Koganei MSU Series User manual

RoHS compliant
product
ISO 9001 / ISO 14001
Catalog No.BK-A5046
Multi-Channel, Multi-Sensor Controller
MSU Series
Are you
troubled?
Best
Answer!
1 controller centrally manages any 4 sensors
with outputs of 1 to 5 V* !
Plus, with the RS485 communication type,
up to 16 controllers can be centrally
managed! (Maximum of 64 sensor heads)
Do you have these problems?
* Including other manufacturer’s products
RS232C
communication
RS485
communication
Connect any
sensor with 1 to
5 V output
Pressure and
flow sensor
heads are
available
5 output mode
patterns
There are too many types of sensors (pressure, flow, etc.) inside the equipment...
Monitoring and controlling each sensor is too complicated!
Added PNP output type
NEW
*Only NPN type is UL compliant.

●❶ CAUTION Read the safety precautions on page 3before using this product.
Pressure sensor head variations
Output mode setting
Flow rate sensor head variations (existing models) *Not UL/CE compliant.
* To use Window Comparator Mode 1 and Window Comparator Mode, setting must be L1 > L2.
Pressure sensor head
options
Any sensor that can be connected
-101.3 kPa 0 kPa
-3ℓ/min
-500
mℓ/min 500 mℓ/min
10ℓ/min
3ℓ/min
-100 kPa
-100 kPa
0ℓ/min
220 kPa
1000 kPa
For negative
pressure
MSU-PH-EA-□
FS-R3
Compound
pressure (for
low pressure)
MSU-PH-ER-□
FS-R05
Compound
pressure (for
high pressure)
MSU-PH-EM-□
FS-10
MSU-PH-EA-S
MSU-PH-ER-S
MSU-PH-EM-S
Sensor head
Sensor head
Reducer connection type
φ4 [0.157]: −UR4
φ6 [0.236]: −UR6
Female threaded
connection type
M5: −M5
Operating pressure range 1 kPa = 0.295 inHg
Operating flow range 1ℓ/min = 0.035 ft3/min
-100
-3
0
0
100
3
200 1000 (kPa)
10 (ℓ/min)
Extensive output settings can support your application!
Any type of sensor can be connected!
Multi-channel multi-sensor controller MSU Series
L1
L2
Hysteresis H2
Hysteresis H1
L1
Hysteresis H1
L1
Hysteresis H1
L2(OFF lit) L1(ON lit)
When L1 < L2
When L1 > L2
No output when L1 = L2.
L1(ON lit) L2(OFF lit)
Switch output
L1
L2 Hysteresis
ON t
• Hysteresis Mode • Window comparator mode 1
• Window comparator mode • High Mode • Low Mode
Mode for turning output ON within the set value range for L1 and L2
(OFF point depends on response differential setting)
Mode for turning output ON when above the ON point
(OFF point depends on response differential setting)
Mode for turning output ON when below the ON point
(OFF point depends on response differential setting)
Mode for setting the ON point and OFF point
(mode that does not turn on when between L1 and L2 while rising)
Mode for turning output ON within the set value range for L1 and L2
(OFF point depends on response differential setting)
Does not turn on when entering range while rising
You can use a 1 to 5 V linear
output sensor by setting the
display value at 5 V and display
value at 1 V.
1V
5V
Displayvaluefor1V Displayvalueat5V
1 to 5 V output type

I/O
MSU
Pressure sensor head
or
Flow rate sensor head
or
Any 1 to 5 V sensor
4 point switch output
Command communications + 4 point switch output
Maximum of 16 controllers can be connected (maximum of 64 sensor heads)
I/O
MSU-232
I/O
MSU-485
RS232C
unit
4 point switch output
4 point switch output
RS232C communication
RS485 communication
4 point switch output
4 point switch output
External network
External network
RS485
unit
Network
unit
Network
unit
Daisy chain Max. 16 units
(64 heads)
Upper controller
Upper controller
Upper controller
Example connection 1
MSU
Example connection 2
MSU-232
Example connection 3
MSU-485
Equipped with communication mode compatible with existing models
Pressure sensor head
or
Flow rate sensor head
or
Any 1 to 5 V sensor
Pressure sensor head
or
Flow rate sensor head
or
Any 1 to 5 V sensor
Note1 Note 2
Note 1: 120 Ωtermination resistance required.
Note 2: When using RS485 communications,
connect a termination resistance
connector (IBFL-K-TR).
Command communications + 4 point switch output
●❷
* To use Window Comparator Mode 1 and Window Comparator Mode, setting must be L1 > L2.
Any sensor that can be connected
1 controller centrally manages multiple
sensors!
Any type of sensor can be connected!

Safety Precautions Always read these precautions carefully before use.
Before selecting and using products, please read all the Safety Precautions carefully to ensure proper product use.
The Safety Precautions shown below are to help you use the product safely and correctly, and to prevent injury or damage to assets beforehand.
Follow the Safety Precautions in ISO4414 (Pneumatic fluid power—General rules and safety requirements for systems and their components), JIS B
8370 (Pneumatic system regulations), and other safety regulations.
The directions are ranked according to degree of potential danger or damage:
"DANGER"
,
"WARNING"
,
"CAUTION!"
, and
"ATTENTION!"
.
DANGER
Expresses situations that can be clearly predicted as dangerous.
If the noted danger is not avoided, it could result in death or serious injury.
It could also result in damage or destruction of assets.
WARNING
Expresses situations that, while not immediately dangerous, could become dangerous.
If the noted danger is not avoided, it could result in death or serious injury.
It could also result in damage or destruction of assets.
CAUTION
Expresses situations that, while not immediately dangerous, could become dangerous.
If the noted danger is not avoided, it could result in light or semi-serious injury.
It could also result in damage or destruction of assets.
ATTENTION While there is little chance of injury, this content refers to points that should be observed for appropriate use of the
product.
■
This product was designed and manufactured as parts for use in General Industrial Machinery.
■
When selecting and handling equipment, the system designer or another person with sufficient knowledge and experience should always read the
safety precautions, catalog, instruction manual and other literature before commencing operation. Making mistakes in handling is dangerous.
■
After reading the Owner’s Manual, Catalog, etc., always place them where they can be easily available for reference to users of this product.
■
If transferring or lending the product to another person, always attach the Owner’s Manual, Catalog, etc., to the product where they are easily
visible, to ensure that the new user can use the product safely and properly.
■
The danger, warning, and caution items listed under these “Safety Precautions” do not cover all possible cases. Read the Catalog and Owner’s
Manual carefully, and always keep safety first.
DANGER
●
Do not use for the applications listed below:
1. Medical equipment related to maintenance or management of
human lives or bodies.
2.
Mechanical devices or equipment designed for the purpose of
moving or transporting people.
3.
Critical safety components in mechanical devices.
This product has not been planned or designed for purposes that
require advanced stages of safety. It could cause injury to human life.
●
Do not use in locations where explosives, flammables, or other
dangerous substances are present. This product is not an
explosion-proof type unit. Explosion or ignition may occur.
●
When mounting the product and workpiece, always firmly support
and secure them in place. Dropping or falling the product or
improper operation could result in injury.
●
Never attempt to remodel the product. It could result in abnormal
operation leading to injury, electric shock, fire, etc.
●
Never attempt inappropriate disassembly, or assembly of the
product relating to its basic inner construction, or to its performance
or functions. It could result in injury, electric shock, fire, etc.
●
Do not splash water on the product. Spraying it with water, washing
it, or using it underwater could result in malfunction of the product
leading to injury, electric shock, fire, etc.
●
Do not make any adjustments (connecting or disconnecting wiring
connectors, mounting or positioning sensor heads, etc.) to
mechanisms attached to the product while the product is operating.
This could result in abnormal operation leading to injury.
WARNING
●
Because Koganei products may be used under a wide variety of
conditions, decisions concerning conformance with a particular
system should be made upon the careful evaluation by the person
in charge of system design.
Assurances concerning expected system performance and safety are
the responsibility of the designer who decides system conformity. Be
sure to use the latest catalogs and technical materials to study and
evaluate specification details, to consider the possibility of machine
breakdown, and to configure a system that ensures fail-safe safety and
reliability.
●
Do not use the product in excess of its specification range. Doing so
creates the risk of product breakdown, loss of function, or damage.
It could also drastically reduce the operating life.
●
Before supplying air or electricity to the device and before starting
operation, always conduct a safety check of the area of machine
operation. Unintentional supply of air or electricity could possibly
result in injury caused by contact with moving parts.
●
Do not touch the terminals and the miscellaneous switches, etc.,
while the device is powered on. There is a possibility of electric
shock and abnormal operation.
●
Do not throw the product into fire. The product could explode and/or
release toxic gases.
●
Do not sit on the product, place your foot on it, or place other objects
on it. Accidents such as falling could result in injury. Dropping or top-
pling the product may result in injury, or it might also damage or break
it, resulting in abnormal or erratic operation, runaway, etc.
●
Before doing maintenance inspections, repairs, or replacement of
any parts, always completely cut off all air and vacuum pressure
connections, and confirm that the pressure in the product and con-
nected pipes is atmospheric pressure. In particular, be aware that
pressure remains in compressors, vacuum pumps, and air tanks.
The actuator may move abruptly if residual air pressure remains
inside the piping, causing injury.
●
Use safety circuits or system designs to prevent damage to
machinery or injury to personnel when the machine is shut down
due to emergency stop or electrical power failure.
●
Before performing any kind of wiring work, be sure to turn off the
power. Failure to do so creates the risk of electric shock.
●
Do not allow lead wires and other cords to become damaged.
Allowing the cords to be damaged, bent excessively, pulled, rolled
up, placed under heavy objects or squeezed between two objects,
may result in current leaks or defective continuity that will lead to
fire, electric shock, or abnormal operation.
●
Do not connect or disconnect connectors while the power is turned
on. Also, never apply unnecessary force to connectors. Doing so
creates the risk of personal injury, device damage, and electric
shock due to abnormal machine operation.
●
Always check the catalog and other reference materials for correct
product wiring and piping. Improper wiring or piping causes
abnormal operation of the actuator, etc.
●
Use countermeasures for heat dissipation so that the ambient
temperature of the product stays within the specified temperature
range if the energizing time is long or if the product is installed
inside a control panel. Also, contact Koganei when continuously
energizing for long periods of time.
●
Do not locate solenoid valves or their control wires near power lines
carrying large currents, or in locations subject to strong magnetic
fields or surges. It could result in unintended operation.
●
Do not use the product near the ocean, in direct sunlight, near mercu-
ry vapor lamps, or near equipment that generates ozone.
Deterioration of rubber parts caused by ozone may reduce perfor-
mance and functions or stop functions. (except for ozone resistant
products)
●
Do not use any type of medium that is not specifically stipulated in
the specifications. Using a non-specified medium could lead to short
term loss of function, sudden degradation of performance, and a
reduced operating life.
●
After completing wiring work, check to make sure that all
connections are correct before turning on the power.

Safety Precautions
Other
●Always observe the following items.
1.
When using this product in pneumatic systems, always use
genuine Koganei parts or compatible parts (recommended parts).
When doing maintenance or repairs, always use genuine Koganei
parts or compatible parts (recommended parts).
Always follow the designated procedures and methods.
2.
Never do inappropriate disassembly or assembly of the product
related to basic construction, performance, or functions.
3.
Sensor heads are for use with non-corrosive gas. Do not use it for
liquids or corrosive gas.
4.
Check the power fluctuation to ensure that the input power does
not exceed the rated value.
5.
Avoid use during the transitional state (0.5 seconds) when the
power is turned on.
6.
Do not insert wires from the detection ports of the sensor heads.
Doing so may damage the diaphragm and cause it to be unable to
operate normally.
7.
Never use a needle or any other sharp pointed object to perform
key operations.
Koganei cannot be responsible if these items are not properly observed.
●
Do not use the product in locations subject to direct sunlight (ultraviolet
radiation); in locations subjected to high temperature or humidity; in
locations where dust, salt, or iron particles are present; or in locations
with media and/or an ambient atmosphere that includes organic
solvents, phosphate ester type hydraulic oil, sulfur dioxide gas, chlorine
gas, acids, etc. It could lead to early shutdown of some functions, a
sudden degradation of performance, and a reduced operating life. For
information about materials, see Major Parts and Materials.
●
Do not apply an external magnetic field to the product while it is operating.
Unintended operations could damage equipment or cause injury.
●
Make sure that the polarity of wiring connections is correct.
Incorrect polarity could result in damage to the product.
●
Pressure sensor heads could be damaged by static electricity if you
touch them with your hand while they are energized.
CAUTION
●
When installing the product, leave room for adequate working space
around it. Failure to ensure adequate working space will make it
more difficult to conduct daily inspections or maintenance, which
could eventually lead to system shutdown or damage to the product.
●
Do not scratch, dent, or deform the product by climbing on it, using it as a
step, or placing objects on top of it. It could result in damaged or broken a
product that results in operation shutdown or degraded performance.
●
Always post an “operations in progress” sign for installations,
adjustments, or other operations, to avoid unintentional supplying of
air, electrical power, etc. Unintended power supply can cause electric
shock and sudden operation, creating the risk of personal injury.
●
Depending on the product, unintended operations may occur when
a leakage current occurs in the control circuit. Use countermeasures
for circuit leakages in the control circuit so as not to exceed the
allowable leakage current values for the product's specifications.
●
Use only sensor heads that satisfy the specifications of the sensor
controller with multi-channel multi-sensor controllers.
Using one that is outside the specifications causes erratic operation.
●
Use the correct tightening torque to mount sensor heads.
Over-tightening beyond the allowed tightening torque may damage the
mounting threads or sensor head, etc. However, insufficient tightening
torque may cause leaks or shifts in the sensor head position, resulting in
unstable operation. Refer to “Instruction Manual” for the tightening torques.
●
While handling multi-channel multi-sensor controllers or sensor heads,
do not subject them to excessive shock (over 490 m/s
2
[50 G]) by hitting,
dropping, or bumping them. Even if the product appears undamaged,
damage to internal components can cause abnormal operation.
●
Avoid short circuiting the loads. Turning a sensor’s output on while
the load is short-circuited causes overcurrent, which will damage
the sensor head instantly. Furthermore, even with multi-channel
multi-sensor controllers, turning on SW output while the load is
short-circuited may damage the products due to over current.
Example of short-circuit load:
Output lead wire for sensor output (SW output)
is directly connected to the power supply.
ATTENTION
●
When considering the possibility of using this product in situations or
environments not specifically noted in the Catalog or Owner’s
Manual, or in applications where safety is an important requirement
such as in an airplane facility, combustion equipment, leisure
equipment, safety equipment, and other places where human life or
assets may be greatly affected, take adequate safety precautions
such as an application with enough margins for ratings and
performance or failsafe measure. Be sure to consult us about such
applications.
●
Use a protective cover, etc., to ensure that human bodies do not come
into direct contact with the operating portion of mechanical devices, etc.
●
Do not control in a way that would cause workpieces to fall during power failure.
Take control measures so that they prevent the workpieces, etc., from
falling during power failure or emergency stop of the mechanical devices.
●
When handling the product, wear protective gloves, safety glasses,
safety shoes, etc., to keep safety.
●
When the product can no longer be used, or is no longer necessary,
dispose of it appropriately as industrial waste.
●
Pneumatic equipment can exhibit degraded performance and
function over its operating life. Always conduct daily inspections of
the pneumatic equipment, and confirm that all requisite system
functions are satisfied, to prevent accidents from happening.
●
For inquiries about the product, contact your nearest Koganei sales
office or Koganei overseas department. The address and telephone
number is shown on the back cover of this catalog.
Warranty and General Disclaimer
1.
Warranty Period
The warranty period for Koganei products is 1 year from the
date of delivery.
*
However, some products have a 2-year warranty; contact your
nearest Koganei sales office or the Koganei overseas
department for details.
2.
Scope of Warranty and General Disclaimer
(1)
When a product purchased from Koganei or from an
authorized Koganei distributor or agent malfunctions during the
warranty period in a way that is attributable to Koganei's
responsibility, Koganei will repair or replace the product free of
charge. Even if a product is still within the warranty period, its
durability is determined by its operation cycles and other
factors. Contact your nearest Koganei sales office or the
Koganei overseas department for details.
(2)
The Koganei product warranty covers individual products.
Therefore, Koganei is not responsible for incidental losses
(repair of this product, various expenses required for
replacement, etc.) caused by breakdown, loss of function, or
loss of performance of Koganei products.
(3)
Koganei is not responsible for any losses or for any damages
to other machinery caused by breakdown, loss of function, or
loss of performance of Koganei products.
(4)
Koganei is not responsible for any losses due to use or storage
of the product in a way that is outside of the product
specifications prescribed in Koganei catalogs and instruction
manuals, and/or due to actions that violate the mounting,
installation, adjustment, maintenance or other safety
precautions.
(5)
Koganei is not responsible for any losses caused by breakdown
of the product due to factors outside the responsibility of Koganei,
including but not limited to fire, natural disaster, the actions of third
parties, and intentional actions or errors by the purchaser.
General precautions
1. When using a power supply with a commercially available
switching regulator, be sure to connect a frame ground (F.G.).
Use Class 2 switching regulator.
2. When using devices that generate noise (switching regulator,
inverter motor, etc.) in the vicinity of the sensor installation, be
sure to connect a frame ground (F.G.) to the devices.
3. After completing wiring work, check to make sure that all
connections are correct.
Wiring
Handling Instructions and Precautions
4

When the sensor head MSU-PH-□-□is supplied, the sensor head
body and mini clamp connector (male) are not yet connected. Follow
the procedure below to perform the connection.
1. Check that the connector cover (the part where lead wires are to
be inserted) is protruding from the connector body.
It cannot be used if it’s flat and placed at the same level against the body.
2. Cut the cable at the length required for the sensor head. Strip off the
cable sheath for 50 mm [1.97 in.] from the cable end, and expose the
lead wires. At this time, do not take off the lead wire insulation.
3.
Follow the instructions in the table below to insert the lead wires into the
hole in the connector cover. Look through the top of the semi-
transparent cover to check that the lead wires have been firmly inserted
all the way to the back. (Insertion length is about 9 mm [0.35 in.].)
Use caution in making the connections, since switching on the power
with wrong connections will damage the sensor head and controller.
Handling Instructions and Precautions
Sensor head and connector connection procedure
Use the small screws provided to
mount the sensor head.
The tightening torque should not
exceed 6.0N·cm [0.53in·lbf].
Sensor head body
Use the hex socket
head screws
(M2.6×0.45, length
5 mm [0.197 in.]) to
mount the mounting
bracket into the
mounting holes on the
back of the sensor
controller. The
tightening torque should
not exceed 32 N·cm
[2.83 in·lbf].
Attaching the panel mounting parts and protective front cover
PSU-BR
2-M2.6 ×0.45 Depth 6
(Mounting thread)
Mounting bracket
Hex socket head screw
(Provided with
mounting bracket)
Attaching the mounting bracket
Panel plate
Mounting
body
Protective
front cover
(sold separately)
Multi-Channel, Multi
Sensor controller
Mounting holder
Groove on panel mounting body
1)
2)
3)4)
1) Insert the mounting
body from the front
of the panel hole.
2) Insert the sensor
controller from the
back of the mounting
body.
3)
From the back of the
position in 2), place
the mounting holder
on the mounting body
groove, and insert it.
4) Set the separately
sold protective front
cover in place.
※For removal, follow the above
procedure in reverse, using a
screwdriver or other tool to
remove the mounting holder.
To mount the sensor head and the power supply, switch, and
communication cable, align the lock lever position in the direction of
the arrow as shown in the figure, and push until the lock hooks on
the controller-side connector.
To remove, push down completely on the lock lever, take the
connector and pull it out. At this time, be careful to avoid applying
excessive force on the lead wires.
Attaching and removing of the sensor head, and the
power supply, switch, and communication cable
MSU-□, MSU-232-□MSU-485-□
4-sensor head connector
Lock lever
Comxmunication connector
Lock lever
Comxmunication
connector
Lock lever
Lock lever
Power connector
Lock lever
Power, switch,
communication
connector
4-sensor head connector
Lock lever
No. on the
connector
1
2
3
4
Color of lead wire
Sensor head brown wire
Sensor head black wire
Sensor head blue wire
Prepared by customer
AWG 24-26 (0.14-0.3sq)
Insulation diameter:
φ0.8-1.0 mm [0.031-0.039 in.]
Signal name
Sensor head power supply
(+)
Sensor head voltage output
Sensor head power supply (0V)
Reference pressure capture
4. Taking care to avoid letting the lead wires slip out from the
connector, use pliers or some other hand tool to crimp the cover
and connector body, and push the cover into the connector body.
Limit the crimping force to 980.7 N [220.5 lbf].
When the cover is flat and placed at the same level against the
connector body, the connection is complete.
5. In the same way, handle the sensor head relay cable PSUK-□
mini-clamp connectors (male, female).
6. Check one more time that the wiring is correct.
Reference pressure capture
Sensor head
Brown
Black
Blue
Sensor head
1234
PLC etc.
50mm
50mm
[1.97 in.]

Specifications
List of controller specications
Item Specications
Power
supply
Voltage 12 to 24 VDC ±10% *Use a Class 2
power supply.
Sensor head supply
voltage
12 to 24 VDC ±10% (*Depending on
power supply voltage)
Consumption
current
100 mA MAX. (Not including supply
power to sensors)
Sensor input
Number of
connected sensors 4
Maximum
consumption current
for sensor head
Each channel; under 150 mA
Input voltage range 1.0 to 5.0 VDC
Input impedance 1 MΩ
Maximum applied
voltage 5.6 V MAX.
Compatible sensor
heads
MSU-PH-EA: -101.3 to 0.0 kPa
[-29.9 to 0.000 inHg]
MSU-PH-ER: -100.0 to 220.0 kPa
[-29.5 to 65.0 inHg]
MSU-PH-EM: -100 to 1000 kPa
[-29.5 to 295 inHg]
FS-R05: -500 to 500 mL/min
[-0.018 to 0.018 ft3/min]
FS-R3: -3.00 to 3.00 L/min
[-0.106 to 0.106 ft3/min]
FS-10: 0.00 to 10.00 L/min
[0.000 to 0.353 ft3/min]
Any sensor (set display at 1 V and 5 V)
External
output
Output points 4
Output method
MSU-□
NPN open collector
MSU-□-PNP
PNP open collector
Responsiveness 5 ms (when lter function is OFF)
Load voltage 30 V MAX.
Load current 50 mA MAX.
Internal voltage
drop
NPN: 0.3 V MAX. (when 5 mA)
PNP: 2V MAX. (when 50 mA)
Output mode
Hysteresis mode, window comparator
mode 1, window comparator mode,
high
mode, low mode, output OFF mode
Repeatability 1% FS
Functions
Threshold value setting, response differential
setting, output inversion, ON delay
External
imput
Input points 4
Functions Zero reset or import reference pressure
Display
Display type LCD display
Color 2 color display (red, green)
Number of digits
displayed (-) 4-digit display
Display resolution
MSU-PH-EA: 0.1 kPa [0.030 inHg]
MSU-PH-ER: 0.1 kPa [0.030 inHg]
MSU-PH-EM: 1 kPa [0.295 inHg]
FS-R05: 1 mL/min [0.000 ft3/min]
FS-R3: 0.01 L/min [0.000 ft3/min]
FS-10: 0.01 L/min [0.000 ft3/min]
(if more than 5.00 L/min [0.177 ft3/min],
then it is 0.05 L/min [0.002 ft3/min])
Switch output
conrmation LED
Lit when external output is ON
(red LED)
Display channel
conrmation LED
LED that corresponds to the currently
displayed pressure lights (green LED)
Display accuracy
1%F.S. ±1digit (Controller stand alone)
Functions
Auto scan, zero adjust, display update
cycle, backlight setting, setting for turning
LEDs off, peak-hold, bottom-hold
Filter
(Applicable to both SW output and display)
OFF to level 7
Item Specications
Main unit keys Up key: △Down key: ▽Enter key:
Communication
Communications
standard RS232C RS485
Communication
speed 9600, 19200 bps
9600, 19200,
38400, 57600,
115200 bps
Address settings None Rotary switches
Number of daisy
chain connections Not applicable MAX. 16
General
Operating
temperature range
-10 to 50℃[14 to 122°F];
when stored: -20 to 80℃[-4 to 176°F]
(non-condensation, non-freezing)
Operating humidity
range 35 to 85% RH
Dielectric strength 500 VAC for 1 minute
Insulation
resistance 100 MΩMIN (at 500VDC megger)
Vibration resistance
Endurance: 10 to 55 Hz; secondary
amplitude: 1.5 mm [0.059 in.], 2 hours
in each direction (XYZ)
Shock resistance
Endurance: 490 m/s2[50 G],
5 times in each direction (XYZ)
(when not electried)
Materials Surface seal: PET; case: PBT, PC;
mounting screws: brass
Altitude 2000 m [6562 ft] or less
Mass 50 g [1.764 oz] (not including other
optional cables)
Environment Indoor use, POLLUTION DEGREE 2
Standard CE, UL (Recognition)
Note: Only NPN type is UL compliant.
List of pressure sensor head specications
Item Negative
pressure Compound pressure
Model MSU-PH-EA MSU-PH-ER MSU-PH-EM
Media Air or non-corrosive gas
Power
supply
Voltage 24 VDC ±10%
Consumption
current 6 mA MAX.
Analog
output
Output voltage 1 to 5 V
Zero-point
voltage (Vzero) 1.00 ±0.05 3.75 ±0.05 4.64 ±0.05
Span voltage 4.00 ±0.07 (reference value)
Temperature
characteristics Vzero: within ±30 mV; span: within ±2% F.S.
Output current 1 mA max. (load resistance of 5 kΩor more)
General
Operating
pressure range
kPa [inHg]
-101.3 to
0 [-29.9 to
0.000]
-100.0 to
220.0 [-29.5
to 65.0]
-100 to 1000
[-29.5 to 295]
Proof pressure
kPa [inHg] 900 [265.9] 1500 [443]
Operating
temperature
range
0 to 50℃[32 to 122°F];
when stored: -20 to 80℃[-4 to 176°F]
(when stored: humidity of less than 65%
RH, atmospheric pressure)
Operating
humidity range 35 to 85% RH
Insulation
resistance 100 MΩMIN (at 500VDC megger)
Dielectric
strength 500 VAC 1 minute
Altitude 2000 m [6562 ft] or less
Environment Indoor use, POLLUTION DEGREE 2
Mass 40 g [1.411 oz]
Standard CE, UL (Recognition)
Note: UL compliant when connected to NPN controller.
6

Wiring specications for the controller
<MSU-□, MSU-232-□>
Wiring specifications
<MSU-485-□>
Pressure sensor head: Characteristic tables of pressure and output
0 10 20 30 40 50 60 70 80 90 101.3
Pressure (kPa)
Output (V)
0.0
1.0
2.0
3.0
4.0
5.0
●MSU-PH-EA-□
−100 −50 50 100 150 2000 220
Pressure (kPa)
Output (V)
3.75
0.0
1.0
2.0
3.0
4.0
5.0
●MSU-PH-ER-□
−100 0 100 200 300 400 500 600 700 800 900 1000
Pressure (kPa)
Output (V)
4.64
0.0
1.0
2.0
3.0
4.0
5.0
●MSU-PH-EM-□1 kPa = 0.295 inHg
Connector type Item Specications
Manufactured by JST
B6B-XASK-1
Power supply
Pin 1: 24 V (red)
Pin 2: 0 V (black)
Switch output
Pin 3: SW1 (white)
Pin 4: SW2 (green)
Pin 5: SW3 (yellow)
Pin 6: SW4 (brown)
Manufactured by
Sumitomo 3M Limited
37104-3101
Data input
Pin 1: +V (brown)
Pin 2: sensor output
(black)
Pin 3: 0 V (blue)
Pin 4: IN
Manufactured by JST Data input/output
RS485
Pin 1: A (white)
Pin 2: B (pink)
Pin 3: 0 V (yellow)
Pin 4: N.C.
Pin 5: N.C.
Connector type Item Specications
Made by JST
B11B-XASK-1
Power supply
1 pin : 24V (red)
2 pin : 0V (black)
Data input
and output
Switch
output
3 pin : SW1 (white)
4 pin : SW2 (green)
5 pin : SW3 (yellow)
6 pin : SW4 (brown)
RS232CNote
7 pin : 0V (black)
8 pin : RXD (white)
9 pin : TXD (red)
10 pin : N.C
11 pin : N.C
Made by
SUMITOMO 3M
37104-3101
Data input
1 pin : +V (brown)
2 pin : Sensor output
(black)
3 pin : 0V (blue)
4 pin : IN
Note 1: MSU-232-□only.
Note 2: When wiring any other sensors, the lead wire colors are different
from those noted above.

Wiring
When connecting, refer to the gure below and use the provided power and signal cables.
CAUTION
●In case noise generating equipment (switching regulator, inverter motor, etc.) is used in the vicinity of this sensor, connect the frame
ground (F.G.) terminal of the equipment to an actual ground. Additionally, when selecting a power supply, choose one that is Class 2.
●Securely insert the connector.
●After completing wiring work, check to make sure that all connections are correct.
●Use a mechanical switch, photo coupler, or relay for external input. If the grounding potential of the external device to be used and the
grounding potential of this product are different, the external device should have an insulated on/off procedure for the 0V line.
●Verify that the supply voltage variation is within the rating.
Circuit Diagram
<NPN output type>
External
connection side
IN1
Tr1
Tr2
Tr3
Tr4
Sensor head Channel
1ch
(Brown)+V
(Black)Vout:1 TO 5V
(Blue) 0V
1
2
3
4Zd 1
Zd 2
Zd 3
Zd 4
D
Main
circuit
1
3
4
5
6
2
Power/switch output cable
(Red)+V
(White) OUT1
(Green)OUT2
(Yellow)OUT3
(Brown) OUT4
(Black) 0V
Load
Separate type 4-channel controller
DC12
~24
V
+
-
1
2
3
RS-232C communication cable
(Black)0V
(white)RXD
(Red) TXD
Host device with
RS-232C built-in
R1
innter circuit
RS-232C type
1
2
3
RS-485 communication cable
(White)A
(Pink)B
(Yellow)0V
Host device with
RS-485 built-in
RS-485 type
1
2
3
IN2
1
2
3
4R2
IN3
1
2
3
4R3
IN4
1
2
3
4R4
FLoad
Load
Load
Sensor head Channel
2ch
Sensor head Channel 3ch
Sensor head Channel
4ch
(Brown)+V
(Blue) 0V
(Brown)+V
(Blue) 0V
(Brown)+V
(Blue) 0V
(Black)Vout:1 TO 5V
(Black)Vout:1 TO 5V
(Black)Vout:1 TO 5V
External
connection side
<PNP output type>
IN1
Tr1
Tr2
Tr3
Tr4
1
2
3
4
Zd 1
Zd 2
Zd 3
Zd 4
1
3
4
5
6
2
DC12
~24
V
+
-
1
2
3
R1
RS-232C type
1
2
3
RS-485 type
1
2
3
IN2
1
2
3
4R2
IN3
1
2
3
4R3
IN4
1
2
3
4R4
+V
+V
+V
+V
Load
Load
Load
Load
Sensor head Channel
1ch
(Brown)+V
(Black)Vout:1 TO 5V
(Blue) 0V
Sensor head Channel
2ch
(Brown)+V
(Black)Vout:1 TO 5V
(Blue) 0V
Sensor head Channel
3ch
(Brown)+V
(Black)Vout:1 TO 5V
(Blue) 0V
Sensor head Channel
4ch
(Brown)+V
(Black)Vout:1 TO 5V
(Blue) 0V
External
connection side
Separate type 4-channel controller
Main
circuit
innter circuit
Power/switch output cable
(Red)+V
(White) OUT1
(Green)OUT2
(Yellow)OUT3
(Brown) OUT4
(Black) 0V
RS-232C communication cable
RS-485 communication cable
External
connection side
Host device with
RS-232C built-in
Host device with
RS-485 built-in
(Black)0V
(white)RXD
(Red) TXD
(White)A
(Pink)B
(Yellow)0V
8

Order Codes
●
Mounting
bracket
PSU-BR
●Parts for panel
mount
PM100
●Front protection
cover
KB100
●Mini clamp wire mount
plug
PSU-M
●Communication cable (1)
●Sensor controller
●USB-RS485 converter
●Termination resistance connector
Cable length
005RL : 50 mm [1.969 in.]
1RL : 1000 mm [39 in.]
3RL : 3000 mm [118 in.]
1RLN : 1000 mm [39 in.] one end has no connector (loose wires)
Cable included
Blank: USB (mini-B) ⇔USB (A), male
N : Cable not included
IBFL-K-TR
Cable included
(USB cable)
50 mm [1.969 in.]
Loose
wires
-1RL
-3RL
-1RLN -005RL
Cable(*2)
Blank: None
3L: 3000 mm [118 in.] power supply, switch cable (for no MSU communications)
5L: 5000 mm [197 in.] power supply, switch cable (for no MSU communications)
3LD: 3000 mm [118 in.] power supply, switch, communication cable (for MSU-232)
5LD: 5000 mm [197 in.] power supply, switch, communication cable (for MSU-232)
3LE: 3000 mm [118 in.] power supply, switch cable (for MSU-485) (*3)
5LE: 5000 mm [197 in.] power supply, switch cable (for MSU-485) (*3)
Front protection cover (*1)
Blank: None
C: With protective
front cover
Mounting parts
Blank: None
B: With mounting bracket
P: With panel mount parts
Output method
Blank: NPN output type
PNP: PNP output type (*5)
Communication specifications
Blank: No communication
232: RS232C communication
485: RS485 communication (*4)
●Pressure sensor head
Piping options
Blank: None
UR4: φ4 reducer
UR6: φ6 reducer
M5: M5 inline
Cable orientation
L: Vertical out
S: Horizontal out
Pressure range
EA : -101.3 to 0 kPa [-29.9 to 0 inHg]
ER : -100 to 220 kPa [-29.5 to 65.0 inHg]
EM: -100 to 1000 kPa [-29.5 to 295 inHg]
MSU - PH - - -
●Power supply/switching/communication cable
MSU -K -
IBFL - K - IBM2A - H1 -
*1) Protective front cover -C can be selected only if panel mount parts -P are
selected.
*2) 3L and 5L can be selected only if no communication is selected
3LD and 5LD can be selected only if -232 is selected
3LE and 5LE can be selected only if -485 is selected
*3) Communication cables are sold separately. Purchase by selecting
IBFL-K-□separately.
*4) When using RS485 communications, be sure to connect a termination
resistance connector.
*5) Only NPN type is UL compliant.
*When using RS485 communications, be sure to connect a termination resistance connector.
Cable type
3L: 3000 mm [118 in.] power supply, switch cable (for no MSU communications)
5L: 5000 mm [197 in.] power supply, switch cable (for no MSU communications)
3LD: 3000 mm [118 in.] power supply, switch, communication cable (for MSU-232)
5LD: 5000 mm [197 in.] power supply, switch, communication cable (for MSU-232)
3LE: 3000 mm [118 in.] power supply, switch cable (for MSU-485)
5LE: 5000 mm [197 in.] power supply, switch cable (for MSU-485)
3HE: 3000 mm [118 in.] sensor head extension cable
5HE: 5000 mm [197 in.] sensor head extension cable
MSU -----

Dimensions (mm [in.])
●MSU
MSU-232
No communication/RS-232C communication specication
●MSU-485
RS-485 communication specication
5 [0.197]30 [1.181]32 [1.260]
8.3 [0.327]27.6 [1.087]
2.65 [0.104]
Address setting (0 to F) Note 1 Sensor connector
RS-485 communication connector
Power, switch output connector
Power, switch output,
(RS-232C communication) connector
Sensor connector
M2.6 × 6 (Depth 6 [0.236])
40 [1.575]
40 [1.575]
MSU
kPa
mL/min
L/min
1 2 3 4
SW
CH
C
B
7
8
9
A
4
5
6
0
1
2
3
D
E
F
MSU
kPa
mL/min
L/min
1 2 3 4
SW
CH
OUT4
OUT3
OUT2
N.C.
N.C.
TXD
RXD
0V
OUT1
0V
+V
11
10
9
8
7
6
5
4
3
2
1
1ch
2ch
3ch
4ch
SENSOR
1 +V
IN
0V
ANLG
4
3
2
Enlarged diagram of wiring labels
* The label above shows the
MSU-232.
For the MSU (no
communications), 7 to 9 are
N.C.
* Only NPN type is UL
compliant.
Note 1: The diagram shows when the address is 0.
5 [0.197]30 [1.181]32 [1.260]
8.3 [0.327]27.6 [1.087]
2.65 [0.104]
Address setting (0 to F) Note 1 Sensor connector
RS-485 communication connector
Power, switch output connector
Power, switch output,
(RS-232C communication) connector
Sensor connector
M2.6 × 6 (Depth 6 [0.236])
40 [1.575]
40 [1.575]
MSU
kPa
mL/min
L/min
1 2 3 4
SW
CH
C
B
7
8
9
A
4
5
6
0
1
2
3
D
E
F
MSU
kPa
mL/min
L/min
1 2 3 4
SW
CH
Enlarged diagram of wiring labels
1ch
2ch
3ch
4ch
RS485
1
2
3
4
5
6
+V
0V
OUT1
OUT2
OUT3
OUT4
RS485
3
2
1B(-)
A(+)
0V
RS485
1 +V
IN
0V
ANLG
4
3
2
SENSOR
* Only NPN type is UL
compliant.
10

Dimensions (mm [in.])
●MSU-PH-EA-L
MSU-PH-ER-L
MSU-PH-EM-L
●MSU-PH-EA-□-UR□
MSU-PH-ER-□-UR□
MSU-PH-EM-□-UR□
●MSU-PH-EA-□-M5
MSU-PH-ER-□-M5
MSU-PH-EM-□-M5
●
Note: The sensor head MSU-PH-□-□comes with 2 mounting screws (M2×0.4, length 13 [0.512]).
Note: The sensor head MSU-PH-□-□comes with 2 mounting screws (M2×0.4, length 13 [0.512]).
19 [0.748] (for -UR6)
φ6 [0.236] (for -UR6)
(3000 [118])
φ2 [0.079] (pressure port)
12 [0.472]
5 [0.197]
10 [0.394]
20 [0.787]
4 [0.157]
11 [0.433]
(3000 [118])
Note) -UR4 can be connected to the φ4 [0.157] quick fitting and -UR6 to theφ6 [0.236] quick fitting.
* 16.5 [0.65] for -UR4
* φ4 [0.157] for -UR4
For -S
For -L
Cap
MADE IN JAPAN
KOGANEI
Cap color
-EA: Grey
-ER: Pink
-EM: Blue
(3000 [118])
11 [0.433]
8 [0.315]
9 [0.354]
5.5 [0.217]
4 [0.157]
4 [0.157]
6 [0.236]
4 [0.157]
20 [0.787]
2 [0.079] 6 [0.236]
10 [0.394]
(3000 [118])
For -S
For -L
MADE IN JAPAN
2-M3, depth 3 [0.118]
For mounting
2-M5, depth 4 [0.157]
Cap
KOGANEI
Cap color
-EA: Grey
-ER: Pink
-EM: Blue
(3000 [118])
Pin 1
5 [0.197]
14.9 [0.587]
15.6 [0.614]
12.4 [0.488]
5.9 [0.232]
4 3 2 1
(50 [1.969])
φ2.6 [0.102]
3.7 [0.146]
5 [0.197]
12 [0.472]
11 [0.433]
9.8 [0.386]
10 [0.394]
20 [0.787]
7 [0.276]
17 [0.669]
O-ring
(Detection port)
φ3 [0.118]
Cap color
-EA :Gray
-ER :Pink
-EM:Blue
1.5 [0.059]
2-φ2.1 [0.083]
6.4 [0.252]
Mini clamp wire
mounting plug
(Mounting hole)
1.5 [0.059]
7 [0.276]
17 [0.669]
(Detection port location)
2-φ3 [0.118] or smaller
3.5 [0.138] or more
10.5 [0.413]
4-M2×0.4 depth 3 [0.118] or more
(Mounting hole)
3.5 [0.138]
3.5 [0.138]
7 [0.276]
●Sensor head mounting dimensions
(For 2 pcs. mounting)
Surface roughness Ry6.3
7.4 [0.291]
(3000 [118])
5 [0.197]
12 [0.472]
11 [0.433]
9.8 [0.386]
10 [0.394]
20 [0.787]
7 [0.276]
17 [0.669]
6.4 [0.252]
Pin 1
5 [0.197]
14.9 [0.587]
15.6 [0.614]
12.4 [0.488]
5.9 [0.232]
O-ring
4 3 2 1
(50 [1.969])
φ2.6 [0.102]
φ3 [0.118] (Detection port)
1.5 [0.059]
1.5 [0.059]
2-φ2.1 [0.083]
(Mounting hole)
Mini clamp wire
mounting plug
Cap color
-EA :Gray
-ER :Pink
-EM:Blue

Dimensions (mm [in.])
(L)
Pin 1
5 [0.197]
14.9 [0.587]
15.6 [0.614]
12.4 [0.488]
5.9 [0.232]
4 3 2 1
(20 [0.787])
φ2.6 [0.102]
(20 [0.787])
1 2 3 4
13.5 [0.531]
23.4 [0.921]
13.4 [0.528]
15.8 [0.622]
10 [0.394]
6.4 [0.252]
Pin
1
Mini clamp wire
mount plug Mini clamp wire
mount socket
●MSU-K-□HE
2-φ4.5 [0.177]
9 [0.354]
11 [0.433]
4.5 [0.177]
16
[
0.630
]
2-φ
2.9 [0.114]
9.6 [0.378]
(7 [0.276])
24 [0.945]
7 [0.276]
30
[
1.181
]
4 [0.157]
38 [1.496]
12.6 [0.496]
1.6 [0.063]
11 [0.433]
●PSU-BR
Hexagon socket head screw
M 2.6 × 0.45 Length 5 [0.197], Two included
70 [2.756]
70 [2.756]
45 [1.772]+0.6 [0.024]
0
45 [1.772]+0.6 [0.024]
0
●Dimensions for drilling holes to mount the sensor controller
Note 1: Use a mounting panel thickness of 1 to 3.2 mm
[0.039 to 0.126 in.] mm.
2: For adjacent mounting, provide at least the amount
of spacing between holes as shown to the right.
3: DIN43700 standard.
Model L
MSU-K-3HE 3000 [118]
MSU-K-5HE 5000 [197]
29.8 [1.173]
9.5 [0.374](50 [1.969])
(L)
φ5.1 [0.201]
(6 wires)
Power/switch output cable
φ4.2 [0.165]
Serial communication cableNote
(3 wires)
7 [0.276]
●MSU-K-□L
MSU-K-□LD
Model L
MSU-K-3L 3000 [118]
MSU-K-5L 5000 [197]
MSU-K-3LD 3000 [118]
MSU-K-5LD 5000 [197]
●MSU-K-□LE
Model L
MSU-K-3LE 3000 [118]
MSU-K-5LE 5000 [197]
17.3 [0.681]
9.5 [0.374]
L
No. 1 terminal
●MSU-□-P (installation diagram for panel mount parts)
51.2 [2.016]
51.2 [2.016]
9.5 [0.374]
8 [0.315]
●KB100
33.2 [1.307]4 [0.157]
48 [1.890]
55.4 [2.181]
48 [1.890]
Parts for panel mount
PM100
1 2 3 4
SW
CH
L/min
mL/min
kPa
F
E
D
3
2
1
0
6
5
4
A
9
8
7
B
C
MSU
* The diagram shows the MSU-485.
12

Specifications
■Introduction to New Products (Separate Type Multi-Channel Flow Rate Sensor
Controller Series)
●Flow rate sensor head * Not UL/CE compliant.
Model
Item FS-R3 FS-R05 FS-10
Measurement target gas Air or nitrogen, however, the detected fluid must not contain any salt, sulfur, acid, or other corrosive elements. Also, air must be dry.
Clean gas that does not include any dust or mist (oil mist).
Flow rate measurement range -3 to +3ℓ/min [-0.106 to +0.106 ft3/min]
-500 to +500 mℓ/min [-0.018 to +0.018 ft
3
/min]
0 to +10ℓ/min [0 to +0.353 ft3/min]
Volumetric flow rate conversion value for 20°C [68°F] at 1 atm
Responsiveness 5 ms or lower (95% response to stepped flow rate change)
Output signal 1 to 5 VDC (non-linear characteristics); allowable load resistance: 10 kΩor greater
Operating temperature range 0 to 50°C [32 to 122°F] (Both ambient temperature and measured fluid temperature)
Storage temperature range -10 to 60°C [14 to 140°F]
Operating/storage humidity range
10 to 80% RH (no condensation)
Operating pressure range
-100 to +200 kPa [-29.5 to +59.1 inHg] (However, the guaranteed pressure characteristics range is -70 to +200 kPa [-20.678 to +59.1 inHg])
Proof pressure 300 kPa [88.6 inHg]
Output voltage accuracy ±5%FS MAX. ±5%FS MAX. ±5%FS MAX.
Standard flow rate
characteristics
0.0ℓ/min [0.000 ft3/min]: 3.00±0.15V 0.0ℓ/min [0.000 ft3/min]: 3.00±0.20V 0.0ℓ/min [0.000 ft3/min]: 1.00±0.20V
0.5ℓ/min [0.018 ft3/min]: 3.88±0.15V 0.1ℓ/min [0.004 ft3/min]: 3.77±0.20V 3.0ℓ/min [0.106 ft3/min]: 3.89±0.15V
1.5ℓ/min [0.053 ft3/min]: 4.49±0.15V 0.3ℓ/min [0.011 ft3/min]: 4.53±0.20V 5.0ℓ/min [0.177 ft3/min]: 4.46±0.15V
3.0ℓ/min [0.106 ft3/min]: 5.00±0.20V 0.5ℓ/min [0.018 ft3/min]: 5.00±0.20V 10.0ℓ/min [0.353 ft3/min]: 5.00±0.20V
Reproducibility ±3.5%FS MAX. ±2%FS MAX. ±6%FS MAX.
Same conditions apply to temperature and pressure during measurement.
Output characteristics ±0.01%FS/kPa ±0.01%FS/kPa
±0.01%FS/kPa (0 to +200 kPa [0 to +59.1 inHg])
In -70 to +200 kPa [-20.678 to +59.1 inHg] pressure range
±0.03%FS/kPa (-70 to 0 kPa [-20.678 to 0 inHg])
Temperature characteristics 0.0ℓ/min [0.000 ft3/min]: ±0.1%FS/°C 0.0ℓ/min [0.000 ft3/min]: ±0.1%FS/°C 0.0ℓ/min [0.000 ft3/min]: ±0.1%FS/°C
1.5ℓ/min [0.053 ft3/min]: ±0.15%FS/°C 0.3ℓ/min [0.011 ft3/min]: ±0.15%FS/°C 5.0ℓ/min [0.177 ft3/min]: ±0.2%FS/°C
Voltage 24 VDC (Supply from sensor controller)
Allowable voltage fluctuation range
In the 21.6 to 26.4 VDC range, ±2% FS or lower relative to an output value during 24 VDCNote 2
Output stabilization time Time required until output is within ±5% FS of maximum voltage attained (flow rate): Instantaneous
Time required until output is within ±1% FS of maximum voltage attained (flow rate): Within 10 seconds
Consumption current 12mA MAX.
Dielectric strength Between all external connector terminals and the body: 500 VAC for 1 minute, or 600 VAC for one second
Insulation resistance Between all external connector terminals and the body: 50 MΩ(500 VDC megger)
Connection type M5 female thread (brass insertion); tightening torque: 2.5 N·m [22.128 in·lbf] or less
Material Gas contact part: PPS resin (main flow path), ceramic (substrate) brass (contacts)
Cover: PC resin (polycarbonate)
Mounting direction Excluding directions where the cover is facing downwards.
Mounting criteria When using this device's mounting holes, use M3 screws, and tighten to a torque of 0.6 N·m [5.311 in·lbf] or less.
A filter that captures dust and mist with a particle size of 10 μm or greater can be installed on the upstream side of this device.
Straight piping length Not required for both upstream and downstream.
Vibration resistance 10 to 55 Hz; total amplitude: 1.5 mm [0.059 in]; each direction (XYZ) for two hours
Mass 9 g [0.317 oz]
Electric connection
(Special connector)
Cable with special connector
Flow rate sensor head side: J.S.T. Mfg. Co., Ltd. SM03B-SRSS-G-TB
Other side: J.S.T. SHR-03V-S-B (housing), SSH-003GA-P0.2 (contact)
Note 1: The % FS shown here assumes output voltage 4 V (1 to 5 V) full scale.
2: In the vicinity of the measurement range upper limit flow rate, output fluctuation of ±1% FS (drift volume 500 seconds from flow rate stabilization) at most is
generated following flow rate stabilization.

Flow rate sensor head [flow rate] - [output characteristics] charts
[Flow rate]-[Output] characteristics
0.0
0.5
1.0
1.5
2.0
2.5
3.0
3.5
4.0
4.5
5.0
−500 −400 −300 −200 −100 0 100 200 300 400
500
Flow rate mℓ/min (ANR)
Output (V)
[Flow rate]-[Output] characteristics
0.0
0.5
1.0
1.5
2.0
2.5
3.0
3.5
4.0
4.5
5.0
−3.0 −2.5 −2.0 −1.5 −1.0 −0.5 0.0 0.5 1.0 1.5 2.0 2.5
3.0
Flow rate ℓ/min (ANR)
Output (V)
[Flow rate]-[Output] characteristics
0.0
0.5
1.0
1.5
2.0
2.5
3.0
3.5
4.0
4.5
5.0
0.0 1.0 2.0 3.0 4.0 5.0 6.0 7.0 8.0 9.0
10.0
Output (V)
Flow rate ℓ/min (ANR)
●FS-R05 ●FS-R3 ●FS-10
1
ℓ
/min (ANR) = 0.035 ft3/min (SCFM)
10.5 [0.413]
32.5 [1.280]
17 [0.669]
5.3 [0.209]
5.25 [0.207] 5.25 [0.207]
5.3 [0.209]
5.7 [0.224]
11.2 [0.441] 10.2 [0.402]
2−M5×0.8 Inflow port
2-φ3.1 [0.122] mounting hole
CoverConnector connection por
t
Sensor head connector
12.4 [0.488]
15.6 [0.614]
14.9 [0.587]
5.9 [0.232]
5 [0.197]
Pin 1
2000±20 [79±0.787]
4 3 2 1
●FS-□
Dimensions (mm [in.])
Order Codes
Additional Parts (available separately)
Flow range
R05: -500 to 500 mℓ/min(ANR)
[-0.018 to 0.018 ft3/min(SCFM)]
R3: -3 to 3ℓ/min(ANR)
[-0.106 to 0.106 ft3/min(SCFM)]
10: 0 to 10ℓ/min(ANR)
[0 to 0.353 ft3/min(SCFM)]
Flow rate sensor
head
Flow rate sensor head
●FS
14

Limited Warranty
KOGANEI CORP. warrants its products to be free from defects
in material and workmanship subject to the following provisions.
The warranty period is 180 days from the date
of delivery.
If a defect in material or workmanship is found
during the warranty period, KOGANEI CORP.
will replace any part proved defective under
normal use free of charge and will provide the
service necessary to replace such a part.
This warranty is in lieu of all other warranties,
expressed or implied, and is limited to the
original cost of the product and shall not
include any transportation fee, the cost of
installation or any liability for direct, indirect
or consequential damage or delay resulting
from the defects.
KOGANEI CORP. shall in no way be liable or responsible for
injuries or damage to persons or property arising out of the
use or operation of the manufacturer’s product.
This warranty shall be void if the engineered safety devices
are removed, made inoperative or not periodically checked for
proper functioning.
Any operation beyond the rated capacity, any improper use or
application, or any improper installation of the product, or any
substitution upon it with parts not furnished or approved by
KOGANEI CORP., shall void this warranty.
This warranty covers only such items supplied by KOGANEI
CORP. The products of other manufacturers are covered only by
such warranties made by those original manufacturers, even
though such items may have been included as the components.
The specifications are subject to change without notice.
Warranty Period
Koganei
Responsibility
Limitations •
•
•
•
•
9/'19 AB
©KOGANEI CORP. PRINTED IN JAPAN
URL http://www.koganei.co.jp
E-mail: [email protected]
OVERSEAS DEPARTMENT
3-11-28, Midori-cho, Koganei City, Tokyo 184-8533, Japan
Tel: 81-42-383-7271 Fax: 81-42-383-7276
KOGANEI International America, Inc.
48860 Milmont Drive, Suite 108C Fremont, CA 94538, U.S.A
TEL: (+1)510-744-1626 FAX: (+1)510-744-1676
SHANGHAI KOGANEI INTERNATIONAL TRADING CORPORATION
RM2606-2607, Tongda Venture Building NO.1 Lane 600, Tianshan Road, Shanghai, China
TEL: (+86)021-6145-7313 FAX: (+86)021-6145-7323
TAIWAN KOGANEI TRADING CO., LTD
Rm.2,16F.,No88,Sec.2,zhongxiao E.Rd.,ZhongZheng Dist.,Taipei City10050,Taiwan(ROC)
TEL: (+886)02-2393-2717 FAX: (+886)02-2393-2719
KOGANEI KOREA CO., LTD
A-3001, Heungdeok IT Valley Bldg., Heungkeok 1-ro, 13, Giheung-gu, Yongin-si, Gyeonggi-do,
446-908, KOREA
TEL: (+82)31-246-0414 FAX: (+82)31-246-0415
KOGANEI(THAILAND) CO., LTD
555 Rasa TowerⅠ, Unit1207,1202, 12th floor, Phaholyothin Road, Chatuchak, Chatuchak,
Bangkok 10900 Thailand
TEL: (+66)02-513-1228 FAX: (+66)02-513-1232
KOGANEI ASIA PTE. LTD.
69 Ubi Road 1, #05-18 Oxley Bizhub Singapore 408731
TEL: (+65)6293-4512 FAX: (+65)6293-4513
URL http://www.koganei.co.jp
E-mail: [email protected]
This manual suits for next models
2
Table of contents
Other Koganei Controllers manuals
Popular Controllers manuals by other brands
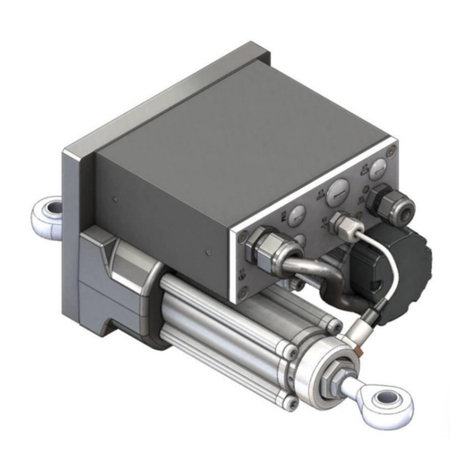
Maxcess
Maxcess Fife GMA-BL user manual
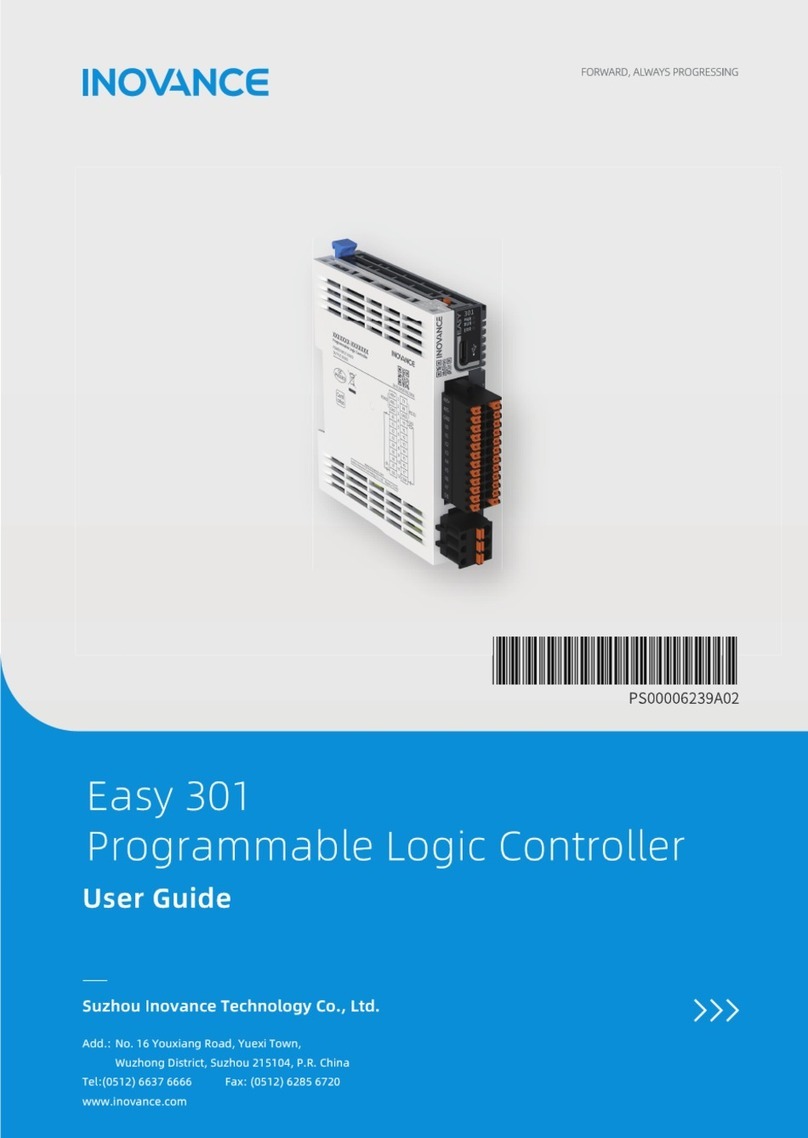
Inovance
Inovance Easy 301 user guide
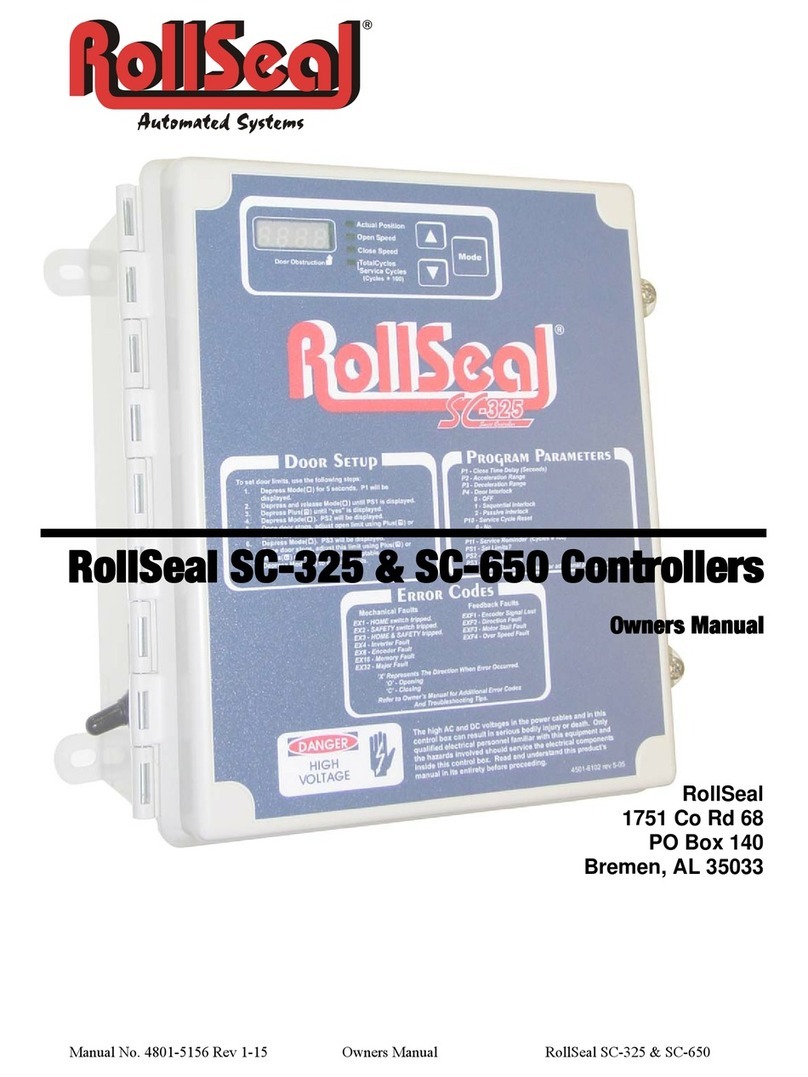
RollSeal
RollSeal SC-325-V01-0 owner's manual

pass & seymour
pass & seymour legrand LightSense PSWCR installation instructions

Mitsubishi Electric
Mitsubishi Electric FX3U-4DA installation manual
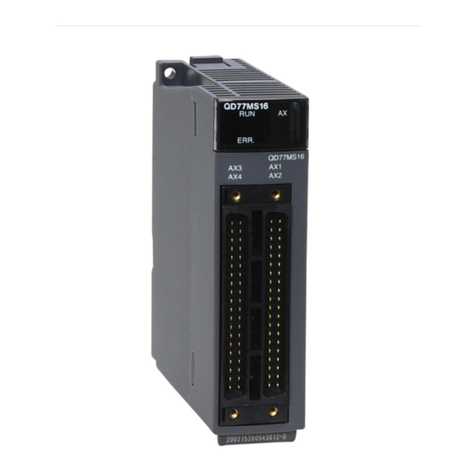
Mitsubishi Electric
Mitsubishi Electric MELSEC Q Series user manual
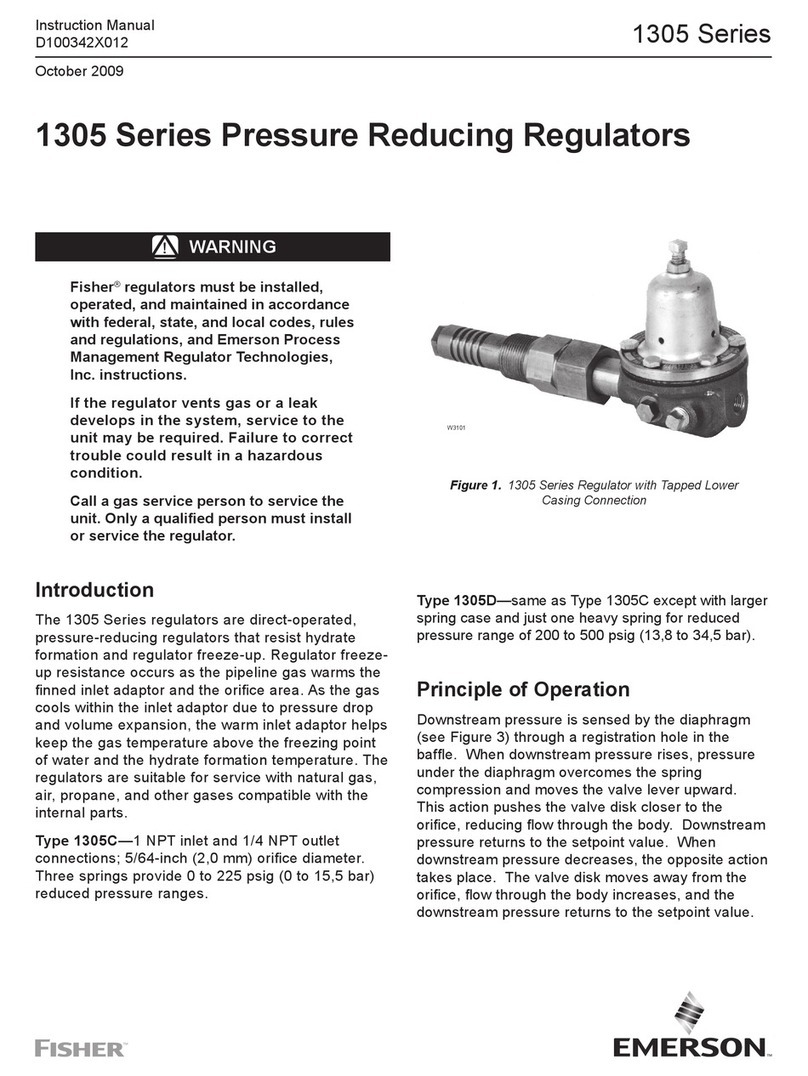
Emerson
Emerson Fisher 1305 Series instruction manual
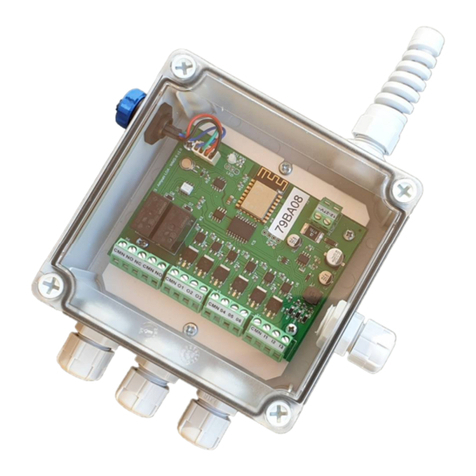
Amyuni Water Systems
Amyuni Water Systems WMS-6 Installation and user manual
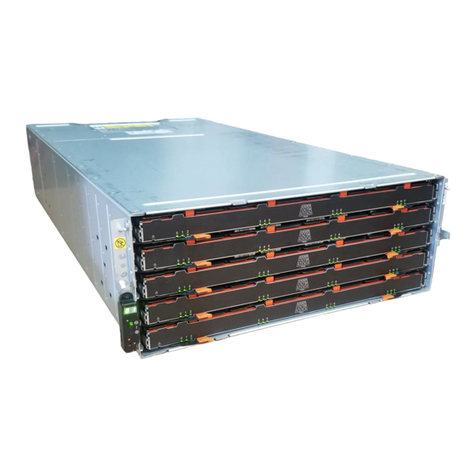
NetApp
NetApp E Series Replacing Guide

Black arrow
Black arrow Prospero X-3 Product user instruction manual
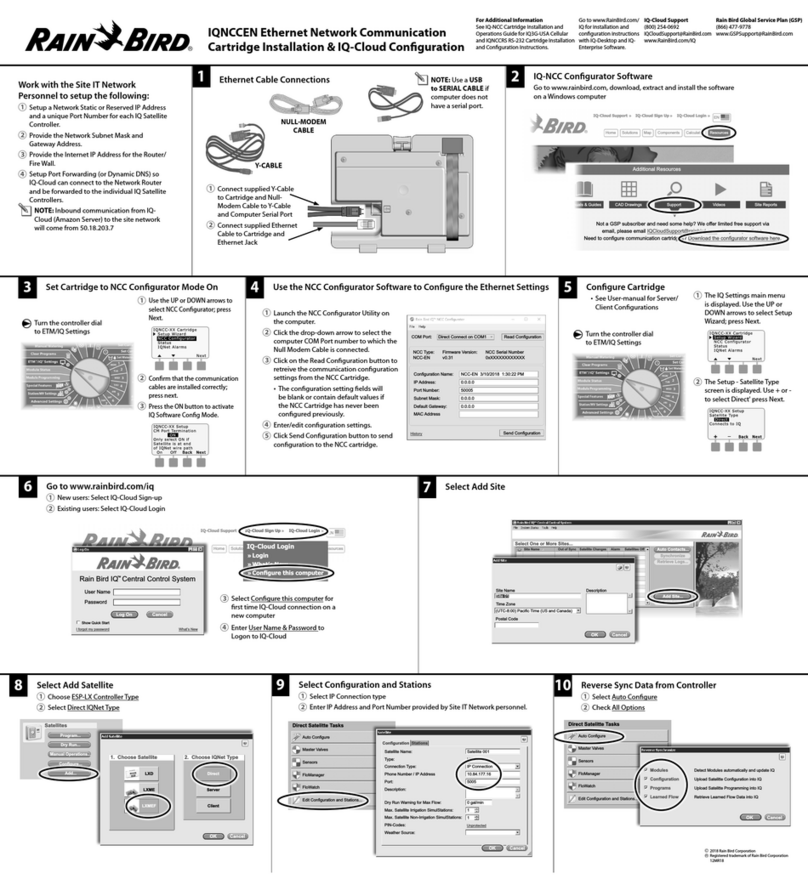
Rain Bird
Rain Bird IQNCCEN Installation/configuration
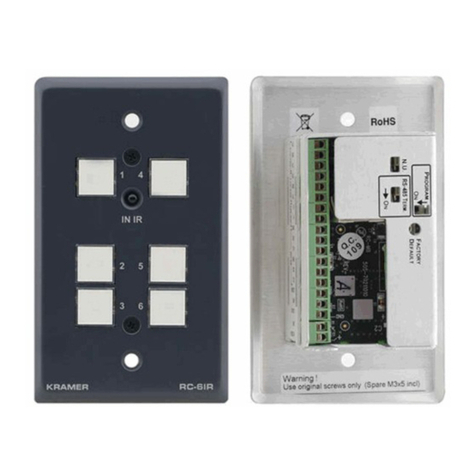
Kramer
Kramer RC-6IR user manual