Label ETERNA 150 Series User manual

INSTALLATION MANUAL
ETERNA 150 - EN - Rel.2.3 - 12/2020 - CD0715EN
TRANSLATION OF THE ORIGINAL INSTRUCTIONS
ETERNA 150
Automation for
automatic sliding doors
EN

CONTENTS:
GENERAL SAFETY WARNINGS 4
GENERAL SAFETY OBLIGATIONS 4
1) DESCRIPTION OF THE MODELS 5
MECHANICAL COMPONENTS OF THE SLIDING DOOR AUTOMATION
2) TECHNICAL SPECIFICATIONS OF THE ETERNA 150 AUTOMATION 5
3) ETERNA 150 AUTOMATION COMPONENTS 6
4) TECHNICAL DRAWINGS 7
5) COVER 9
6) BELT TIGHTENING ADJUSTMENT 10
7) POSITIONING THE MECHANICAL LIMIT DEVICE 10
8) ANCHORING THE LEAVES TO THE TROLLEYS AND ADJUSTING THEM 11
9) INSTALLATION DIMENSIONS 12
10) ELECTRIC LOCKS 14
10.1) GENERAL DESCRIPTION 14
10.2) POSITIONING AND ELECTRIC CONNECTION 14
10.3) MANUAL RELEASE 15
10.4) INSTALLATION OF THE MANUAL RELEASE ON THE WALL 19
10.5) INSTALLATION OF THE MANUAL RELEASE OVER THE TRANSOM 20

ELECTRONICS
11) ELECTRIC ARRANGEMENTS 22
12) ELECTRIC CONNECTIONS 23
13) DIGITAL SELECTOR ET‑DSEL – PURPOSE AND CONNECTIONS 27
14) COMMISSIONING OF THE AUTOMATION (INITIAL SETUP) 28
14.1) FIRST START OF THE DIGITAL SELECTOR ET‑DSEL 28
14.2) SERIAL COMMUNICATION SETTINGS 28
14.3) INITIAL SETUP 29
14.4) FUNCTIONAL TESTING 31
14.5) INPUT DIAGNOSTICS 31
15) BATTERY‑POWERED EMERGENCY OPENING DEVICE ET‑BAT150 32
15.1) BATTERY‑POWERED EMERGENCY OPENING DEVICE ET‑BAT150P 33
16) SWITCHING TO STAND‑BY MODE 34
17) SAFETY SENSORS 35
17.1) SENSOR OA‑AXIS T / OA‑FLEX T 35
17.2) SENSOR OAM‑DUAL TE 35
17.3) SENSOR OA‑PRESENCE T 36
18) PROGRAM SELECTORS 37
18.1) MECHANICAL KEY SELECTOR EV‑MSEL 37
18.2) DIGITAL SELECTOR ET‑DSEL – USED AS PROGRAM SELECTOR 38
19) GENERAL PROGRAMMING MENU 40
20) FUNCTIONS AND SETTINGS 41
20.1) FUNCTIONS SETTING 41
20.2) PARAMETER SETTING 41
21) LANGUAGE 48
22) PASSWORD MANAGEMENT 48
22.1) HOW TO CHANGE THE TECHNICAL PASSWORD 49
22.2) HOW TO CHANGE THE PRIMARY PASSWORD 49
22.3) HOW TO CHANGE THE SERVICE PASSWORD 50
22.4) ENABLING USER PASSWORD USAGE (PRIMARY AND SERVICE) 51
22.5) DISABLING USER PASSWORD USAGE 51
23) SELECTOR OPTIONS 52
24) INFORMATION AND EVENT MEMORY 53
25) MAINTENANCE 56
25.1) PLUG AND PLAY 56
26) MODULE “UR24” 57
27) GONG FUNCTION 58
28) RADIORECEIVER EN/RF1 59
29) FORCED CLOSING FUNCTION 60
30) INTERLOCK SYSTEM 61
30.1) ELECTRICAL CONNECTION FOR INTERLOCK 61
30.2) INTERLOCK APPLICATION WITH INDEPENDENT INTERNAL DETECTORS 62
30.3) INTERLOCK APPLICATION WITH A SINGLE INTERNAL DETECTOR 62
31) SPECIAL FUNCTIONS WITH DUAL ELECTRIC LOCK 63
31.1) PHARMACY FUNCTION 63
31.2) ANTI‑ROLL FUNCTION FOR BOATS 63
32) PRIVACY FUNCTION 64
32.1) ELECTRIC CONNECTIONS 64
32.2) OPERATION OF THE PRIVACY SYSTEM 65
32.3) SETTINGS 65
33) MEANING OF BUZZER WARNING SIGNALS 66
34) MAINTENANCE PROGRAM 66
DECLARATION OF INCORPORATION OF PARTLY ASSEMBLED MACHINERY 67

4
GENERAL SAFETY WARNINGS
Carefully read this instruction manual for the safe installation and operation of the automatic door.
Improper installation and incorrect use of the product could cause serious injury.
Keep the instruction manual for future reference.
The installer must provide all the information about operation and provide the system user with the user manual delivered with the
product.
MEANING OF THE SYMBOLS USED IN THESE INSTRUCTIONS
DANGER:
Notication of dangerous situations that could cause material damage and personal injury.
WARNING:
Identies the procedures that must be understood and followed mandatorily in order to avoid damage to the product or
malfunctions.
NOTE:
Highlights important information.
GENERAL SAFETY OBLIGATIONS
The mechanical and electric installation must be performed by specialised personnel in accordance with the applicable
directives and regulations.
The installer must make sure that the structure to be automated is stable and robust and, if necessary, make structural
modications to make it so.
Keep product and packaging materials out of children's reach, as they might be a source of danger.
Do not let children stay or play within the operating range of the door.
This product is designed and built exclusively for the purpose described in this documentation. Any other use that is not specically
indicated could adversely impact the condition of the product and the safety of people.
Label accepts no responsibility for incorrect product installation and usage, as well as for any damage caused by changes made without
its prior consent.
Label is not responsible for the construction of the frames to be motorised.
The IP22 protection class requires that the automation is installed only on the inner side of buildings.
This product cannot be installed in explosive environments or atmospheres, or in the presence of ammable gases or fumes.
Make sure that the characteristics of the electric distribution network are compatible with the technical data indicated in this manual and
that upstream of the system there is an omnipolar switch with an opening distance of the contacts of at least 3mm and a residual current
device.
Connect the ground wire of the electric system.
The automatic door must be checked, started up, and tested by personnel skilled and trained about the product.
A technical dossier must be compiled for every automation, as established in the Machinery Directive.
Disconnect the power supply before working on the automation and before opening the cover.
Maintenance is of fundamental importance for the proper operation and safety of the automation. Check the eciency of all parts every
six months.
Use only original spare parts for maintenance and when replacing product components.
Cleaning operations must be performed with the power supply disconnected, using a damp cloth. Do not deposit or let water or other
liquids penetrate into the automation or the accessories that are part of the system.
It is recommended to subscribe a maintenance contract.
The automatic sliding doors must be designed and installed so as to protect users against the risk and danger of crushing,
impact, shearing and conveying between the leaf and adjacent parts near the door outline.
The person responsible for starting-up the automation must perform a risk assessment based on the place of installation
and the type of users that could use the automatic door.
Safety during the opening cycle is ensured by the application of one of the following methods:
• Safety distances between the secondary closing edge and the adjacent environment parts.
• Force limitation on the leaf.
• Use of protection devices (sensors) complying with the standard EN12978.
• Installation of protections like xed panels or barriers, preventing people from reaching the
dangerous points.
• Low Energy motion.
Safety during the closing cycle is ensured by the application of one of the following methods:
• Use of protection devices (sensors) complying with the standard EN12978.
• LOW ENERGY motion.
It is essential to be aware that when most users are old/ill/disabled people and children, any contact
of the door with the user is not acceptable.
Any residual risks must be properly highlighted.
AMain closing edge
BSecondary closing edge
SLIDING DOOR
HAZARDOUS AREA

5
1) DESCRIPTION OF THE MODELS
The ETERNA 150 automation has been designed and manufactured for the control of pedestrian automatic sliding doors.
A list of the ETERNA 150 sliding door automation models produced by Label is provided below:
• ETERNA 150D
Automation for double leaf doors, max. weight 150Kg./leaf.
• ETERNA 150S
Automation for single leaf doors, max. weight 200Kg.
The choice of the model depends on the type of door to be automated (single- or double-leaf sliding door, or telescopic door equipped
with two or four movable leaves).
All ETERNA 150 automation models can be equipped with the battery for emergency opening and with the electric lock.
The automation must be installed in indoor environments.
MECHANICAL COMPONENTS OF THE SLIDING DOOR AUTOMATION
ETERNA 150
2) TECHNICAL SPECIFICATIONS OF THE ETERNA 150 AUTOMATION
MODEL ETERNA 150D 2 leaves ETERNA 150S 1 leaf
Power supply 230V~ 50Hz +/‑ 10%, 115V~ 60 Hz +/‑ 10%
Max. power 100 W
Stand-by consumption 6W
Maximum weight of leaves Max. 150 Kg/leaf Max. 200 Kg/leaf
Brushless Motor 24Vdc with built‑in encoder
Opening speed Max. 80 cm/s (per leaf)
Closing speed Max. 60 cm/s (per leaf)
Pause time 0 to 30 seconds
Operating temperature ‑15°C ÷ +50°C
Protection class IP22
Sound pressure emission LpA ≤ 70dB (A)
Power supply for external accessories 24 Vdc
Transom dimensions (H x D) 120 x 150 mm
Transom length max 6,500 mm
Frequency of use continuous

6
upper belt coupling
lower belt coupling
cable clamp
idle pulley
mechanical limit device
driving belt
side caps pair
ET‑LOGIC‑B 150 electronic control unit
motor unit with ET‑MOT 150 encoder
cover links
double wheel trolley
clip
transom
slideway rail
cover
cover adjustable closing prole
rail gasket
brush
3) ETERNA 150 AUTOMATION COMPONENTS

7
4) TECHNICAL DRAWINGS
LAYOUT OF THE COMPONENTS
DOUBLE LEAF WITHOUT ELECTRIC LOCK
LT = TRANSOM
LENGTH
LT = 2PL‑B+2S+24
PL = FREE
PASSAGE
PL = (LT+B)/2‑S‑6
LM = LEAF WIDTH
LM = (LT‑B)/4+S/2‑6
F = IDLE
PULLEY
LT*3/4+75
M = MOTOR
400mm
C = CONTROL
UNIT
345mm
LC = BELT
LENGTH
LC = (F-M+120)x2
SINGLE RH LEAF WITHOUT ELECTRIC LOCK
LT = TRANSOM
LENGTH
LT = 2PL‑B+S+24
PL = FREE
PASSAGE
PL = (LT+B‑S)‑12
LM = LEAF WIDTH
LM = (LT‑B+S)/2‑12
F = IDLE
PULLEY
LT‑87
M = MOTOR
LT‑LM‑342
C = CONTROL
UNIT
LT‑LM‑397
LC = BELT
LENGTH
LC = (F-M+120)x2
SINGLE LH LEAF WITHOUT ELECTRIC LOCK
LT = TRANSOM
LENGTH
LT = 2PL‑B+S+24
PL = FREE
PASSAGE
PL = (LT+B‑S)‑12
LM = LEAF WIDTH
LM = (LT‑B+S)/2‑12
F = IDLE
PULLEY
LT‑87
M = MOTOR
LT‑LM‑342
C = CONTROL
UNIT
LT‑LM‑397
LC = BELT
LENGTH
LC = (F-M+120)x2

8
DOUBLE LEAF WITH ELECTRIC LOCK
LT = TRANSOM LENGTH
LT = 2PL‑B+2S+24
PL = FREE PASSAGE
PL = (LT+B)/2‑S‑6
LM = LEAF WIDTH
LM = (LT‑B)/4+S/2‑6
F = IDLE PULLEY
T*3/4+100
M = MOTOR
400mm
C = CONTROL UNIT
345mm
E = ELECTRIC LOCK
T/2 + 5mm
LC = BELT LENGTH
LC = (F-M+120)x2
SINGLE RH LEAF WITH ELECTRIC LOCK
LT = TRANSOM LENGTH
LT = 2PL‑B+S+24
PL = FREE PASSAGE
PL = (LT+B‑S)/2‑12
LM = LEAF WIDTH
LM = (LT‑B+S)/2‑12
F = IDLE PULLEY
LT‑212
M = MOTOR
LT‑LM‑467
C = CONTROL UNIT
LT‑LM‑522
E = ELECTRIC LOCK
LT‑62
LC = BELT LENGTH
LC = (F-M+120)x2
SINGLE LH LEAF WITH ELECTRIC LOCK
LT = TRANSOM LENGTH
LT = 2PL‑B+S+24
PL = FREE PASSAGE
PL = (LT+B‑S)/2‑12
LM = LEAF WIDTH
LM = (LT‑B+S)/2‑12
F = IDLE PULLEY
LT‑87
M = MOTOR
LT‑LM‑342
C = CONTROL UNIT
LT‑LM‑397
E = ELECTRIC LOCK
75
LC = BELT LENGTH
LC = (F-M+120)x2

9
5) COVER
To remove completely the automation cover, press the terminal
end of the pins (B) of the support articulations and remove them
pulling them from the opposite side (FIG.1)
Manually support the cover before extracting the pin.
In the lower section of the cover you can install an optional
adjustable closing prole allowing to close the gap between the
door and the cover, thus improving the look of the automation.
To adjust the adjustable closing prole depth you must detach the
cover from the automation and put it on a at surface FIG. 3.
Arrange the adjustable closing prole as shown in the gure and
fasten it to the cover by means of the special clips.
Select the ideal adjustment of the adjustable closing prole,
referring to Fig.4 and secure each of the plastic clips, entering rst
the teeth of the clip in the slot of the adjustable closing prole and
then push, pushing forward the top of the clip until the engagement
on the cover is achieved.
Ret the cover on the automation, retting the support articulations
with the specic pins, then close the cover on the automation
engaging the top part with the transom FIG.5.
The cover of the automation ETERNA 150 features two support
links (A) specially designed to ensure that it remains stable in the
opening position.
FIG. 1
Fasten the cover by means of the screws on the side caps FIG.6.
If the transom is ush with the wall, it is possible to secure the
cover on the front, drilling a hole corresponding to the front seat
prearranged on the side cap and secure the cover by means of
the specic Kit EV-KFCF (option) FIG.7.
FIG. 2
FIG. 7
FIG. 3
FIG. 5
FIG. 6
FIG. 4
No. of
engagement
teeth
height X
8 66.8
7 62.7
6 58.5
5 54.4
4 50.2
3 46.1
SIDE CAP SIDE VIEW
SIDE PANEL FRONT VIEW

10
Upon request, the standard cover can be replaced with a smaller one, when the door section dimensions prevent the standard cover from
closing on the transom.
The smaller cover includes the slot for brush insertion.
STANDARD COVER SMALLER COVER
6) BELT TIGHTENING ADJUSTMENT
To adjust belt tensioning, slightly loosen the screw A of
the idle pulley, then screw in (to increase belt tensioning)
or unscrew (to decrease belt tensioning) the hexagonal
screw B.
After achieving the optimum driving belt tightening, fully
tighten screw A.
FIG. 8
7) POSITIONING THE MECHANICAL LIMIT DEVICE
The mechanical limit device must be adjusted so that both during opening and
closing it stops the trolley run before the mobile leaf hits any other component.
It is also used by the electronic control unit to get the leaf limit points.
When adjusting the opening mechanical limit device, take into account that
except for the set-up manoeuvre and for the rst manoeuvre after a power
failure, at the end of the opening the mobile leaf stops about 5 mm before
coming into contact with the limit device.
To adjust the limit device, loosen the 2 setscrews, move the limit device to the
desired position, then fully tighten the 2 screws again.
FIG. 9 SETSCREWS

11
8) ANCHORING THE LEAVES TO THE TROLLEYS AND ADJUSTING THEM
• Unscrew the two front screws "A" of every trolley and remove the movable part "C".
• Secure the removed mobile part “C” on the door at the distance indicated in gure 11 if there is no electric lock or gure 12 if the
electric lock is present.
• Now hang the leaf to the automation matching the two parts of the trolley, then screw the screws "A" into their seats without tightening
them.
• Adjust leaf height using the control screw “B” and fully tighten the two screws “A”.
• Adjust the leaf horizontally by means of the eyelets "E" provided in the movable part of the trolley.
• To ensure the correct operation of the automation, it is important that the mobile leaf is perpendicular to the transom.
• Adjust the height of the opposing wheel operating the adjustment screw (D) so that the wheel almost touches the top inner part of the
transom without applying pressure.
• Then manually move the leaf until it reaches the run end and check that there are no frictions at any point; otherwise adjust the
opposing wheel position again.
FIG. 10
FIG. 9
FIG. 10
DOUBLE LEAF WITHOUT ELECTRIC LOCK
DOUBLE LEAF WITH ELECTRIC LOCK

12
9) INSTALLATION DIMENSIONS
The transom must be fastened to a perfectly smooth at surface, solid
enough to bear the weight of the leaf to be handled.
If the wall or the support do not meet these characteristics you will have
to provide a suitable tubular element, as the transom is not self-bearing.
Fasten the transom by means of M6 or equivalent steel dowels.
The xing points must be distributed alternately between the reference
lines on the transom (L1 and L2) every 300mm.
The gure shows the fastening dimensions.
When drilling the transom and the wall, take care not to damage the
slideway rail (B1) as that would aect the operation and the quietness
of the automation.
After securing the transom, thoroughly clean the sliding area from any
drilling scraps.
TOOLS REQUIRED
Tape measure, drill, level, thin at-head screwdriver, medium-
sized at-head screwdriver, cross-head screwdriver, Allen
wrenches with handle (sizes 3 - 4 - 5 - 6), at-head wrench 10.
FIG. 13
FIG. 14

13
SECTION WITH COMMERCIAL PROFILES SECTION WITH FRAMELESS COUPLING
DIMENSIONAL TABLE FOR ETERNA 150 AUTOMATIONS
LEGEND:
PL = FREE PASSAGE
LT = AUTOMATION LENGTH
LM = LEAF WIDTH
H = PASSAGE OPENING HEIGHT
ETERNA 150S - 1 MOBILE LEAF ETERNA 150D - 2 MOBILE LEAVES
Sizing mm Sizing mm
LT= automation length
LT=2PL-B+S+24
LM= leaf S= overlap
B= contact with
S=50 B=10
LM = LT-B+S - 12
2
PL = nominal passage
opening
PL = LT+B-S - 12
2
LT= automation length
LT=2PL-B+2S+24
LM= leaf S= overlap
B= contact with
S = 50 B = 10
LM = LT-B + S - 6
4 2
PL = nominal passage
opening
PL = LT+B - S - 6
2
2000 1008 968 2000 516.5 949
2500 1258 1218 2500 641.5 1199
3000 1508 1468 3000 766.5 1449
3500 1758 1718 3500 891.5 1699
4000 2008 1968 4000 1016.5 1949
4500 2258 2218 4500 1141.5 2199
5000 2508 2468 5000 1266.5 2449
5500 2758 2718 5500 1391.5 2699
6000 3008 2968 6000 1516.5 2949

14
10) ELECTRIC LOCKS
10.1) GENERAL DESCRIPTION
The electric lock for the ETERNA 150 automation is available in 3 models, which have dierent behaviour during a power failure.
10.2) POSITIONING AND ELECTRIC CONNECTION
a) FAIL SAFE “ET-EBSFSA”
In the case of a power failure, of both mains power supply and emergency battery power, the
electric lock will release the leaves, which can then be moved manually.
b) FAIL SECURE “ET-EBSFSE”
In the case of a power failure, of both mains power supply and
emergency battery power, the electric lock will keep the leaves locked.
c) BISTABLE “ET-EBSBIS”
In the case of a power failure, of both mains power supply and emergency battery power, the
electric lock will remain at its current position.
Therefore, the leaves are free if the electric lock was disabled, or will remain locked if the electric
lock was enabled.
Set the Jumper J10 to position "2" on the ET-LOGIC-B control unit.
The electric locks are supplied in kit, that includes the fastening brackets and xing
accessories.
The dimensions for securing the electric lock to the automation are specied in
Paragraph "TECHNICAL DRAWINGS".
The electric lock is fastened to the automation by 2 screws M6 x 10 on nuts M6,
which are located in the special lower slot in the transom.
The sliding trolleys must be regulated so that when the leaf is in closed position, the
electric lock level can engage the trolley bracket and keep the leaves locked.
The electric lock kit includes a power supply cable. This cable has two wires on one
end that are connected to the electric lock solenoid wires (black colour) with the
specic terminals. The other end of the cable has a connection that is inserted in
the connector LOCK1 on the electronic control unit of the automation ETERNA 150.
If the bistable electric lock ET‑EBSBIS is installed, there will be a second power
supply cable. One end of it must be connected to the secondary solenoid cables
(LOCK2) of the electric lock (red colour) and the other end must be connected to the
LOCK 2 output on the electronic control unit where the connector is located.

15
10.3) MANUAL RELEASE
RELEASE HANDLE FASTENING
The models Fail Secure ET‑EBSFSE and Bistable ET‑EBSBIS
are equipped with the manual release system ET‑EBSSMA, that
is used to release the electric lock in the case of a power failure.
Therefore it is possible to move the leaves freely.
For fastening on both the right and left side of the automation,
you need to fasten the adjustment register on the bottom of the
release handle.
Insert the steel cable located inside the exible sheath as shown
in the gure.
Fix the bottom of the release knob to the side panel, using the
supplied self-threading screws, on the two holes existing in the
side panel.
A
B
C

16
D
E
F
Apply the adhesive label as shown in the gure, taking as a
reference the four black bands on the label that must be positioned
in correspondence of the 4 cardinal points.
Insert the steel cable end into the release handle as shown in the
gure and fasten the handle to the bottom with the special screw.
Apply the screw cover label on the setscrew.
By moving the release handle to UNRELEASED position, only the
orange part of the label with the black arrows must be visible.
Insert the exible sheath into the special hole on the side panel.
Use the hole which is furthest from the register, to ensure that the sheath retains a wide enough bending radius.
LEFT SIDE PANEL RIGHT SIDE PANEL
SCREW COVER
LABELS

17
G
H
I
L
Insert the sheath using the cable guides until reaching the electric
lock.
Cut o the excess sheath.
Insert the steel cable into the release handle and into the sheath
until reaching the electric lock.
Fit the sheath end on the tip of the sheath which has been cut.
Position the compression spring and insert the metal cable inside
the special release anchor, then lock it with the screw clamp.
Adjust cable tightening so as to give the spring a light pre-load.

18
M
N
O
Check manual release operation, when the handle is in locked
position, the electric lock must operate normally.
When the handle is in released position, the electric lock must
remain open and release the leaves.
Cut the excess cable from the release anchor.
NOTE:
In the case of a FAIL SECURE electric lock, by releasing the release, the electric lock sets to closed.
In the case of a bistable electric lock, by releasing the release, it sets to open.
In the case that it is necessary to manually close the door with a bistable electric lock, it will be sucient to raise the core of the secondary
solenoid with a screwdriver.

19
10.4) INSTALLATION OF THE MANUAL RELEASE ON THE WALL
Identify the fastening point on the wall, taking into account
that the standard cable sheath is 3 metre long and that it must
reach the electric lock.
Thread the release cable in the slit in the base and then inside
the adjustment register as shown in the gure. Then position
the cable terminal on the release handle cable lock (see gure).
Drill the wall and secure the bottom of the release mechanism
by means of the setscrews.
Apply the adhesive label as shown in the gure, taking as
a reference the four black bands on the label that must be
positioned in correspondence of the 4 cardinal points.
Insert the adjustment register with 2 nuts, one in the slot of the
plastic and the other outside the same.
Now, insert the release handle on the base of the mechanism,
being careful to keep the cable terminal in the seat of the cable
lock and the handle in the correct position. When inserting the
handle, the cable terminal must be in the position just beyond
(in clockwise direction) the lower setscrew.
Once you have inserted the knob, x the setscrew, insert the
sheath and turn the knob to position UNRELEASED. In this
position, only the orange part of the label with the black arrows
must be visible.
Make sure the system is operating by turning the handle
clockwise and keeping the cable taut with your hand.
WARNING!:
THE HANDLE TURNS BY MAX 45-50 DEGREES AND AT
THE END, IT IS PROVIDED WITH CATCHES IN ORDER TO
MAINTAIN THE POSITION AFTER THE LOCK.
Apply the provided screw cover label as shown in the gure
and return the handle to the UNRELEASED position.
SETSCREW
CABLE LOCK LOWER SCREW
SETSCREW
BLACK BANDS
LUGS
SCREW COVER
LABEL
LUGS
BLACK BANDS

20
A
B
C
D
Put the drilling template into place, aligning it with the reference
marks at the top of the transom.
Align the template with the centre of the solenoid axle.
Drill a hole into the transom as indicated on the template.
Fix the release knob bottom using the supplied screws.
Insert the 250mm sheath.
Apply the adhesive label as shown in the gure, taking as a
reference the four black bands on the label that must be positioned
in correspondence of the 4 cardinal points.
Insert the steel cable end into the release handle as shown in the
gure and fasten the handle to the bottom with the special screw.
10.5) INSTALLATION OF THE MANUAL RELEASE OVER THE TRANSOM
Table of contents
Popular Home Automation manuals by other brands
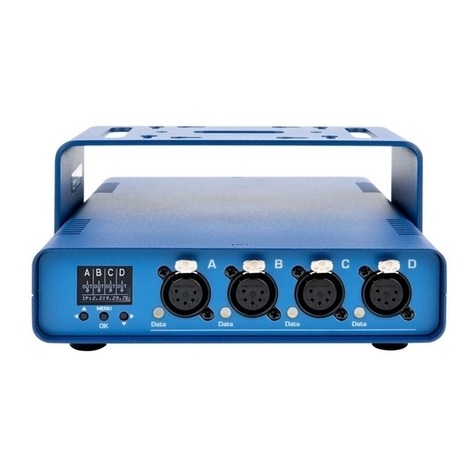
TMB
TMB ProPlex IQ One+ Mini manual

Ingersoll-Rand
Ingersoll-Rand American Standart Nexia Installation and Account Setup

AUTO HOMATION
AUTO HOMATION MULTI CONTROLLER installation manual
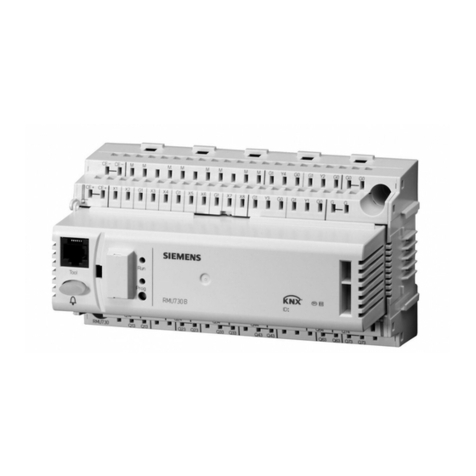
Siemens
Siemens RXB Series Basic documentation
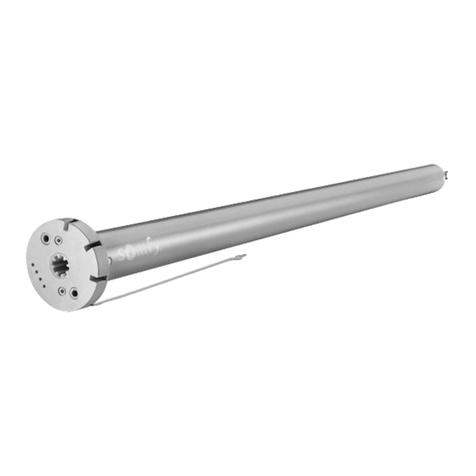
SOMFY
SOMFY RU Basic 28 WF RTS Li-ion II instructions
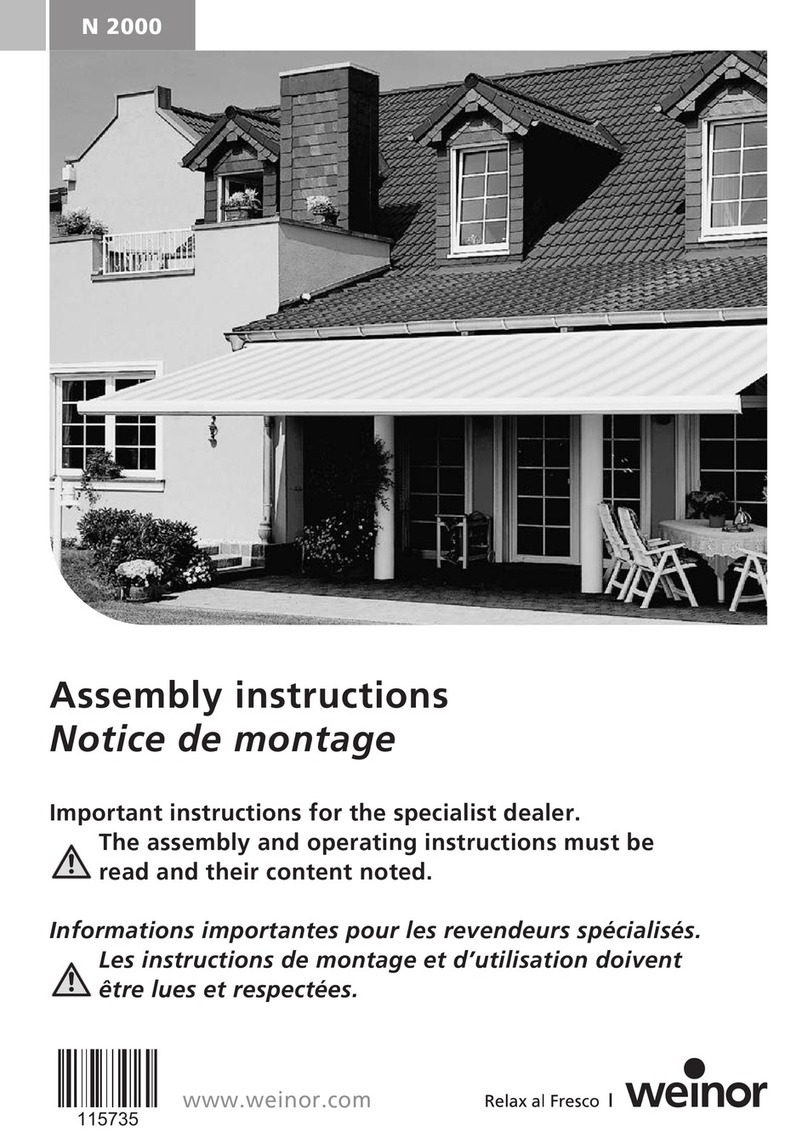
weinor
weinor N 2000 Assembly instructions
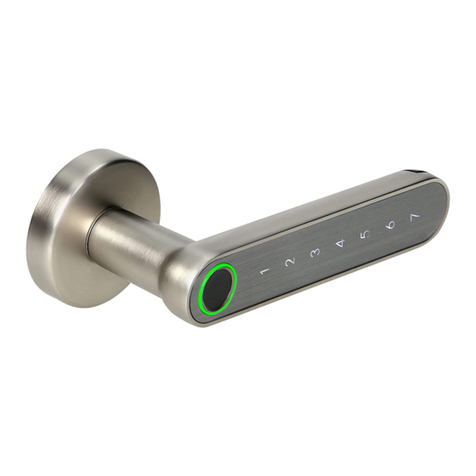
Orno
Orno OR-ZS-853/N manual
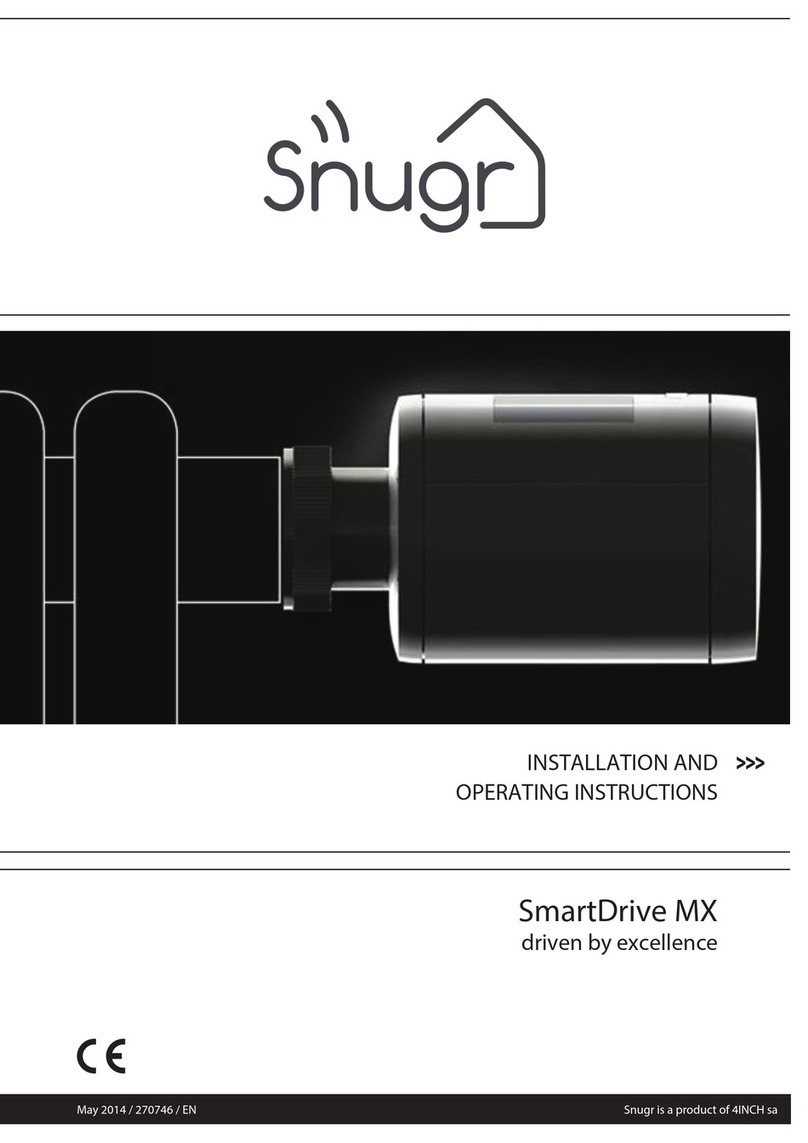
Snugr
Snugr SmartDrive MX Installation and operating instructions
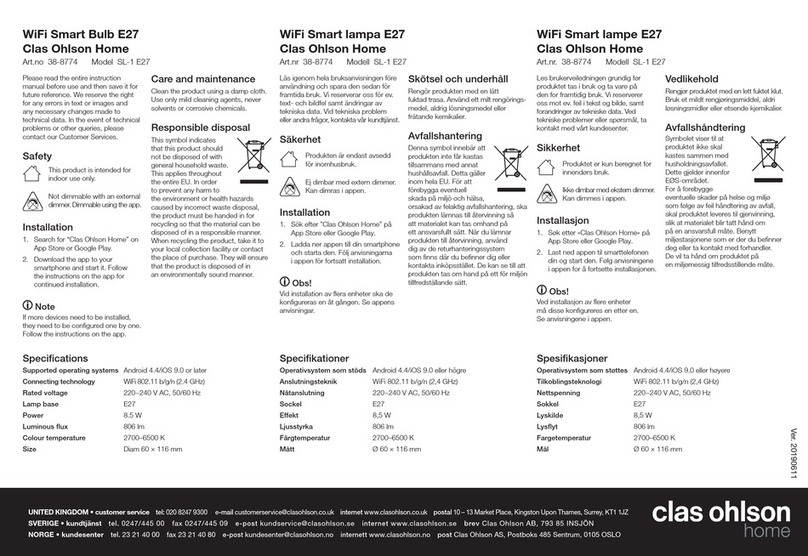
Clas Ohlson
Clas Ohlson SL-1 E27 instruction manual
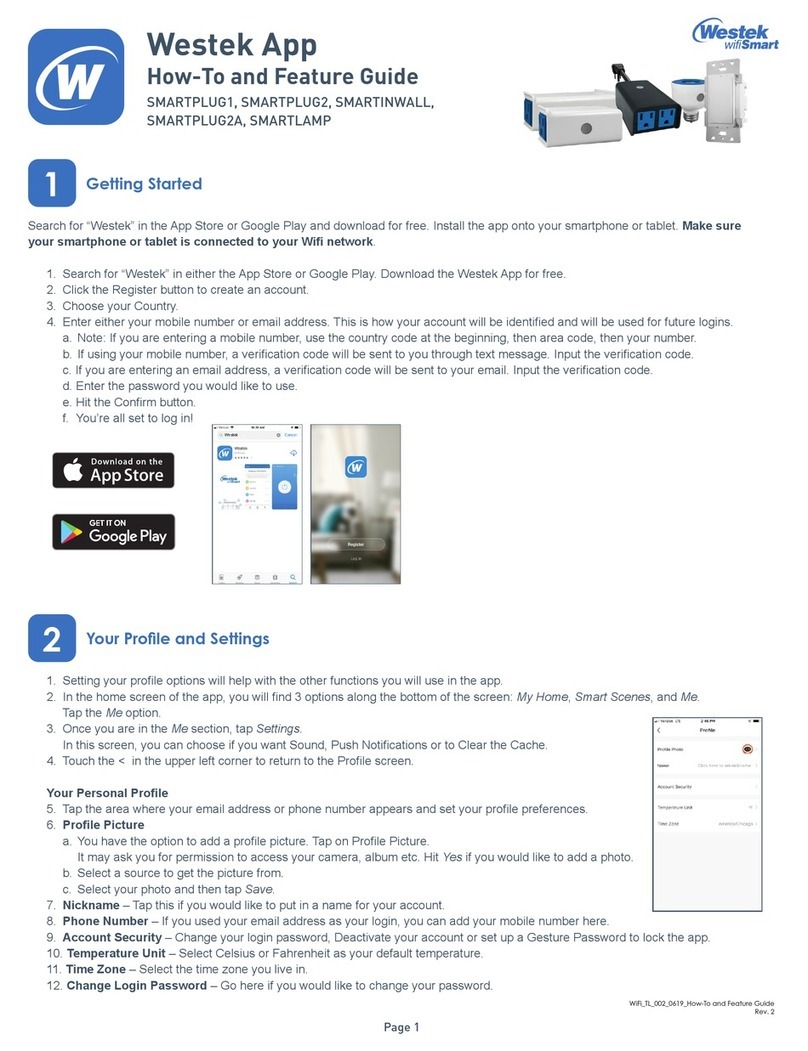
WESTEK
WESTEK SMARTPLUG1 How-To and Feature Guide
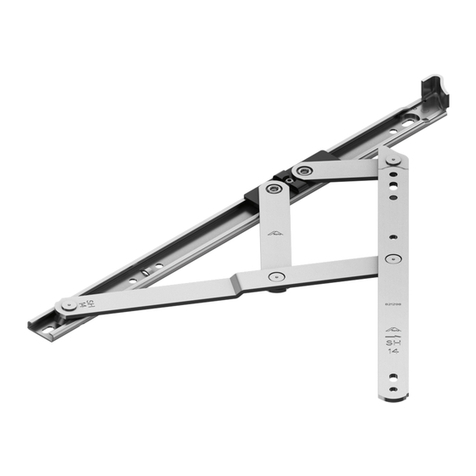
Roto
Roto FS Kempton Installation, maintenance and operation instructions

HomeMatic
HomeMatic HM-PB-6-WM55 Installation and operating manual