Lamtec ETAMATIC V User manual

www.lamtec.de
Sensors and Systems for Combustion Technology
Quick Reference for Endusers
ETAMATIC V
ETAMATIC V S


2
Table of Contents
Table of Contents
1 General Information . . . . . . . . . . . . . . . . . . . . . . . . . . . . . . . . . . . . . . . . . . . . . . . . . . . . . . . . . 3
1.1 Validity of these Instructions. . . . . . . . . . . . . . . . . . . . . . . . . . . . . . . . . . . . . . . . . . . . . . . 3
2 Safety . . . . . . . . . . . . . . . . . . . . . . . . . . . . . . . . . . . . . . . . . . . . . . . . . . . . . . . . . . . . . . . . . . . . 4
2.1 For Your Safety . . . . . . . . . . . . . . . . . . . . . . . . . . . . . . . . . . . . . . . . . . . . . . . . . . . . . . . . 4
3 Description . . . . . . . . . . . . . . . . . . . . . . . . . . . . . . . . . . . . . . . . . . . . . . . . . . . . . . . . . . . . . . . . 5
3.1 Brief Description. . . . . . . . . . . . . . . . . . . . . . . . . . . . . . . . . . . . . . . . . . . . . . . . . . . . . . . . 5
3.2 Operating Description . . . . . . . . . . . . . . . . . . . . . . . . . . . . . . . . . . . . . . . . . . . . . . . . . . . 7
3.3 Operator Device. . . . . . . . . . . . . . . . . . . . . . . . . . . . . . . . . . . . . . . . . . . . . . . . . . . . . . . . 8
4 Operation . . . . . . . . . . . . . . . . . . . . . . . . . . . . . . . . . . . . . . . . . . . . . . . . . . . . . . . . . . . . . . . . 10
4.1 Reading Faults. . . . . . . . . . . . . . . . . . . . . . . . . . . . . . . . . . . . . . . . . . . . . . . . . . . . . . . . 10
4.2 Resetting Faults . . . . . . . . . . . . . . . . . . . . . . . . . . . . . . . . . . . . . . . . . . . . . . . . . . . . . . . 10
4.3 Recalling Fault History . . . . . . . . . . . . . . . . . . . . . . . . . . . . . . . . . . . . . . . . . . . . . . . . . . 10
4.4 What Happens if a Fault Occurs in the O2Controller? . . . . . . . . . . . . . . . . . . . . . . . . . 10
4.5 Resetting O2Errors . . . . . . . . . . . . . . . . . . . . . . . . . . . . . . . . . . . . . . . . . . . . . . . . . . . . 11
4.6 Calling Fault History O2trim . . . . . . . . . . . . . . . . . . . . . . . . . . . . . . . . . . . . . . . . . . . . . 11
4.7 How to switch the Display . . . . . . . . . . . . . . . . . . . . . . . . . . . . . . . . . . . . . . . . . . . . . . . 11
4.8 Operation and Display of the O2 Trim . . . . . . . . . . . . . . . . . . . . . . . . . . . . . . . . . . . . . . 12
4.9 Display and Interpretation of the Operating Modes . . . . . . . . . . . . . . . . . . . . . . . . . . . . 12
4.10 Calling up O2Trim Text Messages. . . . . . . . . . . . . . . . . . . . . . . . . . . . . . . . . . . . . . . . . 12
4.11 Calling up the Hour Counter . . . . . . . . . . . . . . . . . . . . . . . . . . . . . . . . . . . . . . . . . . . . . 12
4.12 Call up the checksums and safety times . . . . . . . . . . . . . . . . . . . . . . . . . . . . . . . . . . . . 13
5 Internal Burner Firing Rate Controller . . . . . . . . . . . . . . . . . . . . . . . . . . . . . . . . . . . . . . . . . 14
5.1 Purpose . . . . . . . . . . . . . . . . . . . . . . . . . . . . . . . . . . . . . . . . . . . . . . . . . . . . . . . . . . . . . 14
5.2 Brief Description. . . . . . . . . . . . . . . . . . . . . . . . . . . . . . . . . . . . . . . . . . . . . . . . . . . . . . . 14
5.3 Range Limits . . . . . . . . . . . . . . . . . . . . . . . . . . . . . . . . . . . . . . . . . . . . . . . . . . . . . . . . . 14
5.4 Moving Screen "Actual Temperature is too high". . . . . . . . . . . . . . . . . . . . . . . . . . . . . . 14
5.5 Enter Setpoint of Firing Rate Controller . . . . . . . . . . . . . . . . . . . . . . . . . . . . . . . . . . . . . 14
5.6 Thermostat and Control Range . . . . . . . . . . . . . . . . . . . . . . . . . . . . . . . . . . . . . . . . . . . 15
5.7 Manual Control. . . . . . . . . . . . . . . . . . . . . . . . . . . . . . . . . . . . . . . . . . . . . . . . . . . . . . . . 15
5.8 Meaning of the Display . . . . . . . . . . . . . . . . . . . . . . . . . . . . . . . . . . . . . . . . . . . . . . . . . 16
6 Appendix. . . . . . . . . . . . . . . . . . . . . . . . . . . . . . . . . . . . . . . . . . . . . . . . . . . . . . . . . . . . . . . . . 17
6.1 Mode Abbreviations Used . . . . . . . . . . . . . . . . . . . . . . . . . . . . . . . . . . . . . . . . . . . . . . . 17
6.2 Fault Codes . . . . . . . . . . . . . . . . . . . . . . . . . . . . . . . . . . . . . . . . . . . . . . . . . . . . . . . . . . 18
6.3 Calling Up the Condition of the Digital Inputs . . . . . . . . . . . . . . . . . . . . . . . . . . . . . . . . 40
6.4 Process Sequence Charts . . . . . . . . . . . . . . . . . . . . . . . . . . . . . . . . . . . . . . . . . . . . . . . 41
6.5 Connecting Diagram . . . . . . . . . . . . . . . . . . . . . . . . . . . . . . . . . . . . . . . . . . . . . . . . . . . 43
6.6 Switch and Key Combinations . . . . . . . . . . . . . . . . . . . . . . . . . . . . . . . . . . . . . . . . . . . . 45
6.7 Technical Data . . . . . . . . . . . . . . . . . . . . . . . . . . . . . . . . . . . . . . . . . . . . . . . . . . . . . . . . 47
6.8 Declaration of Conformity . . . . . . . . . . . . . . . . . . . . . . . . . . . . . . . . . . . . . . . . . . . . . . . 52

3
1 General Information
1 General Information
1.1 Validity of these Instructions
These instructions apply to the ETAMATIC V and ETAMATIC V S in any configuration.
These devices conform to the following standards and regulations:
• EN 230
• EN 267 (where applicable)
• EN 298
• EN 676 (where applicable)
• EN 746-2 (where applicable)
• EN 12952-8 and 11 (where applicable)
• EN 12953-7 and 9 (where applicable)
• 2004/108/EC EMC - Directive, Low-Voltage Directive
• 2006/95/EC Low Voltage Directive
• 97/23/EC Pressure Equipment Directive
• 2009/142/EC Gas Appliance Directive
Test symbols: CE-0085 AU 0207
The ETAMATIC V is a control unit for combustion systems.

4
2 Safety
2 Safety
2.1 For Your Safety
The following symbols are used in this document to draw the user's attention to important safe-
ty information. They are located at points where the information is required. It is essential that
the safety information is observed and followed, and that applies particularly to the warnings.
DANGER!
This draws the user's attention to imminent danger. If it is not avoided, it will result in death or
very serious injury. The plant including its surroundings could be damaged.
WARNING!
This draws the user's attention to the possibility of imminent danger. If it is not avoided, it may
result in death or very serious injury. The plant including its surroundings could be damaged.
CAUTION!
This draws the user's attention to the possibility of imminent danger. If it is not avoided, it may
result in minor injuries. The plant including its surroundings could be damaged.
NOTICE
This draws the user's attention to important additional information about the system or system
components and offers further tips.
The safety information described above is incorporated into the instructions.
Thus, the operator is requested to:
1 Comply with the accident prevention regulations whenever work is being carried out.
2 Do everything possible within his control to prevent personal injury and damage to prop-
erty.

5
3 Description
3 Description
3.1 Brief Description
The ETAMATIC V positions up to 4 actuators, according to freely programmable curves, in de-
pendence on a reference input variable. The "V" version has 4 three-step positioning outputs
and the "VS" variant has 3 three-step positioning outputs and a 4 - 20 mA output.
Examples of possible actuators:
• Combustion air valve
• Combustion air blower (ETAMATIC VS only)
• Fuel air valve
• Recirculation valve
Up to 20 points (usual 11) can be programmed per channel. The Display is relative between
0 and 999.
The ETAMATIC has a 25-pole Sub-D connector with serial interface for remote operation / re-
mote display via a PC (Windows software available separately). Connections for Interbus- S,
PROFIBUS-DP, CANopen, TCP/IP (Modbus TCP) and Modbus are available as optional
equipment. Other BUS-systems available on enquiry. The connection of other plant compo-
nents, e.g. fault signal systems and O2trim, is via the LAMTEC SYSTEM BUS interface to a
9-pole Sub-D connector.
Operation is via a front panel laminated keyboard. The parameters are displayed on a 2-row
LCD screen.
Operation via PC software is described in a separate manual.
The ETAMATIC V continuously monitors its own functions and those of the connected control
elements.
Unlike the ETAMATIC, the "V" version does not have a control unit, so the functions of the dig-
ital inputs and outputs differ from those described in the ETAMATIC basic documentation.This
means that the "gas-tightness check" and "integral flame monitor" options available with the
ETAMATIC cannot be used with the "V" version.
External messages to the ETAMATIC V are supplied via potential free contacts or contact
chains.
The following signals can be predefined:
– Burner on
– Pre-purge
– Flame signal (burner operating)
– Control enable
– Recirculation on
– Curve set selection
– Setpoint switchover (for output controller)
230 V-outputs for the communication with the external control device (isolated contacts via re-
lay module type 660R0027):

6
3 Description
– error main processor
– error monitoring processor
– ignition position main processor
– ignition position monitoring processor
– indication: high firing rate
The integral firing-rate controller is built as a PID-controller with special functions for combus-
tion engineering. You may use it as a set-value controller or controlled by atmospheric condi-
tions.
The following signals may be provided:
– actual value (analogue) - (PT100 or 4 - 20 mA)
– outside temperature or another analogue signal for setpoint switching (only with controller
controlled by atmospheric conditions) - (PT100, potentiometer, 0/4...20 mA)
– setpoint switching (via floating contact)
The release of the combustion with the firing-rate controller is carried out by an output at the
ETAMATIC V. A digital signal is the output for activating a relay for the connection with a burn-
er sequencer (floating contacts via relay module type 660R0027).
Using the display- and operating unit
The display- and operating unit allows you to operate and program the ETAMATIC V without
front panel.
Connecting the ETAMATIC V
The operating unit is to be connected by the 9-p Sub D plug with the ETAMATIC V. Use for it
the provided lead with the type no. 6 63 R 0430. The data communication runs via the
LAMTEC SYSTEM BUS.Alternatively the possibility exists to attach the operating unit at the
cable of the customer interface. An adaptor cable is attached, with the type no. 6 63 R 0426.
Pull the 6-pol. plugs at the customer interface off and put the adaptor cable on the 6-pol. plug.

7
3 Description
3.2 Operating Description
Selection of a curve-set
A signal first fed is "Burner ON", indicating when the burner is to start. The flue gas damper
runs „OPEN“. After that the pre-purge signal appears. The air- and the fuel-channels and the
continuous fan output run to 20mA. The three-point-step outputs are set to continuous output.
The recirculation channels only start, when the signal is present at the terminal and the corre-
sponding channel (mostly air damper) is open at 75%. If you do not want a delay of the recir-
culation damper, set a continuous signal to the recirculation terminal. In this case the delay of
the recirculation damper occurs automatically. If all active channels have reached the highest
point, the output closes the high firing rate terminals. The fuel channel runs to ignition position.
The pre-purge time in the external burner sequence controller may start running.
After the end of the pre-purge period the air channels and the recirculation channels run to
ignition position as well. After that, the signals ignition position HP and ignition position ÜP are
fed and the output closes the terminals for "burner firing rate controller" and "actual value" on
the relay module type 660R0027.The flue gas damper remains open or the flue gas fan re-
mains at the highest speed.
The external burner sequence controller is now ready to start the ignition. After the ignition has
completed the external burner sequence controller sets the flame signal (burner is running) to
the ETAMATIC V.
3 seconds after ignition all channels are running to the programmed base firing rate position.
The ETAMATIC V remains in base firing rate position until control release is set. After control
release the device follows the input of the burner firing rate controller. After laps of the burner
ON signal a shut-down occurs.
If you have configured „post-purge“ plus "flame signal" (burner is running), the air channels
will open again for that period. The ETAMATIC V runs to mode „OFF“.
Starting without pre-purge
Even if the plant shall be started without pre-purge, the pre-purge signal has to be set for at
least 3 seconds, the device switch to the next sequence and runs to ignition position.
Not before the pre-purge signal is pending for more than 10 seconds, the pre-purge has to be
run to the end, i.e. the channels are running to their end position.
If the pre-purge signal is taken before all actuators are run their end position, this will be ig-
nored and the actuators will be running to their end position anyway.

8
3 Description
3.3 Operator Device
Select operating modes: UEAN PARA O21 )AUTO EINS SPLO
Select operating parameters: Status Firing rate rating Setpoint Actual value feedback Setpoint feedback 2)Dig-
ital inputs
Display change:
-Compound
- O2
- Flame inten-
sity
* UEAN = Monitoring processor display 1.) only if activated in parameter sec-
tion
PARA = Parameter settings 2.) only in ETAMATIC S OEM
AUTO = Automatic
EINS = Set
SPLO = Clear memory

9
3 Description
Select operating
modes:
UEAN PARA O2*AUTO EINS SPLO
Select operating
parameters:
Status Firing rate rating Setpoint Actual value feedback Setpoint feedback ** digital inputs
* only available, if activated in the parameter section
** only available with ETAMATIC V / ETAMATIC V S the option "Integrated Flame Monitor"
Customer Interface Using the Keys
reset
firing-rate / fault history up
firing-rate / fault history down
manual mode ON / OFF
display change
- compound
-O2*
-flame intensity**
Display change
-compound
-O2*
-flame intensity **
UEAN monitoring processor display
PARA parameterisation
AUTO automatic
EINS clear memory
SPLO

10
4 Operation
4 Operation
4.1 Reading Faults
NOTICE
Press key 16 for reading other display values at time of the fault. All display values are frozen.
4.2 Resetting Faults
4.3 Recalling Fault History
The ETAMATIC V stores the last 10 faults with the associated data of the running time counter.
Requirement: ETAMATIC V must not be in fault condition.
NOTICE
If it is certain that the ETAMATIC V has carried a voltage at all times since the last fault, it is
possible, that from the present output of the running time counter and the current time, to de-
termine at which time the fault occurred.
4.4 What Happens if a Fault Occurs in the O2Controller?
In the event of a malfunction, the display shows a warning and the O2trim is deactivated. The
specified base value "without control” (correction value at deactivated O2 trim) or the one for
"air deficiency” (correction value at air deficiency) is set. The display shows the running text
"O2trim disturbed”.
The burner doesn’t shut down.
Red fault LED is on
Press key 17 to get STATUS display fault code
Press key ENTER Plain text message is shown on display (incl. output of running
time counter)
Press key RESET
Alternatively:
Use an external switch to send a short signal (min. 2 sec.) to terminal 57.
The error is cleared!
Press key 17 until the display shows "Status".
Press key 3 the display shows the last fault code
Press key 11 (Enter) the display shows the associated plain text and the running
time hours.
Press key 3 again the display shows the last but one fault code.
Press keys 3 and 2 to browse through the fault history.

11
4 Operation
Set the selector switch to "Status" to call up the corresponding error code.
4.5 Resetting O2Errors
Each new burner start-up resets O2errors automatically. This is permissible, because a 100%
O2measurement test is performed at each start-up.
Manual resetting of O2errors is possible at any time, as follows:
4.6 Calling Fault History O2trim
Display:
The display hides the O2history automatically after 5 sec. O2trim faults, which last for more
than 30 sec are stored. They are only stored in the EEPROM once the fault is cleared up or
the ETAMATIC V leaves the operating mode or control or base firing rate.
4.7 How to switch the Display
NOTICE
You can set the O2trim only, if you have completed the programming of the fuel/air ratio con-
trol.
Press key 11 ENTER The display shows a plain text message about the cause of
the error.
Press key RESET
ETAMATIC V in O2trim mode
If not, switch over to O2trim mode
Press key 15 M once
Press key ENTER and call up the cause of error (mandatory!)
Press key 7
Switch over to fuel/air ratio control mode, if necessary press M.
Use key 4 and 5 to browse the fault history.
1 147 1 000 487
current fault internal firing
rate
curve set operating hours
Press key 15 to change the display from status of the fuel/air ratio control to O2value (if
active), to flame intensity (if active) and intern burner firing rate controller (if active).

12
4 Operation
4.8 Operation and Display of the O2 Trim
When you have switched to "Status", the display shows the O2actual value and O2setpoint
value. The display shows the values in brackets, if O2trim is deactivated.
NOTICE
O2actual value and O2setpoint are only displayed, if O2trim or O2display are activated in
parameter 896.
In automatic operation, the display switches during regular operation automatically to O2trim
mode. However, it is always possible to switch the display over with key "M". The manually
preselected setting only remains in force until the next switch to "Regular operation” or "Base
firing rate operation”, and then returns automatically to the base setting.
4.9 Display and Interpretation of the Operating Modes
4.10 Calling up O2Trim Text Messages
Switch display to O2trim
4.11 Calling up the Hour Counter
Press key 15 once, to switch the display to O2-trim.
Mode "O2-trim": By pressing key "ENTER" (display in position "Status"), you can call up
information texts (running texts)
op O2trim in standby (during burner start-up), or O2trim temporarily switched off as a func-
tion firing rate via parameters 914 and 915.
or O2- trim active.
ot O2trim temporarily deactivated (air deficiency, probe dynamics etc).
od O2trim deactivated (fault), e.g. test routine failed during burner start-up, dynamic test
negative, O2trim temporarily deactivated for over 1 hour etc.
C Optimisation at increasing firing rate
c Optimisation at decreasing firing rate
press key "RESET"
press key M
press key "ENTER" to call up the text messages
press key "ENTER" again back
press key 10 the display shows the running text of the following data succes-
sively:

13
4 Operation
The total of running times for curve set 1and curve set 2 do not necessarily add up to the dis-
played total running time.
NOTICE
The total counter refers to the ETAMATIC V 's running time. It starts timing as soon as the unit
is connected to a voltage source (this also provides the basis for the fault history).
The individual running time counters refer to the burner's running time. They start timing as
soon as the burner is in operation with the relevant curve set (flame signal is present).
4.12 Call up the checksums and safety times
1st safety time oil in seconds
2nd safety time oil in seconds
1st safety time gas in seconds
2nd safety time gas in seconds
pre-purge time in seconds
In the ETAMATIC V without pilot burner, the 2nd safety time includes the safety time. The 1st
safety time figure is then irrelevant.
If you have changed parameters, reset the ETAMATIC V. Only a reset refreshes a checksum.
Total running time
Running time on curve set 1
Starts on curve set
Running time on curve set 2
Starts on curve set 2
Running time on curve set 3*
Starts on curve set 3*
Running time on curve set 4*
Starts on curve set 4*
* if parameterised
Press keys 16 and 17 to select "setpoint feedback”.
Press key 11 ENTER.
The following values are displayed one by one:
CRC 16 of the levels 0, 1 and 2: adjustable at commissioning time
4: adjustable by LAMTEC only
Press key 11 ENTER again.

14
5 Internal Burner Firing Rate Controller
5 Internal Burner Firing Rate Controller
5.1 Purpose
The internal firing rate controller calculates the burner firing rate against a pre-defined setpoint
value (e.g. as a function of temperature or pressure) by comparison with the actual value. This
position will be transferred to the electronic fuel/air ratio control as a default value.
5.2 Brief Description
The integral firing rate control unit is a PID controller with special combustion engineering
functions. You can use it as a fixed value control or as a control by atmospheric condition. The
following signals can be pre-set:
• Actual value (temperaturePT 100 max 320 °C or steam pressure)
• Outside temperature or another analog signal for setpoint shift (only on control by atmos-
pheric condition). The ETAMATIC V must be equipped with the optional hardware for con-
trol by atmospheric condition.
• Setpoint switching (via floating contact). The burner firing rate controller releases the com-
bustion internally.
Combustion is triggered internally by the power control unit.
5.3 Range Limits
You must set limit values in the parameters, switching the burner on and off. After a burner
shut-down while actual temperature has not reached the switch-on threshold yet, a display will
inform you that firing rate controller is refusing a start-up.
5.4 Moving Screen "Actual Temperature is too high"
NOTICE
The limit values should always be entered in the form of a difference from the setpoint value.
5.5 Enter Setpoint of Firing Rate Controller
Up to software version A3i1023 you can change the setpoint with parameter settings only.
From software version A3i1023 on you can change the setpoint of the firing rate controller.
This function works in case of running burner only.
-display on firing rate rating
Press key 12 HAND to override this and start the ETAMATIC V, if the maximum tem-
perature has not exceeded.
Press key 12 HAND again to switch back to automatic mode.
Press key 9 and 6 simultaneously the setpoint in the display is blinking.

15
5 Internal Burner Firing Rate Controller
NOTICE
If you change the setpoint, regard that also the on and off switchpoints are shifted, because
they were defined as difference value to the setpoint.
5.6 Thermostat and Control Range
The thermostat function switches the burner on and off on the basis of the temperature and/
or pressure value, but only when burner is released by the start signal. The control range is
formed by entering the controller setpoint value and the parameters P 802 (switch-on point),
P803 (upper control range) and P 804 (burner OFF). The cut-off hysteresis is divided into 2
ranges. The first part lies above the setpoint and forms the upper control range. The second
part lies below the setpoint and forms the lower control range.
The control range may lie asymmetrically around the setpoint.
The power control unit functions within the upper and lower control range according to its set-
tings in the parameters and the default values.
If the actual value of the control unit reaches the shut-down range, the base firing rate request
is emitted. If the control unit’s setpoint exceed the shut-down range a control shut-off occurs.
This is done by internal processing. If the actual value drops below the lower control range, a
re-start can occur.
NOTICE
This function can replace the control thermostat, which is required on the plant.
It does not replace a safety thermostat.
5.7 Manual Control
You also may switch the ETAMATIC V to "Manual Control" with the terminals. By short-circu-
iting the PT 100 signal (e.g. bridge terminal 19 and 20) the burner firing rate controller is
switched off. The fuel/air ratio controller then directly follows the input at the default firing rate
input. The display shows LE instead of HA.
Use keys 4 and 5 to change the value.
Press key 11 ENTER to confirm the new value
Press keys 7 and 8 simultaneously to leave this mode without changes.
press key "Manual" to move the regular firing rate input of the firing rate controller.
press the keys 2 and 3 to variegate the burner firing rate.
to cancel firing rate controller, press key "Manual" again

16
5 Internal Burner Firing Rate Controller
NOTICE
Only use manual control while monitoring the system.
5.8 Meaning of the Display
Display in "FIRING RATE" switch position
setpoint actual value regular firing
rate input
internal
firing rate
Display in mode "MANUAL"
regular firing
rate input
(via channel 1)
internal firing
rate
actual value

17
6 Appendix
6 Appendix
6.1 Mode Abbreviations Used
Fig. 6-1 Status display at customer interface
Short text Description
BE →READY (signal on terminal 58)
ZÜ →IGNITION POSITION or IGNITION
EZ →SETTING/IGNITION position (same as IGNITION, but ETAMATIC V
on SETTING)
GL →BASE FIRING RATE
EG →SETTING/BASE FIRING RATE” (as BASIC FIRING RATE, but ETA-
MATIC V on SETTING)
NA →POST-PURGE
AU →BURNER OFF (no signal present)
EL →SETTING
SL →CLEAR MEMORY
EV →SETTING/PRE-PURGE" (as "PRE-PURGE", but ETAMATIC V on
SETTING)
ES →SETTING/CONTROL (as AUTOMATIC but ETAMATIC V on SET)
ST →FAULT
VO →PRE-PURGE
HA
or Hand
→MANUAL MODE (burner efficiency may be adjusted manually)
no display →Burner set to AUTOMATIC during OPERATION
LE →EXTERNAL FIRING RATE (firing rate controller disabled by digital
input)
op O2TRIM READY (with burner start-up) or O2TRIM via
P 914 and P 915 depending on firing rate, temporarily switched off
or O2TRIM ACTIVE
ot O2TRIM TEMPORARILY DEACTIVATED (air deficiency, probe
dynamic etc.)
od O2TRIM DEACTIVATED (in fault mode) e.g. testing routines with
burner start-up not successfully completed,
O2trim switched off temporarily for more than 1 hour

18
6 Appendix
6.2 Fault Codes
The letter "H" preceding a fault code indicates that the main processor has discovered the
cause of the fault.
A "Ü" preceding the code indicates that the monitoring processor has activated the fault.
A * indicates that a re-start is permitted for this fault. A flashing fault LED indicates that a re-
start is to be initiated within a short period.
** indicates, that restarts are to be initiated without limit.
Fault
Code
No.
Restart according to Description
TRD EN676
000 0 0 No fault code available for this fault
001 0 3 Ignition flame does not appear.
H/Ü Check flame stability.
Check wiring.
Check ignition transformer and pilot burner.
Check flame sensor.
Check Parameter 788.
002 0 0 parasitic light failure
H/Ü Check wiring.
Check setting flame sensor.
Check Parameter 788.
003 0 3 Flame fault during ignition
H/Ü Check flame stability.
Check ignition transformer and pilot burner
Check flame sensor settings
004 1 1 Flame fault during operation
H/Ü Check flame stability
The switch off time for digital input "flame signal is <200ms!
For this reason, a flame fault can also have another cause, e.g.:
- The fuel solenoid valves close.(EMV, low voltage))
- "gas pressure < min" switch off time <1s
FMS with 660 R 0016 V4.3 with burner stationary
Check wiring between FMS and 660R0016 V4.3
Change 660 R 0016 V4.3 if wiring is correct.
005 0 3 Flame signal does not appear during 1st safety time
H/Ü Check flame stability.
Check wiring.
Check ignition transformer and pilot burner.
Check flame sensor.
Check Parameter 774, 775 and 788.
006 0 3 Flame signal goes out during stabilising time
H/Ü Check flame stability.
Check set pilot burner.
Check flame sensor.

19
6 Appendix
Fault
Code
No.
Restart according to Description
TRD EN676
007 0 3 The flame signal extinguishes during the first safety time
H/Ü Check flame stability.
Check set pilot burner.
Check flame sensor.
ETAMATIC: Check Jumper.
008 0 0 The flame signal extinguishes during the second safety time
H/Ü Check flame stability.
Check wiring.
Check flame sensor.
009 0 0 Flame signal does not appear during safety time
H/Ü Check flame stability.
Check wiring.
Check flame sensor.
Check Parameter 774, 775 and 788.
010 0 0 Flame signal goes out immediately after ignition
H/Ü If the flame extinguishes within three seconds after ignition, fault H010 is shown;
after that, fault H004 appears.
Check the flame stability.
Check the flame sensor setting.
Check the sensitivity of the sensor.
The deactivation time for the "Flame signal" digital input amounts to <200ms!
For this reason, a flame fault can also have another cause, e.g.:
- The solenoid fuel valve closes (EMC, low voltage)
- "Gas pressure < min" deactivation time <1s.
011 0 0 Internal fault: 5 sec. outside light monitoring period not kept
The fault can occur during an internal self-test.
Reset the fault. In the process, switch the mains voltage off and on again if neces-
sary.
Check all fuses in the device.
If the fault persists despite reset exchange the device or respective card
012 0 0 relay module not connected or missing 24V supply for relay
Check the wiring between FMS and relay module 660R0016 and fuse F2 on the
FMS front panel.
FMS with relay module type 660 R 0016 V4.3 when the burner is at a standstill:
Check the wiring between FMS and 660 R 0016 V4.3.
If the wiring has been performed correctly:
Exchange relay module type 660 R 0016 V4.3.
013 1 3 main flame signals appears during ignition
Other manuals for ETAMATIC V
1
This manual suits for next models
1
Table of contents
Other Lamtec Control Unit manuals
Popular Control Unit manuals by other brands
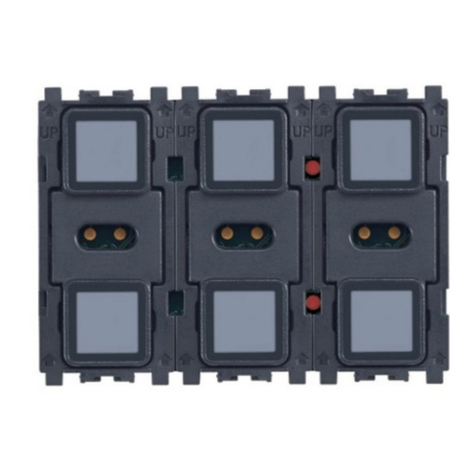
Vimar
Vimar 21125 Installer manual
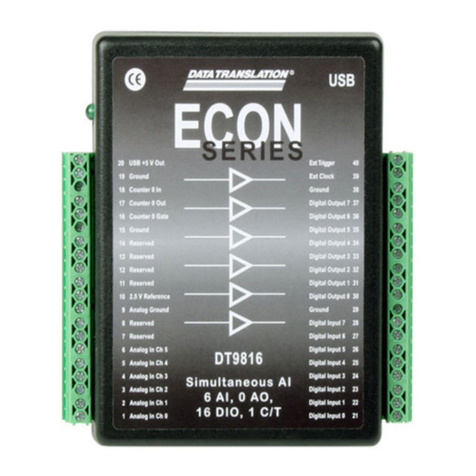
Data Translation
Data Translation DT9816 Series user manual
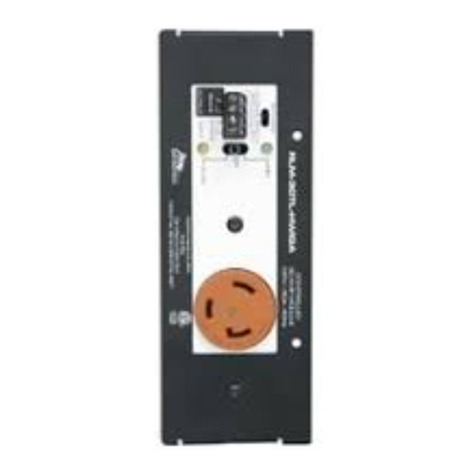
Intertec Data Systems
Intertec Data Systems MPR-A Series instruction sheet
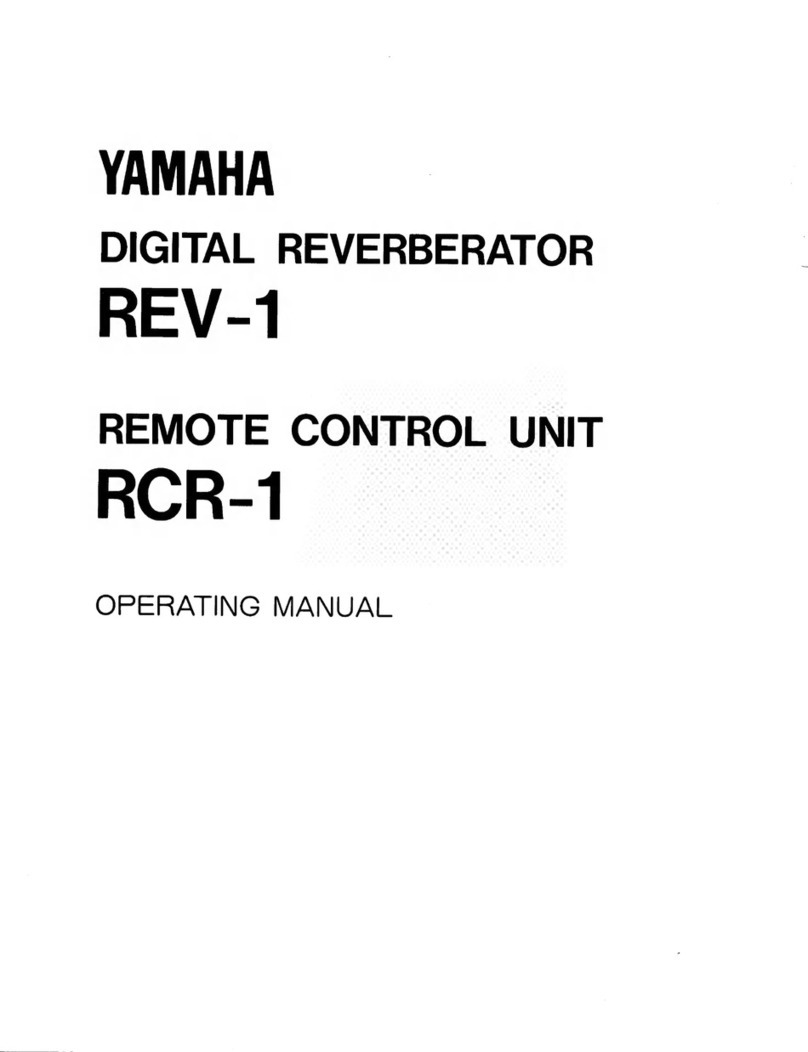
Yamaha
Yamaha REV-1 operating manual
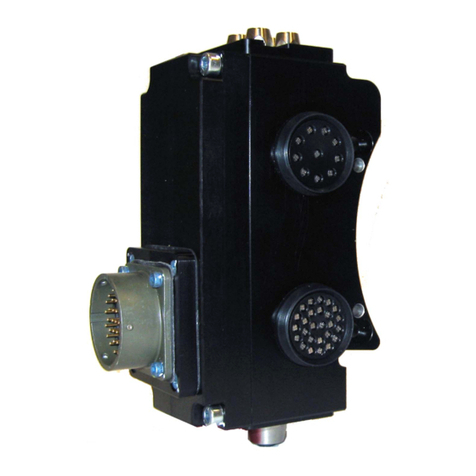
ATI Technologies
ATI Technologies VB12-M Installation and operation manual
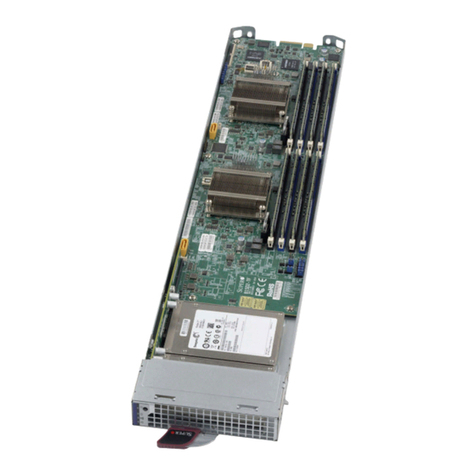
Supermicro
Supermicro MicroBlade MBI-6218G-T41X user manual