LS ELECTRIC G100 Programming manual

0.4~7.5kW(200V,400V)
AC Variable Speed Drive
G100 Troubleshooting Manual
Safety Instructions
Read this manual carefully before servicing or inspecting this equipment..
Keep this manual within easy reach for quick reference.

1
Quick Reference Table
The following table listed situations frequently encountered while working with inverters. Refer to the
typical situations to quickly and easily locate solutions to your questions.
Situation
Reference
The motor is too noisy.
P. 30
I want to review recent fault trip and warning histories.
P. 14
The motor is producing too much heat.
P. 27
The cooling fan is not working.
P. 31
I want to know how I can keep the inverter when I am not using it.
P. 40
ERR message is displayed on the keypad.
P. 17
I want to initialize all parameters.
P. 13
I want to terminate the inverter.
P. 40
I want to review the input/output module.
P. 35
I want to change the fan when it exceeded the replacement period.
P. 38
I want to change the carrier frequency.
P. 12
I cannot set the parameters.
P. 26
The motor is not working.
P. 30
The motor stops when it is connected to the load or accelerated.
P. 28

2
Contents
INTRODUCTION 3
PRODUCT IDENTIFICATION 4
ASSOCIATION MANUAL 4
SAFETY INFORMATION 5
REVISION RECORD 7
1 BASIC CHECKLIST 8
1.1 Before You Think It Failed 8
1.2 Basic Operations 10
1.3 Change Parameter 12
1.3.1 Change Carrier Frequency 12
1.3.2 Initialize All Parameters 13
1.4 Monitor Fault Trip 14
2 TROUBLESHOOTING 16
2.1 Trips and Warnings 16
2.1.1 Failure/Warning List 17
2.1.2 Troubleshooting Fault Trips 20
2.2 Troubleshooting Other Faults 25
3 MAINTENANCE 31
3.1 Regular Inspection List 31
3.1.1 Daily Inspections 32
3.1.2 Annual Inspections 33
3.1.3 Bi-Annual Inspections 33
3.1.4 Check Input/Output Module 34
3.1.5 Replace Cooling Fan 38
3.2 Storage and Disposal 39
3.2.1 Storage 39
3.2.2 Disposal 39

3
Introduction
Manual Composition
1.1 Before You Think It Failed
1.2 Basic Operations
1.3 Change Parameter
1.3.1 Change Carrier Frequency
1.3.2 Initialize all Parameters
1.3.3 Read and Write Parameters
1.4 Monitor Fault Trip
2.1 Trips and Warnings
2.1.1 Failure/Warning List
2.1.2 Troubleshooting Fault Trips
2.2 Troubleshooting Other Faults
3.1 Regular Inspection List
3.1.1 Daily Inspections
3.1.2 Annual Inspections
3.1.3 Bi-annual Inspections
3.1.4 Check Input/Output Module
3.1.5 Replace Cooling Fan
3.2 Storage and Disposal
3.2.1 Proper Storage of the
Product
3.2.2 Proper Disposal of the
Product
This section explains troubleshooting fault
trips and other common faults.
If problems are not solved, please contact
your vendor or LS ELECTRIC.
This section provides information on
how to maintain the inverters on a
regular basis for different time
periods.
When there is a problem in the
inverter, please check the
input/output module. This is the basic
method to check the hardware.
This section covers check points
when there is a problem in the
inverter.
Then check the parameter settings
using basic operations and the trip
records.
1 Basic Checklist
2 Troubleshooting
3 Maintenance

4
Association Manual
G100 user manual can be downloaded through LS ELECTRIC homepage.
Link : https://www.ls-electric.com/support/download-center
Product Identification
Motor Capacity
.
specifications
Series Name
.
specifications
Input voltage
.
specifications
Keypad
.
specifications
UL Type
.
specifications
EMC Filter
.
specifications
Reactor
.
specifications
Model name
Power source
specifications
Output spec.
0004 – 0.4kW
0008 – 0.75kW
0015 – 1.5kW
0022 – 2.2kW
0040 – 4.0kW
0055 – 5.5kW
0075 – 7.5kW
2 – 3 phase 200V
4 – 3 phase 400V
E – LED Keypad
O – UL Open Type
E – UL Type 1
N – Non-Reactor
N – Non EMC
F – Built-in EMC

5
Safety Information
Read and follow all safety instructions in this manual precisely to avoid unsafe operating
conditions, property damage, personal injury, or death.
Safety symbols in this manual
Danger
Indicates an imminently hazardous situation which, if not avoided, will result in severe injury or
death.
Warning
Indicates a potentially hazardous situation which, if not avoided, could result in injury or death.
Caution
Indicates a potentially hazardous situation that, if not avoided, could result in minor injury
or property damage.
Safety information
Danger
Do not open the cover of the equipment while it is on or operating. Likewise, do not operate
the inverter while the cover is open. Exposure of high voltage terminals or charging are to the
external environment may cause an electric shock. Do not remove any covers or touch the
internal circuit boards (PCBs) or electrical contacts on the product when the power is on or
during operation. Doing so may cause serious injury, death or serious property damage.
Do not open the cover of the equipment even when the power supply to the inverter has been
turned off unless it is necessary for maintenance or regular inspection. Opening the cover
may lead to an electric shock even when the power supply is off.
The equipment may hold charge long after the power supply has been turned off. Use a multi-
meter to make sure that there is no voltage before working on the inverter, motor, or motor
cable.

6
Warning
This equipment must be grounded for safe and proper operation.
Do not supply power to a faulty inverter. If you find that the inverter is faulty, disconnect the
power supply and have the Inverter repaired.
The Inverter becomes hot during operation. Avoid touching the Inverter until it has cooled
down to avoid burns.
Do not allow external objects, such as screws, metal chips, debris, water, or oil to get inside
the Inverter. Allowing external substances inside the Inverter may cause the Inverter to
malfunction or ignite fire.
Do not operate the Inverter with wet hands. Doing so may cause electric shock.
Caution
Do not modify the interior structure/components of the Inverter. Doing so will void the
warranty.
The Inverter is designed for 3-phase motor operation. Do not use the Inverter to operate 1-
phase motor.
Do not place heavy objects on top of electric cables. Doing so may damage the cable and
cause an electric shock.

7
Revision Record
Version
Date
Changed main
contents
Reference Page
V1.0
2019.09
1. First edition
-

8
1 Basic Checklist
1.1 Before You Think It Failed
Items
Check Point
Result
Installed
Environment /
Input/Output
voltage
Is the installed location appropriate?
Does the environment meet the inverters operating conditions?
Does the power source match the inverter’s rated input?
Is the rated output of the inverter sufficient to supply the equipment?
Power Terminal
Wiring
Is the circuit breaker installed on the input side of the inverter?
Is the circuit breaker correctly rated?
Are the power source cables correctly connected to the R/S/T terminals
of the inverter?
(Caution: Connecting the power source to the U/V/W terminals may
damage the inverter)
Are the motor output cables connected in the correct phase rotation
(U/V/W)?
(Caution: Motors will rotate in reverse direction if three phase cables are
not wired in the correct rotation)
Are the cables used to connect power terminals correctly rated?
Is the inverter grounded properly?
Are the power terminal screws and the ground terminal screws tightened
to their specific torques?
Are the overload protection circuits installed correctly on the motors (if
multiple motors are running using one inverter)?
Is the inverter separated from the power source by a magnetic contactor
(if a braking resistor is in use)?
Are advanced-phase capacitors, surge protection and electromagnetic
interference filters installed correctly?
(These devices MUST NOT be installed on the output side of the
inverter)

1. Basic Checklist
9
Items
Check Point
Result
Control Terminal
Wiring
Are STP (shielded twisted pair) cables used for control terminal wiring?
Is the shielding of the STP wiring properly grounded?
If 3-wire operation is required, are the multi-function input terminals
defined prior to the installation of the control wiring connections?
Did you wire the control cables after setting the parameters?
Are the control cables properly wired?
Are the control terminal screws tightened to their specified torques?
Is the total cable length of all control wiring less than 165ft (50m)?
Is the total length of safety wiring less than 100ft (30m)?
Miscellaneous
Are optional cards connected correctly?
Is there any debris left inside the inverter?
Are there any cables (contacting adjacent terminals) creating a potential
short circuit risk?
Are the control terminal connections separated from the power terminal
connections?
Have the capacitors been replaced if they have been in use for more
than 2 years?
Has a fuse been installed for the power source?
Has a fuse been installed for the power source?

1. Basic Checklist
10
1.2 Basic Operations
About the Keypad
The keypad is composed of two main components – the display and the operation (input) keys. Refer to
the following illustration to identify part names and functions.
About the Display
The following table lists display part names and their functions.
No.
Name
Function
❶
7-Segment Display
Displays current operational status and parameter information.
❷
SET Indicator
LED flashes during parameter configuration and when the ESC key
operates as the multi-function key.
❸
RUN Indicator
LED turns on (steady) during an operation, and flashes during
acceleration or deceleration.
❹
FWD Indicator
LED turns on (steady) during forward operation.
❺
REV Indicator
LED turns on (steady) during reverse operation.

1. Basic Checklist
11
The table below lists the way that the keypad displays characters (letters and numbers).
Display
Number/
character
Display
Number/
character
Display
Number/
character
Display
Number/
character
0
A
K
U
1
B
L
V
2
C
M
W
3
D
N
X
4
E
O
Y
5
F
P
Z
6
G
Q
7
H
R
8
I
S
Operation Keys
Key
Key name
Function Description
[RUN]
Used to run the inverter.
[STOP/RESET]
STOP: Stops the inverter.
RESET: Resets the inverter if a fault or failure occurs.
[▲] , [▼]
Switches between codes, or increases or decreases parameter values.
[MODE/SHIFT]
Moves between groups or moves to the digit on the left when setting the
parameter. Press the MODE/SHIFT key once again on the maximum
number of digits to move to the minimum number of digits.
[ENTER]
Switches from the selected state of parameter to the input state.
Edits parameter and apply change.
Accesses the operation information screen during failure on the failure
screen.
[Volume]
Used to set the operation frequency.
* Operates as ESC key if two keys out of [MODE/SHIFT] key, [▲] key and [▼] key are entered at the same
time.
- Press ESC in the group navigation mode to go to the initial screen (the frequency display screen).
- Press ESC in the mode to change parameter to go to group navigation mode without saving.
Caution
Install a separate emergency stop switch in the circuit. The [STOP/RESET] key on the keypad works
only when the inverter has been configured to accept an input from the keypad.

1. Basic Checklist
12
1.3 Change Parameter
1.3.1 Change Carrier Frequency
The following example demonstrates how to configure carrier frequency by modifying CN.4 from
15Hz to 5 Hz. It is possible to configure the parameters for different codes in any other group in the
same method.
Step
Instructions
Keypad Display
1
Shift to CN group 4 code.
2
Press [ENT] key.
Display shows 15 which is the current CN.4 code parameter value.
3
Press [▼] key multiple times until it becomes 5 (wanted value).
4
Press [ENT] key.
The set parameter flickers.
5
Press [ENT] key again to save.
Display shows CN.4. The parameter value has changed.
Adjust motor operational noise by changing carrier frequency settings. Power transistors (IGBT) in
the inverter generate and supply high frequency switching voltage to the motor. The switching speed
in this process refers to the carrier frequency. If the carrier frequency is set high, it reduces
operational noise from the motor, and if the carrier frequency is set low, it increases operational noise
from the motor.
There are advantages and disadvantages depending on carrier frequency setting.
Item
Carrier Frequency
LOW
HIGH
Motor noise
↑
↓
Motor temperature
↑
↓
Inverter heat Loss
↓
↑
High frequency
↑
↓
Inverter noise
↓
↑
Inverter leakage current
↓
↑
c n .4
15
5
05
c n . 4
15
5
05
c n . 4

1. Basic Checklist
13
1.3.2 Parameter Initialization
The following example demonstrates parameter initialization using code dr.93 (Parameter Initialization) in
the Drive group.
Step
Instructions
Keypad Display
1
Go to code 0 in the Drive group.
2
Press the [ENT] key.
The current parameter value "9" will be displayed.
3
To make the target value "93", press the [▼] key to change
the ones' place value to "3".
4
Press the [MODE] key to move to the tens' place value.
5
To make the target value "93", press the [▲] or [▼] key
to change the tens' place value "9".
6
Press the [ENT] key.
Code dr.93 will be displayed.
7
Press the [ENT] key once again.
The current parameter value for code dr.93 is set to 0
(Do not initialize).
8
Press the [▲] key to change the value to 1 (All Grp), and
then press the [ENT] key.
The parameter value will flash.
9
Press the [ENT] key once again.
Parameter initialization begins. Parameter initialization is
complete when code dr.93 reappears on the display.
Note
Following parameter initialization, all parameters are reset to factory default values.
Ensure that parameters are reconfigured before running the inverter again after an initialization.
dr.0
9
3
03
93
dr.93
0
1
dr.93

1. Basic Checklist
14
1.4 Monitor Fault Trip
The following shows an example procedure how to monitor trips in Operation group.
1
Refer to the example keypad display.
An over current trip fault has occurred.
2
Press the [ENT] key, and then the [▲] key.
The operation frequency at the time of the fault (30.00 Hz) is
displayed.
3
Press the [▲] key.
The output current at the time of the fault (5.0 A) is displayed.
4
Press the [▲] key.
The operation status at the time of the fault is displayed.
ACC on the display indicates that the fault occurred during
acceleration.
5
Press the [STOP/RESET] key.
The inverter resets and the fault condition is cleared. The
frequency reference is displayed on the keypad.
If a warning situation occurs while operating with the entered frequency, a
display and the current screen will flash in 1 second intervals. Refer to 6.3 Under load
Fault Trip and Warning on page 18 for more details.
oct
30.00
5.0
acc
30.00
Over
Current
Trip
Acceleration
Current (A)
Frequency

1. Basic Checklist
15
Multiple Failures at the same time
It is possible to review the information of maximum 3 Trips when multiple trips occurred at the
same time.
Check Trip History
The table below is an example how to monitor trip history.
Group
Code
Code Description
Set value
Set range
Initial
Value
Unit
Function
Group 2
Pr91
Fault History 1
-
~
Pr95
Fault History 5
-
Pr96
Delete Fault History
-
0 ~ 1
0
It is possible to save maximum 5 Trip information that occurred while operating. The figure below
demonstrates how to review each Trip information.
Delete Trip History
Change parameter
value to 1 then
press [ENT]
pr. 9 6
pr. 0
1
pr. 9 1
p r . 0
o v t
pr. 9 5
l v t
3
Simultaneous
trips
Over load
Over Voltage
Over Current

2. Troubleshooting
16
2 Troubleshooting
This chapter explains how to troubleshoot when the protective functions, fault trips, warning signals, or a
fault occurs while operating the inverter. If the inverter does not work as expected after following the
suggested troubleshooting steps, please contact the LSIS Customer Service Center.
2.1 Trips and Warnings
The Inverter will stop operating or send out a warning signal when it detected a fault. The keypad
will show brief information of the trip and warning signal. If the model is using the LCD keypad, the
LCD will show detailed information.
Up to 5 failures can be saved and can be found in code Pr.91. When there are more than 2 trips, the
keypad display will show in the order of priority. The LCD will show in the order the fault occurred.
Failure history is saved by either resetting the Inverter or when the inverter turns off due to low
voltage failure. If the number of failures exceeds 5, the last 5 messages will be deleted automatically.
The following is how the fault conditions are categorized:
•Level: After the fault is corrected, the trip or warning signal disappears. The fault is not saved in
the fault history.
•Latch: After the fault is corrected, the trip or warning signal disappears once the Inverter is reset.
•Fatal: After the fault is corrected, the trip or warning signal disappears when conducted the
following procedure. Turn off the Inverter and wait until the charge indicator light goes off. Then,
turn on the Inverter. If the Inverter still failed, please contact the supplier or LS ELECTRIC
Customer Service Center.

2. Troubleshooting
17
2.1.1 Failure/Warning List
The following table shows a list of faults and warning signals that can occur while operating G100.
Category
KPD Display
Details
Page
Critical
Latch
(Over Current1)
Trip from overcurrent
P. 21
((Over Voltage)
Trip from overvoltage
P. 22
(External Trip)
Trip from external signals
-
(NTC Open)
Trip from temperature sensors
P. 25
(Over Current2)
Trip from ARM short current
P. 22
(Option Trip-x*)
Option Trip *
-
(Over Heat)
Inverter overheat
P. 24
(Out Phase Open)
Trip from output phase open
P. 23
(In Phase Open)
Trip from input phase open
P. 23
(Inverter OLT)
Trip from Inverter Overload
P. 21
(Ground Trip**)
Trip from ground fault **
P. 22
(Fan Trip)
Trip from fan operation
P. 24
(E-Thermal)
Trip from overheat of motor
P. 20
(Pre-PID Fail)
Trip due to Pre-PID failure
-
(IO Board Trip)
Trip from IO Board connection
P. 24
(Ext-Brake)
Trip from External brake
-
(No Motor Trip)
Trip due to no motor
-
(Low Voltage2)
Low voltage during operation
-
(Over torque trip1)
Trip from Over torque 1
oct
o v t
e x t
n t c
oc2
opt
oht
pot
ipo
i o l
gft
fan
e t h
pid
iot
x b r
n m t
lv2
o t d 1

2. Troubleshooting
18
Category
KPD Display
Details
Page
(Under torque trip1)
Trip from Under torque 1
(Over torque trip2)
Trip from Over torque 2
(Under torque trip2)
Trip from Under torque 2
-
Level
(Low Voltage)
Trip due to low voltage
P. 23
(BX)
Trip from Emergency stop
-
(Lost Command)
Trip from lost command
-
Fatal
(EEP Err)
External memory error
P. 20
(ADC Off
Set)
Analog input error
P. 20
(Watch
Dog)
Trip from CPU watchdog
P. 20
Minor Failure
(Over Load)
Trip from Motor overload
P. 20
(Under Load)
Trip from Motor under load
P. 20
Warning
(Lost Command)
Warning for lost command
-
(Over Load)
Warning for Motor overload
-
(Under Load)
Warning for Motor under load
-
(Inverter OLT)
Warning for Inverter overload
-
(Fan Warning)
Warning for fan operation
-
(DB Warn %ED)
Warning for braking resistance %
-
(Retry Tr Tune)
Warning for TR turning retrial
(Fan Exchange)
Warning for fan exchange
(Overheat Pre
Alarm)
Warning for Inverter overheat
* ONLY OCCURS WHEN USING THE OPTION BOARD.
** The Ground Trip (GFT) feature is not provided in products under 4.0 kW except for 4.0 kW 200 V and
otd2
utd2
lvt
bx
lor
hwt
eep
hwt
adc
hwt
w d o g
o l t
u l t
l c w
o l w
u l w
i o l w
f a n w
d b w
trer
e f a n
o h
u t d 1

2. Troubleshooting
19
2.2 kW 200 V. An over current trip (OCT) or over voltage trip (OVT) may occur during low resistance
grounding.
Table of contents
Other LS ELECTRIC Inverter manuals
Popular Inverter manuals by other brands
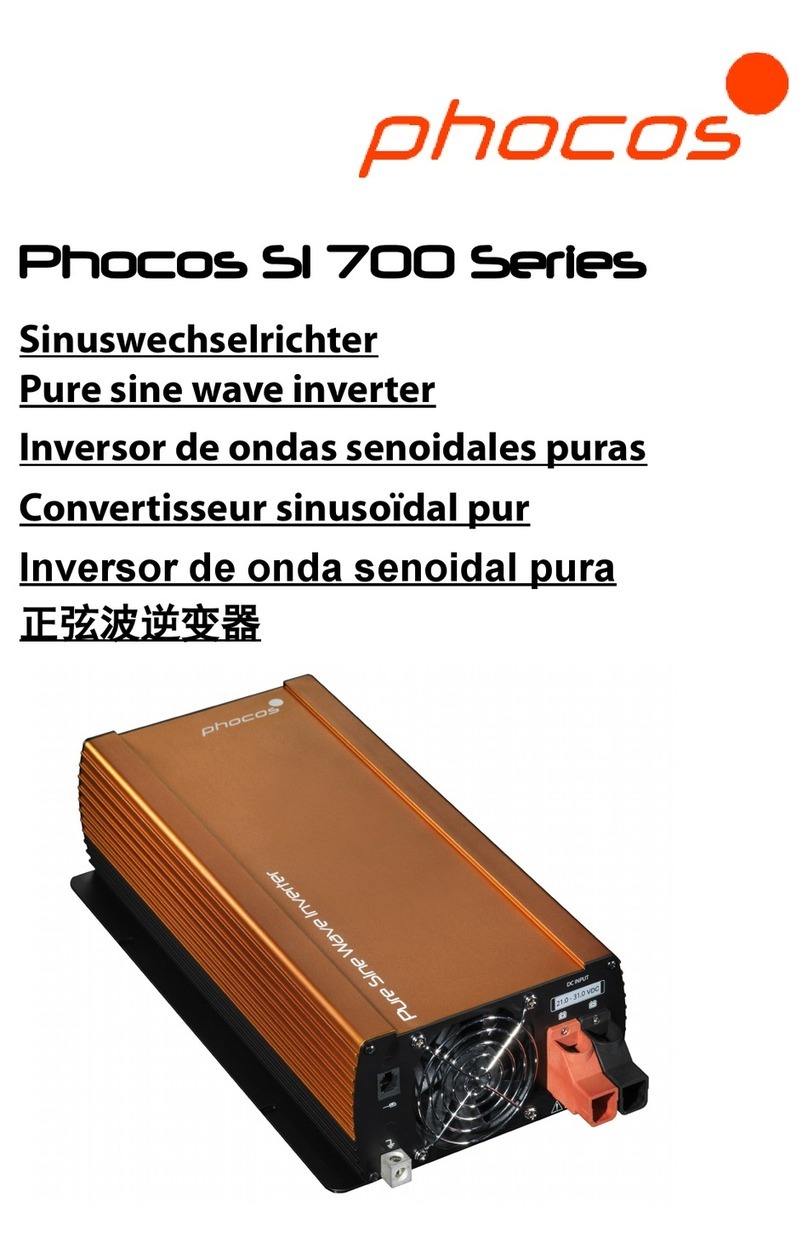
Phocos
Phocos SI700-24110 user manual

TECO-Westinghouse Motor
TECO-Westinghouse Motor GA7200 Operation manual
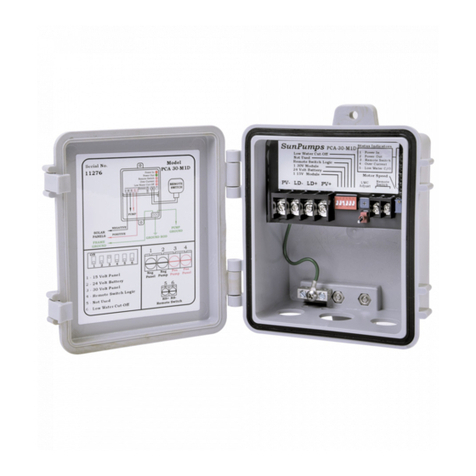
SUNPUMPS
SUNPUMPS SDS Series Operation and installation manual

HP
HP E1340A user manual
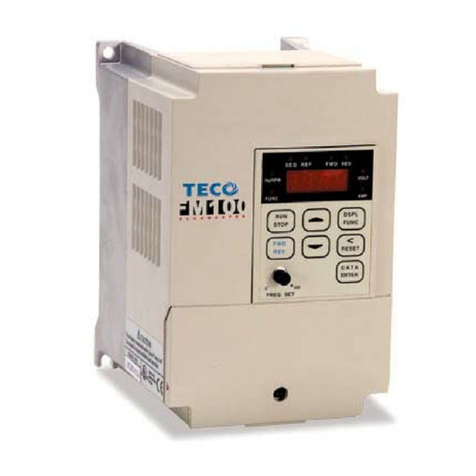
TECO-Westinghouse
TECO-Westinghouse FLUXMASTER 100 Series MAINTENANCE and Operation manual
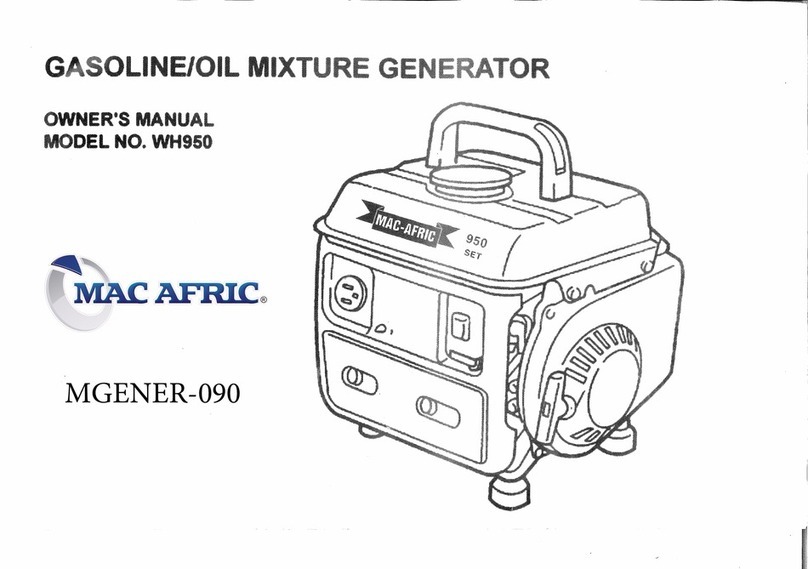
Mac Afric
Mac Afric WH950 owner's manual