Memsic AHRS500GA Series User manual

Powerful Sensing Solutions for a Better Life
AHRS500GA Series
OPERATORS MANUAL
Document Part Number: 7430-0060-09 Rev A
MEMSIC, Inc., 1759 McCarthy Blvd, Milpitas, CA 95035
Tel: 408-964-9700, Fax: 408-854-7702

AHRS500GA-[] Series Operator’s Manual
Doc# 7430-0060-09 Rev. A Page ii
Revision History
Revision Date Author Comments
-01_A 9/16/02 JR Initial Release
-02_A 12/02 DJ Added limitation section, changed startup
time to 90 seconds
-03_A 11/03 DJ Changed the alignment process
-04_A 08/04 GB Updated manual to be specific to model
numbers -222 and -226. Updated the
installation drawing to reflect new models.
-05_A 12/04 DIP Added -224 and -220 models to support
external aiding.
-06_A 2/05 GB/DIP Updated address and MagAlign.
-07_A 8/05 GB/DIP Added -221, -223, -225 and -227 models.
Updated MagAlign.
-07_B 2/07 MPS Added Usage Clause
-07_C 8/07 MPS BIT Messages Updated
-08_A 11/09 PAL Added models -320 through -327 to
support improved dynamic response and
velocity aiding performance, and to
include MagAlign auto-leveling per ECO
1312
-09_A 12/10 AP Updated w/ MEMSIC logo and address
per ECO 1886
0WARNING
This product has been developed by MEMSIC exclusively for commercial applications. It has not been tested for, and MEMSIC makes no
representation or warranty as to conformance with, any military specifications or that the product is appropriate for any military application or
end-use. Additionally, any use of this product for nuclear, chemical, biological weapons, or weapons research, or for any use in missiles,
rockets, and/or UAV's of 300km or greater range, or any other activity prohibited by the Export Administration Regulations, is expressly
prohibited without the written consent of MEMSIC and without obtaining appropriate US export license(s) when required by US law. Diversion
contrary to U.S. law is prohibited.
©2010 MEMSIC, Inc. All rights reserved. Information in this document is subject to change without notice.
MEMSIC and SoftSensor are registered trademarks and AHRS500GA-[] is a trademark of MEMSIC, Inc. Other product and trade names are trademarks or
registered trademarks of their respective holders.

AHRS500GA-[] Series Operator’s Manual
Doc# 7430-0060-09 Rev. A Page iii
Table of Contents
1Introduction.................................................................................................................................................................................1
1.1 The AHRS500GA-[] Series Motion and Attitude Sensing Units........................................................................................1
2Package Contents........................................................................................................................................................................1
3AHRS500GA-[] Description ......................................................................................................................................................2
3.1 AHRS500GA-[] Coordinate System...................................................................................................................................2
3.2 Connections ........................................................................................................................................................................2
3.2.1 I/O Cable.....................................................................................................................................................................3
3.2.2 Power Input and Power Input Ground ........................................................................................................................3
3.2.3 Case Ground ...............................................................................................................................................................3
3.2.4 Serial Data Interface ...................................................................................................................................................3
3.2.5 BIT Status Output Pin.................................................................................................................................................4
3.2.6 Magnetometer alignment Input Pin.............................................................................................................................4
3.2.7 No Connection............................................................................................................................................................4
3.3 Measurements.....................................................................................................................................................................5
3.3.1 Attitude and Heading..................................................................................................................................................5
3.3.2 Sensor Measurements .................................................................................................................................................5
3.3.3 BIT Processing............................................................................................................................................................5
3.4 Commands..........................................................................................................................................................................6
3.5 Data Packet Format.............................................................................................................................................................7
3.6 Timing.................................................................................................................................................................................7
3.7 Magnetic Heading...............................................................................................................................................................8
3.8 External Velocity Input (models -22x and higher)..............................................................................................................8
4AHRS500GA-[] Operation.........................................................................................................................................................9
4.1 Normal Operation...............................................................................................................................................................9
4.2 Alignment Operation ..........................................................................................................................................................9
5Viewing AHRS500GA-[] Data with GyroView.......................................................................................................................10
5.1 GyroView Computer Requirements..................................................................................................................................10
5.2 Install GyroView...............................................................................................................................................................10
5.3 Connections ......................................................................................................................................................................10
5.4 Setup GyroView ...............................................................................................................................................................10
5.5 Take Measurements..........................................................................................................................................................11
6Limitations................................................................................................................................................................................11
6.1 Installation ........................................................................................................................................................................11
6.2 Alignment.........................................................................................................................................................................11
6.3 Operation in Magnetic Environment.................................................................................................................................11
6.4 Range Limitations.............................................................................................................................................................11
7AHRS500GA-[] Installation.....................................................................................................................................................12
8Warranty and Support Information...........................................................................................................................................13
8.1 Customer Service..............................................................................................................................................................13
8.2 Contact Directory..............................................................................................................................................................13
8.3 Return Procedure ..............................................................................................................................................................13
8.3.1 Authorization............................................................................................................................................................13
8.3.2 Identification and Protection.....................................................................................................................................13

AHRS500GA-[] Series Operator’s Manual
Doc# 7430-0060-09 Rev. A Page iv
8.3.3 Sealing the Container................................................................................................................................................13
8.3.4 Marking.....................................................................................................................................................................13
8.3.5 Return Shipping Address ..........................................................................................................................................14
8.4 Warranty ...........................................................................................................................................................................14
9Appendix A. Mechanical Specifications...................................................................................................................................15
10 Appendix B. AHRS500GA-[] Output Quick Reference.......................................................................................................17
11 Appendix C. Velocity Input Packet Format..........................................................................................................................18

AHRS500GA-[] Series Operator’s Manual
Doc# 7430-0060-09 Rev. A Page v
About this Manual
The following annotations have been used to provide additional information.
;NOTE
Note provides additional information about the topic.
;EXAMPLE
Examples are given throughout the manual to help the reader understand the terminology.
3IMPORTANT
This symbol defines items that have significant meaning to the user
0WARNING
The user should pay particular attention to this symbol. It means there is a chance that physical harm could happen to either the
person or the equipment.


AHRS500GA-[] Series Operator’s Manual
Doc# 7430-0060-09 Rev. A Page 1
1Introduction
1.1 The AHRS500GA-[] Series Motion and Attitude Sensing Units
This manual explains the use of the AHRS500GA-[] Series of products, nine-axis measurement system designed to measure
stabilized pitch, roll and yaw angles in a dynamic environment.
The AHRS500GA-[] is a nine-axis measurement system that combines linear accelerometers, rotational rate sensors, and
magnetometers. The AHRS500GA-[] uses the 3-axis accelerometer and 3-axis rate sensor to make a complete measurement of
the dynamics of your system. The addition of a 3-axis magnetometer also allows the AHRS500GA-[] to make a true
measurement of magnetic heading.
The AHRS500GA-[] is the solid-state equivalent of a vertical gyro/artificial horizon display combined with a directional gyro.
The AHRS500GA-[] series units are low power, fast turn on, reliable and accurate solutions for a wide variety of stabilization and
measurement applications.
See Table 3 for the serial interface for each AHRS500GA-[] model. Data is streamed continuously.
MEMSIC AHRS500GA-[] units employ onboard digital processing to compensate for deterministic error sources within the unit
and to compute attitude information. The AHRS500GA-[] units accomplish these tasks with an analog to digital converter and
high performance Digital Signal Processors.
The AHRS500GA-[] uses angular rate sensors and linear acceleration sensors that are micro-machined devices. The three angular
rate sensors consist of vibrating ceramic plates that utilize the Coriolis force to output angular rate independently of acceleration.
The three MEMS accelerometers are surface micro-machined silicon devices that use differential capacitance to sense
acceleration. Solid-state MEMS sensors make the AHRS500GA-[] both responsive and reliable. The magnetic sensors are state-
of-the-art miniature fluxgate sensors. Fluxgate sensors make the AHRS500GA-[] sensitive and responsive, with better
temperature performance than other technologies such as magneto-resistive sensors.
The AHRS500GA-[] Series of products utilize a sophisticated Kalman filter algorithm to allow the unit to track orientation
accurately through dynamic maneuvers. The Kalman filter will automatically adjust for changing dynamic conditions without
any external user input. No user intervention or configuration is required at power-up.
2Package Contents
In addition to your AHRS500GA-[] sensor product and the AHRS500GA-[] Series Operator’s Manual, you should have:
•1 CD with AHRS500 Installation MagAlign Software
AHRS500 Installation MagAlign Software graphically displays the AHRS500GA-[] output and provides step-by-step
alignment instructions on a PC running Microsoft® Windows™. You can also download this software from MEMSIC’s
web site at http://www.xbow.com.
•1 Digital Signal Alignment/Maintenance Cable.
This links the AHRS500GA-[] directly to a serial port. Only transmit, receive, power, ground and magnetometer
alignment pins are used. The magnetometer alignment switch is located on a cable stub attached to the PC connector
end.
•1 set of Mounting Hardware
Non-magnetic fasteners are provided to mount the AHRS500GA-[].
•AHRS500GA-[] Installation Manual
This contains the installation and alignment information for the AHRS500GA-[] model type ordered.
•AHRS500GA-[] Installation Drawing
•AHRS500GA-[] Installation Wiring Diagram

AHRS500GA-[] Series Operator’s Manual
Doc# 7430-0060-09 Rev. A Page 2
3AHRS500GA-[] Description
3.1 AHRS500GA-[] Coordinate System
The AHRS500GA-[] uses the following coordinate system. With the connector facing you, and the mounting plate down, the axes
are defined as:
X-axis – from face with connector through the AHRS500GA
Y-axis – along the face with connector from left to right
Z-axis – along the face with the connector from top to bottom
This is the default configuration for the generic AHRS500GA-[] model. Other coordinate frame orientations are supported given
the model type purchased, and these will be reflected in the label as well as through the model configuration number. The axes
form an orthogonal right-handed coordinate system. Acceleration is positive when it is oriented towards the negative side of the
coordinate axis. For example, with the AHRS500GA-[] sitting on a level table, it will measure zero g along the x- and y-axes and
+1 g along the z-axis. Gravitational acceleration is directed downward, and thus will be defined as positive for the AHRS500GA-
[] z-axis.
The angular rate sensors are aligned with these same axes. The rate sensors measure angular rotation rate around a given axis.
The rate measurements are labeled by the appropriate axis. The direction of a positive rotation is defined by the right-hand rule.
With the thumb of your right hand pointing along the axis in a positive direction, your fingers curl around in the positive rotation
direction. For example, if the AHRS500GA-[] is sitting on a level surface and you rotate it clockwise on that surface, this will be
a positive rotation around the z-axis. The x- and y-axis rate sensors would measure zero angular rates, and the z-axis sensor
would measure a positive angular rate.
The magnetic sensors are aligned with the same axes definitions and sign as the linear accelerometers.
Pitch is defined positive for a positive rotation around the y-axis (pitch up). Roll is defined as positive for a positive rotation
around the x-axis (roll right). Yaw is defined as positive for a positive rotation around the z-axis (turn right).
The angles are defined as standard Euler angles using a 3-2-1 system. To rotate from the body frame to an earth-level frame, roll
first, then pitch, and then yaw.
3.2 Connections
The AHRS500GA-[] has a male DB-15 connector. The signals are as shown in Table 1.
Table 1 Connector Pin Assignments
Pin Signal Electrical Specifications
1 RS-232 Transmit +/- 4.5 VDC min wrt power ground.
2 RS-232 Receive +/- 25 VDC max wrt power ground.
3 VDC Power Input 10-40 VDC normal, 9VDC emergency
4 Power Input Ground
5 No connection Do not connect
6 No connection Do not connect
7 RS-422 Transmit + A
8 RS-422 Transmit – A 2.0 VDC differential output (min) into 100 ohms. Common mode output voltage,
3VDC max.
9 Signal Ground Capacitive coupling to internal system ground. Should be connected to user’s
system ground to reduce RS-232 and RS-422 signal noise.
10 Factory mode pin Factory reserved; do not connect
11 Factory mode pin Factory reserved; do not connect
12 Magnetometer alignment input (hard
and soft iron cal) Active: Short to power ground.
Inactive: Open circuit. (Internally pulled to +3.3VDC through 10Kohm resistor)
13 Hardware BIT Status Open collector, requires user pull-up resistor. Max pull-up voltage: +15VDC
Max current sink: 10mA.

AHRS500GA-[] Series Operator’s Manual
Doc# 7430-0060-09 Rev. A Page 3
14 RS-422 Receive + A
15 RS-422 Receive – A Common mode input voltage range: 3VDC wrt power ground.
N/A Case Ground Electrically connected to I/O connector shell
ter alignment, and
provide routine magnetometer alignment maintenance of the system, and will not provide adequate shielding.
perate with either a nominal 14VDC
or 28VDC aircraft power system and me .
lectric
Item GA-[] specification
3.2.1 I/O Cable
The user must provide a shielded cable with the shield connected to the I/O connector shell in order to provide the required EMI
protection. The cable sent with the unit is intended to provide the user with the ability to perform a magnetome
3.2.2 Power Input and Power Input Ground
The AHRS500GA-[] power requirements are described in the table below. It is designed to o
ets all DO-160D, part 16, category B requirements
Table 2 E al Power Input Requirements
Requirement AHRS500
1. pply 10-40 VDCInput Su
voltage
2. ly
Current Amp (max)
Input Supp 1
3.2.3 Case Ground
The case is electrically connected to the I/O connector shell. The shell should be electrically connected to the user’s cable shield.
The case is isolated from the Power Input Ground, and should be bolted to a good conducting surface that is grounded.
the model configuration chosen. Data output is continuous at a fixed frequency dependant on the baud rate
(see table 3 below).
3.2.4 Serial Data Interface
The interface specification is a factory configurable RS-422 or RS-232, also with factory configurable baud rates (see table
below) depending on

AHRS500GA-[] Series Operator’s Manual
Doc# 7430-0060-09 Rev. A Page 4
Table 3 Supported BAUD Rates and Output Rates
Model :
AHRS500GA Interface BAUD
Rate Output
Rate Connector
Facing
-200 RS-232 38400 100 AFT
-201 RS-232 38400 100 FORWARD
-202 RS-232 9600 25 AFT
-203 RS-232 9600 25 FORWARD
-204 RS-232 9600 25 AFT
-205 RS-232 9600 25 FORWARD
-206 RS-422 38400 100 AFT
-207 RS-422 38400 100 FORWARD
-220*RS-232 38400 100 AFT
-221*RS-232 38400 100 FORWARD
-222*RS-232 9600 25 AFT
-223*RS-232 9600 25 FORWARD
-224*RS-232 9600 25 AFT
-225*RS-232 9600 25 FORWARD
-226*RS-422 38400 100 AFT
-227*RS-422 38400 100 FORWARD
-320* RS-232 38400 100 AFT
-321* RS-232 38400 100 FORWARD
-322* RS-232 9600 25 AFT
-323* RS-232 9600 25 FORWARD
-324* RS-232 9600 25 AFT
-325* RS-232 9600 25 FORWARD
-326* RS-422 38400 100 AFT
-327* RS-422 38400 100 FORWARD
*Refer to Appendix C for input velocity data packet format
3.2.5 BIT Status Output Pin
The BIT status output pin will become active high if the system is experiencing a failure. The BIT is an open collector signal and
requires a pull-up resistor for proper operation.
3.2.6 Magnetometer alignment Input Pin
The AHRS500GA-[] has an input pin to control the magnetometer hard-iron alignment function. When this pin is active (low) the
unit will collect the data necessary for magnetometer alignment. When it becomes inactive, the alignment data shall be used to
compute the hard and soft iron compensation values. During normal operation, no connection should be made to this pin; this pin
shall be tied high internally with a pull-up resistor. This feature has been added as a means to perform a Hard Iron/Soft Iron
alignment without sending the alignment commands to the unit. Please see the AHRS500GA-[] Installation Manual for a
complete explanation of the Hard Iron/Soft Iron alignment process, and how this pin can be used as a means of implementing the
alignment.
3.2.7 No Connection
During normal operation of the AHRS500GA-[], no connection is made to the factory test pin. This pin has an internal pull-up
mechanism and must have no connection for the AHRS500GA-[] to operate properly.

AHRS500GA-[] Series Operator’s Manual
Doc# 7430-0060-09 Rev. A Page 5
3.3 Measurements
The AHRS500GA-[] Series is designed to operate as a complete attitude and heading reference system. See the “Data Packet
Format” section for the actual structure of the data packet.
3.3.1 Attitude and Heading
The AHRS500GA-[] acts as a complete attitude and heading reference system and outputs the stabilized pitch, roll, and yaw
angles along with the angular rate, acceleration, and magnetic field information. The angular rate, acceleration, and magnetic
field values are calculated as described in the sensor section.
The Kalman filter operates in angle mode to track the rate sensor bias and calculate the stabilized roll, pitch, and yaw angles.
The AHRS500GA-[] uses the angular rate sensors to integrate over your rotational motion and find the actual pitch, roll, and yaw
angles. The AHRS500GA-[] uses the accelerometers to correct for rate sensor drift in the vertical angles (pitch and roll); the
AHRS500GA-[] uses the magnetometers to correct for rate sensor drift in the yaw angle. This is the modern equivalent of an
analog vertical gyro that used a plumb bob in a feedback loop to keep the gyro axis stabilized to vertical. The AHRS500GA-[]
takes advantage of the rate gyros’ sensitivity to quick motions to maintain an accurate orientation when accelerations would
otherwise throw off the accelerometers measurement of the AHRS500GA-[] orientation relative to gravity; the AHRS500GA-[]
then uses the accelerometers to provide long term stability to keep the rate gyro drift in check.
The AHRS500GA-[] uses a sophisticated Kalman filter algorithm to track the bias in the rate sensors. This allows the
AHRS500GA-[] to use a very low effective weighting on the accelerometers when the AHRS500GA-[] is moved. This makes the
AHRS500GA-[] very accurate in dynamic maneuvers.
The AHRS500GA-[] outputs the stabilized pitch, roll and yaw angles in the digital data packet in angle mode. To convert the
digital data to angle, use the following relation:
angle = data*(SCALE)/215
where angle is the actual angle in degrees (pitch, roll or yaw), data is the signed integer data output in the data packet, and
SCALE is a constant. SCALE = 180°for roll, pitch and yaw.
3.3.2 Sensor Measurements
The analog accelerometer and gyro sensors are sampled, converted to digital data, temperature compensated, corrected for
misalignment, and scaled to engineering units. The digital data represents the actual value of the quantities measured. A
calibration table for each sensor is stored in the AHRS500GA-[] non-volatile memory. The data is sent as signed 16-bit 2’s
complement integers. To convert the acceleration data into G’s, use the following conversion:
accel = data*(10 * 1.5)/215
where accel is the actual measured acceleration in G’s, data is the digital data sent by the AHRS500GA, and 10 is the G Range
for your AHRS500GA. (The data is scaled so that 1 G = 9.80 m s-2.) This maximum G range is a default value.
To convert the angular rate data into degrees per second, use the following conversion:
rate = data*(800*1.5)/215
where rate is the actual measured angular rate in °/sec, data is the digital data sent by the AHRS500GA, and 800 is the Angular
rate Range of the AHRS500GA. This maximum angular rate is a default value.
3.3.3 BIT Processing
The BIT message in each packet provides comprehensive information into system health. The following information is supplied
in the BIT byte fields of the data packet. Table 4 contains the actual bit definition present in the two-byte output BIT field in the
angle mode data packet (see section 3.5 below).
Table 4 BIT Message Definition
Bit BIT Data Description
0 Hard Failure 0: No hard failure
1: An unrecoverable failure has been detected
1 Soft Failure 0: No soft failure
1: A soft failure has been detected. If the soft failure lasts for more than 4500
data packets the Hard Failure bit is turned on and the Soft Failure bit is

AHRS500GA-[] Series Operator’s Manual
Doc# 7430-0060-09 Rev. A Page 6
permanently on.
2 Reserved
3 Power Failure 0: No power failure
1: A power loss has been detected and the system is running on back-up
power. Power loss will occur within 200 msec.
4 Comm Error 0: No serial port communication failure has been detected.
1: A serial port communications failure has been detected such as overrun,
parity.
5 Reboot Detect 0: No warm reboot of the processor has been detected.
1: A warm processor reboot was detected possibly due to a watchdog timeout
or low-power setting.
6 Calibration Failure 0: Calibration table in flash memory is correct.
1: A bad calibration table in flash memory has been detected.
7*External Aiding Comm Status 0: Receiving and processing valid external aiding data packets
1: External aiding data not present or bad external aiding data
8 Coordinated Turn
Detect 0: Unit is not executing a coordinated turn
1: Unit is executing a coordinated turn
9 Magnetometer Align Status
(MSB) 10: Remote magnetometer or internal magnetometer hard iron/soft iron
alignment in progress
11: Remote magnetometer heading offset alignment in progress
10 Algorithm Status 0: Full accuracy data
1: Not ready, waiting for power-up, post gyro saturation, or initialization
11 Magnetometer Align Status
(LSB) 00: No magnetometer alignment being performed
01: Remote magnetometer leveling in progress
12 Magnetometer Leveling Status 0: Remote magnetometer leveling valid
1: Remote magnetometer leveling invalid
13 Hardiron/Softiron Valid 0: Magnetometer hard iron/soft iron alignment valid
1: Magnetometer hard iron/soft iron alignment invalid
14 Heading Offset 0: Remote magnetometer heading offset alignment is valid
1: Remote magnetometer heading offset alignment is invalid
15*Remote Magnetometer Comm
Status 0: Communication with Remote Magnetometer valid (processing data
packets)
1: Communication with Remote Magnetometer invalid (no data packets being
processed)
*External aiding AND Remote magnetometer do not apply to models -200, -201, -202, -203, -204, -205, -206 and -207
3.4 Commands
The AHRS500GA-[] does not have a command structure. The default serial interface is provided in table 3 with serial port
settings of 8 data bits, 1 start bit, 1 stop bit, no parity, and no flow control.

AHRS500GA-[] Series Operator’s Manual
Doc# 7430-0060-09 Rev. A Page 7
3.5 Data Packet Format
In general, the digital data representing each measurement is sent as a 16-bit number (two bytes). The data is sent MSB first then
LSB.
Table 5 AHRS500GA-[] Series Data Packet Format
Byte Data
0 Header (0xAA)
1 Header (0x55)
2 Roll Angle (MSB)
3 Roll Angle (LSB)
4 Pitch Angle (MSB)
5 Pitch Angle (LSB)
6 Heading Angle (MSB)
7 Heading Angle (LSB)
8 Roll Angular Rate (MSB)
9 Roll Angular Rate (LSB)
10 Pitch Angular Rate (MSB)
11 Pitch Angular Rate (LSB)
12 Yaw Angular Rate (MSB)
13 Yaw Angular Rate (LSB)
14 X-Axis Acceleration (MSB)
15 X-Axis Acceleration (LSB)
16 Y-Axis Acceleration (MSB)
17 Y-Axis Acceleration (LSB)
18 Z-Axis Acceleration (MSB)
19 Z-Axis Acceleration (LSB)
20 Model Number (MSB)
21 Model Number (LSB)
22 BIT (MSB)
23 BIT (LSB)
24 Checksum (MSB)
25 Checksum (LSB)
These numbers are sent as a 16-bit signed integer in 2's complement format. The data is sent as two bytes, MSB first then LSB.
Each data packet will begin with a two-byte header (hex AA 55) and end with a two-byte checksum. The checksum is calculated
in the following manner:
1. Sum all packet contents except header and checksum.
2. Divide the sum by hex FFFF.
3. The remainder should equal the checksum.
The packet also contains the model type configuration number, and the BIT word output. Please refer to section 3.3.3 for details
about the BIT word processing.
3.6 Timing
The AHRS500GA-[] data output rate is set based on the model configuration chosen. See table 3 for currently supported output
rates. Depending on the configuration chosen, the system output sample rate can be set to a different constant value.

AHRS500GA-[] Series Operator’s Manual
Doc# 7430-0060-09 Rev. A Page 8
In some applications, using the AHRS500GA-[]’s digital output requires a precise understanding of the internal timing of the
device. The processor internal to the AHRS500GA-[] runs in a loop - collecting data from the sensors, processing the data, and
then collecting more data. The data is reported to the user through a parallel process.
The unit goes through three processes in one data cycle. First, the sensors are sampled. Second, the unit processes the data for
output. After processing the data, the AHRS500GA-[] will make another measurement while presenting the current measurement
for output. Third, the unit actually transfers the data out over the RS-232 port.
3.7 Magnetic Heading
Magnetic north is the direction toward the magnetic north pole; true north is the direction towards the true North Pole.
The AHRS500GA-[] yaw angle output is referenced to magnetic north. The direction of true north will vary from magnetic north
depending on your position on the earth. The difference between true and magnetic north is called declination or magnetic
variance. You will need to know your declination to translate the AHRS500GA-[] magnetic heading into a heading referenced to
true north.
3.8 External Velocity Input (models -22x and higher)
An external velocity input is accepted (when available) to provide improved accuracy on high performance aircraft capable of
sustained acceleration and deceleration. The AHRS500GA-22x models (and higher) include a communications interface
designed to listen for external velocity sensor information. This interface determines when the velocity information is available on
the input port (RS232 UART), parses the velocity information, and makes the airspeed data available for use in the attitude
algorithm. In the event that the external velocity data is not present, or the external velocity data fails after correct operation, the
algorithm reverts back to the standard algorithm defined above. The external velocity input packet format is defined in Appendix
C.

AHRS500GA-[] Series Operator’s Manual
Doc# 7430-0060-09 Rev. A Page 9
4AHRS500GA-[] Operation
4.1 Normal Operation
The AHRS500GA-[] is configured to output data continuously when power is applied. The AHRS500GA-[] does not recognize
any input serial commands. A magnetic alignment process must be completed before use of the AHRS500GA-[]. See the
AHRS500GA-[] Installation Manual for specific instructions. The AHRS500GA-[] requires a 90 second initialization period after
power is applied before the output data is valid. Valid data is indicated by the BIT status word having all bits cleared to zero,
indicating no BIT failures, a valid magnetometer alignment, and completion of initialization.
4.2 Alignment Operation
The AHRS500GA-[] can be commanded to perform a hard/soft iron alignment for the magnetometers using the procedure in the
AHRS500GA-[] Installation Manual. Data supplied during normal operation will not be available and the data output should not
be used for flight purposes.

AHRS500GA-[] Series Operator’s Manual
Doc# 7430-0060-09 Rev. A Page 10
5Viewing AHRS500GA-[] Data with GyroView
MEMSIC includes GyroView software to allow you to directly view the AHRS500GA-[] data.
5.1 GyroView Computer Requirements
The following are minimum capabilities that your computer should have to run GyroView successfully:
•CPU: Pentium-class
•RAM Memory: 32MB minimum, 64MB recommended
•Hard Drive Free Memory: 15MB
•Operating System: Windows 95, 98, NT4, 2000, XP
5.2 Install GyroView
To install GyroView in your computer:
1. Insert the CD “Support Tools” in the CD-ROM drive.
2. Find the GyroView folder. Double click on the setup file.
3. Follow the setup wizard instructions. You will install GyroView and a LabVIEW Runtime Engine. You will need both
these applications.
If you have any problems or questions, you may contact MEMSIC directly.
5.3 Connections
The AHRS500GA-[] is shipped with an alignment/maintenance cable to connect the AHRS500GA-[] to a PC communications
port.
1. Connect the 15-pin end of the digital signal alignment/maintenance cable to the port on the AHRS500GA-[].
2. Start the PC before connecting the alignment/maintenance cable to the serial port of your computer. Some versions of
Windows treat a serial connection at boot time as a signal that a serial mouse is connected to the serial port. The serial
mouse driver will be loaded and the AHRS500GA-[] output will drive the cursor around the screen.
3. Connect the 9-pin end of the alignment/maintenance cable to the serial port of your computer.
4. Connect the 15-pin end of the digital signal alignment/maintenance cable to the aircraft mating cable.
5. Bolt the base of the unit to a grounded surface. A good ground is required for EMI and lightning over-voltage
protection.
0WARNING
Do not reverse the power leads! Applying the wrong power to the AHRS500GA-[] can damage the unit.
5.4 Setup GyroView
With the AHRS500GA-[] connected to your PC serial port and powered, open the GyroView software (Rev 2.3 or later).
1. GyroView should automatically detect the AHRS500GA-[] and display the serial data connection information.
2. If GyroView does not connect, check that you have the correct COM port selected. You find this under the “DMU”
menu.
3. Select the type of display you want under the menu item “Windows”. Graph displays a real time graph of all the
AHRS500GA-[] data; FFT displays a Fast-Fourier transform of the data; Navigation shows an artificial horizon display.
4. You can log data to a file by entering a data file name. You can select the rate at which data is saved to disk.
5. If the status indicator says, “Connected”, you’re ready to go. If the status indicator doesn’t say connected, check the
connections between the AHRS500GA-[] and the computer; check the power; check the serial COM port assignment on
your computer.

AHRS500GA-[] Series Operator’s Manual
Doc# 7430-0060-09 Rev. A Page 11
5.5 Take Measurements
Once you have configured GyroView to work with your AHRS500GA-[], pick what kind of measurement you wish to see.
“Graph” will show you the output you choose as a strip-chart type graph of value vs. time. “FFT” will show you a real-time Fast-
Fourier transform of the output you choose. “Navigation” will show an artificial horizon and the stabilized pitch and roll output
of the AHRS500GA-[].
Let the AHRS500GA-[] warm up for 90 seconds when first turned on. This allows the Kalman filter to estimate the rate sensor
biases. Now you’re ready to use the AHRS500GA-[]!
6Limitations
6.1 Installation
The AHRS500GA-[] must be mounted in accordance with the procedures outlined in the AHRS500GA-[] Installation Manual.
The AHRS500GA-[] must be mounted in a location with limited magnetic material near the unit. Refer to the installation manual
for detailed instructions.
6.2 Alignment
The AHRS500GA-[] must successfully complete a hard iron alignment to reach full accuracy. Refer to the AHRS500GA-[]
installation manual for detailed instructions.
6.3 Operation in Magnetic Environment
Introduction of large ferrous or magnetic material objects close to the AHRS500GA-[], after alignment, will affect the heading
performance. Maintain at least 24 inches of distance between moving ferrous metal or magnetic material and the AHRS500GA-
[].
6.4 Range Limitations
The internal sensors in the AHRS500GA-[] are limited to maneuvers of less than 200 deg/sec and less than 10 Gs acceleration in
bank, pitch, and heading. Over range of a sensor is indicated in the data packet message to the display system. Over range will
start a new initialization cycle of the AHRS500GA-[] and will require 90 seconds of straight and level flight to reinitialize the
AHRS500GA-[].
The AHRS500GA-[], like all magnetometer and magnetic compass-based systems, will not perform properly at the magnetic
North and South Poles.
The AHR500GA-[] will not operate properly in low gravitational fields and magnetic fields encountered during space flight.

AHRS500GA-[] Series Operator’s Manual
Doc# 7430-0060-09 Rev. A Page 12
7AHRS500GA-[] Installation
Refer to the AHRS500GA-[] Installation Manual (Doc# 7410-0001-08) for detailed mounting instructions for the AHRS500GA-
[].

AHRS500GA-[] Series Operator’s Manual
Doc# 7430-0060-09 Rev. A Page 13
8Warranty and Support Information
8.1 Customer Service
As a MEMSIC customer you have access to product support services, which include:
•Single-point return service
•Web-based support service
•Same day troubleshooting assistance
•Worldwide MEMSIC representation
•Onsite and factory training available
•Preventative maintenance and repair programs
•Installation assistance available
8.2 Contact Directory
United States: Phone: 1-408-965-3300 (8 AM to 5 PM PST)
Fax: 1-408-854-7702 (24 hours)
Non-U.S.: Refer to website www.memsic.com
8.3 Return Procedure
8.3.1 Authorization
Before returning any equipment, please contact MEMSIC to obtain a Returned Material Authorization number (RMA).
Be ready to provide the following information when requesting an RMA:
•Name
•Address
•Telephone, Fax, Email
•Equipment Model Number
•Equipment Serial Number
•Installation Date
•Failure Date
•Fault Description
•Will it connect to GyroView?
8.3.2 Identification and Protection
If the equipment is to be shipped to MEMSIC for service or repair, please attach a tag TO THE EQUIPMENT, as well as the
shipping container(s), identifying the owner. Also indicate the service or repair required, the problems encountered, and any
other information considered valuable to the service facility such as the list of information provided to request the RMA number.
Place the equipment in the original shipping container(s), making sure there is adequate packing around all sides of the
equipment. If the original shipping containers were discarded, use heavy boxes with adequate padding and protection.
8.3.3 Sealing the Container
Seal the shipping container(s) with heavy tape or metal bands strong enough to handle the weight of the equipment and the
container.
8.3.4 Marking
Please write the words, “FRAGILE, DELICATE INSTRUMENT” in several places on the outside of the shipping container(s).
In all correspondence, please refer to the equipment by the model number, the serial number, and the RMA number.

AHRS500GA-[] Series Operator’s Manual
Doc# 7430-0060-09 Rev. A Page 14
8.3.5 Return Shipping Address
Use the following address for all returned products:
MEMSIC, Inc.
1751 McCarthy Blvd.
Milpitas, CA 95035
Attn: RMA Number (XXXXXX)
8.4 Warranty
The MEMSIC product warranty is one year from date of shipment.
This manual suits for next models
24
Table of contents
Other Memsic Measuring Instrument manuals
Popular Measuring Instrument manuals by other brands
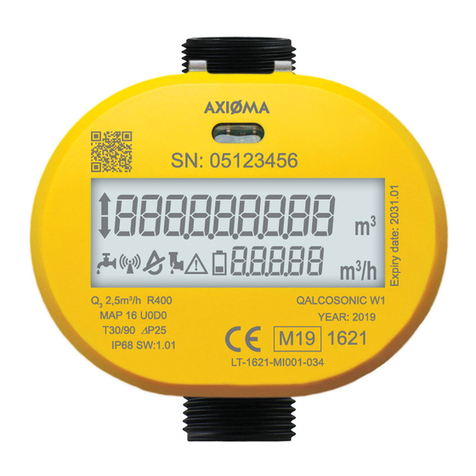
AXIOMA METERING UAB
AXIOMA METERING UAB QALCOSONIC W1 TECHNICAL DESCRIPTION, INSTALLATION MANUAL AND USER GUIDE
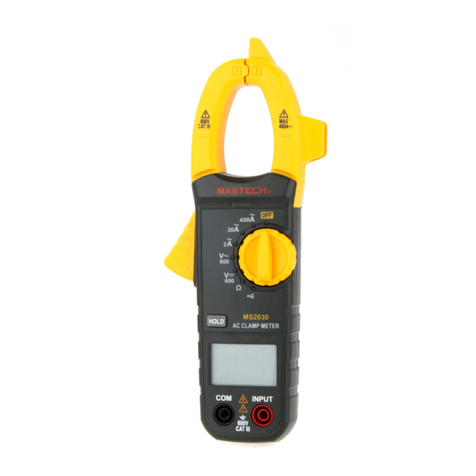
Mastech
Mastech MS2030 manual
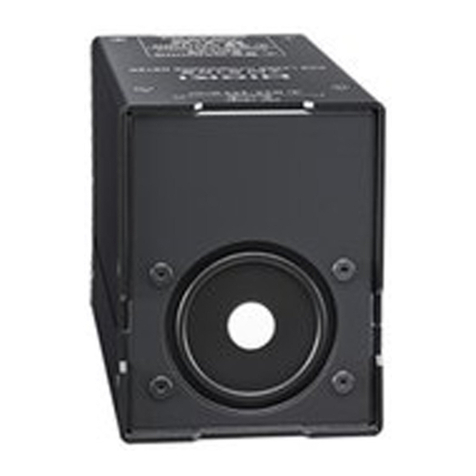
Hioki
Hioki TM6102 Communication instruction manual
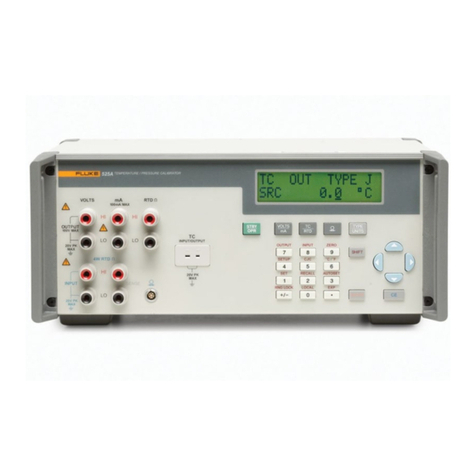
Fluke Calibration
Fluke Calibration 525B/A0 120V user manual
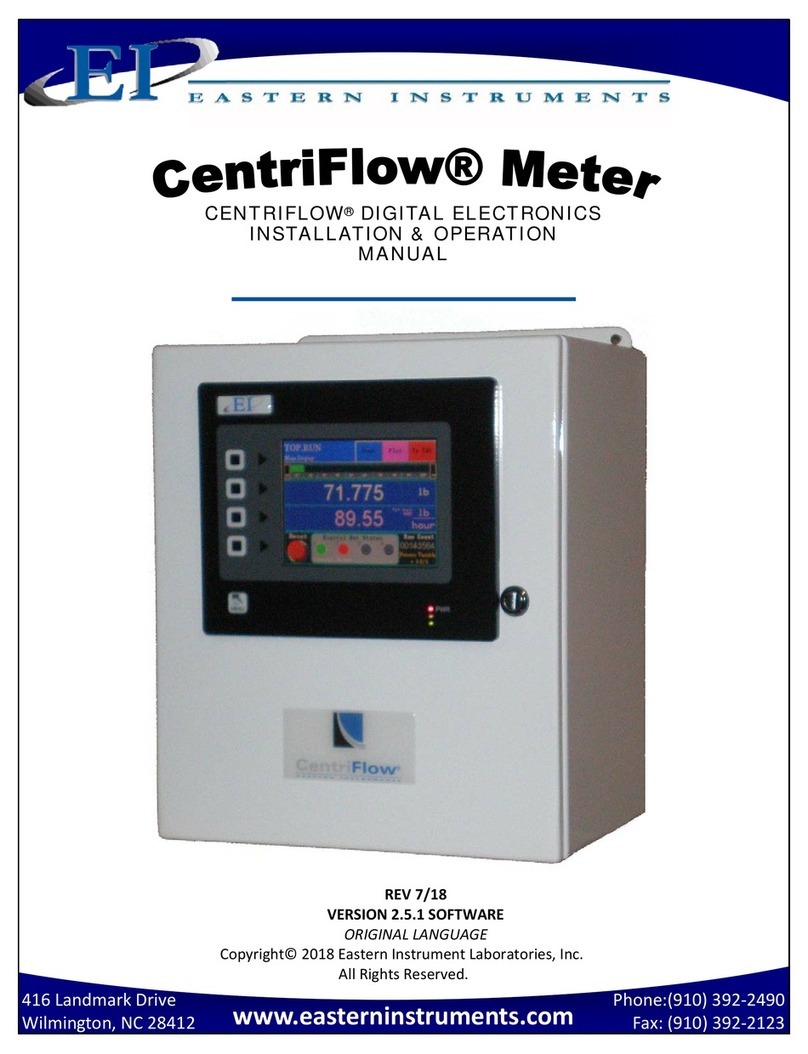
EASTERN INSTRUMENTS
EASTERN INSTRUMENTS CentriFlow Installation & operation manual

Mitsubishi Electric
Mitsubishi Electric ME96NSR user manual