Matelec FPC-30040-CON Instructions for use












Other Matelec Controllers manuals
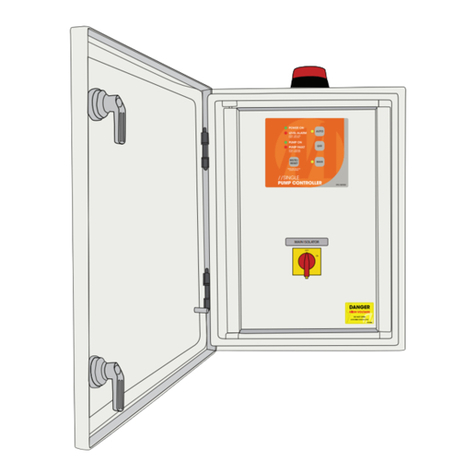
Matelec
Matelec FPC-15207 Instructions for use
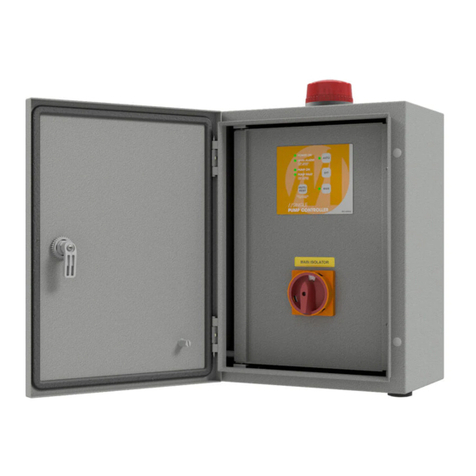
Matelec
Matelec FPC-15007 Instructions for use
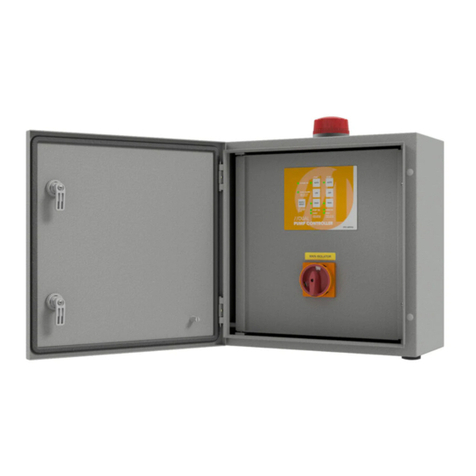
Matelec
Matelec FPC-30240 Instructions for use
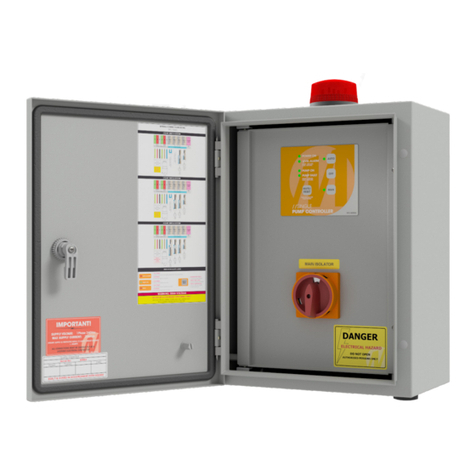
Matelec
Matelec FPC-15205 Instructions for use
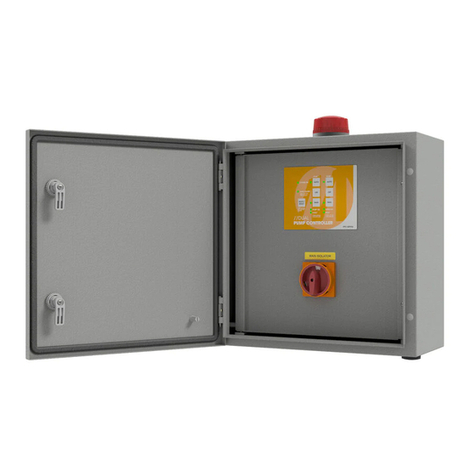
Matelec
Matelec FPC-30020-CON Instructions for use
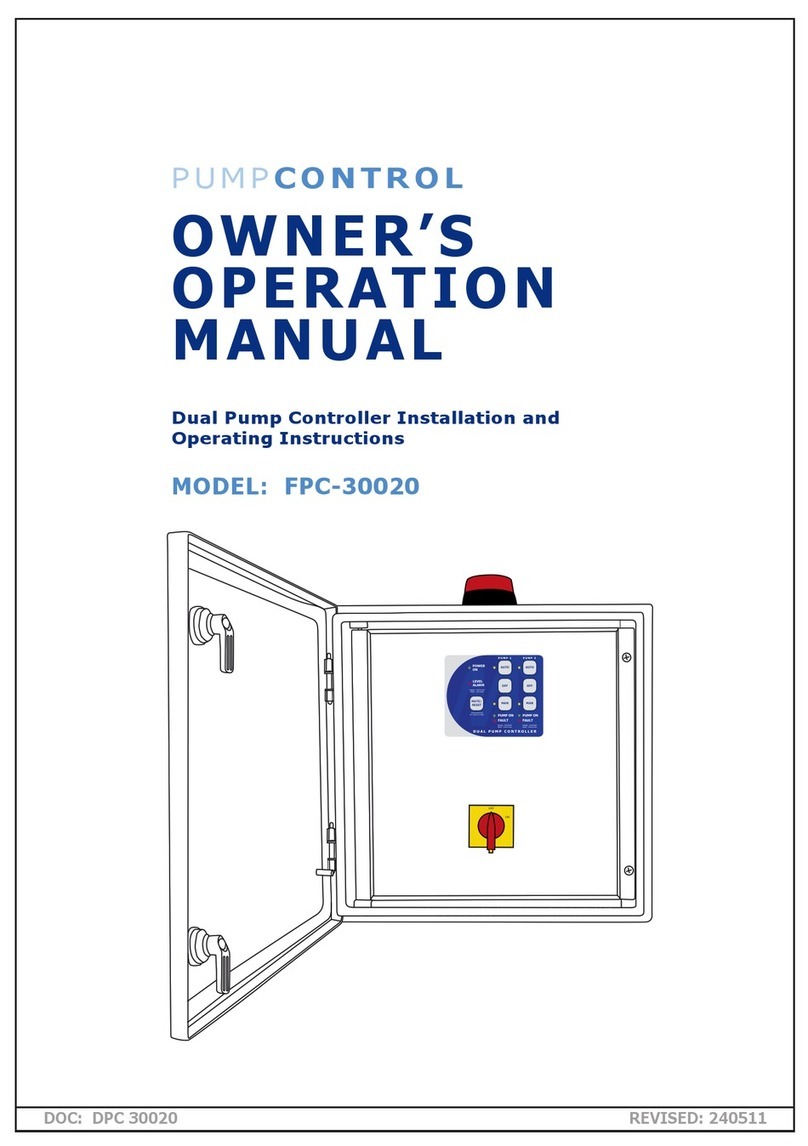
Matelec
Matelec FPC-30020 Instructions for use
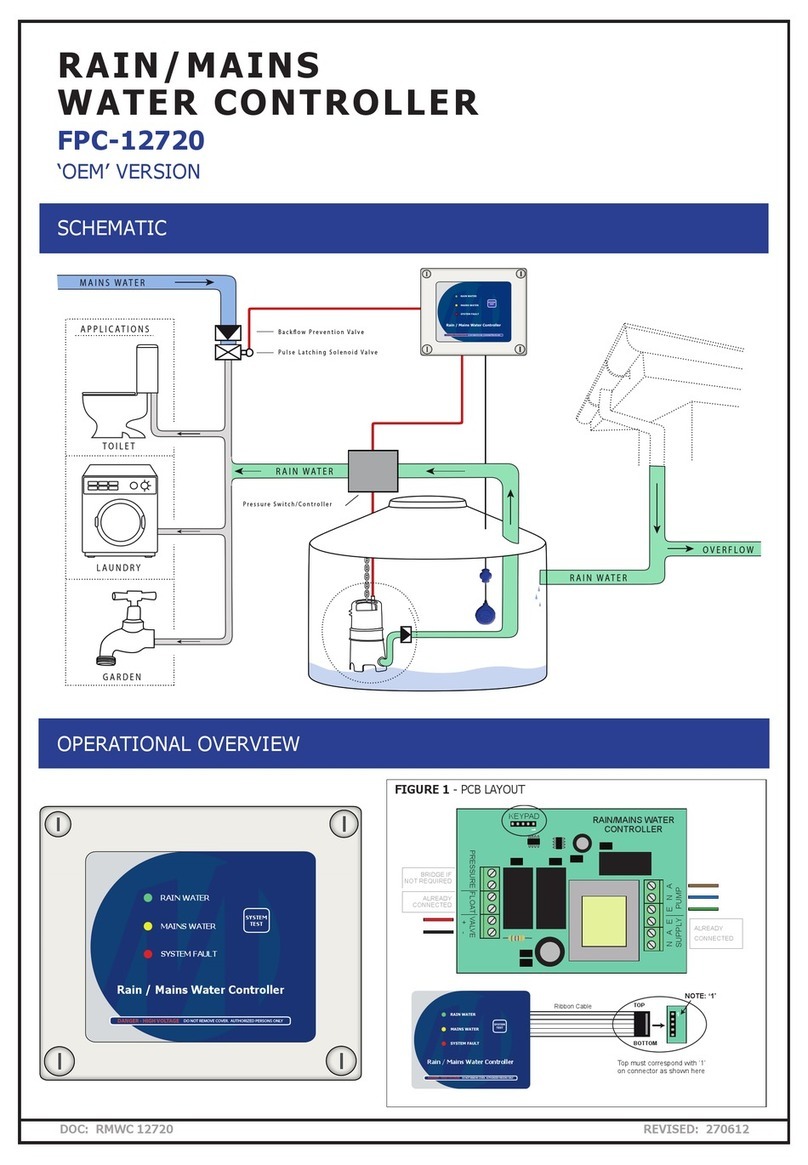
Matelec
Matelec FPC-12720 User manual
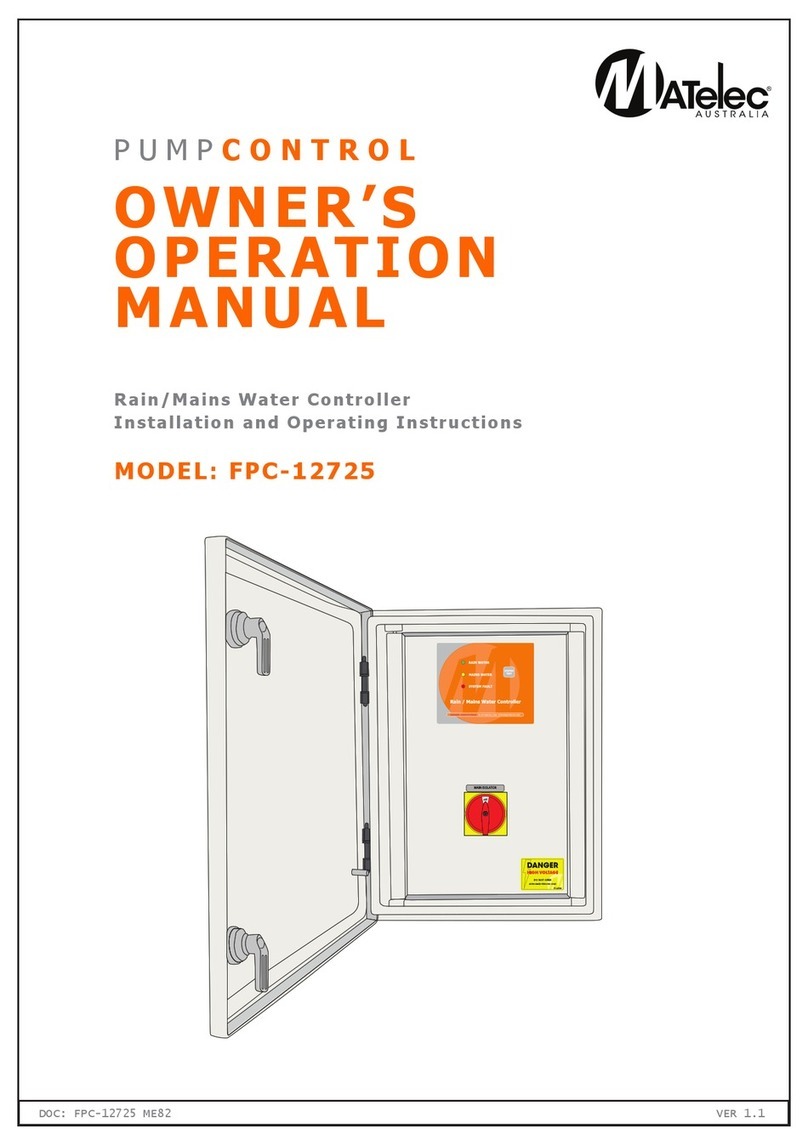
Matelec
Matelec FPC-12725 Instructions for use
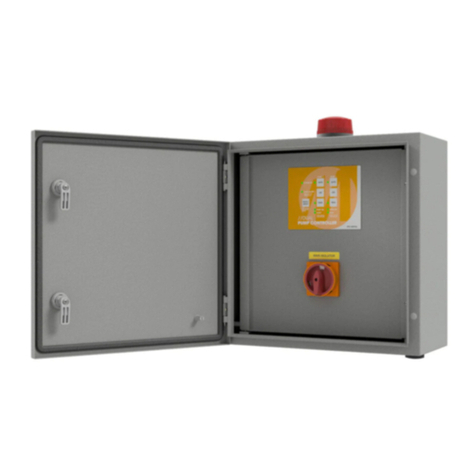
Matelec
Matelec FPC-30220 Instructions for use
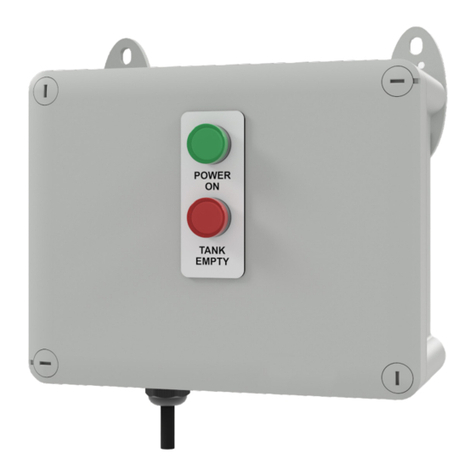
Matelec
Matelec FPC-11010 User manual
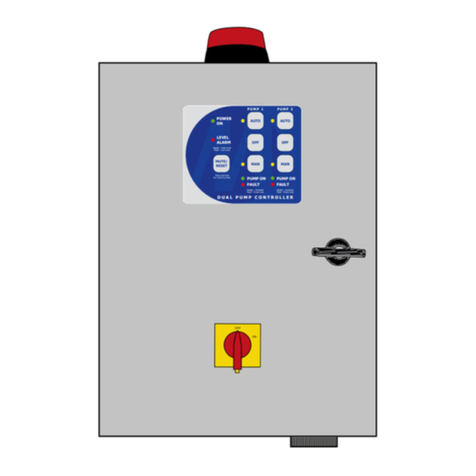
Matelec
Matelec RPC-30030 Instructions for use
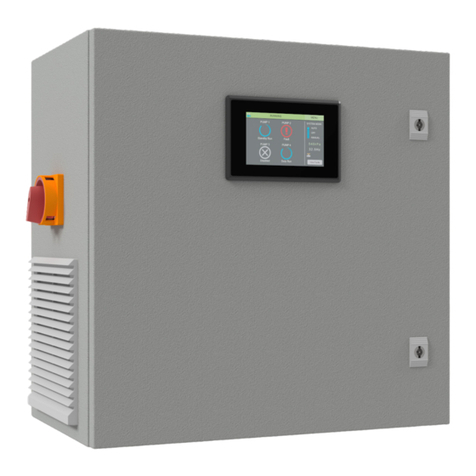
Matelec
Matelec Hydrowhiz FPC-63X21 User manual
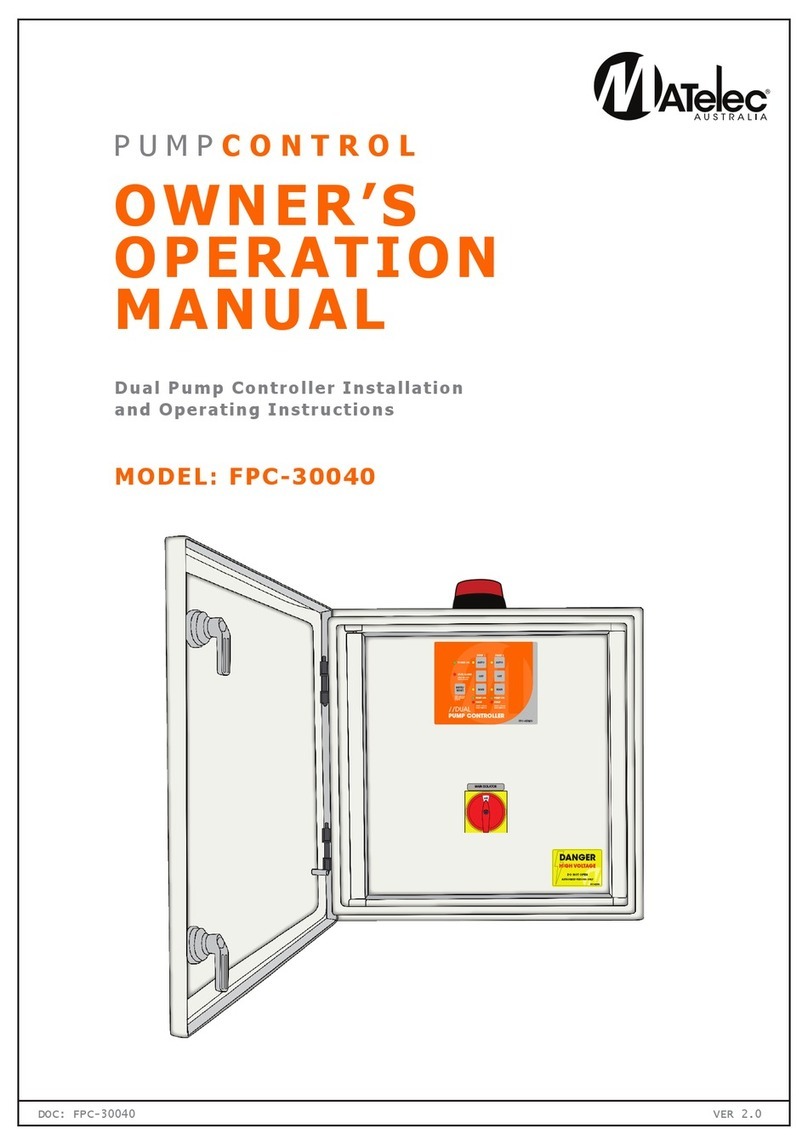
Matelec
Matelec FPC-30040 Instructions for use
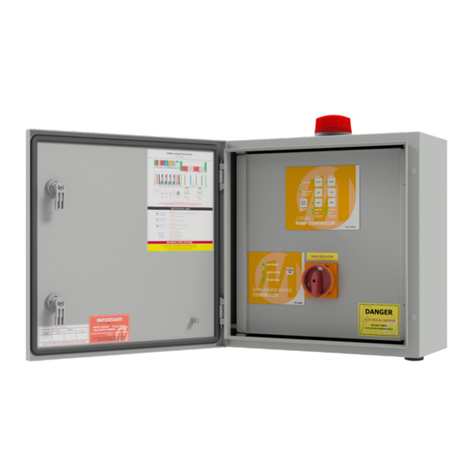
Matelec
Matelec FPC-32020 Instructions for use
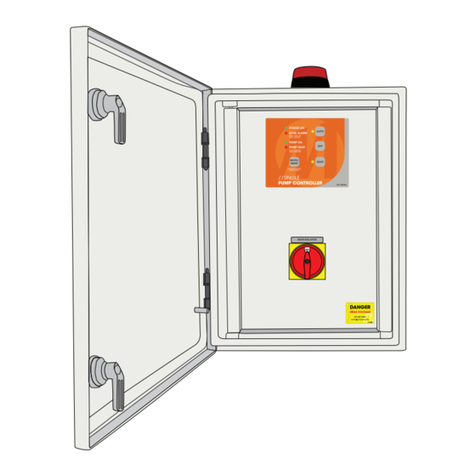
Matelec
Matelec FPC-15007-INT Instructions for use
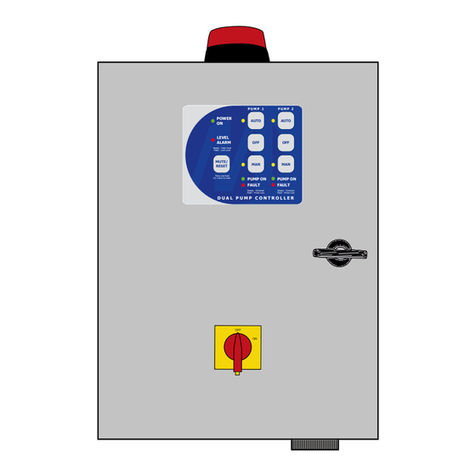
Matelec
Matelec FPC-30000 Instructions for use
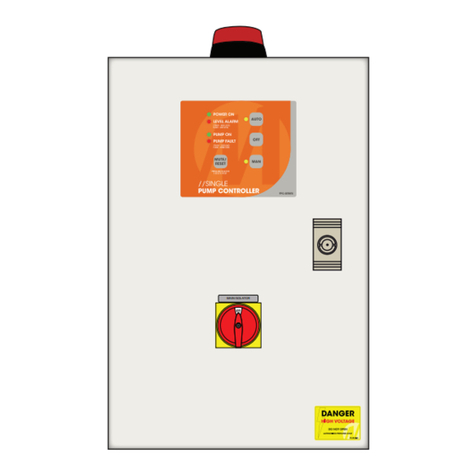
Matelec
Matelec FPC-15007-CON User manual
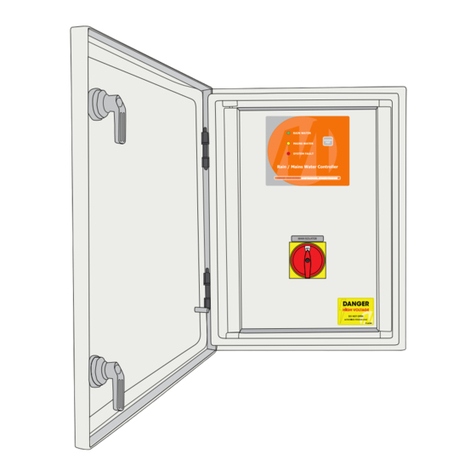
Matelec
Matelec FPC-12724 Instructions for use
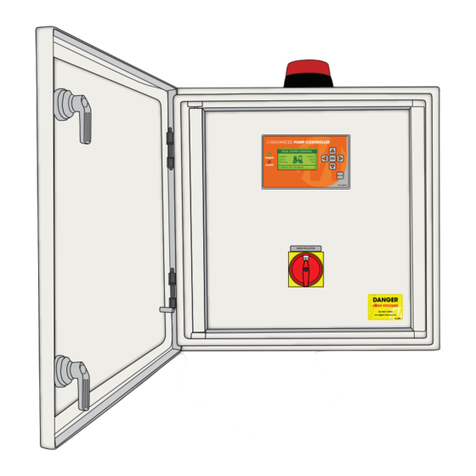
Matelec
Matelec FPC-36040 Instructions for use
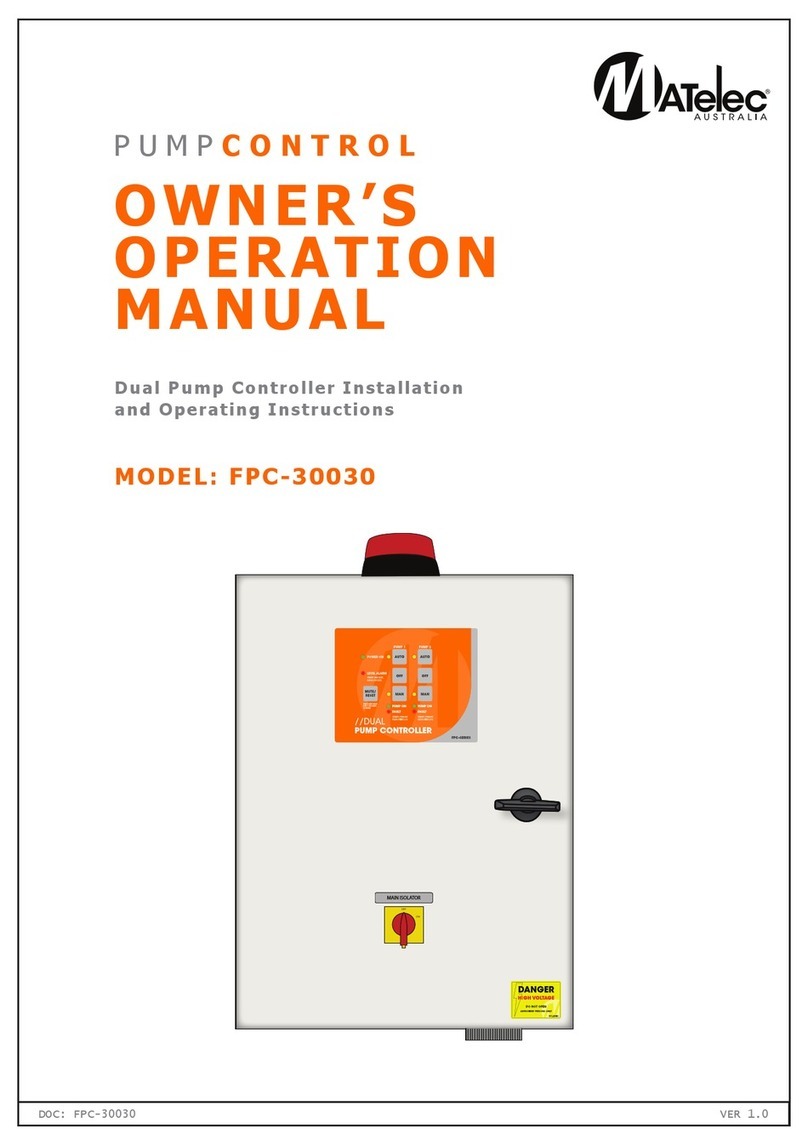
Matelec
Matelec FPC-30030 Instructions for use
Popular Controllers manuals by other brands
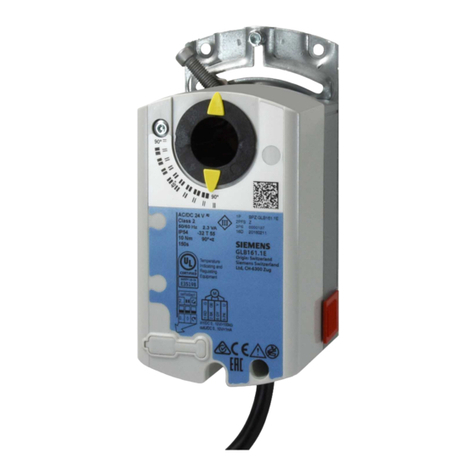
Siemens
Siemens OpenAir GLB 1E Series manual
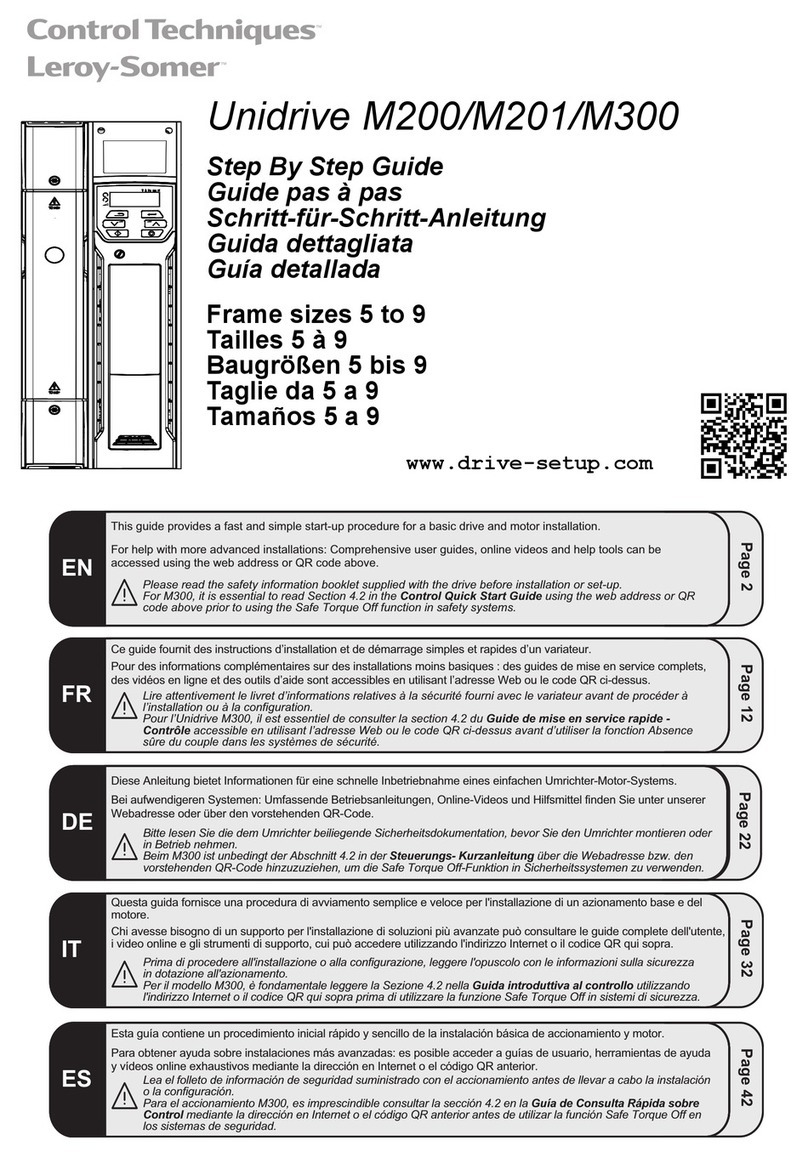
Control Techniques
Control Techniques Unidrive M200 Step-by-step guide
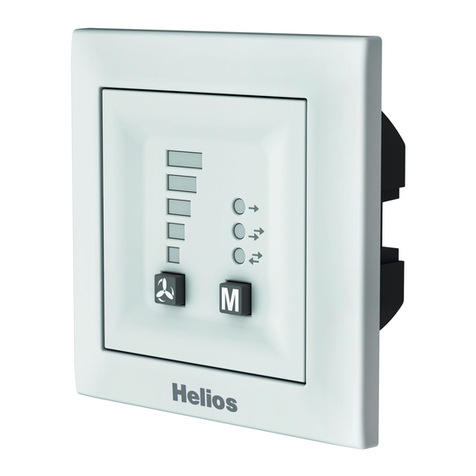
Helios
Helios KWL 45 BEU Installation and operating instructions
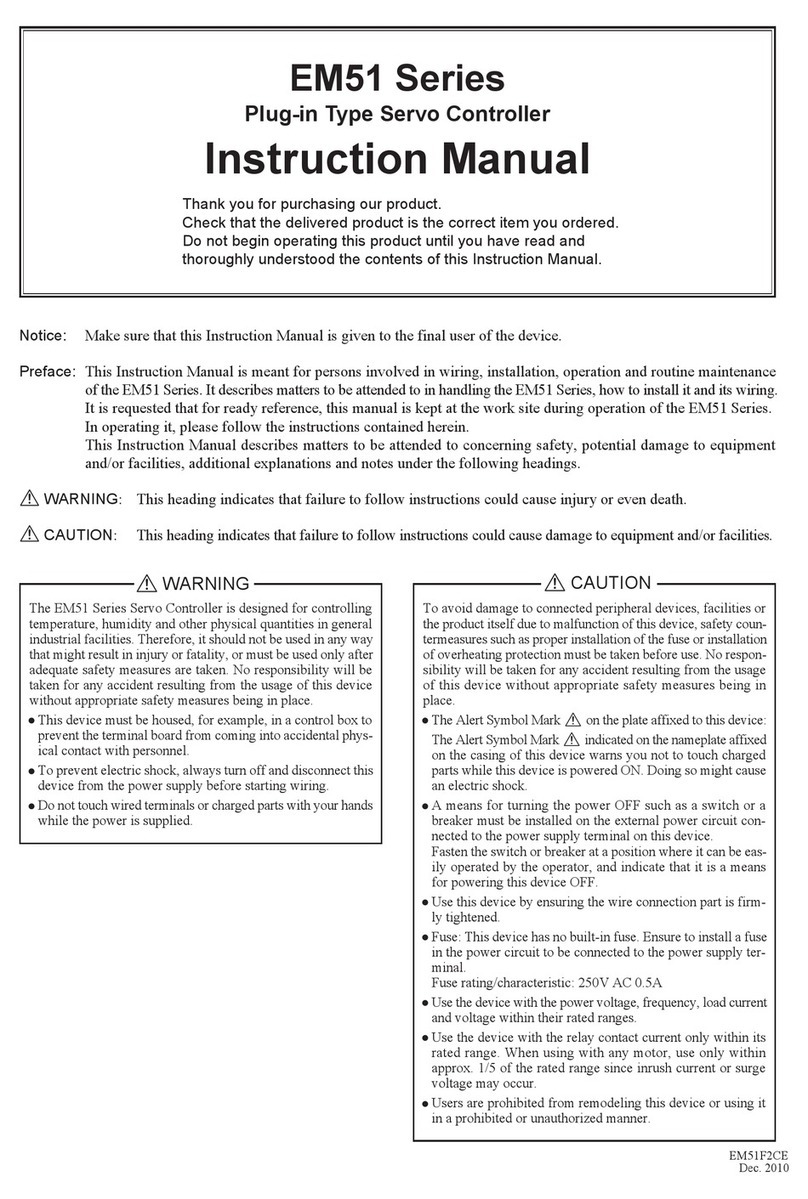
Shimaden
Shimaden EM51 series instruction manual
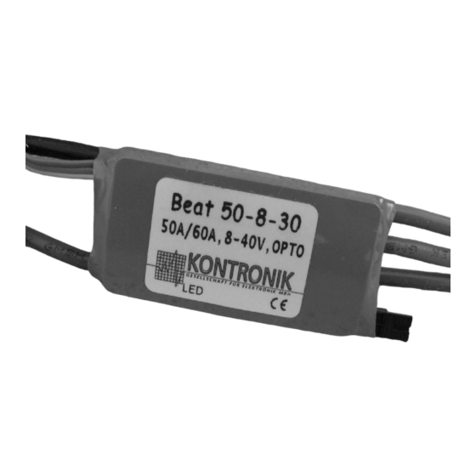
KONTRONIK
KONTRONIK BEAT Operation manual
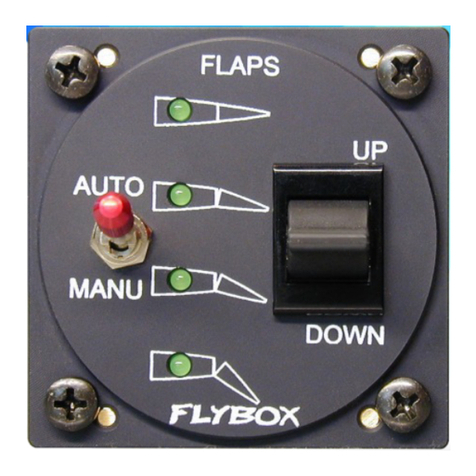
Flybox
Flybox EFC57-P Installation and user manual
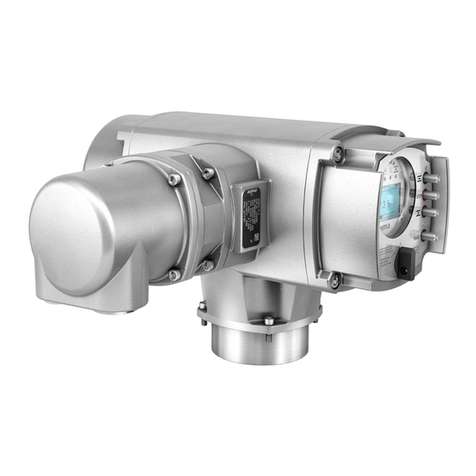
AUMA
AUMA ACVExC 01.2 Series Operation and setting Manual
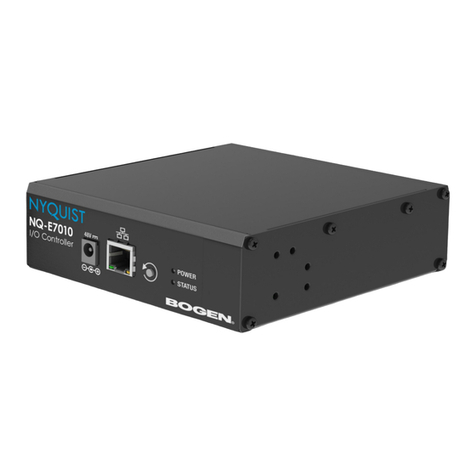
Bogen
Bogen NQ-E7010 Configuration guide
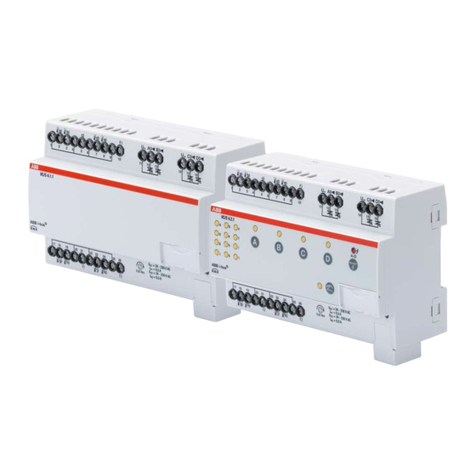
ABB
ABB i-bus VC/S 4 1 Series product manual

Mitsubishi
Mitsubishi FX-32E-TB/UL Hardware manual
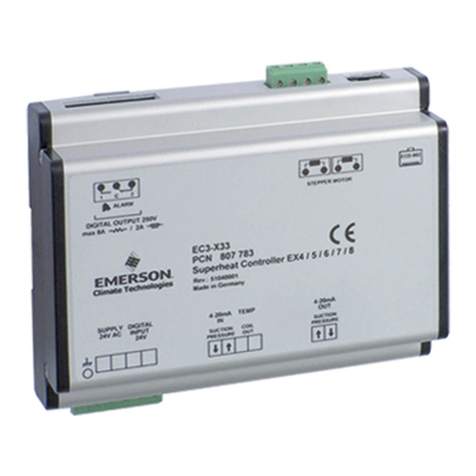
Emerson
Emerson Alco Controls EC3 Series operating instructions

maxon motor
maxon motor ESCON 36/3 EC Hardware reference