Loren Cook LXUL User manual

1PROPELLER UPBLAST IO&M B51071-005
Receiving and Inspection
Carefully inspect the fan and accessories for any damage
and shortage immediately upon receipt of the fan.
• Turn the propeller by hand to ensure it turns freely and does
not bind
• Check dampers (if included) for free operation of all moving
parts
• Record on the Delivery Receipt any visible sign of damage
TUB
Rotating Parts & Electrical Shock Hazard:
Fans should be installed and serviced by qualied personnel
only.
Disconnect electric power before working on unit (prior to re-
moval of guards or entry into access doors).
Follow proper lockout/tagout procedures to ensure the unit
cannot be energized while being installed or serviced.
A disconnect switch should be placed near the fan in order that
the power can be swiftly cut o, in case of an emergency and
in order that maintenance personnel are provided complete
control of the power source.
Grounding is required. All eld-installed wiring must be com-
pleted by qualied personnel. All eld installed wiring must
comply with National Electric Code (NFPA 70) and all applica-
ble local codes.
Fans and blowers create pressure at the discharge and vac-
uum at the inlet. This may cause objects to get pulled into the
unit and objects to be propelled rapidly from the discharge.
The discharge should always be directed in a safe direction
and inlets should not be left unguarded. Any object pulled into
the inlet will become a projectile capable of causing serious in-
jury or death.
When air is allowed to move through a non-powered fan,
the impeller can rotate, which is referred to as windmilling.
Windmilling will cause hazardous conditions due to unexpect-
ed rotation of components. Impellers should be blocked in po-
sition or air passages blocked to prevent draft when working
on fans.
Friction and power loss inside rotating components will cause
them to be a potential burn hazard. All components should be
approached with caution and/or allowed to cool before con-
tacting them for maintenance.
Under certain lighting conditions, rotating components may
appear stationary. Components should be veried to be sta-
tionary in a safe manner, before they come into contact with
personnel, tools or clothing.
Failure to follow these instructions could result in death or se-
rious injury.
The attachment of roof mounted fans to the roof curb as well
as the attachment of roof curbs to the building structure must
exceed the structural requirements based on the environmen-
tal loading derived from the applicable building code for the
site. The local code ocial may require variations from the rec-
ognized code based on local data. The licensed engineer of
record will be responsible for prescribing the correct attach-
ment based on construction materials, code requirements and
environmental eects specic to the installation.
®
PROPELLER UPBLAST
Upblast Propeller Roof Fans
INSTALLATION, OPERATION AND MAINTENANCE MANUAL
This publication contains the installation, operation and
maintenance instructions for standard units of the Upblast:
Upblast Propeller Roof Fans.
• LXUL & LXUM
• LTU
• LEU
• LXULMO &
LXUMMO
• LTU MO
• LEUMO
• TUB
• EUB
• AUB
• TUD
• EUD
• AUD
• SUB
• SUBH
• AI Upblast
Carefully read this publication and any
supplemental documents prior to any
installation or maintenance procedure.
Loren Cook catalogs, Propeller Upblast and Propeller Roof,
provide additional information describing the equipment, fan
performance, available accessories and specication data.
For additional safety information, refer to AMCA Publication
410-96, Safety Practices for Users and Installers of Industrial
and Commercial Fans.
All of the publications listed above can be obtained from:
• lorencook.com
• 417-869-6474 ext. 166
For information and instructions on special equipment, con-
tact Loren Cook Company at 417-869-6474.

PROPELLER UPBLAST IO&M B51071-0052
Handling
Lift propeller roof ventila-
tors by lifting lugs located in-
side the wind band. Never lift
by the shaft, motor, propeller,
or coupling. If your fan has a
special protective nish, han-
dle with extreme care. Even
a small chip will break the
coating’s continuity and de-
stroy its ability to protect the
metal. Propellers are carefully
balanced to give smooth, vibration
free operation. If the propeller is dam-
aged during handling, it will require re-balancing.
Storage
If the fan is stored for any length of time prior to installation,
store it in its original shipping crate and protect it from dust,
debris and the weather.
Outdoor Storage
To maintain good working condition of the fan when it is
stored outdoors or at a construction site, follow the additional
instructions below.
• Coat the shaft and bearings with grease or rust preventative
compound to help seal out moisture
• Periodically rotate the propeller and operate the dampers (if
supplied) to keep a coating of grease on all internal bearing
parts
• Periodically inspect the fan to prevent damaging conditions
• Block propeller to prevent natural rotation
• Cover the unit with some type of weather cover to prevent
moisture, corrosion, dirt or dust accumulation
Installation
Damper Installation
1. Place the damper inside the curb. Ensure the damper will
open freely for the correct direction of the airow.
2. Secure to curb at the damper shelf by installing at least
two sheet metal screws (#10 x 1/2”) on each side of the
damper, through the tray, with the screw head catching
the ange on the damper. This will prevent the dampers
from lifting.
3. Drill a hole in the curb shelf for conduit needed for motor
wiring.
4. Operate the dampers manually to ensure the blades move
freely. Dampers should be released from full open posi-
tion to check for proper closing.
Safety Recommendation
An inlet guard is recommended. An inlet guard prevents
any large debris from being pulled into the fan and damag-
ing the propeller. The inlet guard is installed on top of the
curb prior to the installation of the fan.
Motor Installation
To prevent damage to the fan during shipping, motors 5HP
and larger and extremely heavy motors (cast iron or severe
duty) are shipped loose and must be eld mounted.
The motor should be mounted so that the motor plate is
between the fan shaft and motor shaft.
• Remove the motor plate mounting bolts and the motor plate
• Remove the motor mounting bolts from the motor plate
• Mount the motor to the motor plate aligning to the appropri-
ate holes
• Place the motor plate on the power assembly and rein-stall
the mounting bolts
Figure 1
1
foot
1/4
inch
Belt and Pulley Installation
If your fan is a direct drive (models AI, AUD, EUD and TUD),
proceed to Wiring Installation.
Belt tension is determined by the sound of the belts when
the fan is rst started. The belts will produce a loud squeal,
which dissipates after the fan is operating at full capacity. If
belt tension is too tight or too loose, lost eciency and dam-
age can occur.
Do not change the pulley pitch diameter to change tension.
The change will result in a dierent fan speed.
• Loosen the motor plate adjustment nuts on motor base and
move motor plate in order that the belts can easily slip into
the grooves on the pulleys. Never pry, roll or force the belts
over the rim of the pulley
• Adjust the motor plate until proper tension is reached. For
proper tension, a deection of approximately 1/4” per foot of
center distance should be obtained by rmly pressing the
belt. Refer to Figure 1
• Lock the motor plate adjustment nuts in place
• Ensure pulleys are properly aligned. Refer to Figure 2
Tolerance
Center
Distance
Max.
Gap
Up through 12” 1/16”
12” through 48 1/8”
Over 48 1/4”
OFFSET ANGULAR OFFSET/ANGULAR
A
W
X
Y
ZB
CENTER
DISTANCE
(CD)
GAP GAP
Pulley Alignment
Pulley alignment is adjusted by loosening the motor pulley set-
screw and by moving the motor pulley on the motor shaft.
Figure 2 indicates where to measure the allowable gap for
the drive alignment tolerance. All contact points (indicated by
WXYZ) are to have a gap less than the tolerance shown in the
Lifting Lugs
Figure 2

3PROPELLER UPBLAST IO&M B51071-005
table. When the pulleys are not the same
width, the allowable gap must be adjusted
by half of the dierence in width. Figure
3illustrates using a carpenter’s square to
adjust the position of the motor pulley until
the belt is parallel to the longer leg of the
square.
Wiring Installation
All wiring should be in accordance with
local ordinances and the National Elec-
trical Code, NFPA 70. Ensure the power supply (voltage,
frequency, and current carrying capacity of wires) is in ac-
cordance with the motor nameplate. Refer to the Wiring Dia-
grams, on page 3.
Lock o all power sources before unit is wired to power
source.
Leave enough slack in the wiring to allow for motor move-
ment when adjusting belt tension. Some fractional motors
have to be removed in order to make the connection with the
terminal box at the end of the motor.
Wiring Diagrams
Single Speed, Single Phase Motor
T-
1
T-
4
Ground B
L2
L1
Ground A
Line
When ground is required, attach to ground A or B with No. 6 thread
forming screw. To reverse, interchange T-1 and T-4.
2 Speed, 2 Winding, Single Phase Motor
Ground A
Ground B
T-1
T-
4
Low Speed
High Speed
L1
L2
Line
When ground is required, attach to ground A or B with No. 6 thread
forming screw. To reverse, interchange T-1 and T-4 leads.
Single Speed, Single Phase, Dual Voltage
Ground B
J-10
T-5
Ground A
Link A
Link B
Low Voltage
Line
L2
L1
Ground A
Link A
and B
L1
L2
Line
Ground B
T-5
J-10
When ground is required, attach to ground A or B with No. 6 thread
forming screw. To reverse, interchange T-5 and J-10 leads.
3-Phase, 9 Lead Motor
456
1
7
2
8
3
9
L1L2L3
456
789
12 3
L1L2L3
Low Voltage
208/230 Volts
High Voltage
460 Volts
3 Phase, 9 Lead Motor
Y-Connection
7
1
6789
456
12 3
Low Voltage
208/230 V
olts
High V
oltage
460 Volts
8
2
4
9
3
5
L
1
L
3
L
2
L1L3
L2
3 Phase, 9 Lead Motor
Delta-Connection
To reverse, interchange any two line leads.
2 Speed, 1 Winding, 3-Phase Motor
Motor
1
2
3
4
5
6
Together
High Speed
Line
L1
L2
L
3
1
2
3
4
5
6
Open
Low Speed
Line
L1
L2
L3
Motor
To reverse, interchange any two line leads. Motors require magnetic
control.
2 Speed, 2 Winding, 3-Phase
L1
T1
T2
T3Low Speed
Low Speed
Low Speed
High Speed
High Speed
High Speed
Motor
T13
T12
T11
L2Line
L3
To reverse, High Speed: interchange leads T11 and T12; Low
Speed: interchange leads T1 and T2; Both Speeds: interchange any
two line leads.
Typical Damper Motor Schematic
Fan
Motor
Damper
Motor*
Second
Damper
Motor
Tr
ansformer** Transformer*
*
L3
L2
L1
For 3-Phase, damper motor voltage should be the same between L1
and L2. For single phase application, disregard L3.
*Damper motors may be available in 115, 230 and 460 volt mod-
els. The damper motor nameplate voltage should be veried prior to
connection.
**A transformer may be provided in some installations to correct the
damper motor voltage to the specied voltage.
Follow the wiring diagram in the disconnect switch and
the wiring diagram provided with the motor. Correctly la-
bel the circuit on the main power box and always identify a
closed switch to promote safety (i.e., red tape over a closed
switch).

PROPELLER UPBLAST IO&M B51071-0054
Fan Installation
The fan support (roof curb) should provide a level surface
for installation. If the roof is pitched more than 1/2:12, a sloped
curb must be used to correct for the incline. If the unit is in-
stalled on a non-level surface, the damper door pivot should
be positioned perpendicular to the peak of the roof. Consult
factory for additional details.
• Place fan over roof opening
• Secure the fan with lag screws, anchor bolts, or other suit-
able fasteners
Final Installation Steps
1. Inspect fasteners and setscrews, particularly fan mount-
ing and bearing fasteners, and tighten according to the
recommended torque shown in the table, Recommended
Torque for Setscrews/Bolts.
2. Inspect for correct voltage with voltmeter.
3. Ensure all accessories are installed.
4. Test the fan to be sure the rotation is the same as indicat-
ed by the arrow marked Rotation.
Do not allow the fan to run in the wrong direction. This
will overheat the motor and cause serious damage.
For 3-phase motors, if the fan is running in the wrong
direction, check the control switch. It is possible to
interchange two leads at this location so that the fan is
operating in the correct direction.
Smoke Control Units Additional Installation Steps
The damper actuator arms are safety bolted at the factory
to prevent damage or personnel injury during handling and in-
stallation. The bolt must be removed for the damper actuator
to operate correctly. Refer to Figure 4.
• Remove Bolt “A” from each of the damper arms
• Be sure that linkage hook “B” is in contact with bolt “C” to
prevent excessive load on the fusible link
The damper arms will not operate unless this bolt is re-
moved. This bolt should be replaced before any maintenance
or repair work is started.
Bolt C
Linkage
Bolt A
Figure 4 - Safety Bolt Removal
Hook B
Operation
Pre-Start Checks
1. Lock out all the primary and secondary power sources.
Inspect fasteners and setscrews, particularly those used
for mounting the unit, and tighten if necessary.
2. Inspect belt tension and pulley alignment. (Remember, if belt
tension is correct, a loud squeal occurs as the fan increases
to full power.)
3. Inspect motor wiring.
4. Ensure the belt touches only the pulleys.
5. Rotate the propeller to ensure it does not rub against the
base.
6. Ensure fan and ductwork are clean and free of debris.
7. Test the fan to ensure the rotation of the propeller is the
same as indicated by the rotation label.
8. Close and secure all access doors.
9. Restore power to unit.
Recommended Torque for Setscrews/Bolts (IN-LB)
Setscrews Hold Down Bolts
Size
Key Hex
Across
Flats
Recommended
Torque Size Recommended
Torque
Min. Max.
#8 5/64” 15 21 3/8”-16 324
#10 3/32” 27 33 1/2”-13 780
1/4 1/8” 70 80 5/8”-11 1440
5/16 5/32” 140 160 3/4”-10 2400
3/8 3/16” 250 290 7/8”-9 1920
7/16 7/32” 355 405 1”-8 2700
1/2 1/4” 560 640 1-1/8”-7 4200
5/8 5/16” 1120 1280 1-1/4”-7 6000
3/4 3/8” 1680 1920 - -
7/8 1/2” 4200 4800 - -
1 9/16” 5600 6400 - -
Start Up
Turn the fan on. In variable speed units, set the fan to its
lowest speed. Inspect for the following:
• Direction of rotation
• Excessive vibration
• Unusual noise
• Bearing noise
• Improper belt alignment or tension (listen for a continuous
squealing noise)
• Improper motor amperage or voltage
If a problem is discovered, immediately shut o the
fan. Lock out all electrical power and check for the
cause of the trouble. Refer to Troubleshooting.
Inspection
Inspection of the fan should be conducted at the rst
30-minute,8-hour and 24-hour intervals of satisfactory op-
eration. During the inspections, stop the fan and inspect as
per the information below.
30-Minute Interval:
Inspect bolts, setscrews, and motor mounting bolts. Adjust
and tighten as necessary.
8-Hour Interval
Inspect belt alignment and tension. Adjust and tighten as
necessary.
24-Hour Interval
Inspect belt tension. Adjust and tighten as necessary.
Maintenance
Establish a schedule for inspecting all parts of the fan. The
frequency of inspection depends on the operating conditions
and location of the fan.
Inspect fans exhausting corrosive or contaminated air within
the rst month of operation. Fans exhausting contaminated air
(airborne abrasives) should be inspected every three months.
Clean the propeller and air inlets if material build-up is exces-
sive. Excessive build-up can cause imbalance and failure of
the propeller.

5PROPELLER UPBLAST IO&M B51071-005
Regular inspections are recommended for fans exhausting
non-contaminated air.
It is recommended the following inspections be con-
ducted twice per year.
• Inspect bolts and setscrews for tightness. Tighten as
necessary
• Inspect belt wear and alignment. Replace worn belts with
new belts and adjust alignment as needed. See Belt and Pul-
ley Installation, page 2
• Bearings should be inspected as recommended in the Con-
ditions Chart
• Inspect for cleanliness. Clean exterior surfaces only. Remov-
ing dust and grease on motor housing assures proper motor
cooling
Lubricants
Loren Cook Company uses petroleum lubricant in a lithium
base conforming to NLGI grade 2 consistency. Other grades
of grease should not be used unless the bearings and lines
have been ushed clean. If another grade of grease is used, it
should be lithium-based.
An NLGI grade 2 grease is a light viscosity, low-torque,
rust-inhibiting lubricant that is water resistant. Its tempera-
ture range is from -30°F to +200°F and capable of intermittent
highs of +250°F.
Motor Bearings
Motors are provided with prelubricated bearings. Any lubri-
cation instructions shown on the motor nameplate supersede
instructions below.
Motor bearings without provisions for relubrication will op-
erate up to 10 years under normal conditions with no mainte-
nance. In severe applications, high temperatures or excessive
contaminates, it is advisable to have the maintenance depart-
ment disassemble and lubricate the bearings after 3 years of
operation to pre-vent interruption of service.
For motors with provisions for relubrication, follow intervals
of the table below.
Relubrication Intervals
Service
Conditions
NEMA Frame Size
Up to and
including 184T 213T–365T 404T and larger
1800 RPM
and less
Over
1800
RPM
1800
RPM
and less
Over
1800 RPM
1800
RPM
and less
Over 1800
RPM
Standard 1-1/2 yrs. 3
months 1 yr. 3 months 6 months 1-1/2
months
Severe 6 months 1-1/2
months 6 months 1-1/2
months 3 months 2 weeks
Motors are provided with a polyurea mineral oil NGLI #2
grease. All additions to the motor bearings are to be with
a compatible grease such as Exxon Mobil Polyrex EM and
Chevron SRI.
Fan Bearings
Fan bearings are lubricated through a grease connector and
should be lubricated by the schedule, Conditions Chart, below
Conditions Chart
RPM Temp °F Greasing Interval
Up to 1000 -30 to 120 6 months
120 to 200 2 months
1000 to 3000 -30 to 120 3 months
120 to 200 1 month
Over 3000 -30 to 120 1 month
120 to 200 2 weeks
Any Speed < -30 Consult Factory
Any Speed > 200 1 week
For best results, lubricate the bearing while the fan is rotat-
ing. Slowly pump grease into the bearing until a slight bead
forms around the bearing seals. Excessive grease can burst
seals thus reduce bearing life.
In the event the bearing cannot be seen, use no more than
three injections with a hand-operated grease gun.
Motor Services
Should the motor prove defective within a one-year period,
contact your local Loren Cook representative or your nearest
authorized electric motor service representative.
Changing Shaft Speed
All belt driven propeller roof fans with motors up to and in-
cluding 5HP are equipped with variable pitch pulleys. To
change the fan speed, perform the following:
• Loosen setscrew on driver (motor) pulley and remove key,
if equipped
• Turn the pulley rim to open or close the groove facing. If
the pulley has multiple grooves, all must be adjusted to the
same width
• After adjustment, inspect for proper belt tension
Speed Reduction
Open the pulley in order that the belt rides deeper in the
groove (smaller pitch diameter).
Speed Increase
Close the pulley in order that the belt rides higher in the
groove (larger pitch diameter). Ensure that the RPM limits of
the fan and the horsepower limits of the motor are maintained.
Maximum RPM
LTU
Size
Max.
RPM
20 2361
24 1964
30 1581
36 1314
42 110 6
48 973
54 829
60 767
AUB
Size
Max.
RPM
24 1585
30 1180
36 1015
42 935
48 845
LXUM
Size
Max.
RPM
24 1650
30 1305
36 1305
42 1200
48 1150
54 900
60 870
72 688
LXUL
Size
Max.
RPM
20 1270
24 1110
30 930
36 720
42 600
48 508
54 478
60 450
LXUM
Size
Max.
RPM
20 1460
24 1400
30 1170
36 860
42 718
48 598
54 522
60 476
LEU Size Max.
RPM
20 1675
24 1650
30 1350
36 1310
42 1210
48 1214
54 946
60 854
TUB, SUB,
SUBH Size
Max.
RPM
20 2633
24 1993
30 1605
36 1314
42 110 6
48 973
54 888
60 783
72 616
AI Ublast
Size
Max.
RPM
31 3500
36 3500
41 3500
47 3500
54 3500
63 2360
72 2360
80 2360
90 2360
103 2271
113 1788
123 1560
140 1492
160 1300

PROPELLER UPBLAST IO&M B51071-0056
Pulley and Belt Replacement
1. Clean the motor and fan shafts.
2. Loosen the motor plate mounting bolts to relieve the belt
tension. Remove the belt.
3. Loosen the pulley setscrews and remove the pulleys from
the shaft. If excessive force is required to remove the pul-
leys, a three-jaw puller can be used. This tool, however,
can easily warp a pulley. If the puller is used, inspect the
trueness of the pulley after it is removed from the shaft.
The pulley will need replacement if it is more than 0.020
inch out of true.
4. Clean the bores of the pulleys and place a light coat of oil
on the bores.
5. Remove grease, rust and burrs from the shaft.
6. Place fan pulley on the fan shaft and the motor pulley on
the motor shaft. Damage to the pulleys can occur when
excessive force is used in placing the pulleys on their re-
spective shafts.
7. After the pulleys have been correctly placed back onto
their shafts, tighten the pulley setscrews.
8. Install the belts on the pulleys. Align and adjust the belts
to the proper tension as described in Belt and Pulley In-
stallation, page 2.
Bearing Replacement
1. The fan bearings are pillow block ball bearings.
2. Remove the wind band and damper assembly to gain ac-
cess to the fan.
3. Loosen the motor plate mounting bolts and remove the
drive belts.
4. Remove the propeller from the shaft.
5. Remove the bearing cover. Remove the four (4) bearing
hold-down bolts and then remove the shaft, bearings, and
driven sheave from the unit as an assembly.
6. Measure and record the location of the bearings and
sheave on the shaft. This will aid the reassembly.
7. Remove the anti-corrosion coating from the shaft with a
suitable degreaser and then remove the pulley from the
shaft. An emery cloth or le may be needed to remove im-
perfections in the shaft left by the setscrews.
8. Remove the bearing from the shaft using a bearing puller.
9. Clean the shaft and bearing bores thoroughly.
10. Place the bearings into position making sure they are not
on a worn section of the shaft. Tapping the inner ring face
with a soft driver may be required. Tighten the setscrews
on the lower bearing.
11. Install the pulley in the correct location on the shaft. Se-
cure the bearing hold-down bolts, but do not fully tighten.
12. Align the setscrews on the top bearing with those on the
lower bearing. Tighten one of them.
13. Rotate the shaft to allow the bearing outer rings to nd
their center of free movement. If your fan is supplied with
a lube line, attach it to the grease connection.
14. Install the propeller on the shaft and adjust bearing posi-
tion to center the propeller in the opening.
15. Tighten hold-down bolts to proper torque. Refer to Rec-
ommended Torque Chart, page 4.
16. Turn the shaft by hand. Resistance should be the same as
it was before hold-down bolts were fully tightened.
17. Tighten bearing setscrews to specied torque.
18. Reassembly the fan.
After 24 hours of continuous operation, tighten the set-
screws to the appropriate torque. This assures the full locking
of the inner race to the shaft. Ensure the socket key or driver
is in good condition with no rounded corners. The key should
be fully engaged in the setscrew and held squarely to prevent
the rounding out of the setscrew socket when applying maxi-
mum torque.
Propeller and Shaft Replacement Precautions
• If the shaft is dropped and bent, it may cause unbalanced
operation of the fan
• When handling the propeller separately from the shaft,
place a support through the hub for lifting, making sure not
to injure the nished bore of the propeller
• Never allow the propeller to rest its entire weight on the
blades. The propeller and shaft can be lifted by slings
around the shaft on each side of the propeller so the propel-
ler is supported by its hub
• If using a chain to lift the propeller, make sure there is su-
cient padding on the shaft and propeller. This prevents the
scoring of the shaft or injury to the propeller. The chain or
cable should be spread with timbers, or braced by some
other method to prevent damage to the propeller side plates
Troubleshooting
Problem and Potential Cause
Low Capacity or Pressure:
• Incorrect direction of rotation. Make sure the fan rotates
in same direction as the arrows on the motor or belt drive
assembly
• Poor fan inlet conditions. There should be a straight clear
duct at the inlet
• Improper propeller alignment
Excessive Vibration and Noise:
• Damaged or unbalanced propeller
• Belts too loose; worn or oily belts
• Speed too high
• Incorrect direction of rotation. Make sure the fan rotates
in same direction as the arrows on the motor or belt drive
assembly
• Bearings need lubrication or replacement
• Fan surge
Overheated Motor:
• Motor improperly wired
• Incorrect direction of rotation. Make sure the fan rotates
in same direction as the arrows on the motor or belt drive
assembly
• Cooling air diverted or blocked
• Improper inlet clearance
• Incorrect fan RPMs
• Incorrect voltage
Overheated Bearings:
• Improper bearing lubrication
• Excessive belt tension

7PROPELLER UPBLAST IO&M B51071-005
1
2
3
4
5
6
7
8
9
10
AUD / EUD / TUD Parts List
Part
No.
Description
AUD (Sizes 24 - 48) EUD (Sizes 20 - 60) TUD (Sizes 20 - 60)
1Damper Stop Damper Stop Damper Stop
2Rubber Bumper(2) Rubber Bumper(2) Rubber Bumper(2)
3Wind Band Wind Band Wind Band
4Cast Aluminum
Propeller Aluminum Propeller Triton®Propeller
5Power Assembly Power Assembly Power Assembly
6Motor Plate Motor Plate Motor Plate
7Lower Drum
Assembly
Lower Drum
Assembly
Lower Drum
Assembly
8Motor Motor Motor
9Damper Rubber
Extrusion (2)
Damper Rubber
Extrusion (2)
Damper Rubber
Extrusion (2)
10 Damper Assembly Damper Assembly Damper Assembly
12
3
4
5
6
7
8
9
10
11
12
13
14
15
16
17
18
19
20
Part
No.
Description
SUB/TUB (Sizes 24 - 72) SUBH (Sizes 24 - 72) TUB with Smoke Control
(Sizes 24 - 72)
1Damper Backstop Damper Backstop Damper Backstop
2Rubber Bumper (2) Rubber Bumper (2) Rubber Bumper (2)
3Damper Rubber Extrusion Damper Rubber Extrusion Damper Rubber Extrusion
4Weather Cover Rubber
Extrusion
Weather Cover Rubber
Extrusion
Weather Cover Rubber
Extrusion
5Motor Plate Motor Plate Motor Plate
6Weather Cover Weather Cover Weather Cover
7Motor Motor Motor
8Driver Sheave Driver Sheave Driver Sheave
9 Belt Set Belt Set Belt Set
10 Split Locking Collar Split Locking Collar Split Locking Collar
11 Driven Sheave Driven Sheave Driven Sheave
12 Bearings (2) Bearings (2) Bearings (2)
13 Bearing Cover Bearing Cover Bearing Cover
14 Lower Drum Assembly Lower Drum Assembly Lower Drum Assembly
15 Shaft Shaft Shaft
16 Heat Slinger (optional) Heat Slinger (optional) Heat Slinger
17 Steel Propeller Steel Propeller Triton®Propeller
18 Spring Loaded Damper
(optional) Spring Loaded Damper Spring Loaded Damper
19 Wind Band Assembly Wind Band Assembly Wind Band Assembly
20 Damper Assembly Damper Assembly Damper Assembly
Parts Numbers
AUD/EUD/TUD
SUB/SUBH/TUB with Smoke Control

PROPELLER UPBLAST IO&M B51071-0058
EUB Sizes 24 - 72
12
3
4
5
6
7
8
9
10
11
12
13
14
15
16
17
18
12
3
4
56
7
8
9
10
11
12
13
14
15
16
17
18
AUB Sizes 24 - 48
Part
No.
Description
EUB (Sizes 24 - 72) AUB (Sizes 24 - 48)
1Damper Backstop Damper Backstop
2Rubber Bumper (2) Rubber Bumper (2)
3 Damper Rubber Extrusion (2) Damper Rubber Extrusion (2)
4Shaft Shaft
5Weather Cover Rubber Extrusion Weather Cover Rubber Extrusion
6Motor Plate Motor Plate
7Weather Cover Weather Cover
8Motor Motor
9Driver Sheave Driver Sheave
10 Belt Set Belt Set
11 Split Locking Collar Split Locking Collar
12 Driven Sheave Driven Sheave
13 Bearings (2) Bearings (2)
14 Bearing Cover Bearing Cover
15 Lower Drum Assembly Lower Drum Assembly
16 Extruded Aluminum Cast Aluminum
17 Wind Band Assembly Wind Band Assembly
18 Damper Assembly Damper Assembly
EUB/AUB
EUB Sizes 24–72
AUB Sizes 24–48

9PROPELLER UPBLAST IO&M B51071-005
19
18
17
16
15
14
12
11 10 9
8
7
6
5
4
3
2
1
13
Part
No.
LXUL/LXUM Description
Size 20-36 Size 42-60
1Damper Stop
Bracket (2)
Damper Stop
Bracket (2)
2Damper Stop
Channel
Damper Stop
Channel
3Damper
Bumper (2)
Damper
Bumper (2)
4Windband Windband
5X.STREAM
Propeller
X.STREAM
Propeller
6Base Weldment Base Weldment
7Motor Plate Motor Plate
8Motor Motor
9Drive Sheave Drive Sheave
10 Belt Belt
11 Driven Sheave Driven Sheave
12 -Locking Collar
13 Bearing (2) Bearing (2)
14 Shaft Shaft
15 Rain Gutter Rain Gutter
16 Damper Door
(2)
Damper Door
(2)
17 Damper Hinge
(4)
Damper Hinge
(8)
18 Damper Pivot
Rod
Damper Pivot
Rod
19 Damper Pivot
Bracket
Damper Pivot
Bracket
LEU Parts List
19
18
17
16
15
14
12
11 10 9
8
7
6
5
4
3
2
1
13
Part
No.
LEU Description
Size 20-36 Size 42-60
1Damper Stop Bracket
(2)
Damper Stop Bracket
(2)
2Damper Stop
Channel
Damper Stop
Channel
3 Damper Bumper (2) Damper Bumper (2)
4Windband Windband
5Extruded Propeller Extruded Propeller
6Base Weldment Base Weldment
7Motor Plate Motor Plate
8Motor Motor
9Drive Sheave Drive Sheave
10 Belt Belt
11 Driven Sheave Driven Sheave
12 -Locking Collar
13 Bearing (2) Bearing (2)
14 Shaft Shaft
15 Rain Gutter Rain Gutter
16 Damper Door (2) Damper Door (2)
17 Damper Hinge (4) Damper Hinge (8)
18 Damper Pivot Rod Damper Pivot Rod
19 Damper Pivot
Brackets (2)
Damper Pivot
Brackets (2)
LXUL/LXUM
LEU

PROPELLER UPBLAST IO&M B51071-00510
19
18
1716
15
14
12
11 10 9
8
7
6
5
4
3
2
1
13
17
18
16
15
14
12 11 10 9
8
7
6
5
20
4
32
1
13
22
19
21
Part No. Description
1Damper Stop Bracket
2Damper Stop Channel
3 Damper Bumper (2)
4Windband
5TRITON® Propeller
6Base Weldment
7Motor Plate
8Motor
9Drive Sheave
10 Belt
11 Driven Sheave
12 Locking Collar
13 Bearings (2)
14 Shaft
15 Rain Gutter
16 Damper Door (2)
17 Damper Hinge
18 Damper Pivot Rod
19 Damper Pivot Bracket
Part
No.
Description
LXULMO/LXUMMO With Smoke Control
1Damper Stop Bracket Damper Stop Bracket
2Damper Stop Channel Damper Stop Channel
3 Damper Bumper (2) Damper Bumper (2)
4Windband Windband
5X.STREAM Series
Propeller
X.STREAM Series
Propeller
6Shaft Shaft
7Bearing Cover Bearing Cover
8Bearings (2) Bearings (2)
9Driven Sheave Driven Sheave
10 Belt Set Belt Set
11 Motor Plate Motor Plate
12 Drive Sheave Drive Sheave
13 Motor Motor
14 Motor Cover Motor Cover
15 Lower Drum Weldment Lower Drum Weldment
16 Damper Pivot Bracket Damper Pivot Bracket
17 Damper Hinge Damper Hinge
18 Damper Pivot Rod Damper Pivot Rod
19 Belt Tunnel (Optional) Belt Tunnel
20 -Heat Slinger
21 Damper Doors (2) Damper Doors (2)
22 -Fire Damper Assembly
LTU
LXULMO/LXUMMO

11PROPELLER UPBLAST IO&M B51071-005
17
16
15
14
12 11 10 9
8
7
6
5
4
13
19
21 18 32
1
20
22
17
16
15
14
12 11 10 9
8
7
6
5
4
3
2
1
13
18
Part
No.
Description
LTUMO With Smoke Control
1Damper Stop Bracket Damper Stop Bracket
2Damper Stop Channel Damper Stop Channel
3 Damper Bumper (2) Damper Bumper (2)
4Windband Windband
5TRITON® Propeller TRITON® Propeller
6Shaft Shaft
7Bearing Cover Bearing Cover
8Bearings (2) Bearings (2)
9Driven Sheave Driven Sheave
10 Belt Set Belt Set
11 Motor Plate Motor Plate
12 Drive Sheave Drive Sheave
13 Motor Motor
14 Motor Cover Motor Cover
15 Lower Drum Weldment Lower Drum Weldment
16 Damper Pivot Bracket Damper Pivot Bracket
17 Damper Hinge Damper Hinge
18 Damper Pivot Rod Damper Pivot Rod
19 Belt Tunnel (Optional) Belt Tunnel
20 -Heat Slinger
21 Damper Doors (2) Damper Doors (2)
22 -Fire Damper Assembly
Part No. Description
1Damper Stop Bracket
2Damper Stop Channel
3 Damper Bumper (2)
4Windband
5E Series Propeller
6Shaft
7Bearing Cover
8Bearings (2)
9Driven Sheave
10 Belt Set
11 Motor Plate
12 Drive Sheave
13 Motor
14 Motor Cover
15 Lower Drum Weldment
16 Damper Pivot Bracket
17 Damper Hinge
18 Damper Pivot Rod
LTUMO
LEUMO

PROPELLER UPBLAST IO&M B51071-00512
Limited Warranty
Loren Cook Company warrants that your Loren Cook fan was manufactured free of defects in materials and workmanship, to the extent stated herein.
For a period of one (1) year after date of shipment, we will replace any parts found to be defective without charge, except for shipping costs which will be
paid by you. This warranty is granted only to the original purchaser placing the fan in service. This warranty is void if the fan or any part thereof has been
altered or modied from its original design or has been abused, misused, damaged or is in worn condition or if the fan has been used other than for the
uses described in the company manual. This warranty does not cover defects resulting from normal wear and tear. To make a warranty claim, notify Loren
Cook Company, General Oces, 2015 East Dale Street, Springeld, Missouri 65803-4637, explaining in writing, in detail, your complaint and referring to
the specic model and serial numbers of your fan. Upon receipt by Loren Cook Company of your written complaint, you will be notied, within thirty (30)
days of our receipt of your complaint, in writing, as to the manner in which your claim will be handled. If you are entitled to warranty relief, a warranty ad-
justment will be completed within sixty (60) business days of the receipt of your written complaint by Loren Cook Company. This warranty gives only the
original purchaser placing the fan in service specically the right. You may have other legal rights which vary from state to state.
June 2019
Corporate Oces: 2015 E. Dale St. Springeld, MO 65803
Phone 417-869-6474 | Fax 417-862-3820 | lorencook.com
7
6
8
5
4
1
2
3Part No. Description
1Damper Stop Assembly
2Damper Assembly
3Lifting Lugs
4Windband
5AI Propeller
6AI Vertical Housing
7 Curb Cap
8Motor
AI Upblast
This manual suits for next models
16
Table of contents
Other Loren Cook Fan manuals
Popular Fan manuals by other brands
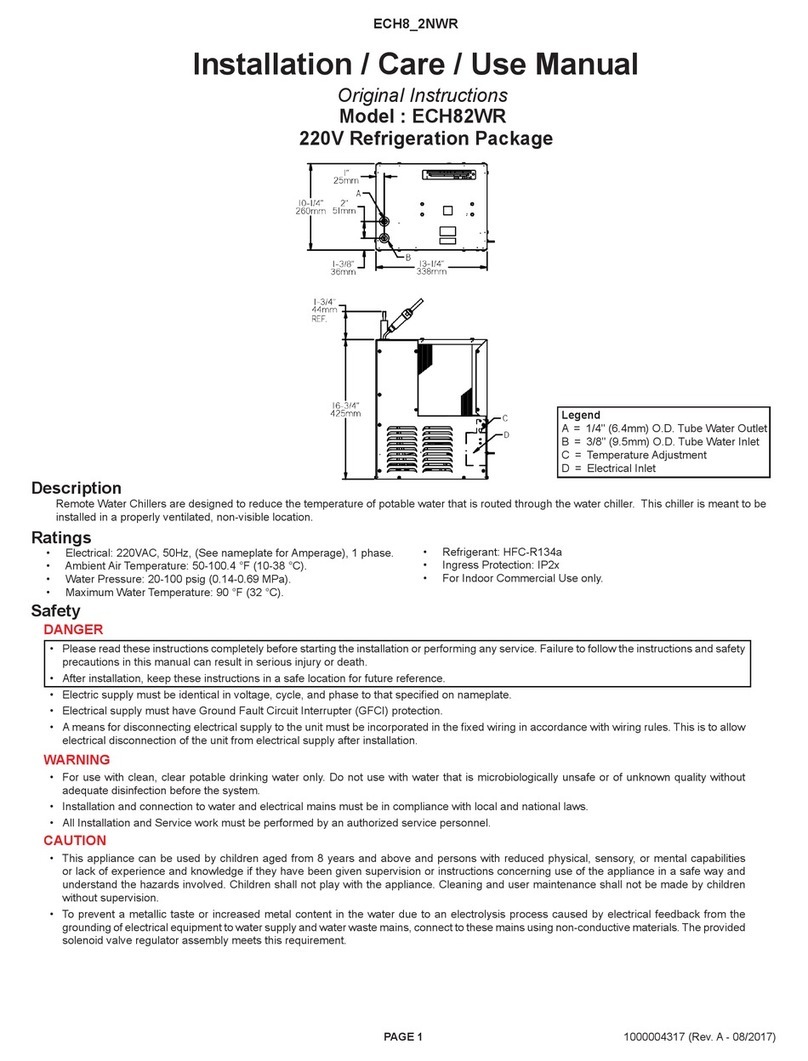
Elkay
Elkay ECH82WR Installation, care & use manual
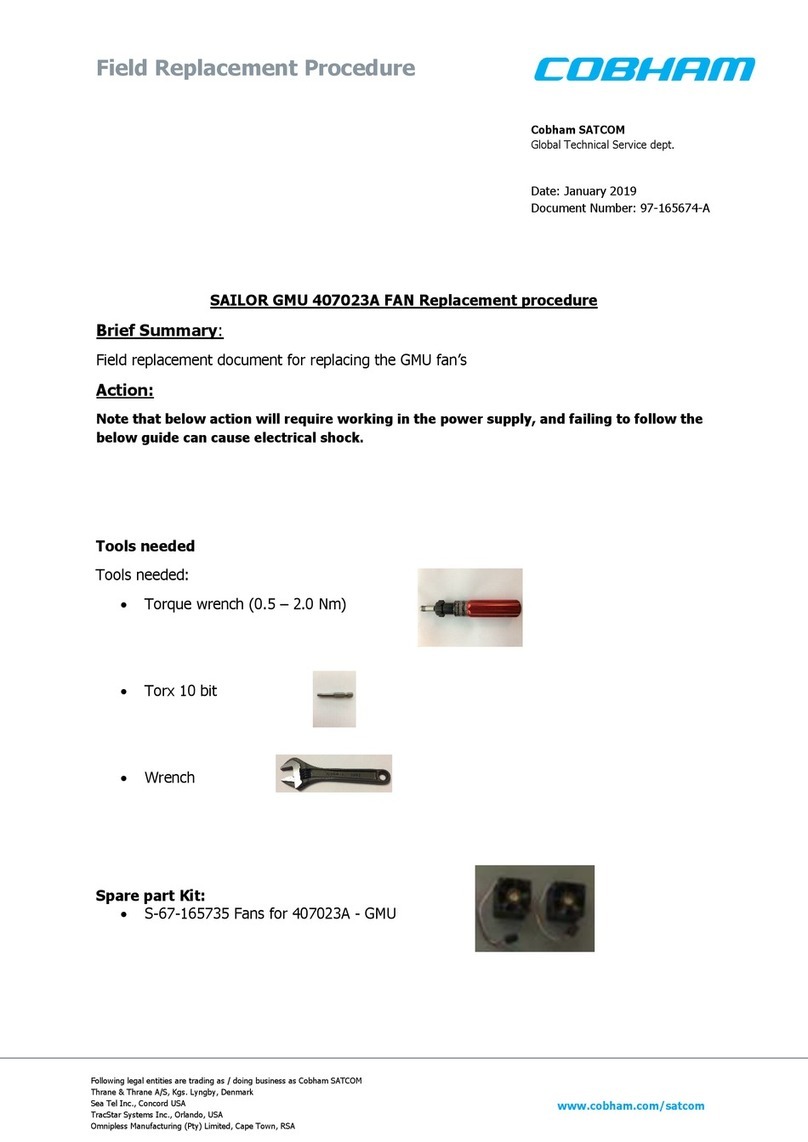
COBHAM
COBHAM SAILOR GMU 407023A Replacement procedure

Litex
Litex COS52OSB5CR installation guide

Inverter
Inverter Pulsar Installation and operation instruction

Bestron
Bestron SUMMER BREEZE AWF40REM instruction manual

Casablanca
Casablanca Wailea 59523 owner's manual

System air
System air Fantech ATMO Series Installation, operation and maintenance manual
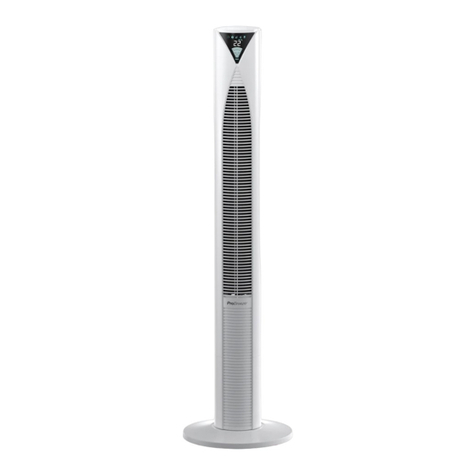
Pro Breeze
Pro Breeze PB-F16-US instruction manual
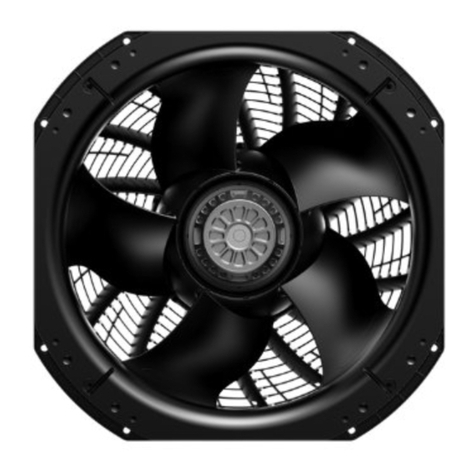
Ebmpapst
Ebmpapst W4E300-ZB02-01 operating instructions
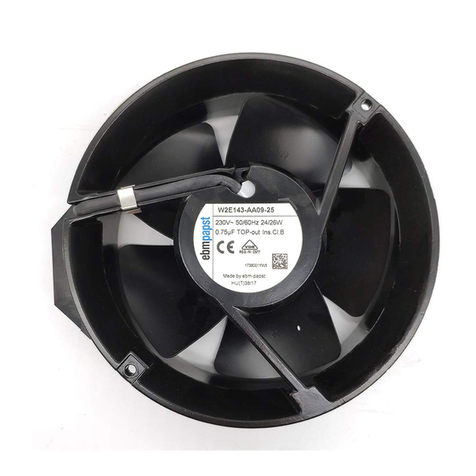
Ebmpapst
Ebmpapst W2E143-AA09-25 operating instructions
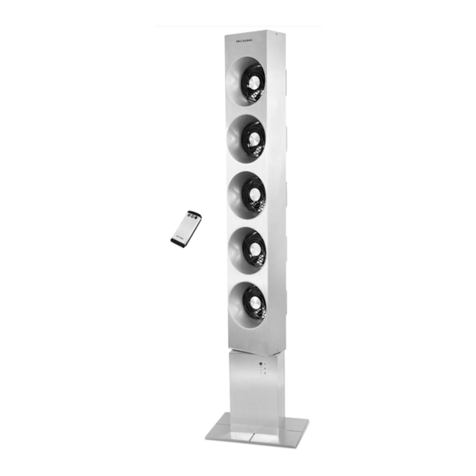
ProKlima
ProKlima TFN-111449.2 instruction manual
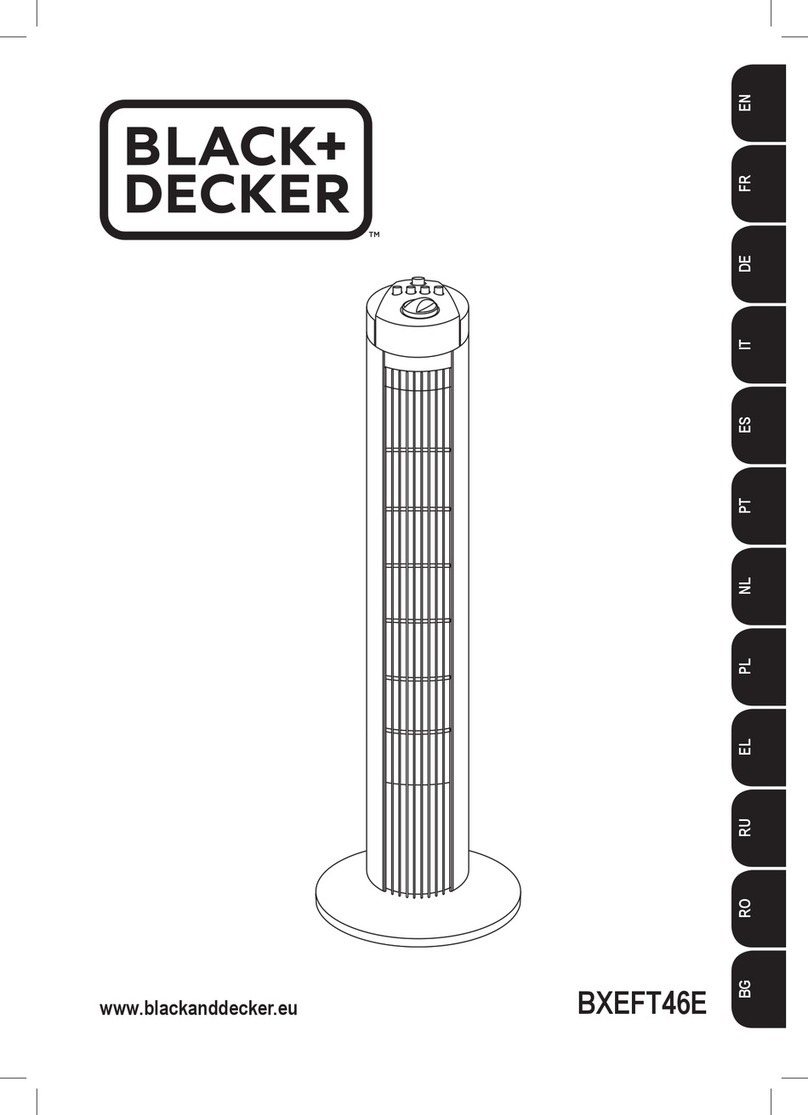
BLACK DECKER
BLACK DECKER BXEFT46E manual