or breaking away
due to system operation and vibration.
!
CAUTION: Secure all dampers when
servicing damper, actuator or linkages. Dampers
may activate automatically; disconnect control
circuits or pneumatic control systems to avoid injury.
!
CAUTION: Protect adjacent flammable
materials when brazing. Use flame and heat
protection barriers where needed. Have fire
extinguisher available and ready for immediate use.
Code No. LIT-1201894 www.johnsoncontrols.com

Pre-startup
!
WARNING: Improper installation,
adjustment, alterations, service or maintenance can
cause injury and property damage, as well as
possible voiding of factory warranty.
Receiving and Inspecting
To receive and inspect the unit, perform the following
steps:
1. Thoroughly examine the exterior and interior of all
units for transportation damage to the cabinet,
blower(s), motor(s), coil, electric heat, and
electrical components. Interior damage may occur
without visible exterior damage. If damage is
found, immediately file a claim with the carrier.
Note the damage on the bill of lading before
signing for the shipment.
2. Check the bill of lading to verify receipt of the
indicated items (including loose items). Notify your
local representative of any shortages or items
shipped in error.
3. Store the units in a clean, dry location, stacking no
more than four high, unless using original packing.
Installation
!
CAUTION: Do not use flow sensor,
connecting tubes, coil stub-outs or damper shaft as
a handle when lifting or moving equipment. Damage
to the flow sensor or controls may occur. In addition,
do not handle equipment-heating elements as
permanent damage may occur.
Unit Placement and Installation
To place and install the unit, perform the following
steps:
1. Before installation, remove the fan packing (if
provided) and foreign material from the unit
interior. Check the blower wheel for free rotation.
2. Do not handle the unit using coil stub-outs,
controls, probe, or damper shaft, as damage may
occur.
3. Make sure the installation conforms to local
building codes and to the National Electrical Code
(NEC).
4. Locate the unit in accordance with the project
plans.
5. Avoid unit contact with rigid objects such as
conduit, sprinkler piping, and support rods.
IMPORTANT: Fan-powered unit location
should follow Sheet Metal and Air Conditioning
Contractors' National Association (SMACNA)
guidelines with respect to proximity to downstream
transitions, take-offs, elbows, and tees.
IMPORTANT: Fan-powered terminals should
never be installed over small, occupied spaces
where the wall partitions extend from slab-to-slab
(for example, fire walls or privacy walls).
6. Suspend the unit from the building structure in a
horizontal plane adhering to unit orientation labels.
Use the support method shown on the project
plans.
Note: Fan powered terminals are equipped with
sufficient internal vibration dampening means to
prevent the need for external vibration isolation.
When using sheet metal straps, up to 1” long
screws may be used to penetrate the main casing.
Do not secure hanging straps to unit equipment
such as (but not limited to) electric heater
cabinets, hot water coils, and control enclosures.
The unit may be equipped with optional hanging
brackets; rods up to 3/8” diameter may be used.
Four brackets are typically provided near the unit
corners. Hanger rod locations are approximately
1 1/2” to 3” from the corner of the unit for most
terminal configurations. Contact your local
representative if precise bracket locations are
required.
IMPORTANT: Do not obstruct the access
panels with support channels or straps.
2Parallel Flow Fan Powered Terminal (Model TVS) Installation Instructions

Clearance Requirements
Observe the following clearance requirements:
• The unit, including electric heat option, is ETL
listed for 0” clearance to combustibles.
Note: ETL is a mark issued by Intertek Testing
Services (ITS) ETL SEMKO Division.
• Ensure sufficient clearance to service the fan
assembly and access all electrical and control
enclosures, as indicated on the submittal drawing.
The bottom casing access panel requires sufficient
clearance to access fasteners and to lower and
slide panel horizontally until clear of bottom of unit.
Units equipped with an optional filter require
sufficient access to enable filter replacement.
• The unit should not make contact with the
structure above. Model TVS units equipped with
an induction sound baffle require a minimum of 5”
between the top of the unit and the structure.
• Line voltage and low voltage electrical enclosures
must have adequate service and working
clearances to meet requirements of National Fire
Protection Association (NFPA) 70 (NEC) or
approval by the authority having jurisdiction.
• Additional clearance requirements may be
required by local codes and are the responsibility
of the installing contractor.
Duct Connections
The connecting duct should be configured and
installed in accordance with SMACNA guidelines and
local code requirements.
Outlet
Observe the following outlet guidelines:
• Flexible connectors at the unit outlet are not
recommended. The sagging membrane of these
fittings can cause turbulence and higher air
velocities that generate noise. The lightweight
material allows noise to break out, which can
increase sound levels in the space below.
• Fasten and seal the downstream duct in
accordance with the project plans. Outlet
construction varies with the type of heat as shown
on the submittal drawing. Units with discharge-
mounted electric heaters accept a flanged duct
connection on all four sides. The end of the heater
control cabinet serves as a receiving flange. Sheet
metal screws no longer than 1/2” can be used. For
screw penetrations into the control enclosure, care
must be exercised to avoid damaging wire or
electrical components.
Inlet
Observe the following inlet guidelines:
• The inlet duct should be the same nominal size as
unit inlet. Straight duct yields the best airflow and
acoustical performance. Flexible duct should not
be used if critically sensitive acoustical
performance is required in the space directly
below the unit.
• Slide the duct over the inlet collar and fasten and
seal it in accordance with the project plans.
Electrical Connections
To connect power to the terminal, perform the
following steps:
1. Observe unit label electrical requirements before
connecting power to the terminal.
Note: Electrical wiring must comply with the
current revision of the NEC and local codes.
2. Make sure all disconnect switches are in the OFF
position while making electrical power
connections.
Note: More than one disconnect may be
provided; use tag-out/lock-out procedures. Unless
otherwise specified, the unit is suitable for a single
point electrical connection using copper
conductors only. Disconnect switches are optional
factory components. Refer to the wiring diagram(s)
located within the electrical enclosure(s) for
additional information.
IMPORTANT: The single-phase fan motor is
connected to L1 unless otherwise specified. For
three-phase systems, the electrical contractor should
alternate incoming service to help balance the
electrical load. Unless otherwise specified,
three-phase systems require a fourth (neutral)
conductor as shown on the wiring diagram.
3. Mount and wire field-installed electrical
components per factory supplied wiring diagram.
IMPORTANT: Factory wiring must not be
altered without written approval; violation of this will
void the warranty. Power source must be within 10%
of nameplate voltage for safe, reliable operation. If
incoming voltage is 10% above or below nameplate
voltage, contact the power company to correct
before operating the terminal.
Parallel Flow Fan Powered Terminal (Model TVS) Installation Instructions 3

Hydronic Connections (Optional)
Hot water or steam heating coils require a male sweat
connection. Refer to the unit construction submittal
drawing for specific connection size. Use the
appropriate brazing alloy for the connection; BCuP-6
or equivalent is acceptable. Do not use soft solder.
The system water operating pressure must not exceed
300 psig.
Operation
Startup
To start the terminal, perform the following steps:
1. Verify that internal fan packing (if provided) is
removed.
2. Verify that all electrical wire terminations are
secure prior to energizing the terminal.
Notes:
• The plenum inlet air filter (if provided) should be
installed prior to unit startup.
• The unit fan should not be energized without
sufficient downstream resistance as indicated on
the specific fan performance curve. This is
typically 0.1 or 0.2 inches wg static pressure. Units
with electric heat require a minimum of 0.1” wg
pressure unless the specific fan curve indicates a
higher value.
• For temporary heat, a field-fabricated perforated
baffle can be used to obtain the necessary
resistance. The manual electronic Speed
Controller Relay (SCR) should not be adjusted
downward unless the specified downstream duct
is installed and airflow capacity is verified to be
within the specified range for the unit size.
• Prior to startup, the project specific control
sequence/wiring diagram should be obtained and
understood. If factory supplied analog or Direct
Digital Controls (DDC) are used, refer to the
applicable startup and balancing instructions.
• The unit fan must not be balanced to a capacity
below that shown on the applicable fan
performance curve. Otherwise, the motor is not
lubricated properly, causing premature failure and
voiding of the warranty.
• Units with electric heat require the fan capacity to
have at least 70 Cubic Feet per Minute (CFM) per
kW.
Air Balance
Do not balance the unit until the incoming power
supply is at the permanent voltage condition. Unless
otherwise specified, the fan motor has three speeds.
Select fan speed by placing a jumper wire on a
terminal strip located within the electrical enclosure. A
three-position rotary switch is an optional component.
Adjust units with an electronic SCR fan speed
controller using a small (1/8”) flat blade screwdriver.
Running the Terminal
To run the terminal, perform the following steps:
1. Referring to the controller instructions, balance the
primary air valve to the specified maximum and
minimum airflow capacity with the unit fan
deenergized.
2. Calibrate the unit fan to be energized at the
specified primary airflow capacity or space
temperature setpoint.
3. Set the unit to the full heating condition; the
primary air valve should be at the minimum airflow
capacity and the unit fan should be on.
4. Measuring the airflow capacity downstream of the
unit, adjust the fan capacity until the total airflow
equals the sum of the minimum primary airflow
capacity and the unit fan capacity.
Notes:
• The unit fan is shipped for low-speed operation to
optimize energy efficiency.
• Fan capacity should be initially verified with the
electronic SCR controller potentiometer adjusted
fully clockwise. If additional capacity is required,
select medium or high speed on the fan motor by
moving the jumper wire located within the
electrical enclosure.
• Balance fan capacity by adjusting the electronic
SCR controller counterclockwise.
• Final fan balance should occur after the motor has
been running for 15 minutes.
• Record incoming voltage at the time of air
balance.
4Parallel Flow Fan Powered Terminal (Model TVS) Installation Instructions

Maintenance 3. Beginning at the bottom, remove the four nuts
from the mounting lugs securing the fan housing to
the unit casing (be prepared to support the fan
housing as the last nut is removed).
Observe the following maintenance guidelines:
• Fan Motor: No maintenance is required as the
motor is equipped with permanently lubricated
bearings. 4. Remove the fan assembly.
5. Loosen the set screw that secures the fan wheel
to the motor.
• Fan Wheel: Periodically inspect the fan wheel for
accumulation of dust; clean as necessary. 6. Remove the three nuts that secure the motor
brackets to the fan housing.
!
CAUTION: Verify that the capacitor is fully
discharged prior to performing the next step.
• Filter (Optional): Replace the filter(s) as dictated
by specific project conditions.
• Hot Water Coil (Optional): Inspect the hot water
coil periodically and clean fins if necessary.
Fan Motor Replacement 7. Disconnect the two capacitor leads.
!
CAUTION: Disconnect all electrical power
sources before servicing unit. More than one
disconnect may be supplied; use proper
tag-out/lock-out procedures.
8. Slide the motor shaft out of the fan wheel collar.
Notes:
• Make sure the fan wheel is centered within the
housing before tightening the set screw. To avoid
vibration problems, do not over-tighten the motor
bracket nuts.
Note: For Models TVS and TVS-E, access is
provided through the plenum inlet opening. For Model
TVS-W, access is provided through the bottom access
panel. • Reverse the fan motor replacement procedure
when installing a new motor.
To replace the fan motor, perform the following steps:
1. Remove the optional filter and/or induction sound
baffle (Models TVS and TVS-E only).
2. Disconnect the four electrical conductors from the
quick disconnect plug located at the base of the
motor.
• Electrical components are not serviceable. Faulty
components should be replaced with authorized
parts to avoid conflict with the ETL listing.
Controls Group
507 E. Michigan Street
P.O. Box 423 Published in U.S.A.
Milwaukee, WI 53201 www.johnsoncontrols.com
Parallel Flow Fan Powered Terminal (Model TVS) Installation Instructions 5
Table of contents
Other Johnson Controls Touch Terminal manuals
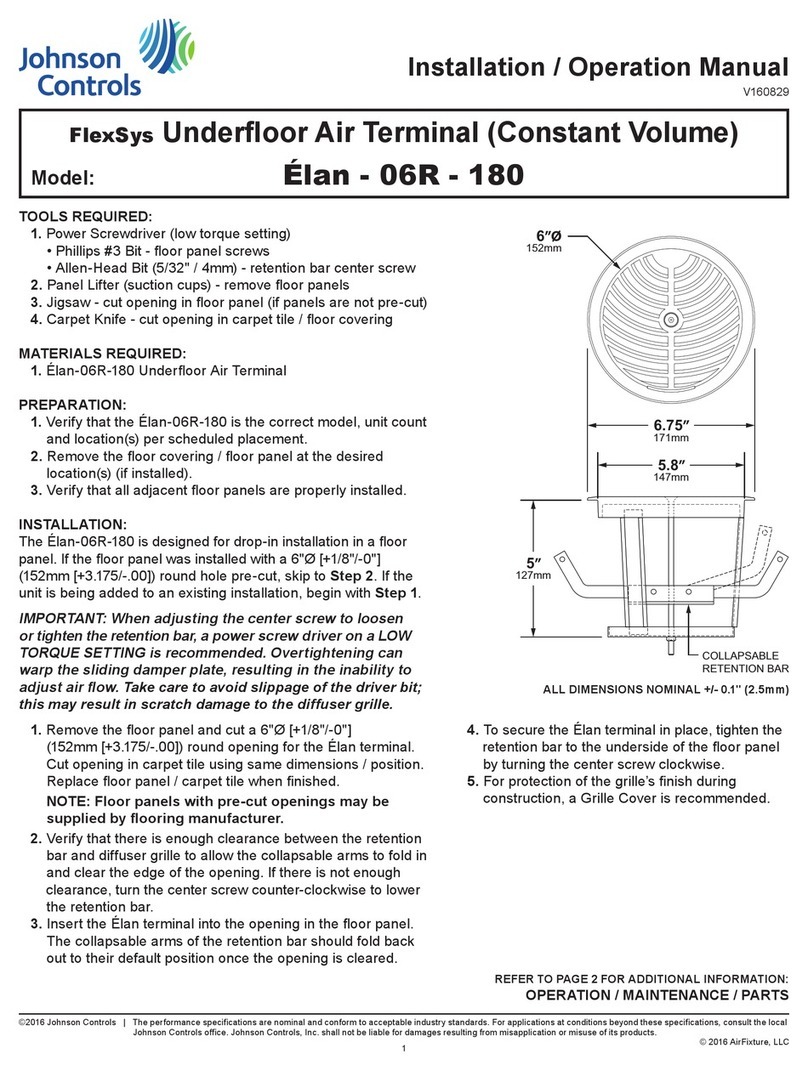
Johnson Controls
Johnson Controls FlexSys Elan-06R-180 User manual
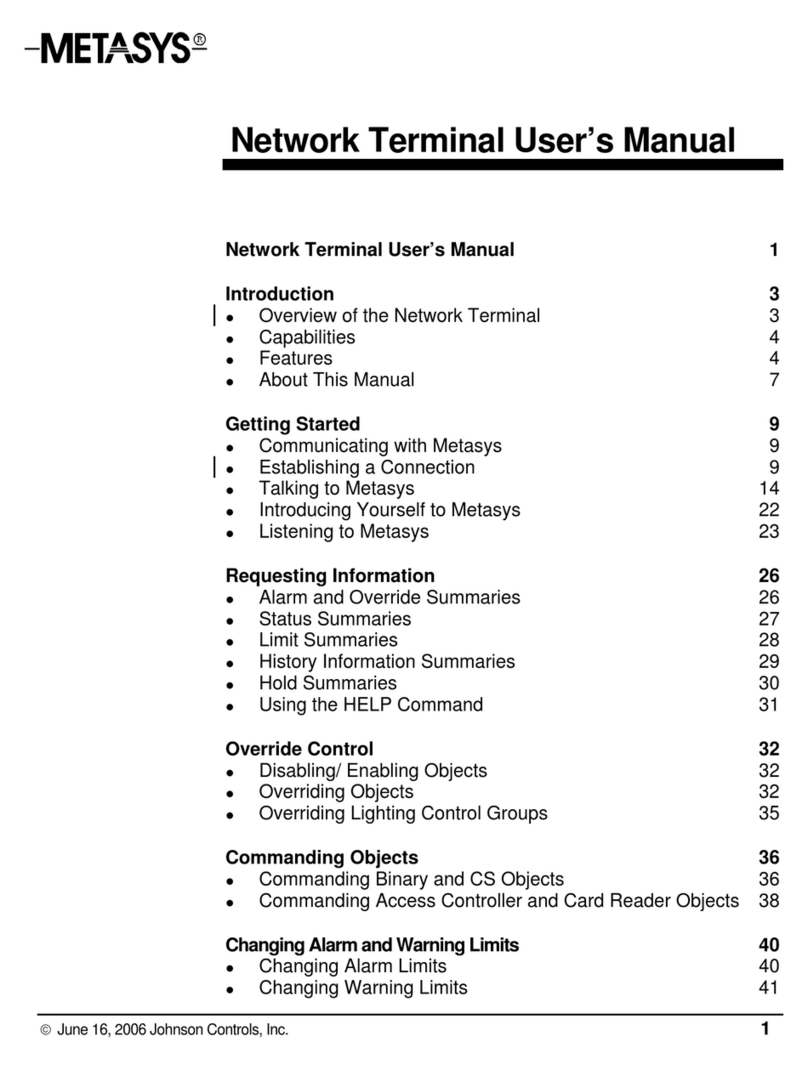
Johnson Controls
Johnson Controls METASYS User manual
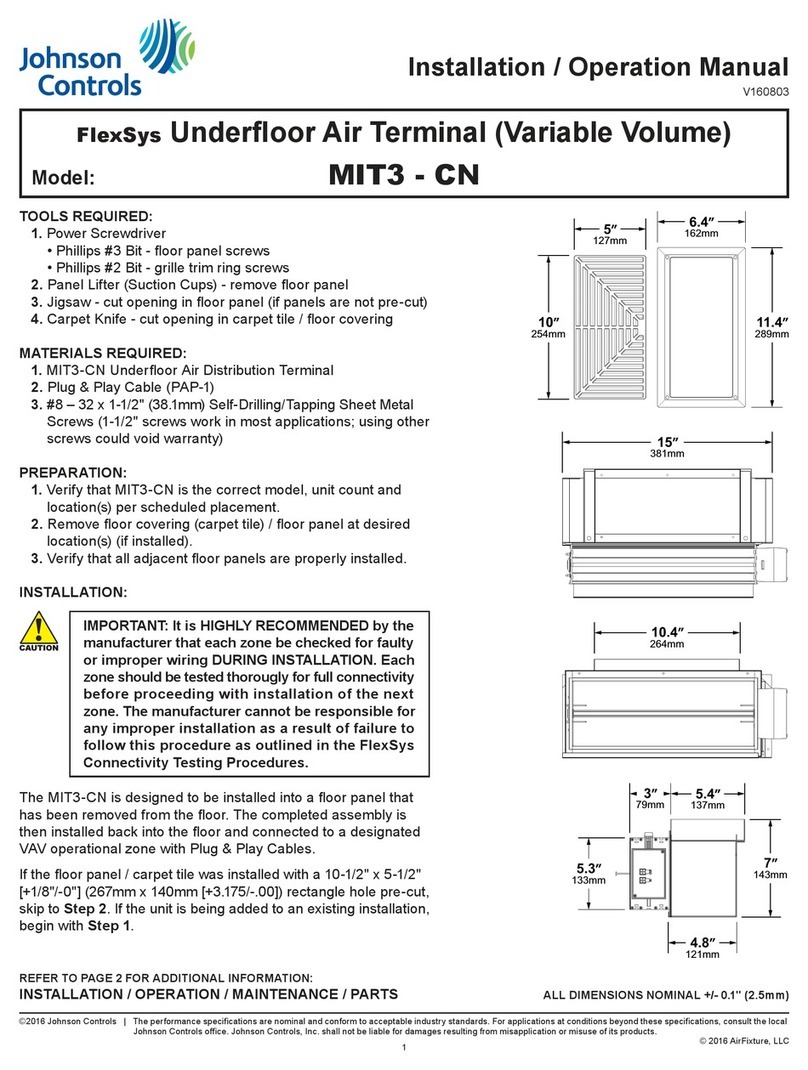
Johnson Controls
Johnson Controls FlexSys MIT3-CN User manual
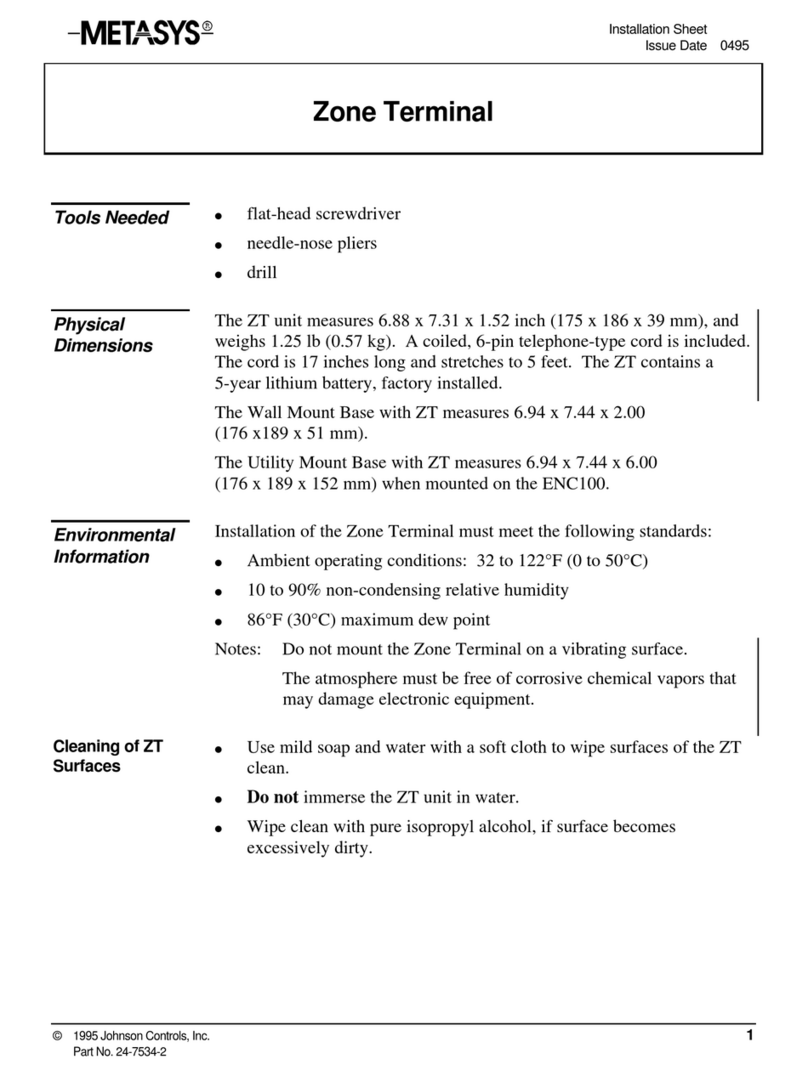
Johnson Controls
Johnson Controls METASYS Series Assembly instructions

Johnson Controls
Johnson Controls METASYS Zone Terminal Assembly instructions