MANN+HUMMEL MICRODYN MD020CP2N User manual

MICRODYN CAPILLARY MODULES | USER MANUAL
MANN+HUMMEL Water & Fluid Solutions | REVISION DATE: 09/09/2021
1
MICRODYN
Capillary Modules
User Manual

MICRODYN CAPILLARY MODULES | USER MANUAL
MANN+HUMMEL Water & Fluid Solutions | REVISION DATE: 09/09/2021
2
Contact
Europe
Germany: +49 611 962 6001
Italy: +39 0721 1796201
info@microdyn
-nadir.com
Americas
USA: +1 805 964 8003
sales.mnus@microdyn
-nadir.com
Asia
Singapore: +65 6457 7533
China: +86 10 8413 9860
waterchina@mann
-hummel.com

MICRODYN CAPILLARY MODULES | USER MANUAL
MANN+HUMMEL Water & Fluid Solutions | REVISION DATE: 09/09/2021
3
Table of Contents
1Introduction ......................................................................................................................................4
2Product Description....................................................................................................................5
2.1
PRODUCT DESIGN ...................................................................................................................... 5
2.2
CROSS-FLOW MICROFILTRATION .............................................................................................. 5
2.3
PRODUCT CODES & MODULE TYPES......................................................................................... 5
3Shipping, Handling & Storage.................................................................................................6
3.1
SHIPPING & HANDLING............................................................................................................... 6
3.2
STORAGE CONDITIONS .............................................................................................................. 6
3.3
RETURNING A MODULE.............................................................................................................. 6
4Installation & Activation.............................................................................................................7
4.1
INSTALLATION............................................................................................................................ 7
4.2
ACTIVATION WITH WATER PRESSURE ...................................................................................... 8
4.3
ACTIVATION WITH WETTING AGENTS........................................................................................ 8
5Operation.......................................................................................................................................9
5.1
GENERAL SYSTEM SET-UP ........................................................................................................ 9
5.2
PRESSURE DROP AND TRANSMEMBRANE PRESSURE............................................................. 9
5.3
OPERATION PROCESSES ...........................................................................................................11
5.3.1 Open Loop Operation............................................................................................................................11
5.3.2 Closed Loop Operation .........................................................................................................................11
5.3.3 Multistage operation ............................................................................................................................ 12
5.4
PERIODIC BACK PULSE (PBP)...................................................................................................13
5.4.1 PBP with Compressed Air....................................................................................................................14
5.4.2 PBP with Pump Pressure ..................................................................................................................... 15
5.4.3 Backwashing with Special Pump & Disconnected Feed Pump .............................................................16
5.5
ADJUSTMENT OF FILTRATE FLOW ...........................................................................................16
5.6
CHEMICAL CLEANING ...............................................................................................................19
6Piloting ........................................................................................................................................20
6.1
FILTRATION WITH CONSTANT CONCENTRATION ....................................................................20
6.2
DETERMINING MAX CONCENTRATION FACTOR ......................................................................20
6.3
SETTINGS FOR PERIODIC BACK PULSE ..................................................................................20
6.4
CLEANING TESTING..................................................................................................................20
7Appendix...................................................................................................................................... 21

MICRODYN CAPILLARY MODULES | USER MANUAL
MANN+HUMMEL Water & Fluid Solutions | REVISION DATE: 09/09/2021
4
1Introduction
MANN+HUMMEL Water & Fluid Solutions (WFS) offers a wide variety of capillary modules under the MICRODYN brand.
MICRODYN cross-flow microfiltration (MF) modules are used to separate suspended solids larger than 0.2 micron.
The highly porous polypropylene (PP) membrane is backwashable, allowing for stable and efficient filtration with continuously
high product flux.
The smart construction techniques employed in the module manufacturing allow them to be used in applications that require
highly stable polymer materials, pH stability (0 to 14), and high resistance against abrasive substances.
The advantages of MICRODYN microfiltration modules include:
•Well-defined flow conditions
•High packing density
•Minimized dead zones
•Extremely abrasion resistant
•Strong chemical resistance
•Backwashable
•Low specific energy consumption
Typical applications where MICRODYN capillary modules are used are food applications like wine and vinegar filtration or
pharmaceutical applications where specific proteins are concentrated.

MICRODYN CAPILLARY MODULES | USER MANUAL
MANN+HUMMEL Water & Fluid Solutions | REVISION DATE: 09/09/2021
5
2Product Description
2.1
PRODUCT DESIGN
MICRODYN capillary modules contain a bundle of symmetric, hydrophobic polypropylene capillary membranes with a nominal
pore size of 0.2 micron. The capillary membranes are potted in polyurethane. MICRODYN capillary modules were developed for
cross-flow microfiltration (CMF), a modern filtration procedure for separating suspended solids and for low concentrations of
emulsions.
2.2
CROSS-FLOW MICROFILTRATION
The feed flows inside the membrane lumen (or inside the membrane fibers) are as shown in Figure 1. A part of this feed exits the
capillary membrane as filtrate, or clean water, due to a pressure difference across the membrane. The remaining liquid is called the
retentate/concentrate.
Feed Retentate
Filtrate
Filtrate
2.3
PRODUCT CODES & MODULE TYPES
The following coding applies to MICRODYN products:
MD150
-
CP
-
2N
/
DF
Module Type & Size Membrane Geometry &
Shell Material Pore Size (0.2µm) &
Module Length Module Connection
(∅diameter of housing in mm)
CP: Capillary membrane
with polypropylene housing
FP: Hollow fiber membrane
with polypropylene housing
CS: Capillary membrane
with Stainless Steel housing
CU: Capillary membrane
with Polysulfone housing
CV: Capillary membrane
with PVC/PVC-C housing
M: medium
N: normal
AF: ANSI flange
DF: DIN flange
JF: JIS flange
C: Clamp connection
F/R
CC: Clamp connection
F/R/P
AS: Thread connection
Please refer to Appendix 1, Table 1 for an overview of available MICRODYN capillary modules.
For more module-specific data, please refer to the respective datasheet on the webpage (Capillary & Tubular Modules -
MANN+HUMMEL Water & Fluid Solutions (microdyn-nadir.com)
Figure 1. Scheme of lumen function.

MICRODYN CAPILLARY MODULES | USER MANUAL
MANN+HUMMEL Water & Fluid Solutions | REVISION DATE: 09/09/2021
6
3Shipping, Handling & Storage
3.1
SHIPPING & HANDLING
Transportation and handling of MICRODYN capillary modules should be done with extreme care as a module may crack or break if
dropped. Having proper equipment is also essential for safely handling the modules.
Modules should not come into contact with organic solvents, nor should splicing tape be used as this may lead to the damage of
the module casing.
Wipe the module casing with water or ethanol to remove debris from the module casing.
3.2
STORAGE CONDITIONS
The following conditions are recommended when storing the modules:
•Store the modules inside a cool building or warehouse out of direct sunlight.
•Temperature limits: between 5°C and 35°C (41°F and 95°F).
•Humidity must not exceed 70%.
•All new modules being stored prior to use should remain in original packaging.
3.3
RETURNING A MODULE
If a module is returned for any reason, MANN+HUMMEL WFS must approve the shipment first. Please contact the appropriate
MANN+HUMMEL WFS representative before sending the product back. Non-approved return shipments will be rejected.
If MANN+HUMMEL WFS approves a return of a module, it must be appropriately cleaned, preserved, packed, and labeled to
transport safely and retain the integrity of the materials.

MICRODYN CAPILLARY MODULES | USER MANUAL
MANN+HUMMEL Water & Fluid Solutions | REVISION DATE: 09/09/2021
7
4Installation & Activation
4.1
INSTALLATION
MICRODYN capillary modules may be installed into a system vertically or horizontally.
A horizontal position is recommended for filtration of suspensions with a large quantity of solids (Figure 2). While each module has
two permeate outlets, only one is typically used during filtration. In the horizontal position, the permeate port must be facing
upwards to allow the module to fill fully with liquid. Additionally, the permeate port should be at the end of the module (low
pressure side) if the module is in the horizontal position.
Feed Concentrate
Permeate
Drainage for
Cleaning
In the vertical position, the permeate outlet must always be toward the top of the module so that air can be removed completely
from the module prior to operation (Figure 3).
Concentrate
Feed
Drainage for
Cleaning
Permeate
Figure 2. Module in the horizontal position.
Figure 3. Module in the vertical position.

MICRODYN CAPILLARY MODULES | USER MANUAL
MANN+HUMMEL Water & Fluid Solutions | REVISION DATE: 09/09/2021
8
4.2
ACTIVATION WITH WATER PRESSURE
Typically, activation of the module’s membranes is required. The PP membrane is hydrophobic in nature. Liquids like water with
high surface tension of 0.072 N/m do not wet the membrane.
A simple and safe way to activate the membrane in the module(s) is the use of water at higher pressure. The first step is to fill the
module(s) bubble free with water (25 °C) from both sides (feed and permeate side). A pressure of 6 bar must be applied to the
module(s) for 1 minute. Typically, this is the tap line pressure. (Please notice the difference to the max. operating pressure given in
the data sheet.)
After this procedure, the pressure must be released to zero. The water must be exchanged, and the procedure must be repeated
four to six times. Now the module is activated and can be used for filtration.
4.3
ACTIVATION WITH WETTING AGENTS
For all filtration purposes where the module must be tested by a bubble point test for process safety reasons, the module has to be
activated by means of water-soluble liquids with a surface tension of less than 0.035 N/m.
Appropriate liquids to be used are:
•a mixture of water and 50 vol. % of isopropanol
•a mixture of water and 25 vol. % tert. butanol (not inflammable)
•surfactants
With this method, it is necessary to run the module in a system for about 30 minutes in cross-flow mode until a sufficiently high
flux is reached.
After wetting, the module is flushed either with water or with the solution to be filtered to rinse any remaining agents. As long as it
stays in fluid, the membrane is activated. If the membrane dries up, it must be activated again as per the description. The
membrane’s separation properties will not change by drying.
Heavily gasifying liquids (carbonated beverages or beer) require a counter-pressure on the permeate side (e.g. 1 bar) in order to
prevent the release of gases. Gases will deactivate the membranes.
In the PBP process, a part of the permeate is pushed back by compressed gas (e.g. air). Care must be taken so that the gas is not
pressed into the membrane. Otherwise, the membranes will be made a partially hydrophobic with reduced flux. A reactivation
must then be performed.

MICRODYN CAPILLARY MODULES | USER MANUAL
MANN+HUMMEL Water & Fluid Solutions | REVISION DATE: 09/09/2021
9
5Operation
5.1
GENERAL SYSTEM SET-UP
In cross-flow filtration, a liquid is pumped through the modules. A typical arrangement is shown in Figure 4 below. The favorable
flow velocity for MICRODYN modules ranges between 1-2 m/s (3.3-6.6 ft/s).
5.2
PRESSURE DROP AND TRANSMEMBRANE PRESSURE
For filtration to occur, the inlet, or feed pressure (P1), must be greater than the outlet pressure (P2) and filtrate pressure (PF), as
shown in Figure 5. This difference in pressure, also called pressure drop, is the loss of pressure from the feed end to the
concentrate end of a module and occurs due to the resistance of flow.
To achieve stable filtration, begin operation at a low feed pressure and gradually increase the feed pressure until optimal filtration
performance is achieved. The driving force for filtration is the transmembrane pressure, which is defined by the difference of the
pressure on the filtrate side and the averaged pressure on the feed/concentrate side (see also below equations). The allowable
operating pressure is listed on the respective product data sheet.
Pressure
Module Length
Pressure Drop in
the Module
Effective Operating
Pressure
P
1
P
2
P
F
Concentrate
Permeate
PI
PI
TI
PT
Back Pulse
Tank
FT
Feed
Figure 4. Simplified flow diagram using MICRODYN modules.
Figure 5. The pressure drop along the length of the module.

MICRODYN CAPILLARY MODULES | USER MANUAL
MANN+HUMMEL Water & Fluid Solutions | REVISION DATE: 09/09/2021
10
To calculate the pressure drop and transmembrane pressure, please refer to the below equations.
Pressure drop:
∆P = P
1−P
2
Transmembrane (operating) pressure:
P
TMP =
P
1−P
2t
2−P
F
The energy consumption of a cross-flow microfiltration system is determined mainly by the circulating volume and the pressure
losses of the module. The pressure loss is affected by:
•The properties of the circulating fluid (e.g. rheological behavior, viscosity, and the concentration of suspended particles)
•The velocity resistance in circulation (modules, fittings, piping system)
•Operating conditions (flow velocity)
The greatest resistance to velocity in circulation occurs when the modules are operated in parallel or in series. Figure 6 shows the
relationship between pressure drop and the mean linear velocity of water through MICRODYN capillary modules at 20°C.
Figure 6. Relationship between pressure drop and velocity of water at 20°C measured in a MD 150 CP 2N.

MICRODYN CAPILLARY MODULES | USER MANUAL
MANN+HUMMEL Water & Fluid Solutions | REVISION DATE: 09/09/2021
11
5.3
OPERATION PROCESSES
5.3.1 Open Loop Operation
An open loop design is commonly used for batch processes, where a highly concentrated retentate is desirable. In an open loop
design, the retentate is sent back to the feed tank for further concentrating. A continuous operation is possible with an open loop
by continuously sending raw feed to the system and with concentrate bleeding.
Circulation Pump
Concentrate
Permeate
PIPI TI
PT
PBP
Device
Feed
SEPRODYN
®
Module
PI
FT
5.3.2 Closed Loop Operation
In a closed loop operation, the concentrate stream is sent back to the circulation pump ahead of the module. The advantage with
this design is that the circulation pumping pressure is reduced. The feed pump is what supplies the system pressure. Overall, the
pumping volume only includes the filtration flow rate and the bleed concentrate. The concentration of the concentrate is based on
the mixing ratio of feed and bleed flow. It is important to keep the periodic back pulse (PBP) valve wide open to bleed the high
amount of back pulsing water and to protect the feed side for a pressure increase.
Circulation Pump
Concentrate
Permeate
PI
PI TI
PT
Feed
SEPRODYN®
Module
Feed Pump
PBP
Tank FI
PI
Compressed Air
Deaeration
Timer
PBP Bleed
Back
Pulse
Tank
Back
Pulse
Tank
Figure 7. Simplified flow diagram for open loop operation.
Figure 8. Simplified flow diagram for closed loop operation.

MICRODYN CAPILLARY MODULES | USER MANUAL
MANN+HUMMEL Water & Fluid Solutions | REVISION DATE: 09/09/2021
12
5.3.3 Multistage operation
If the filtrate flow rate decreases with increasing feed concentration, it is possible to operate in a multistage configuration. In this
configuration, the concentrate from the first stage is fed to the second stage. This means that the flow rate is higher in the first
stages and only lower in the later stages. This configuration allows for fewer modules for a system.
Figure 9. Simplified diagram (without control devices and back pulsing system) of a multistage system.

MICRODYN CAPILLARY MODULES | USER MANUAL
MANN+HUMMEL Water & Fluid Solutions | REVISION DATE: 09/09/2021
13
5.4
PERIODIC BACK PULSE (PBP)
During filtration, some particles will settle down
on the surface of the membrane. This decreases
the performance of the membrane. The purpose
of the periodic back pulse (PBP) system is to
remove these particles from the surface of the
membrane, which helps restore the performance
of the membrane. PBP may also decrease the
system’s overall energy consumption.
During PBP, a small amount of the filtrate is sent
through the backside of the membrane
(reversed flow) and is forced toward the feed
side of the membrane. Figure 10A shows how
the flow direction changes from normal filtration
to back pulsing. In this moment, the filtrate
pressure is higher than the feed pressure (PF> P1
and P2), as shown in Figure 10B.
When filtrate is sent through the backside of the
membrane and gets pushed through the feed
side of the membrane, the fouling and scaling
materials are loosened and removed from the
membrane surface. Typically, a back pulse is
done every 5 – 30 minutes, but trials may be
done to determine how frequently a back pulse
should be performed so that the system runs
most efficiently. Figure 10C shows how
important it is to perform regular PBP and
chemical cleanings to help maintain membrane
performance for extended periods of time.
It is recommended to install a PBP overflow for
the concentrate because of the high backflow
volume (nearly 1 L per 1 m2of installed
membrane area, or 0.26 gal per 10.8 ft2of
membrane area, in a range of 2-5 seconds).
A)
B)
C)
Figure 10.. A) Diagram showing the difference in flow direction
in the
capillary membranes during filtration and back pulsing.
B)
During PBP, the filtrate pressure must be higher than the feed
p
ressure.
C)
A simplified graph showing the decline in membrane
performance
without PBP or chemical cleaning. PBP and chemical
cleanings help restore membrane performance by removing
particles from the membrane surface.

MICRODYN CAPILLARY MODULES | USER MANUAL
MANN+HUMMEL Water & Fluid Solutions | REVISION DATE: 09/09/2021
14
5.4.1 PBP with Compressed Air
Figure 11 shows the closed standard loop with a switch diagram of the pressurized back pulse. The compressed air (or compressed
gases like N2) is not used as a cleaning substance. The air is only used to pressurize the back pulse tank to push the liquid
backwards through the membrane.
Figure 11. Simplified flow diagram with PBP using compressed air, along with the switch diagram for the valves.

MICRODYN CAPILLARY MODULES | USER MANUAL
MANN+HUMMEL Water & Fluid Solutions | REVISION DATE: 09/09/2021
15
5.4.2 PBP with Pump Pressure
In large systems, it is possible to back pulse the modules individually or in groups. In this case, it is best to use a pressure-controlled
pump. To keep the pump small and to get the necessary flow volume, it is possible to use a pressure vessel with a rubber
membrane for the storage of pressurized filtrate. The pump will pressurize this filtrate in the vessel up to the regulated pressure.
The vessel needs to be big enough to store the back pulsing volume of 1 L per installed m2of membrane area (or 0.26 gal per 10.8
ft2of membrane area).
Feed Pump
(On)
Concentrate
PI2
PI1
Feed
SEPRODYN®
Module
PBP Bleed
PI1 TI
PI
PI
PI2
SEPRODYN®
Module
FI
Compressed
PBP-Tank
Permeate
Timer
Back Flush
Usually, the outlet on the upper, downstream side is used for the filtrate due to the module’s automatic ventilation. However, it is
also possible to use the outlet on the other side of the module for back pulsing, especially when it is used for chemical cleaning
with automatic valving.
Feed Pump
(Off)
PRS-Bleed
Open
PI2
PI1
Feed SEPRODYN
®
Module
PI1 TI PI2
SEPRODYN
®
Module
FI
Permeate
Timer
PI
Timer
Closed
Open
Compressed
PBP-Tank
Closed
Open
Figure 12. Simplified flow diagram of PBP with pump pressure.
Figure 13. Flow diagram of PBP with the second filtrate socket.

MICRODYN CAPILLARY MODULES | USER MANUAL
MANN+HUMMEL Water & Fluid Solutions | REVISION DATE: 09/09/2021
16
5.4.3 Backwashing with Special Pump & Disconnected Feed Pump
In some cases, backwashing is better than back pulsing. It is not used often – typically performed once every hour, but for a longer
period of time (between 10 – 60 seconds). Backwashing is also done with the feed pump disconnected. For this procedure, a
bigger filtrate storage vessel is needed and may require a sterile air vent filter.
5.5
ADJUSTMENT OF FILTRATE FLOW
At very high filtrate flow (high membrane permeability) there is a high potential for mechanical blocking or fouling of the
membranes. To maintain good membrane performance, it is best to limit and control the flow of filtrate by throttling the regulator
valve (VR).
Circulation Pump
Concentrate
Permeate
PIPI TI
PT
Feed
SEPRODYN®
Module
FI
Compressed Air
Deaeration
Timer
VR
Figure 14.. Flow diagram of PBP with the second filtrate socket.
Figure 15. Flow diagram showing the adjustment of filtrate flow with regulator valve VR.

MICRODYN CAPILLARY MODULES | USER MANUAL
MANN+HUMMEL Water & Fluid Solutions | REVISION DATE: 09/09/2021
17
Resistance to chemicals
Most MICRODYN capillary modules are made of polypropylene (PP) capillary membranes potted in polyurethane, with a plastic
casing made of polypropylene. The below content is only valid for modules with PP housing. For resistance of modules with
housings made of stainless steel, polysulfone, or PVC/PVC-C, please contact your MANN+HUMMEL WFS representative.
Aromatic and aliphatic hydrocarbons with low boiling points – such as petrol ether, benzene, and carbon tetrachloride – diffuse
into the polymers of the membrane and will cause swelling and decrease mechanical strength. Before filtration of these
substances, please consult with your MANN+HUMMEL WFS representative. Exceptions include low volatile substances such as
grease, oil, and wax; these substances cause negligible swelling and little reduction to mechanical strength.
Peroxides may be used in small quantities and for short periods of time for cleaning purposes. Before applying, please consult your
MANN+HUMMEL WFS representative.
The chemical resistance of MICRODYN capillary modules is listed in the following table. The resistance depends on many factors
such as temperature, concentration, and intensity of mechanical stress. The data in the table is for reference only.
The symbols in the below table are as follows:
+ resistant at operating conditions as per data sheet
/ limited resistance, swelling (only limited operating conditions)
- not resistant
Table 1. Chemical Resistance
Chemical
Module
O-Rings (Viton Material)
20°C (68°F)
60°C (140°F)
Acetone
+
/
+
Ethanol, 96%
+
+
+
Ethyl acetate
/
-
-
Ethyl ether
+
+
/
Ethylene glycol
+
+
+
Formic acid (diluted)
+
+
-
Amylic alcohol
+
+
+
Aniline dye
+
+
+
Petrol ether, KP100-140 C
/
-
+
Benzene
/
-
/
Succinic acid (diluted)
+
+
+
Beer
+
+
+
Bromic water, cold saturated
-
-
+
Butanol
+
/
+
Butyl
/
-
/
Butyl glycol
+
+
+
Calcium chloride sol. aqueous
+
+
+
Chlorobenzene
+
/
+
Chloroform
+
-
+
Chlorosulfonic acid
-
-
/
Chloric water (short time)
+
/
+
Cyclohexane
+
+
+
Cyclohexanol
+
/
+
Cyclohexanon
/
+
/
Diethanol amine
+
+
+
Dichloroethylene
/
+
/
Dichlorobenzene, cold saturated
/
N/A
/
Dimethyl amine
/
-
+
Ferric chloride (III), saturated
+
+
+
Vinegar
+
+
+
Acetic acid, 10%
+
/
+
Hydrofluoric acid, 10%
+
+
+
Formaldehyde, 30%, aqueous
+
+
+

MICRODYN CAPILLARY MODULES | USER MANUAL
MANN+HUMMEL Water & Fluid Solutions | REVISION DATE: 09/09/2021
18
Chemical
Module
O-Rings (Viton Material)
20°C (68°F)
60°C (140°F)
Juices, aqueous
+
+
+
Fructose, aqueous, cold saturated
+
+
+
Galvanic baths
+
+
+
Gelatin
+
+
+
Glucose, aqueous
+
+
+
Glycerol
+
+
+
Glycol
+
+
+
Hexane
+
/
/
Isopropanol
+
+
+
Potassium hydroxide, aqueous
+
+
+
Potassium permanganate (2N)
-
-
+
Saline, saturated
+
+
+
Linseed oil
+
+
+
Machine oil
+
/
+
Sea water
+
+
+
Methanol
+
+
+
Methylene chloride
+
-
/
Molasses
+
+
+
Milk
+
+
+
Lactic acid, aqueous, 10%
+
+
+
Mineral oils
+
/
+
Mineral water, commercial qual.
+
+
+
Natrium sulfite, 40%
+
+
+
Sodium hydroxide solution (2N)
+
+
+
Sodium hydroxide solution, 52%
+
+
+
Nitrobenzene
/
/
/
Fruit juices
+
+
+
Oleum, 100%
-
-
/
Olive oil
+
+
+
Petrol ether
+
+
+
Peracetic acid, 0.2% (see note)
-
-
+
Plant oils
+
/
+
Pyridine
/
-
/
Nitric acid (2N), aqueous
/
-
+
Chloric acid, 30% ig, aqueous
+
/
+
Sulfuric acid (2N), aqueous
+
/
+
Soap solution
+
+
+
Silicon oil
+
+
+
Sodium carbonate solution
+
+
+
Soybean oil, cold saturated, aqueous
+
+
+
Starch solution
+
+
+
Turpentine
-
-
-
Carbon tetrachloride
-
-
-
Toluene
/
-
/
Trichloro ethylene
+
+
/
Trichloro acetic acid
+
/
+
Water
+
+
+
Tartaric acid, aqueous, 10%
+
+
+
Whisky
+
+
+
Xylol
-
-
/
Citric acid, aqueous, 10%
+
+
+

MICRODYN CAPILLARY MODULES | USER MANUAL
MANN+HUMMEL Water & Fluid Solutions | REVISION DATE: 09/09/2021
19
5.6
CHEMICAL CLEANING
Regular chemical cleanings are recommended to help maintain the module over time. Chemical cleanings require acidic or caustic
solutions with a pH within the range of 0.5 to 14. The cleaning chemical solutions may be flushed through the membrane from the
permeate side. Employing a cross-flow along the membrane surface at low pressure also has a favorable effect on the cleaning
process; it is very effective and saves cleaning agents. In fact, unspent chemicals may be pumped down for further use.
The following steps describe how to properly clean the modules:
1. Uncouple the filtration system from other systems
2. Empty the system on both sides of the membrane (feed and filtrate)
3. Flush the system with clean water and drain again
4. Fill the system completely with the cleaning solution (e.g. sodium hydroxide) from the filtrate side
5. The cleaning chemicals must soak in the module for 30 minutes to 1 hour
6. Drain the complete system
7. Flush the system with clean water to remove residual cleaning agents
8. Repeat steps 4-7 with another cleaning solution (e.g. citric acid) if required
9. Connect the filtration system to the other systems.
Circulation Pump
Feed
SEPRODYN
®
Module
To Drain
(Concentrate Side) To Drain
(Permeate Side)
Aeration &
Deaeration
Aeration &
Deaeration
Cleaning
Agent
DI Water
Notes to be considered during cleaning:
•Cleaning temperatures must not exceed those listed on the product data sheets.
•Detailed cleaning instructions must be determined on-site and are depending on the application.
•Organic fouling of the membrane is predominantly cleaned by using alkaline cleaning agents. Typically, 1-5% NaOH is
used at a temperature of 20-60°C (68-140°F).
•Cleaning aids (e.g. surfactants) speed up the dissolution of oily and greasy substances.
•Inorganic fouling (e.g. mineral salts, ferrous compounds) is removed using acidic agents. Organic acids like citric acid,
oxalic acid, or mixtures of hydrochloric acid and oxalic acid have proven favorable.
•For more information about cleaning, please consult MANN+HUMMEL WFS.
Figure 16.CIP flow diagram

MICRODYN CAPILLARY MODULES | USER MANUAL
MANN+HUMMEL Water & Fluid Solutions | REVISION DATE: 09/09/2021
20
6Piloting
Pilot testing is usually required to determine the feasibility and process parameters of the filtration/concentration process utilizing
MICRODYN.
Please note that MANN+HUMMEL WFS offers compact pilot units (see Figure 17) and supervision of piloting. For more details,
please contact your MANN+HUMMEL WFS representative.
6.1
FILTRATION WITH CONSTANT CONCENTRATION
A typical pilot test starts with filtration at a constant concentration. The permeate and the concentrate flow back into the feed
tank, so there is no increase in concentration. Once the flux is not changing any more, the concentration step can start.
6.2
DETERMINING MAX CONCENTRATION FACTOR
By concentrating the feed, the influence of the growing filter cake can be seen and assessed for the process. The permeate flows
into a separate tank, the concentrate goes back to the feed tank. Please consider the increasing viscosity during concentration as
well as an increase in temperature. The max. temperature for MICRODYN modules is 60°C (140°F). Additionally, the pressure drop
- inlet pressure to outlet pressure - is increasing, so a pressure adjustment might be necessary.
6.3
SETTINGS FOR PERIODIC BACK PULSE
The tangential flow along the membrane surface reduces the speed of a cake build-up on the membrane but does not avoid the
cake formation itself. At some point, the filtration performance hits its limit, and the filter cake must be disturbed to stop further
compaction.
During the periodical back pulse (PBP) a part of the permeate is pressed back through the membrane. For each application, the
desired frequency and extent of the PBP needs to be determined to guarantee a stable process. As a starting point, a frequency of
every 5-15 minutes can be chosen. The default duration of the PBP is 2-3 seconds.
6.4
CLEANING TESTING
Depending on the fluid processed, a slow blockage of the filter modules takes place. A chemical cleaning might be necessary. The
chemicals to be used for the cleaning are related to the substances that are forming the cake on the membrane. In general, alkaline
or acids in combination with detergents, enzymes, etc. are good cleaning chemicals.
In principle, there are two different ways of cleaning, (a) cleaning in filtration direction and (b) cleaning from permeate side to feed
side. Please refer to section 5.6 for more details.
Figure 17. Picture of compact MICRODYN pilot unit.
This manual suits for next models
7
Table of contents
Popular Control Unit manuals by other brands

Mitsubishi Electric
Mitsubishi Electric PMFY-P-NBMU-ER5 Engineering manual
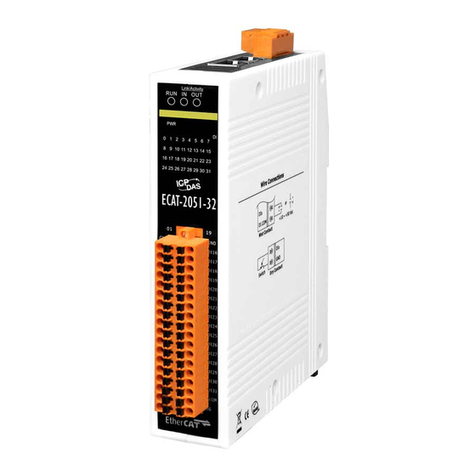
ICP DAS USA
ICP DAS USA ECAT-2000 Series user manual
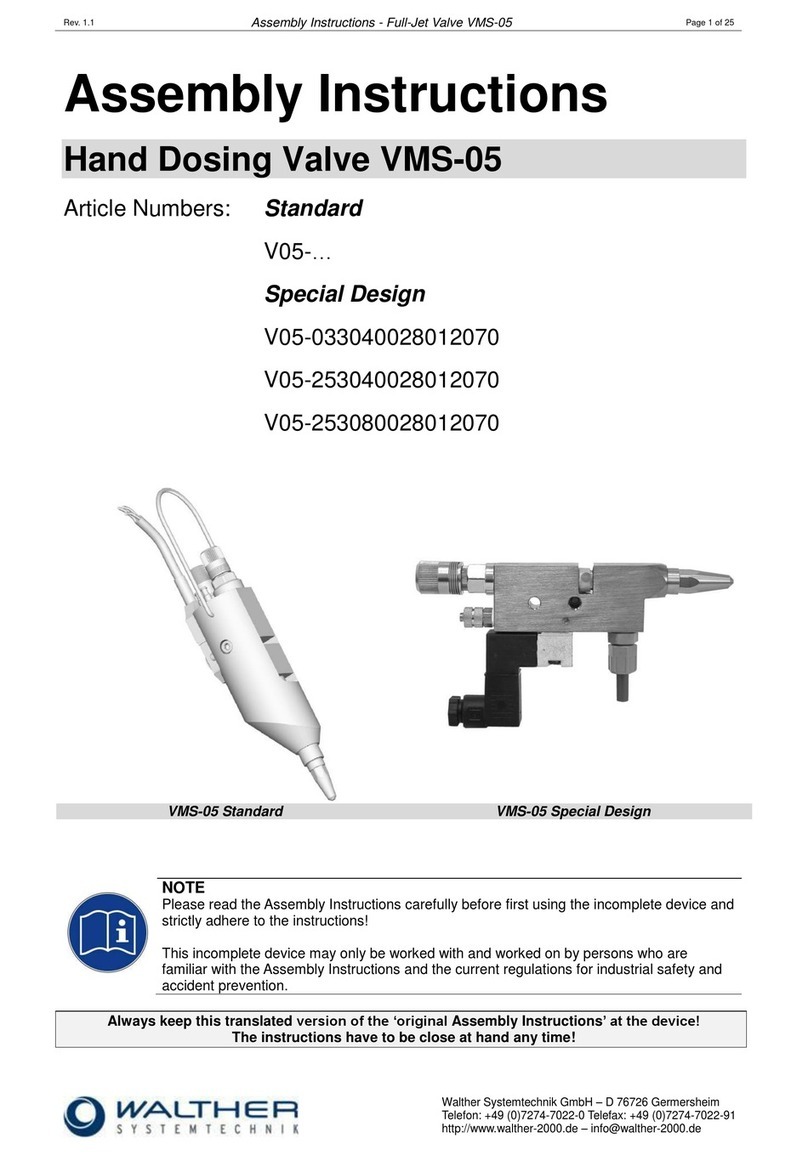
Walther Systemtechnik
Walther Systemtechnik VMS-05 Assembly instructions
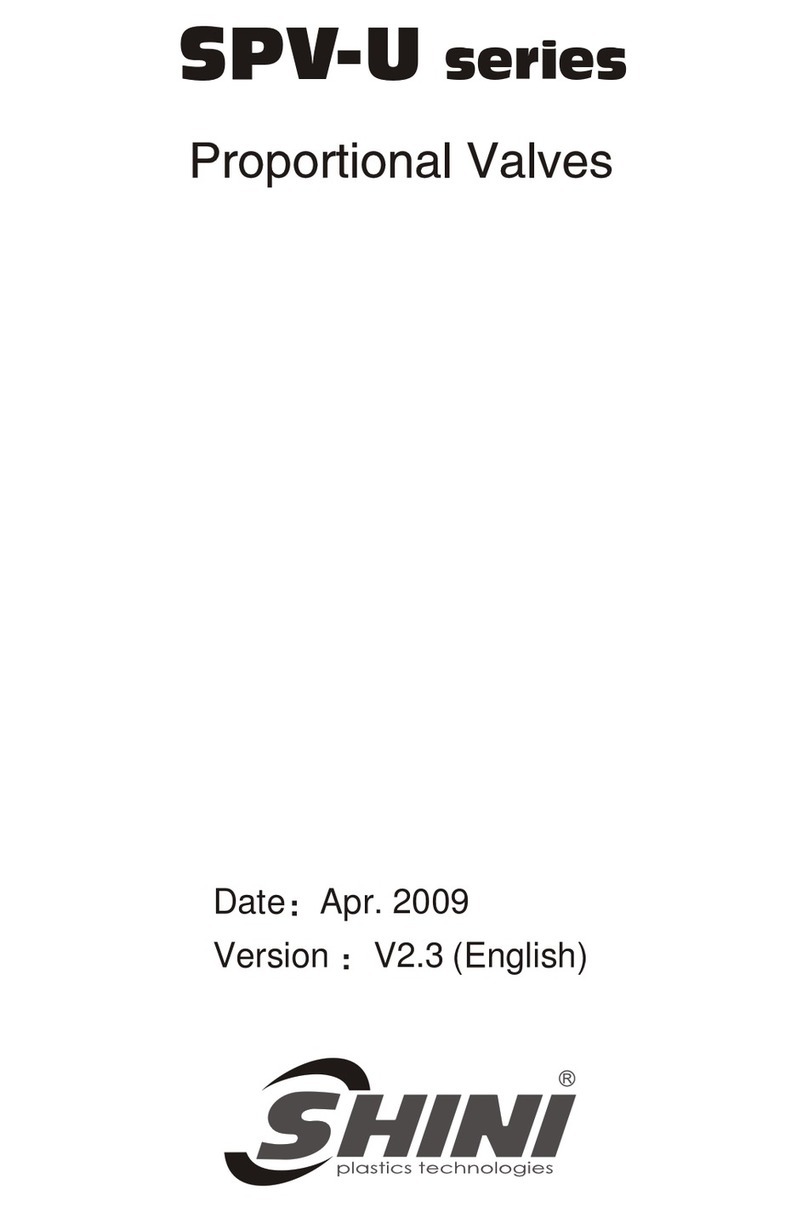
Shini
Shini SPV-U Series manual
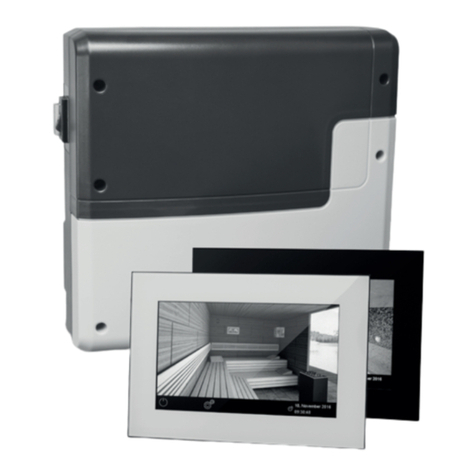
EOS
EOS EmoTouch 3 operating instructions
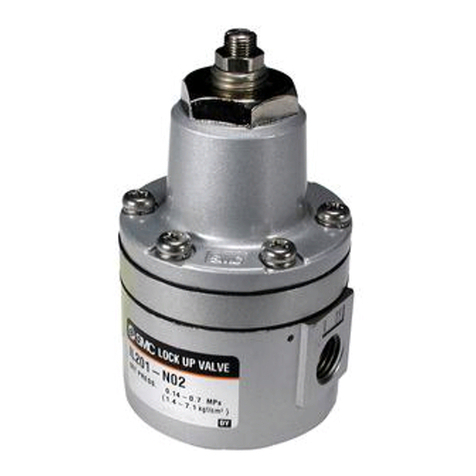
SMC Corporation
SMC Corporation IL211 Series instruction manual