Madill 3000 Manual

3000/4000 LOG LOADER
OPERATION & MAINTENANCE MANUAL

TABLE OF CONTENTS
SAFETY INDICATORS......................................................................................................1
FOREWORD......................................................................................................................2
MACHINE OVERVIEW ......................................................................................................3
GENERAL LAYOUT...........................................................................................................4
EMERGENCY EXIT...........................................................................................................5
Emergency Exit Operation...................................................................................................... 5
Emergency Roof Exit.............................................................................................................. 5
Outside Release:...................................................................................................................... 6
Alternative Side Window Exits .............................................................................................. 6
SAFETY PRECAUTIONS ..................................................................................................7
Before you start....................................................................................................................... 7
After Transporting .................................................................................................................. 7
Starting Up.............................................................................................................................. 7
While Operating...................................................................................................................... 7
Travelling................................................................................................................................ 8
Before Performing Service ..................................................................................................... 7
Night Switch ........................................................................................................................... 8
Overloading............................................................................................................................. 8
Fire prevention........................................................................................................................ 9
Welding Precautions............................................................................................................. 10
Fuse Panel............................................................................................................................. 11
Fuse Ratings.......................................................................................................................... 12
MACHINE FUNCTIONS...................................................................................................13
Heeler Joystick Controls....................................................................................................... 13
Butt N’ Top Joystick Controls .............................................................................................. 14
Keypad Controls ................................................................................................................... 15
Key Switch............................................................................................................................ 16
Pilot isolator.......................................................................................................................... 16
Air ConditioningUnit ........................................................................................................... 16
Travel - Left & Right Pedals ................................................................................................. 16
DiagnosticPlug..................................................................................................................... 16
Stereo .................................................................................................................................... 17
Seat Controls ......................................................................................................................... 21
Secondary House Tilt Location ............................................................................................ 22

INTERFACE & WARNING LIGHTS .................................................................................23
Main Display......................................................................................................................... 23
Warning Lights and Buzzers................................................................................................. 24
Climate Control..................................................................................................................... 25
Joystick Set-up...................................................................................................................... 26
Engine Coolant/ Hydraulic Oil Temperature........................................................................ 29
Engine Oil Pressure............................................................................................................... 29
Voltmeter............................................................................................................................... 29
Fuel/ DEF Level Gauge......................................................................................................... 30
Low Fuel/ DEF ..................................................................................................................... 30
Hour Meter............................................................................................................................ 30
Hydraulic Filter ..................................................................................................................... 30
SERVICE & LUBRICATION.............................................................................................31
Lubrication............................................................................................................................ 31
Fuel Tank............................................................................................................................... 32
Hydraulic Oil Tank................................................................................................................ 32
Urea (DEF) Tank .................................................................................................................. 32
Engine Crankcase.................................................................................................................. 32
Radiator................................................................................................................................. 32
Batteries................................................................................................................................. 32
Engine Oil Filter.................................................................................................................... 33
Hydraulic Return Filter ......................................................................................................... 33
Primary Fuel Filter/WaterSeparator....................................................................................... 33
SecondaryFuel Filter (4000 ONLY)..................................................................................... 33
Engine Air Cleaner Filter....................................................................................................... 33
Swing Drive Gearbox............................................................................................................ 33
Track Drive Gearbox............................................................................................................. 33
Tracks, Rollers & Rails......................................................................................................... 34
Third Party/Second-Hand Attachments................................................................................ 34
3000 Log Loader Service & Lubrication Chart.................................................................... 36
4000 Log Loader Service & Lubrication Chart.................................................................... 37
GENERAL INFORMATION..............................................................................................38

1
SAFETY INDICATORS
For your safety it is imperative to read and comprehend this operator’s manual before
operating or providing service on the Madill Log Loader. Through this manual these
symbols will be used to draw your attention to safety information.
(Red)
Indicates an imminently hazardous situation which, if not avoided, will result in death or
serious injury. This signal word is to be limited to the most extreme situations.
(Orange)
Indicates a potentially hazardous situation which, if not avoided, could result in death or
serious injury.
(Yellow)
Indicates a potentially hazardous situation which, if not avoided, may result in minor or
moderate injury. It may also be used to alert against unsafe practices.
(Blue)
Indicates information pertinent to the operation and maintenance of the machine, which,
if not heeded, may result in premature component wear or failure.

2
FOREWORD
The operation and maintenance manual is designed to familiarize the operator with the
machine and all the necessary information so they may take full advantage of the built-
in capabilities. If the machine is operated and maintained properly, it will lessen the
need for costly out-of-warranty repairs and downtime. For this reason, it is imperative
that the basic needs of the machine be satisfied. The machine must be lubricated with
the specified lubricants at the recommended intervals.
When ordering parts, please include the
Madill serial number of the machine and
Volvo serial number of the engine.
Note: Madill reserves the right to make technical changes on the machine without notice.
Between boom pins

3
When checking for leaks in the
hydraulic system, use a piece of
cardboard or wood. A small
stream of high pressure oil can
penetrate the skin and cause
serious injury.
DO NOT USE YOUR HAND OR
FINGERS TO SEARCH FOR
LEAKS.
If you are struck by pressurized
hydraulic fluid, seek medical
attention immediately.
During break in period (first
100-200 hours of operation)
higher oil consumption is
normal. For this reason,
check the oil level more
frequently than the normal
recommendation.
MACHINE OVERVIEW
When the machine is first delivered, it is
important to go through a series of inspections
and checks before placing the machine in
service.
Checking the positions of the shipping blocks
supporting the machine can indicate damage
that may have occurred during shipping. All
blocking should be tightly in place and all
cables should be properly tensioned. Loose
cables and blocks may mean the machine has
been jarred or subjected to unusual vibration;
this could mean loose parts and bolts. Inspect
the machine surface for damage. Walk around
the machine and perform a visual inspection.
Before the machine is run, the oil level in the
engine should be checked to ensure it is at the
proper level. Also check the coolant level and
concentration in the radiator. Hydraulic fluid in
the reservoir should be in the proper range
pointed out on the sight glass; do not overfill
this, room must be allowed for fluid expansion
due to heat. Check the oil level in all gearboxes. Consult the Service & Lubrication
Section for correct service procedures. Lubricate all fittings to be sure they will accept
grease.
Read the procedure for machine start-up before running the engine on
assembled machine.
Start and run the engine until it warms up. Cycle the
various functions and monitor the system for
unexpected behavior such as stalling or pressure
loss.
Normally the first hours of operation or break in
period are the most crucial to the machine. It is at
this time that bolts loosen due to wearing-in process
and metal contact is greatest in the hydraulic system.
Open the doors of the machine and look over the
wiring, hoses, clamps and piping. Verify the fluid
levels of the engine, radiator and hydraulic reservoir
are still sufficient. Inspect the side frames for oil on
the rollers and the drive gear boxes.

4
GENERAL LAYOUT

5
EMERGENCY EXIT
The Madill Log Loader is equipped with an emergency exit. To ensure the proper
operation of this exit, regular inspection and proper maintenance is essential. The
latch and knobs should be checked for proper operation regularly and lubricated as
required.
This exit should be tested / opened monthly.
Emergency Exit Operation
The window located in the roof of the cab serves as the secondary emergency exit
for this machine
Emergency Roof Exit
Inside Release:
1. Pull down on rubber latches.
2. Move seated ball out of retaining clips.
3. Swing the window up.

6
Outside Release:
1. Unscrew the two outside star knobs and remove them.
2. Push threaded rods through emergency exit housing.
3. Swing window open.
Alternative Side Window Exits
Inside Release:
1. Unscrew the three star knobs that run
up the edge of the window
2. Push threaded rod through cab wall
3. Swing window open
The Alternate Side Window
Exists are only operable from
inside the cab. There is no
outside release for these
windows.

7
Starting spray of any kind is
never permitted
NEVER start the engine
without an air filter in place
Cab to Riser bolts to be
torqued to 1100 Ft.-lb. per bolt
with Loctite C5-A applied.
SAFETY PRECAUTIONS
Before you start
Know your machine; become familiar with the machine’s work envelope/area. Adhere
to proper cleaning and maintenance schedules. Do not operate the machine without
wearing PPE as per your worksite and/or local regulations. Ensure protective guards
are in place. Check height, weight and width restrictions for your work area. Be sure
you know about any hazards, such as power lines. Be familiar with the hand signals
used in your workplace.
After Transporting
Always ensure all six cab to riser mounting bolts
are installed and properly torqued.
Starting Up
Make sure all controls are in proper position for
starting. Check for warning tags. Start the machine
only from the operator’s cab and do not leave the
cab while the engine is running. Warm the
machine up gradually. Operate the machine to
confirm correct functions. Report any unusual
noises or conditions for immediate repair.
Before Performing Service
Place attachment on ground, shut off engine and
remove keys from ignition. Attach a “DO NOT
OPERATE” tag in an obvious place in operator’s cab.
While Operating
PAY ATTENTION! Know the working range of your machine. Know where any
obstructions might be. Be sure everyone is in the clear before moving any part of the
machine. Never swing or position any attachment or load over ground crew or
vehicles. Never allow anyone to ride on any attachment or load. Never attempt to
operate the machine from any position outside the operator’s cab. Never operate in a
location where the machine or load may contact electric power lines. ALWAYS
operate with seat belt fastened.

8
Before performing any
service on this machine,
the Night switch must be
turned to the OFF position,
unless otherwise specified
for testing procedures.
Overloading the machine
may result in rollover which
may cause serious injury
or death.
Travelling
Always ensure that the working area is free of persons before swinging or travelling
the machine. Never get on or off the machine while it is in motion. Lock the swing
brake when you travel. Cross obstacles at an angle and at low speed. Watch to see
that your boom clears all obstacles.
Hydraulically released travel brakes are automatically released when any travel
control is engaged. Loss of system pressure will cause the brake to apply
automatically. When traveling downgrade and loading/unloading the machine it is
highly recommended to lock the travel mode selector into the low gear setting. To
avoid unnecessary wear or track skipping/ falling off, it is crucial to travel the machine
such that the drive sprockets are at the ‘rear’ of the travel direction. Neglecting to do
so may lead to premature failures.
Night Switch
The night switch is located in the cab riser on the bottom right hand side. This switch
is used to completely disconnect all
electrical circuits in the machine from
the battery. It is good practice and
highly recommended to turn this
switch to the OFF position every day
after use and during shipping.
Note: When cycling the night switch
on ensure that the ignition is also cycled once before
leaving the machine for extended periods. Failure to
cycle the ignition can leave the display buzzer and
console backlights active.
Note: The orange light beside the cab tilt rocker switch will flash while
engine shut down sequence is in progress. DO NOT turn the night switch
to the OFF position while the light is flashing, doing so will cause engine
code and check engine light to illuminate. Once the orange light stops
flashing, the night switch may be safely turned to the OFF position.
Overloading
Overloading is hazardous. Make certain you are
within the safe load and work radius limits of your
machine for prevailing conditions. Uneven or sloping
terrain will reduce the load and working radius of your
machine. Overloading the machine can result in
rollover which may cause serious injury or death.

9
Fire prevention
Due to the operating conditions found in mechanized logging there are significant fire
hazards that can arise over time if the equipment is not kept clean and well
maintained on a continual basis. In order to minimize the fire hazards present on the
machine it is important to reduce or eliminate both potential sources of fuel for a fire
and potential sources of ignition.
The following precautions must be taken for the safe operation of the machine:
Accumulation of needles, leaves, bark, wood chips, sawdust or other debris
must be removed daily
Hydraulic leaks, accumulations of grease, diesel fuel or oil must be repaired
and cleaned up immediately
Electrical wires, battery cables, hydraulic hoses and fuel lines must be
inspected daily and replaced immediately if damaged or worn
The radiator and engine cooling system should be cleaned and serviced daily
to maintain moderate engine temperatures
Ensure a fire extinguisher and other required firefighting equipment are on the
machine and properly maintained
If welding on the machine, ensure that the area to be welded has been
thoroughly cleaned of any flammable materials and that a fire extinguisher is
within close reach
Refuel the machine only after the engine has been stopped and allowed to cool
down
For machines with an automatic fire suppression system the following
precautions are required to ensure maximum effectiveness:
The house must be kept down with all access doors closed while the machine
is running except when required for service, maintenance and inspections
If a fire is detected before the system has discharged, activate the system
manually
DO NOT wait for the system to automatically activate
In the event of a fire while the house is open, immediately close the house
after ensuring that all personnel are clear of the area. Once closed, manually
activate fire suppression system

10
Welding on engine or
engine mounted
components is NEVER
recommended.
Welding Precautions
When welding, the following must be done to avoid damage to the machine electrical
systems.
1. Turn the night switch to the OFF position as per
the Night Switch procedure in this manual.
2. Both the positive (+) and the negative (-) battery leads must be disconnected
before welding.
3. Unplug the following four computer harnesses, located in the cab riser prior to
welding.
4. Ground cable must be in close proximity to welding location. Locate ground
near electrode so that no current will flow through bearings, bushings or pinned
connections.

11
If the fuse blows a second time, the
circuit must be inspected and tested
for shorts or malfunctioning parts.
Failure to do so can harm other
equipment or result in a fire. It is
never recommended to bypass a fuse.
Fuse Panel
Every circuit on the machine is protected by a
fuse located in either MVEC #1 or MVEC #2 on
the wall in the cab riser. If a fuse blows it MUST
be replaced with one of the correct value (see
Chart).
MVEC #1
MVEC #2
MVEC #2
MVEC #1

12
Fuse Ratings
MVEC-1
MVEC-2
FUSE
FUNCTION
LABEL
RATING
FUSE
FUNCTION
LABEL
RATING
F1
Low Beam Lights
LHTS_LO
20A
F1
Not Used
3A
F2
High Beam Lights
LHTS_HI
10A
F2
Blower High
15A
F3
Horn
HORN
20A
F3
Wash Pump
10A
F4
HFX48 Load Power #1
HFX48_LP1
10A
F4
Blower Low
15A
F5
HFX48 Load Power #2
HFX48_LP2
10A
F5
Wiper
15A
F6
HFX48 Load Power #3
HFX48_LP3
10A
F6
A/C Comp Clutch
10A
F7
HFX48 Load Power #4
HFX48_LP4
10A
F7
Blower Med
15A
F8
HFX48 Load Power #5
HFX48_LP5
10A
F8
Pressurizer
15A
F9
Ignition Power
IGN_PWR
10A
F9
RC Card (4000 Only)
3A
F10
Rear Light
LHTS_REAR
10A
F10
Not Used
3A
F11
Display Power
VA_PWR
5A
F11
115V Inverter
30A
F12
HFX48 Load Power #6
HFX48_LP6
10A
F12
RC Card (4000 Only)
10A
F13
HFX48 ECU Power
HFX48_PWR
5A
F13
Seat Heat
10A
F14
HFX20 Load Power #1
HFX20_LP1
10A
F14
24V Sensors
5A
F15
HFX20 Load Power #2
HFX20_LP2
10A
F15
Not Used
3A
F16
HFX20 Load Power #3
HFX20_LP3
10A
F16
24V/12V Converter
20A
F17
HFX20 ECU Power
HFX20_PWR
5A
F18
Keypad Power
E31_PWR
5A
F19
Not Used
3A
F20
mVEC ECU Power
mVEC_PWR
5A
F21
Not Used
3A
F22
Cab Tilt HPU Power
SVR_PWR
10A
F23
House Light Power
HOUSE_LHT
10A

13
MACHINE FUNCTIONS
Heeler Joystick Controls
Note: Operator can customize joystick function through touch screen display

14
Butt N’ Top Joystick Controls
Note: Operator can customize joystick function through touch screen display

15
Keypad Controls
Park Function Press Sequence
-Activates pilot pressure and hydraulic function
-Deactivates pilot pressure and hydraulic function
Travel Mode Press Sequence
-Allows automatic gear selection of HIGH/LOW
-Locks travel drives in low gear
Engine Fan Reverse
-Press to reverse fan direction
-Press and hold button will activate max fan override
Swing Brake Press Sequence
-Locks swing function
-Unlocks and allows swing function
Work Light
-Triple function press sequence: LOW/HIGH/OFF
Rear Light
-Press sequence: ON/OFF
Interior Light
-Press sequence: ON/OFF
Throttle Control Press Sequence
-Brings idle to 2000 rpm for 3000 or 1650 rpm for 4000
-Brings idle to 1800 rpm for 3000 or 1500 rpm for 4000
-Brings idle to 1200 rpm for 3000 or 900 rpm for 4000
House Up
-Press and hold
Window Wiper Press Sequence
-10 second delay/ 3 second delay/ Continuous /OFF
Left Window UP
-Press and hold
Right Window UP
-Press and hold
House down
-Press and hold
Washer Fluid
-Press and hold
Left Window Down
-Press and hold
Right Window Down
-Press and hold

16
The pilot isolator must not be
tampered with or deactivated in any
way. Never operate the machine
from anywhere but the operators
seat.
Key Switch
OFF –Disconnects all electrical power, Turn to OFF position to shut down engine.
Leave key in this position when machine is not operating.
RUN –Battery is connected and electrical function is regained, Key will stay in this
position while engine is running.
START –This will start the engine by connecting the battery to the start relay, hold
here until engine starts. Once released the key will return to RUN position.
Pilot isolator
This safety feature is provided to prevent
accidental and improper use of the hydraulic
controls. The pilot isolator requires the
operator to be seated to unlock hydraulic
functions.
Air Conditioning Unit
The air conditioning unit in your Madill machine must be cycled on a bi-weekly basis to
ensure that the compressor seals remain lubricated.
Refrigerant may leak from the compressor if the unit is not run regularly, particularly
over the fall and winter months. The air conditioner warranty does not cover claims for
refrigerant loss that are compressor seal related if the unit has not been run on a
regular basis.
Travel - Left& Right Pedals
To maximize undercarriage component life keep the drive sprockets to the rear of the
machine. This orientation is assumed for travel direction descriptions.
FORWARD Depress front of both pedals
REVERSE Depress rear for both pedals
STEER LEFT Depress front of right pedal and rear of left pedal to steer left
STEER RIGHT Depress front of left pedal and rear of right pedal to steer right
Diagnostic Plug
Located in the right arm rest, allows for quick and easy connection of diagnostics
equipment.

17
Stereo
The stereo control is located in the left arm rest and is connected to two rear mounted
speakers. See manufacturer’s operator manual for complete instructions.
Basic Functions
Power
Press the JENSEN power button (1) to turn the unit on/off.
Restore Factory Settings
Perform the following steps to reset the radio to factory default settings:
1. Press and hold the power button (1) to display the software version.
2. Press the VOL+ button (3) to display “RESET”
3. Press the power button to confirm factory default restore. After reset, the unit will default to FM
mode.
Volume
Press the VOL +button (3) to increase the volume.
Press the VOL -button (2) to decrease the volume.
Press and hold either button to change the volume level quickly.
Mute - Press the MUTE button (9) to silence the audio output in tuner, AUX or USB mode. Press
again to restore the previous volume level.
Mode
Press the MODE button (8) to select a mode of operation: FM, AM, AUX, USB and Bluetooth.
This manual suits for next models
1
Table of contents
Other Madill Utility Vehicle manuals
Popular Utility Vehicle manuals by other brands

Club Car
Club Car TURF 2 XRT owner's manual
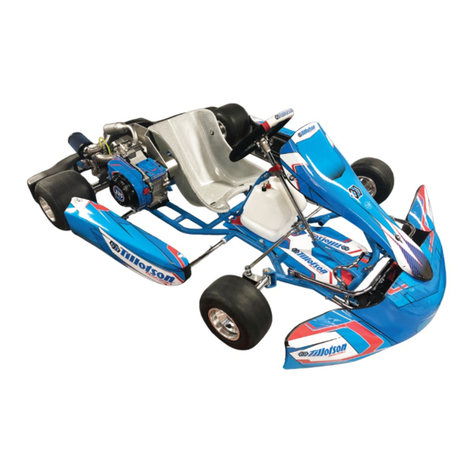
TILLOTSON
TILLOTSON T4 Assembly guidelines
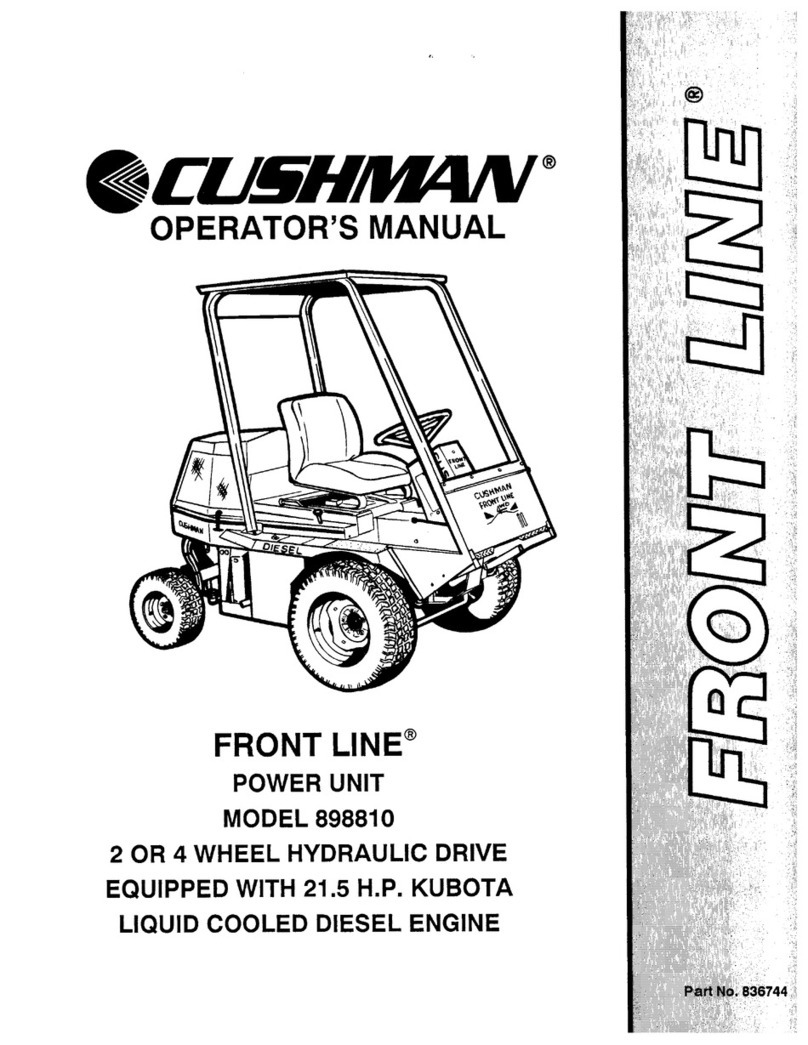
Cushman
Cushman Front Line 898810 Operator's manual

Clam Corp
Clam Corp Polar HD 1200 Specification sheet

Demountable Concepts
Demountable Concepts Warehouse On Wheels Quick reference guide
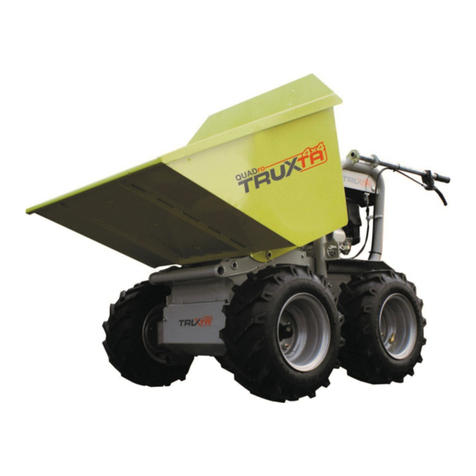
Truxta
Truxta QUADro Q300G Operator's manual & parts list