koino K30 Series User manual

1*%5&.1 $0/530--&3
,4&3*&4
,4&3*&4
1" 3 5

74
MICRO COMPUTER
Digital PID Controller
User' s Manual
K30-SERIES
PID CONTROLLER

75
Preface
Pay attention to the followings!
Safety requirements!
WARNING
CAUTION
Thank you for purchasing the K30 series from Koino.
The K30 series is a precision industrial controller that uses an advanced
2 degree-of-freedom (DOF) algorithm.
The K30 series consists of 5 models, which are K32, K33, K34, K37, and K39.
This manual explains the installation, the functions, the operation,
and the handling of the products.
Please read the manual thoroughly before using the products.
If any difficulties arise while using our products, please call our customer service
at +82-2-2242-1275.
Use the products under the conditions specified in this manual.
Please heed the cautions and warnings listed in this manual.
The contents of the manual may be changed without notice.
The product is designed to be used installed on a control panel.
This manual is copyrighted, and may not be copied in part or in whole without
permission.
The manufacturer takes no responsibility for direct or indirect damages caused by
careless operation or operation under unpredictable or risky environments
Safety requirements are intended to prevent accidents and dangers through the proper use of the products, so
please heed them at all times.
The safety requirements are divided into “cautions” and “warnings”, which indicate the following.
△
!
△
!
Serious injury or death may be caused if instructions are not observed.
Failure to observe these instructions may cause damage to the instrument or some injury to the user.
PID CONTROLLER

76
WARNING
△
!
CAUTION
△
!
1. Use a separate safety device when this product is used to control a device
that could harm lives or expensive property in the event of a malfunction
or a breakdown. (This may cause fires, deaths, or damage to property)
2. Do not use this controller at place where there are flammable or
explosive gas. (It may cause a fire or explosion.)
3. Before turning the power on, please check that wiring is correct to the
number of terminal. (It may cause a fire)
4. Turn off the power during wiring and maintenance to avoid an electric shock.
5. Do not touch the terminals when it is power on.
(It may give an electric shock.)
6. This controller must be mounted on the panel to avoid an electric shock.
7. Do not attempt to disassemble, modify and repair.
1. Please conduct an inspection when water has entered the product.
(It may cause short circuits, fires, and malfunction.)
2. This controller should be used indoors.
(It may shorten the controller’s life or give an electric shock.)
3. Observe the rated voltage and specification.
(It may cause a fire or shorten the controller’s life.)
4. Be careful that any of foreign materials do not inflow into the controller.
(It may cause a fire or malfunction of the controller.)
5. Do not give direct vibration or shock to the controller.
(It may cause of malfunction of the controller.)
6. Do not use chemical detergent or solvent, but use a dry towel in cleaning the controller.
(It may cause an electric shock or a fire.)
7. Please check the polarity of power before wiring and connecting the sensor.
(It may cause an electric shock or explosion.)
PID CONTROLLER

77
Contents
1. Ordering Information
2. Input ranges & Output constitutions
3. Dimensions & Panel cutouts
4. Terminal Arrangements & wirings
5. Ratings & Specifications
6. Name & Function
7. Check points before using
8. Initial installation & Min. operation procedures
9. Flow chart (Parameter structure)
10. Setting mode
11. Alarm(ALARM1, 2) setting
12. Details explanation of primary function
12-1. Auto tuning(AT) function
12-2. Manipulated variable(Mvn) check mode
12-3. Alarm(ALARM1, 2) function
12-4. Retransmission output
12-5. Input function
12-6. SV1, 2 set up control by external contact signal
12-7. Set value “LOCK” function
78
80
82
85
87
88
89
90
91
92
94
96
96
96
97
98
98
99
99
PID CONTROLLER

78
K3 -
①Size
②Control mode
③Optional function
④Power supply voltage
④Power supply voltage
①Size
Code Model Size Remarks
2 K32-SERIES 48(W) × 96(H) × 77(D) No option (Basic function)
3 K33-SERIES 96(W) × 48(H) ×77(D) No option (Basic function)
4 K34-SERIES 48(W) × 48(H) ×99(D) Option : 0, 1, 2, 3
7 K37-SERIES 72(W) × 72(H) ×77(D) Option : 0, 3
9 K39-SERIES 96(W) × 96(H) × 77(D) No option (Basic function)
②Control mode
Code Description Remarks
S SINGLE : Standard Heating or Cooling control
Code Description Remarks
0 100 ~ 240 V AC General-purpose usage
1 24 V AC or DC Alternating or Direct current usage
PID CONTROLLER
1. Ordering Information

79
③Optional function
Model Code Description Remarks
K32, K33
SERIES
Basic function
(0)
RELAY output 1, Alarm output 2,
No function
(Basic function S0x)
SCR(4~20mA), SSR(Voltage pulse) 1,
RET(4~20mA Retransmission output)
D.I(SV2, 3) External input
K34
SERIES
Basic function
(0)
RELAY output 1 (ALARM or MAIN), Basic function +
Option code
(0 : No option)
SCR(4~20mA), SSR(Voltage pulse) 1
1 RET(4~20mA Retransmission), Alarm 2 Ex) K34-S10
3 D.I(SV2, 3) External input, Alarm output 2 Ex) K34-S30
K37
SERIES
Basic function
(0)
RELAY output 1, Alarm output 2, Basic function +
Option code
(0 : No option)
SCR(4~20mA), SSR(Voltage pulse) 1
3 D.I(SV2, 3), RET(4~20mA Retransmission) Ex) K37-S30
K39
SERIES
Basic function
(0)
RELAY output 1, Alarm output 2, Basic function +
Option code
(0 : No option)
SCR(4~20mA), SSR(Voltage pulse) 1,
RET(4~20mA Retransmission)
Example of model building
K34-S00
①Size : 48(W)×48(H)×99(D) ☞“4”
②Control mode : SINGLE ☞“S”
③Optional function : Basic function ☞“0”
④Supply voltage : 100~240V AC ☞“0”
K37-S30
①Size : 72(W) ×72(H) ×77(D) ☞“7”
②Control mode : SINGLE ☞“S”
③Optional function : DI(SV1,2), RET ☞“3”
④Supply voltage : 100~240V AC ☞“0”
K34-S00
K37-S30
PID CONTROLLER

80
2. Input ranges and output constitutions
2-1. Input ranges ※The K30 series has multiple inputs, which may be set and changed by the user.
Input type Signal Setting
Code Temperature range Accuracy Remarks
Thermocouple
(T.C)
K1 -200 ~ 1370
±0.3% of F.S +1Digit
* F.S is max. value to min. value
of each range
* Digit is minimum of display
①0~400℃range : ±10% of
F.S+1Digit
2 -199.9 ~ 999.9
J15 -200 ~ 1000
3 -199.9 ~ 999.9
E16 -200 ~ 1000
4 199.9 ~ 999.9
T 5 -199.9 ~ 400.0
R 6 0 ~ 1700
B ①7 0 ~ 1800
S 8 0 ~ 1700
L17 -200 ~ 900
9 -199.9 ~ 900.0
N 10 -200 ~ 1300
U 11 -199.9 ~ 400.0
C (W5) 12 0 ~ 2300
D (W3) 13 0 ~ 2400
RTD
JPt100
(JIS,KS)
20 -199.9 ~ 500.0
22 -200 ~ 500
Pt100
(DIN,IEC)
21 -199.9 ~ 640.0
23 -200 ~ 640
Voltage
(VDC/mVDC)
0~100 mV DC 33 0 ~ 100mV DC
-10~20 mV DC 32 -10 ~ 20 mV DC
1~5V DC 30 1~5V DC
Current 4~20mA DC 30
When using current input, use
the resistor 250on input
terminal.
How to change the interior switch when using 1~5V input
①Remove the jumper cover
on the underside of the K30,
or remove the rear case.
②Detach the jumper using
tweezers and move it to the
1-2 pins to the left.
③Once this has been com-
pleted, put the jumper
cover back on, as shown
on the picture above.
※When using 1~5V input (30),
the interior jumper switch must be
relocated.
OTHER TYPES 1~5V DC INPUT ONLY
PID CONTROLLER

81
2-2. Output constitutions
The K30 series
has multiple outputs.
※The figure on the left uses the
terminal
socket of K37-S30 as an example
to illustrate the output response
relationship.
General type Setting
number
OUTPUT-1 OUTPUT-2 (ALARM1,2)
Relay output SSR/SCR OUTPUT AL1 AL2 SCR output
SSR output SCR output
K30-Sxx
0 OUT(ON/OFF) ALM1(34-S0x) -
ALARM1 ALARM2 RET
1 ALM1(34-S0x) OUT(PID) -
2 ALM1(34-S0x) - OUT(PID)
3 OUT(PID) ALM1(34-S0x) -
Summary and explanation of output settings
Relay output of ON/OFF control [ Output setting number : 0 ]
This is a simple on/off control, mainly used to control cooling devices.
SSR output of PID control (Voltage pulse) [ Output setting number : 1 ]
This is the most widely used setting, and the default value at the point of manufacture.
SCR output of PID control (4~20mA current output) [ Output setting number : 2 ]
This setting is used mainly with thyristor power regulator (TPR) modules, and is capable of
precision control.
Relay output of PID control [ Output setting number : 3 ]
This is the most cost-efficient method of implementing PID control and is used mainly with
magnetic switches (electric switches). However, it may wear the contact point, and is
difficult to use in places that require fast response.
Alarm output of K34(48´48) basic type(S00)
With the basic model of K34 (48x48), caution is required when using it alarm output. When control output is being used as a relay, the
alarm output will be SSR output (voltage pulse). In this case, use SSR or alarm option (S10, S30) enabled models.
1(SSR) or 2(SCR) 0(ON/OFF) or 3(RELAY)
ALARM1
output
ALARM1
output
Control output Control output
※It is only for K34-S00!
PID CONTROLLER

82
1) K32 (48×96 mm) Dimensions
45±0.5
92±0.5
Min. 20
Min. 30
K32 / K33 (48×96)
Panel cutouts
(Unit : mm)
2) K33 (96 ×48 mm) Dimensions
3) K34 (48×48 mm) Dimensions
(Unit : mm)
45-0
+0.5
45-0
+0.5
Min. 17
Min. 17
K34 (48×48) Panel cutouts
3. Dimensions and panel cutouts
PID CONTROLLER

83
4) K37 (72×72 mm) Dimensions
5) K39 (96×96 mm) Dimensions
(Unit : mm)
(Unit : mm)
68 ±0.5
68 ±0.5
Min. 20
Min. 30
K37 (72×72) Panel cutouts
K39 (96×96) Panel cutouts
92±0.5
92±0.5
Min. 20
Min. 30
PID CONTROLLER

84
Installation
K34-SERIES
K32 / K33 / K37 / K39-SERIES
①Bore a hole in the panel, referring to the panel cutouts on the previous page.
②Insert this device into the front of the panel.
③From the rear of controller, slide the bracket over the housing.
④Push the bracket in until the device has been fixed securely onto the panel.
⑤Secure using screws on the two locations at top and bottom as shown on Figure 2.
①Bore a hole in the panel, referring to the panel cutouts on the previous page.
②Insert this device into the front of the panel.
③Insert 2 brackets, one each on the B/K holes on the top and the bottom of the device.
④Secure using screws on the two locations at top and bottom.
[Picture 1]
[Picture 1] Top side [Picture 2] Bottom side [Picture 3] Fixing completion
[Picture 2]
Turn the screw 3-4
times after contact
with panel.
Turn the screw 2-3
times after contact
with panel.
Hole of fixing screw Hole of fixing screw
B/K hole B/K hole
Direction
Fixing screw
PID CONTROLLER

85
4. Terminal arrangements and wirings
K32
K33
1) K32 (48×96 mm), K33 (96×48 mm)
2) K34 (48×48mm)
K3
2
K33
Basic type
(K32-S0x)
(K33-S0x)
OPTION (Basic type)
OPTION
Option 1
(K34-S1x)
Option 3
(K34-S3x)
PID CONTROLLER

86
3) K37 (72×72 mm)
4) K39 (96×96 mm)
OPTION
Terminal explanation (K39-S00)
Terminal (1)-(2)-(3) : OUT1 only for output
selection no. 0, 3 (Relay output) mode.
Terminal (4)-(5) : OUT2 only for output.
selection no. 1, 2 (SSR, SCR output) mode.
Terminal (6)-(7) : RET(Retransmission 4~20mA)
or for power of sensor SPS. (DC 15V)
Terminal (8)-(9) : Power supply terminal.
Terminal (11)-(12) : Alarm1 output terminal.
Terminal (13)-(14) : Alarm2 output terminal.
Terminal (15)-(16)-(17) : The external D.I input
terminal may be used when (DIS=ON), and the
target value may be controlled. (SV1, SV2, SV3)
Terminal (18)-(19)-(20) : Input terminals.
Option 3
(K37-S3x)
PID CONTROLLER

87
5. Ratings and specifications
Model K30-SERIES
Power supply 100~240V AC 50~60Hz (Operating voltage range 85~265V AC)
24V AC or DC (Operating voltage range 20~28V DC)
Power consumption 6VA (Max.)
Sensor input
Thermocouple (TC) : K, J, T, E, R, B, S, L, N, U, C(W5), D(W3)
Resistance temp. detector (RTD) : KPt100(KS), JPt100(JIS), Pt100(DIN)
Current input : 4~20mA DC
Voltage input : 1~5V DC, -10~20mV DC, 0~100mV DC
Accuracy ±0.3% of FS +1Digit
Input impedance
Current input (250), Voltage input (including TC) 1Mmin.
(RTD allowable wiring resistance :
10max., but, 3 wires have a equal resistance)
Input sampling period 250ms (changeable according to SG-PID algorithm)
Control output
Relay 1c 250VAC, 3A(resistive load) Electrical life 100,000 min.
(PID output or ON/OFF output)
Voltage (S.S.R) DC15V 25mA (Built-in short protection circuit)
Voltage pulse (PID output)
Current (S.C.R) 4~20mA DC, allowable load impedance 600max. (PID output)
Control type Super 2 degree-of-freedom PID (SG-PID algorithm),
S-Fuzzy, Auto-Tuning
Digital Input ON : 1Kmax., OFF : 100Kmin. (SV1, 2, 3 external control input)
Retransmission output 4~20mA DC, allowable load impedance 600or less.
Resolution 1/4600 PV, SV, MV[%], SPS
Alarm ALARM1, 2 1a 250V AC 3A (Resistive load)
HBA(C.T) com. HBA : 1~50AAC (Resolution 0.5A)
Ambient temperature
and humidity
-10~50℃/ 25~85% RH
(with no condensation or icing)
Weight
(incl. B/K & accessories)
K32, K33, K37-SERIES : 230g K34 : 140g K39 : 320g
※When option + 30g
PID CONTROLLER

88
6. Name & Function (ex. K34-SERIES )
①Process value (PV)
Display (Red color)
③Set value (SV)
Display (green color)
⑩Set value Up key
⑨Set value Down key
⑧Shift key
⑦Storage & function key
④Control output lamp
⑤SV-2 display lamp
⑥Alarm output lamp
②Auto tuning (AT) lamp
◈Description
Name Function
①Process value Display the process value. (red color)
②Auto tuning lamp Flash every 0.5 second during auto tuning.
③Set value display Display the set value, codes, and modes.
④Control output lamp Lights when the control output is ON.
⑤SV-2 display lamp Lights when the SV 2 is displayed.
⑥Alarm output lamp Lights during the alarm is ON.
⑦Function key Use to move the menus, to store, and to operate.
⑧Shift key Use to shift the digits.
⑨Set value down key Use to decrease set value and to move the menu.
⑩Set value up key Use to increase set value and to move the menu.
SET
PID CONTROLLER

89
7. Check Points before Using
1) Default values at the point of manufacture
2) 7 Segment display indications
The default input and output values of the product at the point of manufacture are as follows.
Input : K-Type (Sel. code 1) Output : SSR mode (Sel. code 1)
※In the case of the basic model of K34-S00 only, when SSR(1) or SCR(2) is chosen as the
output mode, Alarm 1 output will be in main relay. (Refer to page 8 for details)
3) Initial display on power supply (K34-SERIES basis)
Model Name
Option indication
Output type indication
Input type indication
Firmware version display
0 : Basic type (No option)
1 : RET, ALARM1, 2
3 : DI(SV1, 2), ALARM1, 2
0 : RELAY ON/OFF control
1 : SSR (VOLT-PULSE) PID control
2 : SCR (4~20mA) PID control
3 : RELAY PID control
01 : K-Type (-200~1370 ℃)
02 : K-Type (-199.9~999.9 ℃)
33 : mV DC (0~100mV)
PID CONTROLLER

90
The following are the instructions for initial installation and minimum operation procedures.
Please read the contents of this manual, including the general functions outlined here, as thoroughly as possible before operating the
device.
1)Check the external wiring diagram and specifications
(power supply and terminal arrangement)
2)Check input and output specifications!
The default setting for the K30 series at the point of manufacturer are as follows.
Input : K(CA) Type (setting code 1)
Output : SSR mode (setting code 1)
If you wish to change the input or the output type, please select the option
you desire on the input group and the output group menus.
※The input type settings must be configured first before changes to other set values are made.
When the input type is changed, all other parameters (set values) are reverted to their
factory default.
3)Select the desired set value (SV).
4)Please set auto-tuning or P, I, D values to suit the operating environment.
Auto-tuning is recommended except under special circumstances
Set value(SV) setting [ in condition of Mvn = OFF (basic) ]
①Enter to setting mode by key
②Set a desired value by key
③Store a value by key
SET
SET
Auto tuning
AT command lamp (flash every 0.5sec.)
SET
AT operation start:+ 0.5 second
SET
AT stop by perforce:+ 0.5 second
Tuning is required before operating for the first time. Set the target value(SV) in the range mainly used and run auto-tuning. When auto-
tuning begins, the “auto-tuning command lamp” will flash every 0.5 second and will turn off upon completion of the tuning process. Please
refrain from operating the keys while auto-tuning is in progress.
8. Initial installation and minimum operation procedures
PID CONTROLLER

91
9. Flow Chart (Parameter structure)
AUTO TUNING..
If the device is left idle for approximately
50 seconds after entering a setting menu
other than the basic drive menu,
it will return automatically to
the basic drive menu.
0.5 sec.
〈Basic drive menu〉( IOSE = ON )
3 sec.
3 sec.
3 sec.
3 sec. 3 sec.
3 sec.
3 sec.
3 sec.
press more than 3 sec.
within 4 sec. shortly
after power on.
〈In/Out set mode〉
Input type selection
Input type selection
The full menu diagram above
shows all control and setting
menus
on the K30 series,
But during actual
operations the menus that are
the most
relevant to the situation
according to the options and
the drive mode, providing a
simpler user interface while
retaining
functionality.
〈
General set mode〉〈
Initial set
〉
ON
Set value1 (SV1) Enable of
In/out setting
Highest limit
Lowest limit
Input digital filter
Input correction
Decimal point positioning (On voltage input)
Set highest scale (On voltage input)
Type of alarm 1
Type of alarm 2
Hysteresis of alarm 1
Hysteresis of alarm 2
Delay time of alarm 1
Delay time of alarm 2
Retransmission type
or SPS selection
Set of menu lock
External contact input
ON/OFF switch
Set lowest scale (On voltage input)
Output action selection (Reverse/Direct action)
REV. (Heating), DIR. (Cooling)
Input unit
( Fixed ℃)
Set value2 (SV2)
Set value of alarm 1
Set value of alarm 2
Select of (SV1 or 2) number
Proportional band (℃)
Integral time (sec.)
Differential time (sec.)
Control loop break alarm
Highest limit
of retransmission
Lowest limit
of retransmission
Hysteresis
(ON/OFF Control)
Manual reset [%]
(Integral time OFF only)
Cycle time of output
(SSR or Relay)
※in/output setting mistake
prevention system
〈Process of “in/output set mode”〉
Method 1.
Method 2.
Press more than 3 seconds within 4 seconds shortly after power on.
※To enter “Input/Output settings” by “IOSE” On is valid for only one time. If you want to enter “Input/Output settings”
again you must turn on “IOSE” first. If there is no Key action the “IOSE” will be OFF automatically in 40 seconds.
PID CONTROLLER

92
10. Setting mode
1) General setting mode
The general setting mode is for changing environment parameters on ad hoc basis and also for tuning performance enhancement and
configuring other functionalities.
Display Description Setting range Condition Initial value
Display general setting mode
Set value 1 (SV1) setting EU (0 ~ 100 %) D.I Option
in use EU (0 %)
Set value 2 (SV2) setting EU (0 ~ 100 %) D.I Option
in use EU (0 %)
Set value of alarm 1 (AL1) EU (0 ~ 100 %) Use Alarm 1 EU (100 %)
Set value of alarm 2 (AL2) EU (0 ~ 100 %) Use Alarm 2 EU (0 %)
Selection of (SV1, 2) number 1 / 2 Always 1
SV1, 2 proportional band (P) 0 ~ 999.9 ℃PID control 20.0 ℃
SV1,2 Integral time (I) OFF / 1 ~ 6000 sec. PID control 240 sec.
SV1,2 Differential time (D) OFF / 1 ~ 6000 sec. PID control 60 sec.
SV1,2 Manual reset (MR) -5.0 ~ 105.0 % Integral time
OFF 50.0 %
Cycle Time (P.I.D Control Only) 1 ~ 1000 sec. PID control
(SSR or RELAY) 2 sec.
Hysteresis (ON/OFF control) EUS (0 ~ 100 %) ON/OFF
control EUS (0.5 %)
Control loop break alarm (LBA) OFF / 1 ~ 9999 sec. ALARM1
No. 21 selection 480 sec.
Highest limit of retransmission
(RET.H) TC/RTD : _IN.H~_IN.L
DCV IN : _SL.H~_SL.L
( But, RET.H > RET.L )
Use
retransmission and select PV
or SV
EU (100 %)
lowest limit of retransmission
(RET.L) EU (0 %)
※EU : An engineering unit in compliance with the input range
ex) Input selection no. : 01 (K-TYPE)
EU 0 % = -200
EU 100 % = 1370
EUS 0 % = 0
EUS 100 % = 1570
INPUT
INPUT
EU
EUS
-200
-200
(200)
0
0
(0)
0
0
1370 [℃]
1370 [℃]
(1570)
100%
100%
PID CONTROLLER
This manual suits for next models
5
Table of contents
Other koino Controllers manuals
Popular Controllers manuals by other brands
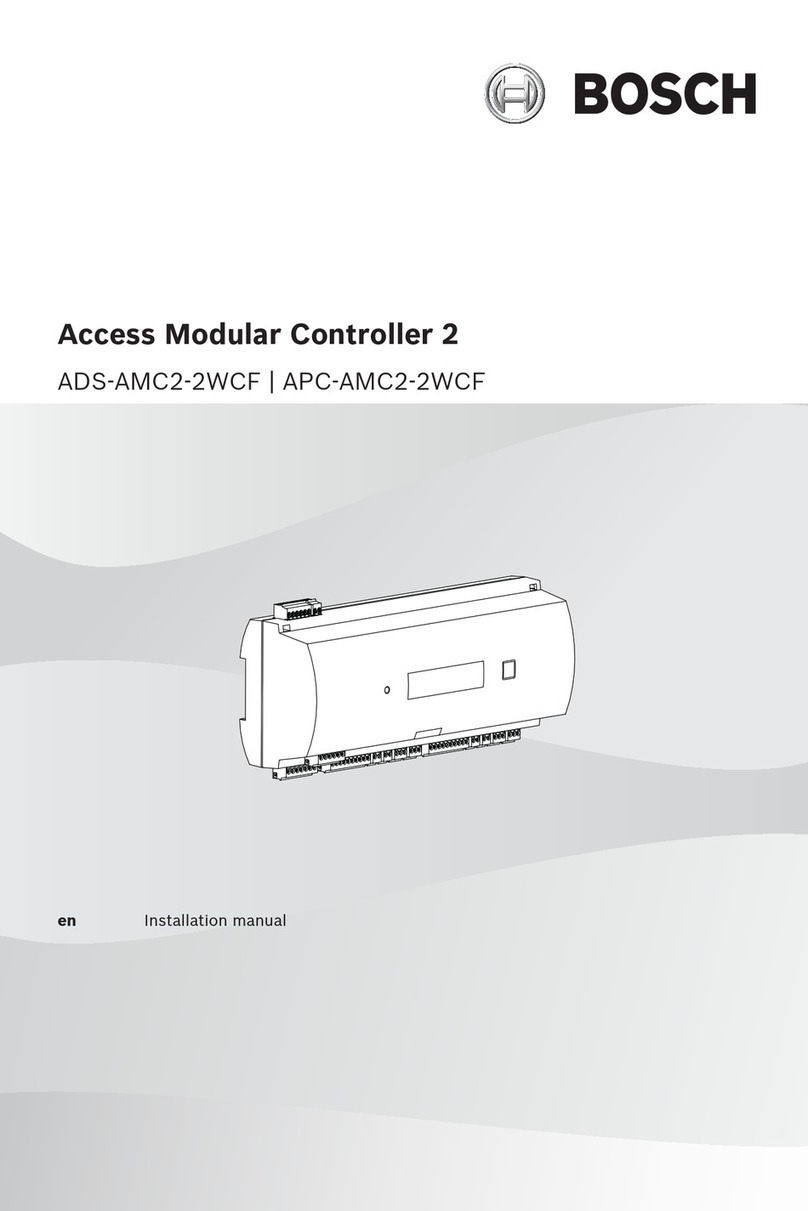
Bosch
Bosch ADS?AMC2?2WCF installation manual
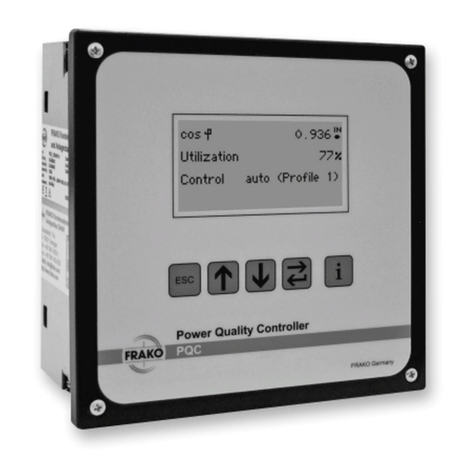
frako
frako PQC operating manual

Energy Master
Energy Master HHPM SERIES Installation, Operation, Maintenance, Service Manuals
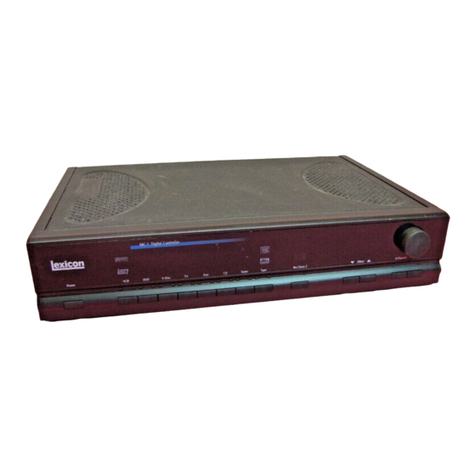
Lexicon
Lexicon MC-1 owner's manual

Oilon
Oilon VSi 6-14 Installation and operation manual
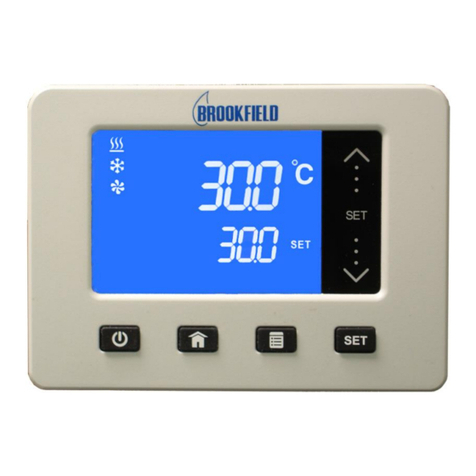
Ametek
Ametek BrookField TC Series Operator's manual