Larco Zone Monitor 3000 User manual

Zone Monitor 3000
Installation and Operation Manual

2
Industrial Safety Products
Zone Monitor 3000 Installation and Operation
Important Safety Message …………………………..........3
Zone Monitor 3000 Overview........................................3
Installation Instructions ...............................................5
Testing and Using the System .....................................11
Troubleshooting Guide ..................................................13
Controller Specifications...............................................14
Details and Dimensions ................................................15

3
Industrial Safety Products
Zone Monitor 3000 Installation and Operation
Important Safety Message
Zone Monitor 3000 Overview
Minimizing the hazards surrounding heavy automated equipment and industrial machinery can be a complex and difficult task.
With every advance in machinery design and increased levels of automation, the task becomes more difficult. The dangers and
hazards created by these machines can be made safer through the use of Larco Industrial Safety Mat Systems, including the
Larco Zone Monitor 3000 control unit.
The information contained in this manual will help with installation and make full use of the Larco Zone Monitor 3000 in
combination with Larco safety mats. This manual should be read in its entirety prior to beginning the installation.
The Larco Safety Mat and Zone Monitor 3000 control system should not be used as a substitute for machine guarding
requirements set forth by local and national organizations, such as OSHA. The installer must be appropriately qualified for the
installation task and familiar with the requirements for the particular application, as well as any local codes or ordinances,
before attempting to install any safeguarding systems. Proper ESD practices and procedures should be followed during
installation to protect against possible electronic damage to the Larco Zone Monitor 3000.
1Green Run LED
Indicates normal operation. The machine control relays
will be energized to allow machine operation.
2Red Activated Mat LEDs.
The red Stop LED will also be lit.
3Yellow Disconnected Mat LEDs.
Four yellow LEDs indicate mat fault condition.
The red Stop LED will also be lit.
4Red Stop LED
Indicates normal operation. The machine control relays
will be de-energized due to mat activation or detected
system fault.
1
2
3
4
Figure 1

4
Industrial Safety Products
Zone Monitor 3000 Installation and Operation
Zone Monitor 3000 Overview
5Redundant Safety Relay Pack
Removable relay pack allows for easy field
replacement.
6Machine Control Connector
7Remote Restart Connector (under the relay pack –
see Figure 2 -inset)
Connection point for remote restart switch option,
when applicable.
8Option Jumpers (under relay pack –
see Figure 2 -inset) Used for choosing automatic
restart or guard only mode of operation.
9Mat Connectors
Four mat connectors make wiring faster and easier.
Optional quick-disconnects available.
10 Relay Fault LED
Used in normal operation to indicate a detected
relay fault,or temporary line power drop out.
11 Manual Restart Switch
Momentary contact switch used to restart the
Zone Monitor 3000 and/or associated equipment.
12 Manual Reset Switch
Momentary contact switch used to reset the
Zone Monitor 3000. Will clear the Relay Fault
Latch if fault has been removed.
13 Power Connector (under the relay pack –
see Figure 2 -inset) For incoming 110/230 VAC
or 24 VDC power.
14 Earth Ground Lug
101211
9
6
5
8
Figure 2
13 14
7
Figure 2 - inset
Power Connector
(under relay pack)

5
Industrial Safety Products
Zone Monitor 3000 Installation and Operation
Refer to the Safety Mat Installation Guide that accompanies the Larco safety mats.
If there is more than one safety mat in the system, it may be helpful to identify and label the mats by number
according to the connection point in the Zone Monitor that it will be wired to in step 4. Identification of the mats will
allow full advantage of the Zone Monitor 3000 mat diagnostic capabilities.
The Zone Monitor 3000 is designed to operate with Larco’s standard mat cord. It is possible to order mats with
longer leads to reach the control box, as long as the total length of each mat cord connected does not exceed
40 feet.
.
Locate the Zone Monitor outside of the safeguarded space and, whenever possible close enough to the mats to
allow all of the mat leads to be routed directly into the control enclosure.
Select a sturdy horizontal or vertical mounting surface that has enough room to allow the cover door to open aer
installation. The machine operator should be able to view the status lights easily on the face of the control.
Access holes have been provided at the bottom of the enclosure for safety mat wires, incoming power, and control
signal wires. If additional holes are required, remove the internal electronics prior to drilling. The circuit board
mounted on the inside of the cover should also be removed and reinstalled along with the main board.
Mount the unit using the mounting holes provided on the upper and lower mounting flanges.
1Choose the Safety Mat Locations
2Mount the Zone Monitor
Zone Monitor Installation Instructions
The Larco Zone Monitor 3000 was designed with safety and convenience in mind. Unpack and become familiar with the unit
before installing it.
WARNING! Always use proper ESD (Electrostatic Discharge) avoidance practices by wearing the appropriate
grounding apparel whenever opening or working inside the Zone Monitor 3000 enclosure.

6
Industrial Safety Products
Zone Monitor 3000 Installation and Operation
Two optional modes of operation are available with the Zone Monitor 3000. They are enabled or disabled by
changing option jumpers, which are located on the main board, under the relay module (see Figure 3).
WARNING! Always ensure the Zone Monitor’s power is off before making or changing selections. Power
should be removed from the unit, then operating changes completed and power restored.
Refer to Figure 4 to select the desired mode of operation.
• Option 1: Guard Only Mode requires pressing the restart switch to resume operation each time the control
enters a Stop condition or the power is cycled to the Zone Monitor. The Zone Monitor 3000 is shipped from the
factory in Guard Only Mode.
• Option 2: Automatic Restart Mode allows the machine to resume operation immediately once an activated
mat is cleared.
WARNING! The automatic restart mode of operation should not be used unless the machinery has its own
control reliable latching stop circuitry to prevent unexpected restart. Selecting the automatic restart mode
of operation will allow the Zone Monitor and associated machinery to automatically restart upon clearing
an activated mat.
3Select Operating Options
Figure 3 – Option Jumpers
Figure 4 – Option Jumper Selections
Automatic Restart Mode Guard Only Mode
(factory setting)
1
J11 J14
2
3
1
2
3
J11 J14

7
Industrial Safety Products
Zone Monitor 3000 Installation and Operation
a. Prepare the Mat Lead Wires
Remove approximately 1” (25mm) of the outer jacket from the four-wire mat cord, being careful not to cut the
insulation on the four individual mat wires.
Next, strip off approximately 3/16” (5mm) of insulation from the ends of the four individual mat wires. If there
is more than one safety mat, the installer will want to make sure that each mat lead is labeled to indicate the
corresponding mat.
b. Become Familiar with the Connector Positions
When viewing the four mat connectors, note that the wiring sequence begins with connector number 1 being the
highest connector. The sequence travels down, with the lowest connector being number 4. Each position at each
mat connector is marked with a Bfor black wires and a Wfor white wires.
c. Route the Mat Lead Wires
Route the mat lead wires into the control box through watertight conduits and the wiring entry holes, making sure
to use watertight fittings to maintain the Type 12/IP65 rating.
4Connect the Safety Mats
Figure 5 – Mat Connectors with Positions Indicated
1
3
2
4

8
Industrial Safety Products
Zone Monitor 3000 Installation and Operation
d. Connect Mats
While wiring the mats, use caution not to insert the insulation of the mat wires into the connector by pushing
too far in.
Starting with the mat connector at the top le, connect the black mat wires from mat number one into the first
and second screw terminals of that connector, and the white wires from mat number one into the third and fourth
screw terminals of that connector. (see Figure 5).
If there are additional mats in the system, remove the factory-installed jumpers and make mat connections as
done for mat number one. NOTE: Any unused mat connectors must have the jumpers le in them, black must be
jumped to black and white to white.
NOTE: When wiring the mats, ensure the mat clamps in the terminal blocks are in the fully open position
by turning the screws counterclockwise several turns. Once the mat wires in the terminal blocks are
secured, gently pull on the mat wire to ensure it is securely and properly installed.
In the Guard Only Mode of operation, the Restart switch is used to re-energize the machine control relays and
allow the machinery to operate aer the Zone Monitor has changed to a Stop condition. A Remote Restart
switch may be added to the Zone Monitor for ease of use and to avoid entry into the enclosure for each restart. If
a switch is added, it must be a normally-open, momentary contact switch with a contact rating of 0.5 A at 24 VDC
minimum. Connect the switch to the connector positions marked Remote Restart (see Figure 6).
4Connect the Safety Mats (cont.)
5Connect Optional Remote Restart Switch
Figure 6 – Remote
Restart Connector

9
Industrial Safety Products
Zone Monitor 3000 Installation and Operation
Two sets of isolated, normally-open contacts and one normally-closed set of contacts are provided for machine
control (see Figure 7). Connect to the machine’s control as required to maintain proper safety. The contact positions
are as follows.
A Note Regarding Inductive Loads
Inductive loads from the machine’s control circuit can
greatly affect the life of the Zone Monitor 3000 machine
control relays. An effective and proven method for
extending the life of the relays is to use a varistor for surge
suppression installed across the inductive load. Size the
varistor according to the specific load characteristics.
A good general formula for sizing the varistor is to add
20 percent to the maximum voltage.
WARNING! Never install a varistor across the machine control contacts of the Zone Monitor 3000. Failure
of the varistor to a shorted condition in this position would allow the machinery to continue to operate
regardless of the Zone Monitor’s output signals.
Position 1 & 2 Normally Open (Closed When Run)
Position 3 & 4 Normally Closed (Open When Run)
Position 5 & 6 Normally Open (Closed When Run)
6Connect Machine to Control Wiring
Figure 7 – Machine Control Connector
6Connect Machine to Control Wiring
Figure 8 – Input Power Connections
(under Relay Module)
Electrical connections must be made by qualified service personnel. The enclosure must be permanently
attached to a surface and the wiring must run through water tight conduit as specified below.
The standard Zone Monitor 3000 can be powered with
either 110 VAC, 230 VAC or 24 VDC (see Figure 8).
A minimum of 18 AWG wire should be used to connect the
Zone Monitor 3000 to the main power. Use 1/2” (12.7mm) steel or
malleable iron liquid-tight conduit and fittings to connect the
Zone Monitor 3000 to the main power junction box. This will maintain
the Type 12/IP65 rating.
Strip 1/4” (6mm) from the ends of the wires and insert them into
the J1 terminal block, under the removable relay module, using
the wiring guide in sections 7a, 7c, 7c. Do not tin the ends of the
wires. Tighten the terminal block screws until the wires are
compressed and cannot be pulled out with a slight tug.
7Connecting Input Power
110/230 VAC
Power Connection
24 VDC
Power Connection

10
Industrial Safety Products
Zone Monitor 3000 Installation and Operation
a. 120 VAC Configuration
Position 1: Not Used
Position 2: Not Used
Position 3: Do Not Connect (use earth ground lug)
Position 4: Neutral
Position 5: 120 VAC Hot
Position 6: Not Used
b. 230 VAC Configuration (J1)
NOTE: 240 VAC is designed for use in Europe. If this power input is used in the U.S., install a fuse in the second
240 V hot line (L2) before hooking it to the neutral input (position 4).
Position 1: Not Used
Position 2: Not Used
Position 3: Do not Connect (use earth ground lug)
Position 4: Neutral (or L2 hot for U.S. applications if a fuse is added in the line)
Position 5: Not Used
Position 6: 240 VAC Hot
c. 24 VDC Configuration (J19)
Position 1: 24 VDC
Position 2: 24 VDC Ground
Position 3: ESD Ground Protection
Position 4: Not Used
Position 5: Not Used
Position 6: Not Used
d. Ground Connection
The AC earth ground wire must be connected to the chassis ground stud.
Use a crimping tool specified for use with 14-16 AWG PIDG connectors and follow the manufacturer’s instructions
for its use.
Strip 5/16” (78mm) from the end of the ground wire and insert it into the supplied terminal lug located on the
grounding stud (see Figure 9). Crimp the wire lug so the wire will not slip out. Insert the ground wire lug onto the
ground stud over the star washer. Place the nut over the ground lug and tighten the lug securely.
Figure 9 – Earth Ground Lug
7Connecting Input Power (cont.)

11
Industrial Safety Products
Zone Monitor 3000 Installation and Operation
Testing and Using the System
When the installer begins the verification of equipment, assume that the equipment could start at any
moment until system check out and verification is complete.
Make sure that all personnel are out of and cannot enter the hazardous area during the testing procedure.
During testing of the system the installer will be asked to observe the lights that are part of the Zone Monitor 3000.
All of these lights are on the face of the unit, except for the internally mounted yellow Relay Fault LED. Refer to
Figures 1 and 2 to become familiar with the location of the lights.
a. Checking Operation in Guard Only Mode
(If Automatic Restart Mode of operation was chosen, skip to step 4b.) Make sure that the machinery is not
powered and that the machine control wiring connector is unplugged. Apply power to the Zone Monitor 3000 while
observing the indicator and diagnostic lights.
1. In the Guard Only Mode of operation the red Stop LED should turn on.
2. Press and release the Restart button and verify the red Stop LED turns off and the green Run LED turns on.
The two machine control relays energize.
3. Remove jumper J4 on the relay board.
4. In the Guard Only Mode of operation the red Stop and yellow Relay Fault LEDs should turn on.
5. Place the jumper J4 on the relay board.
6. Press and release the Reset button. The yellow Relay Fault LED should turn off.
7. Press and release the Restart button and verify the red Stop LED turns off and the green Run LED turns on.
The two machine control relays energize.
8. Next, apply and release pressure to safety mat 1 in the system and verify that the green Run LED turns off
and the red Stop LED turns on. Verify that the appropriate red Activated Mat LED for mat number is on.
The machine control relays de-energize.
9. Now press and release the Restart switch to return to a Run condition and check each of the safety mats in the
system the same way as was done for mat 1.
10. Next, while in a green Run condition, carefully disconnect one of the safety mats by removing one of the mat
wires from any of the mat connectors and verify that the unit changes to a Stop condition. Verify the
Disconnected LED of the disconnected mat is on and that the unit remains in a Stop condition. Reconnect the
mat, press the Restart switch and verify that the unit changes to a Run condition.
If the unit does not function as described, note the condition of the indicator lights and refer to the troubleshooting
guide on page 13.
1Use Extreme Caution to Verify Equipment
2Clear the Area
3Become Familiar with the Indicator and Diagnostic Lights
4Check Operation

12
Industrial Safety Products
Zone Monitor 3000 Installation and Operation
5Periodic Checkout Procedure
The functioning of the safety mat monitoring system must be verified periodically to ensure proper operation of the
safety relays.
b. Checking Operation in Automatic Restart Mode
Make sure the machinery is not powered and that the control output wiring connector is unplugged. Remove
jumper from J4 of the relay module. Apply power to the Zone Monitor 3000. Observe the indicator lights.
1. In the Automatic Restart Mode of operation verify that the green Run LED turns on.
2. Remove jumper J4 on the relay board.
3. In the Automatic Restart Mode of operation the red Stop and the yellow Relay Fault LEDs should turn on.
4. Place the jumper J4 on the relay board.
5. Press and release the Reset button. The yellow Relay Fault LED and the red Stop LED should both turn off.
The green Run LED should turn on. The two machine control relays energize.
6. Next, while in the green Run condition, apply continuous pressure to safety mat 1 in the system and verify that
the green Run LED turns off and the red Stop LED turns on. Verify that the appropriate red Activated Mat LED
for mat number 1 is on. Now release the pressure to the safety mat and verify that the unit changes to a green
Run condition automatically. If there is more than one mat in the system, continue by checking all of the mats
in the system in the same way as tested mat 1, noting that the activated mat corresponds to the number of the
Activated Mat LED that turns on. NOTE: If more than one mat is activated, the mat with the lowest number will
be displayed.
7. Next, while in a green Run condition, carefully disconnect one of the safety mats by removing one of the
mat wires from any of the mat connectors and verify that the unit changes to a red Stop condition and the
Disconnected Mat LED of the mat disconnected is on. Reconnect the mat, and verify that the unit changes
to a green Run condition automatically.
If the unit does not function as described, note the condition of the indicator lights and refer to the troubleshooting
guide on page 13.
c. Check the Relay Pack
Remove the relay pack jumper (J4) and verify that the yellow Relay Fault LED is on. Replace the jumper and press
the Reset button. If the unit is in Guard Only Mode, press the Restart button as well. Verify that the unit returns to
a green Run condition.
NOTE: Perform this check monthly.
d. Checking the Machinery
Use Extreme Caution. Be aware that with some machinery, sudden stopping and starting could be a
hazard in itself. Take every precaution when entering the protected area to activate and test the safety mat
system. If all is working as expected, plug the control wiring connector back into the relay pack and apply
drive power to the machine. Check that the equipment stops and starts as expected when stepping on and
off the safety mats.
4Check Operation (cont.)

13
Industrial Safety Products
Zone Monitor 3000 Installation and Operation
WARNING! If diagnosing the installation, be aware that some of the following instructions for clearing fault
conditions may cause the machinery to start. Make sure the area is clear of personnel and the machinery is
powered down before proceeding with caution.
Condition: All lights are off
Probable Cause:
• No power to the Zone Monitor 3000.
• Poor (loose) connections.
• Relay pack is loose.
Solution:
• Test for incoming power.
• Recheck terminal block for screw-clamp tightness and receptacle position.
• Refer to step 7 on page 9 and recheck configuration.
• Check to ensure relay pack is securely seated.
Condition: Red Stop LED stays on
Probable Cause:
• The unit is in Guard Only Mode and is waiting for a restart signal.
• A relay fault or intermittent power failure occurred.
Solution:
• Refer to installation instructions regarding restart in guard only mode
• Open the case and observe the yellow Relay Fault LED. If it is lit, press the Reset button, and the Restart
button if in Guard Only Mode, and test one of the mats. If the internal yellow Relay Fault LED stays on, or
comes back on at any time during this test, replace the relay pack.
Condition: Internal yellow Relay Fault LED is on
Probable Cause:
• Machine control relay pack has failed.
• Temporary line power drop occurred.
Solution:
• Press the Reset button, and the Restart button if in Guard Only Mode, and test a mat. If the internal yellow
Relay Fault LED stays on or comes back on at any time during this test, replace the relay pack.
Condition: Yellow Mat Disconnected and red Stop LED stays on
Probable Cause:
• Broken or intermittent mat wire connection.
Solution:
• For mat or mat wire problems, refer to the Mat Status LEDs on the front of the unit. The number of the LED
that is on corresponds to the disconnected safety mat.
Condition: Green Run LED stays on but the machine will not operate
Probable Cause:
• The machine control relay signal is not reaching the machine control.
• A different device or machine interlock is preventing operation.
Solution:
• Check the wiring to the machine from the machine control connector to the machine’s control connection point.
• Replace the machine control relays of the Zone Monitor 3000.
• Check for other machine interlocks that may be preventing operation.
Troubleshooting Guide

14
Industrial Safety Products
Zone Monitor 3000 Installation and Operation
Controller Specifications
Response Time <30 ms
Indicators Run = Green LED
Stop = Red LED
Mat Status = 4 Mat Activated Red LEDs and 4 Mat Disconnects Yellow LEDs
Relay Fault =Internal Yellow LED
Operational Modes Selectable Guard Only or Automatic Restart
Power Input 120 VAC (for 60Hz); 240 VAC (for 50Hz) or 24 VDC
Rated Supply Current 0.125A AC, 0.75A DC
Safety Inputs Removable Connectors for up to Four 4-wire Safety Mats with up to 40’ Cord
Length Each (quick disconnect mat connections available)
Safety Output Relays Two Captive Contact Relays with Two Closed when Run (NO) and One Open
when Run (NC). Sets of Contacts Rated 8 Amps at 230 VAC
Relay Life Mechanical 10,000,000 Operations;
Electrical 500,000 Operations at 1 Amp at 240 VAC
Operating Temperature 32°F - 122°F
Relative Humidity 20-90% Acceptable Range
Restart Function Selectable Manual or Automatic Restart; Internal/Lockout Restart and
External/Remote Restart Available
Reset Function Power-up/Relay Fault Reset Internal Manual Push Button
Enclosure Steel, Powder Coat, 8” h x 6” w x 3.75” d
Enclosure Rating Type 12, IP65
Mounting Surface Mount
Shipping Weight 9 lbs

15
Industrial Safety Products
Zone Monitor 3000 Installation and Operation
Details and Dimensions
Dimensions in inches, (mm)
Warning! Usage of safety mats and safety mat devices is governed by each user’s local codes and
applicable industry standards. Improper usage of these devices could result in severe injuries. Applications
must be limited to machines that can be stopped consistently. In the event that Larco Safety Mats do not
prevent all access to the hazardous operation, the unprotected access must be guarded by other appropriate
safeguarding devices or barriers.
For more information on Larco Industrial Safety products and accessories, visit www.larco.com.
8.88
225
.30
8
4.43
112
4.00
102
.59
15
1.13
29
1.88
48
1.13
29
.88
22
.63
16
1.25
32 8.00
203
6.00
152
6.25
159
.91
23
9.50
241
1.75
44
1.75
44
8.25
210
4.12
105

ATEK Access Technologies
10025 Valley View Road, Ste. 190
Eden Prairie, MN 55344 U.S.A.
PH: 1.800.523.6996
FAX: 1.800.589.3705
+1.218.829.9797
www.atekaccess.com
223-0120-000 Rev. C 5/19
©2019 ATEK Access Technologies, LLC. All Rights Reserved. Larco images and marketing materials are protected by various patents, copyrights and/or
trademarks. ATEK assumes no responsibility for any errors which may appear in this document, reserves the right to change devices or specifications
detailed herein at any time without notice, and does not make any commitment to update the information contained herein. No licenses to patents or
other intellectual property of ATEK are granted by the Company in connection with the sale of Larco products, expressly or by implication.
WARNING: Cancer and Reproductive Harm - www.P65Warnings.ca.gov
Industrial Safety Products
Zone Monitor 3000 Installation and Operation
Table of contents
Other Larco Control Unit manuals
Popular Control Unit manuals by other brands

Karibu
Karibu Sauna Control FIN Installation and operating instructions

VIPA
VIPA 900-2H611 manual

Aritech
Aritech ATS608 Installation sheet
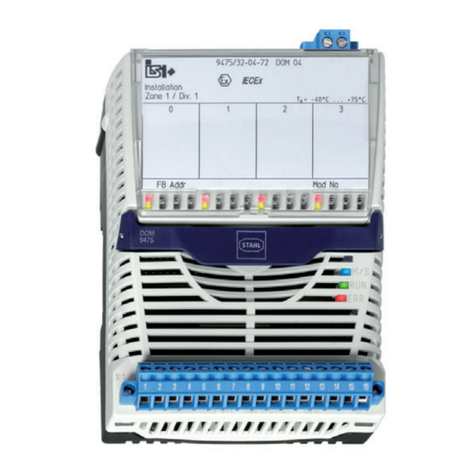
Stahl
Stahl IS1+ 9475/32-04-72 Series operating instructions
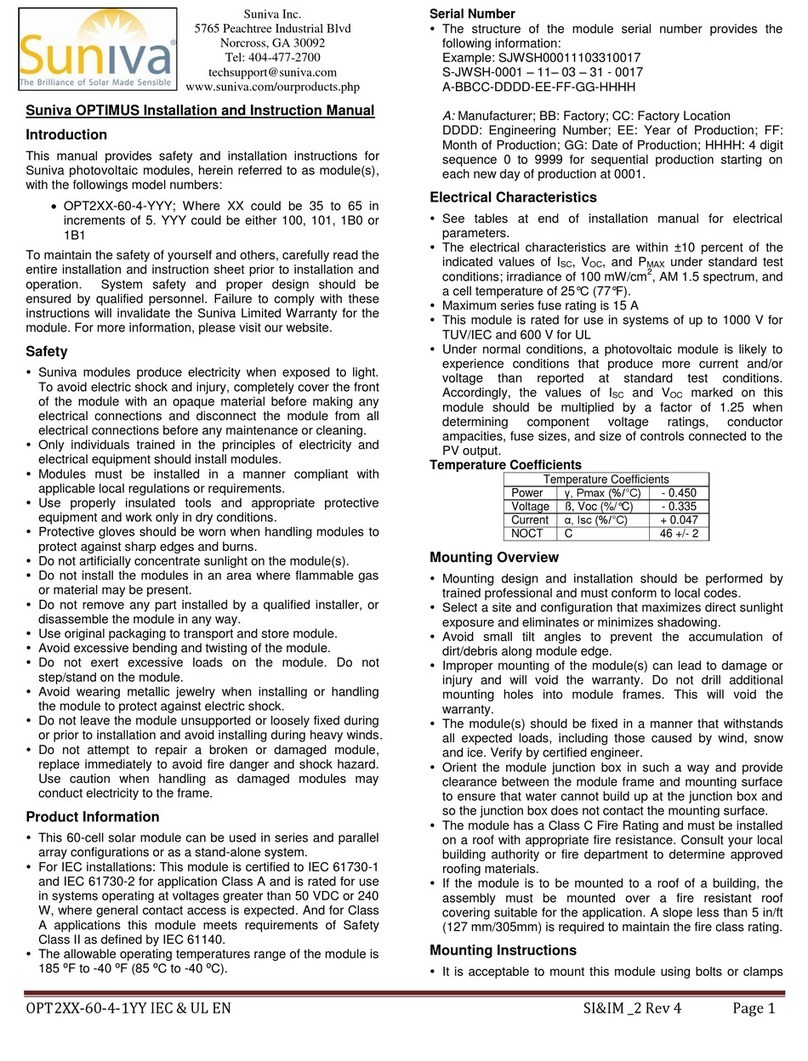
Suniva
Suniva OPTIMUS OPT240-60-4-1 Series Installation and instruction manual

Graco
Graco Dispensit 1052 operation & maintenance

Allmatic
Allmatic ACTION Instructions for installation
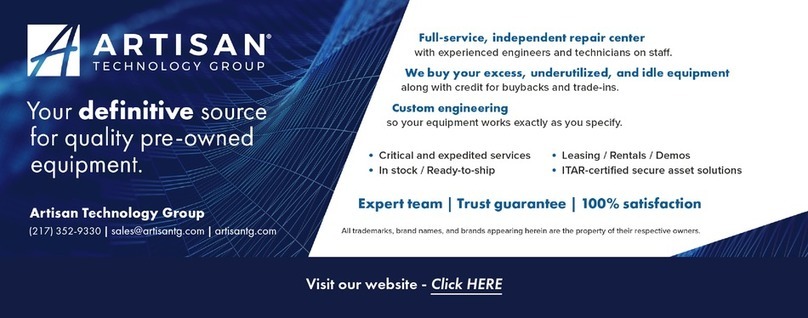
Motorola
Motorola PRPMC750 Installation and use manual
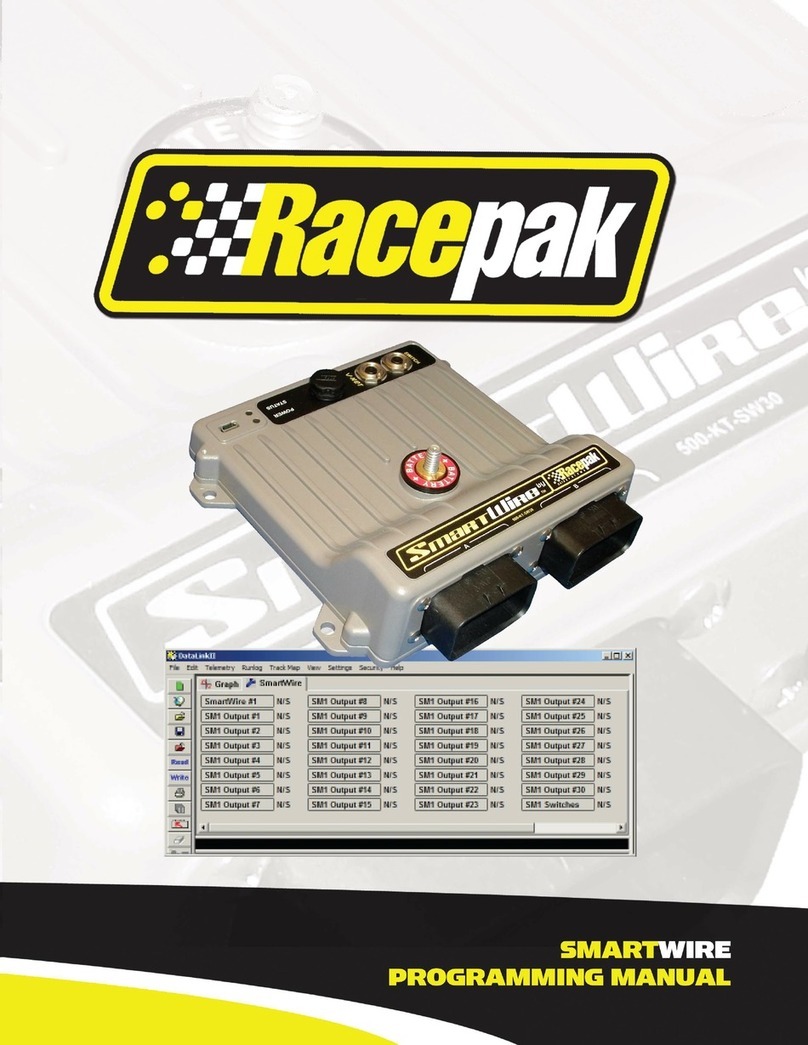
Racepak
Racepak SmartWire Programming manual
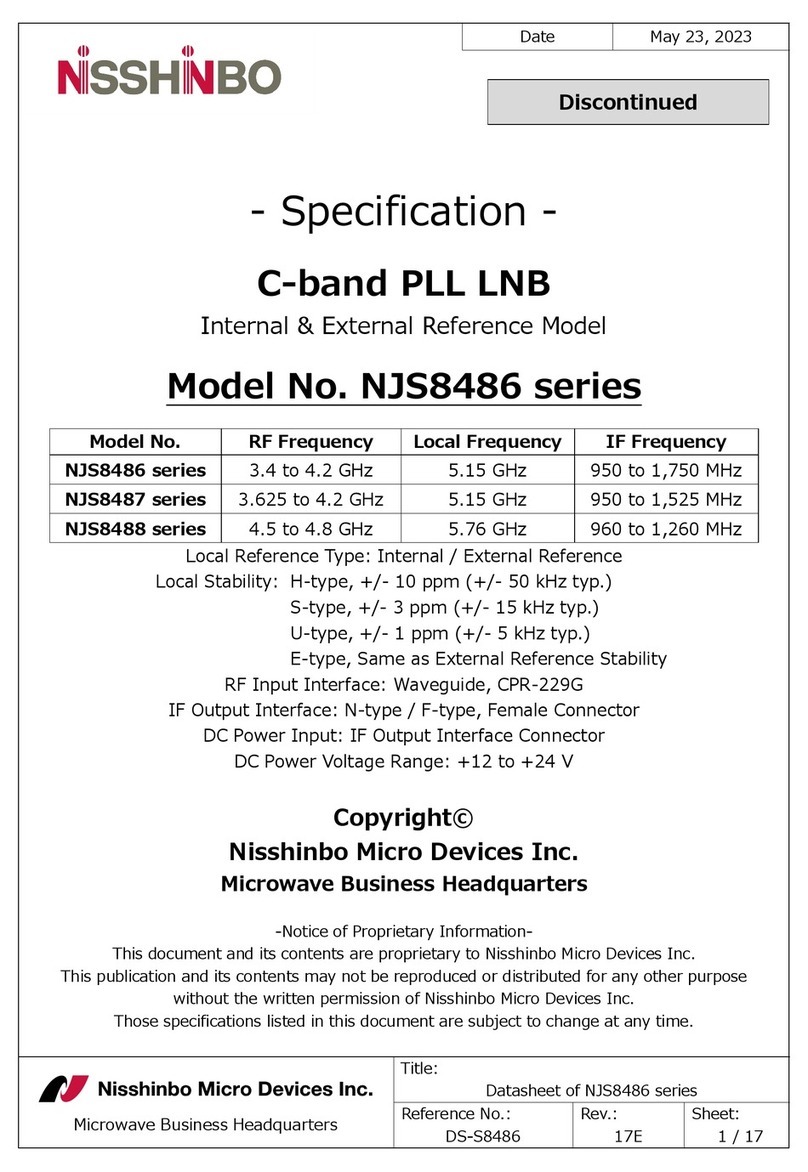
Nisshinbo Micro Devices
Nisshinbo Micro Devices NJS8486 Series manual

Polytron
Polytron SPM-STCT-CI user manual

American Standard
American Standard 6047.8 Series installation instructions