King nutronics 3666-12-101 User manual

CONTROL VALVE ASSEMBLY
Overhaul Instructions
Rev. 6/2014
King Nutronics Corporation PUB 3666-245-15
6421 Independence Ave. Woodland Hills, CA 91367
PH: (818) 877-5460 • www.kingnutronics.com
3666-12-101

For assistance, contact:
King Nutronics Corporaon
6421 Independence Avenue
Woodland Hills, California 91367
Phone: (818) 887-5460
Fax: (818) 887-2766
E-mail: inf[email protected]
Web Site: www.kingnutronics.com
NOTICE OF PROPRIETARY RIGHTS
The design concepts and engineering details embodied in this manual, which are the property of King Nutronics
Corporaon, are to be maintained in strict condence. No element or detail of this manual is to be spurious-
ly used, nor disclosed, without the express wrien permission of King Nutronics Corporaon. All rights are
reserved. No part of this publicaon may be reproduced, stored in a retrieval system, or transmied in any form
or by any means, electronic, mechanical, photocopying, recording, or otherwise, without prior wrien permis-
sion from King Nutronics Corporaon.
COPYRIGHT © 2005 BY King Nutronics Corporaon
ALL RIGHTS RESERVED
PRINTED IN THE UNITED STATES OF AMERICA

Fig. 1. King Nutronics Corporaon PN 3666-12-101 Control Valve Assembly and Components
i.
King Nutronics Corporaon PUB 3666-245-15, Rev 6/2014

Table 1
Parts Idencaon for King Nutronics Corporaon PN 3666-12-101 Control Valve
Descripon Part Number Fig. 1 Item No.
Solenoid coil assembly 3666-254-1 1
Gland nut 3666-257-1 2
Idencaon label 3666-245-5 3
Spacer 3666-253-3 4
Washer 3666-253-1 5
Ball guide 3666-272-1 6
Ball spring * 3666-263-1 7
Ball * 3666-12-9 8
O-ring packing * KP150000800000 9
O-ring packing * KP150011200000 10
Valve seat assembly * 3666-249-1 11
O-ring packing * KP150011000000 12
* Included in King Nutronics Corporaon PN 3666-245-1 Control Valve Repair Kit.
ii.

1.1 OVERVIEW
These instrucons contain the procedures for replacing the seals, ceramic ball, seat assembly, and spring used in the
pressure and venng solenoid assemblies incorporated in the Model 3666 Automac Pressure Calibrator Control Valve
Assembly, King Nutronics Corporaon PN 3666-12-101. All parts required for Control Valve overhaul are included in
the King Nutronics Corporaon PN 3666-245-1 repair kit. Each solenoid in the Control Valve requires one repair kit for
overhaul.
The following should be noted prior to overhauling the Control Valve Assembly:
1. The King Nutronics Corporaon PN 3666-245-1 repair kit can only be used for repair of King Nutronics Corporaon
PN 3666-12-101 Control Valve Assemblies. The repair kit cannot be used with the earlier version of the control
valve, King Nutronics Corporaon PN 3666-12-1.
2. Seal and ball component replacement should only be performed aer it has been determined that improper valve
operaon has been caused by faulty seals or worn parts associated with the ball actuaon mechanism.
3. If replacing the seals and ball components does not recfy the Control Valve problem, contact King Nutronics Cor-
poraon for assistance.
4. Control Valve overhaul should be performed at the Depot level by a technician with experience in the repair and
overhaul of mechanical instruments and components. A clean and well-lighted workbench is also required to en-
sure dust- and contaminant-free assembly of the component parts.
1.2 VALVE REPAIR KIT CONTENTS
The King Nutronics Corporaon PN 3666-245-1 Control Valve Repair Kit contains all of the parts necessary to overhaul
the solenoid assembly on either the “pressure side” or the “vent side” of the PN 3666-12-101 Control Valve. It should
be noted that the components in both of the solenoids are idencal, and the repair kit can be used in either one.
NOTE: Due to the ght tolerances required for proper Control Valve operaon, avoid unnecessary swapping of solenoid
components, such as coils, actuators, seat assemblies, and bodies.
Locaons of the repair kit components in the Control Valve Assembly are depicted in Figure 1 of these instrucons. The
contents of the repair kit are listed below in Table 2.
Table 2
Contents of Control Valve Repair Kit PN 3666-245-1
Quanty Part Number Descripon Fig. 1 Item Number
1 3666-12-9 Ceramic ball 8
1 3666-249-1 Valve seat assembly 11
1 3666-263-1 Ball spring 7
1 KP150011000000 O-ring packing 12
1 KP150000800000 O-ring packing 9
1 KP150011200000 O-ring packing 10
OVERHAUL INSTRUCTIONS FOR
KING NUTRONICS CORPORATION PN 3666-12-101
CONTROL VALVE ASSEMBLY
1-1
King Nutronics Corporaon PUB 3666-245-15, Rev 6/2014

1.3 OVERHAUL PROCEDURES
NOTE: In the following instrucons, the numbers in parentheses refer to the parts shown in Figure 1.
CAUTION
Do not break the Stroke Adjustment Seal or loosen the Stroke Adjustment Assembly on the
Solenoid Coil Assembly. This adjustment is set at the factory and should not require readjustment.
1.3.1 VALVE DISASSEMBLY PROCEDURE
To disassemble the King Nutronics Corporaon PN 3666-12-101 Control Valve, do the following:
1. Remove the control unit chassis assembly from the case. Place the chassis assembly on the workbench, or other
suitable work surface, with the Main PCB assembly facing upward.
2. Main PCB assembly is hinged on one side. Remove the screws and washers securing the other side of the Main
PCB assembly to the chassis, then swing the PCB assembly aside on its hinges to access the inside of the chassis.
Set the screws and washers aside.
3. Disconnect the Control Valve wiring harness from its connector on the exible circuit assembly. This connector is
located on the side of the chassis assembly.
4. Disconnect the three tubing assemblies from the Control Valve using an appropriate wrench.
5. Remove the two screws and washers securing the control valve to the chassis assembly and set aside.
6. Remove the control valve assembly and rubber pad from the chassis.
NOTE: The orientaon of the Control Valve should be noted to ensure that the input and output ports are posioned
correctly when the valve is reinstalled. The input port is idened by the word “IN” stamped on the valve body. The
output port has the word “OUT” stamped on the valve body.
7. Place the Control Valve Assembly in a vise with the faulty Solenoid Coil Assembly (1) facing upward.
8. Remove the Safety Wire from the Gland Nut (2).
9. Loosen the Gland Nut (2) using an appropriate wrench, then remove the Solenoid Coil Assembly (1).
10. Remove the O-ring packing (12) from the Valve Seat Assembly (11). Discard the O-ring packing.
11. Remove the Valve Seat Assembly (11) by pulling straight up unl it is free of the valve body.
12. Remove the O-ring packing (9) from the Valve Seat Assembly or the cavity in the valve body. Discard the O-ring
packing.
13. Remove the O-ring packing (10) from the Valve Seat Assembly. Discard the O-ring packing.
14. Using tweezers, remove the Ball (8) from the Ball Guide (6) cavity. Discard the Ball.
15. Remove the Ball Spring (7) from the Ball Guide (6). Discard the Ball Spring.
16. Clean all parts with isopropyl alcohol, then blow dry with compressed air. The Control Valve is now ready for over-
haul and reassembly.
1-2

1.3.2 VALVE OVERHAUL AND ASSEMBLY PROCEDURE
To overhaul and reassemble the King Nutronics Corporaon PN 3666-12-101 Control Valve Assembly, do the following:
NOTE: The Valve Seat Assembly, King Nutronics Corporaon PN 3666-249-1, consists of a Valve Seat permanently ce-
mented onto an Actuator Guide Assembly. This unit supersedes earlier versions in which a replaceable Valve Seat was
pressed onto the Actuator Guide Assembly. Do not aempt to remove the Valve Seat from the PN 3666-249-1 Valve
Seat Assembly or damage will result.
1. Insert the Spacer (4) and Washer (5) into the valve body.
2. Insert the Ball Guide (6) into the valve body.
3. Insert the replacement Ball Spring (7) included in the kit into the Ball Guide (6).
4. Posion the replacement Ball (8) on top of the Ball Spring (7) in the Ball Guide (6).
5. Install the replacement O-ring packing (9) on the Valve Seat Assembly (11) as shown in Figure 1.
6. Install the replacement O-ring packings (10) and (12) on the Valve Seat Assembly (11) as shown in Figure 1.
7. Carefully clean the face of the valve seat using a coon swab moistened with isopropyl alcohol. Blow dry gently
with compressed air.
8. Insert the Valve Seat Assembly (11) into the valve body by gently turning and pushing straight down.
9. Posion the Solenoid Coil Assembly (1) on the Valve Seat Assembly (11). Secure the Solenoid Coil Assembly (1)
with the Gland Nut (2).
10. Using a torque wrench, ghten the Gland Nut (2) to 45 -lbs.
11. Safety wire the Gland Nut (2) to the valve body.
12. Posion the Control Valve in the Chassis Assembly. Connect the three tubing assemblies in the chassis to the Con-
trol Valve. The tube ngs should be “nger ght” for this step.
13. Posion the rubber pad in the chassis assembly. Secure the rubber pad and Control Valve using the two screws and
washers removed during disassembly.
14. Tighten the three tubing connecons to the Control Valve using an appropriate wrench.
15. Connect the Control Valve wiring harness to its connector on the exible circuit assembly.
16. Swing the Main PCB assembly back onto the chassis and secure it using the screws and washers removed during
disassembly.
17. Install the Chassis Assembly in the case.
1-3King Nutronics Corporaon PUB 3666-245-15, Rev 6/2014

1.3.3 FUNCTION AND LEAK TESTS
Following overhaul, the King Nutronics Corporaon PN 3666-12-101 Control Valve Assembly must be tested for
proper funcon and leakage in accordance with the following procedure:
1. Congure the Model 3666 Automac Pressure Calibrator for standard gauge calibraon.
2. Install the dust plug into the Control Unit Quick Disconnect TEST port.
3. Program the following test points using psi units in the upscale and downscale direcons: 20; 200; 2,000;
5,000; and 10,000. Operate the unit through the programmed range.
4. Program a new test with a 20-psi test point. Press the [ADV] key to commence tesng.
5. Wait for the MANUAL SET message to be displayed. Aer this message appears, observe the ACTUAL pressure
in the display for stability.
a. If the displayed value connues to increase past the programmed setpoint, the “pressure side” of the
valve is leaking.
b. If the displayed value decreases, apply a bubble soluon to the VAC port to check for leakage. If leakage
is evident, the “vent side” of the valve is leaking.
1-4
Popular Control Unit manuals by other brands
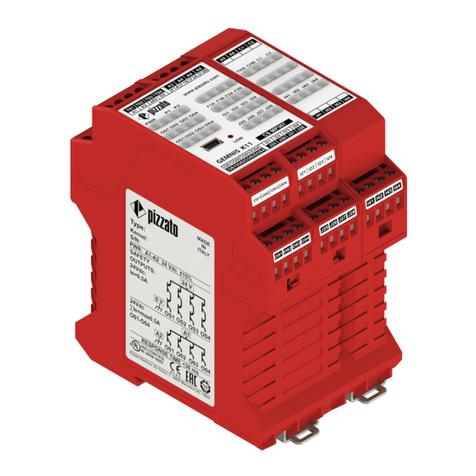
pizzato
pizzato CS MP307M0 quick start guide

Advanced Energy
Advanced Energy Thyro-PX Anybus Modbus TCP Guide
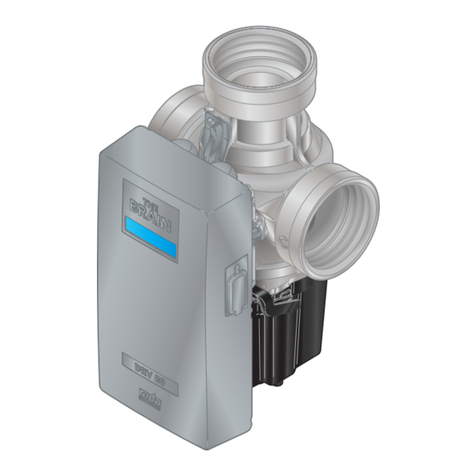
Armstrong
Armstrong The Brain DRV80R manual

American Standard
American Standard 7017 Series installation instructions

Viessmann
Viessmann SM1 Installation and service instructions
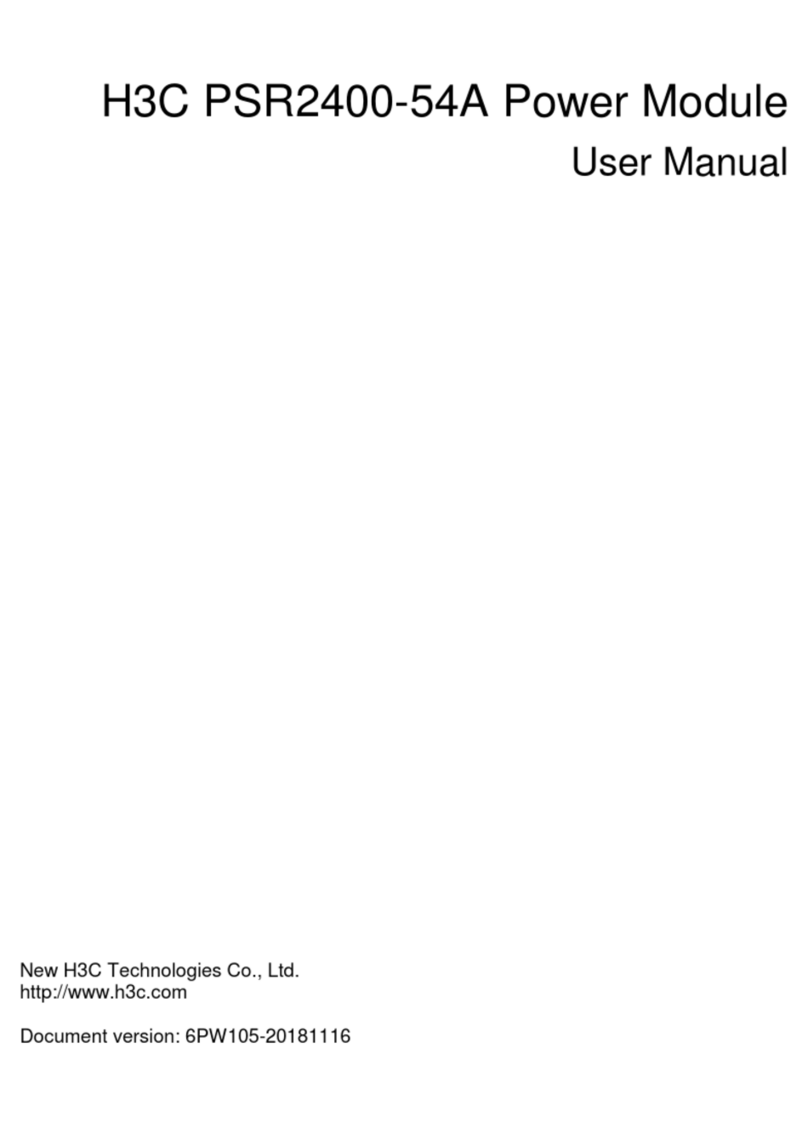
H3C
H3C PSR2400-54A user manual

Siemens
Siemens S7-1500 PROFIBUS operating instructions
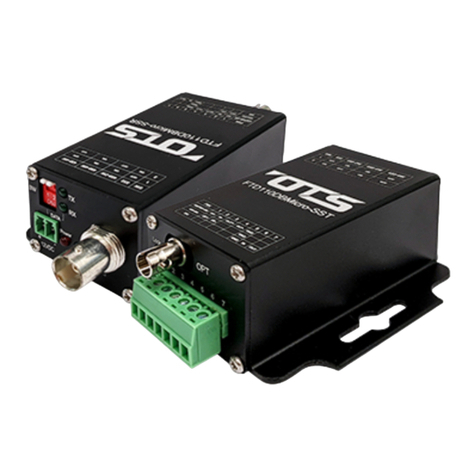
OTS
OTS FTD110DBMicro Quick installation guide

Lauda
Lauda LRZ 914 Operation manual
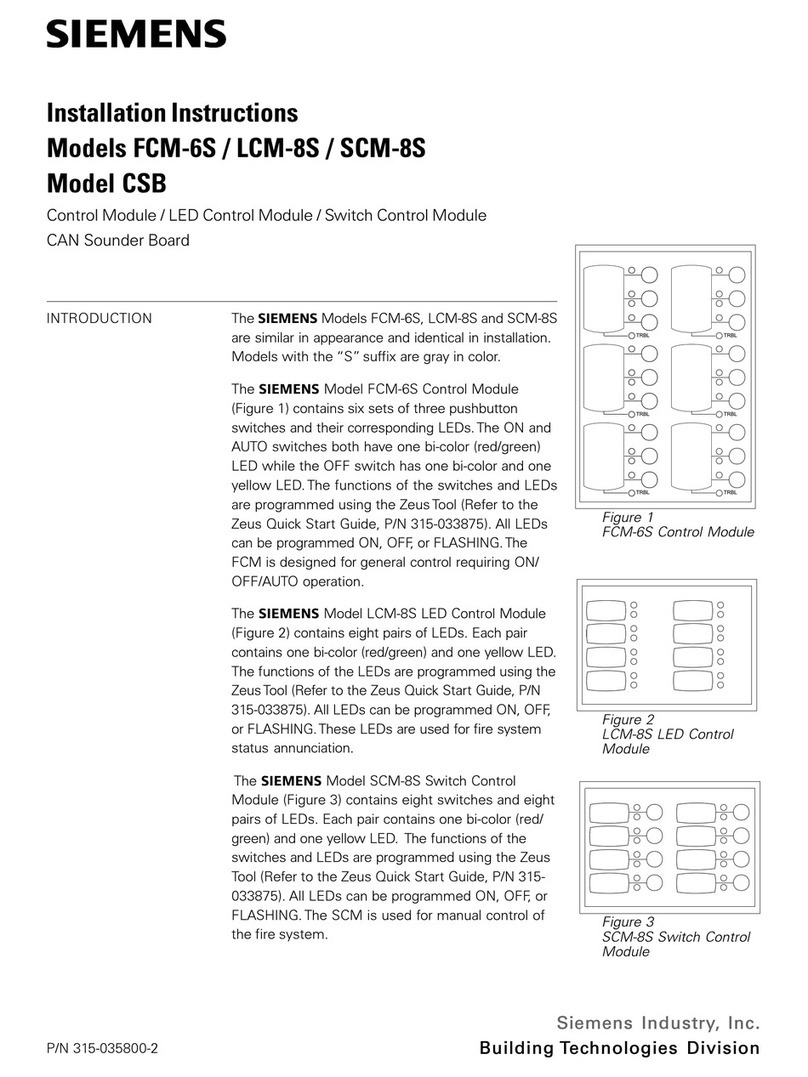
Siemens
Siemens FCM-6S installation instructions
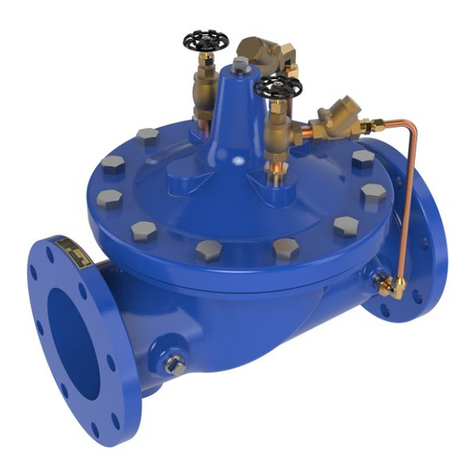
CLA-VAL
CLA-VAL 81-02/681-02 Installation operation & maintenance
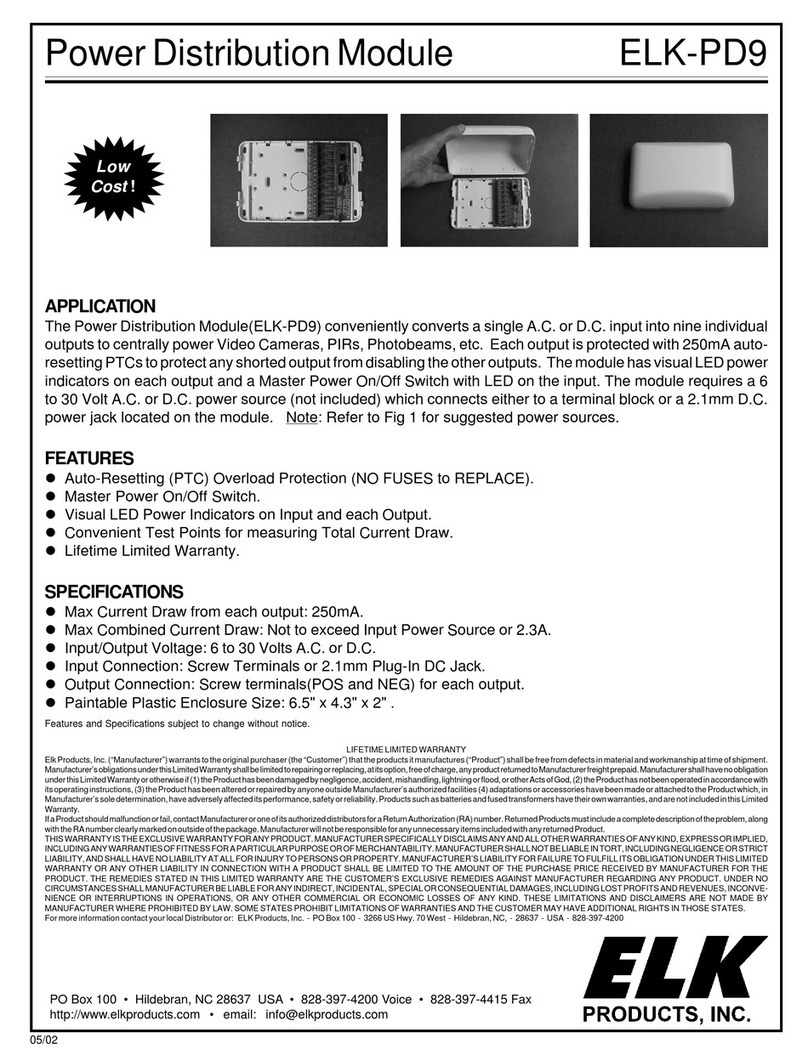
Elk Products
Elk Products ELK-PD9 installation instructions