KAMA KM376QC User manual

THREE-CYLINDER
WATER-COOLED
DIESEL
KM376 SERIES

PREFACE
Thank you for purchasing KAMA KM376 series three-cylinder water-cooled diesel
engine.
This manual describes safe information, operation instruction and maintenance of
KM376 series diesel engine. Be sure to read this manual carefully before
operation, for keeping your engine at the best working condition.
Keep this manual at hand for easy checking up. Contact with your agent if it
destroyed or missed.
This manual is considered a permanent part of the engine, and it must stay with
the engine if resold.
Any question or suggestion happened, contact with our After-service Dept.
Indicates a strong possibility of severe personal injury or
death if instructions are not followed.
Indicates personal injury of equipment damage will result if
instructions are not followed.
Indicates the severe personal injury will result if instructions
are not followed. To prevent you from injury, be sure to read
the safety marks and correctly operate engine.
DANGER
WARNING
CAUTION


Contents
1. Safety Information
1.1 Safety Mark
1.2 Safety Caution
2. Product Instructions
2.1 Main Specifications and Data
2.2 Specifications and Data of Key Parts
2.3 Main Adjusting Data Table
2.4 Tightening Torque of Main Bolts and Nuts
2.5 Operation Control Device
3. Preparation before Operation
3.1 Prepare the Fuel, Lubricating Oil and Cooling Water
3.2 Preparation before Starting
4. Operation Instruction
4.1 Starting
4.2 Running
4.3 Check Engine during the Running
4.4 Stop the Engine
5. Break-in Period and Trial Run
6. The Storage for a Long time
7. The Method of the Maintenance and Service
7.1 Daily Technical Maintenance
7.2 Periodically Check and Service
8. The Adjustment of the Technical Data
8.1 The Adjustment of Valve clearance
8.2 The Adjustment of the Injection Timing
8.3 The Adjustment of the Fuel Injector
8.4 The Adjustment of the Injection Pump
8.5 The Adjustment of the V Belt
Electric Wiring Diagram
(8) The grow plug
(9) The current sensor
(10) The warm-up timer
(11) The grow plug resistance
(12) The grow plug relay
(13) The water temperature sensor
(14) The battery
(1) The alternator
(2) The voltage regulator.
(3) The CHG indication lamp.
(4) The hot insulation indication lamp
(5) The Current meter (10A)
(6) The generator (15A)
(7) The starter motor
1
1
1
4
4
5
6
7
8
10
10
12
15
15
16
18
19
20
21
22
22
22
29
29
30
31
31
31

9. The Engine Fault and the Elimination Method
9.1 Starting hard or can't start
9.2 The Exhaust Gas is Excessive and Its Color is Abnormal
9.3 Fuel Consumption is Too Large
9.4 The Power is Not Enough
9.5 The Running is Not Stable
9.6 Stopping the Engine Suddenly
9.7 The Engine Can't Stop When the solenoid is Cut Off
9.8 The Engine Temperature is Over High
9.9 Engine Oil Pressure is Abnormal
9.10 Engine Oil Consumption is Over Large
9.11 There is Abnormal Sound When Running the Engine
9.12 The Engine Oil Level rises
10. Storage
10.1 Storage
11. Appendix
The Outline of the Tilt-type engine
Electric Wiring Diagram
The outline of the tilt-position engine
NOTE: According to actral requirement, the dimension and dimension can
be deduced further.
11. APPENDIX
To the oil pump MAX. height position
The center line of the crankcase.
The center line of the engine.
Supercharger
The center of the exhaust export
The center of the inlet
To oil pipe MAX height
32
32
33
34
34
35
35
35
36
36
38
38
39
40
40
41
41
42

1.1 Safety Marks
Be sure to read and follow the instructions on the manual and safety marks.
Operating the engine without proper training or instruction is not allowed.
CAUTION: Many accidents are resulted from false operating. For your safety,
please obey to the following instructions:
1. SAFETY INFORMATION
[]
OPERATING NOTICE
Covers important safe information. Be sure to pay special attention to and
follow it, otherwise the engine performance will decrease or the engine fault
and parts damage will result.
1.2 Safety Caution
Be sure to pay attention to the following safety cautions while running the engine:
DANGER
CAUTION: To avoid being scalded with vapor.
Do not open the radiator cap while the engine is running, otherwise the
vapor scald will result. Be sure to open the radiator cap with cloth covered it
after the engine temperature decreased, and tighten the radiator cap while
the engine is running.
DANGER
CAUTION: To provide well ventilation for the battery.
To keep the battery at well-ventilated place and far away from the fire,
otherwise hydrogen explosive will result.
10.1 Storage
10.1.1 The diesel and spare parts and tools leaved from the factory should be
wrapped in the water-proof plastic cover. The bottom bracket should be mounted
at the casing box bottom. And the casing box should closed and clenched firmly.
10.1.2 The casing box should be put the dry and ventilated room. Forbid putting it
the open air, and putting it with the chemical (such as pesticide and chemical
fertilizer).
10.1.3 The effective period of the oil seal is one year. Check the corrosion of the
diesel after one year. Store the engine after coating it with oil seal if necessary.
10. STORAGE

DANGER
CAUTION: To avoid fire resulted from improper operating.
Use the recommended grade diesel oil. Other fuels such as gasoline and
kerosene will cause engine rough running, fuel injection system fault even
the fire or explosive. Be sure to use the recommended fuel described in this
manual.
Refuel in a well-ventilated area with the engine stopped. Keep flames and
sparks away. If the fuel spilled, immediately clean up the overflowed fuel with
rag.
Keep the engine far away from gasoline, kerosene, match and other
explosive or flammable materials, otherwise will result fire.
WARNING
CAUTION: To avoid inhale the poisonous exhaust.
The exhaust contains poisonous content. Do not run the engine at poor
ventilated places, such as confined rooms, tunnels, tents and cabins. Be
sure run the engine at well-ventilated place.
WARNING
CAUTION: To avoid being caught into the moving parts.
When the engine is running, keep your hands, body and clothes away
from rotary parts such as cooling fan, V-type belt and starter axle.
CAUTION
CAUTION: To avoid touching the hot parts to prevent from scald.
Be careful not to be scaled with hot engine body when the engine just
stopped. Keep hands, body and clothes far away from muffler, exhaust pipe
and radiator etc parts.
Do not operate the engine after drinking alcoholic beverage.
9.12 The engine oil level rises
2. There is water leakage in the cylinder
head or engine body
2. Check and repair, or replace
The cause of the fault Elimination method
1. There is water leakage at the cylinder
head gasket
1. Repalce the cylinder head gasket

Safety information about inspection and maintenance:
DANGER
CAUTION: To avoid touching the battery electrolyte.
The electrolyte contains diluted sulphuric acid, which can cause blindness
and burn if eyes or skin contacted with it. If electrolyte splash into your eyes,
flush thoroughly with water immediately and call a physician.
WARNING
CAUTION: To avoid short circuit to prevent from fire.
Do not confuse the earth terminals while checking electric system;
otherwise the fire will result from short circuit.
WARNING
CAUTION: To avoid being caught into the rotary parts.
Be sure to carry out maintenance with the engine stopped.
Do not remove the cover of rotary parts.
CAUTION
Do not rebuild product without permission.
Do not release the control the high-speed limiting screw and oil level
limiting bolt, otherwise the engine life will be shortened. Any rebuilding or
disassembling of the engine will decrease safety even cause severe
accident. If necessary, contact your local KAMA agents for replacing the
genuine parts or technical support.
9.10 Engine oil consumption is over large
6. There is oil leakage in the air valve seal
6. Replace the air valve seal
The cause of the fault
1. The engine oil viscosity is too low, and
its brand isn't proper
2. The gap between piston and cylinder
is too large, and the oil hole in the piston
circle groove is clogged.
3. The piston ring is clogged circuit groove
or the installation position of the
4. There isoil leakage in the front seal and
rear seal of the crankcase
5. The engine oil temperature and
pressure is excessive
Elimination method
1. Replace the engine oil brand
2. Clean or replace the oil hole
3. Clean, repair or replace
4. Check and replace the relative parts
5. Decrease the temperature, check and
regulate the pressure-limited valve
9.11 There is abnormal sound when running the engine
9.The oil injector assembly is snapped 9. Clean or replace the nozzle assembly
The cause of the fault
1. The gap between piston and cylinder
is too large
2. The gap between piston pin and small-
end bush of connecting rod is too large
3. The gap between main bush and the
connecting rod bush is too large
4 The gap between the piston ring and
piston ring circuit groove is too large
5. The gap between pressure surface
and thrust piece is too large
6.The piston bumps into the air valve
7. The abrasion of the gears is serious,
and the gap between the gears is
excessively large. There is a clash bump
when reducing the speed suddenly
8. The timing of oil supply is too early
Elimination method
1. Replace the piston ring, piston, and
bore the cylinder if necessary.
2. Repalce the worn parts, keep the
specified gap
3. Replace main bush, connecting rod
bush, keep the radial gap specified
4. Replace the piston ring, and replace
the piston if necessary
5. Replace the thrust piece, and keep the
specified gap
6. Check the clearance height
7. Judge whether replace the gear or not
according to the abrasion degree
8. Check and regulate the timing of oil supply

2. PRODUCT INSTRUCTION
2.1 Main Specifications and Data
Type
Combustion chamber type
Bore cycle(mm)
Cylinder no.
Piston displacement (L)
Fire order (from the free end)
Compression ratio
Rated power (kW)
Rated speed(r/min) (15 minutes power)
Max torque/speed (N.m/r/min)
Max steady speed at zero-load(r/min)
Idle speed(r/min)
Exhaust smoke FSU
Rotation direction (in the face of flywheel)
Starting system
Lubricating system
Overall dimension (L W H) mm
Net weight (kg)
Min fuel consumption at max throttle (g/kW.h)
Lube oil/fuel consumption ratio at full speed and full load
Item
Model KM376AG
KM376QC KM376G
Tilt, 4-stroke,
water-cooled
In-line,
4-stroke,
water-cooled
In-line,4-stroke,
water-cooled
21.5
Swirl type
76 73
3
0.993
1-2-3
300
25
5000
54/ 3200
312
18.7/20.6
3000/3600
56/ 3000
300
19.5/23
3000/3600
62.5/ 3000
110
5800 150
900 50
0.8%
4.4
Counterclockwise
12V DC electric start
Pressure and splash
594 451 623
110 110
76 77
1.048
9.9 Engine oil pressure is abnormal
(3) Eliminate the dirt that restricts the eng-
ine oil, and clean the oil passage of the
cylinder head.
The cause of the fault
1. The engine oil lack of pressure or the pressure is too low
(1) The engine oil in the oil sump is not
enough
(2) The engine oil becomes thin
(3) The oil pipe is broken, pipe connector
is loosened, and there is oil leakage in the
oil pipe
(4) The gap of the engine oil pump is too large
(5) The plunger of pressure-limited valve
isn't quick and the spring is broken or
distorted
(6) The drive pin of engine oil pump is broken
(7) The fit clearance between the main
bearing and connecting rod is too large
(8) The plug of the oil pipe is loosened
(9) The engine oil air filter is clogged by
the dirt.
(10)The engine oil filter is too dirty
(11)
(12) The engine oil manomenter is broken
2. The engine oil pressure is over high
(1) The adjustment of the pressure-limited
valve is not right, and the engine oil can't
return
(2) The air temperature is over low, and
the oil viscosity is too large
(3) The lubrication at the camshaft neck is
not good
Elimination method
(1) Refill the engine oil up to the specified
level
(2) Choose the specified fuel type
(3) Replace or tighten it
(4) Replace it
(5) Replace it
(6) Replace it
(7) Check, adjust or replace
(8) Check the plug
(9) Check and clean air filter
(10) Clean or replace the element
(11) Check and replace
(12) Replace
(1) Check and adjust
(2) Use the specified fuel type, its
viscosity will fall automatically
after warming up

2.2 Specifications and Data of Key Parts
Cooling water
pump
Specifications and Data
VE distributor pump
VE3/9F2500LND
9mm
Mechanical full length
S series; (P series) thread coupling
Dual function throttling pintle nozzle
13.5~14.5Mpa
2500r/min
249Kpa
Above 20L/min
Centrifugal
5000r/min
55L/min
Screw-in type
Type
Model
Plunger diameter
Governor
Model
Nozzle type
Fuel delivery pressure
Working speed
Working pressure
Flow volume
Type
Speed
Flow volume
Item
Fuel injection
pump
Fuel injector
Lube oil pump
Lube oil filter
Specifications and Data
Silicon rectifying, parallel excitation
14V
40A (45A in cold area)
DC motor
12V
1.4kW
11V
7-8 seconds
Above 750
Paraffin type
Item
Type
Voltage
Rated current
Type
Voltage
Power
Working voltage
Working seconds
Working temperature
Paper element (with fuel/water
separator and portable pump)
Glow plug
Generator
Starter motor
Diesel oil filter
Thermoregulator
9.8 The engine temperature is over high
(7)The engine oil temperature meter doen't work
The cause of the fault
1. The water temperature of exhausted is over high
(1) The water in the reservoir is not
enough
(2) The dirt clings to the surface of the
radiator pieces and copper pipes
(3) The scale deposit in the cooling sys-
tem is too thick to cool the system down
(4) There is water leakage in the pump or
the shaft of pump is broken, the impeller
can't rotate
(5) The fan belt is broken or too loosened
(7) Replace it
(6) The cooling water line pipe or engine
cooler is clogged
(7) The thermoregulator is damaged
(8) The diesel runs under over load
2. The engine oil temperature is over high
(1)The engine oil is insufficient or
excessive
(2) The engine cooler is clogged by dirt
(3) The quality of the engine oil is bad
(4) The amount of air flee is excessive in
crankcase
(5) The cooling water temperature is over
high
(6) The diesel runs under over load
Elimination method
(1) Add water, and eliminate the air
(2) Clean the dirt with the compressed air
(3) Clean the scale deposit.
(4) Disassemble, check and repair
(5) Replace the belt or adjust the belt
tension
(6) Clean the water line
(7) Replace it
(8) Reduce the load
(1) Add the engine oil as specified
(2) Clean it
(3) Replace the engine oil as specified
(4) Check the air flee for the piston ring
(5)Reduce the temperature as described
above
(6) Reduce the load

2.3 Main Adjusting Data Table
Exhaust temperature
Non-compression space
height inside the cylinder
Fuel delivery timing
Fuel spraying pressure
(two bundle)
750
Normal adjusting data value
0.7-1.0mm
When the piston is at the upper dead
point, the stroke of fuel pump plunger is:
0.97 0.03mm or 0.89 0.03mm
13.5-14Mpa(green) and
14.1-14.5Mpa(pink)
Open at BTDC16 10 ;
close at ABDC 40 10
Open at BBDC52 10 ;
close at ATDC 14 10
Intake 0.25 0.05mm;
exhaust 0.3 0.05mm
1.2-1.6mm
0.7-1mm
Press the belt down 6-7mm with
10kg pressure
(New belt: press down 5-6mm)
0.4-0.6Mpa, idle speed 0.15Mpa
60 ~110
95
Valve close
and open
phase
Intake valve
Exhaust valve
Valve clearance
(cold state)
Valve (intake&exhaust)
joint ring width
Valve sunk volume
Belt tension
Lube oil pressure
Lube oil temperature
Drained water temperature
Specification
Item
Limit value
9.5 The running is not stable
5.One of the nozzles is bad 5.Check and replace the bad nozzle
1.There is some air in the fuel
system
1. Check the air leakage and remedy the
fault then eliminate the air in the fuel
system
2.The speed-regulating slide cushion lost
its flexility
3.The speed-regulating level is worn or
not flexible
4.The fuel distributed to each cylinder is
not even
2. Send the oil pump to the service station
3. Send the oil pump to the service station
4. Send the oil pump to the service station
9.6 Stopping the engine suddenly
b) The oil pressure is too low and the lube
oil is not enough to cause the crankshaft
sticking to cylinder.
b) Send it to the service station and
check the lubricating system.
The cause of the fault
1.The fuel in the tank is used out
2.There is some air in the fuel line
3.The fuel filter is clogged
4. The plunger and inner oil ring is snapped
5. The plunger spring is broken
6. The solenoid plug of fuel pump is not
electrified
7. The denticulate belt is broken
8. The crankcase can't crank
a) The piston sticks to the cylinder
Elimination method
1. Add fuel to the fuel tank
2. Exliminate the air in the fuel line
3. Clean or replace the element
4. Send the oil pump to the service station
5. Send the oil pump to the service station
6. Check the circuit
7. Replace and test
8. Replace and test
a) Send it to the service station
9.7 The engine can't stop when the solenoid is cut off
3. The switch of the solenoid doesn't work 3. Replace or repair
The cause of the fault
1. There is some fault about the solenoid
2. The seal surface of the solenoid loses
its seal function
Elimination method
1. Replace the solenoid and clean the
element
2. Send the oil pump to the service station

2.4 Tightening Torque of Main Bolts and Nuts
Bolt qty.
Thread
specification
Tightening
torque (Nm)
Cylinder head bolt
Camshaft bearing bolt
Main bearing bolt*)
Oil sump bolt
Connecting rod bolt
Flywheel bolt
Thread of fuel injector body
Glow plug thread
Other bolts and nuts
M12 1.25
M8
M10 1.25
M6
M9 1.0
M10 1.25
M20 1.25
M10 1.25
M6
M8
M10 1.25
M12 1.25
90+10
16 1
60 5
5.5 1.5
47 5
55 5
60 10
12 2
7.5 1.5
18.5 3.5
37.5 7.5
60 10
8
8
8
20
6
6
3
3
Note: *Turbocharger-type: main bearing bolt M12 1.25;
tightening torque 85 5N.m.
9.3 Fuel consumption is too large
(5) injector or nozzle assembly doesn't
work normally
(5) Clean, regulate
The cause of the fault Elimination method
(1) Fuel leakage
(2) idle speed is too high
(3) the max rotation speed is too high
at the no load
(4) injection timing is abnormal
(2) regulate idle speed
(3) check the max speed set bolt of the
injector pump
(4) regulate the injecting timing
9.4 The power is not enough
The bolt of the cylinder is loosened
The cause of the fault
(1)The air cleaner is too dirty and the
fuel is restricted
(2) The throttle doesn't work normally
(3) Fuel pipe is clogged,
(4) There is leakage or there is some air
in the fuel system
(5) The speed-regulation spring is slack
(6)The timing of the supplying fuel is not
correct.
(7) There are some faults in the injector
(8)The air cleaner is too dirty
(9) Mix air phase or valve clearance isn't
correct
(10) The compression pressure of the cylinder is not enough
There is air leakage at the valve
There is air leakage at the cylinder
cushion
The cylinder, piston ring or piston is
worn out
There is air leakage when install the
injector
Tighten the bolt again as required
Elimination method
(1) Clean and replace
(2) Regulate the throttle
(3) Check and clean
(4) Tighten it again, eliminate the air in
the system
(5) Regulate the max speed limited screw
(6) Regulate it as specified
(7) Check the pressure of oil injection
and atomization condition
(8) Clean and replace the element
(9) Check and regulate it
Abrade the surface or replace the
valve and valve base ring
Replace the cylinder cushion
Replace the relative parts and abrade
the cylinder surface
Replace the seal gasket or adiabatic
line of the nozzle
(1) replace or tighten securely

2.5 Operation Control Device
The operation control device connected to warm-up unit, electric starter and fuel
pump solenoid valve respectively.
The electric wiring of the control device is as below figure 2-1.
The electric wiring of the starting motor is as below figure2-2.
Recommended voltage is DC 12V.
Recommended current is less than 90A.
The electric wiring of the glow plug is as below figure 2-3.
The resistance of the glow plug is 0.4~0.6Ohm.
The function and operation of the electric starting switch is as below.
The operation procedure
Of the switch is:
OFF ON START ON
Rotary 3-position switch
The key can be pulled out when the switch is on
OFF position. Meanwhile, the current is cut off at
this position.
When the switch is on ON position:
(1) the warm-up indicating lamp of glow plug will
keep light for 7~8 seconds, and then goes out
automatically.
(2) The solenoid of fuel injection pump is acted.
When the switch is on START position, release
the key and let it automatically return back to ON
position. The solenoid of fuel injection pump is
acted, however the glow plug is still unconnected.
9.2 The exhaust gas is excessive and its color is abnormal.
The cause of the fault
1. The smoke exhausted is too thick
(1) the injecting timing is improper
(2) the fuel filter is restricted
(3) the assembly in injector nozzle
doesn't work normally.
2.the exhaust gas is black smoke
(1) Fuel injector is clogged by the carbon cumu-
lated and the needle valve is blocked up
(2) The load is too large
(3) Fuel injection is too late, part of fuel
is burnt in the exhausting course
(4) The clearance is not accurate and
it's seal is not effective.
(5) The distribution of the fuel to each
cylinder isn't even
(6) The inlet pipe and air cleaner is
clogged, so the air is restricted
3. the exhaust gas is white smoke
(1) Injection pressure is too low, atomi-
zation isn't good, and there is oil leakage
(2) The temperature of the cooling water
is too low
(3) The cylinder is penetrated by water
4. The exhaust gas is blue smoke
(1) The piston ring is worn excessively or
engine oil enters into the combustion
chamber in cause of the spring of the
carbon clogged is not enough.
(2) The engine oil level is too high
(3) The installation of the air ring is
converse in up and down direction
(4) Valve seal is damaged
Elimination method
(1) Adjust the injecting timing
(2) Replace the fuel filter
(3) clean, repair
(1) Check, repair or replace
(2) Reduce the load to the specified range
a) Replace the cable or tight connection
(1) Check, regulate, repair or replace
the nozzle assembly
(2) Increase the temperature of
cooling water
(3) Check the cylinder head shim
(1) Clean or replace the piston ring
(2) Drain out the excessive engine oil
(4) Replace the valve seal
(3) Make the surface marked
with "T" toward up
(6) Remove the air cleaner and clean it
(4) Check the valve clearance and seal
surface of valve
(5) Regulate the fuel distribution of each
cylinder

1. The solenoid of fuel injection pump
2. Warm-up indicating lamp
3. Voltmeter (10A)
Figure 2-1 The electric wiring diagram of control device
Figure 2-2 Electric wiring diagram of starter motor
1. Housing ground
2.Terminal 50
3. Terminal 30
Figure2-3 Electric wiring of glow plug
1.To the solenoid of fuel injection pump
2.To warm-up indicating lamp
3. To voltmeter (10A)
7. Glow plug relay
8. Warm-up timer
9. Battery
4. Starter motor
5. Glow plug
6. Glow plug resistance
9. THE ENGINE FAULT AND THE ELIMINATION METHOD
(4) Replace the fuel injector assembly.
The cause of the fault Elimination method
1. Starting speed is low.
(1) Battery electric amount isn't enough
or the connection is loosened.
(2)The contact of between the carbon
brush and rectifier is poor.
(3)The gear of the starter engine can't
be embedded into flying wheel circle
(4) The electric battle cable is too long,
too thick; voltage decrease is too large.
2.the fuel system doesn't work normally.
A. There is no fuel injected.
(1) The fuel in the tank is used up.
(2) There is fault in the solenoid Injection pump
a) The cable is cut and the connection is loosened
b) The winding of the solenoid is damaged
c) The solenoid element is snapped
d) There is fault in the starter switch
(3)There is some air in the injector pump
(4) Fuel filter element is clogged
(5) The plunger of the injection pump is
broken or snapped
(6) The transmission bolt in the plane
cam of the injector pump is broken
(7) The inner oil ring of the injector
pump is snapped
B the warm-up system doesn't work normally
(1) The grow plug relay doesn't work normally
(2) Warm-up timer doesn't work normally
C Water temperature sensor doesn't work normally
D Injector doesn't inject fuel or atomization quality is too bad
(1) Nozzle is snapped
(2) The atomization quality of nozzle is too bad
(3) Pressure-regulating spring is broken
(4)There is oil leakage at the
high-pressure oil seal
(1) Charge the battery; tighten the connec-
tion and repair the terminal if necessary.
(2) Repair or replace the carbon brush
(3) Revolve the flying wheel until the small re-
gulating gear levels with the denticulate circuit
(4) Replace the electrical battle cable
(1) refuel the fuel and drain out the air
a) Replace the cable or tight connection
b) Replace solenoid
c) Replace solenoid
d) Check or replace
(3) Drain out the air, tighten the connection of the oil pipe
(4) Clean or replace fuel filter element
(5) Replace the parts of the injector
pump distributor.
(6) Replace the transmission bolt in the
plane cam of the injector pump
(7) Replace the parts of the injector
pump distributor.
(1) check and repair, or replace
(2) check and repair, or replace
C check and repair, or replace
(1) Replace the nozzle assembly
(2) Replace the nozzle assembly
(3) Replace pressure-regulating spring

3. PREPARATION BEFORE OPERATION
3.1 Prepare the Fuel, Lubricating Oil and Cooling Water
3.1.1 Fuel
(1) To keep the engine in best working condition, be sure to use the recommend-
ed fuel: light diesel oil JIS K2204 (GB252-87)
However, be sure to choose the appropriate brand for the light diesel oil
according to actual ambient temperature.
Light diesel oil brand:
Temperature:
(2) Fuel usage
The fuel with water or dust contaminated will cause the rough running of the
engine. Be sure to use the clean container for storing the fuel, meanwhile, the
container must be stored at a clean and dry place. Then suck out the upper level
clean fuel with a pump as below figure.
[]
OPERATION NOTE
The improper fuel cannot make the engine
achieve the best performance, and even
cause the fault of the part.
Only use the upper level clean fuel. Do not
use the lower deposited fuel.
3.1.2 Lubricating oil
(1) Do use L-ECD grade oil; the quality index is 15W/30 or 15W/40.
(2) The usage of lubricating oil:
A. Carefully store and use the lubricating oil. Avoid any dust and impurity in the oil.
B. Do not mix two different type lubricating oil, otherwise the lubrication
performance will be decreased.
8.3 The adjustment of the fuel injector
The test and regulation of the injector should be done on the fuel injector test bed.
Its purpose is regulating the oil pressure and watching the atomization quality and
eliminating the fault.
1. Pump the oil by using the hand pump unit the injection pressure is 14 0.5Mpa,
check the Injection condition and atomization quality whether accords with
injection requirement. If there is oil leakage or dropping in the injector, you should
remove the fuel injecting assembly to clean or repair it until make injection up to
requirement.
2. The adjustment of injection pump.
Pump the oil by using the hand pump. When the reading of the fuel injection
starting pressure can't reach 13Mpa, you can remove the injection assembly by
increasing the thickness of the adjustment shims to improve the injection pressure
until the pressure reading is up to standard. If the reading is over 13Mpa, you
should reduce the thickness of the adjustment shims.
8.4 The adjustment of the injection pump
Injection pump has been tested and adjusted before leaving from the factory. If
you need to readjust it, you should perform the adjustment on the test bed
according to relative regulations.
8.5 The adjustment of the V belt
As shown in the figure, make the tension check in the arrowhead direction. As to
new products, put a 100N force on the it and loosen the belt until looseness
degree reaches 4 5 mm. Under the normal condition, put on a 100N force until
the looseness degree is 6 7mm. If you put on a 100N force but the looseness is
no less than 9mm, replace the V belt.
Generator Water
pump
Crankshaft

[]
OPERATION NOTE
Using the improper type lubricating oil will burn out the inner part of the
engine, even cause the engine to wear rapidly. And the service life of the
engine will be also shortened.
3.1.3 Cooling water
Be sure to adopt tap water as cooling water.
[]
OPERATION NOTE
Be sure to add anti-rusting or anti-freeze solution to the cooling water.
Add anti-freezing solution to the cooling water in winter, otherwise, the
frozen water may damage the cooling water system.
A. Anti-rusting solution:
Be sure to use the superior quality anti-rusting solution. But do not use it in winter
because it may freeze when the air temperature is low. Its standard mixing ratio is
6%.
B. Anti-freezing solution:
Be sure to use the superior quality anti-freezing solution. However, it's not
necessary to use it with anti-rusting solution simultaneously. This kind of solution
can be added to cooling water in all seasons. Its mixing ratio is 30%~55%.
[]
OPERATION NOTE
If the mixing ratio of anti-freezing solution is too low, cooling water will
freeze in low temperature, which causes damage or rust to the water pipe.
If the mixing ratio of it is too high, the engine performance will be
decreased.
45
The lowest temp
Mixing ratio %
-15 -20 -24 -29
30 35 40
Use the commercial available anti-freezing solution with the mixing ratio
recommended by manufacturer, meanwhile, it must be replaced every year.
8.2 The adjustment of the injection timing
In order to obtain the most economical fuel consumption ratio and better running
performance, the injecting ahead angle should be set properly. The adjustment
method of KM376QC/ KM376ZQC ahead angle should be as followed:
(1) Crank the crankshaft to make crankshaft lies on the 30 spot NO.1 cylinder (In
other word, it's the injection pump bolt fan mark)
(2) Loosen the mounting nuts in the fuel injection pump and the bolts in the
supporting plate of the fuel injector rear end until the fuel injection pump can
revolve. Then keep the fuel injection pump toward the inner surface to the bottom.
(3) Install the lever-type micrometer calipers in the front end of the fuel injection
pump, and let the pointer needle point at naught.
(4) Crank the crankcase to make NO.1 cylinder of the engine stay at upper dead
center of the compression stroke.
(5) Turn the injection pump toward outside surface slowly until the reading of the
meter is 0.97 0.03mm.
(6) Check the meter again. (Crank the crankcase to position 1, watch the reading
of meter whether reset to naught position. Then crank the crankcase until it
reaches the upper dead center, check the meter reading whether is 0.97
0.03mm. If the reading is right, the adjustment is completed. If the reading isn't
right, repeat the above adjusting steps.)
(7) Tighten loosened nuts and bolts above mentioned.

3.2 Preparation before starting
3.2.1 Add the lubricating oil
(1) The amount of the lubricating oil added should flush with height of the
lubricating oil level in the oil sump. Put the engine on a level surface at first, then
check the oil level.
(2) The lubricating oil level in the oil sump should between the lower and upper
marked line of the oil stick.
[]
OPERATION NOTE
The lubricating oil level in the oil sump should between the lower and
upper marked line of the oil stick. If the lubricating oil is not enough, it will
damage the engine easily. However, if excessive, the lubricating oil will spill
over from the air opening hole.
3.2.2 Refill the fuel tank
(1) Add the fuel to the fuel tank.
Add the fuel without containing dirt and water. To prevent the fuel from overfilling
during the running course, the amount of the refilled fuel should be 90% of the fuel
tank capacity.
DANGER
Make certain whether the type of the fuel refilled is right or not. If improper
fuel is added, it will cause the fire. If the fuel is overfilled, wipe it up at once.
(2) Eliminate the air in the fuel system
When refill the fuel at first time or refuel the tank normally as required, you should
eliminate the air in the fuel line which begins from the fuel tank, though water-oil
separator or fuel filter or primary oil delivery pump, to the fuel injection pump.
If the air mixes with the fuel in the fuel line, the fuel injection pump won't provide
the high-pressure fuel for the fuel injector, and the engine can't start also.
This product adopts the VE distributor pump, and the lubricating and cooling of the
VE distributor pump relies on the fuel. So if the fuel is cut off, it will result in
damage of VE distributor pump.
8. THE ADJUSTMENT OF THE TECHNICAL DATA
KM376 series engines are different from the general-use diesels in the structure.
In order to ensure maintenance quality, please read this additional section
carefully.
8.1 The adjustment of valve clearance
The valve clearance refers to the cam surface the clearance of inlet valve should
be 0.25 mm in cold condition, and that of the exhaust valve should be 0.30 mm. In
hot condition, the clearance of inlet valve should be 0.30 mm, and that of the
exhaust valve should be 0.35mm. If the clearance is improper, make it reach to
the standard by adjusting the shim thickness.
8.1.1 The measurement of the clearance
Measure the clearance using the ruler as shown in the figure 8-1
(1) Measure the clearance in cold condition.
(2) The rabbet in the cam should be toward up.
8.1.2 The selection of the adjusting shim clearance
T = T +(A'-A)
21
T the thickness of the shim replaced
2:
T the thickness of the shim measured
1:
A': the metrical value A: the standard value
8.1.3 The replacement of the adjusting shim
Press the valve tappet down using the special tools, and get out the shim used for
the measurement, then replace the shims that need to install to primary position.
Fig. 8-1 Check the valve clearance

The fuel line of the engine fuel system is as shown in figure 3.2.2 followed:
To eliminate the air in the low-pressure fuel line, loosen the connector of the intake
pipe in the VE dispensing pump at first, then expel the air from the fuel.
Inspect the connector of the VE pump return pipe. If there is a lot of fuel
overflowed and no air bubble occur, It indicates that there is no air in the low-
pressure fuel line.
primary oil delivery pump
diesel fuel filter
Oil return tube
solenoid valve
fuel injector
fuel tank
oil-water separator
VE distributor pump
3.2.3 Eliminate the air in the high-pressure fuel line.
The high-pressure fuel line begins from VE dispensing pump, through high-
pressure fuel pipe, to the fuel Injector.
Method of the treatment: loosen the connector where the high-pressure fuel pipe
connects with fuel injector, then start the starter motor and let it run at low speed
until the fuel overflows around the connector, finally tighten it. If there is still some
air in the high-pressure fuel-pipe, the engine won't start.
(7) Check the air cleaner
If the dust is drawn into the air cleaner and clings to air cleaner parts, it will affect
the output of the engine sooner or later. When the combustion chamber draws the
dust in, it will accelerate the worn of the moving parts and cause the engine not to
run normally. When you run the engine in the dusty place, the service interval
should be shortened as possible as you can, paper air cleaner element.
Loosen the wing nuts in center of air cleaner, remove the air cleaner cap, then get
out the paper element inside the air cleaner.
Blow and clean the inner surface of the parts using the compressured air (below
0.2 Mpa). Clean the dirt and dust clinging to the surface.
If the elements are dirty or broken always, replace them with new elements.
Reinstall the paper element after cleaning the dirt and dust clinging to the air
cleaner and chassis.
7.3 The technical maintenance after the engine works 1000 hours
Repeat those items as technical maintenance after working 500 hours , then
perform the following maintenance items:
1. Check the tightness degree of the bolt in the connecting rod and main bearing.
2. Check the seal of the inlet and exhaust valve. If necessary, machining the
surface of the valve seat over again.
3. Check the starter motor and generator. If necessary, add the lubricating oil, and
run the engine at idle speed after reinstalling it. Add grease to the bearing before
putting the engine to use.
4. Check each part of the diesel engine.
5. Reinstall the parts removed in the maintenance course to primary position,
eliminating the potential fault.

3.2.4 Add the cooling water.
(1) The water in the radiator water tank should be sufficient. Expel the air from the
water line when adding the water. At the same time, check the water tank and
connector of pipes for leakage, and remedy if in time.
(2) After adding water, tighten the radiator water tank cap. Otherwise it will cause
scald for the hot water.
(3) If there is some air in the water line, it will cause the restriction of cooling water,
even engine damage because of the excessive high temperature in the engine.
3.2.5 Check the all operation control systems, and the operation reliability of each
connection. Remedy the fault as soon as find it.
3.2.6 Check the connection of the bolt mounted to ground and the driven
machinery. If loosened, tighten it securely at once.
3.2.7 Before connecting the battery, make sure that the connection of the negative
lapping iron and the electrical diagram is right and electric capacity of the battery
is sufficient.
[]
OPERATION NOTICE
1) If you continue to use the battery when the electrolyte is not enough, you
will cause the damage of the battery. Periodically check the electrolyte
capacity. If the electrolyte level is below the standard specified, please refill
the electrolyte in time.
In hot summer, the electrolyte tends to be vaporized. So check it ahead of
the specified time.
2) If the engine can't start using the accelerating return, use the gravity
meter to measure the density. When charged fully, the density should be
above the 1.27 g/ml(20 hours).
If the density is below to 1.24 g/ml, it indicates that the battery needs to be
charged.
If the density doesn't increase after charging, please replace the battery.
(6) Check the battery electrolyte
When check the electric circuit, you must close the battery switch, disconnect the
ground terminal. If there is a shortcut in the circuit, it may result in fire.
Please recharge the battery in a good ventilated place. Keep all fire sources away,
because the hydrogen produced in the battery causes fire easily.
The electrolyte contains a mount of sulfuric acid. It could cause burnt injury even
blind, if the eyes and skin contact with it.
Please wear the glasses and rubber gloves when you handle the battery
electrolyte.
If you touch the electrolyte without precaution, use a large quantity of water to
wash it and see the physician as soon as you can.
Check the electrolyte level every month. If the level is lower than the lower limit
mark, refill the distilled water to the upper limit mark.
Upper limit mark
Lower limit mark

4. OPERATION INSTRUCTION
4.1 Starting
4.1.1 Start the engine under no load.
When starting the engine on the vehicle, let the vehicle to stop before.
4.1.2 Set the throttle lever at the half-open position when you start the engine.
4.1.3 Insert the key to the engine switch hole, then
turn it to the ON position clockwise. At this time, the
grow plug indicator lamp is on. After it last about 7
seconds, it goes out soon. The next step, turn the
key to the START position clockwise, let the starter
motor to start the engine. Finally, release the key,
and it will return to ON position automatically. This
is completing the engine start.
WARNING
Provide the engine with good ventilation condition for its running.
When running the engine, your hands, body, clothes shouldn't close to or
contact with such moving parts as radiator fan, belt, drive shaft and so on.
When check and service the engine near these parts, be sure that the
engine is stopped. Before running it, make sure that there isn't anything left
on these moving parts.
When the engine is running or stopped not for a long time, your hands,
body and clothes should not contact with the muffler, exhaust pipe and
radiator.
[]
OPERATING NOTICE
Don't use the start switch over 15 seconds each time. If you can't start the
engine, wait for 1 minute, then restart the engine. Otherwise, the long-time
running with electricity overheats the engine to cause fault.
Fig. 7-6
(5) Check the tightness of the bolt in the cylinder
Check the tightness of the bolt in the cylinder by using the torque wrench every
100 hours. Check the bolts in sequence as described in figure 7-6. The tightening
+10
torque should be 90 N.m.
(4) Check and adjust the valve clearance
Check the valve clearance every 100 running hours
method: check valve clearance by removing the cylinder head according to the
method described in figure 8-1 of section 8.1. If you want replace the adjusting
shim, use the professional tools for the engine. Then get out the shims according
to figure 7-5, and replace the shims you need to install.
Fig. 7-5
Max. height
Nice
Tappet
Front side
This manual suits for next models
2
Table of contents
Other KAMA Engine manuals
Popular Engine manuals by other brands
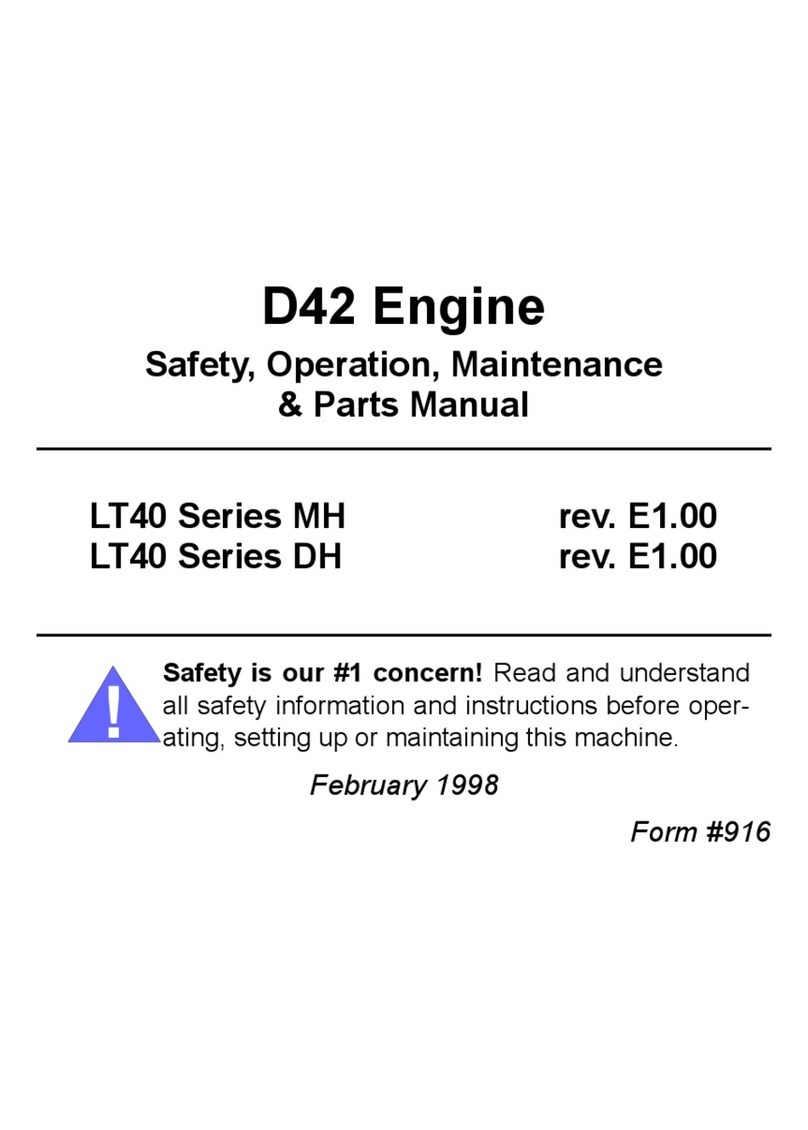
woodmizer
woodmizer D42 Safety, Operation, Maintenance & Parts Manual
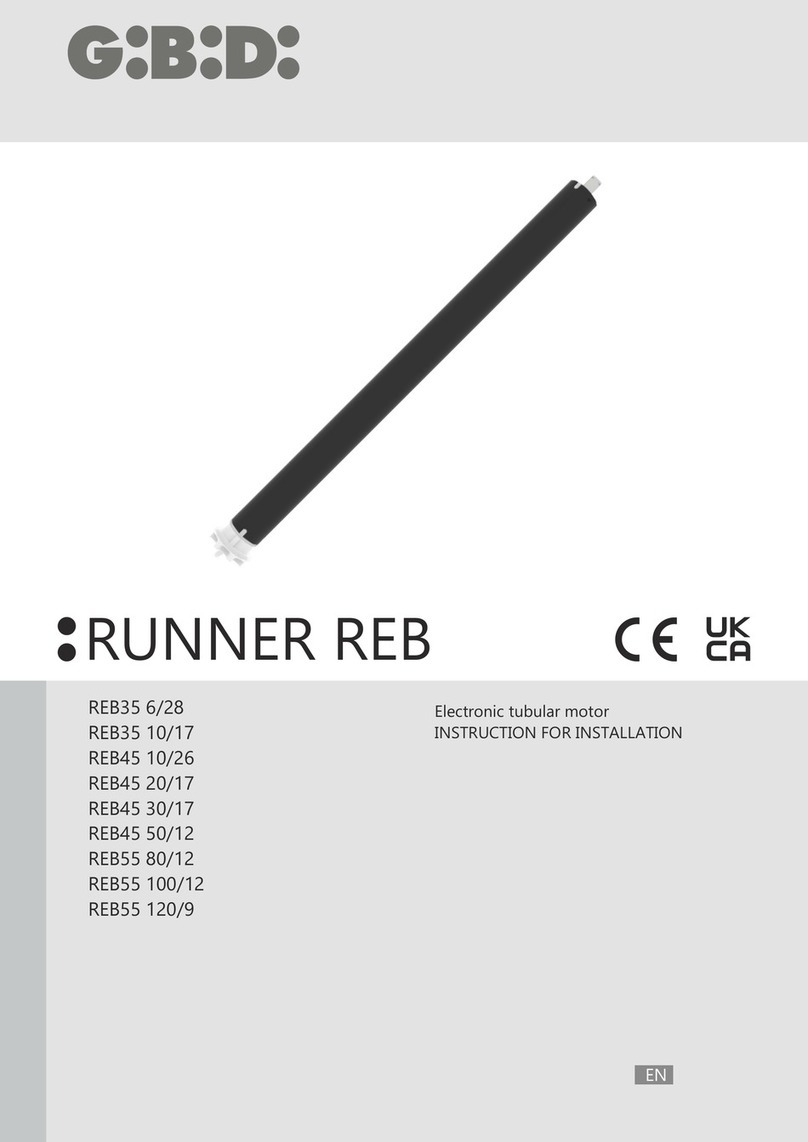
GiBiDi
GiBiDi RUNNER REB35 6/28 Instructions for installation
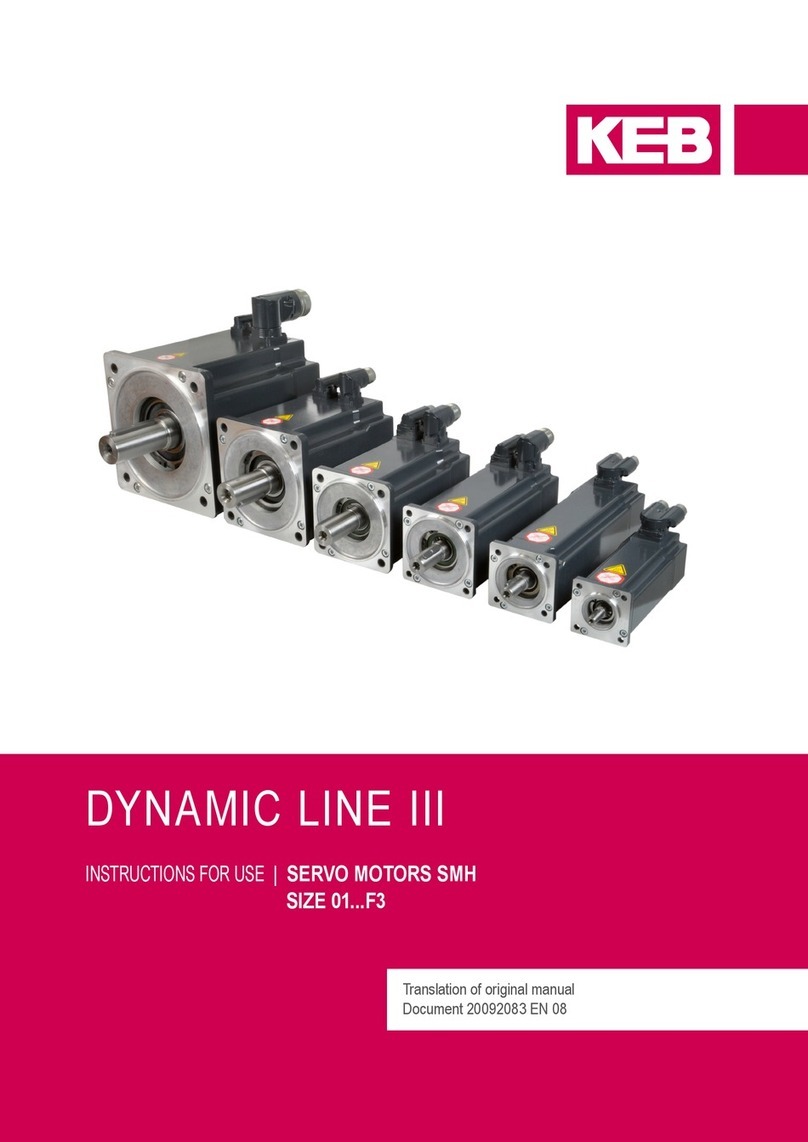
KEBCO
KEBCO DYNAMIC LINE III Instructions for use
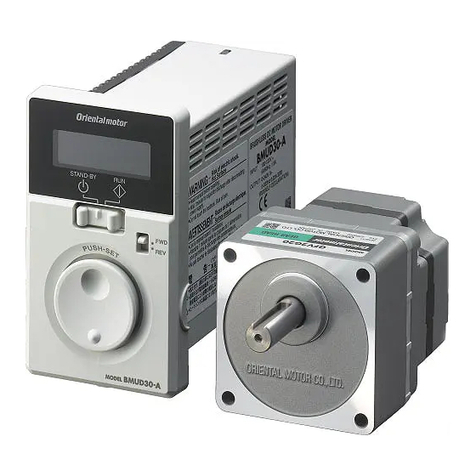
Oriental motor
Oriental motor BMU Series quick start guide

woodmizer
woodmizer D19 Safety, Operation, Maintenance & Parts Manual
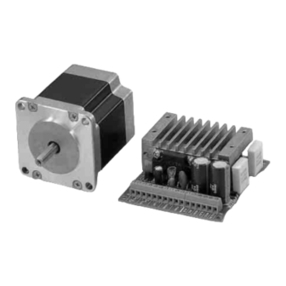
Oriental motor
Oriental motor CSK243-ATA operating manual